lights LAND ROVER DISCOVERY 2002 Workshop Manual
[x] Cancel search | Manufacturer: LAND ROVER, Model Year: 2002, Model line: DISCOVERY, Model: LAND ROVER DISCOVERY 2002Pages: 1672, PDF Size: 46.1 MB
Page 26 of 1672
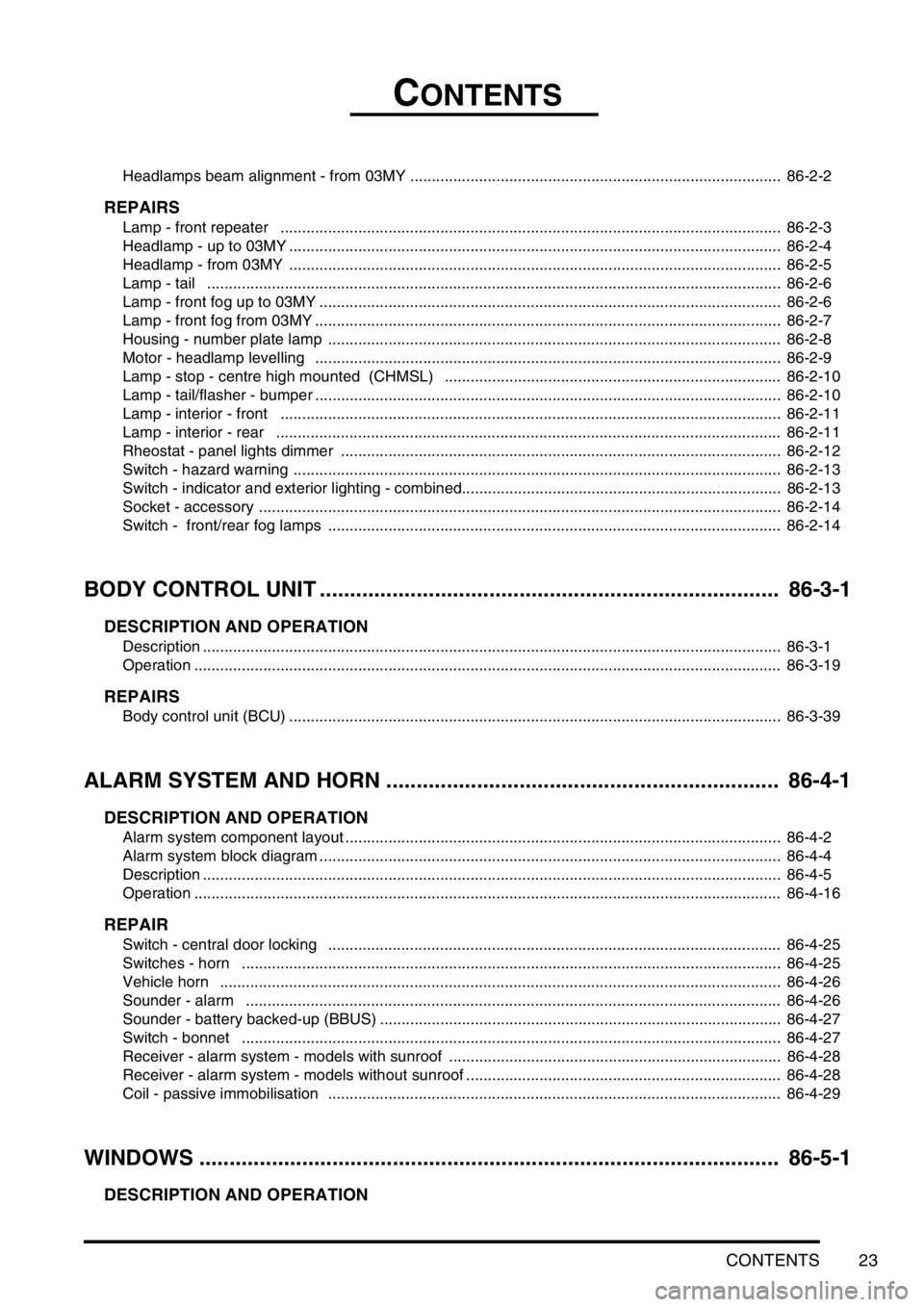
CONTENTS
CONTENTS 23
Headlamps beam alignment - from 03MY ...................................................................................... 86-2-2
REPAIRS
Lamp - front repeater .................................................................................................................... 86-2-3
Headlamp - up to 03MY .................................................................................................................. 86-2-4
Headlamp - from 03MY .................................................................................................................. 86-2-5
Lamp - tail ..................................................................................................................................... 86-2-6
Lamp - front fog up to 03MY ........................................................................................................... 86-2-6
Lamp - front fog from 03MY ............................................................................................................ 86-2-7
Housing - number plate lamp ......................................................................................................... 86-2-8
Motor - headlamp levelling ............................................................................................................ 86-2-9
Lamp - stop - centre high mounted (CHMSL) .............................................................................. 86-2-10
Lamp - tail/flasher - bumper ............................................................................................................ 86-2-10
Lamp - interior - front .................................................................................................................... 86-2-11
Lamp - interior - rear ..................................................................................................................... 86-2-11
Rheostat - panel lights dimmer ...................................................................................................... 86-2-12
Switch - hazard warning ................................................................................................................. 86-2-13
Switch - indicator and exterior lighting - combined.......................................................................... 86-2-13
Socket - accessory ......................................................................................................................... 86-2-14
Switch - front/rear fog lamps ......................................................................................................... 86-2-14
BODY CONTROL UNIT ............................................................................ 86-3-1
DESCRIPTION AND OPERATION
Description ...................................................................................................................................... 86-3-1
Operation ........................................................................................................................................ 86-3-19
REPAIRS
Body control unit (BCU) .................................................................................................................. 86-3-39
ALARM SYSTEM AND HORN ................................................................. 86-4-1
DESCRIPTION AND OPERATION
Alarm system component layout ..................................................................................................... 86-4-2
Alarm system block diagram ........................................................................................................... 86-4-4
Description ...................................................................................................................................... 86-4-5
Operation ........................................................................................................................................ 86-4-16
REPAIR
Switch - central door locking ......................................................................................................... 86-4-25
Switches - horn ............................................................................................................................. 86-4-25
Vehicle horn .................................................................................................................................. 86-4-26
Sounder - alarm ............................................................................................................................ 86-4-26
