drain bolt MITSUBISHI MONTERO 1998 Service Manual
[x] Cancel search | Manufacturer: MITSUBISHI, Model Year: 1998, Model line: MONTERO, Model: MITSUBISHI MONTERO 1998Pages: 1501, PDF Size: 25.81 MB
Page 14 of 1501
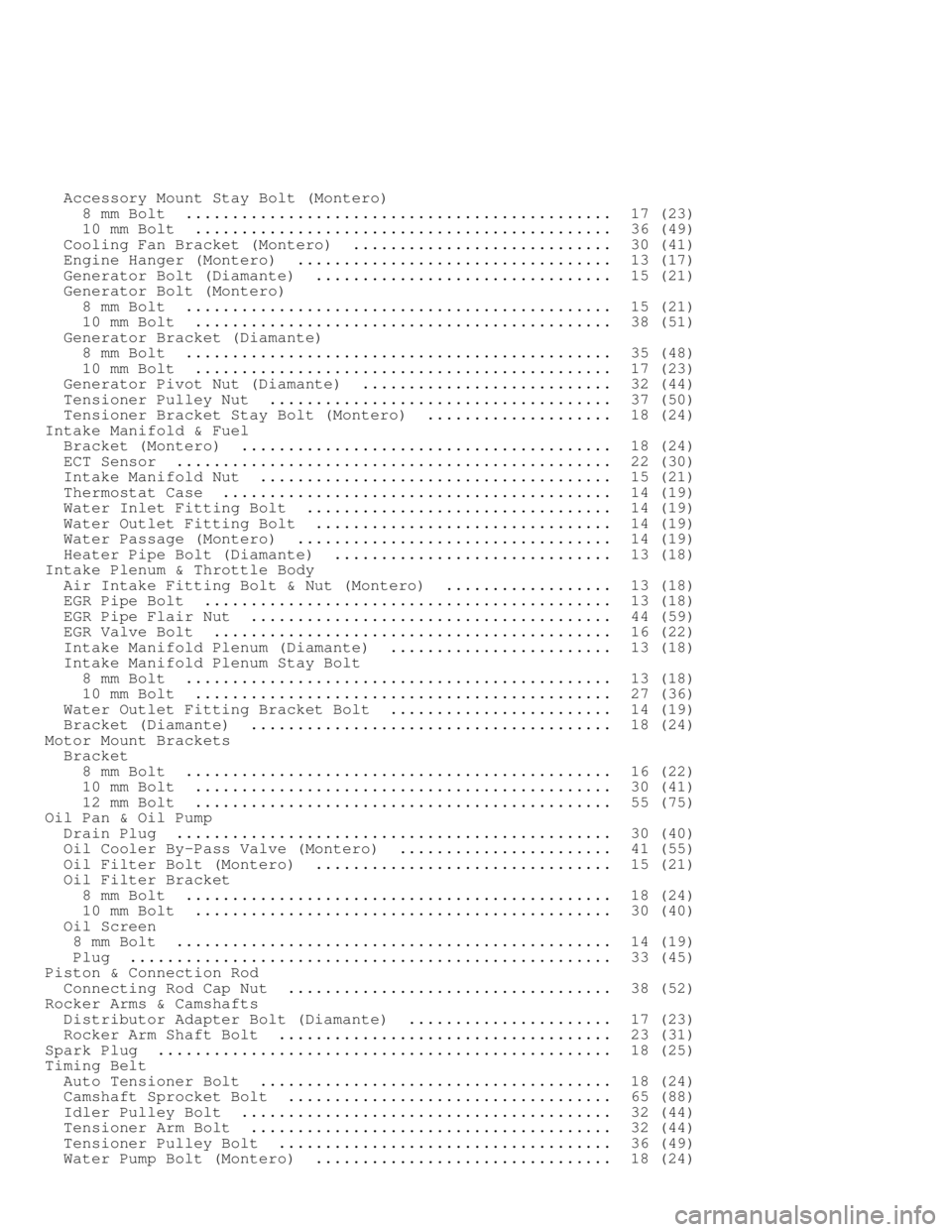
Accessory Mount Stay Bolt (Montero)
8 mm Bolt .............................................. 17 (23)\
10 mm Bolt ............................................. 36 (49)\
Cooling Fan Bracket (Montero) ............................ 30 (41\
)
Engine Hanger (Montero) .................................. 13 (17\
)
Generator Bolt (Diamante) ................................ 15 (21\
)
Generator Bolt (Montero)
8 mm Bolt .............................................. 15 (21)\
10 mm Bolt ............................................. 38 (51)\
Generator Bracket (Diamante)
8 mm Bolt .............................................. 35 (48)\
10 mm Bolt ............................................. 17 (23)\
Generator Pivot Nut (Diamante) ........................... 32 (44\
)
Tensioner Pulley Nut ..................................... 37 (50)\
Tensioner Bracket Stay Bolt (Montero) .................... 18 (24\
)
Intake Manifold & Fuel
Bracket (Montero) ........................................ 18 (24\
)
ECT Sensor ............................................... 22 (30)\
Intake Manifold Nut ...................................... 15 (21)\
Thermostat Case .......................................... 14 (19)\
Water Inlet Fitting Bolt ................................. 14 (19)\
Water Outlet Fitting Bolt ................................ 14 (19)\
Water Passage (Montero) .................................. 14 (19\
)
Heater Pipe Bolt (Diamante) .............................. 13 (18\
)
Intake Plenum & Throttle Body
Air Intake Fitting Bolt & Nut (Montero) .................. 13 (18\
)
EGR Pipe Bolt ............................................ 13 (18)\
EGR Pipe Flair Nut ....................................... 44 (59)\
EGR Valve Bolt ........................................... 16 (22)\
Intake Manifold Plenum (Diamante) ........................ 13 (18\
)
Intake Manifold Plenum Stay Bolt
8 mm Bolt .............................................. 13 (18)\
10 mm Bolt ............................................. 27 (36)\
Water Outlet Fitting Bracket Bolt ........................ 14 (19)\
Bracket (Diamante) ....................................... 18 (24\
