Compressor MITSUBISHI MONTERO 1987 1.G Owner's Manual
[x] Cancel search | Manufacturer: MITSUBISHI, Model Year: 1987, Model line: MONTERO, Model: MITSUBISHI MONTERO 1987 1.GPages: 284, PDF Size: 14.74 MB
Page 276 of 284
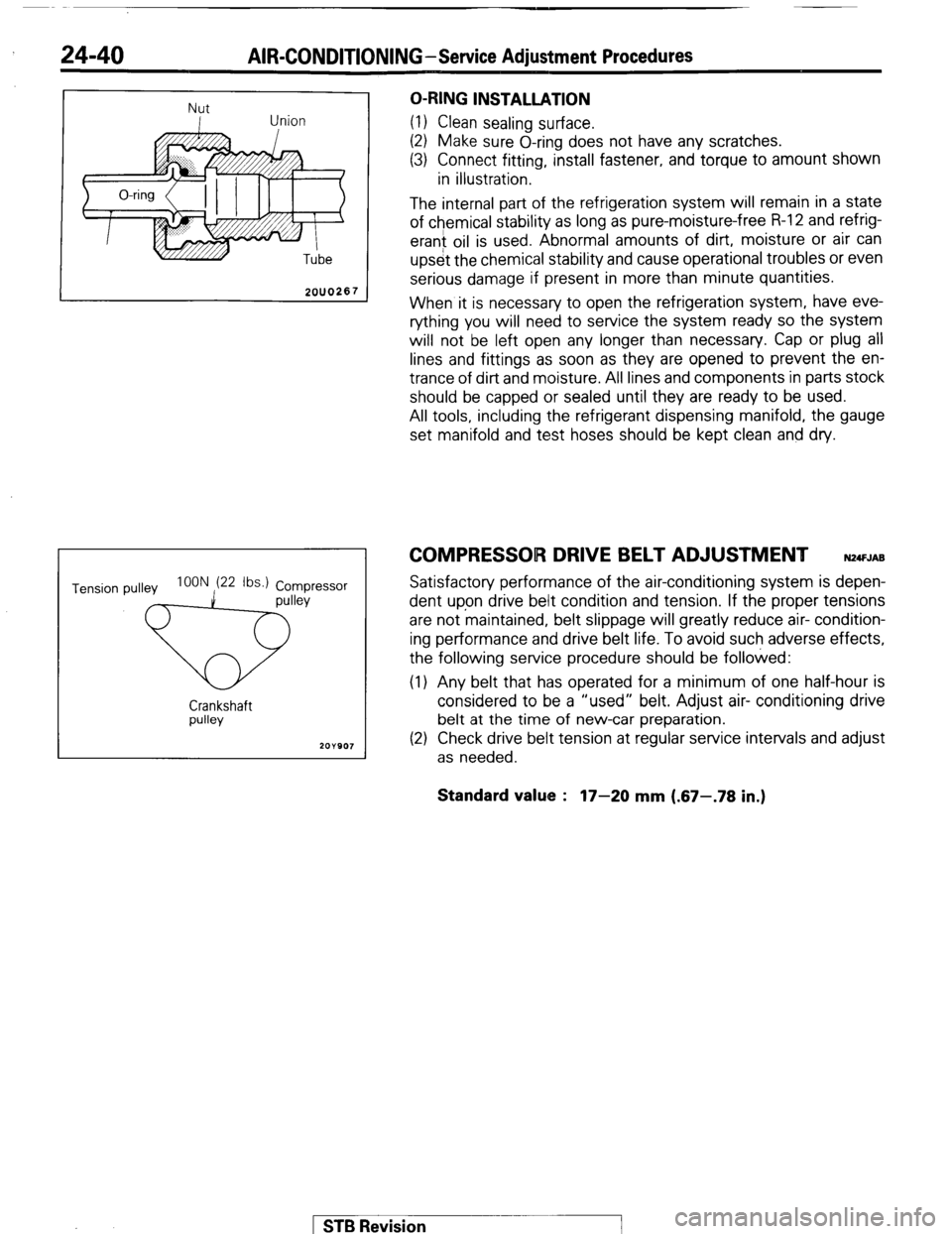
24-40 AIR-CONDITIONING-Service Adjustment Procedures
Nut
I Union
20110267
Tension pulley IOON (22 Ibs.1 Compressor
Crankshaft
pulley
I 2OY907 1 O-RING INSTALLATION
(1) Clean sealing surface.
(2) Make sure O-ring does not have any scratches.
(3) Connect fitting, install fastener, and torque to amount shown
in illustration.
The internal part of the refrigeration system will remain in a state
of chemical stability as long as pure-moisture-free R-l 2 and refrig-
erant oil is used. Abnormal amounts of dirt, moisture or air can
upset the chemical stability and cause operational troubles or even
serious damage if present in more than minute quantities.
When it is necessary to open the refrigeration system, have eve-
rything you will need to service the system ready so the system
will not be left open any longer than necessary. Cap or plug all
lines and fittings as soon as they are opened to prevent the en-
trance of dirt and moisture. All lines and components in parts stock
should be capped or sealed until they are ready to be used.
All tools, including the refrigerant dispensing manifold, the gauge
set manifold and test hoses should be kept clean and dry.
