compression ratio OPEL GT-R 1973 Service Manual
[x] Cancel search | Manufacturer: OPEL, Model Year: 1973, Model line: GT-R, Model: OPEL GT-R 1973Pages: 625, PDF Size: 17.22 MB
Page 20 of 625
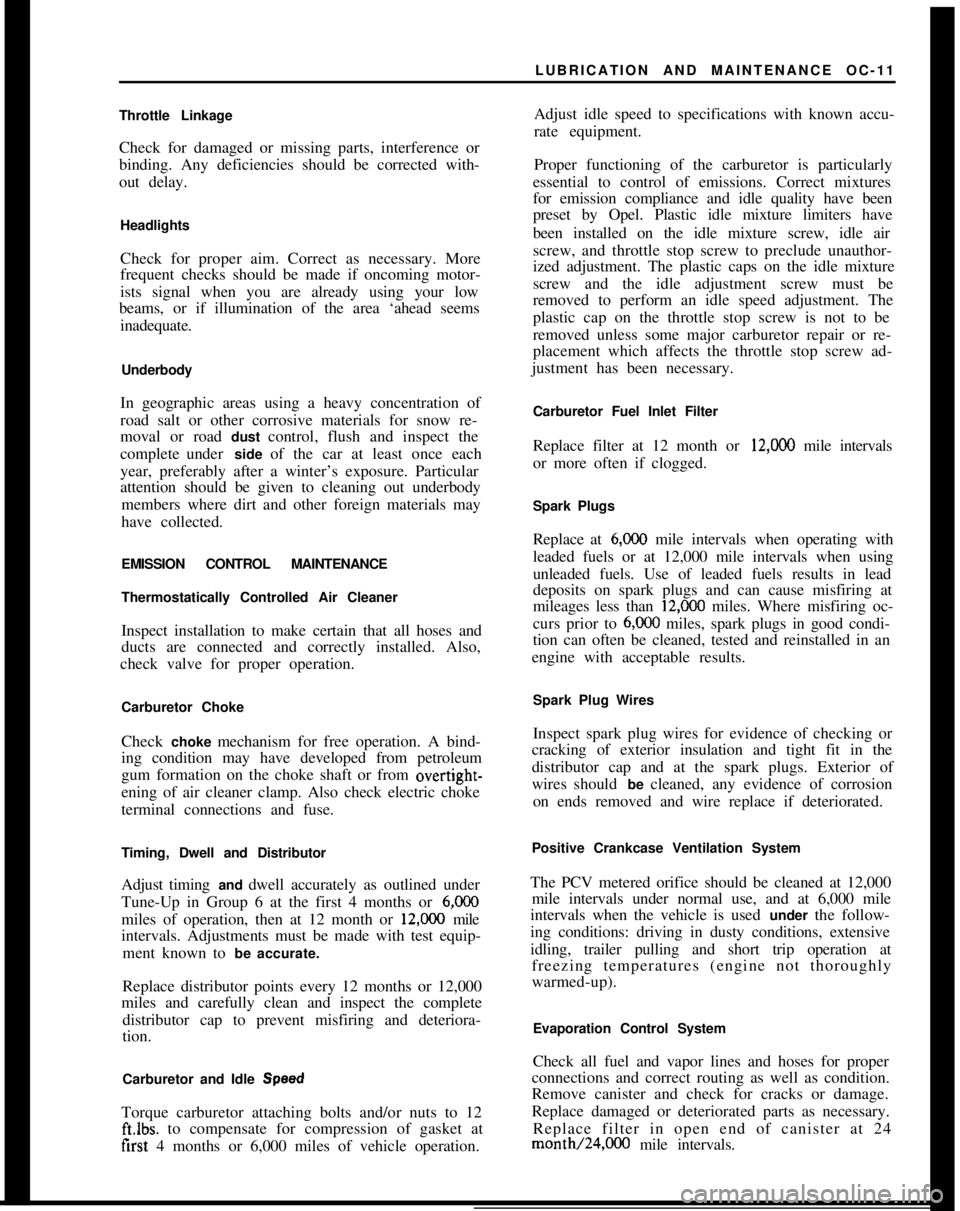
LUBRICATION AND MAINTENANCE OC-11
Throttle Linkage
Check for damaged or missing parts, interference or
binding. Any deficiencies should be corrected with-
out delay.
Headlights
Check for proper aim. Correct as necessary. More
frequent checks should be made if oncoming motor-
ists signal when you are already using your low
beams, or if illumination of the area ‘ahead seems
inadequate.
Underbody
In geographic areas using a heavy concentration of
road salt or other corrosive materials for snow re-
moval or road dust control, flush and inspect the
complete under side of the car at least once each
year, preferably after a winter’s exposure. Particular
attention should be given to cleaning out underbody
members where dirt and other foreign materials may
have collected.
EMISSION CONTROL MAINTENANCE
Thermostatically Controlled Air Cleaner
Inspect installation to make certain that all hoses and
ducts are connected and correctly installed. Also,
check valve for proper operation.
Carburetor Choke
Check choke mechanism for free operation. A bind-
ing condition may have developed from petroleum
gum formation on the choke shaft or from overtight-
ening of air cleaner clamp. Also check electric choke
terminal connections and fuse.
Timing, Dwell and Distributor
Adjust timing and dwell accurately as outlined under
Tune-Up in Group 6 at the first 4 months or 6,ooOmiles of operation, then at 12 month or
12,OQO mile
intervals. Adjustments must be made with test equip-
ment known to be accurate.
Replace distributor points every 12 months or 12,000
miles and carefully clean and inspect the complete
distributor cap to prevent misfiring and deteriora-
tion.
Carburetor and Idle
SpeedTorque carburetor attaching bolts and/or nuts to 12
ft.lbs. to compensate for compression of gasket atiirst 4 months or 6,000 miles of vehicle operation.Adjust idle speed to specifications with known accu-
rate equipment.
Proper functioning of the carburetor is particularly
essential to control of emissions. Correct mixtures
for emission compliance and idle quality have been
preset by Opel. Plastic idle mixture limiters have
been installed on the idle mixture screw, idle air
screw, and throttle stop screw to preclude unauthor-
ized adjustment. The plastic caps on the idle mixture
screw and the idle adjustment screw must be
removed to perform an idle speed adjustment. The
plastic cap on the throttle stop screw is not to be
removed unless some major carburetor repair or re-
placement which affects the throttle stop screw ad-
justment has been necessary.
Carburetor Fuel Inlet Filter
Replace filter at 12 month or
12,OCO mile intervals
or more often if clogged.
Spark Plugs
Replace at
6,ooO mile intervals when operating with
leaded fuels or at 12,000 mile intervals when using
unleaded fuels. Use of leaded fuels results in lead
deposits on spark plugs and can cause misfiring at
mileages less than
12,OilO miles. Where misfiring oc-
curs prior to
6,ooO miles, spark plugs in good condi-
tion can often be cleaned, tested and reinstalled in an
engine with acceptable results.
Spark Plug Wires
Inspect spark plug wires for evidence of checking or
cracking of exterior insulation and tight fit in the
distributor cap and at the spark plugs. Exterior of
wires should be cleaned, any evidence of corrosion
on ends removed and wire replace if deteriorated.
Positive Crankcase Ventilation System
The PCV metered orifice should be cleaned at 12,000
mile intervals under normal use, and at 6,000 mile
intervals when the vehicle is used under the follow-
ing conditions: driving in dusty conditions, extensive
idling, trailer pulling and short trip operation at
freezing temperatures (engine not thoroughly
warmed-up).
Evaporation Control System
Check all fuel and vapor lines and hoses for proper
connections and correct routing as well as condition.
Remove canister and check for cracks or damage.
Replace damaged or deteriorated parts as necessary.
Replace filter in open end of canister at 24month/24,000 mile intervals.
