brake sensor MITSUBISHI MONTERO 1998 Owner's Manual
[x] Cancel search | Manufacturer: MITSUBISHI, Model Year: 1998, Model line: MONTERO, Model: MITSUBISHI MONTERO 1998Pages: 1501, PDF Size: 25.81 MB
Page 172 of 1501
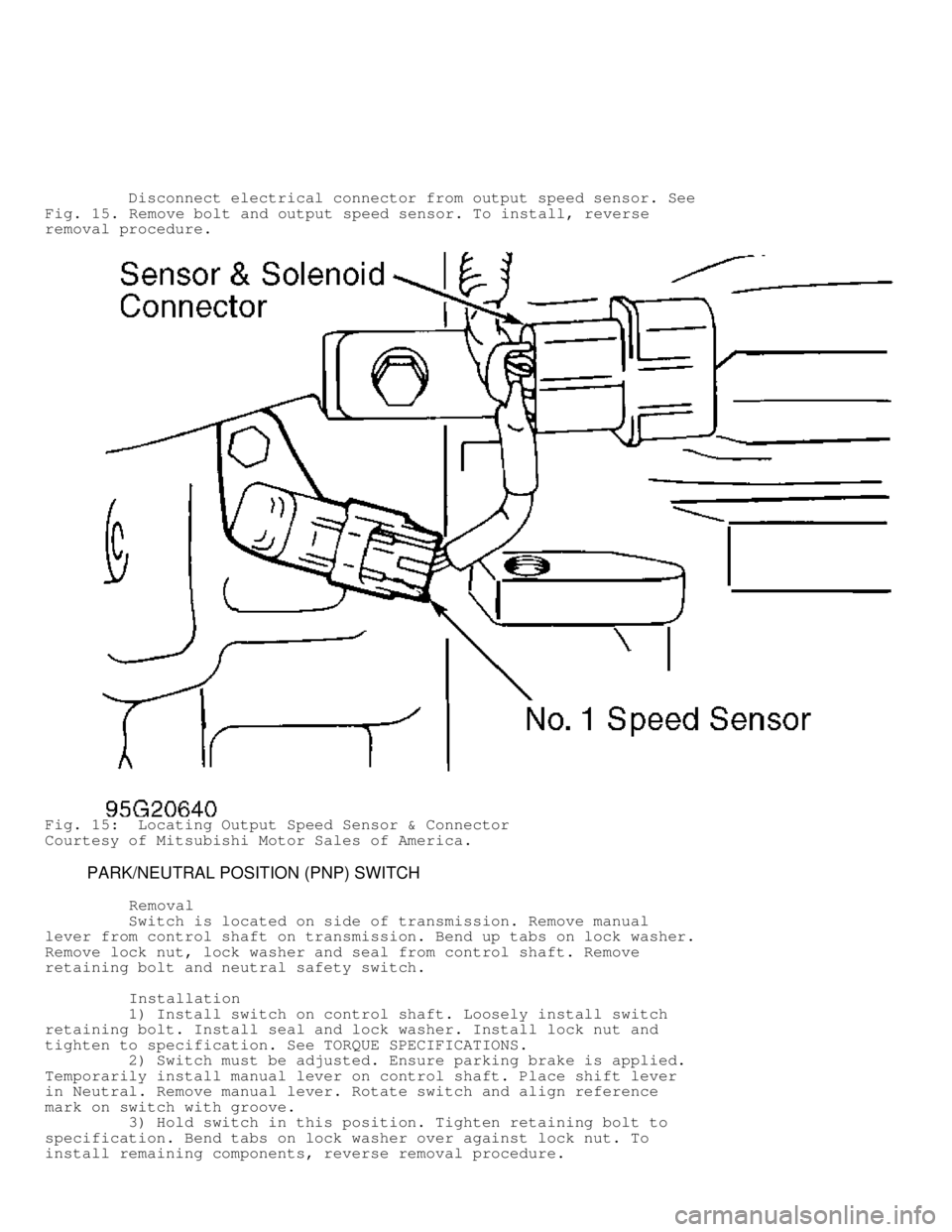
Disconnect electrical connector from output speed sensor. See
Fig. 15. Remove bolt and output speed sensor. To install, reverse
removal procedure.
Fig. 15: Locating Output Speed Sensor & Connector
Courtesy of Mitsubishi Motor Sales of America.
PARK/NEUTRAL POSITION (PNP) SWITCH
Removal
Switch is located on side of transmission. Remove manual
lever from control shaft on transmission. Bend up tabs on lock washer.
Remove lock nut, lock washer and seal from control shaft. Remove
retaining bolt and neutral safety switch.
Installation
1) Install switch on control shaft. Loosely install switch
retaining bolt. Install seal and lock washer. Install lock nut and
tighten to specification. See TORQUE SPECIFICATIONS.
2) Switch must be adjusted. Ensure parking brake is applied.
Temporarily install manual lever on control shaft. Place shift lever
in Neutral. Remove manual lever. Rotate switch and align reference
mark on switch with groove.
3) Hold switch in this position. Tighten retaining bolt to
specification. Bend tabs on lock washer over against lock nut. To
install remaining components, reverse removal procedure.
