fuel return RENAULT SCENIC 2011 J95 / 3.G Engine And Peripherals EDC16 Injection Workshop Manual
[x] Cancel search | Manufacturer: RENAULT, Model Year: 2011, Model line: SCENIC, Model: RENAULT SCENIC 2011 J95 / 3.GPages: 236, PDF Size: 1.32 MB
Page 66 of 236
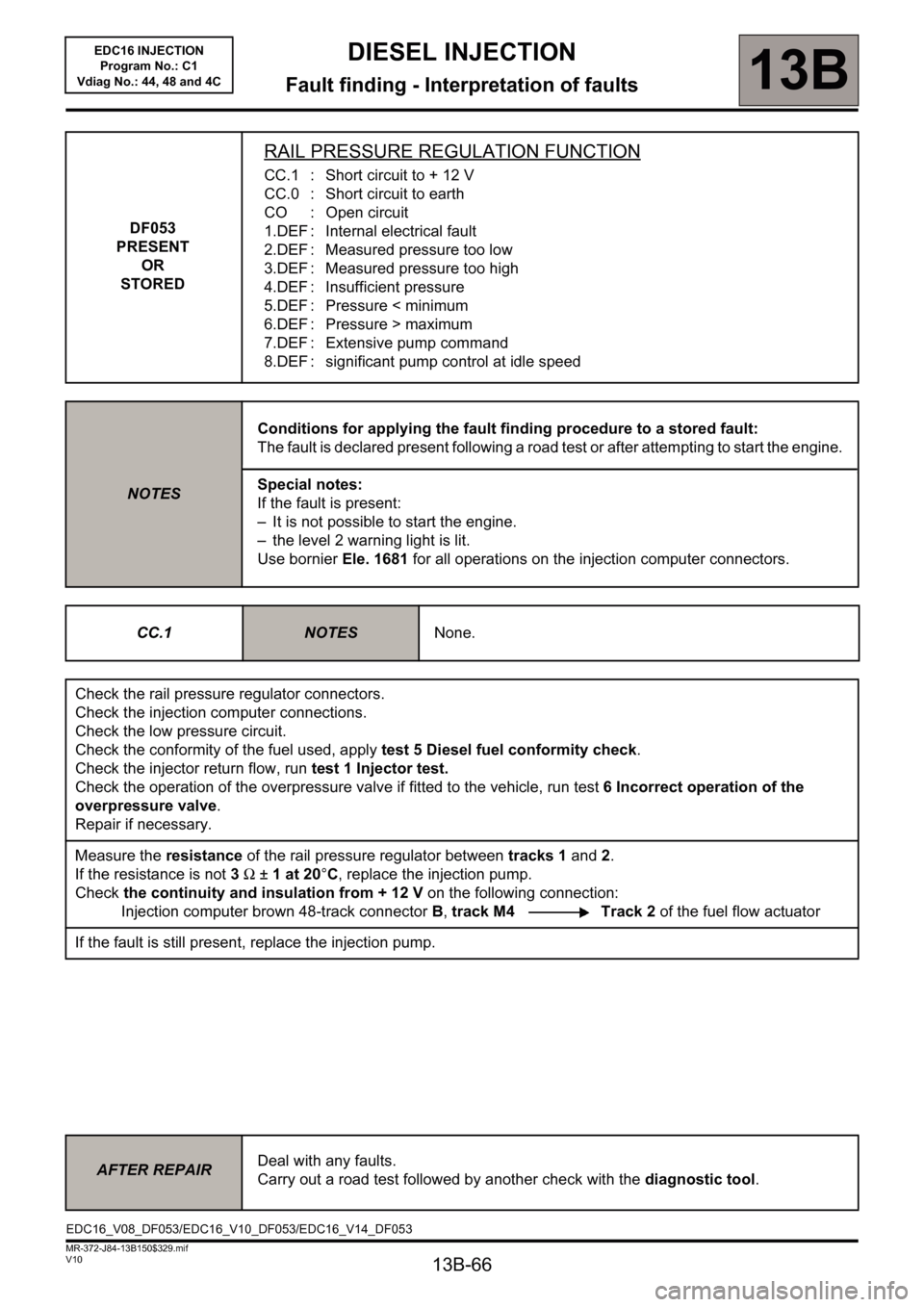
13B-66
DIESEL INJECTION
Fault finding - Interpretation of faults13B
V10 MR-372-J84-13B150$329.mif
EDC16 INJECTION
Program No.: C1
Vdiag No.: 44, 48 and 4C
DF053
PRESENT
OR
STORED
RAIL PRESSURE REGULATION FUNCTION
CC.1 : Short circuit to + 12 V
CC.0 : Short circuit to earth
CO : Open circuit
1.DEF : Internal electrical fault
2.DEF : Measured pressure too low
3.DEF : Measured pressure too high
4.DEF : Insufficient pressure
5.DEF : Pressure < minimum
6.DEF : Pressure > maximum
7.DEF : Extensive pump command
8.DEF : significant pump control at idle speed
NOTESConditions for applying the fault finding procedure to a stored fault:
The fault is declared present following a road test or after attempting to start the engine.
Special notes:
If the fault is present:
– It is not possible to start the engine.
– the level 2 warning light is lit.
Use bornier Ele. 1681 for all operations on the injection computer connectors.
CC.1
NOTESNone.
Check the rail pressure regulator connectors.
Check the injection computer connections.
Check the low pressure circuit.
Check the conformity of the fuel used, apply test 5 Diesel fuel conformity check.
Check the injector return flow, run test 1 Injector test.
Check the operation of the overpressure valve if fitted to the vehicle, run test 6 Incorrect operation of the
overpressure valve.
Repair if necessary.
Measure the resistance of the rail pressure regulator between tracks 1 and 2.
If the resistance is not 3Ω ±1 at 20°C, replace the injection pump.
Check the continuity and insulation from + 12 V on the following connection:
Injection computer brown 48-track connector B, track M4 Track 2 of the fuel flow actuator
If the fault is still present, replace the injection pump.
AFTER REPAIRDeal with any faults.
Carry out a road test followed by another check with the diagnostic tool.
