alternator MITSUBISHI ECLIPSE 1991 Owner's Manual
[x] Cancel search | Manufacturer: MITSUBISHI, Model Year: 1991, Model line: ECLIPSE, Model: MITSUBISHI ECLIPSE 1991Pages: 1216, PDF Size: 67.42 MB
Page 381 of 1216
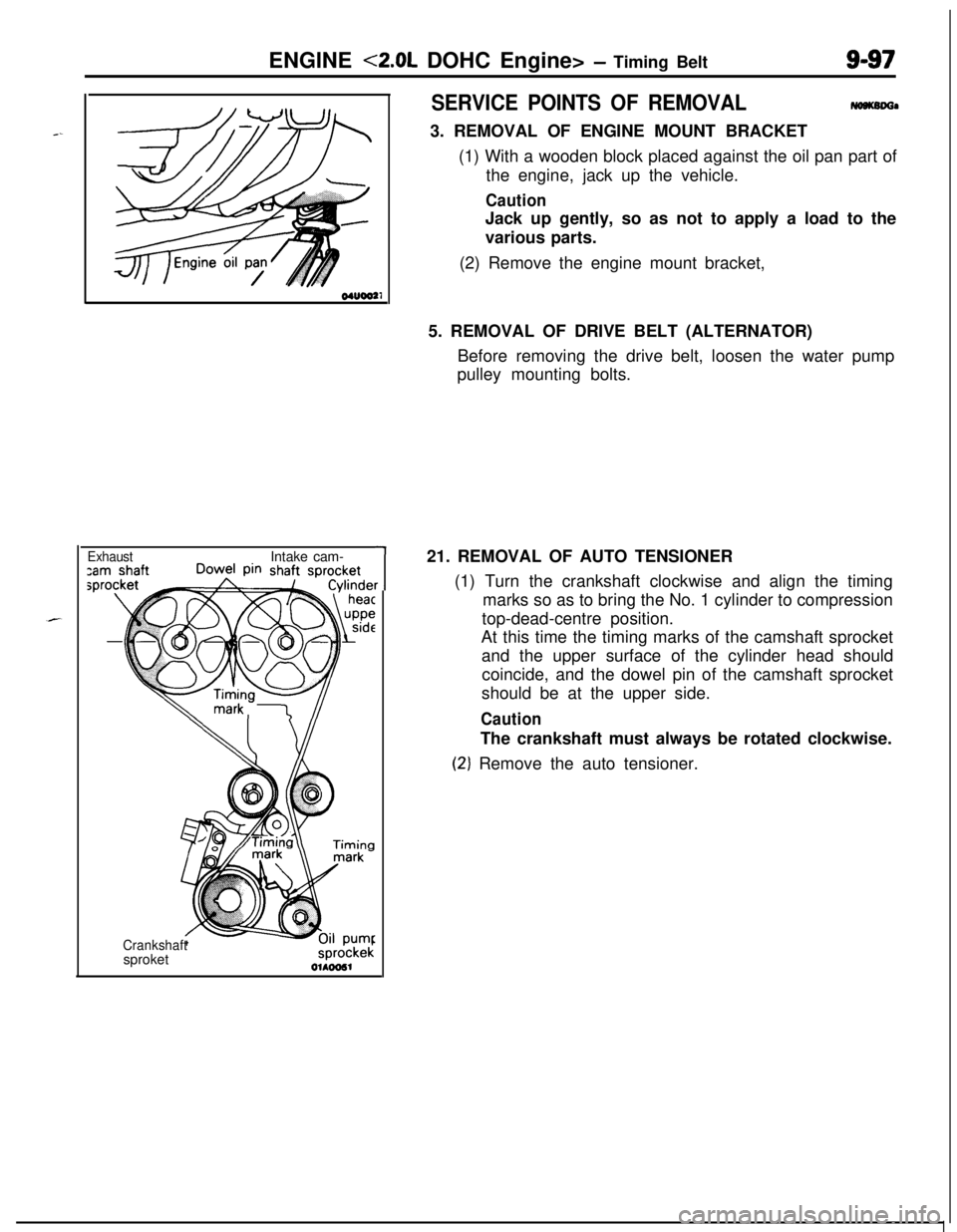
--ENGINE
<2.0L DOHC Engine> - Timing Belt9-97
ExhaustIntake cam-
CrankshaftsproketsprockekOlhw51
1r
SERVICE POINTS OF REMOVAL-a3. REMOVAL OF ENGINE MOUNT BRACKET
(1) With a wooden block placed against the oil pan part of
the engine, jack up the vehicle.
