width MITSUBISHI MONTERO 1998 Service Manual
[x] Cancel search | Manufacturer: MITSUBISHI, Model Year: 1998, Model line: MONTERO, Model: MITSUBISHI MONTERO 1998Pages: 1501, PDF Size: 25.81 MB
Page 17 of 1501
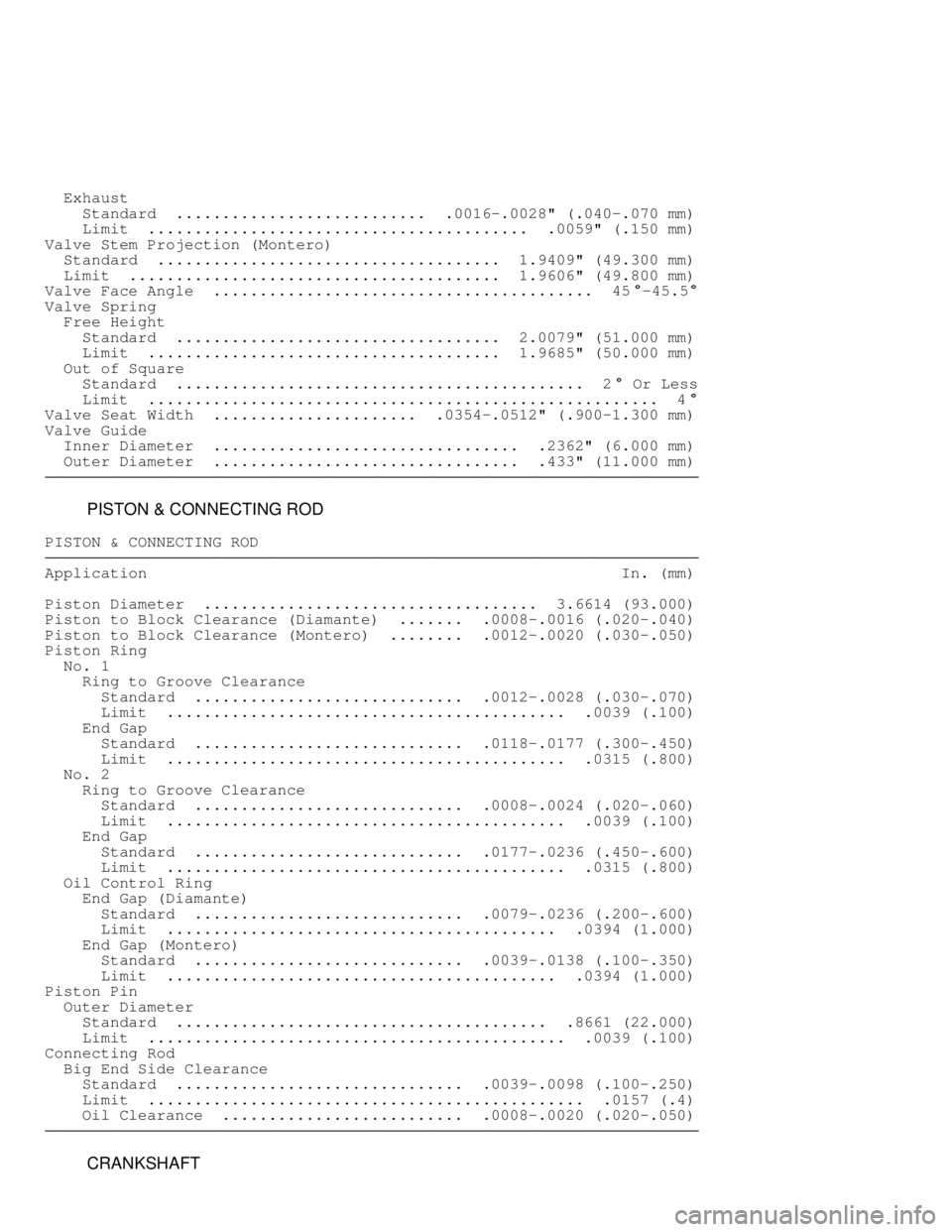
Exhaust
Standard ........................... .0016-.0028" (.040-.070 mm)\
Limit ......................................... .0059" (.150 mm)\
Valve Stem Projection (Montero)
Standard ..................................... 1.9409" (49.300 mm)\
Limit ........................................ 1.9606" (49.800 mm)\
Valve Face Angle ......................................... 45
-45.5Valve Spring
Free Height
Standard ................................... 2.0079" (51.000 mm)\
Limit ...................................... 1.9685" (50.000 mm)\
Out of Square
Standard ............................................ 2
Or Less
Limit ....................................................... 4Valve Seat Width ...................... .0354-.0512" (.900-1.300 mm)\
Valve Guide
Inner Diameter ................................. .2362" (6.000 mm)\
Outer Diameter ................................. .433" (11.000 mm)\
\
\
\
\
\
\
\
PISTON & CONNECTING ROD
PISTON & CONNECTING ROD\
\
\
\
\
\
\
Application In. (mm)\
Piston Diameter .................................... 3.6614 (93.000)\
Piston to Block Clearance (Diamante) ....... .0008-.0016 (.020-.040\
)
Piston to Block Clearance (Montero) ........ .0012-.0020 (.030-.050\
)
Piston Ring
No. 1
Ring to Groove Clearance
Standard ............................. .0012-.0028 (.030-.070)\
Limit ........................................... .0039 (.100)\
End Gap
Standard ............................. .0118-.0177 (.300-.450)\
Limit ........................................... .0315 (.800)\
No. 2
Ring to Groove Clearance
Standard ............................. .0008-.0024 (.020-.060)\
Limit ........................................... .0039 (.100)\
End Gap
Standard ............................. .0177-.0236 (.450-.600)\
Limit ........................................... .0315 (.800)\
Oil Control Ring
End Gap (Diamante)
Standard ............................. .0079-.0236 (.200-.600)\
Limit .......................................... .0394 (1.000)\
End Gap (Montero)
Standard ............................. .0039-.0138 (.100-.350)\
Limit .......................................... .0394 (1.000)\
Piston Pin
Outer Diameter
Standard ........................................ .8661 (22.000)\
Limit ............................................. .0039 (.100)\
Connecting Rod
Big End Side Clearance
Standard ............................... .0039-.0098 (.100-.250)\
Limit ............................................... .0157 (.4)\
