brake sensor MITSUBISHI MONTERO 1998 Owner's Guide
[x] Cancel search | Manufacturer: MITSUBISHI, Model Year: 1998, Model line: MONTERO, Model: MITSUBISHI MONTERO 1998Pages: 1501, PDF Size: 25.81 MB
Page 233 of 1501
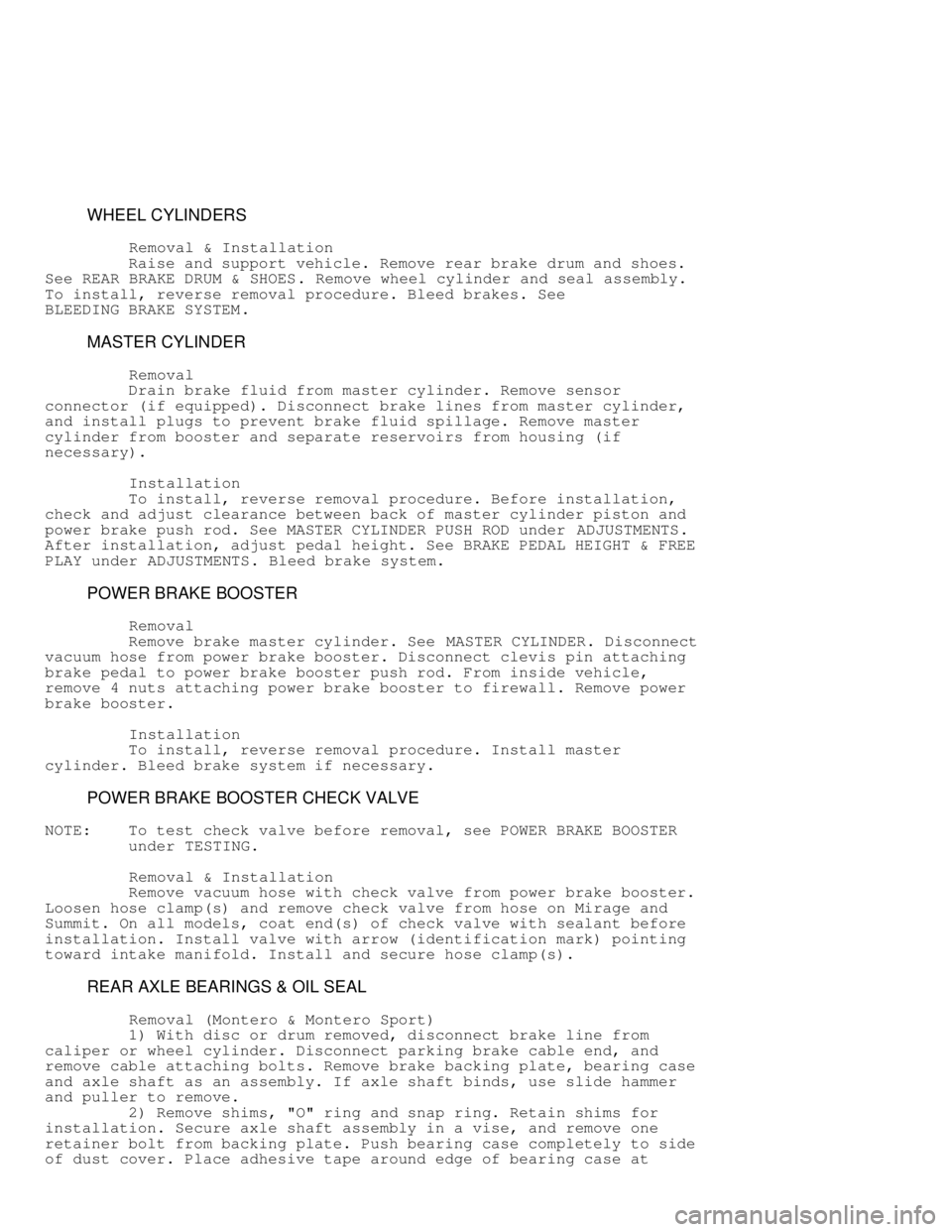
WHEEL CYLINDERS
Removal & Installation
Raise and support vehicle. Remove rear brake drum and shoes.
See REAR BRAKE DRUM & SHOES . Remove wheel cylinder and seal assembly.
To install, reverse removal procedure. Bleed brakes. See
BLEEDING BRAKE SYSTEM .
MASTER CYLINDER
Removal
Drain brake fluid from master cylinder. Remove sensor
connector (if equipped). Disconnect brake lines from master cylinder,
and install plugs to prevent brake fluid spillage. Remove master
cylinder from booster and separate reservoirs from housing (if
necessary).
Installation
To install, reverse removal procedure. Before installation,
check and adjust clearance between back of master cylinder piston and
power brake push rod. See MASTER CYLINDER PUSH ROD under ADJUSTMENTS.
After installation, adjust pedal height. See BRAKE PEDAL HEIGHT & FREE
PLAY under ADJUSTMENTS. Bleed brake system.
POWER BRAKE BOOSTER
Removal
Remove brake master cylinder. See MASTER CYLINDER. Disconnect
vacuum hose from power brake booster. Disconnect clevis pin attaching
brake pedal to power brake booster push rod. From inside vehicle,
remove 4 nuts attaching power brake booster to firewall. Remove power
brake booster.
Installation
To install, reverse removal procedure. Install master
cylinder. Bleed brake system if necessary.