CautionJack up gently, so as not to apply a load to the
various parts.
(2) Remove the engine mount bracket,
5. REMOVAL OF DRIVE BELT (ALTERNATOR)
Before removing the drive belt, loosen the water pump
pulley mounting bolts.
21. REMOVAL OF AUTO TENSIONER
(1) Turn the crankshaft clockwise and align the timing
marks so as to bring the No. 1 cylinder to compression
top-dead-centre position.
At this time the timing marks of the camshaft sprocket
and the upper surface of the cylinder head should
coincide, and the dowel pin of the camshaft sprocket
should be at the upper side.
CautionThe crankshaft must always be rotated clockwise.
(2‘) Remove the auto tensioner.
Page 392 of 1216
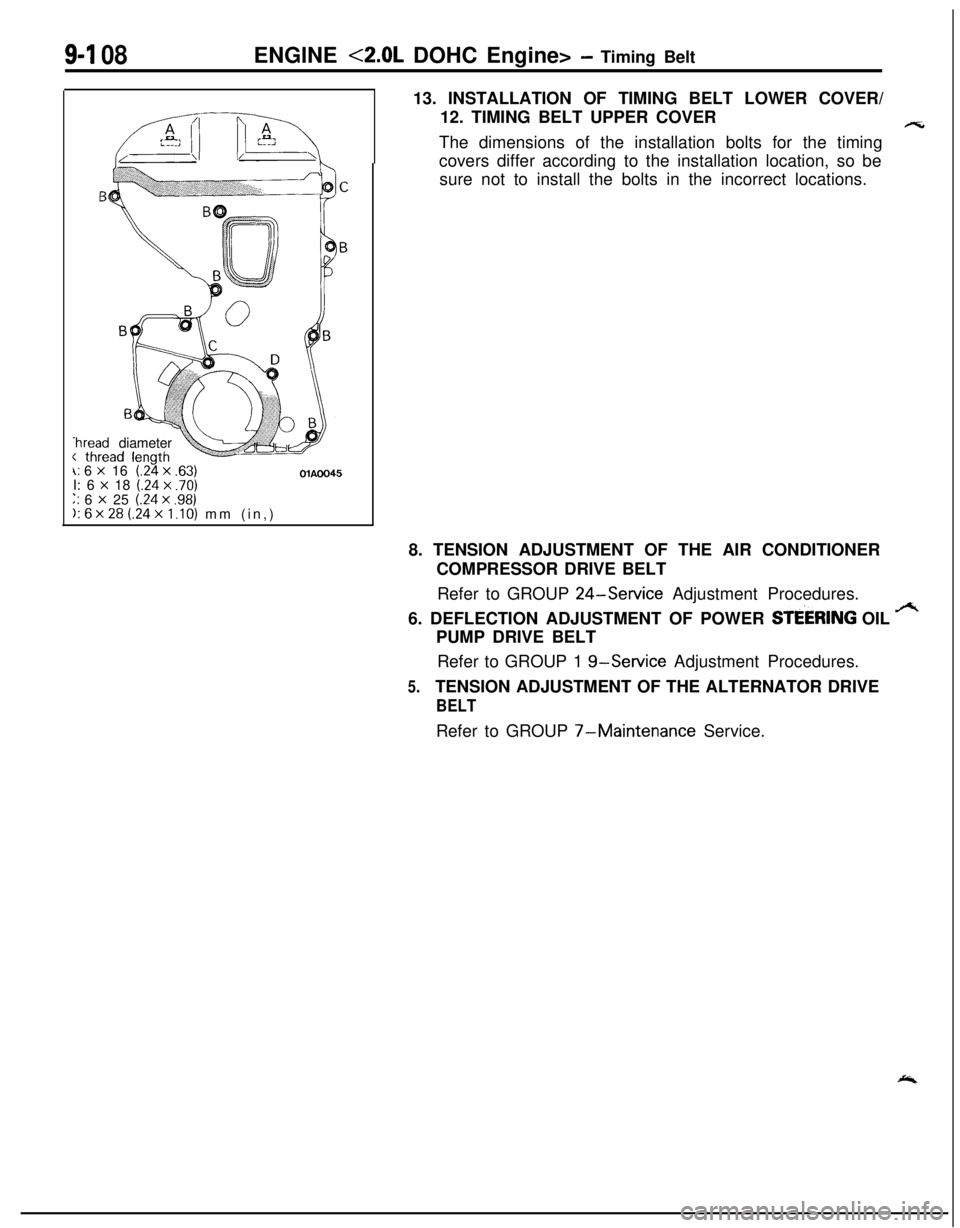
9-l 08ENGINE <2.0L DOHC Engine> - Timing Belt
