ESP LAND ROVER DISCOVERY 1999 Owner's Manual
[x] Cancel search | Manufacturer: LAND ROVER, Model Year: 1999, Model line: DISCOVERY, Model: LAND ROVER DISCOVERY 1999Pages: 1529, PDF Size: 34.8 MB
Page 273 of 1529
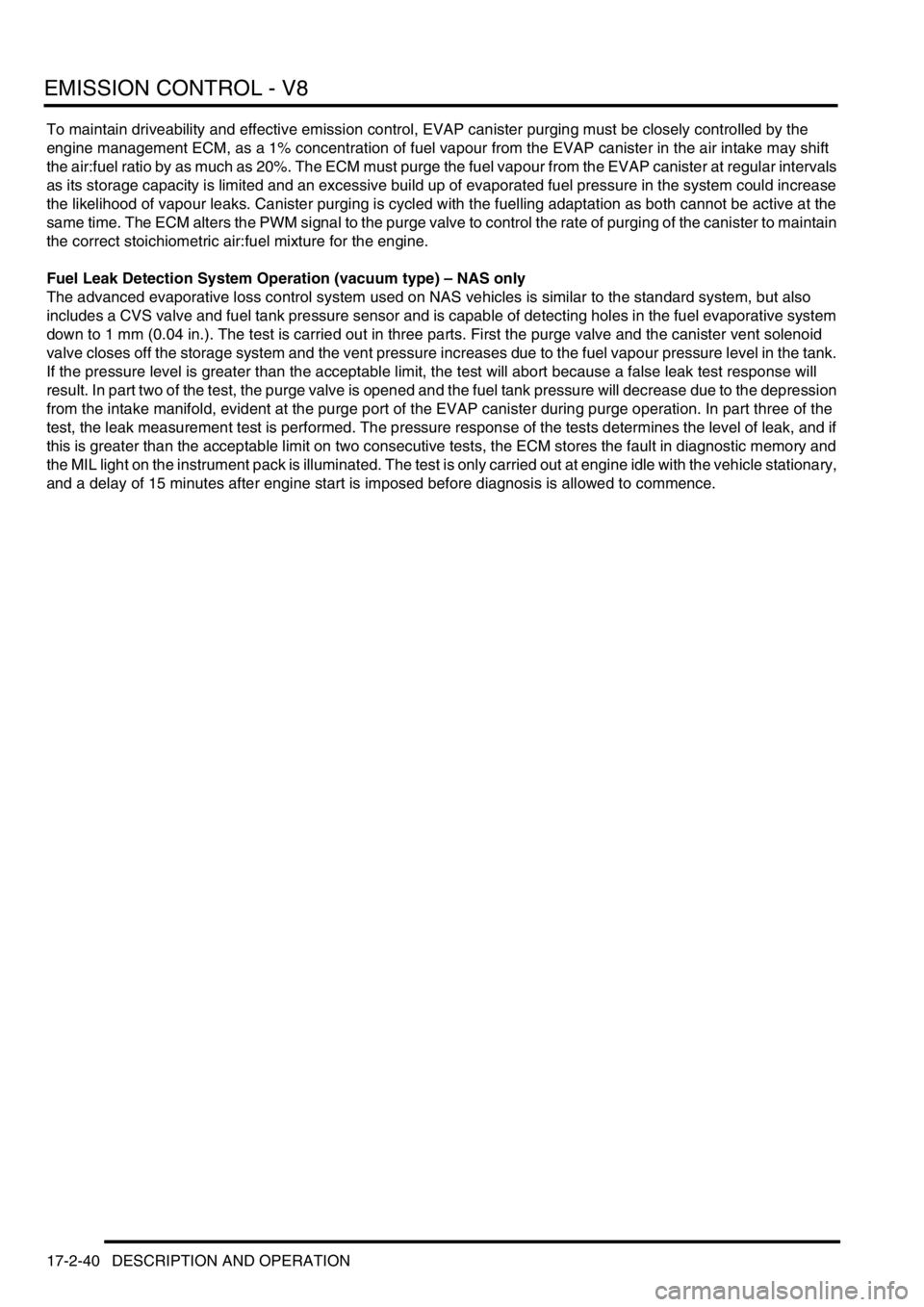
EMISSION CONTROL - V8
17-2-40 DESCRIPTION AND OPERATION
To maintain driveability and effective emission control, EVAP canister purging must be closely controlled by the
engine management ECM, as a 1% concentration of fuel vapour from the EVAP canister in the air intake may shift
the air:fuel ratio by as much as 20%. The ECM must purge the fuel vapour from the EVAP canister at regular intervals
as its storage capacity is limited and an excessive build up of evaporated fuel pressure in the system could increase
the likelihood of vapour leaks. Canister purging is cycled with the fuelling adaptation as both cannot be active at the
same time. The ECM alters the PWM signal to the purge valve to control the rate of purging of the canister to maintain
the correct stoichiometric air:fuel mixture for the engine.
Fuel Leak Detection System Operation (vacuum type) – NAS only
The advanced evaporative loss control system used on NAS vehicles is similar to the standard system, but also
includes a CVS valve and fuel tank pressure sensor and is capable of detecting holes in the fuel evaporative system
down to 1 mm (0.04 in.). The test is carried out in three parts. First the purge valve and the canister vent solenoid
valve closes off the storage system and the vent pressure increases due to the fuel vapour pressure level in the tank.
If the pressure level is greater than the acceptable limit, the test will abort because a false leak test response will
result. In part two of the test, the purge valve is opened and the fuel tank pressure will decrease due to the depression
from the intake manifold, evident at the purge port of the EVAP canister during purge operation. In part three of the
test, the leak measurement test is performed. The pressure response of the tests determines the level of leak, and if
this is greater than the acceptable limit on two consecutive tests, the ECM stores the fault in diagnostic memory and
the MIL light on the instrument pack is illuminated. The test is only carried out at engine idle with the vehicle stationary,
and a delay of 15 minutes after engine start is imposed before diagnosis is allowed to commence.