EDC16_V08_DF053/EDC16_V10_DF053/EDC16_V14_DF053
Page 67 of 236
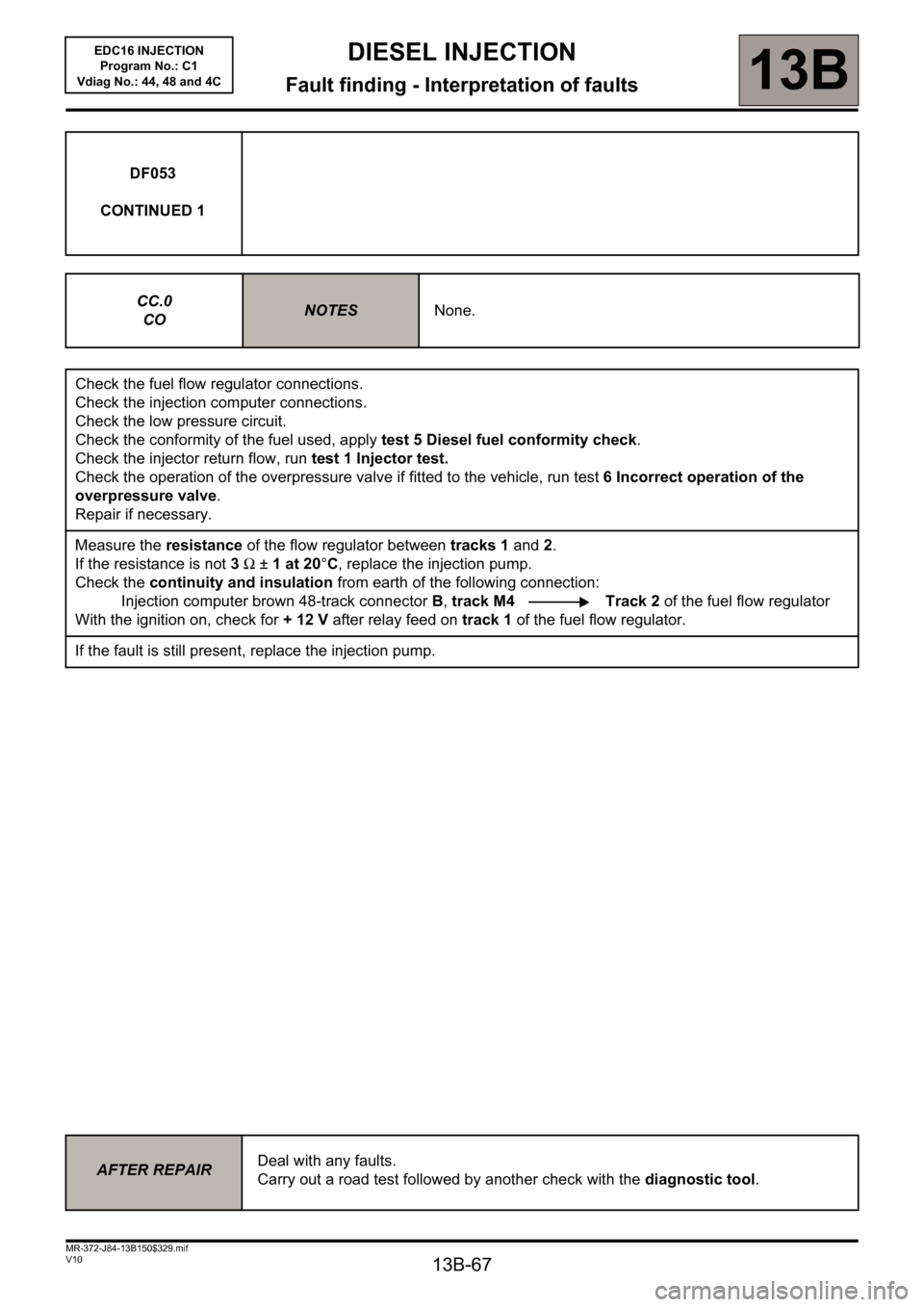
13B-67
DIESEL INJECTION
Fault finding - Interpretation of faults13B
V10 MR-372-J84-13B150$329.mif
EDC16 INJECTION
Program No.: C1
Vdiag No.: 44, 48 and 4C
DF053
CONTINUED 1
CC.0
CO
NOTESNone.
Check the fuel flow regulator connections.
Check the injection computer connections.
Check the low pressure circuit.
Check the conformity of the fuel used, apply test 5 Diesel fuel conformity check.
Check the injector return flow, run test 1 Injector test.
Check the operation of the overpressure valve if fitted to the vehicle, run test 6 Incorrect operation of the
overpressure valve.
Repair if necessary.
Measure the resistance of the flow regulator between tracks 1 and 2.
If the resistance is not 3Ω ±1 at 20°C, replace the injection pump.
Check the continuity and insulation from earth of the following connection:
Injection computer brown 48-track connector B, track M4 Track 2 of the fuel flow regulator
With the ignition on, check for + 12 V after relay feed on track 1 of the fuel flow regulator.
If the fault is still present, replace the injection pump.
AFTER REPAIRDeal with any faults.
Carry out a road test followed by another check with the diagnostic tool.
