boot LAND ROVER DISCOVERY 2002 Workshop Manual
[x] Cancel search | Manufacturer: LAND ROVER, Model Year: 2002, Model line: DISCOVERY, Model: LAND ROVER DISCOVERY 2002Pages: 1672, PDF Size: 46.1 MB
Page 59 of 1672
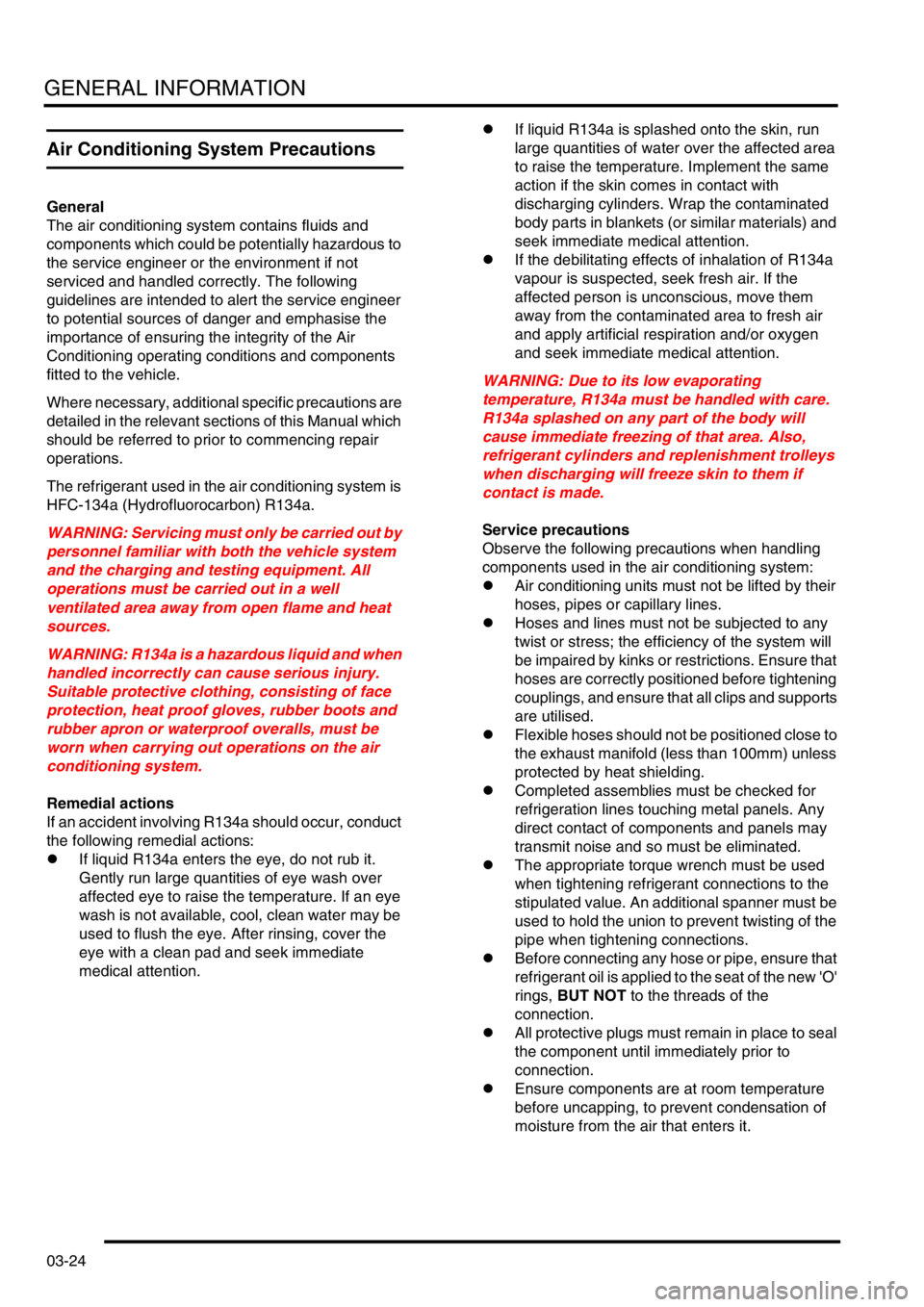
GENERAL INFORMATION
03-24
Air Conditioning System Precautions
General
The air conditioning system contains fluids and
components which could be potentially hazardous to
the service engineer or the environment if not
serviced and handled correctly. The following
guidelines are intended to alert the service engineer
to potential sources of danger and emphasise the
importance of ensuring the integrity of the Air
Conditioning operating conditions and components
fitted to the vehicle.
Where necessary, additional specific precautions are
detailed in the relevant sections of this Manual which
should be referred to prior to commencing repair
operations.
The refrigerant used in the air conditioning system is
HFC-134a (Hydrofluorocarbon) R134a.
WARNING: Servicing must only be carried out by
personnel familiar with both the vehicle system
and the charging and testing equipment. All
operations must be carried out in a well
ventilated area away from open flame and heat
sources.
WARNING: R134a is a hazardous liquid and when
handled incorrectly can cause serious injury.
Suitable protective clothing, consisting of face
protection, heat proof gloves, rubber boots and
rubber apron or waterproof overalls, must be
worn when carrying out operations on the air
conditioning system.
Remedial actions
If an accident involving R134a should occur, conduct
the following remedial actions:
lIf liquid R134a enters the eye, do not rub it.
Gently run large quantities of eye wash over
affected eye to raise the temperature. If an eye
wash is not available, cool, clean water may be
used to flush the eye. After rinsing, cover the
eye with a clean pad and seek immediate
medical attention.lIf liquid R134a is splashed onto the skin, run
large quantities of water over the affected area
to raise the temperature. Implement the same
action if the skin comes in contact with
discharging cylinders. Wrap the contaminated
body parts in blankets (or similar materials) and
seek immediate medical attention.
lIf the debilitating effects of inhalation of R134a
vapour is suspected, seek fresh air. If the
affected person is unconscious, move them
away from the contaminated area to fresh air
and apply artificial respiration and/or oxygen
and seek immediate medical attention.
WARNING: Due to its low evaporating
temperature, R134a must be handled with care.
R134a splashed on any part of the body will
cause immediate freezing of that area. Also,
refrigerant cylinders and replenishment trolleys
when discharging will freeze skin to them if
contact is made.