Page 274 of 1529
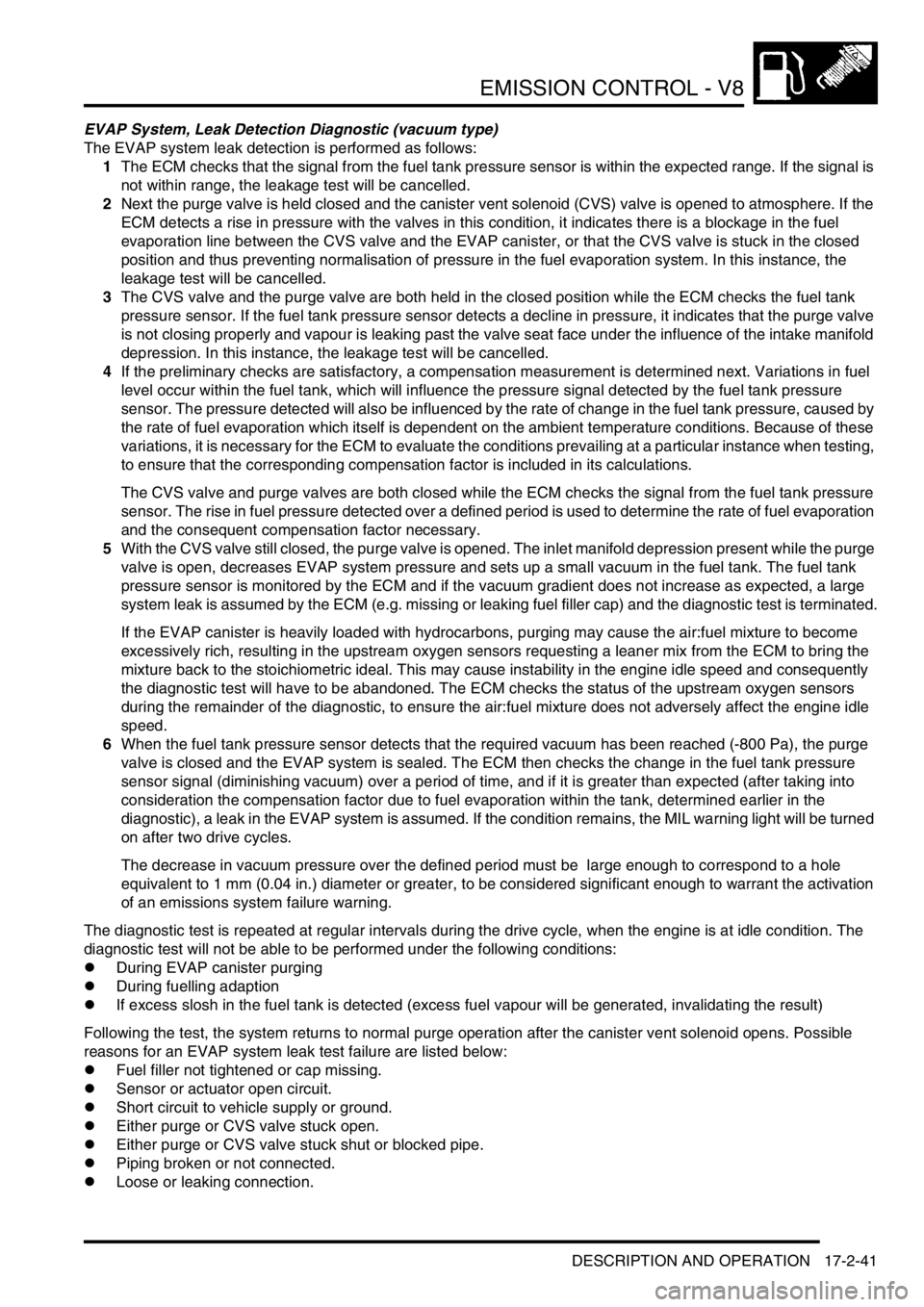
EMISSION CONTROL - V8
DESCRIPTION AND OPERATION 17-2-41
EVAP System, Leak Detection Diagnostic (vacuum type)
The EVAP system leak detection is performed as follows:
1The ECM checks that the signal from the fuel tank pressure sensor is within the expected range. If the signal is
not within range, the leakage test will be cancelled.
2Next the purge valve is held closed and the canister vent solenoid (CVS) valve is opened to atmosphere. If the
ECM detects a rise in pressure with the valves in this condition, it indicates there is a blockage in the fuel
evaporation line between the CVS valve and the EVAP canister, or that the CVS valve is stuck in the closed
position and thus preventing normalisation of pressure in the fuel evaporation system. In this instance, the
leakage test will be cancelled.
3The CVS valve and the purge valve are both held in the closed position while the ECM checks the fuel tank
pressure sensor. If the fuel tank pressure sensor detects a decline in pressure, it indicates that the purge valve
is not closing properly and vapour is leaking past the valve seat face under the influence of the intake manifold
depression. In this instance, the leakage test will be cancelled.
4If the preliminary checks are satisfactory, a compensation measurement is determined next. Variations in fuel
level occur within the fuel tank, which will influence the pressure signal detected by the fuel tank pressure
sensor. The pressure detected will also be influenced by the rate of change in the fuel tank pressure, caused by
the rate of fuel evaporation which itself is dependent on the ambient temperature conditions. Because of these
variations, it is necessary for the ECM to evaluate the conditions prevailing at a particular instance when testing,
to ensure that the corresponding compensation factor is included in its calculations.
The CVS valve and purge valves are both closed while the ECM checks the signal from the fuel tank pressure
sensor. The rise in fuel pressure detected over a defined period is used to determine the rate of fuel evaporation
and the consequent compensation factor necessary.
5With the CVS valve still closed, the purge valve is opened. The inlet manifold depression present while the purge
valve is open, decreases EVAP system pressure and sets up a small vacuum in the fuel tank. The fuel tank
pressure sensor is monitored by the ECM and if the vacuum gradient does not increase as expected, a large
system leak is assumed by the ECM (e.g. missing or leaking fuel filler cap) and the diagnostic test is terminated.
If the EVAP canister is heavily loaded with hydrocarbons, purging may cause the air:fuel mixture to become
excessively rich, resulting in the upstream oxygen sensors requesting a leaner mix from the ECM to bring the
mixture back to the stoichiometric ideal. This may cause instability in the engine idle speed and consequently
the diagnostic test will have to be abandoned. The ECM checks the status of the upstream oxygen sensors
during the remainder of the diagnostic, to ensure the air:fuel mixture does not adversely affect the engine idle
speed.
6When the fuel tank pressure sensor detects that the required vacuum has been reached (-800 Pa), the purge
valve is closed and the EVAP system is sealed. The ECM then checks the change in the fuel tank pressure
sensor signal (diminishing vacuum) over a period of time, and if it is greater than expected (after taking into
consideration the compensation factor due to fuel evaporation within the tank, determined earlier in the
diagnostic), a leak in the EVAP system is assumed. If the condition remains, the MIL warning light will be turned
on after two drive cycles.
The decrease in vacuum pressure over the defined period must be large enough to correspond to a hole
equivalent to 1 mm (0.04 in.) diameter or greater, to be considered significant enough to warrant the activation
of an emissions system failure warning.
The diagnostic test is repeated at regular intervals during the drive cycle, when the engine is at idle condition. The
diagnostic test will not be able to be performed under the following conditions:
lDuring EVAP canister purging
lDuring fuelling adaption
lIf excess slosh in the fuel tank is detected (excess fuel vapour will be generated, invalidating the result)
Following the test, the system returns to normal purge operation after the canister vent solenoid opens. Possible
reasons for an EVAP system leak test failure are listed below:
lFuel filler not tightened or cap missing.
lSensor or actuator open circuit.
lShort circuit to vehicle supply or ground.
lEither purge or CVS valve stuck open.
lEither purge or CVS valve stuck shut or blocked pipe.
lPiping broken or not connected.
lLoose or leaking connection.
