LAND ROVER DISCOVERY 1999 Workshop Manual
Manufacturer: LAND ROVER, Model Year: 1999, Model line: DISCOVERY, Model: LAND ROVER DISCOVERY 1999Pages: 1529, PDF Size: 34.8 MB
Page 1281 of 1529
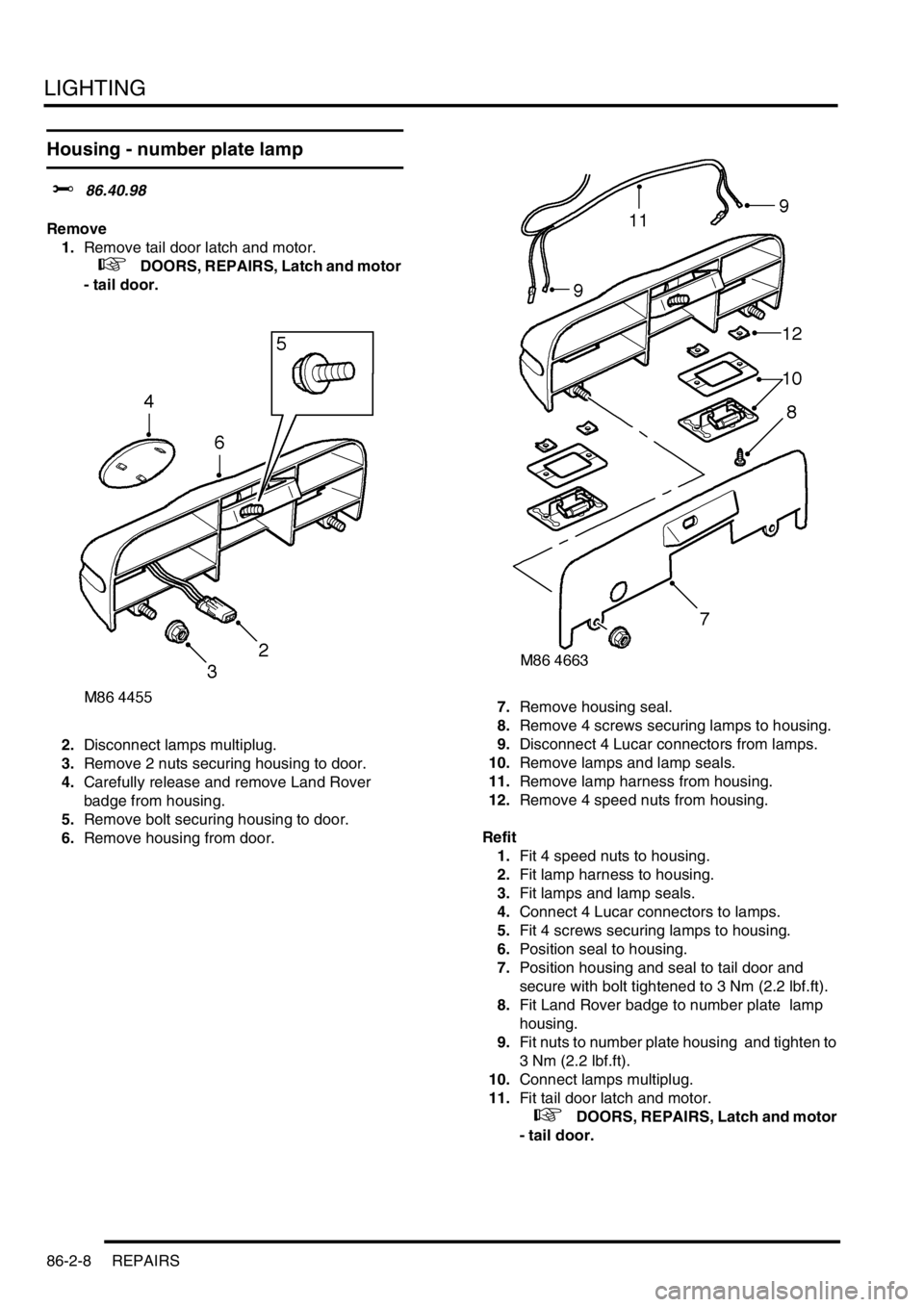
LIGHTING
86-2-8 REPAIRS
Housing - number plate lamp
$% 86.40.98
Remove
1.Remove tail door latch and motor.
+ DOORS, REPAIRS, Latch and motor
- tail door.
2.Disconnect lamps multiplug.
3.Remove 2 nuts securing housing to door.
4.Carefully release and remove Land Rover
badge from housing.
5.Remove bolt securing housing to door.
6.Remove housing from door. 7.Remove housing seal.
8.Remove 4 screws securing lamps to housing.
9.Disconnect 4 Lucar connectors from lamps.
10.Remove lamps and lamp seals.
11.Remove lamp harness from housing.
12.Remove 4 speed nuts from housing.
Refit
1.Fit 4 speed nuts to housing.
2.Fit lamp harness to housing.
3.Fit lamps and lamp seals.
4.Connect 4 Lucar connectors to lamps.
5.Fit 4 screws securing lamps to housing.
6.Position seal to housing.
7.Position housing and seal to tail door and
secure with bolt tightened to 3 Nm (2.2 lbf.ft).
8.Fit Land Rover badge to number plate lamp
housing.
9.Fit nuts to number plate housing and tighten to
3 Nm (2.2 lbf.ft).
10.Connect lamps multiplug.
11.Fit tail door latch and motor.
+ DOORS, REPAIRS, Latch and motor
- tail door.
