engine LAND ROVER DISCOVERY 1999 Workshop Manual
[x] Cancel search | Manufacturer: LAND ROVER, Model Year: 1999, Model line: DISCOVERY, Model: LAND ROVER DISCOVERY 1999Pages: 1529, PDF Size: 34.8 MB
Page 345 of 1529
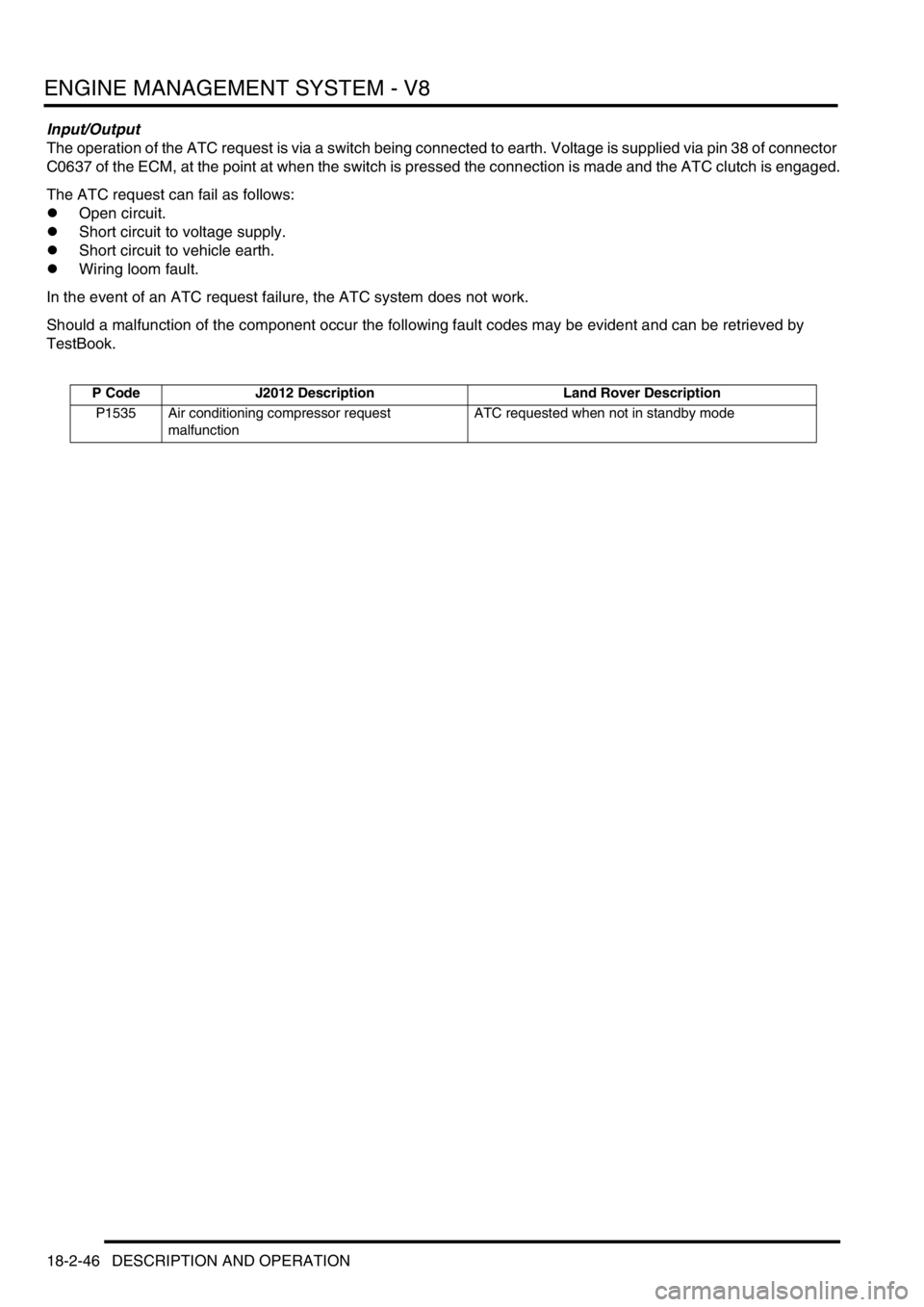
ENGINE MANAGEMENT SYSTEM - V8
18-2-46 DESCRIPTION AND OPERATION
Input/Output
The operation of the ATC request is via a switch being connected to earth. Voltage is supplied via pin 38 of connector
C0637 of the ECM, at the point at when the switch is pressed the connection is made and the ATC clutch is engaged.
The ATC request can fail as follows:
lOpen circuit.
lShort circuit to voltage supply.
lShort circuit to vehicle earth.
lWiring loom fault.
In the event of an ATC request failure, the ATC system does not work.
Should a malfunction of the component occur the following fault codes may be evident and can be retrieved by
TestBook.
P Code J2012 Description Land Rover Description
P1535 Air conditioning compressor request
malfunctionATC requested when not in standby mode
Page 346 of 1529
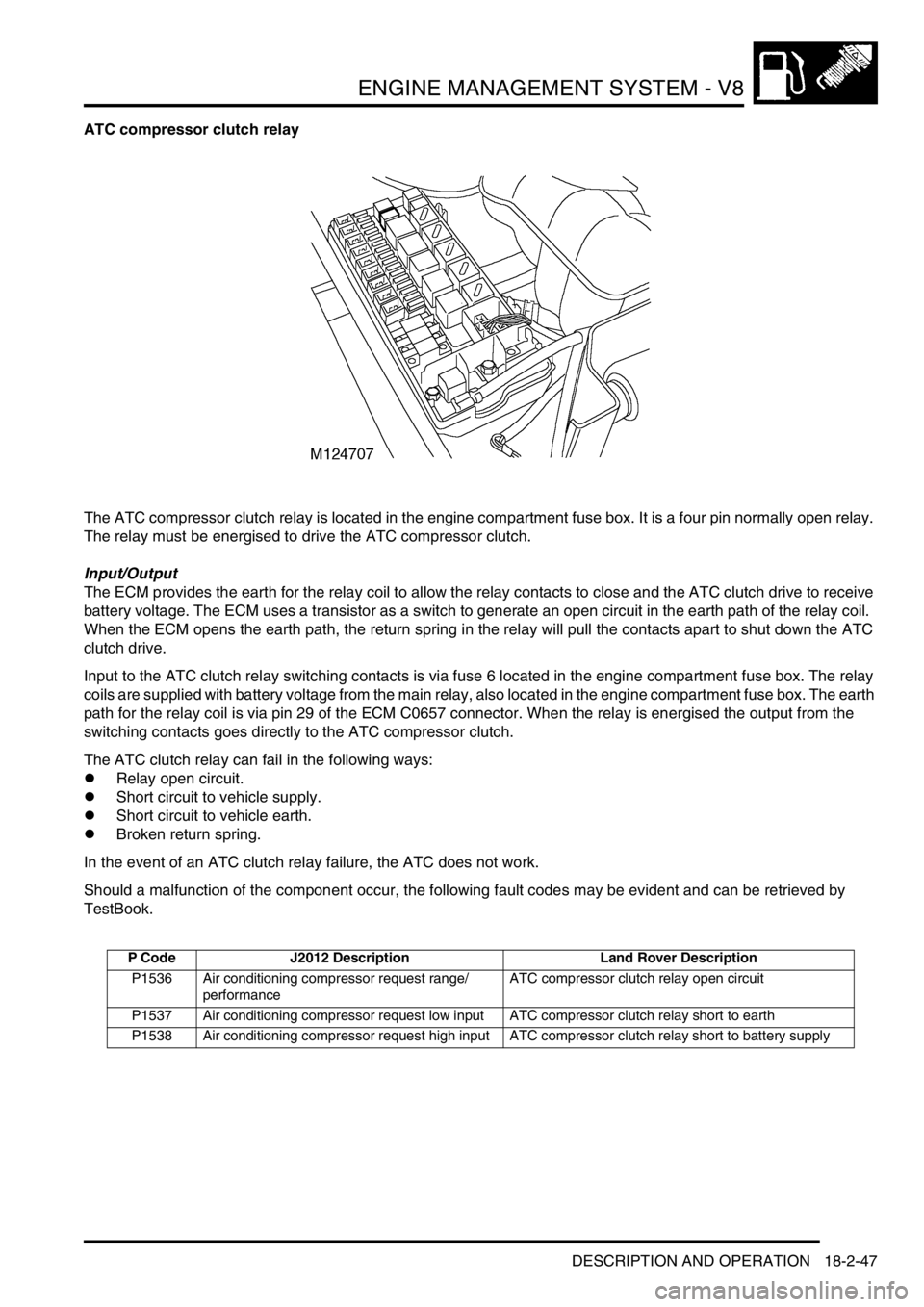
ENGINE MANAGEMENT SYSTEM - V8
DESCRIPTION AND OPERATION 18-2-47
ATC compressor clutch relay
The ATC compressor clutch relay is located in the engine compartment fuse box. It is a four pin normally open relay.