COMPRESSOR DRIVE BELT ADJUSTMENT N24FJAE
Satisfactory performance of the air-conditioning system is depen-
dent upon drive belt condition and tension. If the proper tensions
are not maintained, belt slippage will greatly reduce air- condition-
ing performance and drive belt life. To avoid such adverse effects,
the following service procedure should be followed:
(1) Any belt that has operated for a minimum of one half-hour is
considered to be a “used” belt. Adjust air- conditioning drive
belt at the time of new-car preparation.
(2) Check drive belt tension at regular service intervals and adjust
as needed.
Standard value :
17-20 mm (.67-.78 in.)
1 STB Revision
-7
Page 277 of 284
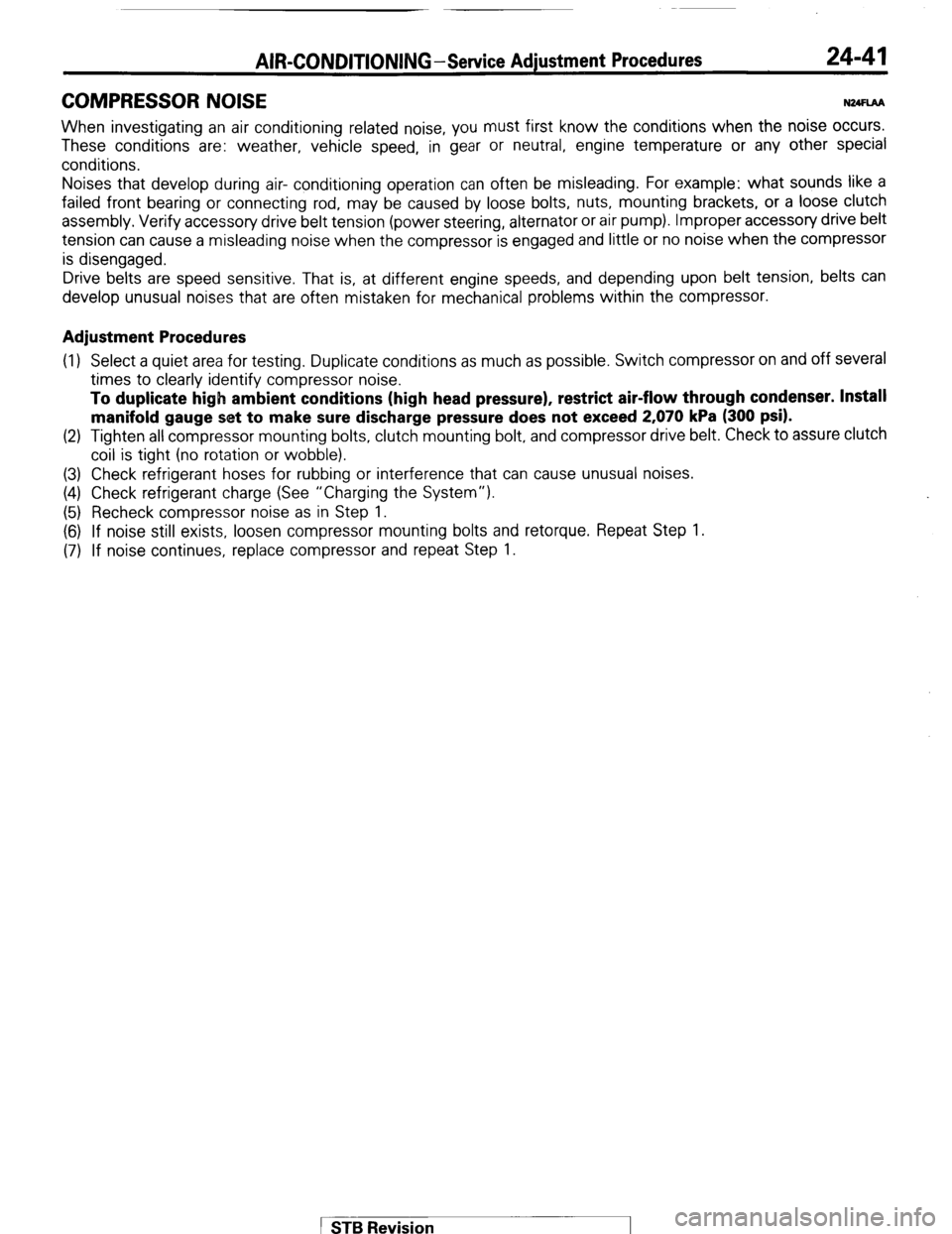
AIR-CONDITIONING -Service Adjustment Procedures 24-41
COMPRESSOR NOISE NWLM
When investigating an air conditioning related noise, you must first know the conditions when the noise occurs.
These conditions are: weather, vehicle speed, in gear or neutral, engine temperature or any other special
conditions.
Noises that develop during air- conditioning operation can often be misleading. For example: what sounds like a
failed front bearing or connecting rod, may be caused by loose bolts, nuts, mounting brackets, or a loose clutch
assembly. Verify accessory drive belt tension (power
steering, alternator or air pump). Improper accessory drive belt
tension can cause a misleading noise when the compressor is engaged and little or no noise when the compressor
is disengaged.