Service precautions
Observe the following precautions when handling
components used in the air conditioning system:
lAir conditioning units must not be lifted by their
hoses, pipes or capillary lines.
lHoses and lines must not be subjected to any
twist or stress; the efficiency of the system will
be impaired by kinks or restrictions. Ensure that
hoses are correctly positioned before tightening
couplings, and ensure that all clips and supports
are utilised.
lFlexible hoses should not be positioned close to
the exhaust manifold (less than 100mm) unless
protected by heat shielding.
lCompleted assemblies must be checked for
refrigeration lines touching metal panels. Any
direct contact of components and panels may
transmit noise and so must be eliminated.
lThe appropriate torque wrench must be used
when tightening refrigerant connections to the
stipulated value. An additional spanner must be
used to hold the union to prevent twisting of the
pipe when tightening connections.
lBefore connecting any hose or pipe, ensure that
refrigerant oil is applied to the seat of the new 'O'
rings, BUT NOT to the threads of the
connection.
lAll protective plugs must remain in place to seal
the component until immediately prior to
connection.
lEnsure components are at room temperature
before uncapping, to prevent condensation of
moisture from the air that enters it.
Page 129 of 1672
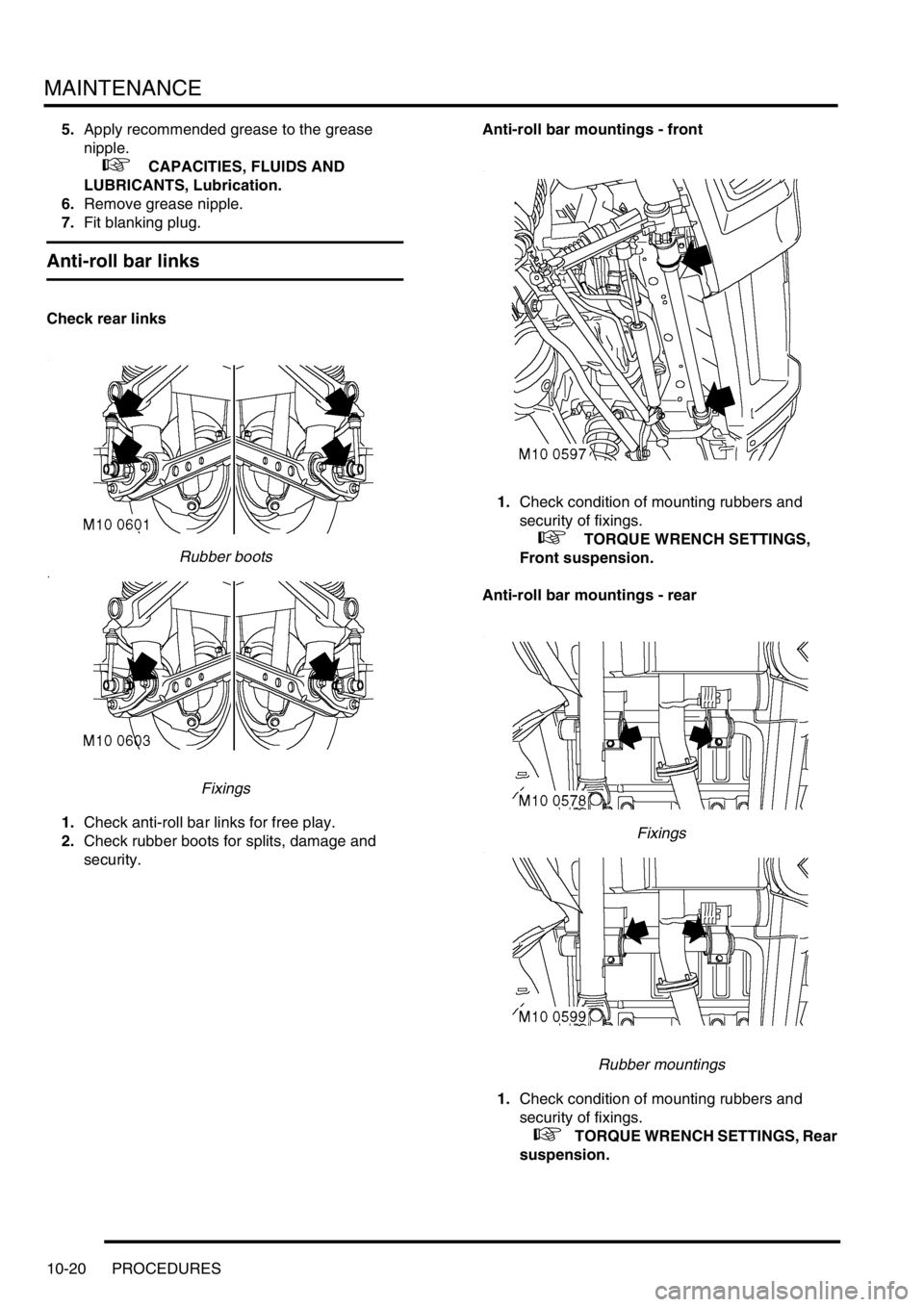
MAINTENANCE
10-20 PROCEDURES
5.Apply recommended grease to the grease
nipple.
+ CAPACITIES, FLUIDS AND
LUBRICANTS, Lubrication.
6.Remove grease nipple.
7.Fit blanking plug.
Anti-roll bar links
Check rear links
Rubber boots
Fixings
1.Check anti-roll bar links for free play.
2.Check rubber boots for splits, damage and
security.Anti-roll bar mountings - front
1.Check condition of mounting rubbers and
security of fixings.
+ TORQUE WRENCH SETTINGS,
Front suspension.
Anti-roll bar mountings - rear
Fixings
Rubber mountings
1.Check condition of mounting rubbers and
security of fixings.
+ TORQUE WRENCH SETTINGS, Rear
suspension.