Page 184 of 1501
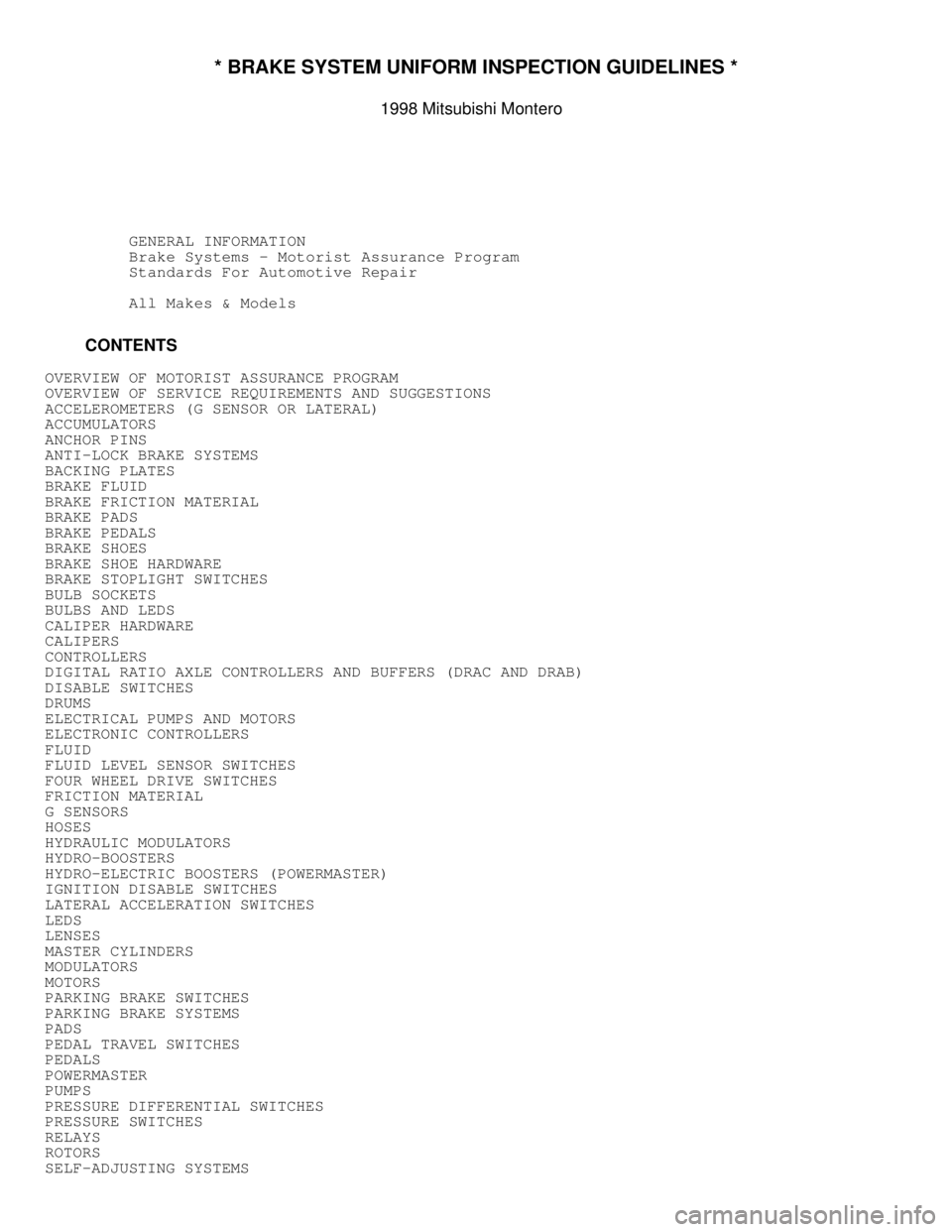
* BRAKE SYSTEM UNIFORM INSPECTION GUIDELINES *
1998 Mitsubishi Montero
GENERAL INFORMATION
Brake Systems - Motorist Assurance Program
Standards For Automotive Repair
All Makes & Models
CONTENTS
OVERVIEW OF MOTORIST ASSURANCE PROGRAM
OVERVIEW OF SERVICE REQUIREMENTS AND SUGGESTIONS
ACCELEROMETERS (G SENSOR OR LATERAL)
ACCUMULATORS
ANCHOR PINS
ANTI-LOCK BRAKE SYSTEMS
BACKING PLATES
BRAKE FLUID
BRAKE FRICTION MATERIAL
BRAKE PADS
BRAKE PEDALS
BRAKE SHOES
BRAKE SHOE HARDWARE
BRAKE STOPLIGHT SWITCHES
BULB SOCKETS
BULBS AND LEDS
CALIPER HARDWARE
CALIPERS
CONTROLLERS
DIGITAL RATIO AXLE CONTROLLERS AND BUFFERS (DRAC AND DRAB)
DISABLE SWITCHES
DRUMS
ELECTRICAL PUMPS AND MOTORS
ELECTRONIC CONTROLLERS
FLUID
FLUID LEVEL SENSOR SWITCHES
FOUR WHEEL DRIVE SWITCHES
FRICTION MATERIAL
G SENSORS
HOSES
HYDRAULIC MODULATORS
HYDRO-BOOSTERS
HYDRO-ELECTRIC BOOSTERS (POWERMASTER)
IGNITION DISABLE SWITCHES
LATERAL ACCELERATION SWITCHES
LEDS
LENSES
MASTER CYLINDERS
MODULATORS
MOTORS
PARKING BRAKE SWITCHES
PARKING BRAKE SYSTEMS
PADS
PEDAL TRAVEL SWITCHES
PEDALS
POWERMASTER
PUMPS
PRESSURE DIFFERENTIAL SWITCHES
PRESSURE SWITCHES
RELAYS
ROTORS
SELF-ADJUSTING SYSTEMS
Page 185 of 1501
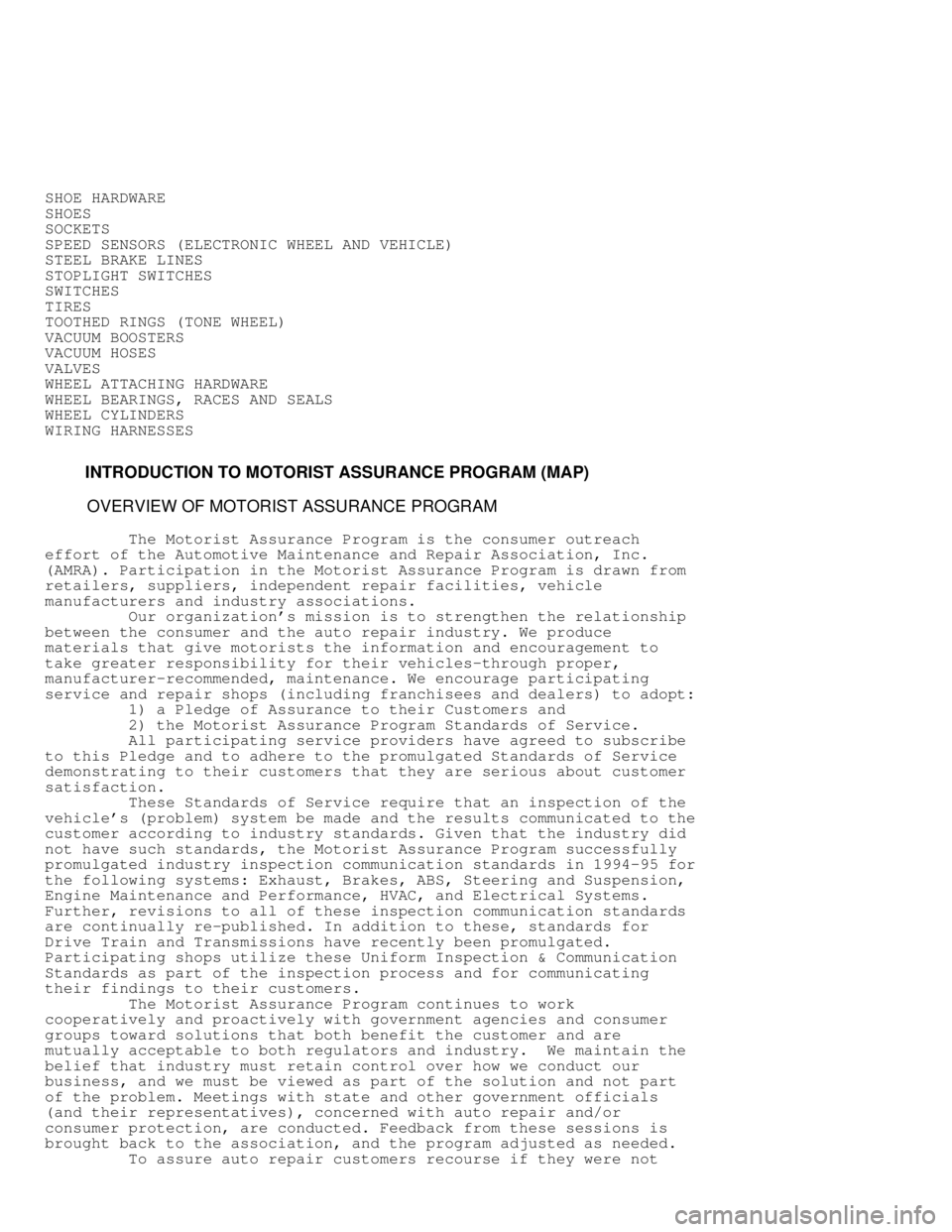
SHOE HARDWARE
SHOES
SOCKETS
SPEED SENSORS (ELECTRONIC WHEEL AND VEHICLE)
STEEL BRAKE LINES
STOPLIGHT SWITCHES
SWITCHES
TIRES
TOOTHED RINGS (TONE WHEEL)
VACUUM BOOSTERS
VACUUM HOSES
VALVES
WHEEL ATTACHING HARDWARE
WHEEL BEARINGS, RACES AND SEALS
WHEEL CYLINDERS
WIRING HARNESSES
INTRODUCTION TO MOTORIST ASSURANCE PROGRAM (MAP)
OVERVIEW OF MOTORIST ASSURANCE PROGRAM
The Motorist Assurance Program is the consumer outreach
effort of the Automotive Maintenance and Repair Association, Inc.
