set clock LAND ROVER DISCOVERY 1995 Workshop Manual
[x] Cancel search | Manufacturer: LAND ROVER, Model Year: 1995, Model line: DISCOVERY, Model: LAND ROVER DISCOVERY 1995Pages: 873, PDF Size: 12.89 MB
Page 55 of 873
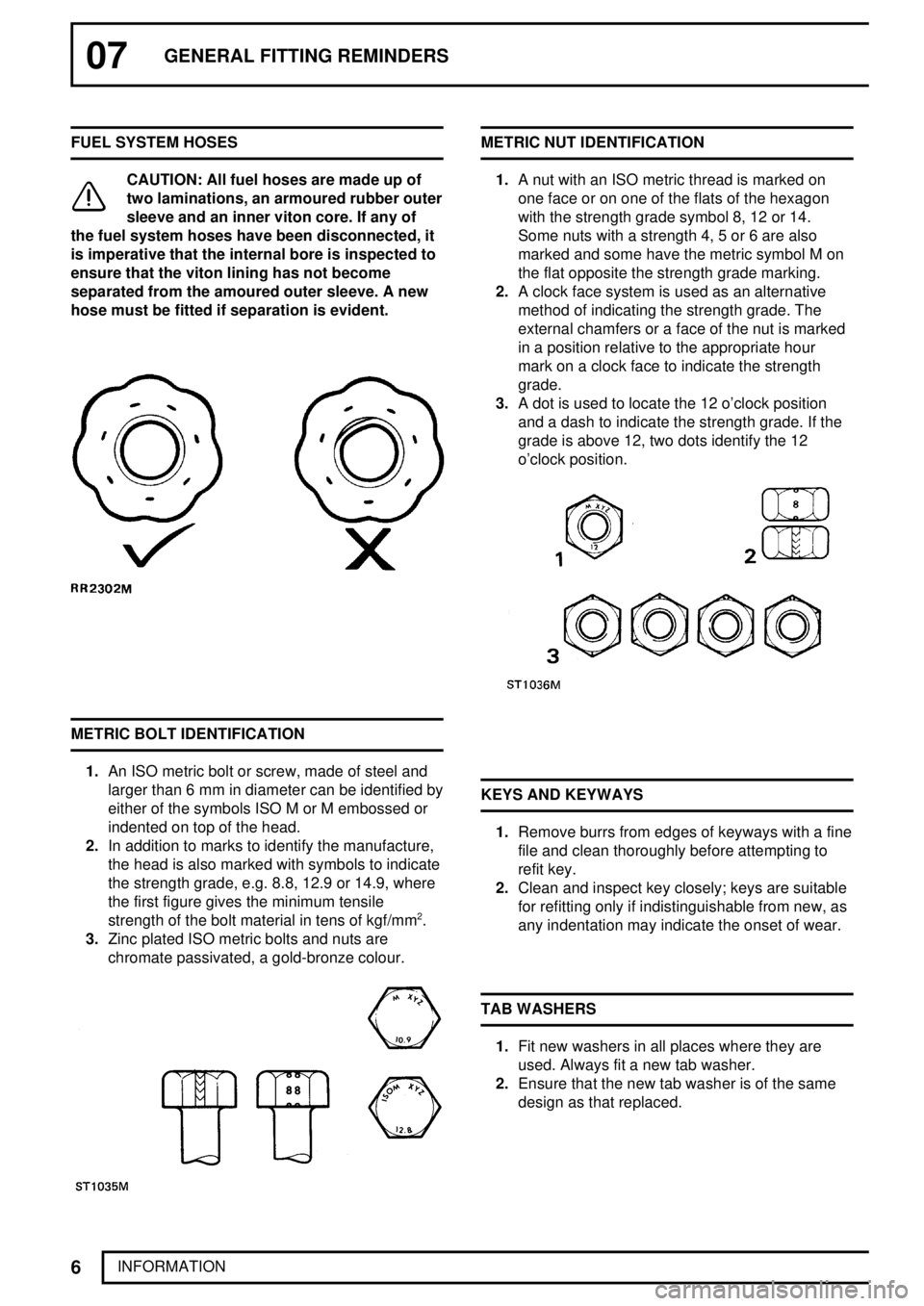
07GENERAL FITTING REMINDERS
6
INFORMATION FUEL SYSTEM HOSES
CAUTION: All fuel hoses are made up of
two laminations, an armoured rubber outer
sleeve and an inner viton core. If any of
the fuel system hoses have been disconnected, it
is imperative that the internal bore is inspected to
ensure that the viton lining has not become
separated from the amoured outer sleeve. A new
hose must be fitted if separation is evident.
METRIC BOLT IDENTIFICATION
1.An ISO metric bolt or screw, made of steel and
larger than 6 mm in diameter can be identified by
either of the symbols ISO M or M embossed or
indented on top of the head.
2.In addition to marks to identify the manufacture,
the head is also marked with symbols to indicate
the strength grade, e.g. 8.8, 12.9 or 14.9, where
the first figure gives the minimum tensile
strength of the bolt material in tens of kgf/mm
2.
3.Zinc plated ISO metric bolts and nuts are
chromate passivated, a gold-bronze colour.
METRIC NUT IDENTIFICATION
1.A nut with an ISO metric thread is marked on
one face or on one of the flats of the hexagon
with the strength grade symbol 8, 12 or 14.
Some nuts with a strength 4, 5 or 6 are also
marked and some have the metric symbol M on
the flat opposite the strength grade marking.
2.A clock face system is used as an alternative
method of indicating the strength grade. The
external chamfers or a face of the nut is marked
in a position relative to the appropriate hour
mark on a clock face to indicate the strength
grade.
3.A dot is used to locate the 12 o'clock position
and a dash to indicate the strength grade. If the
grade is above 12, two dots identify the 12
o'clock position.
KEYS AND KEYWAYS
1.Remove burrs from edges of keyways with a fine
file and clean thoroughly before attempting to
refit key.
2.Clean and inspect key closely; keys are suitable
for refitting only if indistinguishable from new, as
any indentation may indicate the onset of wear.
TAB WASHERS
1.Fit new washers in all places where they are
used. Always fit a new tab washer.
2.Ensure that the new tab washer is of the same
design as that replaced.