)
Motor Mount Brackets
Bracket
8 mm Bolt .............................................. 16 (22)\
10 mm Bolt ............................................. 30 (41)\
12 mm Bolt ............................................. 55 (75)\
Oil Pan & Oil Pump
Drain Plug ............................................... 30 (40)\
Oil Cooler By-Pass Valve (Montero) ....................... 41 (55\
)
Oil Filter Bolt (Montero) ................................ 15 (21\
)
Oil Filter Bracket
8 mm Bolt .............................................. 18 (24)\
10 mm Bolt ............................................. 30 (40)\
Oil Screen
8 mm Bolt ............................................... 14 (19)\
Plug .................................................... 33 (45)\
Piston & Connection Rod
Connecting Rod Cap Nut ................................... 38 (52)\
Rocker Arms & Camshafts
Distributor Adapter Bolt (Diamante) ...................... 17 (23\
)
Rocker Arm Shaft Bolt .................................... 23 (31)\
Spark Plug ................................................. 18 (25)\
Timing Belt
Auto Tensioner Bolt ...................................... 18 (24)\
Camshaft Sprocket Bolt ................................... 65 (88)\
Idler Pulley Bolt ........................................ 32 (44)\
Tensioner Arm Bolt ....................................... 32 (44)\
Tensioner Pulley Bolt .................................... 36 (49)\
Water Pump Bolt (Montero) ................................ 18 (24\
)
Page 97 of 1501
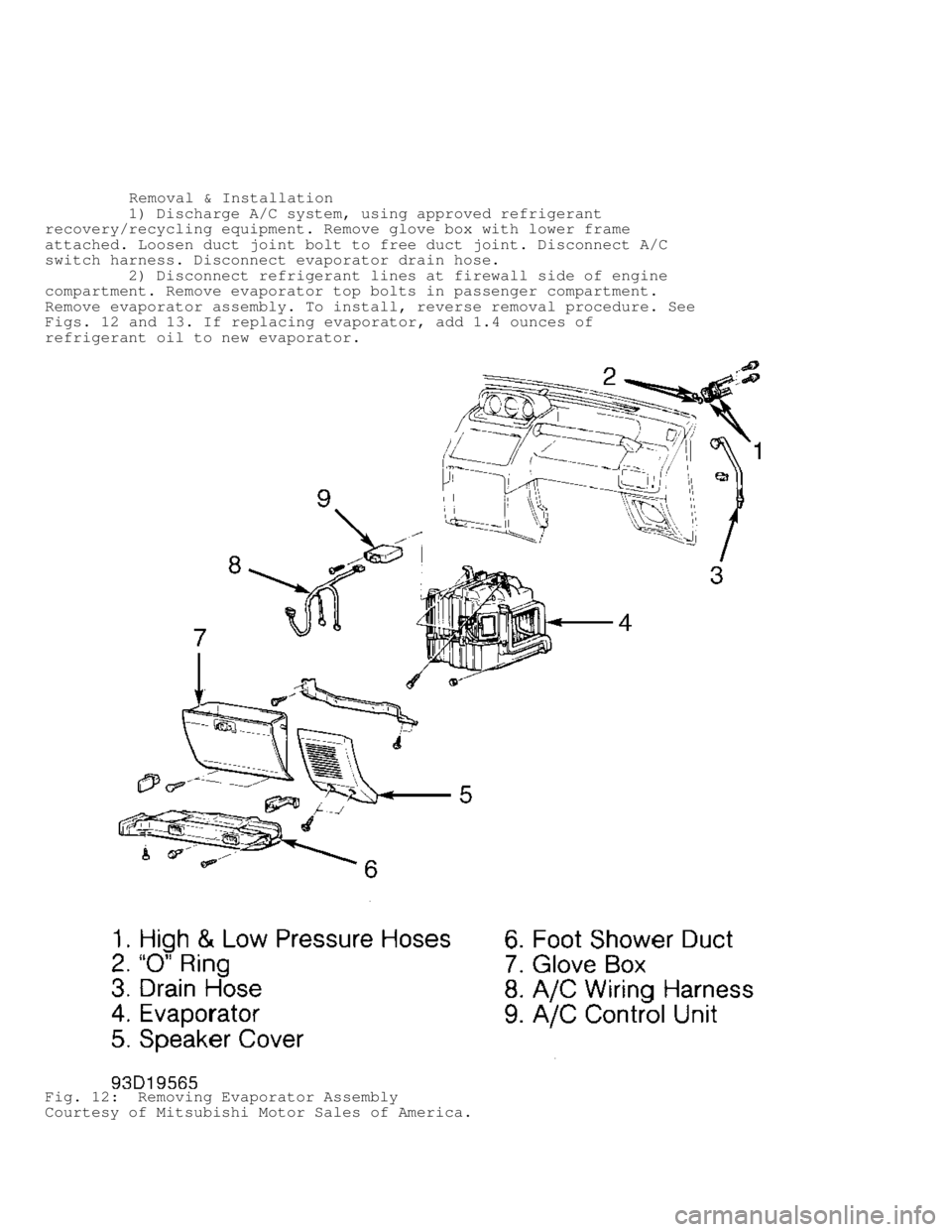
Removal & Installation
1) Discharge A/C system, using approved refrigerant
recovery/recycling equipment. Remove glove box with lower frame
attached. Loosen duct joint bolt to free duct joint. Disconnect A/C
switch harness. Disconnect evaporator drain hose.
2) Disconnect refrigerant lines at firewall side of engine
compartment. Remove evaporator top bolts in passenger compartment.
Remove evaporator assembly. To install, reverse removal procedure. See
Figs. 12 and 13. If replacing evaporator, add 1.4 ounces of
refrigerant oil to new evaporator.
Fig. 12: Removing Evaporator Assembly
Courtesy of Mitsubishi Motor Sales of America.
Page 233 of 1501
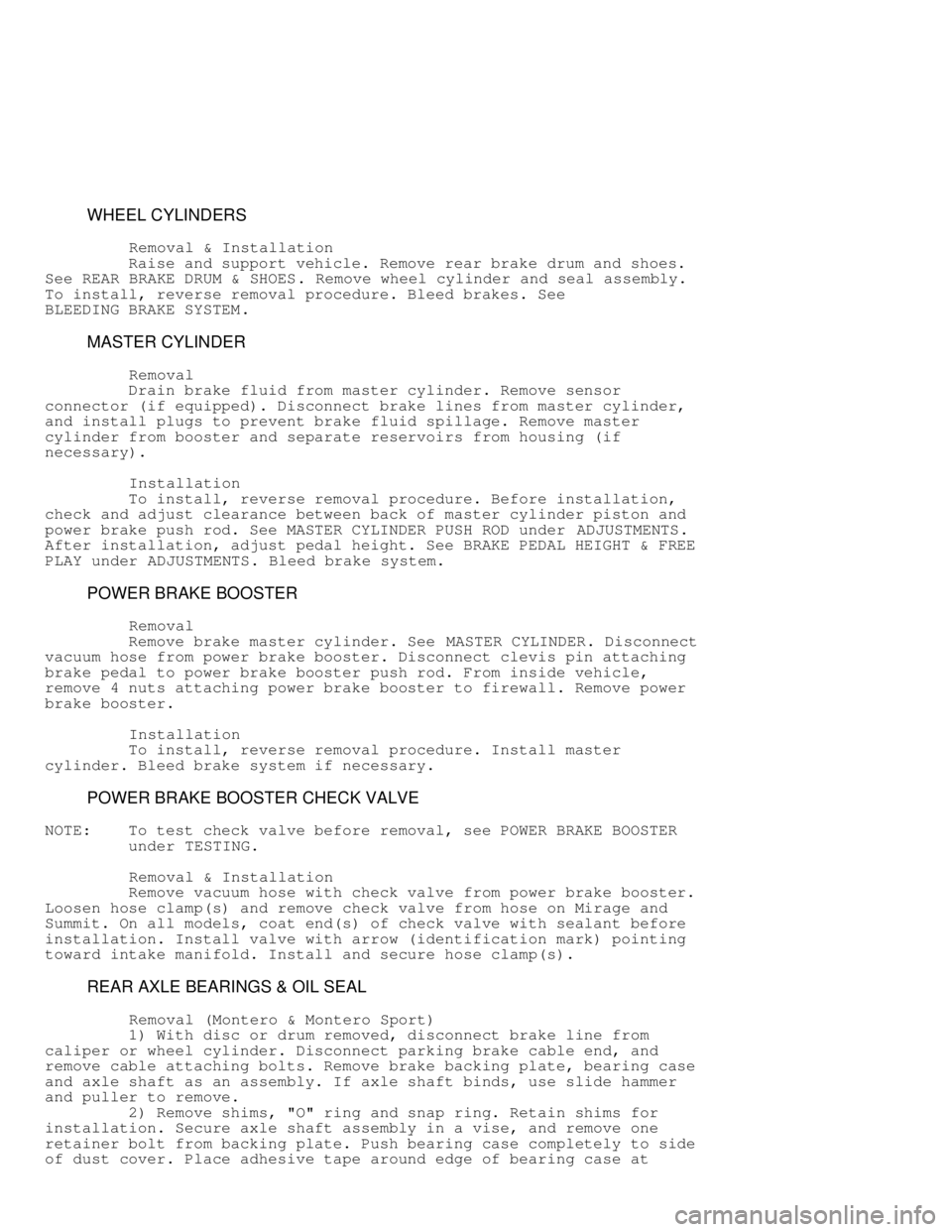
WHEEL CYLINDERS
Removal & Installation
Raise and support vehicle. Remove rear brake drum and shoes.
