RENAULT SCENIC 2011 J95 / 3.G Engine And Peripherals EDC16C36 Workshop Manual
Manufacturer: RENAULT, Model Year: 2011, Model line: SCENIC, Model: RENAULT SCENIC 2011 J95 / 3.GPages: 431, PDF Size: 2.03 MB
Page 411 of 431
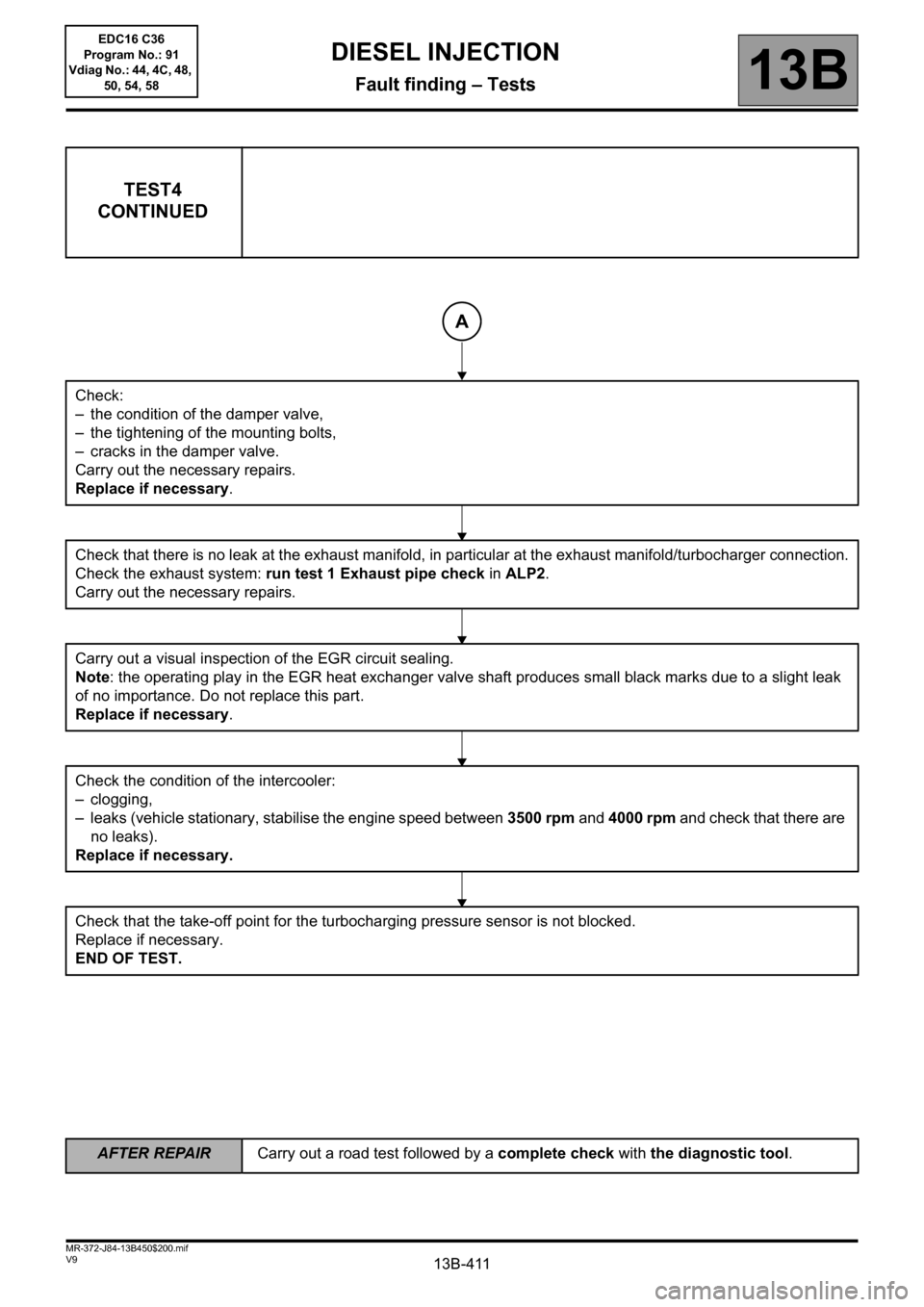
13B-411V9 MR-372-J84-13B450$200.mif
DIESEL INJECTION
Fault finding – Tests13B
TEST4
CONTINUED
Check:
– the condition of the damper valve,
– the tightening of the mounting bolts,
– cracks in the damper valve.
Carry out the necessary repairs.
Replace if necessary.
Check that there is no leak at the exhaust manifold, in particular at the exhaust manifold/turbocharger connection.
Check the exhaust system: run test 1 Exhaust pipe check in ALP2.
Carry out the necessary repairs.