Page 68 of 236
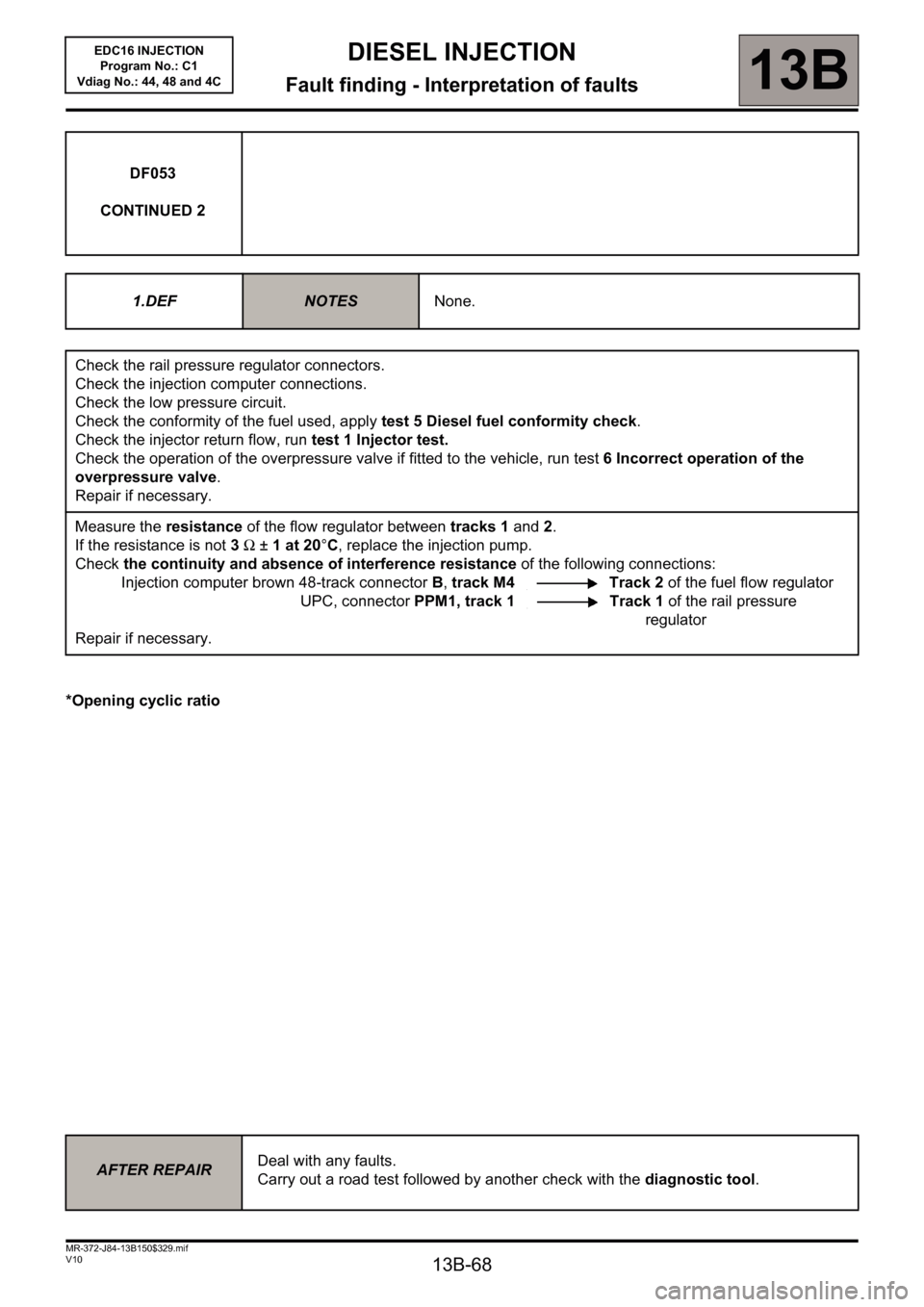
13B-68
DIESEL INJECTION
Fault finding - Interpretation of faults13B
V10 MR-372-J84-13B150$329.mif
EDC16 INJECTION
Program No.: C1
Vdiag No.: 44, 48 and 4C
*Opening cyclic ratioDF053
CONTINUED 2
1.DEF
NOTESNone.
Check the rail pressure regulator connectors.
Check the injection computer connections.
Check the low pressure circuit.
Check the conformity of the fuel used, apply test 5 Diesel fuel conformity check.
Check the injector return flow, run test 1 Injector test.
Check the operation of the overpressure valve if fitted to the vehicle, run test 6 Incorrect operation of the
overpressure valve.
Repair if necessary.
Measure the resistance of the flow regulator between tracks 1 and 2.
If the resistance is not 3Ω ±1 at 20°C, replace the injection pump.
Check the continuity and absence of interference resistance of the following connections:
Injection computer brown 48-track connector B, track M4 Track 2 of the fuel flow regulator
UPC, connector PPM1, track 1 Track 1 of the rail pressure
regulator
Repair if necessary.
AFTER REPAIRDeal with any faults.
Carry out a road test followed by another check with the diagnostic tool.
Page 205 of 236
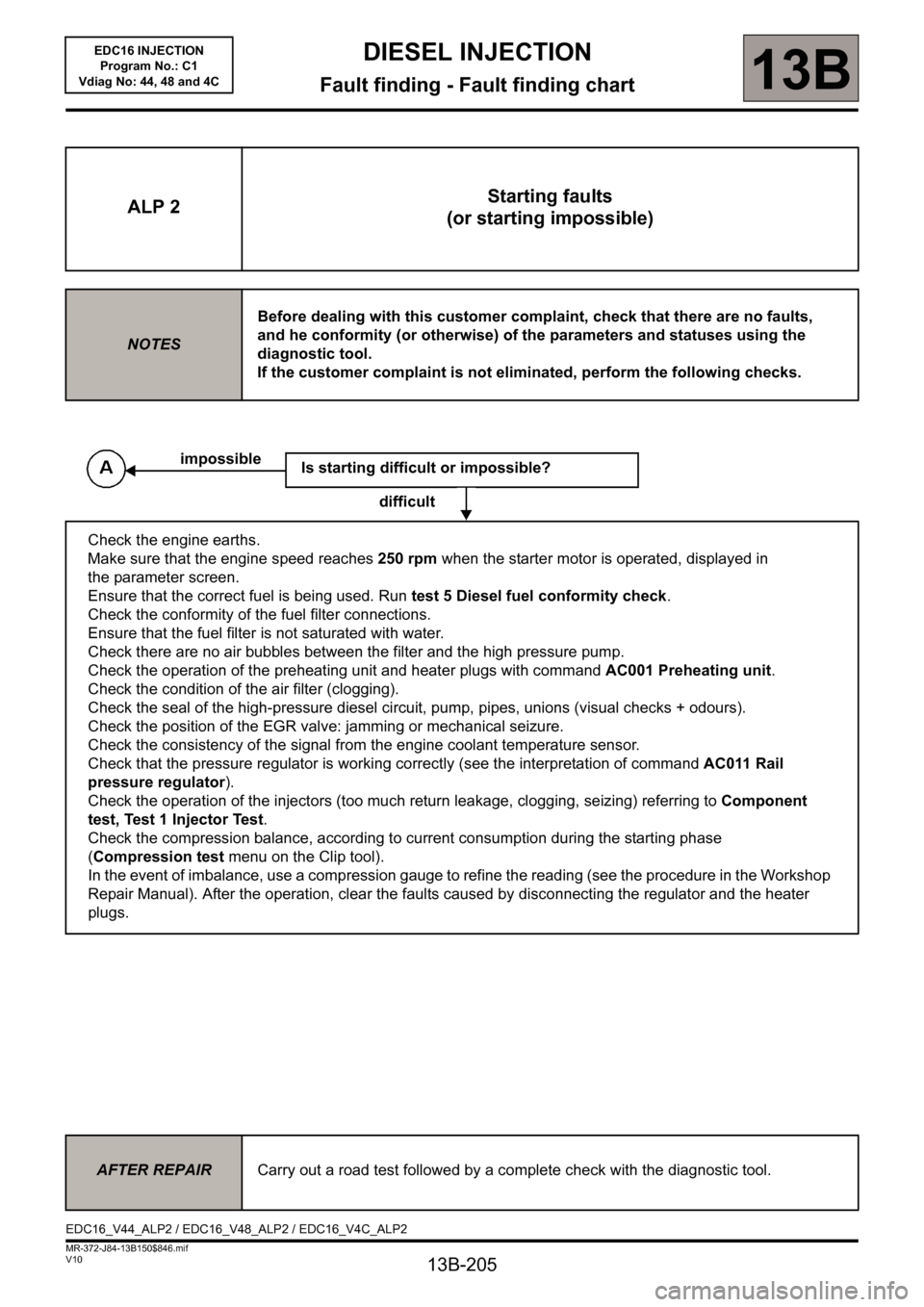
13B-205
MR-372-J84-13B150$846.mif
V10
DIESEL INJECTION
Fault finding - Fault finding chart13B
ALP 2Starting faults
(or starting impossible)
NOTESBefore dealing with this customer complaint, check that there are no faults,
and he conformity (or otherwise) of the parameters and statuses using the
diagnostic tool.