POWER BRAKE BOOSTER CHECK VALVE
NOTE: To test check valve before removal, see POWER BRAKE BOOSTER
under TESTING.
Removal & Installation
Remove vacuum hose with check valve from power brake booster.
Loosen hose clamp(s) and remove check valve from hose on Mirage and
Summit. On all models, coat end(s) of check valve with sealant before
installation. Install valve with arrow (identification mark) pointing
toward intake manifold. Install and secure hose clamp(s).
REAR AXLE BEARINGS & OIL SEAL
Removal (Montero & Montero Sport)
1) With disc or drum removed, disconnect brake line from
caliper or wheel cylinder. Disconnect parking brake cable end, and
remove cable attaching bolts. Remove brake backing plate, bearing case
and axle shaft as an assembly. If axle shaft binds, use slide hammer
and puller to remove.
2) Remove shims, "O" ring and snap ring. Retain shims for
installation. Secure axle shaft assembly in a vise, and remove one
retainer bolt from backing plate. Push bearing case completely to side
of dust cover. Place adhesive tape around edge of bearing case at
Page 235 of 1501
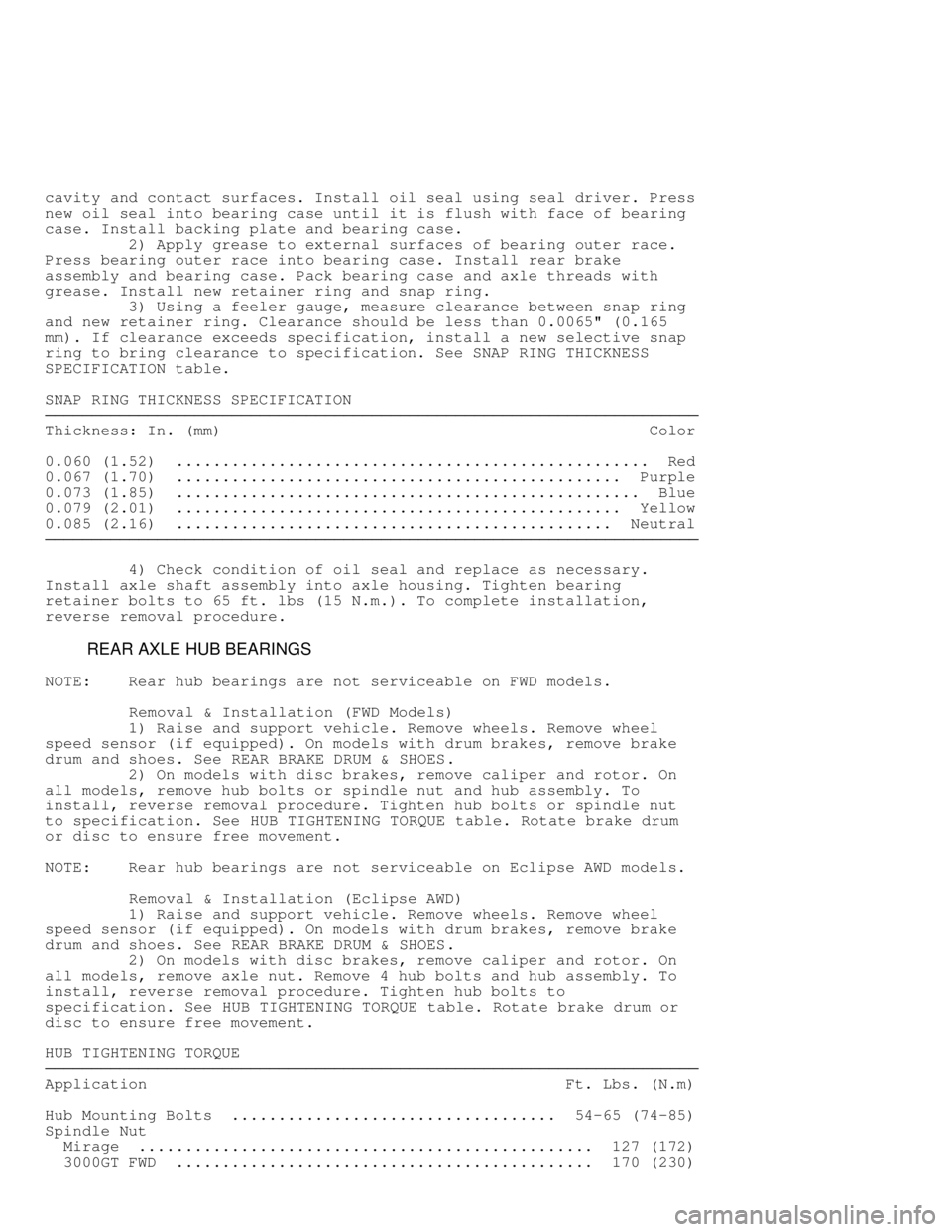
cavity and contact surfaces. Install oil seal using seal driver. Press
new oil seal into bearing case until it is flush with face of bearing
case. Install backing plate and bearing case.
2) Apply grease to external surfaces of bearing outer race.
Press bearing outer race into bearing case. Install rear brake
assembly and bearing case. Pack bearing case and axle threads with
grease. Install new retainer ring and snap ring.
3) Using a feeler gauge, measure clearance between snap ring
and new retainer ring. Clearance should be less than 0.0065" (0.165
mm). If clearance exceeds specification, install a new selective snap
ring to bring clearance to specification. See SNAP RING THICKNESS
SPECIFICATION table.
