width MITSUBISHI MONTERO 1998 User Guide
[x] Cancel search | Manufacturer: MITSUBISHI, Model Year: 1998, Model line: MONTERO, Model: MITSUBISHI MONTERO 1998Pages: 1501, PDF Size: 25.81 MB
Page 967 of 1501
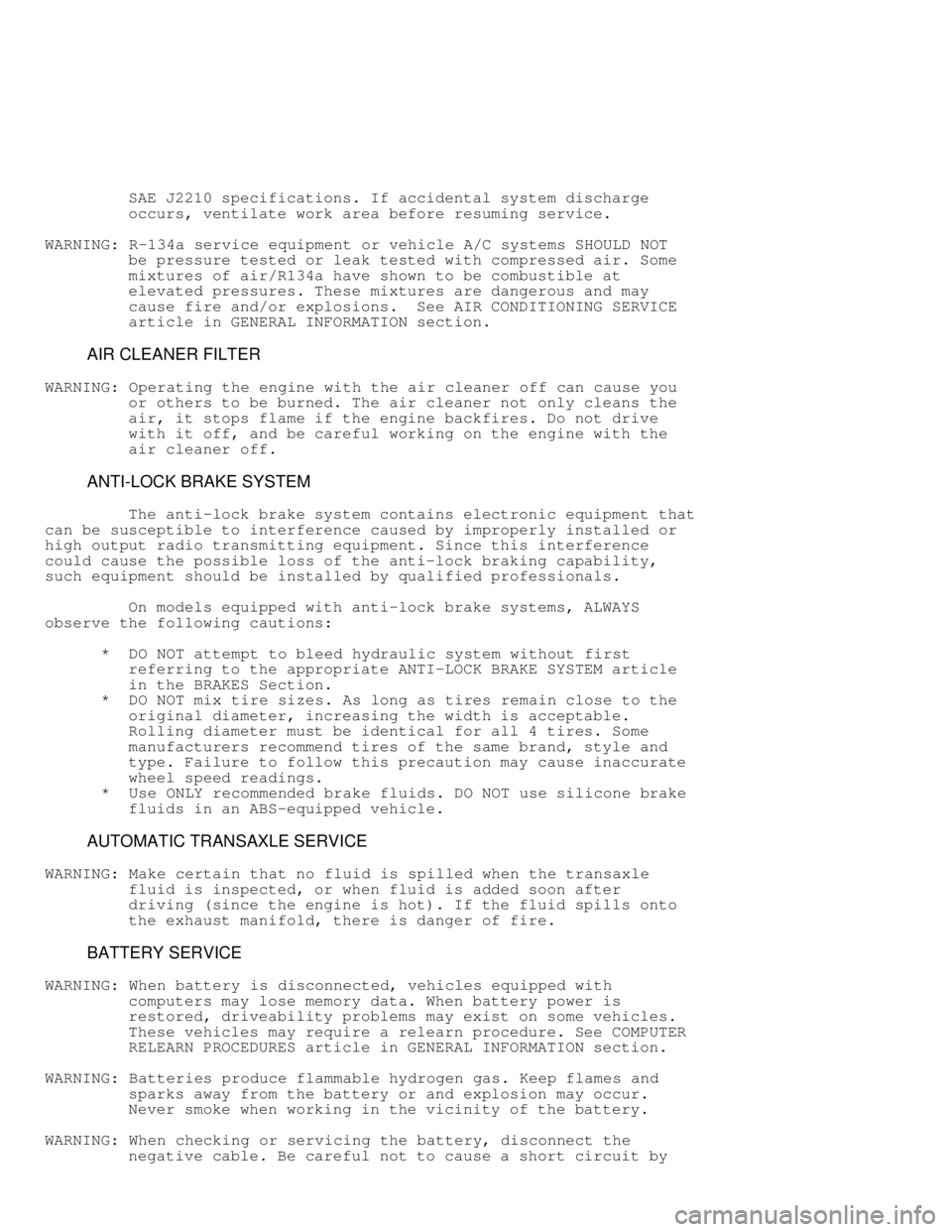
SAE J2210 specifications. If accidental system discharge
occurs, ventilate work area before resuming service.
WARNING: R-134a service equipment or vehicle A/C systems SHOULD NOT
be pressure tested or leak tested with compressed air. Some
mixtures of air/R134a have shown to be combustible at
elevated pressures. These mixtures are dangerous and may
cause fire and/or explosions. See AIR CONDITIONING SERVICE
article in GENERAL INFORMATION section.
AIR CLEANER FILTER
WARNING: Operating the engine with the air cleaner off can cause you
or others to be burned. The air cleaner not only cleans the
air, it stops flame if the engine backfires. Do not drive
with it off, and be careful working on the engine with the
air cleaner off.
ANTI-LOCK BRAKE SYSTEM
The anti-lock brake system contains electronic equipment that
can be susceptible to interference caused by improperly installed or
high output radio transmitting equipment. Since this interference
could cause the possible loss of the anti-lock braking capability,
such equipment should be installed by qualified professionals.
On models equipped with anti-lock brake systems, ALWAYS
observe the following cautions:
* DO NOT attempt to bleed hydraulic system without first
referring to the appropriate ANTI-LOCK BRAKE SYSTEM article
in the BRAKES Section.
* DO NOT mix tire sizes. As long as tires remain close to the
original diameter, increasing the width is acceptable.
Rolling diameter must be identical for all 4 tires. Some
manufacturers recommend tires of the same brand, style and
type. Failure to follow this precaution may cause inaccurate
wheel speed readings.
* Use ONLY recommended brake fluids. DO NOT use silicone brake
fluids in an ABS-equipped vehicle.
AUTOMATIC TRANSAXLE SERVICE
WARNING: Make certain that no fluid is spilled when the transaxle
fluid is inspected, or when fluid is added soon after
driving (since the engine is hot). If the fluid spills onto
the exhaust manifold, there is danger of fire.
BATTERY SERVICE
WARNING: When battery is disconnected, vehicles equipped with
computers may lose memory data. When battery power is
restored, driveability problems may exist on some vehicles.
These vehicles may require a relearn procedure. See COMPUTER
RELEARN PROCEDURES article in GENERAL INFORMATION section.
WARNING: Batteries produce flammable hydrogen gas. Keep flames and
sparks away from the battery or and explosion may occur.
Never smoke when working in the vicinity of the battery.