Page 276 of 1529
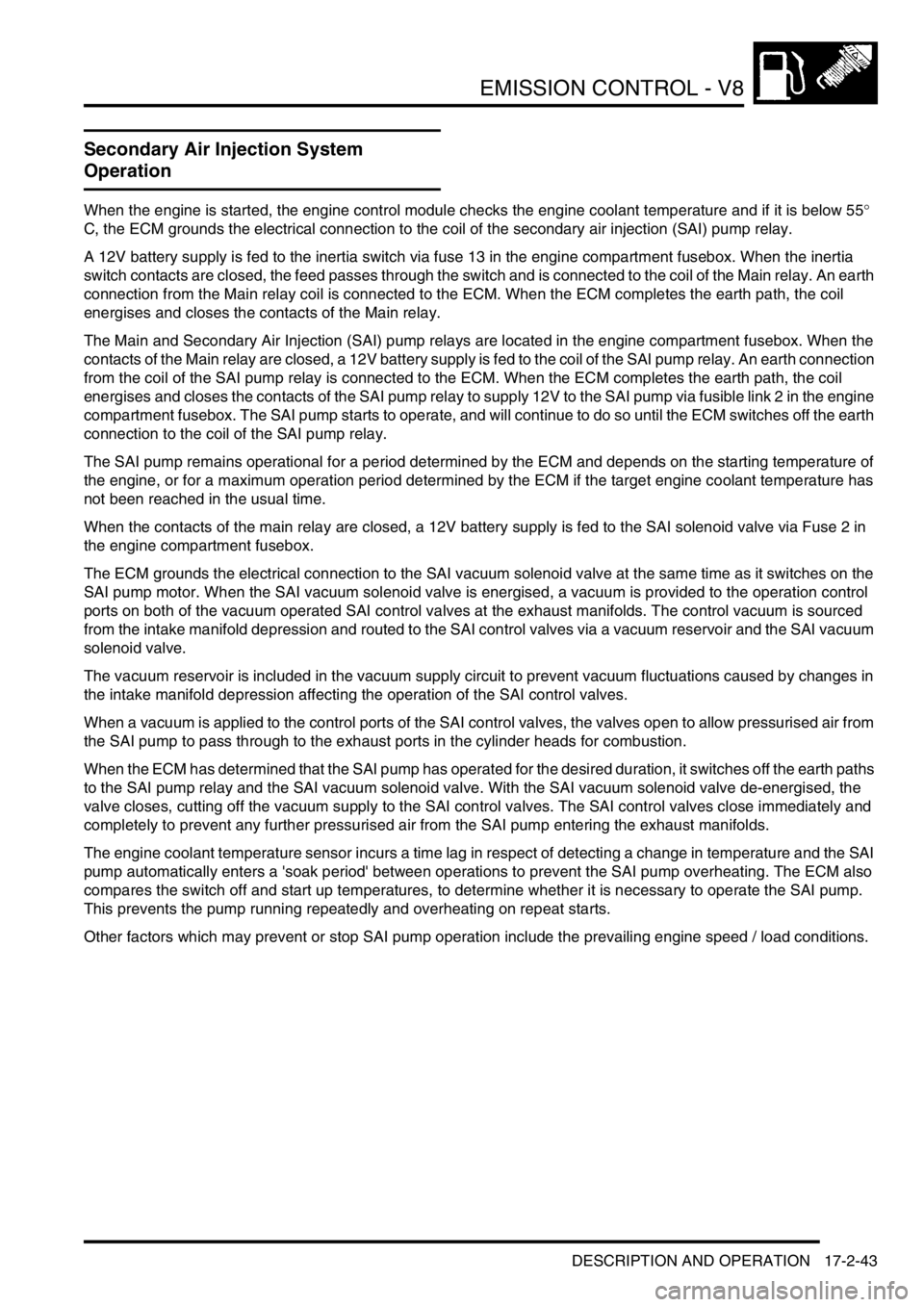
EMISSION CONTROL - V8
DESCRIPTION AND OPERATION 17-2-43
Secondary Air Injection System
Operation
When the engine is started, the engine control module checks the engine coolant temperature and if it is below 55°
C, the ECM grounds the electrical connection to the coil of the secondary air injection (SAI) pump relay.
A 12V battery supply is fed to the inertia switch via fuse 13 in the engine compartment fusebox. When the inertia
switch contacts are closed, the feed passes through the switch and is connected to the coil of the Main relay. An earth
connection from the Main relay coil is connected to the ECM. When the ECM completes the earth path, the coil
energises and closes the contacts of the Main relay.
The Main and Secondary Air Injection (SAI) pump relays are located in the engine compartment fusebox. When the
contacts of the Main relay are closed, a 12V battery supply is fed to the coil of the SAI pump relay. An earth connection
from the coil of the SAI pump relay is connected to the ECM. When the ECM completes the earth path, the coil
energises and closes the contacts of the SAI pump relay to supply 12V to the SAI pump via fusible link 2 in the engine
compartment fusebox. The SAI pump starts to operate, and will continue to do so until the ECM switches off the earth
connection to the coil of the SAI pump relay.
The SAI pump remains operational for a period determined by the ECM and depends on the starting temperature of
the engine, or for a maximum operation period determined by the ECM if the target engine coolant temperature has
not been reached in the usual time.
When the contacts of the main relay are closed, a 12V battery supply is fed to the SAI solenoid valve via Fuse 2 in
the engine compartment fusebox.
The ECM grounds the electrical connection to the SAI vacuum solenoid valve at the same time as it switches on the
SAI pump motor. When the SAI vacuum solenoid valve is energised, a vacuum is provided to the operation control
ports on both of the vacuum operated SAI control valves at the exhaust manifolds. The control vacuum is sourced
from the intake manifold depression and routed to the SAI control valves via a vacuum reservoir and the SAI vacuum
solenoid valve.
The vacuum reservoir is included in the vacuum supply circuit to prevent vacuum fluctuations caused by changes in
the intake manifold depression affecting the operation of the SAI control valves.
When a vacuum is applied to the control ports of the SAI control valves, the valves open to allow pressurised air from
the SAI pump to pass through to the exhaust ports in the cylinder heads for combustion.
When the ECM has determined that the SAI pump has operated for the desired duration, it switches off the earth paths
to the SAI pump relay and the SAI vacuum solenoid valve. With the SAI vacuum solenoid valve de-energised, the
valve closes, cutting off the vacuum supply to the SAI control valves. The SAI control valves close immediately and
completely to prevent any further pressurised air from the SAI pump entering the exhaust manifolds.
The engine coolant temperature sensor incurs a time lag in respect of detecting a change in temperature and the SAI
pump automatically enters a 'soak period' between operations to prevent the SAI pump overheating. The ECM also
compares the switch off and start up temperatures, to determine whether it is necessary to operate the SAI pump.
This prevents the pump running repeatedly and overheating on repeat starts.
Other factors which may prevent or stop SAI pump operation include the prevailing engine speed / load conditions.
Page 278 of 1529
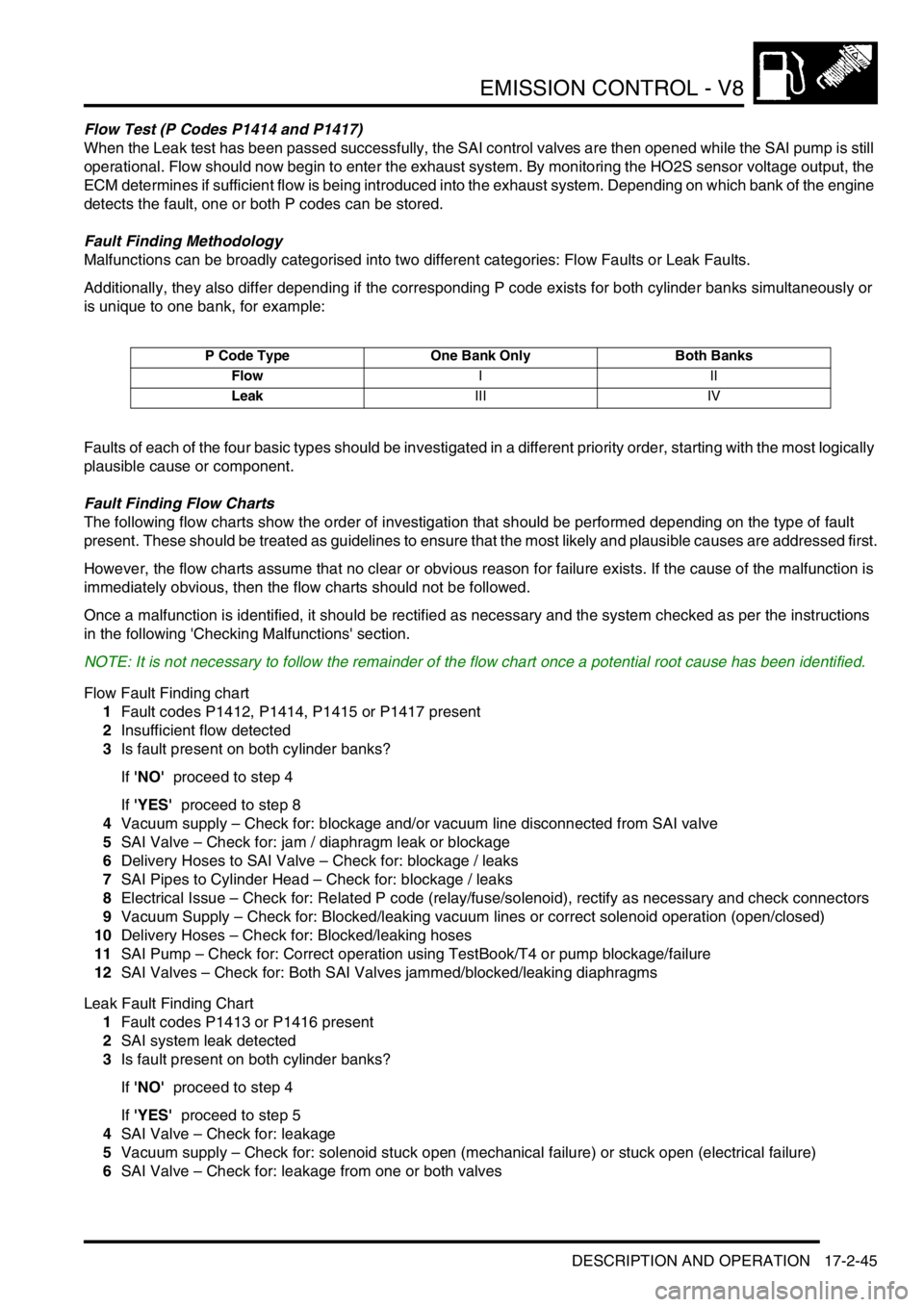
EMISSION CONTROL - V8
DESCRIPTION AND OPERATION 17-2-45
Flow Test (P Codes P1414 and P1417)
When the Leak test has been passed successfully, the SAI control valves are then opened while the SAI pump is still
operational. Flow should now begin to enter the exhaust system. By monitoring the HO2S sensor voltage output, the
ECM determines if sufficient flow is being introduced into the exhaust system. Depending on which bank of the engine
detects the fault, one or both P codes can be stored.
