weight MITSUBISHI LANCER 2006 Workshop Manual
[x] Cancel search | Manufacturer: MITSUBISHI, Model Year: 2006, Model line: LANCER, Model: MITSUBISHI LANCER 2006Pages: 800, PDF Size: 45.03 MB
Page 141 of 800
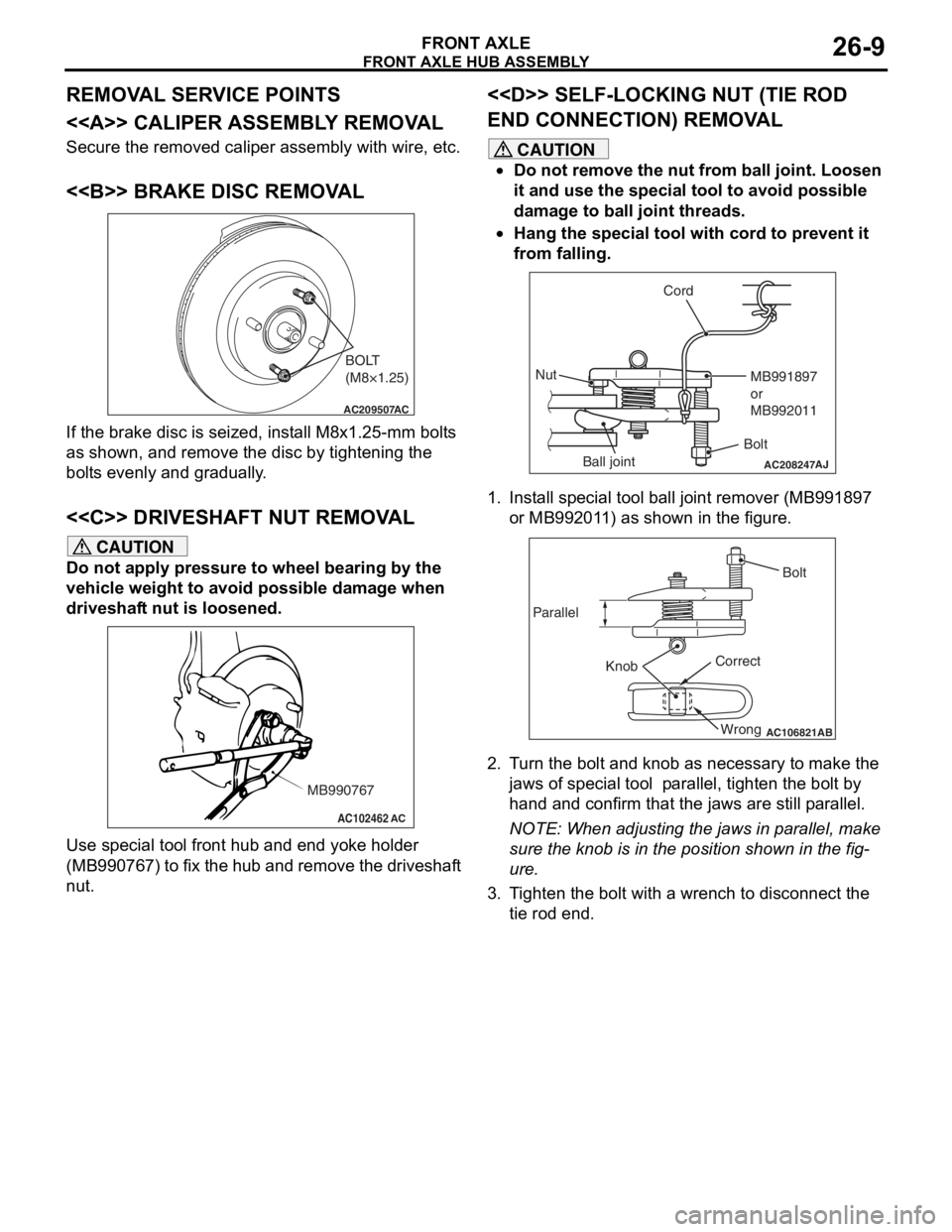
Page 147 of 800
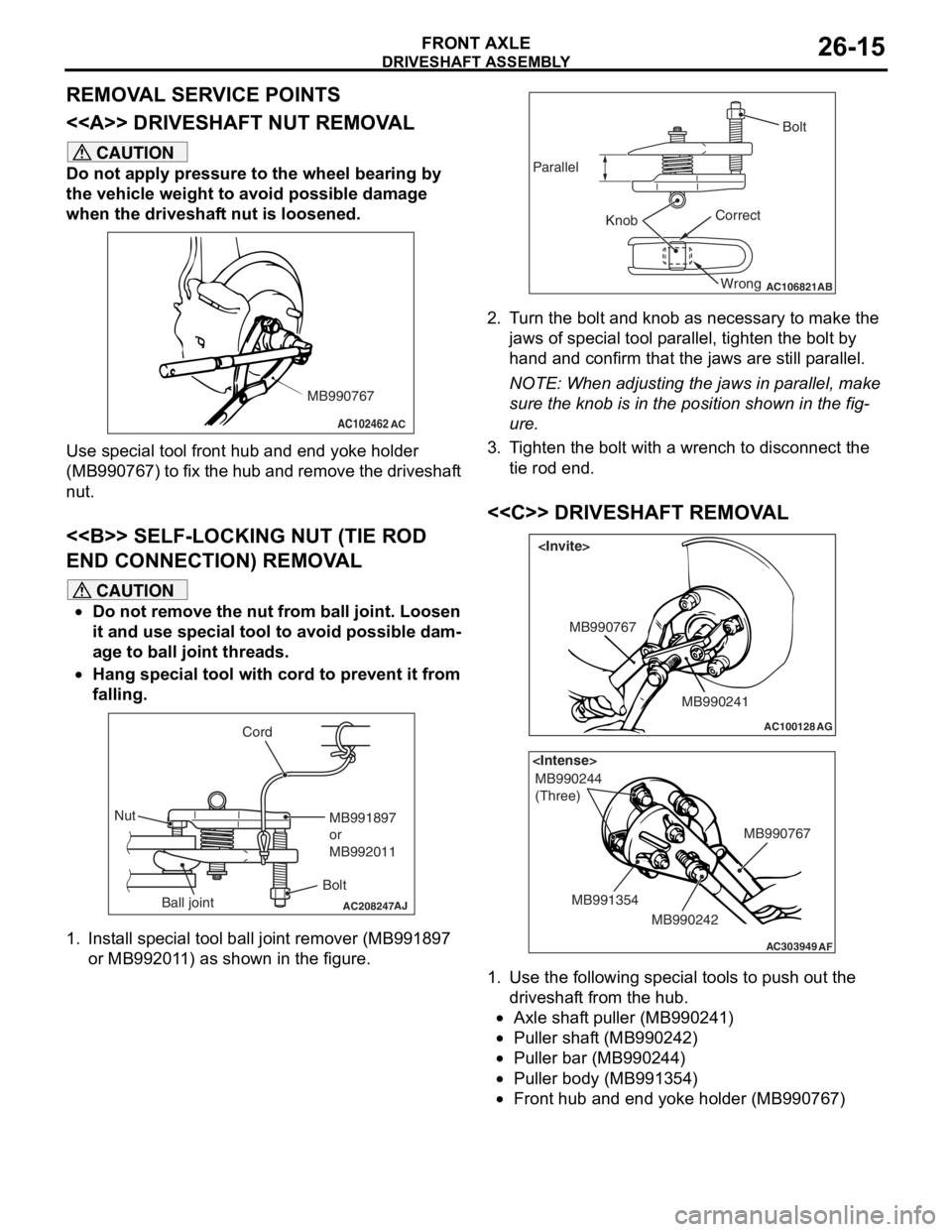
Page 148 of 800
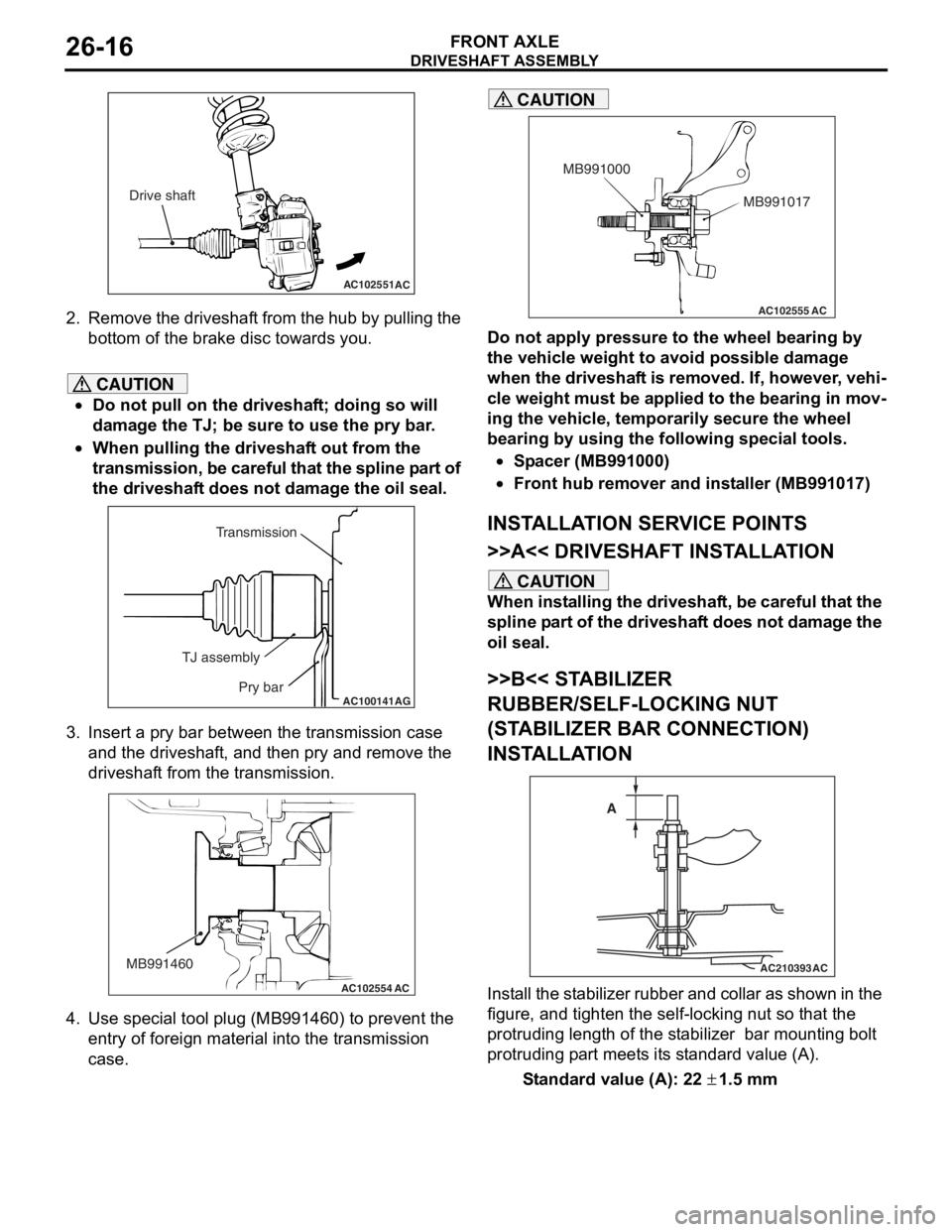
AC102551AC
Drive shaft
DRIVESHAFT ASSEMBL Y
FRONT AXLE26-16
2.Remove th e dr ivesh a f t from th e h ub b y p u lling the
bo ttom of the brake disc toward s you.
CAUTION
•Do not pull on the driveshaft; doing so will
damage the TJ; be sure to use the pry bar.
•
AC100141
Transmission
TJ assembly Pry bar
AG
When pulling the driveshaft out from the
transmission, be careful that the spline part of
the driveshaft does not damage the oil seal.
3. Insert a pry bar between the transmission case and the driveshaft, and then pry and remove the
driveshaft from the transmission.
AC102554
MB991460
AC
4. Use special tool plug (MB991460) to prevent the
entry of foreign material into the transmission
case.
AC102555 AC
MB991017
MB991000
CAUTION
Do not apply pressure to the wheel bearing by
the vehicle weight to avoid possible damage
when the driveshaft is removed. If, however, vehi
-
cle weight must be applied to the bearing in mov-
ing the vehicle, temporarily secure the wheel
bearing by using the following special tools.
•Spacer (MB991000)
•Front hub remover and installer (MB991017)
INSTALLATION SERVICE POINTS
>>A<< DRIVESHAFT INSTALLATION
CAUTION
When installing the driveshaft, be careful that the
spline part of the driveshaft does not damage the
oil seal.