WARNING: When checking or servicing the battery, disconnect the
negative cable. Be careful not to cause a short circuit by
Page 1213 of 1501
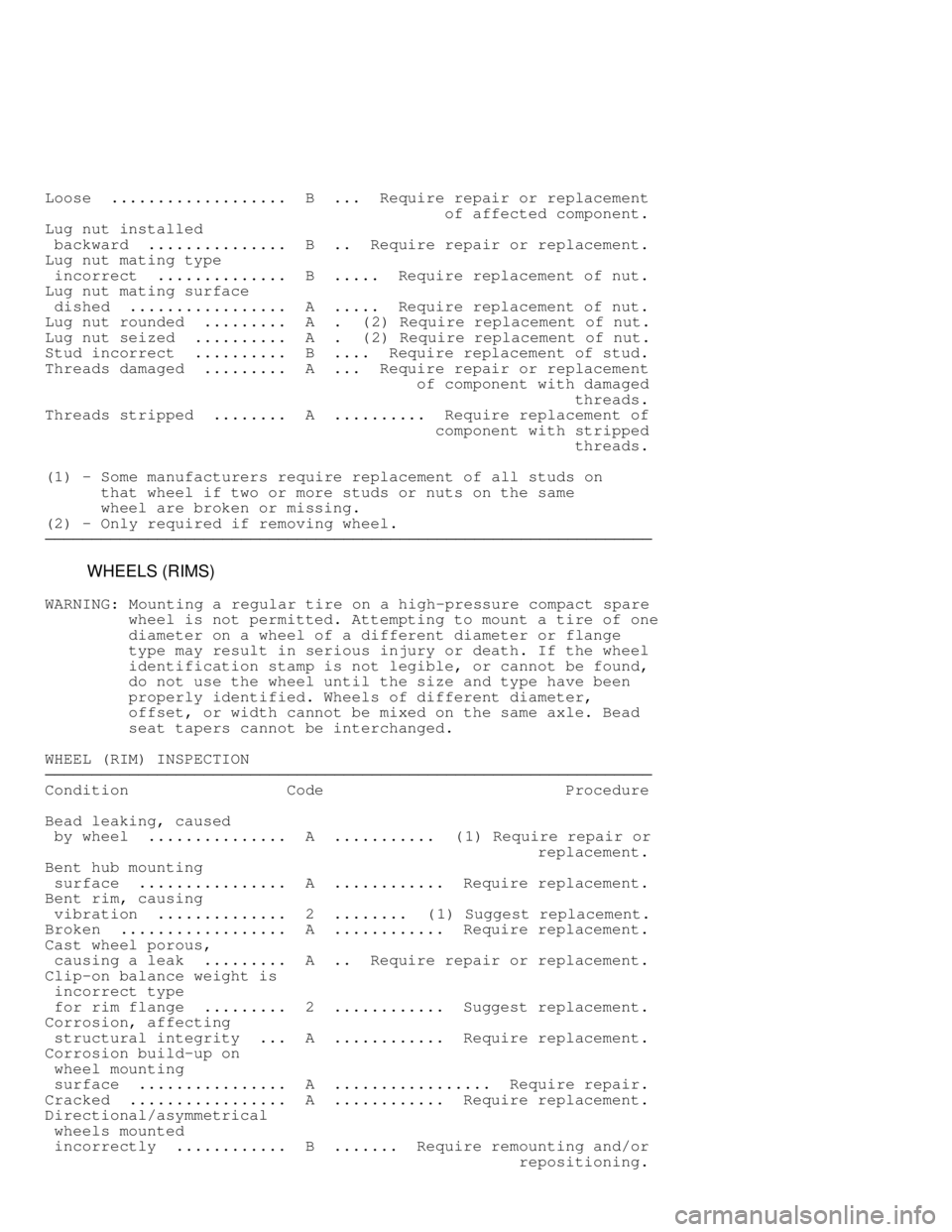
Loose ................... B ... Require repair or replacement
of affected component.
Lug nut installed
backward ............... B .. Require repair or replacement.
Lug nut mating type
incorrect .............. B ..... Require replacement of nut.
Lug nut mating surface
dished ................. A ..... Require replacement of nut.
Lug nut rounded ......... A . (2) Require replacement of nut.
Lug nut seized .......... A . ( 2) Require replacement of nut.
Stud incorrect .......... B .... Require replacement of stud.
Threads damaged ......... A ... Require repair or replacement
of component with damaged
threads.
Threads stripped ........ A .......... Require replacement of
component with stripped
threads.
( 1) - Some manufacturers require replacement of all studs on
that wheel if two or more studs or nuts on the same
wheel are broken or missing.
( 2) - Only required if removing wheel.
\
\
\
\
\
\
\
WHEELS (RIMS)
WARNING: Mounting a regular tire on a high-pressure compact spare
wheel is not permitted. Attempting to mount a tire of one
diameter on a wheel of a different diameter or flange
type may result in serious injury or death. If the wheel
identification stamp is not legible, or cannot be found,
do not use the wheel until the size and type have been
properly identified. Wheels of different diameter,
offset, or width cannot be mixed on the same axle. Bead
seat tapers cannot be interchanged.
WHEEL (RIM) INSPECTION
\
\
\
\
\
\
\
Condition Code Procedure
Bead leaking, caused
by wheel ............... A ........... ( 1) Require repair or
replacement.
Bent hub mounting
surface ................ A ............ Require replacement.
Bent rim, causing
vibration .............. 2 ........ ( 1) Suggest replacement.
Broken .................. A ............ Require replacement.
Cast wheel porous,
causing a leak ......... A .. Require repair or replacement.
Clip-on balance weight is
incorrect type
for rim flange ......... 2 ............ Suggest replacement.
Corrosion, affecting
structural integrity ... A ............ Require replacement.
Corrosion build-up on
wheel mounting
surface ................ A ................. Require repair.
Cracked ................. A ............ Require replacement.
Directional/asymmetrical
wheels mounted
incorrectly ............ B ....... Require remounting and/or
repositioning.
Page 1294 of 1501
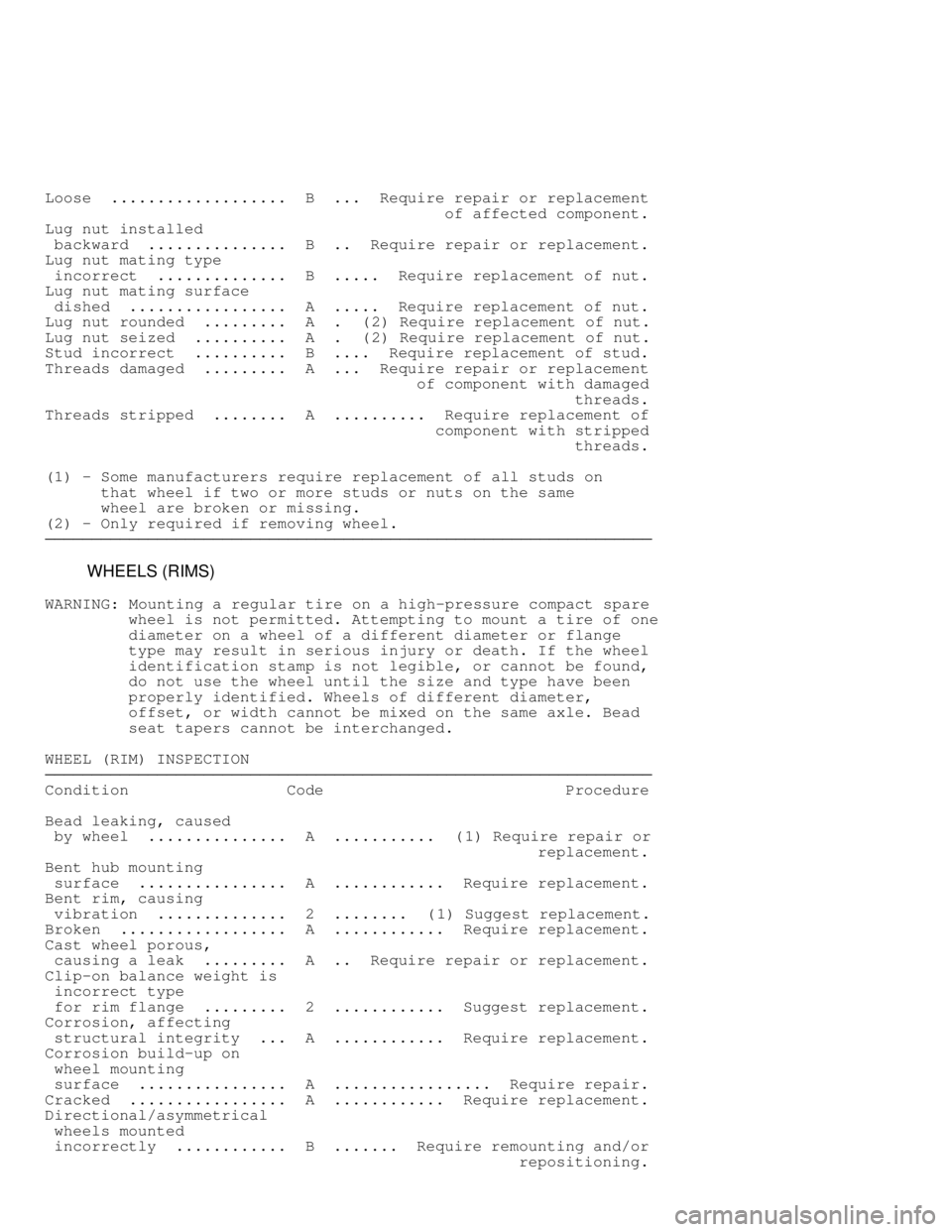
Loose ................... B ... Require repair or replacement
of affected component.
