Throttle Position sensor LEXUS SC400 1991 Service User Guide
[x] Cancel search | Manufacturer: LEXUS, Model Year: 1991, Model line: SC400, Model: LEXUS SC400 1991Pages: 4087, PDF Size: 75.75 MB
Page 951 of 4087
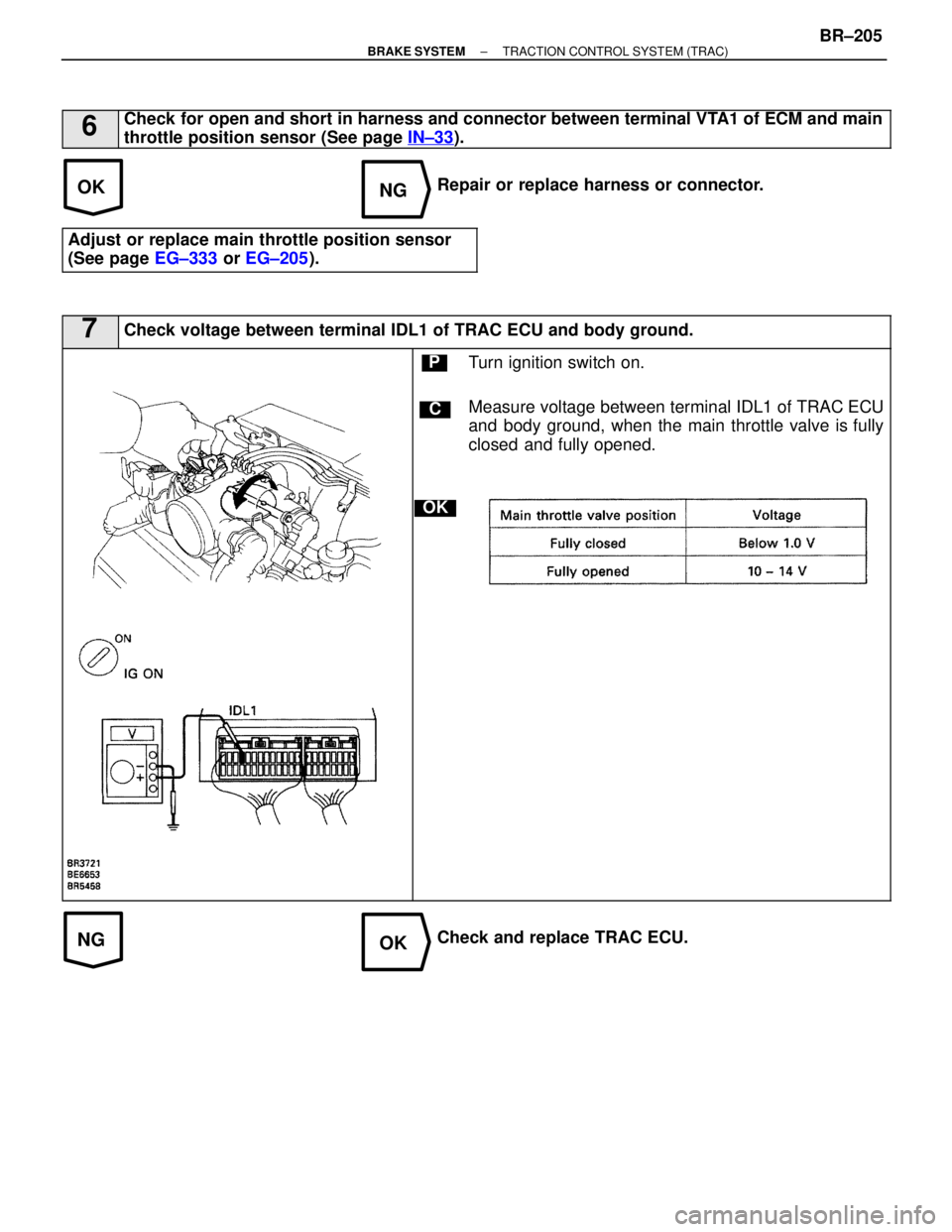
OKNG
NGOK
6Check for open and short in harness and connector between terminal VTA1 of ECM and main
throttle position sensor (See page IN±33
).
Repair or replace harness or connector.
Adjust or replace main throttle position sensor
(See page EG±333 or EG±205 ).
7Check voltage between terminal IDL1 of TRAC ECU and body ground.
C
OK
PTurn ignition switch on.
Measure voltage between terminal IDL1 of TRAC ECU
and body ground, when the main throttle valve is fully
closed and fully opened.
Check and replace TRAC ECU.