Drive belts are speed sensitive. That is, at different engine speeds, and depending upon belt tension, belts can
develop unusual noises that are often mistaken for mechanical problems within the compressor.
Adjustment Procedures
(1) Select a quiet area for testing. Duplicate conditions as much as possible. Switch compressor on and off several
times to clearly identify compressor noise.
To duplicate high ambient conditions (high head pressure), restrict air-flow through
condenser. Install
manifold gauge set to make sure discharge pressure does not exceed 2,070 kPa (300 psi).
(2) Tighten all compressor mounting bolts, clutch mounting bolt, and compressor drive belt. Check to assure clutch
coil is tight (no rotation or wobble).
(3) Check refrigerant hoses for rubbing or interference that can cause unusual noises.
(4) Check refrigerant charge (See “Charging the System”).
(5) Recheck compressor noise as in Step 1.
(6) If noise still exists, loosen compressor mounting bolts and retorque. Repeat Step 1.
(7) If noise continues, replace compressor and repeat Step 1.
1 STB Revision
Page 279 of 284
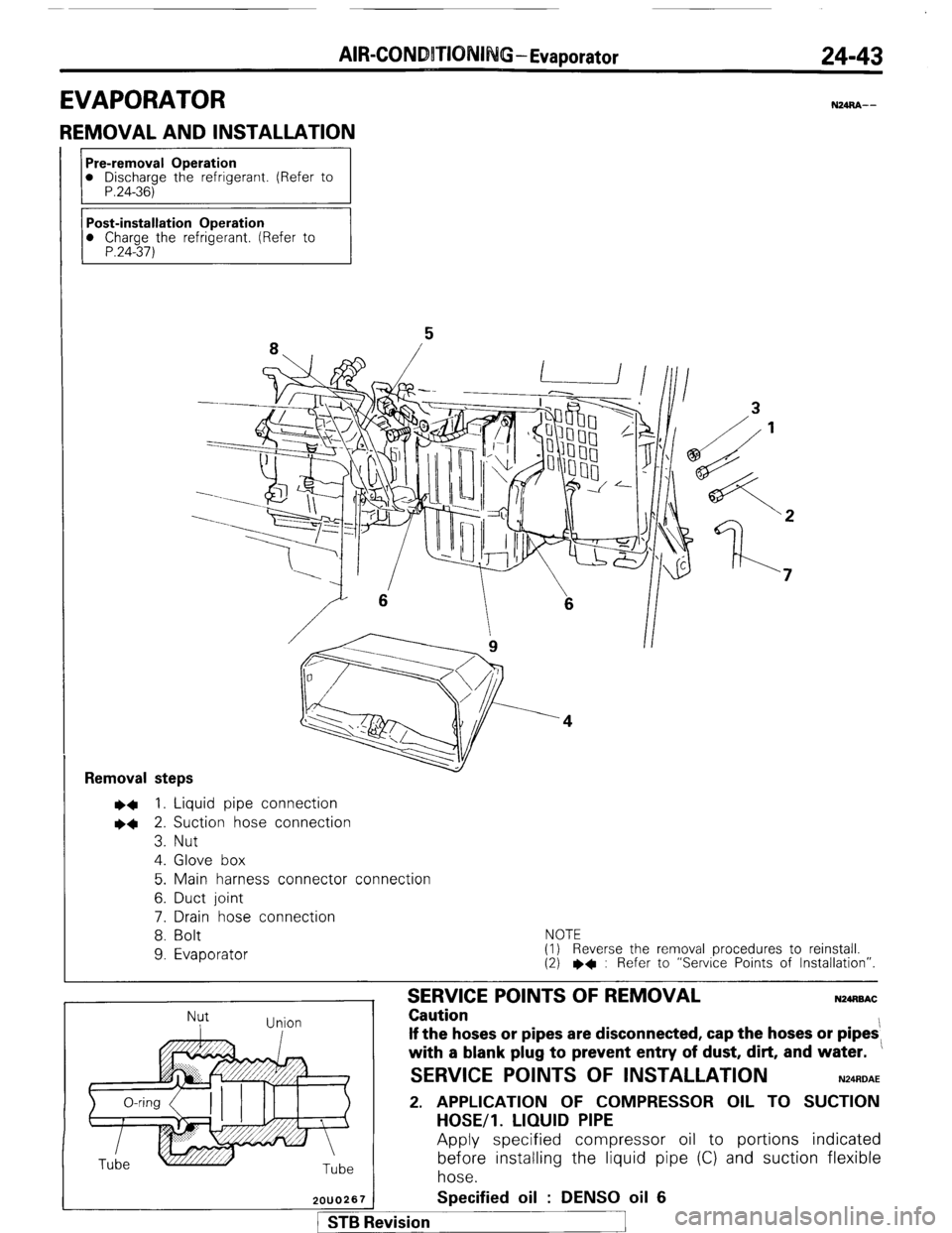
AIR-CONDBTIONI G - Evaporator 24-43
EVAPORATOR
REMOVAL AND INSTALLATION
N24RA--
Pre-removal Operation
l
Discharge the refrigerant. (Refer to
P.24-36) Removal
steps ~~ 1. Liquid pipe connection
l + 2. Suction hose connection
3. Nut
4. Glove box
5. Main harness connector connection
6. Duct joint
7. Drain hose connection
8. Bolt
9. Evaporator
NOTE
(I) Reverse the removal procedures to reinstall.