Page 21 of 625
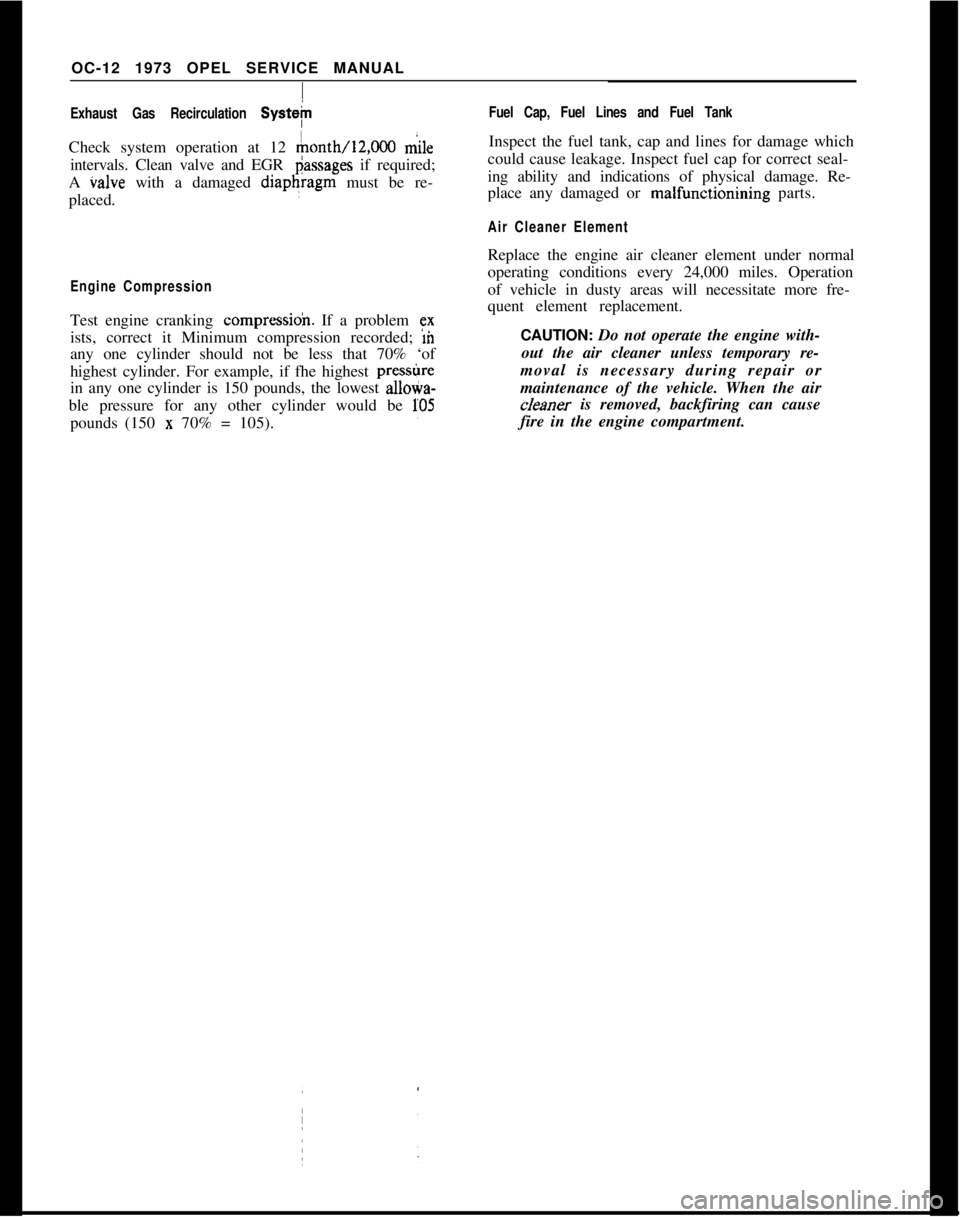
!
OC-12 1973 OPEL SERVICE MANUAL iExhaust Gas Recirculation Systep
Check system operation at 12 &onth/12,000 mile
intervals. Clean valve and EGR &usages if required;
A valve with a damaged diaphragm must be re-
placed.I
Engine CompressionTest engine cranking compressi& If a problem
exists, correct it Minimum compression recorded;
many one cylinder should not be less that 70% ‘of
highest cylinder. For example, if fhe highest presstire
in any one cylinder is 150 pounds, the lowest
alloka-ble pressure for any other cylinder would be
l-05pounds (150
x 70% = 105).~
Fuel Cap, Fuel Lines and Fuel TankInspect the fuel tank, cap and lines for damage which
could cause leakage. Inspect fuel cap for correct seal-
ing ability and indications of physical damage. Re-
place any damaged or malfunctionining parts.
Air Cleaner ElementReplace the engine air cleaner element under normal
operating conditions every 24,000 miles. Operation
of vehicle in dusty areas will necessitate more fre-
quent element replacement.
CAUTION: Do not operate the engine with-
out the air cleaner unless temporary re-
moval is necessary during repair or
maintenance of the vehicle. When the aircIeaner is removed, backfiring can cause
fire in the engine compartment.
Page 293 of 625
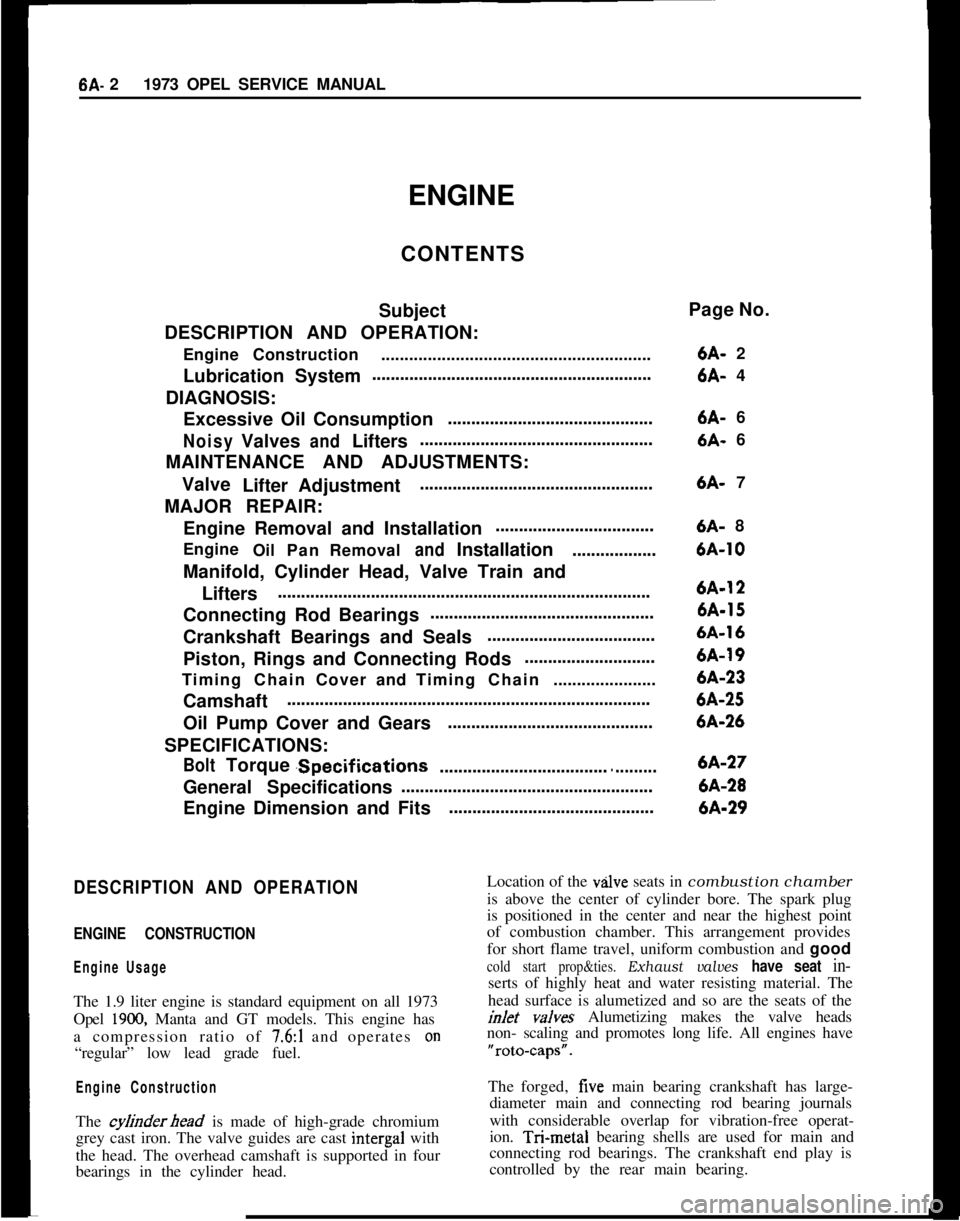
6A- 21973 OPEL SERVICE MANUAL
ENGINE
CONTENTS
Subject
DESCRIPTION AND OPERATION:
EngineConstruction..........................................................
LubricationSystem............................................................
DIAGNOSIS:
Excessive Oil Consumption............................................NoisyValvesandLifters..................................................