.hread diameter
\: 6 x 16(24 x .63)OlAOO45I: 6 x 18 (.24x .70)‘. 6 x 25 (.24 x .98);. 6x28 (.24~1.10) mm (in,)13. INSTALLATION OF TIMING BELT LOWER COVER/
12. TIMING BELT UPPER COVER
F-sThe dimensions of the installation bolts for the timing
covers differ according to the installation location, so be
sure not to install the bolts in the incorrect locations.
8. TENSION ADJUSTMENT OF THE AIR CONDITIONER
COMPRESSOR DRIVE BELT
Refer to GROUP
24-Service Adjustment Procedures.
6. DEFLECTION ADJUSTMENT OF POWER
STEERING OIL .++PUMP DRIVE BELT
Refer to GROUP 1
g-Service Adjustment Procedures.
5.TENSION ADJUSTMENT OF THE ALTERNATOR DRIVE
BELTRefer to GROUP
7-Maintenance Service.
Page 688 of 1216
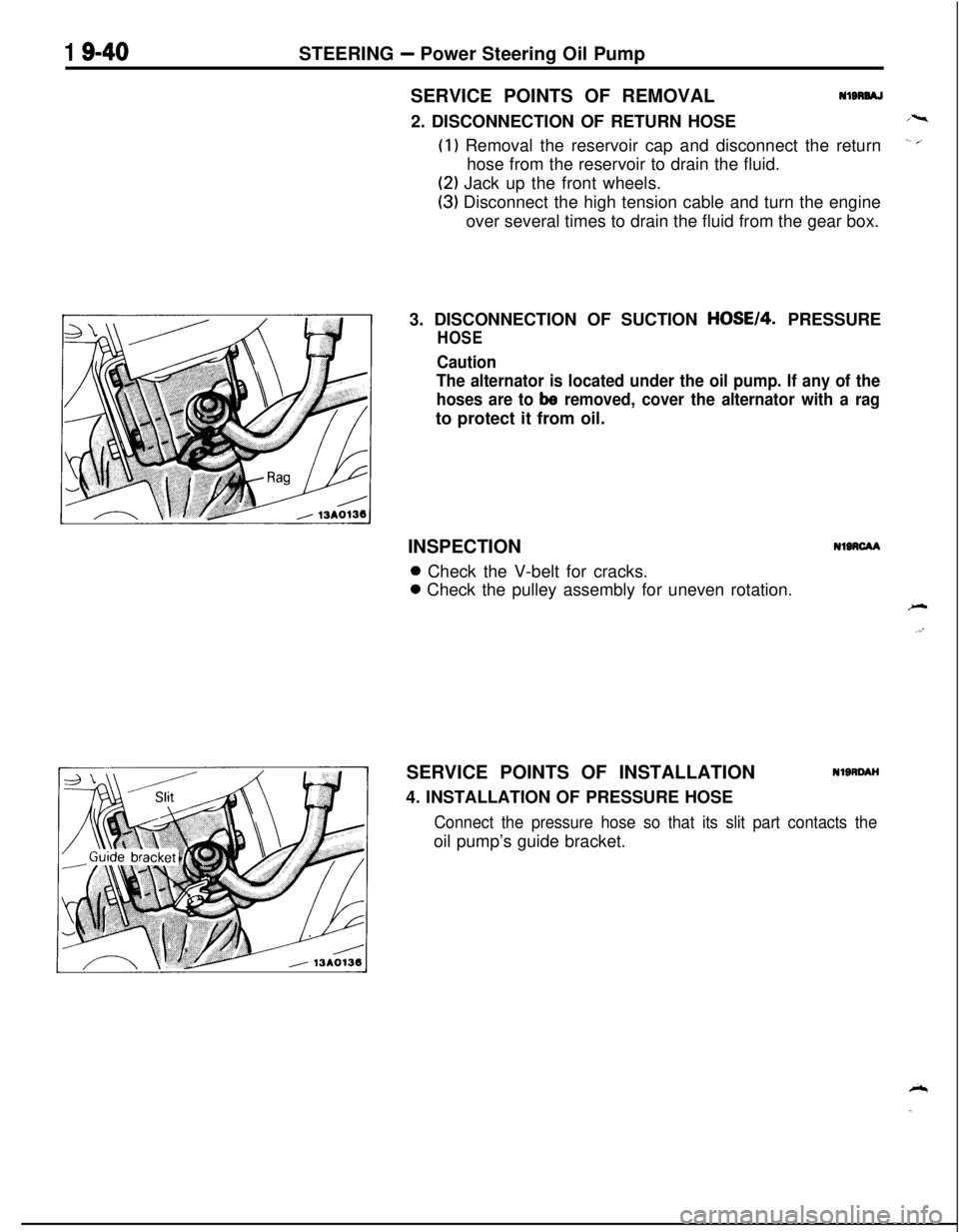
1 S-40STEERING - Power Steering Oil Pump
SERVICE POINTS OF REMOVAL
Nl8RW2. DISCONNECTION OF RETURN HOSE
(1) Removal the reservoir cap and disconnect the return
hose from the reservoir to drain the fluid.
(2) Jack up the front wheels.
(3) Disconnect the high tension cable and turn the engine
over several times to drain the fluid from the gear box.
3. DISCONNECTION OF SUCTION
HOSE14. PRESSURE
HOSE
Caution
The alternator is located under the oil pump. If any of the
hoses are to
be removed, cover the alternator with a ragto protect it from oil.
INSPECTION
NIRCAA0 Check the V-belt for cracks.0 Check the pulley assembly for uneven rotation.
SERVICE POINTS OF INSTALLATION
4. INSTALLATION OF PRESSURE HOSE
NlSRDAH
Connect the pressure hose so that its slit part contacts theoil pump’s guide bracket.