(2) l
* : Refer to “Service Points of Installation”.
Nut
I Union
/
2OUO267
SERVICE POINTS OF REMOVAL Caution N24MAC If the hoses or pipes are disconnected, cap the hoses or pipes:
with a blank plug to prevent entry of dust, dirt, and water.
SERVICE POINTS OF INSTALLATION N24AOAE 2. APPLICATION OF COMPRESSOR OIL TO SUCTION
HOSE/l. LIQUID PIPE
Apply specified compressor oil to portions indicated
before installing the liquid pipe (C) and suction flexible
hose.
Specified oil : DENS0 oil 6
!vision
Page 280 of 284
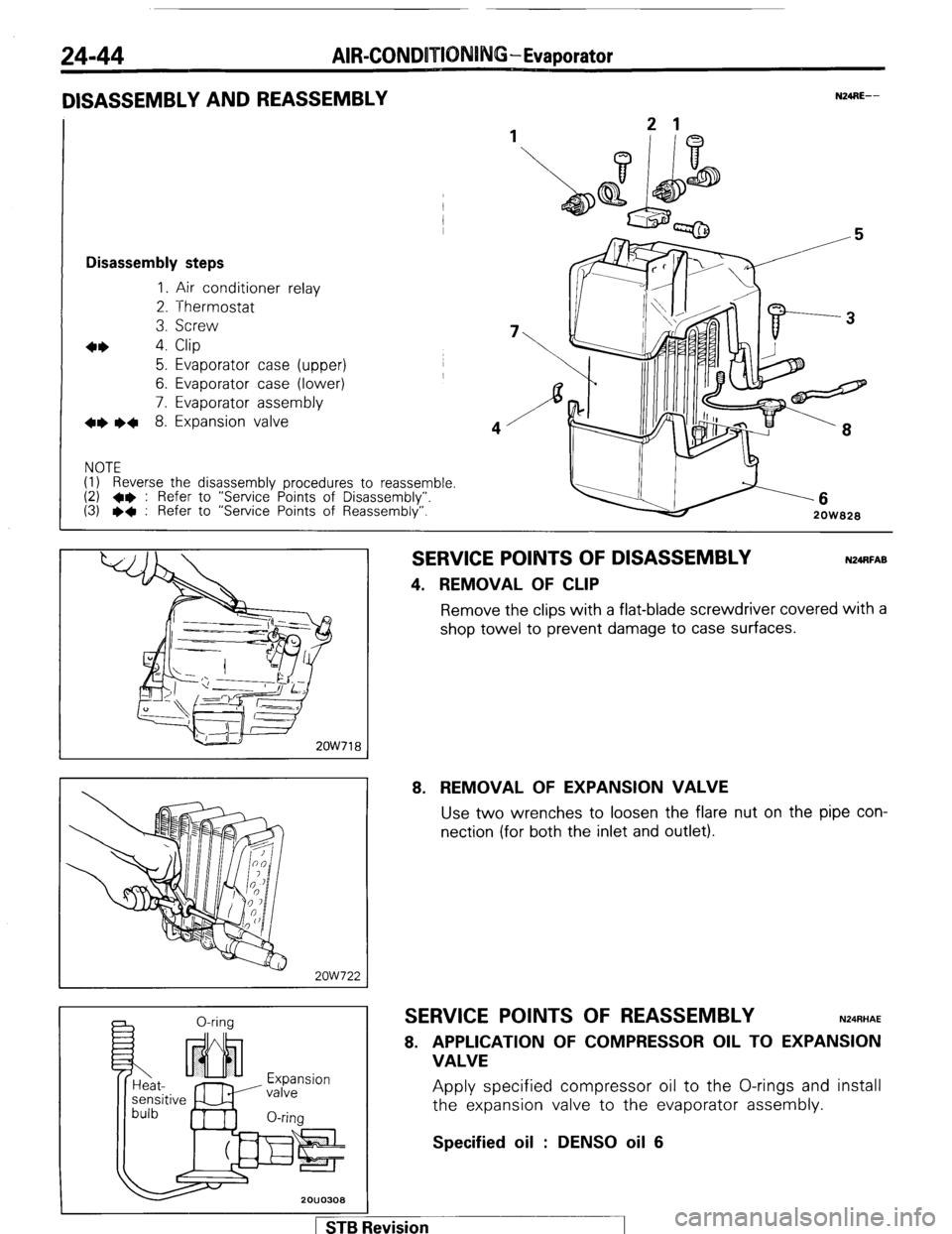
24-44 AIR-CONDOTIONING-Evaporator
DISASSEMBLY AND REASSEMBLY
1
Disassembly steps
1. Air conditioner relay
2. Thermostat
3. Screw
4* 4. Clip
5. Evaporator case (upper)
6. Evaporator case (lower)
7. Evaporator assembly
+e l + 8. Expansion valve
NOTE
(1) Reverse the disassembly procedures to reassemble.
(2) +e : Refer to “Service Points of Disassembly”.
(3) l + : Refer to “Service Points of Reassembly”.
N24RE-- -6
2OW828
2OW718
2ow722
a 0-rina
Expansion
valve
O-rim
SERVICE POINTS OF DISASSEMBLY
4. REMOVAL OF CLIP
N24RFAB Remove the clips with a flat-blade screwdriver covered with a
shop towel to prevent damage to case surfaces.