See REAR BRAKE DRUM & SHOES . Remove wheel cylinder and seal assembly.
To install, reverse removal procedure. Bleed brakes. See
BLEEDING BRAKE SYSTEM .
MASTER CYLINDER
Removal
Drain brake fluid from master cylinder. Remove sensor
connector (if equipped). Disconnect brake lines from master cylinder,
and install plugs to prevent brake fluid spillage. Remove master
cylinder from booster and separate reservoirs from housing (if
necessary).
Installation
To install, reverse removal procedure. Before installation,
check and adjust clearance between back of master cylinder piston and
power brake push rod. See MASTER CYLINDER PUSH ROD under ADJUSTMENTS.
After installation, adjust pedal height. See BRAKE PEDAL HEIGHT & FREE
PLAY under ADJUSTMENTS. Bleed brake system.
POWER BRAKE BOOSTER
Removal
Remove brake master cylinder. See MASTER CYLINDER. Disconnect
vacuum hose from power brake booster. Disconnect clevis pin attaching
brake pedal to power brake booster push rod. From inside vehicle,
remove 4 nuts attaching power brake booster to firewall. Remove power
brake booster.
Installation
To install, reverse removal procedure. Install master
cylinder. Bleed brake system if necessary.
POWER BRAKE BOOSTER CHECK VALVE
NOTE: To test check valve before removal, see POWER BRAKE BOOSTER
under TESTING.
Removal & Installation
Remove vacuum hose with check valve from power brake booster.
Loosen hose clamp(s) and remove check valve from hose on Mirage and
Summit. On all models, coat end(s) of check valve with sealant before
installation. Install valve with arrow (identification mark) pointing
toward intake manifold. Install and secure hose clamp(s).
REAR AXLE BEARINGS & OIL SEAL
Removal (Montero & Montero Sport)
1) With disc or drum removed, disconnect brake line from
caliper or wheel cylinder. Disconnect parking brake cable end, and
remove cable attaching bolts. Remove brake backing plate, bearing case
and axle shaft as an assembly. If axle shaft binds, use slide hammer
and puller to remove.
2) Remove shims, "O" ring and snap ring. Retain shims for
installation. Secure axle shaft assembly in a vise, and remove one
retainer bolt from backing plate. Push bearing case completely to side
of dust cover. Place adhesive tape around edge of bearing case at
Page 260 of 1501
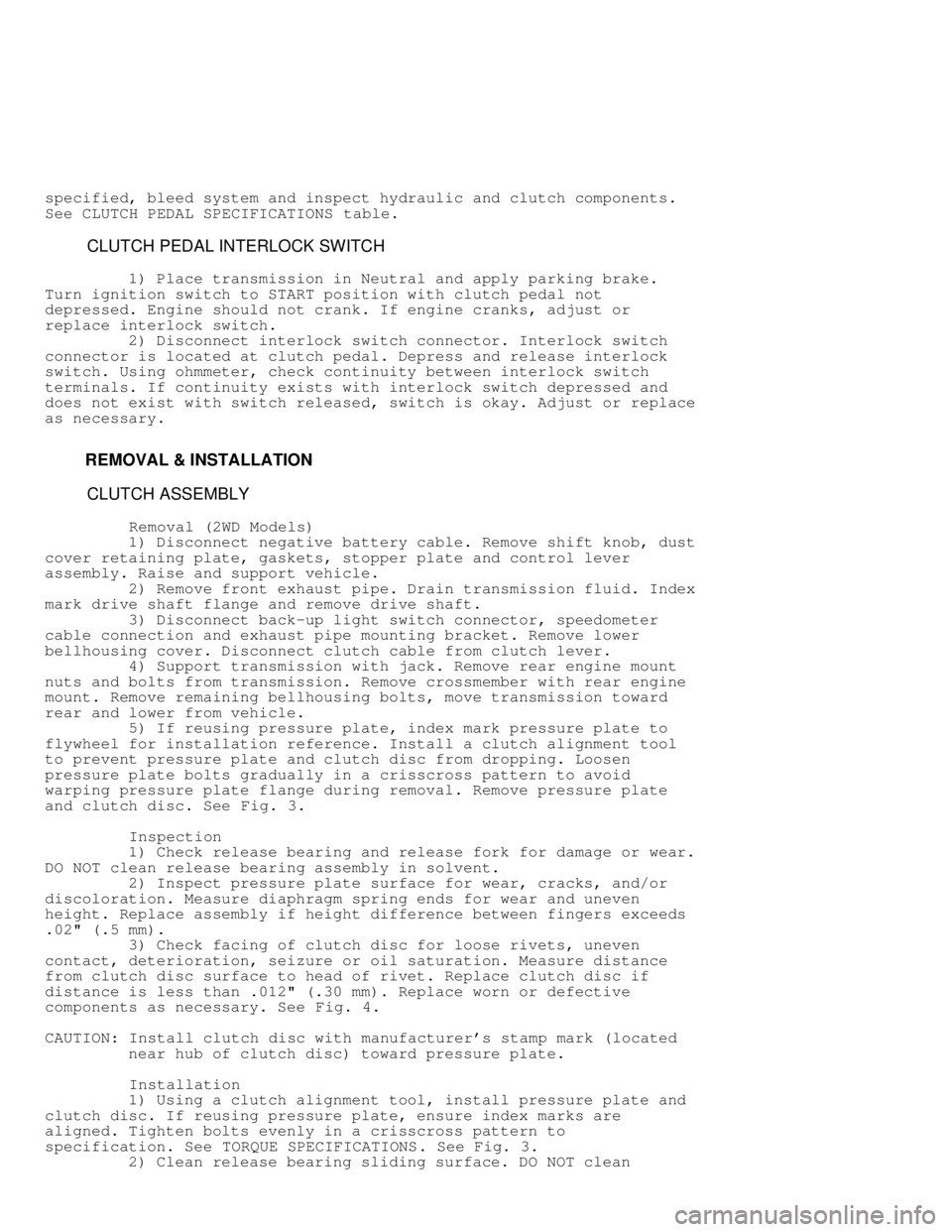
specified, bleed system and inspect hydraulic and clutch components.
See CLUTCH PEDAL SPECIFICATIONS table.
CLUTCH PEDAL INTERLOCK SWITCH
1) Place transmission in Neutral and apply parking brake.
Turn ignition switch to START position with clutch pedal not
depressed. Engine should not crank. If engine cranks, adjust or
replace interlock switch.
2) Disconnect interlock switch connector. Interlock switch
connector is located at clutch pedal. Depress and release interlock
switch. Using ohmmeter, check continuity between interlock switch
terminals. If continuity exists with interlock switch depressed and
does not exist with switch released, switch is okay. Adjust or replace
as necessary.
REMOVAL & INSTALLATION
CLUTCH ASSEMBLY
Removal (2WD Models)
1) Disconnect negative battery cable. Remove shift knob, dust
cover retaining plate, gaskets, stopper plate and control lever
assembly. Raise and support vehicle.