Page 1168 of 1216
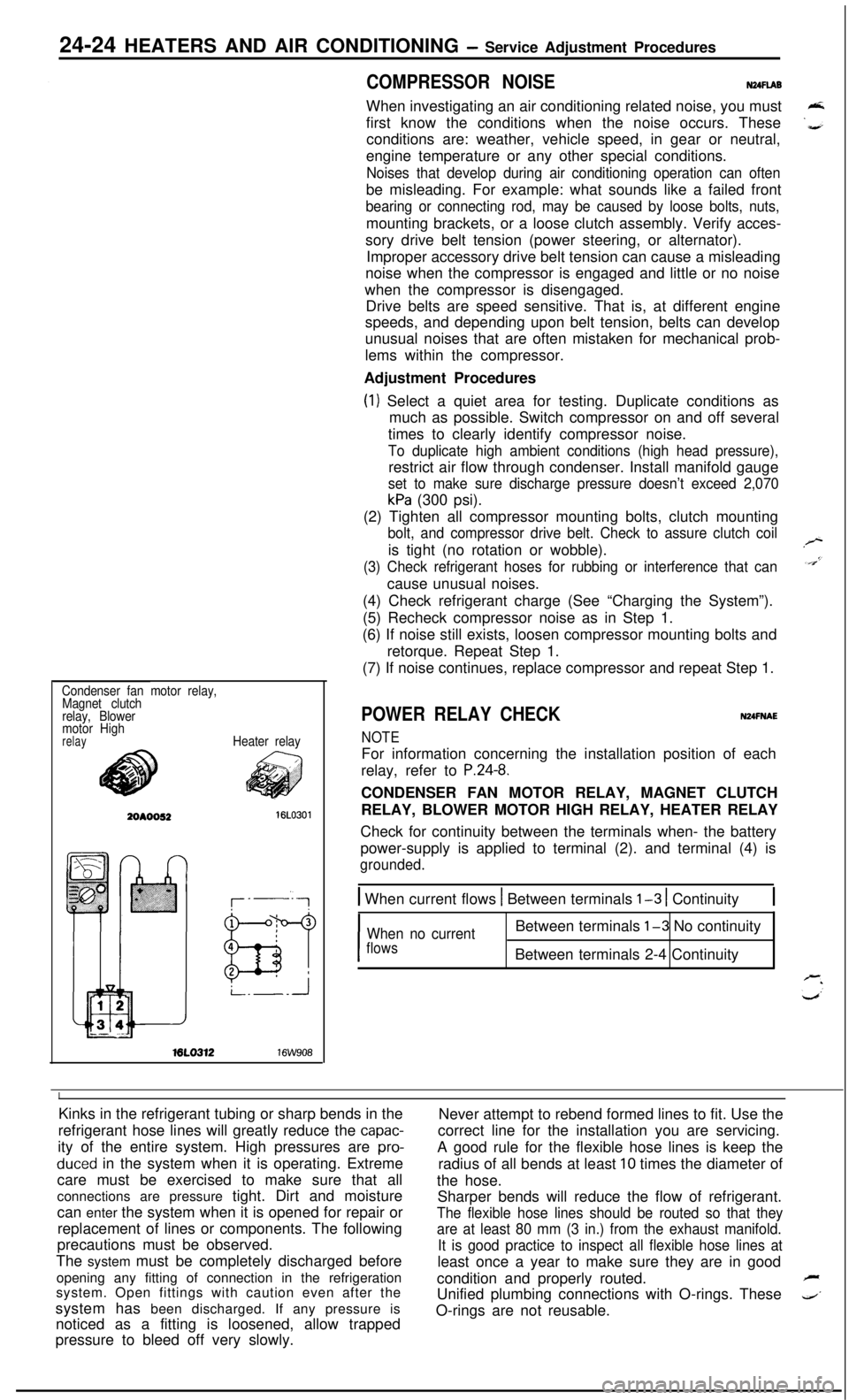
24-24 HEATERS AND AIR CONDITIONING - Service Adjustment Procedures
COMPRESSOR NOISENUFIABWhen investigating an air conditioning related noise, you must
first know the conditions when the noise occurs. These
conditions are: weather, vehicle speed, in gear or neutral,
engine temperature or any other special conditions.
Noises that develop during air conditioning operation can oftenbe misleading. For example: what sounds like a failed front
bearing or connecting rod, may be caused by loose bolts, nuts,mounting brackets, or a loose clutch assembly. Verify acces-
sory drive belt tension (power steering, or alternator).
Improper accessory drive belt tension can cause a misleading
noise when the compressor is engaged and little or no noise
when the compressor is disengaged.
Drive belts are speed sensitive. That is, at different engine
speeds, and depending upon belt tension, belts can develop
unusual noises that are often mistaken for mechanical prob-
lems within the compressor.
Adjustment Procedures
(1) Select a quiet area for testing. Duplicate conditions as
much as possible. Switch compressor on and off several
times to clearly identify compressor noise.
To duplicate high ambient conditions (high head pressure),restrict air flow through condenser. Install manifold gauge
set to make sure discharge pressure doesn’t exceed 2,070
kPa (300 psi).