Carry out a visual inspection of the EGR circuit sealing.
Note: the operating play in the EGR heat exchanger valve shaft produces small black marks due to a slight leak
of no importance. Do not replace this part.
Replace if necessary.
Check the condition of the intercooler:
– clogging,
– leaks (vehicle stationary, stabilise the engine speed between 3500 rpm and 4000 rpm and check that there are
no leaks).
Replace if necessary.
Check that the take-off point for the turbocharging pressure sensor is not blocked.
Replace if necessary.
END OF TEST.
A
AFTER REPAIRCarry out a road test followed by a complete check with the diagnostic tool.
EDC16 C36
Program No.: 91
Vdiag No.: 44, 4C, 48,
50, 54, 58
Page 412 of 431
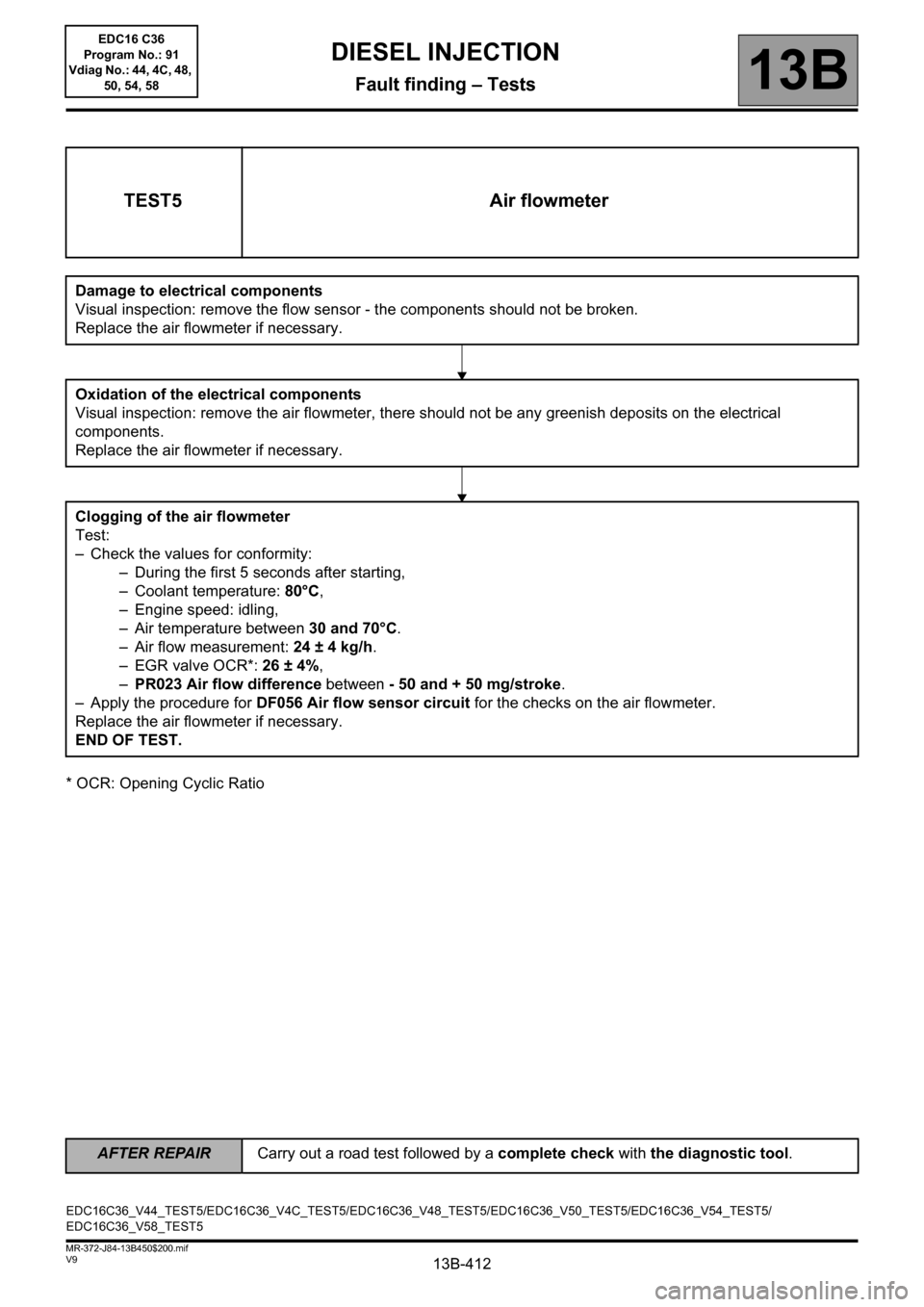
13B-412V9 MR-372-J84-13B450$200.mif
DIESEL INJECTION
Fault finding – Tests13B
* OCR: Opening Cyclic Ratio
TEST5 Air flowmeter
Damage to electrical components
Visual inspection: remove the flow sensor - the components should not be broken.