(AMRA). Participation in the Motorist Assurance Program is drawn from
retailers, suppliers, independent repair facilities, vehicle
manufacturers and industry associations.
Our organization's mission is to strengthen the relationship
between the consumer and the auto repair industry. We produce
materials that give motorists the information and encouragement to
take greater responsibility for their vehicles-through proper,
manufacturer-recommended, maintenance. We encourage participating
service and repair shops (including franchisees and dealers) to adopt:\
1) a Pledge of Assurance to their Customers and
2) the Motorist Assurance Program Standards of Service.
All participating service providers have agreed to subscribe
to this Pledge and to adhere to the promulgated Standards of Service
demonstrating to their customers that they are serious about customer
satisfaction.
These Standards of Service require that an inspection of the
vehicle's (problem) system be made and the results communicated to the\
customer according to industry standards. Given that the industry did
not have such standards, the Motorist Assurance Program successfully
promulgated industry inspection communication standards in 1994-95 for
the following systems: Exhaust, Brakes, ABS, Steering and Suspension,
Engine Maintenance and Performance, HVAC, and Electrical Systems.
Further, revisions to all of these inspection communication standards
are continually re-published. In addition to these, standards for
Drive Train and Transmissions have recently been promulgated.
Participating shops utilize these Uniform Inspection & Communication
Standards as part of the inspection process and for communicating
their findings to their customers.
The Motorist Assurance Program continues to work
cooperatively and proactively with government agencies and consumer
groups toward solutions that both benefit the customer and are
mutually acceptable to both regulators and industry. We maintain the
belief that industry must retain control over how we conduct our
business, and we must be viewed as part of the solution and not part
of the problem. Meetings with state and other government officials
(and their representatives), concerned with auto repair and/or
consumer protection, are conducted. Feedback from these sessions is
brought back to the association, and the program adjusted as needed.
To assure auto repair customers recourse if they were not
Page 188 of 1501
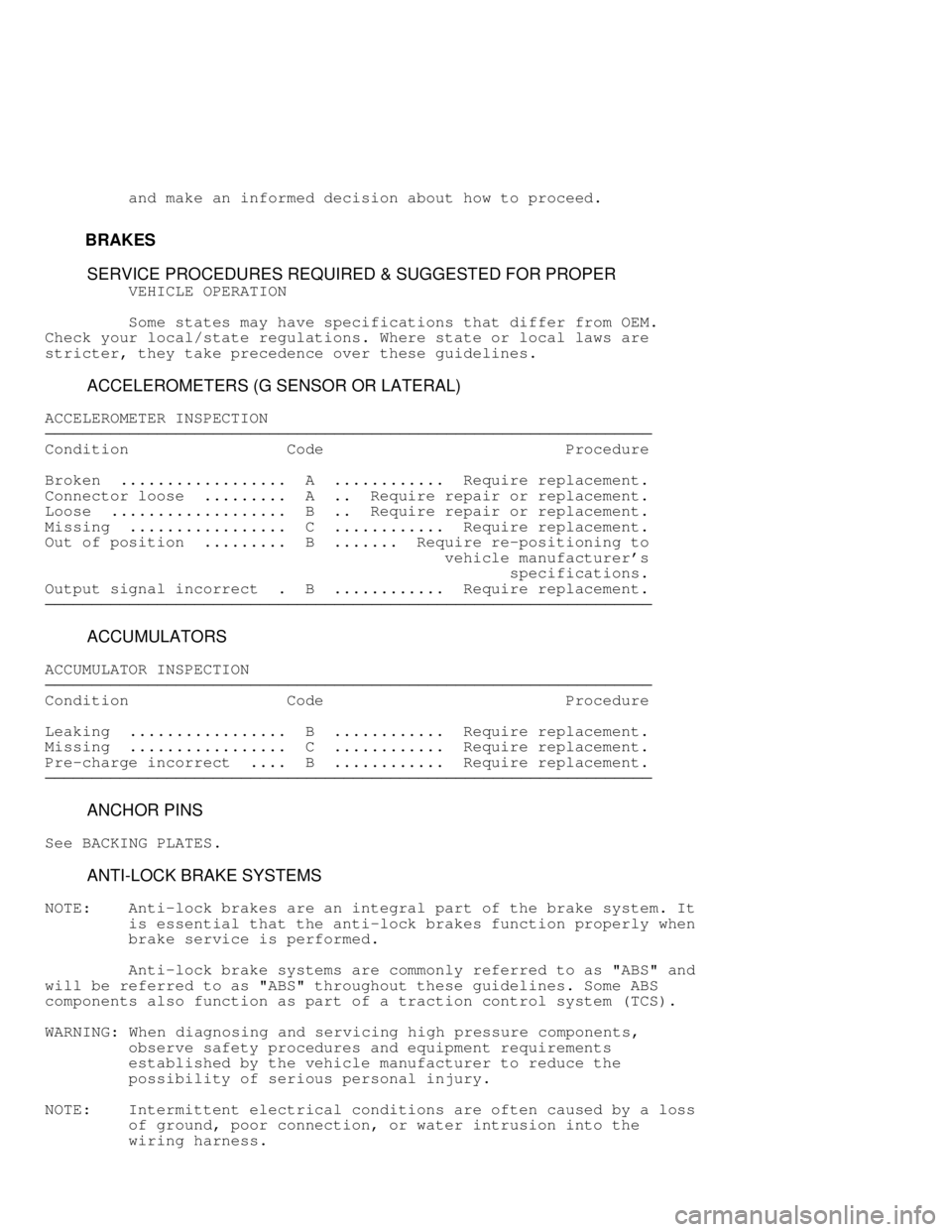
and make an informed decision about how to proceed.
