engine oil RENAULT KANGOO 1998 KC / 1.G Heating And Ventilation Workshop Manual
[x] Cancel search | Manufacturer: RENAULT, Model Year: 1998, Model line: KANGOO, Model: RENAULT KANGOO 1998 KC / 1.GPages: 73
Page 13 of 73
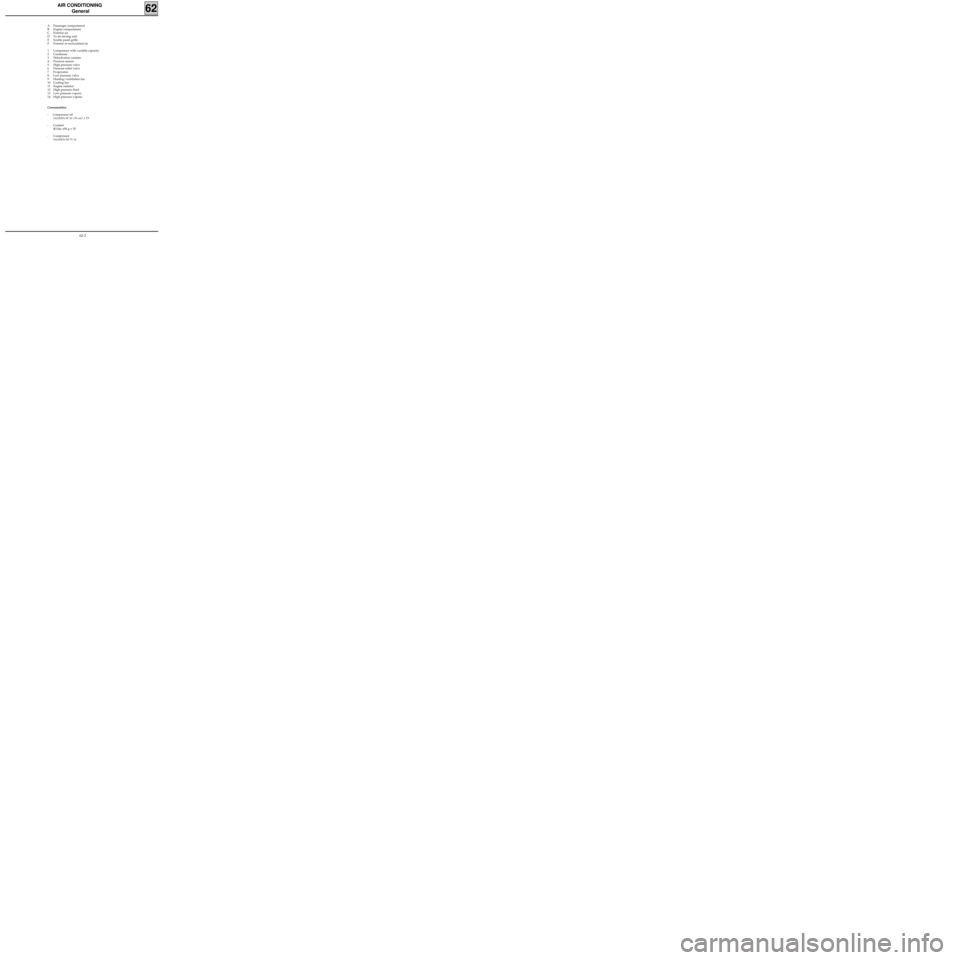
AIR CONDITIONING
General
62
A Passenger compartment
B Engine compartment
C Exterior air
D To air mixing unit
E Scuttle panel grille
F Exterior or recirculated air
1 Compressor with variable capacity
2 Condenser
3 Dehydration canister
4 Pressure sensor
5 High pressure valve
6 Pressure relief valve
7 Evaporator
8 Low pressure valve
9 Heating/ventilation fan
10 Cooling fan
11 Engine radiator
12 High pressure fluid
13 Low pressure vapour
14 High pressure vapour
Consumables:
- Compressor oil
SANDEN SP 10: 135 cm3 ± 15
- Coolant
R134a: 650 g ± 35
- Compressor
SANDEN SD 7V 16
62-2
Page 62 of 73
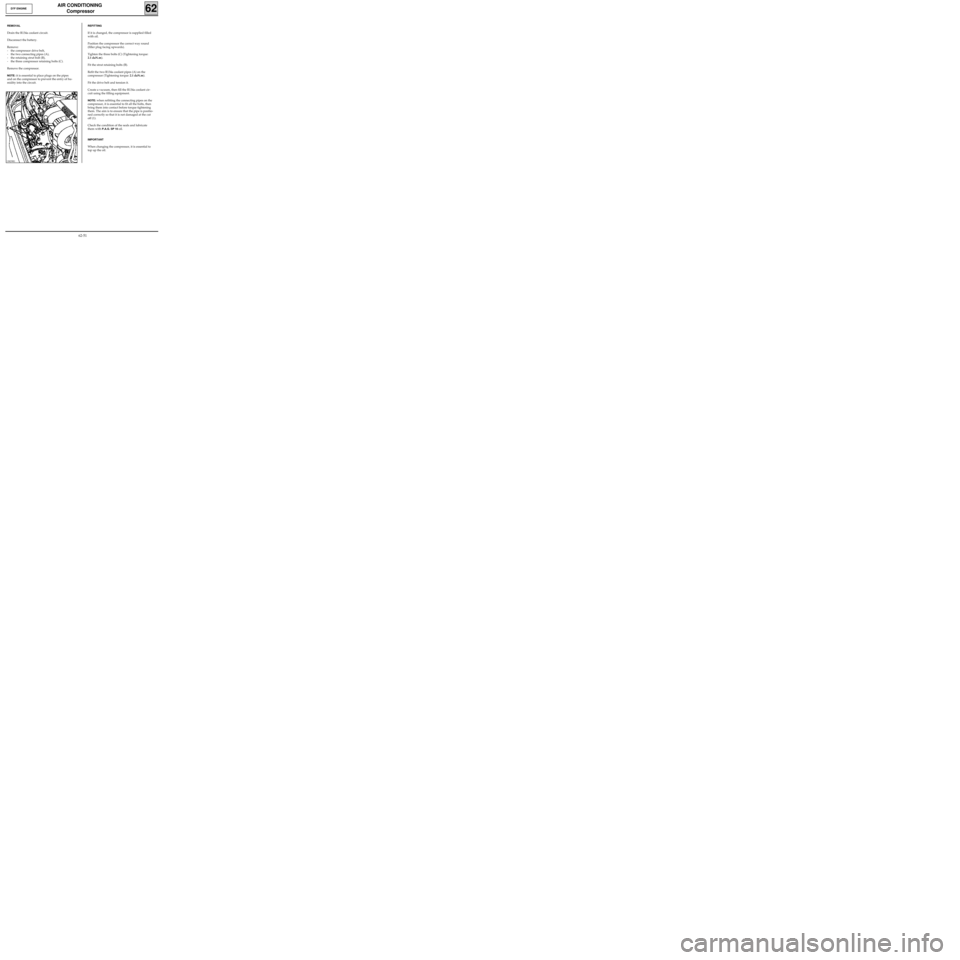
AIR CONDITIONING
Compressor
62D7F ENGINE
13829R1
REMOVAL
Drain the R134a coolant circuit.
Disconnect the battery.
Remove:
- the compressor drive belt,
- the two connecting pipes (A),
- the retaining strut bolt (B),
- the three compressor retaining bolts (C).
Remove the compressor.
NOTE: it is essential to place plugs on the pipes
and on the compressor to prevent the entry of hu-
midity into the circuit.
REFITTING
If it is changed, the compressor is supplied filled
with oil.
Position the compressor the correct way round
(filler plug facing upwards).
Tighten the three bolts (C) (Tightening torque:
2.1 daN.m).
Fit the strut retaining bolts (B).
Refit the two R134a coolant pipes (A) on the
compressor (Tightening torque:
2.1 daN.m).
Fit the drive belt and tension it.
Create a vacuum, then fill the R134a coolant cir-
cuit using the filling equipment.
NOTE: when refitting the connecting pipes on the
compressor, it is essential to fit all the bolts, then
bring them into contact before torque tightening
them. The aim is to ensure that the pipe is positio-
ned correctly so that it is not damaged at the cut
off (1).
Check the condition of the seals and lubricate
them with
P.A.G. SP 10 oil.
IMPORTANT
When changing the compressor, it is essential to
top up the oil.