Lug nut installed
backward ............... B .. Require repair or replacement.
Lug nut mating type
incorrect .............. B ..... Require replacement of nut.
Lug nut mating surface
dished ................. A ..... Require replacement of nut.
Lug nut rounded ......... A . (2) Require replacement of nut.
Lug nut seized .......... A . ( 2) Require replacement of nut.
Stud incorrect .......... B .... Require replacement of stud.
Threads damaged ......... A ... Require repair or replacement
of component with damaged
threads.
Threads stripped ........ A .......... Require replacement of
component with stripped
threads.
( 1) - Some manufacturers require replacement of all studs on
that wheel if two or more studs or nuts on the same
wheel are broken or missing.
( 2) - Only required if removing wheel.
\
\
\
\
\
\
\
WHEELS (RIMS)
WARNING: Mounting a regular tire on a high-pressure compact spare
wheel is not permitted. Attempting to mount a tire of one
diameter on a wheel of a different diameter or flange
type may result in serious injury or death. If the wheel
identification stamp is not legible, or cannot be found,
do not use the wheel until the size and type have been
properly identified. Wheels of different diameter,
offset, or width cannot be mixed on the same axle. Bead
seat tapers cannot be interchanged.
WHEEL (RIM) INSPECTION
\
\
\
\
\
\
\
Condition Code Procedure
Bead leaking, caused
by wheel ............... A ........... ( 1) Require repair or
replacement.
Bent hub mounting
surface ................ A ............ Require replacement.
Bent rim, causing
vibration .............. 2 ........ ( 1) Suggest replacement.
Broken .................. A ............ Require replacement.
Cast wheel porous,
causing a leak ......... A .. Require repair or replacement.
Clip-on balance weight is
incorrect type
for rim flange ......... 2 ............ Suggest replacement.
Corrosion, affecting
structural integrity ... A ............ Require replacement.
Corrosion build-up on
wheel mounting
surface ................ A ................. Require repair.
Cracked ................. A ............ Require replacement.
Directional/asymmetrical
wheels mounted
incorrectly ............ B ....... Require remounting and/or
repositioning.
Page 1384 of 1501
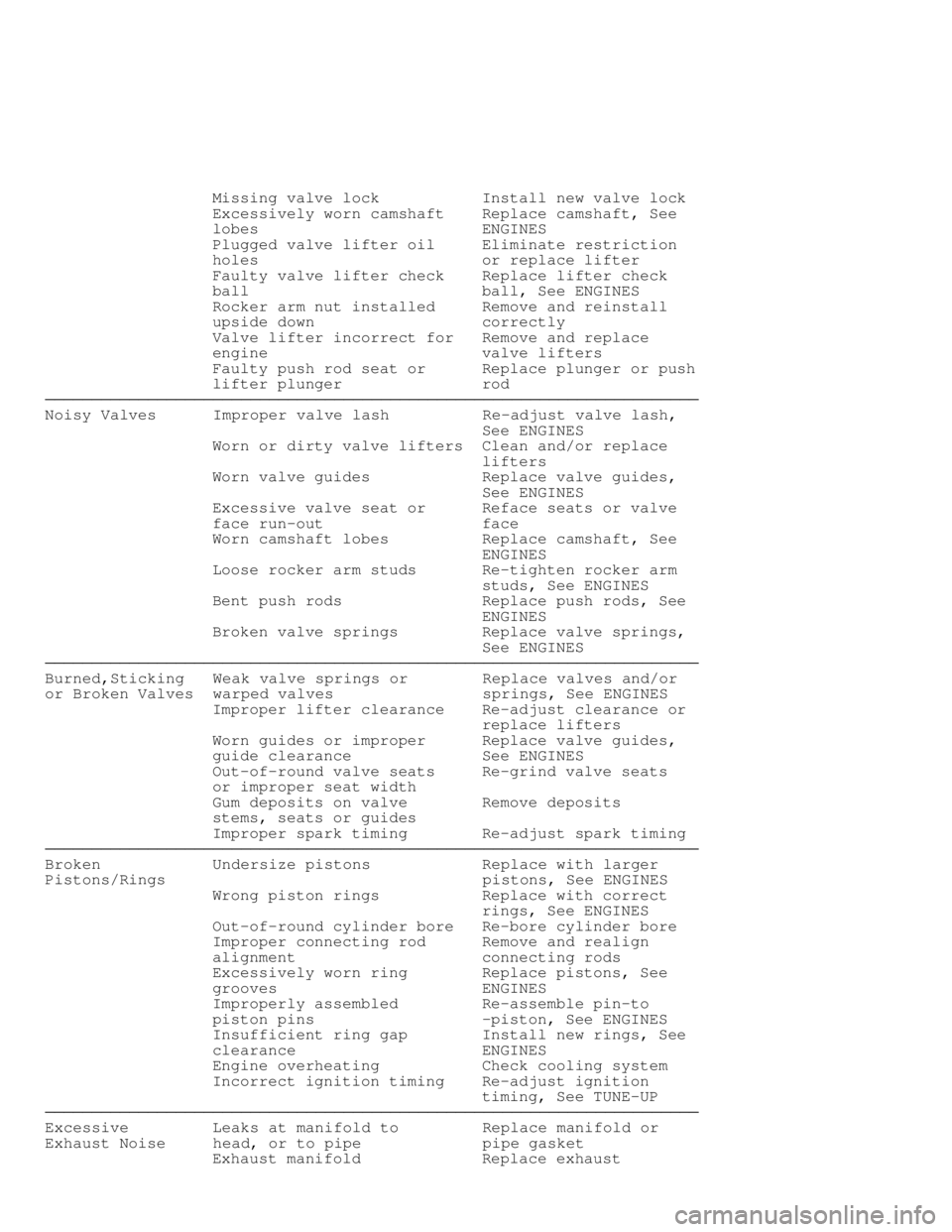
Missing valve lock Install new valve lock
Excessively worn camshaft Replace camshaft, See
lobes ENGINES
Plugged valve lifter oil Eliminate restriction
holes or replace lifter
Faulty valve lifter check Replace lifter check
ball ball, See ENGINES
Rocker arm nut installed Remove and reinstall
upside down correctly
Valve lifter incorrect for Remove and replace
engine valve lifters
Faulty push rod seat or Replace plunger or push
lifter plunger rod
\
\
\
\
\
\
\
Noisy Valves Improper valve lash Re-adjust valve lash,