BRAKES
SERVICE PROCEDURES REQUIRED & SUGGESTED FOR PROPER
VEHICLE OPERATION
Some states may have specifications that differ from OEM.
Check your local/state regulations. Where state or local laws are
stricter, they take precedence over these guidelines.
ACCELEROMETERS (G SENSOR OR LATERAL)
ACCELEROMETER INSPECTION \
\
\
\
\
\
\
Condition Code Procedure
Broken .................. A ............ Require replacement.
Connector loose ......... A .. Require repair or replacement.
Loose ................... B .. Require repair or replacement.
Missing ................. C ............ Require replacement.
Out of position ......... B ....... Require re-positioning to
vehicle manufacturer's
specifications.
Output signal incorrect . B ............ Require replacement.
\
\
\
\
\
\
\
ACCUMULATORS
ACCUMULATOR INSPECTION \
\
\
\
\
\
\
Condition Code Procedure
Leaking ................. B ............ Require replacement.
Missing ................. C ............ Require replacement.
Pre-charge incorrect .... B ............ Require replacement.
\
\
\
\
\
\
\
ANCHOR PINS
See BACKING PLATES .
ANTI-LOCK BRAKE SYSTEMS
NOTE: Anti-lock brakes are an integral part of the brake system. It
is essential that the anti-lock brakes function properly when
brake service is performed.
Anti-lock brake systems are commonly referred to as "ABS" and
will be referred to as "ABS" throughout these guidelines. Some ABS
components also function as part of a traction control system (TCS).
WARNING: When diagnosing and servicing high pressure components,
observe safety procedures and equipment requirements
established by the vehicle manufacturer to reduce the
possibility of serious personal injury.
NOTE: Intermittent electrical conditions are often caused by a loss
of ground, poor connection, or water intrusion into the
wiring harness.
Page 198 of 1501
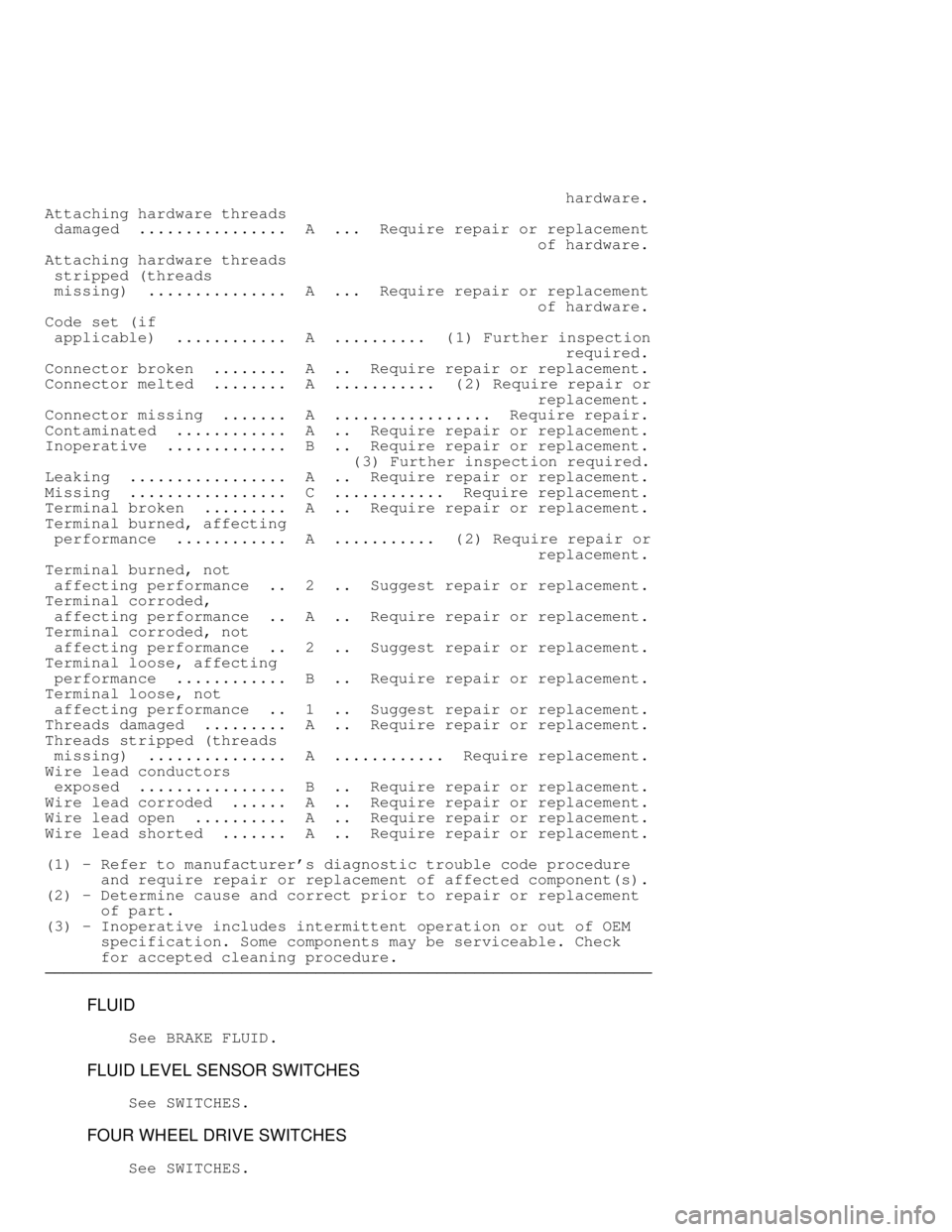
hardware.
Attaching hardware threads
damaged ................ A ... Require repair or replacement
of hardware.
Attaching hardware threads
stripped (threads
missing) ............... A ... Require repair or replacement
of hardware.
Code set (if
applicable) ............ A .......... (1) Further inspection
required.
Connector broken ........ A .. Require repair or replacement.
Connector melted ........ A ........... ( 2) Require repair or
replacement.
Connector missing ....... A ................. Require repair.
Contaminated ............ A .. Require repair or replacement.
Inoperative ............. B .. Require repair or replacement.
( 3) Further inspection required.
Leaking ................. A .. Require repair or replacement.
Missing ................. C ............ Require replacement.
Terminal broken ......... A .. Require repair or replacement.
Terminal burned, affecting
performance ............ A ........... ( 2) Require repair or
replacement.
Terminal burned, not
affecting performance .. 2 .. Suggest repair or replacement.
Terminal corroded,
affecting performance .. A .. Require repair or replacement.
Terminal corroded, not
affecting performance .. 2 .. Suggest repair or replacement.
Terminal loose, affecting
performance ............ B .. Require repair or replacement.
Terminal loose, not
affecting performance .. 1 .. Suggest repair or replacement.