Replace the air flowmeter if necessary.
Oxidation of the electrical components
Visual inspection: remove the air flowmeter, there should not be any greenish deposits on the electrical
components.
Replace the air flowmeter if necessary.
Clogging of the air flowmeter
Test:
– Check the values for conformity:
– During the first 5 seconds after starting,
– Coolant temperature: 80°C,
– Engine speed: idling,
– Air temperature between 30 and 70°C.
– Air flow measurement: 24 ± 4 kg/h.
– EGR valve OCR*: 26 ± 4%,
–PR023 Air flow difference between - 50 and + 50 mg/stroke.
– Apply the procedure for DF056 Air flow sensor circuit for the checks on the air flowmeter.
Replace the air flowmeter if necessary.
END OF TEST.
EDC16C36_V44_TEST5/EDC16C36_V4C_TEST5/EDC16C36_V48_TEST5/EDC16C36_V50_TEST5/EDC16C36_V54_TEST5/
EDC16C36_V58_TEST5
AFTER REPAIRCarry out a road test followed by a complete check with the diagnostic tool.
EDC16 C36
Program No.: 91
Vdiag No.: 44, 4C, 48,
50, 54, 58
Page 413 of 431
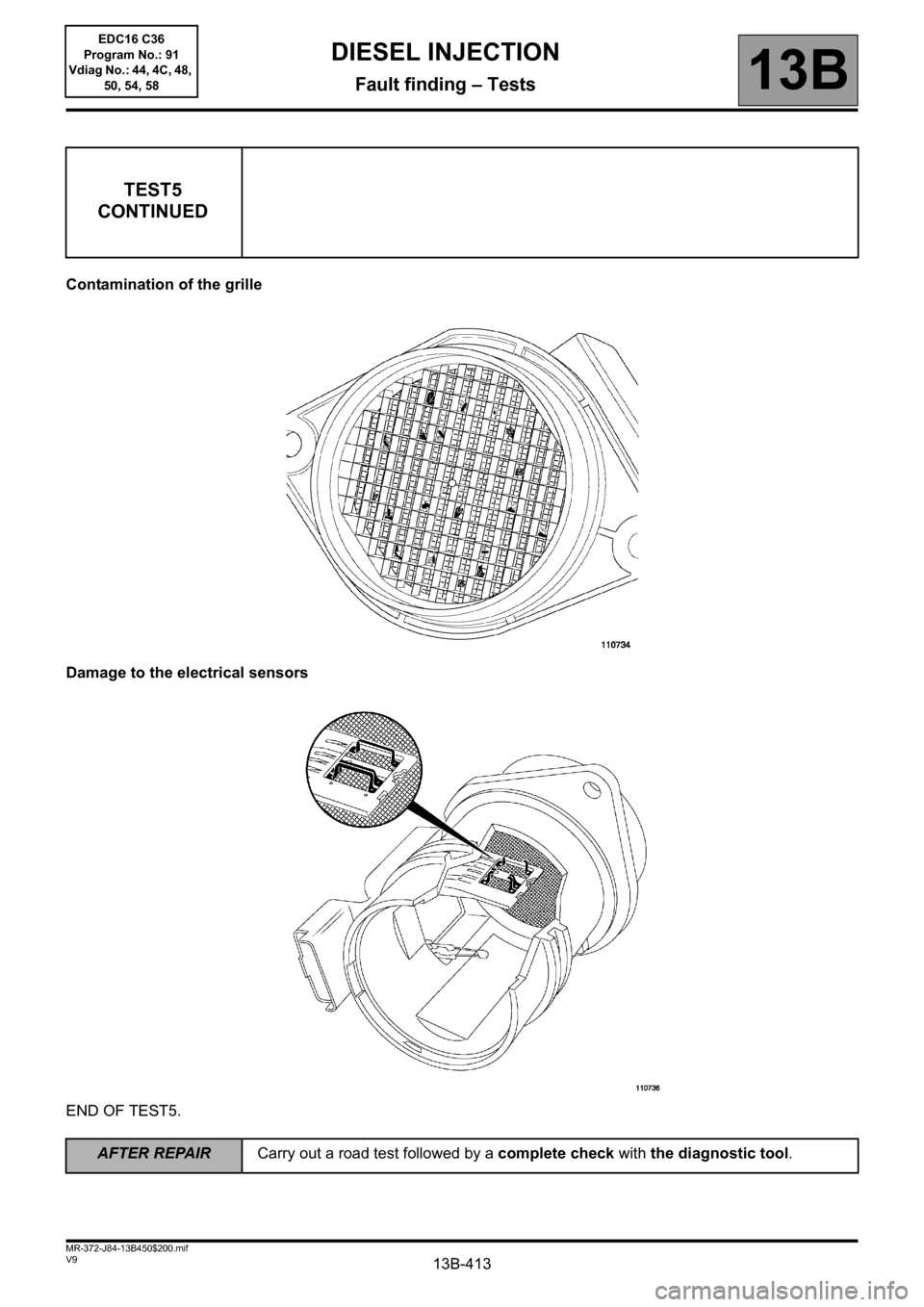
13B-413V9 MR-372-J84-13B450$200.mif
DIESEL INJECTION
Fault finding – Tests13B
Contamination of the grille
Damage to the electrical sensors
END OF TEST5.