The relay must be energised to drive the ATC compressor clutch.
Input/Output
The ECM provides the earth for the relay coil to allow the relay contacts to close and the ATC clutch drive to receive
battery voltage. The ECM uses a transistor as a switch to generate an open circuit in the earth path of the relay coil.
When the ECM opens the earth path, the return spring in the relay will pull the contacts apart to shut down the ATC
clutch drive.
Input to the ATC clutch relay switching contacts is via fuse 6 located in the engine compartment fuse box. The relay
coils are supplied with battery voltage from the main relay, also located in the engine compartment fuse box. The earth
path for the relay coil is via pin 29 of the ECM C0657 connector. When the relay is energised the output from the
switching contacts goes directly to the ATC compressor clutch.
The ATC clutch relay can fail in the following ways:
lRelay open circuit.
lShort circuit to vehicle supply.
lShort circuit to vehicle earth.
lBroken return spring.
In the event of an ATC clutch relay failure, the ATC does not work.
Should a malfunction of the component occur, the following fault codes may be evident and can be retrieved by
TestBook.
P Code J2012 Description Land Rover Description
P1536 Air conditioning compressor request range/
performanceATC compressor clutch relay open circuit
P1537 Air conditioning compressor request low input ATC compressor clutch relay short to earth
P1538 Air conditioning compressor request high input ATC compressor clutch relay short to battery supply
Page 347 of 1529
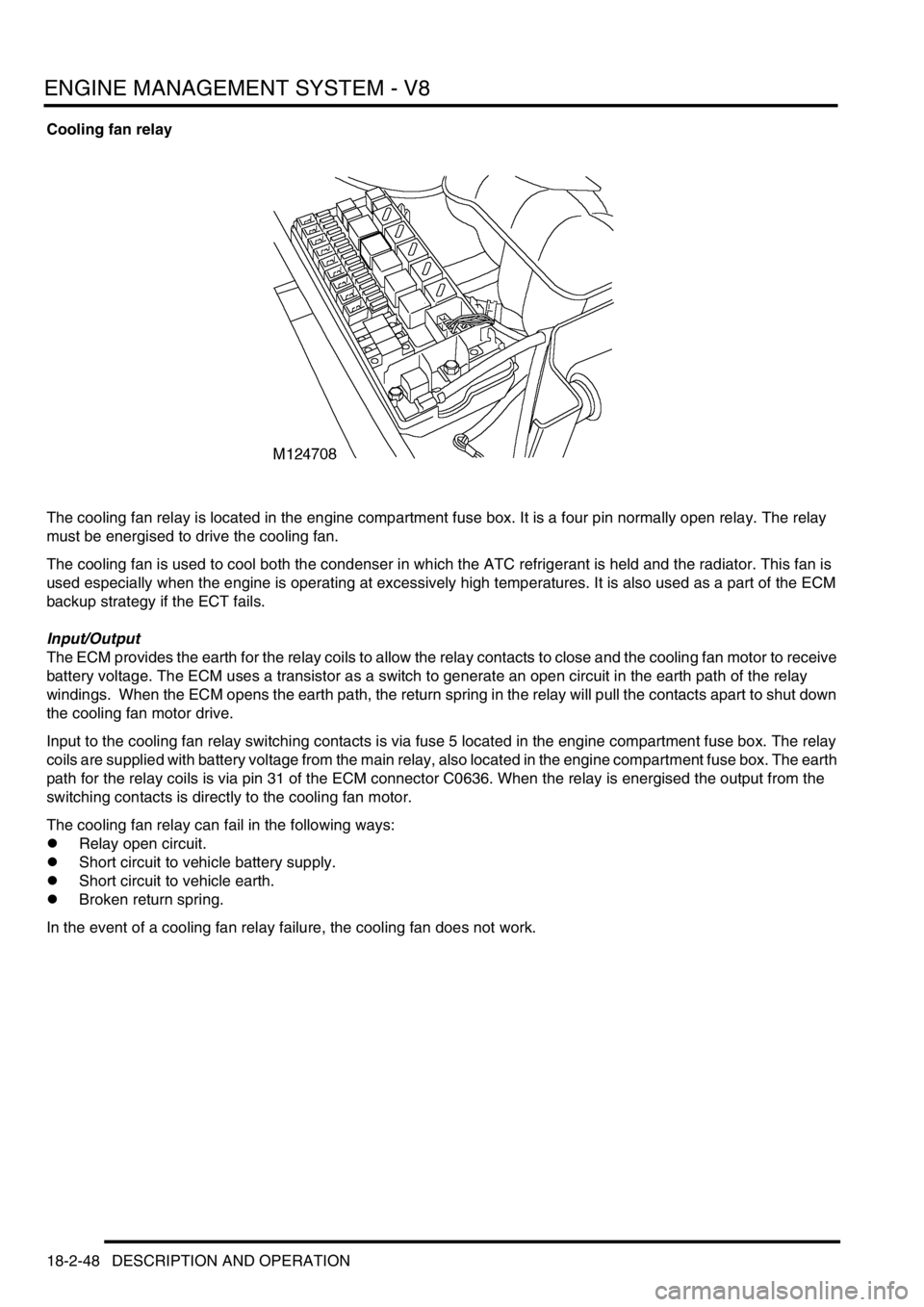
ENGINE MANAGEMENT SYSTEM - V8
18-2-48 DESCRIPTION AND OPERATION
Cooling fan relay
The cooling fan relay is located in the engine compartment fuse box. It is a four pin normally open relay. The relay
must be energised to drive the cooling fan.
The cooling fan is used to cool both the condenser in which the ATC refrigerant is held and the radiator. This fan is
used especially when the engine is operating at excessively high temperatures. It is also used as a part of the ECM
backup strategy if the ECT fails.
Input/Output
The ECM provides the earth for the relay coils to allow the relay contacts to close and the cooling fan motor to receive
battery voltage. The ECM uses a transistor as a switch to generate an open circuit in the earth path of the relay
windings. When the ECM opens the earth path, the return spring in the relay will pull the contacts apart to shut down
the cooling fan motor drive.
Input to the cooling fan relay switching contacts is via fuse 5 located in the engine compartment fuse box. The relay
coils are supplied with battery voltage from the main relay, also located in the engine compartment fuse box. The earth
path for the relay coils is via pin 31 of the ECM connector C0636. When the relay is energised the output from the
switching contacts is directly to the cooling fan motor.
The cooling fan relay can fail in the following ways:
lRelay open circuit.
lShort circuit to vehicle battery supply.
lShort circuit to vehicle earth.
lBroken return spring.