>>B<< STABILIZER
RUBBER/SELF-LOCKING NUT
(STABILIZER BAR CONNECTION)
INSTALLATION
AC210393
AC
A
Install the stabilizer rubber and collar as shown in the
figure, and tighten the self-locking nut so that the
protruding length of the stabilizer bar mounting bolt
protruding part meets its standard value (A).
Standard value (A): 22 ± 1.5 mm
Page 161 of 800
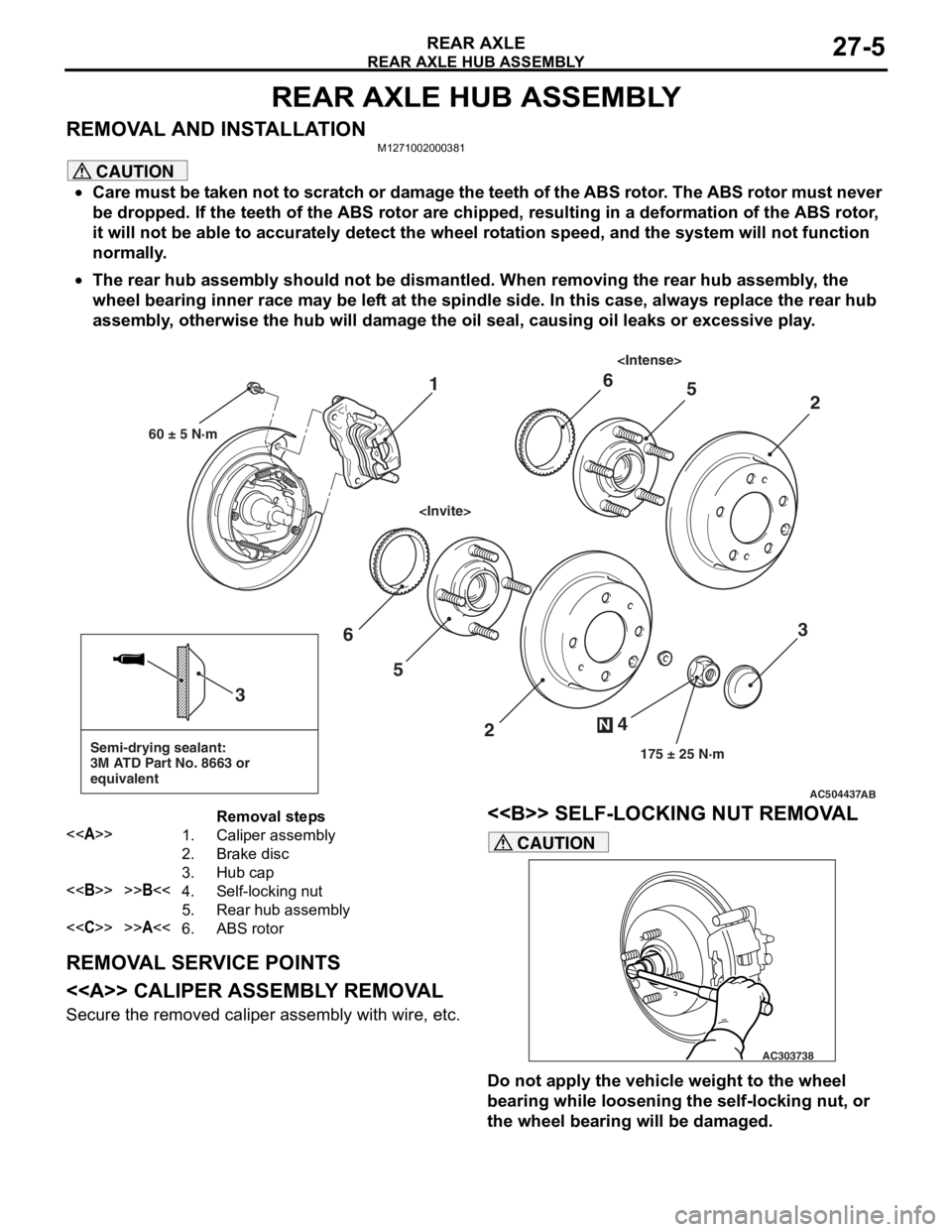
REAR AXLE HUB ASSEMBLY
REAR AXLE27-5
REAR AXLE HUB ASSEMBLY
REMOVAL AND INSTALLATIONM1271002000381
CAUTION
•Care must be taken not to scratch or damage the teeth of the ABS rotor. The ABS rotor must never
be dropped. If the teeth of the ABS rotor are chipped, resulting in a deformation of the ABS rotor,
it will not be able to accurately detect the wheel rotation speed, and the system will not function
normally.
•
AC504437
Semi-drying sealant:
3M ATD Part No. 8663 or
equivalent
2
3
5
6
4
N
175 ± 25 N·m
3
AB
1
60 ± 5 N·m
2
56
Removal steps
<>1.Caliper assembly
2.Brake disc
3.Hub cap
<>>>B<<4.Self-locking nut
5.Rear hub assembly
<
The rear hub assembly should not be dismantled. When removing the rear hub assembly, the
wheel bearing inner race may be left at the spindle side. In this case, always replace the rear hub
assembly, otherwise the hub will damage the oil seal, causing oil leaks or excessive play.
REMOVAL SERVICE POINTS
<> CALIPER ASSEMBLY REMOVAL
Secure the removed caliper assembly with wire, etc.
<> SELF-LOCKING NUT REMOVAL
AC303738
CAUTION
Do not apply the vehicle weight to the wheel
bearing while loosening the self-locking nut, or
the wheel bearing will be damaged.