MAINTENANCE AND ADJUSTMENTS:
Valve
LifterAdjustment..................................................
MAJOR REPAIR:
Engine Removal and Installation..................................
Engine
OilPanRemoval
andInstallation..................
Manifold, Cylinder Head, Valve Train and
Lifters................................................................................
Connecting Rod Bearings................................................
Crankshaft Bearings and Seals....................................
Piston, Rings and Connecting Rods............................
TimingChainCoverandTimingChain......................
Camshaft..............................................................................
Oil Pump Cover and Gears............................................
SPECIFICATIONS:
BoltTorque.Specifications
..............................................General Specifications......................................................
Engine Dimension and Fits............................................Page No.
6A- 2
6A- 4
6A- 6
6A- 6
6A- 7
6A- 86A-106A-126A-156A-166A-196A-236A-256A-266A-276A-286A-29
DESCRIPTION AND OPERATION
ENGINE CONSTRUCTION
Engine UsageThe 1.9 liter engine is standard equipment on all 1973
Opel
1900, Manta and GT models. This engine has
a compression ratio of
7.6:1 and operates on“regular” low lead grade fuel.
Engine ConstructionThe
cyfinderhead is made of high-grade chromium
grey cast iron. The valve guides are cast intergal with
the head. The overhead camshaft is supported in four
bearings in the cylinder head.Location of the
vzllve seats in combustion chamber
is above the center of cylinder bore. The spark plug
is positioned in the center and near the highest point
of combustion chamber. This arrangement provides
for short flame travel, uniform combustion and good
cold start prop&ties. Exhaust valves have seat in-serts of highly heat and water resisting material. The
head surface is alumetized and so are the seats of the
inlet v&es Alumetizing makes the valve heads
non- scaling and promotes long life. All engines have“rota-caps”.
The forged, five main bearing crankshaft has large-
diameter main and connecting rod bearing journals
with considerable overlap for vibration-free operat-
ion. T&metal bearing shells are used for main and
connecting rod bearings. The crankshaft end play is
controlled by the rear main bearing.
Page 311 of 625
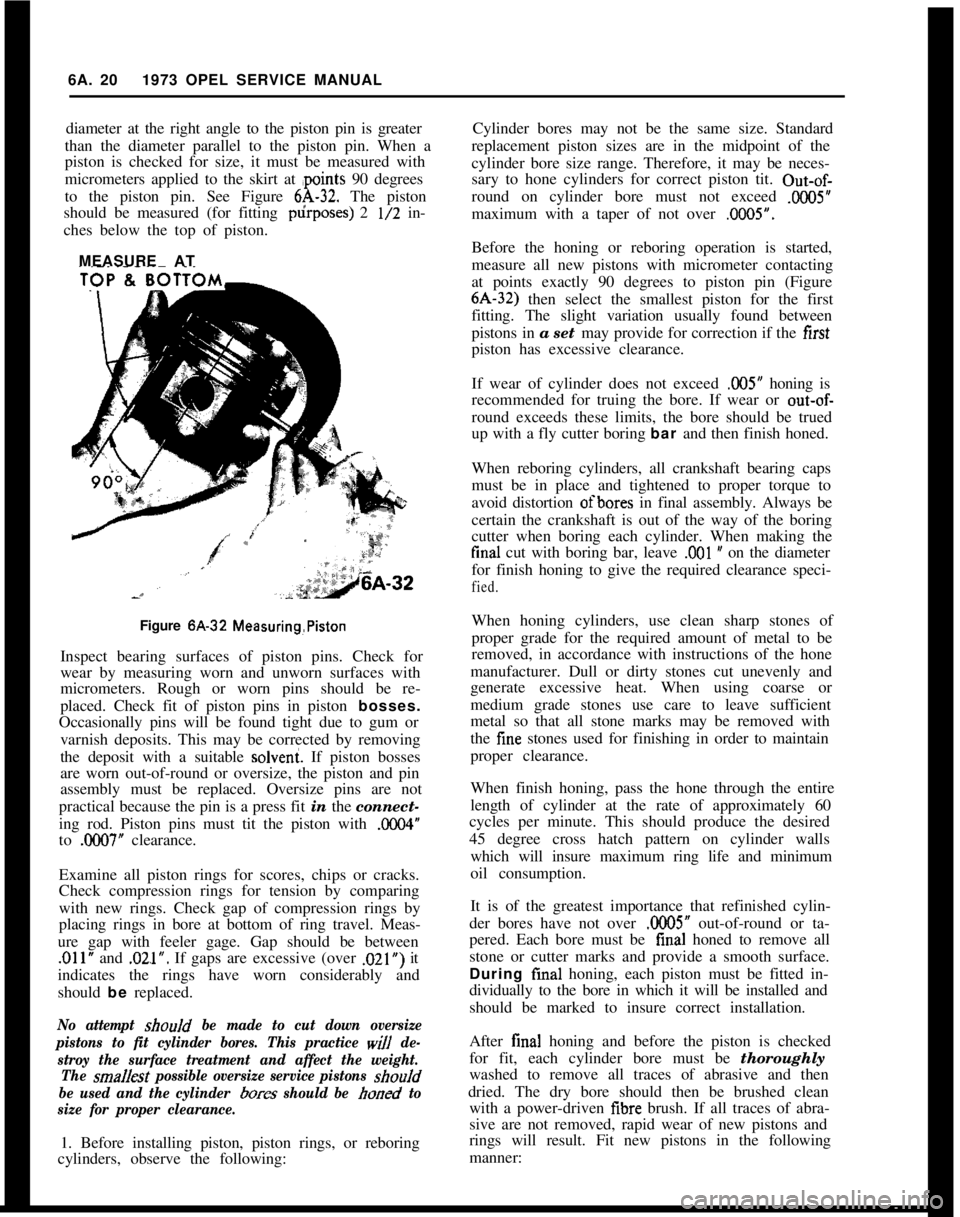
6A. 201973 OPEL SERVICE MANUAL
diameter at the right angle to the piston pin is greater
than the diameter parallel to the piston pin. When a
piston is checked for size, it must be measured with
micrometers applied to the skirt at ,points 90 degrees
to the piston pin. See Figure
6A-32. The piston
should be measured (for fitting p&poses) 2
l/2 in-
ches below the top of piston.
MEASURE AT
Figure 6A-32
Measuring,PistonInspect bearing surfaces of piston pins. Check for
wear by measuring worn and unworn surfaces with
micrometers. Rough or worn pins should be re-
placed. Check fit of piston pins in piston bosses.
Occasionally pins will be found tight due to gum or
varnish deposits. This may be corrected by removing
the deposit with a suitable solveni. If piston bosses
are worn out-of-round or oversize, the piston and pin
assembly must be replaced. Oversize pins are not
practical because the pin is a press fit in the connect-
ing rod. Piston pins must tit the piston with
0X4”to
.OCHl7” clearance.
Examine all piston rings for scores, chips or cracks.
Check compression rings for tension by comparing
with new rings. Check gap of compression rings by
placing rings in bore at bottom of ring travel. Meas-
ure gap with feeler gage. Gap should be between
,011” and .02.1”. If gaps are excessive (over .021”) it
indicates the rings have worn considerably and
should be replaced.
No attempt should be made to cut down oversize
pistons to fit cylinder bores. This practice
will de-
stroy the surface treatment and affect the weight.
The
sma/Jest possible oversize service pistons shouId
be used and the cylinder
bores should be honed to
size for proper clearance.1. Before installing piston, piston rings, or reboring
cylinders, observe the following:Cylinder bores may not be the same size. Standard
replacement piston sizes are in the midpoint of the
cylinder bore size range. Therefore, it may be neces-
sary to hone cylinders for correct piston tit. Out-of-
round on cylinder bore must not exceed
.ooO5”maximum with a taper of not over
.OilO5”.Before the honing or reboring operation is started,
measure all new pistons with micrometer contacting
at points exactly 90 degrees to piston pin (Figure6A-32) then select the smallest piston for the first
fitting. The slight variation usually found between
pistons in a set may provide for correction if the first
piston has excessive clearance.
If wear of cylinder does not exceed
.005” honing is
recommended for truing the bore. If wear or
out-of-round exceeds these limits, the bore should be trued
up with a fly cutter boring bar and then finish honed.