In the event of a cooling fan relay failure, the cooling fan does not work.
Page 348 of 1529
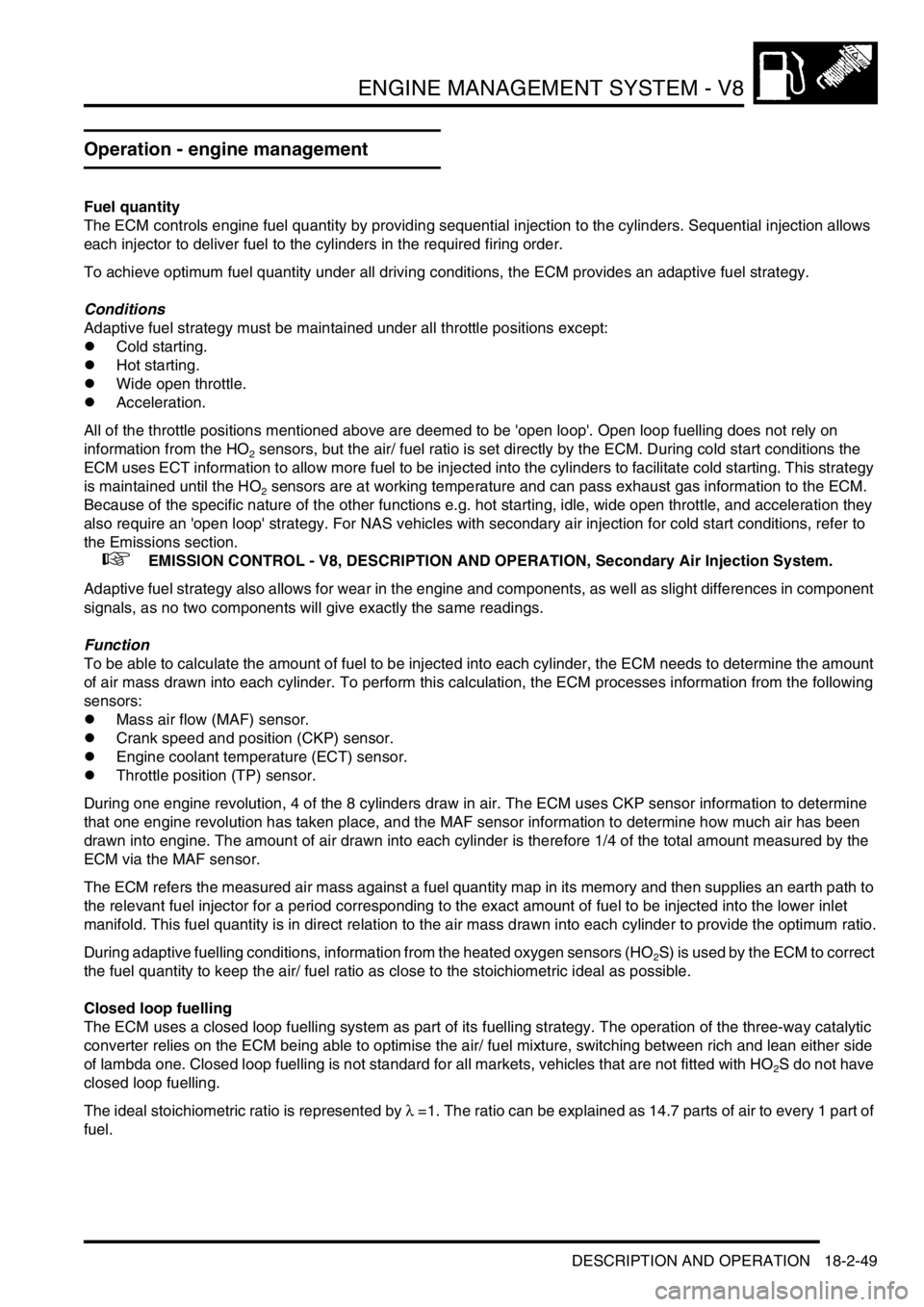
ENGINE MANAGEMENT SYSTEM - V8
DESCRIPTION AND OPERATION 18-2-49
Operation - engine management
Fuel quantity
The ECM controls engine fuel quantity by providing sequential injection to the cylinders. Sequential injection allows
each injector to deliver fuel to the cylinders in the required firing order.
To achieve optimum fuel quantity under all driving conditions, the ECM provides an adaptive fuel strategy.
Conditions
Adaptive fuel strategy must be maintained under all throttle positions except:
lCold starting.
lHot starting.
lWide open throttle.
lAcceleration.
All of the throttle positions mentioned above are deemed to be 'open loop'. Open loop fuelling does not rely on
information from the HO
2 sensors, but the air/ fuel ratio is set directly by the ECM. During cold start conditions the
ECM uses ECT information to allow more fuel to be injected into the cylinders to facilitate cold starting. This strategy
is maintained until the HO
2 sensors are at working temperature and can pass exhaust gas information to the ECM.
Because of the specific nature of the other functions e.g. hot starting, idle, wide open throttle, and acceleration they
also require an 'open loop' strategy. For NAS vehicles with secondary air injection for cold start conditions, refer to
the Emissions section.
+ EMISSION CONTROL - V8, DESCRIPTION AND OPERATION, Secondary Air Injection System.
Adaptive fuel strategy also allows for wear in the engine and components, as well as slight differences in component
signals, as no two components will give exactly the same readings.
Function
To be able to calculate the amount of fuel to be injected into each cylinder, the ECM needs to determine the amount
of air mass drawn into each cylinder. To perform this calculation, the ECM processes information from the following
sensors:
lMass air flow (MAF) sensor.
lCrank speed and position (CKP) sensor.
lEngine coolant temperature (ECT) sensor.
lThrottle position (TP) sensor.
During one engine revolution, 4 of the 8 cylinders draw in air. The ECM uses CKP sensor information to determine
that one engine revolution has taken place, and the MAF sensor information to determine how much air has been
drawn into engine. The amount of air drawn into each cylinder is therefore 1/4 of the total amount measured by the
ECM via the MAF sensor.
The ECM refers the measured air mass against a fuel quantity map in its memory and then supplies an earth path to
the relevant fuel injector for a period corresponding to the exact amount of fuel to be injected into the lower inlet
manifold. This fuel quantity is in direct relation to the air mass drawn into each cylinder to provide the optimum ratio.
During adaptive fuelling conditions, information from the heated oxygen sensors (HO
2S) is used by the ECM to correct
the fuel quantity to keep the air/ fuel ratio as close to the stoichiometric ideal as possible.
Closed loop fuelling
The ECM uses a closed loop fuelling system as part of its fuelling strategy. The operation of the three-way catalytic
converter relies on the ECM being able to optimise the air/ fuel mixture, switching between rich and lean either side
of lambda one. Closed loop fuelling is not standard for all markets, vehicles that are not fitted with HO
2S do not have
closed loop fuelling.
The ideal stoichiometric ratio is represented by λ =1. The ratio can be explained as 14.7 parts of air to every 1 part of
fuel.