Page 64 of 873
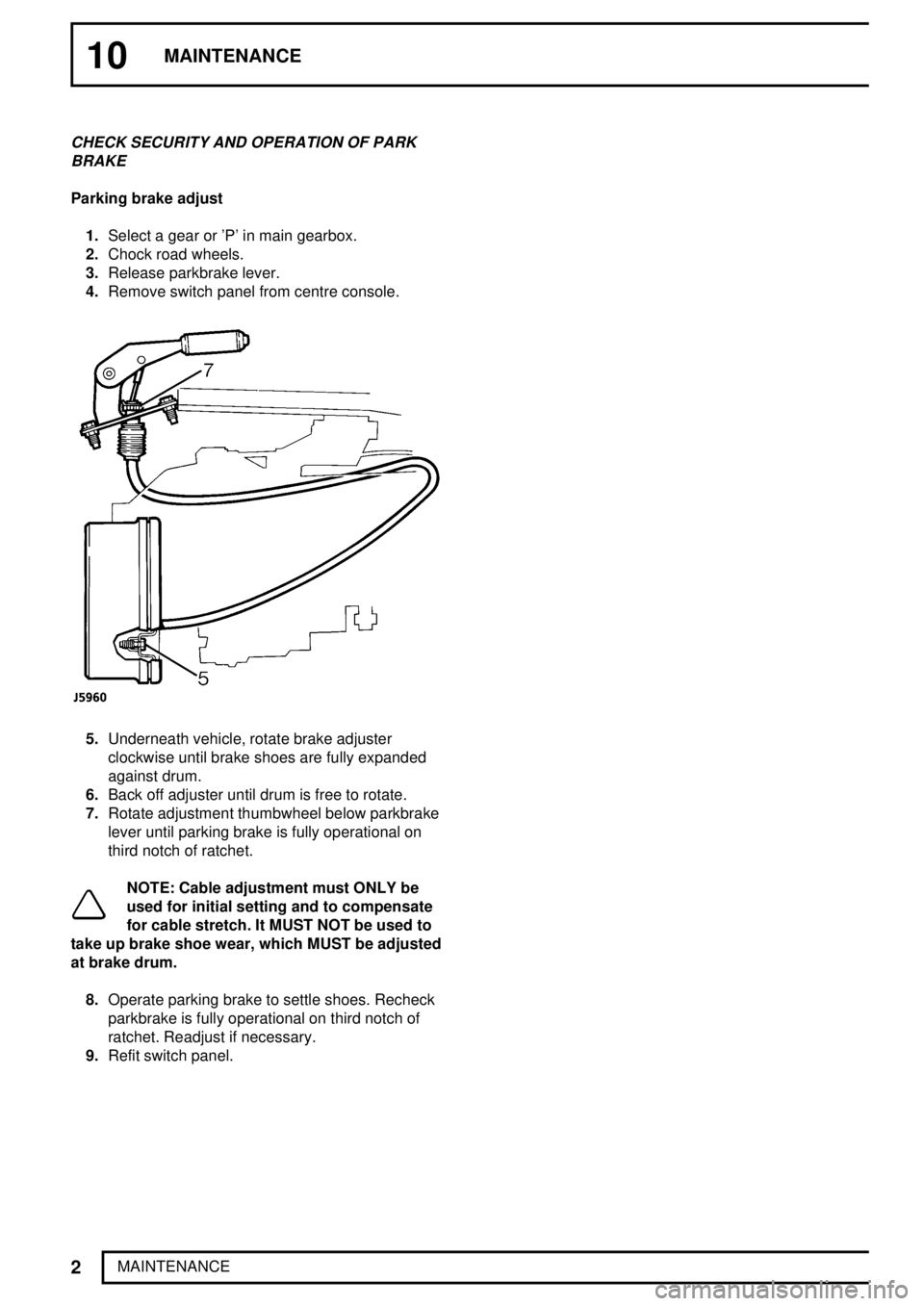
10MAINTENANCE
2
MAINTENANCE
CHECK SECURITY AND OPERATION OF PARK
BRAKE
Parking brake adjust
1.Select a gear or 'P' in main gearbox.
2.Chock road wheels.
3.Release parkbrake lever.
4.Remove switch panel from centre console.
5.Underneath vehicle, rotate brake adjuster
clockwise until brake shoes are fully expanded
against drum.
6.Back off adjuster until drum is free to rotate.
7.Rotate adjustment thumbwheel below parkbrake
lever until parking brake is fully operational on
third notch of ratchet.
NOTE: Cable adjustment must ONLY be
used for initial setting and to compensate
for cable stretch. It MUST NOT be used to
take up brake shoe wear, which MUST be adjusted
at brake drum.
8.Operate parking brake to settle shoes. Recheck
parkbrake is fully operational on third notch of
ratchet. Readjust if necessary.
9.Refit switch panel.
Page 72 of 873
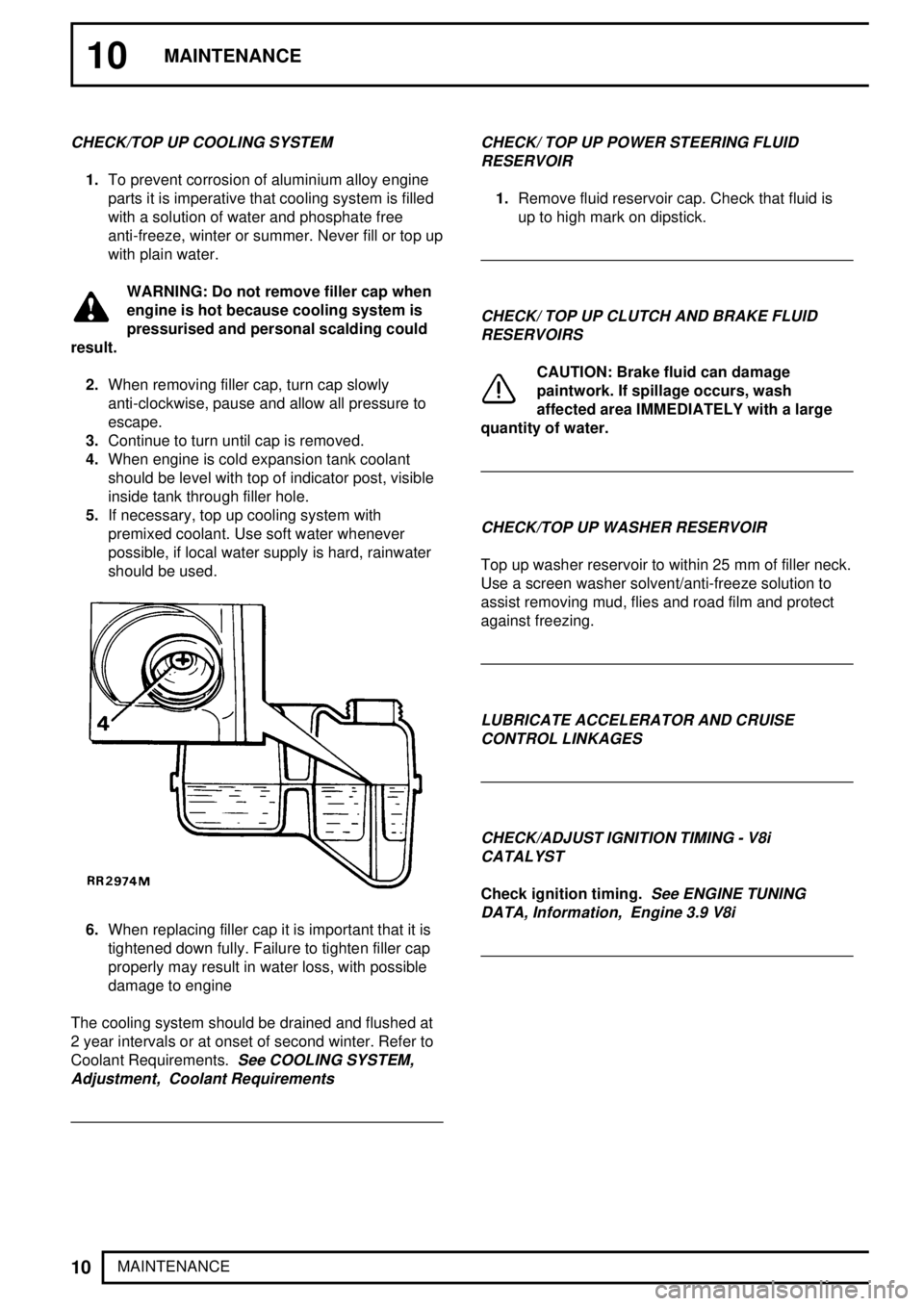
10MAINTENANCE
10
MAINTENANCE
CHECK/TOP UP COOLING SYSTEM
1.To prevent corrosion of aluminium alloy engine
parts it is imperative that cooling system is filled
with a solution of water and phosphate free
anti-freeze, winter or summer. Never fill or top up
with plain water.