±
BRAKE SYSTEM TRACTION CONTROL SYSTEM (TRAC)BR±205
WhereEverybodyKnowsYourName
Page 953 of 4087
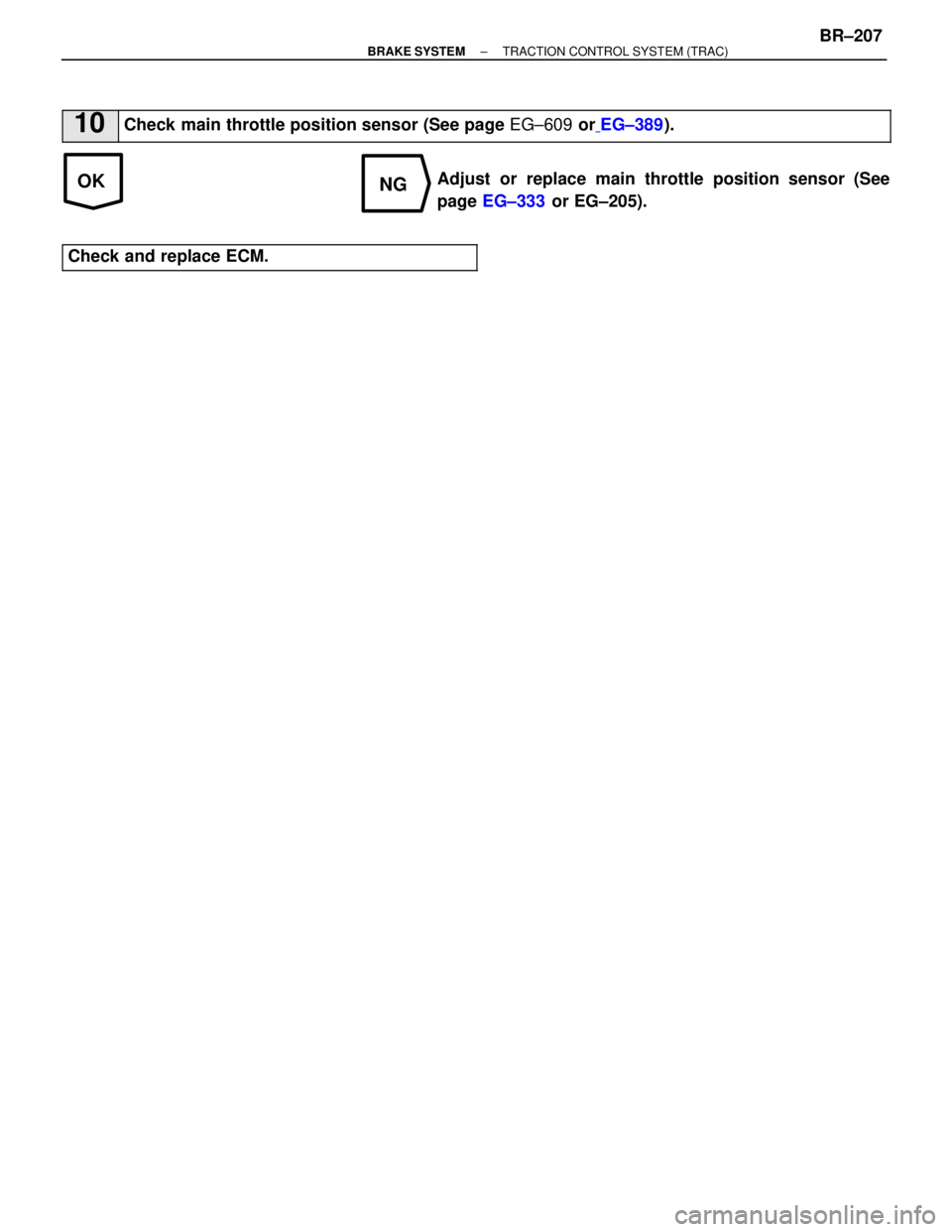
OKNG
10Check main throttle position sensor (See page EG±609 or EG±389 ).
Adjust or replace main throttle position sensor (See
page EG±333 or EG±205).
Check and replace ECM.
±
BRAKE SYSTEM TRACTION CONTROL SYSTEM (TRAC)BR±207
WhereEverybodyKnowsYourName
Page 954 of 4087
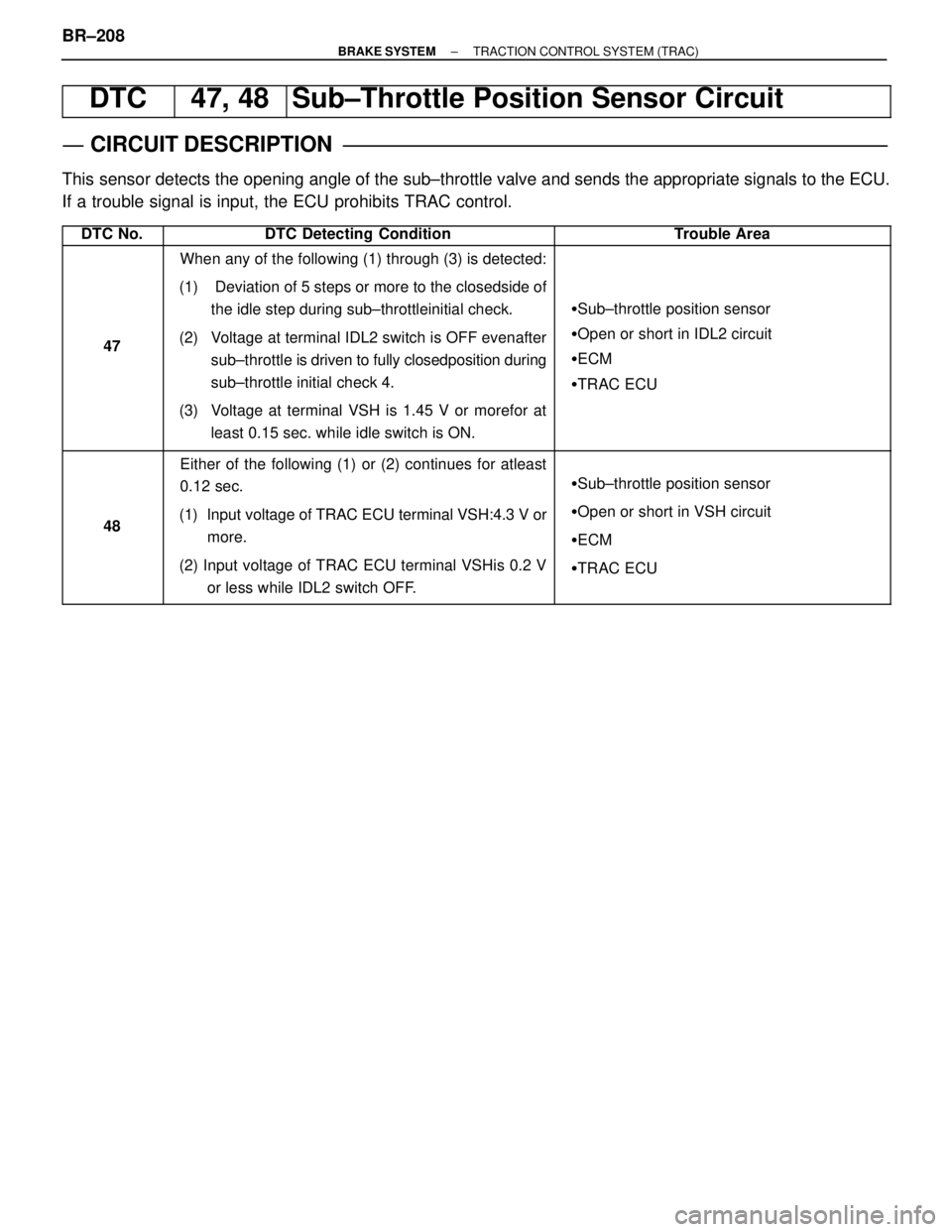
DTC47, 48Sub±Throttle Position Sensor Circuit
CIRCUIT DESCRIPTION
This sensor detects the opening angle of the sub±throttle valve and sends the appropriate signals to the ECU.