Page 130 of 1672
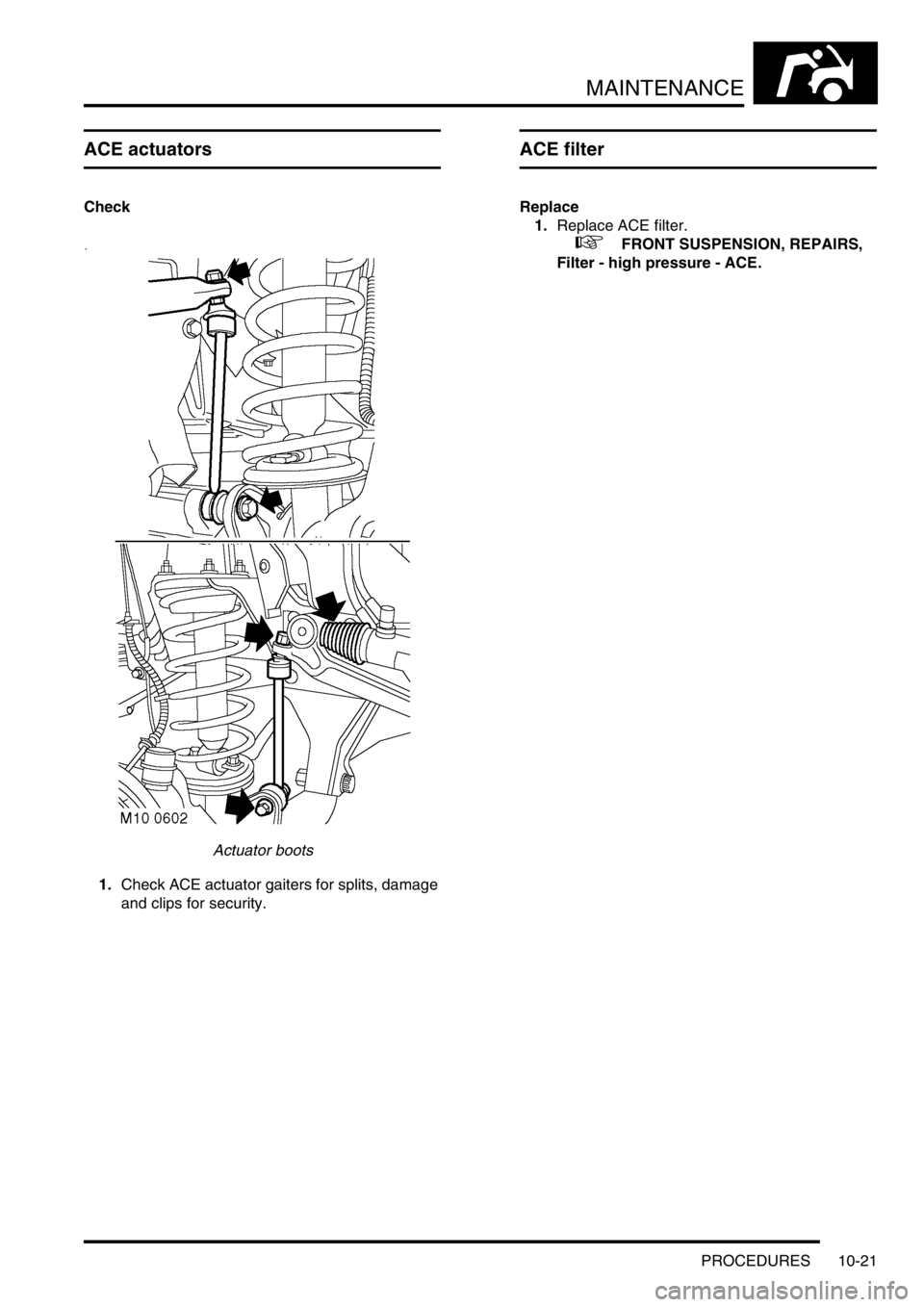
MAINTENANCE
PROCEDURES 10-21
ACE actuators
Check
Actuator boots
1.Check ACE actuator gaiters for splits, damage
and clips for security.
ACE filter
Replace
1.Replace ACE filter.
+ FRONT SUSPENSION, REPAIRS,
Filter - high pressure - ACE.
Page 327 of 1672
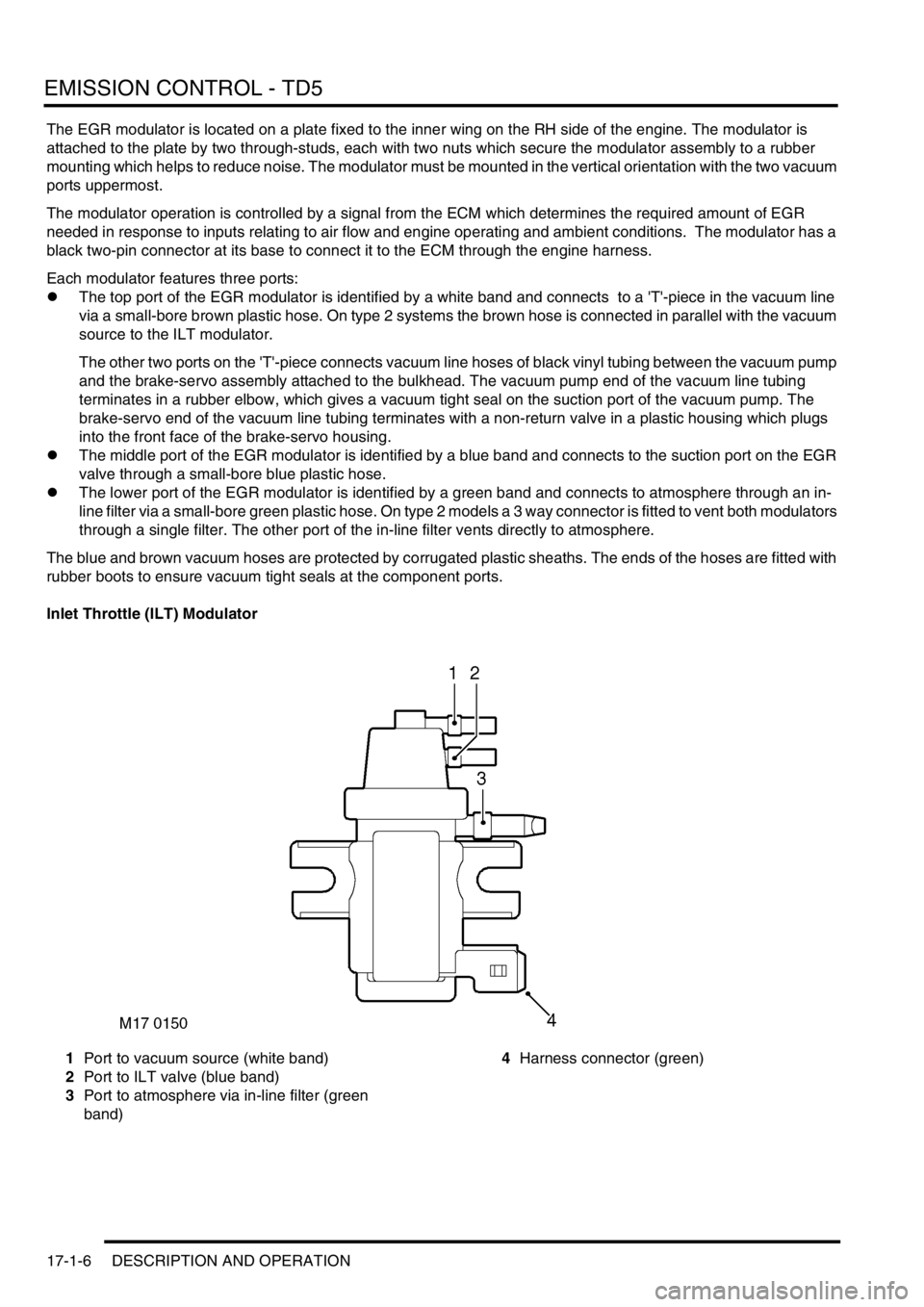
EMISSION CONTROL - TD5
17-1-6 DESCRIPTION AND OPERATION
The EGR modulator is located on a plate fixed to the inner wing on the RH side of the engine. The modulator is
attached to the plate by two through-studs, each with two nuts which secure the modulator assembly to a rubber
mounting which helps to reduce noise. The modulator must be mounted in the vertical orientation with the two vacuum
ports uppermost.
