fuel filter RENAULT SCENIC 2011 J95 / 3.G Engine And Peripherals EDC16 User Guide
[x] Cancel search | Manufacturer: RENAULT, Model Year: 2011, Model line: SCENIC, Model: RENAULT SCENIC 2011 J95 / 3.GPages: 365, PDF Size: 2.11 MB
Page 317 of 365
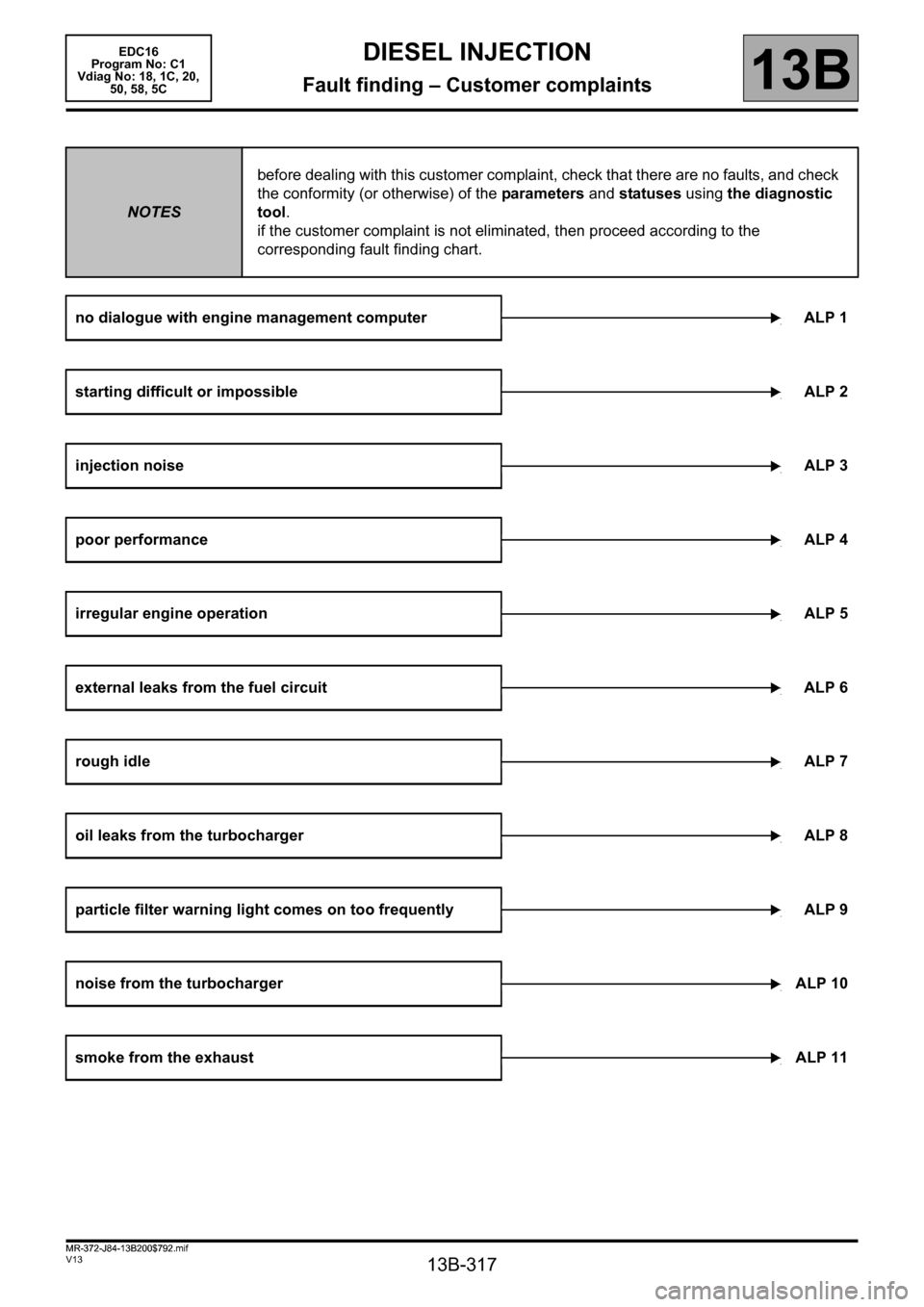
13B-317
MR-372-J84-13B200$792.mif
V13
13B
DIESEL INJECTION
Fault finding – Customer complaints
NOTESbefore dealing with this customer complaint, check that there are no faults, and check
the conformity (or otherwise) of the parameters and statuses using the diagnostic
tool.
if the customer complaint is not eliminated, then proceed according to the
corresponding fault finding chart.
no dialogue with engine management computer ALP 1
starting difficult or impossibleALP 2
injection noiseALP 3
poor performanceALP 4
irregular engine operationALP 5
external leaks from the fuel circuit ALP 6
rough idleALP 7
oil leaks from the turbochargerALP 8
particle filter warning light comes on too frequently ALP 9
noise from the turbochargerALP 10
smoke from the exhaustALP 11
EDC16
Program No: C1
Vdiag No: 18, 1C, 20,
50, 58, 5C
MR-372-J84-13B200$792.mif
Page 321 of 365
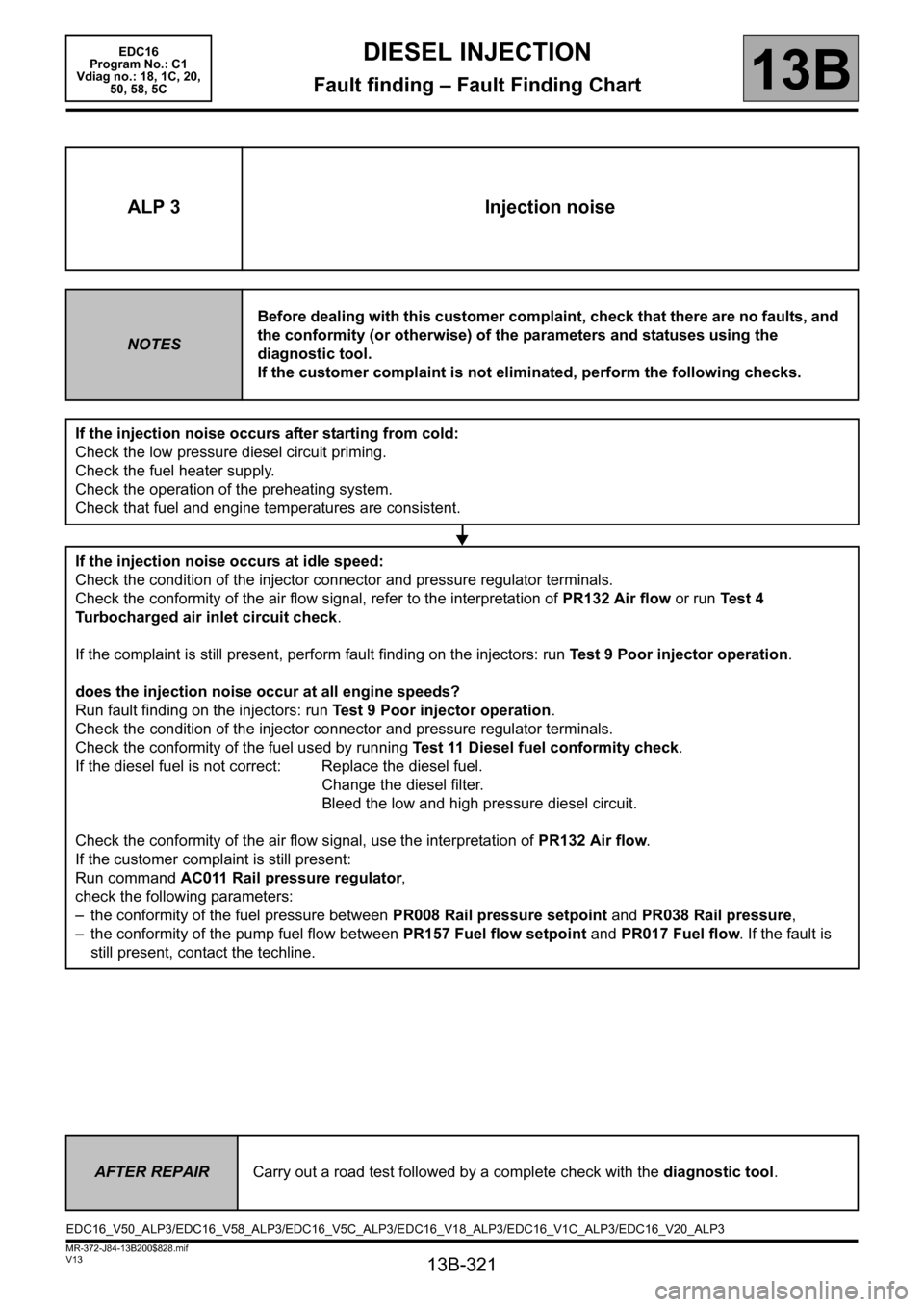
13B-321
MR-372-J84-13B200$828.mif
V13
DIESEL INJECTION
Fault finding – Fault Finding Chart
EDC16
Program No.: C1
Vdiag no.: 18, 1C, 20,
50, 58, 5C
13B
ALP 3 Injection noise
NOTESBefore dealing with this customer complaint, check that there are no faults, and
the conformity (or otherwise) of the parameters and statuses using the
diagnostic tool.
If the customer complaint is not eliminated, perform the following checks.
If the injection noise occurs after starting from cold:
Check the low pressure diesel circuit priming.
Check the fuel heater supply.
Check the operation of the preheating system.
Check that fuel and engine temperatures are consistent.