If a trouble signal is input, the ECU prohibits TRAC control.
DTC No.DTC Detecting ConditionTrouble Area
47
When any of the following (1) through (3) is detected:
(1) Deviation of 5 steps or more to the closedside of the idle step during sub±throttleinitial check.
(2) Voltage at terminal IDL2 switch is OFF evenafter sub±throttle is driven to fully closedposition during
sub±throttle initial check 4.
(3) Voltage at terminal VSH is 1.45 V or morefor at least 0.15 sec. while idle switch is ON.
Sub±throttle position sensor
Open or short in IDL2 circuit
ECM
TRAC ECU
48
Either of the following (1) or (2) continues for atleast
0.12 sec.
(1) Input voltage of TRAC ECU terminal VSH:4.3 V or more.
(2) Input voltage of TRAC ECU terminal VSHis 0.2 V or less while IDL2 switch OFF.
Sub±throttle position sensor
Open or short in VSH circuit
ECM
TRAC ECU
BR±208±
BRAKE SYSTEM TRACTION CONTROL SYSTEM (TRAC)
WhereEverybodyKnowsYourName
Page 959 of 4087
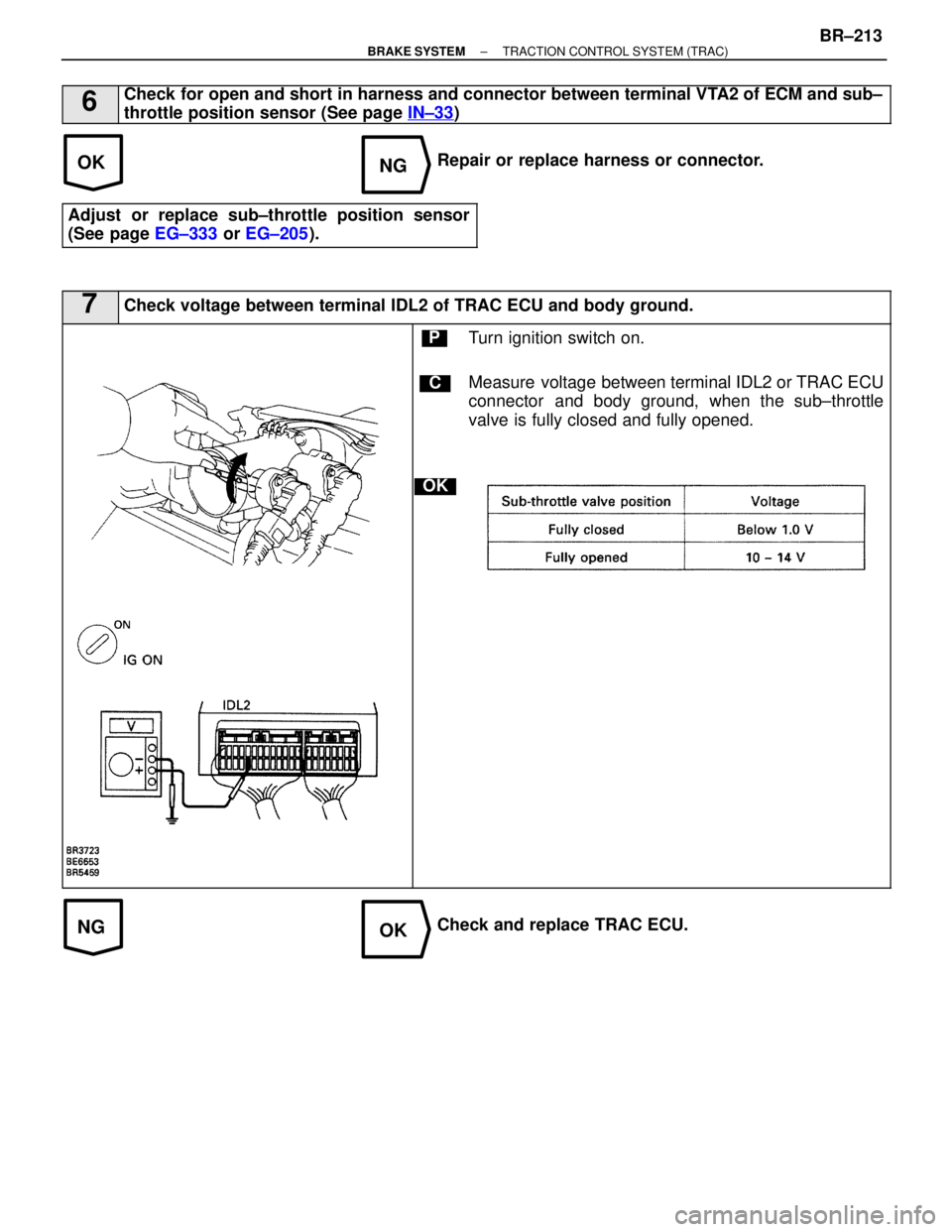
OKNG
NGOK
6Check for open and short in harness and connector between terminal VTA2 of ECM and sub±
throttle position sensor (See page IN±33
)
Repair or replace harness or connector.
Adjust or replace sub±throttle position sensor
(See page EG±333 or EG±205 ).
7Check voltage between terminal IDL2 of TRAC ECU and body ground.
C
OK
PTurn ignition switch on.
Measure voltage between terminal IDL2 or TRAC ECU
connector and body ground, when the sub±throttle
valve is fully closed and fully opened.
Check and replace TRAC ECU.