(2) Tighten all compressor mounting bolts, clutch mounting
bolt, and compressor drive belt. Check to assure clutch coilis tight (no rotation or wobble).
(3) Check refrigerant hoses for rubbing or interference that cancause unusual noises.
(4) Check refrigerant charge (See “Charging the System”).
(5) Recheck compressor noise as in Step 1.
(6) If noise still exists, loosen compressor mounting bolts and
retorque. Repeat Step 1.
(7) If noise continues, replace compressor and repeat Step 1.
Condenser fan motor relay,
Magnet clutch
relay, Blower
motor High
relayHeater relayML0312
16W908
POWER RELAY CHECKNUFNAE
NOTEFor information concerning the installation position of each
relay, refer to
P.24-8.CONDENSER FAN MOTOR RELAY, MAGNET CLUTCH
RELAY, BLOWER MOTOR HIGH RELAY, HEATER RELAY
Check for continuity between the terminals when- the battery
power-supply is applied to terminal (2). and terminal (4) is
grounded.
1 When current flows 1 Between terminals l-3 1 Continuity1
I
When no currentBetween terminals l-3 No continuity
flowsBetween terminals 2-4 Continuity
IKinks in the refrigerant tubing or sharp bends in the
Never attempt to rebend formed lines to fit. Use the
refrigerant hose lines will greatly reduce the
capac-correct line for the installation you are servicing.
ity of the entire system. High pressures are
pro-A good rule for the flexible hose lines is keep the
duced in the system when it is operating. Extreme
radius of all bends at least 10 times the diameter of
care must be exercised to make sure that all
the hose.
connections are pressure tight. Dirt and moisture
Sharper bends will reduce the flow of refrigerant.
can enter the system when it is opened for repair or
The flexible hose lines should be routed so that theyreplacement of lines or components. The following
are at least 80 mm (3 in.) from the exhaust manifold.precautions must be observed.