Page 349 of 1529
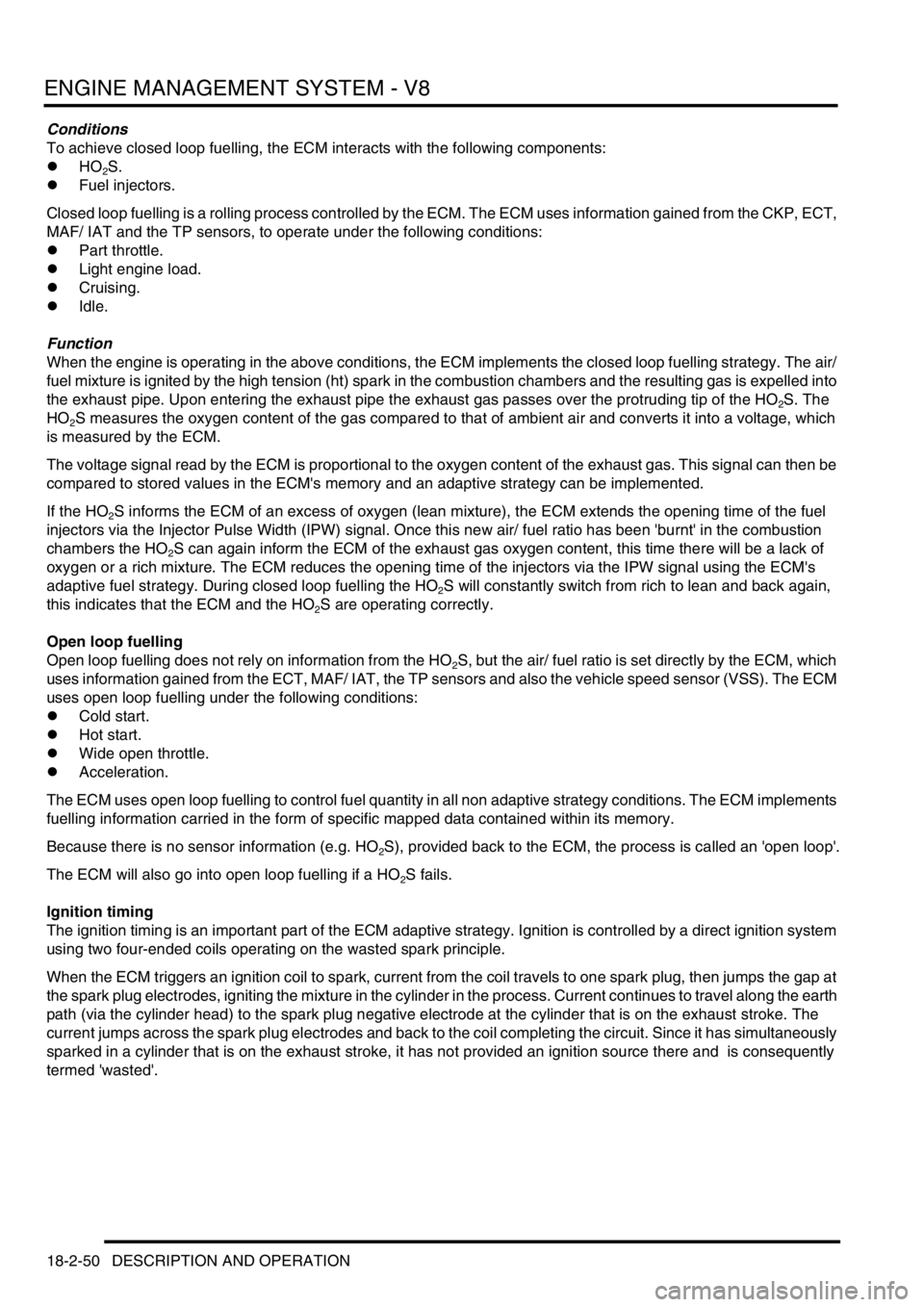
ENGINE MANAGEMENT SYSTEM - V8
18-2-50 DESCRIPTION AND OPERATION
Conditions
To achieve closed loop fuelling, the ECM interacts with the following components:
lHO
2S.
lFuel injectors.
Closed loop fuelling is a rolling process controlled by the ECM. The ECM uses information gained from the CKP, ECT,
MAF/ IAT and the TP sensors, to operate under the following conditions:
lPart throttle.
lLight engine load.
lCruising.
lIdle.
Function
When the engine is operating in the above conditions, the ECM implements the closed loop fuelling strategy. The air/
fuel mixture is ignited by the high tension (ht) spark in the combustion chambers and the resulting gas is expelled into
the exhaust pipe. Upon entering the exhaust pipe the exhaust gas passes over the protruding tip of the HO
2S. The
HO
2S measures the oxygen content of the gas compared to that of ambient air and converts it into a voltage, which
is measured by the ECM.
The voltage signal read by the ECM is proportional to the oxygen content of the exhaust gas. This signal can then be
compared to stored values in the ECM's memory and an adaptive strategy can be implemented.
If the HO
2S informs the ECM of an excess of oxygen (lean mixture), the ECM extends the opening time of the fuel
injectors via the Injector Pulse Width (IPW) signal. Once this new air/ fuel ratio has been 'burnt' in the combustion
chambers the HO
2S can again inform the ECM of the exhaust gas oxygen content, this time there will be a lack of
oxygen or a rich mixture. The ECM reduces the opening time of the injectors via the IPW signal using the ECM's
adaptive fuel strategy. During closed loop fuelling the HO
2S will constantly switch from rich to lean and back again,
this indicates that the ECM and the HO
2S are operating correctly.
Open loop fuelling
Open loop fuelling does not rely on information from the HO
2S, but the air/ fuel ratio is set directly by the ECM, which
uses information gained from the ECT, MAF/ IAT, the TP sensors and also the vehicle speed sensor (VSS). The ECM
uses open loop fuelling under the following conditions:
lCold start.
lHot start.
lWide open throttle.
lAcceleration.
The ECM uses open loop fuelling to control fuel quantity in all non adaptive strategy conditions. The ECM implements
fuelling information carried in the form of specific mapped data contained within its memory.
Because there is no sensor information (e.g. HO
2S), provided back to the ECM, the process is called an 'open loop'.
The ECM will also go into open loop fuelling if a HO
2S fails.
Ignition timing
The ignition timing is an important part of the ECM adaptive strategy. Ignition is controlled by a direct ignition system
using two four-ended coils operating on the wasted spark principle.
When the ECM triggers an ignition coil to spark, current from the coil travels to one spark plug, then jumps the gap at
the spark plug electrodes, igniting the mixture in the cylinder in the process. Current continues to travel along the earth
path (via the cylinder head) to the spark plug negative electrode at the cylinder that is on the exhaust stroke. The
current jumps across the spark plug electrodes and back to the coil completing the circuit. Since it has simultaneously
sparked in a cylinder that is on the exhaust stroke, it has not provided an ignition source there and is consequently
termed 'wasted'.