If the customer complaint is not eliminated, perform the following checks.
Is starting difficult or impossible?
difficult
Check the engine earths.
Make sure that the engine speed reaches 250 rpm when the starter motor is operated, displayed in
the parameter screen.
Ensure that the correct fuel is being used. Run test 5 Diesel fuel conformity check.
Check the conformity of the fuel filter connections.
Ensure that the fuel filter is not saturated with water.
Check there are no air bubbles between the filter and the high pressure pump.
Check the operation of the preheating unit and heater plugs with command AC001 Preheating unit.
Check the condition of the air filter (clogging).
Check the seal of the high-pressure diesel circuit, pump, pipes, unions (visual checks + odours).
Check the position of the EGR valve: jamming or mechanical seizure.
Check the consistency of the signal from the engine coolant temperature sensor.
Check that the pressure regulator is working correctly (see the interpretation of command AC011 Rail
pressure regulator).
Check the operation of the injectors (too much return leakage, clogging, seizing) referring to Component
test, Test 1 Injector Test.
Check the compression balance, according to current consumption during the starting phase
(Compression test menu on the Clip tool).
In the event of imbalance, use a compression gauge to refine the reading (see the procedure in the Workshop
Repair Manual). After the operation, clear the faults caused by disconnecting the regulator and the heater
plugs.
impossible
AFTER REPAIRCarry out a road test followed by a complete check with the diagnostic tool.
EDC16_V44_ALP2 / EDC16_V48_ALP2 / EDC16_V4C_ALP2
EDC16 INJECTION
Program No.: C1
Vdiag No: 44, 48 and 4C
Page 211 of 236
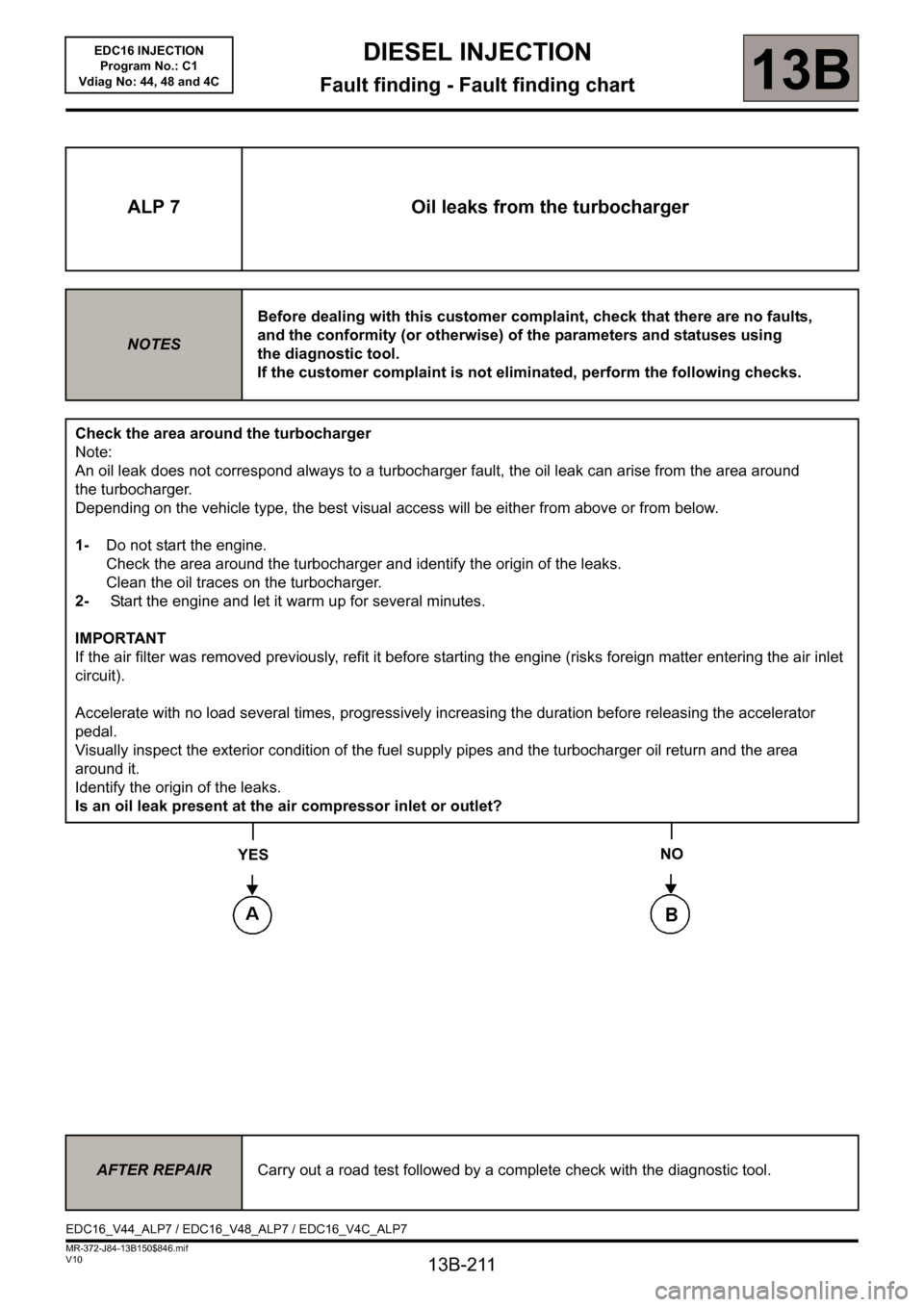
13B-211
MR-372-J84-13B150$846.mif
V10
DIESEL INJECTION
Fault finding - Fault finding chart13B
ALP 7 Oil leaks from the turbocharger
NOTESBefore dealing with this customer complaint, check that there are no faults,
and the conformity (or otherwise) of the parameters and statuses using
the diagnostic tool.