Page 1282 of 1529
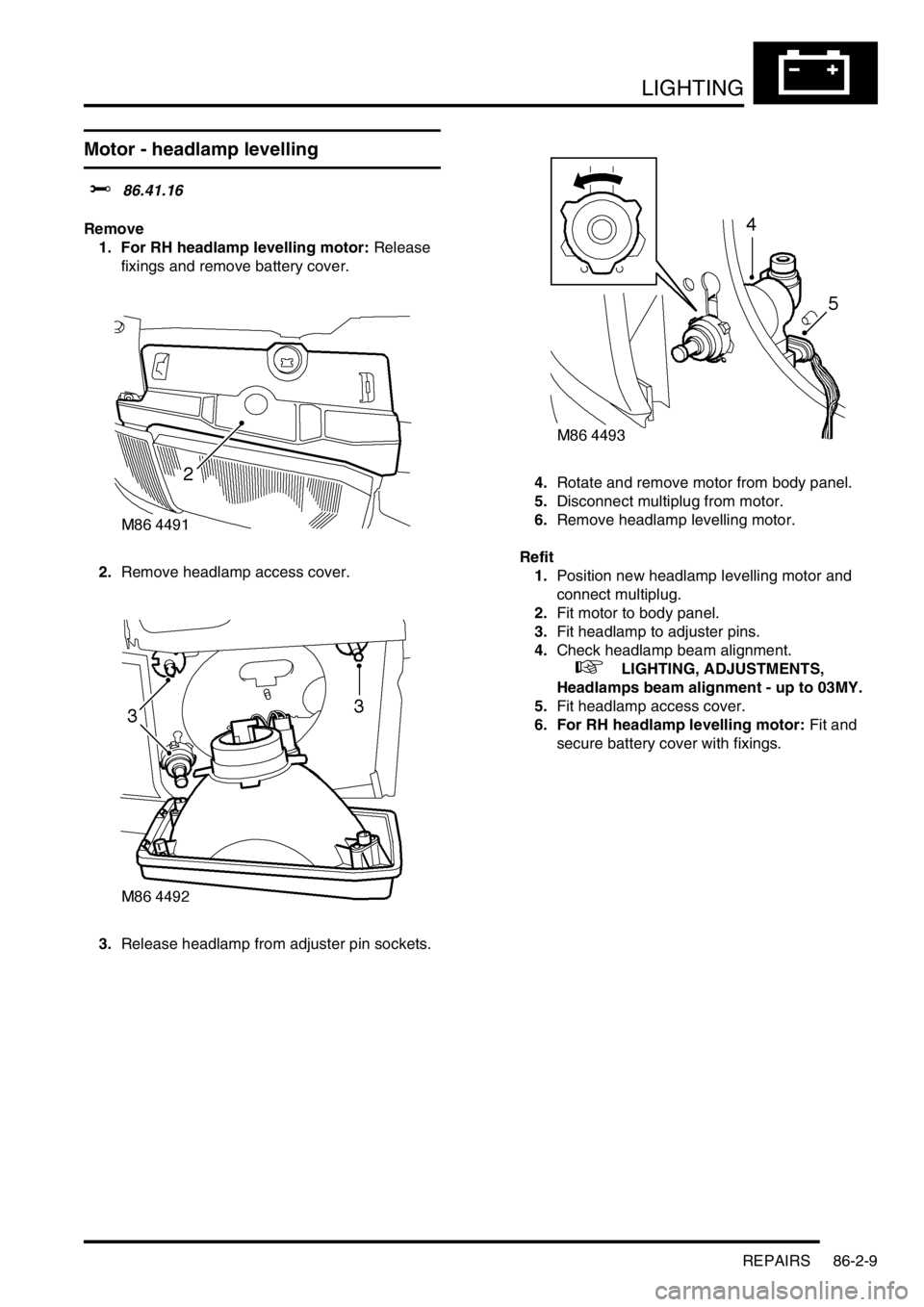
LIGHTING
REPAIRS 86-2-9
Motor - headlamp levelling
$% 86.41.16
Remove
1. For RH headlamp levelling motor: Release
fixings and remove battery cover.
2.Remove headlamp access cover.
3.Release headlamp from adjuster pin sockets. 4.Rotate and remove motor from body panel.
5.Disconnect multiplug from motor.
6.Remove headlamp levelling motor.
Refit
1.Position new headlamp levelling motor and
connect multiplug.
2.Fit motor to body panel.
3.Fit headlamp to adjuster pins.
4.Check headlamp beam alignment.
+ LIGHTING, ADJUSTMENTS,
Headlamps beam alignment - up to 03MY.
5.Fit headlamp access cover.
6. For RH headlamp levelling motor: Fit and
secure battery cover with fixings.