Threads damaged ......... A .. Require repair or replacement.
Threads stripped (threads
missing) ............... A ............ Require replacement.
Wire lead conductors
exposed ................ B .. Require repair or replacement.
Wire lead corroded ...... A .. Require repair or replacement.
Wire lead open .......... A .. Require repair or replacement.
Wire lead shorted ....... A .. Require repair or replacement.
( 1) - Refer to manufacturer's diagnostic trouble code procedure
and require repair or replacement of affected component(s).
( 2) - Determine cause and correct prior to repair or replacement
of part.
( 3) - Inoperative includes intermittent operation or out of OEM
specification. Some components may be serviceable. Check
for accepted cleaning procedure.
\
\
\
\
\
\
\
FLUID
See BRAKE FLUID.
FLUID LEVEL SENSOR SWITCHES
See SWITCHES.
FOUR WHEEL DRIVE SWITCHES
See SWITCHES.
Page 207 of 1501
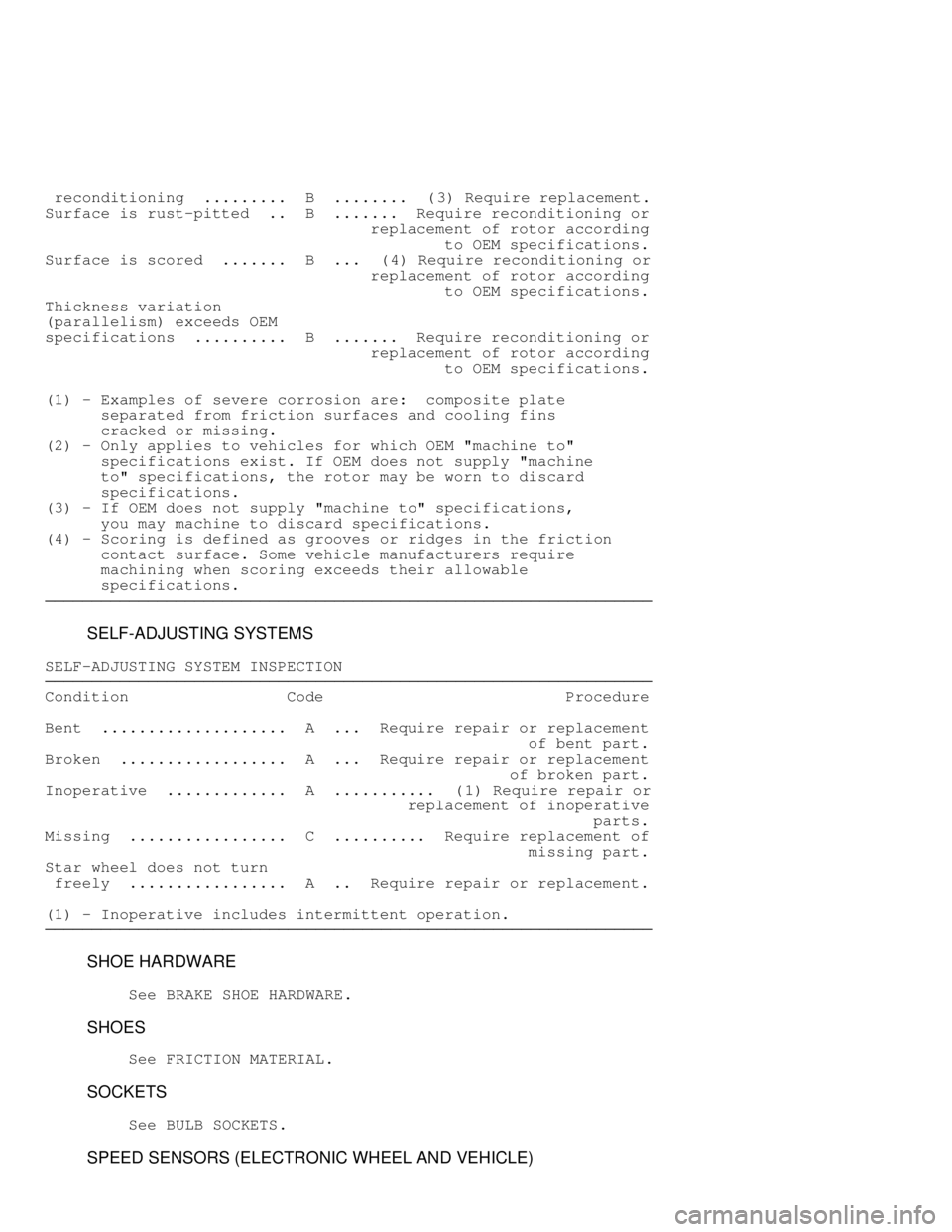
reconditioning ......... B ........ (3) Require replacement.
Surface is rust-pitted .. B ....... Require reconditioning or
replacement of rotor according
to OEM specifications.
Surface is scored ....... B ... ( 4) Require reconditioning or
replacement of rotor according
to OEM specifications.
Thickness variation
(parallelism) exceeds OEM
specifications .......... B ....... Require reconditioning or
replacement of rotor according
to OEM specifications.
( 1) - Examples of severe corrosion are: composite plate
separated from friction surfaces and cooling fins
cracked or missing.
( 2) - Only applies to vehicles for which OEM "machine to"
specifications exist. If OEM does not supply "machine
to" specifications, the rotor may be worn to discard
specifications.
( 3) - If OEM does not supply "machine to" specifications,
you may machine to discard specifications.
( 4) - Scoring is defined as grooves or ridges in the friction
contact surface. Some vehicle manufacturers require
machining when scoring exceeds their allowable
specifications.
\
\
\
\
\
\
\
SELF-ADJUSTING SYSTEMS
SELF-ADJUSTING SYSTEM INSPECTION \
\
\
\
\
\
\
Condition Code Procedure
Bent .................... A ... Require repair or replacement
of bent part.
Broken .................. A ... Require repair or replacement
of broken part.
Inoperative ............. A ........... ( 1) Require repair or
replacement of inoperative
parts.
Missing ................. C .......... Require replacement of
missing part.
Star wheel does not turn
freely ................. A .. Require repair or replacement.
( 1) - Inoperative includes intermittent operation.
\
\
\
\
\
\
\
SHOE HARDWARE
See BRAKE SHOE HARDWARE .
SHOES
See FRICTION MATERIAL .
SOCKETS
See BULB SOCKETS.