Sounder - battery backed-up (BBUS) ............................................................................................. 86-4-27
Switch - bonnet ............................................................................................................................. 86-4-27
Receiver - alarm system - models with sunroof ............................................................................. 86-4-28
Receiver - alarm system - models without sunroof ......................................................................... 86-4-28
Coil - passive immobilisation ......................................................................................................... 86-4-29
WINDOWS ................................................................................................ 86-5-1
DESCRIPTION AND OPERATION
Page 40 of 1672
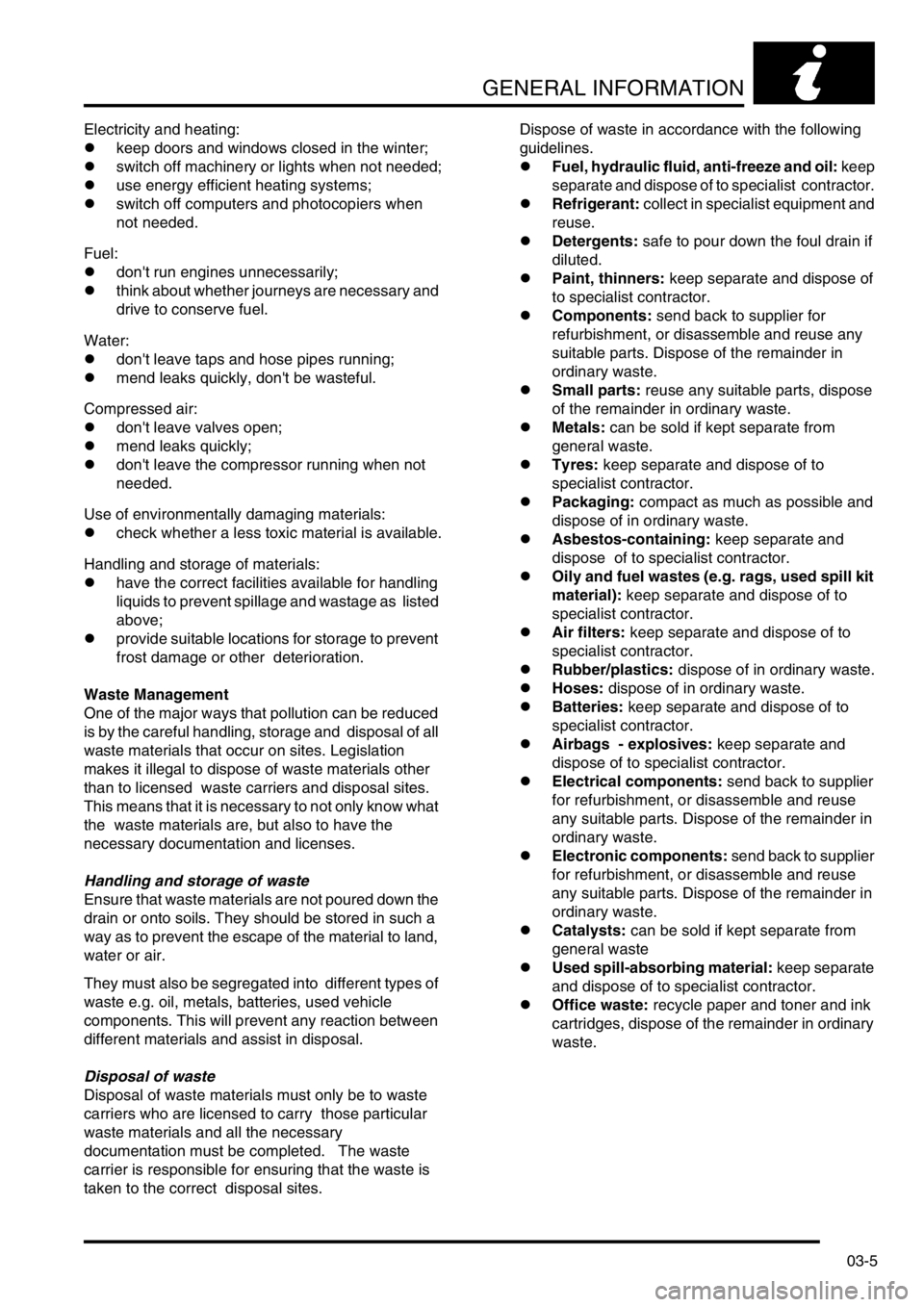
GENERAL INFORMATION
03-5
Electricity and heating:
lkeep doors and windows closed in the winter;
lswitch off machinery or lights when not needed;
luse energy efficient heating systems;
lswitch off computers and photocopiers when
not needed.
Fuel:
ldon't run engines unnecessarily;
lthink about whether journeys are necessary and
drive to conserve fuel.
Water:
ldon't leave taps and hose pipes running;
lmend leaks quickly, don't be wasteful.
Compressed air:
ldon't leave valves open;
lmend leaks quickly;
ldon't leave the compressor running when not
needed.
Use of environmentally damaging materials:
lcheck whether a less toxic material is available.
Handling and storage of materials:
lhave the correct facilities available for handling
liquids to prevent spillage and wastage as listed
above;
lprovide suitable locations for storage to prevent
frost damage or other deterioration.
Waste Management
One of the major ways that pollution can be reduced
is by the careful handling, storage and disposal of all
waste materials that occur on sites. Legislation
makes it illegal to dispose of waste materials other
than to licensed waste carriers and disposal sites.
This means that it is necessary to not only know what
the waste materials are, but also to have the
necessary documentation and licenses.
Handling and storage of waste
Ensure that waste materials are not poured down the
drain or onto soils. They should be stored in such a
way as to prevent the escape of the material to land,
water or air.
They must also be segregated into different types of
waste e.g. oil, metals, batteries, used vehicle
components. This will prevent any reaction between
different materials and assist in disposal.
Disposal of waste
Disposal of waste materials must only be to waste
carriers who are licensed to carry those particular
waste materials and all the necessary
documentation must be completed. The waste
carrier is responsible for ensuring that the waste is
taken to the correct disposal sites.Dispose of waste in accordance with the following
guidelines.
lFuel, hydraulic fluid, anti-freeze and oil: keep
separate and dispose of to specialist contractor.
lRefrigerant: collect in specialist equipment and
reuse.
lDetergents: safe to pour down the foul drain if
diluted.
lPaint, thinners: keep separate and dispose of
to specialist contractor.
lComponents: send back to supplier for
refurbishment, or disassemble and reuse any
suitable parts. Dispose of the remainder in
ordinary waste.
lSmall parts: reuse any suitable parts, dispose
of the remainder in ordinary waste.
lMetals: can be sold if kept separate from
general waste.
lTyres: keep separate and dispose of to
specialist contractor.
lPackaging: compact as much as possible and
dispose of in ordinary waste.
lAsbestos-containing: keep separate and
dispose of to specialist contractor.
lOily and fuel wastes (e.g. rags, used spill kit
material): keep separate and dispose of to
specialist contractor.
lAir filters: keep separate and dispose of to
specialist contractor.
lRubber/plastics: dispose of in ordinary waste.
lHoses: dispose of in ordinary waste.
lBatteries: keep separate and dispose of to
specialist contractor.
lAirbags - explosives: keep separate and
dispose of to specialist contractor.
lElectrical components: send back to supplier
for refurbishment, or disassemble and reuse
any suitable parts. Dispose of the remainder in
ordinary waste.
lElectronic components: send back to supplier
for refurbishment, or disassemble and reuse
any suitable parts. Dispose of the remainder in
ordinary waste.
lCatalysts: can be sold if kept separate from
general waste
lUsed spill-absorbing material: keep separate
and dispose of to specialist contractor.
lOffice waste: recycle paper and toner and ink
cartridges, dispose of the remainder in ordinary
waste.