When reboring cylinders, all crankshaft bearing caps
must be in place and tightened to proper torque to
avoid distortion ofbores in final assembly. Always be
certain the crankshaft is out of the way of the boring
cutter when boring each cylinder. When making thefinal cut with boring bar, leave
,001 w on the diameter
for finish honing to give the required clearance speci-
fied.When honing cylinders, use clean sharp stones of
proper grade for the required amount of metal to be
removed, in accordance with instructions of the hone
manufacturer. Dull or dirty stones cut unevenly and
generate excessive heat. When using coarse or
medium grade stones use care to leave sufficient
metal so that all stone marks may be removed with
the fine stones used for finishing in order to maintain
proper clearance.
When finish honing, pass the hone through the entire
length of cylinder at the rate of approximately 60
cycles per minute. This should produce the desired
45 degree cross hatch pattern on cylinder walls
which will insure maximum ring life and minimum
oil consumption.
It is of the greatest importance that refinished cylin-
der bores have not over
.0005” out-of-round or ta-
pered. Each bore must be final honed to remove all
stone or cutter marks and provide a smooth surface.
During final honing, each piston must be fitted in-
dividually to the bore in which it will be installed and
should be marked to insure correct installation.
After final honing and before the piston is checked
for fit, each cylinder bore must be thoroughly
washed to remove all traces of abrasive and then
dried. The dry bore should then be brushed clean
with a power-driven iibre brush. If all traces of abra-
sive are not removed, rapid wear of new pistons and
rings will result. Fit new pistons in the following
manner:
Page 313 of 625
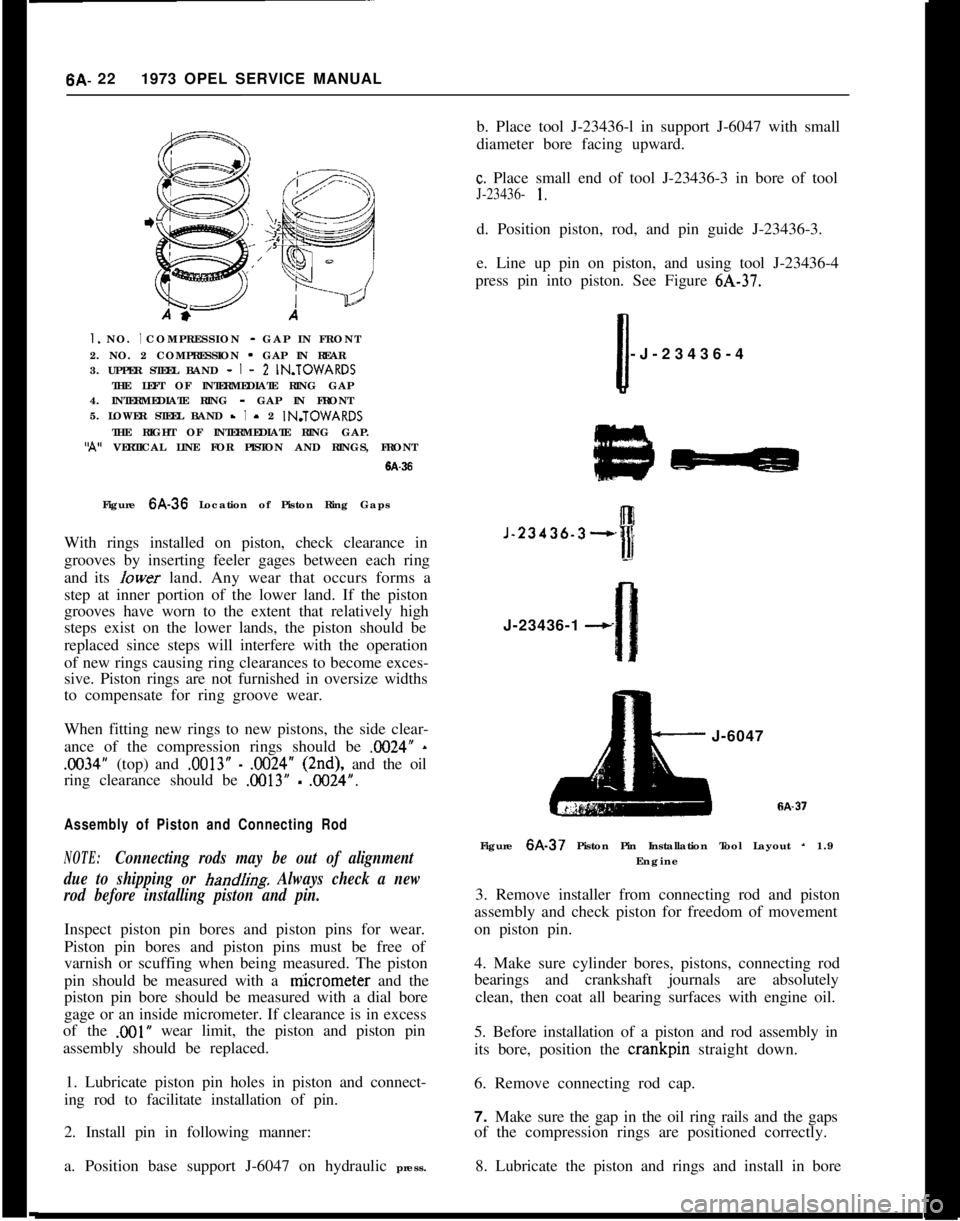
6A- 221973 OPEL SERVICE MANUALI. NO. I COMPRESSION - GAP IN FRONT
2. NO. 2 COMPRESSION - GAP IN REAR
3. UPPER STEEL BAND -
I - 2 IN.TOWARDS
THE LEFT OF INTERMEDIATE RING GAP
4. INTERMEDIATE RING - GAP IN FRONT
5. LOWER STEEL BAND -
I - 2 IN.TOWARDS
THE RIGHT OF INTERMEDIATE RING GAP.‘A” VERTICAL LINE FOR PISTON AND RINGS, FRONT
6A-36Figure 6A-36 Location of Piston Ring Gaps
With rings installed on piston, check clearance in
grooves by inserting feeler gages between each ring
and its Iower land. Any wear that occurs forms a
step at inner portion of the lower land. If the piston
grooves have worn to the extent that relatively high
steps exist on the lower lands, the piston should be
replaced since steps will interfere with the operation
of new rings causing ring clearances to become exces-
sive. Piston rings are not furnished in oversize widths
to compensate for ring groove wear.
When fitting new rings to new pistons, the side clear-
ance of the compression rings should be X024”
-
.1X34” (top) and .0013” - .OO24” (2nd), and the oil
ring clearance should be
.OO13” - .0024”.
Assembly of Piston and Connecting Rod
NOTE:Connecting rods may be out of alignment
due to shipping or
hand/i& Always check a new
rod before installing piston and pin.Inspect piston pin bores and piston pins for wear.
Piston pin bores and piston pins must be free of
varnish or scuffing when being measured. The piston
pin should be measured with a niicrometer and the
piston pin bore should be measured with a dial bore
gage or an inside micrometer. If clearance is in excess
of the
,001” wear limit, the piston and piston pin
assembly should be replaced.
1. Lubricate piston pin holes in piston and connect-
ing rod to facilitate installation of pin.
2. Install pin in following manner:
a. Position base support J-6047 on hydraulic press.b. Place tool J-23436-l in support J-6047 with small
diameter bore facing upward.
c. Place small end of tool J-23436-3 in bore of tool
J-23436- 1.d. Position piston, rod, and pin guide J-23436-3.
e. Line up pin on piston, and using tool J-23436-4
press pin into piston. See Figure 6A-37.
Ii-J-23436-4
J-23436-3--,J-23436-1
--cJ-6047
Figure 6A-37 Piston Pin Installation Tool Layout
- 1.9
Engine
3. Remove installer from connecting rod and piston
assembly and check piston for freedom of movement
on piston pin.
4. Make sure cylinder bores, pistons, connecting rod
bearings and crankshaft journals are absolutely
clean, then coat all bearing surfaces with engine oil.
5. Before installation of a piston and rod assembly in
its bore, position the crankpin straight down.
6. Remove connecting rod cap.
7. Make sure the gap in the oil ring rails and the gaps
of the compression rings are positioned correctly.