±
BRAKE SYSTEM TRACTION CONTROL SYSTEM (TRAC)BR±213
WhereEverybodyKnowsYourName
Page 961 of 4087
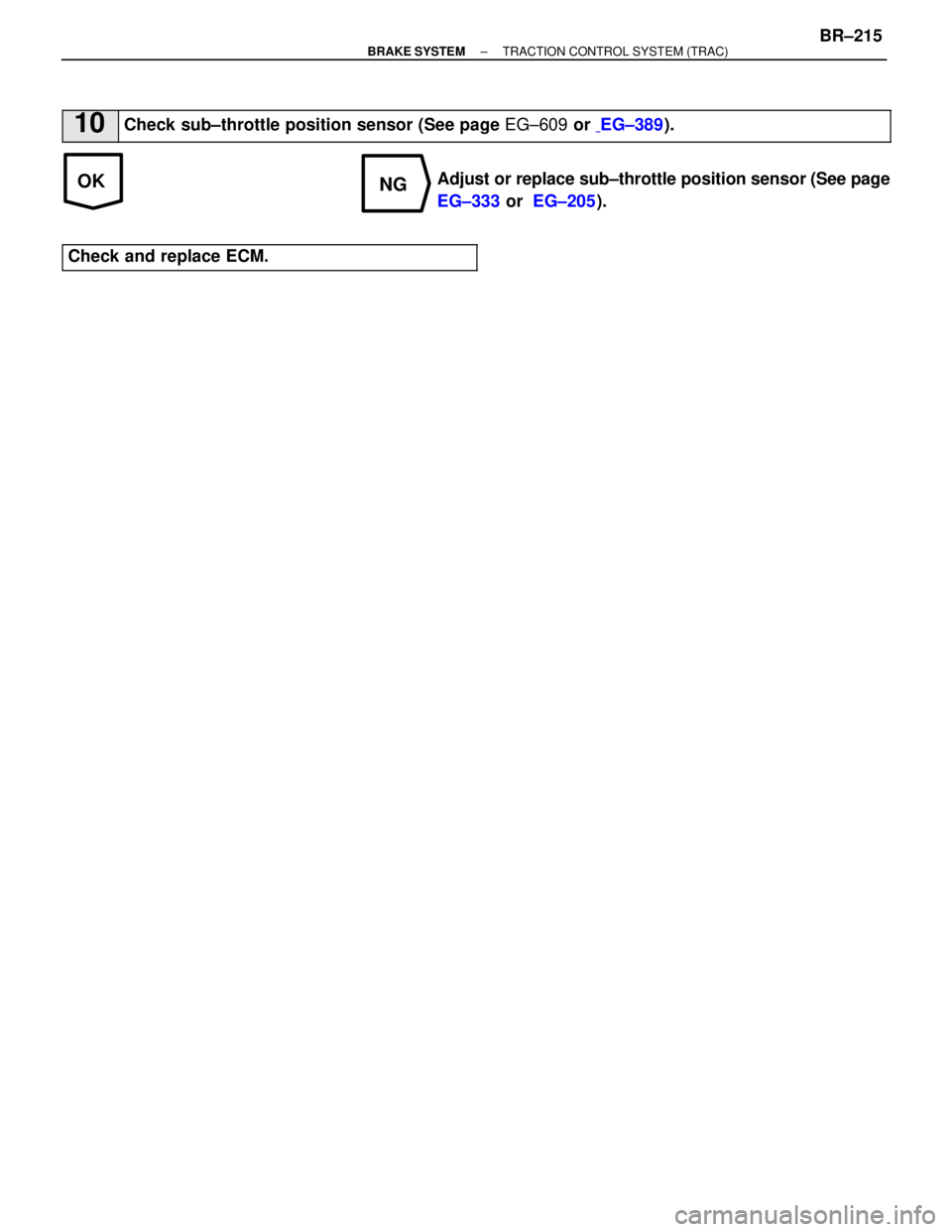
OKNG
10Check sub±throttle position sensor (See page EG±609 or EG±389 ).
Adjust or replace sub±throttle position sensor (See page
EG±333 or EG±205 ).
Check and replace ECM.
±
BRAKE SYSTEM TRACTION CONTROL SYSTEM (TRAC)BR±215
WhereEverybodyKnowsYourName
Page 1392 of 4087
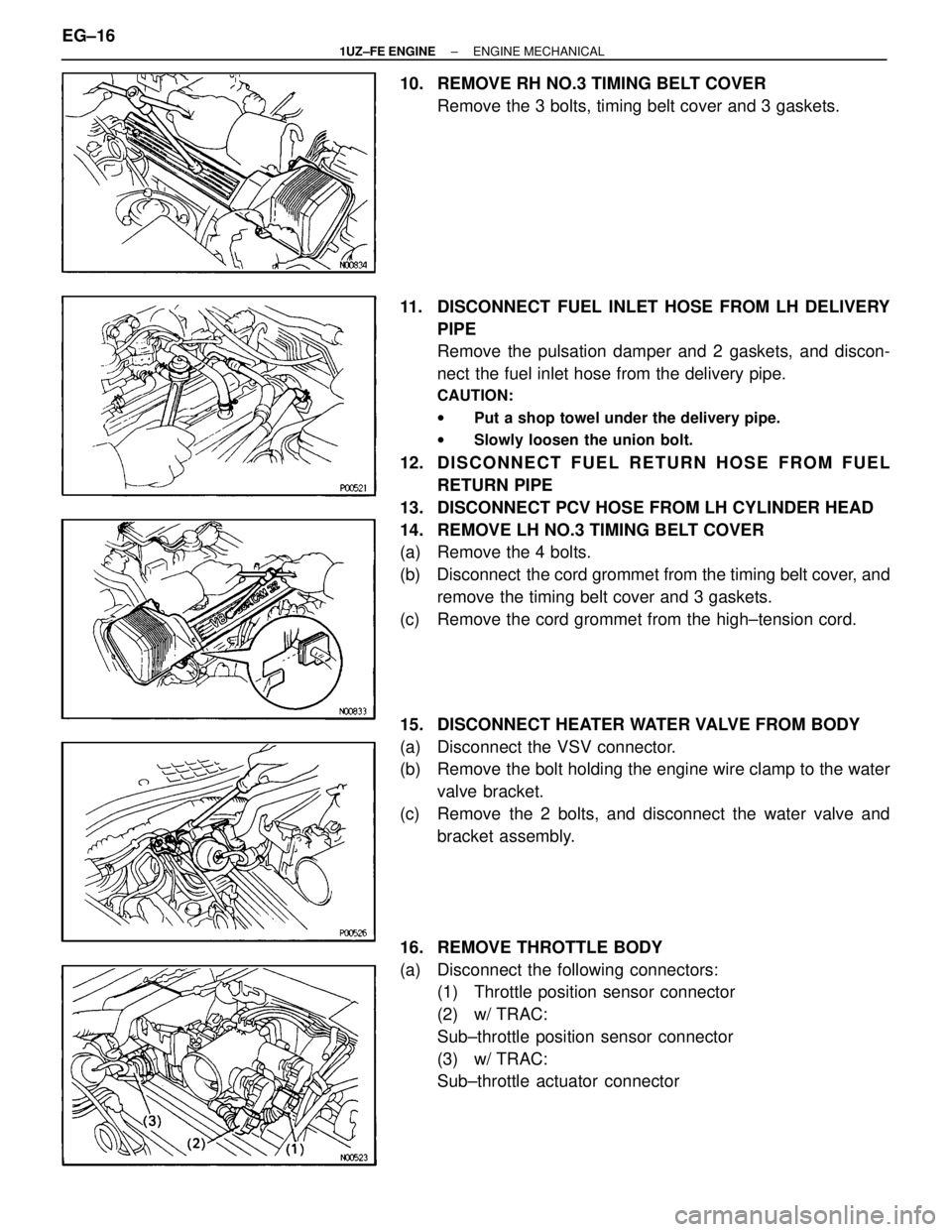
10. REMOVE RH NO.3 TIMING BELT COVERRemove the 3 bolts, timing belt cover and 3 gaskets.
11. DISCONNECT FUEL INLET HOSE FROM LH DELIVERY PIPE
Remove the pulsation damper and 2 gaskets, and discon-
nect the fuel inlet hose from the delivery pipe.
CAUTION:
w Put a shop towel under the delivery pipe.
w Slowly loosen the union bolt.
12. D I S C O N N E C T F U E L R E T U R N H O S E F R O M F U E L
RETURN PIPE
13. DISCONNECT PCV HOSE FROM LH CYLINDER HEAD
14. REMOVE LH NO.3 TIMING BELT COVER
(a) Remove the 4 bolts.