SNAP RING THICKNESS SPECIFICATION
\
\
\
\
\
\
\
Thickness: In. (mm) Color\
0.060 (1.52) ................................................... Red\
0.067 (1.70) ................................................ Purple\
0.073 (1.85) .................................................. Blue\
0.079 (2.01) ................................................ Yellow\
0.085 (2.16) ............................................... Neutral\
\
\
\
\
\
\
\
4) Check condition of oil seal and replace as necessary.
Install axle shaft assembly into axle housing. Tighten bearing
retainer bolts to 65 ft. lbs (15 N.m.). To complete installation,
reverse removal procedure.
REAR AXLE HUB BEARINGS
NOTE: Rear hub bearings are not serviceable on FWD models.
Removal & Installation (FWD Models)
1) Raise and support vehicle. Remove wheels. Remove wheel
speed sensor (if equipped). On models with drum brakes, remove brake
drum and shoes. See REAR BRAKE DRUM & SHOES .
2) On models with disc brakes, remove caliper and rotor. On
all models, remove hub bolts or spindle nut and hub assembly. To
install, reverse removal procedure. Tighten hub bolts or spindle nut
to specification. See HUB TIGHTENING TORQUE table. Rotate brake drum
or disc to ensure free movement.
NOTE: Rear hub bearings are not serviceable on Eclipse AWD models.
Removal & Installation (Eclipse AWD)
1) Raise and support vehicle. Remove wheels. Remove wheel
speed sensor (if equipped). On models with drum brakes, remove brake
drum and shoes. See REAR BRAKE DRUM & SHOES .
2) On models with disc brakes, remove caliper and rotor. On
all models, remove axle nut. Remove 4 hub bolts and hub assembly. To
install, reverse removal procedure. Tighten hub bolts to
specification. See HUB TIGHTENING TORQUE table. Rotate brake drum or
disc to ensure free movement.
HUB TIGHTENING TORQUE
\
\
\
\
\
\
\
Application Ft. Lbs. (N.m)\
Hub Mounting Bolts ................................... 54-65 (74-85)\
Spindle Nut
Mirage ................................................. 127 (172)\
3000GT FWD ............................................. 170 (230)\
Page 299 of 1501
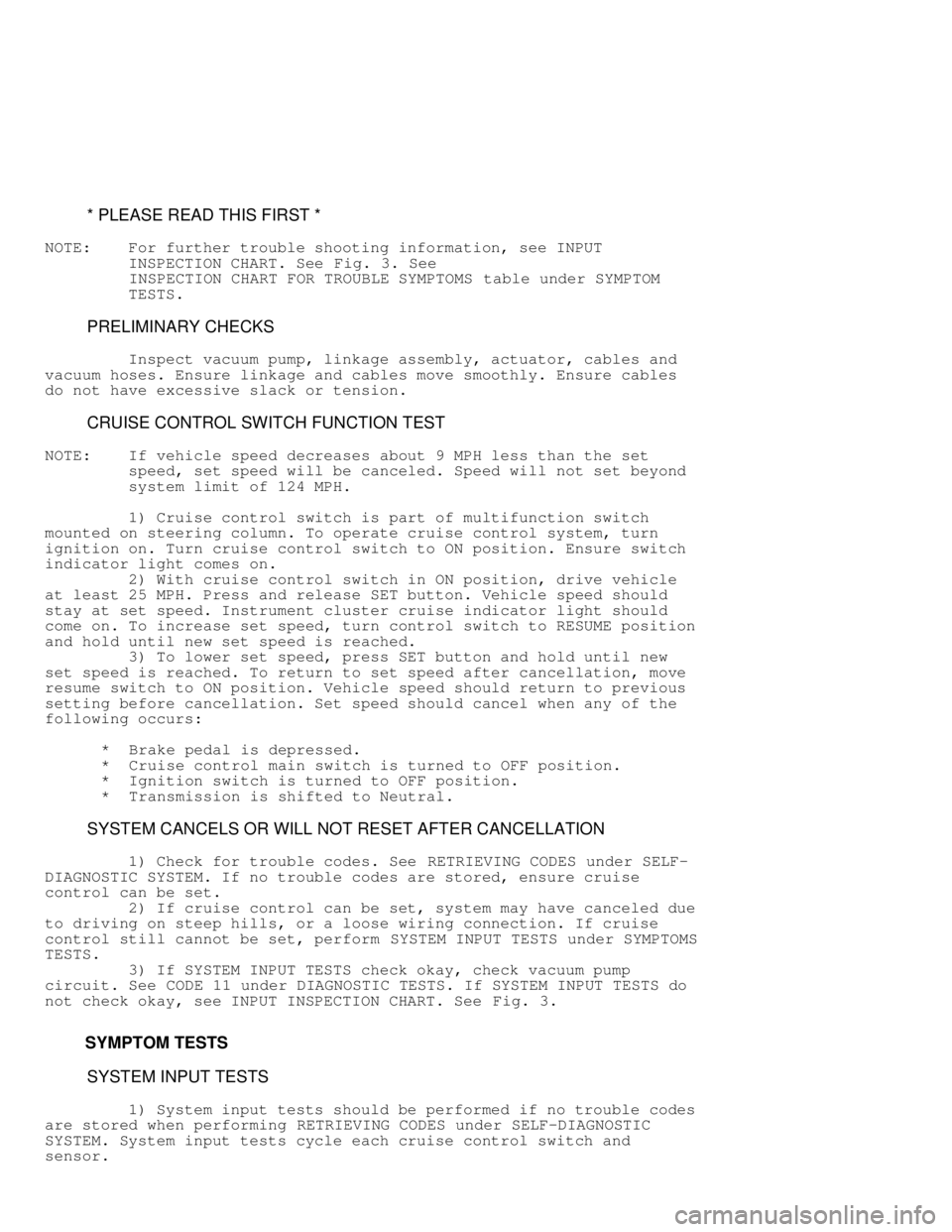
* PLEASE READ THIS FIRST *
NOTE: For further trouble shooting information, see INPUT
INSPECTION CHART. See Fig. 3. See
INSPECTION CHART FOR TROUBLE SYMPTOMS table under SYMPTOM
TESTS.