Page 61 of 1672
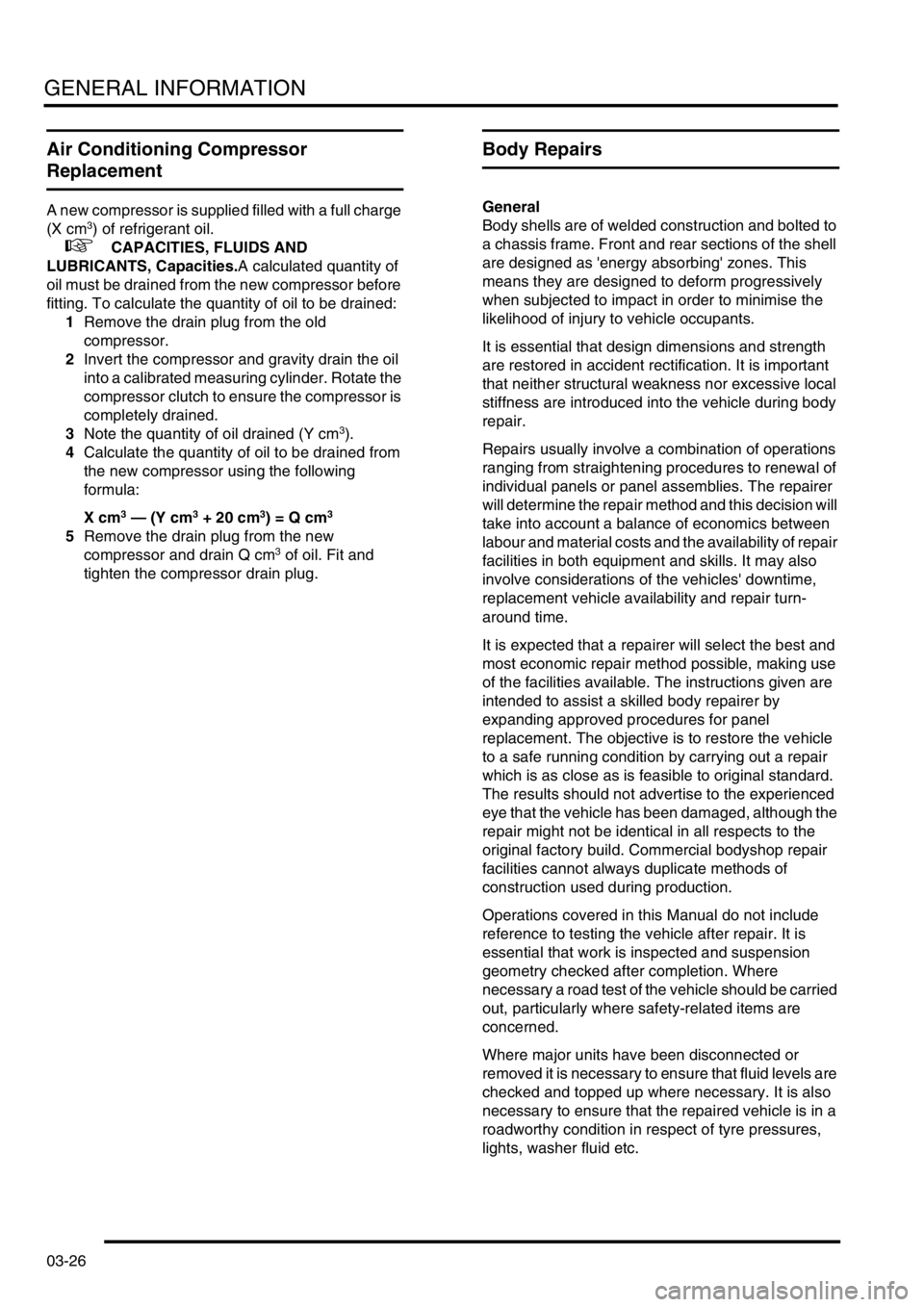
GENERAL INFORMATION
03-26
Air Conditioning Compressor
Replacement
A new compressor is supplied filled with a full charge
(X cm3) of refrigerant oil.
+ CAPACITIES, FLUIDS AND
LUBRICANTS, Capacities.A calculated quantity of
oil must be drained from the new compressor before
fitting. To calculate the quantity of oil to be drained:
1Remove the drain plug from the old
compressor.
2Invert the compressor and gravity drain the oil
into a calibrated measuring cylinder. Rotate the
compressor clutch to ensure the compressor is
completely drained.
3Note the quantity of oil drained (Y cm
3).
4Calculate the quantity of oil to be drained from
the new compressor using the following
formula:
X cm
3 — (Y cm3 + 20 cm3) = Q cm3
5Remove the drain plug from the new
compressor and drain Q cm3 of oil. Fit and
tighten the compressor drain plug.
Body Repairs
General
Body shells are of welded construction and bolted to
a chassis frame. Front and rear sections of the shell
are designed as 'energy absorbing' zones. This
means they are designed to deform progressively
when subjected to impact in order to minimise the
likelihood of injury to vehicle occupants.
It is essential that design dimensions and strength
are restored in accident rectification. It is important
that neither structural weakness nor excessive local
stiffness are introduced into the vehicle during body
repair.
Repairs usually involve a combination of operations
ranging from straightening procedures to renewal of
individual panels or panel assemblies. The repairer
will determine the repair method and this decision will
take into account a balance of economics between
labour and material costs and the availability of repair
facilities in both equipment and skills. It may also
involve considerations of the vehicles' downtime,
replacement vehicle availability and repair turn-
around time.
It is expected that a repairer will select the best and
most economic repair method possible, making use
of the facilities available. The instructions given are
intended to assist a skilled body repairer by
expanding approved procedures for panel
replacement. The objective is to restore the vehicle
to a safe running condition by carrying out a repair
which is as close as is feasible to original standard.
The results should not advertise to the experienced
eye that the vehicle has been damaged, although the
repair might not be identical in all respects to the
original factory build. Commercial bodyshop repair
facilities cannot always duplicate methods of
construction used during production.
Operations covered in this Manual do not include
reference to testing the vehicle after repair. It is
essential that work is inspected and suspension
geometry checked after completion. Where
necessary a road test of the vehicle should be carried
out, particularly where safety-related items are
concerned.
Where major units have been disconnected or
removed it is necessary to ensure that fluid levels are
checked and topped up where necessary. It is also
necessary to ensure that the repaired vehicle is in a
roadworthy condition in respect of tyre pressures,
lights, washer fluid etc.
Page 114 of 1672
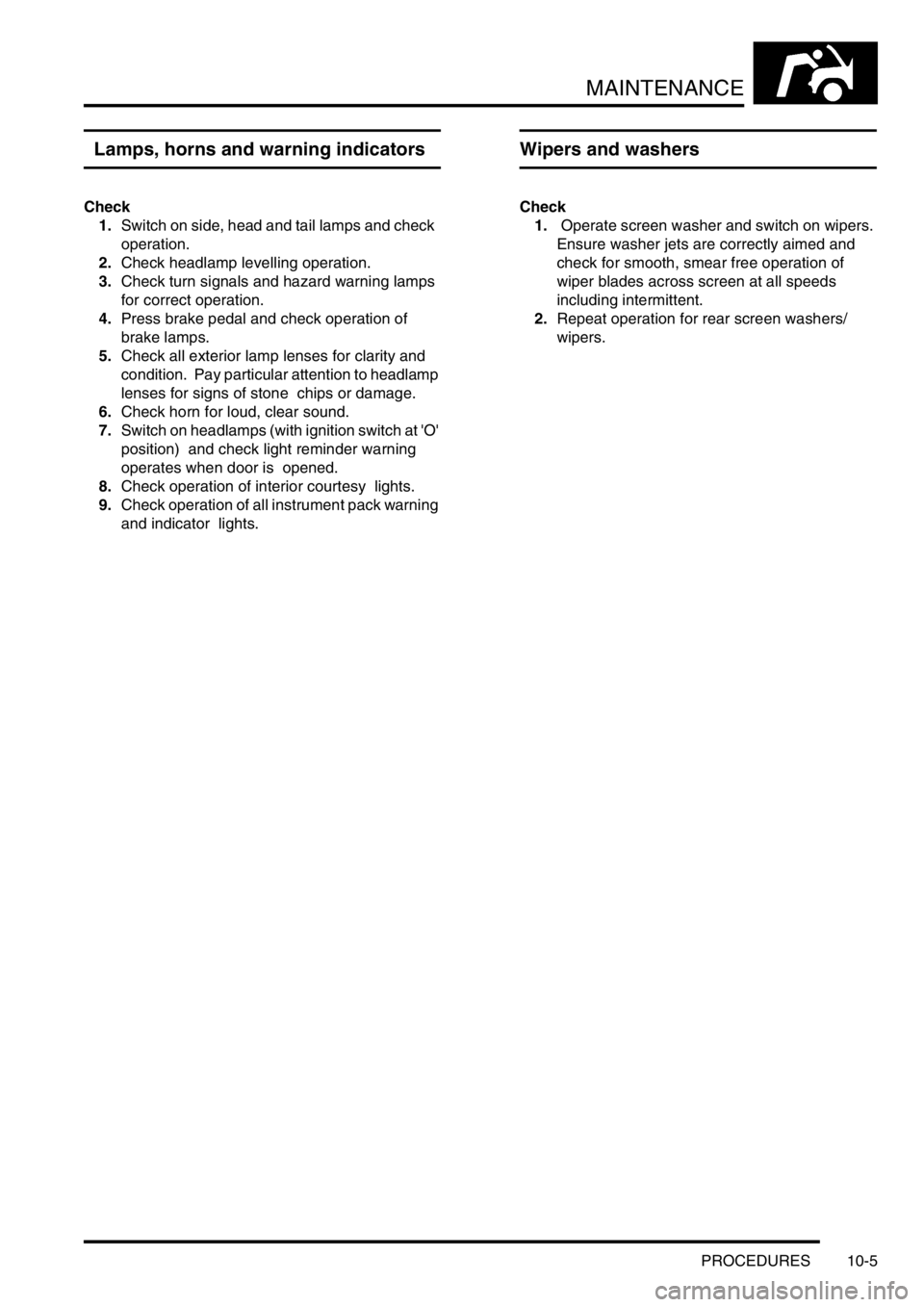
MAINTENANCE
PROCEDURES 10-5
Lamps, horns and warning indicators
Check
1.Switch on side, head and tail lamps and check
operation.