Page 166 of 800
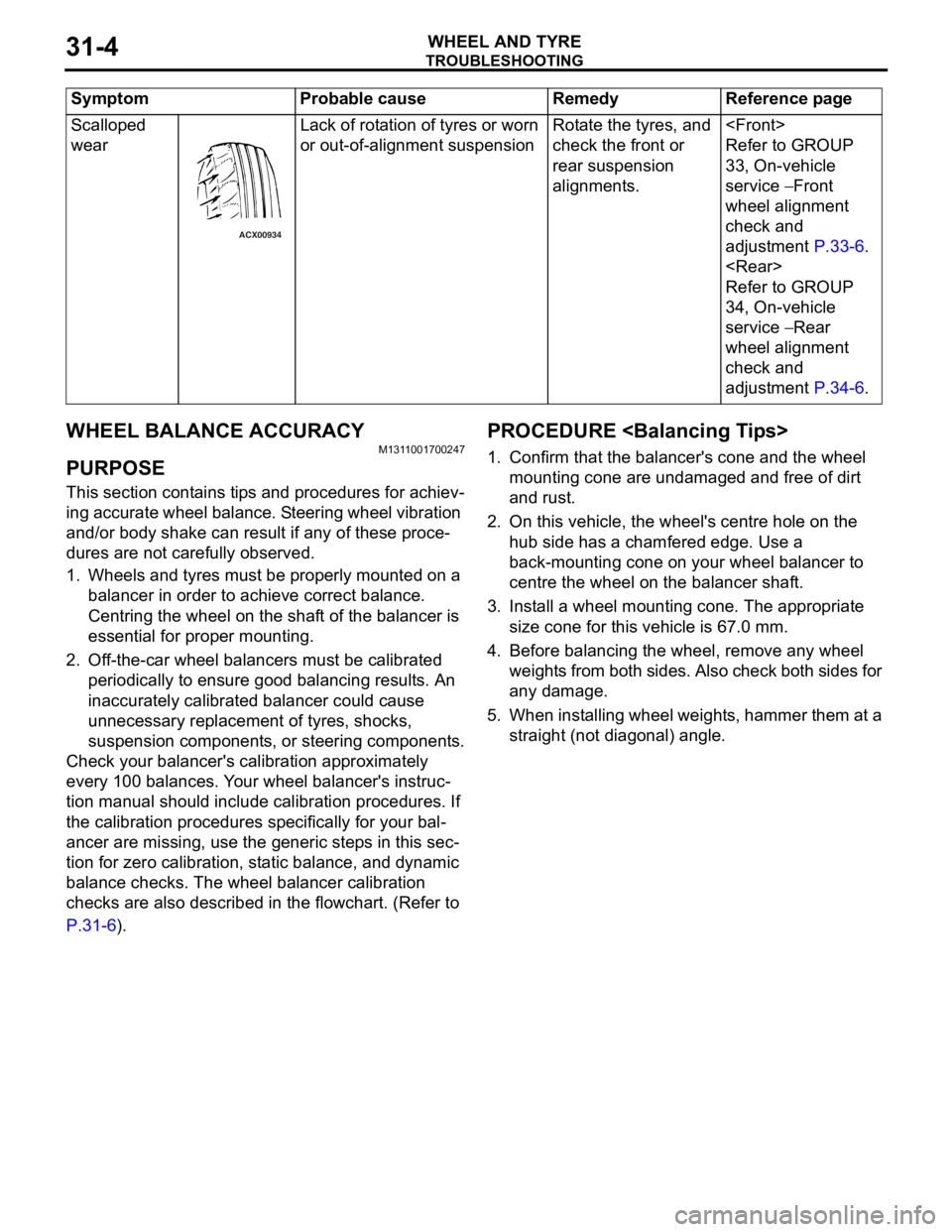
TROUBLESHOOTING
WHEEL AND TYRE31-4
WHEEL BALANCE ACCURACY
M1311001700247
PURPOSE
This section contains tips and procedures for achiev-
ing accurate wheel balance. Steering wheel vibration
and/or body shake can result if any of these proce
-
dures are not carefully observed.
1. Wheels and tyres must be properly mounted on a balancer in order to achieve correct balance.
Centring the wheel on the shaft of the balancer is
essential for proper mounting.
2. Off-the-car wheel balancers must be calibrated periodically to ensure good balancing results. An
inaccurately calibrated balancer could cause
unnecessary replacement of tyres, shocks,
suspension components, or steering components.
Check your balancer's calibration approximately
every 100 balances. Your wheel balancer's instruc
-
tion manual should include calibration procedures. If
the calibration procedures specifically for your bal
-
ancer are missing, use the generic steps in this sec-
tion for zero calibration, static balance, and dynamic
balance checks. The wheel balancer calibration
checks are also described in the flowchart. (Refer to
P.31-6).
PROCEDURE
1. Confirm that the balancer's cone and the wheel
mounting cone are undamaged and free of dirt
and rust.
2. On this vehicle, the wheel's centre hole on the hub side has a chamfered edge. Use a
back-mounting cone on your wheel balancer to
centre the wheel on the balancer shaft.
3. Install a wheel mounting cone. The appropriate size cone for this vehicle is 67.0 mm.
4. Before balancing the wheel, remove any wheel weights from both sides. Also check both sides for
any damage.
5. When installing wheel weights, hammer them at a straight (not diagonal) angle.
Scalloped
wear
ACX00934
Lack of rot a tio n of tyres or worn
or out-of-a
lign m ent suspensionRota te th e tyre s, an d
check the f
r ont or
rea
r suspension
alignment
s.
Refer to GROUP
33
, On -vehicle
serv
ic e
− Front
whee
l alignment
check and
ad
justmen t
P.33-6.
Refer to GROUP
34
, On -vehicle
serv
ic e
− Rear
whee
l alignment
check and
ad
justmen t
P.34-6.