2) Remove front exhaust pipe. Drain transmission fluid. Index
mark drive shaft flange and remove drive shaft.
3) Disconnect back-up light switch connector, speedometer
cable connection and exhaust pipe mounting bracket. Remove lower
bellhousing cover. Disconnect clutch cable from clutch lever.
4) Support transmission with jack. Remove rear engine mount
nuts and bolts from transmission. Remove crossmember with rear engine
mount. Remove remaining bellhousing bolts, move transmission toward
rear and lower from vehicle.
5) If reusing pressure plate, index mark pressure plate to
flywheel for installation reference. Install a clutch alignment tool
to prevent pressure plate and clutch disc from dropping. Loosen
pressure plate bolts gradually in a crisscross pattern to avoid
warping pressure plate flange during removal. Remove pressure plate
and clutch disc. See Fig. 3.
Inspection
1) Check release bearing and release fork for damage or wear.
DO NOT clean release bearing assembly in solvent.
2) Inspect pressure plate surface for wear, cracks, and/or
discoloration. Measure diaphragm spring ends for wear and uneven
height. Replace assembly if height difference between fingers exceeds
.02" (.5 mm).
3) Check facing of clutch disc for loose rivets, uneven
contact, deterioration, seizure or oil saturation. Measure distance
from clutch disc surface to head of rivet. Replace clutch disc if
distance is less than .012" (.30 mm). Replace worn or defective
components as necessary. See Fig. 4.
CAUTION: Install clutch disc with manufacturer's stamp mark (located
near hub of clutch disc) toward pressure plate.
Installation
1) Using a clutch alignment tool, install pressure plate and
clutch disc. If reusing pressure plate, ensure index marks are
aligned. Tighten bolts evenly in a crisscross pattern to
specification. See TORQUE SPECIFICATIONS . See Fig. 3.
2) Clean release bearing sliding surface. DO NOT clean
Page 261 of 1501
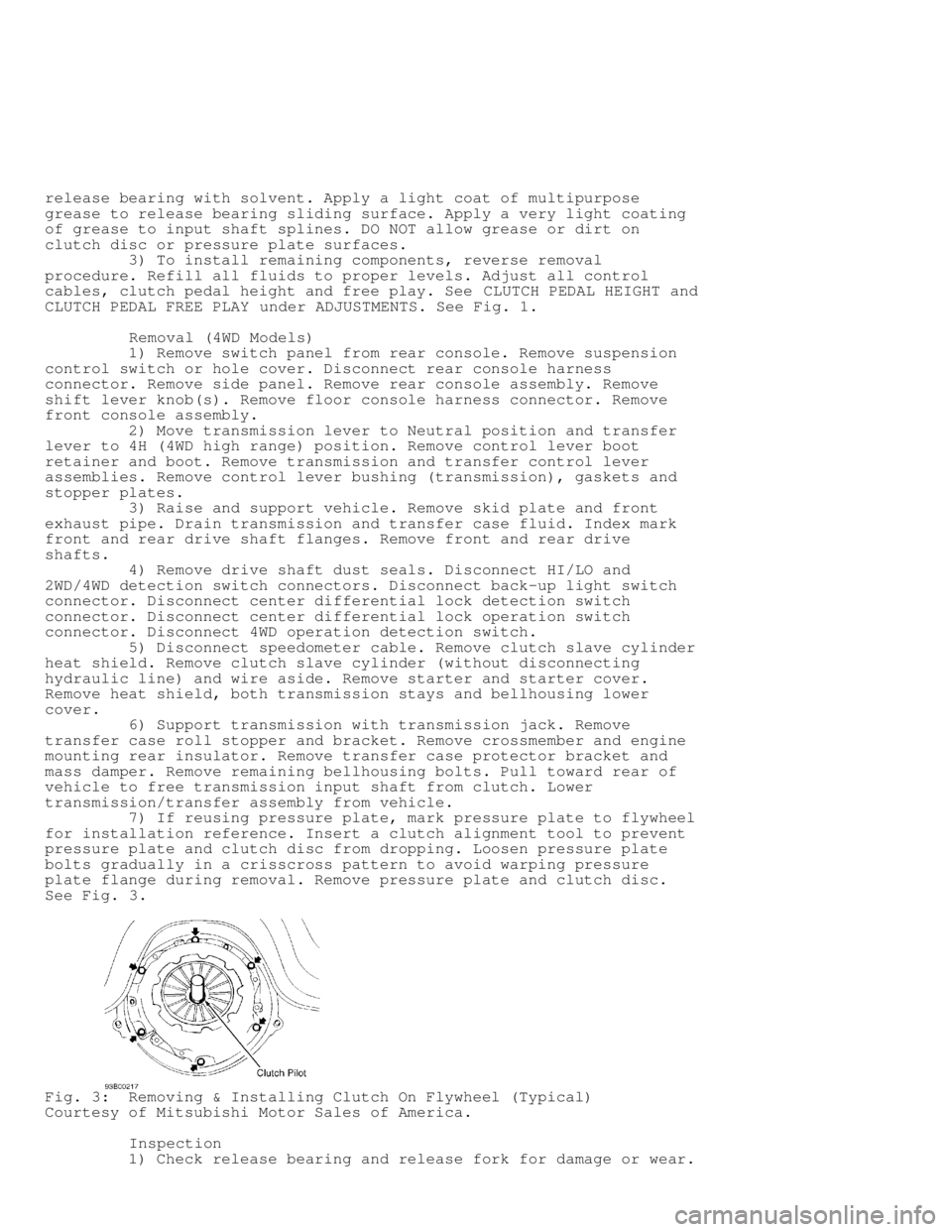
release bearing with solvent. Apply a light coat of multipurpose
grease to release bearing sliding surface. Apply a very light coating
of grease to input shaft splines. DO NOT allow grease or dirt on
clutch disc or pressure plate surfaces.
3) To install remaining components, reverse removal
procedure. Refill all fluids to proper levels. Adjust all control
cables, clutch pedal height and free play. See CLUTCH PEDAL HEIGHT and
CLUTCH PEDAL FREE PLAY under ADJUSTMENTS. See Fig. 1.
Removal (4WD Models)
1) Remove switch panel from rear console. Remove suspension
control switch or hole cover. Disconnect rear console harness
connector. Remove side panel. Remove rear console assembly. Remove
shift lever knob(s). Remove floor console harness connector. Remove
front console assembly.
2) Move transmission lever to Neutral position and transfer
lever to 4H (4WD high range) position. Remove control lever boot
retainer and boot. Remove transmission and transfer control lever
assemblies. Remove control lever bushing (transmission), gaskets and
stopper plates.
3) Raise and support vehicle. Remove skid plate and front
exhaust pipe. Drain transmission and transfer case fluid. Index mark
front and rear drive shaft flanges. Remove front and rear drive
shafts.
4) Remove drive shaft dust seals. Disconnect HI/LO and
2WD/4WD detection switch connectors. Disconnect back-up light switch
connector. Disconnect center differential lock detection switch
connector. Disconnect center differential lock operation switch
connector. Disconnect 4WD operation detection switch.
5) Disconnect speedometer cable. Remove clutch slave cylinder
heat shield. Remove clutch slave cylinder (without disconnecting
hydraulic line) and wire aside. Remove starter and starter cover.
Remove heat shield, both transmission stays and bellhousing lower
cover.