(b) Disconnect the cord grommet from the timing belt cover, and remove the timing belt cover and 3 gaskets.
(c) Remove the cord grommet from the high±tension cord.
15. DISCONNECT HEATER WATER VALVE FROM BODY
(a) Disconnect the VSV connector.
(b) Remove the bolt holding the engine wire clamp to the water valve bracket.
(c) Remove the 2 bolts, and disconnect the water valve and bracket assembly.
16. REMOVE THROTTLE BODY
(a) Disconnect the following connectors: (1) Throttle position sensor connector
(2) w/ TRAC:
Sub±throttle position sensor connector
(3) w/ TRAC:
Sub±throttle actuator connector
EG±16
±
1UZ±FE ENGINE ENGINE MECHANICAL
WhereEverybodyKnowsYourName
Page 1405 of 4087
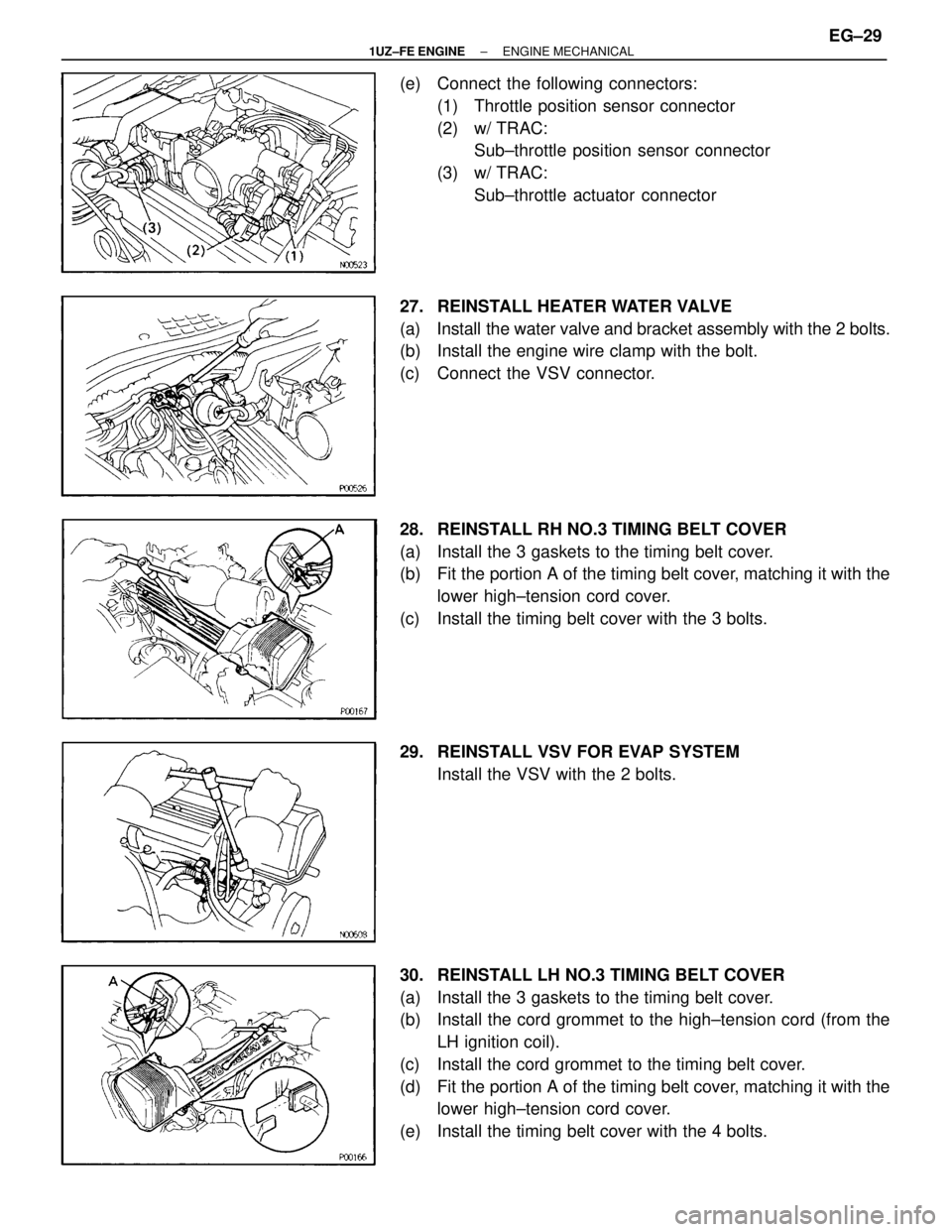
(e) Connect the following connectors:(1) Throttle position sensor connector
(2) w/ TRAC:Sub±throttle position sensor connector
(3) w/ TRAC: Sub±throttle actuator connector
27. REINSTALL HEATER WATER VALVE
(a) Install the water valve and bracket assembly with the 2 bolts.