Page 1283 of 1529
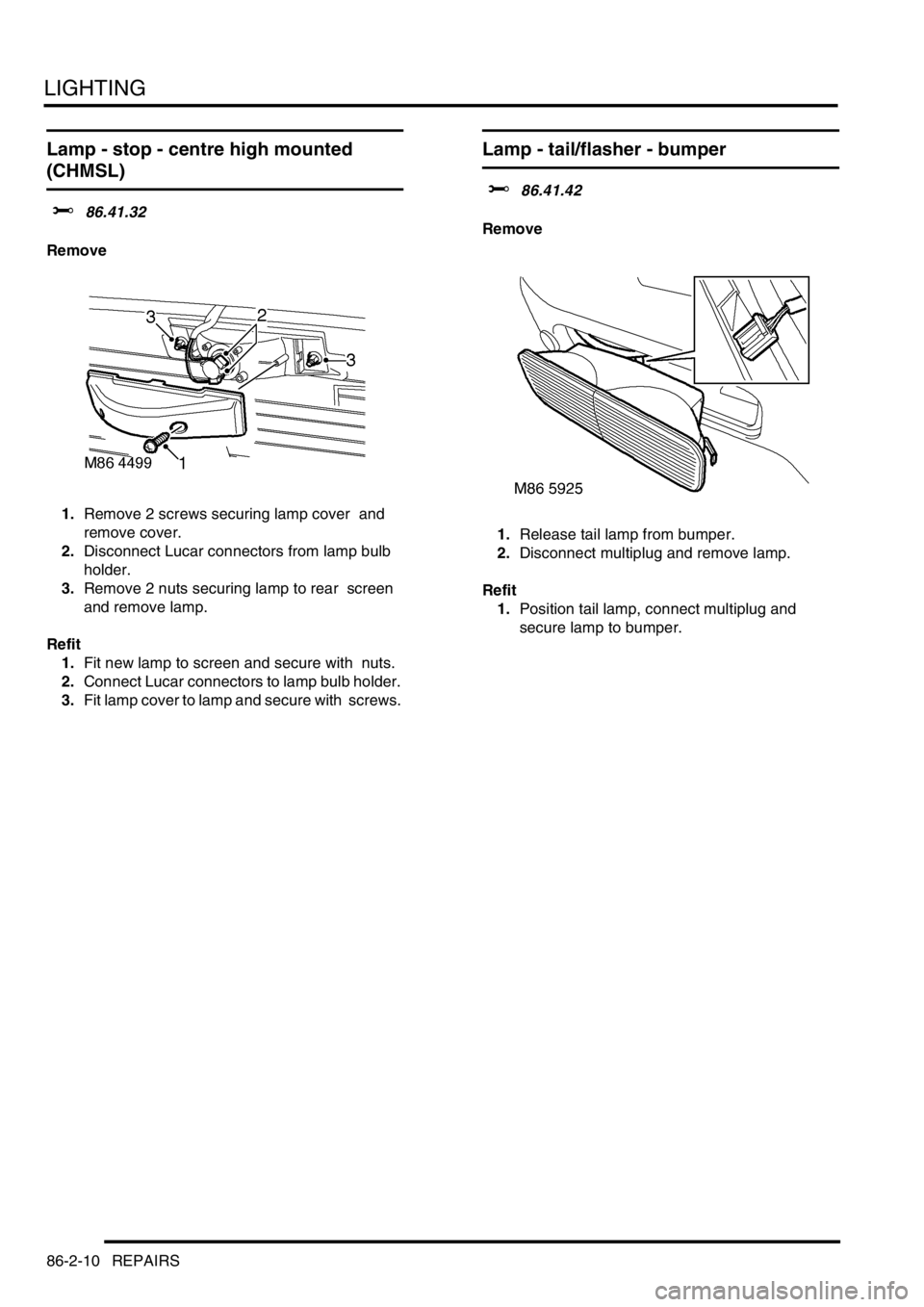
LIGHTING
86-2-10 REPAIRS
Lamp - stop - centre high mounted
(CHMSL)
$% 86.41.32
Remove
1.Remove 2 screws securing lamp cover and
remove cover.
2.Disconnect Lucar connectors from lamp bulb
holder.
3.Remove 2 nuts securing lamp to rear screen
and remove lamp.
Refit
1.Fit new lamp to screen and secure with nuts.
2.Connect Lucar connectors to lamp bulb holder.
3.Fit lamp cover to lamp and secure with screws.
Lamp - tail/flasher - bumper
$% 86.41.42
Remove
1.Release tail lamp from bumper.
2.Disconnect multiplug and remove lamp.
Refit
1.Position tail lamp, connect multiplug and
secure lamp to bumper.
Page 1284 of 1529
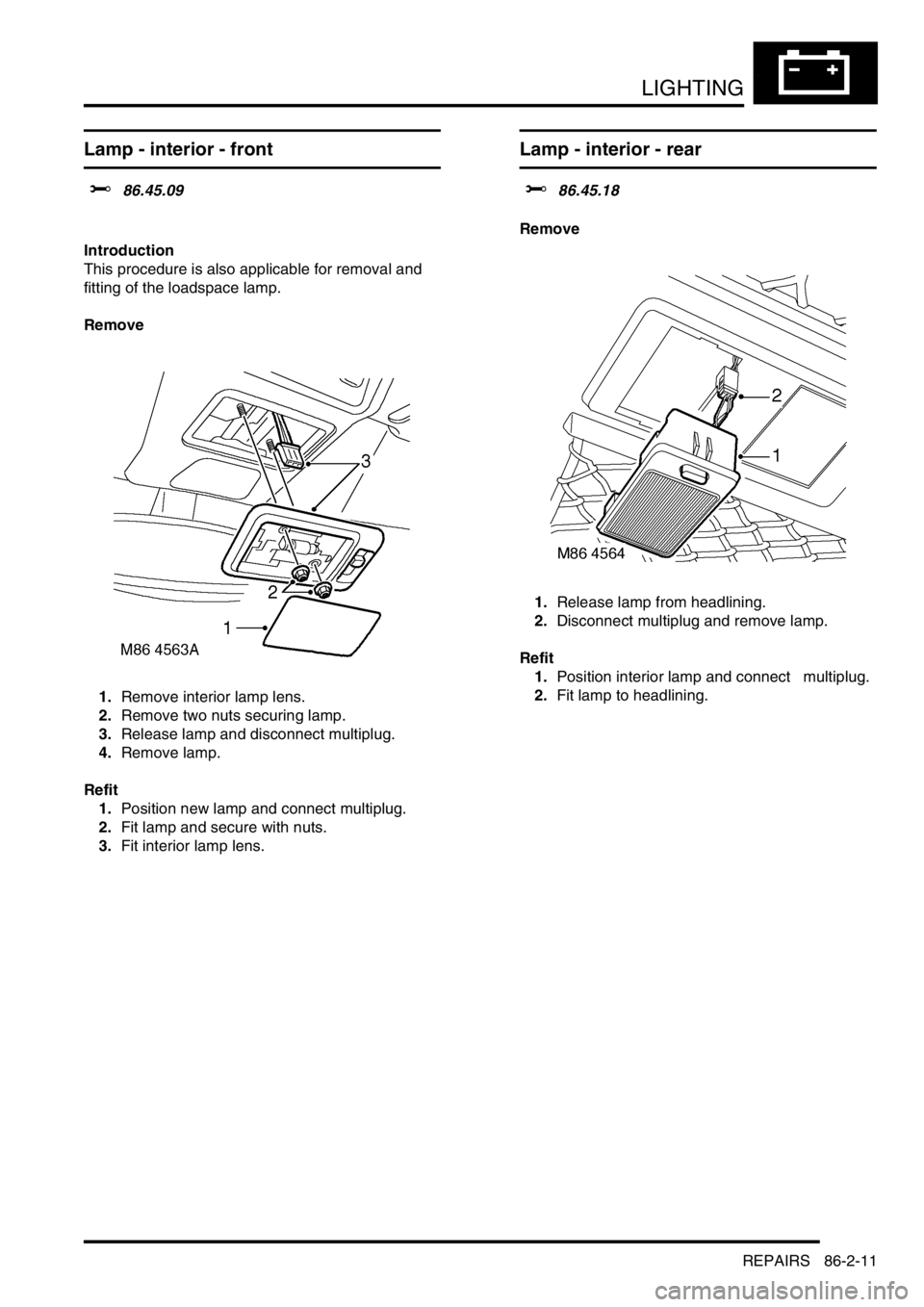
LIGHTING
REPAIRS 86-2-11
Lamp - interior - front
$% 86.45.09
Introduction
This procedure is also applicable for removal and
fitting of the loadspace lamp.