6) Support transmission with transmission jack. Remove
transfer case roll stopper and bracket. Remove crossmember and engine
mounting rear insulator. Remove transfer case protector bracket and
mass damper. Remove remaining bellhousing bolts. Pull toward rear of
vehicle to free transmission input shaft from clutch. Lower
transmission/transfer assembly from vehicle.
7) If reusing pressure plate, mark pressure plate to flywheel
for installation reference. Insert a clutch alignment tool to prevent
pressure plate and clutch disc from dropping. Loosen pressure plate
bolts gradually in a crisscross pattern to avoid warping pressure
plate flange during removal. Remove pressure plate and clutch disc.
See Fig. 3 .
Fig. 3: Removing & Installing Clutch On Flywheel (Typical)
Courtesy of Mitsubishi Motor Sales of America.
Inspection
1) Check release bearing and release fork for damage or wear.
Page 265 of 1501
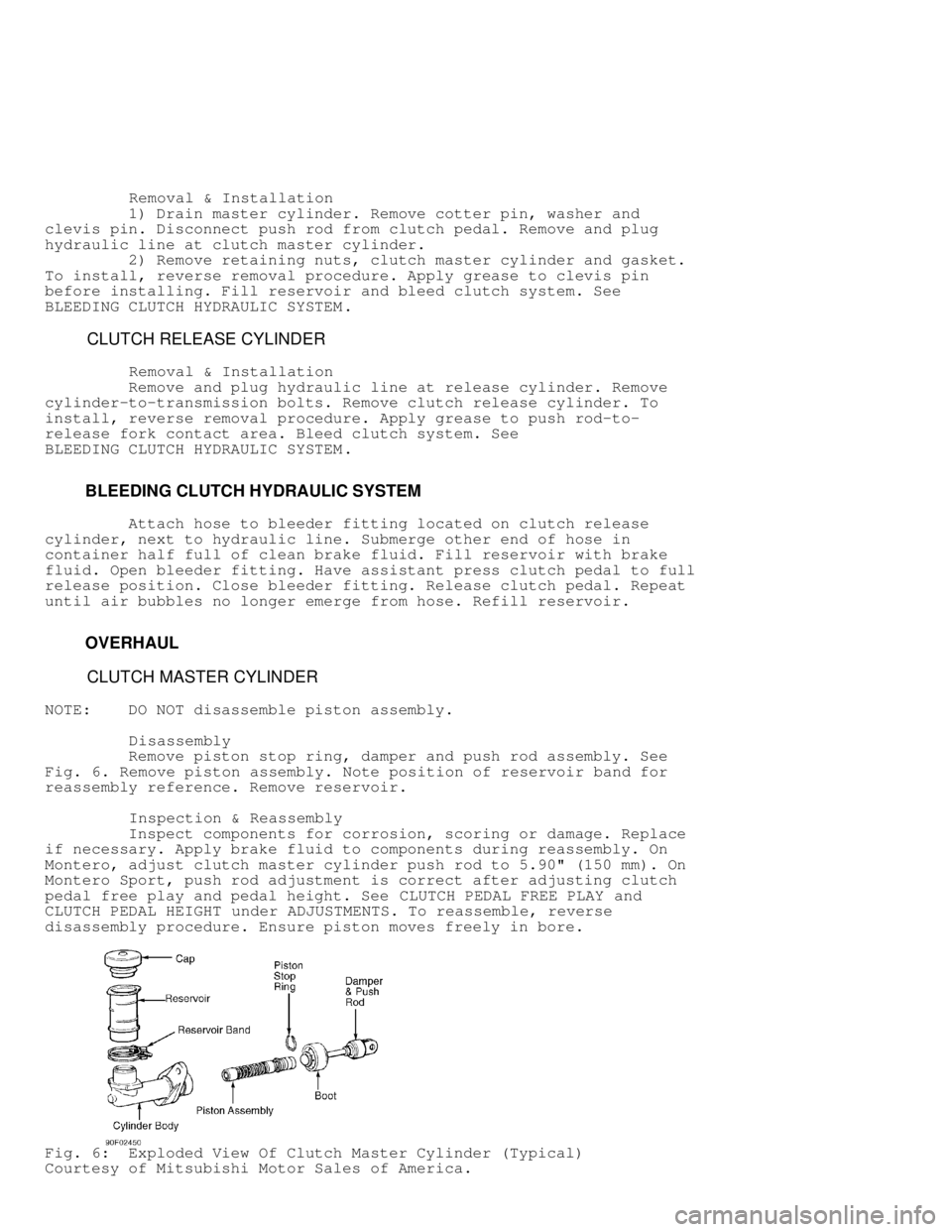
Removal & Installation
1) Drain master cylinder. Remove cotter pin, washer and
clevis pin. Disconnect push rod from clutch pedal. Remove and plug
hydraulic line at clutch master cylinder.
2) Remove retaining nuts, clutch master cylinder and gasket.
To install, reverse removal procedure. Apply grease to clevis pin
before installing. Fill reservoir and bleed clutch system. See
BLEEDING CLUTCH HYDRAULIC SYSTEM .
CLUTCH RELEASE CYLINDER
Removal & Installation
Remove and plug hydraulic line at release cylinder. Remove
cylinder-to-transmission bolts. Remove clutch release cylinder. To
install, reverse removal procedure. Apply grease to push rod-to-
release fork contact area. Bleed clutch system. See
BLEEDING CLUTCH HYDRAULIC SYSTEM .
BLEEDING CLUTCH HYDRAULIC SYSTEM
Attach hose to bleeder fitting located on clutch release
cylinder, next to hydraulic line. Submerge other end of hose in
container half full of clean brake fluid. Fill reservoir with brake
fluid. Open bleeder fitting. Have assistant press clutch pedal to full
release position. Close bleeder fitting. Release clutch pedal. Repeat
until air bubbles no longer emerge from hose. Refill reservoir.
OVERHAUL
CLUTCH MASTER CYLINDER
NOTE: DO NOT disassemble piston assembly.
Disassembly
Remove piston stop ring, damper and push rod assembly. See
Fig. 6 . Remove piston assembly. Note position of reservoir band for
reassembly reference. Remove reservoir.
Inspection & Reassembly
Inspect components for corrosion, scoring or damage. Replace
if necessary. Apply brake fluid to components during reassembly. On
Montero, adjust clutch master cylinder push rod to 5.90" (150 mm). On
Montero Sport, push rod adjustment is correct after adjusting clutch
pedal free play and pedal height. See CLUTCH PEDAL FREE PLAY and
CLUTCH PEDAL HEIGHT under ADJUSTMENTS. To reassemble, reverse
disassembly procedure. Ensure piston moves freely in bore.
Fig. 6: Exploded View Of Clutch Master Cylinder (Typical)
Courtesy of Mitsubishi Motor Sales of America.
