display MITSUBISHI MONTERO 1998 User Guide
[x] Cancel search | Manufacturer: MITSUBISHI, Model Year: 1998, Model line: MONTERO, Model: MITSUBISHI MONTERO 1998Pages: 1501, PDF Size: 25.81 MB
Page 326 of 1501
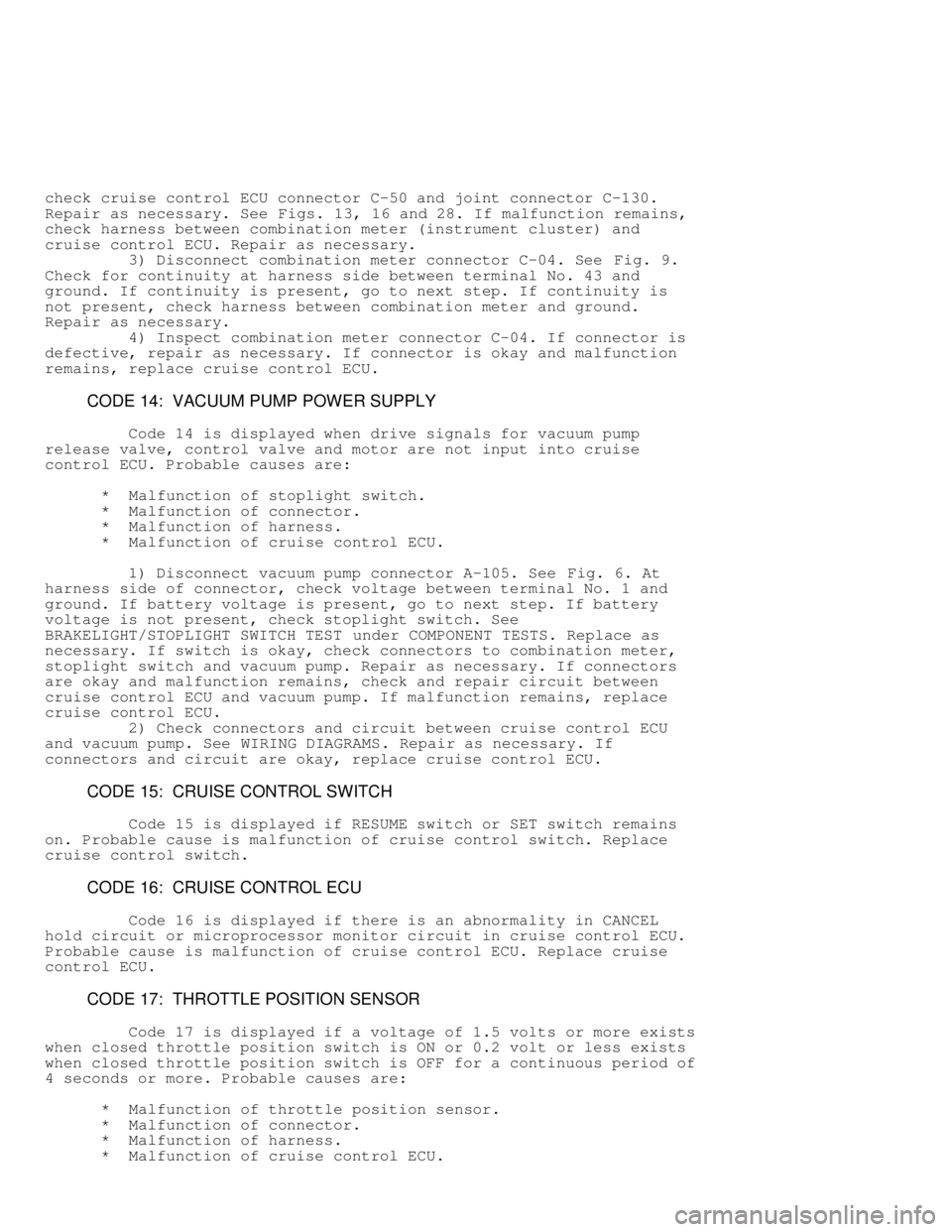
check cruise control ECU connector C-50 and joint connector C-130.
Repair as necessary. See Figs. 13, 16 and 28. If malfunction remains,
check harness between combination meter (instrument cluster) and
cruise control ECU. Repair as necessary.
3) Disconnect combination meter connector C-04. See Fig. 9.
Check for continuity at harness side between terminal No. 43 and
ground. If continuity is present, go to next step. If continuity is
not present, check harness between combination meter and ground.
Repair as necessary.
4) Inspect combination meter connector C-04. If connector is
defective, repair as necessary. If connector is okay and malfunction
remains, replace cruise control ECU.
CODE 14: VACUUM PUMP POWER SUPPLY
Code 14 is displayed when drive signals for vacuum pump
release valve, control valve and motor are not input into cruise
control ECU. Probable causes are:
* Malfunction of stoplight switch.
* Malfunction of connector.
* Malfunction of harness.
* Malfunction of cruise control ECU.
1) Disconnect vacuum pump connector A-105. See Fig. 6. At
harness side of connector, check voltage between terminal No. 1 and
ground. If battery voltage is present, go to next step. If battery
voltage is not present, check stoplight switch. See
BRAKELIGHT/STOPLIGHT SWITCH TEST under COMPONENT TESTS. Replace as
necessary. If switch is okay, check connectors to combination meter,
stoplight switch and vacuum pump. Repair as necessary. If connectors
are okay and malfunction remains, check and repair circuit between
cruise control ECU and vacuum pump. If malfunction remains, replace
cruise control ECU.
2) Check connectors and circuit between cruise control ECU
and vacuum pump. See WIRING DIAGRAMS. Repair as necessary. If
connectors and circuit are okay, replace cruise control ECU.
CODE 15: CRUISE CONTROL SWITCH
Code 15 is displayed if RESUME switch or SET switch remains
on. Probable cause is malfunction of cruise control switch. Replace
cruise control switch.
CODE 16: CRUISE CONTROL ECU
Code 16 is displayed if there is an abnormality in CANCEL
hold circuit or microprocessor monitor circuit in cruise control ECU.
Probable cause is malfunction of cruise control ECU. Replace cruise
control ECU.
CODE 17: THROTTLE POSITION SENSOR
Code 17 is displayed if a voltage of 1.5 volts or more exists
when closed throttle position switch is ON or 0.2 volt or less exists
when closed throttle position switch is OFF for a continuous period of
4 seconds or more. Probable causes are:
* Malfunction of throttle position sensor.
* Malfunction of connector.
* Malfunction of harness.
* Malfunction of cruise control ECU.