Oil Clearance .......................... .0008-.0020 (.020-.050)\
\
\
\
\
\
\
\
CRANKSHAFT
Page 127 of 1501
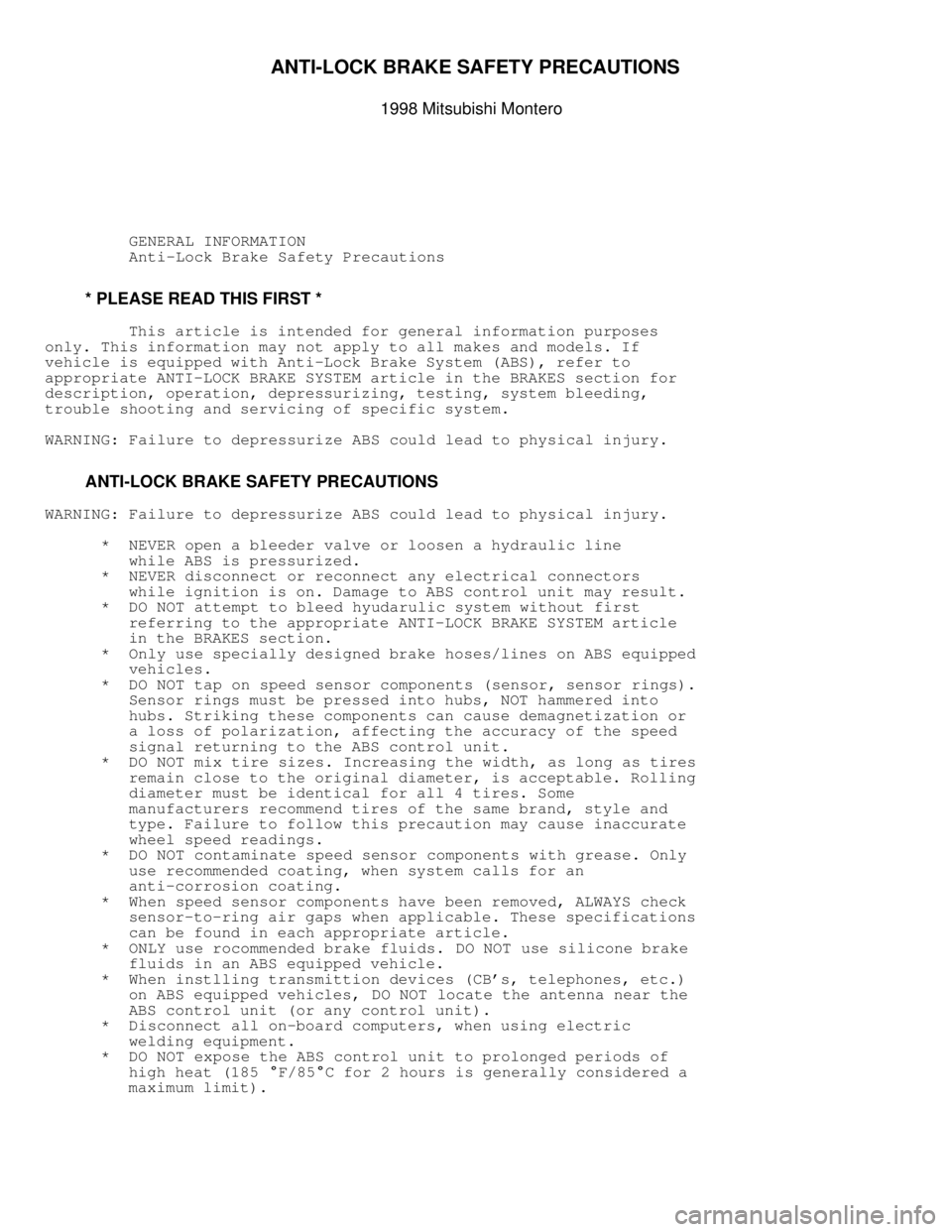
ANTI-LOCK BRAKE SAFETY PRECAUTIONS
1998 Mitsubishi Montero
GENERAL INFORMATION
Anti-Lock Brake Safety Precautions
* PLEASE READ THIS FIRST *
This article is intended for general information purposes
only. This information may not apply to all makes and models. If
vehicle is equipped with Anti-Lock Brake System (ABS), refer to
appropriate ANTI-LOCK BRAKE SYSTEM article in the BRAKES section for
description, operation, depressurizing, testing, system bleeding,
trouble shooting and servicing of specific system.
WARNING: Failure to depressurize ABS could lead to physical injury.
ANTI-LOCK BRAKE SAFETY PRECAUTIONS
WARNING: Failure to depressurize ABS could lead to physical injury.
* NEVER open a bleeder valve or loosen a hydraulic line
while ABS is pressurized.
* NEVER disconnect or reconnect any electrical connectors
while ignition is on. Damage to ABS control unit may result.
* DO NOT attempt to bleed hyudarulic system without first
referring to the appropriate ANTI-LOCK BRAKE SYSTEM article
in the BRAKES section.
* Only use specially designed brake hoses/lines on ABS equipped
vehicles.
* DO NOT tap on speed sensor components (sensor, sensor rings).
Sensor rings must be pressed into hubs, NOT hammered into
hubs. Striking these components can cause demagnetization or
a loss of polarization, affecting the accuracy of the speed
signal returning to the ABS control unit.
* DO NOT mix tire sizes. Increasing the width, as long as tires
remain close to the original diameter, is acceptable. Rolling
diameter must be identical for all 4 tires. Some
manufacturers recommend tires of the same brand, style and
type. Failure to follow this precaution may cause inaccurate
wheel speed readings.
* DO NOT contaminate speed sensor components with grease. Only
use recommended coating, when system calls for an
anti-corrosion coating.
* When speed sensor components have been removed, ALWAYS check
sensor-to-ring air gaps when applicable. These specifications
can be found in each appropriate article.
* ONLY use rocommended brake fluids. DO NOT use silicone brake
fluids in an ABS equipped vehicle.
* When instlling transmittion devices (CB's, telephones, etc.)
on ABS equipped vehicles, DO NOT locate the antenna near the
ABS control unit (or any control unit).
* Disconnect all on-board computers, when using electric
welding equipment.
* DO NOT expose the ABS control unit to prolonged periods of
high heat (185
F/85 C for 2 hours is generally considered a
maximum limit).
