timing MITSUBISHI MONTERO 1998 Owner's Guide
[x] Cancel search | Manufacturer: MITSUBISHI, Model Year: 1998, Model line: MONTERO, Model: MITSUBISHI MONTERO 1998Pages: 1501, PDF Size: 25.81 MB
Page 577 of 1501
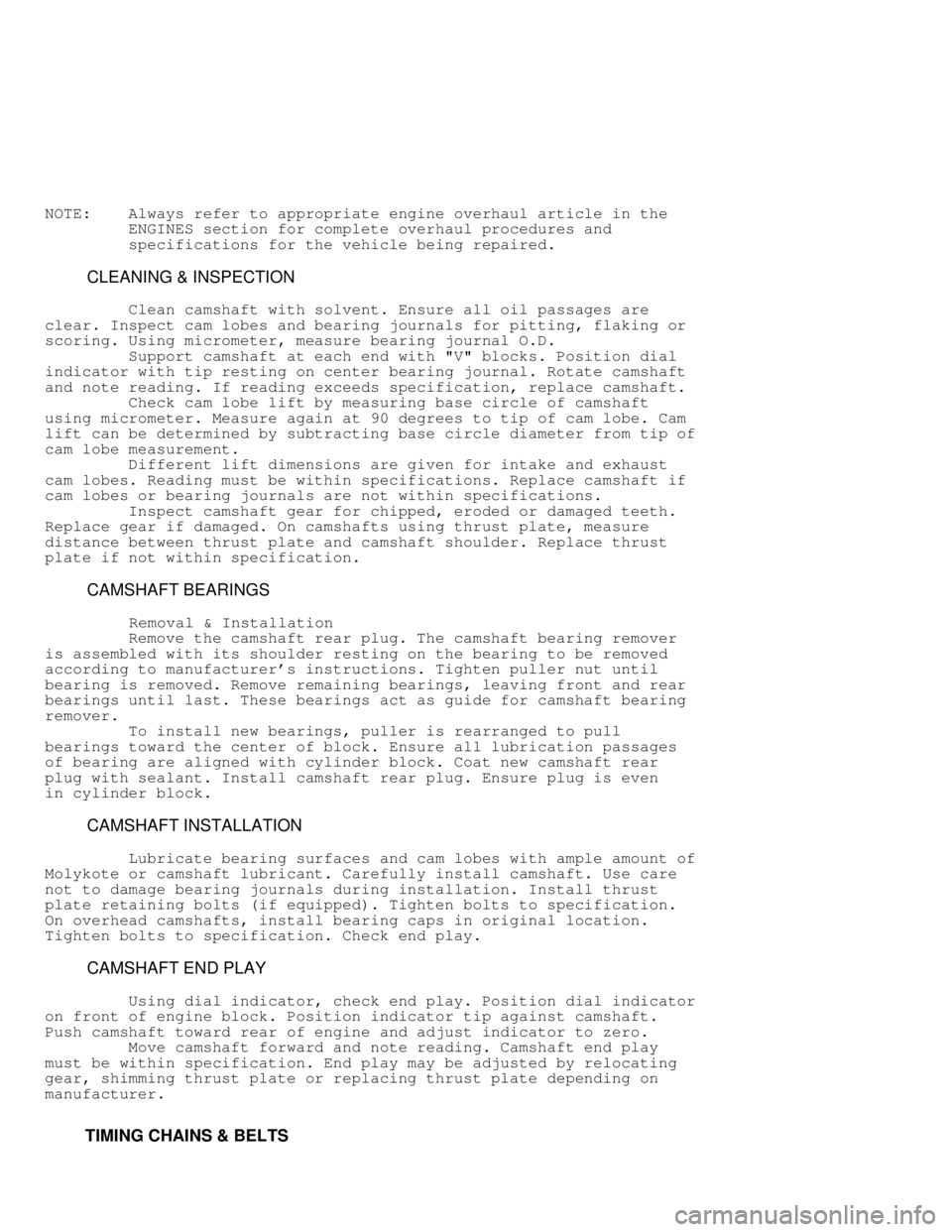
NOTE: Always refer to appropriate engine overhaul article in the
ENGINES section for complete overhaul procedures and
specifications for the vehicle being repaired.
CLEANING & INSPECTION
Clean camshaft with solvent. Ensure all oil passages are
clear. Inspect cam lobes and bearing journals for pitting, flaking or
scoring. Using micrometer, measure bearing journal O.D.
Support camshaft at each end with "V" blocks. Position dial
indicator with tip resting on center bearing journal. Rotate camshaft
and note reading. If reading exceeds specification, replace camshaft.
Check cam lobe lift by measuring base circle of camshaft
using micrometer. Measure again at 90 degrees to tip of cam lobe. Cam
lift can be determined by subtracting base circle diameter from tip of
cam lobe measurement.
Different lift dimensions are given for intake and exhaust
cam lobes. Reading must be within specifications. Replace camshaft if
cam lobes or bearing journals are not within specifications.
Inspect camshaft gear for chipped, eroded or damaged teeth.
Replace gear if damaged. On camshafts using thrust plate, measure
distance between thrust plate and camshaft shoulder. Replace thrust
plate if not within specification.
CAMSHAFT BEARINGS
Removal & Installation
Remove the camshaft rear plug. The camshaft bearing remover
is assembled with its shoulder resting on the bearing to be removed
according to manufacturer's instructions. Tighten puller nut until
bearing is removed. Remove remaining bearings, leaving front and rear
bearings until last. These bearings act as guide for camshaft bearing
remover.
To install new bearings, puller is rearranged to pull
bearings toward the center of block. Ensure all lubrication passages
of bearing are aligned with cylinder block. Coat new camshaft rear
plug with sealant. Install camshaft rear plug. Ensure plug is even
in cylinder block.