If the customer complaint is not eliminated, perform the following checks.
Check the area around the turbocharger
Note:
An oil leak does not correspond always to a turbocharger fault, the oil leak can arise from the area around
the turbocharger.
Depending on the vehicle type, the best visual access will be either from above or from below.
1-Do not start the engine.
Check the area around the turbocharger and identify the origin of the leaks.
Clean the oil traces on the turbocharger.
2- Start the engine and let it warm up for several minutes.
IMPORTANT
If the air filter was removed previously, refit it before starting the engine (risks foreign matter entering the air inlet
circuit).
Accelerate with no load several times, progressively increasing the duration before releasing the accelerator
pedal.
Visually inspect the exterior condition of the fuel supply pipes and the turbocharger oil return and the area
around it.
Identify the origin of the leaks.
Is an oil leak present at the air compressor inlet or outlet?
YES
NO
AFTER REPAIRCarry out a road test followed by a complete check with the diagnostic tool.
EDC16_V44_ALP7 / EDC16_V48_ALP7 / EDC16_V4C_ALP7EDC16 INJECTION
Program No.: C1
Vdiag No: 44, 48 and 4C
Page 219 of 236
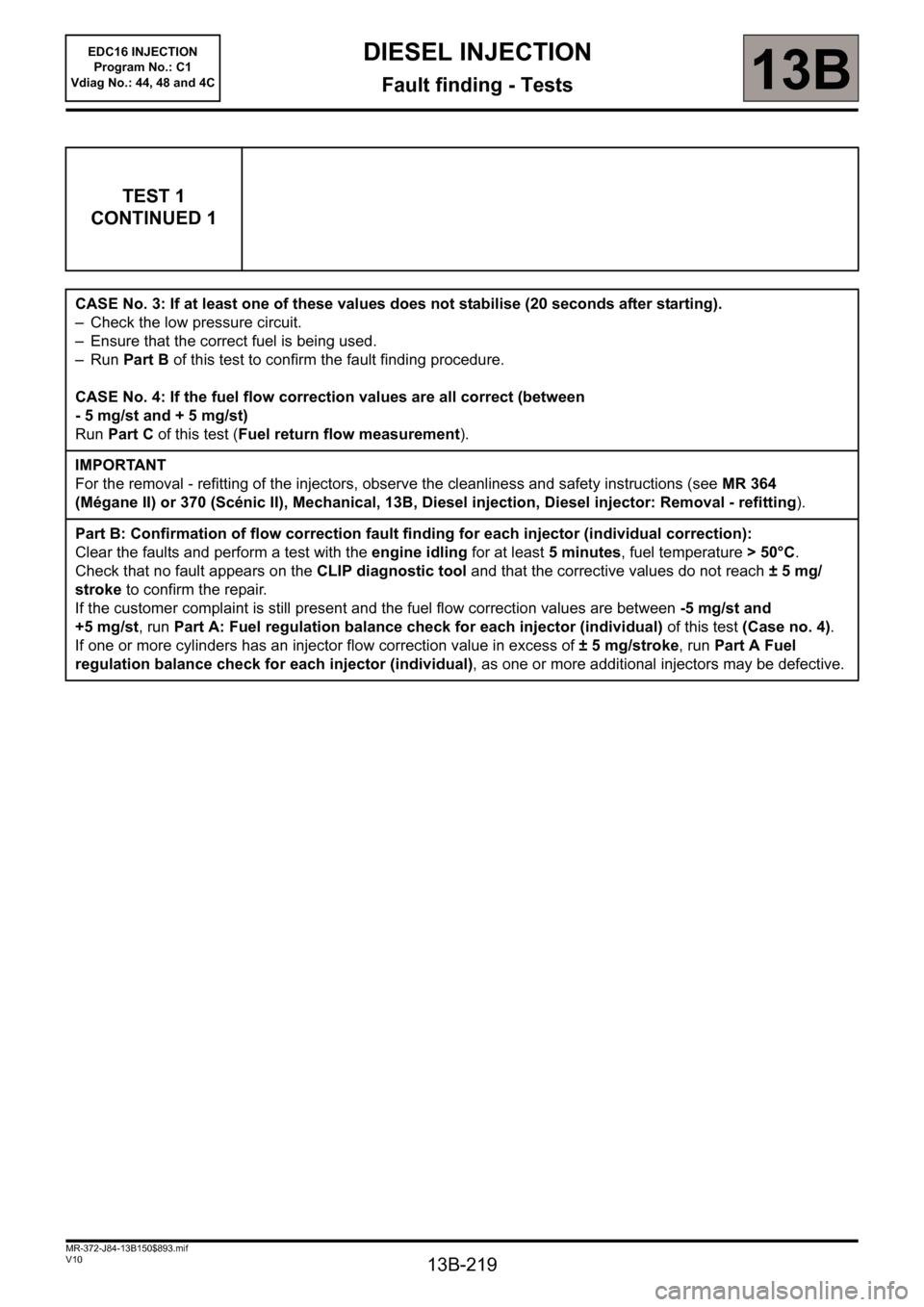
13B-219
MR-372-J84-13B150$893.mif
V10
DIESEL INJECTION
Fault finding - Tests
EDC16 INJECTION
Program No.: C1
Vdiag No.: 44, 48 and 4C
13B
TEST 1
CONTINUED 1
CASE No. 3: If at least one of these values does not stabilise (20 seconds after starting).
– Check the low pressure circuit.
– Ensure that the correct fuel is being used.
–Run Part B of this test to confirm the fault finding procedure.
CASE No. 4: If the fuel flow correction values are all correct (between
- 5 mg/st and + 5 mg/st)
Run Part C of this test (Fuel return flow measurement).
IMPORTANT
For the removal - refitting of the injectors, observe the cleanliness and safety instructions (see MR 364
(Mégane II) or 370 (Scénic II), Mechanical, 13B, Diesel injection, Diesel injector: Removal - refitting).
Part B: Confirmation of flow correction fault finding for each injector (individual correction):
Clear the faults and perform a test with the engine idling for at least 5 minutes, fuel temperature > 50°C.
Check that no fault appears on the CLIP diagnostic tool and that the corrective values do not reach ± 5 mg/
stroke to confirm the repair.