8. REMOVAL OF EXPANSION VALVE Use two wrenches to loosen the flare nut on the pipe con-
nection (for both the inlet and outlet).
SERVICE POINTS OF REASSEMBLY N24RHAE
8. APPLICATION OF COMPRESSOR OIL TO EXPANSION
VALVE Apply specified compressor oil to the O-rings and install
the expansion valve to the evaporator assembly.
Specified oil : DENS0 oil 6
1 STB Revision
Page 281 of 284
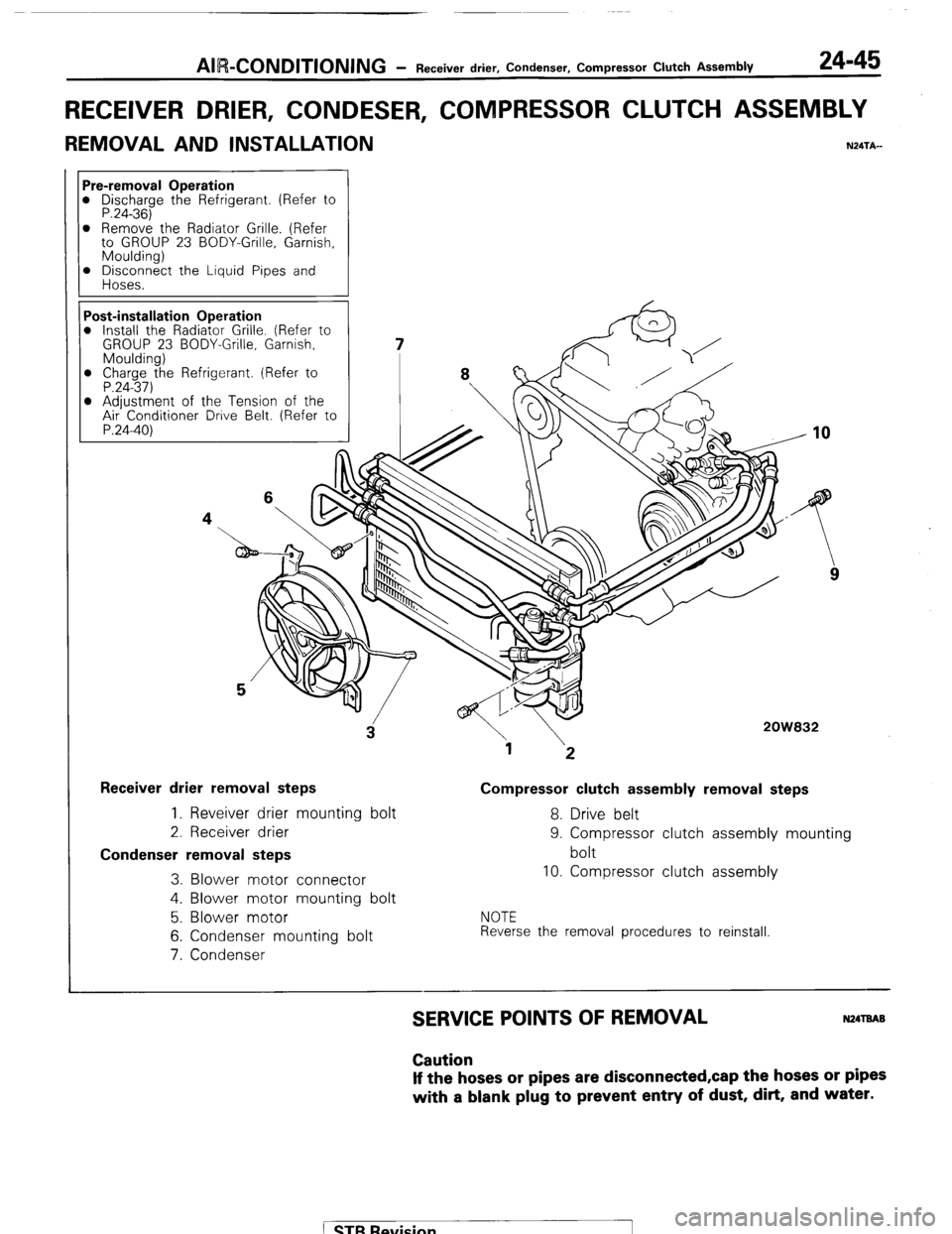
AIR-CONDITIONING - Receiver drier, Condenser, Compressor Clutch Assembly 24-45
RECEIVER DRIER, CONDESER, COMPRESSOR CLUTCH ASSEMBLY
REMOVAL AND INSTALLATION N24TA--
Pre-removal Operation l Discharge the Refrigerant. (Refer to
P.24-36)
l Remove the Radiator Grille. (Refer
to GROUP 23 BODY-Grille, Garnish,
Moulding)
l Disconnect the Liquid Pipes and
Hoses.