CAMSHAFT INSTALLATION
Lubricate bearing surfaces and cam lobes with ample amount of
Molykote or camshaft lubricant. Carefully install camshaft. Use care
not to damage bearing journals during installation. Install thrust
plate retaining bolts (if equipped). Tighten bolts to specification.
On overhead camshafts, install bearing caps in original location.
Tighten bolts to specification. Check end play.
CAMSHAFT END PLAY
Using dial indicator, check end play. Position dial indicator
on front of engine block. Position indicator tip against camshaft.
Push camshaft toward rear of engine and adjust indicator to zero.
Move camshaft forward and note reading. Camshaft end play
must be within specification. End play may be adjusted by relocating
gear, shimming thrust plate or replacing thrust plate depending on
manufacturer.
TIMING CHAINS & BELTS
Page 578 of 1501

* PLEASE READ THIS FIRST *
NOTE: Always refer to appropriate engine overhaul article in the
ENGINES section for complete overhaul procedures and
specifications for the vehicle being repaired.
TIMING CHAINS
Timing chains will stretch during operation. Limits are
placed upon amount of stretch before replacement is required. Timing
chain stretch will alter ignition timing and valve timing.
To check timing chain stretch, rotate crankshaft to eliminate
slack from one side of timing chain. Mark reference point on cylinder
block. Rotate crankshaft in opposite direction to eliminate slack from
remaining side of timing chain. Force other side of chain outward
and measure distance between reference point and timing chain. See
Fig. 23 . Replace timing chain and gears if not within specification.
Fig. 23: Measuring Timing Chain Stretch - Typical
This Graphic For General Information Only
Timing chains must be installed so that timing marks on
camshaft gear and crankshaft gear are aligned according to
Page 579 of 1501
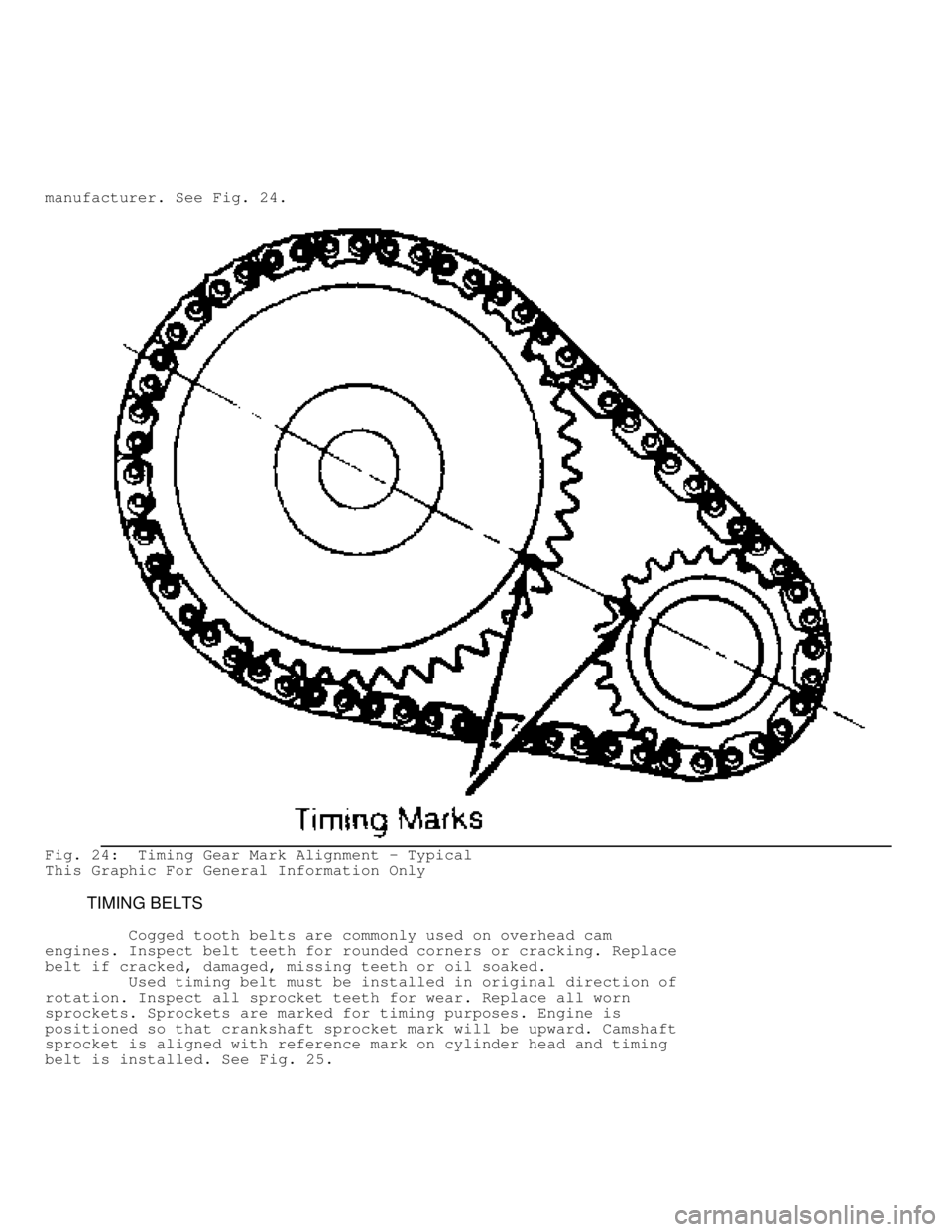
manufacturer. See Fig. 24.
Fig. 24: Timing Gear Mark Alignment - Typical
This Graphic For General Information Only
TIMING BELTS
Cogged tooth belts are commonly used on overhead cam
engines. Inspect belt teeth for rounded corners or cracking. Replace
belt if cracked, damaged, missing teeth or oil soaked.