If the customer complaint is still present and the fuel flow correction values are between -5 mg/st and
+5 mg/st, run Part A: Fuel regulation balance check for each injector (individual) of this test (Case no. 4).
If one or more cylinders has an injector flow correction value in excess of ± 5 mg/stroke, run Part A Fuel
regulation balance check for each injector (individual), as one or more additional injectors may be defective.
Page 220 of 236
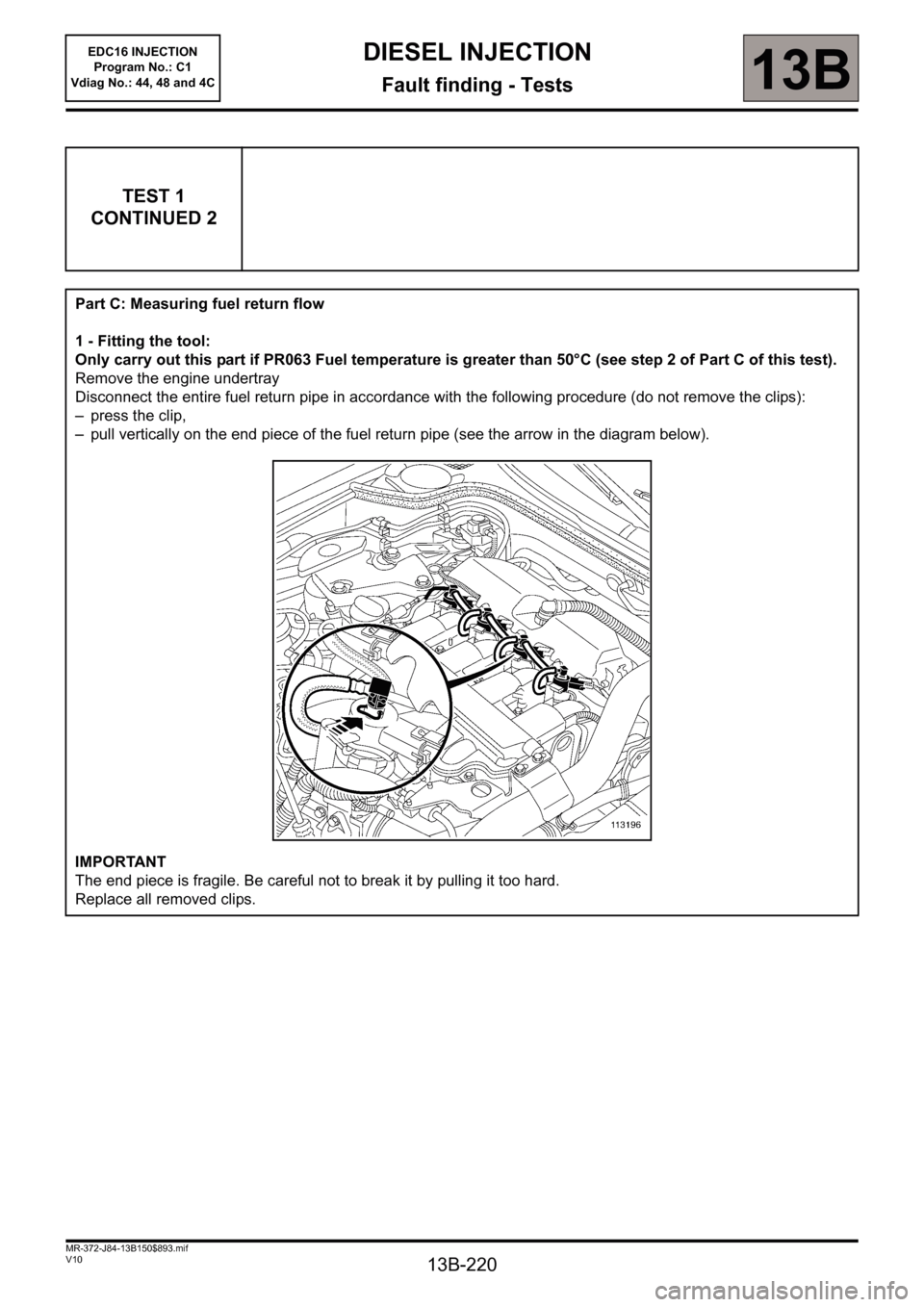
13B-220
MR-372-J84-13B150$893.mif
V10
DIESEL INJECTION
Fault finding - Tests
EDC16 INJECTION
Program No.: C1
Vdiag No.: 44, 48 and 4C
13B
TEST 1
CONTINUED 2
Part C: Measuring fuel return flow
1 - Fitting the tool:
Only carry out this part if PR063 Fuel temperature is greater than 50°C (see step 2 of Part C of this test).
Remove the engine undertray
Disconnect the entire fuel return pipe in accordance with the following procedure (do not remove the clips):
– press the clip,
– pull vertically on the end piece of the fuel return pipe (see the arrow in the diagram below).
IMPORTANT
The end piece is fragile. Be careful not to break it by pulling it too hard.
Replace all removed clips.