Post-installation Operation
l Install the Radiator Grille. (Refer to
GROUP 23 BODY-Grille, Garnish,
Moulding)
l Charge the Refrigerant. (Refer to
P.24.37)
l Adjustment of the Tension of the
Air Conditioner Drive Belt. (Refer to
P.24-40)
2OW832 Receiver drier removal steps
Compressor clutch assembly removal steps
1. Reveiver drier mounting bolt
8. Drive belt
2. Receiver drier
9. Compressor clutch assembly mounting
Condenser removal steps
3. Blower motor connector
4. Blower motor mounting bolt
5. Blower motor
6. Condenser mounting bolt
7. Condenser bolt
10. Compressor clutch assembly
NOTE
Reverse the removal procedures to reinstall.
SERVICE POINTS OF REMOVAL N24TBAB 1 STB Revision Caution
If the hoses or pipes are disconnected,cap the hoses or pipes
with a blank plug to prevent entry of dust, dirt, and water.
Page 282 of 284
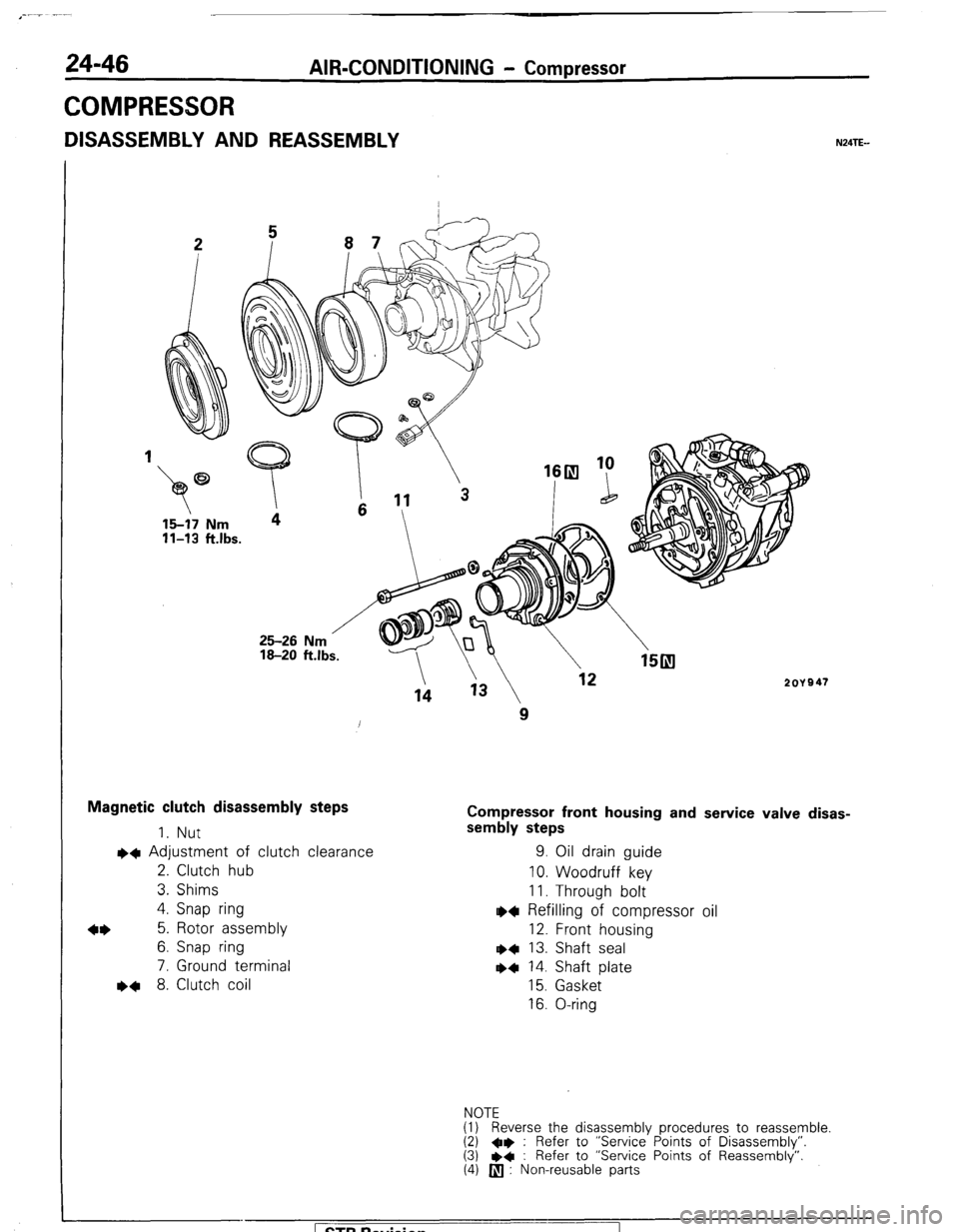
24-46
COMPRESSOR
AIR-CONDITIONING - Compressor
DISASSEMBLY AND REASSEMBLY N24TE-
15-h Nm
11-13 ftlbs 16
a 0
I
26-26 Nm
16-20 ftlbs. Magnetic clutch disassembly steps
1. Nut
~~ Adjustment of clutch clearance
2. Clutch hub
3. Shims
4.
Snap ring
4* 5. Rotor assembly
6.
Snap ring
7.
Ground terminal
l + 8. Clutch coil
l5Dl
2QY947 Compressor front housing and service valve disas-
sembly steps
9. Oil drain guide
10.