Page 350 of 1529
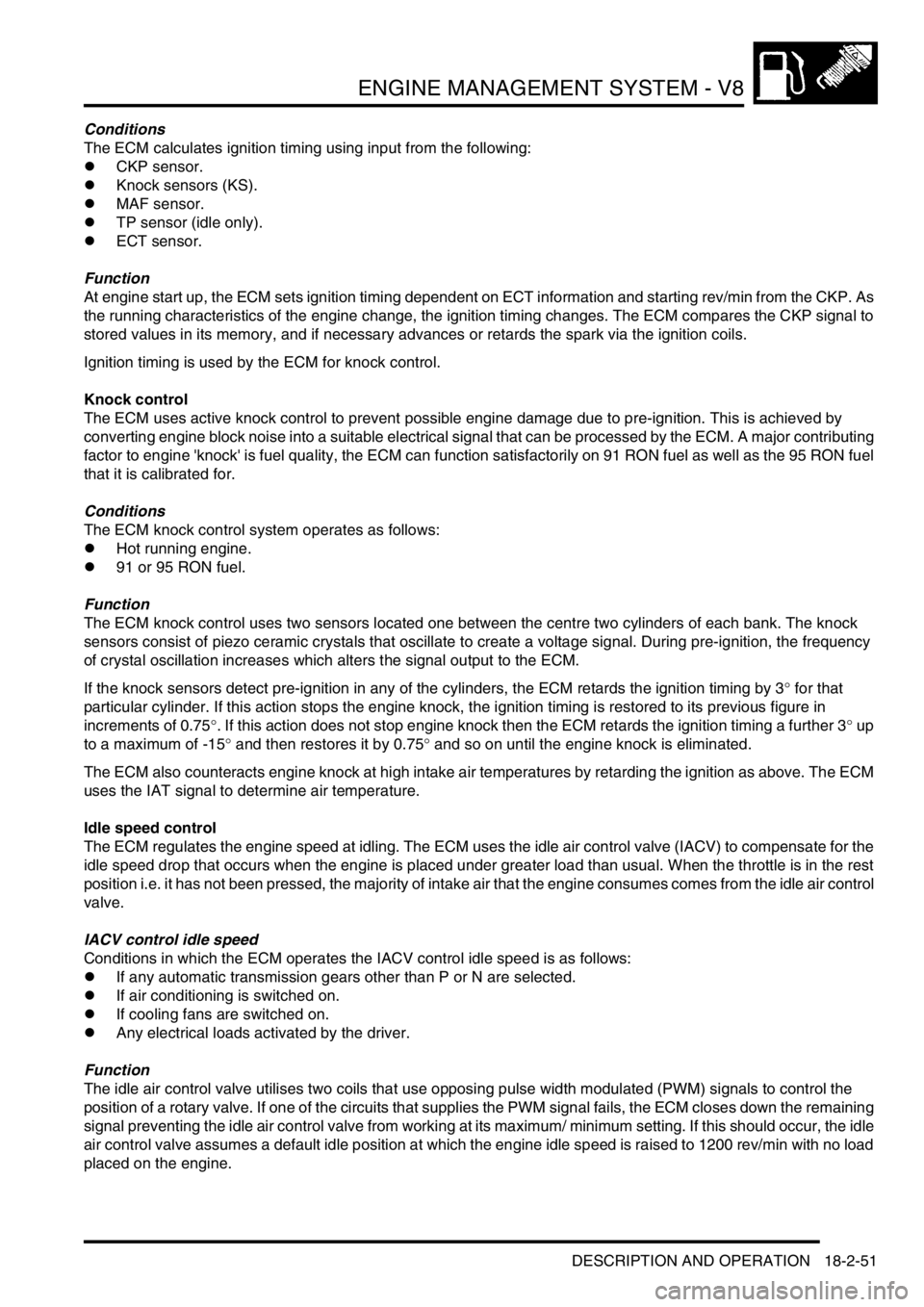
ENGINE MANAGEMENT SYSTEM - V8
DESCRIPTION AND OPERATION 18-2-51
Conditions
The ECM calculates ignition timing using input from the following:
lCKP sensor.
lKnock sensors (KS).
lMAF sensor.
lTP sensor (idle only).
lECT sensor.
Function
At engine start up, the ECM sets ignition timing dependent on ECT information and starting rev/min from the CKP. As
the running characteristics of the engine change, the ignition timing changes. The ECM compares the CKP signal to
stored values in its memory, and if necessary advances or retards the spark via the ignition coils.
Ignition timing is used by the ECM for knock control.
Knock control
The ECM uses active knock control to prevent possible engine damage due to pre-ignition. This is achieved by
converting engine block noise into a suitable electrical signal that can be processed by the ECM. A major contributing
factor to engine 'knock' is fuel quality, the ECM can function satisfactorily on 91 RON fuel as well as the 95 RON fuel
that it is calibrated for.
Conditions
The ECM knock control system operates as follows:
lHot running engine.
l91 or 95 RON fuel.
Function
The ECM knock control uses two sensors located one between the centre two cylinders of each bank. The knock
sensors consist of piezo ceramic crystals that oscillate to create a voltage signal. During pre-ignition, the frequency
of crystal oscillation increases which alters the signal output to the ECM.
If the knock sensors detect pre-ignition in any of the cylinders, the ECM retards the ignition timing by 3° for that
particular cylinder. If this action stops the engine knock, the ignition timing is restored to its previous figure in
increments of 0.75°. If this action does not stop engine knock then the ECM retards the ignition timing a further 3° up
to a maximum of -15° and then restores it by 0.75° and so on until the engine knock is eliminated.
The ECM also counteracts engine knock at high intake air temperatures by retarding the ignition as above. The ECM
uses the IAT signal to determine air temperature.
Idle speed control
The ECM regulates the engine speed at idling. The ECM uses the idle air control valve (IACV) to compensate for the
idle speed drop that occurs when the engine is placed under greater load than usual. When the throttle is in the rest
position i.e. it has not been pressed, the majority of intake air that the engine consumes comes from the idle air control
valve.
IACV control idle speed
Conditions in which the ECM operates the IACV control idle speed is as follows:
lIf any automatic transmission gears other than P or N are selected.
lIf air conditioning is switched on.
lIf cooling fans are switched on.
lAny electrical loads activated by the driver.
Function
The idle air control valve utilises two coils that use opposing pulse width modulated (PWM) signals to control the
position of a rotary valve. If one of the circuits that supplies the PWM signal fails, the ECM closes down the remaining
signal preventing the idle air control valve from working at its maximum/ minimum setting. If this should occur, the idle
air control valve assumes a default idle position at which the engine idle speed is raised to 1200 rev/min with no load
placed on the engine.
Page 351 of 1529
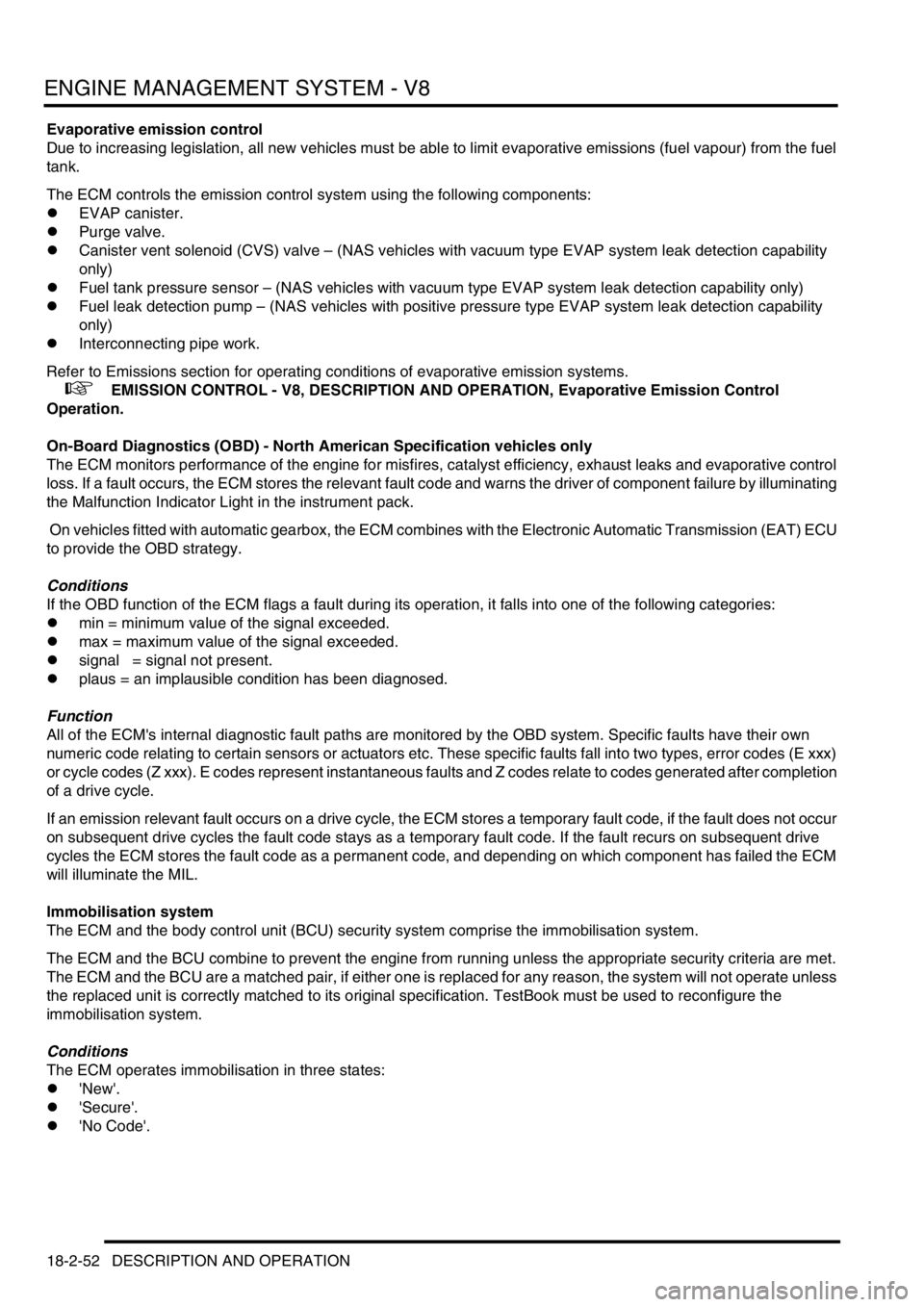
ENGINE MANAGEMENT SYSTEM - V8
18-2-52 DESCRIPTION AND OPERATION
Evaporative emission control
Due to increasing legislation, all new vehicles must be able to limit evaporative emissions (fuel vapour) from the fuel
tank.