WARNING: Do not remove filler cap when
engine is hot because cooling system is
pressurised and personal scalding could
result.
2.When removing filler cap, turn cap slowly
anti-clockwise, pause and allow all pressure to
escape.
3.Continue to turn until cap is removed.
4.When engine is cold expansion tank coolant
should be level with top of indicator post, visible
inside tank through filler hole.
5.If necessary, top up cooling system with
premixed coolant. Use soft water whenever
possible, if local water supply is hard, rainwater
should be used.
6.When replacing filler cap it is important that it is
tightened down fully. Failure to tighten filler cap
properly may result in water loss, with possible
damage to engine
The cooling system should be drained and flushed at
2 year intervals or at onset of second winter. Refer to
Coolant Requirements.
See COOLING SYSTEM,
Adjustment, Coolant RequirementsCHECK/ TOP UP POWER STEERING FLUID
RESERVOIR
1.Remove fluid reservoir cap. Check that fluid is
up to high mark on dipstick.
CHECK/ TOP UP CLUTCH AND BRAKE FLUID
RESERVOIRS
CAUTION: Brake fluid can damage
paintwork. If spillage occurs, wash
affected area IMMEDIATELY with a large
quantity of water.
CHECK/TOP UP WASHER RESERVOIR
Top up washer reservoir to within 25 mm of filler neck.
Use a screen washer solvent/anti-freeze solution to
assist removing mud, flies and road film and protect
against freezing.
LUBRICATE ACCELERATOR AND CRUISE
CONTROL LINKAGES
CHECK/ADJUST IGNITION TIMING - V8i
CATALYST
Check ignition timing.See ENGINE TUNING
DATA, Information, Engine 3.9 V8i
Page 217 of 873
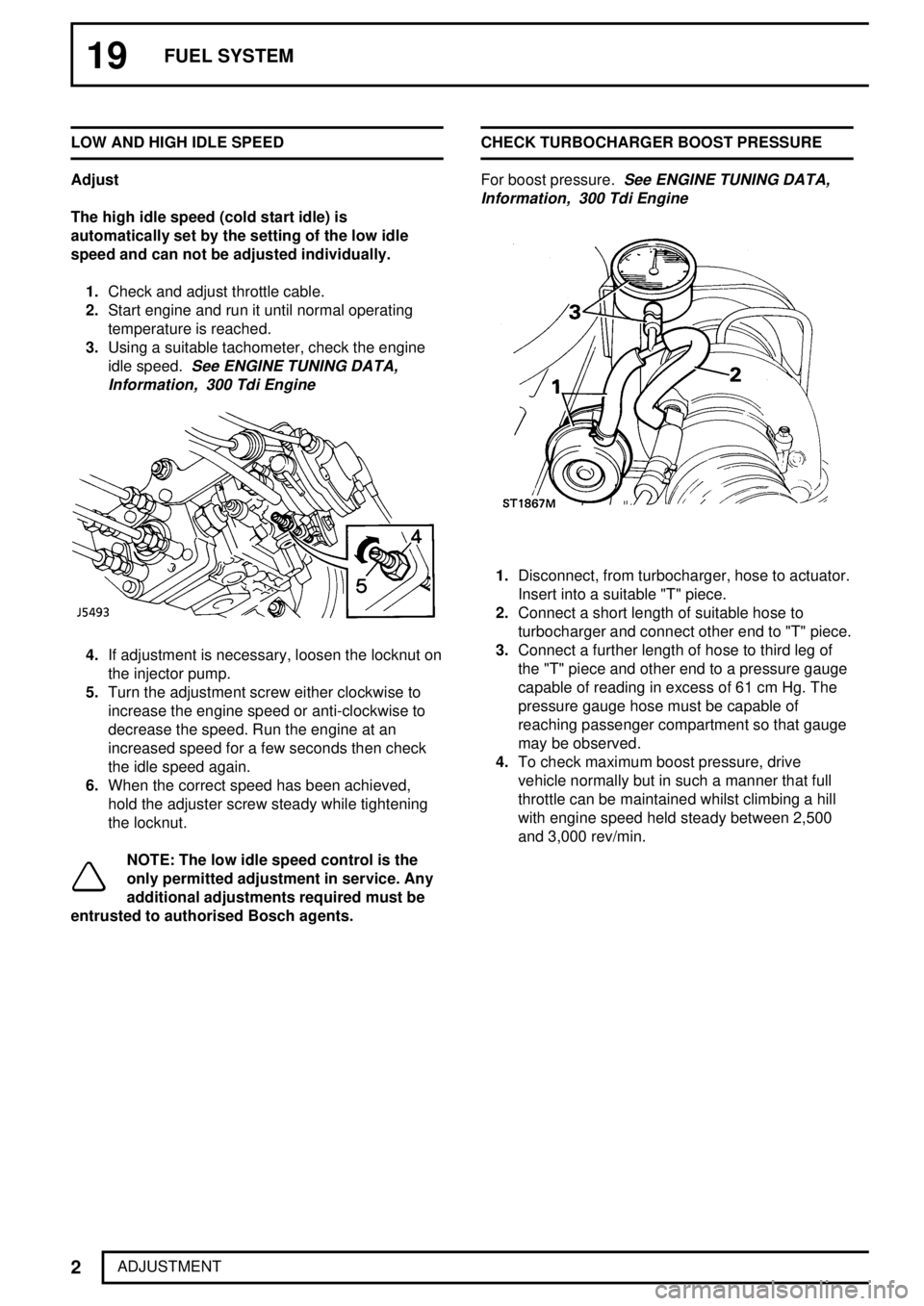
19FUEL SYSTEM
2
ADJUSTMENT LOW AND HIGH IDLE SPEED
Adjust
The high idle speed (cold start idle) is
automatically set by the setting of the low idle
speed and can not be adjusted individually.