Page 381 of 1501
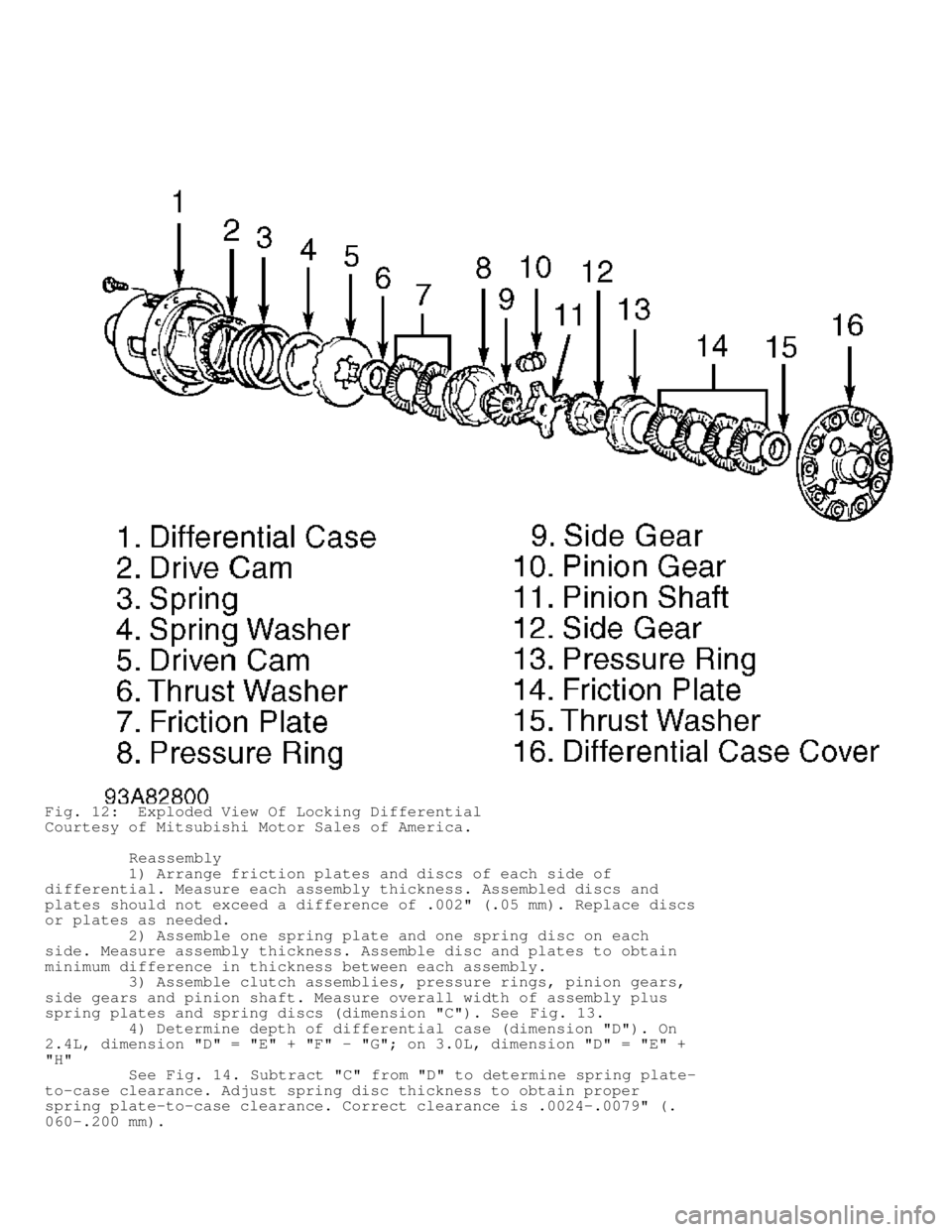
Fig. 12: Exploded View Of Locking Differential
Courtesy of Mitsubishi Motor Sales of America.
Reassembly
1) Arrange friction plates and discs of each side of
differential. Measure each assembly thickness. Assembled discs and
plates should not exceed a difference of .002" (.05 mm). Replace discs\
or plates as needed.
2) Assemble one spring plate and one spring disc on each
side. Measure assembly thickness. Assemble disc and plates to obtain
minimum difference in thickness between each assembly.
3) Assemble clutch assemblies, pressure rings, pinion gears,
side gears and pinion shaft. Measure overall width of assembly plus
spring plates and spring discs (dimension "C"). See Fig. 13.
4) Determine depth of differential case (dimension "D"). On
2.4L, dimension "D" = "E" + "F" - "G"; on 3.0L, dimension "D" = "E" +
"H"
See Fig. 14. Subtract "C" from "D" to determine spring plate-
to-case clearance. Adjust spring disc thickness to obtain proper
spring plate-to-case clearance. Correct clearance is .0024-.0079" (.
060-.200 mm).
Page 382 of 1501
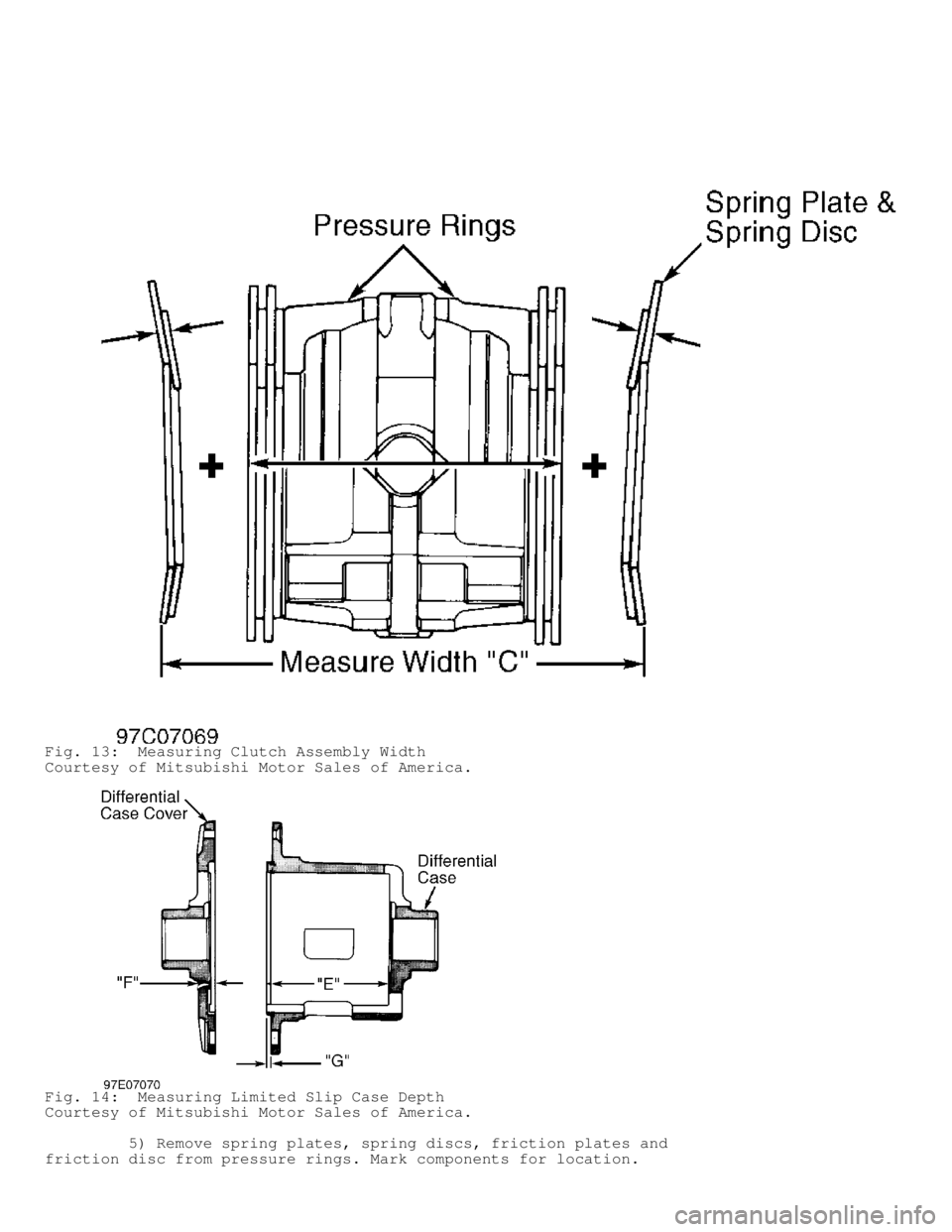
Fig. 13: Measuring Clutch Assembly Width
Courtesy of Mitsubishi Motor Sales of America.
