lug pattern MITSUBISHI MONTERO 1998 Service Manual
[x] Cancel search | Manufacturer: MITSUBISHI, Model Year: 1998, Model line: MONTERO, Model: MITSUBISHI MONTERO 1998Pages: 1501, PDF Size: 25.81 MB
Page 575 of 1501
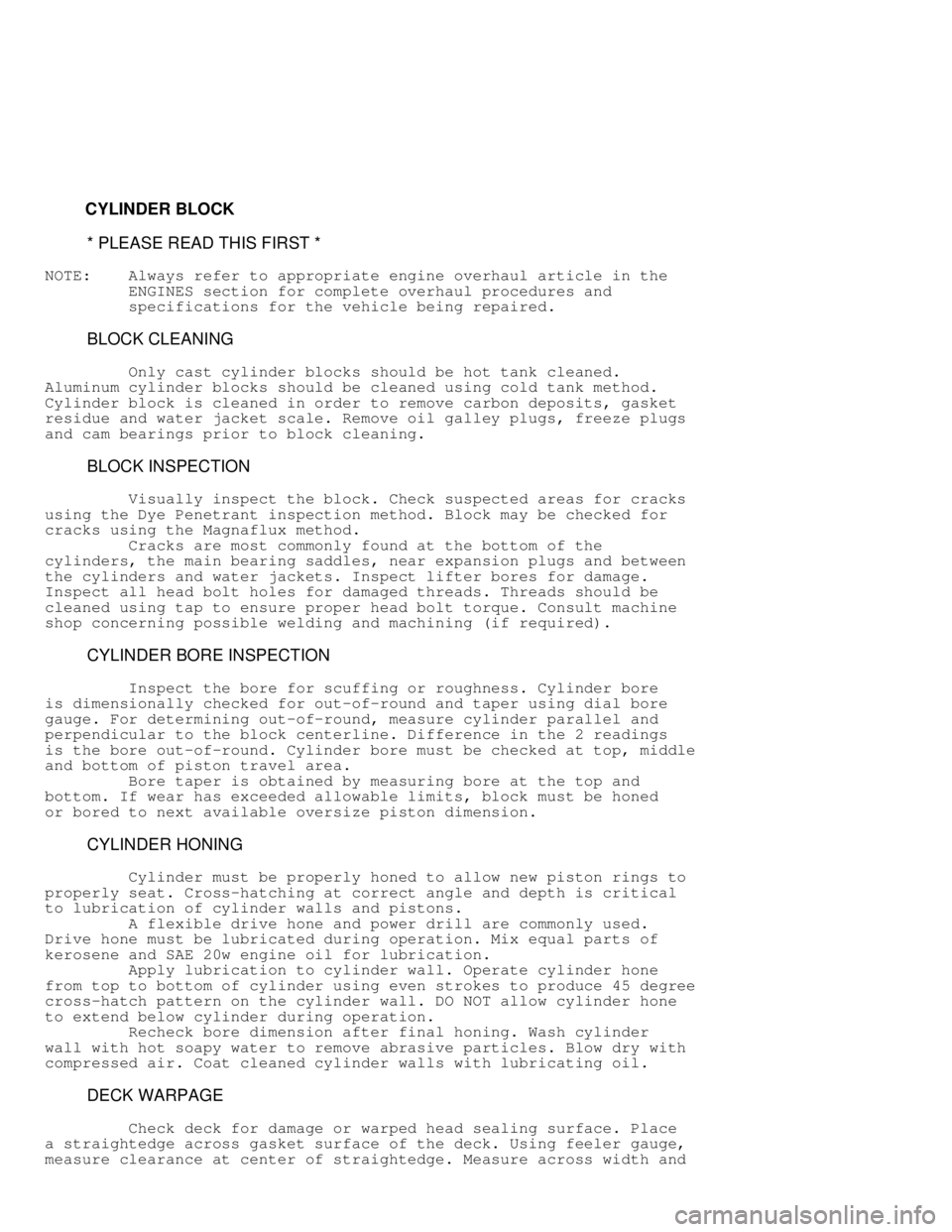
CYLINDER BLOCK
* PLEASE READ THIS FIRST *
NOTE: Always refer to appropriate engine overhaul article in the
ENGINES section for complete overhaul procedures and
specifications for the vehicle being repaired.
BLOCK CLEANING
Only cast cylinder blocks should be hot tank cleaned.