TEST5
CONTINUED
AFTER REPAIRCarry out a road test followed by a complete check with the diagnostic tool.
EDC16 C36
Program No.: 91
Vdiag No.: 44, 4C, 48,
50, 54, 58
Page 414 of 431
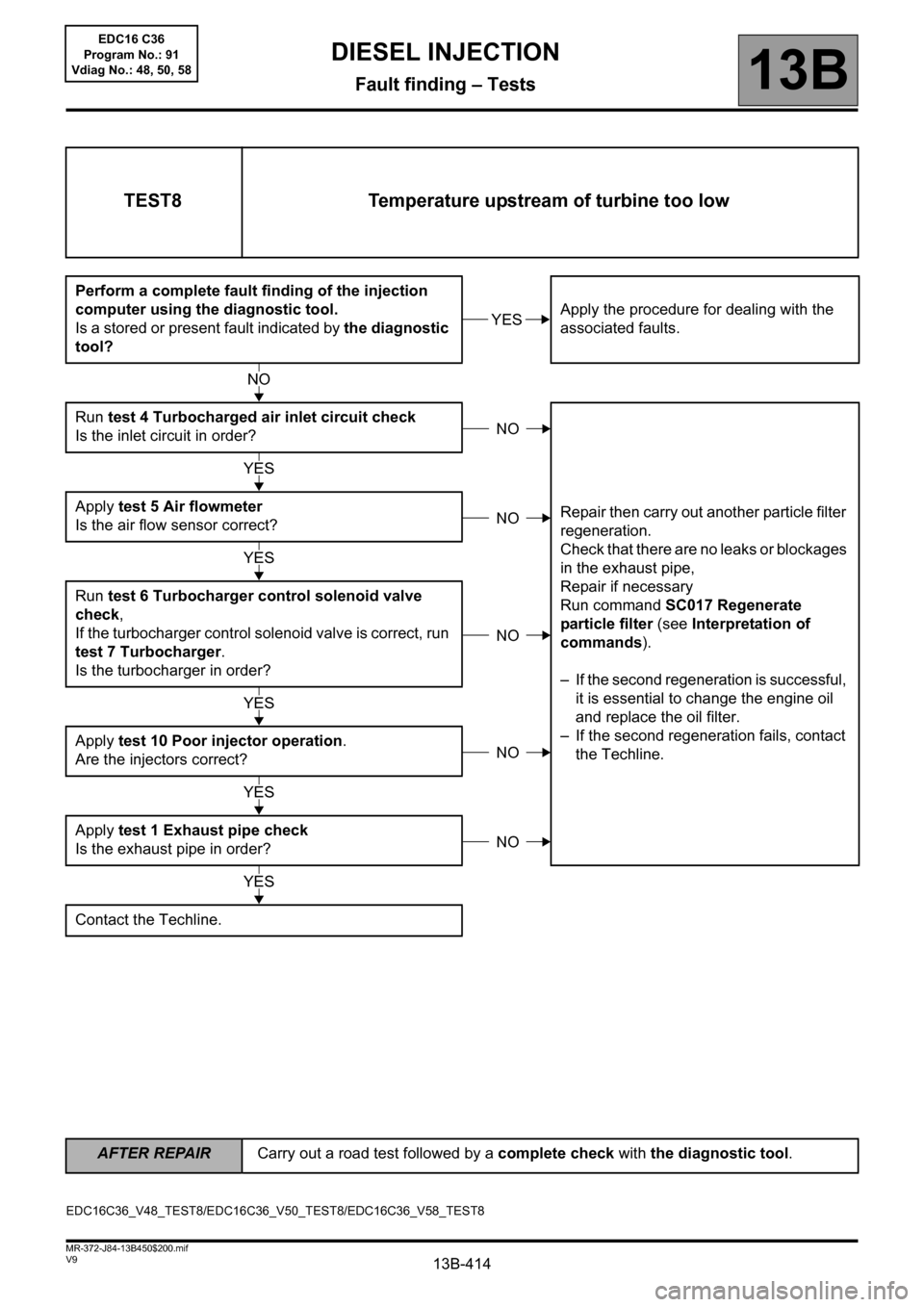
13B-414V9 MR-372-J84-13B450$200.mif
DIESEL INJECTION
Fault finding – Tests13B
TEST8 Temperature upstream of turbine too low
Perform a complete fault finding of the injection
computer using the diagnostic tool.