The ECM controls the emission control system using the following components:
lEVAP canister.
lPurge valve.
lCanister vent solenoid (CVS) valve – (NAS vehicles with vacuum type EVAP system leak detection capability
only)
lFuel tank pressure sensor – (NAS vehicles with vacuum type EVAP system leak detection capability only)
lFuel leak detection pump – (NAS vehicles with positive pressure type EVAP system leak detection capability
only)
lInterconnecting pipe work.
Refer to Emissions section for operating conditions of evaporative emission systems.
+ EMISSION CONTROL - V8, DESCRIPTION AND OPERATION, Evaporative Emission Control
Operation.
On-Board Diagnostics (OBD) - North American Specification vehicles only
The ECM monitors performance of the engine for misfires, catalyst efficiency, exhaust leaks and evaporative control
loss. If a fault occurs, the ECM stores the relevant fault code and warns the driver of component failure by illuminating
the Malfunction Indicator Light in the instrument pack.
On vehicles fitted with automatic gearbox, the ECM combines with the Electronic Automatic Transmission (EAT) ECU
to provide the OBD strategy.
Conditions
If the OBD function of the ECM flags a fault during its operation, it falls into one of the following categories:
lmin = minimum value of the signal exceeded.
lmax = maximum value of the signal exceeded.
lsignal = signal not present.
lplaus = an implausible condition has been diagnosed.
Function
All of the ECM's internal diagnostic fault paths are monitored by the OBD system. Specific faults have their own
numeric code relating to certain sensors or actuators etc. These specific faults fall into two types, error codes (E xxx)
or cycle codes (Z xxx). E codes represent instantaneous faults and Z codes relate to codes generated after completion
of a drive cycle.
If an emission relevant fault occurs on a drive cycle, the ECM stores a temporary fault code, if the fault does not occur
on subsequent drive cycles the fault code stays as a temporary fault code. If the fault recurs on subsequent drive
cycles the ECM stores the fault code as a permanent code, and depending on which component has failed the ECM
will illuminate the MIL.
Immobilisation system
The ECM and the body control unit (BCU) security system comprise the immobilisation system.
The ECM and the BCU combine to prevent the engine from running unless the appropriate security criteria are met.
The ECM and the BCU are a matched pair, if either one is replaced for any reason, the system will not operate unless
the replaced unit is correctly matched to its original specification. TestBook must be used to reconfigure the
immobilisation system.
Conditions
The ECM operates immobilisation in three states:
l'New'.
l'Secure'.
l'No Code'.
Page 352 of 1529
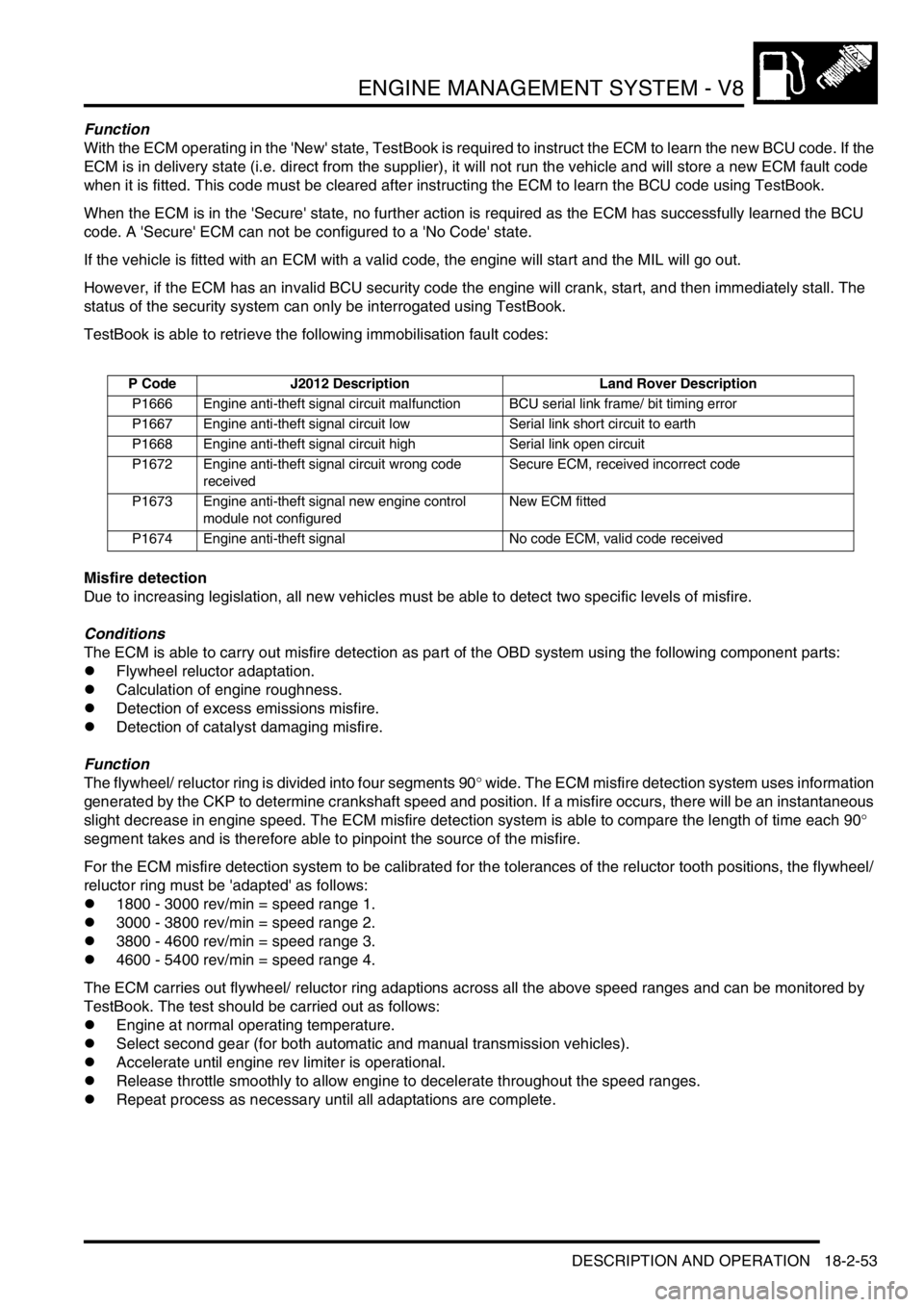
ENGINE MANAGEMENT SYSTEM - V8
DESCRIPTION AND OPERATION 18-2-53
Function
With the ECM operating in the 'New' state, TestBook is required to instruct the ECM to learn the new BCU code. If the
ECM is in delivery state (i.e. direct from the supplier), it will not run the vehicle and will store a new ECM fault code
when it is fitted. This code must be cleared after instructing the ECM to learn the BCU code using TestBook.