Aluminum cylinder blocks should be cleaned using cold tank method.
Cylinder block is cleaned in order to remove carbon deposits, gasket
residue and water jacket scale. Remove oil galley plugs, freeze plugs
and cam bearings prior to block cleaning.
BLOCK INSPECTION
Visually inspect the block. Check suspected areas for cracks
using the Dye Penetrant inspection method. Block may be checked for
cracks using the Magnaflux method.
Cracks are most commonly found at the bottom of the
cylinders, the main bearing saddles, near expansion plugs and between
the cylinders and water jackets. Inspect lifter bores for damage.
Inspect all head bolt holes for damaged threads. Threads should be
cleaned using tap to ensure proper head bolt torque. Consult machine
shop concerning possible welding and machining (if required).
CYLINDER BORE INSPECTION
Inspect the bore for scuffing or roughness. Cylinder bore
is dimensionally checked for out-of-round and taper using dial bore
gauge. For determining out-of-round, measure cylinder parallel and
perpendicular to the block centerline. Difference in the 2 readings
is the bore out-of-round. Cylinder bore must be checked at top, middle
and bottom of piston travel area.
Bore taper is obtained by measuring bore at the top and
bottom. If wear has exceeded allowable limits, block must be honed
or bored to next available oversize piston dimension.
CYLINDER HONING
Cylinder must be properly honed to allow new piston rings to
properly seat. Cross-hatching at correct angle and depth is critical
to lubrication of cylinder walls and pistons.
A flexible drive hone and power drill are commonly used.
Drive hone must be lubricated during operation. Mix equal parts of
kerosene and SAE 20w engine oil for lubrication.
Apply lubrication to cylinder wall. Operate cylinder hone
from top to bottom of cylinder using even strokes to produce 45 degree
cross-hatch pattern on the cylinder wall. DO NOT allow cylinder hone
to extend below cylinder during operation.
Recheck bore dimension after final honing. Wash cylinder
wall with hot soapy water to remove abrasive particles. Blow dry with
compressed air. Coat cleaned cylinder walls with lubricating oil.
DECK WARPAGE
Check deck for damage or warped head sealing surface. Place
a straightedge across gasket surface of the deck. Using feeler gauge,
measure clearance at center of straightedge. Measure across width and
Page 756 of 1501
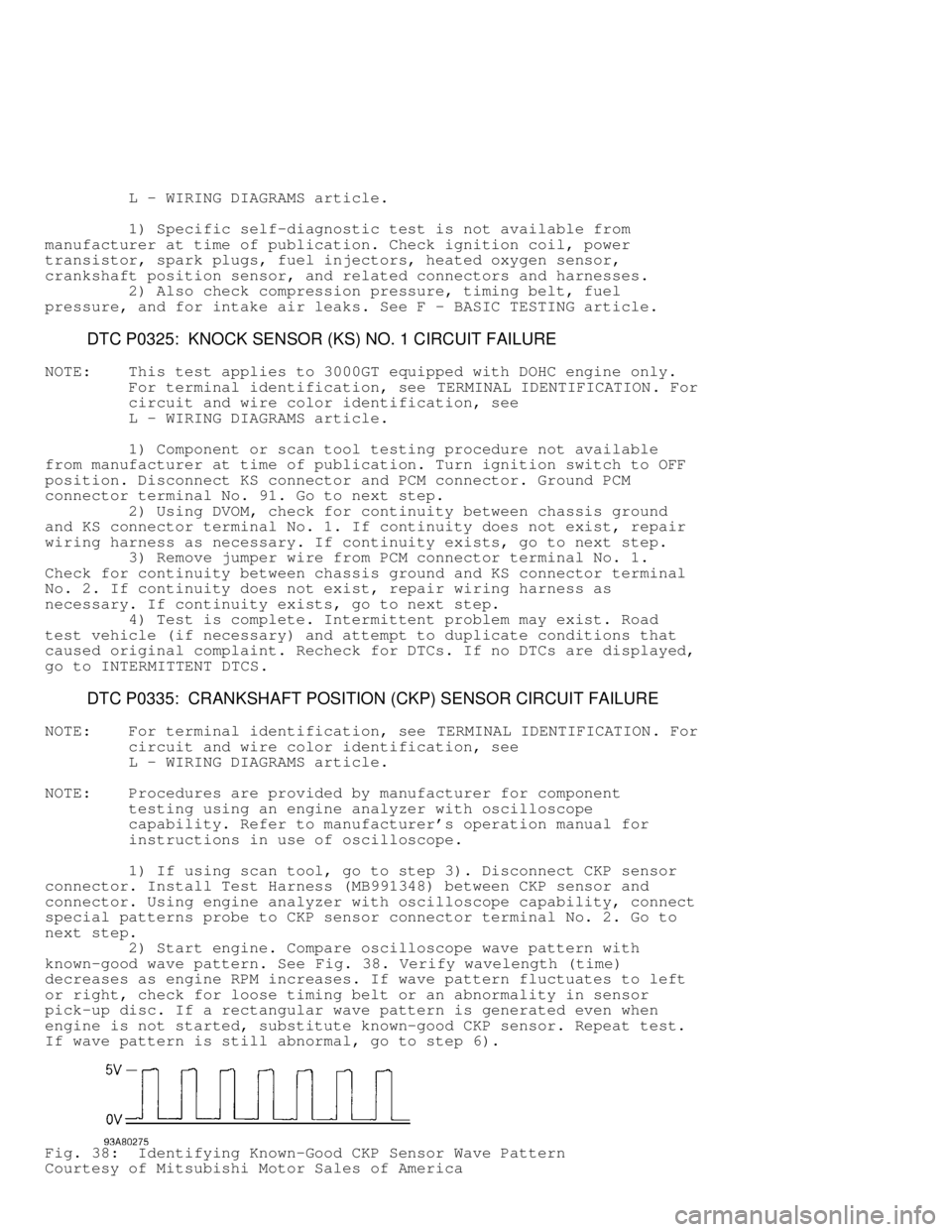
L - WIRING DIAGRAMS article.
1) Specific self-diagnostic test is not available from
manufacturer at time of publication. Check ignition coil, power