Fault Finding Methodology
Malfunctions can be broadly categorised into two different categories: Flow Faults or Leak Faults.
Additionally, they also differ depending if the corresponding P code exists for both cylinder banks simultaneously or
is unique to one bank, for example:
Faults of each of the four basic types should be investigated in a different priority order, starting with the most logically
plausible cause or component.
Fault Finding Flow Charts
The following flow charts show the order of investigation that should be performed depending on the type of fault
present. These should be treated as guidelines to ensure that the most likely and plausible causes are addressed first.
However, the flow charts assume that no clear or obvious reason for failure exists. If the cause of the malfunction is
immediately obvious, then the flow charts should not be followed.
Once a malfunction is identified, it should be rectified as necessary and the system checked as per the instructions
in the following 'Checking Malfunctions' section.
NOTE: It is not necessary to follow the remainder of the flow chart once a potential root cause has been identified.
Flow Fault Finding chart
1Fault codes P1412, P1414, P1415 or P1417 present
2Insufficient flow detected
3Is fault present on both cylinder banks?
If 'NO' proceed to step 4
If 'YES' proceed to step 8
4Vacuum supply – Check for: blockage and/or vacuum line disconnected from SAI valve
5SAI Valve – Check for: jam / diaphragm leak or blockage
6Delivery Hoses to SAI Valve – Check for: blockage / leaks
7SAI Pipes to Cylinder Head – Check for: blockage / leaks
8Electrical Issue – Check for: Related P code (relay/fuse/solenoid), rectify as necessary and check connectors
9Vacuum Supply – Check for: Blocked/leaking vacuum lines or correct solenoid operation (open/closed)
10Delivery Hoses – Check for: Blocked/leaking hoses
11SAI Pump – Check for: Correct operation using TestBook/T4 or pump blockage/failure
12SAI Valves – Check for: Both SAI Valves jammed/blocked/leaking diaphragms
Leak Fault Finding Chart
1Fault codes P1413 or P1416 present
2SAI system leak detected
3Is fault present on both cylinder banks?
If 'NO' proceed to step 4
If 'YES' proceed to step 5
4SAI Valve – Check for: leakage
5Vacuum supply – Check for: solenoid stuck open (mechanical failure) or stuck open (electrical failure)
6SAI Valve – Check for: leakage from one or both valves
P Code Type One Bank Only Both Banks
FlowIII
LeakIII IV
Page 317 of 1529
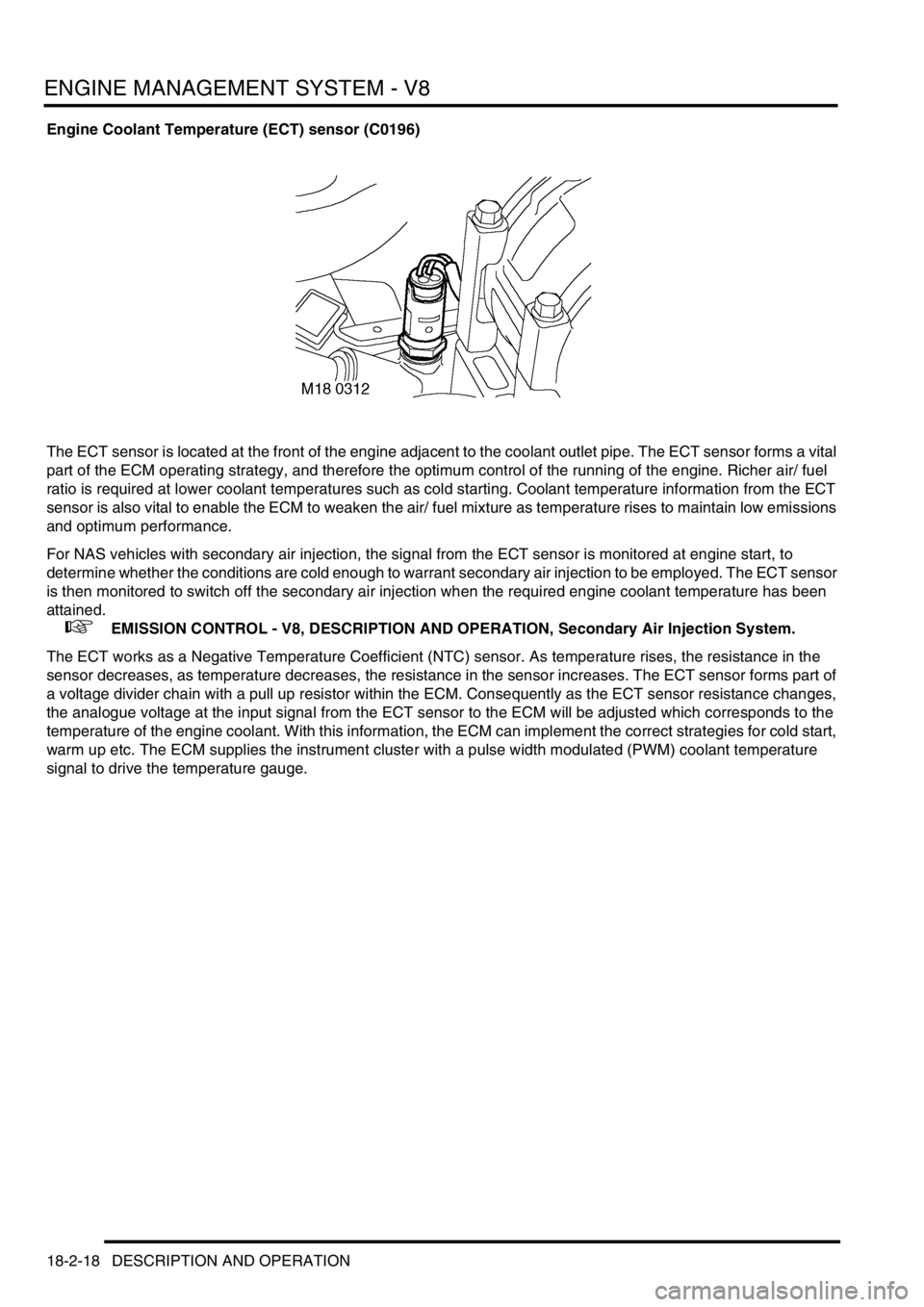
ENGINE MANAGEMENT SYSTEM - V8
18-2-18 DESCRIPTION AND OPERATION
Engine Coolant Temperature (ECT) sensor (C0196)
The ECT sensor is located at the front of the engine adjacent to the coolant outlet pipe. The ECT sensor forms a vital
part of the ECM operating strategy, and therefore the optimum control of the running of the engine. Richer air/ fuel
ratio is required at lower coolant temperatures such as cold starting. Coolant temperature information from the ECT
sensor is also vital to enable the ECM to weaken the air/ fuel mixture as temperature rises to maintain low emissions
and optimum performance.