62-51
Page 63 of 73
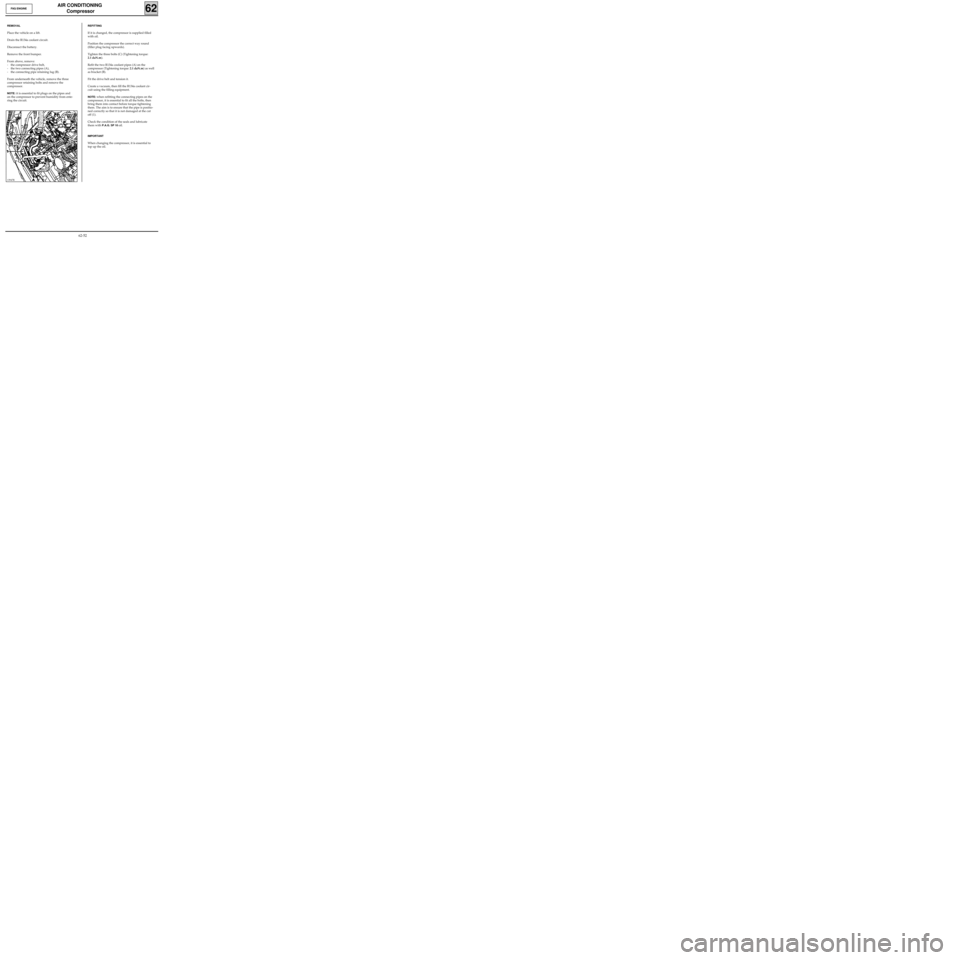
AIR CONDITIONING
Compressor
62F8Q ENGINE
REMOVAL
Place the vehicle on a lift.
Drain the R134a coolant circuit.
Disconnect the battery.
Remove the front bumper.
From above, remove:
- the compressor drive belt,
- the two connecting pipes (A),
- the connecting pipe retaining lug (B).
From underneath the vehicle, remove the three
compressor retaining bolts and remove the
compressor.
NOTE: it is essential to fit plugs on the pipes and
on the compressor to prevent humidity from ente-
ring the circuit.
13947R
REFITTING
If it is changed, the compressor is supplied filled
with oil.
Position the compressor the correct way round
(filler plug facing upwards).
Tighten the three bolts (C) (Tightening torque:
2.1 daN.m).
Refit the two R134a coolant pipes (A) on the
compressor (Tightening torque:
2.1 daN.m) as well
as bracket (B).
Fit the drive belt and tension it.
Create a vacuum, then fill the R134a coolant cir-
cuit using the filling equipment.
NOTE: when refitting the connecting pipes on the
compressor, it is essential to fit all the bolts, then
bring them into contact before torque tightening
them. The aim is to ensure that the pipe is positio-
ned correctly so that it is not damaged at the cut
off (1).
Check the condition of the seals and lubricate
them with
P.A.G. SP 10 oil.