When the ECM is in the 'Secure' state, no further action is required as the ECM has successfully learned the BCU
code. A 'Secure' ECM can not be configured to a 'No Code' state.
If the vehicle is fitted with an ECM with a valid code, the engine will start and the MIL will go out.
However, if the ECM has an invalid BCU security code the engine will crank, start, and then immediately stall. The
status of the security system can only be interrogated using TestBook.
TestBook is able to retrieve the following immobilisation fault codes:
Misfire detection
Due to increasing legislation, all new vehicles must be able to detect two specific levels of misfire.
Conditions
The ECM is able to carry out misfire detection as part of the OBD system using the following component parts:
lFlywheel reluctor adaptation.
lCalculation of engine roughness.
lDetection of excess emissions misfire.
lDetection of catalyst damaging misfire.
Function
The flywheel/ reluctor ring is divided into four segments 90° wide. The ECM misfire detection system uses information
generated by the CKP to determine crankshaft speed and position. If a misfire occurs, there will be an instantaneous
slight decrease in engine speed. The ECM misfire detection system is able to compare the length of time each 90°
segment takes and is therefore able to pinpoint the source of the misfire.
For the ECM misfire detection system to be calibrated for the tolerances of the reluctor tooth positions, the flywheel/
reluctor ring must be 'adapted' as follows:
l1800 - 3000 rev/min = speed range 1.
l3000 - 3800 rev/min = speed range 2.
l3800 - 4600 rev/min = speed range 3.
l4600 - 5400 rev/min = speed range 4.
The ECM carries out flywheel/ reluctor ring adaptions across all the above speed ranges and can be monitored by
TestBook. The test should be carried out as follows:
lEngine at normal operating temperature.
lSelect second gear (for both automatic and manual transmission vehicles).
lAccelerate until engine rev limiter is operational.
lRelease throttle smoothly to allow engine to decelerate throughout the speed ranges.
lRepeat process as necessary until all adaptations are complete.
P Code J2012 Description Land Rover Description
P1666 Engine anti-theft signal circuit malfunction BCU serial link frame/ bit timing error
P1667 Engine anti-theft signal circuit low Serial link short circuit to earth
P1668 Engine anti-theft signal circuit high Serial link open circuit
P1672 Engine anti-theft signal circuit wrong code
receivedSecure ECM, received incorrect code
P1673 Engine anti-theft signal new engine control
module not configuredNew ECM fitted
P1674 Engine anti-theft signal No code ECM, valid code received
Page 353 of 1529
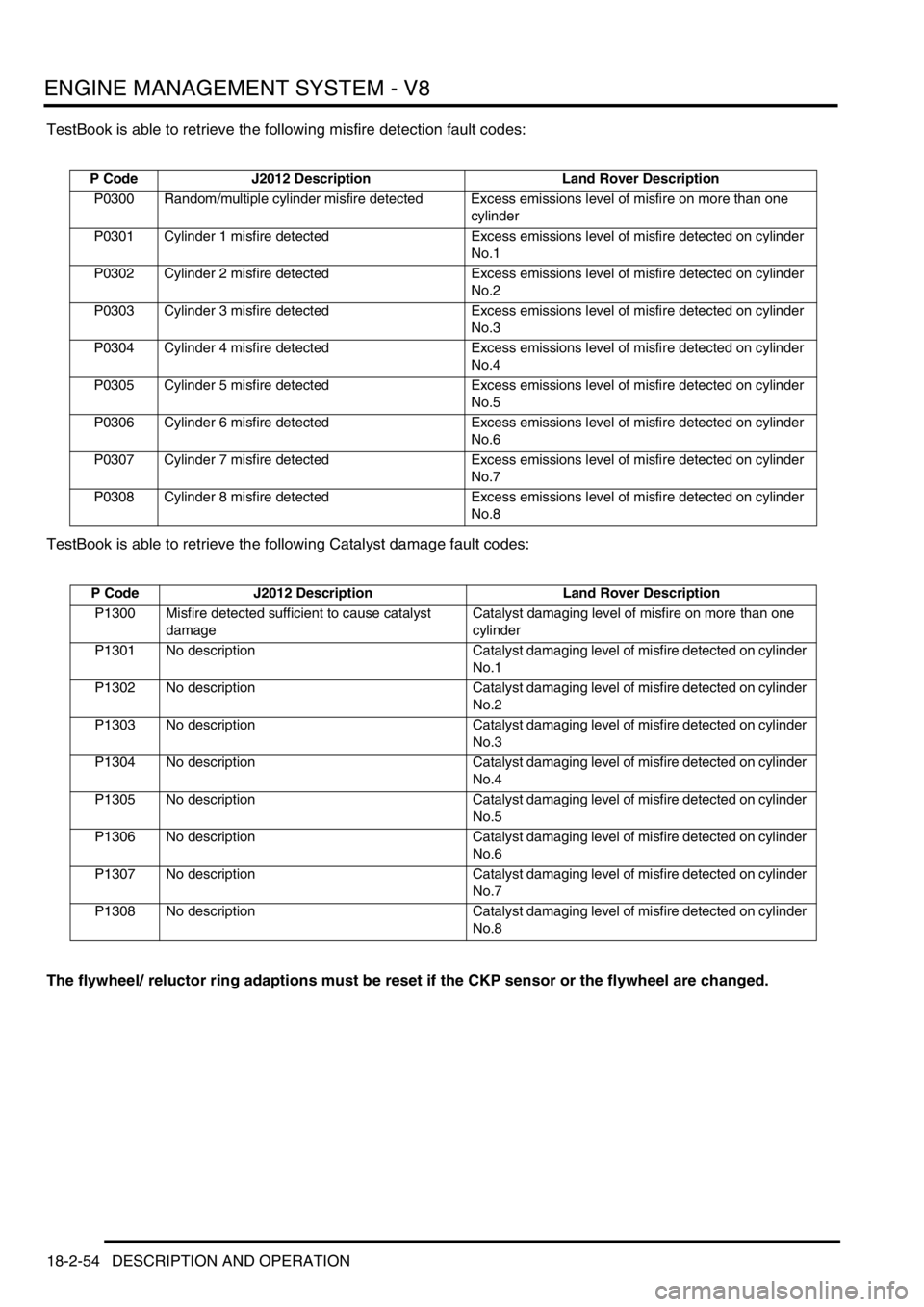
ENGINE MANAGEMENT SYSTEM - V8
18-2-54 DESCRIPTION AND OPERATION
TestBook is able to retrieve the following misfire detection fault codes:
TestBook is able to retrieve the following Catalyst damage fault codes:
The flywheel/ reluctor ring adaptions must be reset if the CKP sensor or the flywheel are changed.