1.Check and adjust throttle cable.
2.Start engine and run it until normal operating
temperature is reached.
3.Using a suitable tachometer, check the engine
idle speed.
See ENGINE TUNING DATA,
Information, 300 Tdi Engine
4.If adjustment is necessary, loosen the locknut on
the injector pump.
5.Turn the adjustment screw either clockwise to
increase the engine speed or anti-clockwise to
decrease the speed. Run the engine at an
increased speed for a few seconds then check
the idle speed again.
6.When the correct speed has been achieved,
hold the adjuster screw steady while tightening
the locknut.
NOTE: The low idle speed control is the
only permitted adjustment in service. Any
additional adjustments required must be
entrusted to authorised Bosch agents.CHECK TURBOCHARGER BOOST PRESSURE
For boost pressure.
See ENGINE TUNING DATA,
Information, 300 Tdi Engine
1.Disconnect, from turbocharger, hose to actuator.
Insert into a suitable "T" piece.
2.Connect a short length of suitable hose to
turbocharger and connect other end to "T" piece.
3.Connect a further length of hose to third leg of
the "T" piece and other end to a pressure gauge
capable of reading in excess of 61 cm Hg. The
pressure gauge hose must be capable of
reaching passenger compartment so that gauge
may be observed.
4.To check maximum boost pressure, drive
vehicle normally but in such a manner that full
throttle can be maintained whilst climbing a hill
with engine speed held steady between 2,500
and 3,000 rev/min.
Page 245 of 873
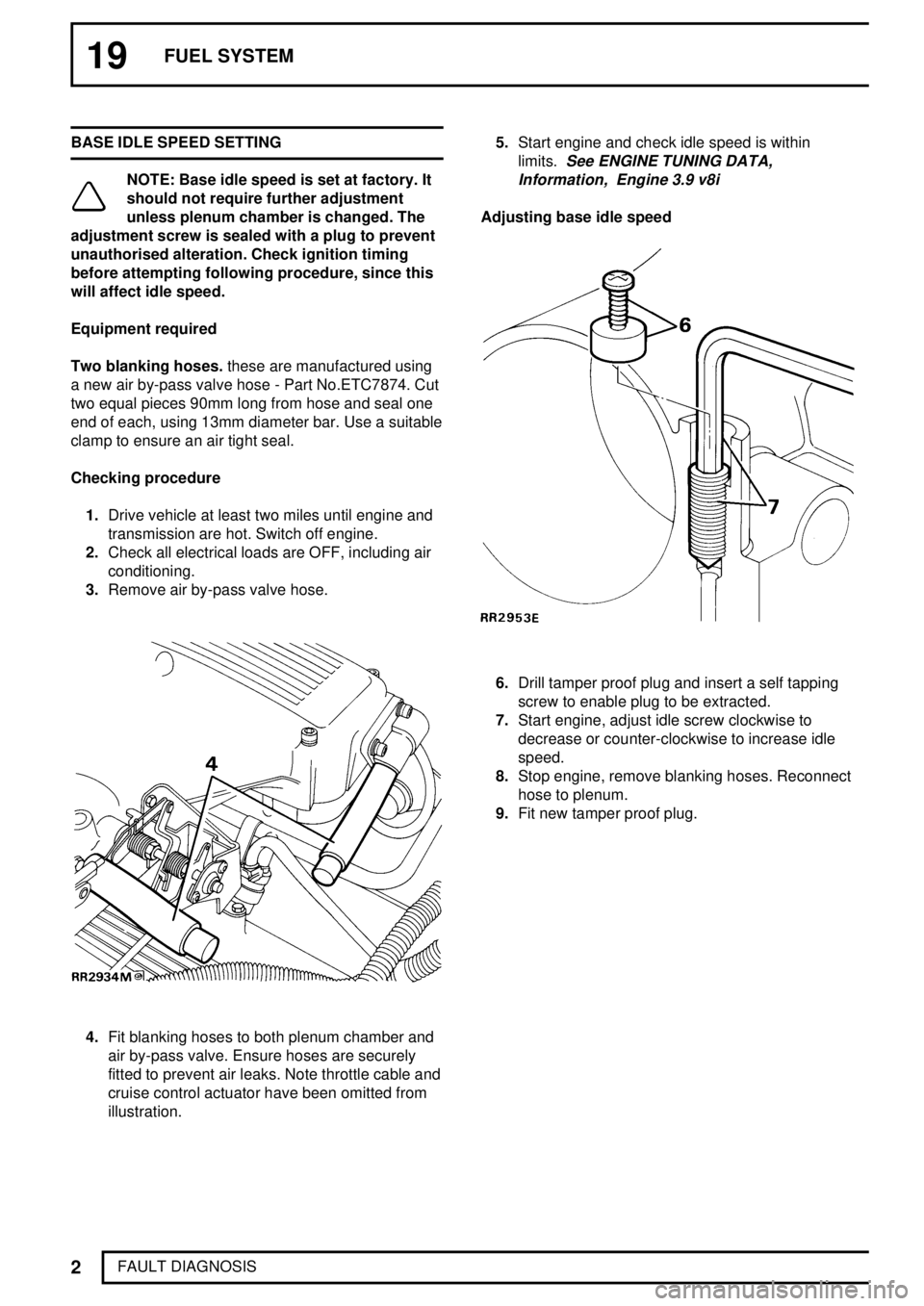
19FUEL SYSTEM
2
FAULT DIAGNOSIS BASE IDLE SPEED SETTING
NOTE: Base idle speed is set at factory. It
should not require further adjustment
unless plenum chamber is changed. The
adjustment screw is sealed with a plug to prevent
unauthorised alteration. Check ignition timing
before attempting following procedure, since this
will affect idle speed.
Equipment required
Two blanking hoses.these are manufactured using
a new air by-pass valve hose - Part No.ETC7874. Cut
two equal pieces 90mm long from hose and seal one
end of each, using 13mm diameter bar. Use a suitable
clamp to ensure an air tight seal.
Checking procedure
1.Drive vehicle at least two miles until engine and
transmission are hot. Switch off engine.
2.Check all electrical loads are OFF, including air
conditioning.