See ENGINES
Worn or dirty valve lifters Clean and/or replace
lifters
Worn valve guides Replace valve guides,
See ENGINES
Excessive valve seat or Reface seats or valve
face run-out face
Worn camshaft lobes Replace camshaft, See
ENGINES
Loose rocker arm studs Re-tighten rocker arm
studs, See ENGINES
Bent push rods Replace push rods, See
ENGINES
Broken valve springs Replace valve springs,
See ENGINES
\
\
\
\
\
\
\
Burned,Sticking Weak valve springs or Replace valves and/or
or Broken Valves warped valves springs, See ENGINES
Improper lifter clearance Re-adjust clearance or
replace lifters
Worn guides or improper Replace valve guides,
guide clearance See ENGINES
Out-of-round valve seats Re-grind valve seats
or improper seat width
Gum deposits on valve Remove deposits
stems, seats or guides
Improper spark timing Re-adjust spark timing
\
\
\
\
\
\
\
Broken Undersize pistons Replace with larger
Pistons/Rings pistons, See ENGINES
Wrong piston rings Replace with correct
rings, See ENGINES
Out-of-round cylinder bore Re-bore cylinder bore
Improper connecting rod Remove and realign
alignment connecting rods
Excessively worn ring Replace pistons, See
grooves ENGINES
Improperly assembled Re-assemble pin-to
piston pins -piston, See ENGINES
Insufficient ring gap Install new rings, See
clearance ENGINES
Engine overheating Check cooling system
Incorrect ignition timing Re-adjust ignition
timing, See TUNE-UP
\
\
\
\
\
\
\
Excessive Leaks at manifold to Replace manifold or
Exhaust Noise head, or to pipe pipe gasket
Exhaust manifold Replace exhaust
Page 1430 of 1501
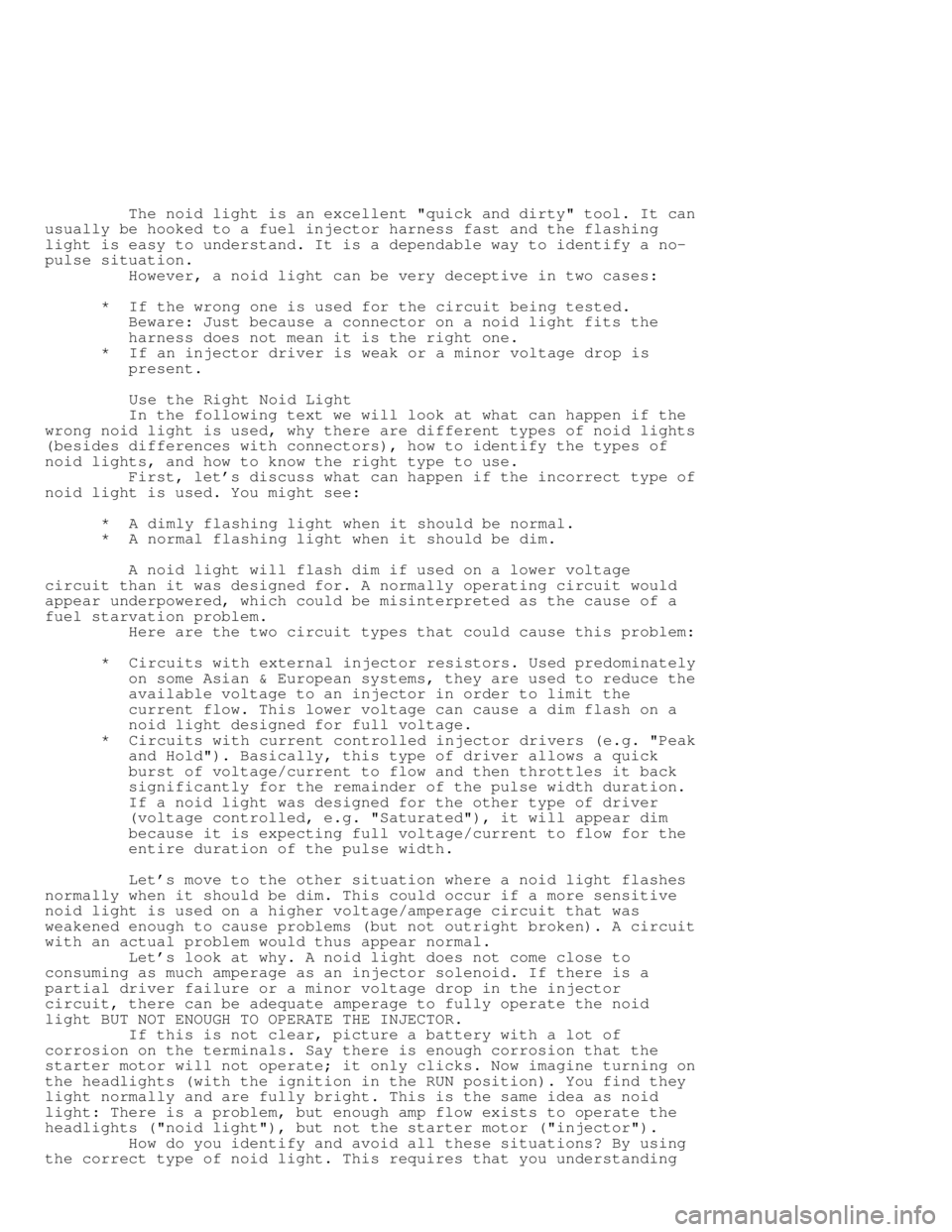
The noid light is an excellent "quick and dirty" tool. It can
usually be hooked to a fuel injector harness fast and the flashing
light is easy to understand. It is a dependable way to identify a no-
pulse situation.
However, a noid light can be very deceptive in two cases:
* If the wrong one is used for the circuit being tested.
Beware: Just because a connector on a noid light fits the
harness does not mean it is the right one.
* If an injector driver is weak or a minor voltage drop is
present.
Use the Right Noid Light
In the following text we will look at what can happen if the
wrong noid light is used, why there are different types of noid lights
(besides differences with connectors), how to identify the types of
noid lights, and how to know the right type to use.
First, let's discuss what can happen if the incorrect type of
noid light is used. You might see:
* A dimly flashing light when it should be normal.
* A normal flashing light when it should be dim.
A noid light will flash dim if used on a lower voltage
circuit than it was designed for. A normally operating circuit would
appear underpowered, which could be misinterpreted as the cause of a
fuel starvation problem.