2.Check headlamp levelling operation.
3.Check turn signals and hazard warning lamps
for correct operation.
4.Press brake pedal and check operation of
brake lamps.
5.Check all exterior lamp lenses for clarity and
condition. Pay particular attention to headlamp
lenses for signs of stone chips or damage.
6.Check horn for loud, clear sound.
7.Switch on headlamps (with ignition switch at 'O'
position) and check light reminder warning
operates when door is opened.
8.Check operation of interior courtesy lights.
9.Check operation of all instrument pack warning
and indicator lights.
Wipers and washers
Check
1. Operate screen washer and switch on wipers.
Ensure washer jets are correctly aimed and
check for smooth, smear free operation of
wiper blades across screen at all speeds
including intermittent.
2.Repeat operation for rear screen washers/
wipers.
Page 510 of 1672
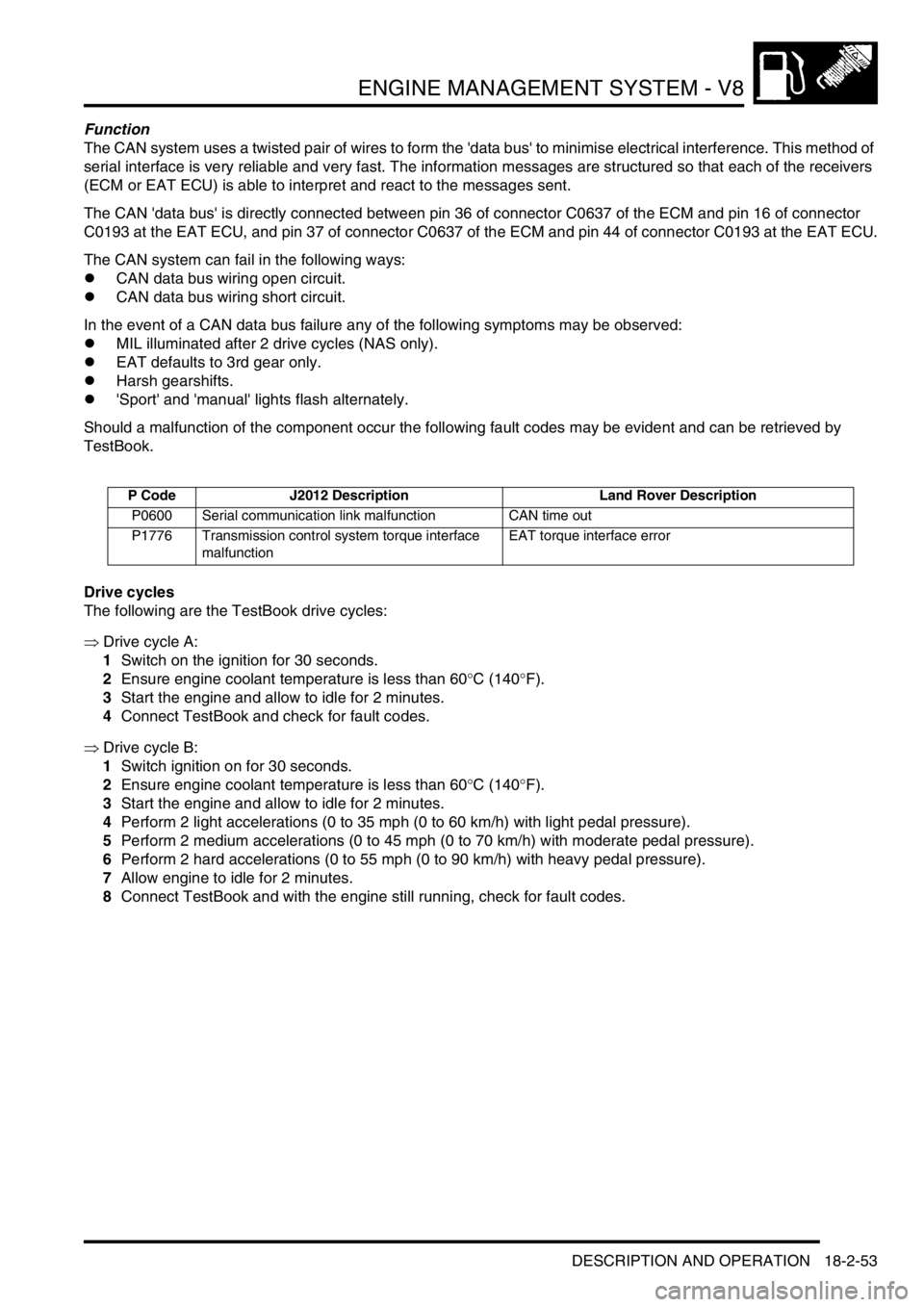
ENGINE MANAGEMENT SYSTEM - V8
DESCRIPTION AND OPERATION 18-2-53
Function
The CAN system uses a twisted pair of wires to form the 'data bus' to minimise electrical interference. This method of
serial interface is very reliable and very fast. The information messages are structured so that each of the receivers
(ECM or EAT ECU) is able to interpret and react to the messages sent.
The CAN 'data bus' is directly connected between pin 36 of connector C0637 of the ECM and pin 16 of connector
C0193 at the EAT ECU, and pin 37 of connector C0637 of the ECM and pin 44 of connector C0193 at the EAT ECU.
The CAN system can fail in the following ways:
lCAN data bus wiring open circuit.
lCAN data bus wiring short circuit.
In the event of a CAN data bus failure any of the following symptoms may be observed:
lMIL illuminated after 2 drive cycles (NAS only).
lEAT defaults to 3rd gear only.
lHarsh gearshifts.
l'Sport' and 'manual' lights flash alternately.