IMPORTANT
When changing the compressor, it is essential to
top up the oil.
62-52
Page 64 of 73
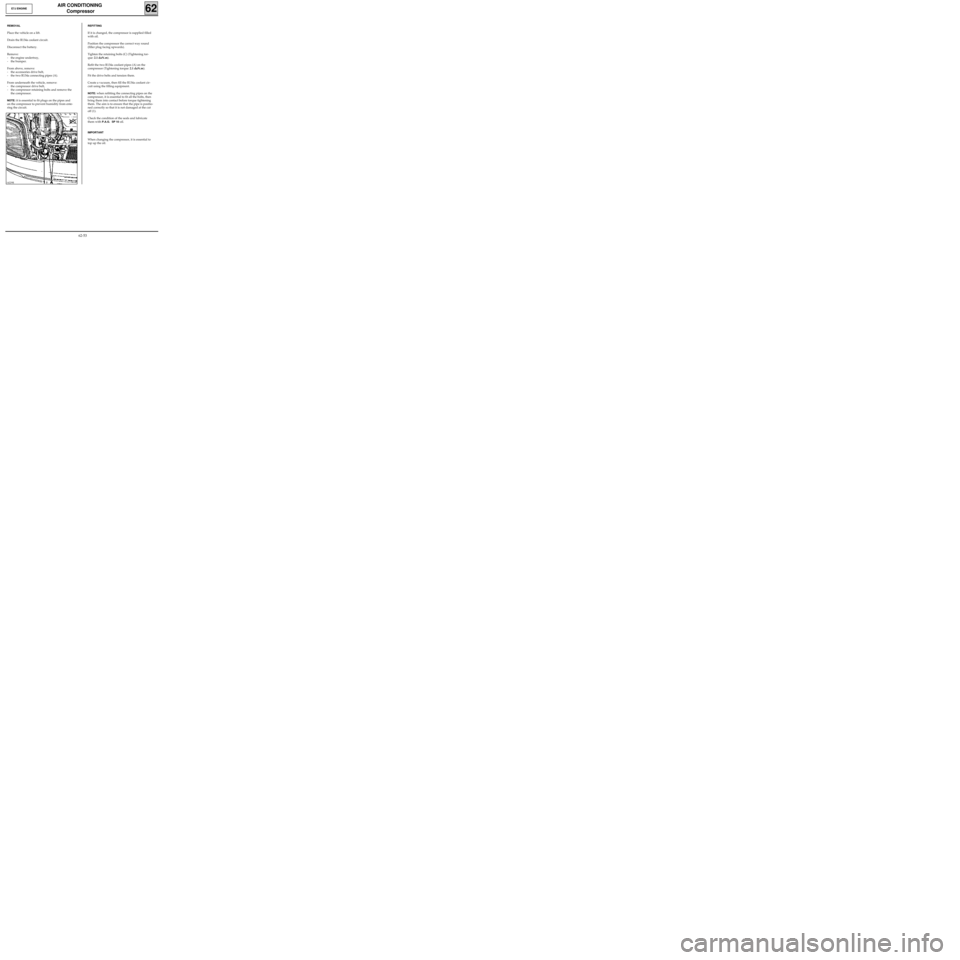
AIR CONDITIONING
Compressor
62E7J ENGINE
REMOVAL
Place the vehicle on a lift.
Drain the R134a coolant circuit.
Disconnect the battery.
Remove:
- the engine undertray,
- the bumper.
From above, remove:
- the accessories drive belt,
- the two R134a connecting pipes (A).
From underneath the vehicle, remove:
- the compressor drive belt,
- the compressor retaining bolts and remove the
the compressor.
NOTE: it is essential to fit plugs on the pipes and
on the compressor to prevent humidity from ente-
ring the circuit.
REFITTING
If it is changed, the compressor is supplied filled
with oil.
Position the compressor the correct way round
(filler plug facing upwards).
Tighten the retaining bolts (C) (Tightening tor-
que: 2.1 daN.m).
Refit the two R134a coolant pipes (A) on the
compressor (Tightening torque:
2.1 daN.m).
Fit the drive belts and tension them.
Create a vacuum, then fill the R134a coolant cir-
cuit using the filling equipment.
NOTE: when refitting the connecting pipes on the
compressor, it is essential to fit all the bolts, then
bring them into contact before torque tightening
them. The aim is to ensure that the pipe is positio-
ned correctly so that it is not damaged at the cut
off (1).