Here are the two circuit types that could cause this problem:
* Circuits with external injector resistors. Used predominately
on some Asian & European systems, they are used to reduce the
available voltage to an injector in order to limit the
current flow. This lower voltage can cause a dim flash on a
noid light designed for full voltage.
* Circuits with current controlled injector drivers (e.g. "Peak
and Hold"). Basically, this type of driver allows a quick
burst of voltage/current to flow and then throttles it back
significantly for the remainder of the pulse width duration.
If a noid light was designed for the other type of driver
(voltage controlled, e.g. "Saturated"), it will appear dim
because it is expecting full voltage/current to flow for the
entire duration of the pulse width.
Let's move to the other situation where a noid light flashes
normally when it should be dim. This could occur if a more sensitive
noid light is used on a higher voltage/amperage circuit that was
weakened enough to cause problems (but not outright broken). A circuit\
with an actual problem would thus appear normal.
Let's look at why. A noid light does not come close to
consuming as much amperage as an injector solenoid. If there is a
partial driver failure or a minor voltage drop in the injector
circuit, there can be adequate amperage to fully operate the noid
light BUT NOT ENOUGH TO OPERATE THE INJECTOR.
If this is not clear, picture a battery with a lot of
corrosion on the terminals. Say there is enough corrosion that the
starter motor will not operate; it only clicks. Now imagine turning on
the headlights (with the ignition in the RUN position). You find they
light normally and are fully bright. This is the same idea as noid
light: There is a problem, but enough amp flow exists to operate the
headlights ("noid light"), but not the starter motor ("injector").
How do you identify and avoid all these situations? By using
the correct type of noid light. This requires that you understanding
Page 1432 of 1501
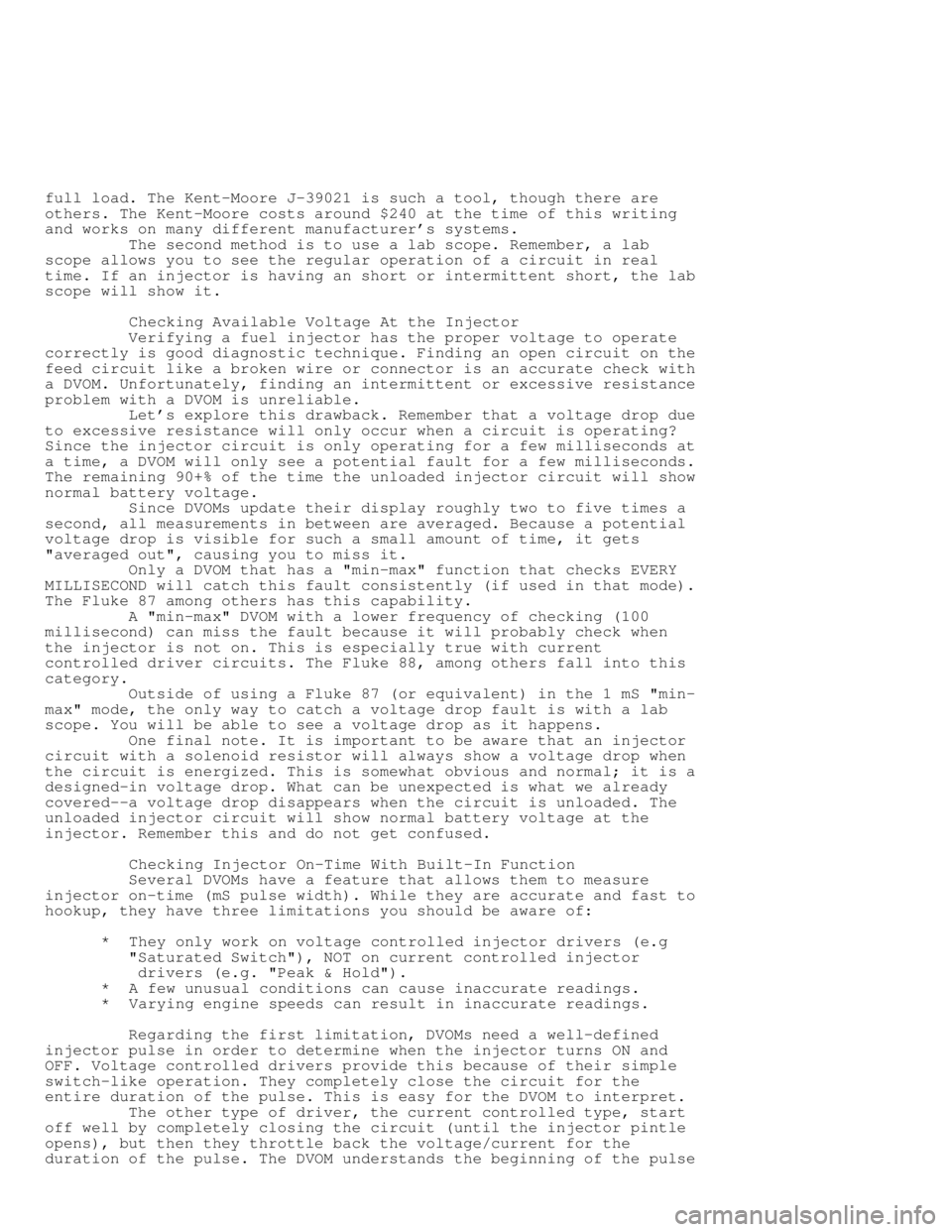
full load. The Kent-Moore J-39021 is such a tool, though there are
others. The Kent-Moore costs around $240 at the time of this writing
and works on many different manufacturer's systems.
The second method is to use a lab scope. Remember, a lab
scope allows you to see the regular operation of a circuit in real
time. If an injector is having an short or intermittent short, the lab
scope will show it.
Checking Available Voltage At the Injector
Verifying a fuel injector has the proper voltage to operate
correctly is good diagnostic technique. Finding an open circuit on the
feed circuit like a broken wire or connector is an accurate check with
a DVOM. Unfortunately, finding an intermittent or excessive resistance
problem with a DVOM is unreliable.
Let's explore this drawback. Remember that a voltage drop due
to excessive resistance will only occur when a circuit is operating?
Since the injector circuit is only operating for a few milliseconds at
a time, a DVOM will only see a potential fault for a few milliseconds.
The remaining 90+% of the time the unloaded injector circuit will show
normal battery voltage.
Since DVOMs update their display roughly two to five times a
second, all measurements in between are averaged. Because a potential
voltage drop is visible for such a small amount of time, it gets
"averaged out", causing you to miss it.
Only a DVOM that has a "min-max" function that checks EVERY
MILLISECOND will catch this fault consistently (if used in that mode).\
The Fluke 87 among others has this capability.
A "min-max" DVOM with a lower frequency of checking (100
millisecond) can miss the fault because it will probably check when
the injector is not on. This is especially true with current
controlled driver circuits. The Fluke 88, among others fall into this
category.
Outside of using a Fluke 87 (or equivalent) in the 1 mS "min-\
max" mode, the only way to catch a voltage drop fault is with a lab
scope. You will be able to see a voltage drop as it happens.