3.Remove air by-pass valve hose.
4.Fit blanking hoses to both plenum chamber and
air by-pass valve. Ensure hoses are securely
fitted to prevent air leaks. Note throttle cable and
cruise control actuator have been omitted from
illustration.5.Start engine and check idle speed is within
limits.
See ENGINE TUNING DATA,
Information, Engine 3.9 v8i
Adjusting base idle speed
6.Drill tamper proof plug and insert a self tapping
screw to enable plug to be extracted.
7.Start engine, adjust idle screw clockwise to
decrease or counter-clockwise to increase idle
speed.
8.Stop engine, remove blanking hoses. Reconnect
hose to plenum.
9.Fit new tamper proof plug.
Page 362 of 873
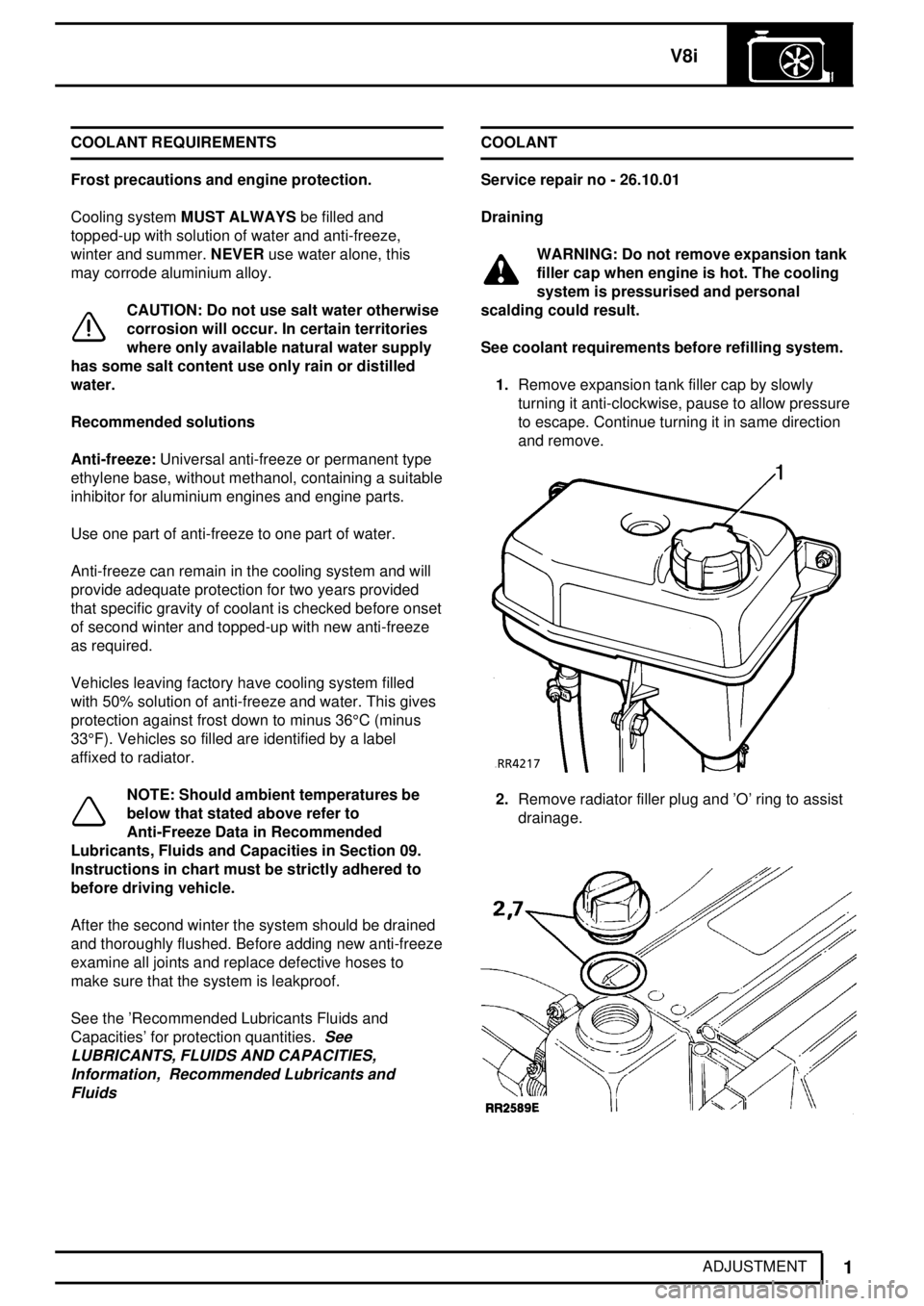
V8i
1
ADJUSTMENT COOLANT REQUIREMENTS
Frost precautions and engine protection.
Cooling systemMUST ALWAYSbe filled and
topped-up with solution of water and anti-freeze,
winter and summer.NEVERuse water alone, this
may corrode aluminium alloy.
CAUTION: Do not use salt water otherwise
corrosion will occur. In certain territories
where only available natural water supply
has some salt content use only rain or distilled
water.
Recommended solutions
Anti-freeze:Universal anti-freeze or permanent type
ethylene base, without methanol, containing a suitable
inhibitor for aluminium engines and engine parts.
Use one part of anti-freeze to one part of water.
Anti-freeze can remain in the cooling system and will
provide adequate protection for two years provided
that specific gravity of coolant is checked before onset
of second winter and topped-up with new anti-freeze
as required.
Vehicles leaving factory have cooling system filled
with 50% solution of anti-freeze and water. This gives
protection against frost down to minus 36°C (minus
33°F). Vehicles so filled are identified by a label
affixed to radiator.
NOTE: Should ambient temperatures be
below that stated above refer to
Anti-Freeze Data in Recommended
Lubricants, Fluids and Capacities in Section 09.
Instructions in chart must be strictly adhered to
before driving vehicle.
After the second winter the system should be drained
and thoroughly flushed. Before adding new anti-freeze
examine all joints and replace defective hoses to
make sure that the system is leakproof.
See the 'Recommended Lubricants Fluids and
Capacities' for protection quantities.
See
LUBRICANTS, FLUIDS AND CAPACITIES,
Information, Recommended Lubricants and
Fluids
COOLANT
Service repair no - 26.10.01
Draining
WARNING: Do not remove expansion tank
filler cap when engine is hot. The cooling
system is pressurised and personal
scalding could result.
See coolant requirements before refilling system.
1.Remove expansion tank filler cap by slowly
turning it anti-clockwise, pause to allow pressure
to escape. Continue turning it in same direction
and remove.
2.Remove radiator filler plug and 'O' ring to assist
drainage.