Page 368 of 1501
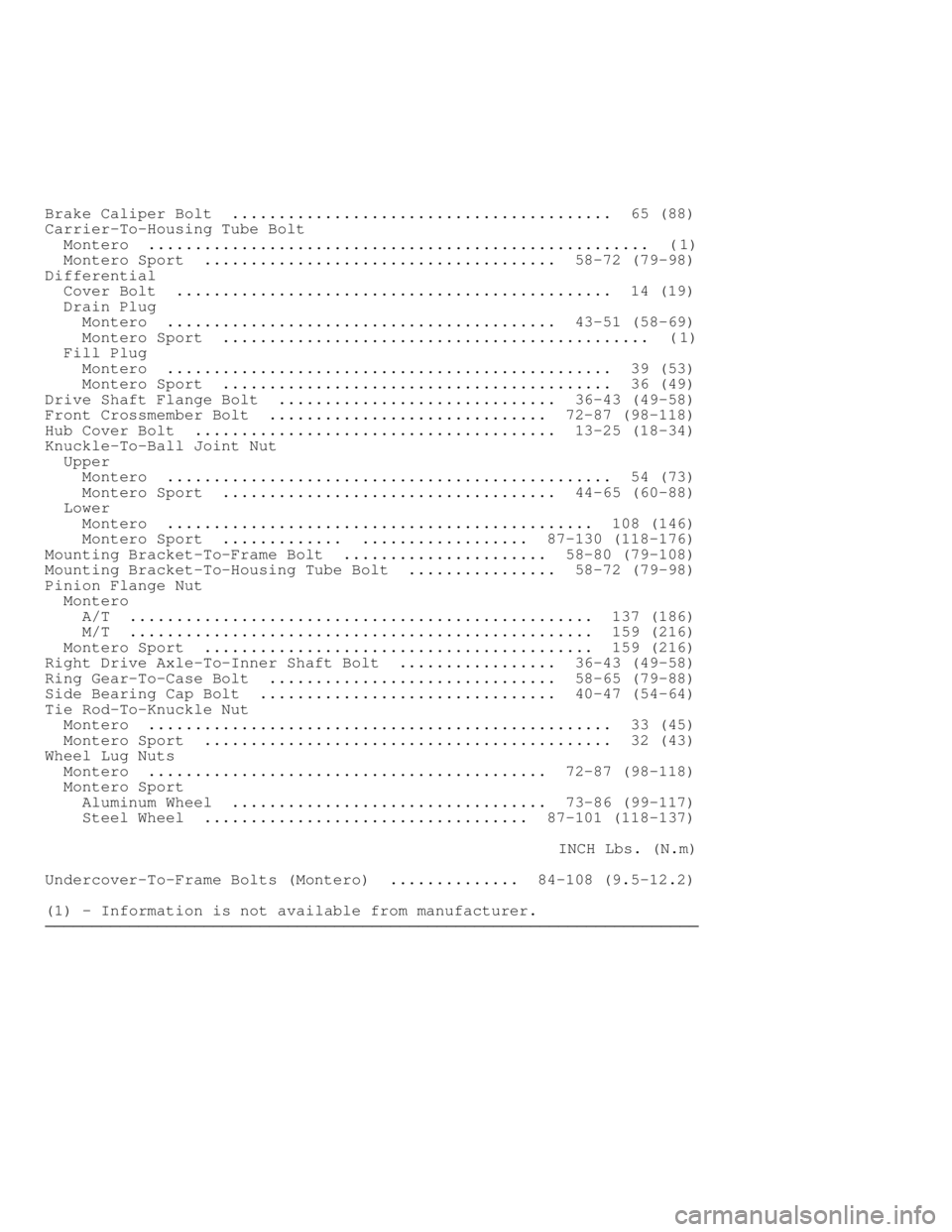
Brake Caliper Bolt ......................................... 65 (88)\
Carrier-To-Housing Tube Bolt
Montero ...................................................... (1)
Montero Sport ...................................... 58-72 (79-98)\
Differential
Cover Bolt ............................................... 14 (19)\
Drain Plug
Montero .......................................... 43-51 (58-69)\
Montero Sport .............................................. ( 1)
Fill Plug
Montero ................................................ 39 (53)\
Montero Sport .......................................... 36 (49)\
Drive Shaft Flange Bolt .............................. 36-43 (49-58)\
Front Crossmember Bolt .............................. 72-87 (98-118)\
Hub Cover Bolt ....................................... 13-25 (18-34)\
Knuckle-To-Ball Joint Nut
Upper
Montero ................................................ 54 (73)\
Montero Sport .................................... 44-65 (60-88)\
Lower
Montero .............................................. 108 (146)\
Montero Sport ............. .................. 87-130 (118-176)\
Mounting Bracket-To-Frame Bolt ...................... 58-80 (79-108)\
Mounting Bracket-To-Housing Tube Bolt ................ 58-72 (79-98)\
Pinion Flange Nut
Montero
A/T .................................................. 137 (186)\
M/T .................................................. 159 (216)\
Montero Sport .......................................... 159 (216)\
Right Drive Axle-To-Inner Shaft Bolt ................. 36-43 (49-58)\
Ring Gear-To-Case Bolt ............................... 58-65 (79-88)\
Side Bearing Cap Bolt ................................ 40-47 (54-64)\
Tie Rod-To-Knuckle Nut
Montero .................................................. 33 (45)\
Montero Sport ............................................ 32 (43)\
Wheel Lug Nuts
Montero ........................................... 72-87 (98-118)\
Montero Sport
Aluminum Wheel .................................. 73-86 (99-117)\
Steel Wheel ................................... 87-101 (118-137)\
INCH Lbs. (N.m)
Undercover-To-Frame Bolts (Montero) .............. 84-108 (9.5-12.2\
)
( 1) - Information is not available from manufacturer.
\
\
\
\
\
\
\
Page 373 of 1501
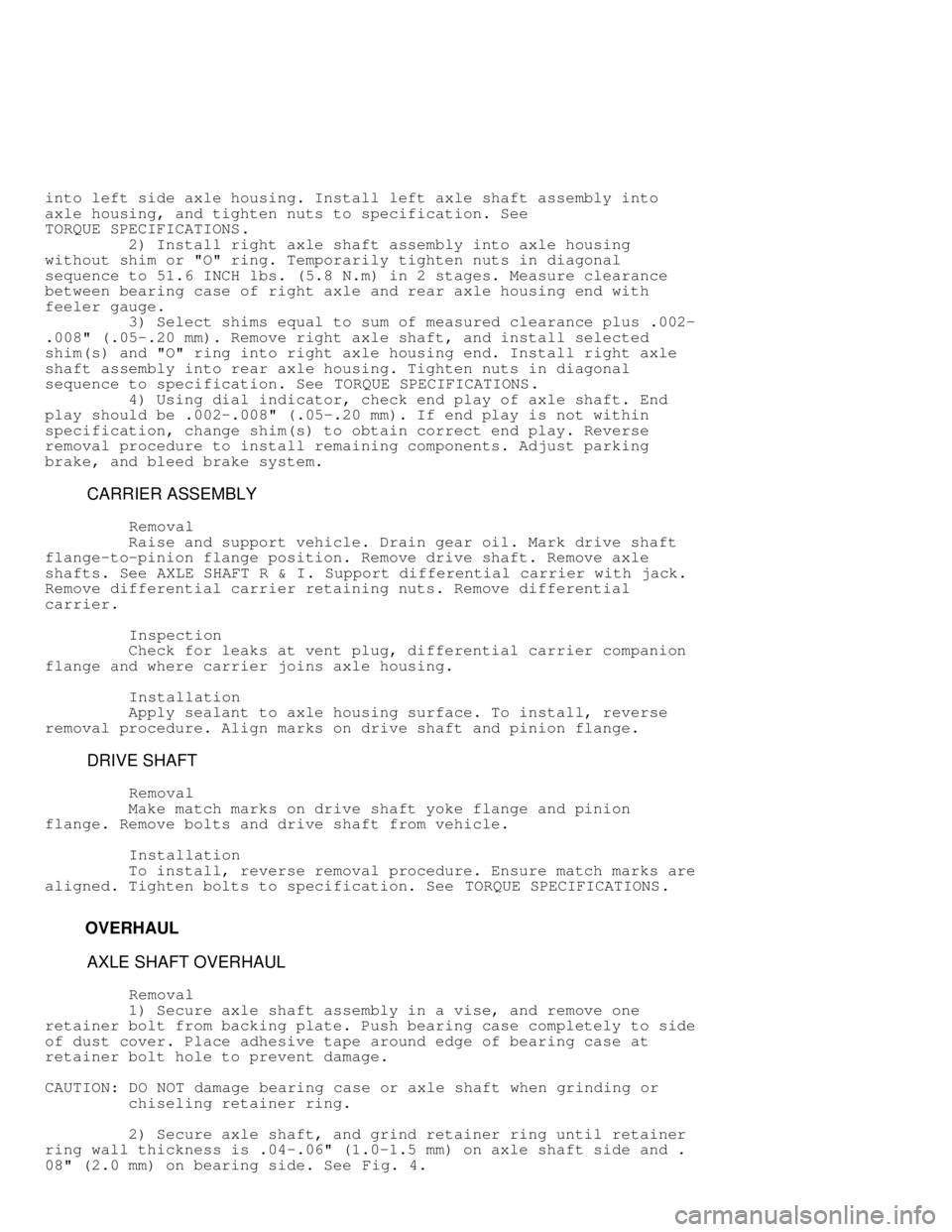
into left side axle housing. Install left axle shaft assembly into
axle housing, and tighten nuts to specification. See
TORQUE SPECIFICATIONS.