One final note. It is important to be aware that an injector
circuit with a solenoid resistor will always show a voltage drop when
the circuit is energized. This is somewhat obvious and normal; it is a
designed-in voltage drop. What can be unexpected is what we already
covered--a voltage drop disappears when the circuit is unloaded. The
unloaded injector circuit will show normal battery voltage at the
injector. Remember this and do not get confused.
Checking Injector On-Time With Built-In Function
Several DVOMs have a feature that allows them to measure
injector on-time (mS pulse width). While they are accurate and fast to\
hookup, they have three limitations you should be aware of:
* They only work on voltage controlled injector drivers (e.g
"Saturated Switch"), NOT on current controlled injector
drivers (e.g. "Peak & Hold").
* A few unusual conditions can cause inaccurate readings.
* Varying engine speeds can result in inaccurate readings.
Regarding the first limitation, DVOMs need a well-defined
injector pulse in order to determine when the injector turns ON and
OFF. Voltage controlled drivers provide this because of their simple
switch-like operation. They completely close the circuit for the
entire duration of the pulse. This is easy for the DVOM to interpret.
The other type of driver, the current controlled type, start
off well by completely closing the circuit (until the injector pintle
opens), but then they throttle back the voltage/current for the
duration of the pulse. The DVOM understands the beginning of the pulse
Page 1434 of 1501
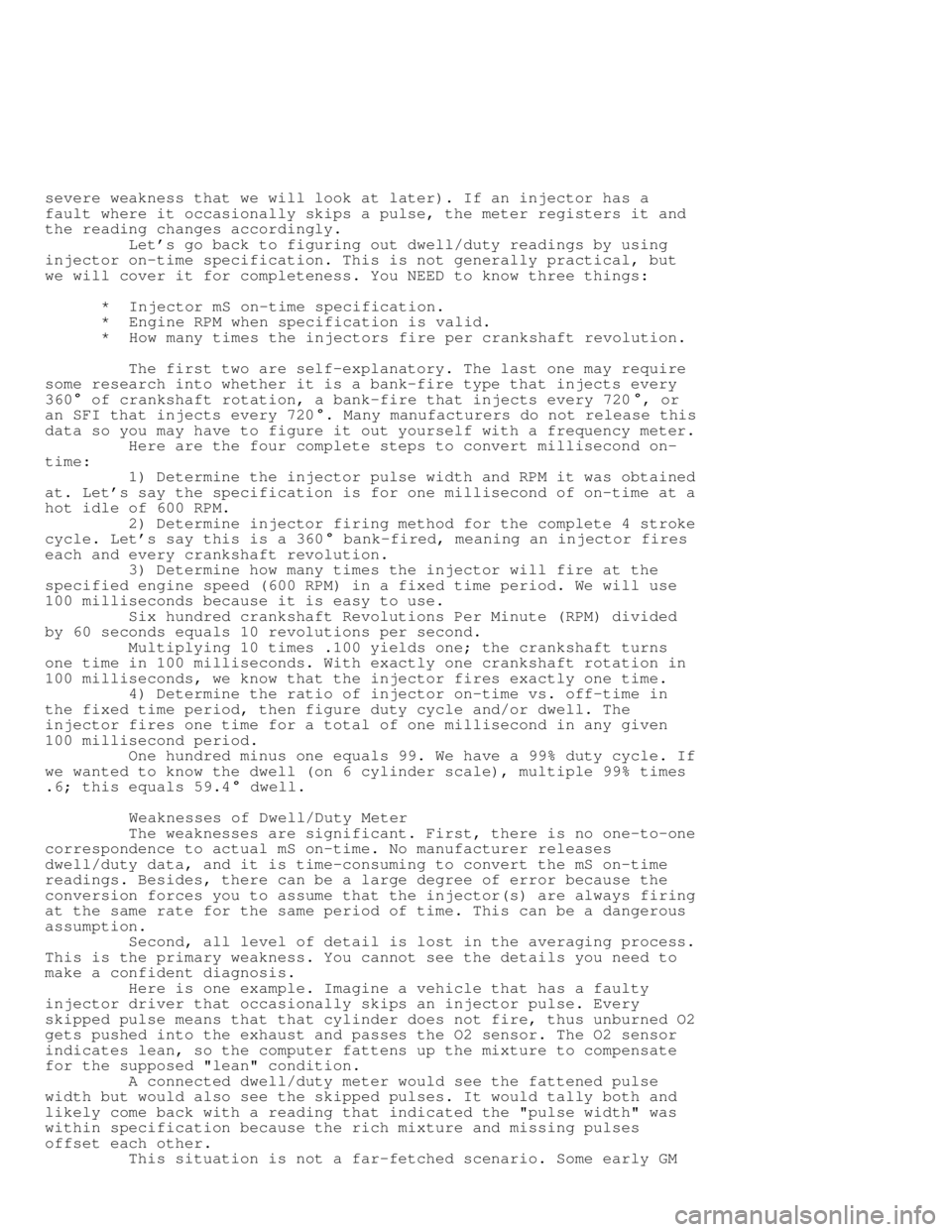
severe weakness that we will look at later). If an injector has a
fault where it occasionally skips a pulse, the meter registers it and
the reading changes accordingly.
Let's go back to figuring out dwell/duty readings by using
injector on-time specification. This is not generally practical, but
we will cover it for completeness. You NEED to know three things:
* Injector mS on-time specification.
* Engine RPM when specification is valid.
* How many times the injectors fire per crankshaft revolution.
The first two are self-explanatory. The last one may require
some research into whether it is a bank-fire type that injects every
360
of crankshaft rotation, a bank-fire that injects every 720 , or
an SFI that injects every 720 . Many manufacturers do not release this
data so you may have to figure it out yourself with a frequency meter.
Here are the four complete steps to convert millisecond on-
time:
1) Determine the injector pulse width and RPM it was obtained
at. Let's say the specification is for one millisecond of on-time at a
hot idle of 600 RPM.
2) Determine injector firing method for the complete 4 stroke
cycle. Let's say this is a 360
bank-fired, meaning an injector fires
each and every crankshaft revolution.
3) Determine how many times the injector will fire at the
specified engine speed (600 RPM) in a fixed time period. We will use
100 milliseconds because it is easy to use.
Six hundred crankshaft Revolutions Per Minute (RPM) divided
by 60 seconds equals 10 revolutions per second.
Multiplying 10 times .100 yields one; the crankshaft turns
one time in 100 milliseconds. With exactly one crankshaft rotation in
100 milliseconds, we know that the injector fires exactly one time.
4) Determine the ratio of injector on-time vs. off-time in
the fixed time period, then figure duty cycle and/or dwell. The
injector fires one time for a total of one millisecond in any given
100 millisecond period.
One hundred minus one equals 99. We have a 99% duty cycle. If
we wanted to know the dwell (on 6 cylinder scale), multiple 99% times
.6; this equals 59.4
dwell.
Weaknesses of Dwell/Duty Meter
The weaknesses are significant. First, there is no one-to-one
correspondence to actual mS on-time. No manufacturer releases
dwell/duty data, and it is time-consuming to convert the mS on-time
readings. Besides, there can be a large degree of error because the
conversion forces you to assume that the injector(s) are always firing\
at the same rate for the same period of time. This can be a dangerous
assumption.