Sy mptom P robable cause Reme dy Referen ce p a g e
Page 167 of 800
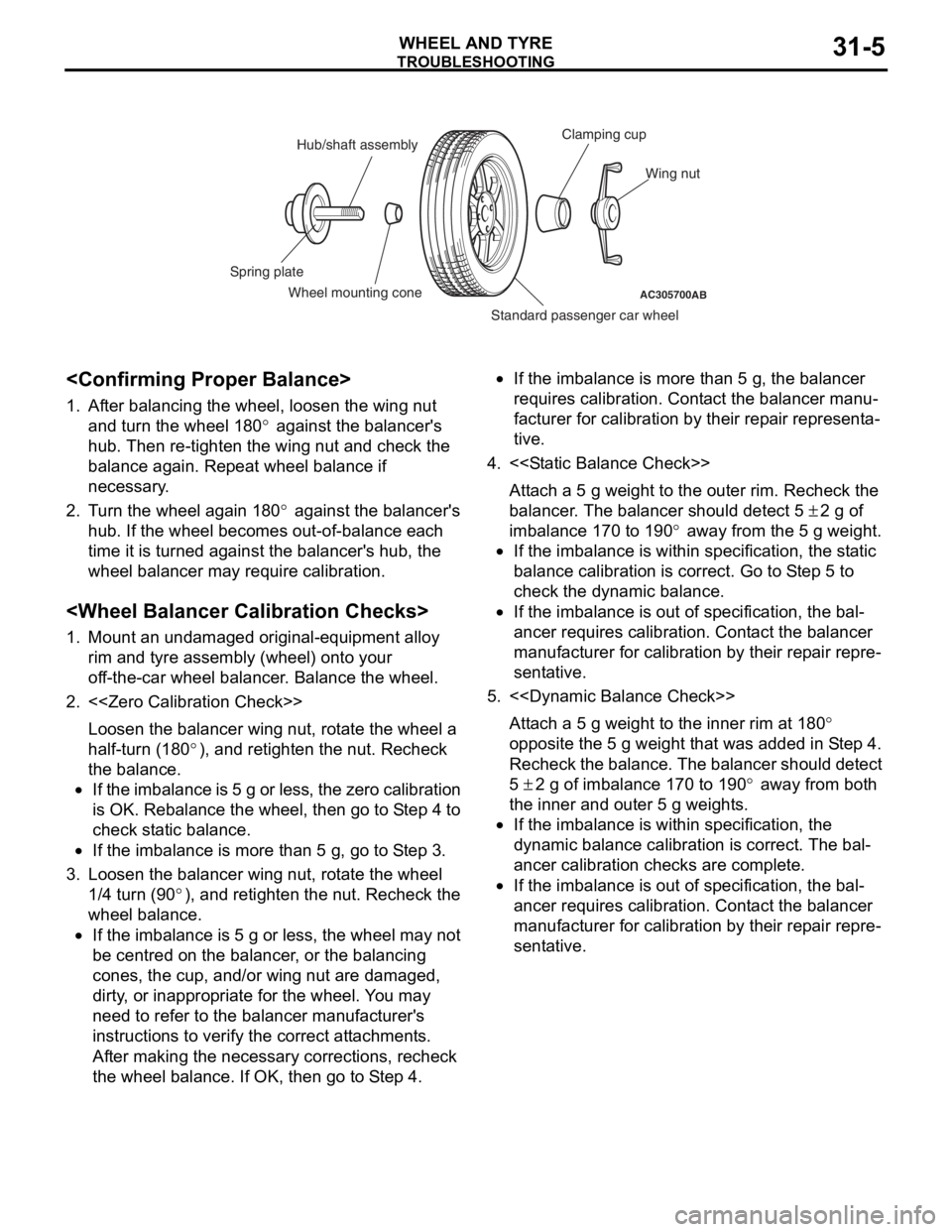
AC305700AB
Hub/shaft assemblyClamping cup
Wing nut
Standard passenger car wheel
Wheel mounting cone
Spring plate
TROUBLESH
OOTING
WHEEL AND TY RE31-5
1.Af ter ba lancing the whee l, lo osen the win g nut
an d turn the wheel 180
° against the b a lancer's
hu
b. The
n re-tighten t
he wing nut an d che c k the
ba
lance aga
in. Rep
eat whee l balance if
ne
cessary
.
2. T u rn the whee l aga in 18 0° against the bala n cer's
hu
b. If th
e wheel becomes out-o f-bala n ce each
time it is turne
d
against
the ba lancer's hub, th e
whee
l balancer ma
y req
u
ire calibration.
1.Mount an und amag ed origina l -equipme n t alloy
rim an d tyre assemb ly (wh eel) o n to your
of f-the-car whee l balancer . Bala nce the wheel.
2.<
Loosen the b a lancer win g nut, ro t a te the whe e l a
ha
lf-turn (180
°), and retig h ten th e nut. Recheck
th
e balance
.
•If t h e imb a la nce is 5 g o r l e ss, t he zero cali brati on
is OK. Reba
lance the whe e l, the n go to S t ep 4 to
ch
eck st atic balance.
•If the imbala n ce is more th an 5 g , go to S t e p 3.
3.Lo osen the b a lancer win g nut, ro t a te the whe e l
1/ 4 turn (90
°), and retig h ten the nu t. Recheck the
whee
l balance.
•If the imbala n ce is 5 g or less, the wheel may not
be
centre d on th e balancer , or th e balancing
co
nes, the cup, an d/or win g nut a r e damaged ,
dirty
, or inappro p riate for the wh eel. Y o u may
nee
d to ref e r to th e balance r man u fact urer's
in
struction s to verify the corre ct at t a chme nt s.
Af
ter ma kin g the n e cessa r y correct ions, recheck
the
wh eel b a lan c e. If OK, the n go t o S t ep 4.
•If the imbala n ce is more t han 5 g , the b a lan c er
requ
ires calibrat ion. Con t a c t the bala n cer manu
-
facturer fo r calibra t ion b y the i r rep a ir represent a-
tive.
4.< >
Atta ch a 5 g we ight to the outer rim. Recheck the
b
a lancer . Th e balance r sho u ld d e tect 5
± 2 g of
imba
lance 170
to 190
° away from the 5 g weigh t .
•If the imbala n ce is within specification, th e st atic
balance ca
libra tion is correct. Go to S t ep 5 to
check the d
y namic balance .
•If the imbala n ce is o u t of specification, the bal-
ancer requ ires ca libra tion. Co nt a c t th e balance r
manufacturer f
o r calibra t ion by th eir rep a ir repre
-
sentative.
5.<
Atta ch a 5 g we ight to the inner rim at 180°
o
pposite the
5
g weight that wa
s
a
dded in S t e p 4.
Recheck the bala
n
ce
.
Th
e
b
a
lancer sho
u
ld dete c t
5
± 2 g of imba lance 170 to 190° away from both
th
e inn
e
r and
outer 5
g weigh
t
s.
•If th e imbala n ce is within specification, th e
dynamic b
a lan c e calibratio n is corre ct. T he bal
-
ancer calibration che c ks are complet e .
•If the imbala n ce is o u t of specification, the bal-
ancer requ ires ca libra tion. Co nt a c t th e balance r
manufacturer f
o r calibra t ion by th eir rep a ir repre
-
sentative.