8. Lubricate the piston and rings and install in bore
Page 319 of 625
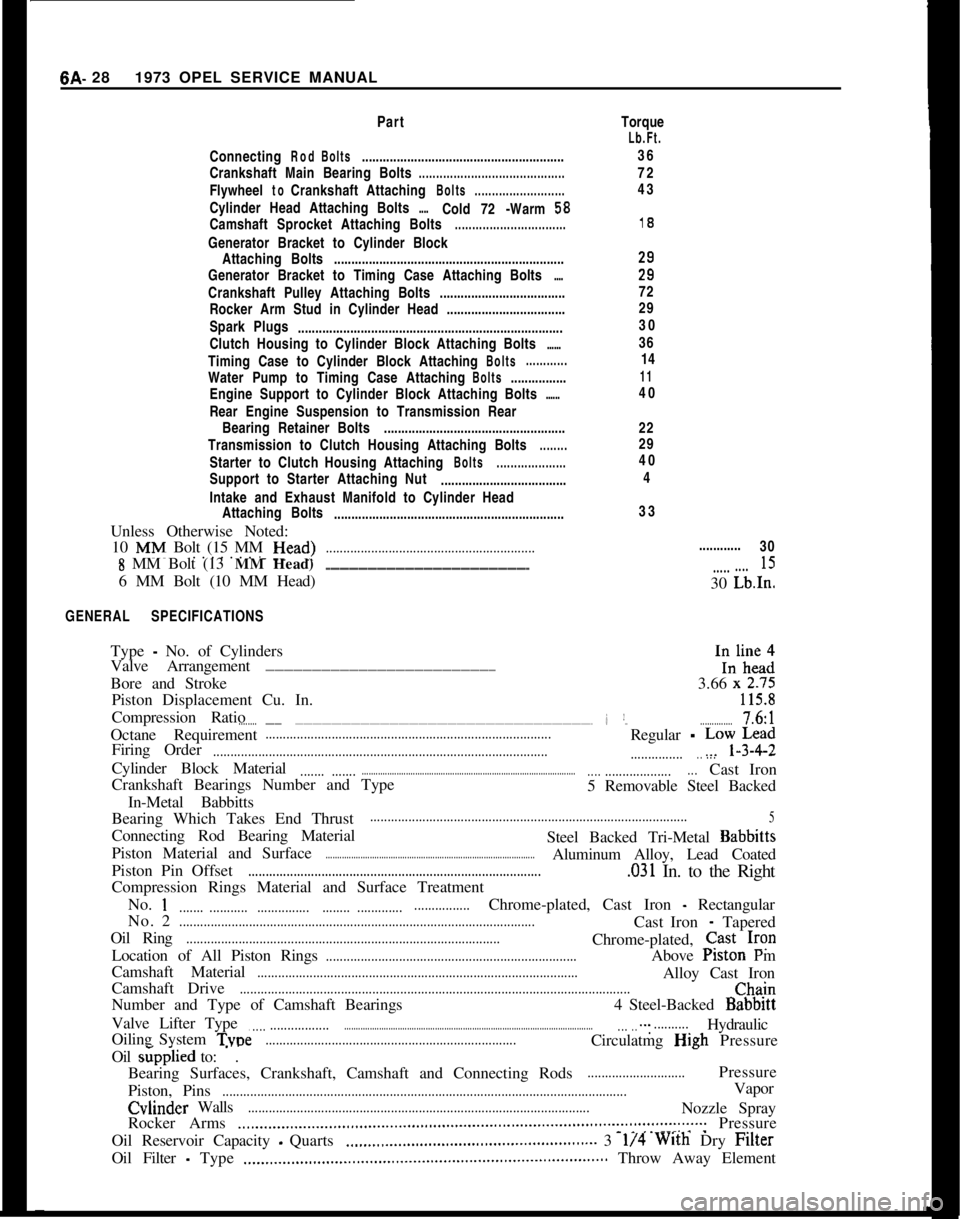
6A- 28 1973 OPEL SERVICE MANUAL
Part
ConnectingRod Bolts..........................................................
Crankshaft Main Bearing Bolts
..........................................
FlywheeltoCrankshaft AttachingBolts..........................
Cylinder Head Attaching Bolts....Cold 72 -Warm 58
Camshaft Sprocket Attaching Bolts................................
Generator Bracket to Cylinder Block
Attaching Bolts ..................................................................
Generator Bracket to Timing Case Attaching Bolts
....
Crankshaft Pulley Attaching Bolts ....................................
Rocker Arm Stud in Cylinder Head ..................................
Spark Plugs ........................................................................\
....
Clutch Housing to Cylinder Block Attaching Bolts
......
Timing Case to Cylinder Block AttachingBolts ............
Water Pump to Timing Case AttachingBolts................
Engine Support to Cylinder Block Attaching Bolts
......
Rear Engine Suspension to Transmission Rear Bearing Retainer Bolts ....................................................
Transmission to Clutch Housing Attaching Bolts
........
Starter to ClutchHousing AttachingBolts....................
Support to Starter Attaching Nut
....................................
Intake and Exhaust Manifold to Cylinder Head Attaching Bolts ..................................................................
Unless Otherwise Noted:
10
@i Bolt (15 MM Hall.....................................................................- -
36
72
43
18
;i
72
29
30
36
14
11
40
22
29
40
4
33 ............30
8 MM Bolt (13 MM Head)........................................................................\
........................................................................\
........................................15
6 MM Bolt (10 MM Head)
30 Lb.In.
Torque
Lb.Ft.
GENERAL SPECIFICATIONS
Type - No. of Cylinders
Valve Arrangement........................................................................\
........................................................................\
......................................................I;nlinzai
Bore and Stroke Piston Displacement Cu. In.
........
3.66 x1:;:;
Compression Ratio......................................................................................\
........................................................................\
........................................................................\
........................................ \fô \
²…..............7.6:1Octane Requirement........................................................................\
..........
Firing Order........................................................................\
........................
Regular - Lo;-?::
....................Cylinder Block Material....... ...............................................................................\
..............................................Cast Iron
Crankshaft Bearings Number and Type 5 Removable Steel Backed
In-Metal Babbitts
Bearing Which Takes End Thrust
........................................................................\
...................5
Connecting Rod Bearing Material
........................................................................\
..................
Steel Backed Tri-Metal Babbttts
Piston Material and Surface Aluminum Alloy, Lead Coated
Piston Pin Offset
........................................................................\
............,031 In. to the RightCompression Rings Material and Surface Treatment
No.
1....... ........... ............... ........ ............. ................Chrome-plated, Cast Iron
- Rectangular
No. 2
........................................................................\
..............................Cast Iron - Tapered
Oil Ring
........................................................................\
..................Chrome-plated, Cast Ir?n
Location of All Piston Rings
........................................................................\
Above Ptston Pm
Camshaft Material
........................................................................\
....................Alloy Cast Iron
Camshaft Drive........................................................................\
........................................Chajn
Number and Type of Camshaft Bearings 4 Steel-Backed Babbttt
Valve Lifter Type
..............................................................................................\
..........................................~..........Hydraulic
Oiling System Tvoe........................................................................\
Circulatmg High Pressure
Oil
&ppiied to: - .