PRELIMINARY CHECKS
Inspect vacuum pump, linkage assembly, actuator, cables and
vacuum hoses. Ensure linkage and cables move smoothly. Ensure cables
do not have excessive slack or tension.
CRUISE CONTROL SWITCH FUNCTION TEST
NOTE: If vehicle speed decreases about 9 MPH less than the set
speed, set speed will be canceled. Speed will not set beyond
system limit of 124 MPH.
1) Cruise control switch is part of multifunction switch
mounted on steering column. To operate cruise control system, turn
ignition on. Turn cruise control switch to ON position. Ensure switch
indicator light comes on.
2) With cruise control switch in ON position, drive vehicle
at least 25 MPH. Press and release SET button. Vehicle speed should
stay at set speed. Instrument cluster cruise indicator light should
come on. To increase set speed, turn control switch to RESUME position
and hold until new set speed is reached.
3) To lower set speed, press SET button and hold until new
set speed is reached. To return to set speed after cancellation, move
resume switch to ON position. Vehicle speed should return to previous
setting before cancellation. Set speed should cancel when any of the
following occurs:
* Brake pedal is depressed.
* Cruise control main switch is turned to OFF position.
* Ignition switch is turned to OFF position.
* Transmission is shifted to Neutral.
SYSTEM CANCELS OR WILL NOT RESET AFTER CANCELLATION
1) Check for trouble codes. See RETRIEVING CODES under SELF-
DIAGNOSTIC SYSTEM. If no trouble codes are stored, ensure cruise
control can be set.
2) If cruise control can be set, system may have canceled due
to driving on steep hills, or a loose wiring connection. If cruise
control still cannot be set, perform SYSTEM INPUT TESTS under SYMPTOMS
TESTS.
3) If SYSTEM INPUT TESTS check okay, check vacuum pump
circuit. See CODE 11 under DIAGNOSTIC TESTS. If SYSTEM INPUT TESTS do
not check okay, see INPUT INSPECTION CHART. See Fig. 3.
SYMPTOM TESTS
SYSTEM INPUT TESTS
1) System input tests should be performed if no trouble codes
are stored when performing RETRIEVING CODES under SELF-DIAGNOSTIC
SYSTEM. System input tests cycle each cruise control switch and
sensor.
Page 325 of 1501
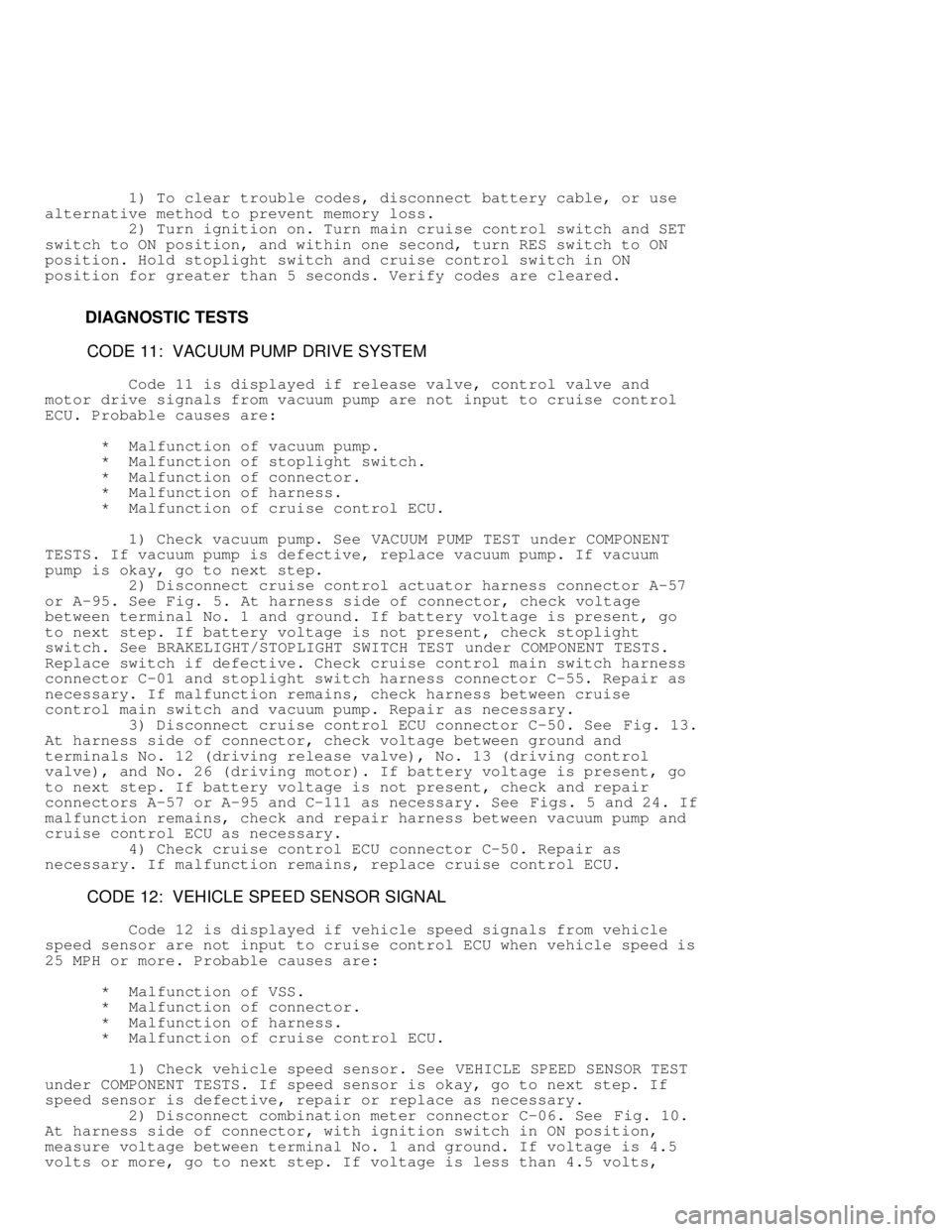
1) To clear trouble codes, disconnect battery cable, or use
alternative method to prevent memory loss.