Page 168 of 800
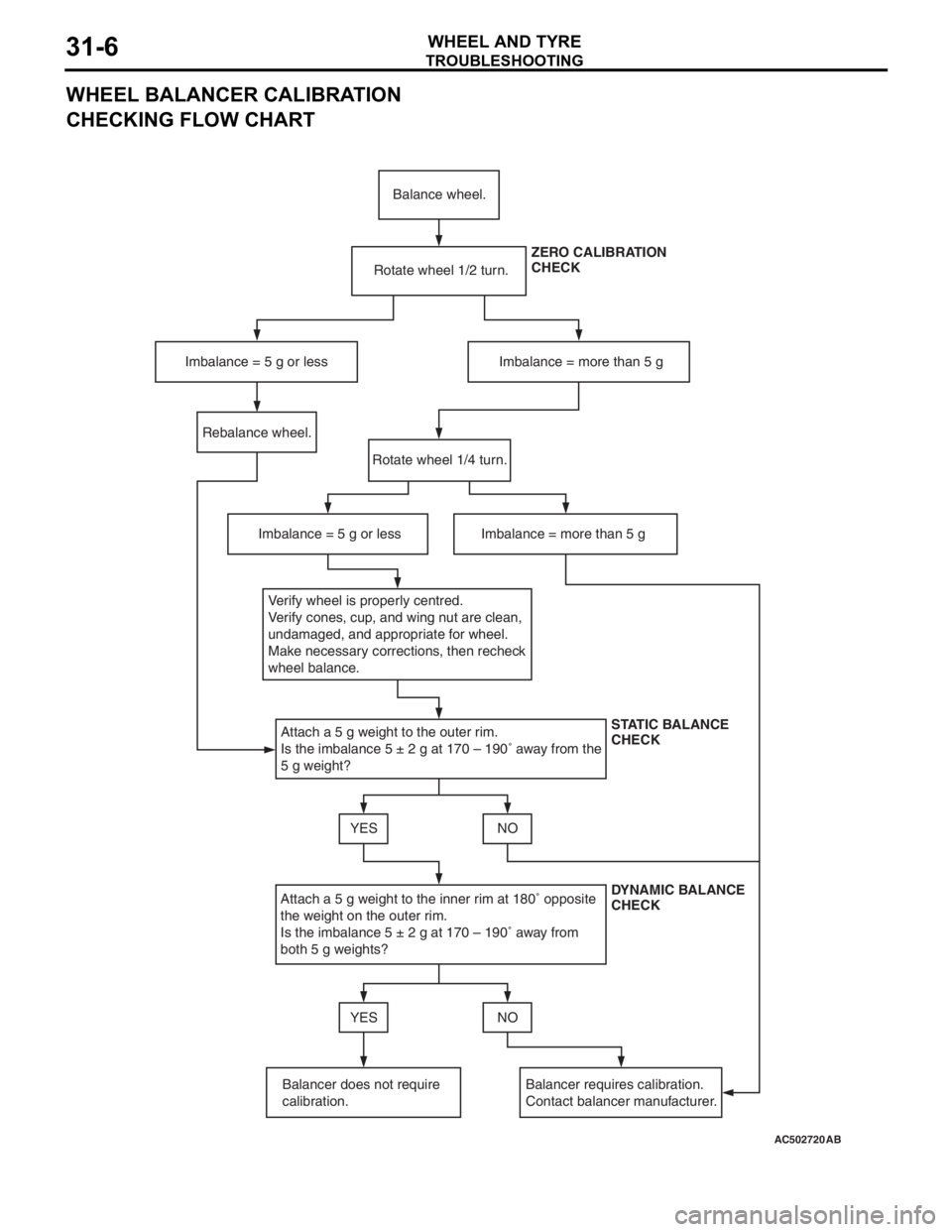
TROUBLESHOOTING
WHEEL AND TYRE31-6
WHEEL BALANCER CALIBRATION
CHECKING FLOW CHART
AC502720AB
Balance wheel.
Rotate wheel 1/2 turn.
Imbalance = 5 g or less Imbalance = more than 5 g Rebalance wheel. Rotate wheel 1/4 turn.
Imbalance = 5 g or less Imbalance = more than 5 g Verify wheel is properly centred.
Verify cones, cup, and wing nut are clean,
undamaged, and appropriate for wheel.
Make necessary corrections, then recheck
wheel balance. Attach a 5 g weight to the outer rim.
Is the imbalance 5 ± 2 g at 170 – 190 away from the
5 g weight? YES NO
Attach a 5 g weight to the inner rim at 180 opposite
the weight on the outer rim.
Is the imbalance 5 ± 2 g at 170 – 190 away from
both 5 g weights? YES NO
Balancer does not require
calibration. Balancer requires calibration.
Contact balancer manufacturer.ZERO CALIBRATION
CHECK
STATIC BALANCE
CHECK
DYNAMIC BALANCE
CHECK
Page 174 of 800
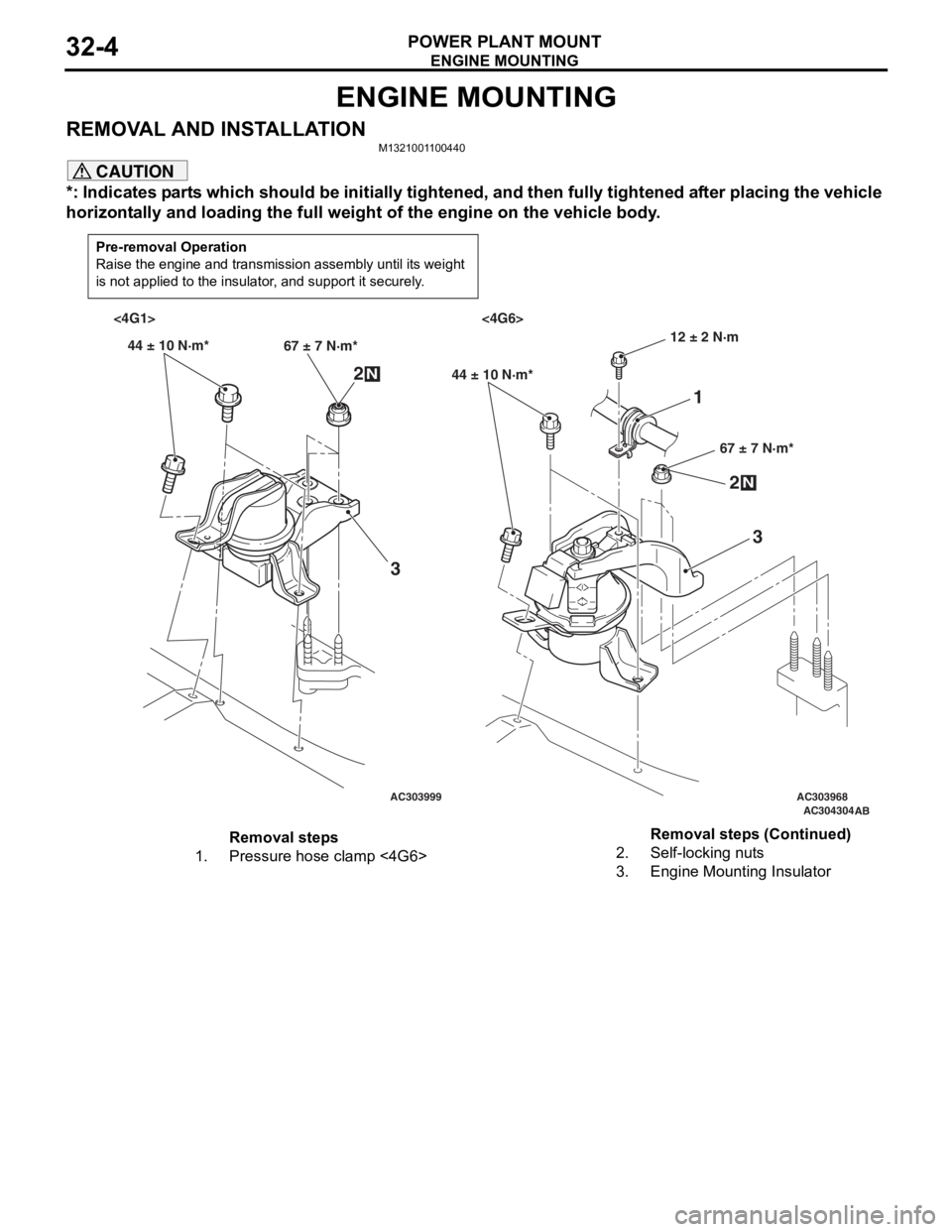
ENGINE MOUNTING