Page 509 of 873
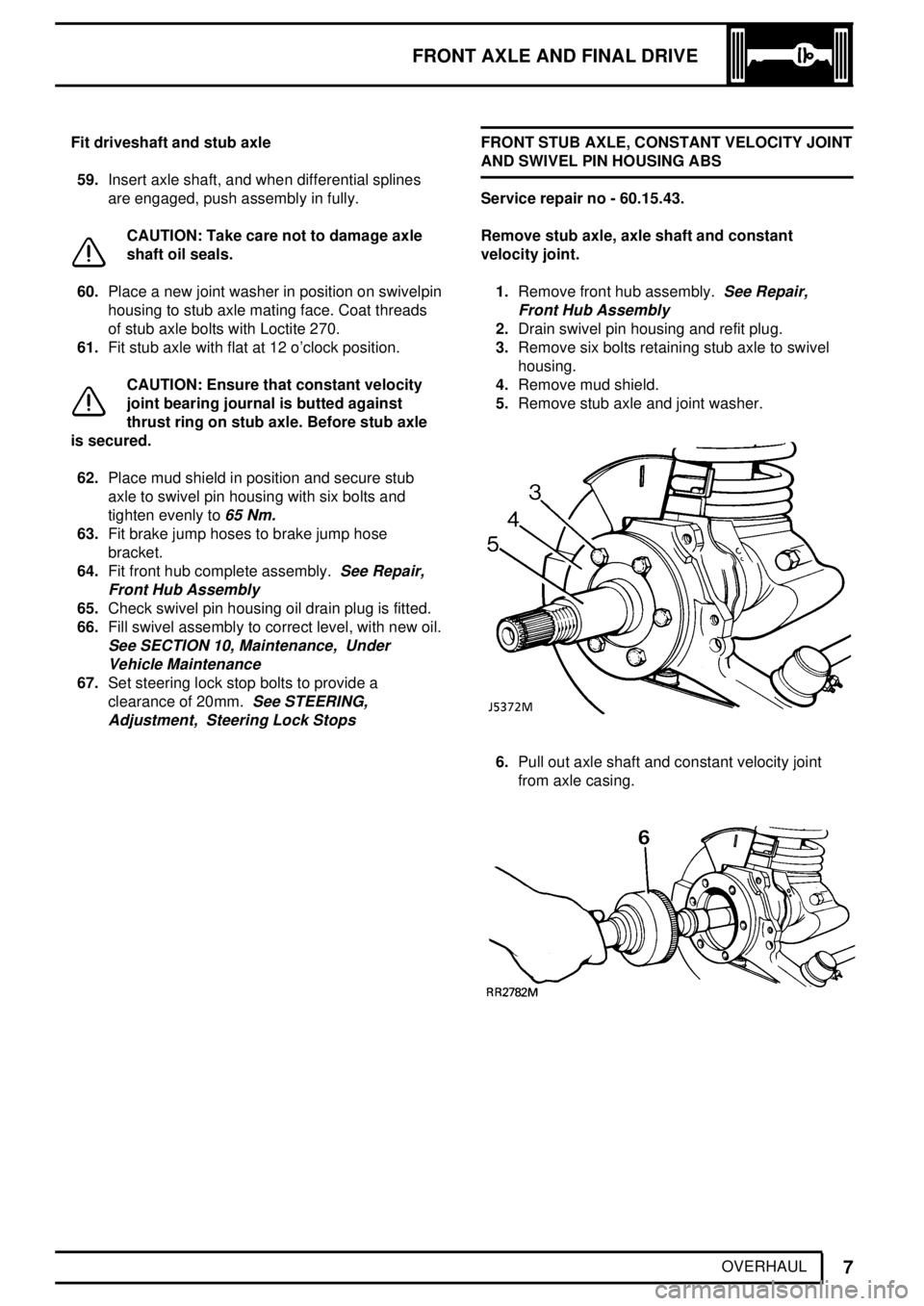
FRONT AXLE AND FINAL DRIVE
7
OVERHAUL Fit driveshaft and stub axle
59.Insert axle shaft, and when differential splines
are engaged, push assembly in fully.
CAUTION: Take care not to damage axle
shaft oil seals.
60.Place a new joint washer in position on swivelpin
housing to stub axle mating face. Coat threads
of stub axle bolts with Loctite 270.
61.Fit stub axle with flat at 12 o'clock position.
CAUTION: Ensure that constant velocity
joint bearing journal is butted against
thrust ring on stub axle. Before stub axle
is secured.
62.Place mud shield in position and secure stub
axle to swivel pin housing with six bolts and
tighten evenly to
65 Nm.
63.Fit brake jump hoses to brake jump hose
bracket.
64.Fit front hub complete assembly.
See Repair,
Front Hub Assembly
65.Check swivel pin housing oil drain plug is fitted.
66.Fill swivel assembly to correct level, with new oil.
See SECTION 10, Maintenance, Under
Vehicle Maintenance
67.Set steering lock stop bolts to provide a
clearance of 20mm.
See STEERING,
Adjustment, Steering Lock Stops
FRONT STUB AXLE, CONSTANT VELOCITY JOINT
AND SWIVEL PIN HOUSING ABS
Service repair no - 60.15.43.
Remove stub axle, axle shaft and constant
velocity joint.
1.Remove front hub assembly.
See Repair,
Front Hub Assembly
2.Drain swivel pin housing and refit plug.
3.Remove six bolts retaining stub axle to swivel
housing.
4.Remove mud shield.
5.Remove stub axle and joint washer.
6.Pull out axle shaft and constant velocity joint
from axle casing.