2) Turn ignition on. Turn main cruise control switch and SET
switch to ON position, and within one second, turn RES switch to ON
position. Hold stoplight switch and cruise control switch in ON
position for greater than 5 seconds. Verify codes are cleared.
DIAGNOSTIC TESTS
CODE 11: VACUUM PUMP DRIVE SYSTEM
Code 11 is displayed if release valve, control valve and
motor drive signals from vacuum pump are not input to cruise control
ECU. Probable causes are:
* Malfunction of vacuum pump.
* Malfunction of stoplight switch.
* Malfunction of connector.
* Malfunction of harness.
* Malfunction of cruise control ECU.
1) Check vacuum pump. See VACUUM PUMP TEST under COMPONENT
TESTS. If vacuum pump is defective, replace vacuum pump. If vacuum
pump is okay, go to next step.
2) Disconnect cruise control actuator harness connector A-57
or A-95. See Fig. 5. At harness side of connector, check voltage
between terminal No. 1 and ground. If battery voltage is present, go
to next step. If battery voltage is not present, check stoplight
switch. See BRAKELIGHT/STOPLIGHT SWITCH TEST under COMPONENT TESTS.
Replace switch if defective. Check cruise control main switch harness
connector C-01 and stoplight switch harness connector C-55. Repair as
necessary. If malfunction remains, check harness between cruise
control main switch and vacuum pump. Repair as necessary.
3) Disconnect cruise control ECU connector C-50. See Fig. 13.
At harness side of connector, check voltage between ground and
terminals No. 12 (driving release valve), No. 13 (driving control
valve), and No. 26 (driving motor). If battery voltage is present, go\
to next step. If battery voltage is not present, check and repair
connectors A-57 or A-95 and C-111 as necessary. See Figs. 5 and 24. If
malfunction remains, check and repair harness between vacuum pump and
cruise control ECU as necessary.
4) Check cruise control ECU connector C-50. Repair as
necessary. If malfunction remains, replace cruise control ECU.
CODE 12: VEHICLE SPEED SENSOR SIGNAL
Code 12 is displayed if vehicle speed signals from vehicle
speed sensor are not input to cruise control ECU when vehicle speed is
25 MPH or more. Probable causes are:
* Malfunction of VSS.
* Malfunction of connector.
* Malfunction of harness.
* Malfunction of cruise control ECU.
1) Check vehicle speed sensor. See VEHICLE SPEED SENSOR TEST
under COMPONENT TESTS. If speed sensor is okay, go to next step. If
speed sensor is defective, repair or replace as necessary.
2) Disconnect combination meter connector C-06. See Fig. 10.
