compression ratio LAND ROVER DISCOVERY 1999 Workshop Manual
[x] Cancel search | Manufacturer: LAND ROVER, Model Year: 1999, Model line: DISCOVERY, Model: LAND ROVER DISCOVERY 1999Pages: 1529, PDF Size: 34.8 MB
Page 34 of 1529
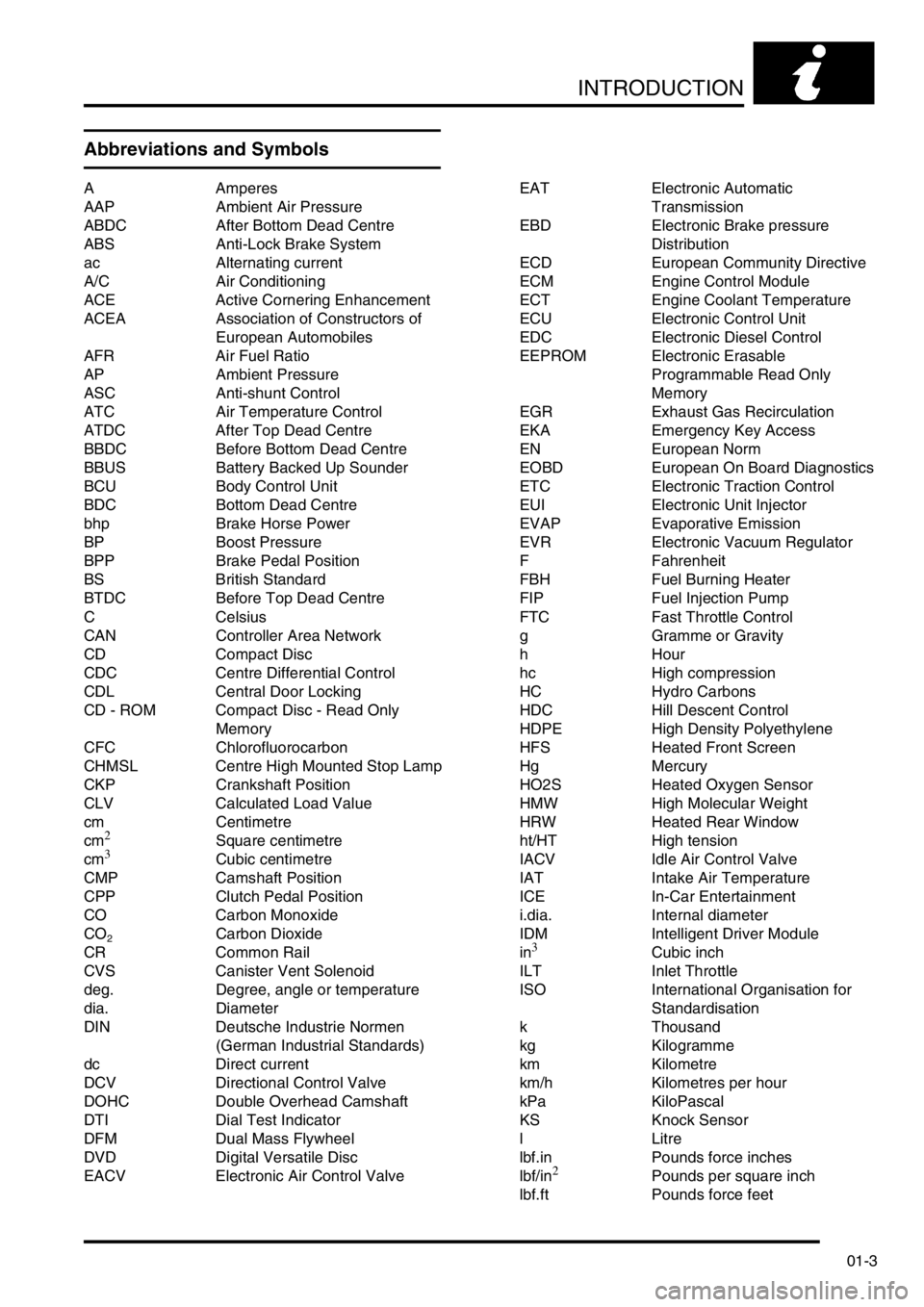
INTRODUCTION
01-3
Abbreviations and Symbols
A Amperes
AAP Ambient Air Pressure
ABDC After Bottom Dead Centre
ABS Anti-Lock Brake System
ac Alternating current
A/C Air Conditioning
ACE Active Cornering Enhancement
ACEA Association of Constructors of
European Automobiles
AFR Air Fuel Ratio
AP Ambient Pressure
ASC Anti-shunt Control
ATC Air Temperature Control
ATDC After Top Dead Centre
BBDC Before Bottom Dead Centre
BBUS Battery Backed Up Sounder
BCU Body Control Unit
BDC Bottom Dead Centre
bhp Brake Horse Power
BP Boost Pressure
BPP Brake Pedal Position
BS British Standard
BTDC Before Top Dead Centre
C Celsius
CAN Controller Area Network
CD Compact Disc
CDC Centre Differential Control
CDL Central Door Locking
CD - ROM Compact Disc - Read Only
Memory
CFC Chlorofluorocarbon
CHMSL Centre High Mounted Stop Lamp
CKP Crankshaft Position
CLV Calculated Load Value
cm Centimetre
cm
2Square centimetre
cm3Cubic centimetre
CMP Camshaft Position
CPP Clutch Pedal Position
CO Carbon Monoxide
CO
2Carbon Dioxide
CR Common Rail
CVS Canister Vent Solenoid
deg. Degree, angle or temperature
dia. Diameter
DIN Deutsche Industrie Normen
(German Industrial Standards)
dc Direct current
DCV Directional Control Valve
DOHC Double Overhead Camshaft
DTI Dial Test Indicator
DFM Dual Mass Flywheel
DVD Digital Versatile Disc
EACV Electronic Air Control Valve EAT Electronic Automatic
Transmission
EBD Electronic Brake pressure
Distribution
ECD European Community Directive
ECM Engine Control Module
ECT Engine Coolant Temperature
ECU Electronic Control Unit
EDC Electronic Diesel Control
EEPROM Electronic Erasable
Programmable Read Only
Memory
EGR Exhaust Gas Recirculation
EKA Emergency Key Access
EN European Norm
EOBD European On Board Diagnostics
ETC Electronic Traction Control
EUI Electronic Unit Injector
EVAP Evaporative Emission
