ECU RENAULT KANGOO 2013 X61 / 2.G Petrol V42 Injection Workshop Manual
[x] Cancel search | Manufacturer: RENAULT, Model Year: 2013, Model line: KANGOO, Model: RENAULT KANGOO 2013 X61 / 2.GPages: 279, PDF Size: 1.29 MB
Page 9 of 279
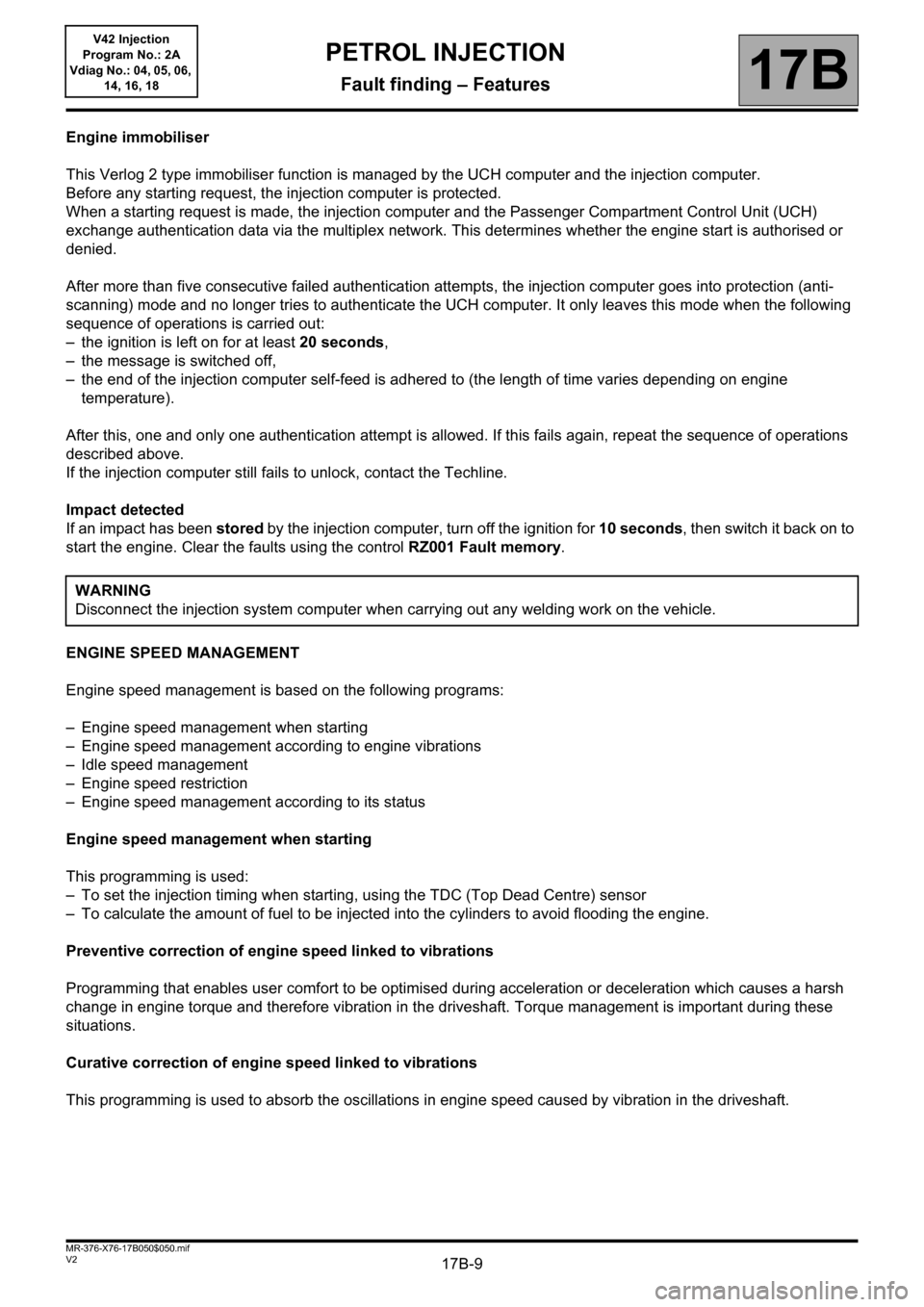
17B-9V2 MR-376-X76-17B050$050.mif
17B
V42 Injection
Program No.: 2A
Vdiag No.: 04, 05, 06,
14, 16, 18
Engine immobiliser
This Verlog 2 type immobiliser function is managed by the UCH computer and the injection computer.