Remove
1.Remove interior lamp lens.
2.Remove two nuts securing lamp.
3.Release lamp and disconnect multiplug.
4.Remove lamp.
Refit
1.Position new lamp and connect multiplug.
2.Fit lamp and secure with nuts.
3.Fit interior lamp lens.
Lamp - interior - rear
$% 86.45.18
Remove
1.Release lamp from headlining.
2.Disconnect multiplug and remove lamp.
Refit
1.Position interior lamp and connect multiplug.
2.Fit lamp to headlining.
Page 1285 of 1529
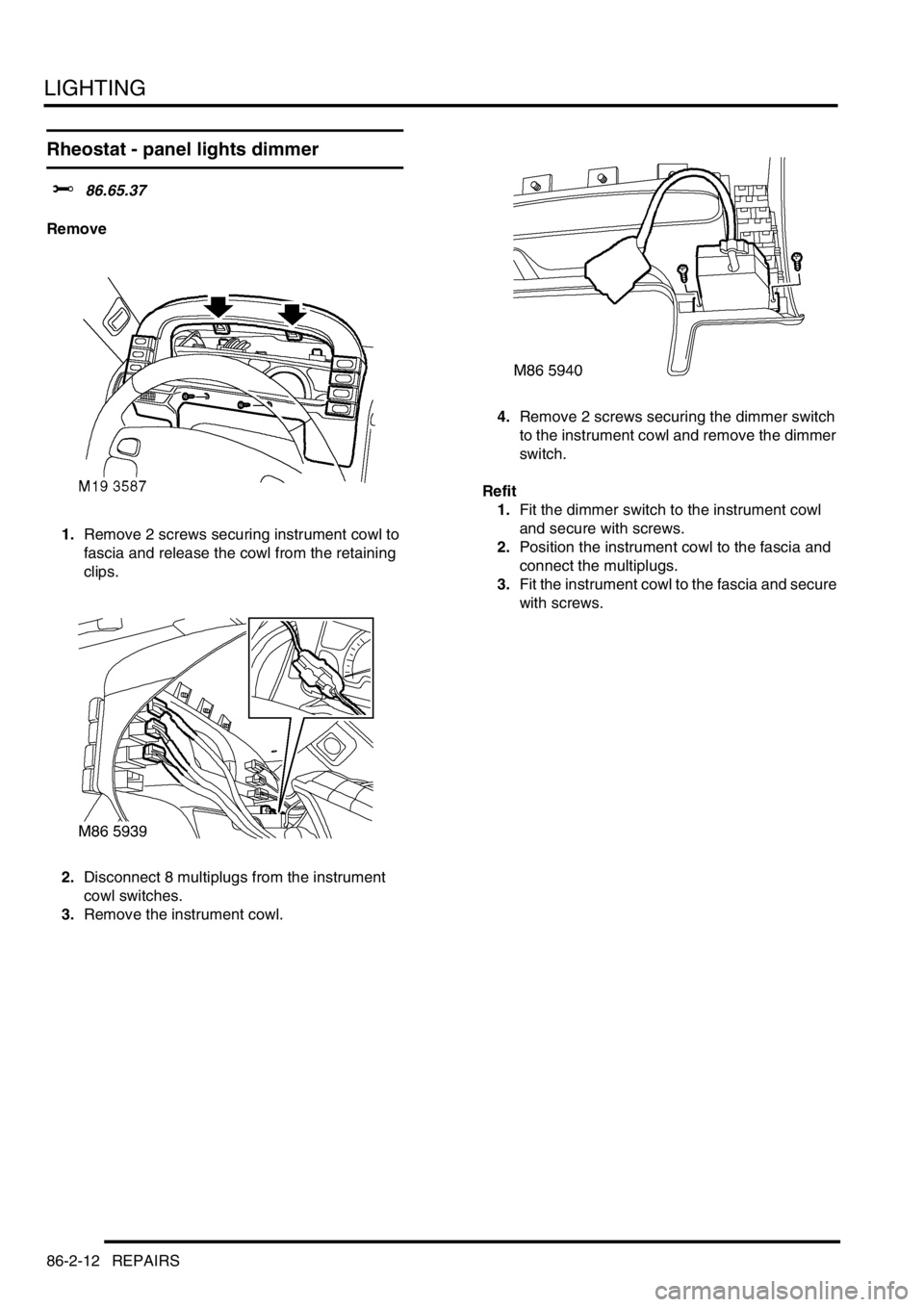
LIGHTING
86-2-12 REPAIRS
Rheostat - panel lights dimmer
$% 86.65.37
Remove
1.Remove 2 screws securing instrument cowl to
fascia and release the cowl from the retaining
clips.
2.Disconnect 8 multiplugs from the instrument
cowl switches.