Is a stored or present fault indicated by the diagnostic
tool?Apply the procedure for dealing with the
associated faults.
Run test 4 Turbocharged air inlet circuit check
Is the inlet circuit in order?
Repair then carry out another particle filter
regeneration.
Check that there are no leaks or blockages
in the exhaust pipe,
Repair if necessary
Run command SC017 Regenerate
particle filter (see Interpretation of
commands).
– If the second regeneration is successful,
it is essential to change the engine oil
and replace the oil filter.
– If the second regeneration fails, contact
the Techline. Apply test 5 Air flowmeter
Is the air flow sensor correct?
Run test 6 Turbocharger control solenoid valve
check,
If the turbocharger control solenoid valve is correct, run
test 7 Turbocharger.
Is the turbocharger in order?
Apply test 10 Poor injector operation.
Are the injectors correct?
Apply test 1 Exhaust pipe check
Is the exhaust pipe in order?
Contact the Techline.
YES
NO
NO
YES
NO
YES
NO
YES
NO
YES
NO
YES
EDC16C36_V48_TEST8/EDC16C36_V50_TEST8/EDC16C36_V58_TEST8
AFTER REPAIRCarry out a road test followed by a complete check with the diagnostic tool.
EDC16 C36
Program No.: 91
Vdiag No.: 48, 50, 58
Page 415 of 431
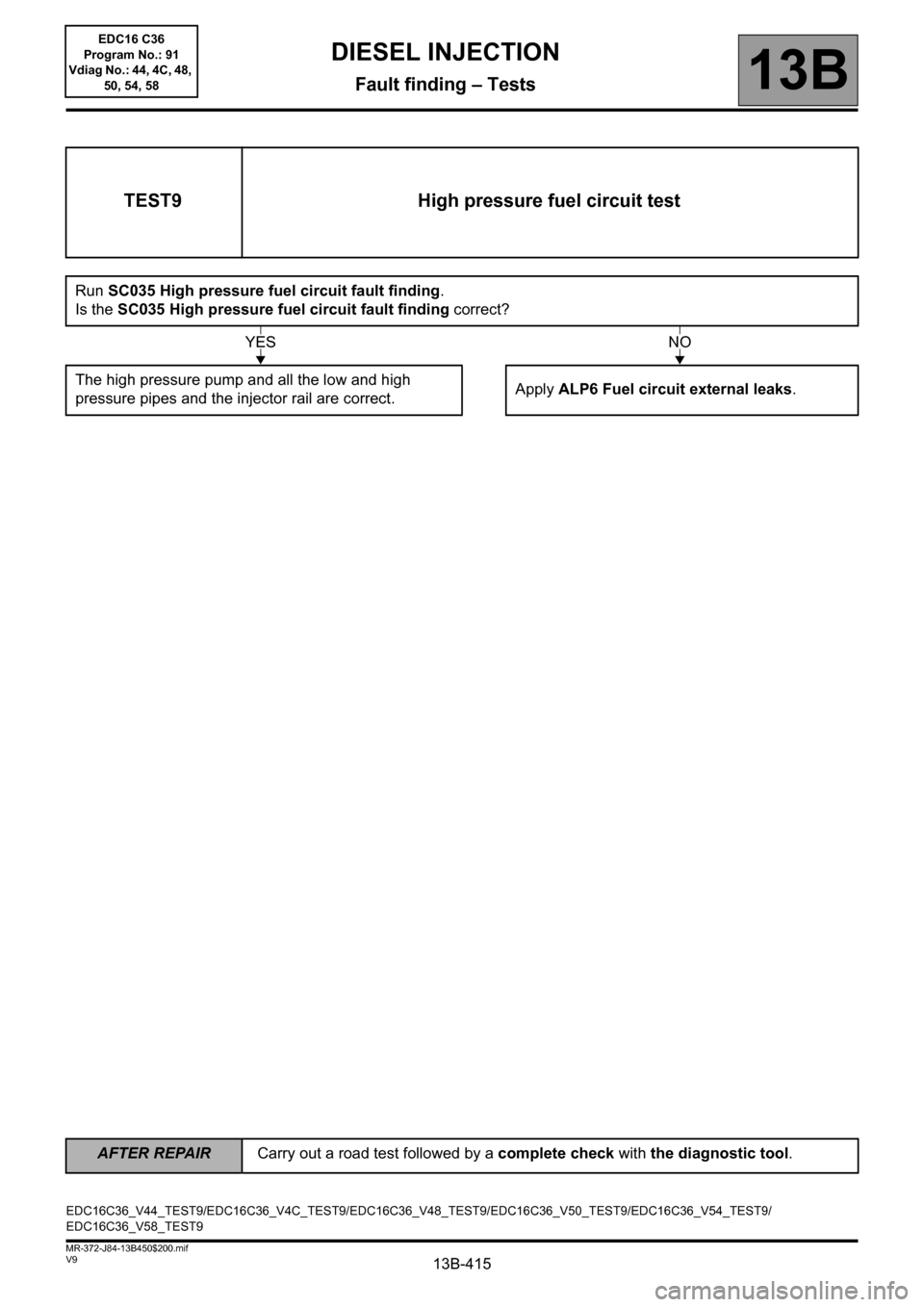
13B-415V9 MR-372-J84-13B450$200.mif
DIESEL INJECTION
Fault finding – Tests13B
TEST9 High pressure fuel circuit test
Run SC035 High pressure fuel circuit fault finding.