SPEED SENSORS (ELECTRONIC WHEEL AND VEHICLE)
Page 209 of 1501
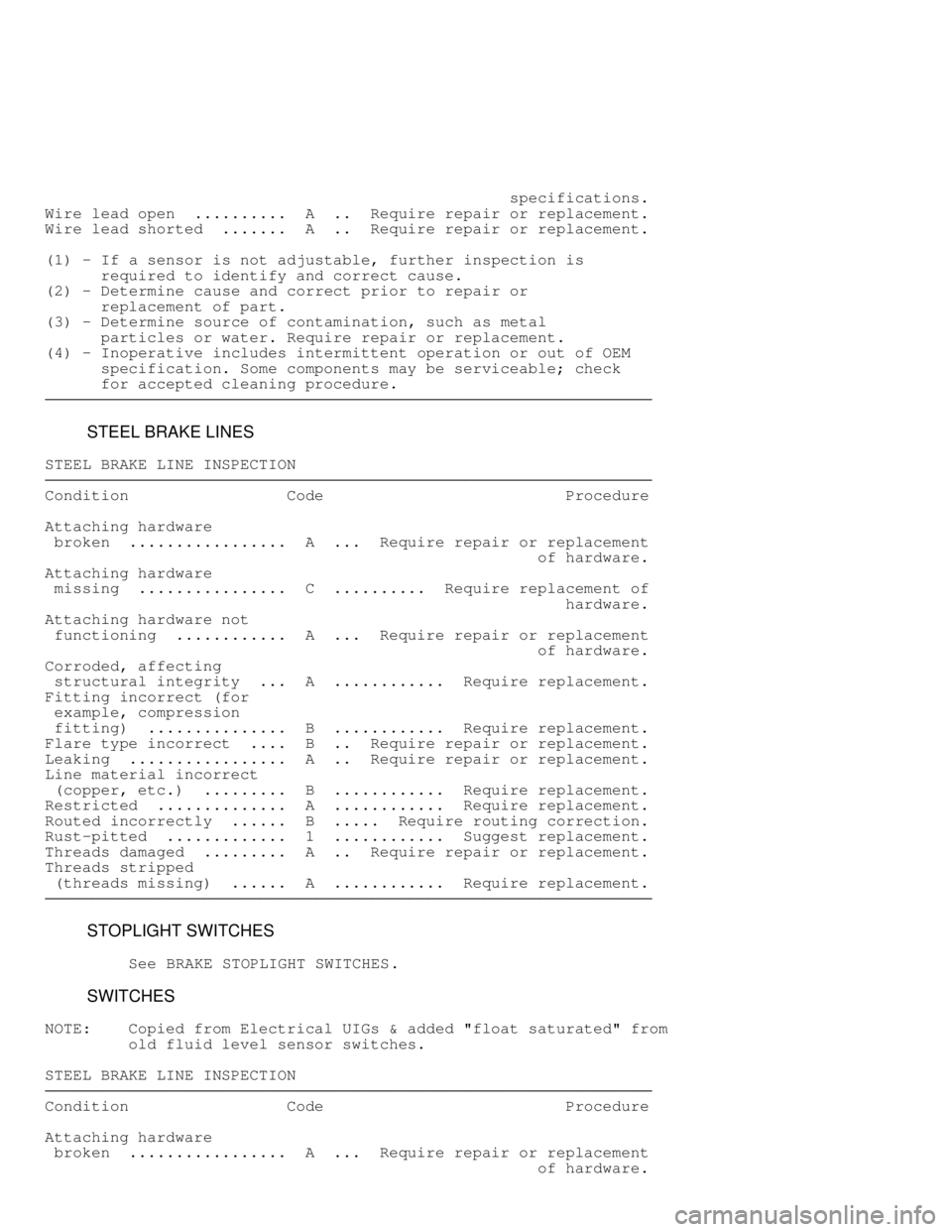
specifications.
Wire lead open .......... A .. Require repair or replacement.
Wire lead shorted ....... A .. Require repair or replacement.
(1) - If a sensor is not adjustable, further inspection is
required to identify and correct cause.
( 2) - Determine cause and correct prior to repair or
replacement of part.
( 3) - Determine source of contamination, such as metal
particles or water. Require repair or replacement.
( 4) - Inoperative includes intermittent operation or out of OEM
specification. Some components may be serviceable; check
for accepted cleaning procedure.
\
\
\
\
\
\
\
STEEL BRAKE LINES
STEEL BRAKE LINE INSPECTION \
\
\
\
\
\
\
Condition Code Procedure
Attaching hardware
broken ................. A ... Require repair or replacement
of hardware.
Attaching hardware
missing ................ C .......... Require replacement of
hardware.
Attaching hardware not
functioning ............ A ... Require repair or replacement
of hardware.
Corroded, affecting
structural integrity ... A ............ Require replacement.
Fitting incorrect (for
example, compression
fitting) ............... B ............ Require replacement.
Flare type incorrect .... B .. Require repair or replacement.
Leaking ................. A .. Require repair or replacement.
Line material incorrect
(copper, etc.) ......... B ............ Require replacement.
Restricted .............. A ............ Require replacement.
Routed incorrectly ...... B ..... Require routing correction.
Rust-pitted ............. 1 ............ Suggest replacement.
Threads damaged ......... A .. Require repair or replacement.
Threads stripped
(threads missing) ...... A ............ Require replacement.
\
\
\
\
\
\
\
STOPLIGHT SWITCHES
See BRAKE STOPLIGHT SWITCHES .
SWITCHES
NOTE: Copied from Electrical UIGs & added "float saturated" from
old fluid level sensor switches.
STEEL BRAKE LINE INSPECTION
\
\
\
\
\
\
\
Condition Code Procedure
Attaching hardware
broken ................. A ... Require repair or replacement
of hardware.