Fig. 14: Measuring Limited Slip Case Depth
Courtesy of Mitsubishi Motor Sales of America.
5) Remove spring plates, spring discs, friction plates and
friction disc from pressure rings. Mark components for location.
Page 383 of 1501
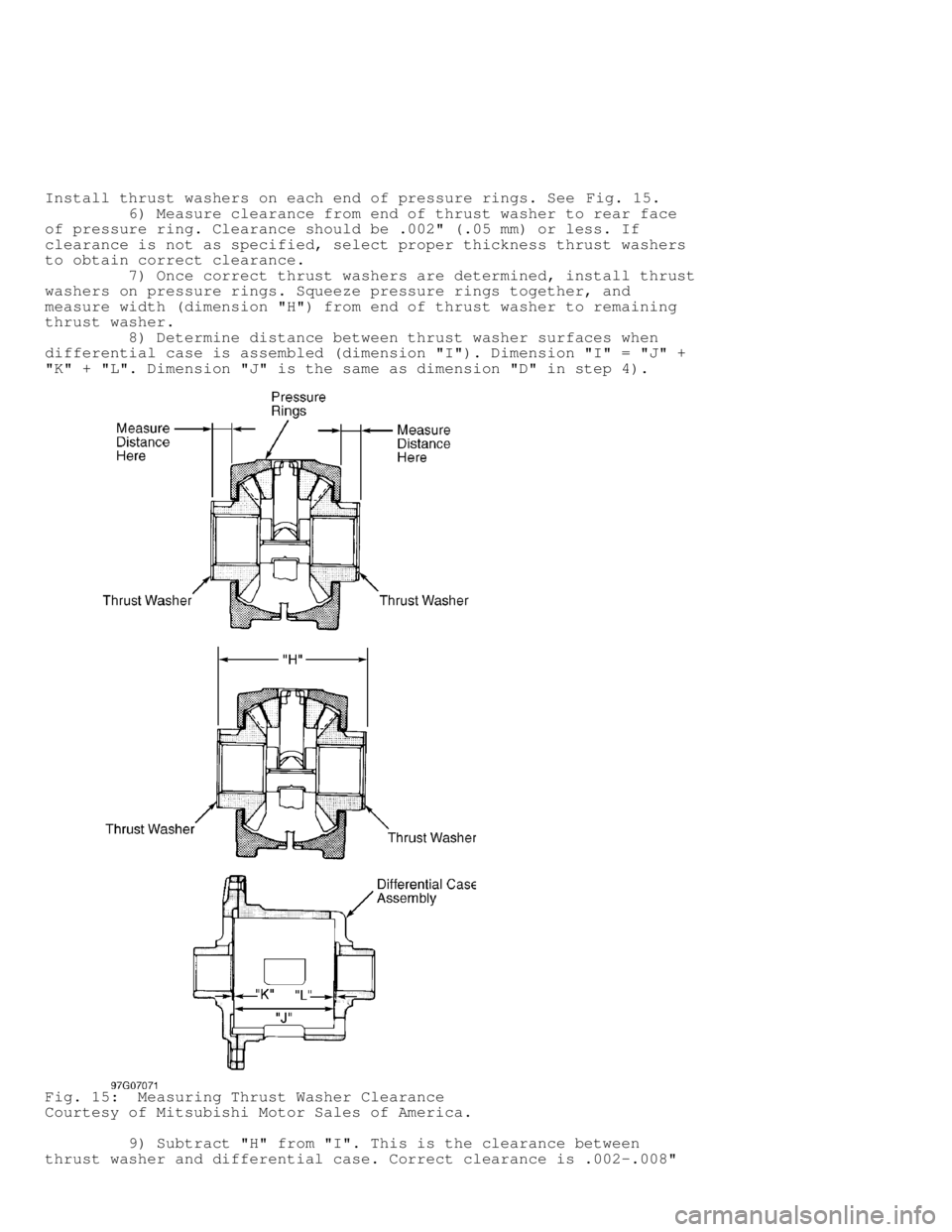
Install thrust washers on each end of pressure rings. See Fig. 15.
6) Measure clearance from end of thrust washer to rear face
of pressure ring. Clearance should be .002" (.05 mm) or less. If
clearance is not as specified, select proper thickness thrust washers
to obtain correct clearance.
7) Once correct thrust washers are determined, install thrust
washers on pressure rings. Squeeze pressure rings together, and
measure width (dimension "H") from end of thrust washer to remaining
thrust washer.
8) Determine distance between thrust washer surfaces when
differential case is assembled (dimension "I"). Dimension "I" = "J" +
"K" + "L". Dimension "J" is the same as dimension "D" in step 4).
Fig. 15: Measuring Thrust Washer Clearance
Courtesy of Mitsubishi Motor Sales of America.