transistor, spark plugs, fuel injectors, heated oxygen sensor,
crankshaft position sensor, and related connectors and harnesses.
2) Also check compression pressure, timing belt, fuel
pressure, and for intake air leaks. See F - BASIC TESTING article.
DTC P0325: KNOCK SENSOR (KS) NO. 1 CIRCUIT FAILURE
NOTE: This test applies to 3000GT equipped with DOHC engine only.
For terminal identification, see TERMINAL IDENTIFICATION. For
circuit and wire color identification, see
L - WIRING DIAGRAMS article.
1) Component or scan tool testing procedure not available
from manufacturer at time of publication. Turn ignition switch to OFF
position. Disconnect KS connector and PCM connector. Ground PCM
connector terminal No. 91. Go to next step.
2) Using DVOM, check for continuity between chassis ground
and KS connector terminal No. 1. If continuity does not exist, repair
wiring harness as necessary. If continuity exists, go to next step.
3) Remove jumper wire from PCM connector terminal No. 1.
Check for continuity between chassis ground and KS connector terminal
No. 2. If continuity does not exist, repair wiring harness as
necessary. If continuity exists, go to next step.
4) Test is complete. Intermittent problem may exist. Road
test vehicle (if necessary) and attempt to duplicate conditions that
caused original complaint. Recheck for DTCs. If no DTCs are displayed,
go to INTERMITTENT DTCS .
DTC P0335: CRANKSHAFT POSITION (CKP) SENSOR CIRCUIT FAILURE
NOTE: For terminal identification, see TERMINAL IDENTIFICATION. For
circuit and wire color identification, see
L - WIRING DIAGRAMS article.
NOTE: Procedures are provided by manufacturer for component
testing using an engine analyzer with oscilloscope
capability. Refer to manufacturer's operation manual for
instructions in use of oscilloscope.
1) If using scan tool, go to step 3). Disconnect CKP sensor
connector. Install Test Harness (MB991348) between CKP sensor and
connector. Using engine analyzer with oscilloscope capability, connect
special patterns probe to CKP sensor connector terminal No. 2. Go to
next step.
2) Start engine. Compare oscilloscope wave pattern with
known-good wave pattern. See Fig. 38. Verify wavelength (time)
decreases as engine RPM increases. If wave pattern fluctuates to left
or right, check for loose timing belt or an abnormality in sensor
pick-up disc. If a rectangular wave pattern is generated even when
engine is not started, substitute known-good CKP sensor. Repeat test.
If wave pattern is still abnormal, go to step 6).
Fig. 38: Identifying Known-Good CKP Sensor Wave Pattern
Courtesy of Mitsubishi Motor Sales of America