Bearing Surfaces, Crankshaft, Camshaft and Connecting Rods............................Pressure
Piston, Pins
........................................................................\
............................................Vapor
Cvlinder Walls........................................................................\
..........................Nozzle Spray
Rocker Arms _,,,..,,....,._..___.,,..,,..............,,,,...,.......,..,,,.,.,,.....\
....,,...,.,.................~...... Pressure
Oil Reservoir Capacity
- Quarts .,,,...,,__.,,..,..,,..,...,..,,,...,,..............,,,... 3 l/4 With Dry Fdter
Oil Filter
- Type ,,....,__.,,...,....,....,,..,,,..,,...........,........................\
............ Throw Away Element
Page 349 of 625
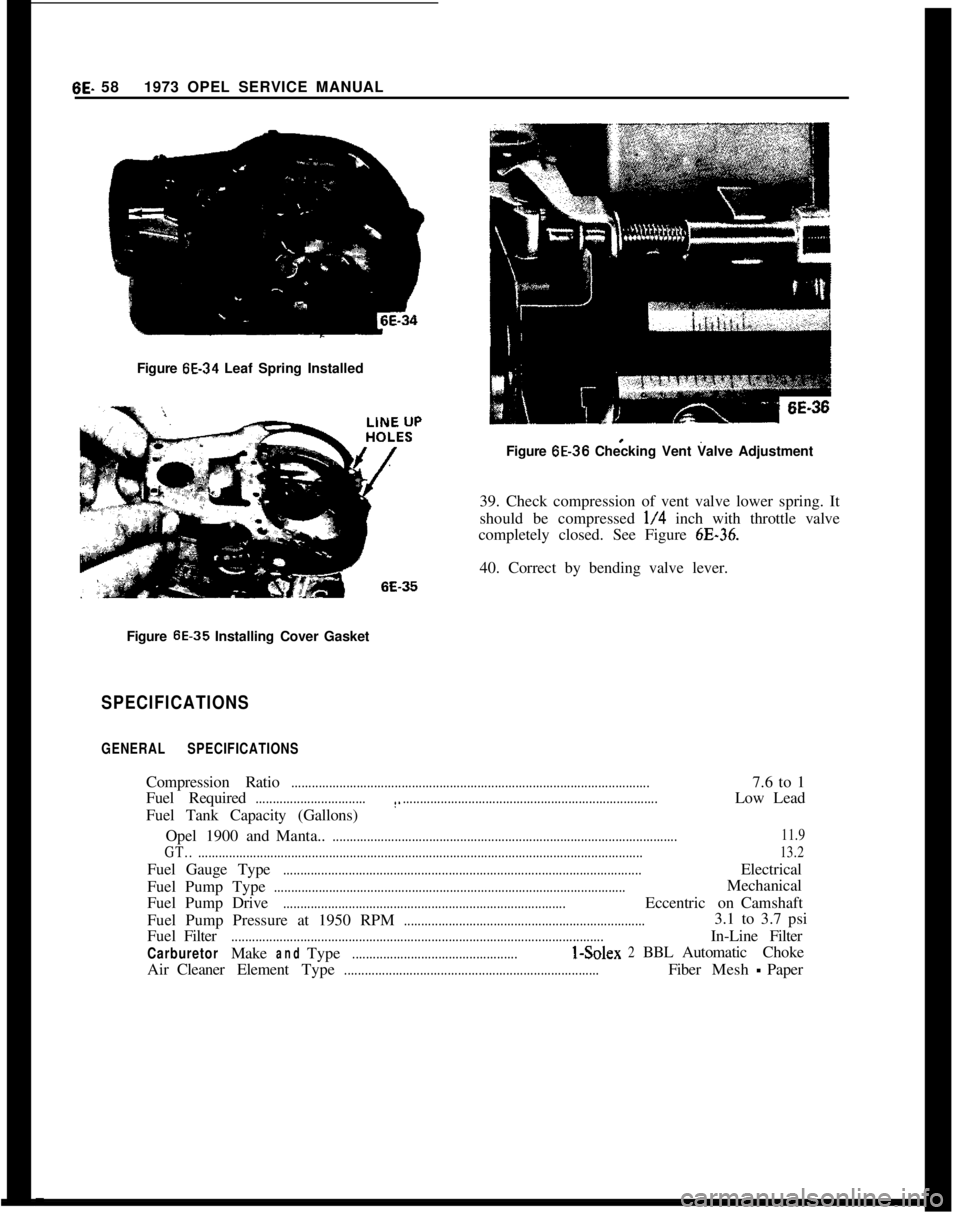
6E- 581973 OPEL SERVICE MANUAL
Figure 6E-34 Leaf Spring Installed
1 6E-36
Figure 6E-36 Checking Vent Valve Adjustment
39. Check compression of vent valve lower spring. It
should be compressed
l/4 inch with throttle valve
completely closed. See Figure
6E-36.40. Correct by bending valve lever.
Figure
6E-35 Installing Cover Gasket
SPECIFICATIONS
GENERAL SPECIFICATIONSCompression Ratio
........................................................................................................7.6 to 1
Fuel Required
................................(...........................................................................Low Lead
Fuel Tank Capacity (Gallons)
Opel1900andManta..
....................................................................................................11.9
GT...................................................................................................................................13.2Fuel Gauge Type
........................................................................................................Electrical
FuelPumpType
......................................................................................................Mechanical
FuelPumpDrive
..................................................................................EccentriconCamshaft
Fuel Pump Pressure at 1950 RPM
......................................................................3.1 to 3.7 psi
FuelFilter
............................................................................................................In-LineFilter
CarburetorMakeandType................................................I-Solex2BBLAutomaticChoke
AirCleanerElementType
..........................................................................FiberMesh-Paper
Page 356 of 625
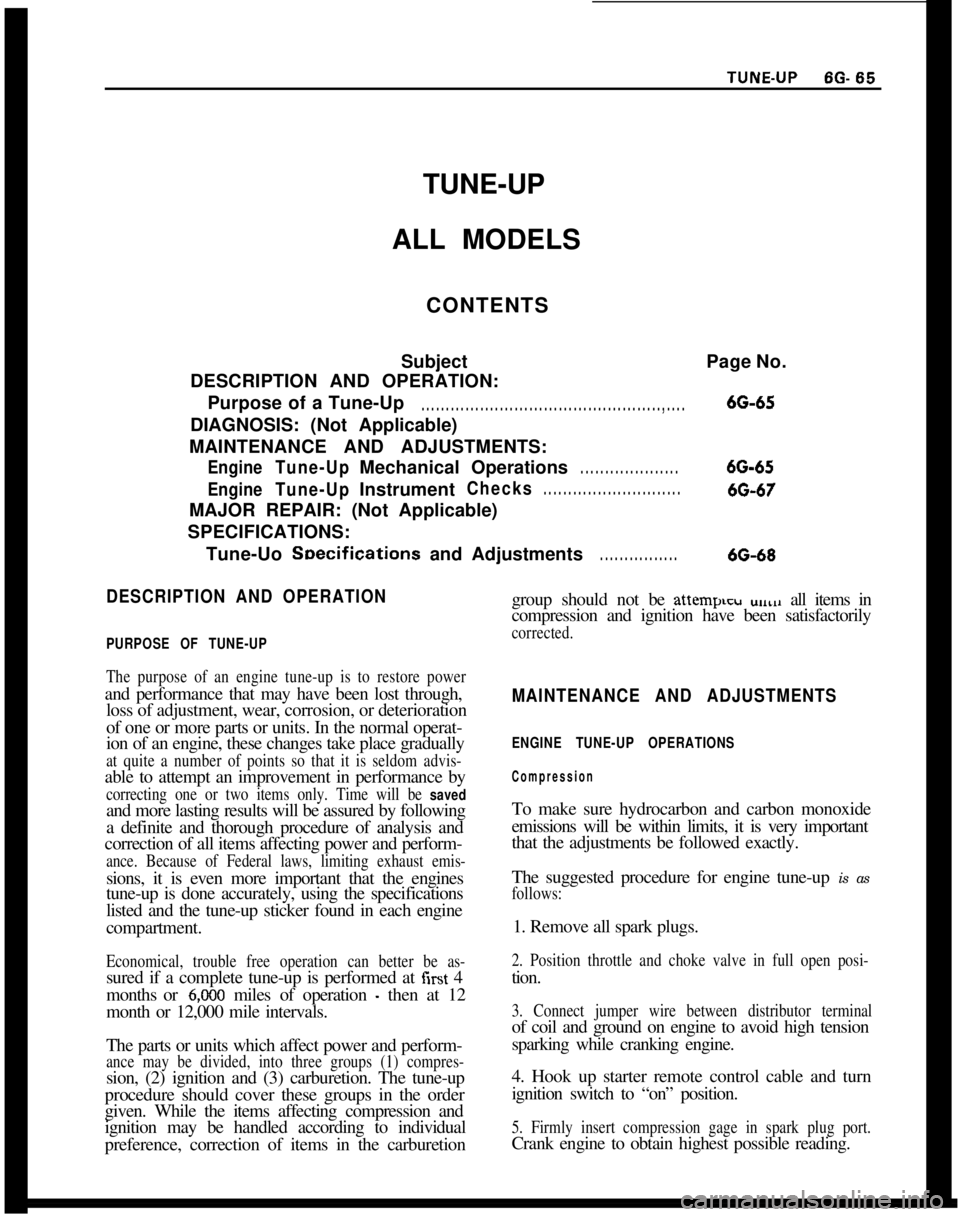
TUNE-UP
ALL MODELS
CONTENTS
Subject
DESCRIPTION AND OPERATION:
Purpose of a Tune-Up. . . . . . . . . . . . . . . . . . . . . . . . . . . . . . . . . . . . . . . . . . . . . . . . . , . . . .DIAGNOSIS: (Not Applicable)
MAINTENANCE AND ADJUSTMENTS:
EngineTune-UpMechanicalOperations. . . . . . . . . . . . . . . . . . . .