EVR Electronic Vacuum Regulator
F Fahrenheit
FBH Fuel Burning Heater
FIP Fuel Injection Pump
FTC Fast Throttle Control
g Gramme or Gravity
hHour
hc High compression
HC Hydro Carbons
HDC Hill Descent Control
HDPE High Density Polyethylene
HFS Heated Front Screen
Hg Mercury
HO2S Heated Oxygen Sensor
HMW High Molecular Weight
HRW Heated Rear Window
ht/HT High tension
IACV Idle Air Control Valve
IAT Intake Air Temperature
ICE In-Car Entertainment
i.dia. Internal diameter
IDM Intelligent Driver Module
in3Cubic inch
ILT Inlet Throttle
ISO International Organisation for
Standardisation
k Thousand
kg Kilogramme
km Kilometre
km/h Kilometres per hour
kPa KiloPascal
KS Knock Sensor
lLitre
lbf.in Pounds force inches
lbf/in
2Pounds per square inch
lbf.ft Pounds force feet
Page 35 of 1529
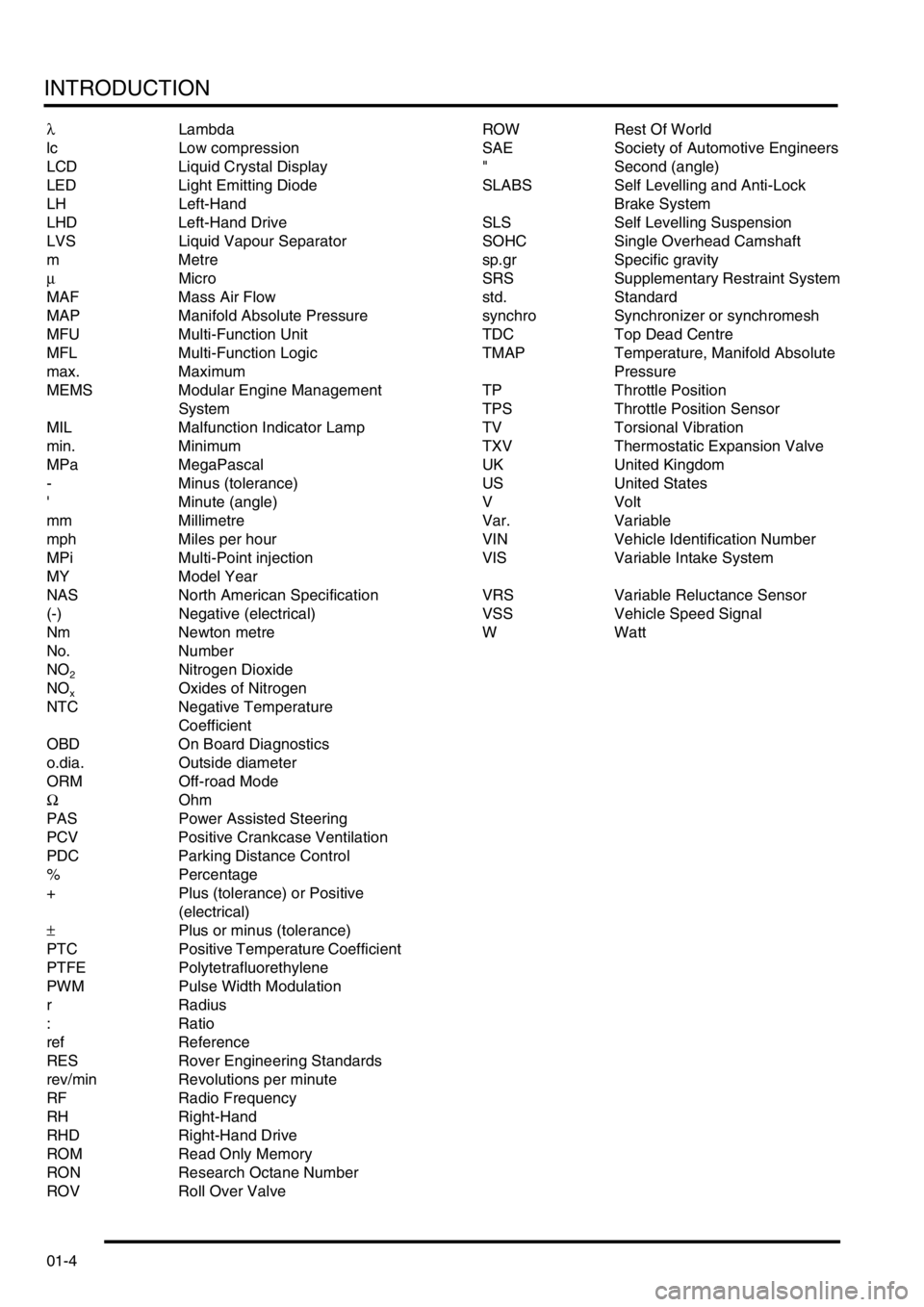
INTRODUCTION
01-4
λLambda
lc Low compression
LCD Liquid Crystal Display
LED Light Emitting Diode
LH Left-Hand
LHD Left-Hand Drive
LVS Liquid Vapour Separator
mMetre
µMicro
MAF Mass Air Flow
MAP Manifold Absolute Pressure
MFU Multi-Function Unit
MFL Multi-Function Logic
max. Maximum
MEMS Modular Engine Management
System
MIL Malfunction Indicator Lamp
min. Minimum
MPa MegaPascal
- Minus (tolerance)
' Minute (angle)
mm Millimetre
mph Miles per hour
MPi Multi-Point injection
MY Model Year
NAS North American Specification
(-) Negative (electrical)
Nm Newton metre
No. Number
NO
2Nitrogen Dioxide
NO
xOxides of Nitrogen
NTC Negative Temperature
Coefficient
OBD On Board Diagnostics
o.dia. Outside diameter
ORM Off-road Mode
ΩOhm
PAS Power Assisted Steering
PCV Positive Crankcase Ventilation
PDC Parking Distance Control
% Percentage
+ Plus (tolerance) or Positive
(electrical)
±Plus or minus (tolerance)
PTC Positive Temperature Coefficient
PTFE Polytetrafluorethylene
PWM Pulse Width Modulation
rRadius
:Ratio
ref Reference
RES Rover Engineering Standards
rev/min Revolutions per minute
RF Radio Frequency
RH Right-Hand
RHD Right-Hand Drive
ROM Read Only Memory
RON Research Octane Number
ROV Roll Over ValveROW Rest Of World
SAE Society of Automotive Engineers
" Second (angle)