Should a malfunction of the component occur the following fault codes may be evident and can be retrieved by
TestBook.
Drive cycles
The following are the TestBook drive cycles:
Drive cycle A:
1Switch on the ignition for 30 seconds.
2Ensure engine coolant temperature is less than 60
°C (140°F).
3Start the engine and allow to idle for 2 minutes.
4Connect TestBook and check for fault codes.
Drive cycle B:
1Switch ignition on for 30 seconds.
2Ensure engine coolant temperature is less than 60
°C (140°F).
3Start the engine and allow to idle for 2 minutes.
4Perform 2 light accelerations (0 to 35 mph (0 to 60 km/h) with light pedal pressure).
5Perform 2 medium accelerations (0 to 45 mph (0 to 70 km/h) with moderate pedal pressure).
6Perform 2 hard accelerations (0 to 55 mph (0 to 90 km/h) with heavy pedal pressure).
7Allow engine to idle for 2 minutes.
8Connect TestBook and with the engine still running, check for fault codes.
P Code J2012 Description Land Rover Description
P0600 Serial communication link malfunction CAN time out
P1776 Transmission control system torque interface
malfunctionEAT torque interface error
Page 1389 of 1672
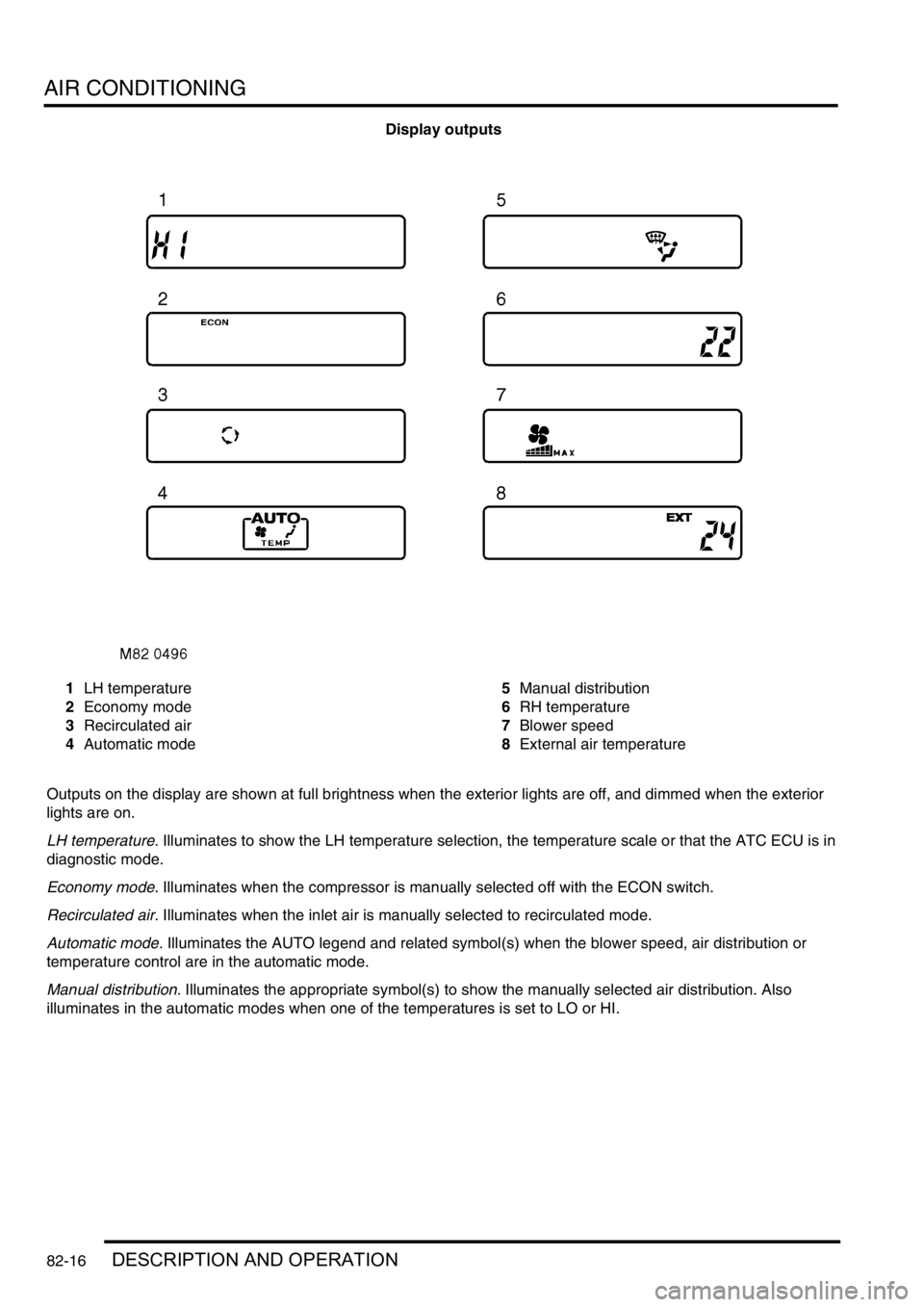
AIR CONDITIONING
82-16DESCRIPTION AND OPERATION
Display outputs
1LH temperature
2Economy mode
3Recirculated air
4Automatic mode5Manual distribution
6RH temperature
7Blower speed
8External air temperature
Outputs on the display are shown at full brightness when the exterior lights are off, and dimmed when the exterior
lights are on.
LH temperature. Illuminates to show the LH temperature selection, the temperature scale or that the ATC ECU is in
diagnostic mode.
Economy mode. Illuminates when the compressor is manually selected off with the ECON switch.
Recirculated air. Illuminates when the inlet air is manually selected to recirculated mode.
Automatic mode. Illuminates the AUTO legend and related symbol(s) when the blower speed, air distribution or
temperature control are in the automatic mode.
Manual distribution. Illuminates the appropriate symbol(s) to show the manually selected air distribution. Also
illuminates in the automatic modes when one of the temperatures is set to LO or HI.