Page 531 of 1501
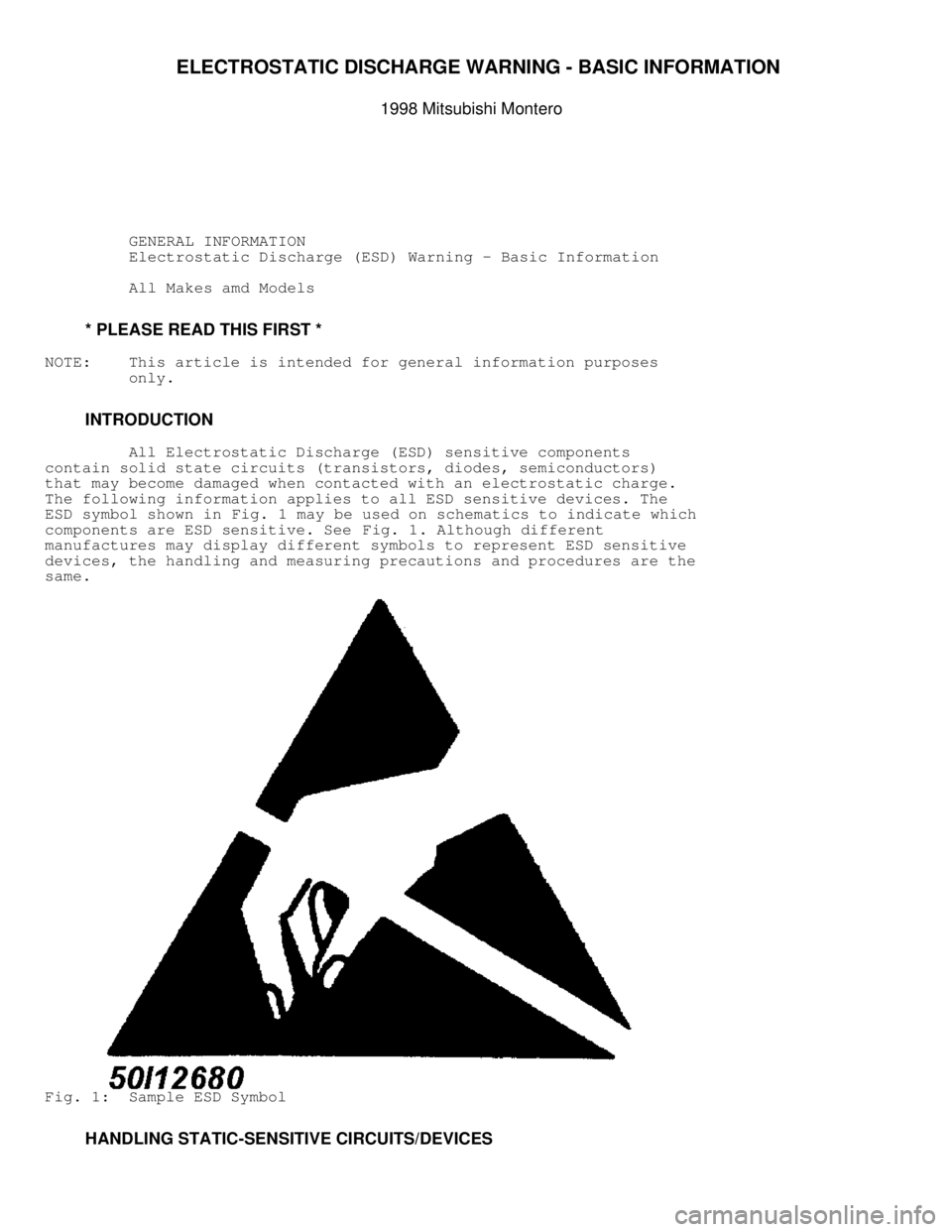
ELECTROSTATIC DISCHARGE WARNING - BASIC INFORMATION
1998 Mitsubishi Montero
GENERAL INFORMATION
Electrostatic Discharge (ESD) Warning - Basic Information
All Makes amd Models
* PLEASE READ THIS FIRST *
NOTE: This article is intended for general information purposes
only.
INTRODUCTION
All Electrostatic Discharge (ESD) sensitive components
contain solid state circuits (transistors, diodes, semiconductors)
that may become damaged when contacted with an electrostatic charge.
The following information applies to all ESD sensitive devices. The
ESD symbol shown in Fig. 1 may be used on schematics to indicate which
components are ESD sensitive. See Fig. 1. Although different
manufactures may display different symbols to represent ESD sensitive
devices, the handling and measuring precautions and procedures are the
same.
Fig. 1: Sample ESD Symbol
HANDLING STATIC-SENSITIVE CIRCUITS/DEVICES
Page 547 of 1501
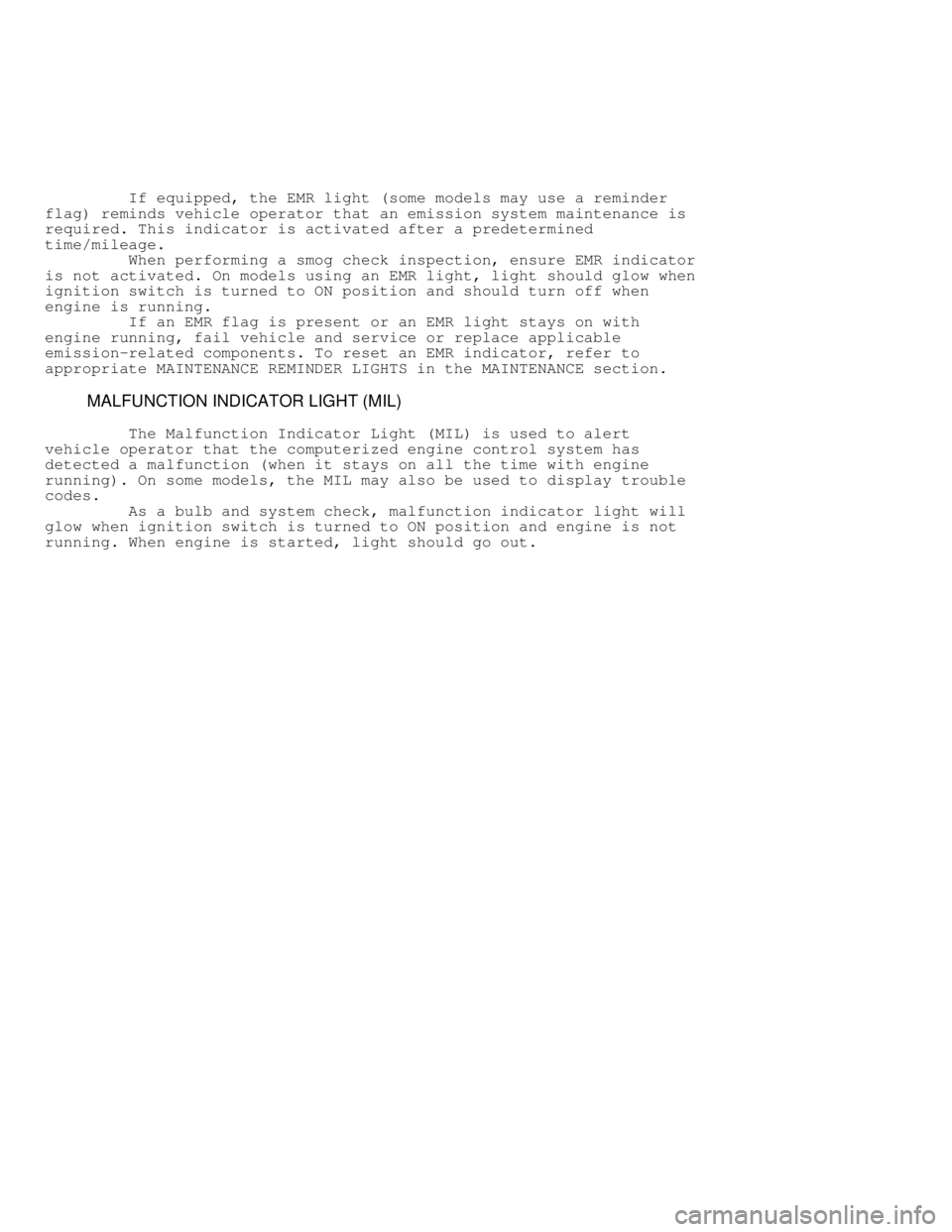
If equipped, the EMR light (some models may use a reminder
flag) reminds vehicle operator that an emission system maintenance is
required. This indicator is activated after a predetermined
time/mileage.
When performing a smog check inspection, ensure EMR indicator
is not activated. On models using an EMR light, light should glow when
ignition switch is turned to ON position and should turn off when
engine is running.
If an EMR flag is present or an EMR light stays on with
engine running, fail vehicle and service or replace applicable
emission-related components. To reset an EMR indicator, refer to
appropriate MAINTENANCE REMINDER LIGHTS in the MAINTENANCE section.