Used timing belt must be installed in original direction of
rotation. Inspect all sprocket teeth for wear. Replace all worn
sprockets. Sprockets are marked for timing purposes. Engine is
positioned so that crankshaft sprocket mark will be upward. Camshaft
sprocket is aligned with reference mark on cylinder head and timing
belt is installed. See Fig. 25.
Page 580 of 1501
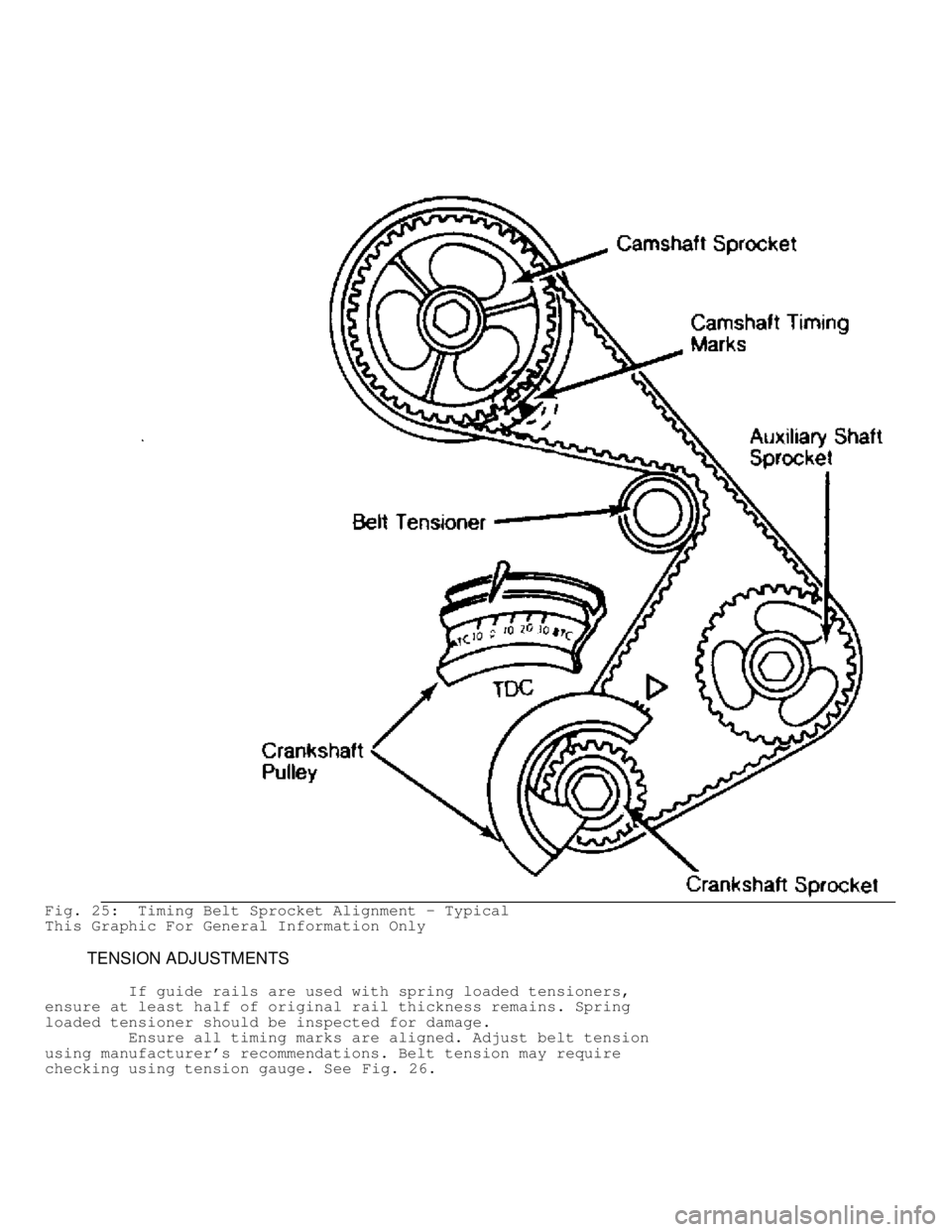
Fig. 25: Timing Belt Sprocket Alignment - Typical
This Graphic For General Information Only
TENSION ADJUSTMENTS
If guide rails are used with spring loaded tensioners,
ensure at least half of original rail thickness remains. Spring
loaded tensioner should be inspected for damage.
Ensure all timing marks are aligned. Adjust belt tension
using manufacturer's recommendations. Belt tension may require
checking using tension gauge. See Fig. 26.
Page 581 of 1501
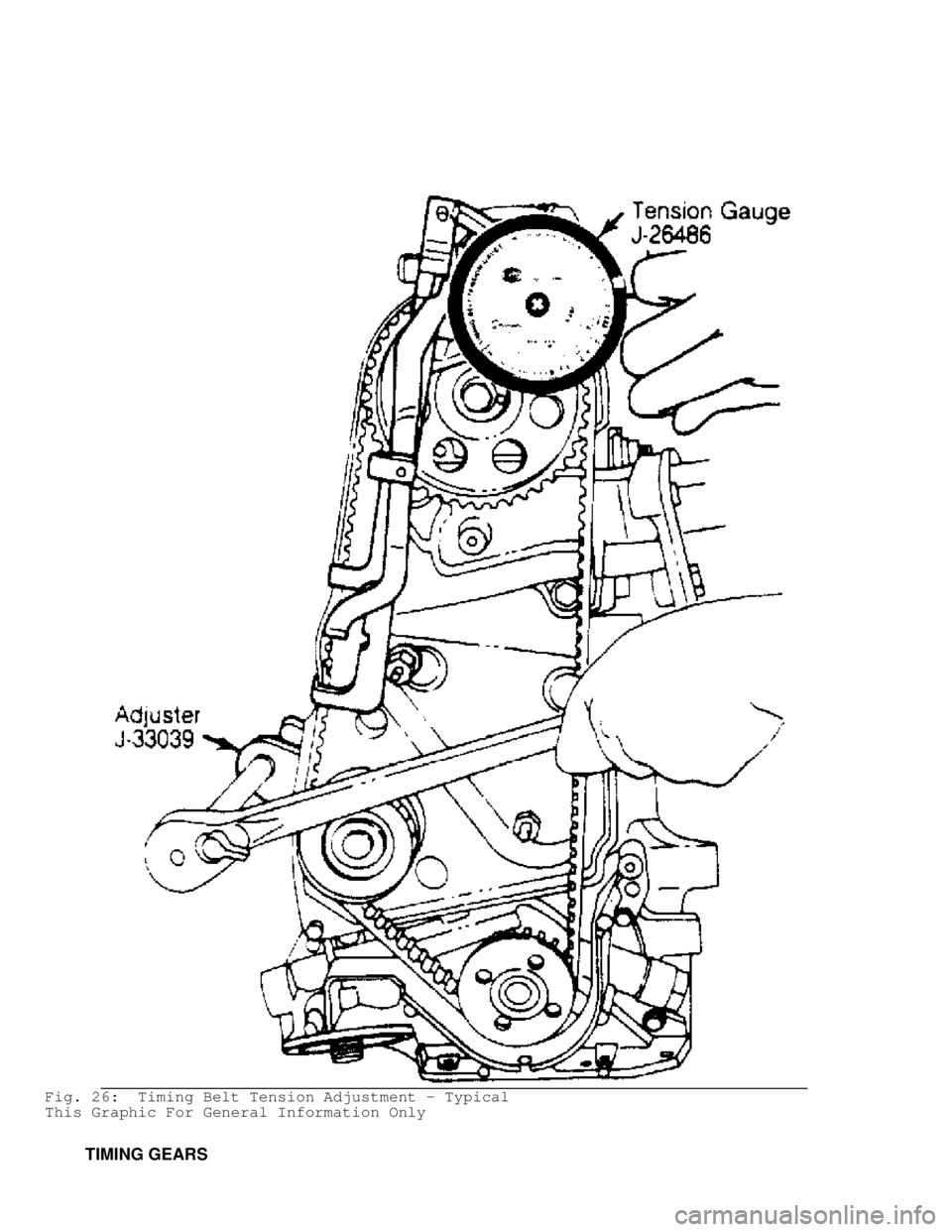
Fig. 26: Timing Belt Tension Adjustment - Typical
This Graphic For General Information Only
TIMING GEARS
Page 582 of 1501
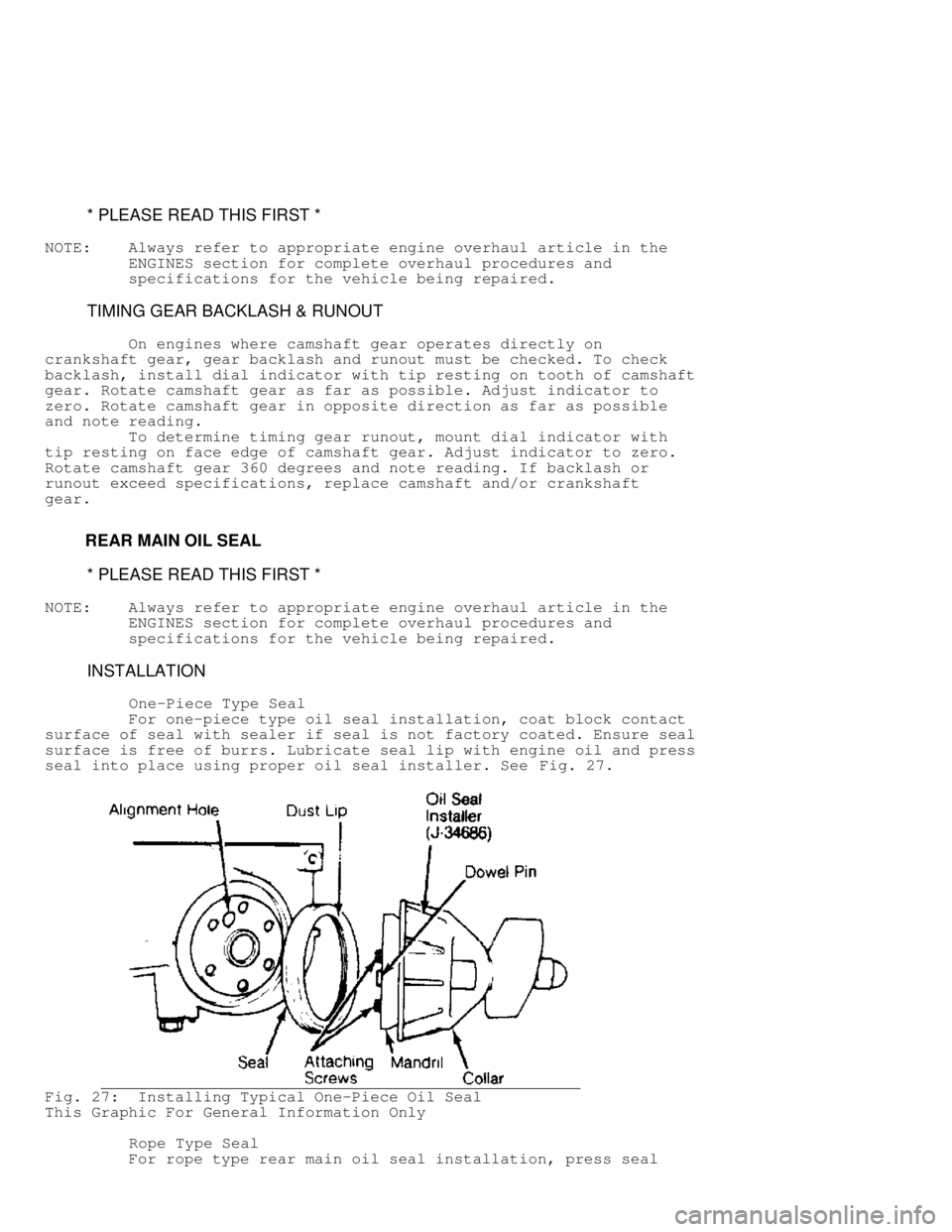
* PLEASE READ THIS FIRST *
NOTE: Always refer to appropriate engine overhaul article in the
ENGINES section for complete overhaul procedures and
specifications for the vehicle being repaired.
TIMING GEAR BACKLASH & RUNOUT
On engines where camshaft gear operates directly on
crankshaft gear, gear backlash and runout must be checked. To check
backlash, install dial indicator with tip resting on tooth of camshaft
gear. Rotate camshaft gear as far as possible. Adjust indicator to
zero. Rotate camshaft gear in opposite direction as far as possible
and note reading.
To determine timing gear runout, mount dial indicator with
tip resting on face edge of camshaft gear. Adjust indicator to zero.
Rotate camshaft gear 360 degrees and note reading. If backlash or
runout exceed specifications, replace camshaft and/or crankshaft
gear.
REAR MAIN OIL SEAL
* PLEASE READ THIS FIRST *
NOTE: Always refer to appropriate engine overhaul article in the
ENGINES section for complete overhaul procedures and
specifications for the vehicle being repaired.
INSTALLATION
One-Piece Type Seal
For one-piece type oil seal installation, coat block contact
surface of seal with sealer if seal is not factory coated. Ensure seal
surface is free of burrs. Lubricate seal lip with engine oil and press
seal into place using proper oil seal installer. See Fig. 27.
Fig. 27: Installing Typical One-Piece Oil Seal
This Graphic For General Information Only
Rope Type Seal
For rope type rear main oil seal installation, press seal
Page 587 of 1501
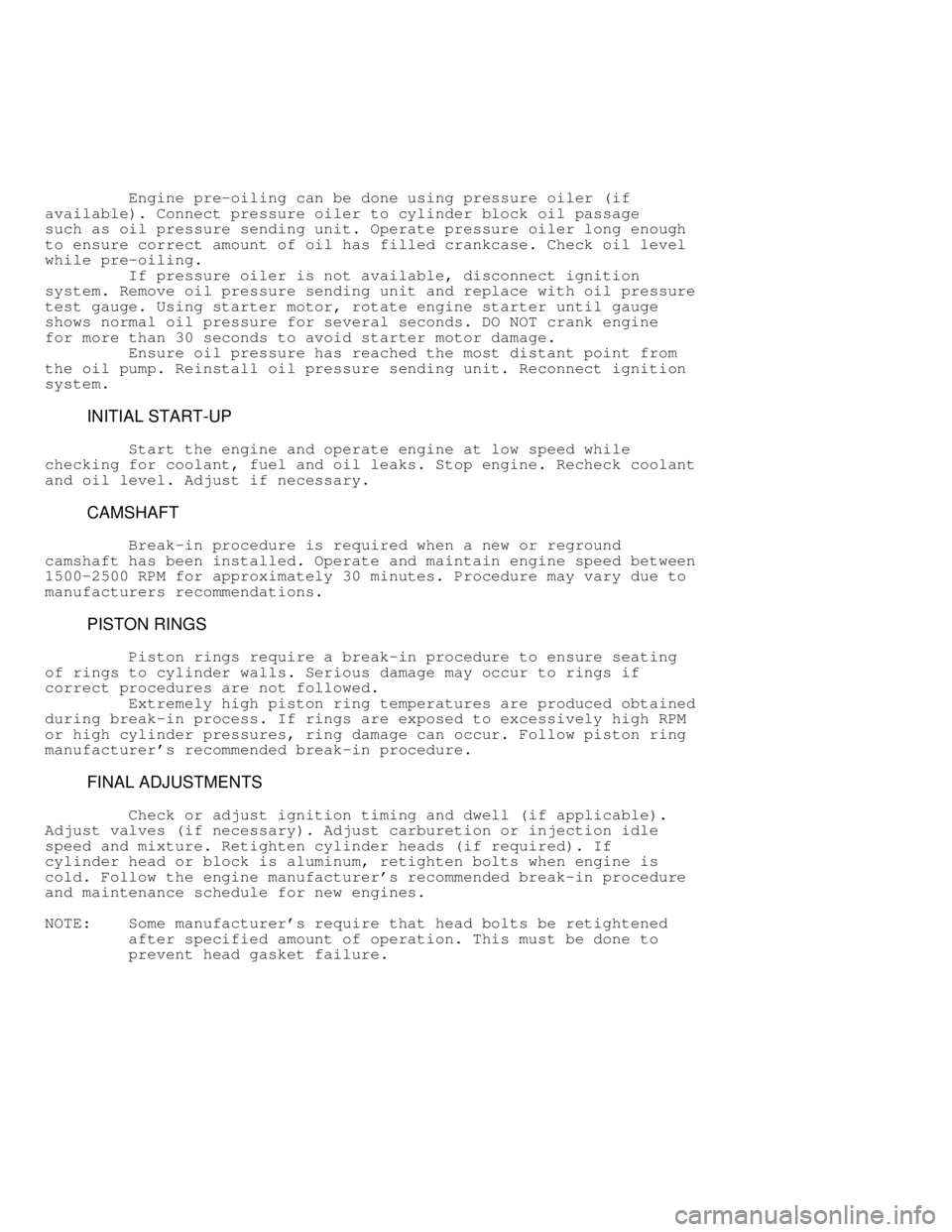
Engine pre-oiling can be done using pressure oiler (if
available). Connect pressure oiler to cylinder block oil passage
such as oil pressure sending unit. Operate pressure oiler long enough
to ensure correct amount of oil has filled crankcase. Check oil level
while pre-oiling.
If pressure oiler is not available, disconnect ignition
system. Remove oil pressure sending unit and replace with oil pressure
test gauge. Using starter motor, rotate engine starter until gauge
shows normal oil pressure for several seconds. DO NOT crank engine
for more than 30 seconds to avoid starter motor damage.
Ensure oil pressure has reached the most distant point from
the oil pump. Reinstall oil pressure sending unit. Reconnect ignition
system.
INITIAL START-UP
Start the engine and operate engine at low speed while
checking for coolant, fuel and oil leaks. Stop engine. Recheck coolant
and oil level. Adjust if necessary.
CAMSHAFT
Break-in procedure is required when a new or reground
camshaft has been installed. Operate and maintain engine speed between
1500-2500 RPM for approximately 30 minutes. Procedure may vary due to
manufacturers recommendations.
PISTON RINGS
Piston rings require a break-in procedure to ensure seating
of rings to cylinder walls. Serious damage may occur to rings if
correct procedures are not followed.
Extremely high piston ring temperatures are produced obtained
during break-in process. If rings are exposed to excessively high RPM
or high cylinder pressures, ring damage can occur. Follow piston ring
manufacturer's recommended break-in procedure.
FINAL ADJUSTMENTS
Check or adjust ignition timing and dwell (if applicable).
Adjust valves (if necessary). Adjust carburetion or injection idle
speed and mixture. Retighten cylinder heads (if required). If
cylinder head or block is aluminum, retighten bolts when engine is
cold. Follow the engine manufacturer's recommended break-in procedure
and maintenance schedule for new engines.
NOTE: Some manufacturer's require that head bolts be retightened
after specified amount of operation. This must be done to
prevent head gasket failure.
Page 589 of 1501
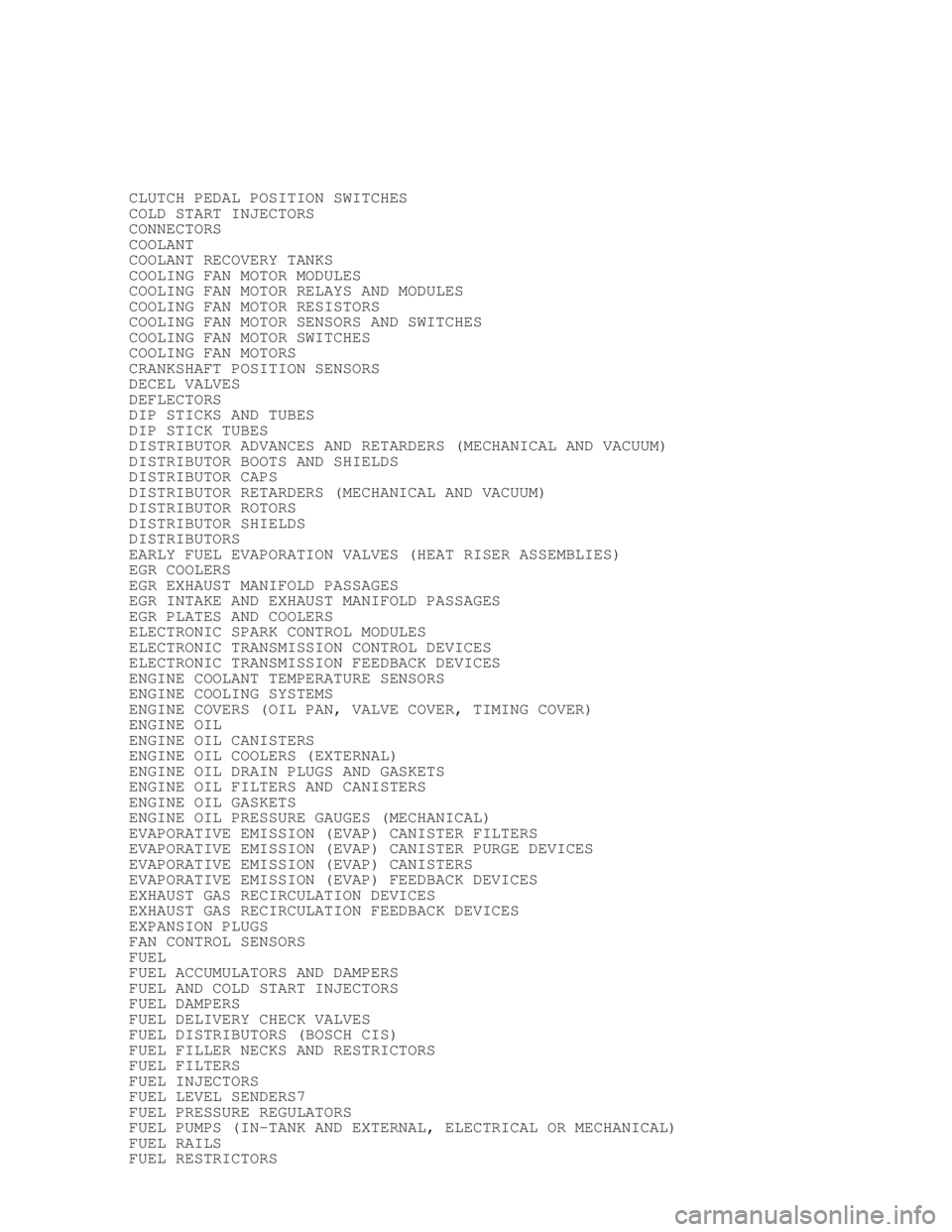
CLUTCH PEDAL POSITION SWITCHES
COLD START INJECTORS
CONNECTORS
COOLANT
COOLANT RECOVERY TANKS
COOLING FAN MOTOR MODULES
COOLING FAN MOTOR RELAYS AND MODULES
COOLING FAN MOTOR RESISTORS
COOLING FAN MOTOR SENSORS AND SWITCHES
COOLING FAN MOTOR SWITCHES
COOLING FAN MOTORS
CRANKSHAFT POSITION SENSORS
DECEL VALVES
DEFLECTORS
DIP STICKS AND TUBES
DIP STICK TUBES
DISTRIBUTOR ADVANCES AND RETARDERS (MECHANICAL AND VACUUM)
DISTRIBUTOR BOOTS AND SHIELDS
DISTRIBUTOR CAPS
DISTRIBUTOR RETARDERS (MECHANICAL AND VACUUM)
DISTRIBUTOR ROTORS
DISTRIBUTOR SHIELDS
DISTRIBUTORS
EARLY FUEL EVAPORATION VALVES (HEAT RISER ASSEMBLIES)
EGR COOLERS
EGR EXHAUST MANIFOLD PASSAGES
EGR INTAKE AND EXHAUST MANIFOLD PASSAGES
EGR PLATES AND COOLERS
ELECTRONIC SPARK CONTROL MODULES
ELECTRONIC TRANSMISSION CONTROL DEVICES
ELECTRONIC TRANSMISSION FEEDBACK DEVICES
ENGINE COOLANT TEMPERATURE SENSORS
ENGINE COOLING SYSTEMS