Before any starting request, the injection computer is protected.
When a starting request is made, the injection computer and the Passenger Compartment Control Unit (UCH)
exchange authentication data via the multiplex network. This determines whether the engine start is authorised or
denied.
After more than five consecutive failed authentication attempts, the injection computer goes into protection (anti-
scanning) mode and no longer tries to authenticate the UCH computer. It only leaves this mode when the following
sequence of operations is carried out:
– the ignition is left on for at least 20 seconds,
– the message is switched off,
– the end of the injection computer self-feed is adhered to (the length of time varies depending on engine
temperature).
After this, one and only one authentication attempt is allowed. If this fails again, repeat the sequence of operations
described above.
If the injection computer still fails to unlock, contact the Techline.
Impact detected
If an impact has been stored by the injection computer, turn off the ignition for 10 seconds, then switch it back on to
start the engine. Clear the faults using the control RZ001 Fault memory.
ENGINE SPEED MANAGEMENT
Engine speed management is based on the following programs:
– Engine speed management when starting
– Engine speed management according to engine vibrations
– Idle speed management
– Engine speed restriction
– Engine speed management according to its status
Engine speed management when starting
This programming is used:
– To set the injection timing when starting, using the TDC (Top Dead Centre) sensor
– To calculate the amount of fuel to be injected into the cylinders to avoid flooding the engine.
Preventive correction of engine speed linked to vibrations
Programming that enables user comfort to be optimised during acceleration or deceleration which causes a harsh
change in engine torque and therefore vibration in the driveshaft. Torque management is important during these
situations.
Curative correction of engine speed linked to vibrations
This programming is used to absorb the oscillations in engine speed caused by vibration in the driveshaft.WARNING
Disconnect the injection system computer when carrying out any welding work on the vehicle.
PETROL INJECTION
Fault finding – Features
Page 72 of 279
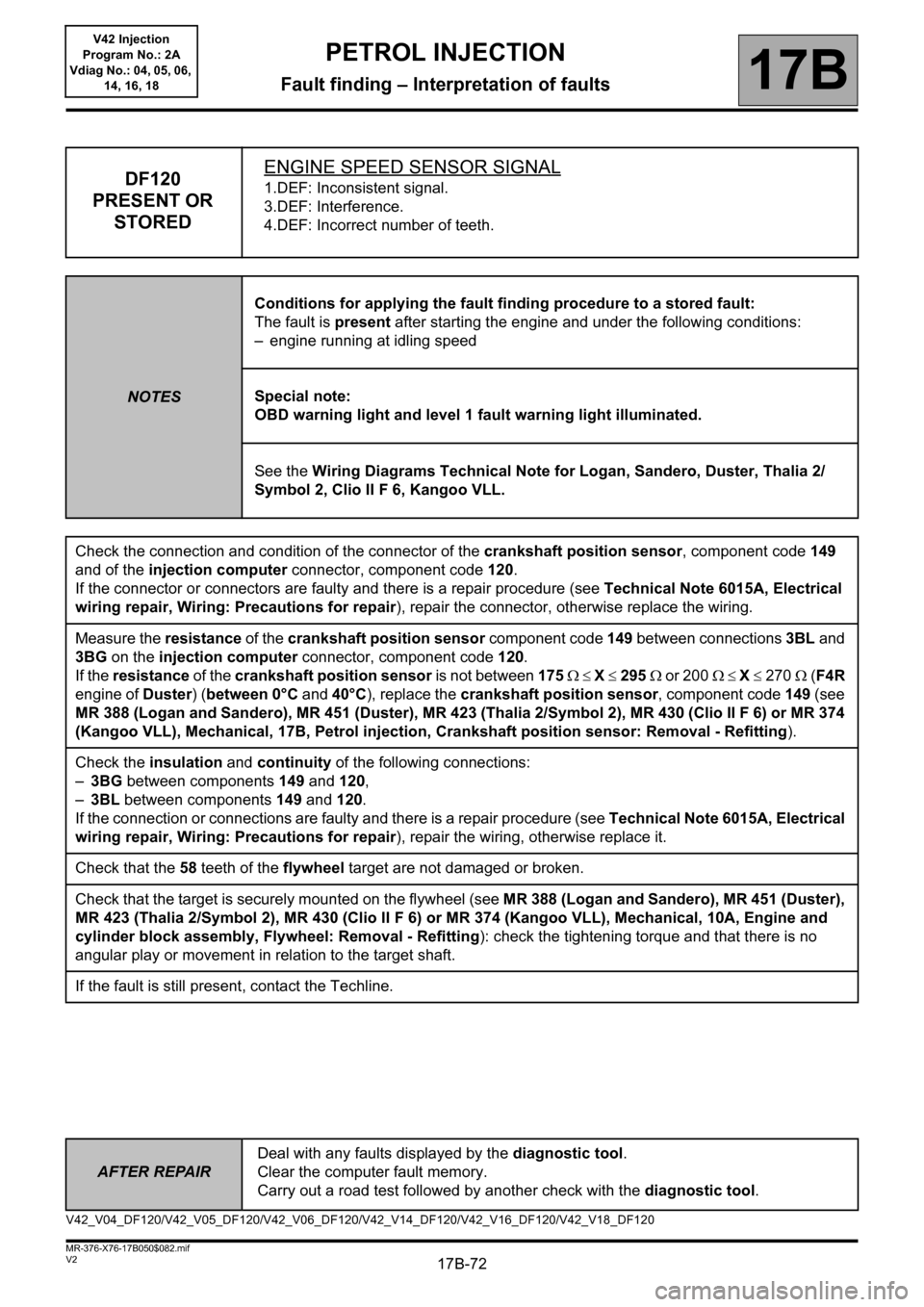
17B-72
AFTER REPAIRDeal with any faults displayed by the diagnostic tool.
Clear the computer fault memory.
Carry out a road test followed by another check with the diagnostic tool.