SLABS Self Levelling and Anti-Lock
Brake System
SLS Self Levelling Suspension
SOHC Single Overhead Camshaft
sp.gr Specific gravity
SRS Supplementary Restraint System
std. Standard
synchro Synchronizer or synchromesh
TDC Top Dead Centre
TMAP Temperature, Manifold Absolute
Pressure
TP Throttle Position
TPS Throttle Position Sensor
TV Torsional Vibration
TXV Thermostatic Expansion Valve
UK United Kingdom
US United States
V Volt
Var. Variable
VIN Vehicle Identification Number
VIS Variable Intake System
VRS Variable Reluctance Sensor
VSS Vehicle Speed Signal
WWatt
Page 64 of 1529
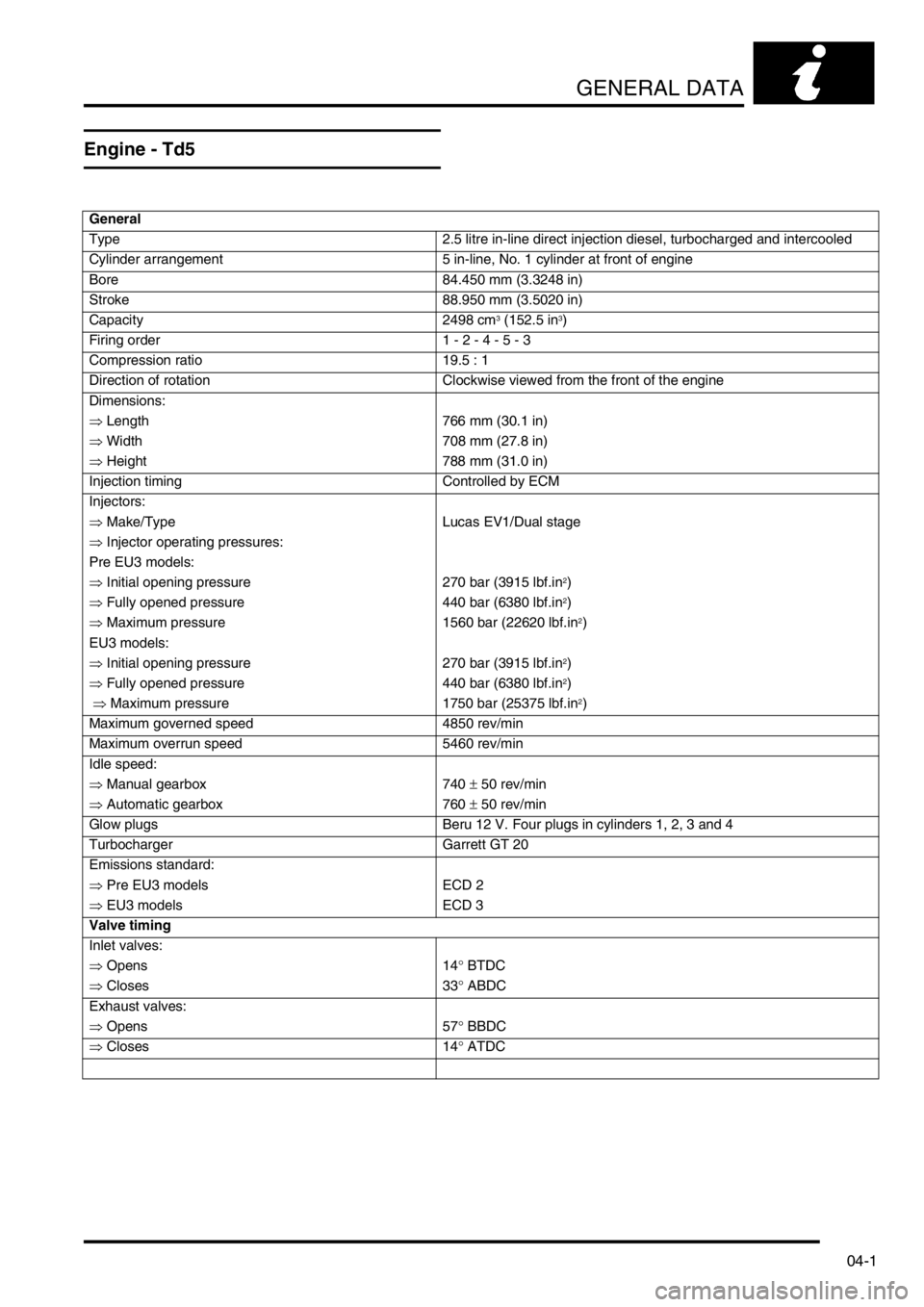
GENERAL DATA
04-1
GENERAL DATA
Engine - Td5
General
Type 2.5 litre in-line direct injection diesel, turbocharged and intercooled
Cylinder arrangement 5 in-line, No. 1 cylinder at front of engine
Bore 84.450 mm (3.3248 in)
Stroke 88.950 mm (3.5020 in)
Capacity 2498 cm
3 (152.5 in3)
Firing order 1 - 2 - 4 - 5 - 3
Compression ratio 19.5 : 1
Direction of rotation Clockwise viewed from the front of the engine
Dimensions:
⇒ Length 766 mm (30.1 in)
⇒ Width 708 mm (27.8 in)
⇒ Height 788 mm (31.0 in)
Injection timing Controlled by ECM
Injectors:
⇒ Make/Type Lucas EV1/Dual stage
⇒ Injector operating pressures:
Pre EU3 models:
⇒ Initial opening pressure 270 bar (3915 lbf.in
2)
⇒ Fully opened pressure 440 bar (6380 lbf.in
2)
⇒ Maximum pressure 1560 bar (22620 lbf.in
2)
EU3 models:
⇒ Initial opening pressure 270 bar (3915 lbf.in
2)
⇒ Fully opened pressure 440 bar (6380 lbf.in
2)
⇒ Maximum pressure 1750 bar (25375 lbf.in
2)
Maximum governed speed 4850 rev/min
Maximum overrun speed 5460 rev/min
Idle speed:
⇒ Manual gearbox 740 ± 50 rev/min
⇒ Automatic gearbox 760 ± 50 rev/min
Glow plugs Beru 12 V. Four plugs in cylinders 1, 2, 3 and 4
Turbocharger Garrett GT 20
Emissions standard:
⇒ Pre EU3 models ECD 2
⇒ EU3 models ECD 3
Valve timing
Inlet valves:
⇒ Opens 14° BTDC
⇒ Closes 33° ABDC
Exhaust valves:
⇒ Opens 57° BBDC
⇒ Closes 14° ATDC
Page 67 of 1529
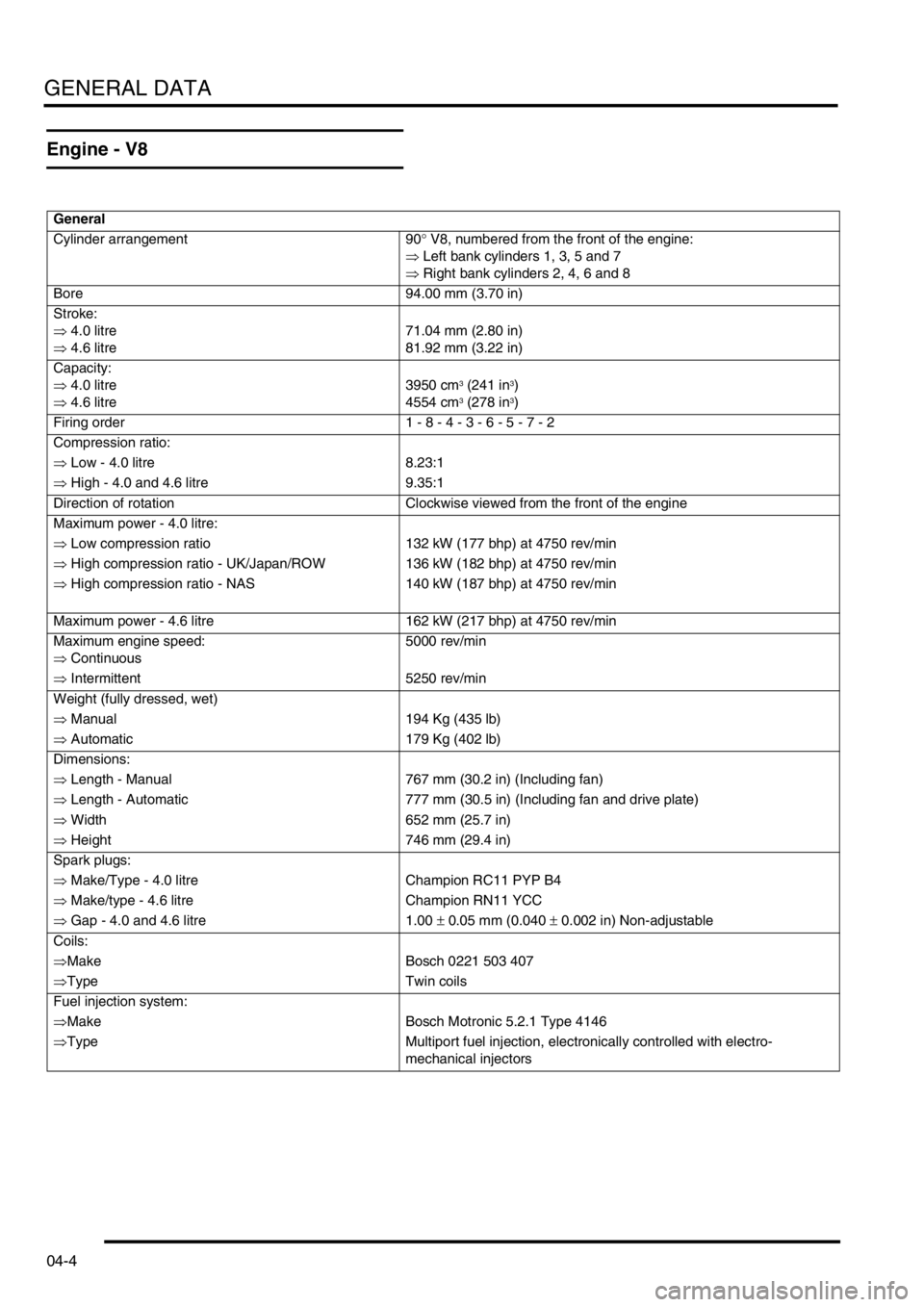
GENERAL DATA
04-4
Engine - V8
General