9) Subtract "H" from "I". This is the clearance between
thrust washer and differential case. Correct clearance is .002-.008"
Page 460 of 1501
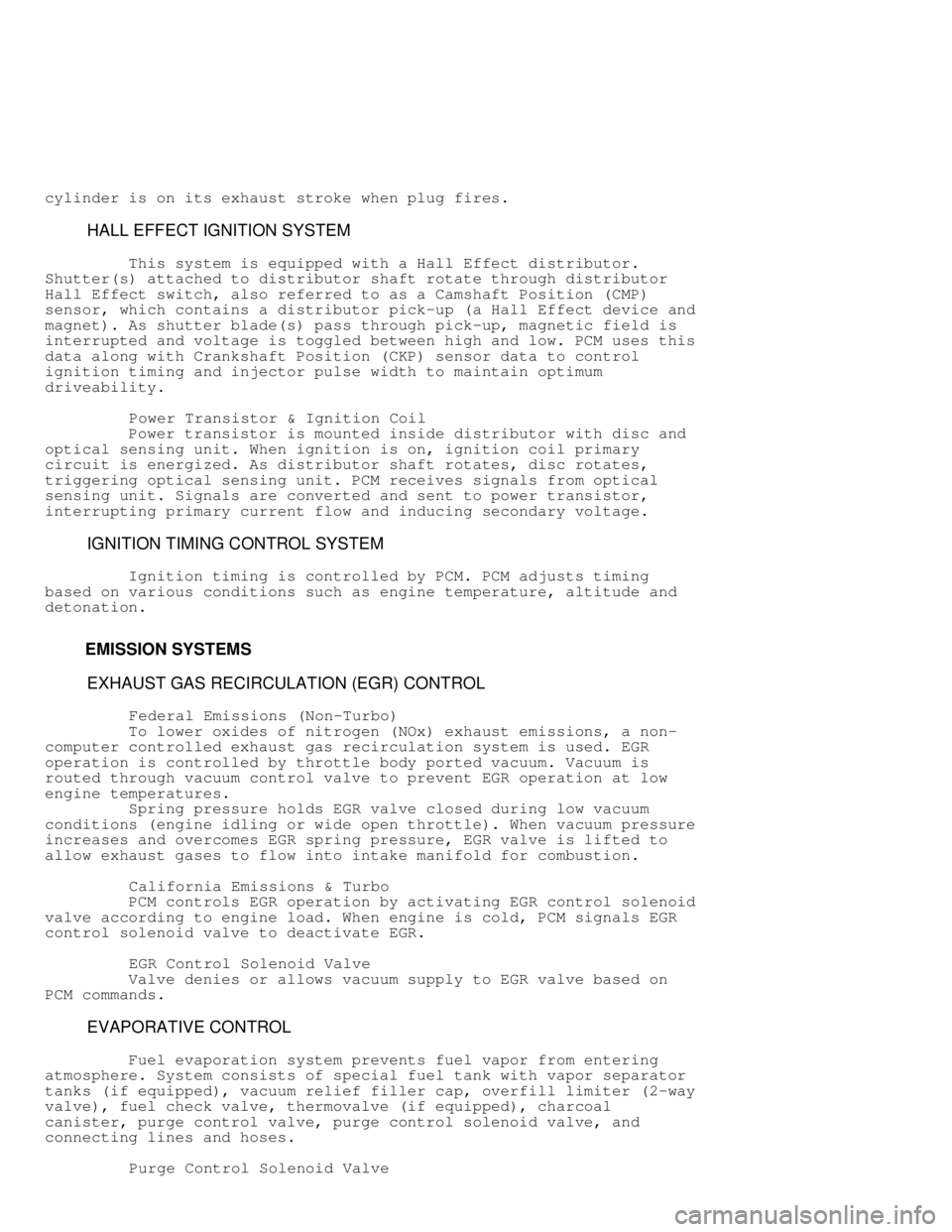
cylinder is on its exhaust stroke when plug fires.
HALL EFFECT IGNITION SYSTEM
This system is equipped with a Hall Effect distributor.
Shutter(s) attached to distributor shaft rotate through distributor
Hall Effect switch, also referred to as a Camshaft Position (CMP)
sensor, which contains a distributor pick-up (a Hall Effect device and
magnet). As shutter blade(s) pass through pick-up, magnetic field is
interrupted and voltage is toggled between high and low. PCM uses this
data along with Crankshaft Position (CKP) sensor data to control
ignition timing and injector pulse width to maintain optimum
driveability.
Power Transistor & Ignition Coil
Power transistor is mounted inside distributor with disc and
optical sensing unit. When ignition is on, ignition coil primary
circuit is energized. As distributor shaft rotates, disc rotates,
triggering optical sensing unit. PCM receives signals from optical
sensing unit. Signals are converted and sent to power transistor,
interrupting primary current flow and inducing secondary voltage.
IGNITION TIMING CONTROL SYSTEM
Ignition timing is controlled by PCM. PCM adjusts timing
based on various conditions such as engine temperature, altitude and
detonation.
EMISSION SYSTEMS
EXHAUST GAS RECIRCULATION (EGR) CONTROL
Federal Emissions (Non-Turbo)
To lower oxides of nitrogen (NOx) exhaust emissions, a non-
computer controlled exhaust gas recirculation system is used. EGR
operation is controlled by throttle body ported vacuum. Vacuum is
routed through vacuum control valve to prevent EGR operation at low
engine temperatures.
Spring pressure holds EGR valve closed during low vacuum
conditions (engine idling or wide open throttle). When vacuum pressure\
increases and overcomes EGR spring pressure, EGR valve is lifted to
allow exhaust gases to flow into intake manifold for combustion.
California Emissions & Turbo
PCM controls EGR operation by activating EGR control solenoid
valve according to engine load. When engine is cold, PCM signals EGR
control solenoid valve to deactivate EGR.
EGR Control Solenoid Valve
Valve denies or allows vacuum supply to EGR valve based on
PCM commands.
EVAPORATIVE CONTROL
Fuel evaporation system prevents fuel vapor from entering
atmosphere. System consists of special fuel tank with vapor separator
tanks (if equipped), vacuum relief filler cap, overfill limiter (2-wa\
y
valve), fuel check valve, thermovalve (if equipped), charcoal
canister, purge control valve, purge control solenoid valve, and
connecting lines and hoses.