Check the condition of the seals and lubricate
them with
P.A.G. SP 10 oil.
IMPORTANT
When changing the compressor, it is essential to
top up the oil.
14229R
62-53
Page 65 of 73
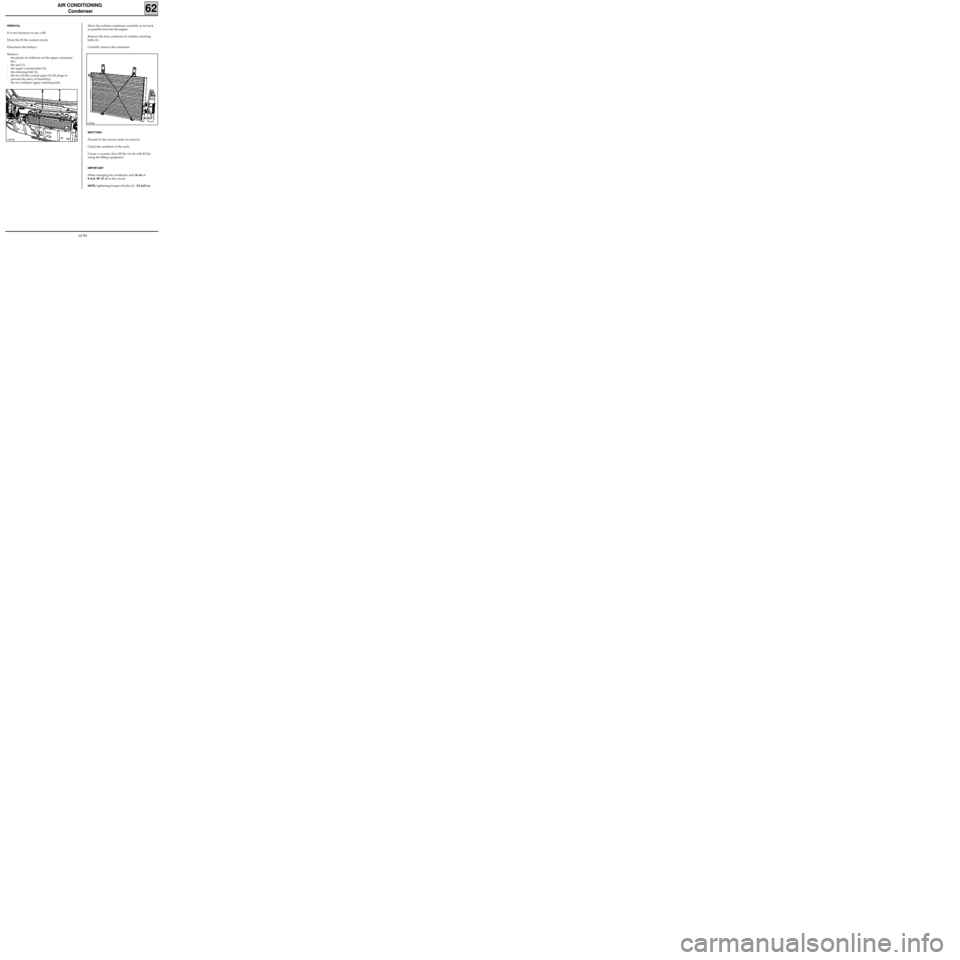
AIR CONDITIONING
Condenser
62
13828R
REMOVAL
It is not necessary to use a lift.
Drain the R134a coolant circuit.
Disconnect the battery.
Remove:
- the plastic air deflector on the upper crossmem-
ber,
- the seal (1),
- the upper crossmember (2),
- the retaining bolt (3),
- the two R134a coolant pipes (4) (fit plugs to
prevent the entry of humidity),
- the two radiator upper retaining bolts.Move the radiator-condenser assembly as far back
as possible towards the engine.
Remove the four condenser to radiator retaining
bolts (6).
Carefully remove the condenser.
REFITTING
Proceed in the reverse order to removal.
Check the condition of the seals.
Create a vacuum, then fill the circuit with R134a
using the filling equipment.
IMPORTANT
When changing the condenser, add 30 ml of
P.A.G. SP 10 oil to the circuit.
NOTE: tightening torque of bolts (6) : 0.8 daN.m.