2) Install right axle shaft assembly into axle housing
without shim or "O" ring. Temporarily tighten nuts in diagonal
sequence to 51.6 INCH lbs. (5.8 N.m) in 2 stages. Measure clearance
between bearing case of right axle and rear axle housing end with
feeler gauge.
3) Select shims equal to sum of measured clearance plus .002-
.008" (.05-.20 mm). Remove right axle shaft, and install selected
shim(s) and "O" ring into right axle housing end. Install right axle
shaft assembly into rear axle housing. Tighten nuts in diagonal
sequence to specification. See TORQUE SPECIFICATIONS.
4) Using dial indicator, check end play of axle shaft. End
play should be .002-.008" (.05-.20 mm). If end play is not within
specification, change shim(s) to obtain correct end play. Reverse
removal procedure to install remaining components. Adjust parking
brake, and bleed brake system.
CARRIER ASSEMBLY
Removal
Raise and support vehicle. Drain gear oil. Mark drive shaft
flange-to-pinion flange position. Remove drive shaft. Remove axle
shafts. See AXLE SHAFT R & I . Support differential carrier with jack.
Remove differential carrier retaining nuts. Remove differential
carrier.
Inspection
Check for leaks at vent plug, differential carrier companion
flange and where carrier joins axle housing.
Installation
Apply sealant to axle housing surface. To install, reverse
removal procedure. Align marks on drive shaft and pinion flange.
DRIVE SHAFT
Removal
Make match marks on drive shaft yoke flange and pinion
flange. Remove bolts and drive shaft from vehicle.
Installation
To install, reverse removal procedure. Ensure match marks are
aligned. Tighten bolts to specification. See TORQUE SPECIFICATIONS.
OVERHAUL
AXLE SHAFT OVERHAUL
Removal
1) Secure axle shaft assembly in a vise, and remove one
retainer bolt from backing plate. Push bearing case completely to side
of dust cover. Place adhesive tape around edge of bearing case at
retainer bolt hole to prevent damage.
CAUTION: DO NOT damage bearing case or axle shaft when grinding or
chiseling retainer ring.
2) Secure axle shaft, and grind retainer ring until retainer
ring wall thickness is .04-.06" (1.0-1.5 mm) on axle shaft side and .
08" (2.0 mm) on bearing side. See Fig. 4.
Page 388 of 1501
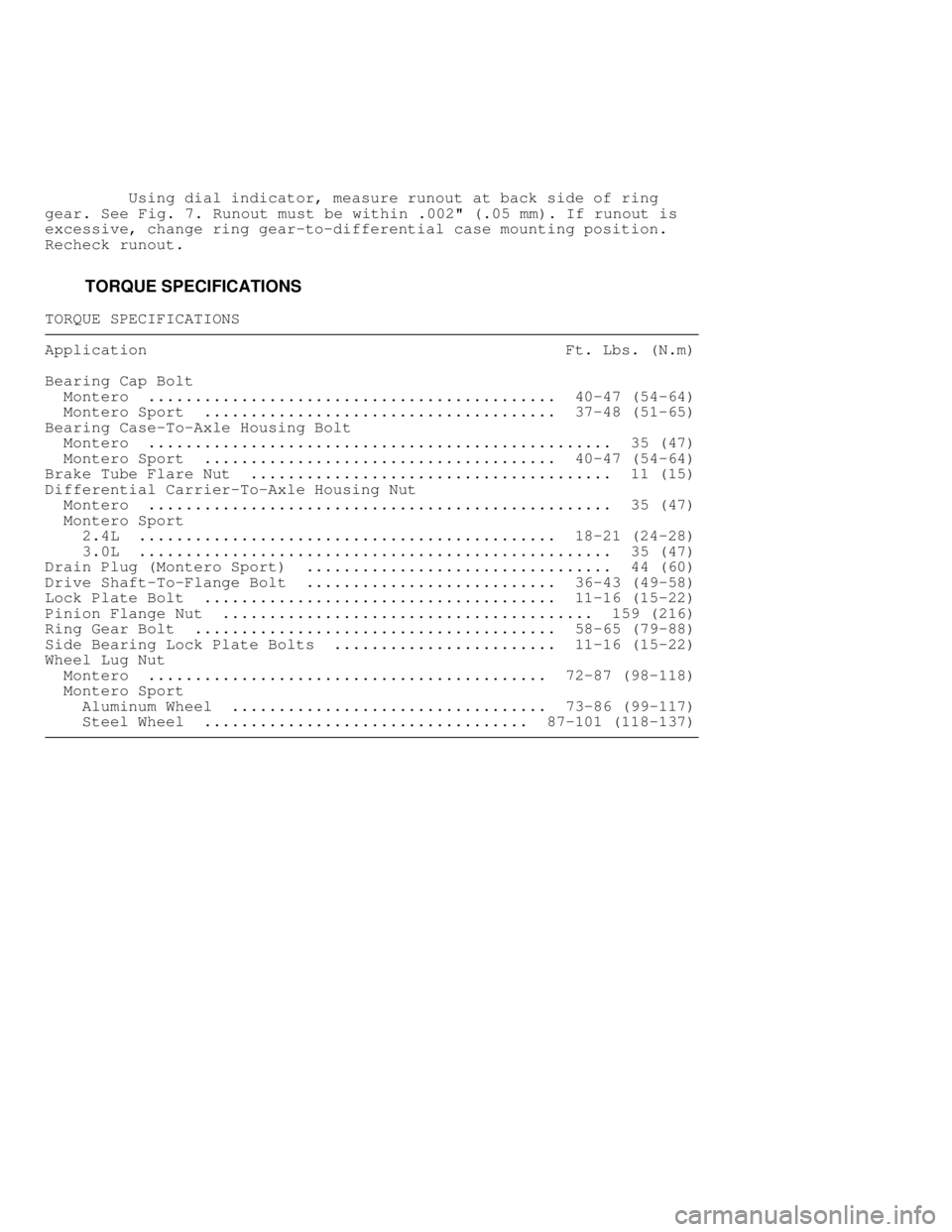
Using dial indicator, measure runout at back side of ring
gear. See Fig. 7. Runout must be within .002" (.05 mm). If runout is
excessive, change ring gear-to-differential case mounting position.