EngineTune-UpInstrumentChecks. . . . . . . . . . . . . . . . . . . . . . . . . . . .MAJOR REPAIR: (Not Applicable)
SPECIFICATIONS:
Tune-Uo Soecifications and Adjustments
. . . . . . . . . . . . . . . .Page No.6G-65
6G-6566-6766-68
DESCRIPTION AND OPERATION
PURPOSE OF TUNE-UP
The purpose of an engine tune-up is to restore powerand performance that may have been lost through,
loss of adjustment, wear, corrosion, or deterioration
of one or more parts or units. In the normal operat-
ion of an engine, these changes take place gradually
at quite a number of points so that it is seldom advis-able to attempt an improvement in performance by
correcting one or two items only. Time will be savedand more lasting results will be assured by following
a definite and thorough procedure of analysis and
correction of all items affecting power and perform-
ance. Because of Federal laws, limiting exhaust emis-sions, it is even more important that the engines
tune-up is done accurately, using the specifications
listed and the tune-up sticker found in each engine
compartment.
Economical, trouble free operation can better be as-sured if a complete tune-up is performed at first 4
months or
6,ooO miles of operation - then at 12
month or 12,000 mile intervals.
The parts or units which affect power and perform-
ance may be divided, into three groups (1) compres-sion, (2) ignition and (3) carburetion. The tune-up
procedure should cover these groups in the order
given. While the items affecting compression and
ignition may be handled according to individual
preference, correction of items in the carburetiongroup should not be attemplcu
ulllll all items in
compression and ignition have been satisfactorily
corrected.
MAINTENANCE AND ADJUSTMENTS
ENGINE TUNE-UP OPERATIONS
CompressionTo make sure hydrocarbon and carbon monoxide
emissions will be within limits, it is very important
that the adjustments be followed exactly.
The suggested procedure for engine tune-up is as
follows:1. Remove all spark plugs.
2. Position throttle and choke valve in full open posi-tion.
3. Connect jumper wire between distributor terminalof coil and ground on engine to avoid high tension
sparking while cranking engine.
4. Hook up starter remote control cable and turn
ignition switch to “on” position.
5. Firmly insert compression gage in spark plug port.Crank engine to obtain highest possible reading.
Page 537 of 625
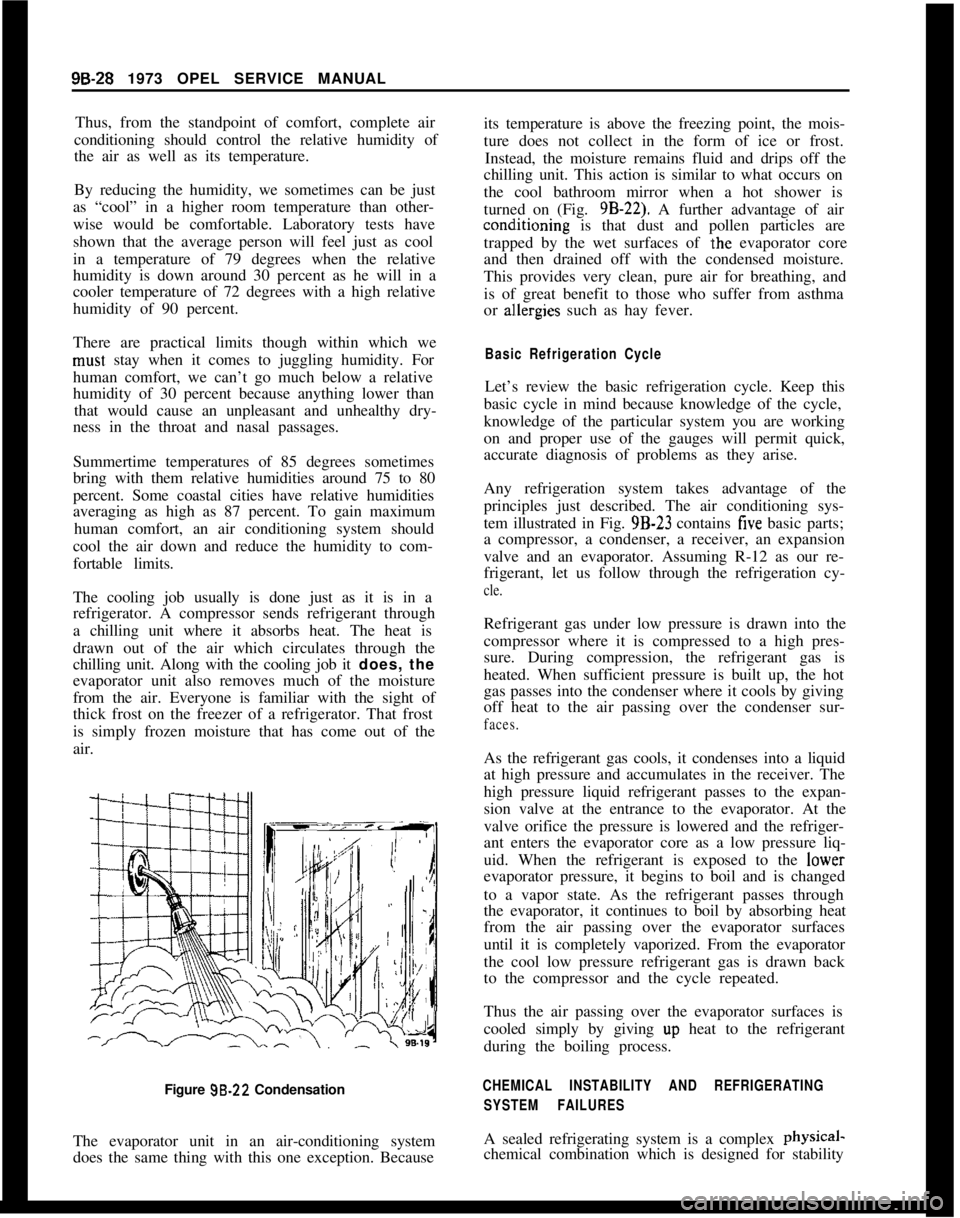
9B-28 1973 OPEL SERVICE MANUAL
Thus, from the standpoint of comfort, complete air
conditioning should control the relative humidity of
the air as well as its temperature.
By reducing the humidity, we sometimes can be just
as “cool” in a higher room temperature than other-
wise would be comfortable. Laboratory tests have
shown that the average person will feel just as cool
in a temperature of 79 degrees when the relative
humidity is down around 30 percent as he will in a
cooler temperature of 72 degrees with a high relative
humidity of 90 percent.
There are practical limits though within which wemust stay when it comes to juggling humidity. For
human comfort, we can’t go much below a relative
humidity of 30 percent because anything lower than
that would cause an unpleasant and unhealthy dry-
ness in the throat and nasal passages.
Summertime temperatures of 85 degrees sometimes
bring with them relative humidities around 75 to 80
percent. Some coastal cities have relative humidities
averaging as high as 87 percent. To gain maximum
human comfort, an air conditioning system should
cool the air down and reduce the humidity to com-
fortable limits.
The cooling job usually is done just as it is in a
refrigerator. A compressor sends refrigerant through
a chilling unit where it absorbs heat. The heat is
drawn out of the air which circulates through the
chilling unit. Along with the cooling job it does, the
evaporator unit also removes much of the moisture
from the air. Everyone is familiar with the sight of
thick frost on the freezer of a refrigerator. That frost
is simply frozen moisture that has come out of the
air.
Figure 99.22 Condensation
The evaporator unit in an air-conditioning system
does the same thing with this one exception. Becauseits temperature is above the freezing point, the mois-
ture does not collect in the form of ice or frost.
Instead, the moisture remains fluid and drips off the
chilling unit. This action is similar to what occurs on
the cool bathroom mirror when a hot shower is
turned on (Fig. 9B-22). A further advantage of airconditioning is that dust and pollen particles are
trapped by the wet surfaces of
.the evaporator core
and then drained off with the condensed moisture.
This provides very clean, pure air for breathing, and
is of great benefit to those who suffer from asthma
or ahergies such as hay fever.
Basic Refrigeration CycleLet’s review the basic refrigeration cycle. Keep this
basic cycle in mind because knowledge of the cycle,
knowledge of the particular system you are working
on and proper use of the gauges will permit quick,
accurate diagnosis of problems as they arise.
Any refrigeration system takes advantage of the
principles just described. The air conditioning sys-
tem illustrated in Fig. 9B-23 contains
five basic parts;
a compressor, a condenser, a receiver, an expansion
valve and an evaporator. Assuming R-12 as our re-
frigerant, let us follow through the refrigeration cy-
cle.Refrigerant gas under low pressure is drawn into the
compressor where it is compressed to a high pres-
sure. During compression, the refrigerant gas is
heated. When sufficient pressure is built up, the hot
gas passes into the condenser where it cools by giving
off heat to the air passing over the condenser sur-
faces.As the refrigerant gas cools, it condenses into a liquid
at high pressure and accumulates in the receiver. The
high pressure liquid refrigerant passes to the expan-
sion valve at the entrance to the evaporator. At the
valve orifice the pressure is lowered and the refriger-
ant enters the evaporator core as a low pressure liq-
uid. When the refrigerant is exposed to the lower
evaporator pressure, it begins to boil and is changed
to a vapor state. As the refrigerant passes through
the evaporator, it continues to boil by absorbing heat
from the air passing over the evaporator surfaces
until it is completely vaporized. From the evaporator
the cool low pressure refrigerant gas is drawn back
to the compressor and the cycle repeated.