If the injection noise occurs at idle speed:
Check the condition of the injector connector and pressure regulator terminals.
Check the conformity of the air flow signal, refer to the interpretation of PR132 Air flow or run Test 4
Turbocharged air inlet circuit check.
If the complaint is still present, perform fault finding on the injectors: run Test 9 Poor injector operation.
does the injection noise occur at all engine speeds?
Run fault finding on the injectors: run Test 9 Poor injector operation.
Check the condition of the injector connector and pressure regulator terminals.
Check the conformity of the fuel used by running Test 11 Diesel fuel conformity check.
If the diesel fuel is not correct: Replace the diesel fuel.
Change the diesel filter.
Bleed the low and high pressure diesel circuit.
Check the conformity of the air flow signal, use the interpretation of PR132 Air flow.
If the customer complaint is still present:
Run command AC011 Rail pressure regulator,
check the following parameters:
– the conformity of the fuel pressure between PR008 Rail pressure setpoint and PR038 Rail pressure,
– the conformity of the pump fuel flow between PR157 Fuel flow setpoint and PR017 Fuel flow. If the fault is
still present, contact the techline.
AFTER REPAIRCarry out a road test followed by a complete check with the diagnostic tool.
EDC16_V50_ALP3/EDC16_V58_ALP3/EDC16_V5C_ALP3/EDC16_V18_ALP3/EDC16_V1C_ALP3/EDC16_V20_ALP3
Page 322 of 365
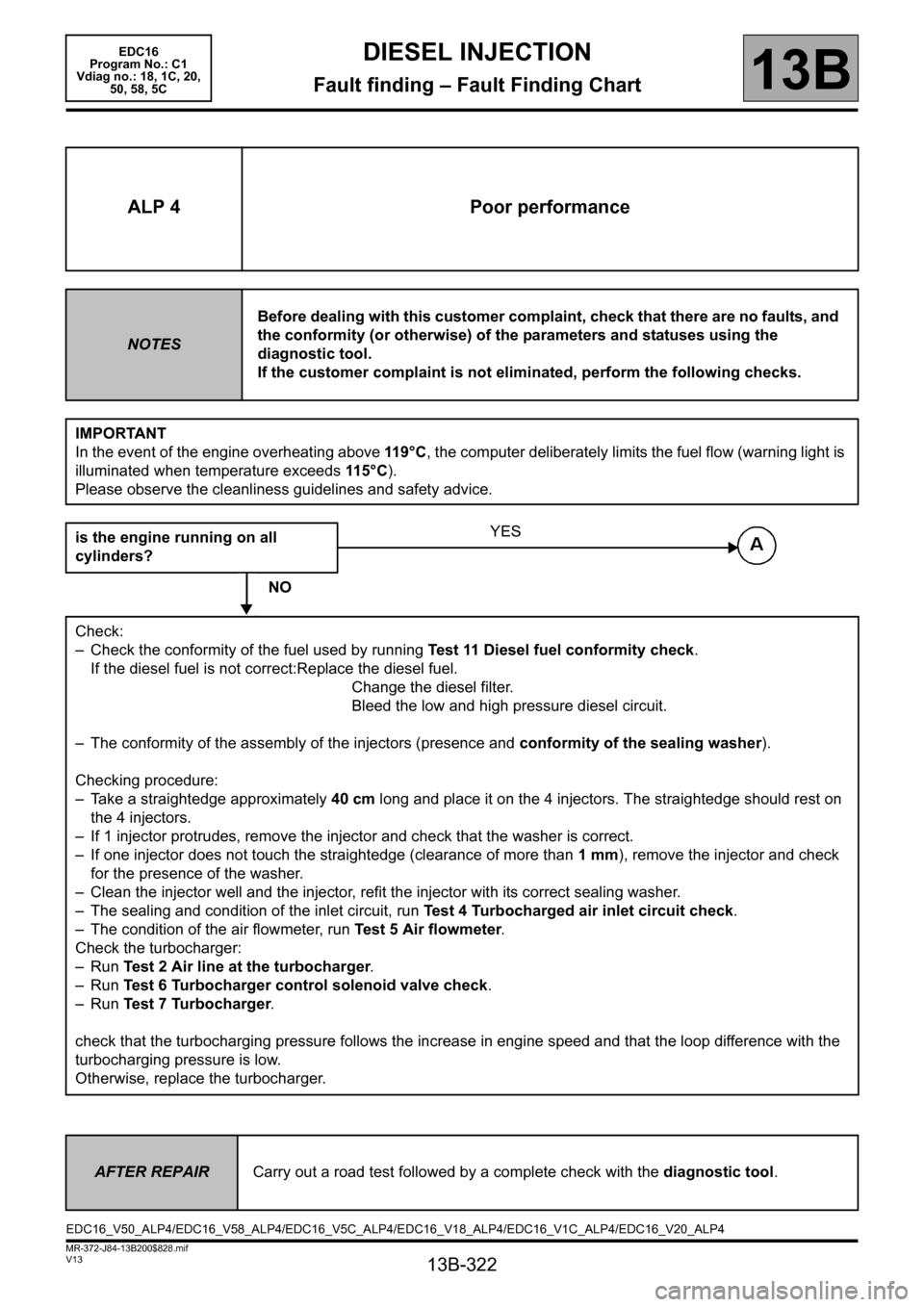
13B-322
MR-372-J84-13B200$828.mif
V13
EDC16
Program No.: C1
Vdiag no.: 18, 1C, 20,
50, 58, 5CDIESEL INJECTION
Fault finding – Fault Finding Chart13B
ALP 4 Poor performance
NOTESBefore dealing with this customer complaint, check that there are no faults, and
the conformity (or otherwise) of the parameters and statuses using the
diagnostic tool.