Cylinder arrangement 90° V8, numbered from the front of the engine:
⇒ Left bank cylinders 1, 3, 5 and 7
⇒ Right bank cylinders 2, 4, 6 and 8
Bore 94.00 mm (3.70 in)
Stroke:
⇒ 4.0 litre
⇒ 4.6 litre71.04 mm (2.80 in)
81.92 mm (3.22 in)
Capacity:
⇒ 4.0 litre
⇒ 4.6 litre3950 cm
3 (241 in3)
4554 cm3 (278 in3)
Firing order 1 - 8 - 4 - 3 - 6 - 5 - 7 - 2
Compression ratio:
⇒ Low - 4.0 litre 8.23:1
⇒ High - 4.0 and 4.6 litre 9.35:1
Direction of rotation Clockwise viewed from the front of the engine
Maximum power - 4.0 litre:
⇒ Low compression ratio 132 kW (177 bhp) at 4750 rev/min
⇒ High compression ratio - UK/Japan/ROW 136 kW (182 bhp) at 4750 rev/min
⇒ High compression ratio - NAS 140 kW (187 bhp) at 4750 rev/min
Maximum power - 4.6 litre 162 kW (217 bhp) at 4750 rev/min
Maximum engine speed:
⇒ Continuous5000 rev/min
⇒ Intermittent 5250 rev/min
Weight (fully dressed, wet)
⇒ Manual 194 Kg (435 lb)
⇒ Automatic 179 Kg (402 lb)
Dimensions:
⇒ Length - Manual 767 mm (30.2 in) (Including fan)
⇒ Length - Automatic 777 mm (30.5 in) (Including fan and drive plate)
⇒ Width 652 mm (25.7 in)
⇒ Height 746 mm (29.4 in)
Spark plugs:
⇒ Make/Type - 4.0 litre Champion RC11 PYP B4
⇒ Make/type - 4.6 litre Champion RN11 YCC
⇒ Gap - 4.0 and 4.6 litre 1.00 ± 0.05 mm (0.040 ± 0.002 in) Non-adjustable
Coils:
⇒Make Bosch 0221 503 407
⇒Type Twin coils
Fuel injection system:
⇒Make Bosch Motronic 5.2.1 Type 4146
⇒Type Multiport fuel injection, electronically controlled with electro-
mechanical injectors
Page 160 of 1529
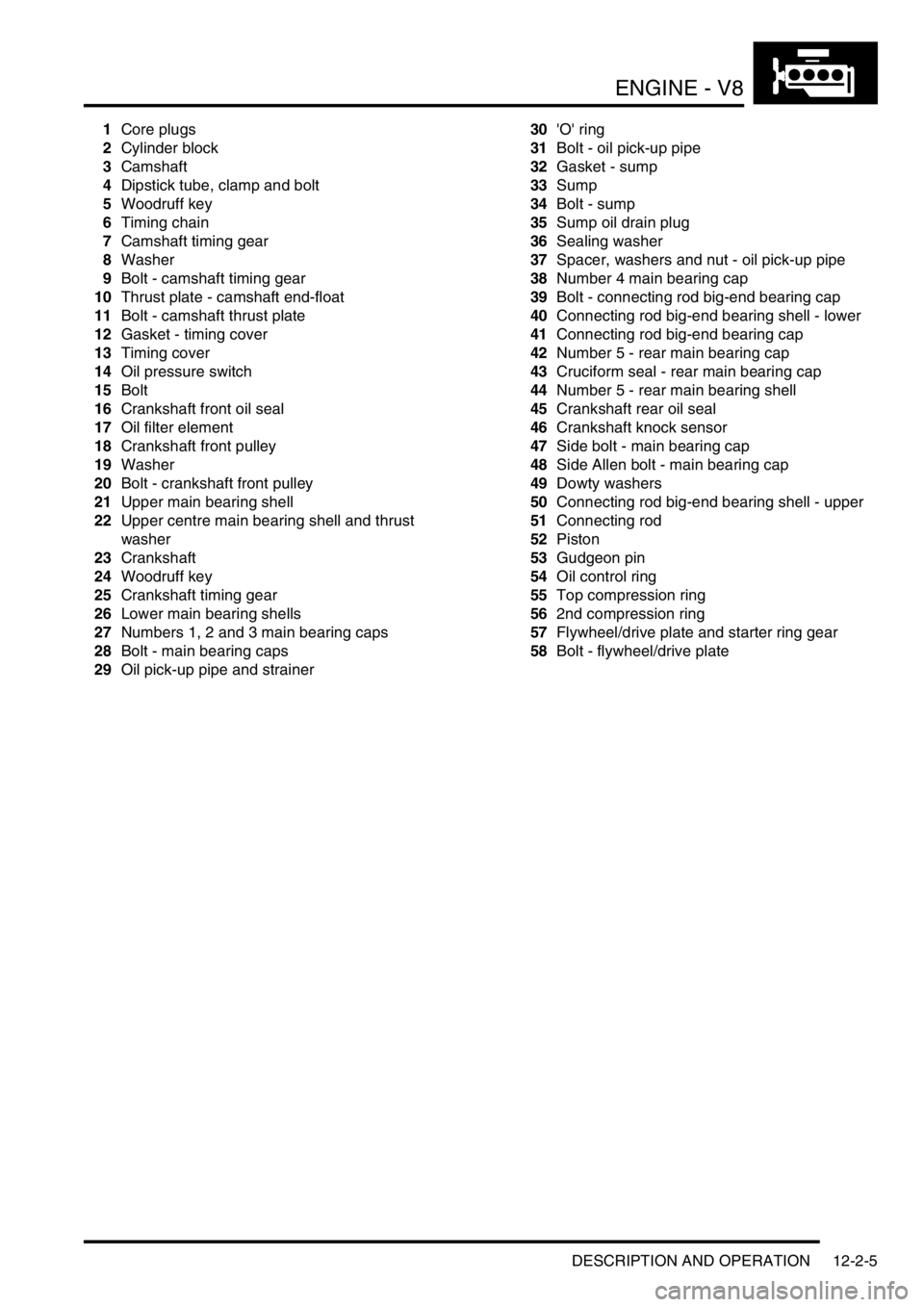
ENGINE - V8
DESCRIPTION AND OPERATION 12-2-5
1Core plugs
2Cylinder block
3Camshaft
4Dipstick tube, clamp and bolt
5Woodruff key
6Timing chain
7Camshaft timing gear
8Washer
9Bolt - camshaft timing gear
10Thrust plate - camshaft end-float
11Bolt - camshaft thrust plate
12Gasket - timing cover
13Timing cover
14Oil pressure switch
15Bolt
16Crankshaft front oil seal
17Oil filter element
18Crankshaft front pulley
19Washer
20Bolt - crankshaft front pulley
21Upper main bearing shell
22Upper centre main bearing shell and thrust
washer
23Crankshaft
24Woodruff key
25Crankshaft timing gear