13830R
62-54
Page 69 of 73
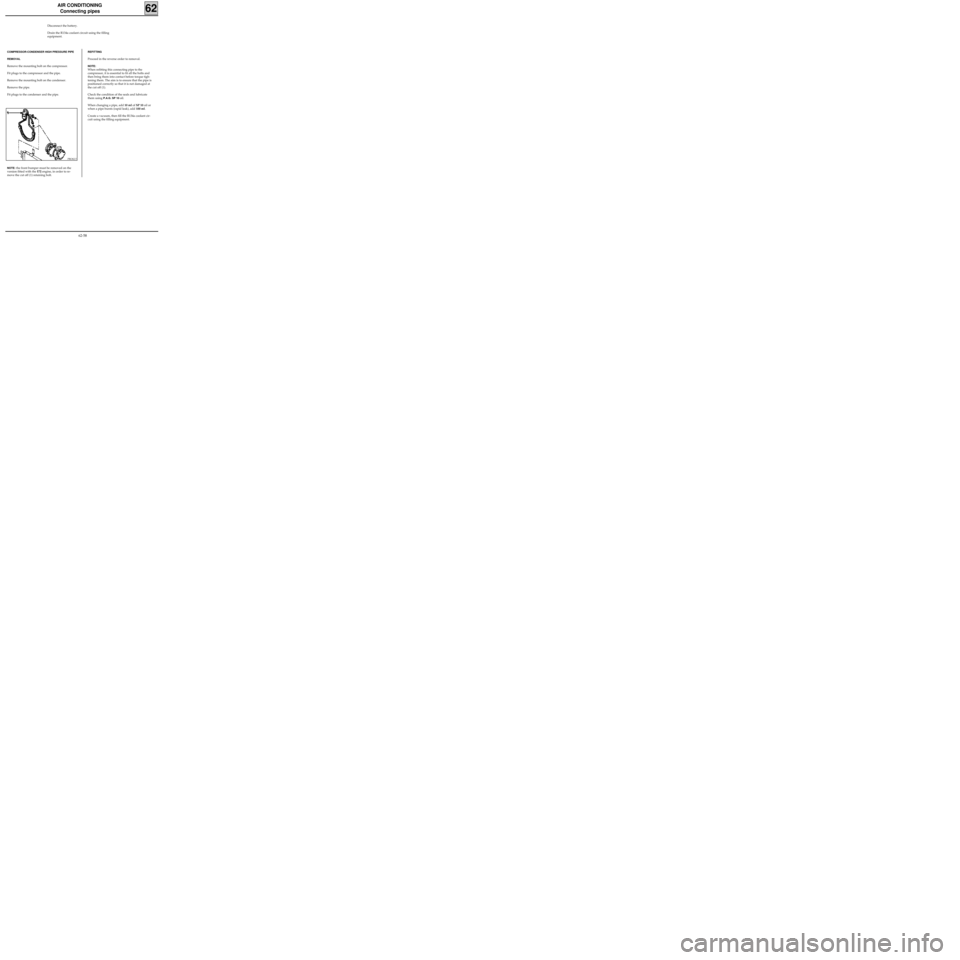
AIR CONDITIONING
Connecting pipes
62
Disconnect the battery.
Drain the R134a coolant circuit using the filling
equipment.
PRO62.5
NOTE: the front bumper must be removed on the
version fitted with the E7J engine, in order to re-
move the cut off (1) retaining bolt.
COMPRESSOR-CONDENSER HIGH PRESSURE PIPE
REMOVAL
Remove the mounting bolt on the compressor.
Fit plugs to the compressor and the pipe.
Remove the mounting bolt on the condenser.
Remove the pipe.
Fit plugs to the condenser and the pipe.
REFITTING
Proceed in the reverse order to removal.
NOTE:
When refitting this connecting pipe to the
compressor, it is essential to fit all the bolts and
then bring them into contact before torque tigh-
tening them. The aim is to ensure that the pipe is
positioned correctly so that it is not damaged at
the cut off (1).
Check the condition of the seals and lubricate
them using
P.A.G. SP 10 oil.
When changing a pipe, add 10 ml of SP 10 oil or
when a pipe bursts (rapid leak), add 100 ml.
Create a vacuum, then fill the R134a coolant cir-
cuit using the filling equipment.