For NAS vehicles with secondary air injection, the signal from the ECT sensor is monitored at engine start, to
determine whether the conditions are cold enough to warrant secondary air injection to be employed. The ECT sensor
is then monitored to switch off the secondary air injection when the required engine coolant temperature has been
attained.
+ EMISSION CONTROL - V8, DESCRIPTION AND OPERATION, Secondary Air Injection System.
The ECT works as a Negative Temperature Coefficient (NTC) sensor. As temperature rises, the resistance in the
sensor decreases, as temperature decreases, the resistance in the sensor increases. The ECT sensor forms part of
a voltage divider chain with a pull up resistor within the ECM. Consequently as the ECT sensor resistance changes,
the analogue voltage at the input signal from the ECT sensor to the ECM will be adjusted which corresponds to the
temperature of the engine coolant. With this information, the ECM can implement the correct strategies for cold start,
warm up etc. The ECM supplies the instrument cluster with a pulse width modulated (PWM) coolant temperature
signal to drive the temperature gauge.
Page 323 of 1529
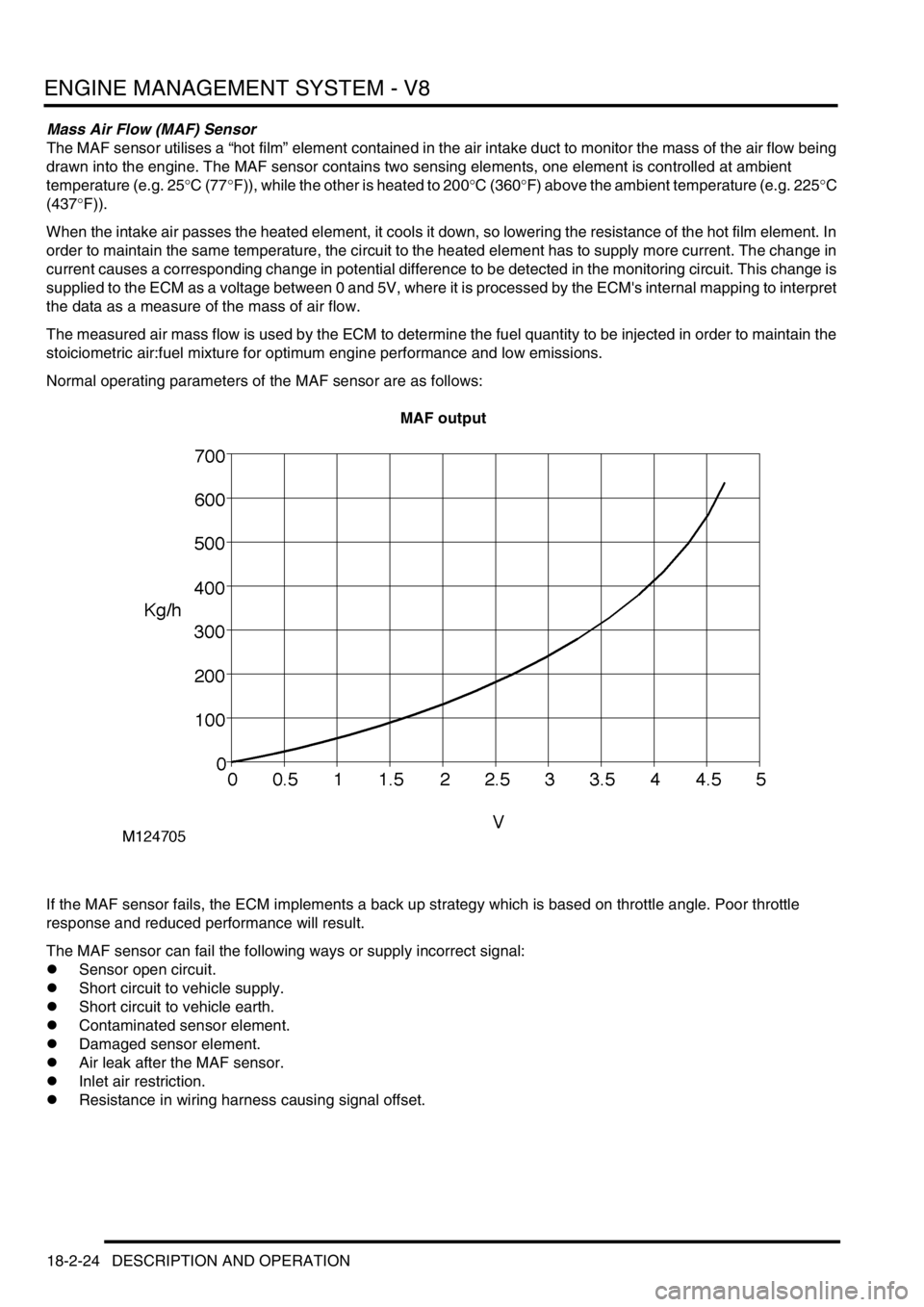
ENGINE MANAGEMENT SYSTEM - V8
18-2-24 DESCRIPTION AND OPERATION
Mass Air Flow (MAF) Sensor
The MAF sensor utilises a “hot film” element contained in the air intake duct to monitor the mass of the air flow being
drawn into the engine. The MAF sensor contains two sensing elements, one element is controlled at ambient
temperature (e.g. 25°C (77°F)), while the other is heated to 200°C (360°F) above the ambient temperature (e.g. 225°C
(437°F)).
When the intake air passes the heated element, it cools it down, so lowering the resistance of the hot film element. In
order to maintain the same temperature, the circuit to the heated element has to supply more current. The change in
current causes a corresponding change in potential difference to be detected in the monitoring circuit. This change is
supplied to the ECM as a voltage between 0 and 5V, where it is processed by the ECM's internal mapping to interpret
the data as a measure of the mass of air flow.
The measured air mass flow is used by the ECM to determine the fuel quantity to be injected in order to maintain the
stoiciometric air:fuel mixture for optimum engine performance and low emissions.
Normal operating parameters of the MAF sensor are as follows:
MAF output
If the MAF sensor fails, the ECM implements a back up strategy which is based on throttle angle. Poor throttle
response and reduced performance will result.
The MAF sensor can fail the following ways or supply incorrect signal:
lSensor open circuit.
lShort circuit to vehicle supply.
lShort circuit to vehicle earth.
lContaminated sensor element.
lDamaged sensor element.
lAir leak after the MAF sensor.
lInlet air restriction.
lResistance in wiring harness causing signal offset.