MALFUNCTION INDICATOR LIGHT (MIL)
The Malfunction Indicator Light (MIL) is used to alert
vehicle operator that the computerized engine control system has
detected a malfunction (when it stays on all the time with engine
running). On some models, the MIL may also be used to display trouble
codes.
As a bulb and system check, malfunction indicator light will
glow when ignition switch is turned to ON position and engine is not
running. When engine is started, light should go out.
Page 719 of 1501
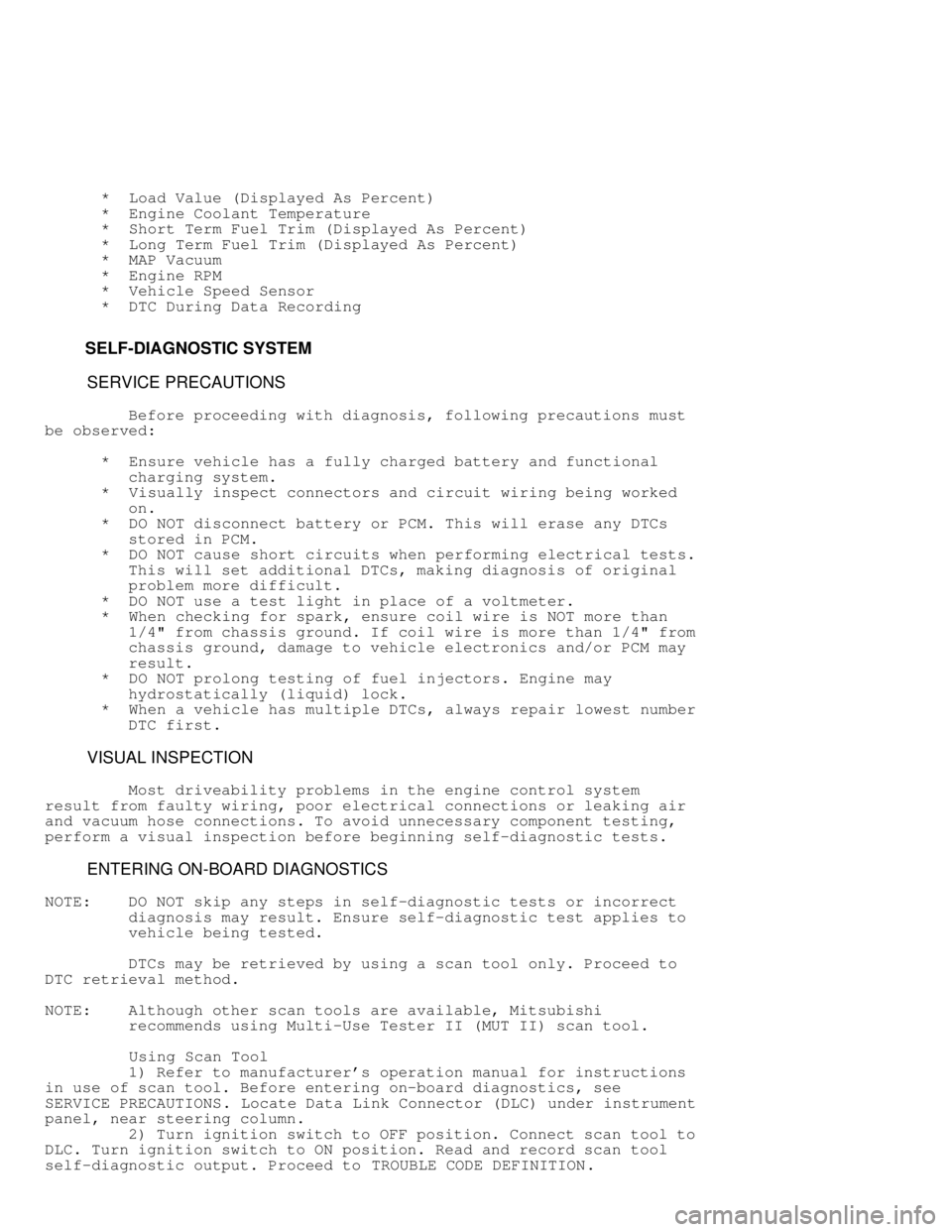
* Load Value (Displayed As Percent)
* Engine Coolant Temperature
* Short Term Fuel Trim (Displayed As Percent)
* Long Term Fuel Trim (Displayed As Percent)
* MAP Vacuum
* Engine RPM
* Vehicle Speed Sensor
* DTC During Data Recording
SELF-DIAGNOSTIC SYSTEM
SERVICE PRECAUTIONS
Before proceeding with diagnosis, following precautions must
be observed:
* Ensure vehicle has a fully charged battery and functional
charging system.
* Visually inspect connectors and circuit wiring being worked
on.
* DO NOT disconnect battery or PCM. This will erase any DTCs
stored in PCM.
* DO NOT cause short circuits when performing electrical tests.
This will set additional DTCs, making diagnosis of original
problem more difficult.
* DO NOT use a test light in place of a voltmeter.
* When checking for spark, ensure coil wire is NOT more than
1/4" from chassis ground. If coil wire is more than 1/4" from
chassis ground, damage to vehicle electronics and/or PCM may
result.
* DO NOT prolong testing of fuel injectors. Engine may
hydrostatically (liquid) lock.
* When a vehicle has multiple DTCs, always repair lowest number
DTC first.
VISUAL INSPECTION
Most driveability problems in the engine control system
result from faulty wiring, poor electrical connections or leaking air
and vacuum hose connections. To avoid unnecessary component testing,
perform a visual inspection before beginning self-diagnostic tests.
ENTERING ON-BOARD DIAGNOSTICS
NOTE: DO NOT skip any steps in self-diagnostic tests or incorrect
diagnosis may result. Ensure self-diagnostic test applies to
vehicle being tested.
DTCs may be retrieved by using a scan tool only. Proceed to
DTC retrieval method.
NOTE: Although other scan tools are available, Mitsubishi
recommends using Multi-Use Tester II (MUT II) scan tool.
Using Scan Tool
1) Refer to manufacturer's operation manual for instructions
in use of scan tool. Before entering on-board diagnostics, see
SERVICE PRECAUTIONS . Locate Data Link Connector (DLC) under instrument
panel, near steering column.
2) Turn ignition switch to OFF position. Connect scan tool to
DLC. Turn ignition switch to ON position. Read and record scan tool
self-diagnostic output. Proceed to TROUBLE CODE DEFINITION.