Second, all level of detail is lost in the averaging process.
This is the primary weakness. You cannot see the details you need to
make a confident diagnosis.
Here is one example. Imagine a vehicle that has a faulty
injector driver that occasionally skips an injector pulse. Every
skipped pulse means that that cylinder does not fire, thus unburned O2
gets pushed into the exhaust and passes the O2 sensor. The O2 sensor
indicates lean, so the computer fattens up the mixture to compensate
for the supposed "lean" condition.
A connected dwell/duty meter would see the fattened pulse
width but would also see the skipped pulses. It would tally both and
likely come back with a reading that indicated the "pulse width" was
within specification because the rich mixture and missing pulses
offset each other.
This situation is not a far-fetched scenario. Some early GM
Page 1436 of 1501
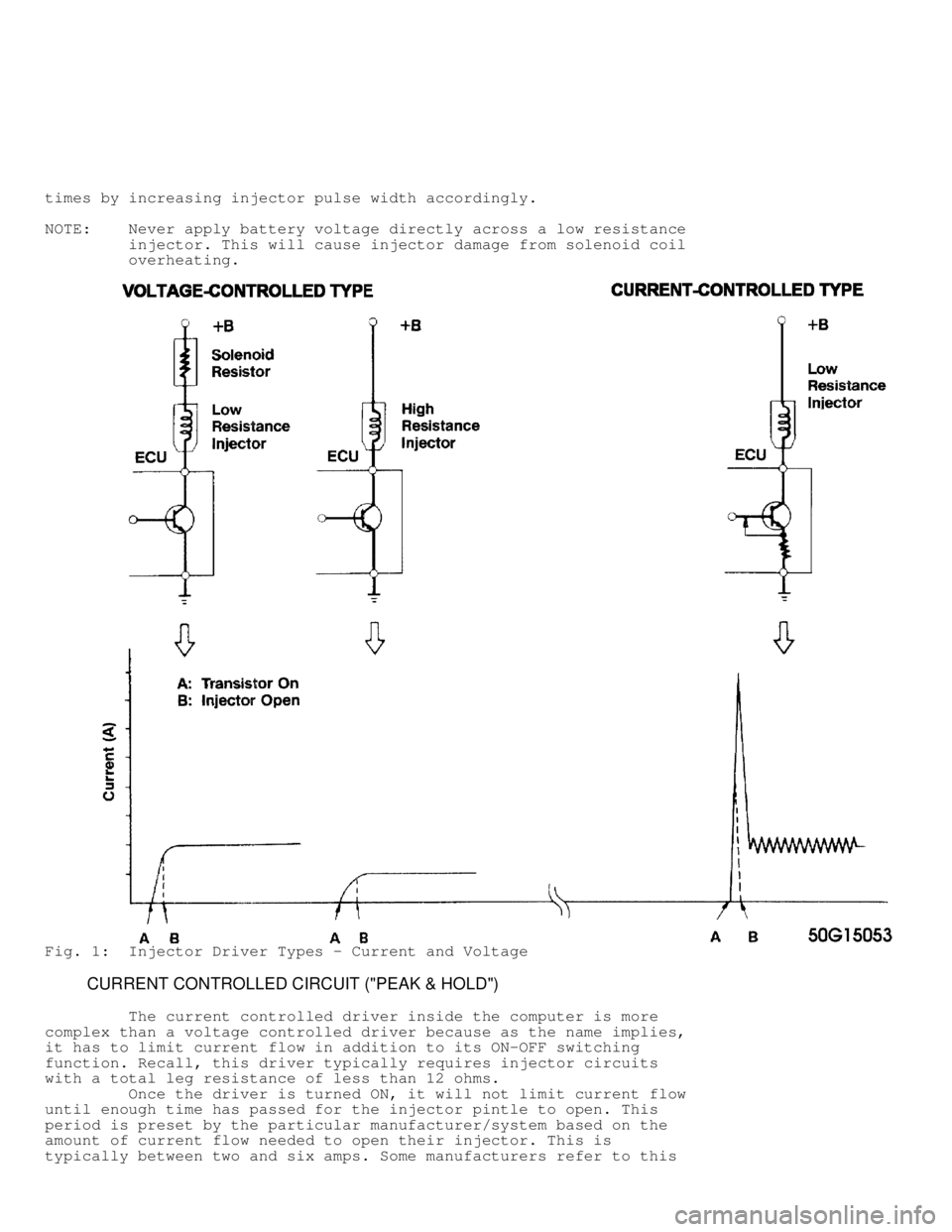
times by increasing injector pulse width accordingly.
NOTE: Never apply battery voltage directly across a low resistance
injector. This will cause injector damage from solenoid coil
overheating.
Fig. 1: Injector Driver Types - Current and Voltage
CURRENT CONTROLLED CIRCUIT ("PEAK & HOLD")
The current controlled driver inside the computer is more
complex than a voltage controlled driver because as the name implies,
it has to limit current flow in addition to its ON-OFF switching
function. Recall, this driver typically requires injector circuits
with a total leg resistance of less than 12 ohms.
Once the driver is turned ON, it will not limit current flow
until enough time has passed for the injector pintle to open. This
period is preset by the particular manufacturer/system based on the
amount of current flow needed to open their injector. This is
typically between two and six amps. Some manufacturers refer to this
Page 1474 of 1501
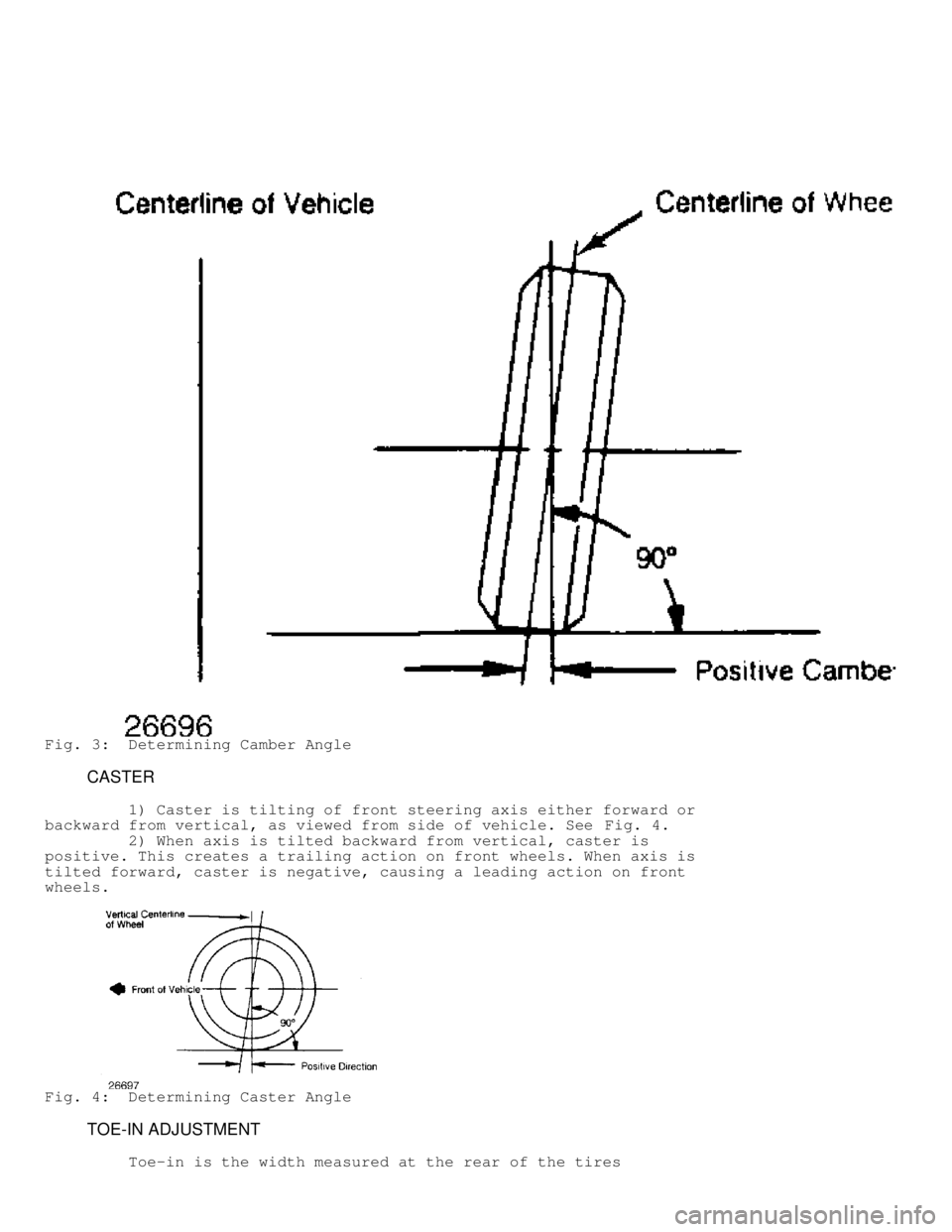
Fig. 3: Determining Camber Angle
CASTER
1) Caster is tilting of front steering axis either forward or
backward from vertical, as viewed from side of vehicle. See Fig. 4.