Page 324 of 1529
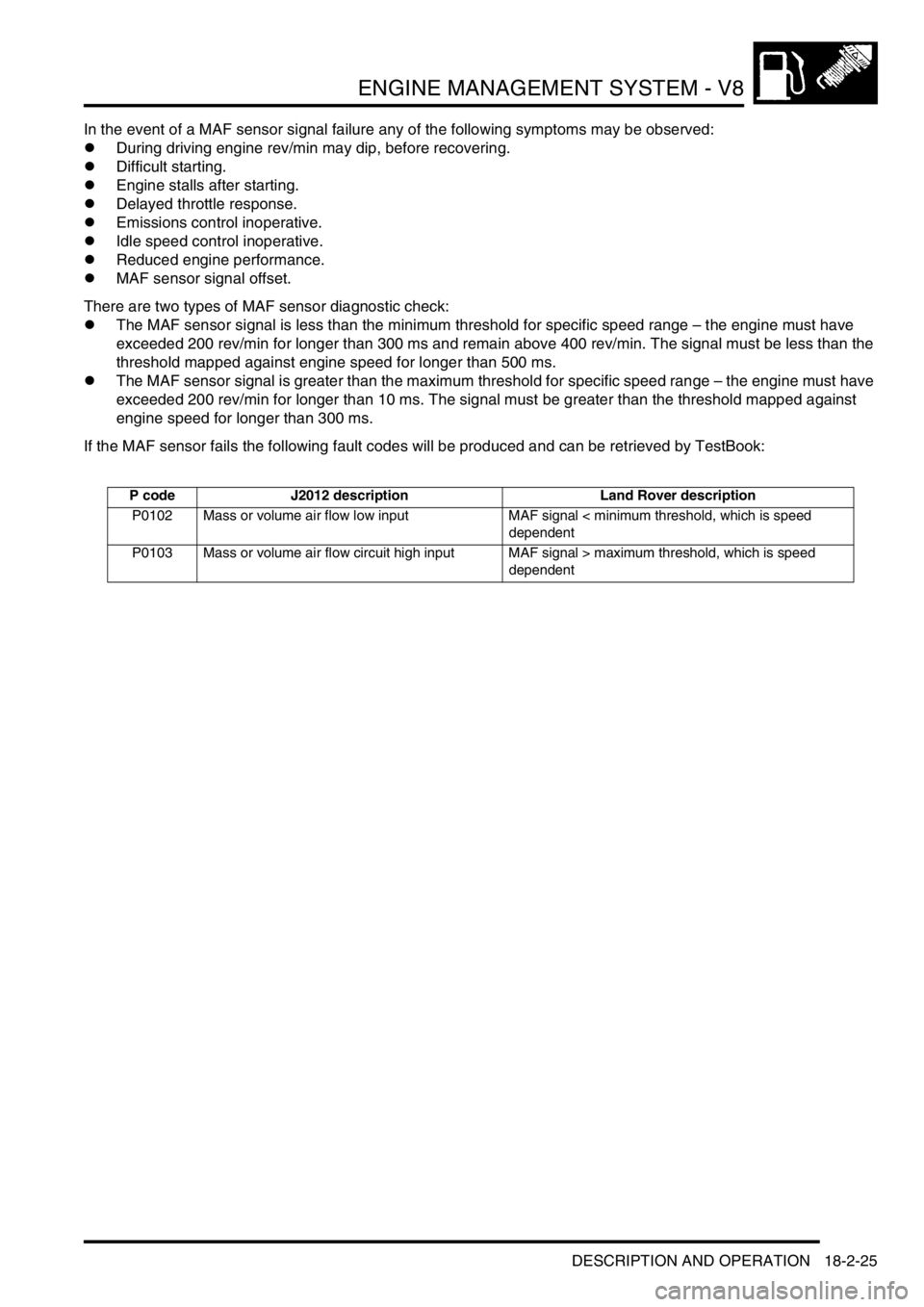
ENGINE MANAGEMENT SYSTEM - V8
DESCRIPTION AND OPERATION 18-2-25
In the event of a MAF sensor signal failure any of the following symptoms may be observed:
lDuring driving engine rev/min may dip, before recovering.
lDifficult starting.
lEngine stalls after starting.
lDelayed throttle response.
lEmissions control inoperative.
lIdle speed control inoperative.
lReduced engine performance.
lMAF sensor signal offset.
There are two types of MAF sensor diagnostic check:
lThe MAF sensor signal is less than the minimum threshold for specific speed range – the engine must have
exceeded 200 rev/min for longer than 300 ms and remain above 400 rev/min. The signal must be less than the
threshold mapped against engine speed for longer than 500 ms.
lThe MAF sensor signal is greater than the maximum threshold for specific speed range – the engine must have
exceeded 200 rev/min for longer than 10 ms. The signal must be greater than the threshold mapped against
engine speed for longer than 300 ms.
If the MAF sensor fails the following fault codes will be produced and can be retrieved by TestBook:
P code J2012 description Land Rover description
P0102 Mass or volume air flow low input MAF signal < minimum threshold, which is speed
dependent
P0103 Mass or volume air flow circuit high input MAF signal > maximum threshold, which is speed
dependent
Page 328 of 1529
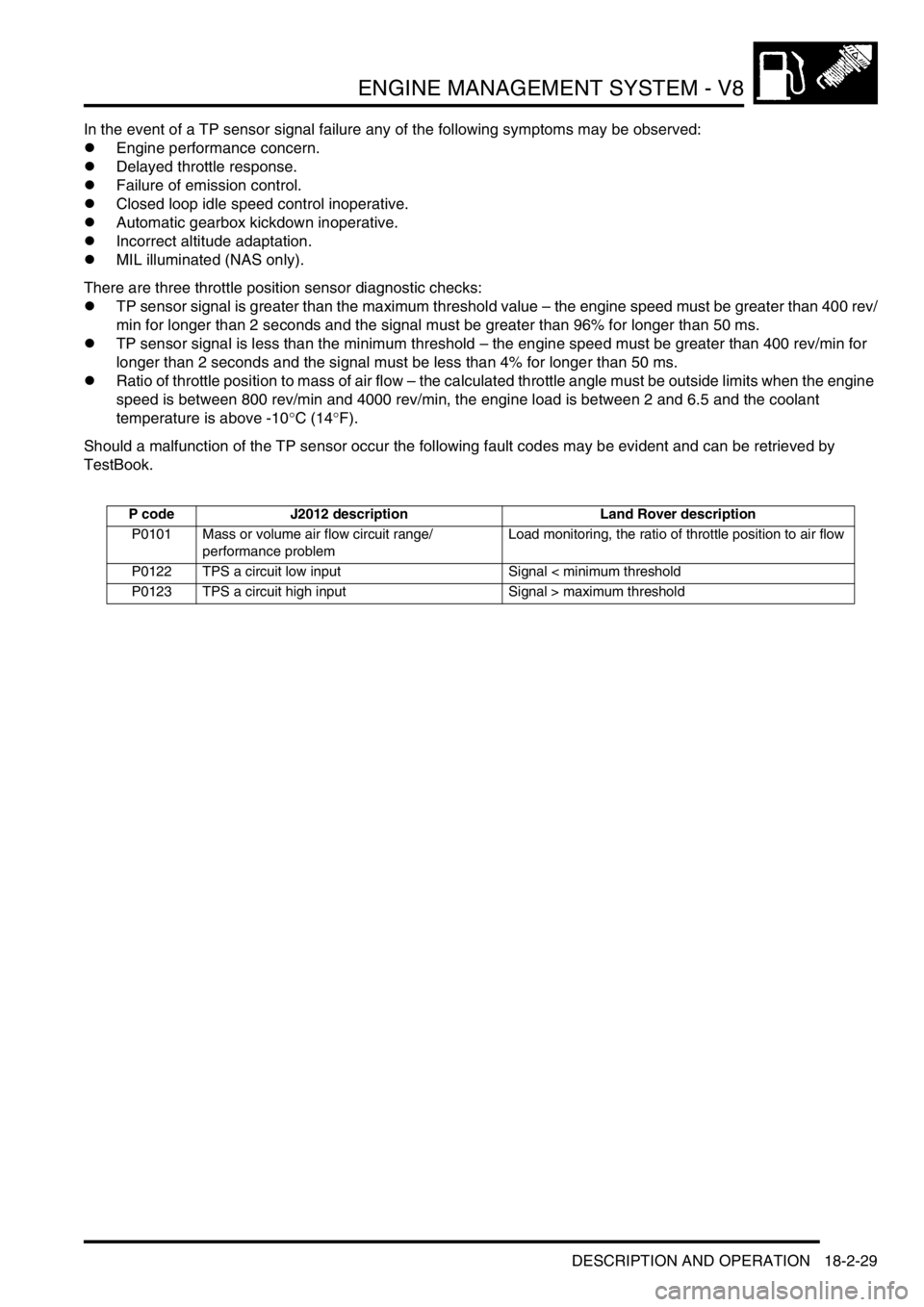
ENGINE MANAGEMENT SYSTEM - V8
DESCRIPTION AND OPERATION 18-2-29
In the event of a TP sensor signal failure any of the following symptoms may be observed:
lEngine performance concern.
lDelayed throttle response.
lFailure of emission control.
lClosed loop idle speed control inoperative.
lAutomatic gearbox kickdown inoperative.
lIncorrect altitude adaptation.
lMIL illuminated (NAS only).