Page 228 of 1501
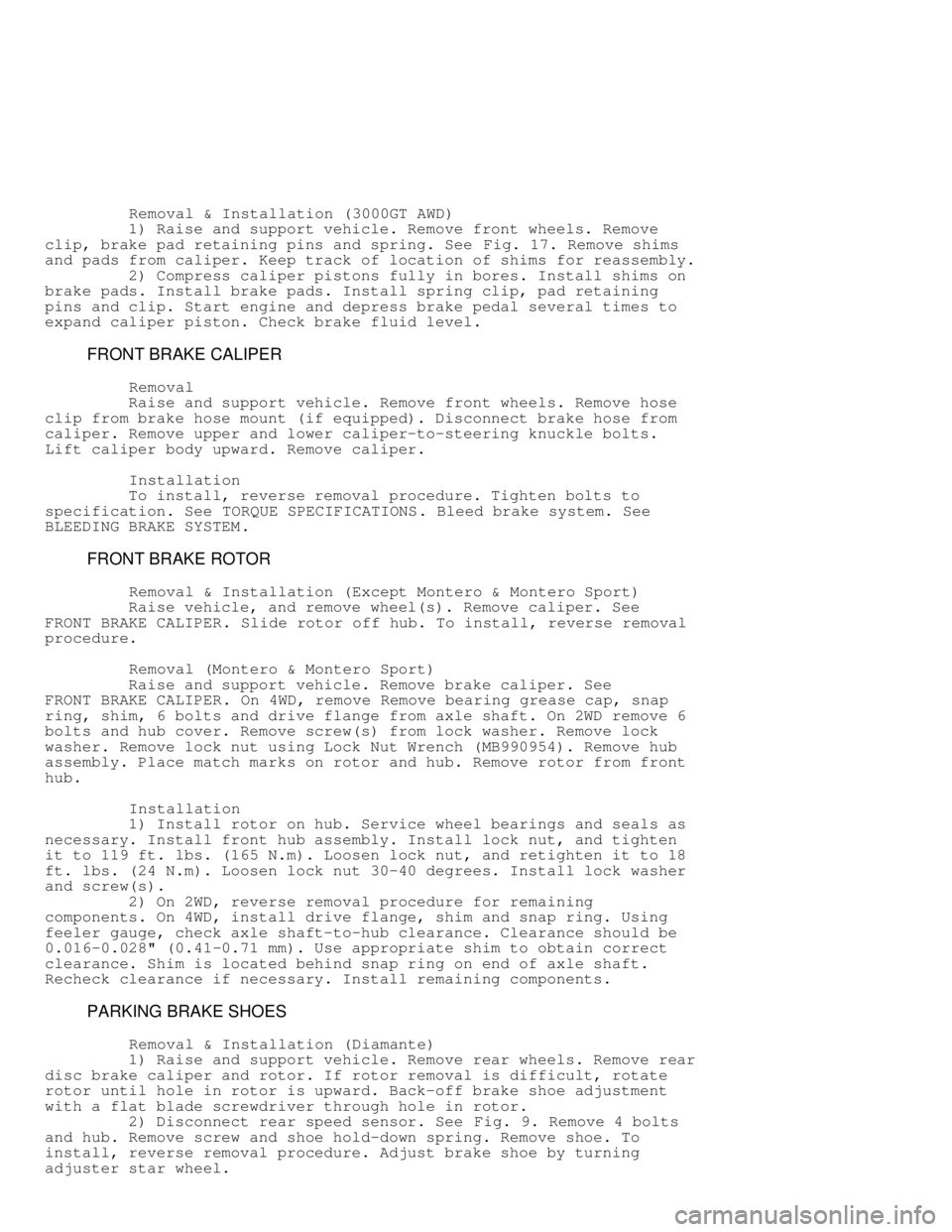
Removal & Installation (3000GT AWD)
1) Raise and support vehicle. Remove front wheels. Remove
clip, brake pad retaining pins and spring. See Fig. 17. Remove shims
and pads from caliper. Keep track of location of shims for reassembly.
2) Compress caliper pistons fully in bores. Install shims on
brake pads. Install brake pads. Install spring clip, pad retaining
pins and clip. Start engine and depress brake pedal several times to
expand caliper piston. Check brake fluid level.
FRONT BRAKE CALIPER
Removal
Raise and support vehicle. Remove front wheels. Remove hose
clip from brake hose mount (if equipped). Disconnect brake hose from
caliper. Remove upper and lower caliper-to-steering knuckle bolts.
Lift caliper body upward. Remove caliper.
Installation
To install, reverse removal procedure. Tighten bolts to
specification. See TORQUE SPECIFICATIONS . Bleed brake system. See
BLEEDING BRAKE SYSTEM .
FRONT BRAKE ROTOR
Removal & Installation (Except Montero & Montero Sport)
Raise vehicle, and remove wheel(s). Remove caliper. See
FRONT BRAKE CALIPER . Slide rotor off hub. To install, reverse removal
procedure.
Removal (Montero & Montero Sport)
Raise and support vehicle. Remove brake caliper. See
FRONT BRAKE CALIPER . On 4WD, remove Remove bearing grease cap, snap
ring, shim, 6 bolts and drive flange from axle shaft. On 2WD remove 6
bolts and hub cover. Remove screw(s) from lock washer. Remove lock
washer. Remove lock nut using Lock Nut Wrench (MB990954). Remove hub
assembly. Place match marks on rotor and hub. Remove rotor from front
hub.
Installation
1) Install rotor on hub. Service wheel bearings and seals as
necessary. Install front hub assembly. Install lock nut, and tighten
it to 119 ft. lbs. (165 N.m). Loosen lock nut, and retighten it to 18
ft. lbs. (24 N.m). Loosen lock nut 30-40 degrees. Install lock washer
and screw(s).
2) On 2WD, reverse removal procedure for remaining
components. On 4WD, install drive flange, shim and snap ring. Using
feeler gauge, check axle shaft-to-hub clearance. Clearance should be
0.016-0.028" (0.41-0.71 mm). Use appropriate shim to obtain correct
clearance. Shim is located behind snap ring on end of axle shaft.
Recheck clearance if necessary. Install remaining components.
PARKING BRAKE SHOES
Removal & Installation (Diamante)
1) Raise and support vehicle. Remove rear wheels. Remove rear
disc brake caliper and rotor. If rotor removal is difficult, rotate
rotor until hole in rotor is upward. Back-off brake shoe adjustment
with a flat blade screwdriver through hole in rotor.
2) Disconnect rear speed sensor. See Fig. 9. Remove 4 bolts
and hub. Remove screw and shoe hold-down spring. Remove shoe. To
install, reverse removal procedure. Adjust brake shoe by turning
adjuster star wheel.
Page 229 of 1501
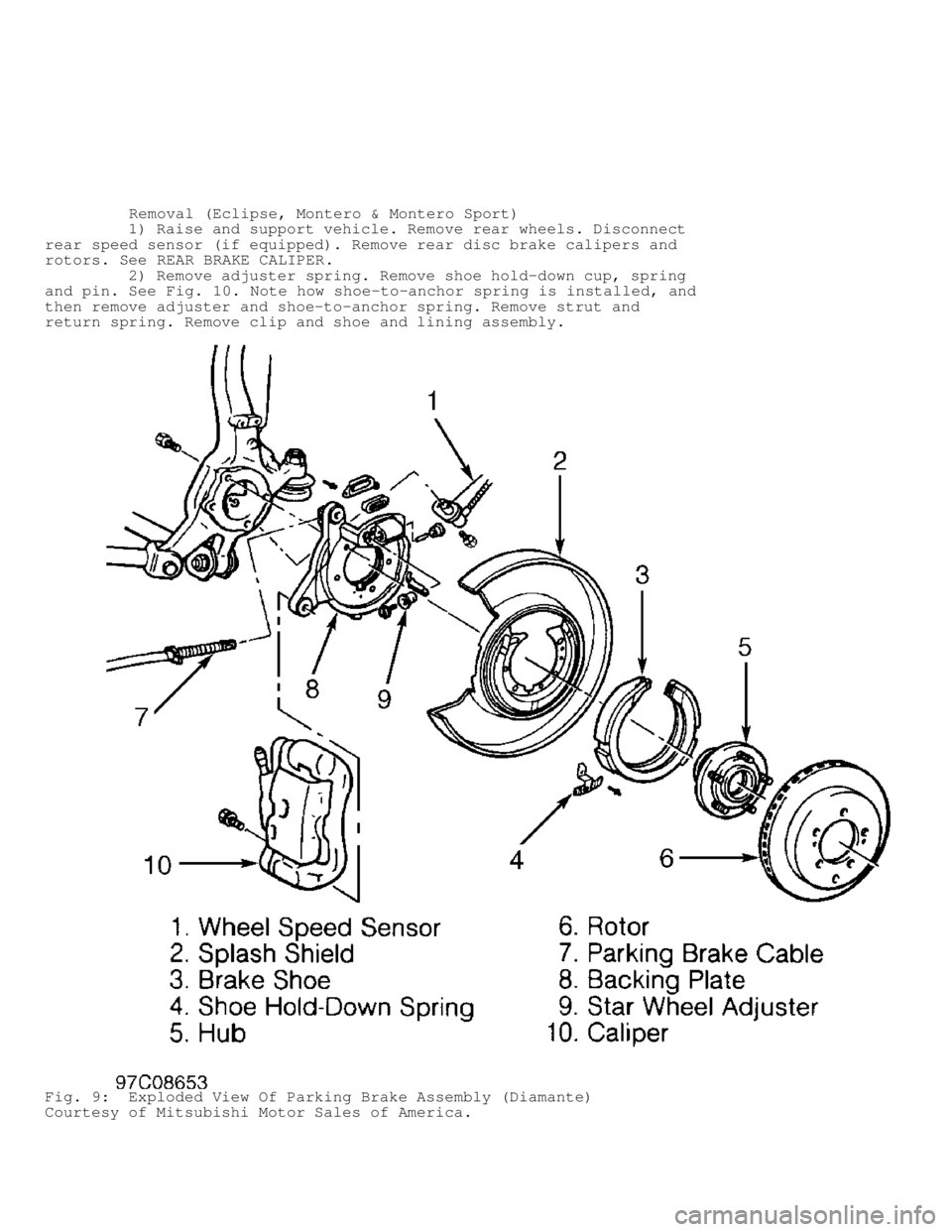
Removal (Eclipse, Montero & Montero Sport)
1) Raise and support vehicle. Remove rear wheels. Disconnect
rear speed sensor (if equipped). Remove rear disc brake calipers and
rotors. See REAR BRAKE CALIPER .