62-58
Page 71 of 73
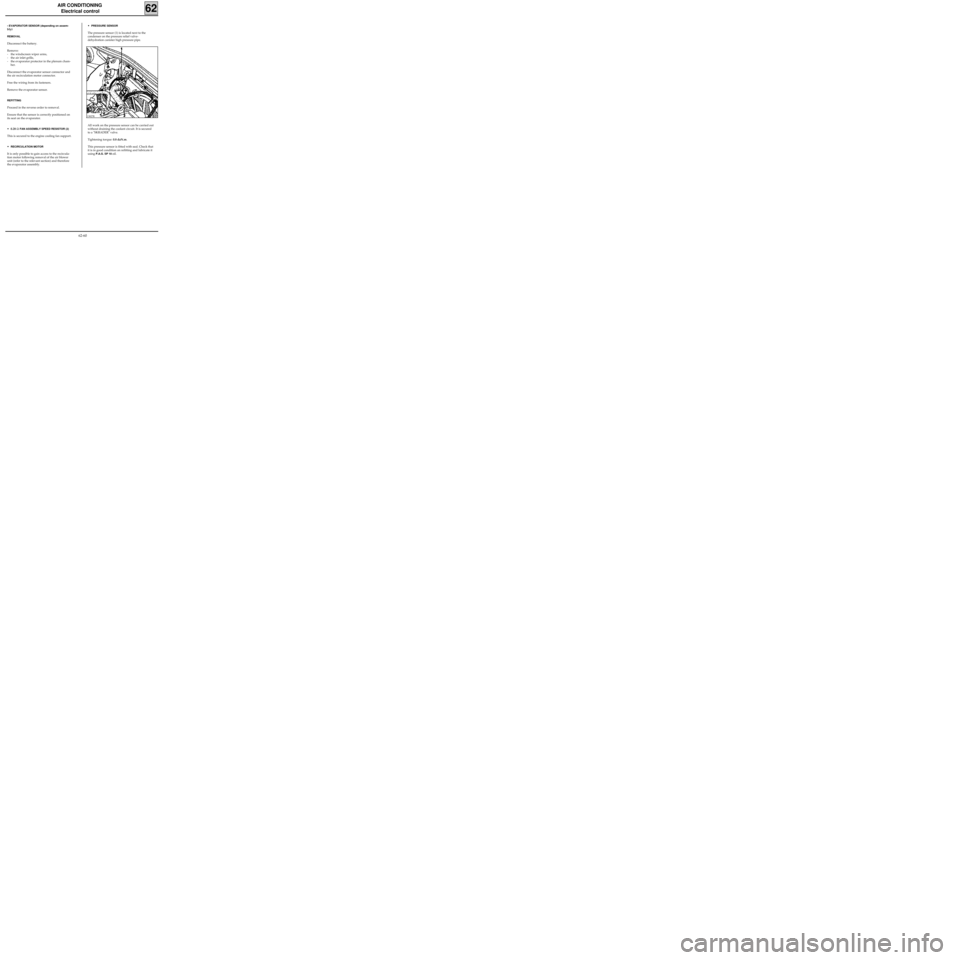
AIR CONDITIONING
Electrical control
62
13827R
• EVAPORATOR SENSOR (depending on assem-
bly)
REMOVAL
Disconnect the battery.
Remove:
- the windscreen wiper arms,
- the air inlet grille,
- the evaporator protector in the plenum cham-
ber.
Disconnect the evaporator sensor connector and
the air recirculation motor connector.
Free the wiring from its fasteners.
Remove the evaporator sensor.
REFITTING
Proceed in the reverse order to removal.
Ensure that the sensor is correctly positioned on
its seat on the evaporator.
•0.28 Ω
FAN ASSEMBLY SPEED RESISTOR (2)
This is secured to the engine cooling fan support.
•
RECIRCULATION MOTOR
It is only possible to gain access to the recircula-
tion motor following removal of the air blower
unit (refer to the relevant section) and therefore
the evaporator assembly. •
PRESSURE SENSOR
The pressure sensor (1) is located next to the
condenser on the pressure relief valve-
dehydration canister high pressure pipe.
All work on the pressure sensor can be carried out
without draining the coolant circuit. It is secured
to a "SKRADER" valve.
Tightening torque: 0.8 daN.m.
This pressure sensor is fitted with seal. Check that
it is in good condition on refitting and lubricate it
using
P.A.G. SP 10 oil.
62-60