Page 1467 of 1672
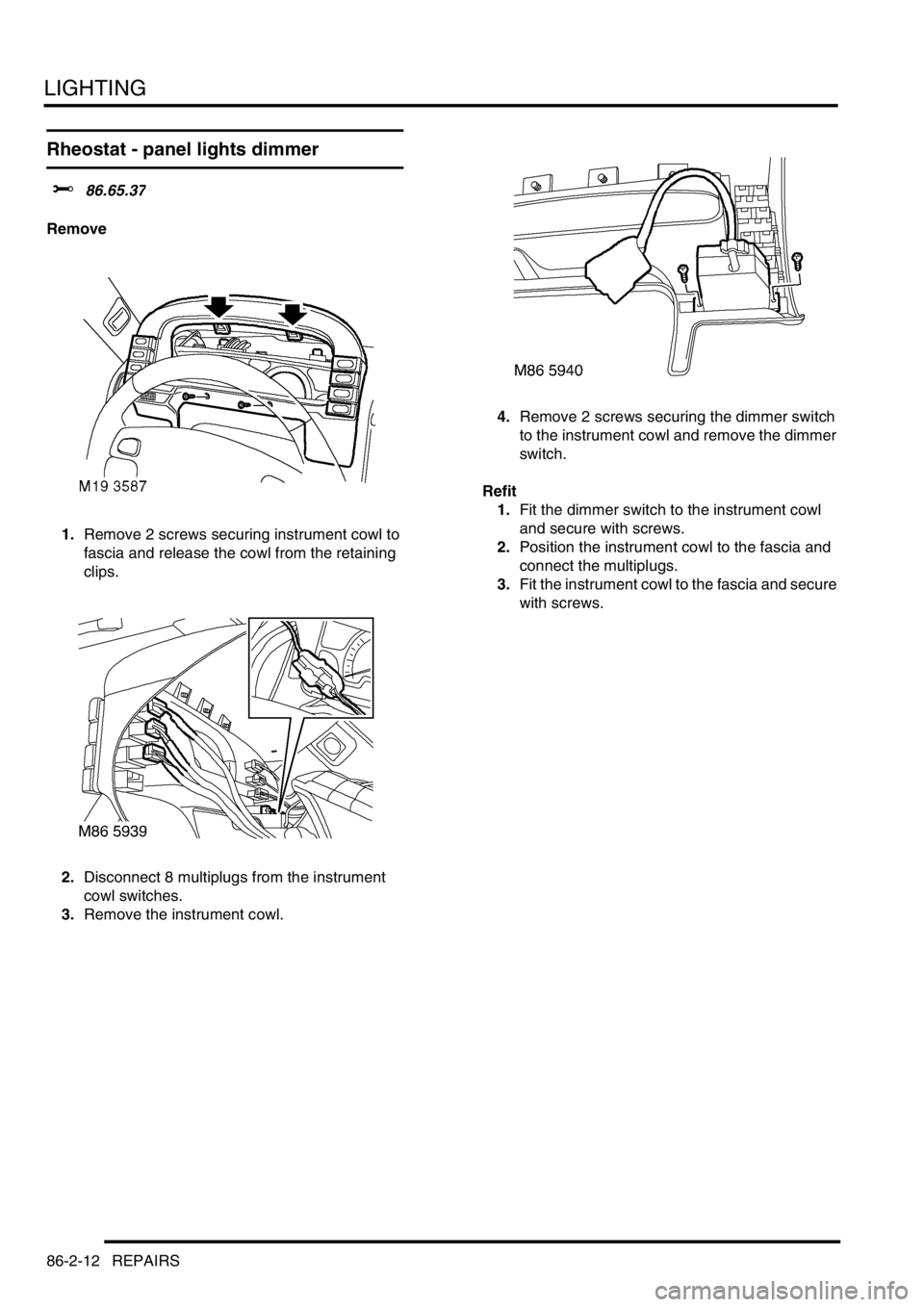
LIGHTING
86-2-12 REPAIRS
Rheostat - panel lights dimmer
$% 86.65.37
Remove
1.Remove 2 screws securing instrument cowl to
fascia and release the cowl from the retaining
clips.
2.Disconnect 8 multiplugs from the instrument
cowl switches.
3.Remove the instrument cowl.4.Remove 2 screws securing the dimmer switch
to the instrument cowl and remove the dimmer
switch.
Refit
1.Fit the dimmer switch to the instrument cowl
and secure with screws.
2.Position the instrument cowl to the fascia and
connect the multiplugs.
3.Fit the instrument cowl to the fascia and secure
with screws.
Page 1480 of 1672
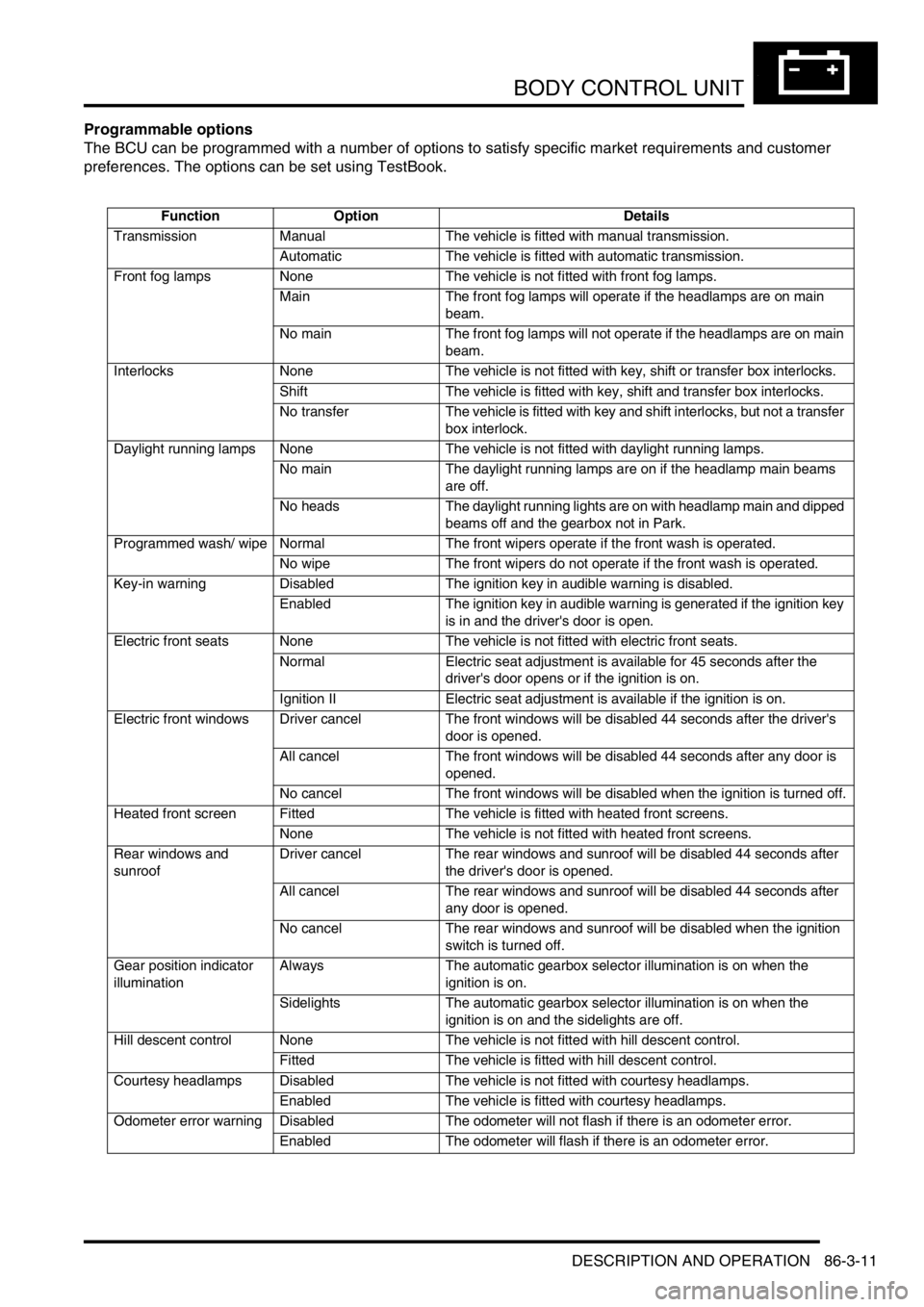
BODY CONTROL UNIT
DESCRIPTION AND OPERATION 86-3-11
Programmable options
The BCU can be programmed with a number of options to satisfy specific market requirements and customer
preferences. The options can be set using TestBook.
Function Option Details
Transmission Manual The vehicle is fitted with manual transmission.
Automatic The vehicle is fitted with automatic transmission.
Front fog lamps None The vehicle is not fitted with front fog lamps.
Main The front fog lamps will operate if the headlamps are on main
beam.
No main The front fog lamps will not operate if the headlamps are on main
beam.
Interlocks None The vehicle is not fitted with key, shift or transfer box interlocks.
Shift The vehicle is fitted with key, shift and transfer box interlocks.