2) When axis is tilted backward from vertical, caster is
positive. This creates a trailing action on front wheels. When axis is
tilted forward, caster is negative, causing a leading action on front
wheels.
Fig. 4: Determining Caster Angle
TOE-IN ADJUSTMENT
Toe-in is the width measured at the rear of the tires
Page 1475 of 1501
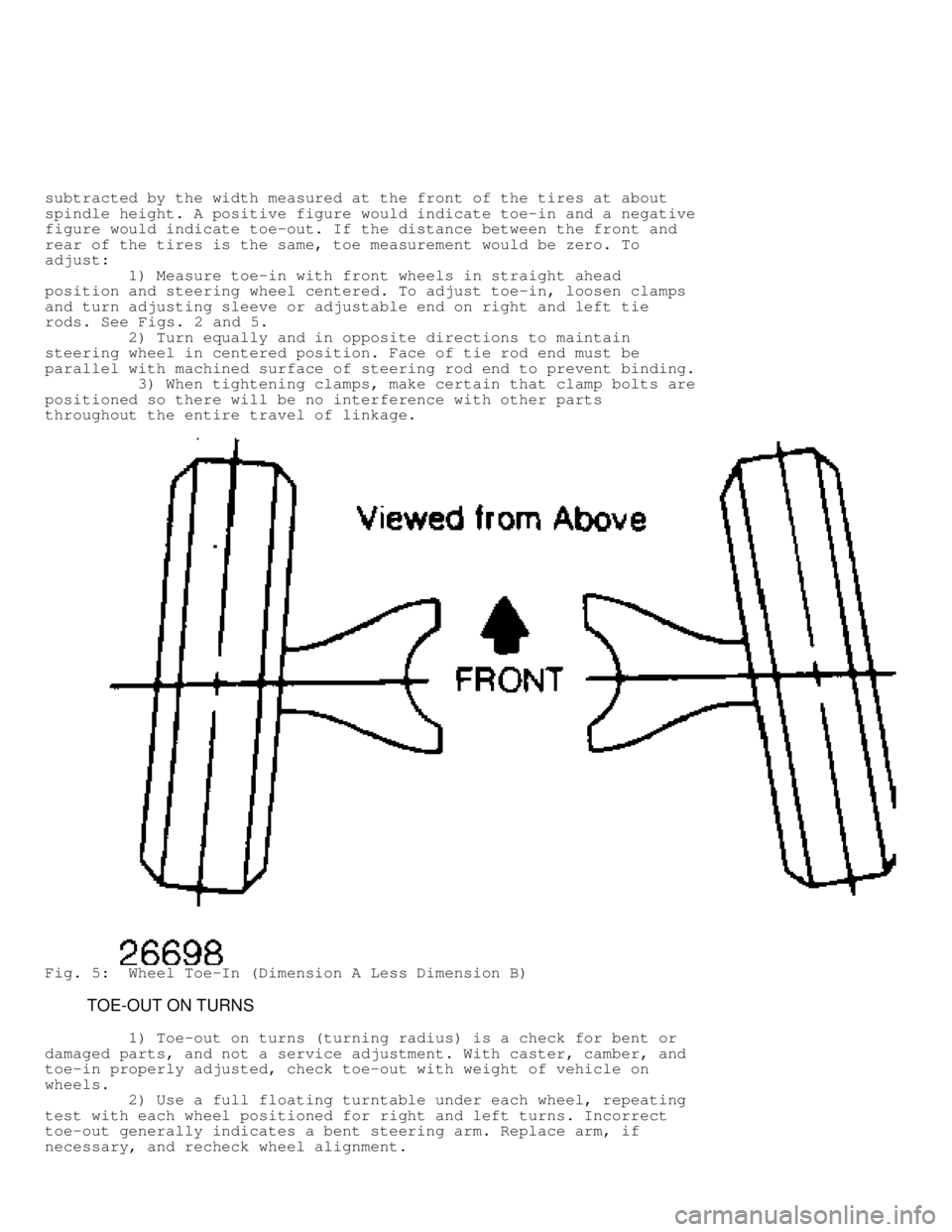
subtracted by the width measured at the front of the tires at about
spindle height. A positive figure would indicate toe-in and a negative
figure would indicate toe-out. If the distance between the front and
rear of the tires is the same, toe measurement would be zero. To
adjust:
1) Measure toe-in with front wheels in straight ahead
position and steering wheel centered. To adjust toe-in, loosen clamps
and turn adjusting sleeve or adjustable end on right and left tie
rods. See Figs. 2 and 5.
2) Turn equally and in opposite directions to maintain
steering wheel in centered position. Face of tie rod end must be
parallel with machined surface of steering rod end to prevent binding.
3) When tightening clamps, make certain that clamp bolts are
positioned so there will be no interference with other parts
throughout the entire travel of linkage.
Fig. 5: Wheel Toe-In (Dimension A Less Dimension B)
TOE-OUT ON TURNS
1) Toe-out on turns (turning radius) is a check for bent or
damaged parts, and not a service adjustment. With caster, camber, and
toe-in properly adjusted, check toe-out with weight of vehicle on
wheels.
2) Use a full floating turntable under each wheel, repeating
test with each wheel positioned for right and left turns. Incorrect
toe-out generally indicates a bent steering arm. Replace arm, if
necessary, and recheck wheel alignment.