If the customer complaint is not eliminated, perform the following checks.
IMPORTANT
In the event of the engine overheating above 119°C, the computer deliberately limits the fuel flow (warning light is
illuminated when temperature exceeds 115 ° C).
Please observe the cleanliness guidelines and safety advice.
is the engine running on all
cylinders?
NO
Check:
– Check the conformity of the fuel used by running Test 11 Diesel fuel conformity check.
If the diesel fuel is not correct:Replace the diesel fuel.
Change the diesel filter.
Bleed the low and high pressure diesel circuit.
– The conformity of the assembly of the injectors (presence and conformity of the sealing washer).
Checking procedure:
– Take a straightedge approximately 40 cm long and place it on the 4 injectors. The straightedge should rest on
the 4 injectors.
– If 1 injector protrudes, remove the injector and check that the washer is correct.
– If one injector does not touch the straightedge (clearance of more than 1 mm), remove the injector and check
for the presence of the washer.
– Clean the injector well and the injector, refit the injector with its correct sealing washer.
– The sealing and condition of the inlet circuit, run Test 4 Turbocharged air inlet circuit check.
– The condition of the air flowmeter, run Test 5 Air flowmeter.
Check the turbocharger:
–Run Test 2 Air line at the turbocharger.
–Run Test 6 Turbocharger control solenoid valve check.
–Run Test 7 Turbocharger.
check that the turbocharging pressure follows the increase in engine speed and that the loop difference with the
turbocharging pressure is low.
Otherwise, replace the turbocharger.
YES
AFTER REPAIRCarry out a road test followed by a complete check with the diagnostic tool.
EDC16_V50_ALP4/EDC16_V58_ALP4/EDC16_V5C_ALP4/EDC16_V18_ALP4/EDC16_V1C_ALP4/EDC16_V20_ALP4
Page 323 of 365
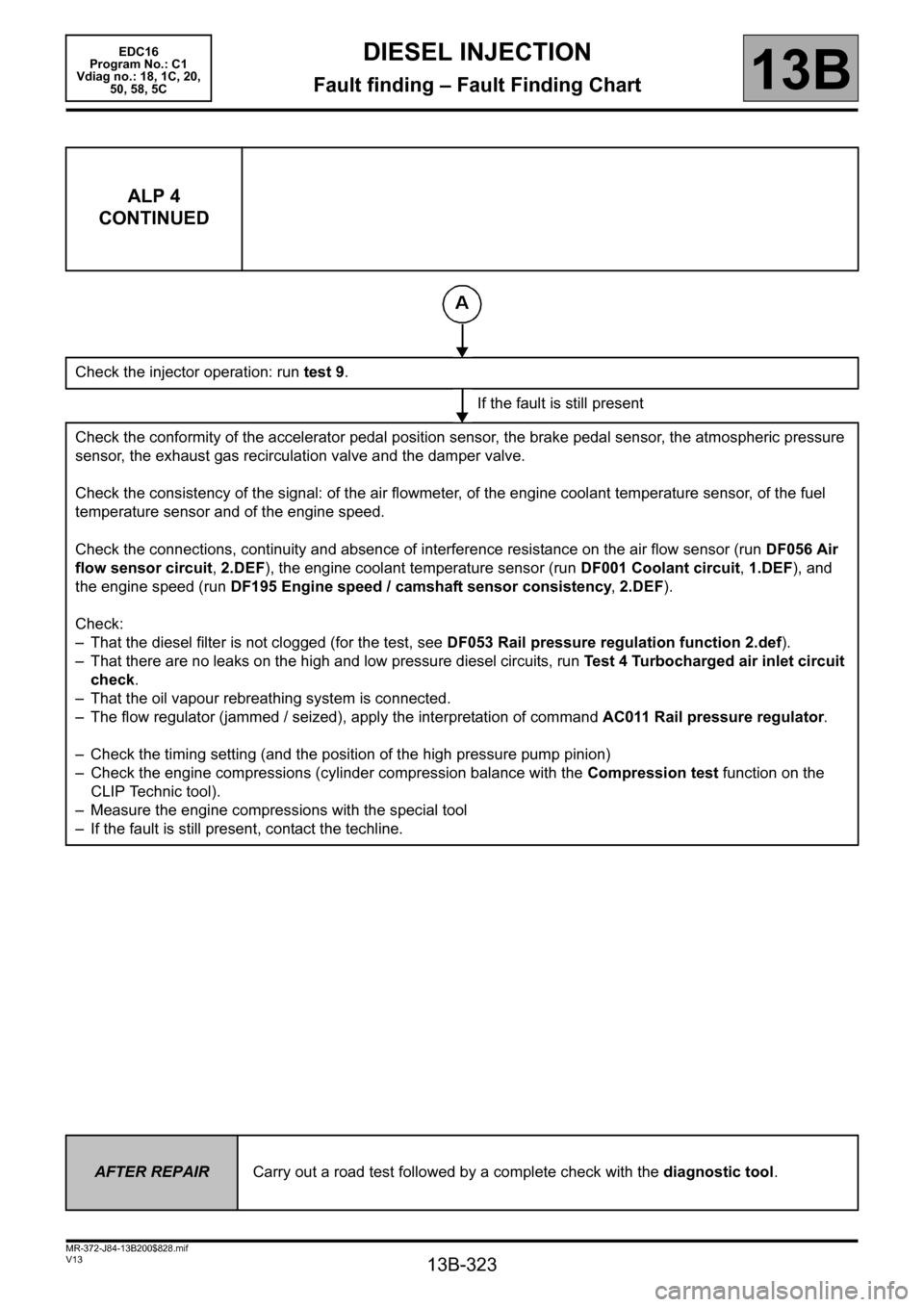
13B-323
MR-372-J84-13B200$828.mif
V13
DIESEL INJECTION
Fault finding – Fault Finding Chart
EDC16
Program No.: C1
Vdiag no.: 18, 1C, 20,
50, 58, 5C
13B
ALP 4
CONTINUED
Check the injector operation: run test 9.