No transfer The vehicle is fitted with key and shift interlocks, but not a transfer
box interlock.
Daylight running lamps None The vehicle is not fitted with daylight running lamps.
No main The daylight running lamps are on if the headlamp main beams
are off.
No heads The daylight running lights are on with headlamp main and dipped
beams off and the gearbox not in Park.
Programmed wash/ wipe Normal The front wipers operate if the front wash is operated.
No wipe The front wipers do not operate if the front wash is operated.
Key-in warning Disabled The ignition key in audible warning is disabled.
Enabled The ignition key in audible warning is generated if the ignition key
is in and the driver's door is open.
Electric front seats None The vehicle is not fitted with electric front seats.
Normal Electric seat adjustment is available for 45 seconds after the
driver's door opens or if the ignition is on.
Ignition II Electric seat adjustment is available if the ignition is on.
Electric front windows Driver cancel The front windows will be disabled 44 seconds after the driver's
door is opened.
All cancel The front windows will be disabled 44 seconds after any door is
opened.
No cancel The front windows will be disabled when the ignition is turned off.
Heated front screen Fitted The vehicle is fitted with heated front screens.
None The vehicle is not fitted with heated front screens.
Rear windows and
sunroofDriver cancel The rear windows and sunroof will be disabled 44 seconds after
the driver's door is opened.
All cancel The rear windows and sunroof will be disabled 44 seconds after
any door is opened.
No cancel The rear windows and sunroof will be disabled when the ignition
switch is turned off.
Gear position indicator
illuminationAlways The automatic gearbox selector illumination is on when the
ignition is on.
Sidelights The automatic gearbox selector illumination is on when the
ignition is on and the sidelights are off.
Hill descent control None The vehicle is not fitted with hill descent control.
Fitted The vehicle is fitted with hill descent control.
Courtesy headlamps Disabled The vehicle is not fitted with courtesy headlamps.
Enabled The vehicle is fitted with courtesy headlamps.
Odometer error warning Disabled The odometer will not flash if there is an odometer error.
Enabled The odometer will flash if there is an odometer error.
Page 1487 of 1672
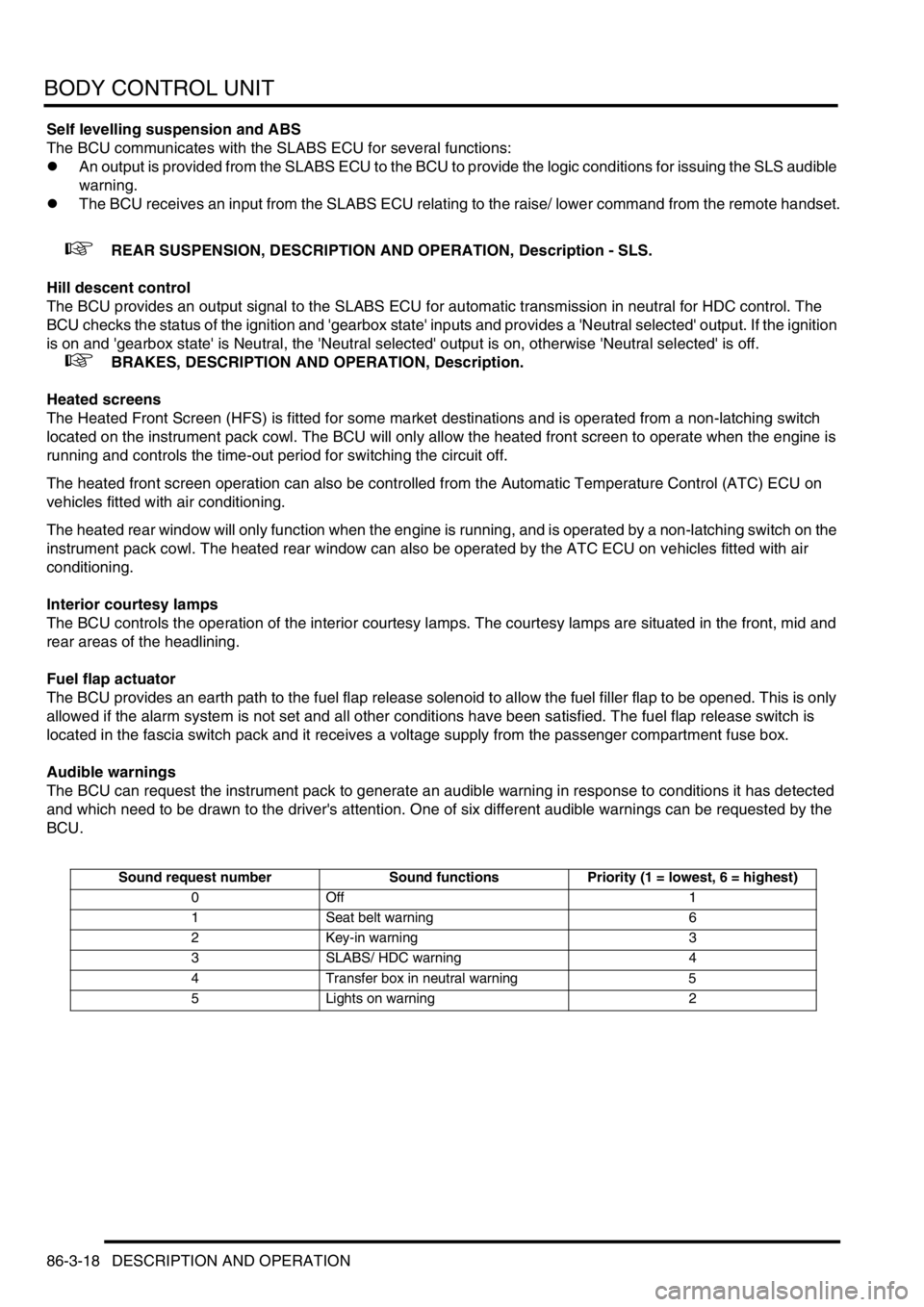
BODY CONTROL UNIT
86-3-18 DESCRIPTION AND OPERATION
Self levelling suspension and ABS
The BCU communicates with the SLABS ECU for several functions:
lAn output is provided from the SLABS ECU to the BCU to provide the logic conditions for issuing the SLS audible
warning.
lThe BCU receives an input from the SLABS ECU relating to the raise/ lower command from the remote handset.
+ REAR SUSPENSION, DESCRIPTION AND OPERATION, Description - SLS.
Hill descent control
The BCU provides an output signal to the SLABS ECU for automatic transmission in neutral for HDC control. The
BCU checks the status of the ignition and 'gearbox state' inputs and provides a 'Neutral selected' output. If the ignition
is on and 'gearbox state' is Neutral, the 'Neutral selected' output is on, otherwise 'Neutral selected' is off.
+ BRAKES, DESCRIPTION AND OPERATION, Description.
Heated screens
The Heated Front Screen (HFS) is fitted for some market destinations and is operated from a non-latching switch
located on the instrument pack cowl. The BCU will only allow the heated front screen to operate when the engine is
running and controls the time-out period for switching the circuit off.
The heated front screen operation can also be controlled from the Automatic Temperature Control (ATC) ECU on
vehicles fitted with air conditioning.
The heated rear window will only function when the engine is running, and is operated by a non-latching switch on the
instrument pack cowl. The heated rear window can also be operated by the ATC ECU on vehicles fitted with air
conditioning.
Interior courtesy lamps
The BCU controls the operation of the interior courtesy lamps. The courtesy lamps are situated in the front, mid and
rear areas of the headlining.