(b) Install the engine wire clamp with the bolt.
(c) Connect the VSV connector.
28. REINSTALL RH NO.3 TIMING BELT COVER
(a) Install the 3 gaskets to the timing belt cover.
(b) Fit the portion A of the timing belt cover, matching it with the lower high±tension cord cover.
(c) Install the timing belt cover with the 3 bolts.
29. REINSTALL VSV FOR EVAP SYSTEM Install the VSV with the 2 bolts.
30. REINSTALL LH NO.3 TIMING BELT COVER
(a) Install the 3 gaskets to the timing belt cover.
(b) Install the cord grommet to the high±tension cord (from the LH ignition coil).
(c) Install the cord grommet to the timing belt cover.
(d) Fit the portion A of the timing belt cover, matching it with the lower high±tension cord cover.
(e) Install the timing belt cover with the 4 bolts.
±
1UZ±FE ENGINE ENGINE MECHANICALEG±29
WhereEverybodyKnowsYourName
Page 1409 of 4087
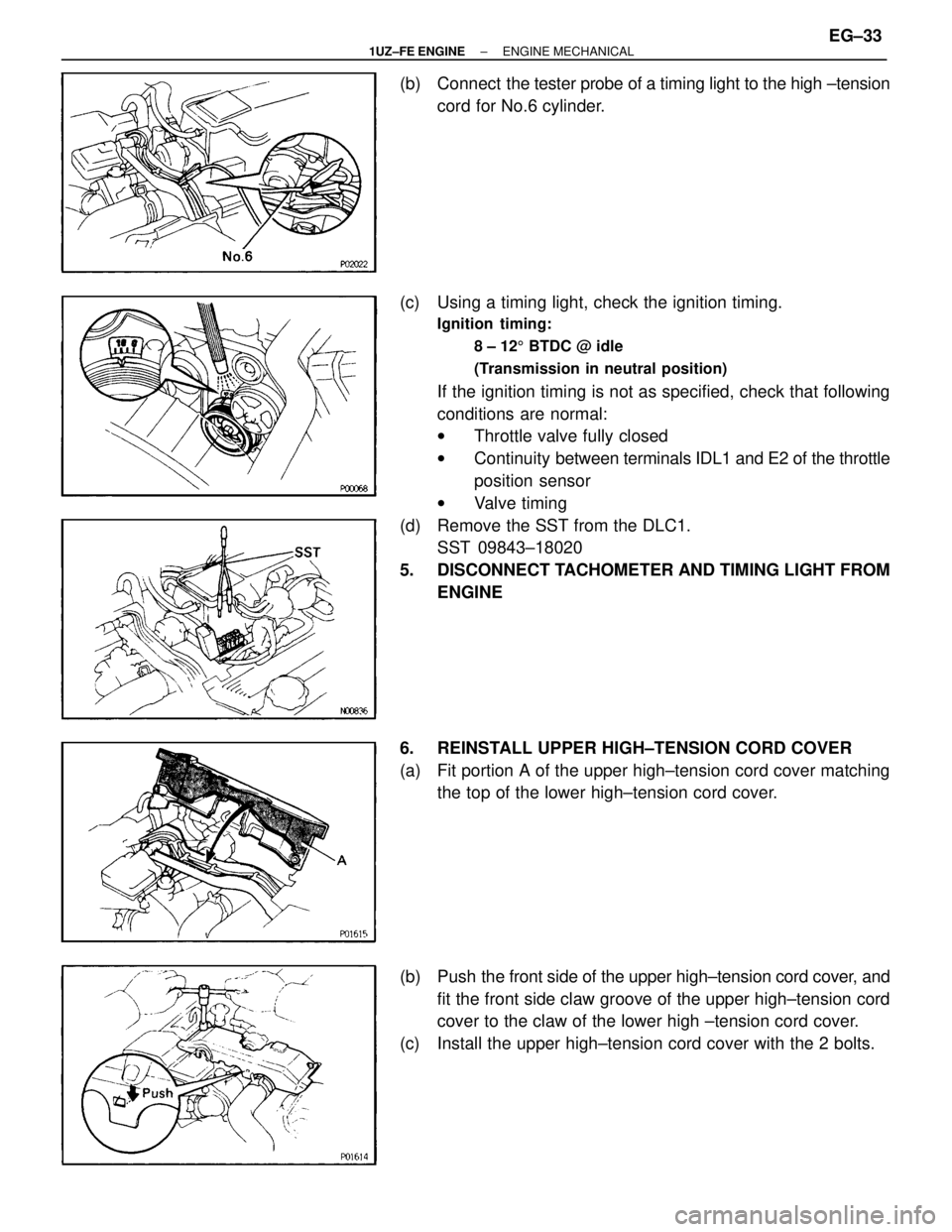
(b) Connect the tester probe of a timing light to the high ±tension
cord for No.6 cylinder.