Page 745 of 1501
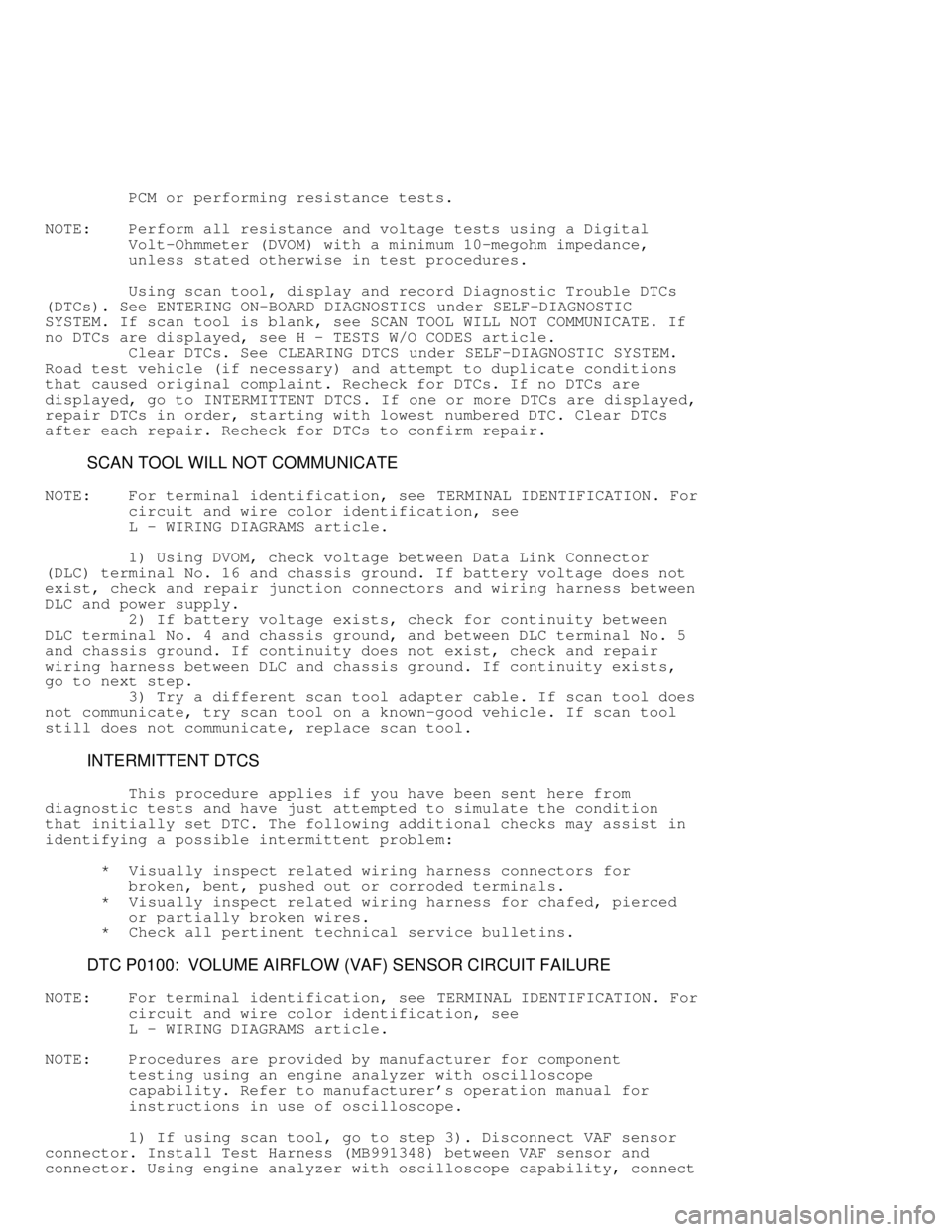
PCM or performing resistance tests.
NOTE: Perform all resistance and voltage tests using a Digital
Volt-Ohmmeter (DVOM) with a minimum 10-megohm impedance,
unless stated otherwise in test procedures.
Using scan tool, display and record Diagnostic Trouble DTCs
(DTCs). See ENTERING ON-BOARD DIAGNOSTICS under SELF-DIAGNOSTIC
SYSTEM. If scan tool is blank, see SCAN TOOL WILL NOT COMMUNICATE. If
no DTCs are displayed, see H - TESTS W/O CODES article.
Clear DTCs. See CLEARING DTCS under SELF-DIAGNOSTIC SYSTEM.
Road test vehicle (if necessary) and attempt to duplicate conditions
that caused original complaint. Recheck for DTCs. If no DTCs are
displayed, go to INTERMITTENT DTCS. If one or more DTCs are displayed,
repair DTCs in order, starting with lowest numbered DTC. Clear DTCs
after each repair. Recheck for DTCs to confirm repair.
SCAN TOOL WILL NOT COMMUNICATE
NOTE: For terminal identification, see TERMINAL IDENTIFICATION. For
circuit and wire color identification, see
L - WIRING DIAGRAMS article.
1) Using DVOM, check voltage between Data Link Connector
(DLC) terminal No. 16 and chassis ground. If battery voltage does not
exist, check and repair junction connectors and wiring harness between
DLC and power supply.
2) If battery voltage exists, check for continuity between
DLC terminal No. 4 and chassis ground, and between DLC terminal No. 5
and chassis ground. If continuity does not exist, check and repair
wiring harness between DLC and chassis ground. If continuity exists,
go to next step.
3) Try a different scan tool adapter cable. If scan tool does
not communicate, try scan tool on a known-good vehicle. If scan tool
still does not communicate, replace scan tool.
INTERMITTENT DTCS
This procedure applies if you have been sent here from
diagnostic tests and have just attempted to simulate the condition
that initially set DTC. The following additional checks may assist in
identifying a possible intermittent problem:
* Visually inspect related wiring harness connectors for
broken, bent, pushed out or corroded terminals.
* Visually inspect related wiring harness for chafed, pierced
or partially broken wires.
* Check all pertinent technical service bulletins.
DTC P0100: VOLUME AIRFLOW (VAF) SENSOR CIRCUIT FAILURE
NOTE: For terminal identification, see TERMINAL IDENTIFICATION. For
circuit and wire color identification, see
L - WIRING DIAGRAMS article.
NOTE: Procedures are provided by manufacturer for component
testing using an engine analyzer with oscilloscope
capability. Refer to manufacturer's operation manual for
instructions in use of oscilloscope.
1) If using scan tool, go to step 3). Disconnect VAF sensor
connector. Install Test Harness (MB991348) between VAF sensor and
connector. Using engine analyzer with oscilloscope capability, connect
Page 746 of 1501
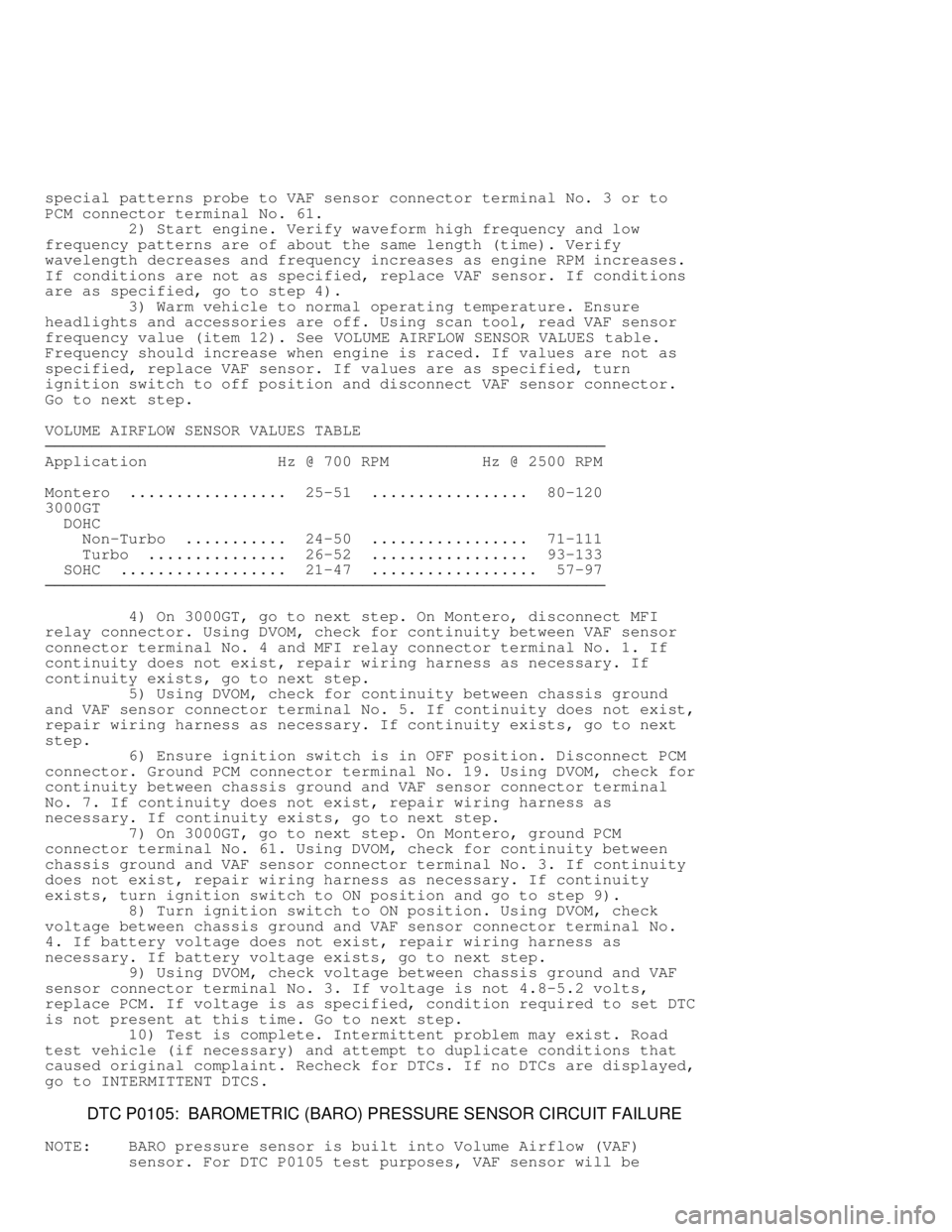
special patterns probe to VAF sensor connector terminal No. 3 or to
PCM connector terminal No. 61.