3.Remove the instrument cowl.4.Remove 2 screws securing the dimmer switch
to the instrument cowl and remove the dimmer
switch.
Refit
1.Fit the dimmer switch to the instrument cowl
and secure with screws.
2.Position the instrument cowl to the fascia and
connect the multiplugs.
3.Fit the instrument cowl to the fascia and secure
with screws.
Page 1286 of 1529
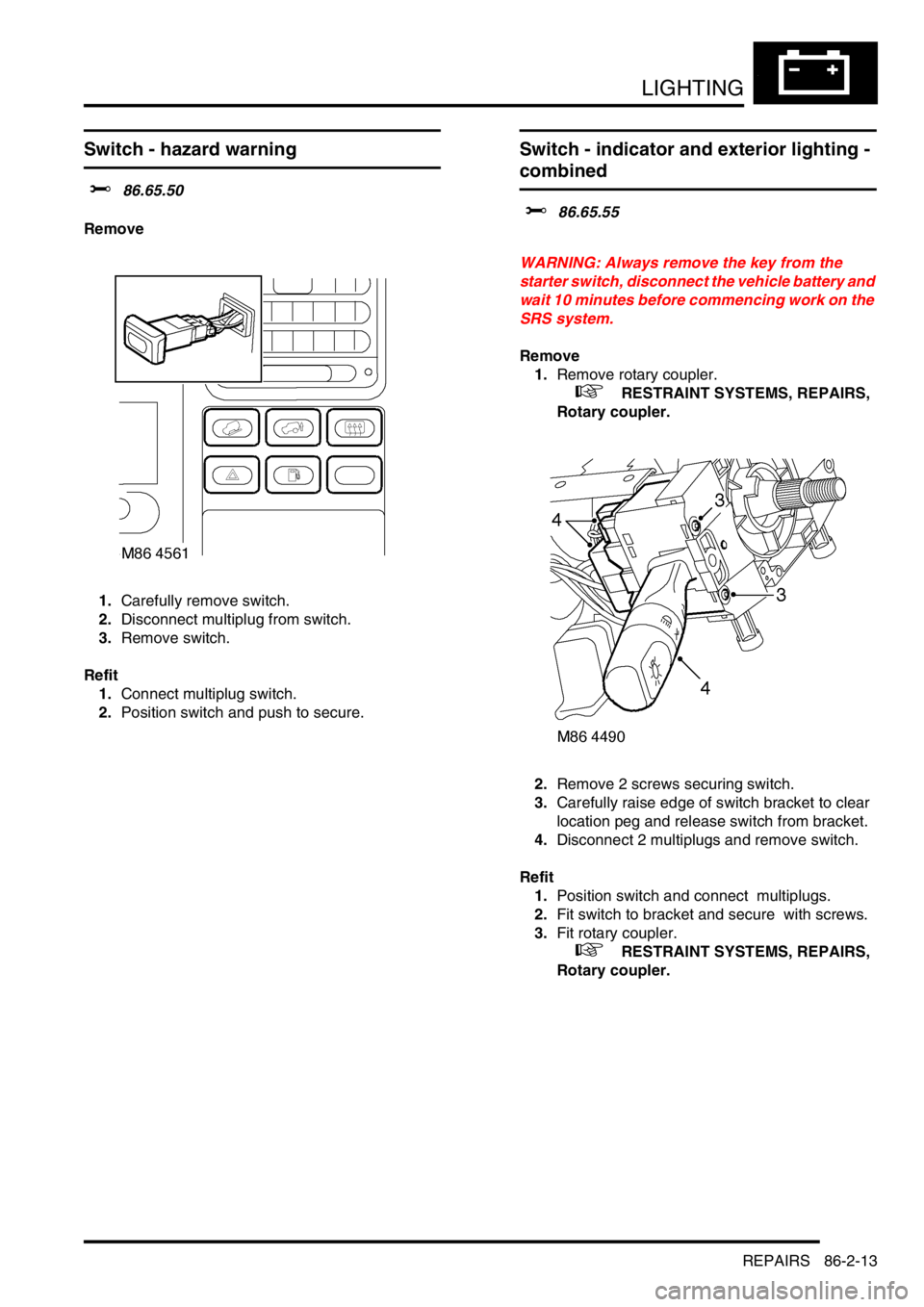
LIGHTING
REPAIRS 86-2-13
Switch - hazard warning
$% 86.65.50
Remove
1.Carefully remove switch.
2.Disconnect multiplug from switch.
3.Remove switch.
Refit
1.Connect multiplug switch.
2.Position switch and push to secure.
Switch - indicator and exterior lighting -
combined
$% 86.65.55
WARNING: Always remove the key from the
starter switch, disconnect the vehicle battery and
wait 10 minutes before commencing work on the
SRS system.
Remove
1.Remove rotary coupler.
+ RESTRAINT SYSTEMS, REPAIRS,
Rotary coupler.
2.Remove 2 screws securing switch.
3.Carefully raise edge of switch bracket to clear
location peg and release switch from bracket.
4.Disconnect 2 multiplugs and remove switch.
Refit
1.Position switch and connect multiplugs.
2.Fit switch to bracket and secure with screws.
3.Fit rotary coupler.
+ RESTRAINT SYSTEMS, REPAIRS,
Rotary coupler.