At harness side of connector, with ignition switch in ON position,
measure voltage between terminal No. 1 and ground. If voltage is 4.5
volts or more, go to next step. If voltage is less than 4.5 volts,
Page 326 of 1501
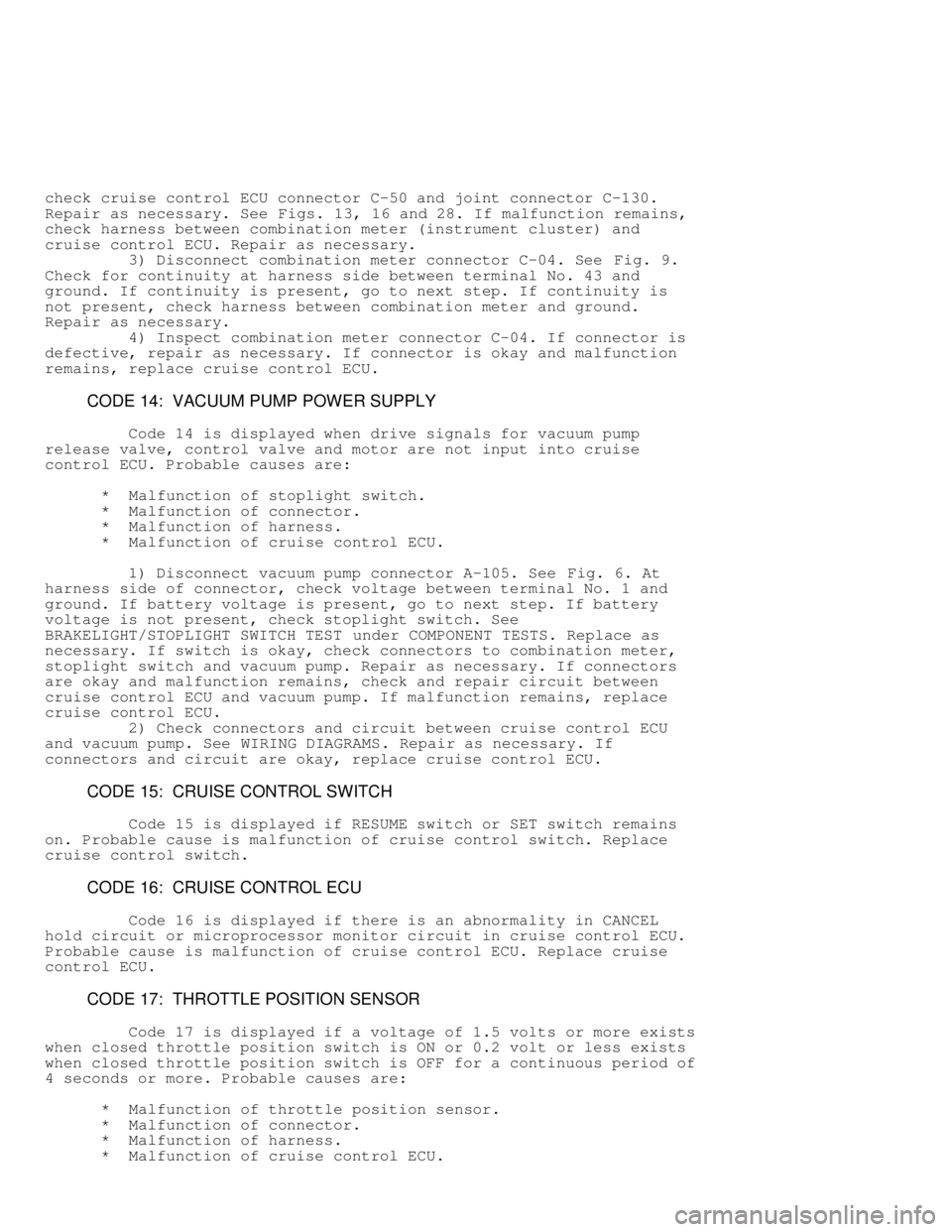
check cruise control ECU connector C-50 and joint connector C-130.
Repair as necessary. See Figs. 13, 16 and 28. If malfunction remains,
check harness between combination meter (instrument cluster) and
cruise control ECU. Repair as necessary.
3) Disconnect combination meter connector C-04. See Fig. 9.
Check for continuity at harness side between terminal No. 43 and
ground. If continuity is present, go to next step. If continuity is
not present, check harness between combination meter and ground.
Repair as necessary.
4) Inspect combination meter connector C-04. If connector is
defective, repair as necessary. If connector is okay and malfunction
remains, replace cruise control ECU.
CODE 14: VACUUM PUMP POWER SUPPLY
Code 14 is displayed when drive signals for vacuum pump
release valve, control valve and motor are not input into cruise
control ECU. Probable causes are:
* Malfunction of stoplight switch.
* Malfunction of connector.
* Malfunction of harness.
* Malfunction of cruise control ECU.
1) Disconnect vacuum pump connector A-105. See Fig. 6. At
harness side of connector, check voltage between terminal No. 1 and
ground. If battery voltage is present, go to next step. If battery
voltage is not present, check stoplight switch. See
BRAKELIGHT/STOPLIGHT SWITCH TEST under COMPONENT TESTS. Replace as
necessary. If switch is okay, check connectors to combination meter,
stoplight switch and vacuum pump. Repair as necessary. If connectors
are okay and malfunction remains, check and repair circuit between
cruise control ECU and vacuum pump. If malfunction remains, replace
cruise control ECU.
2) Check connectors and circuit between cruise control ECU
and vacuum pump. See WIRING DIAGRAMS. Repair as necessary. If
connectors and circuit are okay, replace cruise control ECU.
CODE 15: CRUISE CONTROL SWITCH
Code 15 is displayed if RESUME switch or SET switch remains
on. Probable cause is malfunction of cruise control switch. Replace
cruise control switch.
CODE 16: CRUISE CONTROL ECU
Code 16 is displayed if there is an abnormality in CANCEL
hold circuit or microprocessor monitor circuit in cruise control ECU.
Probable cause is malfunction of cruise control ECU. Replace cruise
control ECU.
CODE 17: THROTTLE POSITION SENSOR
Code 17 is displayed if a voltage of 1.5 volts or more exists
when closed throttle position switch is ON or 0.2 volt or less exists
when closed throttle position switch is OFF for a continuous period of
4 seconds or more. Probable causes are:
* Malfunction of throttle position sensor.
* Malfunction of connector.
* Malfunction of harness.
* Malfunction of cruise control ECU.