2) Start engine. Verify waveform high frequency and low
frequency patterns are of about the same length (time). Verify
wavelength decreases and frequency increases as engine RPM increases.
If conditions are not as specified, replace VAF sensor. If conditions
are as specified, go to step 4).
3) Warm vehicle to normal operating temperature. Ensure
headlights and accessories are off. Using scan tool, read VAF sensor
frequency value (item 12). See VOLUME AIRFLOW SENSOR VALUES table.
Frequency should increase when engine is raced. If values are not as
specified, replace VAF sensor. If values are as specified, turn
ignition switch to off position and disconnect VAF sensor connector.
Go to next step.
VOLUME AIRFLOW SENSOR VALUES TABLE
\
\
\
\
\
\
Application Hz @ 700 RPM Hz @ 2500 RPM
Montero ................. 25-51 ................. 80-120
3000GT
DOHC
Non-Turbo ........... 24-50 ................. 71-111
Turbo ............... 26-52 ................. 93-133
SOHC .................. 21-47 .................. 57-97
\
\
\
\
\
\
4) On 3000GT, go to next step. On Montero, disconnect MFI
relay connector. Using DVOM, check for continuity between VAF sensor
connector terminal No. 4 and MFI relay connector terminal No. 1. If
continuity does not exist, repair wiring harness as necessary. If
continuity exists, go to next step.
5) Using DVOM, check for continuity between chassis ground
and VAF sensor connector terminal No. 5. If continuity does not exist,
repair wiring harness as necessary. If continuity exists, go to next
step.
6) Ensure ignition switch is in OFF position. Disconnect PCM
connector. Ground PCM connector terminal No. 19. Using DVOM, check for
continuity between chassis ground and VAF sensor connector terminal
No. 7. If continuity does not exist, repair wiring harness as
necessary. If continuity exists, go to next step.
7) On 3000GT, go to next step. On Montero, ground PCM
connector terminal No. 61. Using DVOM, check for continuity between
chassis ground and VAF sensor connector terminal No. 3. If continuity
does not exist, repair wiring harness as necessary. If continuity
exists, turn ignition switch to ON position and go to step 9).
8) Turn ignition switch to ON position. Using DVOM, check
voltage between chassis ground and VAF sensor connector terminal No.
4. If battery voltage does not exist, repair wiring harness as
necessary. If battery voltage exists, go to next step.
9) Using DVOM, check voltage between chassis ground and VAF
sensor connector terminal No. 3. If voltage is not 4.8-5.2 volts,
replace PCM. If voltage is as specified, condition required to set DTC
is not present at this time. Go to next step.
10) Test is complete. Intermittent problem may exist. Road
test vehicle (if necessary) and attempt to duplicate conditions that
caused original complaint. Recheck for DTCs. If no DTCs are displayed,
go to INTERMITTENT DTCS .
DTC P0105: BAROMETRIC (BARO) PRESSURE SENSOR CIRCUIT FAILURE
NOTE: BARO pressure sensor is built into Volume Airflow (VAF)
sensor. For DTC P0105 test purposes, VAF sensor will be
Page 747 of 1501
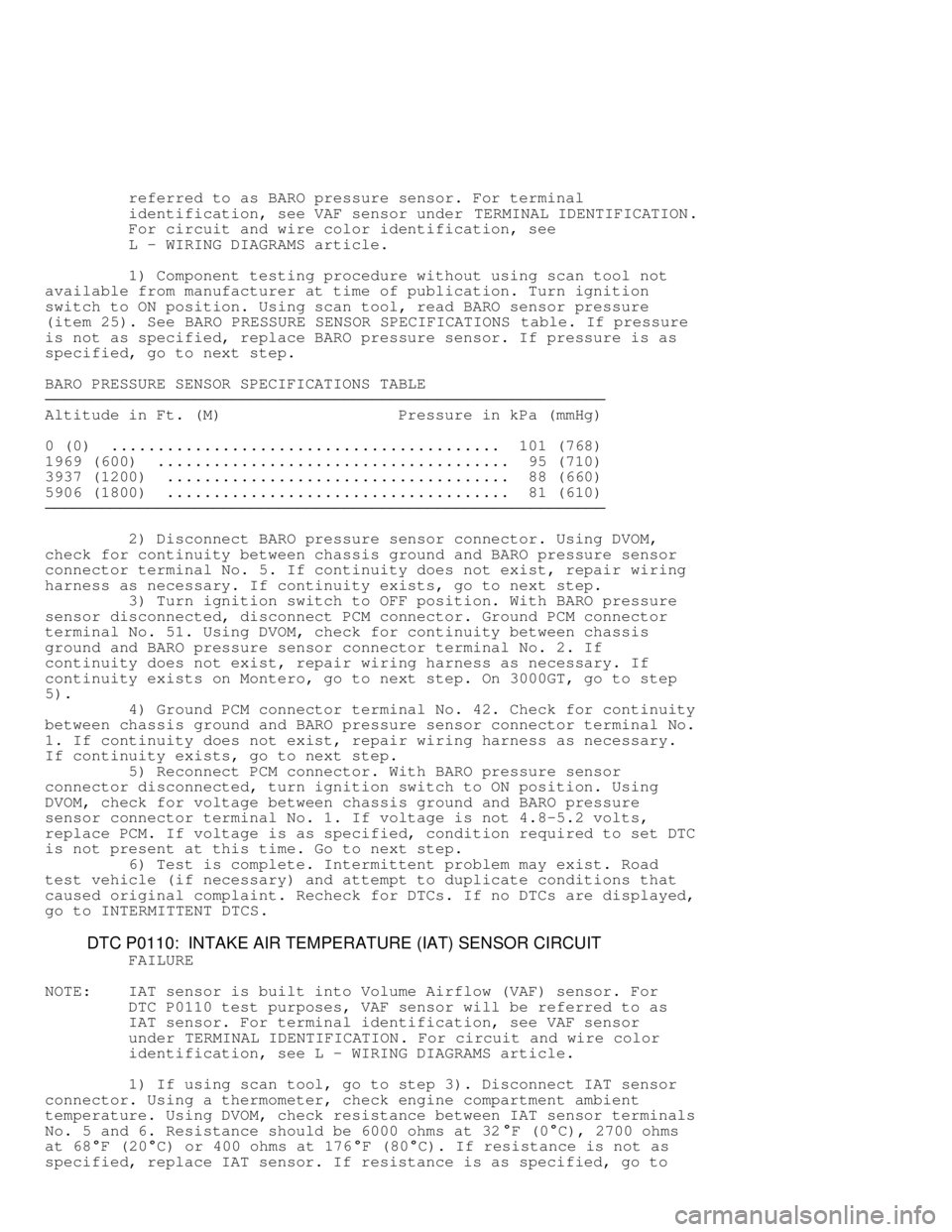
referred to as BARO pressure sensor. For terminal
identification, see VAF sensor under TERMINAL IDENTIFICATION.