It is good practice to inspect all flexible hose lines atThe system must be completely discharged before
least once a year to make sure they are in good
opening any fitting of connection in the refrigeration
condition and properly routed.
Fsystem. Open fittings with caution even after the
Unified plumbing connections with O-rings. These
4’system has been discharged. If any pressure is
noticed as a fitting is loosened, allow trappedO-rings are not reusable.
pressure to bleed off very slowly.
Page 1184 of 1216
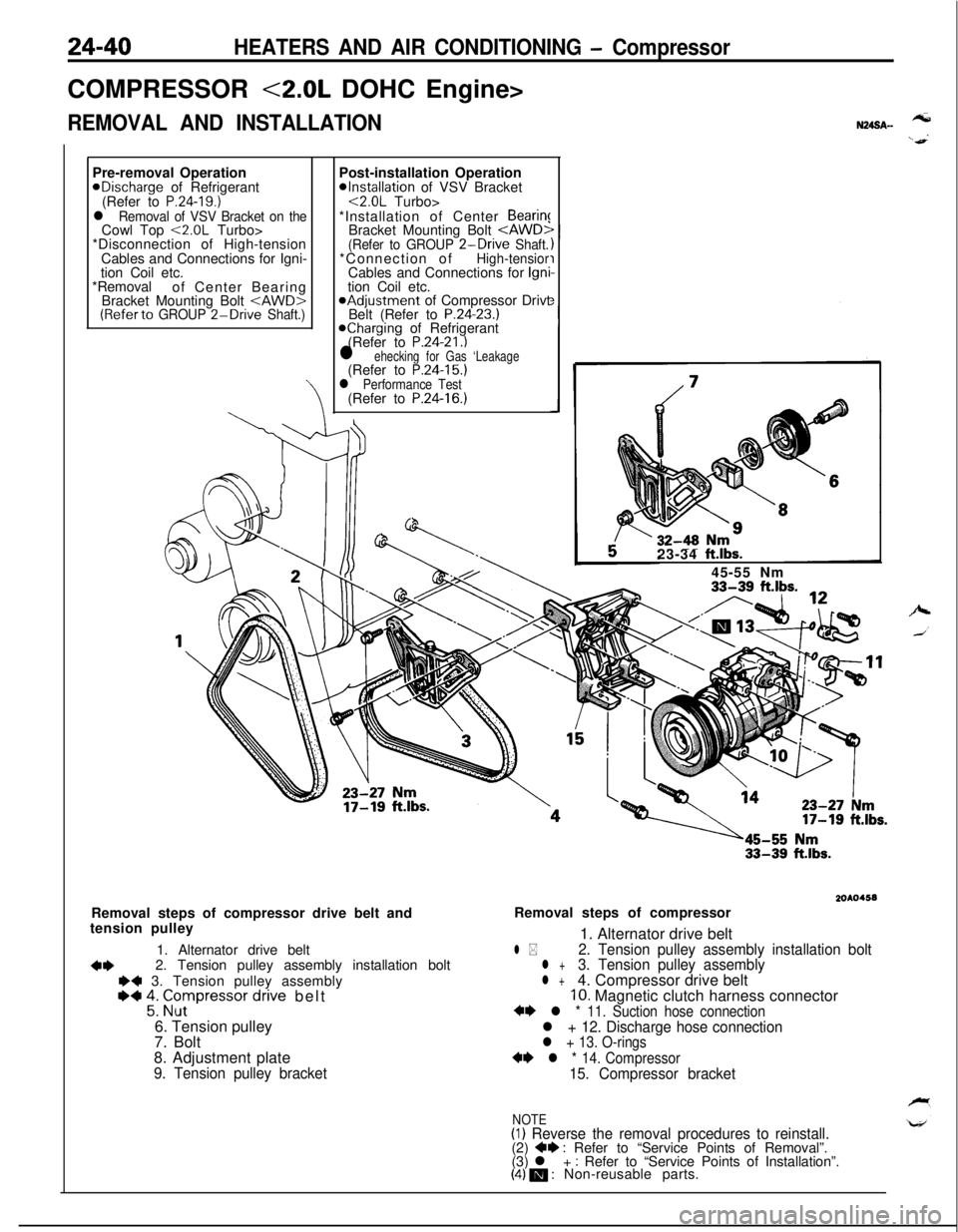
24-40HEATERS AND AIR CONDITIONING - CompressorCOMPRESSOR
<2.0L DOHC Engine>
REMOVAL AND INSTALLATIONPre-removal OperationaDischarge of Refrigerant
(Refer to
P.24-19.)l Removal of VSV Bracket on theCowl Top <2.0L Turbo>
*Disconnection of High-tension
Cables and Connections for Igni-
tion Coil etc.
*Removal
of Center Bearing
Bracket Mounting Bolt
*Installation of VSV Bracket<2.0L Turbo>
*Installation of Center
Bearin!Bracket Mounting Bolt
Belt (Refer to P.24-23.)Kharging of Refrigerant
(Refer to P.24-21.)l ehecking for Gas ‘Leakage(Refer to P.24-15.)l Performance Test(Refer to P.24-16.)
N24SA.-tension pulley
1. Alternator drive belt
4*2. Tension pulley assembly installation boltI)+ 3. Tension pulley assembly~~ 2: Grpressor dnve belt
6. Tension pulley
7. Bolt
8. Adjustment plate
9. Tension pulley bracket23-34
ft.lbs.45-55 Nm
33-39 ft.lbs.
2OAO4.58Removal steps of compressor drive belt andRemoval steps of compressor
1. Alternator drive belt
l *2. Tension pulley assembly installation boltl +3. Tension pulley assemblyl +4. Compressor drive belt10. Magnetic clutch harness connector+* l * 11. Suction hose connectionl + 12. Discharge hose connectionl + 13. O-rings
** l * 14. Compressor15. Compressor bracket
NOTE(I) Reverse the removal procedures to reinstall.(2) +e : Refer to “Service Points of Removal”.
(3) l + : Refer to “Service Points of Installation”.(4) m : Non-reusable parts.