POWER PLANT MOUNT32-4
ENGINE MOUNTING
REMOVAL AND INSTALLATIONM1321001100440
CAUTION
*: Indicates parts which should be initially tightened, and then fully tightened after placing the vehicle
horizontally and loading the full weight of the engine on the vehicle body.
Pre-removal Operation
Raise the engine and transmission assembly until its weight
is not applied to the insulator, and support it securely.
AC303999AC303968AC304304AB
<4G1> <4G6>
44 ± 10 N·m* 67 ± 7 N·m*
2N
3
44 ± 10 N·m*
67 ± 7 N·m*
2N
3
12 ± 2 N·m
1
Removal steps
1.Pressure hose clamp <4G6>2.Self-locking nuts
3.Engine Mounting Insulator
Removal steps (Continued)
Page 175 of 800
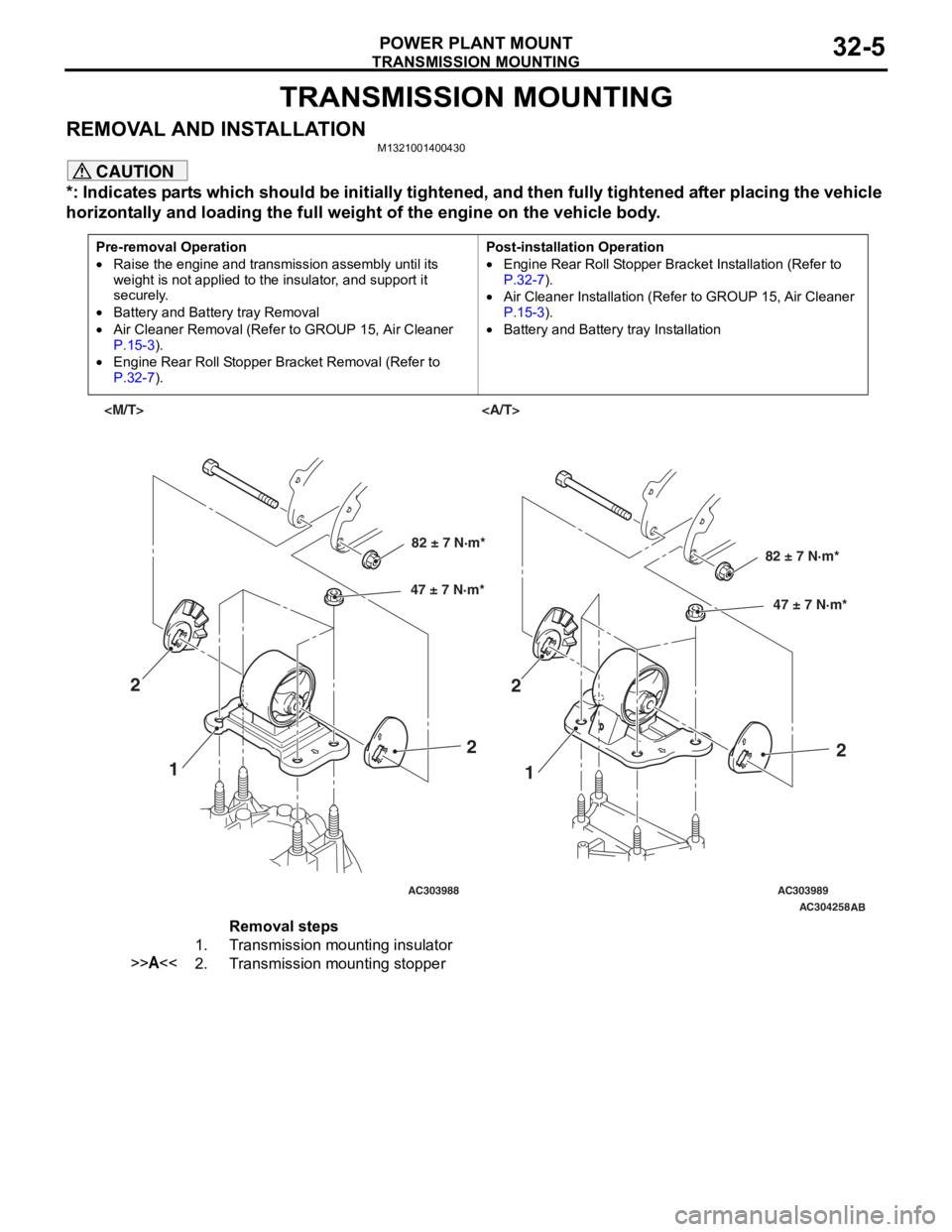
TRANSMISSION MOUNTING
POWER PLANT MOUNT32-5
TRANSMISSION MOUNTING
REMOVAL AND INSTALLATIONM1321001400430
CAUTION
*: Indicates parts which should be initially tightened, and then fully tightened after placing the vehicle
horizontally and loading the full weight of the engine on the vehicle body.