(c) Using a timing light, check the ignition timing.
Ignition timing: 8 ± 12 5 BTDC @ idle
(Transmission in neutral position)
If the ignition timing is not as specified, check that following
conditions are normal:
w Throttle valve fully closed
w Continuity between terminals IDL1 and E2 of the throttle
position sensor
w Valve timing
(d) Remove the SST from the DLC1. SST 09843±18020
5. DISCONNECT TACHOMETER AND TIMING LIGHT FROM ENGINE
6. REINSTALL UPPER HIGH±TENSION CORD COVER
(a) Fit portion A of the upper high±tension cord cover matching the top of the lower high±tension cord cover.
(b) Push the front side of the upper high±tension cord cover, and
fit the front side claw groove of the upper high±tension cord
cover to the claw of the lower high ±tension cord cover.
(c) Install the upper high±tension cord cover with the 2 bolts.
±
1UZ±FE ENGINE ENGINE MECHANICALEG±33
WhereEverybodyKnowsYourName
Page 1412 of 4087
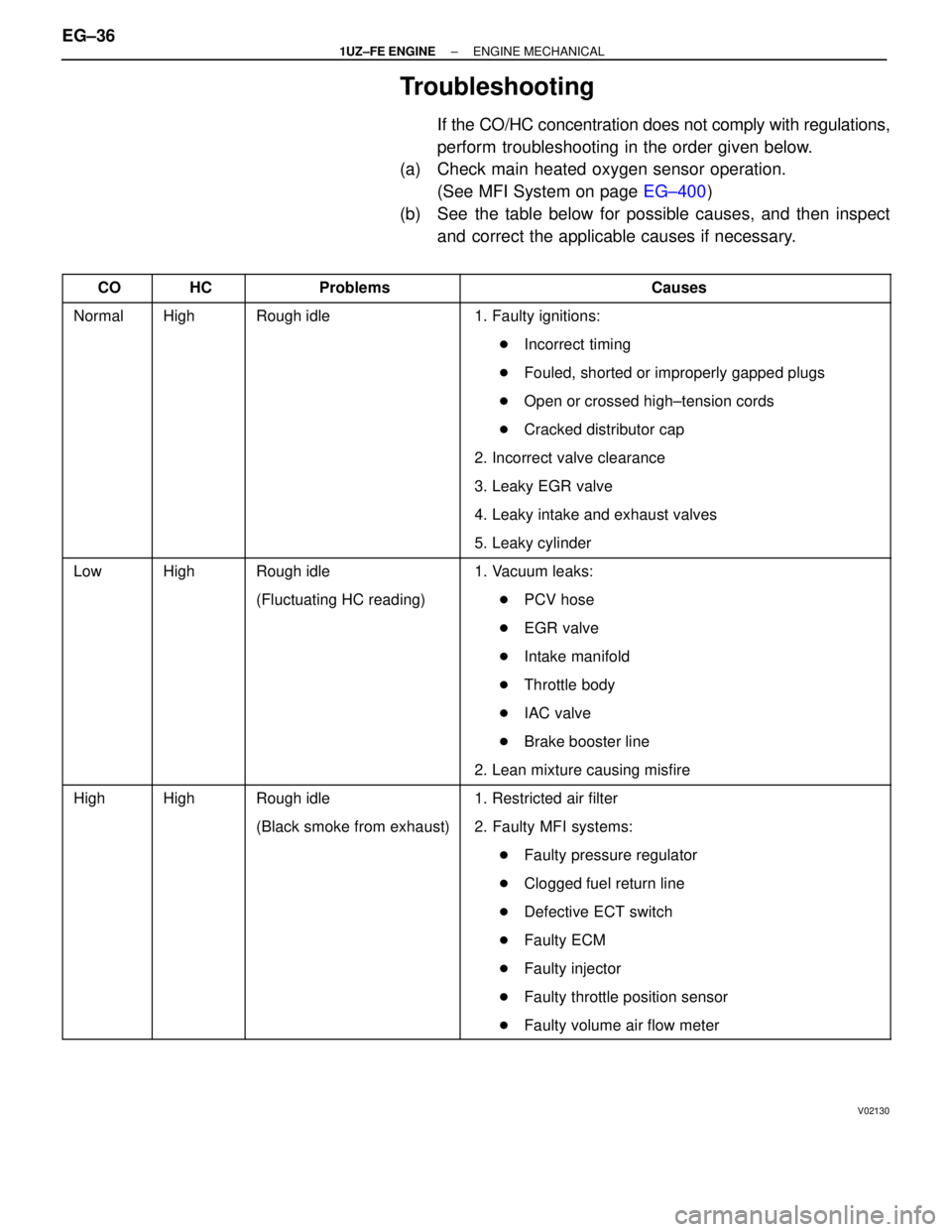
Troubleshooting
If the CO/HC concentration does not comply with regulations,
perform troubleshooting in the order given below.
(a) Check main heated oxygen sensor operation.
(See MFI System on page EG±400)
(b) See the table below for possible causes, and then inspect and correct the applicable causes if necessary.