26Lower main bearing shells
27Numbers 1, 2 and 3 main bearing caps
28Bolt - main bearing caps
29Oil pick-up pipe and strainer30'O' ring
31Bolt - oil pick-up pipe
32Gasket - sump
33Sump
34Bolt - sump
35Sump oil drain plug
36Sealing washer
37Spacer, washers and nut - oil pick-up pipe
38Number 4 main bearing cap
39Bolt - connecting rod big-end bearing cap
40Connecting rod big-end bearing shell - lower
41Connecting rod big-end bearing cap
42Number 5 - rear main bearing cap
43Cruciform seal - rear main bearing cap
44Number 5 - rear main bearing shell
45Crankshaft rear oil seal
46Crankshaft knock sensor
47Side bolt - main bearing cap
48Side Allen bolt - main bearing cap
49Dowty washers
50Connecting rod big-end bearing shell - upper
51Connecting rod
52Piston
53Gudgeon pin
54Oil control ring
55Top compression ring
562nd compression ring
57Flywheel/drive plate and starter ring gear
58Bolt - flywheel/drive plate
Page 162 of 1529

ENGINE - V8
DESCRIPTION AND OPERATION 12-2-7
Oil sump
The oil sump is bolted to the bottom of the cylinder block and the timing cover and is sealed to both components with
a one piece gasket. A removable baffle to prevent oil surge is fitted in the sump. The oil pick-up pipe and strainer
assembly is positioned within the sump and is attached at the pick-up end to a stud screwed into number four main
bearing cap and at the delivery end to the oil pump. The oil drain plug is located in the bottom of the sump and is
sealed with a washer.
Pistons and connecting rods
Each of the aluminium alloy pistons has two compression rings and an oil control ring. The pistons are secured to the
connecting rods by semi-floating gudgeon pins. Each gudgeon pin is offset by 0.5 mm (0.02 in). The top of each piston
is recessed, the depth of recess determining the compression ratio of the engine. Plain, big-end bearing shells are
fitted to each connecting rod and cap.
Page 223 of 1529
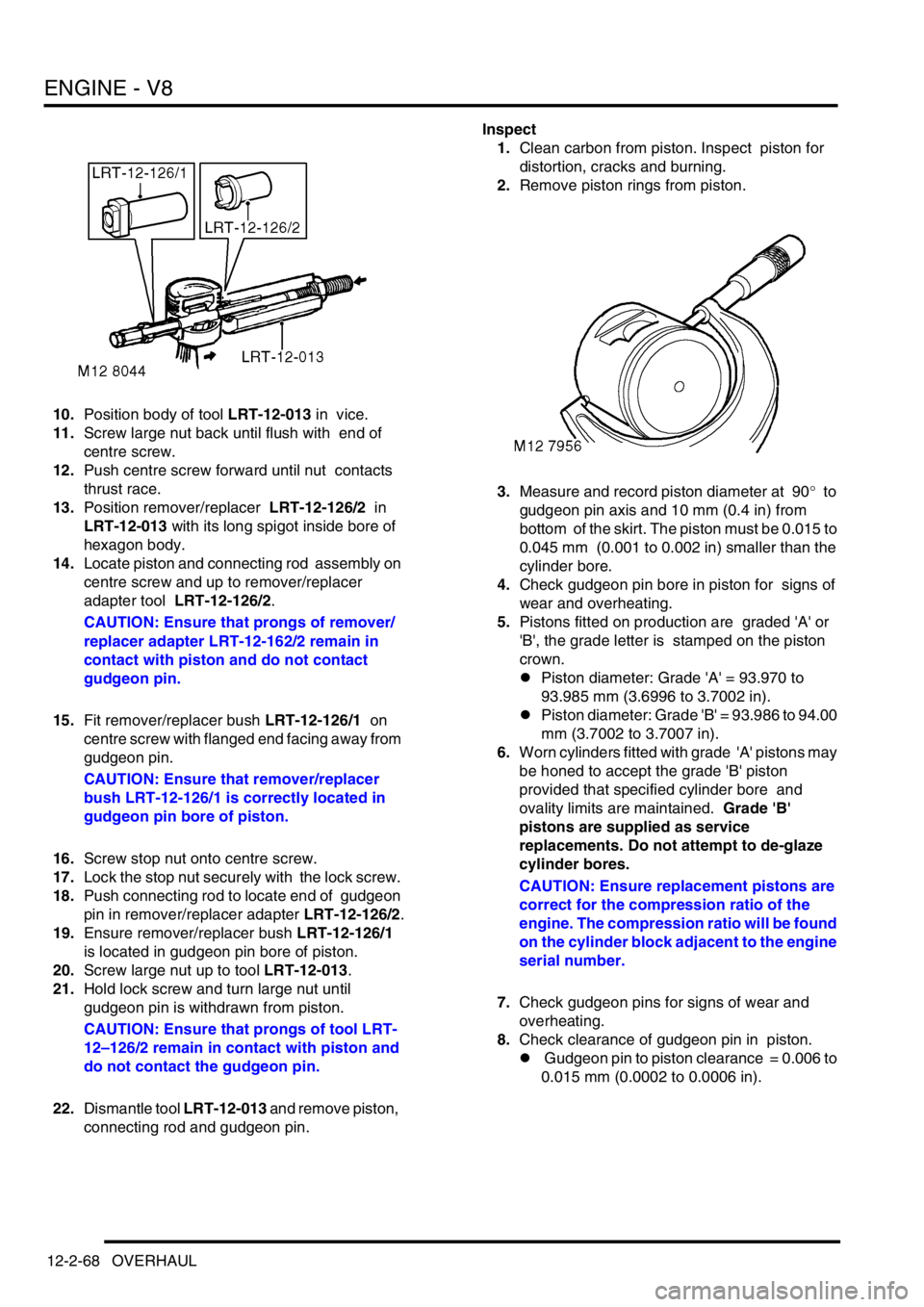
ENGINE - V8
12-2-68 OVERHAUL
10.Position body of tool LRT-12-013 in vice.
11.Screw large nut back until flush with end of
centre screw.