Page 513 of 873
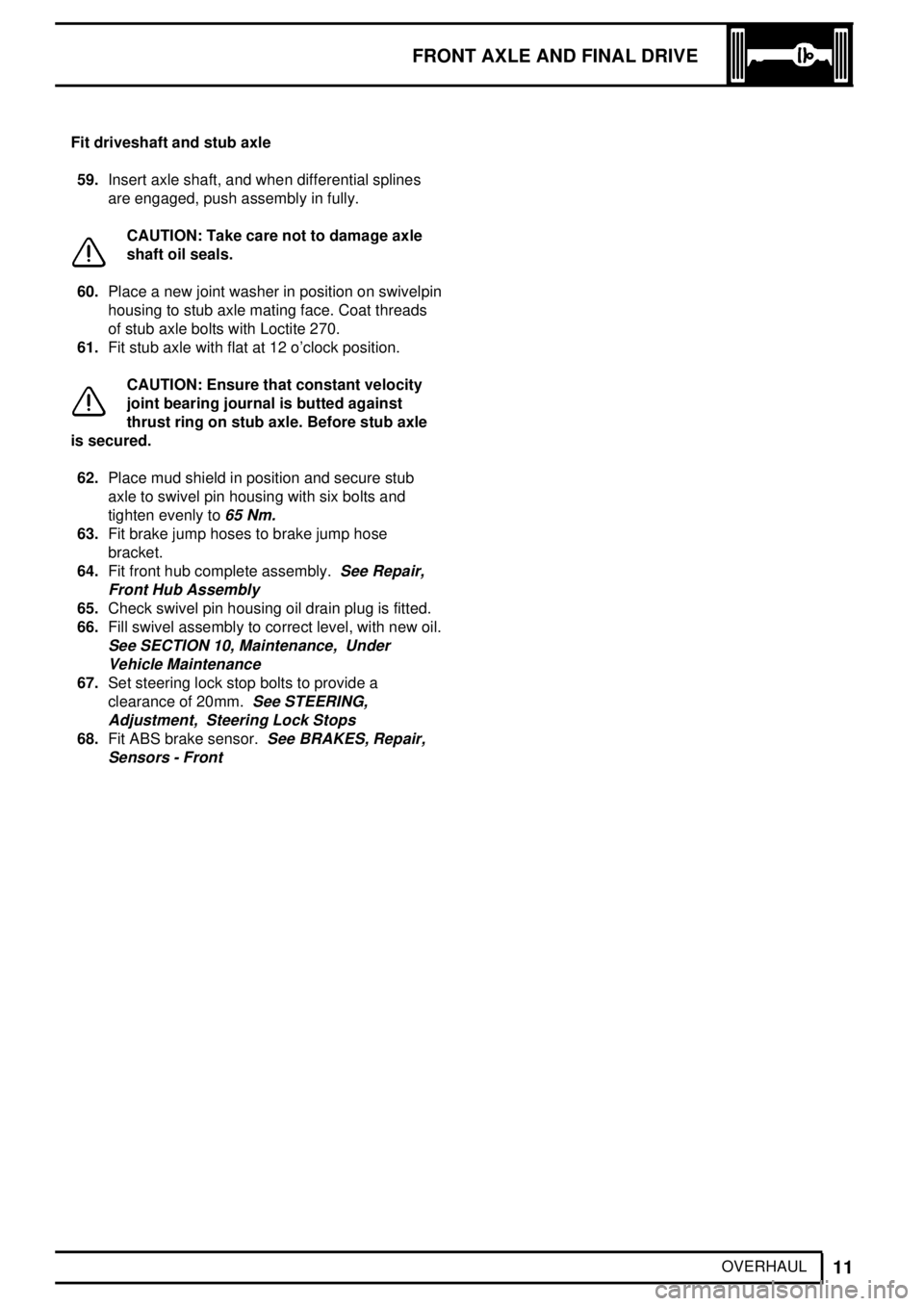
FRONT AXLE AND FINAL DRIVE
11
OVERHAUL Fit driveshaft and stub axle
59.Insert axle shaft, and when differential splines
are engaged, push assembly in fully.
CAUTION: Take care not to damage axle
shaft oil seals.
60.Place a new joint washer in position on swivelpin
housing to stub axle mating face. Coat threads
of stub axle bolts with Loctite 270.
61.Fit stub axle with flat at 12 o'clock position.
CAUTION: Ensure that constant velocity
joint bearing journal is butted against
thrust ring on stub axle. Before stub axle
is secured.
62.Place mud shield in position and secure stub
axle to swivel pin housing with six bolts and
tighten evenly to
65 Nm.
63.Fit brake jump hoses to brake jump hose
bracket.
64.Fit front hub complete assembly.
See Repair,
Front Hub Assembly
65.Check swivel pin housing oil drain plug is fitted.
66.Fill swivel assembly to correct level, with new oil.
See SECTION 10, Maintenance, Under
Vehicle Maintenance
67.Set steering lock stop bolts to provide a
clearance of 20mm.
See STEERING,
Adjustment, Steering Lock Stops
68.Fit ABS brake sensor.See BRAKES, Repair,
Sensors - Front
Page 568 of 873
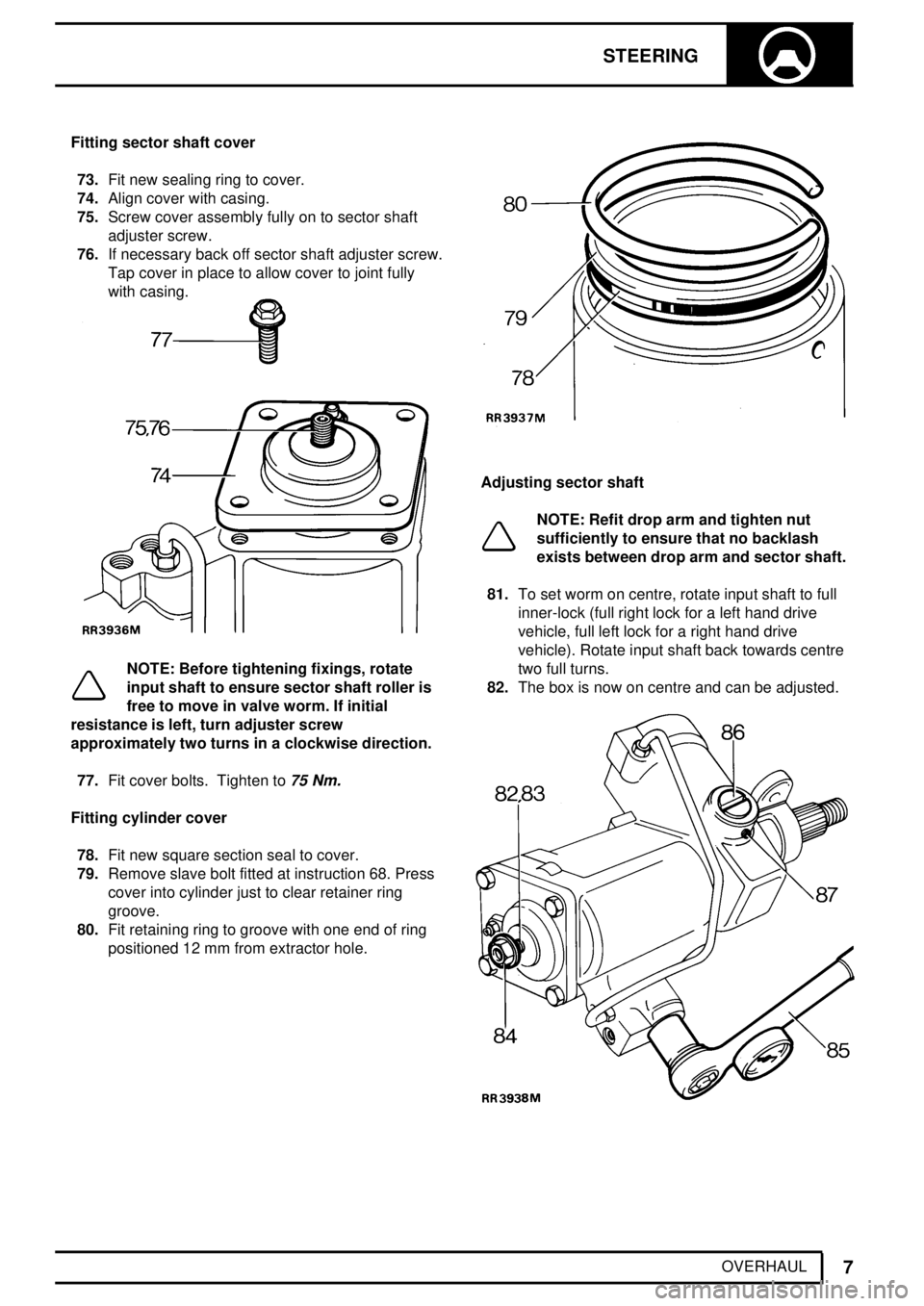
STEERING
7
OVERHAUL Fitting sector shaft cover
73.Fit new sealing ring to cover.