Page 1287 of 1529
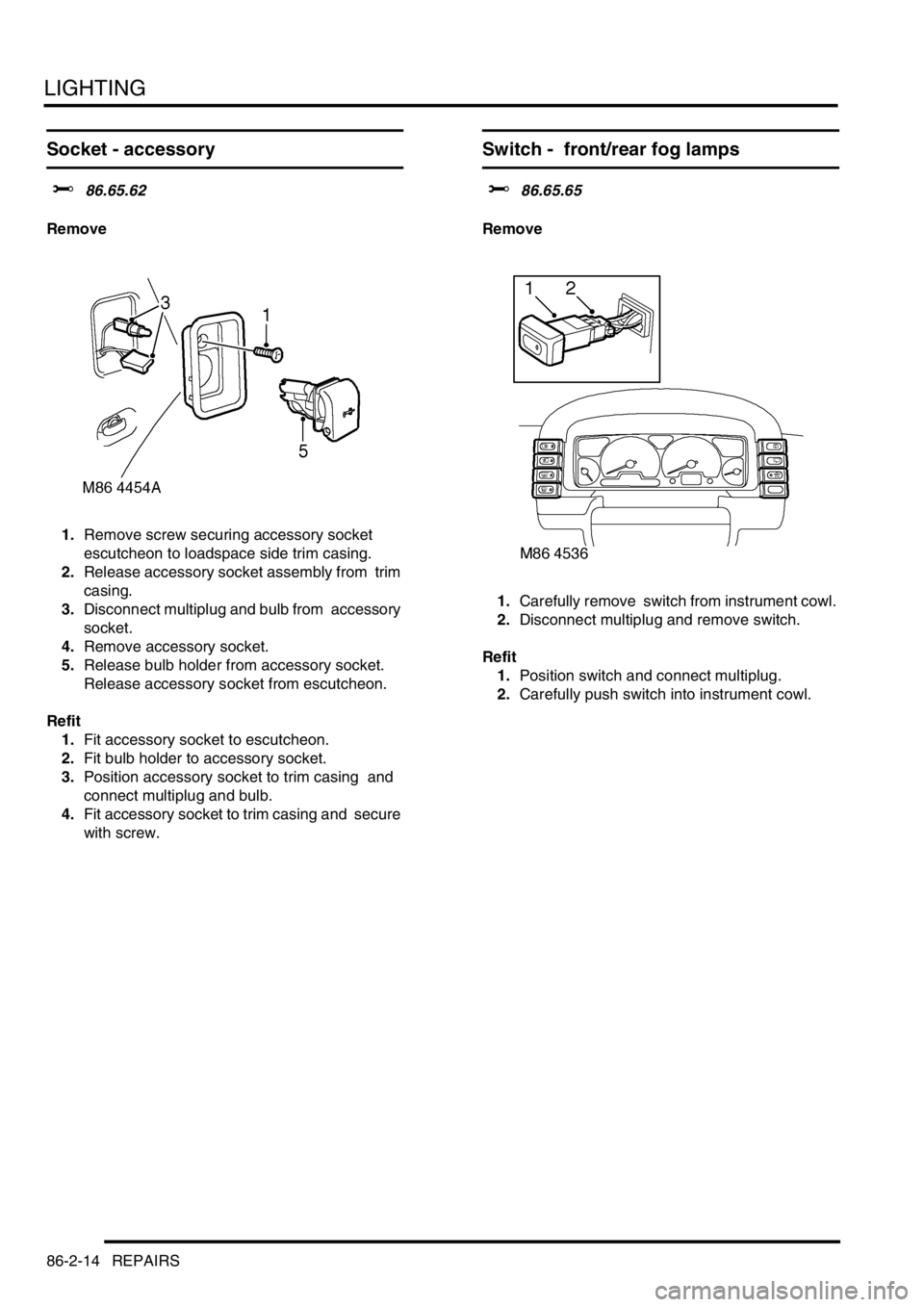
LIGHTING
86-2-14 REPAIRS
Socket - accessory
$% 86.65.62
Remove
1.Remove screw securing accessory socket
escutcheon to loadspace side trim casing.
2.Release accessory socket assembly from trim
casing.
3.Disconnect multiplug and bulb from accessory
socket.
4.Remove accessory socket.
5.Release bulb holder from accessory socket.
Release accessory socket from escutcheon.
Refit
1.Fit accessory socket to escutcheon.
2.Fit bulb holder to accessory socket.
3.Position accessory socket to trim casing and
connect multiplug and bulb.
4.Fit accessory socket to trim casing and secure
with screw.
Switch - front/rear fog lamps
$% 86.65.65
Remove
1.Carefully remove switch from instrument cowl.
2.Disconnect multiplug and remove switch.
Refit
1.Position switch and connect multiplug.
2.Carefully push switch into instrument cowl.
Page 1288 of 1529

BODY CONTROL UNIT
DESCRIPTION AND OPERATION 86-3-1
BODY CONTROL UNIT DESCRIPTION AND OPERAT ION
Description
General
The Body Control Unit (BCU) is located behind the passenger glovebox and is connected to the main harness by four
connectors on its bottom edge and an additional connector located on the side of the BCU casing. Mounting the BCU
behind the fascia makes it reasonably inaccessible for intruders to disable the anti-theft system.
The BCU uses solid-state microprocessor control to perform logical operations and timing functions for a variety of
the vehicle's electrically operated systems, these include:
lDoor locking.
lAnti-theft alarm and immobilisation system.
lExterior lighting including direction indicators and hazard warning lamps.
lCourtesy lighting.
lWipers and washers.
lElectric windows and sunroof.
lHeated windows.
The BCU also communicates with several other electronically controlled systems such as the EAT ECU and SLABS
ECU and also has a datalink between the Intelligent Driver Module (IDM) and the instrument pack. The datalink is a
low speed bus capable of transmitting and receiving messages at a data rate of 10,400 bits per second. Additional
inputs and outputs to peripheral devices are included which are necessary for determining vehicle status for particular
logical operations e.g. crank, ignition key inserted, fuel flap enable etc.
The BCU receives its power supply from the engine compartment fuse box, and is protected by a 10 A fuse.
The BCU communicates with the IDM to provide the control signals to perform power switching operations in
conjunction with dedicated relays.
IDM
The IDM is integrated into the passenger compartment fuse box, which is mounted behind the fascia below the
steering column. There are no harnesses between the fuse box and the IDM. The IDM performs the power switching
operations for several of the vehicle's electrical systems.