CO HC Problems\
\
Causes
Normal High Rough idle\
\
1. Faulty ignitions:
\
\
Incorrect timing
\
\
Fouled, shorted or improperly gapped plugs
\
\
Open or crossed high±tension cords
\
\
Cracked distributor cap
\
\
2. Incorrect valve clearance \
\
3. Leaky EGR valve
\
\
4. Leaky intake and exhaust valves
\
\
5. Leaky cylinder
Low High Rough idle\
\
1. Vacuum leaks:
(Fluctuating HC reading)\
\
PCV hose
\
\
EGR valve
\
\
Intake manifold
\
\
Throttle body
\
\
IAC valve
\
\
Brake booster line
\
\
2. Lean mixture causing misfire
High
High
Rough idle\
\
1. Restricted air filter
(Black smoke from exhaust)\
\
2. Faulty MFI systems:
\
\
Faulty pressure regulator
\
\
Clogged fuel return line
\
\
Defective ECT switch \
\
Faulty ECM
\
\
Faulty injector
\
\
Faulty throttle position sensor
\
\
Faulty volume air flow meter
V02130
EG±36±
1UZ±FE ENGINE ENGINE MECHANICAL
WhereEverybodyKnowsYourName
Page 1416 of 4087
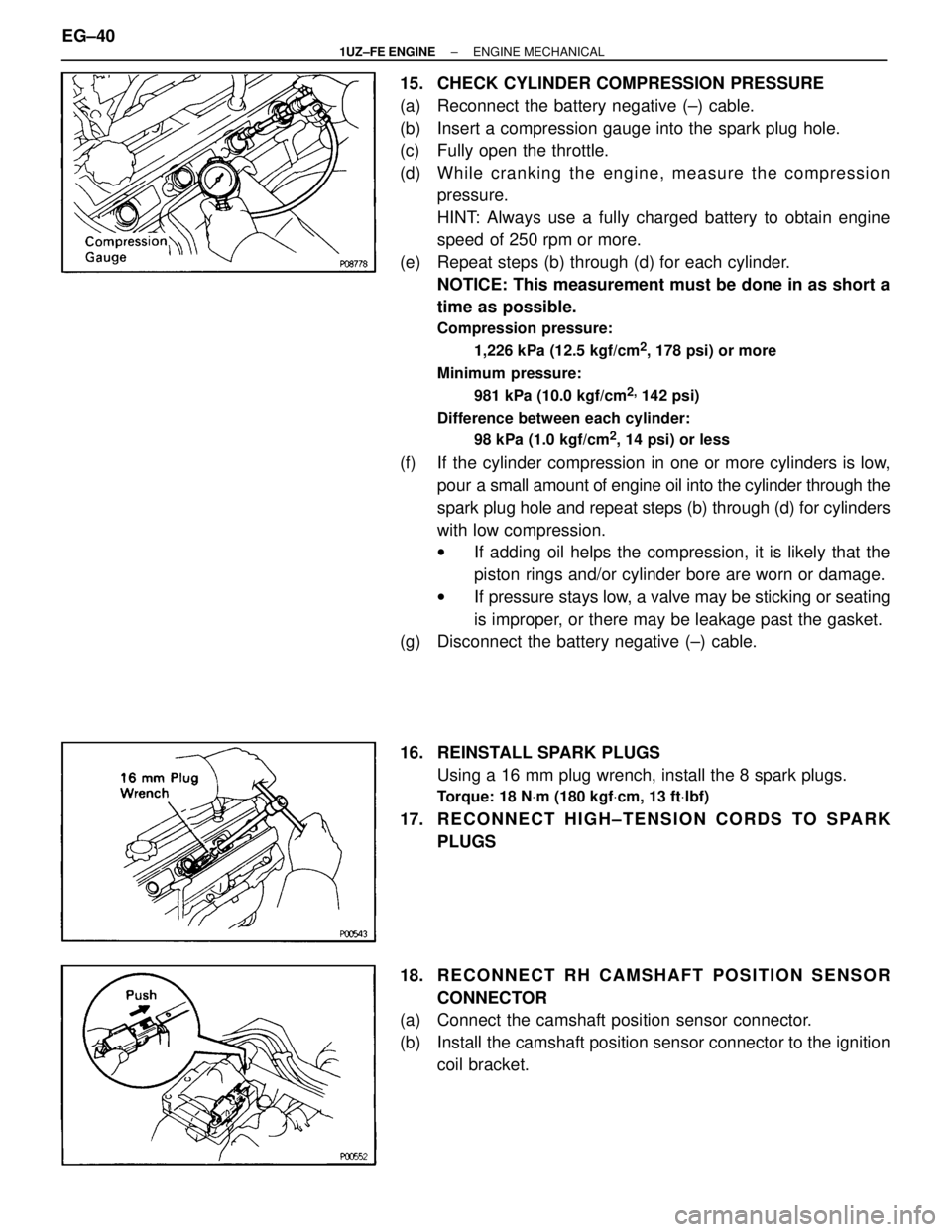
15. CHECK CYLINDER COMPRESSION PRESSURE
(a) Reconnect the battery negative (±) cable.
(b) Insert a compression gauge into the spark plug hole.
(c) Fully open the throttle.
(d) Wh ile cra n kin g th e en g in e , me a su re th e co mp re ssio npressure.
HINT: Always use a fully charged battery to obtain engine
speed of 250 rpm or more.
(e) Repeat steps (b) through (d) for each cylinder. NOTICE: This measurement must be done in as short a
time as possible.
Compression pressure:
1,226 kPa (12.5 kgf/cm
2, 178 psi) or more
Minimum pressure: 981 kPa (10.0 kgf/cm
2, 142 psi)
Difference between each cylinder: 98 kPa (1.0 kgf/cm
2, 14 psi) or less
(f) If the cylinder compression in one or more cylinders is low,pour a sm all amount of engine oil into the cylinder through the
spark plug hole and repeat steps (b) through (d) for cylinders
with low compression.
w If adding oil helps the compression, it is likely that the
piston rings and/or cylinder bore are worn or damage.
w If pressure stays low, a valve may be sticking or seating
is improper, or there may be leakage past the gasket.
(g) Disconnect the battery negative (±) cable.
16. REINSTALL SPARK PLUGS
Using a 16 mm plug wrench, install the 8 spark plugs.
Torque: 18 N Vm (180 kgf Vcm, 13 ft Vlbf)
17. R E C O N N E C T H I G H ± T E N S I O N C O R D S TO S PA R K
PLUGS
18. RECONNECT RH CAMSHAFT POSITION SENSOR CONNECTOR
(a) Connect the camshaft position sensor connector.
(b) Install the camshaft position sensor connector to the ignition
coil bracket.
EG±40
±
1UZ±FE ENGINE ENGINE MECHANICAL
WhereEverybodyKnowsYourName