Thus the air passing over the evaporator surfaces is
cooled simply by giving up heat to the refrigerant
during the boiling process.
CHEMICAL INSTABILITY AND REFRIGERATING
SYSTEM FAILURESA sealed refrigerating system is a complex physical-
chemical combination which is designed for stability
Page 540 of 625
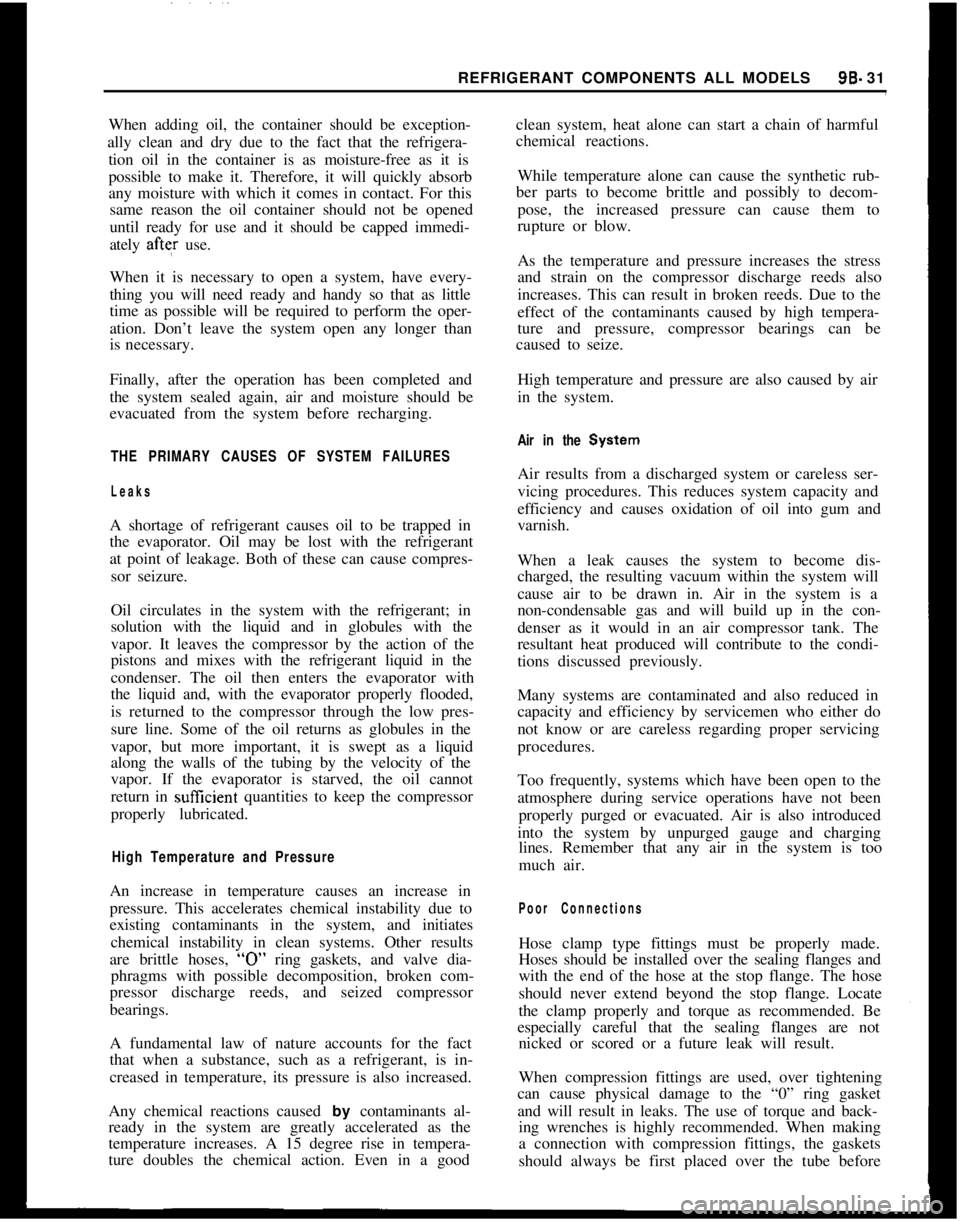
REFRIGERANT COMPONENTS ALL MODELS9B- 31
When adding oil, the container should be exception-
ally clean and dry due to the fact that the refrigera-
tion oil in the container is as moisture-free as it is
possible to make it. Therefore, it will quickly absorb
any moisture with which it comes in contact. For this
same reason the oil container should not be opened
until ready for use and it should be capped immedi-
ately afte;r use.
When it is necessary to open a system, have every-
thing you will need ready and handy so that as little
time as possible will be required to perform the oper-
ation. Don’t leave the system open any longer than
is necessary.
Finally, after the operation has been completed and
the system sealed again, air and moisture should be
evacuated from the system before recharging.
THE PRIMARY CAUSES OF SYSTEM FAILURES
LeaksA shortage of refrigerant causes oil to be trapped in
the evaporator. Oil may be lost with the refrigerant
at point of leakage. Both of these can cause compres-
sor seizure.
Oil circulates in the system with the refrigerant; in
solution with the liquid and in globules with the
vapor. It leaves the compressor by the action of the
pistons and mixes with the refrigerant liquid in the
condenser. The oil then enters the evaporator with
the liquid and, with the evaporator properly flooded,
is returned to the compressor through the low pres-
sure line. Some of the oil returns as globules in the
vapor, but more important, it is swept as a liquid
along the walls of the tubing by the velocity of the
vapor. If the evaporator is starved, the oil cannot
return in sut?icient quantities to keep the compressor
properly lubricated.
High Temperature and PressureAn increase in temperature causes an increase in
pressure. This accelerates chemical instability due to
existing contaminants in the system, and initiates
chemical instability in clean systems. Other results
are brittle hoses,
“0” ring gaskets, and valve dia-
phragms with possible decomposition, broken com-
pressor discharge reeds, and seized compressor
bearings.
A fundamental law of nature accounts for the fact
that when a substance, such as a refrigerant, is in-
creased in temperature, its pressure is also increased.
Any chemical reactions caused by contaminants al-
ready in the system are greatly accelerated as the
temperature increases. A 15 degree rise in tempera-
ture doubles the chemical action. Even in a goodclean system, heat alone can start a chain of harmful
chemical reactions.
While temperature alone can cause the synthetic rub-
ber parts to become brittle and possibly to decom-
pose, the increased pressure can cause them to
rupture or blow.
As the temperature and pressure increases the stress
and strain on the compressor discharge reeds also
increases. This can result in broken reeds. Due to the
effect of the contaminants caused by high tempera-
ture and pressure, compressor bearings can be
caused to seize.
High temperature and pressure are also caused by air
in the system.
Air in the SYstemAir results from a discharged system or careless ser-
vicing procedures. This reduces system capacity and
efficiency and causes oxidation of oil into gum and
varnish.
When a leak causes the system to become dis-
charged, the resulting vacuum within the system will
cause air to be drawn in. Air in the system is a
non-condensable gas and will build up in the con-
denser as it would in an air compressor tank. The
resultant heat produced will contribute to the condi-
tions discussed previously.
Many systems are contaminated and also reduced in
capacity and efficiency by servicemen who either do
not know or are careless regarding proper servicing
procedures.
Too frequently, systems which have been open to the
atmosphere during service operations have not been
properly purged or evacuated. Air is also introduced
into the system by unpurged gauge and charging
lines. Remember that any air in the system is too
much air.
Poor ConnectionsHose clamp type fittings must be properly made.
Hoses should be installed over the sealing flanges and
with the end of the hose at the stop flange. The hose
should never extend beyond the stop flange. Locate
the clamp properly and torque as recommended. Be
especially careful that the sealing flanges are not
nicked or scored or a future leak will result.
When compression fittings are used, over tightening
can cause physical damage to the “0” ring gasket
and will result in leaks. The use of torque and back-
ing wrenches is highly recommended. When making
a connection with compression fittings, the gaskets
should always be first placed over the tube before