The IDM communicates with the BCU and the instrument pack via a serial interface. If the BCU or the IDM is replaced,
the communications link between the two units has to be re-established. This can be done either by switching on the
ignition and leaving it on for five minutes, or by using TestBook. The vehicle immobilisation will remain active until the
communications link between the BCU and IDM has been re-established.
Transit mode
To prevent excessive battery drain during transit to overseas markets, the vehicle is placed in a transit mode. The
following functions are disabled when the vehicle is in transit mode:
lVolumetric sensors.
lPassive immobilisation.
lImmobilisation of the vehicle by use of door lock.
lIgnition key interlock.
lElectric seat enable time-out with driver's door open.
Page 1289 of 1529
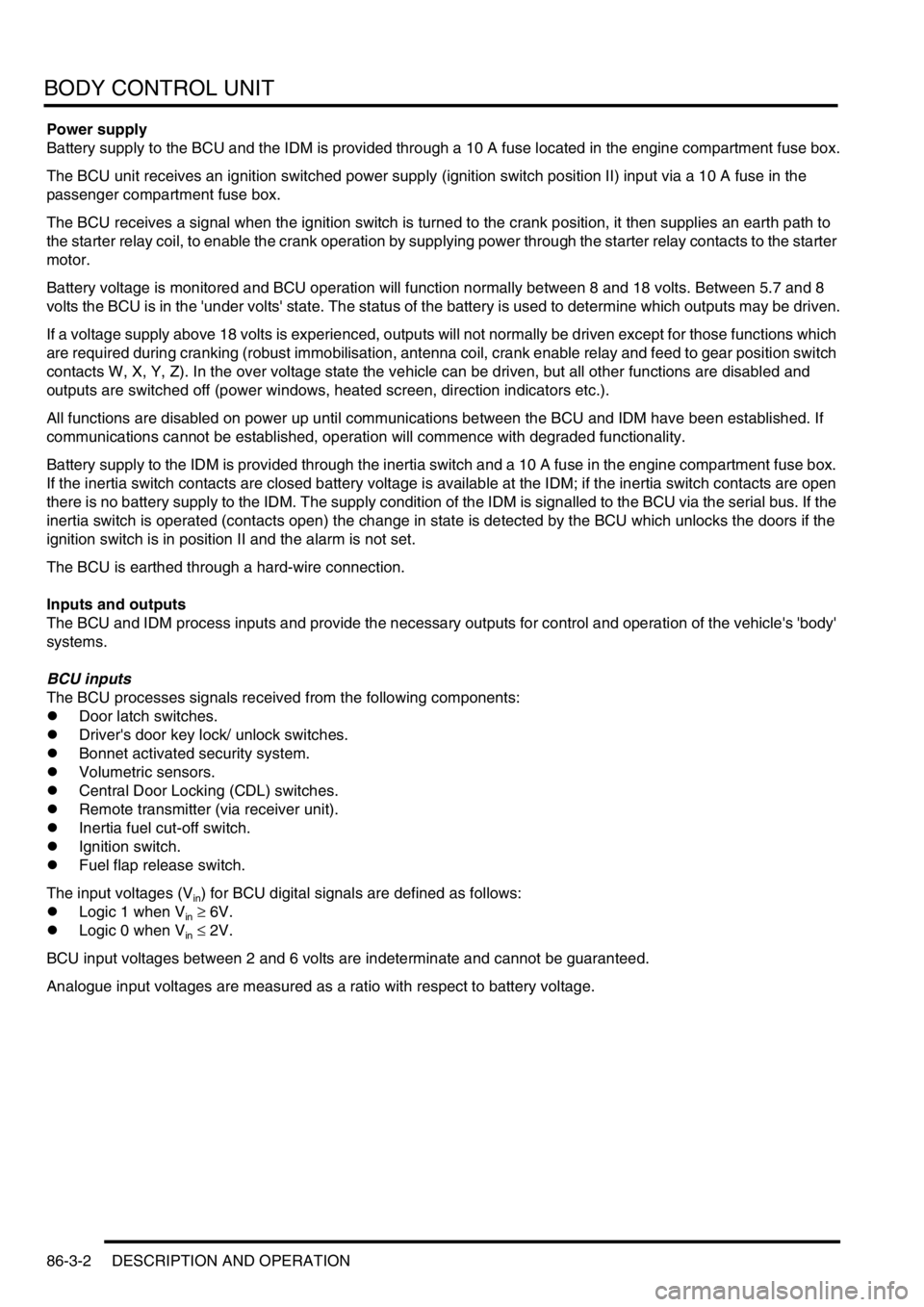
BODY CONTROL UNIT
86-3-2 DESCRIPTION AND OPERATION
Power supply
Battery supply to the BCU and the IDM is provided through a 10 A fuse located in the engine compartment fuse box.
The BCU unit receives an ignition switched power supply (ignition switch position II) input via a 10 A fuse in the
passenger compartment fuse box.
The BCU receives a signal when the ignition switch is turned to the crank position, it then supplies an earth path to
the starter relay coil, to enable the crank operation by supplying power through the starter relay contacts to the starter
motor.
Battery voltage is monitored and BCU operation will function normally between 8 and 18 volts. Between 5.7 and 8
volts the BCU is in the 'under volts' state. The status of the battery is used to determine which outputs may be driven.
If a voltage supply above 18 volts is experienced, outputs will not normally be driven except for those functions which
are required during cranking (robust immobilisation, antenna coil, crank enable relay and feed to gear position switch
contacts W, X, Y, Z). In the over voltage state the vehicle can be driven, but all other functions are disabled and
outputs are switched off (power windows, heated screen, direction indicators etc.).
All functions are disabled on power up until communications between the BCU and IDM have been established. If
communications cannot be established, operation will commence with degraded functionality.
Battery supply to the IDM is provided through the inertia switch and a 10 A fuse in the engine compartment fuse box.