The modulator operation is controlled by a signal from the ECM which determines the required amount of EGR
needed in response to inputs relating to air flow and engine operating and ambient conditions. The modulator has a
black two-pin connector at its base to connect it to the ECM through the engine harness.
Each modulator features three ports:
lThe top port of the EGR modulator is identified by a white band and connects to a 'T'-piece in the vacuum line
via a small-bore brown plastic hose. On type 2 systems the brown hose is connected in parallel with the vacuum
source to the ILT modulator.
The other two ports on the 'T'-piece connects vacuum line hoses of black vinyl tubing between the vacuum pump
and the brake-servo assembly attached to the bulkhead. The vacuum pump end of the vacuum line tubing
terminates in a rubber elbow, which gives a vacuum tight seal on the suction port of the vacuum pump. The
brake-servo end of the vacuum line tubing terminates with a non-return valve in a plastic housing which plugs
into the front face of the brake-servo housing.
lThe middle port of the EGR modulator is identified by a blue band and connects to the suction port on the EGR
valve through a small-bore blue plastic hose.
lThe lower port of the EGR modulator is identified by a green band and connects to atmosphere through an in-
line filter via a small-bore green plastic hose. On type 2 models a 3 way connector is fitted to vent both modulators
through a single filter. The other port of the in-line filter vents directly to atmosphere.
The blue and brown vacuum hoses are protected by corrugated plastic sheaths. The ends of the hoses are fitted with
rubber boots to ensure vacuum tight seals at the component ports.
Inlet Throttle (ILT) Modulator
1Port to vacuum source (white band)
2Port to ILT valve (blue band)
3Port to atmosphere via in-line filter (green
band)4Harness connector (green)
Page 328 of 1672
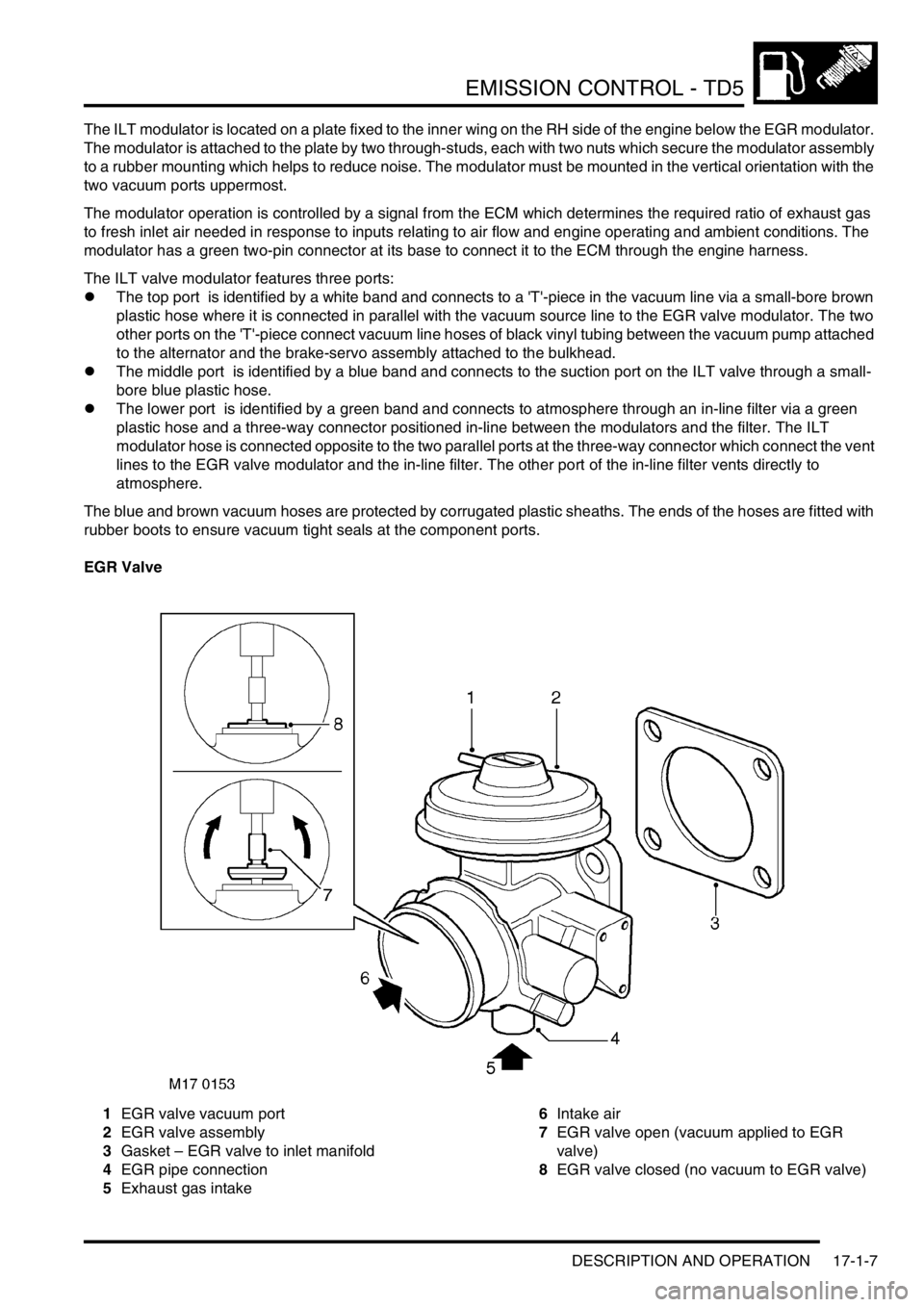
EMISSION CONTROL - TD5
DESCRIPTION AND OPERATION 17-1-7
The ILT modulator is located on a plate fixed to the inner wing on the RH side of the engine below the EGR modulator.
The modulator is attached to the plate by two through-studs, each with two nuts which secure the modulator assembly
to a rubber mounting which helps to reduce noise. The modulator must be mounted in the vertical orientation with the
two vacuum ports uppermost.
The modulator operation is controlled by a signal from the ECM which determines the required ratio of exhaust gas
to fresh inlet air needed in response to inputs relating to air flow and engine operating and ambient conditions. The
modulator has a green two-pin connector at its base to connect it to the ECM through the engine harness.