Recheck runout.
TORQUE SPECIFICATIONS
TORQUE SPECIFICATIONS \
\
\
\
\
\
\
Application Ft. Lbs. (N.m)\
Bearing Cap Bolt
Montero ............................................ 40-47 (54-64)\
Montero Sport ...................................... 37-48 (51-65)\
Bearing Case-To-Axle Housing Bolt
Montero .................................................. 35 (47)\
Montero Sport ...................................... 40-47 (54-64)\
Brake Tube Flare Nut ....................................... 11 (15)\
Differential Carrier-To-Axle Housing Nut
Montero .................................................. 35 (47)\
Montero Sport
2.4L ............................................. 18-21 (24-28)\
3.0L ................................................... 35 (47)\
Drain Plug (Montero Sport) ................................. 44 (60\
)
Drive Shaft-To-Flange Bolt ........................... 36-43 (49-58)\
Lock Plate Bolt ...................................... 11-16 (15-22)\
Pinion Flange Nut ........................................ 159 (216)\
Ring Gear Bolt ....................................... 58-65 (79-88)\
Side Bearing Lock Plate Bolts ........................ 11-16 (15-22)\
Wheel Lug Nut
Montero ........................................... 72-87 (98-118)\
Montero Sport
Aluminum Wheel .................................. 73-86 (99-117)\
Steel Wheel ................................... 87-101 (118-137)\
\
\
\
\
\
\
\
Page 700 of 1501
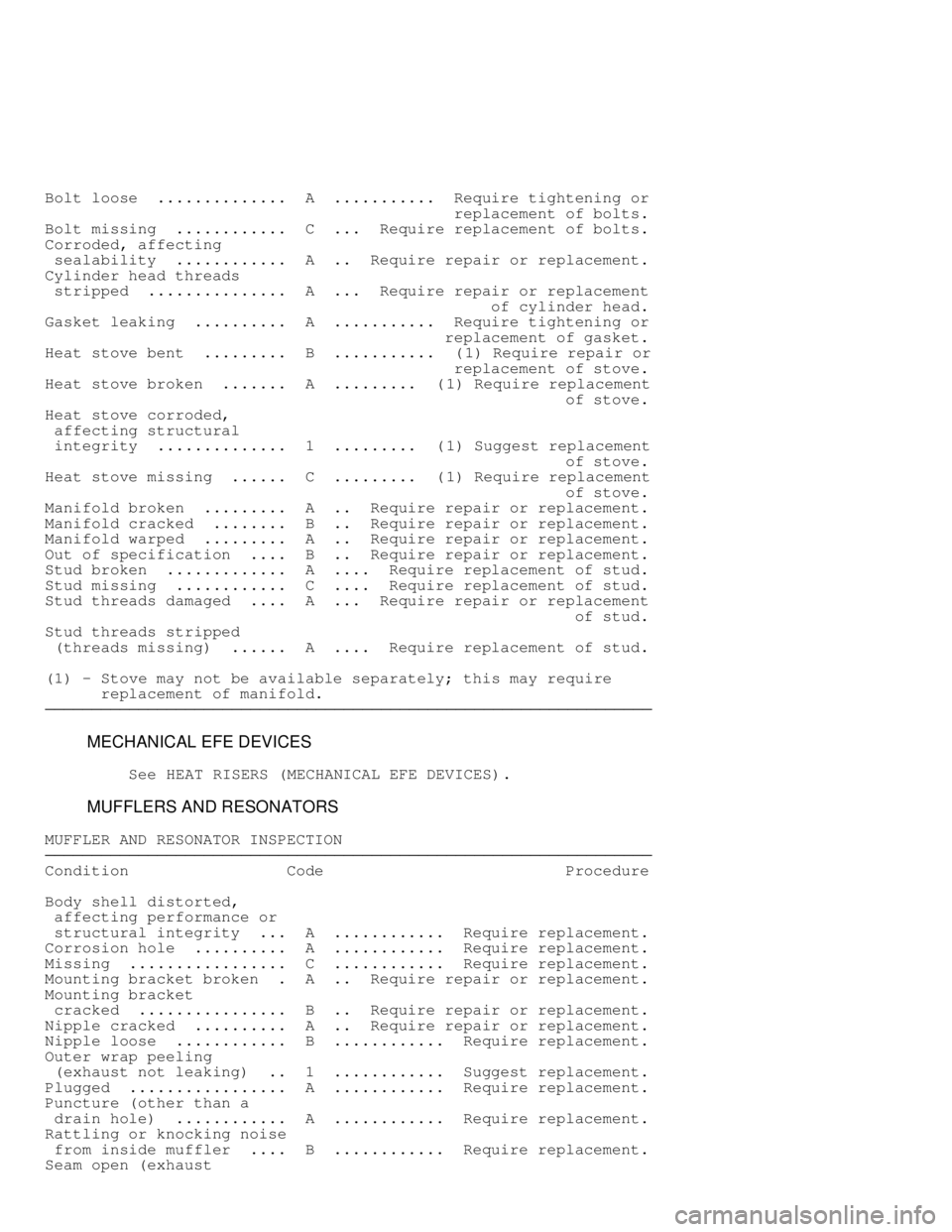
Bolt loose .............. A ........... Require tightening or
replacement of bolts.
Bolt missing ............ C ... Require replacement of bolts.
Corroded, affecting
sealability ............ A .. Require repair or replacement.
Cylinder head threads
stripped ............... A ... Require repair or replacement
of cylinder head.
Gasket leaking .......... A ........... Require tightening or
replacement of gasket.
Heat stove bent ......... B ........... (1) Require repair or
replacement of stove.
Heat stove broken ....... A ......... ( 1) Require replacement
of stove.
Heat stove corroded,
affecting structural
integrity .............. 1 ......... ( 1) Suggest replacement
of stove.
Heat stove missing ...... C ......... ( 1) Require replacement
of stove.
Manifold broken ......... A .. Require repair or replacement.
Manifold cracked ........ B .. Require repair or replacement.
Manifold warped ......... A .. Require repair or replacement.
Out of specification .... B .. Require repair or replacement.
Stud broken ............. A .... Require replacement of stud.
Stud missing ............ C .... Require replacement of stud.
Stud threads damaged .... A ... Require repair or replacement
of stud.
Stud threads stripped
(threads missing) ...... A .... Require replacement of stud.
( 1) - Stove may not be available separately; this may require
replacement of manifold.
\
\
\
\
\
\
\
MECHANICAL EFE DEVICES
See HEAT RISERS (MECHANICAL EFE DEVICES) .
MUFFLERS AND RESONATORS
MUFFLER AND RESONATOR INSPECTION \
\
\
\
\
\
\
Condition Code Procedure
Body shell distorted,
affecting performance or
structural integrity ... A ............ Require replacement.
Corrosion hole .......... A ............ Require replacement.
Missing ................. C ............ Require replacement.
Mounting bracket broken . A .. Require repair or replacement.
Mounting bracket
cracked ................ B .. Require repair or replacement.
Nipple cracked .......... A .. Require repair or replacement.
Nipple loose ............ B ............ Require replacement.
Outer wrap peeling
(exhaust not leaking) .. 1 ............ Suggest replacement.
Plugged ................. A ............ Require replacement.
Puncture (other than a
drain hole) ............ A ............ Require replacement.
Rattling or knocking noise
from inside muffler .... B ............ Require replacement.
Seam open (exhaust