If the fault is still present
Check the conformity of the accelerator pedal position sensor, the brake pedal sensor, the atmospheric pressure
sensor, the exhaust gas recirculation valve and the damper valve.
Check the consistency of the signal: of the air flowmeter, of the engine coolant temperature sensor, of the fuel
temperature sensor and of the engine speed.
Check the connections, continuity and absence of interference resistance on the air flow sensor (run DF056 Air
flow sensor circuit, 2.DEF), the engine coolant temperature sensor (run DF001 Coolant circuit, 1.DEF), and
the engine speed (run DF195 Engine speed / camshaft sensor consistency, 2.DEF).
Check:
– That the diesel filter is not clogged (for the test, see DF053 Rail pressure regulation function 2.def).
– That there are no leaks on the high and low pressure diesel circuits, run Test 4 Turbocharged air inlet circuit
check.
– That the oil vapour rebreathing system is connected.
– The flow regulator (jammed / seized), apply the interpretation of command AC011 Rail pressure regulator.
– Check the timing setting (and the position of the high pressure pump pinion)
– Check the engine compressions (cylinder compression balance with the Compression test function on the
CLIP Technic tool).
– Measure the engine compressions with the special tool
– If the fault is still present, contact the techline.
AFTER REPAIRCarry out a road test followed by a complete check with the diagnostic tool.
Page 325 of 365
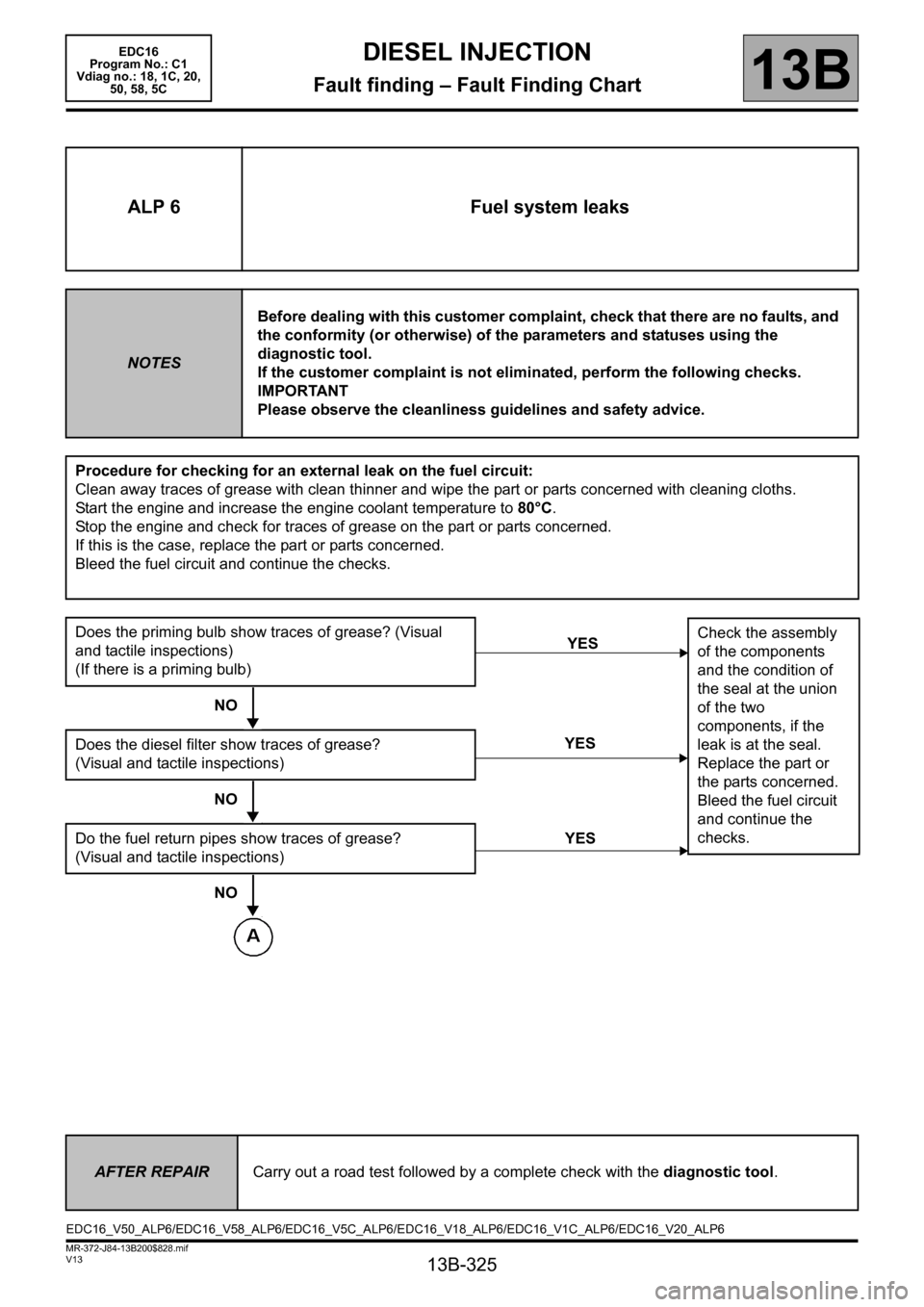
13B-325
MR-372-J84-13B200$828.mif
V13
EDC16
Program No.: C1
Vdiag no.: 18, 1C, 20,
50, 58, 5CDIESEL INJECTION
Fault finding – Fault Finding Chart13B
ALP 6 Fuel system leaks
NOTESBefore dealing with this customer complaint, check that there are no faults, and
the conformity (or otherwise) of the parameters and statuses using the
diagnostic tool.
If the customer complaint is not eliminated, perform the following checks.
IMPORTANT
Please observe the cleanliness guidelines and safety advice.
Procedure for checking for an external leak on the fuel circuit:
Clean away traces of grease with clean thinner and wipe the part or parts concerned with cleaning cloths.
Start the engine and increase the engine coolant temperature to 80°C.
Stop the engine and check for traces of grease on the part or parts concerned.
If this is the case, replace the part or parts concerned.
Bleed the fuel circuit and continue the checks.
Does the priming bulb show traces of grease? (Visual
and tactile inspections)
(If there is a priming bulb)
NO
Does the diesel filter show traces of grease?
(Visual and tactile inspections)
NO
Do the fuel return pipes show traces of grease?
(Visual and tactile inspections)
NO
YESCheck the assembly
of the components
and the condition of
the seal at the union
of the two
components, if the
leak is at the seal.
Replace the part or
the parts concerned.
Bleed the fuel circuit
and continue the
checks.
YES
YES
AFTER REPAIRCarry out a road test followed by a complete check with the diagnostic tool.