The ILT valve modulator features three ports:
lThe top port is identified by a white band and connects to a 'T'-piece in the vacuum line via a small-bore brown
plastic hose where it is connected in parallel with the vacuum source line to the EGR valve modulator. The two
other ports on the 'T'-piece connect vacuum line hoses of black vinyl tubing between the vacuum pump attached
to the alternator and the brake-servo assembly attached to the bulkhead.
lThe middle port is identified by a blue band and connects to the suction port on the ILT valve through a small-
bore blue plastic hose.
lThe lower port is identified by a green band and connects to atmosphere through an in-line filter via a green
plastic hose and a three-way connector positioned in-line between the modulators and the filter. The ILT
modulator hose is connected opposite to the two parallel ports at the three-way connector which connect the vent
lines to the EGR valve modulator and the in-line filter. The other port of the in-line filter vents directly to
atmosphere.
The blue and brown vacuum hoses are protected by corrugated plastic sheaths. The ends of the hoses are fitted with
rubber boots to ensure vacuum tight seals at the component ports.
EGR Valve
1EGR valve vacuum port
2EGR valve assembly
3Gasket – EGR valve to inlet manifold
4EGR pipe connection
5Exhaust gas intake6Intake air
7EGR valve open (vacuum applied to EGR
valve)
8EGR valve closed (no vacuum to EGR valve)
Page 359 of 1672
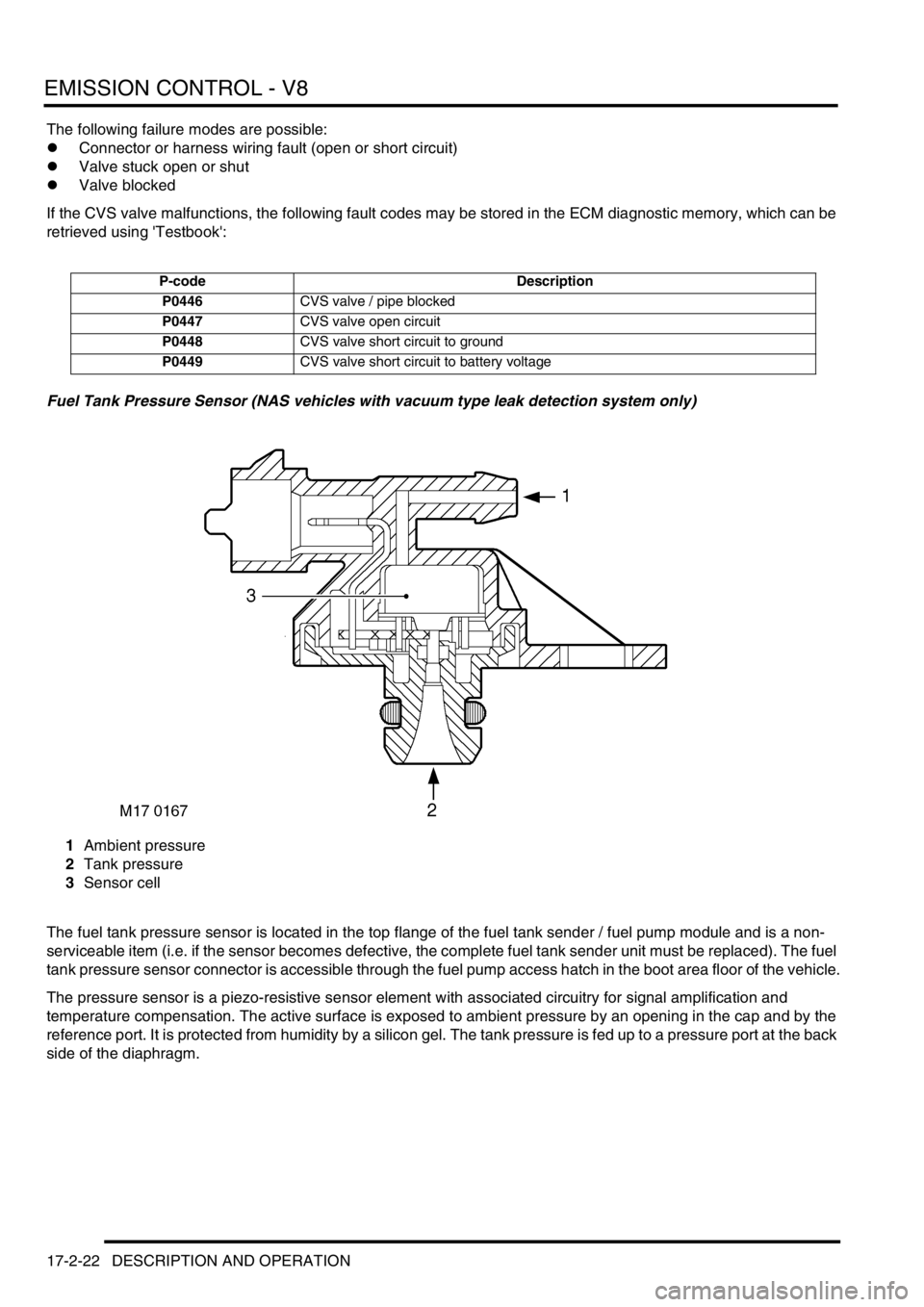
EMISSION CONTROL - V8
17-2-22 DESCRIPTION AND OPERATION
The following failure modes are possible:
lConnector or harness wiring fault (open or short circuit)
lValve stuck open or shut
lValve blocked
If the CVS valve malfunctions, the following fault codes may be stored in the ECM diagnostic memory, which can be
retrieved using 'Testbook':
Fuel Tank Pressure Sensor (NAS vehicles with vacuum type leak detection system only)
1Ambient pressure
2Tank pressure
3Sensor cell
The fuel tank pressure sensor is located in the top flange of the fuel tank sender / fuel pump module and is a non-
serviceable item (i.e. if the sensor becomes defective, the complete fuel tank sender unit must be replaced). The fuel
tank pressure sensor connector is accessible through the fuel pump access hatch in the boot area floor of the vehicle.
The pressure sensor is a piezo-resistive sensor element with associated circuitry for signal amplification and
temperature compensation. The active surface is exposed to ambient pressure by an opening in the cap and by the
reference port. It is protected from humidity by a silicon gel. The tank pressure is fed up to a pressure port at the back
side of the diaphragm.