12.Push centre screw forward until nut contacts
thrust race.
13.Position remover/replacer LRT-12-126/2 in
LRT-12-013 with its long spigot inside bore of
hexagon body.
14.Locate piston and connecting rod assembly on
centre screw and up to remover/replacer
adapter tool LRT-12-126/2.
CAUTION: Ensure that prongs of remover/
replacer adapter LRT-12-162/2 remain in
contact with piston and do not contact
gudgeon pin.
15.Fit remover/replacer bush LRT-12-126/1 on
centre screw with flanged end facing away from
gudgeon pin.
CAUTION: Ensure that remover/replacer
bush LRT-12-126/1 is correctly located in
gudgeon pin bore of piston.
16.Screw stop nut onto centre screw.
17.Lock the stop nut securely with the lock screw.
18.Push connecting rod to locate end of gudgeon
pin in remover/replacer adapter LRT-12-126/2.
19.Ensure remover/replacer bush LRT-12-126/1
is located in gudgeon pin bore of piston.
20.Screw large nut up to tool LRT-12-013.
21.Hold lock screw and turn large nut until
gudgeon pin is withdrawn from piston.
CAUTION: Ensure that prongs of tool LRT-
12–126/2 remain in contact with piston and
do not contact the gudgeon pin.
22.Dismantle tool LRT-12-013 and remove piston,
connecting rod and gudgeon pin. Inspect
1.Clean carbon from piston. Inspect piston for
distortion, cracks and burning.
2.Remove piston rings from piston.
3.Measure and record piston diameter at 90° to
gudgeon pin axis and 10 mm (0.4 in) from
bottom of the skirt. The piston must be 0.015 to
0.045 mm (0.001 to 0.002 in) smaller than the
cylinder bore.
4.Check gudgeon pin bore in piston for signs of
wear and overheating.
5.Pistons fitted on production are graded 'A' or
'B', the grade letter is stamped on the piston
crown.
lPiston diameter: Grade 'A' = 93.970 to
93.985 mm (3.6996 to 3.7002 in).
lPiston diameter: Grade 'B' = 93.986 to 94.00
mm (3.7002 to 3.7007 in).
6.Worn cylinders fitted with grade 'A' pistons may
be honed to accept the grade 'B' piston
provided that specified cylinder bore and
ovality limits are maintained. Grade 'B'
pistons are supplied as service
replacements. Do not attempt to de-glaze
cylinder bores.
CAUTION: Ensure replacement pistons are
correct for the compression ratio of the
engine. The compression ratio will be found
on the cylinder block adjacent to the engine
serial number.
7.Check gudgeon pins for signs of wear and
overheating.
8.Check clearance of gudgeon pin in piston.
l Gudgeon pin to piston clearance = 0.006 to
0.015 mm (0.0002 to 0.0006 in).
Page 225 of 1529
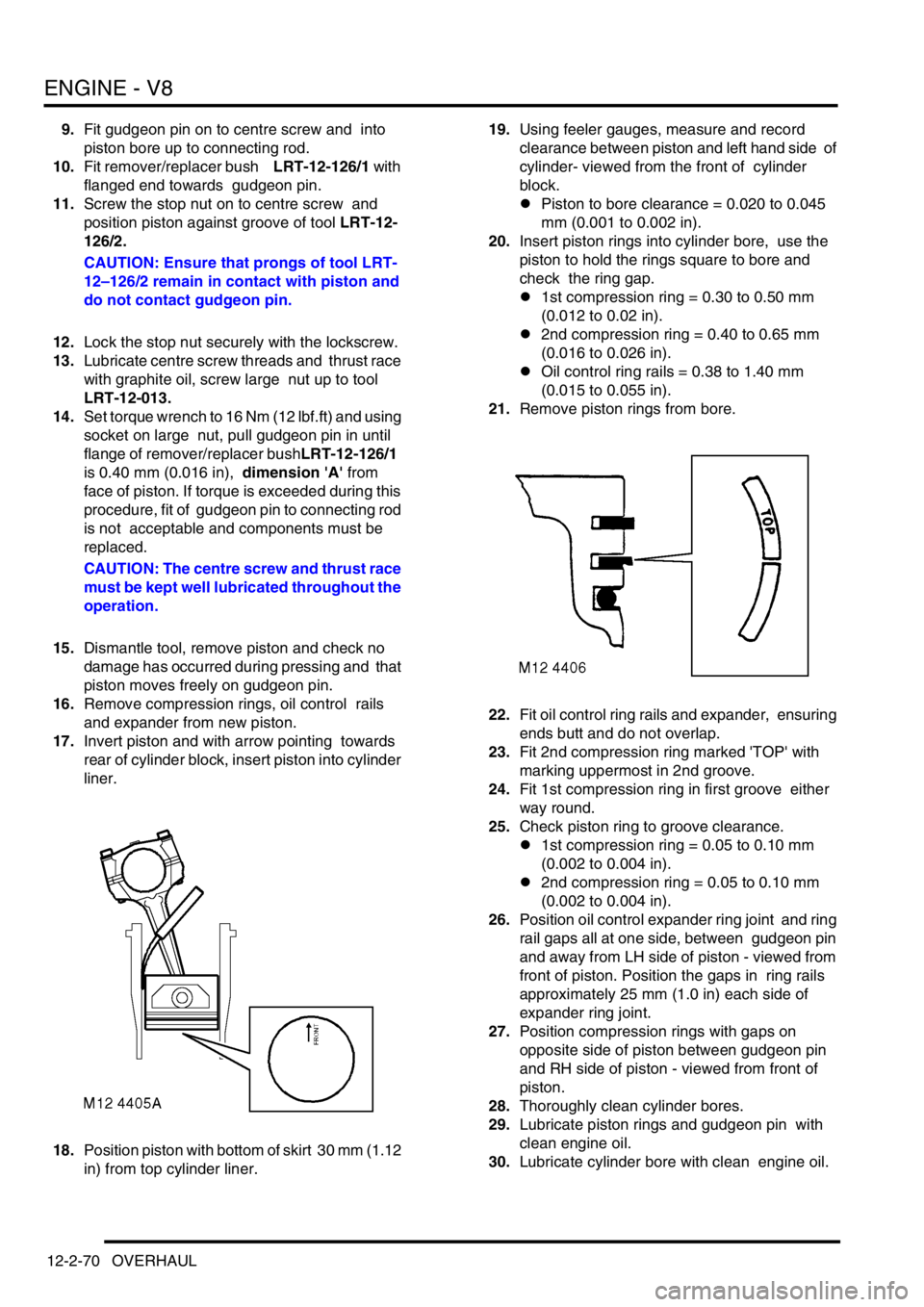
ENGINE - V8
12-2-70 OVERHAUL
9.Fit gudgeon pin on to centre screw and into
piston bore up to connecting rod.
10.Fit remover/replacer bush LRT-12-126/1 with
flanged end towards gudgeon pin.
11.Screw the stop nut on to centre screw and
position piston against groove of tool LRT-12-
126/2.
CAUTION: Ensure that prongs of tool LRT-
12–126/2 remain in contact with piston and
do not contact gudgeon pin.
12.Lock the stop nut securely with the lockscrew.
13.Lubricate centre screw threads and thrust race
with graphite oil, screw large nut up to tool
LRT-12-013.