There are three throttle position sensor diagnostic checks:
lTP sensor signal is greater than the maximum threshold value – the engine speed must be greater than 400 rev/
min for longer than 2 seconds and the signal must be greater than 96% for longer than 50 ms.
lTP sensor signal is less than the minimum threshold – the engine speed must be greater than 400 rev/min for
longer than 2 seconds and the signal must be less than 4% for longer than 50 ms.
lRatio of throttle position to mass of air flow – the calculated throttle angle must be outside limits when the engine
speed is between 800 rev/min and 4000 rev/min, the engine load is between 2 and 6.5 and the coolant
temperature is above -10°C (14°F).
Should a malfunction of the TP sensor occur the following fault codes may be evident and can be retrieved by
TestBook.
P code J2012 description Land Rover description
P0101 Mass or volume air flow circuit range/
performance problemLoad monitoring, the ratio of throttle position to air flow
P0122 TPS a circuit low input Signal < minimum threshold
P0123 TPS a circuit high input Signal > maximum threshold
Page 329 of 1529
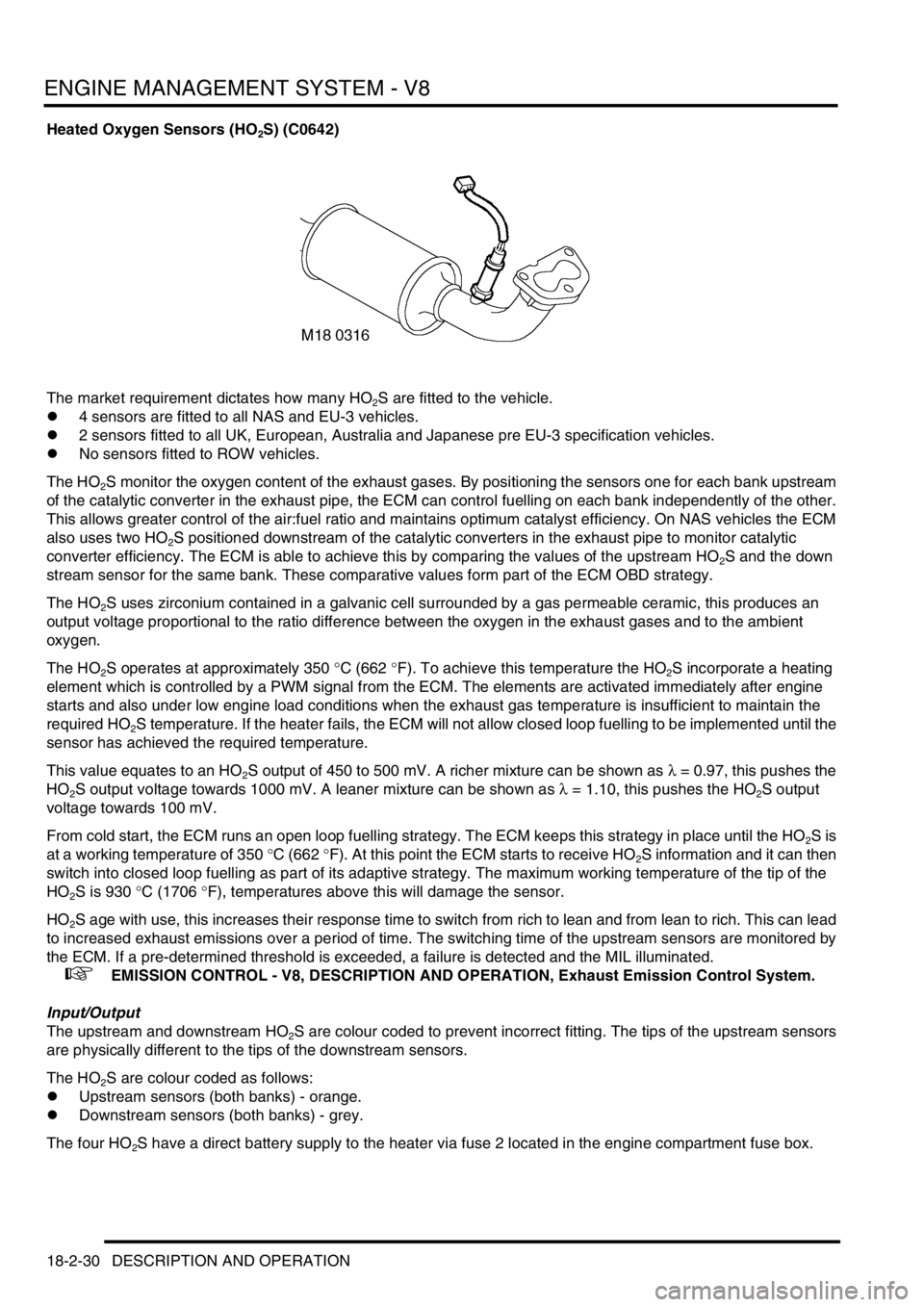
ENGINE MANAGEMENT SYSTEM - V8
18-2-30 DESCRIPTION AND OPERATION
Heated Oxygen Sensors (HO2S) (C0642)
The market requirement dictates how many HO
2S are fitted to the vehicle.
l4 sensors are fitted to all NAS and EU-3 vehicles.
l2 sensors fitted to all UK, European, Australia and Japanese pre EU-3 specification vehicles.
lNo sensors fitted to ROW vehicles.
The HO
2S monitor the oxygen content of the exhaust gases. By positioning the sensors one for each bank upstream
of the catalytic converter in the exhaust pipe, the ECM can control fuelling on each bank independently of the other.
This allows greater control of the air:fuel ratio and maintains optimum catalyst efficiency. On NAS vehicles the ECM
also uses two HO
2S positioned downstream of the catalytic converters in the exhaust pipe to monitor catalytic
converter efficiency. The ECM is able to achieve this by comparing the values of the upstream HO
2S and the down
stream sensor for the same bank. These comparative values form part of the ECM OBD strategy.
The HO
2S uses zirconium contained in a galvanic cell surrounded by a gas permeable ceramic, this produces an
output voltage proportional to the ratio difference between the oxygen in the exhaust gases and to the ambient
oxygen.
The HO
2S operates at approximately 350 °C (662 °F). To achieve this temperature the HO2S incorporate a heating
element which is controlled by a PWM signal from the ECM. The elements are activated immediately after engine
starts and also under low engine load conditions when the exhaust gas temperature is insufficient to maintain the
required HO
2S temperature. If the heater fails, the ECM will not allow closed loop fuelling to be implemented until the
sensor has achieved the required temperature.
This value equates to an HO
2S output of 450 to 500 mV. A richer mixture can be shown as λ = 0.97, this pushes the
HO
2S output voltage towards 1000 mV. A leaner mixture can be shown as λ = 1.10, this pushes the HO2S output
voltage towards 100 mV.
From cold start, the ECM runs an open loop fuelling strategy. The ECM keeps this strategy in place until the HO
2S is
at a working temperature of 350 °C (662 °F). At this point the ECM starts to receive HO
2S information and it can then
switch into closed loop fuelling as part of its adaptive strategy. The maximum working temperature of the tip of the
HO
2S is 930 °C (1706 °F), temperatures above this will damage the sensor.
HO
2S age with use, this increases their response time to switch from rich to lean and from lean to rich. This can lead
to increased exhaust emissions over a period of time. The switching time of the upstream sensors are monitored by
the ECM. If a pre-determined threshold is exceeded, a failure is detected and the MIL illuminated.