Purge Control Solenoid Valve
Page 543 of 1501
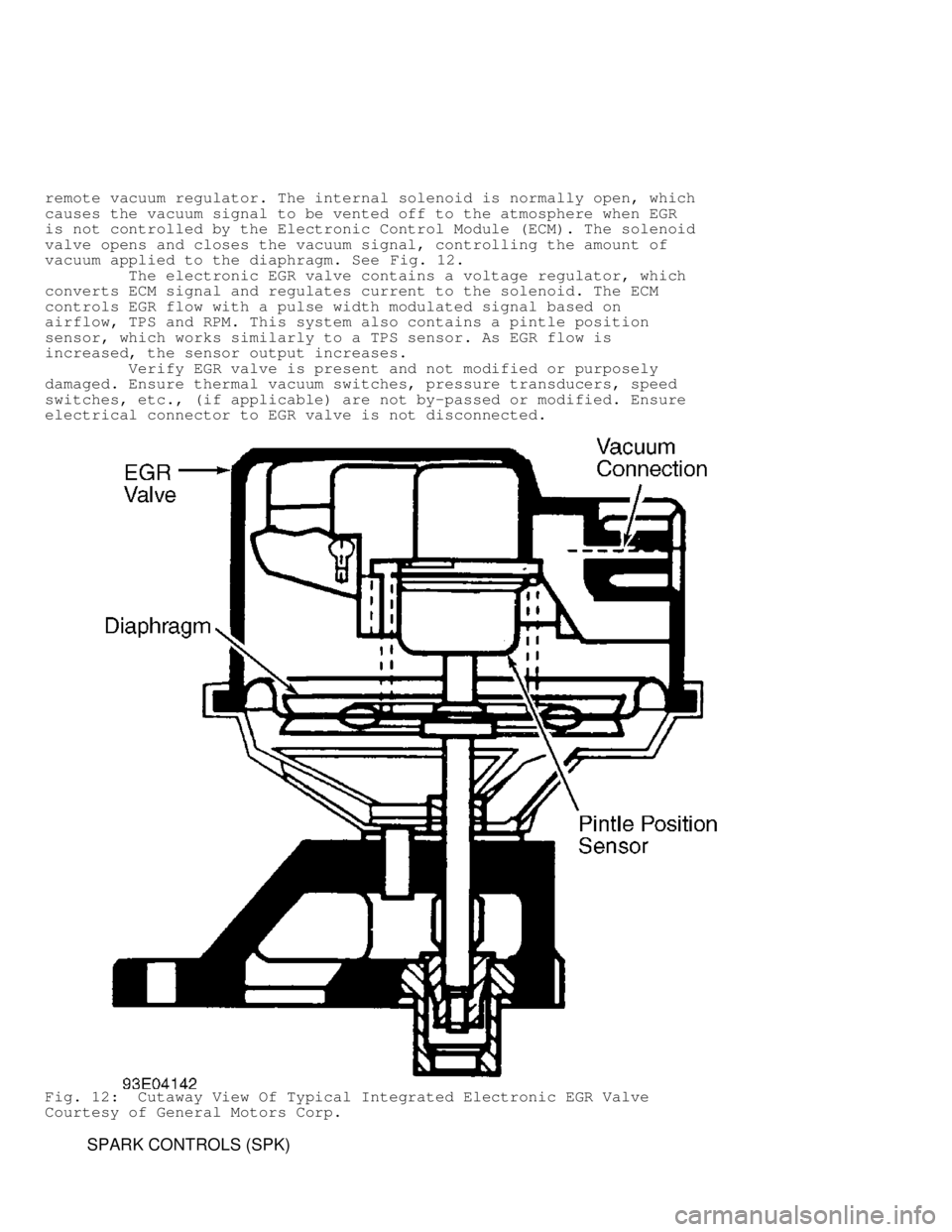
remote vacuum regulator. The internal solenoid is normally open, which
causes the vacuum signal to be vented off to the atmosphere when EGR
is not controlled by the Electronic Control Module (ECM). The solenoid\
valve opens and closes the vacuum signal, controlling the amount of
vacuum applied to the diaphragm. See Fig. 12.
The electronic EGR valve contains a voltage regulator, which
converts ECM signal and regulates current to the solenoid. The ECM
controls EGR flow with a pulse width modulated signal based on
airflow, TPS and RPM. This system also contains a pintle position
sensor, which works similarly to a TPS sensor. As EGR flow is
increased, the sensor output increases.
Verify EGR valve is present and not modified or purposely
damaged. Ensure thermal vacuum switches, pressure transducers, speed
switches, etc., (if applicable) are not by-passed or modified. Ensure
electrical connector to EGR valve is not disconnected.
Fig. 12: Cutaway View Of Typical Integrated Electronic EGR Valve
Courtesy of General Motors Corp.
SPARK CONTROLS (SPK)
Page 559 of 1501
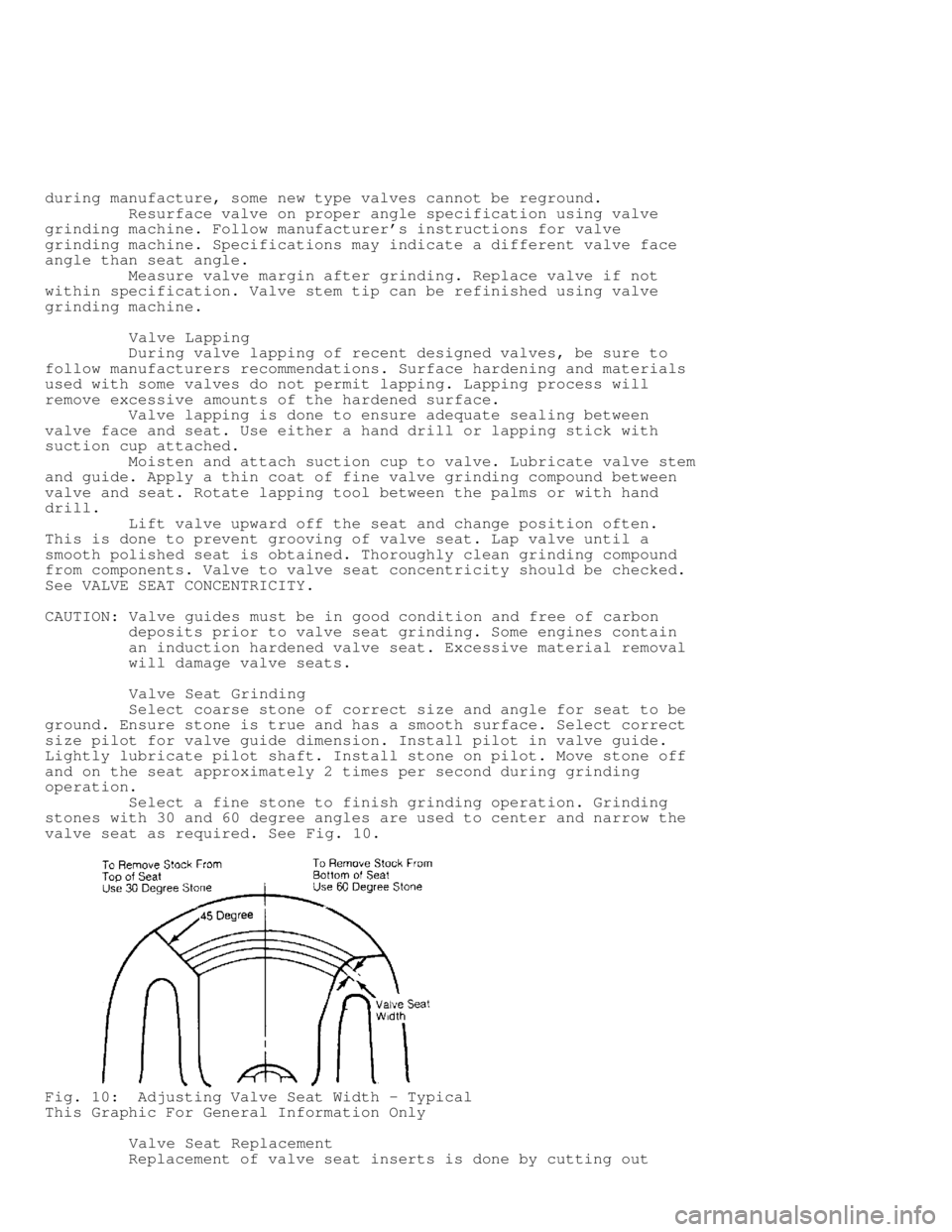
during manufacture, some new type valves cannot be reground.