P-code Description
P0446CVS valve / pipe blocked
P0447CVS valve open circuit
P0448CVS valve short circuit to ground
P0449CVS valve short circuit to battery voltage
Page 692 of 1672
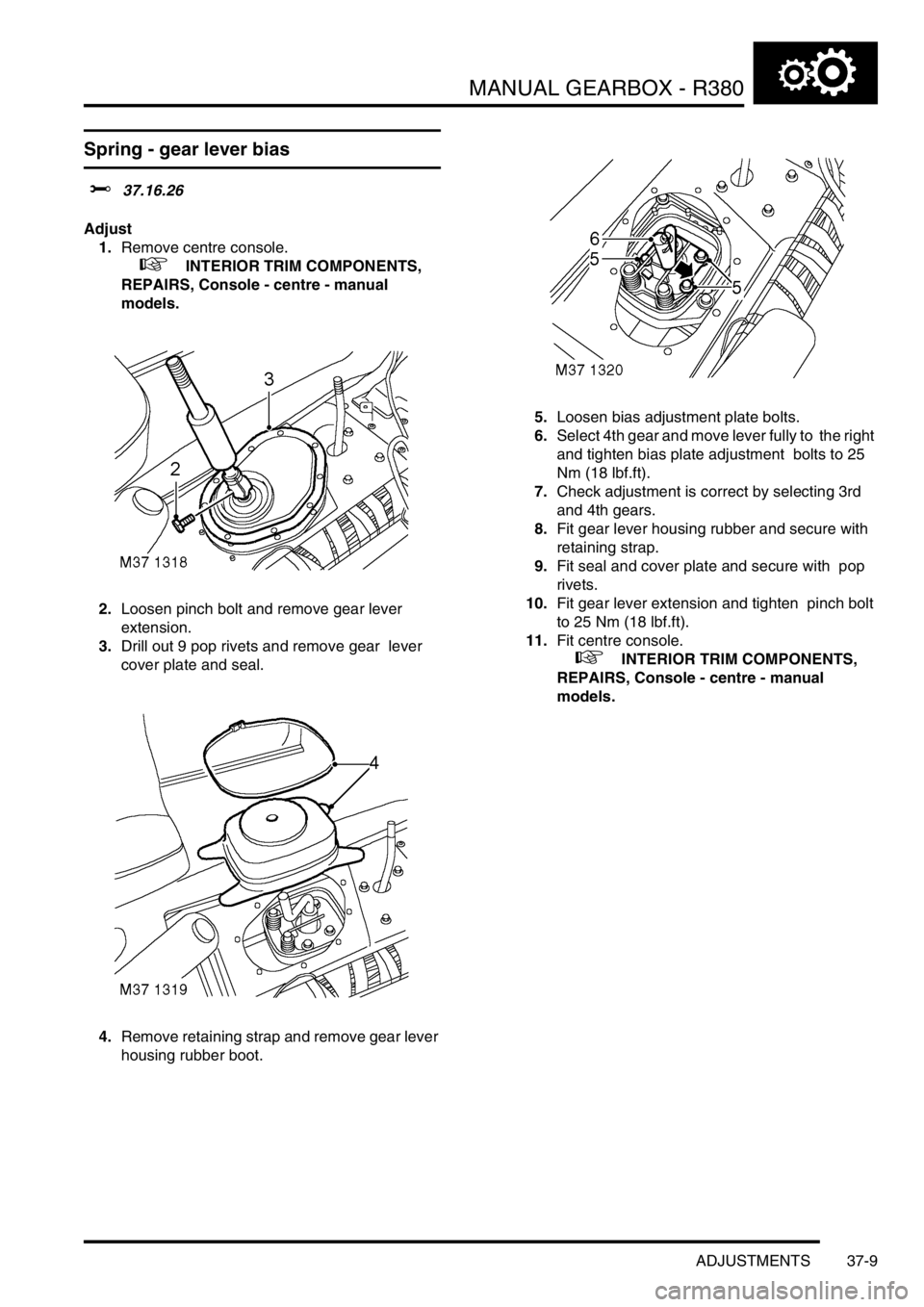
MANUAL GEARBOX - R380
ADJUSTMENTS 37-9
ADJUST ME NTS
Spring - gear lever bias
$% 37.16.26
Adjust
1.Remove centre console.
+ INTERIOR TRIM COMPONENTS,
REPAIRS, Console - centre - manual
models.
2.Loosen pinch bolt and remove gear lever
extension.
3.Drill out 9 pop rivets and remove gear lever
cover plate and seal.
4.Remove retaining strap and remove gear lever
housing rubber boot.5.Loosen bias adjustment plate bolts.
6.Select 4th gear and move lever fully to the right
and tighten bias plate adjustment bolts to 25
Nm (18 lbf.ft).
7.Check adjustment is correct by selecting 3rd
and 4th gears.
8.Fit gear lever housing rubber and secure with
retaining strap.
9.Fit seal and cover plate and secure with pop
rivets.
10.Fit gear lever extension and tighten pinch bolt
to 25 Nm (18 lbf.ft).
11.Fit centre console.
+ INTERIOR TRIM COMPONENTS,
REPAIRS, Console - centre - manual
models.