If the inertia switch contacts are closed battery voltage is available at the IDM; if the inertia switch contacts are open
there is no battery supply to the IDM. The supply condition of the IDM is signalled to the BCU via the serial bus. If the
inertia switch is operated (contacts open) the change in state is detected by the BCU which unlocks the doors if the
ignition switch is in position II and the alarm is not set.
The BCU is earthed through a hard-wire connection.
Inputs and outputs
The BCU and IDM process inputs and provide the necessary outputs for control and operation of the vehicle's 'body'
systems.
BCU inputs
The BCU processes signals received from the following components:
lDoor latch switches.
lDriver's door key lock/ unlock switches.
lBonnet activated security system.
lVolumetric sensors.
lCentral Door Locking (CDL) switches.
lRemote transmitter (via receiver unit).
lInertia fuel cut-off switch.
lIgnition switch.
lFuel flap release switch.
The input voltages (V
in) for BCU digital signals are defined as follows:
lLogic 1 when V
in ≥ 6V.
lLogic 0 when V
in ≤ 2V.
BCU input voltages between 2 and 6 volts are indeterminate and cannot be guaranteed.
Analogue input voltages are measured as a ratio with respect to battery voltage.
Page 1290 of 1529
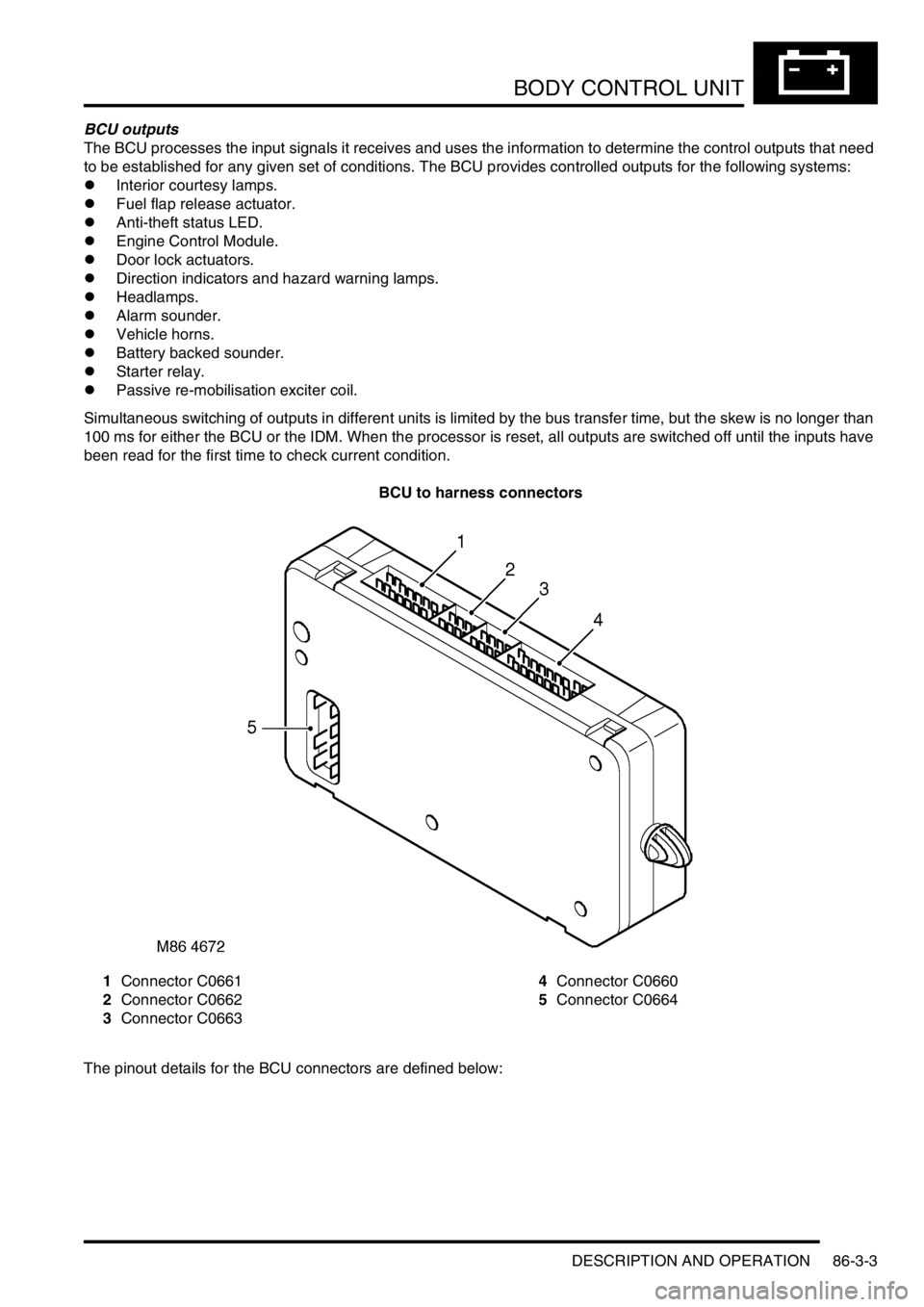
BODY CONTROL UNIT
DESCRIPTION AND OPERATION 86-3-3
BCU outputs
The BCU processes the input signals it receives and uses the information to determine the control outputs that need
to be established for any given set of conditions. The BCU provides controlled outputs for the following systems:
lInterior courtesy lamps.
lFuel flap release actuator.
lAnti-theft status LED.
lEngine Control Module.
lDoor lock actuators.
lDirection indicators and hazard warning lamps.
lHeadlamps.
lAlarm sounder.
lVehicle horns.
lBattery backed sounder.
lStarter relay.
lPassive re-mobilisation exciter coil.
Simultaneous switching of outputs in different units is limited by the bus transfer time, but the skew is no longer than
100 ms for either the BCU or the IDM. When the processor is reset, all outputs are switched off until the inputs have
been read for the first time to check current condition.
BCU to harness connectors
1Connector C0661
2Connector C0662
3Connector C06634Connector C0660
5Connector C0664
The pinout details for the BCU connectors are defined below: