bolt pattern MITSUBISHI MONTERO 1998 Service Manual
[x] Cancel search | Manufacturer: MITSUBISHI, Model Year: 1998, Model line: MONTERO, Model: MITSUBISHI MONTERO 1998Pages: 1501, PDF Size: 25.81 MB
Page 260 of 1501
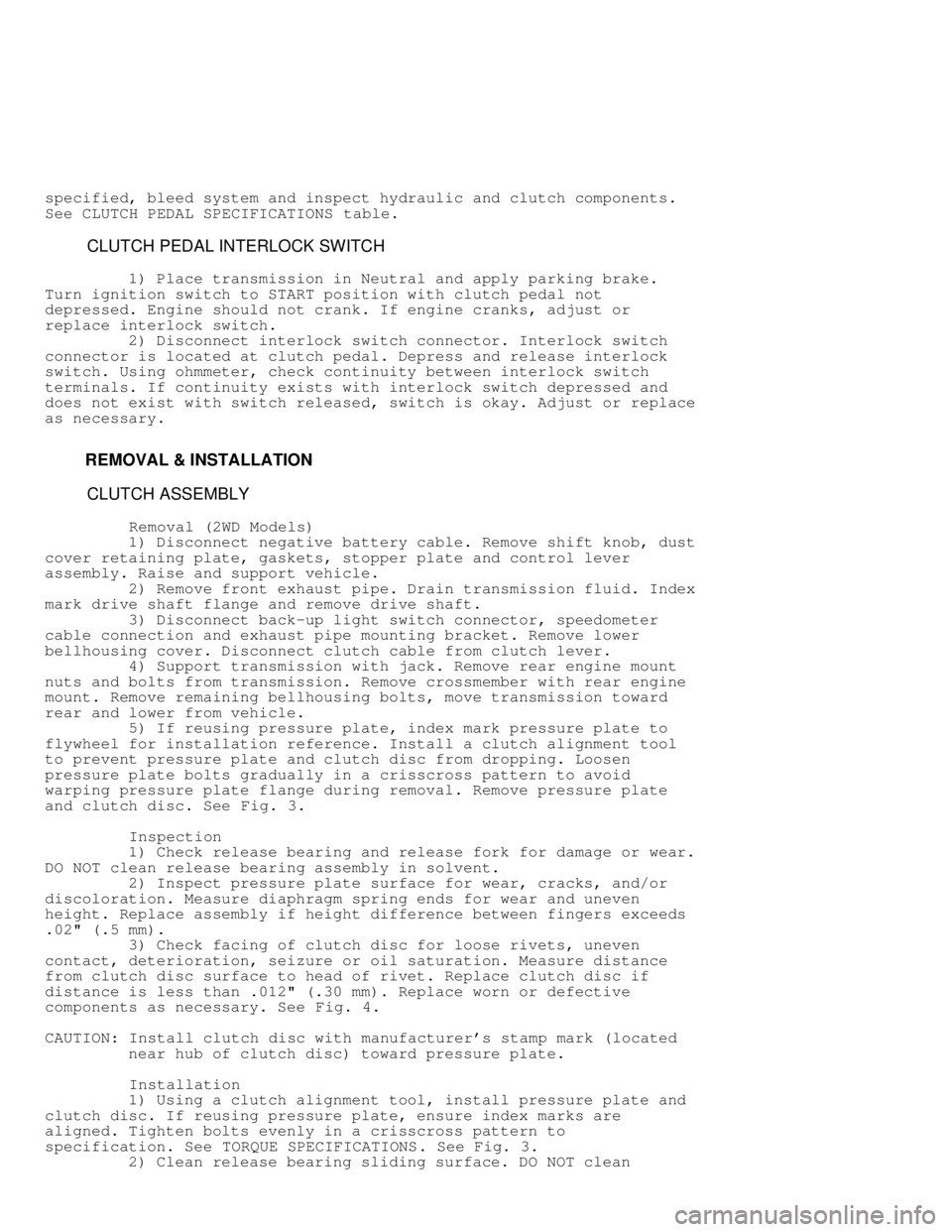
specified, bleed system and inspect hydraulic and clutch components.
See CLUTCH PEDAL SPECIFICATIONS table.
CLUTCH PEDAL INTERLOCK SWITCH
1) Place transmission in Neutral and apply parking brake.
Turn ignition switch to START position with clutch pedal not
depressed. Engine should not crank. If engine cranks, adjust or
replace interlock switch.
2) Disconnect interlock switch connector. Interlock switch
connector is located at clutch pedal. Depress and release interlock
switch. Using ohmmeter, check continuity between interlock switch
terminals. If continuity exists with interlock switch depressed and
does not exist with switch released, switch is okay. Adjust or replace
as necessary.
REMOVAL & INSTALLATION
CLUTCH ASSEMBLY
Removal (2WD Models)
1) Disconnect negative battery cable. Remove shift knob, dust
cover retaining plate, gaskets, stopper plate and control lever
assembly. Raise and support vehicle.
2) Remove front exhaust pipe. Drain transmission fluid. Index
mark drive shaft flange and remove drive shaft.
3) Disconnect back-up light switch connector, speedometer
cable connection and exhaust pipe mounting bracket. Remove lower
bellhousing cover. Disconnect clutch cable from clutch lever.
4) Support transmission with jack. Remove rear engine mount
nuts and bolts from transmission. Remove crossmember with rear engine
mount. Remove remaining bellhousing bolts, move transmission toward
rear and lower from vehicle.
5) If reusing pressure plate, index mark pressure plate to
flywheel for installation reference. Install a clutch alignment tool
to prevent pressure plate and clutch disc from dropping. Loosen
pressure plate bolts gradually in a crisscross pattern to avoid
warping pressure plate flange during removal. Remove pressure plate
and clutch disc. See Fig. 3.
Inspection
1) Check release bearing and release fork for damage or wear.
DO NOT clean release bearing assembly in solvent.
2) Inspect pressure plate surface for wear, cracks, and/or
discoloration. Measure diaphragm spring ends for wear and uneven
height. Replace assembly if height difference between fingers exceeds
.02" (.5 mm).
3) Check facing of clutch disc for loose rivets, uneven
contact, deterioration, seizure or oil saturation. Measure distance
from clutch disc surface to head of rivet. Replace clutch disc if
distance is less than .012" (.30 mm). Replace worn or defective
components as necessary. See Fig. 4.
CAUTION: Install clutch disc with manufacturer's stamp mark (located
near hub of clutch disc) toward pressure plate.
Installation
1) Using a clutch alignment tool, install pressure plate and
clutch disc. If reusing pressure plate, ensure index marks are
aligned. Tighten bolts evenly in a crisscross pattern to
specification. See TORQUE SPECIFICATIONS . See Fig. 3.
2) Clean release bearing sliding surface. DO NOT clean
Page 261 of 1501
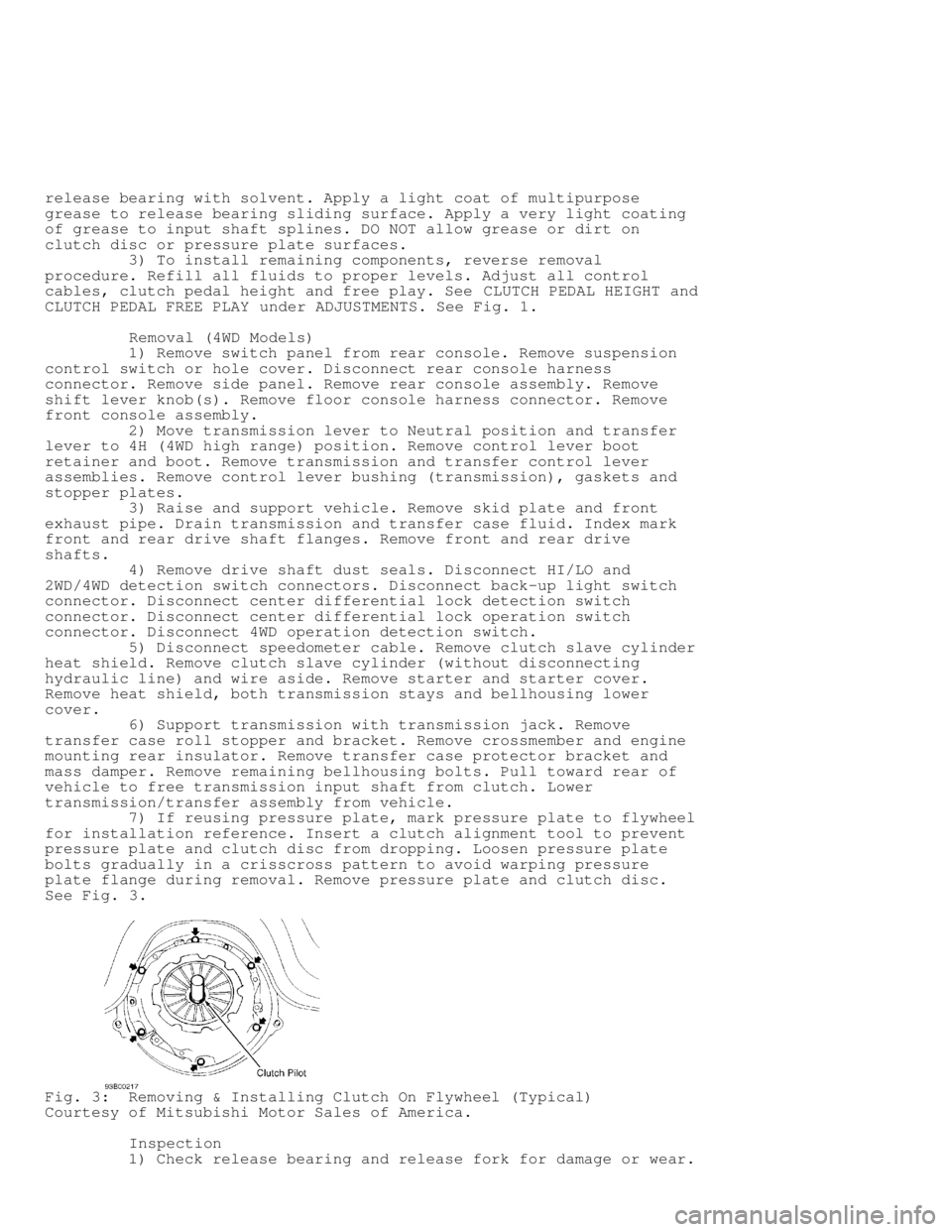
release bearing with solvent. Apply a light coat of multipurpose
grease to release bearing sliding surface. Apply a very light coating
of grease to input shaft splines. DO NOT allow grease or dirt on
clutch disc or pressure plate surfaces.
3) To install remaining components, reverse removal
procedure. Refill all fluids to proper levels. Adjust all control
cables, clutch pedal height and free play. See CLUTCH PEDAL HEIGHT and
CLUTCH PEDAL FREE PLAY under ADJUSTMENTS. See Fig. 1.
Removal (4WD Models)
1) Remove switch panel from rear console. Remove suspension
control switch or hole cover. Disconnect rear console harness
connector. Remove side panel. Remove rear console assembly. Remove
shift lever knob(s). Remove floor console harness connector. Remove
front console assembly.
2) Move transmission lever to Neutral position and transfer
lever to 4H (4WD high range) position. Remove control lever boot
retainer and boot. Remove transmission and transfer control lever
assemblies. Remove control lever bushing (transmission), gaskets and
stopper plates.
3) Raise and support vehicle. Remove skid plate and front
exhaust pipe. Drain transmission and transfer case fluid. Index mark
front and rear drive shaft flanges. Remove front and rear drive
shafts.
4) Remove drive shaft dust seals. Disconnect HI/LO and
2WD/4WD detection switch connectors. Disconnect back-up light switch
connector. Disconnect center differential lock detection switch
connector. Disconnect center differential lock operation switch
connector. Disconnect 4WD operation detection switch.
5) Disconnect speedometer cable. Remove clutch slave cylinder
heat shield. Remove clutch slave cylinder (without disconnecting
hydraulic line) and wire aside. Remove starter and starter cover.
Remove heat shield, both transmission stays and bellhousing lower
cover.
6) Support transmission with transmission jack. Remove
transfer case roll stopper and bracket. Remove crossmember and engine
mounting rear insulator. Remove transfer case protector bracket and
mass damper. Remove remaining bellhousing bolts. Pull toward rear of
vehicle to free transmission input shaft from clutch. Lower
transmission/transfer assembly from vehicle.
7) If reusing pressure plate, mark pressure plate to flywheel
for installation reference. Insert a clutch alignment tool to prevent
pressure plate and clutch disc from dropping. Loosen pressure plate
bolts gradually in a crisscross pattern to avoid warping pressure
plate flange during removal. Remove pressure plate and clutch disc.
See Fig. 3 .
Fig. 3: Removing & Installing Clutch On Flywheel (Typical)
Courtesy of Mitsubishi Motor Sales of America.
Inspection
1) Check release bearing and release fork for damage or wear.
Page 262 of 1501
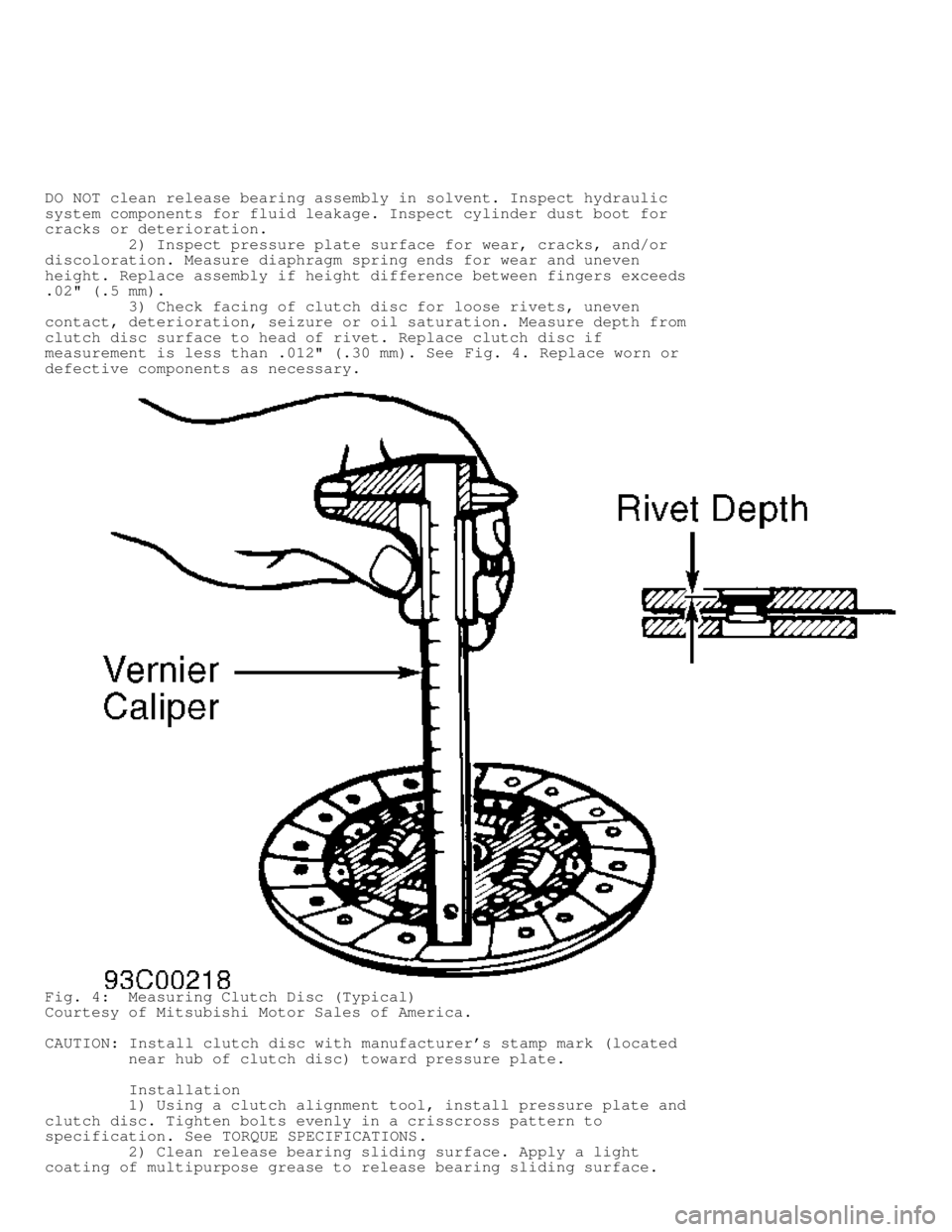
DO NOT clean release bearing assembly in solvent. Inspect hydraulic
system components for fluid leakage. Inspect cylinder dust boot for
cracks or deterioration.
2) Inspect pressure plate surface for wear, cracks, and/or
discoloration. Measure diaphragm spring ends for wear and uneven
height. Replace assembly if height difference between fingers exceeds
.02" (.5 mm).
3) Check facing of clutch disc for loose rivets, uneven
contact, deterioration, seizure or oil saturation. Measure depth from
clutch disc surface to head of rivet. Replace clutch disc if
measurement is less than .012" (.30 mm). See Fig. 4. Replace worn or
defective components as necessary.
Fig. 4: Measuring Clutch Disc (Typical)
Courtesy of Mitsubishi Motor Sales of America.
CAUTION: Install clutch disc with manufacturer's stamp mark (located
near hub of clutch disc) toward pressure plate.
Installation
1) Using a clutch alignment tool, install pressure plate and
clutch disc. Tighten bolts evenly in a crisscross pattern to
specification. See TORQUE SPECIFICATIONS .
2) Clean release bearing sliding surface. Apply a light
coating of multipurpose grease to release bearing sliding surface.
Page 367 of 1501
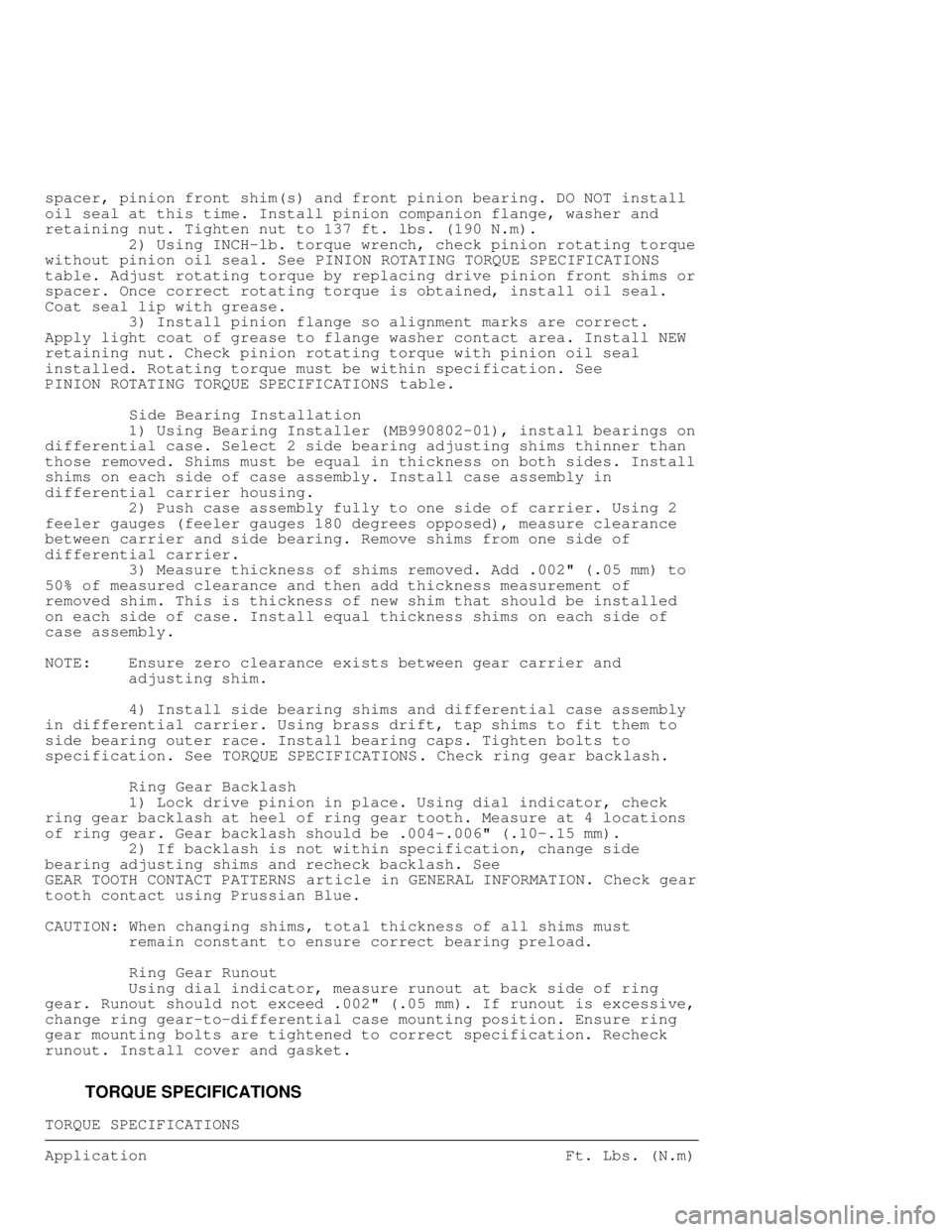
spacer, pinion front shim(s) and front pinion bearing. DO NOT install
oil seal at this time. Install pinion companion flange, washer and
retaining nut. Tighten nut to 137 ft. lbs. (190 N.m).
2) Using INCH-lb. torque wrench, check pinion rotating torque
without pinion oil seal. See PINION ROTATING TORQUE SPECIFICATIONS
table. Adjust rotating torque by replacing drive pinion front shims or
spacer. Once correct rotating torque is obtained, install oil seal.
Coat seal lip with grease.
3) Install pinion flange so alignment marks are correct.
Apply light coat of grease to flange washer contact area. Install NEW
retaining nut. Check pinion rotating torque with pinion oil seal
installed. Rotating torque must be within specification. See
PINION ROTATING TORQUE SPECIFICATIONS table.
Side Bearing Installation
1) Using Bearing Installer (MB990802-01), install bearings o\
n
differential case. Select 2 side bearing adjusting shims thinner than
those removed. Shims must be equal in thickness on both sides. Install
shims on each side of case assembly. Install case assembly in
differential carrier housing.
2) Push case assembly fully to one side of carrier. Using 2
feeler gauges (feeler gauges 180 degrees opposed), measure clearance
between carrier and side bearing. Remove shims from one side of
differential carrier.
3) Measure thickness of shims removed. Add .002" (.05 mm) to\
50% of measured clearance and then add thickness measurement of
removed shim. This is thickness of new shim that should be installed
on each side of case. Install equal thickness shims on each side of
case assembly.
NOTE: Ensure zero clearance exists between gear carrier and
adjusting shim.
4) Install side bearing shims and differential case assembly
in differential carrier. Using brass drift, tap shims to fit them to
side bearing outer race. Install bearing caps. Tighten bolts to
specification. See TORQUE SPECIFICATIONS . Check ring gear backlash.
Ring Gear Backlash
1) Lock drive pinion in place. Using dial indicator, check
ring gear backlash at heel of ring gear tooth. Measure at 4 locations
of ring gear. Gear backlash should be .004-.006" (.10-.15 mm).
2) If backlash is not within specification, change side
bearing adjusting shims and recheck backlash. See
GEAR TOOTH CONTACT PATTERNS article in GENERAL INFORMATION. Check gear
tooth contact using Prussian Blue.
CAUTION: When changing shims, total thickness of all shims must
remain constant to ensure correct bearing preload.
Ring Gear Runout
Using dial indicator, measure runout at back side of ring
gear. Runout should not exceed .002" (.05 mm). If runout is excessive,\
change ring gear-to-differential case mounting position. Ensure ring
gear mounting bolts are tightened to correct specification. Recheck
runout. Install cover and gasket.
TORQUE SPECIFICATIONS
TORQUE SPECIFICATIONS \
\
\
\
\
\
\
Application Ft. Lbs. (N.m)\
Page 379 of 1501
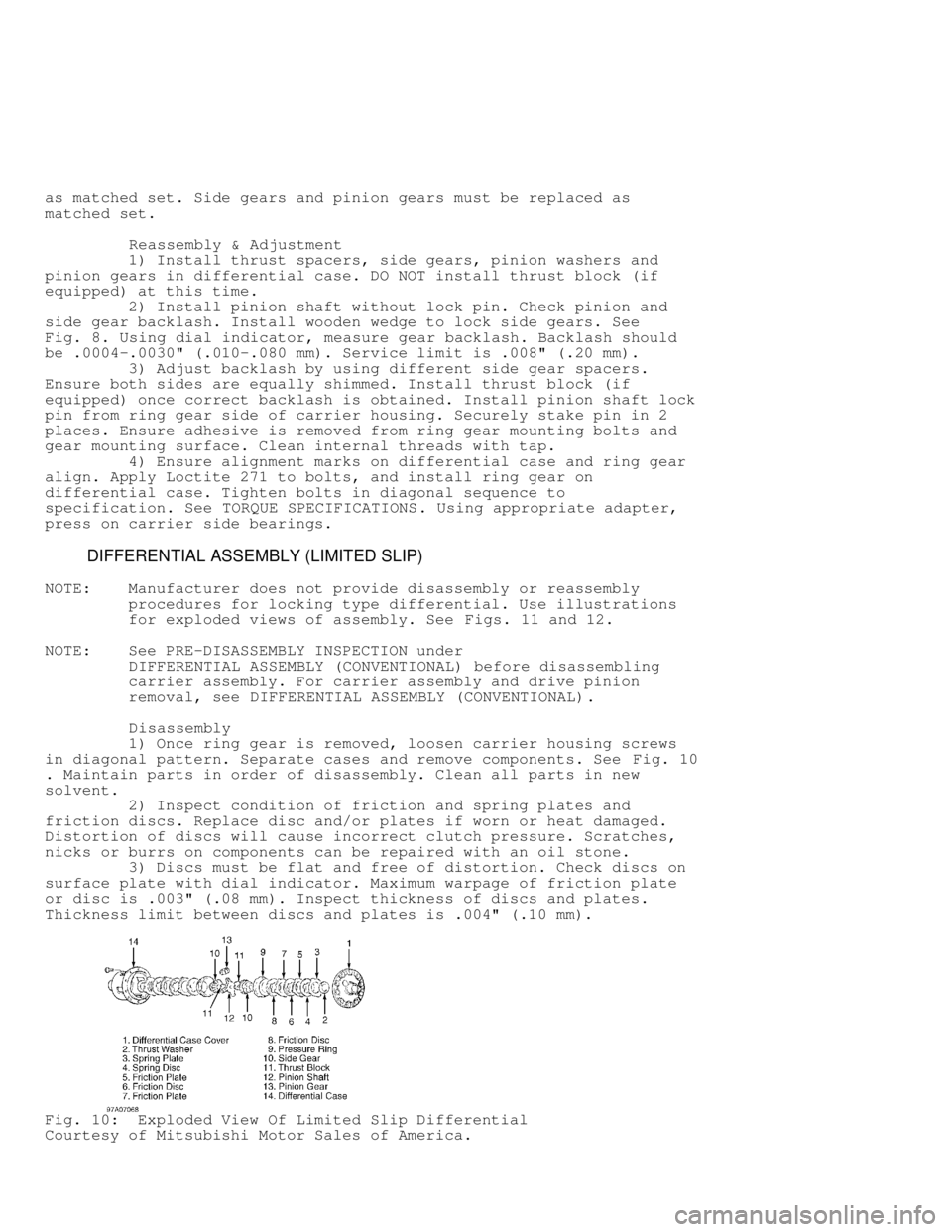
as matched set. Side gears and pinion gears must be replaced as
matched set.
Reassembly & Adjustment
1) Install thrust spacers, side gears, pinion washers and
pinion gears in differential case. DO NOT install thrust block (if
equipped) at this time.
2) Install pinion shaft without lock pin. Check pinion and
side gear backlash. Install wooden wedge to lock side gears. See
Fig. 8 . Using dial indicator, measure gear backlash. Backlash should
be .0004-.0030" (.010-.080 mm). Service limit is .008" (.20 mm).
3) Adjust backlash by using different side gear spacers.
Ensure both sides are equally shimmed. Install thrust block (if
equipped) once correct backlash is obtained. Install pinion shaft lock
pin from ring gear side of carrier housing. Securely stake pin in 2
places. Ensure adhesive is removed from ring gear mounting bolts and
gear mounting surface. Clean internal threads with tap.
4) Ensure alignment marks on differential case and ring gear
align. Apply Loctite 271 to bolts, and install ring gear on
differential case. Tighten bolts in diagonal sequence to
specification. See TORQUE SPECIFICATIONS . Using appropriate adapter,
press on carrier side bearings.
DIFFERENTIAL ASSEMBLY (LIMITED SLIP)
NOTE: Manufacturer does not provide disassembly or reassembly
procedures for locking type differential. Use illustrations
for exploded views of assembly. See Figs. 11 and 12.
NOTE: See PRE-DISASSEMBLY INSPECTION under
DIFFERENTIAL ASSEMBLY (CONVENTIONAL) before disassembling
carrier assembly. For carrier assembly and drive pinion
removal, see DIFFERENTIAL ASSEMBLY (CONVENTIONAL) .
Disassembly
1) Once ring gear is removed, loosen carrier housing screws
in diagonal pattern. Separate cases and remove components. See Fig. 10
. Maintain parts in order of disassembly. Clean all parts in new
solvent.
2) Inspect condition of friction and spring plates and
friction discs. Replace disc and/or plates if worn or heat damaged.
Distortion of discs will cause incorrect clutch pressure. Scratches,
nicks or burrs on components can be repaired with an oil stone.
3) Discs must be flat and free of distortion. Check discs on
surface plate with dial indicator. Maximum warpage of friction plate
or disc is .003" (.08 mm). Inspect thickness of discs and plates.
Thickness limit between discs and plates is .004" (.10 mm).
Fig. 10: Exploded View Of Limited Slip Differential
Courtesy of Mitsubishi Motor Sales of America.