EDC16_V50_ALP6/EDC16_V58_ALP6/EDC16_V5C_ALP6/EDC16_V18_ALP6/EDC16_V1C_ALP6/EDC16_V20_ALP6
Page 328 of 365
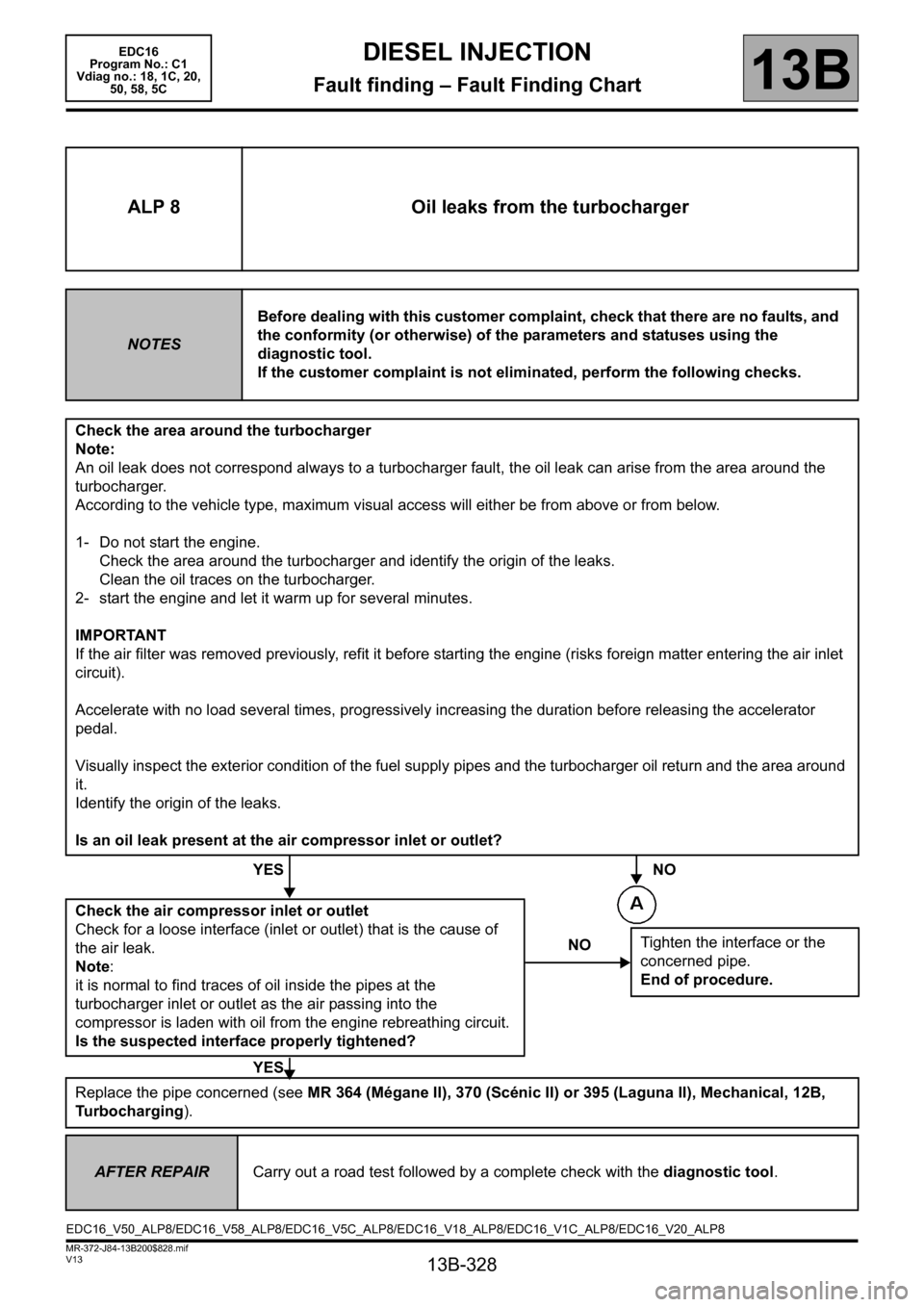
13B-328
MR-372-J84-13B200$828.mif
V13
EDC16
Program No.: C1
Vdiag no.: 18, 1C, 20,
50, 58, 5CDIESEL INJECTION
Fault finding – Fault Finding Chart13B
ALP 8 Oil leaks from the turbocharger
NOTESBefore dealing with this customer complaint, check that there are no faults, and
the conformity (or otherwise) of the parameters and statuses using the
diagnostic tool.
If the customer complaint is not eliminated, perform the following checks.
Check the area around the turbocharger
Note:
An oil leak does not correspond always to a turbocharger fault, the oil leak can arise from the area around the
turbocharger.
According to the vehicle type, maximum visual access will either be from above or from below.
1- Do not start the engine.
Check the area around the turbocharger and identify the origin of the leaks.
Clean the oil traces on the turbocharger.
2- start the engine and let it warm up for several minutes.
IMPORTANT
If the air filter was removed previously, refit it before starting the engine (risks foreign matter entering the air inlet
circuit).
Accelerate with no load several times, progressively increasing the duration before releasing the accelerator
pedal.
Visually inspect the exterior condition of the fuel supply pipes and the turbocharger oil return and the area around
it.
Identify the origin of the leaks.
Is an oil leak present at the air compressor inlet or outlet?
YES NO
Check the air compressor inlet or outlet
Check for a loose interface (inlet or outlet) that is the cause of
the air leak.
Note:
it is normal to find traces of oil inside the pipes at the
turbocharger inlet or outlet as the air passing into the
compressor is laden with oil from the engine rebreathing circuit.
Is the suspected interface properly tightened?
YES
Replace the pipe concerned (see MR 364 (Mégane II), 370 (Scénic II) or 395 (Laguna II), Mechanical, 12B,
Turbocharging).
NOTighten the interface or the
concerned pipe.
End of procedure.
AFTER REPAIRCarry out a road test followed by a complete check with the diagnostic tool.