14.Set torque wrench to 16 Nm (12 lbf.ft) and using
socket on large nut, pull gudgeon pin in until
flange of remover/replacer bushLRT-12-126/1
is 0.40 mm (0.016 in), dimension 'A' from
face of piston. If torque is exceeded during this
procedure, fit of gudgeon pin to connecting rod
is not acceptable and components must be
replaced.
CAUTION: The centre screw and thrust race
must be kept well lubricated throughout the
operation.
15.Dismantle tool, remove piston and check no
damage has occurred during pressing and that
piston moves freely on gudgeon pin.
16.Remove compression rings, oil control rails
and expander from new piston.
17.Invert piston and with arrow pointing towards
rear of cylinder block, insert piston into cylinder
liner.
18.Position piston with bottom of skirt 30 mm (1.12
in) from top cylinder liner. 19.Using feeler gauges, measure and record
clearance between piston and left hand side of
cylinder- viewed from the front of cylinder
block.
lPiston to bore clearance = 0.020 to 0.045
mm (0.001 to 0.002 in).
20.Insert piston rings into cylinder bore, use the
piston to hold the rings square to bore and
check the ring gap.
l1st compression ring = 0.30 to 0.50 mm
(0.012 to 0.02 in).
l2nd compression ring = 0.40 to 0.65 mm
(0.016 to 0.026 in).
lOil control ring rails = 0.38 to 1.40 mm
(0.015 to 0.055 in).
21.Remove piston rings from bore.
22.Fit oil control ring rails and expander, ensuring
ends butt and do not overlap.
23.Fit 2nd compression ring marked 'TOP' with
marking uppermost in 2nd groove.
24.Fit 1st compression ring in first groove either
way round.
25.Check piston ring to groove clearance.
l1st compression ring = 0.05 to 0.10 mm
(0.002 to 0.004 in).
l2nd compression ring = 0.05 to 0.10 mm
(0.002 to 0.004 in).
26.Position oil control expander ring joint and ring
rail gaps all at one side, between gudgeon pin
and away from LH side of piston - viewed from
front of piston. Position the gaps in ring rails
approximately 25 mm (1.0 in) each side of
expander ring joint.
27.Position compression rings with gaps on
opposite side of piston between gudgeon pin
and RH side of piston - viewed from front of
piston.
28.Thoroughly clean cylinder bores.
29.Lubricate piston rings and gudgeon pin with
clean engine oil.
30.Lubricate cylinder bore with clean engine oil.
Page 463 of 1529
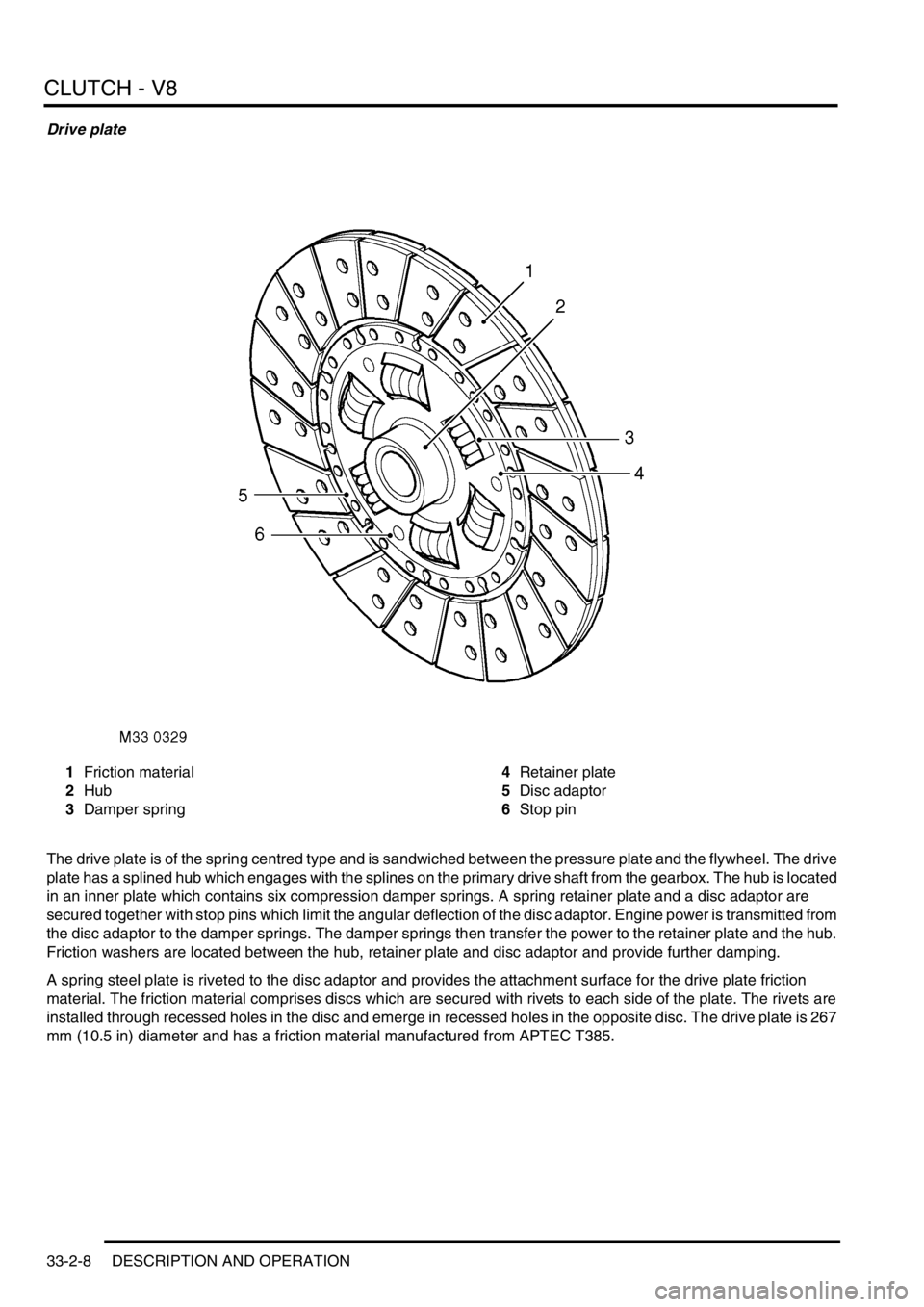
CLUTCH - V8
33-2-8 DESCRIPTION AND OPERATION
Drive plate
1Friction material
2Hub
3Damper spring4Retainer plate
5Disc adaptor
6Stop pin
The drive plate is of the spring centred type and is sandwiched between the pressure plate and the flywheel. The drive
plate has a splined hub which engages with the splines on the primary drive shaft from the gearbox. The hub is located
in an inner plate which contains six compression damper springs. A spring retainer plate and a disc adaptor are
secured together with stop pins which limit the angular deflection of the disc adaptor. Engine power is transmitted from
the disc adaptor to the damper springs. The damper springs then transfer the power to the retainer plate and the hub.
Friction washers are located between the hub, retainer plate and disc adaptor and provide further damping.
A spring steel plate is riveted to the disc adaptor and provides the attachment surface for the drive plate friction
material. The friction material comprises discs which are secured with rivets to each side of the plate. The rivets are
installed through recessed holes in the disc and emerge in recessed holes in the opposite disc. The drive plate is 267
mm (10.5 in) diameter and has a friction material manufactured from APTEC T385.