Woodruff key
Il. Through bolt
** Refilling of compressor oil
12. Front housing
o+
13. Shaft seal
04 14.
Shaft plate
15.
Gasket
16. O-ring
NOTE
(1) Reverse the disassembly procedures to reassemble.
(2) +e : Refer to “Service Points of Disassembly”.
(3) e+ : Refer to “Service Points of Reassembly”.
(4)
q : Non-reusable parts 1 STB Revision
Page 283 of 284
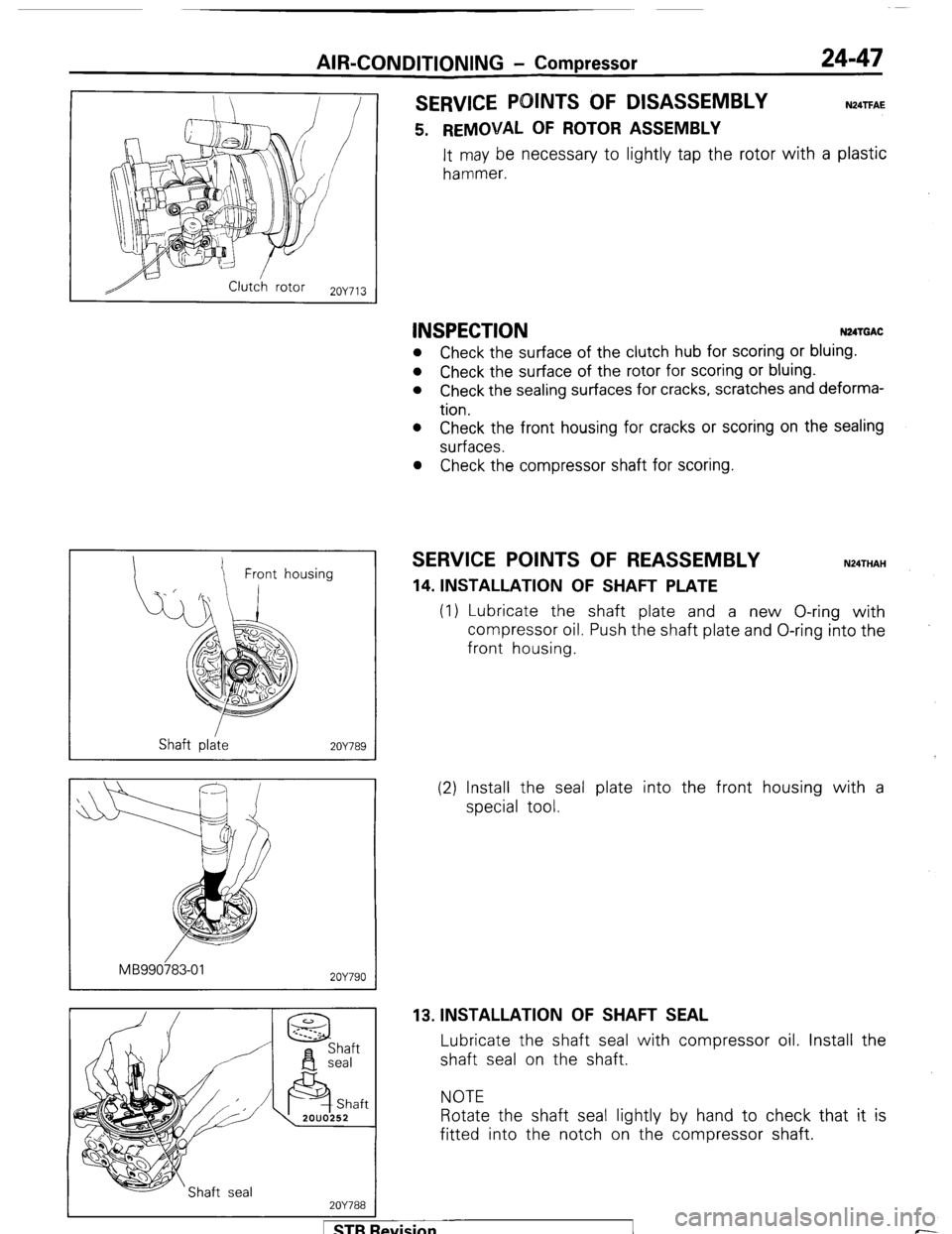
AIR-CONDITIONING - Compressor 24-47
SERVICE POINTS OF DISASSEMBLY N24TFAE
5. REMOVAL OF ROTOR ASSEMBLY
It may be necessary to lightly tap the rotor with a plastic
hammer.
2OY713
Front housing
Shaft pl&e
2OY789
I MB990?83-01 2OY790
2OY788
INSPECTION N24TGAC
l
Check the surface of the clutch hub for scoring or bluing.
l Check the surface of the rotor for scoring or bluing.
l Check the sealing surfaces for cracks, scratches and deforma-
tion.
l Check the front housing for cracks or scoring on the sealing
surfaces.
l Check the compressor shaft for scoring.
SERVICE POINTS OF REASSEMBLY N24THAH
14. INSTALLATION OF SHAFT PLATE
(1) Lubricate the shaft plate and a new O-ring with
compressor oil. Push the shaft plate and O-ring into the
front housing.
(2) Install the seal plate into the front housing with a
special tool.