Resurface valve on proper angle specification using valve
grinding machine. Follow manufacturer's instructions for valve
grinding machine. Specifications may indicate a different valve face
angle than seat angle.
Measure valve margin after grinding. Replace valve if not
within specification. Valve stem tip can be refinished using valve
grinding machine.
Valve Lapping
During valve lapping of recent designed valves, be sure to
follow manufacturers recommendations. Surface hardening and materials
used with some valves do not permit lapping. Lapping process will
remove excessive amounts of the hardened surface.
Valve lapping is done to ensure adequate sealing between
valve face and seat. Use either a hand drill or lapping stick with
suction cup attached.
Moisten and attach suction cup to valve. Lubricate valve stem
and guide. Apply a thin coat of fine valve grinding compound between
valve and seat. Rotate lapping tool between the palms or with hand
drill.
Lift valve upward off the seat and change position often.
This is done to prevent grooving of valve seat. Lap valve until a
smooth polished seat is obtained. Thoroughly clean grinding compound
from components. Valve to valve seat concentricity should be checked.
See VALVE SEAT CONCENTRICITY.
CAUTION: Valve guides must be in good condition and free of carbon
deposits prior to valve seat grinding. Some engines contain
an induction hardened valve seat. Excessive material removal
will damage valve seats.
Valve Seat Grinding
Select coarse stone of correct size and angle for seat to be
ground. Ensure stone is true and has a smooth surface. Select correct
size pilot for valve guide dimension. Install pilot in valve guide.
Lightly lubricate pilot shaft. Install stone on pilot. Move stone off
and on the seat approximately 2 times per second during grinding
operation.
Select a fine stone to finish grinding operation. Grinding
stones with 30 and 60 degree angles are used to center and narrow the
valve seat as required. See Fig. 10.
Fig. 10: Adjusting Valve Seat Width - Typical
This Graphic For General Information Only
Valve Seat Replacement
Replacement of valve seat inserts is done by cutting out
Page 570 of 1501
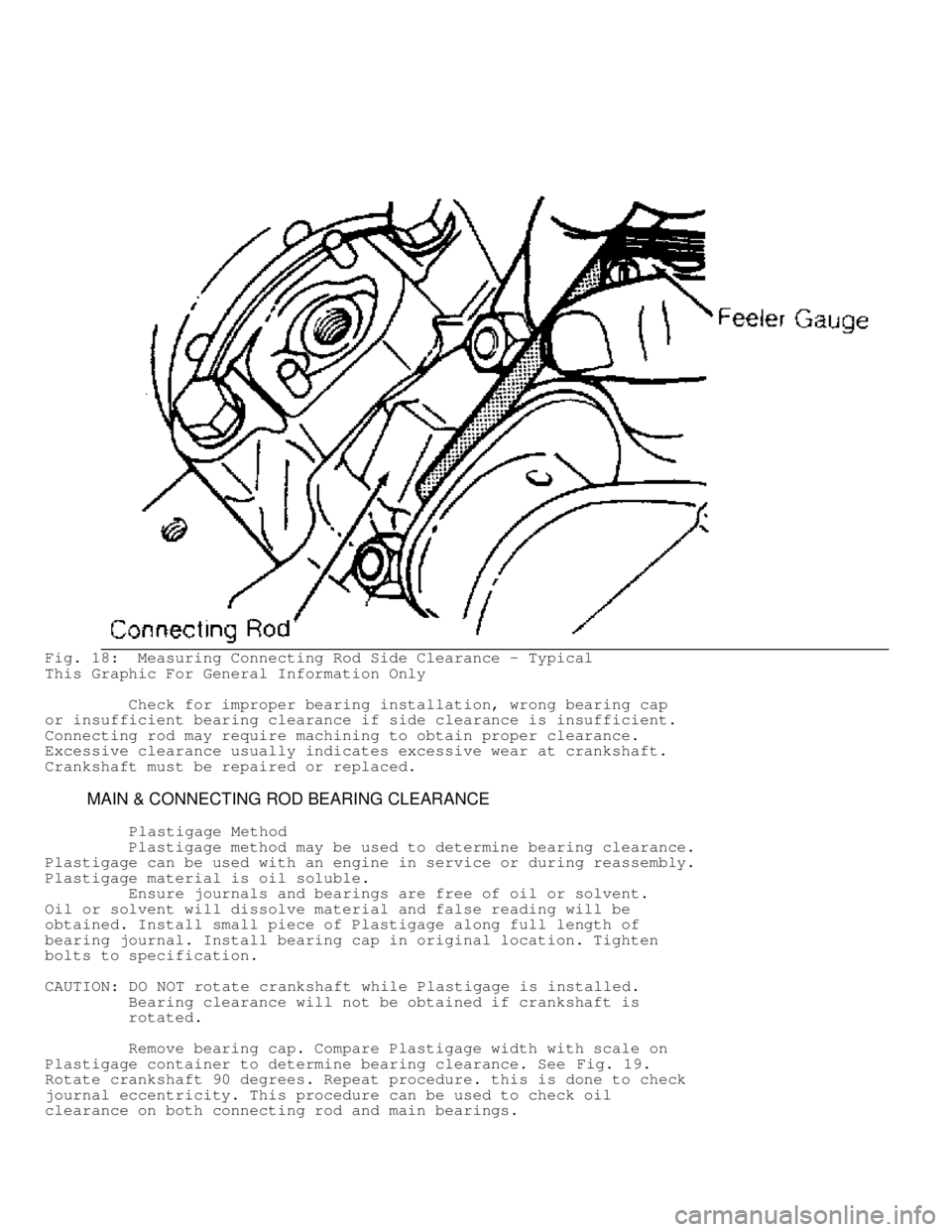
Fig. 18: Measuring Connecting Rod Side Clearance - Typical
This Graphic For General Information Only
Check for improper bearing installation, wrong bearing cap
or insufficient bearing clearance if side clearance is insufficient.
Connecting rod may require machining to obtain proper clearance.
Excessive clearance usually indicates excessive wear at crankshaft.
Crankshaft must be repaired or replaced.
MAIN & CONNECTING ROD BEARING CLEARANCE
Plastigage Method
Plastigage method may be used to determine bearing clearance.
Plastigage can be used with an engine in service or during reassembly.
Plastigage material is oil soluble.
Ensure journals and bearings are free of oil or solvent.
Oil or solvent will dissolve material and false reading will be
obtained. Install small piece of Plastigage along full length of
bearing journal. Install bearing cap in original location. Tighten
bolts to specification.