74.Align cover with casing.
75.Screw cover assembly fully on to sector shaft
adjuster screw.
76.If necessary back off sector shaft adjuster screw.
Tap cover in place to allow cover to joint fully
with casing.
NOTE: Before tightening fixings, rotate
input shaft to ensure sector shaft roller is
free to move in valve worm. If initial
resistance is left, turn adjuster screw
approximately two turns in a clockwise direction.
77.Fit cover bolts. Tighten to
75 Nm.
Fitting cylinder cover
78.Fit new square section seal to cover.
79.Remove slave bolt fitted at instruction 68. Press
cover into cylinder just to clear retainer ring
groove.
80.Fit retaining ring to groove with one end of ring
positioned 12 mm from extractor hole.
Adjusting sector shaft
NOTE: Refit drop arm and tighten nut
sufficiently to ensure that no backlash
exists between drop arm and sector shaft.
81.To set worm on centre, rotate input shaft to full
inner-lock (full right lock for a left hand drive
vehicle, full left lock for a right hand drive
vehicle). Rotate input shaft back towards centre
two full turns.
82.The box is now on centre and can be adjusted.
Page 673 of 873
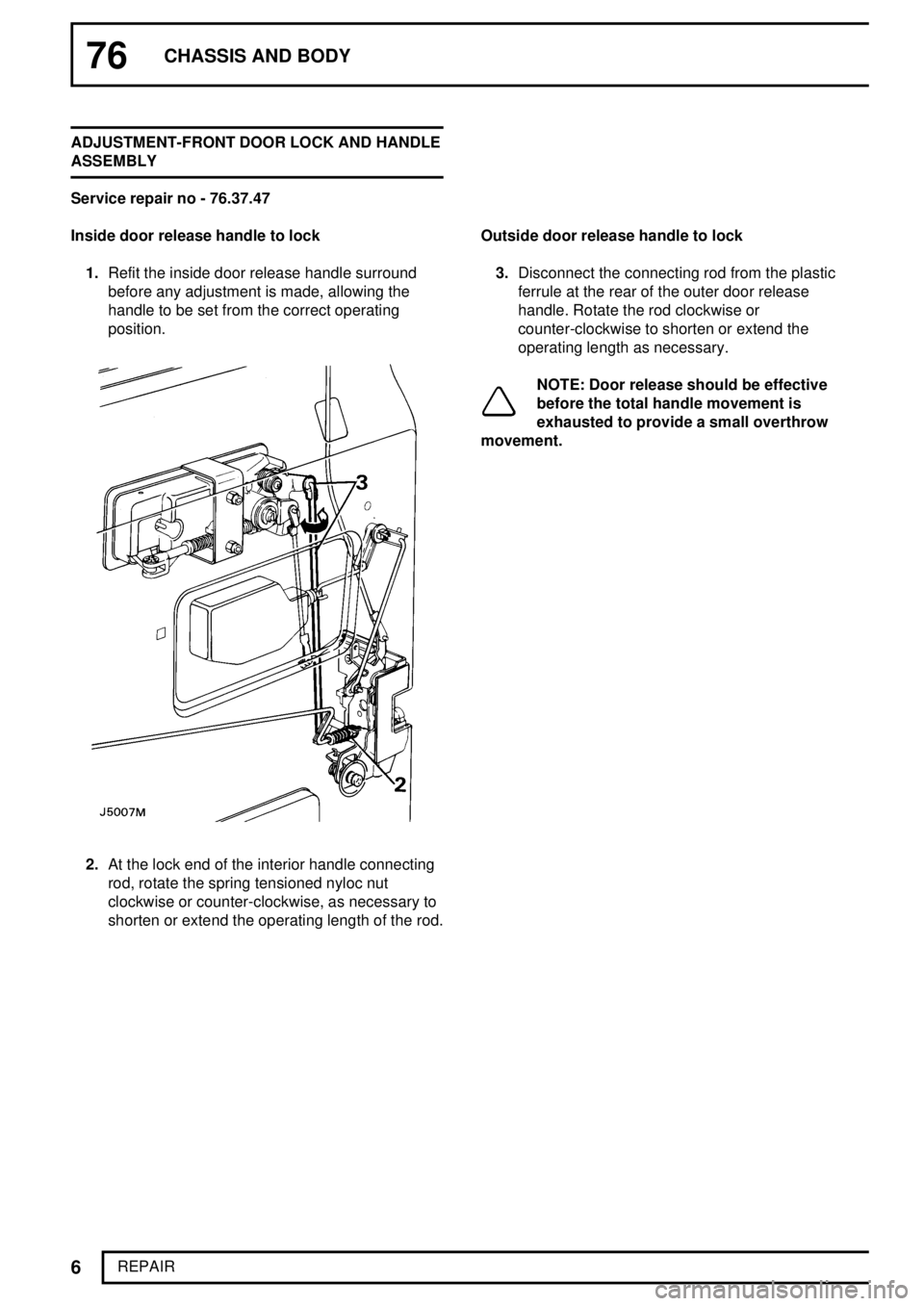
76CHASSIS AND BODY
6
REPAIR ADJUSTMENT-FRONT DOOR LOCK AND HANDLE
ASSEMBLY
Service repair no - 76.37.47
Inside door release handle to lock
1.Refit the inside door release handle surround
before any adjustment is made, allowing the
handle to be set from the correct operating
position.
2.At the lock end of the interior handle connecting
rod, rotate the spring tensioned nyloc nut
clockwise or counter-clockwise, as necessary to
shorten or extend the operating length of the rod.Outside door release handle to lock
3.Disconnect the connecting rod from the plastic
ferrule at the rear of the outer door release
handle. Rotate the rod clockwise or
counter-clockwise to shorten or extend the
operating length as necessary.
NOTE: Door release should be effective
before the total handle movement is
exhausted to provide a small overthrow
movement.