Page 372 of 1501
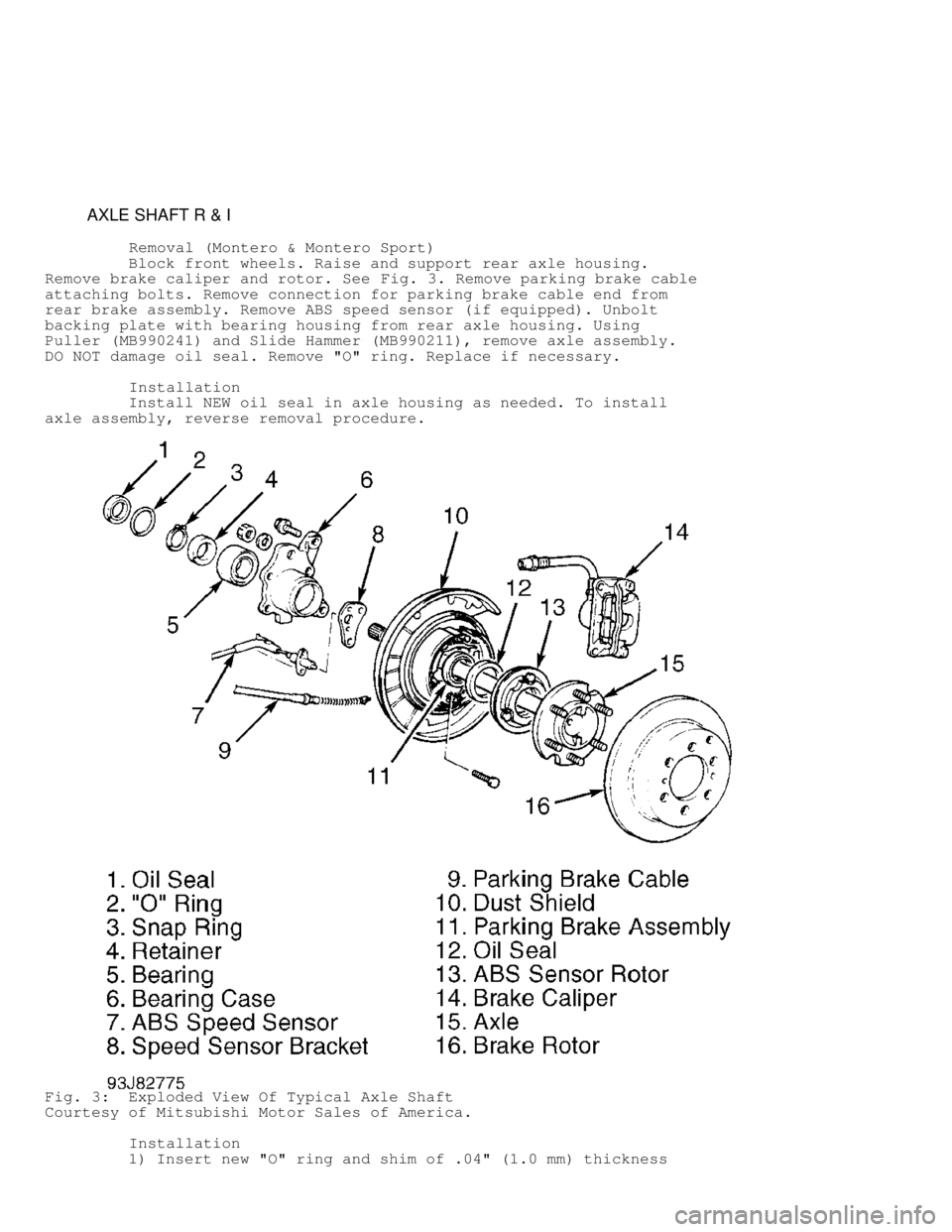
AXLE SHAFT R & I
Removal (Montero & Montero Sport)
Block front wheels. Raise and support rear axle housing.
Remove brake caliper and rotor. See Fig. 3. Remove parking brake cable
attaching bolts. Remove connection for parking brake cable end from
rear brake assembly. Remove ABS speed sensor (if equipped). Unbolt
backing plate with bearing housing from rear axle housing. Using
Puller (MB990241) and Slide Hammer (MB990211), remove axle assembly.\
DO NOT damage oil seal. Remove "O" ring. Replace if necessary.
Installation
Install NEW oil seal in axle housing as needed. To install
axle assembly, reverse removal procedure.
Fig. 3: Exploded View Of Typical Axle Shaft
Courtesy of Mitsubishi Motor Sales of America.