Is the SC035 High pressure fuel circuit fault finding correct?
The high pressure pump and all the low and high
pressure pipes and the injector rail are correct.Apply ALP6 Fuel circuit external leaks.
YESNO
EDC16C36_V44_TEST9/EDC16C36_V4C_TEST9/EDC16C36_V48_TEST9/EDC16C36_V50_TEST9/EDC16C36_V54_TEST9/
EDC16C36_V58_TEST9
AFTER REPAIRCarry out a road test followed by a complete check with the diagnostic tool.
EDC16 C36
Program No.: 91
Vdiag No.: 44, 4C, 48,
50, 54, 58
Page 416 of 431
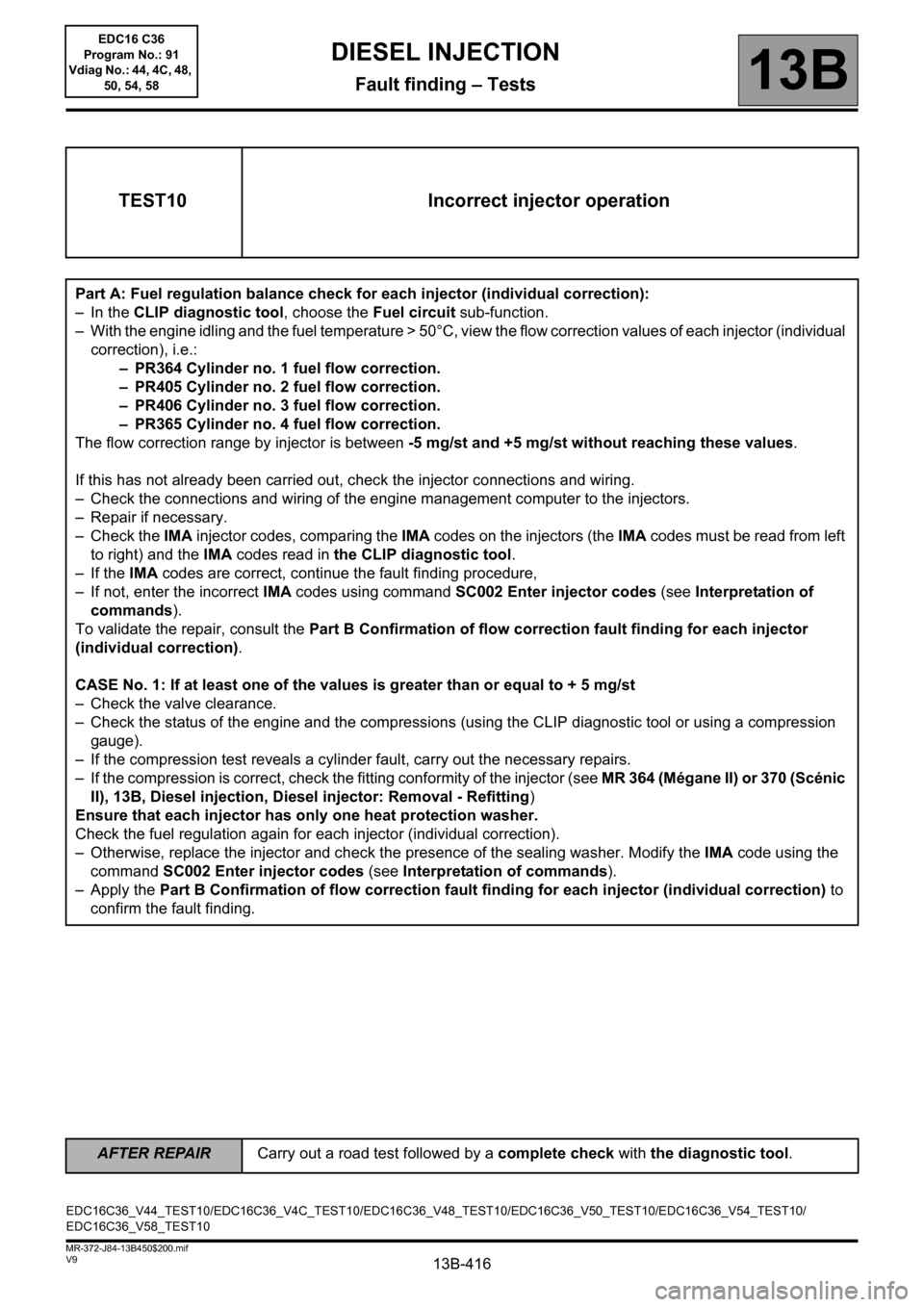
13B-416V9 MR-372-J84-13B450$200.mif
DIESEL INJECTION
Fault finding – Tests13B
TEST10 Incorrect injector operation
Part A: Fuel regulation balance check for each injector (individual correction):
– In the CLIP diagnostic tool, choose the Fuel circuit sub-function.