For circuit and wire color identification, see
L - WIRING DIAGRAMS article.
1) Component testing procedure without using scan tool not
available from manufacturer at time of publication. Turn ignition
switch to ON position. Using scan tool, read BARO sensor pressure
(item 25). See BARO PRESSURE SENSOR SPECIFICATIONS table. If pressure
is not as specified, replace BARO pressure sensor. If pressure is as
specified, go to next step.
BARO PRESSURE SENSOR SPECIFICATIONS TABLE
\
\
\
\
\
\
Altitude in Ft. (M) Pressure in kPa (mmHg)
0 (0) .......................................... 101 (768)
1969 (600) ...................................... 95 (710)
3937 (1200) ..................................... 88 (660)
5906 (1800) ..................................... 81 (610)
\
\
\
\
\
\
2) Disconnect BARO pressure sensor connector. Using DVOM,
check for continuity between chassis ground and BARO pressure sensor
connector terminal No. 5. If continuity does not exist, repair wiring
harness as necessary. If continuity exists, go to next step.
3) Turn ignition switch to OFF position. With BARO pressure
sensor disconnected, disconnect PCM connector. Ground PCM connector
terminal No. 51. Using DVOM, check for continuity between chassis
ground and BARO pressure sensor connector terminal No. 2. If
continuity does not exist, repair wiring harness as necessary. If
continuity exists on Montero, go to next step. On 3000GT, go to step
5).
4) Ground PCM connector terminal No. 42. Check for continuity
between chassis ground and BARO pressure sensor connector terminal No.
1. If continuity does not exist, repair wiring harness as necessary.
If continuity exists, go to next step.
5) Reconnect PCM connector. With BARO pressure sensor
connector disconnected, turn ignition switch to ON position. Using
DVOM, check for voltage between chassis ground and BARO pressure
sensor connector terminal No. 1. If voltage is not 4.8-5.2 volts,
replace PCM. If voltage is as specified, condition required to set DTC
is not present at this time. Go to next step.
6) Test is complete. Intermittent problem may exist. Road
test vehicle (if necessary) and attempt to duplicate conditions that
caused original complaint. Recheck for DTCs. If no DTCs are displayed,
go to INTERMITTENT DTCS .
DTC P0110: INTAKE AIR TEMPERATURE (IAT) SENSOR CIRCUIT
FAILURE
NOTE: IAT sensor is built into Volume Airflow (VAF) sensor. For
DTC P0110 test purposes, VAF sensor will be referred to as
IAT sensor. For terminal identification, see VAF sensor
under TERMINAL IDENTIFICATION . For circuit and wire color
identification, see L - WIRING DIAGRAMS article.
1) If using scan tool, go to step 3). Disconnect IAT sensor
connector. Using a thermometer, check engine compartment ambient
temperature. Using DVOM, check resistance between IAT sensor terminals
No. 5 and 6. Resistance should be 6000 ohms at 32
F (0C), 2700 ohms
at 68F (20C) or 400 ohms at 176F (80C). If resistance is not as
specified, replace IAT sensor. If resistance is as specified, go to
Page 749 of 1501
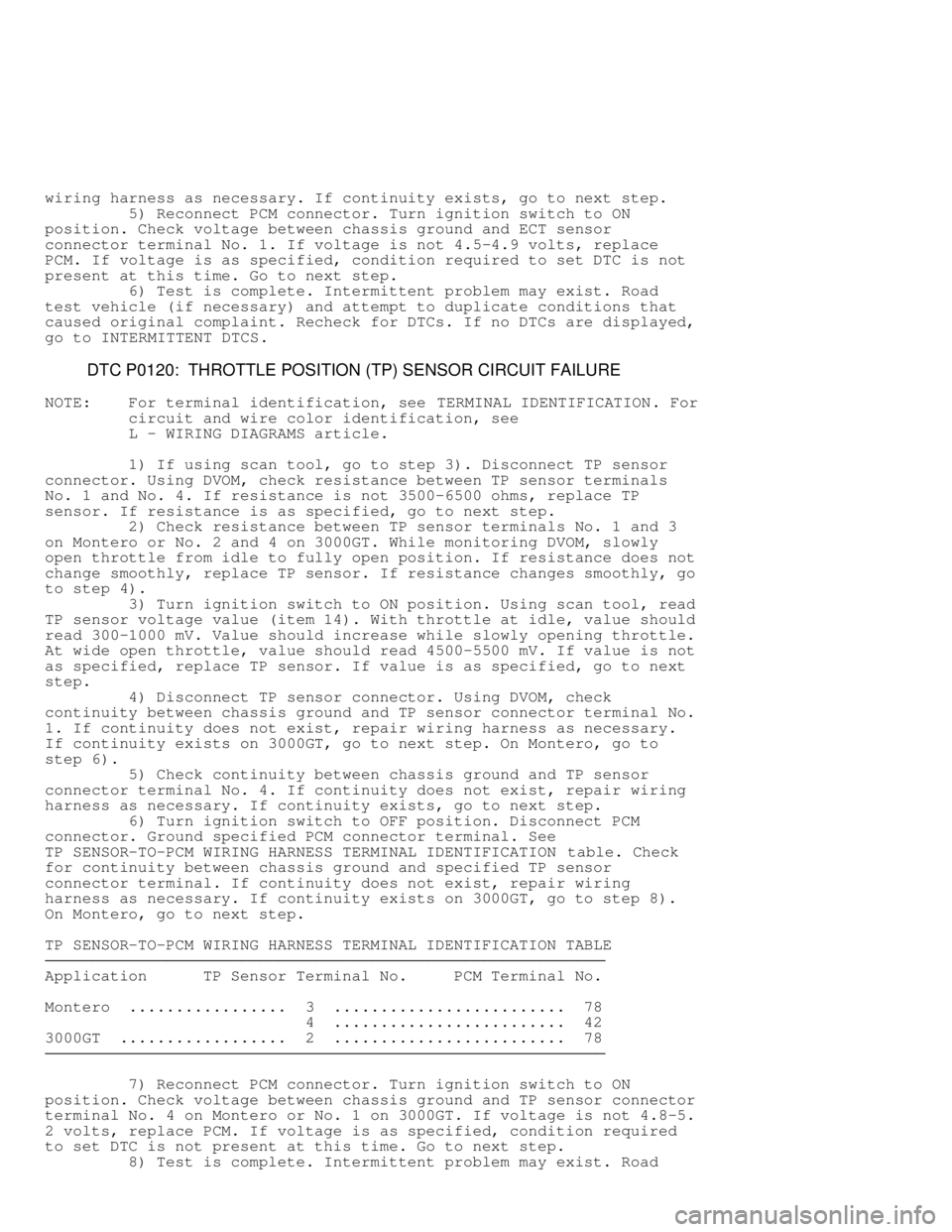
wiring harness as necessary. If continuity exists, go to next step.
5) Reconnect PCM connector. Turn ignition switch to ON
position. Check voltage between chassis ground and ECT sensor
connector terminal No. 1. If voltage is not 4.5-4.9 volts, replace
PCM. If voltage is as specified, condition required to set DTC is not
present at this time. Go to next step.
6) Test is complete. Intermittent problem may exist. Road
test vehicle (if necessary) and attempt to duplicate conditions that
caused original complaint. Recheck for DTCs. If no DTCs are displayed,
go to INTERMITTENT DTCS .