Installation
1) Insert new "O" ring and shim of .04" (1.0 mm) thickness
Page 416 of 1501
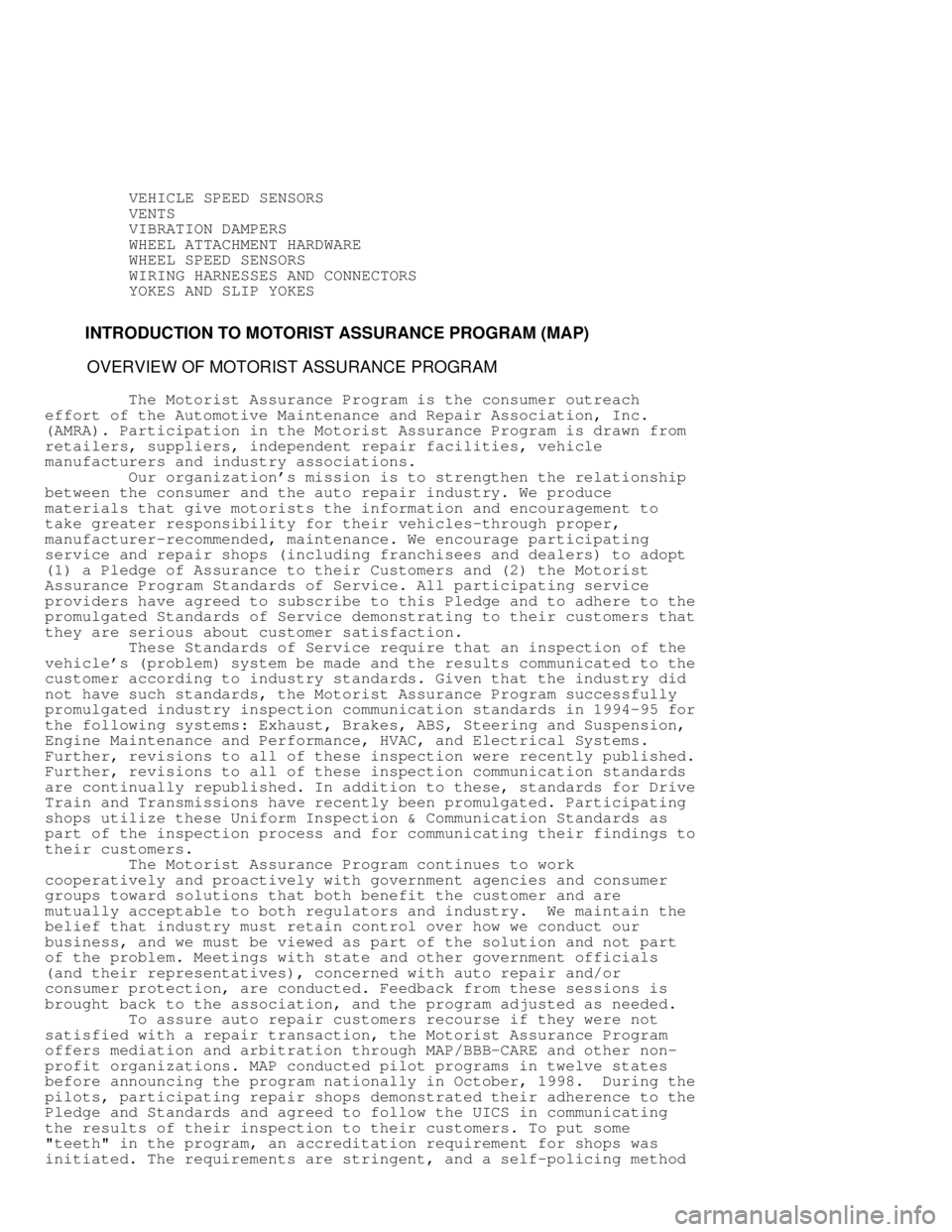
VEHICLE SPEED SENSORS
VENTS
VIBRATION DAMPERS
WHEEL ATTACHMENT HARDWARE
WHEEL SPEED SENSORS
WIRING HARNESSES AND CONNECTORS
YOKES AND SLIP YOKES
INTRODUCTION TO MOTORIST ASSURANCE PROGRAM (MAP)
OVERVIEW OF MOTORIST ASSURANCE PROGRAM
The Motorist Assurance Program is the consumer outreach
effort of the Automotive Maintenance and Repair Association, Inc.
(AMRA). Participation in the Motorist Assurance Program is drawn from
retailers, suppliers, independent repair facilities, vehicle
manufacturers and industry associations.
Our organization's mission is to strengthen the relationship
between the consumer and the auto repair industry. We produce
materials that give motorists the information and encouragement to
take greater responsibility for their vehicles-through proper,
manufacturer-recommended, maintenance. We encourage participating
service and repair shops (including franchisees and dealers) to adopt
(1) a Pledge of Assurance to their Customers and (2) the Motorist
Assurance Program Standards of Service. All participating service
providers have agreed to subscribe to this Pledge and to adhere to the
promulgated Standards of Service demonstrating to their customers that
they are serious about customer satisfaction.
These Standards of Service require that an inspection of the
vehicle's (problem) system be made and the results communicated to the\
customer according to industry standards. Given that the industry did
not have such standards, the Motorist Assurance Program successfully
promulgated industry inspection communication standards in 1994-95 for
the following systems: Exhaust, Brakes, ABS, Steering and Suspension,
Engine Maintenance and Performance, HVAC, and Electrical Systems.
Further, revisions to all of these inspection were recently published.
Further, revisions to all of these inspection communication standards
are continually republished. In addition to these, standards for Drive
Train and Transmissions have recently been promulgated. Participating
shops utilize these Uniform Inspection & Communication Standards as
part of the inspection process and for communicating their findings to
their customers.
The Motorist Assurance Program continues to work
cooperatively and proactively with government agencies and consumer
groups toward solutions that both benefit the customer and are
mutually acceptable to both regulators and industry. We maintain the
belief that industry must retain control over how we conduct our
business, and we must be viewed as part of the solution and not part
of the problem. Meetings with state and other government officials
(and their representatives), concerned with auto repair and/or
consumer protection, are conducted. Feedback from these sessions is
brought back to the association, and the program adjusted as needed.
To assure auto repair customers recourse if they were not
satisfied with a repair transaction, the Motorist Assurance Program
offers mediation and arbitration through MAP/BBB-CARE and other non-
profit organizations. MAP conducted pilot programs in twelve states
before announcing the program nationally in October, 1998. During the
pilots, participating repair shops demonstrated their adherence to the
Pledge and Standards and agreed to follow the UICS in communicating
the results of their inspection to their customers. To put some
"teeth" in the program, an accreditation requirement for shops was
initiated. The requirements are stringent, and a self-policing method