– With the engine idling and the fuel temperature > 50°C, view the flow correction values of each injector (individual
correction), i.e.:
– PR364 Cylinder no. 1 fuel flow correction.
– PR405 Cylinder no. 2 fuel flow correction.
– PR406 Cylinder no. 3 fuel flow correction.
– PR365 Cylinder no. 4 fuel flow correction.
The flow correction range by injector is between -5 mg/st and +5 mg/st without reaching these values.
If this has not already been carried out, check the injector connections and wiring.
– Check the connections and wiring of the engine management computer to the injectors.
– Repair if necessary.
–Check the IMA injector codes, comparing the IMA codes on the injectors (the IMA codes must be read from left
to right) and the IMA codes read in the CLIP diagnostic tool.
– If the IMA codes are correct, continue the fault finding procedure,
– If not, enter the incorrect IMA codes using command SC002 Enter injector codes (see Interpretation of
commands).
To validate the repair, consult the Part B Confirmation of flow correction fault finding for each injector
(individual correction).
CASE No. 1: If at least one of the values is greater than or equal to + 5 mg/st
– Check the valve clearance.
– Check the status of the engine and the compressions (using the CLIP diagnostic tool or using a compression
gauge).
– If the compression test reveals a cylinder fault, carry out the necessary repairs.
– If the compression is correct, check the fitting conformity of the injector (see MR 364 (Mégane II) or 370 (Scénic
II), 13B, Diesel injection, Diesel injector: Removal - Refitting)
Ensure that each injector has only one heat protection washer.
Check the fuel regulation again for each injector (individual correction).
– Otherwise, replace the injector and check the presence of the sealing washer. Modify the IMA code using the
command SC002 Enter injector codes (see Interpretation of commands).
–Apply the Part B Confirmation of flow correction fault finding for each injector (individual correction) to
confirm the fault finding.
EDC16C36_V44_TEST10/EDC16C36_V4C_TEST10/EDC16C36_V48_TEST10/EDC16C36_V50_TEST10/EDC16C36_V54_TEST10/
EDC16C36_V58_TEST10
AFTER REPAIRCarry out a road test followed by a complete check with the diagnostic tool.
EDC16 C36
Program No.: 91
Vdiag No.: 44, 4C, 48,
50, 54, 58
Page 417 of 431
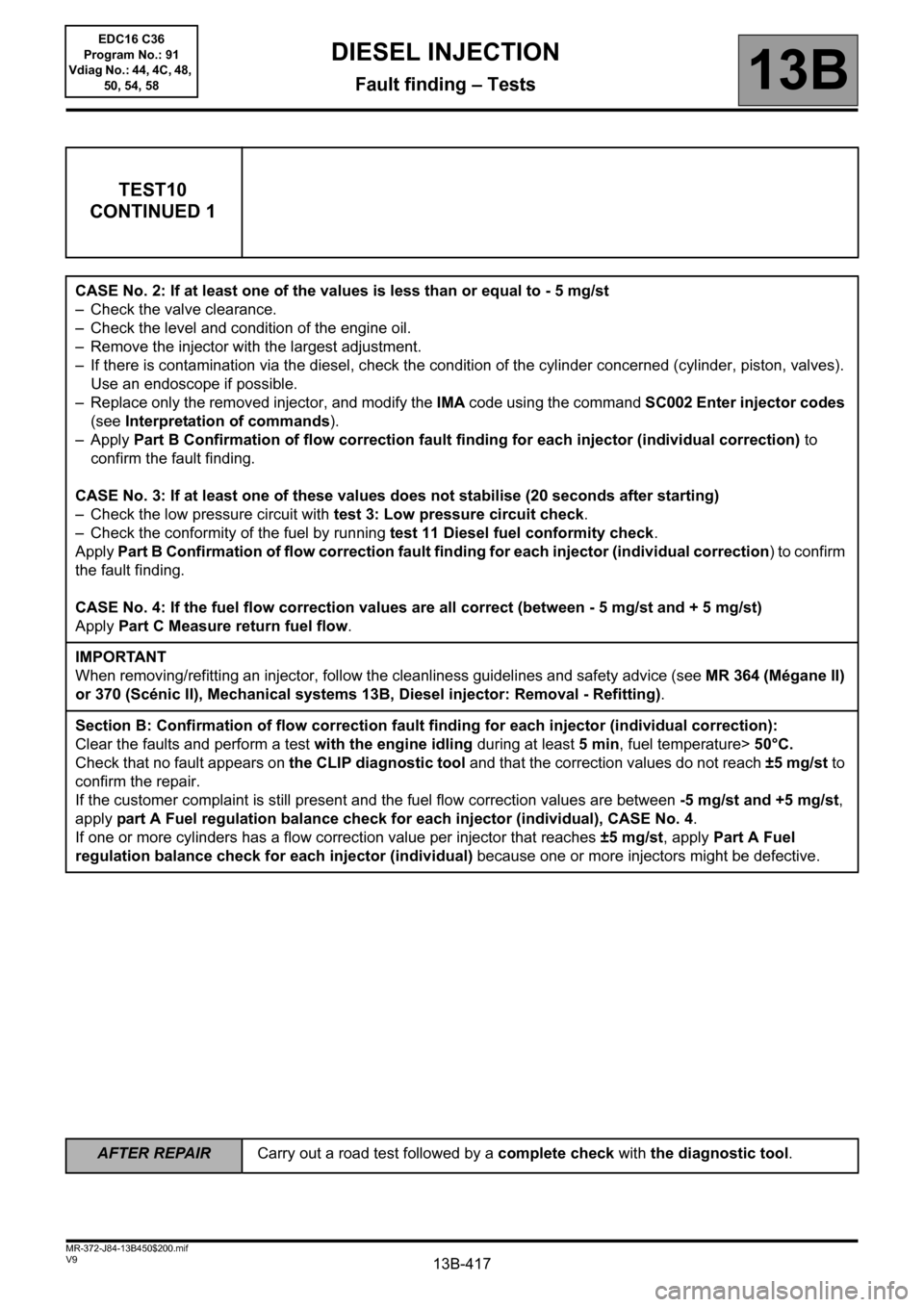