EDC16_V50_ALP8/EDC16_V58_ALP8/EDC16_V5C_ALP8/EDC16_V18_ALP8/EDC16_V1C_ALP8/EDC16_V20_ALP8
Page 341 of 365
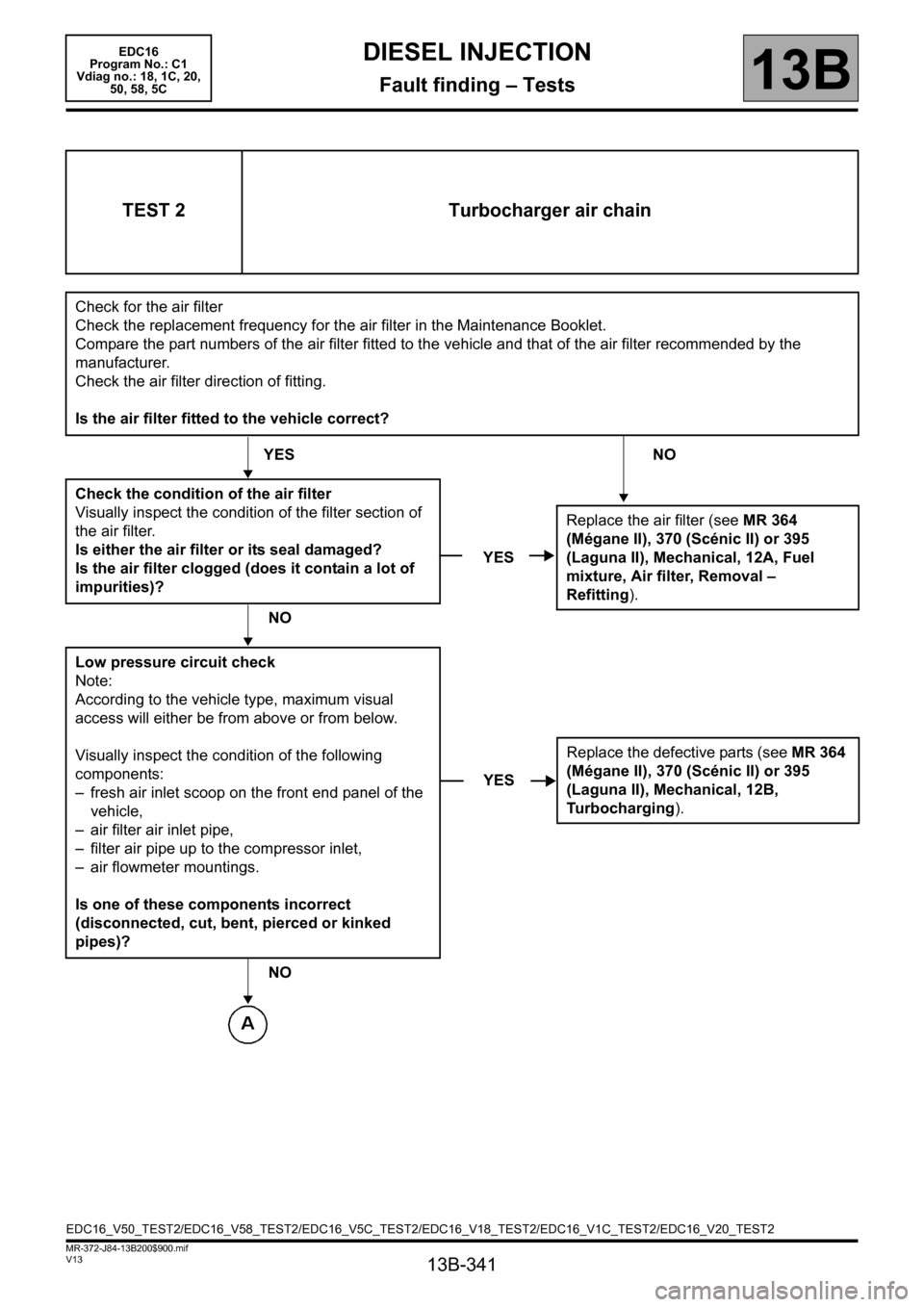
13B-341
MR-372-J84-13B200$900.mif
V13
EDC16
Program No.: C1
Vdiag no.: 18, 1C, 20,
50, 58, 5CDIESEL INJECTION
Fault finding – Tests13B
TEST 2 Turbocharger air chain
Check for the air filter
Check the replacement frequency for the air filter in the Maintenance Booklet.
Compare the part numbers of the air filter fitted to the vehicle and that of the air filter recommended by the
manufacturer.
Check the air filter direction of fitting.
Is the air filter fitted to the vehicle correct?
YES NO
Check the condition of the air filter
Visually inspect the condition of the filter section of
the air filter.
Is either the air filter or its seal damaged?
Is the air filter clogged (does it contain a lot of
impurities)?
NO
Low pressure circuit check
Note:
According to the vehicle type, maximum visual
access will either be from above or from below.
Visually inspect the condition of the following
components:
– fresh air inlet scoop on the front end panel of the
vehicle,
– air filter air inlet pipe,
– filter air pipe up to the compressor inlet,
– air flowmeter mountings.
Is one of these components incorrect
(disconnected, cut, bent, pierced or kinked
pipes)?
NO
YESReplace the air filter (see MR 364
(Mégane II), 370 (Scénic II) or 395
(Laguna II), Mechanical, 12A, Fuel
mixture, Air filter, Removal –
Refitting).
YESReplace the defective parts (see MR 364
(Mégane II), 370 (Scénic II) or 395
(Laguna II), Mechanical, 12B,
Turbocharging).
EDC16_V50_TEST2/EDC16_V58_TEST2/EDC16_V5C_TEST2/EDC16_V18_TEST2/EDC16_V1C_TEST2/EDC16_V20_TEST2
Page 343 of 365
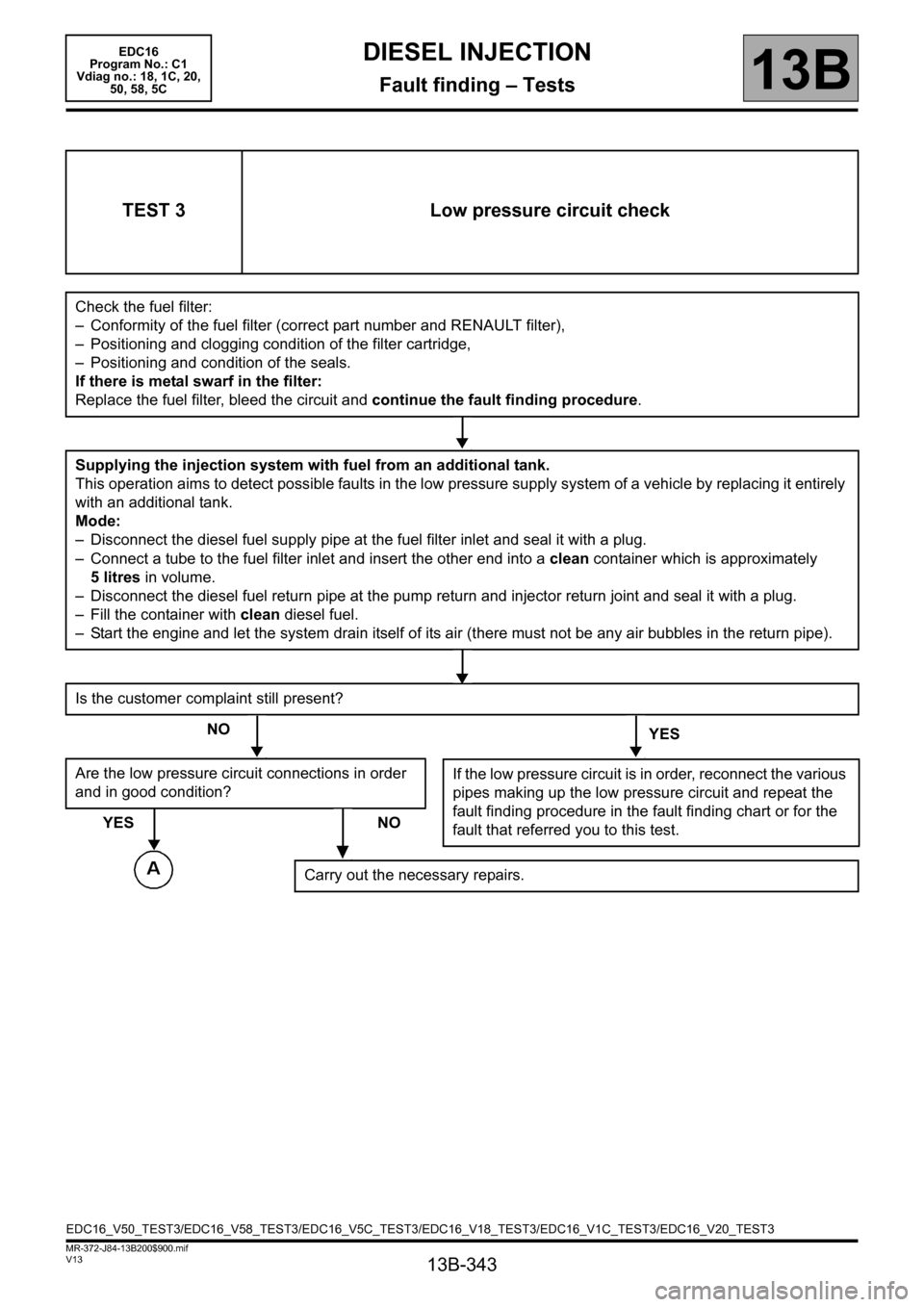
13B-343
MR-372-J84-13B200$900.mif
V13
EDC16
Program No.: C1
Vdiag no.: 18, 1C, 20,
50, 58, 5CDIESEL INJECTION
Fault finding – Tests13B
TEST 3 Low pressure circuit check
Check the fuel filter:
– Conformity of the fuel filter (correct part number and RENAULT filter),
– Positioning and clogging condition of the filter cartridge,
– Positioning and condition of the seals.