CAUTION: DO NOT rotate crankshaft while Plastigage is installed.
Bearing clearance will not be obtained if crankshaft is
rotated.
Remove bearing cap. Compare Plastigage width with scale on
Plastigage container to determine bearing clearance. See Fig. 19.
Rotate crankshaft 90 degrees. Repeat procedure. this is done to check
journal eccentricity. This procedure can be used to check oil
clearance on both connecting rod and main bearings.
Page 575 of 1501
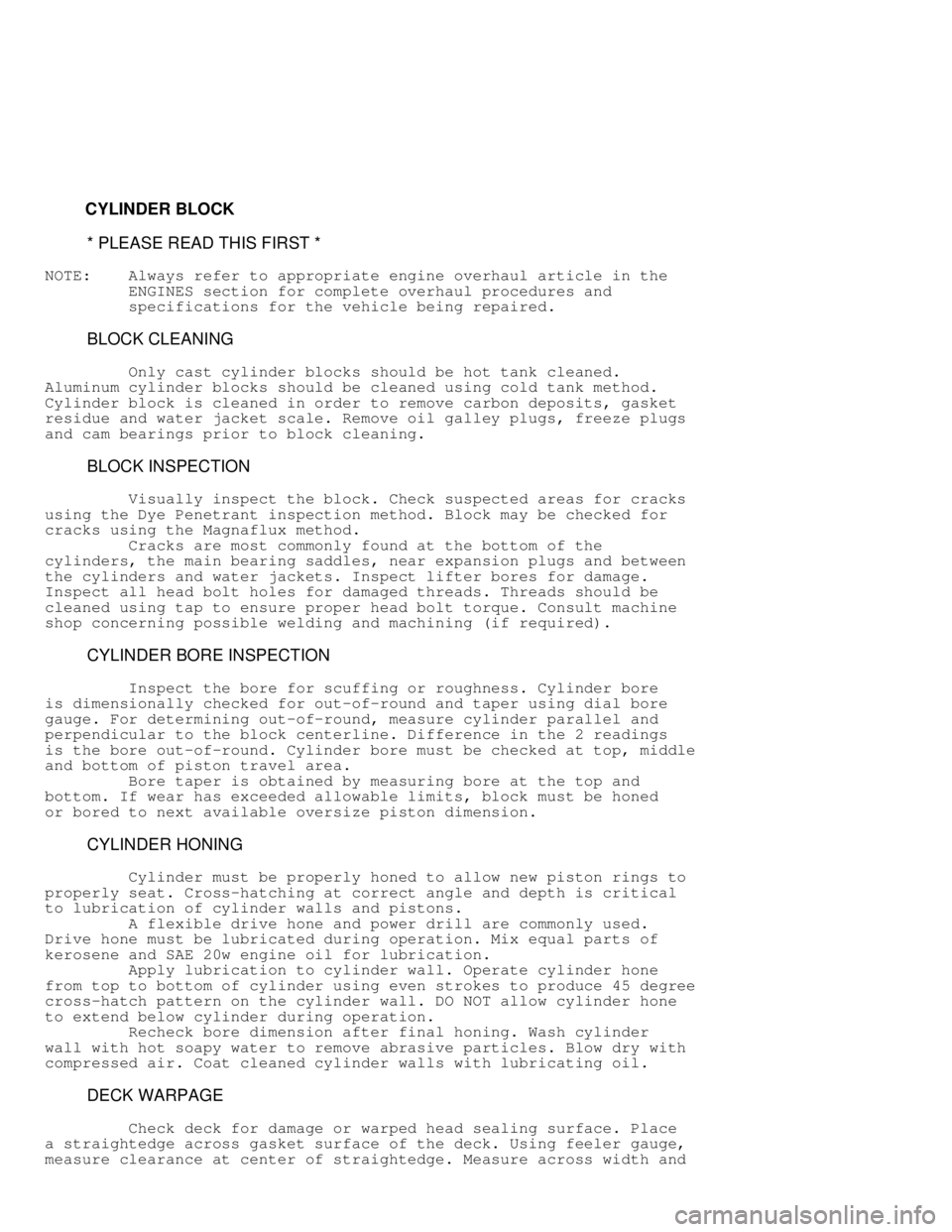
CYLINDER BLOCK
* PLEASE READ THIS FIRST *
NOTE: Always refer to appropriate engine overhaul article in the
ENGINES section for complete overhaul procedures and
specifications for the vehicle being repaired.
BLOCK CLEANING
Only cast cylinder blocks should be hot tank cleaned.
Aluminum cylinder blocks should be cleaned using cold tank method.
Cylinder block is cleaned in order to remove carbon deposits, gasket
residue and water jacket scale. Remove oil galley plugs, freeze plugs
and cam bearings prior to block cleaning.
BLOCK INSPECTION
Visually inspect the block. Check suspected areas for cracks
using the Dye Penetrant inspection method. Block may be checked for
cracks using the Magnaflux method.
Cracks are most commonly found at the bottom of the
cylinders, the main bearing saddles, near expansion plugs and between
the cylinders and water jackets. Inspect lifter bores for damage.
Inspect all head bolt holes for damaged threads. Threads should be
cleaned using tap to ensure proper head bolt torque. Consult machine
shop concerning possible welding and machining (if required).
CYLINDER BORE INSPECTION
Inspect the bore for scuffing or roughness. Cylinder bore
is dimensionally checked for out-of-round and taper using dial bore
gauge. For determining out-of-round, measure cylinder parallel and
perpendicular to the block centerline. Difference in the 2 readings
is the bore out-of-round. Cylinder bore must be checked at top, middle
and bottom of piston travel area.
Bore taper is obtained by measuring bore at the top and
bottom. If wear has exceeded allowable limits, block must be honed
or bored to next available oversize piston dimension.
CYLINDER HONING
Cylinder must be properly honed to allow new piston rings to
properly seat. Cross-hatching at correct angle and depth is critical
to lubrication of cylinder walls and pistons.
A flexible drive hone and power drill are commonly used.
Drive hone must be lubricated during operation. Mix equal parts of
kerosene and SAE 20w engine oil for lubrication.
Apply lubrication to cylinder wall. Operate cylinder hone
from top to bottom of cylinder using even strokes to produce 45 degree
cross-hatch pattern on the cylinder wall. DO NOT allow cylinder hone
to extend below cylinder during operation.
Recheck bore dimension after final honing. Wash cylinder
wall with hot soapy water to remove abrasive particles. Blow dry with
compressed air. Coat cleaned cylinder walls with lubricating oil.
DECK WARPAGE
Check deck for damage or warped head sealing surface. Place
a straightedge across gasket surface of the deck. Using feeler gauge,
measure clearance at center of straightedge. Measure across width and