Page 221 of 236
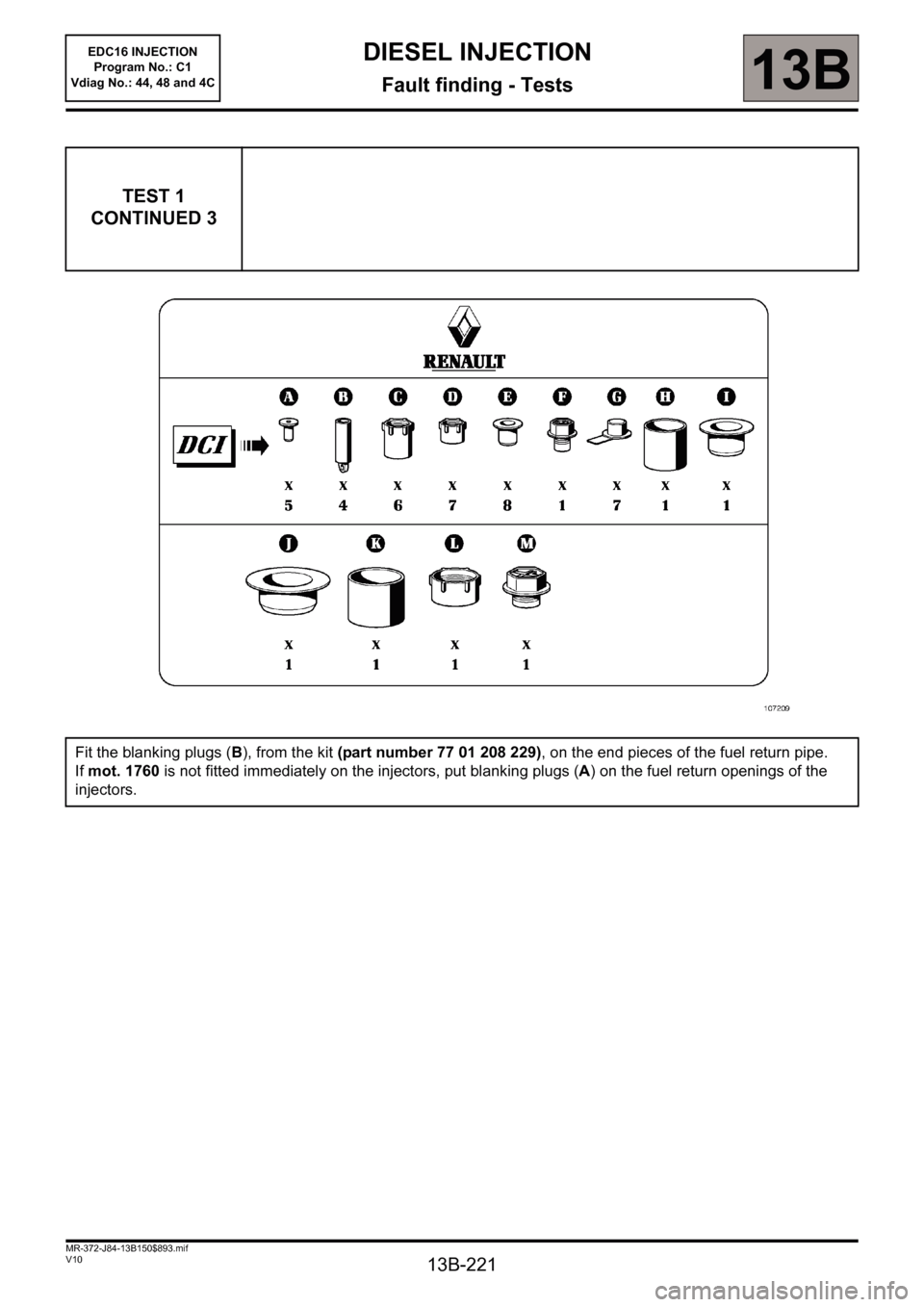
13B-221
MR-372-J84-13B150$893.mif
V10
DIESEL INJECTION
Fault finding - Tests
EDC16 INJECTION
Program No.: C1
Vdiag No.: 44, 48 and 4C
13B
TEST 1
CONTINUED 3
Fit the blanking plugs (B), from the kit (part number 77 01 208 229), on the end pieces of the fuel return pipe.
If mot. 1760 is not fitted immediately on the injectors, put blanking plugs (A) on the fuel return openings of the
injectors.
Page 223 of 236
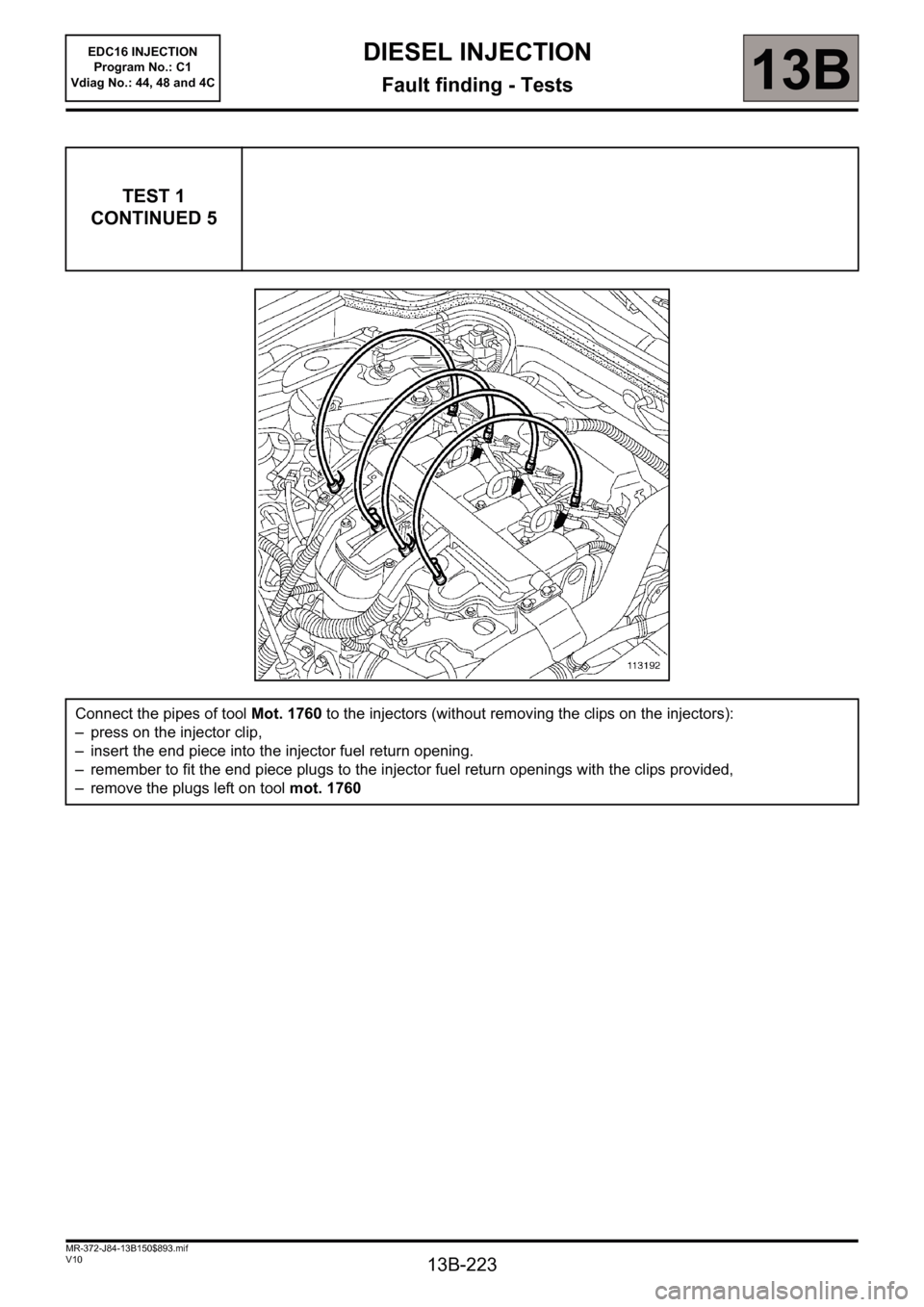
13B-223
MR-372-J84-13B150$893.mif
V10
DIESEL INJECTION
Fault finding - Tests
EDC16 INJECTION
Program No.: C1
Vdiag No.: 44, 48 and 4C
13B
TEST 1
CONTINUED 5
Connect the pipes of tool Mot. 1760 to the injectors (without removing the clips on the injectors):
– press on the injector clip,
– insert the end piece into the injector fuel return opening.