If there is metal swarf in the filter:
Replace the fuel filter, bleed the circuit and continue the fault finding procedure.
Supplying the injection system with fuel from an additional tank.
This operation aims to detect possible faults in the low pressure supply system of a vehicle by replacing it entirely
with an additional tank.
Mode:
– Disconnect the diesel fuel supply pipe at the fuel filter inlet and seal it with a plug.
– Connect a tube to the fuel filter inlet and insert the other end into a clean container which is approximately
5 litres in volume.
– Disconnect the diesel fuel return pipe at the pump return and injector return joint and seal it with a plug.
– Fill the container with clean diesel fuel.
– Start the engine and let the system drain itself of its air (there must not be any air bubbles in the return pipe).
Is the customer complaint still present?
NO
YES
Are the low pressure circuit connections in order
and in good condition?
YES NO
If the low pressure circuit is in order, reconnect the various
pipes making up the low pressure circuit and repeat the
fault finding procedure in the fault finding chart or for the
fault that referred you to this test.
Carry out the necessary repairs.
EDC16_V50_TEST3/EDC16_V58_TEST3/EDC16_V5C_TEST3/EDC16_V18_TEST3/EDC16_V1C_TEST3/EDC16_V20_TEST3
Page 344 of 365
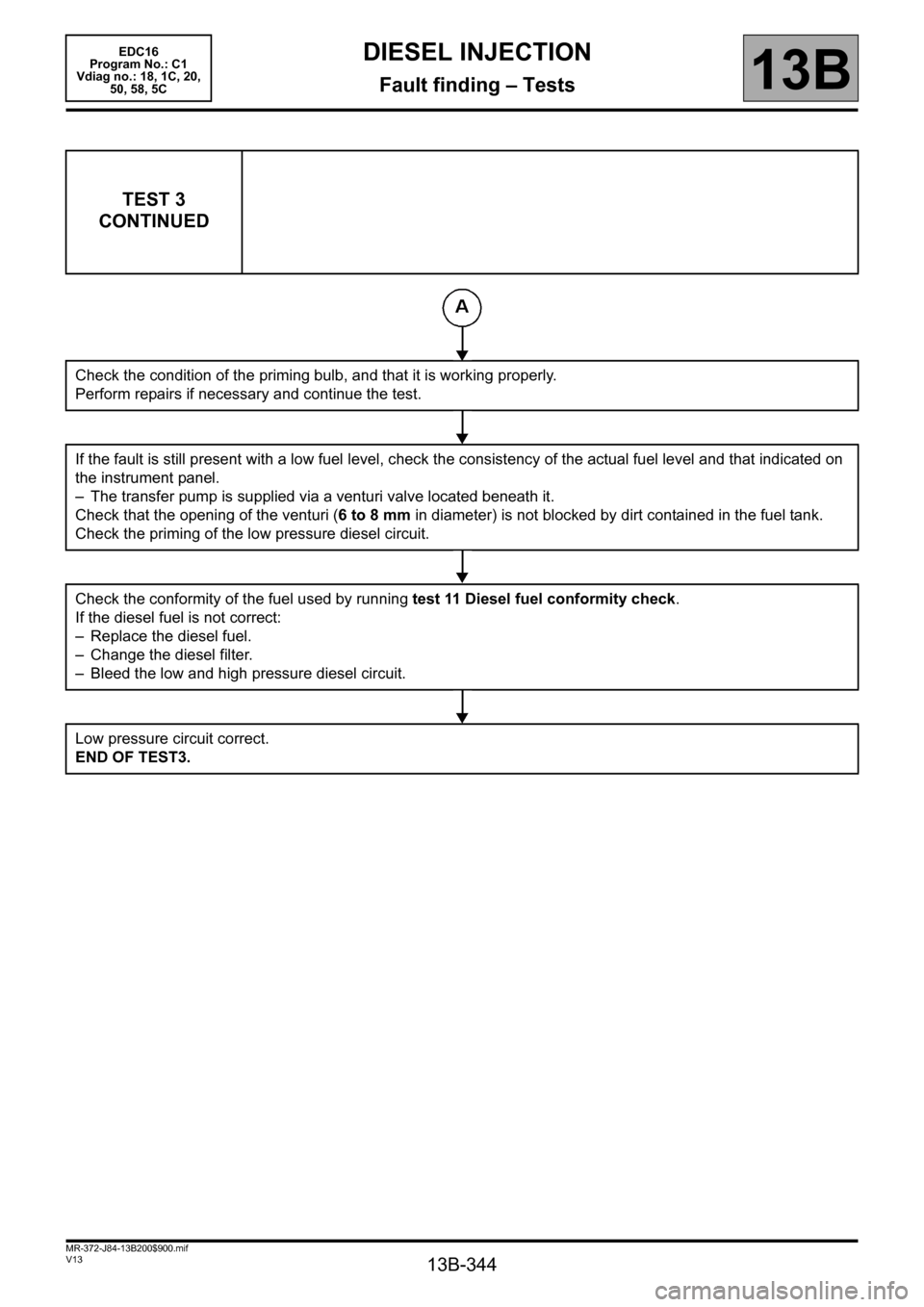
13B-344
MR-372-J84-13B200$900.mif
V13
DIESEL INJECTION
Fault finding – Tests
EDC16
Program No.: C1
Vdiag no.: 18, 1C, 20,
50, 58, 5C
13B
TEST 3
CONTINUED
Check the condition of the priming bulb, and that it is working properly.