Pre-removal Operation
•Raise the engine and transmission assembly until its
weight is not applied to the insulator, and support it
securely.
•Battery and Battery tray Removal
•Air Cleaner Removal (Refer to GROUP 15, Air Cleaner
P.15-3).
•Engine Rear Roll Stopper Bracket Removal (Refer to
P.32-7).
Post-installation Operation
•Engine Rear Roll Stopper Bracket Installation (Refer to
P.32-7).
•Air Cleaner Installation (Refer to GROUP 15, Air Cleaner
P.15-3).
•Battery and Battery tray Installation
AC303988AC303989AC304258
AB
82 ± 7 N·m*
47 ± 7 N·m*82 ± 7 N·m*
47 ± 7 N·m*
1 1
2
22
2
Removal steps
1.Transmission mounting insulator
>>A<<2.Transmission mounting stopper
Page 177 of 800
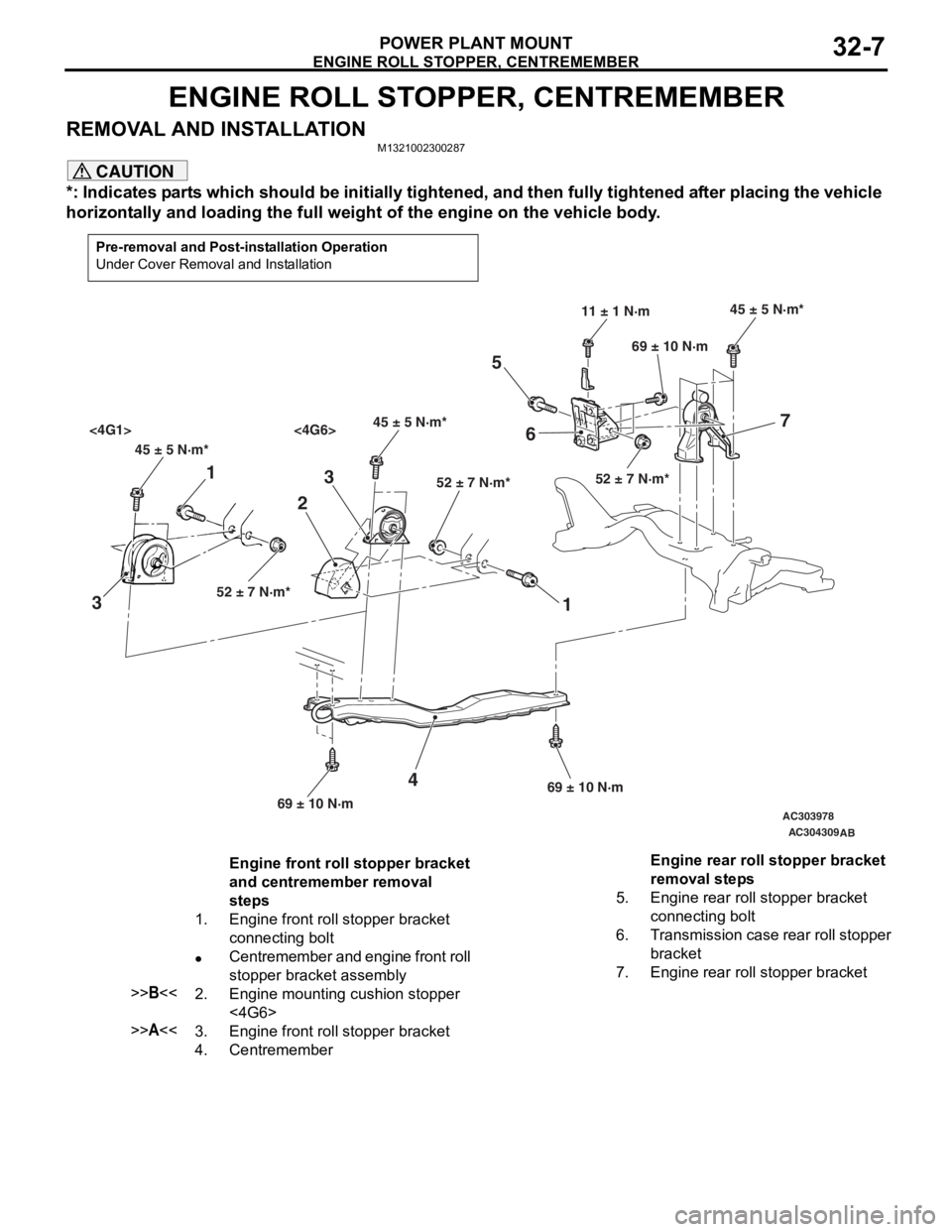
ENGINE ROLL STOPPER, CENTREMEMBER
POWER PLANT MOUNT32-7
ENGINE ROLL STOPPER, CENTREMEMBER
REMOVAL AND INSTALLATIONM1321002300287
CAUTION
*: Indicates parts which should be initially tightened, and then fully tightened after placing the vehicle
horizontally and loading the full weight of the engine on the vehicle body.
Pre-removal and Post-installation Operation
Under Cover Removal and Installation
AC303978
AC304309
45 ± 5 N·m*45 ± 5 N·m*
<4G1> <4G6>
52 ± 7 N·m* 52 ± 7 N·m*
45 ± 5 N·m*
52 ± 7 N·m*
11 ± 1 N·m
69 ± 10 N·m
69 ± 10 N·m 69 ± 10 N·m
1
3 2
1
3
4
56 7
AB
Engine front roll stopper bracket
and centremember removal
steps
1.Engine front roll stopper bracket
connecting bolt
•Centremember and engine front roll
stopper bracket assembly
>>B<<2.Engine mounting cushion stopper
<4G6>
>>A<<3.Engine front roll stopper bracket
4.Centremember
Engine rear roll stopper bracket
removal steps
5.Engine rear roll stopper bracket
connecting bolt
6.Transmission case rear roll stopper
bracket
7.Engine rear roll stopper bracket