ENGINE COVERS (OIL PAN, VALVE COVER, TIMING COVER)
ENGINE OIL
ENGINE OIL CANISTERS
ENGINE OIL COOLERS (EXTERNAL)
ENGINE OIL DRAIN PLUGS AND GASKETS
ENGINE OIL FILTERS AND CANISTERS
ENGINE OIL GASKETS
ENGINE OIL PRESSURE GAUGES (MECHANICAL)
EVAPORATIVE EMISSION (EVAP) CANISTER FILTERS
EVAPORATIVE EMISSION (EVAP) CANISTER PURGE DEVICES
EVAPORATIVE EMISSION (EVAP) CANISTERS
EVAPORATIVE EMISSION (EVAP) FEEDBACK DEVICES
EXHAUST GAS RECIRCULATION DEVICES
EXHAUST GAS RECIRCULATION FEEDBACK DEVICES
EXPANSION PLUGS
FAN CONTROL SENSORS
FUEL
FUEL ACCUMULATORS AND DAMPERS
FUEL AND COLD START INJECTORS
FUEL DAMPERS
FUEL DELIVERY CHECK VALVES
FUEL DISTRIBUTORS (BOSCH CIS)
FUEL FILLER NECKS AND RESTRICTORS
FUEL FILTERS
FUEL INJECTORS
FUEL LEVEL SENDERS7
FUEL PRESSURE REGULATORS
FUEL PUMPS (IN-TANK AND EXTERNAL, ELECTRICAL OR MECHANICAL)
FUEL RAILS
FUEL RESTRICTORS
Page 591 of 1501
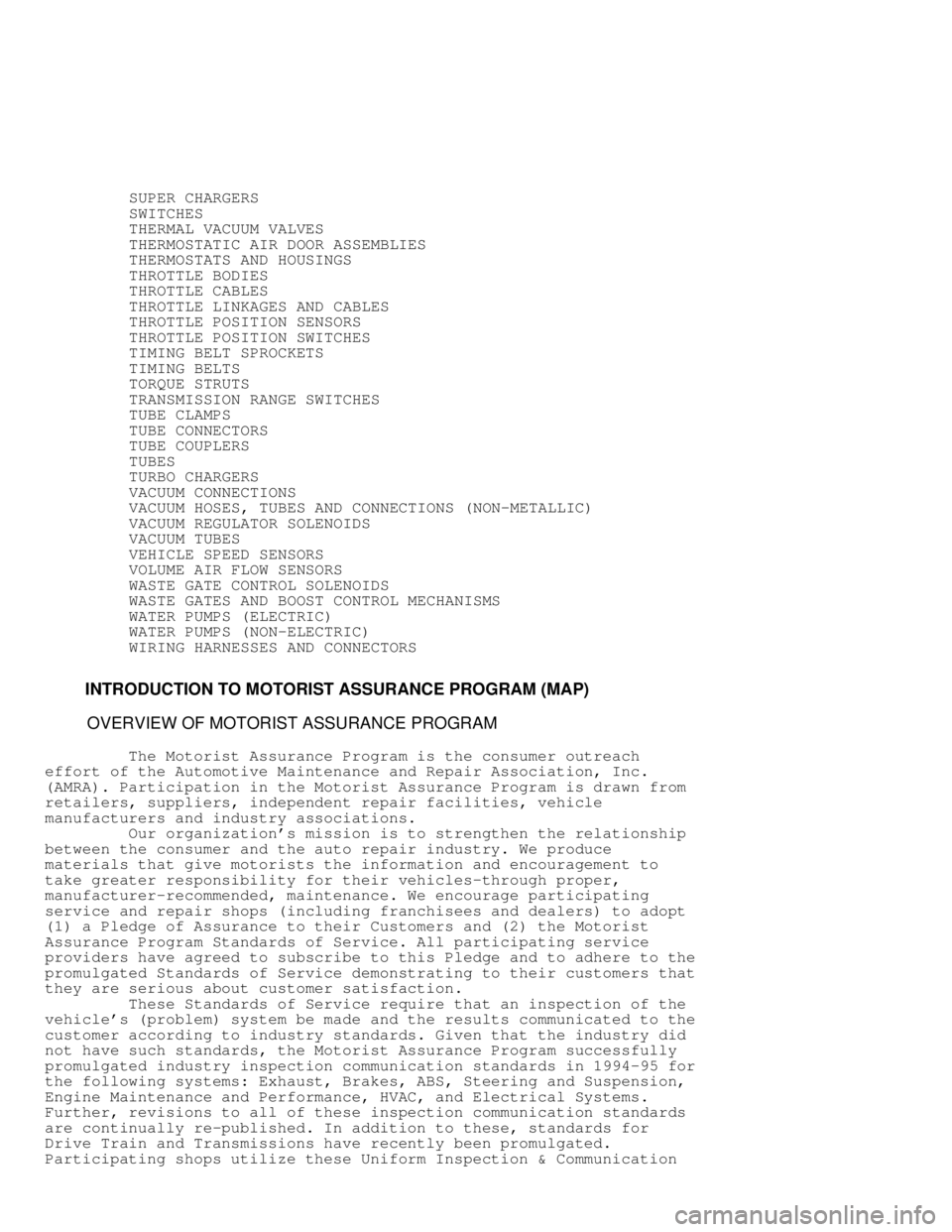
SUPER CHARGERS
SWITCHES
THERMAL VACUUM VALVES
THERMOSTATIC AIR DOOR ASSEMBLIES
THERMOSTATS AND HOUSINGS
THROTTLE BODIES
THROTTLE CABLES
THROTTLE LINKAGES AND CABLES
THROTTLE POSITION SENSORS
THROTTLE POSITION SWITCHES
TIMING BELT SPROCKETS
TIMING BELTS
TORQUE STRUTS
TRANSMISSION RANGE SWITCHES
TUBE CLAMPS
TUBE CONNECTORS
TUBE COUPLERS
TUBES
TURBO CHARGERS
VACUUM CONNECTIONS
VACUUM HOSES, TUBES AND CONNECTIONS (NON-METALLIC)
VACUUM REGULATOR SOLENOIDS
VACUUM TUBES
VEHICLE SPEED SENSORS
VOLUME AIR FLOW SENSORS
WASTE GATE CONTROL SOLENOIDS
WASTE GATES AND BOOST CONTROL MECHANISMS
WATER PUMPS (ELECTRIC)
WATER PUMPS (NON-ELECTRIC)
WIRING HARNESSES AND CONNECTORS
INTRODUCTION TO MOTORIST ASSURANCE PROGRAM (MAP)
OVERVIEW OF MOTORIST ASSURANCE PROGRAM
The Motorist Assurance Program is the consumer outreach
effort of the Automotive Maintenance and Repair Association, Inc.
(AMRA). Participation in the Motorist Assurance Program is drawn from
retailers, suppliers, independent repair facilities, vehicle
manufacturers and industry associations.
Our organization's mission is to strengthen the relationship
between the consumer and the auto repair industry. We produce
materials that give motorists the information and encouragement to
take greater responsibility for their vehicles-through proper,
manufacturer-recommended, maintenance. We encourage participating
service and repair shops (including franchisees and dealers) to adopt
(1) a Pledge of Assurance to their Customers and (2) the Motorist
Assurance Program Standards of Service. All participating service
providers have agreed to subscribe to this Pledge and to adhere to the
promulgated Standards of Service demonstrating to their customers that
they are serious about customer satisfaction.
These Standards of Service require that an inspection of the
vehicle's (problem) system be made and the results communicated to the\