Page 694 of 1672
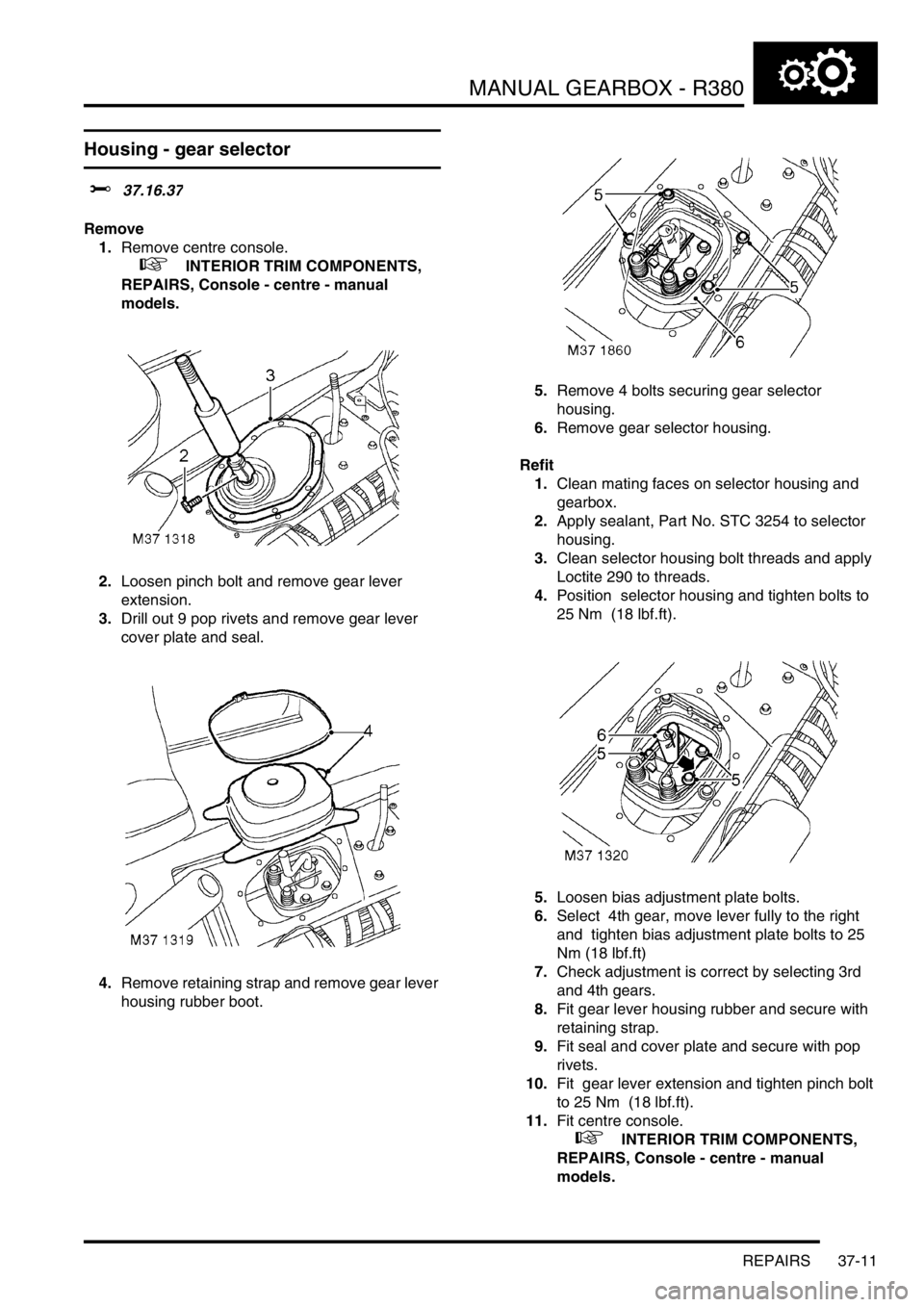
MANUAL GEARBOX - R380
REPAIRS 37-11
REPAIRS
Housing - gear selector
$% 37.16.37
Remove
1.Remove centre console.
+ INTERIOR TRIM COMPONENTS,
REPAIRS, Console - centre - manual
models.
2.Loosen pinch bolt and remove gear lever
extension.
3.Drill out 9 pop rivets and remove gear lever
cover plate and seal.
4.Remove retaining strap and remove gear lever
housing rubber boot.5.Remove 4 bolts securing gear selector
housing.
6.Remove gear selector housing.
Refit
1.Clean mating faces on selector housing and
gearbox.
2.Apply sealant, Part No. STC 3254 to selector
housing.
3.Clean selector housing bolt threads and apply
Loctite 290 to threads.
4.Position selector housing and tighten bolts to
25 Nm (18 lbf.ft).
5.Loosen bias adjustment plate bolts.
6.Select 4th gear, move lever fully to the right
and tighten bias adjustment plate bolts to 25
Nm (18 lbf.ft)
7.Check adjustment is correct by selecting 3rd
and 4th gears.
8.Fit gear lever housing rubber and secure with
retaining strap.
9.Fit seal and cover plate and secure with pop
rivets.
10.Fit gear lever extension and tighten pinch bolt
to 25 Nm (18 lbf.ft).
11.Fit centre console.
+ INTERIOR TRIM COMPONENTS,
REPAIRS, Console - centre - manual
models.
Page 930 of 1672
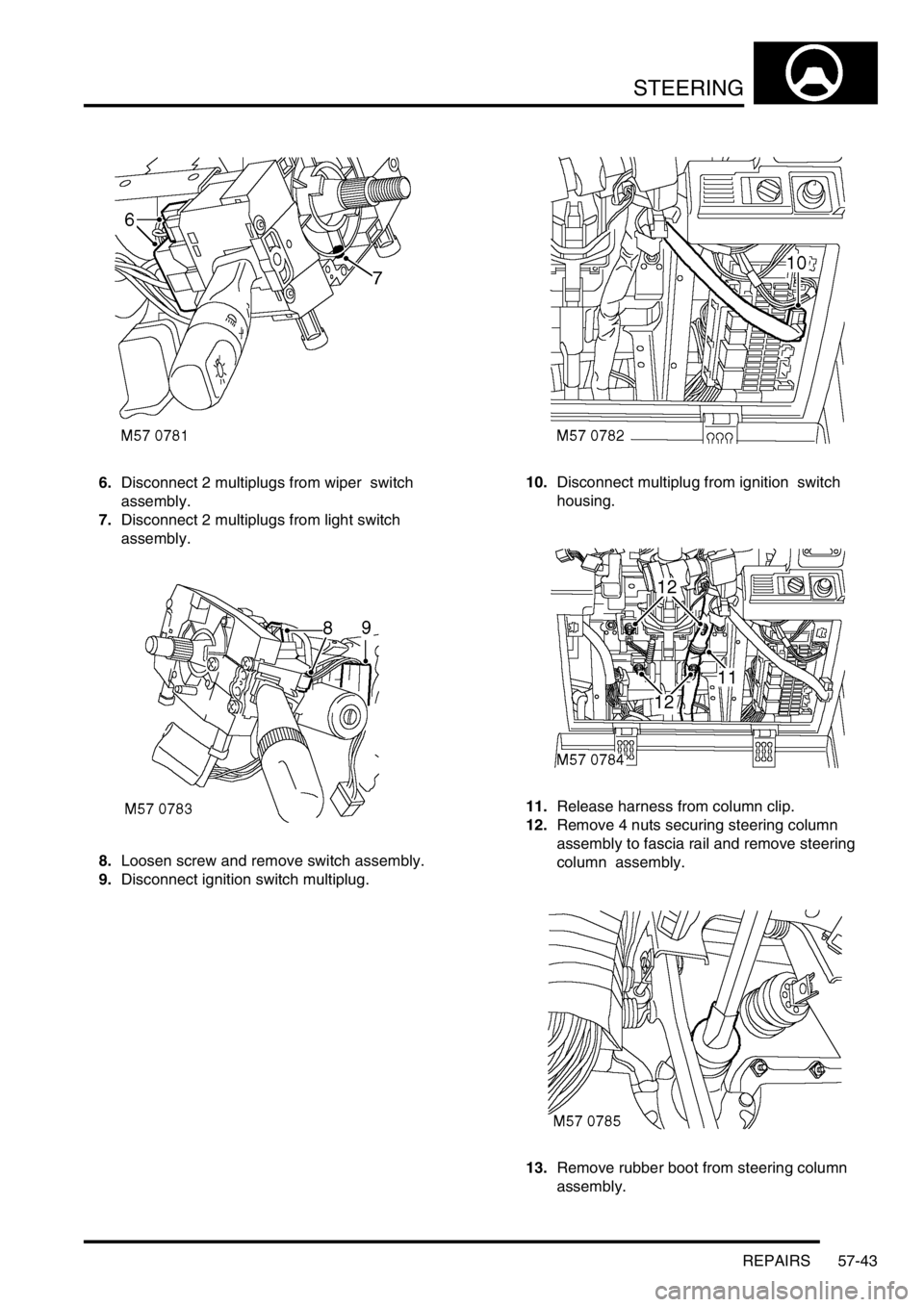
STEERING
REPAIRS 57-43
6.Disconnect 2 multiplugs from wiper switch
assembly.