+ EMISSION CONTROL - V8, DESCRIPTION AND OPERATION, Exhaust Emission Control System.
Input/Output
The upstream and downstream HO
2S are colour coded to prevent incorrect fitting. The tips of the upstream sensors
are physically different to the tips of the downstream sensors.
The HO
2S are colour coded as follows:
lUpstream sensors (both banks) - orange.
lDownstream sensors (both banks) - grey.
The four HO
2S have a direct battery supply to the heater via fuse 2 located in the engine compartment fuse box.
Page 331 of 1529
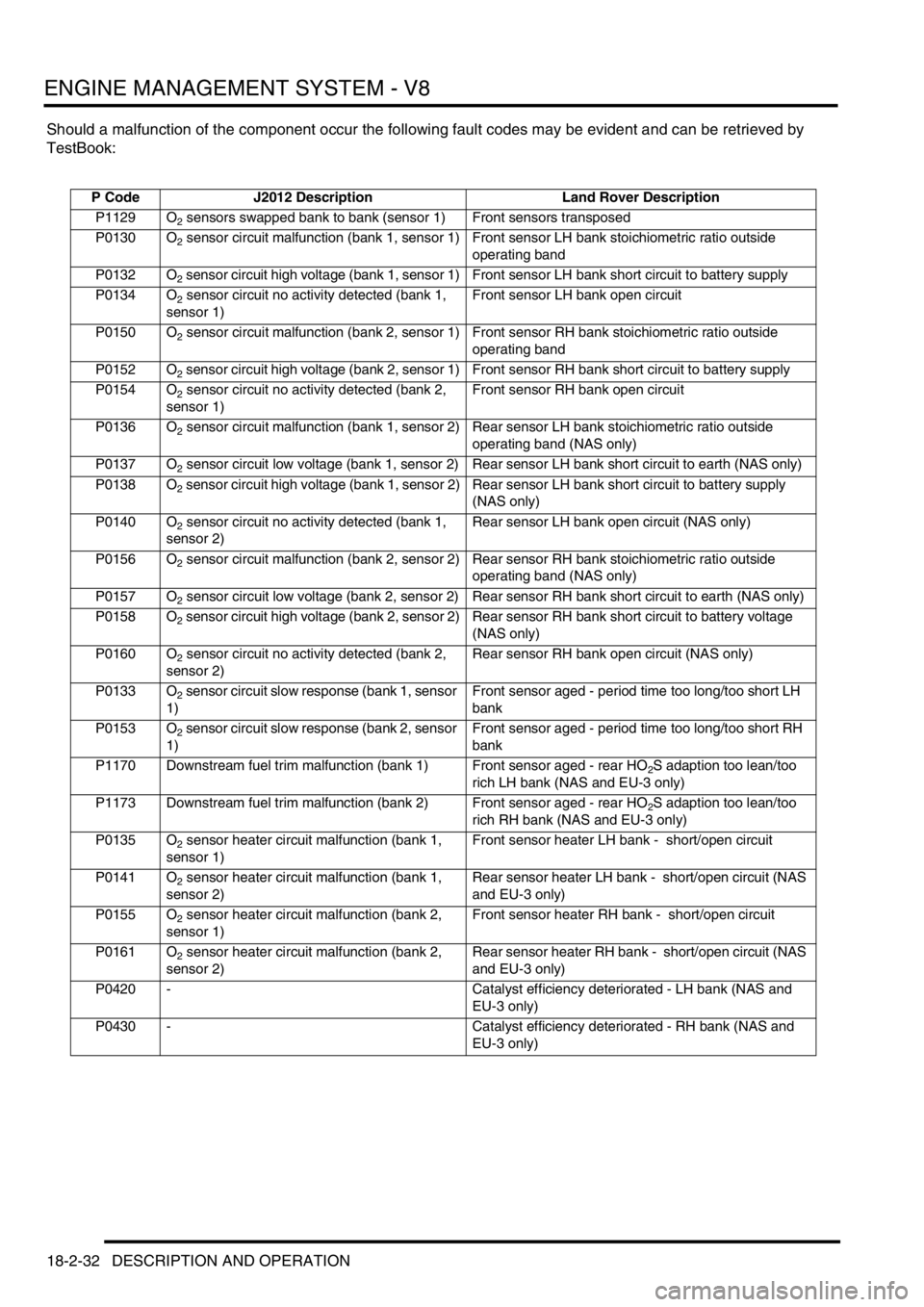
ENGINE MANAGEMENT SYSTEM - V8
18-2-32 DESCRIPTION AND OPERATION
Should a malfunction of the component occur the following fault codes may be evident and can be retrieved by
TestBook:
P Code J2012 Description Land Rover Description
P1129 O
2 sensors swapped bank to bank (sensor 1) Front sensors transposed
P0130 O
2 sensor circuit malfunction (bank 1, sensor 1) Front sensor LH bank stoichiometric ratio outside
operating band
P0132 O
2 sensor circuit high voltage (bank 1, sensor 1) Front sensor LH bank short circuit to battery supply
P0134 O
2 sensor circuit no activity detected (bank 1,
sensor 1)Front sensor LH bank open circuit
P0150 O
2 sensor circuit malfunction (bank 2, sensor 1) Front sensor RH bank stoichiometric ratio outside
operating band
P0152 O
2 sensor circuit high voltage (bank 2, sensor 1) Front sensor RH bank short circuit to battery supply
P0154 O
2 sensor circuit no activity detected (bank 2,
sensor 1)Front sensor RH bank open circuit
P0136 O
2 sensor circuit malfunction (bank 1, sensor 2) Rear sensor LH bank stoichiometric ratio outside
operating band (NAS only)
P0137 O
2 sensor circuit low voltage (bank 1, sensor 2) Rear sensor LH bank short circuit to earth (NAS only)
P0138 O
2 sensor circuit high voltage (bank 1, sensor 2) Rear sensor LH bank short circuit to battery supply
(NAS only)
P0140 O
2 sensor circuit no activity detected (bank 1,
sensor 2)Rear sensor LH bank open circuit (NAS only)
P0156 O
2 sensor circuit malfunction (bank 2, sensor 2) Rear sensor RH bank stoichiometric ratio outside
operating band (NAS only)
P0157 O
2 sensor circuit low voltage (bank 2, sensor 2) Rear sensor RH bank short circuit to earth (NAS only)
P0158 O
2 sensor circuit high voltage (bank 2, sensor 2) Rear sensor RH bank short circuit to battery voltage
(NAS only)
P0160 O
2 sensor circuit no activity detected (bank 2,
sensor 2)Rear sensor RH bank open circuit (NAS only)
P0133 O
2 sensor circuit slow response (bank 1, sensor
1)Front sensor aged - period time too long/too short LH
bank
P0153 O
2 sensor circuit slow response (bank 2, sensor
1)Front sensor aged - period time too long/too short RH
bank
P1170 Downstream fuel trim malfunction (bank 1) Front sensor aged - rear HO
2S adaption too lean/too
rich LH bank (NAS and EU-3 only)
P1173 Downstream fuel trim malfunction (bank 2) Front sensor aged - rear HO
2S adaption too lean/too
rich RH bank (NAS and EU-3 only)
P0135 O
2 sensor heater circuit malfunction (bank 1,
sensor 1)Front sensor heater LH bank - short/open circuit
P0141 O
2 sensor heater circuit malfunction (bank 1,
sensor 2)Rear sensor heater LH bank - short/open circuit (NAS
and EU-3 only)
P0155 O
2 sensor heater circuit malfunction (bank 2,
sensor 1)Front sensor heater RH bank - short/open circuit
P0161 O
2 sensor heater circuit malfunction (bank 2,
sensor 2)Rear sensor heater RH bank - short/open circuit (NAS
and EU-3 only)
P0420 - Catalyst efficiency deteriorated - LH bank (NAS and
EU-3 only)
P0430 - Catalyst efficiency deteriorated - RH bank (NAS and
EU-3 only)