2) Remove adjuster spring. Remove shoe hold-down cup, spring
and pin. See Fig. 10. Note how shoe-to-anchor spring is installed, and
then remove adjuster and shoe-to-anchor spring. Remove strut and
return spring. Remove clip and shoe and lining assembly.
Fig. 9: Exploded View Of Parking Brake Assembly (Diamante)
Courtesy of Mitsubishi Motor Sales of America.
Page 230 of 1501
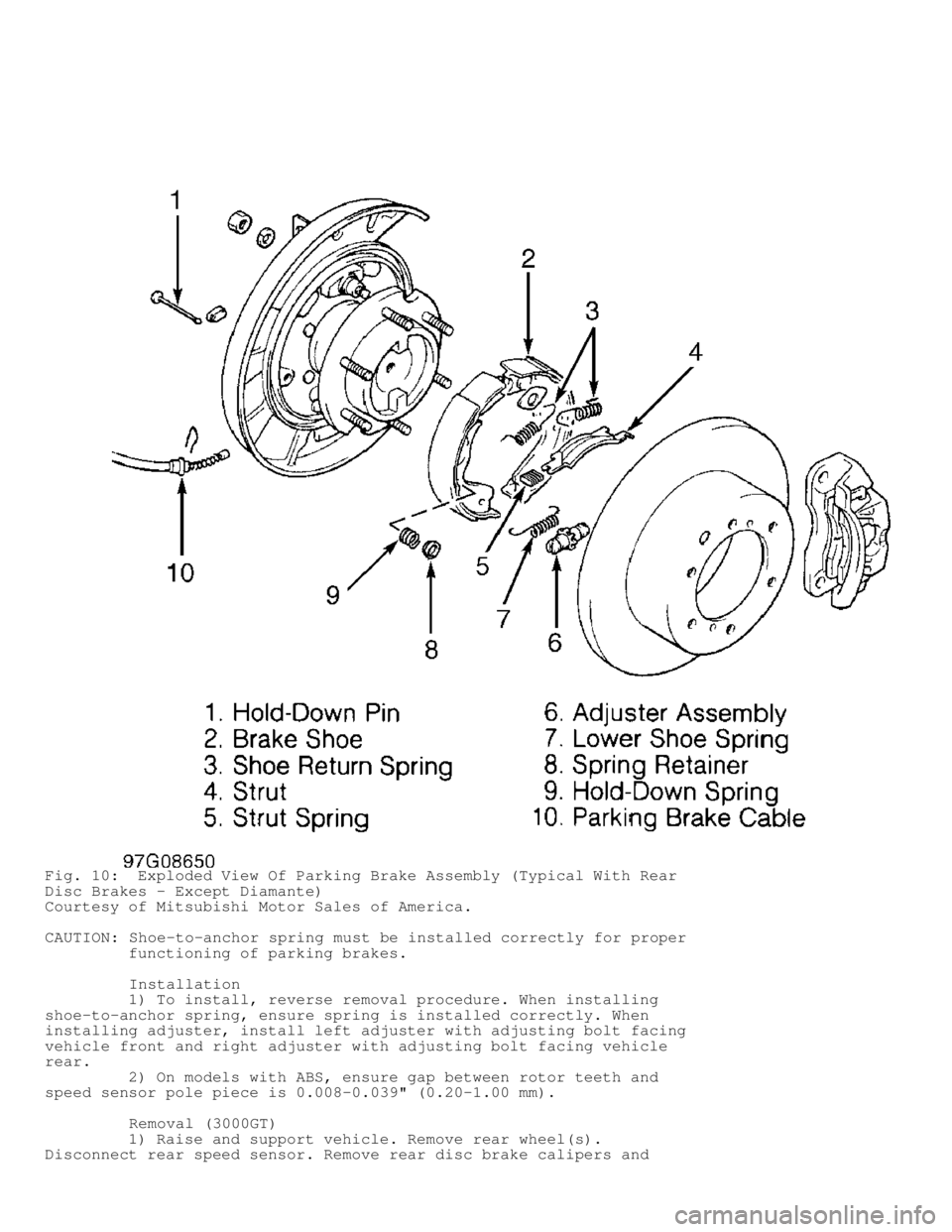
Fig. 10: Exploded View Of Parking Brake Assembly (Typical With Rear
Disc Brakes - Except Diamante)
Courtesy of Mitsubishi Motor Sales of America.
CAUTION: Shoe-to-anchor spring must be installed correctly for proper
functioning of parking brakes.
Installation
1) To install, reverse removal procedure. When installing
shoe-to-anchor spring, ensure spring is installed correctly. When
installing adjuster, install left adjuster with adjusting bolt facing
vehicle front and right adjuster with adjusting bolt facing vehicle
rear.
2) On models with ABS, ensure gap between rotor teeth and
speed sensor pole piece is 0.008-0.039" (0.20-1.00 mm).
Removal (3000GT)
1) Raise and support vehicle. Remove rear wheel(s).
Disconnect rear speed sensor. Remove rear disc brake calipers and