Perform repairs if necessary and continue the test.
If the fault is still present with a low fuel level, check the consistency of the actual fuel level and that indicated on
the instrument panel.
– The transfer pump is supplied via a venturi valve located beneath it.
Check that the opening of the venturi (6 to 8 mm in diameter) is not blocked by dirt contained in the fuel tank.
Check the priming of the low pressure diesel circuit.
Check the conformity of the fuel used by running test 11 Diesel fuel conformity check.
If the diesel fuel is not correct:
– Replace the diesel fuel.
– Change the diesel filter.
– Bleed the low and high pressure diesel circuit.
Low pressure circuit correct.
END OF TEST3.
Page 358 of 365
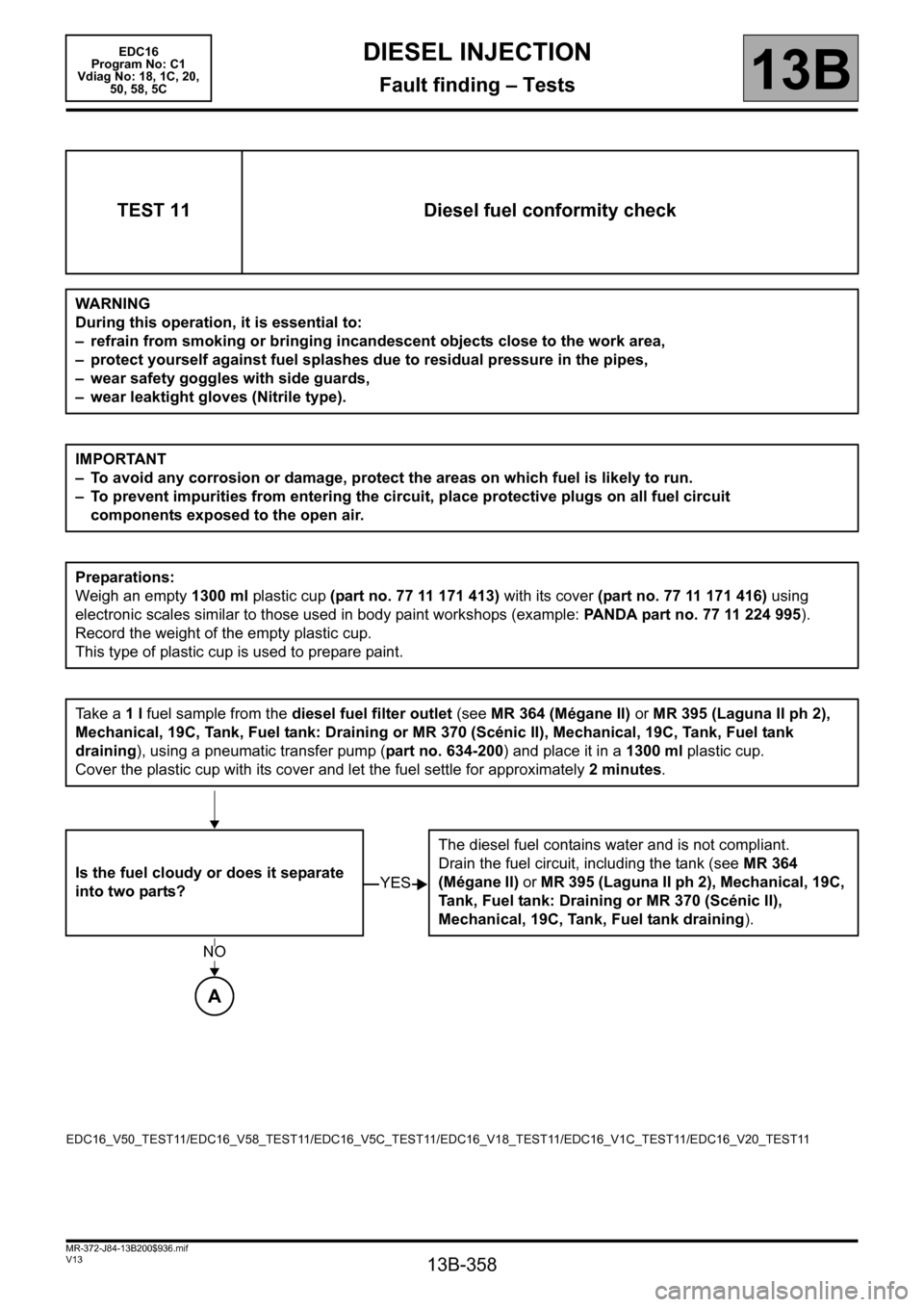
13B-358
MR-372-J84-13B200$936.mif
V13
DIESEL INJECTION
Fault finding – Tests
EDC16
Program No: C1
Vdiag No: 18, 1C, 20,
50, 58, 5C
13B
TEST 11 Diesel fuel conformity check
WARNING
During this operation, it is essential to:
– refrain from smoking or bringing incandescent objects close to the work area,
– protect yourself against fuel splashes due to residual pressure in the pipes,
– wear safety goggles with side guards,
– wear leaktight gloves (Nitrile type).
IMPORTANT
– To avoid any corrosion or damage, protect the areas on which fuel is likely to run.
– To prevent impurities from entering the circuit, place protective plugs on all fuel circuit
components exposed to the open air.
Preparations:
Weigh an empty 1300 ml plastic cup (part no. 77 11 171 413) with its cover (part no. 77 11 171 416) using
electronic scales similar to those used in body paint workshops (example: PANDA part no. 77 11 224 995).
Record the weight of the empty plastic cup.
This type of plastic cup is used to prepare paint.
Ta k e a 1 l fuel sample from the diesel fuel filter outlet (see MR 364 (Mégane II) or MR 395 (Laguna II ph 2),
Mechanical, 19C, Tank, Fuel tank: Draining or MR 370 (Scénic II), Mechanical, 19C, Tank, Fuel tank
draining), using a pneumatic transfer pump (part no. 634-200) and place it in a 1300 ml plastic cup.
Cover the plastic cup with its cover and let the fuel settle for approximately 2 minutes.
Is the fuel cloudy or does it separate
into two parts?The diesel fuel contains water and is not compliant.
Drain the fuel circuit, including the tank (see MR 364
(Mégane II) or MR 395 (Laguna II ph 2), Mechanical, 19C,
Tank, Fuel tank: Draining or MR 370 (Scénic II),
Mechanical, 19C, Tank, Fuel tank draining).
YES
NO
A
EDC16_V50_TEST11/EDC16_V58_TEST11/EDC16_V5C_TEST11/EDC16_V18_TEST11/EDC16_V1C_TEST11/EDC16_V20_TEST11