V2 MR-376-X76-17B050$082.mif
PETROL INJECTION
Fault finding – Interpretation of faults17B
V42 Injection
Program No.: 2A
Vdiag No.: 04, 05, 06,
14, 16, 18
DF120
PRESENT OR
STOREDENGINE SPEED SENSOR SIGNAL1.DEF: Inconsistent signal.
3.DEF: Interference.
4.DEF: Incorrect number of teeth.
NOTESConditions for applying the fault finding procedure to a stored fault:
The fault is present after starting the engine and under the following conditions:
– engine running at idling speed
Special note:
OBD warning light and level 1 fault warning light illuminated.
See the Wiring Diagrams Technical Note for Logan, Sandero, Duster, Thalia 2/
Symbol 2, Clio II F 6, Kangoo VLL.
Check the connection and condition of the connector of the crankshaft position sensor, component code 149
and of the injection computer connector, component code 120.
If the connector or connectors are faulty and there is a repair procedure (see Technical Note 6015A, Electrical
wiring repair, Wiring: Precautions for repair), repair the connector, otherwise replace the wiring.
Measure the resistance of the crankshaft position sensor component code 149 between connections 3BL and
3BG on the injection computer connector, component code 120.
If the resistance of the crankshaft position sensor is not between 175 X 295 or 200 X 270 (F4R
engine of Duster) (between 0°C and 40°C), replace the crankshaft position sensor, component code 149 (see
MR 388 (Logan and Sandero), MR 451 (Duster), MR 423 (Thalia 2/Symbol 2), MR 430 (Clio II F 6) or MR 374
(Kangoo VLL), Mechanical, 17B, Petrol injection, Crankshaft position sensor: Removal - Refitting).
Check the insulation and continuity of the following connections:
–3BG between components 149 and 120,
–3BL between components 149 and 120.
If the connection or connections are faulty and there is a repair procedure (see Technical Note 6015A, Electrical
wiring repair, Wiring: Precautions for repair), repair the wiring, otherwise replace it.
Check that the 58 teeth of the flywheel target are not damaged or broken.
Check that the target is securely mounted on the flywheel (see MR 388 (Logan and Sandero), MR 451 (Duster),
MR 423 (Thalia 2/Symbol 2), MR 430 (Clio II F 6) or MR 374 (Kangoo VLL), Mechanical, 10A, Engine and
cylinder block assembly, Flywheel: Removal - Refitting): check the tightening torque and that there is no
angular play or movement in relation to the target shaft.
If the fault is still present, contact the Techline.
V42_V04_DF120/V42_V05_DF120/V42_V06_DF120/V42_V14_DF120/V42_V16_DF120/V42_V18_DF120