13. INSTALLATION OF SHAFT SEAL
Lubricate the shaft seal with compressor oil. Install the
shaft seal on the shaft.
NOTE
Rotate the shaft seal lightly by hand to check that it is
fitted into the notch on the compressor shaft. evision
r
Page 284 of 284
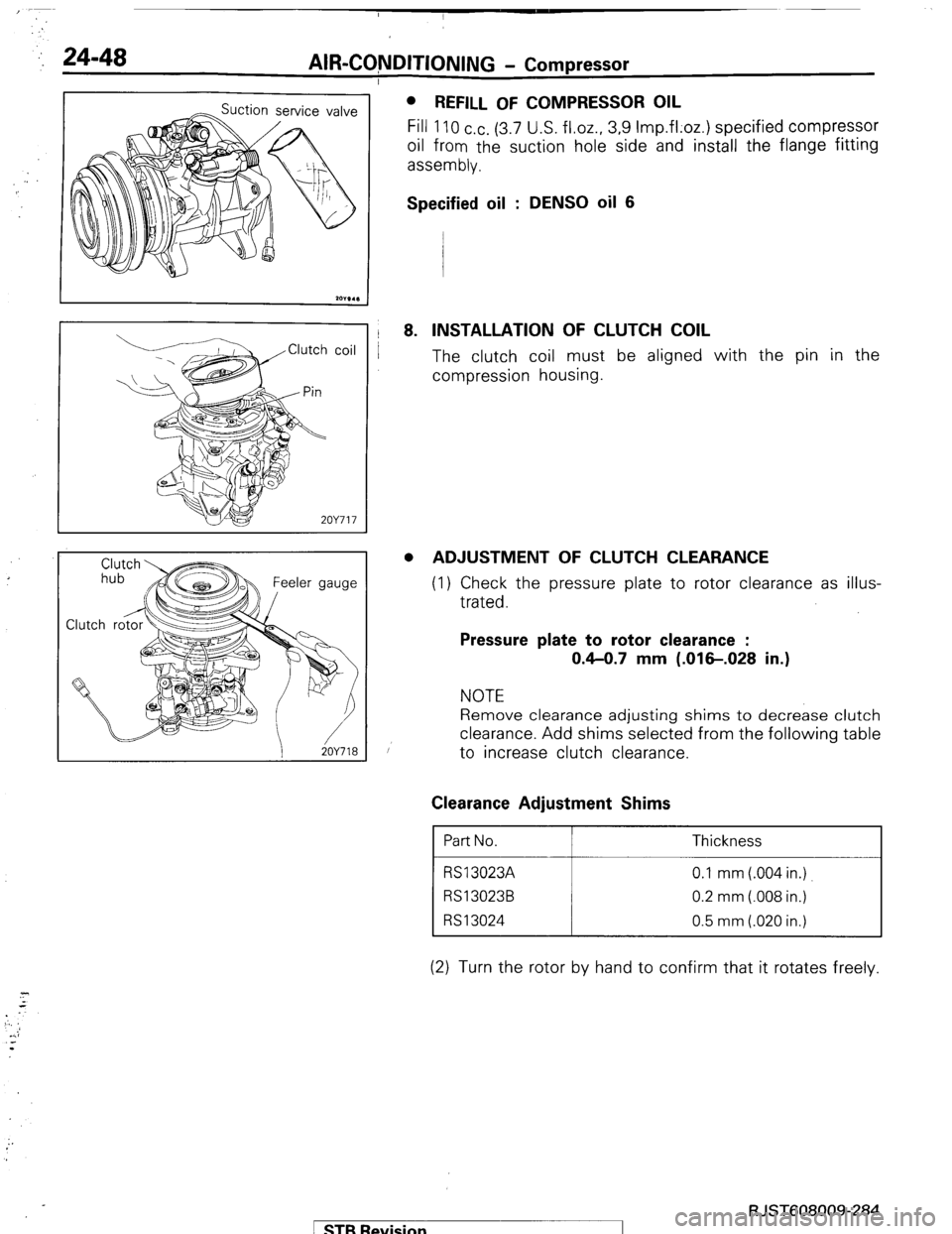
,: 24-48 AIR-CQNDITIONING - Compressor
I
2OY717
1 iOY718 l
REFILL OF COMPRESSOR OIL
Fill 110 cc. (3.7 U.S. fl.oz., 3.9 Imp.fl;oz.) specified compressor
oil from the suction hole side and install the flange fitting
assembly.
Specified oil : DENS0 oil 6
8. INSTALLATION OF CLUTCH COIL
The clutch coil must be aligned with the pin in the
compression housing.
. ADJUSTMENT OF CLUTCH CLEARANCE
(1) Check the pressure plate to rotor clearance as illus-
trated.
Pressure plate to rotor clearance :
0.4-0.7 mm (.016-.028 in.)
NOTE
Remove clearance adjusting shims to decrease clutch
clearance. Add shims selected from the following table
to increase clutch clearance.
Clearance Adjustment Shims
Part No. Thickness
RSI 3023A 0.1 mm (.004 in.).
RSI 3023B 0.2 mm (.008 in.)
RSI 3024 0.5 mm (.020 in.)
(2) Turn the rotor by hand to confirm that it rotates freely.
:.
RJST608009-284
1 STB Revision
-1