customer according to industry standards. Given that the industry did
not have such standards, the Motorist Assurance Program successfully
promulgated industry inspection communication standards in 1994-95 for
the following systems: Exhaust, Brakes, ABS, Steering and Suspension,
Engine Maintenance and Performance, HVAC, and Electrical Systems.
Further, revisions to all of these inspection communication standards
are continually re-published. In addition to these, standards for
Drive Train and Transmissions have recently been promulgated.
Participating shops utilize these Uniform Inspection & Communication
Page 594 of 1501

Reasons to Suggest Repair or Replacement
1 - Part is close to the end of its useful life (just above
discard specifications, or weak; failure likely to occur
soon, etc.)
2 - To address a customer need, convenience, or request (to
stiffen ride, enhance performance, eliminate noise,
etc.)
3 - To comply with maintenance recommended by the vehicle's
Original Equipment Manufacturer (OEM)
4 - Technician's recommendation based on substantial and
informed experience
NOTE: Suggested services are always optional. When presenting
suggested repairs to the customer, you must present the
facts, allowing the customer to draw their own conclusions
and make an informed decision about how to proceed.
ENGINE ASSEMBLIES
SERVICE PROCEDURES REQUIRED AND SUGGESTED FOR PROPER VEHICLE
OPERATION
CYLINDER HEAD ASSEMBLIES
NOTE: A Cylinder Head Assembly is a cylinder head fitted with
valves, associated springs, retainers, and on overhead
camshaft cylinder heads (OHC), camshaft, camshaft
bearings, lash adjusters, tappets and rockers.
CYLINDER HEAD ASSEMBLY INSPECTION
\
\
\
\
\
\
\
Condition Code Procedure
Adjustable valve lash is
out of specification ... B ................. Require repair.
Internal component failure
(any component) ........ A ........... ( 1) Require repair or
replacement of cylinder
head assembly.
( 1) - It is Required that all other failure related components
be inspected for cause and condition. Additional components
or assemblies may be Suggested for repair or replacement,
such as a water pump on a short block (reason code 4,
technician's recommendation based on substantial and
informed experience).
Example:
If there is a failed head gasket with an external coolant
leak, in addition to Requiring replacement of the head
gasket, inspection of the following for cause and condition
is Required: Block, Cooling System, Cylinder Head. It may
be Suggested that additional inspections be performed, such
as the other head gasket on a V-type engine.
\
\
\
\
\
\
\
LONG BLOCK ASSEMBLIES
NOTE: A Long Block Assembly is a short block assembly together
with a cylinder head assembly and all those components
fitted within the rocker or cam cover, and timing cover