7.Disconnect 2 multiplugs from light switch
assembly.
8.Loosen screw and remove switch assembly.
9.Disconnect ignition switch multiplug. 10.Disconnect multiplug from ignition switch
housing.
11.Release harness from column clip.
12.Remove 4 nuts securing steering column
assembly to fascia rail and remove steering
column assembly.
13.Remove rubber boot from steering column
assembly.
Page 931 of 1672
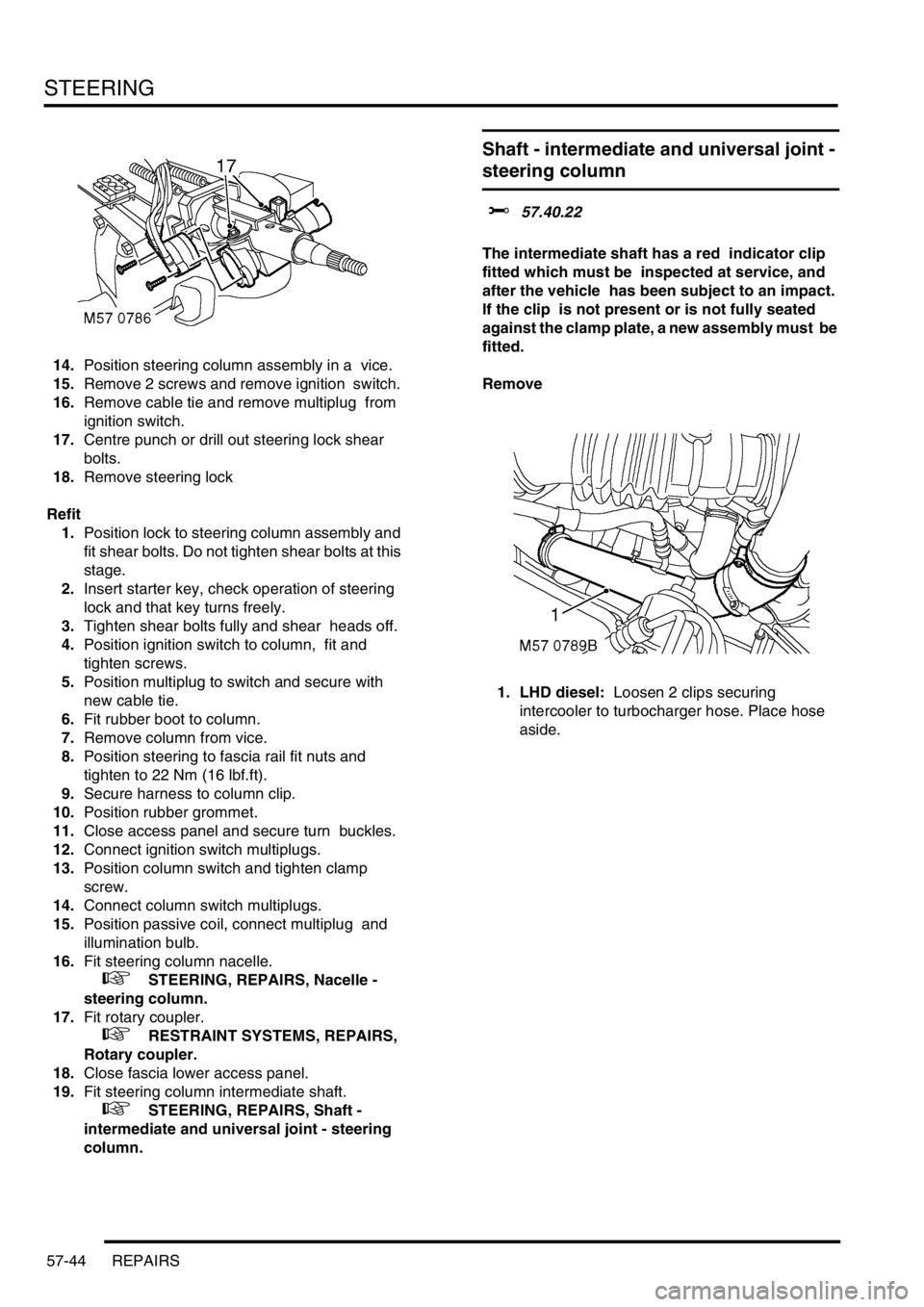
STEERING
57-44 REPAIRS
14.Position steering column assembly in a vice.
15.Remove 2 screws and remove ignition switch.
16.Remove cable tie and remove multiplug from
ignition switch.
17.Centre punch or drill out steering lock shear
bolts.
18.Remove steering lock
Refit
1.Position lock to steering column assembly and
fit shear bolts. Do not tighten shear bolts at this
stage.
2.Insert starter key, check operation of steering
lock and that key turns freely.
3.Tighten shear bolts fully and shear heads off.
4.Position ignition switch to column, fit and
tighten screws.
5.Position multiplug to switch and secure with
new cable tie.
6.Fit rubber boot to column.
7.Remove column from vice.
8.Position steering to fascia rail fit nuts and
tighten to 22 Nm (16 lbf.ft).
9.Secure harness to column clip.
10.Position rubber grommet.
11.Close access panel and secure turn buckles.
12.Connect ignition switch multiplugs.
13.Position column switch and tighten clamp
screw.
14.Connect column switch multiplugs.
15.Position passive coil, connect multiplug and
illumination bulb.
16.Fit steering column nacelle.
+ STEERING, REPAIRS, Nacelle -
steering column.
17.Fit rotary coupler.
+ RESTRAINT SYSTEMS, REPAIRS,
Rotary coupler.
18.Close fascia lower access panel.
19.Fit steering column intermediate shaft.
+ STEERING, REPAIRS, Shaft -
intermediate and universal joint - steering
column.
Shaft - intermediate and universal joint -
steering column
$% 57.40.22
The intermediate shaft has a red indicator clip
fitted which must be inspected at service, and
after the vehicle has been subject to an impact.
If the clip is not present or is not fully seated
against the clamp plate, a new assembly must be
fitted.
Remove
1. LHD diesel: Loosen 2 clips securing
intercooler to turbocharger hose. Place hose
aside.