Fuel flap actuator
The BCU provides an earth path to the fuel flap release solenoid to allow the fuel filler flap to be opened. This is only
allowed if the alarm system is not set and all other conditions have been satisfied. The fuel flap release switch is
located in the fascia switch pack and it receives a voltage supply from the passenger compartment fuse box.
Audible warnings
The BCU can request the instrument pack to generate an audible warning in response to conditions it has detected
and which need to be drawn to the driver's attention. One of six different audible warnings can be requested by the
BCU.
Sound request number Sound functions Priority (1 = lowest, 6 = highest)
0Off 1
1 Seat belt warning 6
2 Key-in warning 3
3 SLABS/ HDC warning 4
4 Transfer box in neutral warning 5
5 Lights on warning 2
Page 1498 of 1672
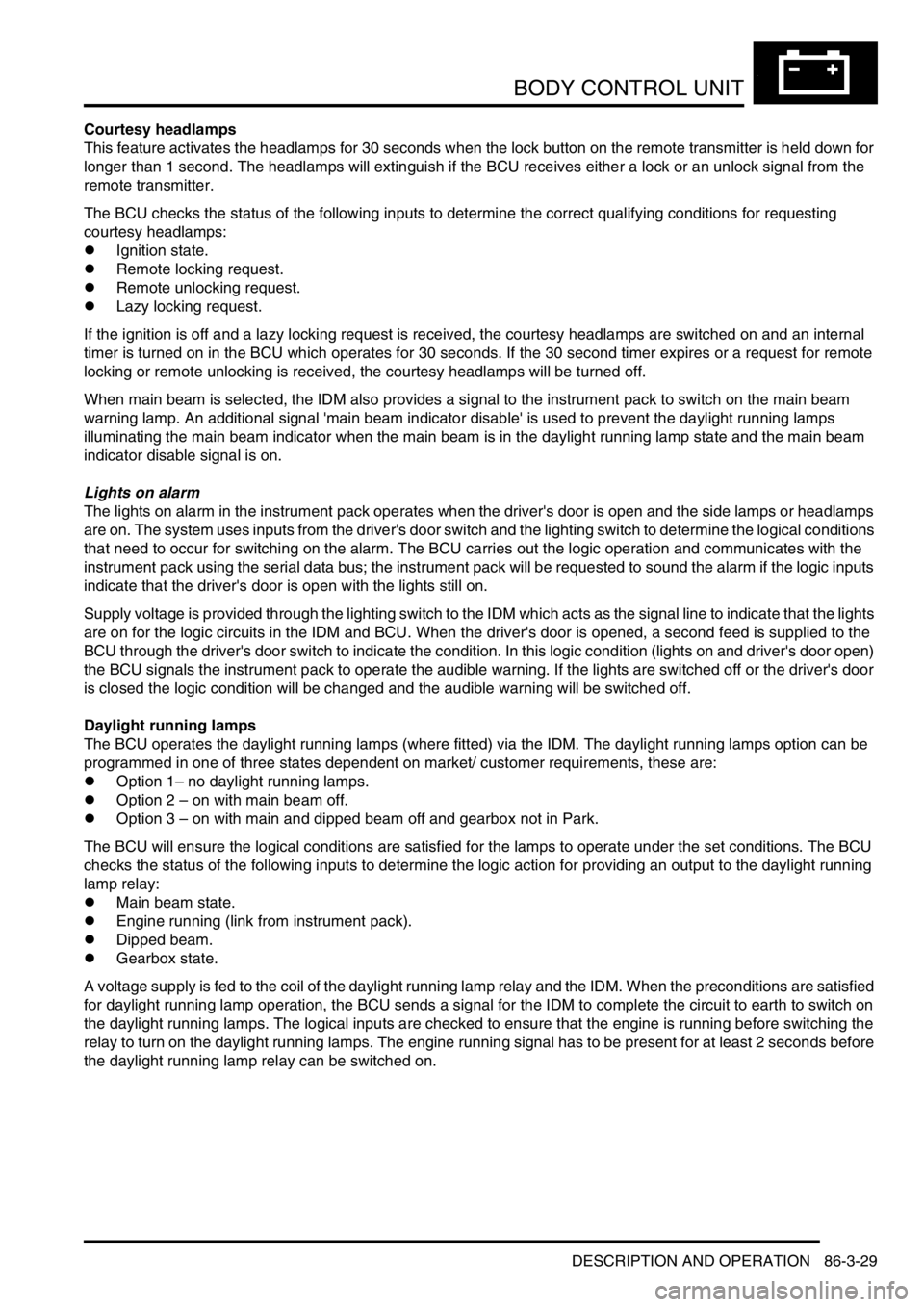
BODY CONTROL UNIT
DESCRIPTION AND OPERATION 86-3-29
Courtesy headlamps
This feature activates the headlamps for 30 seconds when the lock button on the remote transmitter is held down for
longer than 1 second. The headlamps will extinguish if the BCU receives either a lock or an unlock signal from the
remote transmitter.
The BCU checks the status of the following inputs to determine the correct qualifying conditions for requesting
courtesy headlamps:
lIgnition state.
lRemote locking request.
lRemote unlocking request.
lLazy locking request.
If the ignition is off and a lazy locking request is received, the courtesy headlamps are switched on and an internal
timer is turned on in the BCU which operates for 30 seconds. If the 30 second timer expires or a request for remote
locking or remote unlocking is received, the courtesy headlamps will be turned off.
When main beam is selected, the IDM also provides a signal to the instrument pack to switch on the main beam
warning lamp. An additional signal 'main beam indicator disable' is used to prevent the daylight running lamps
illuminating the main beam indicator when the main beam is in the daylight running lamp state and the main beam
indicator disable signal is on.
Lights on alarm
The lights on alarm in the instrument pack operates when the driver's door is open and the side lamps or headlamps
are on. The system uses inputs from the driver's door switch and the lighting switch to determine the logical conditions
that need to occur for switching on the alarm. The BCU carries out the logic operation and communicates with the
instrument pack using the serial data bus; the instrument pack will be requested to sound the alarm if the logic inputs
indicate that the driver's door is open with the lights still on.
Supply voltage is provided through the lighting switch to the IDM which acts as the signal line to indicate that the lights
are on for the logic circuits in the IDM and BCU. When the driver's door is opened, a second feed is supplied to the
BCU through the driver's door switch to indicate the condition. In this logic condition (lights on and driver's door open)
the BCU signals the instrument pack to operate the audible warning. If the lights are switched off or the driver's door
is closed the logic condition will be changed and the audible warning will be switched off.
Daylight running lamps
The BCU operates the daylight running lamps (where fitted) via the IDM. The daylight running lamps option can be
programmed in one of three states dependent on market/ customer requirements, these are:
lOption 1– no daylight running lamps.
lOption 2 – on with main beam off.
lOption 3 – on with main and dipped beam off and gearbox not in Park.
The BCU will ensure the logical conditions are satisfied for the lamps to operate under the set conditions. The BCU
checks the status of the following inputs to determine the logic action for providing an output to the daylight running
lamp relay:
lMain beam state.
lEngine running (link from instrument pack).
lDipped beam.
lGearbox state.
A voltage supply is fed to the coil of the daylight running lamp relay and the IDM. When the preconditions are satisfied
for daylight running lamp operation, the BCU sends a signal for the IDM to complete the circuit to earth to switch on
the daylight running lamps. The logical inputs are checked to ensure that the engine is running before switching the
relay to turn on the daylight running lamps. The engine running signal has to be present for at least 2 seconds before
the daylight running lamp relay can be switched on.