DTC P0120: THROTTLE POSITION (TP) SENSOR CIRCUIT FAILURE
NOTE: For terminal identification, see TERMINAL IDENTIFICATION. For
circuit and wire color identification, see
L - WIRING DIAGRAMS article.
1) If using scan tool, go to step 3). Disconnect TP sensor
connector. Using DVOM, check resistance between TP sensor terminals
No. 1 and No. 4. If resistance is not 3500-6500 ohms, replace TP
sensor. If resistance is as specified, go to next step.
2) Check resistance between TP sensor terminals No. 1 and 3
on Montero or No. 2 and 4 on 3000GT. While monitoring DVOM, slowly
open throttle from idle to fully open position. If resistance does not
change smoothly, replace TP sensor. If resistance changes smoothly, go
to step 4).
3) Turn ignition switch to ON position. Using scan tool, read
TP sensor voltage value (item 14). With throttle at idle, value should\
read 300-1000 mV. Value should increase while slowly opening throttle.
At wide open throttle, value should read 4500-5500 mV. If value is not
as specified, replace TP sensor. If value is as specified, go to next
step.
4) Disconnect TP sensor connector. Using DVOM, check
continuity between chassis ground and TP sensor connector terminal No.
1. If continuity does not exist, repair wiring harness as necessary.
If continuity exists on 3000GT, go to next step. On Montero, go to
step 6).
5) Check continuity between chassis ground and TP sensor
connector terminal No. 4. If continuity does not exist, repair wiring
harness as necessary. If continuity exists, go to next step.
6) Turn ignition switch to OFF position. Disconnect PCM
connector. Ground specified PCM connector terminal. See
TP SENSOR-TO-PCM WIRING HARNESS TERMINAL IDENTIFICATION table. Check
for continuity between chassis ground and specified TP sensor
connector terminal. If continuity does not exist, repair wiring
harness as necessary. If continuity exists on 3000GT, go to step 8).
On Montero, go to next step.
TP SENSOR-TO-PCM WIRING HARNESS TERMINAL IDENTIFICATION TABLE
\
\
\
\
\
\
Application TP Sensor Terminal No. PCM Terminal No.
Montero ................. 3 ......................... 78
4 ......................... 42
3000GT .................. 2 ......................... 78
\
\
\
\
\
\
7) Reconnect PCM connector. Turn ignition switch to ON
position. Check voltage between chassis ground and TP sensor connector
terminal No. 4 on Montero or No. 1 on 3000GT. If voltage is not 4.8-5.
2 volts, replace PCM. If voltage is as specified, condition required
to set DTC is not present at this time. Go to next step.
8) Test is complete. Intermittent problem may exist. Road
Page 750 of 1501
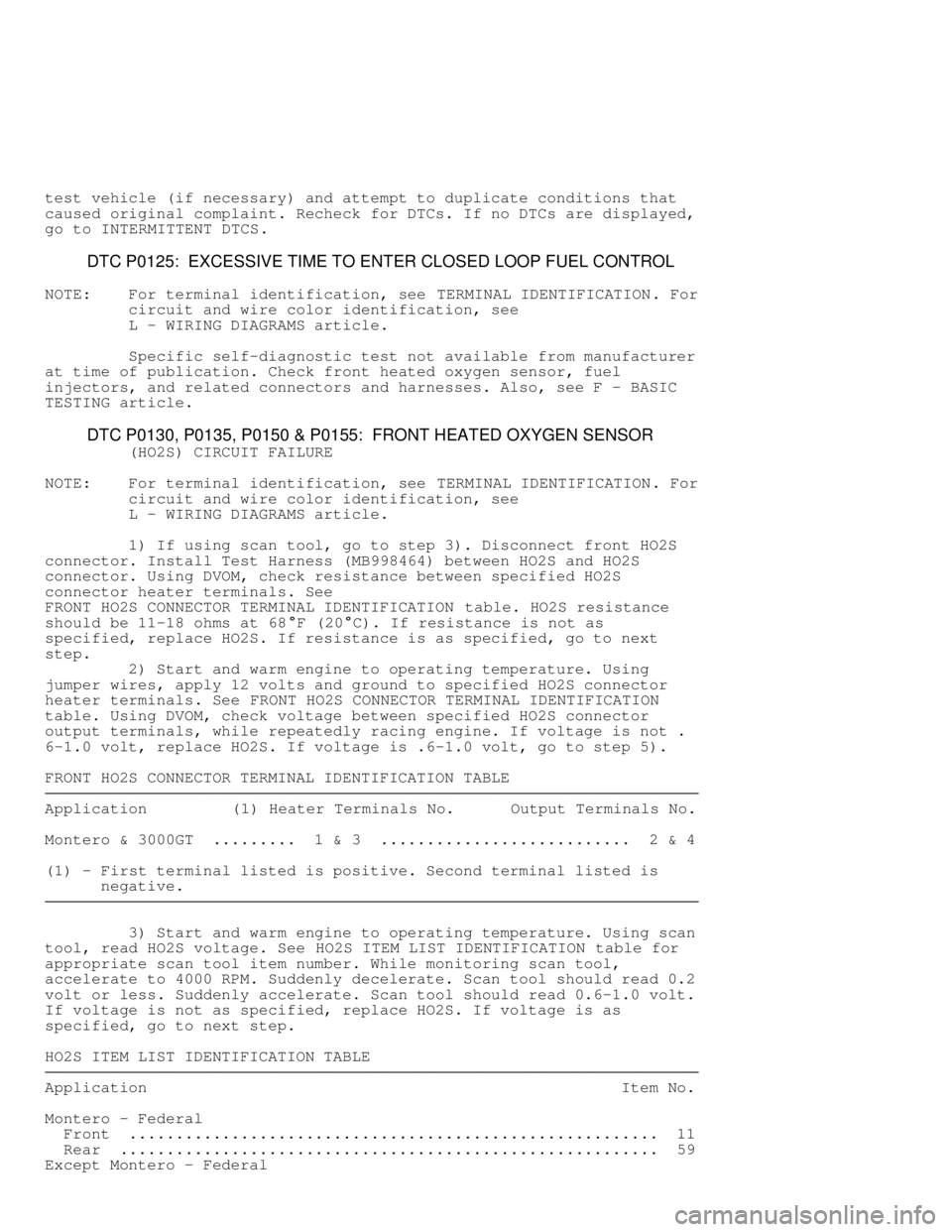
test vehicle (if necessary) and attempt to duplicate conditions that
caused original complaint. Recheck for DTCs. If no DTCs are displayed,
go to INTERMITTENT DTCS .
DTC P0125: EXCESSIVE TIME TO ENTER CLOSED LOOP FUEL CONTROL
NOTE: For terminal identification, see TERMINAL IDENTIFICATION. For
circuit and wire color identification, see
L - WIRING DIAGRAMS article.
Specific self-diagnostic test not available from manufacturer
at time of publication. Check front heated oxygen sensor, fuel
injectors, and related connectors and harnesses. Also, see F - BASIC
TESTING article.
DTC P0130, P0135, P0150 & P0155: FRONT HEATED OXYGEN SENSOR
(HO2S) CIRCUIT FAILURE
NOTE: For terminal identification, see TERMINAL IDENTIFICATION. For
circuit and wire color identification, see
L - WIRING DIAGRAMS article.
1) If using scan tool, go to step 3). Disconnect front HO2S
connector. Install Test Harness (MB998464) between HO2S and HO2S
connector. Using DVOM, check resistance between specified HO2S
connector heater terminals. See
FRONT HO2S CONNECTOR TERMINAL IDENTIFICATION table. HO2S resistance
should be 11-18 ohms at 68
F (20C). If resistance is not as
specified, replace HO2S. If resistance is as specified, go to next
step.