Page 749 of 1529
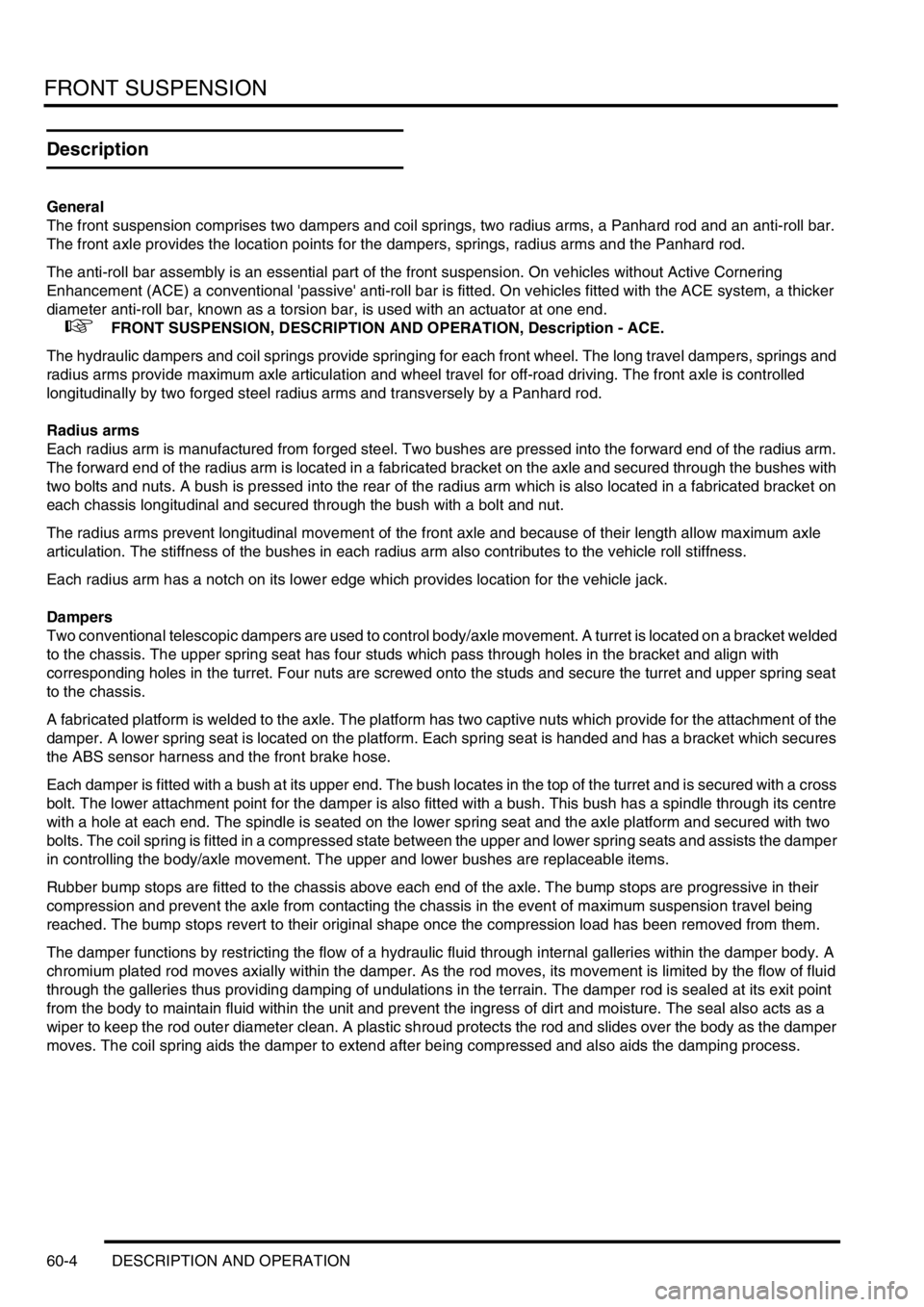
FRONT SUSPENSION
60-4 DESCRIPTION AND OPERATION
Description
General
The front suspension comprises two dampers and coil springs, two radius arms, a Panhard rod and an anti-roll bar.
The front axle provides the location points for the dampers, springs, radius arms and the Panhard rod.
The anti-roll bar assembly is an essential part of the front suspension. On vehicles without Active Cornering
Enhancement (ACE) a conventional 'passive' anti-roll bar is fitted. On vehicles fitted with the ACE system, a thicker
diameter anti-roll bar, known as a torsion bar, is used with an actuator at one end.
+ FRONT SUSPENSION, DESCRIPTION AND OPERATION, Description - ACE.
The hydraulic dampers and coil springs provide springing for each front wheel. The long travel dampers, springs and
radius arms provide maximum axle articulation and wheel travel for off-road driving. The front axle is controlled
longitudinally by two forged steel radius arms and transversely by a Panhard rod.
Radius arms
Each radius arm is manufactured from forged steel. Two bushes are pressed into the forward end of the radius arm.
The forward end of the radius arm is located in a fabricated bracket on the axle and secured through the bushes with
two bolts and nuts. A bush is pressed into the rear of the radius arm which is also located in a fabricated bracket on
each chassis longitudinal and secured through the bush with a bolt and nut.
The radius arms prevent longitudinal movement of the front axle and because of their length allow maximum axle
articulation. The stiffness of the bushes in each radius arm also contributes to the vehicle roll stiffness.
Each radius arm has a notch on its lower edge which provides location for the vehicle jack.
Dampers
Two conventional telescopic dampers are used to control body/axle movement. A turret is located on a bracket welded
to the chassis. The upper spring seat has four studs which pass through holes in the bracket and align with
corresponding holes in the turret. Four nuts are screwed onto the studs and secure the turret and upper spring seat
to the chassis.
A fabricated platform is welded to the axle. The platform has two captive nuts which provide for the attachment of the
damper. A lower spring seat is located on the platform. Each spring seat is handed and has a bracket which secures
the ABS sensor harness and the front brake hose.
Each damper is fitted with a bush at its upper end. The bush locates in the top of the turret and is secured with a cross
bolt. The lower attachment point for the damper is also fitted with a bush. This bush has a spindle through its centre
with a hole at each end. The spindle is seated on the lower spring seat and the axle platform and secured with two
bolts. The coil spring is fitted in a compressed state between the upper and lower spring seats and assists the damper
in controlling the body/axle movement. The upper and lower bushes are replaceable items.
Rubber bump stops are fitted to the chassis above each end of the axle. The bump stops are progressive in their
compression and prevent the axle from contacting the chassis in the event of maximum suspension travel being
reached. The bump stops revert to their original shape once the compression load has been removed from them.
The damper functions by restricting the flow of a hydraulic fluid through internal galleries within the damper body. A
chromium plated rod moves axially within the damper. As the rod moves, its movement is limited by the flow of fluid
through the galleries thus providing damping of undulations in the terrain. The damper rod is sealed at its exit point
from the body to maintain fluid within the unit and prevent the ingress of dirt and moisture. The seal also acts as a
wiper to keep the rod outer diameter clean. A plastic shroud protects the rod and slides over the body as the damper
moves. The coil spring aids the damper to extend after being compressed and also aids the damping process.