P Code J2012 Description Land Rover Description
P0300 Random/multiple cylinder misfire detected Excess emissions level of misfire on more than one
cylinder
P0301 Cylinder 1 misfire detected Excess emissions level of misfire detected on cylinder
No.1
P0302 Cylinder 2 misfire detected Excess emissions level of misfire detected on cylinder
No.2
P0303 Cylinder 3 misfire detected Excess emissions level of misfire detected on cylinder
No.3
P0304 Cylinder 4 misfire detected Excess emissions level of misfire detected on cylinder
No.4
P0305 Cylinder 5 misfire detected Excess emissions level of misfire detected on cylinder
No.5
P0306 Cylinder 6 misfire detected Excess emissions level of misfire detected on cylinder
No.6
P0307 Cylinder 7 misfire detected Excess emissions level of misfire detected on cylinder
No.7
P0308 Cylinder 8 misfire detected Excess emissions level of misfire detected on cylinder
No.8
P Code J2012 Description Land Rover Description
P1300 Misfire detected sufficient to cause catalyst
damageCatalyst damaging level of misfire on more than one
cylinder
P1301 No description Catalyst damaging level of misfire detected on cylinder
No.1
P1302 No description Catalyst damaging level of misfire detected on cylinder
No.2
P1303 No description Catalyst damaging level of misfire detected on cylinder
No.3
P1304 No description Catalyst damaging level of misfire detected on cylinder
No.4
P1305 No description Catalyst damaging level of misfire detected on cylinder
No.5
P1306 No description Catalyst damaging level of misfire detected on cylinder
No.6
P1307 No description Catalyst damaging level of misfire detected on cylinder
No.7
P1308 No description Catalyst damaging level of misfire detected on cylinder
No.8
Page 354 of 1529
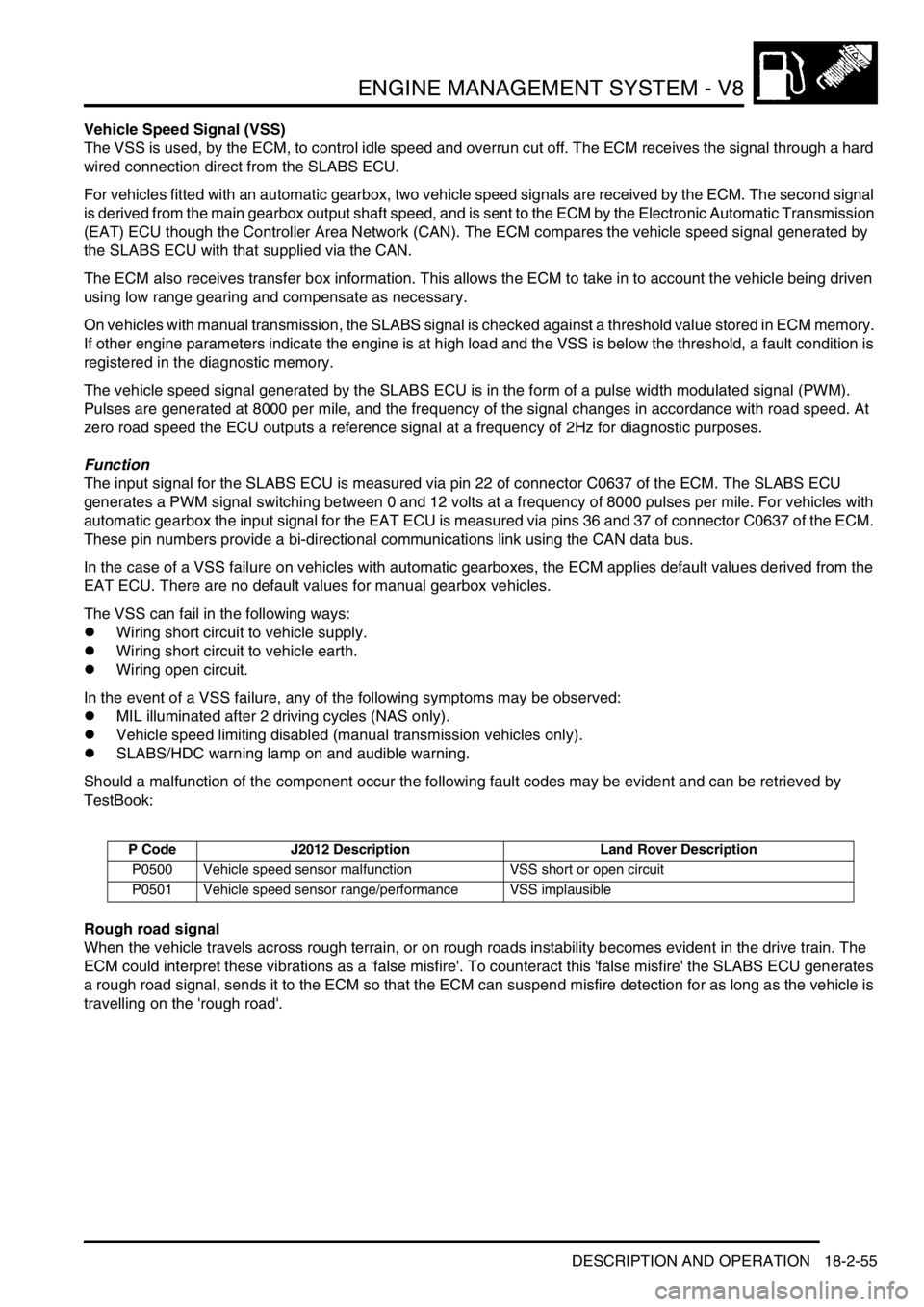
ENGINE MANAGEMENT SYSTEM - V8
DESCRIPTION AND OPERATION 18-2-55
Vehicle Speed Signal (VSS)
The VSS is used, by the ECM, to control idle speed and overrun cut off. The ECM receives the signal through a hard
wired connection direct from the SLABS ECU.
For vehicles fitted with an automatic gearbox, two vehicle speed signals are received by the ECM. The second signal
is derived from the main gearbox output shaft speed, and is sent to the ECM by the Electronic Automatic Transmission
(EAT) ECU though the Controller Area Network (CAN). The ECM compares the vehicle speed signal generated by
the SLABS ECU with that supplied via the CAN.
The ECM also receives transfer box information. This allows the ECM to take in to account the vehicle being driven
using low range gearing and compensate as necessary.
On vehicles with manual transmission, the SLABS signal is checked against a threshold value stored in ECM memory.
If other engine parameters indicate the engine is at high load and the VSS is below the threshold, a fault condition is
registered in the diagnostic memory.
The vehicle speed signal generated by the SLABS ECU is in the form of a pulse width modulated signal (PWM).
Pulses are generated at 8000 per mile, and the frequency of the signal changes in accordance with road speed. At
zero road speed the ECU outputs a reference signal at a frequency of 2Hz for diagnostic purposes.
Function
The input signal for the SLABS ECU is measured via pin 22 of connector C0637 of the ECM. The SLABS ECU
generates a PWM signal switching between 0 and 12 volts at a frequency of 8000 pulses per mile. For vehicles with
automatic gearbox the input signal for the EAT ECU is measured via pins 36 and 37 of connector C0637 of the ECM.
These pin numbers provide a bi-directional communications link using the CAN data bus.
In the case of a VSS failure on vehicles with automatic gearboxes, the ECM applies default values derived from the
EAT ECU. There are no default values for manual gearbox vehicles.
The VSS can fail in the following ways:
lWiring short circuit to vehicle supply.
lWiring short circuit to vehicle earth.
lWiring open circuit.
In the event of a VSS failure, any of the following symptoms may be observed:
lMIL illuminated after 2 driving cycles (NAS only).
lVehicle speed limiting disabled (manual transmission vehicles only).
lSLABS/HDC warning lamp on and audible warning.
Should a malfunction of the component occur the following fault codes may be evident and can be retrieved by
TestBook:
Rough road signal
When the vehicle travels across rough terrain, or on rough roads instability becomes evident in the drive train. The
ECM could interpret these vibrations as a 'false misfire'. To counteract this 'false misfire' the SLABS ECU generates
a rough road signal, sends it to the ECM so that the ECM can suspend misfire detection for as long as the vehicle is
travelling on the 'rough road'.
P Code J2012 Description Land Rover Description
P0500 Vehicle speed sensor malfunction VSS short or open circuit
P0501 Vehicle speed sensor range/performance VSS implausible