2) Start and warm engine to operating temperature. Using
jumper wires, apply 12 volts and ground to specified HO2S connector
heater terminals. See FRONT HO2S CONNECTOR TERMINAL IDENTIFICATION
table. Using DVOM, check voltage between specified HO2S connector
output terminals, while repeatedly racing engine. If voltage is not .
6-1.0 volt, replace HO2S. If voltage is .6-1.0 volt, go to step 5).
FRONT HO2S CONNECTOR TERMINAL IDENTIFICATION TABLE
\
\
\
\
\
\
\
Application (1) Heater Terminals No. Output Terminals No.
Montero & 3000GT ......... 1 & 3 ........................... 2 & 4
( 1) - First terminal listed is positive. Second terminal listed is
negative.
\
\
\
\
\
\
\
3) Start and warm engine to operating temperature. Using scan
tool, read HO2S voltage. See HO2S ITEM LIST IDENTIFICATION table for
appropriate scan tool item number. While monitoring scan tool,
accelerate to 4000 RPM. Suddenly decelerate. Scan tool should read 0.2
volt or less. Suddenly accelerate. Scan tool should read 0.6-1.0 volt.
If voltage is not as specified, replace HO2S. If voltage is as
specified, go to next step.
HO2S ITEM LIST IDENTIFICATION TABLE
\
\
\
\
\
\
\
Application Item No.
Montero - Federal
Front ......................................................... 11
Rear .......................................................... 59
Except Montero - Federal
Page 751 of 1501
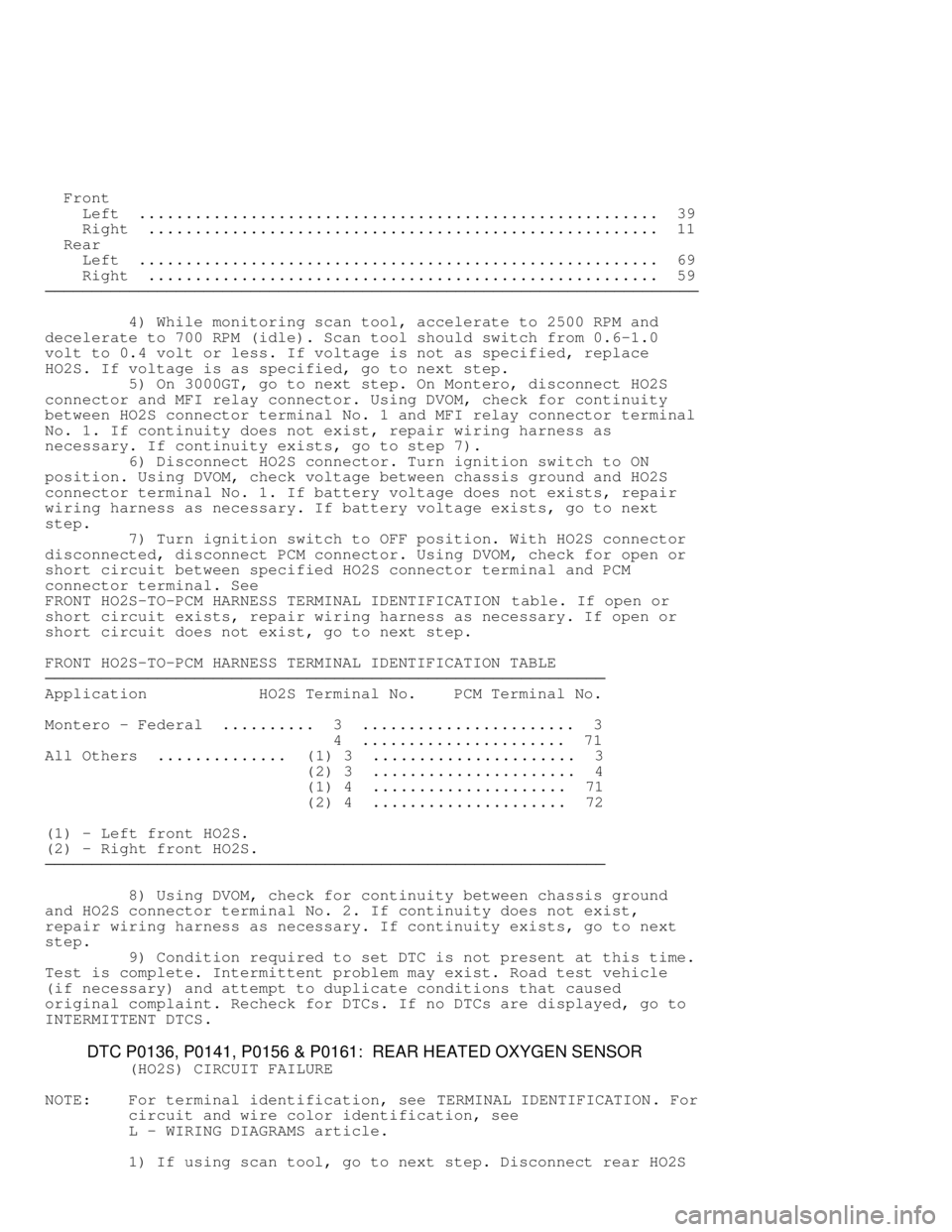
Front
Left ........................................................ 39
Right ....................................................... 11
Rear
Left ........................................................ 69
Right ....................................................... 59
\
\
\
\
\
\
\
4) While monitoring scan tool, accelerate to 2500 RPM and
decelerate to 700 RPM (idle). Scan tool should switch from 0.6-1.0
volt to 0.4 volt or less. If voltage is not as specified, replace
HO2S. If voltage is as specified, go to next step.
5) On 3000GT, go to next step. On Montero, disconnect HO2S
connector and MFI relay connector. Using DVOM, check for continuity
between HO2S connector terminal No. 1 and MFI relay connector terminal
No. 1. If continuity does not exist, repair wiring harness as
necessary. If continuity exists, go to step 7).
6) Disconnect HO2S connector. Turn ignition switch to ON
position. Using DVOM, check voltage between chassis ground and HO2S
connector terminal No. 1. If battery voltage does not exists, repair
wiring harness as necessary. If battery voltage exists, go to next
step.
7) Turn ignition switch to OFF position. With HO2S connector
disconnected, disconnect PCM connector. Using DVOM, check for open or
short circuit between specified HO2S connector terminal and PCM
connector terminal. See
FRONT HO2S-TO-PCM HARNESS TERMINAL IDENTIFICATION table. If open or
short circuit exists, repair wiring harness as necessary. If open or
short circuit does not exist, go to next step.
FRONT HO2S-TO-PCM HARNESS TERMINAL IDENTIFICATION TABLE
\
\
\
\
\
\
Application HO2S Terminal No. PCM Terminal No.
Montero - Federal .......... 3 ....................... 3
4 ...................... 71
All Others .............. ( 1) 3 ...................... 3
( 2) 3 ...................... 4
( 1) 4 ..................... 71
( 2) 4 ..................... 72
( 1) - Left front HO2S.
( 2) - Right front HO2S.
\
\
\
\
\
\
8) Using DVOM, check for continuity between chassis ground
and HO2S connector terminal No. 2. If continuity does not exist,
repair wiring harness as necessary. If continuity exists, go to next
step.
9) Condition required to set DTC is not present at this time.
Test is complete. Intermittent problem may exist. Road test vehicle
(if necessary) and attempt to duplicate conditions that caused
original complaint. Recheck for DTCs. If no DTCs are displayed, go to
INTERMITTENT DTCS .
DTC P0136, P0141, P0156 & P0161: REAR HEATED OXYGEN SENSOR
(HO2S) CIRCUIT FAILURE
NOTE: For terminal identification, see TERMINAL IDENTIFICATION. For
circuit and wire color identification, see
L - WIRING DIAGRAMS article.
1) If using scan tool, go to next step. Disconnect rear HO2S