– remember to fit the end piece plugs to the injector fuel return openings with the clips provided,
– remove the plugs left on tool mot. 1760
Page 225 of 236
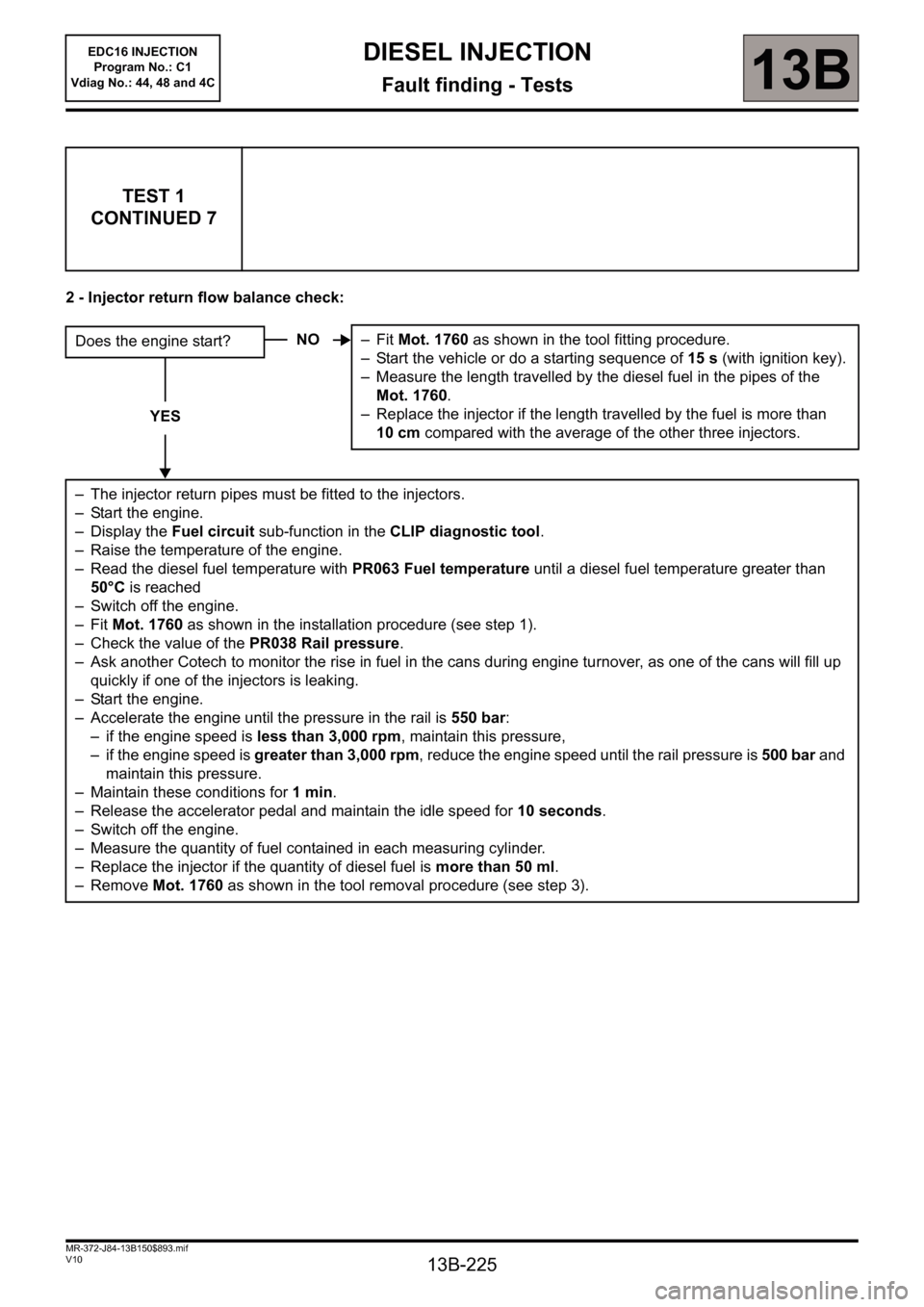
13B-225
MR-372-J84-13B150$893.mif
V10
EDC16 INJECTION
Program No.: C1
Vdiag No.: 44, 48 and 4CDIESEL INJECTION
Fault finding - Tests13B
2 - Injector return flow balance check:
TEST 1
CONTINUED 7
Does the engine start?
YES
– The injector return pipes must be fitted to the injectors.
– Start the engine.
– Display the Fuel circuit sub-function in the CLIP diagnostic tool.
– Raise the temperature of the engine.
– Read the diesel fuel temperature with PR063 Fuel temperature until a diesel fuel temperature greater than
50°C is reached
– Switch off the engine.
–Fit Mot. 1760 as shown in the installation procedure (see step 1).
– Check the value of the PR038 Rail pressure.
– Ask another Cotech to monitor the rise in fuel in the cans during engine turnover, as one of the cans will fill up
quickly if one of the injectors is leaking.
– Start the engine.
– Accelerate the engine until the pressure in the rail is 550 bar:
– if the engine speed is less than 3,000 rpm, maintain this pressure,
– if the engine speed is greater than 3,000 rpm, reduce the engine speed until the rail pressure is 500 bar and
maintain this pressure.
– Maintain these conditions for 1min.
– Release the accelerator pedal and maintain the idle speed for 10 seconds.
– Switch off the engine.
– Measure the quantity of fuel contained in each measuring cylinder.
– Replace the injector if the quantity of diesel fuel is more than 50 ml.
– Remove Mot. 1760 as shown in the tool removal procedure (see step 3).NO–Fit Mot. 1760 as shown in the tool fitting procedure.
– Start the vehicle or do a starting sequence of 15 s (with ignition key).
– Measure the length travelled by the diesel fuel in the pipes of the
Mot. 1760.
– Replace the injector if the length travelled by the fuel is more than
10 cm compared with the average of the other three injectors.