13B-417V9 MR-372-J84-13B450$200.mif
DIESEL INJECTION
Fault finding – Tests13B
TEST10
CONTINUED 1
CASE No. 2: If at least one of the values is less than or equal to - 5 mg/st
– Check the valve clearance.
– Check the level and condition of the engine oil.
– Remove the injector with the largest adjustment.
– If there is contamination via the diesel, check the condition of the cylinder concerned (cylinder, piston, valves).
Use an endoscope if possible.
– Replace only the removed injector, and modify the IMA code using the command SC002 Enter injector codes
(see Interpretation of commands).
–Apply Part B Confirmation of flow correction fault finding for each injector (individual correction) to
confirm the fault finding.
CASE No. 3: If at least one of these values does not stabilise (20 seconds after starting)
– Check the low pressure circuit with test 3: Low pressure circuit check.
– Check the conformity of the fuel by running test 11 Diesel fuel conformity check.
Apply Part B Confirmation of flow correction fault finding for each injector (individual correction) to confirm
the fault finding.
CASE No. 4: If the fuel flow correction values are all correct (between - 5 mg/st and + 5 mg/st)
Apply Part C Measure return fuel flow.
IMPORTANT
When removing/refitting an injector, follow the cleanliness guidelines and safety advice (see MR 364 (Mégane II)
or 370 (Scénic II), Mechanical systems 13B, Diesel injector: Removal - Refitting).
Section B: Confirmation of flow correction fault finding for each injector (individual correction):
Clear the faults and perform a test with the engine idling during at least 5 min, fuel temperature> 50°C.
Check that no fault appears on the CLIP diagnostic tool and that the correction values do not reach ±5 mg/st to
confirm the repair.
If the customer complaint is still present and the fuel flow correction values are between -5 mg/st and +5 mg/st,
apply part A Fuel regulation balance check for each injector (individual), CASE No. 4.
If one or more cylinders has a flow correction value per injector that reaches ±5 mg/st, apply Part A Fuel
regulation balance check for each injector (individual) because one or more injectors might be defective.
AFTER REPAIRCarry out a road test followed by a complete check with the diagnostic tool.
EDC16 C36
Program No.: 91
Vdiag No.: 44, 4C, 48,
50, 54, 58
Page 418 of 431
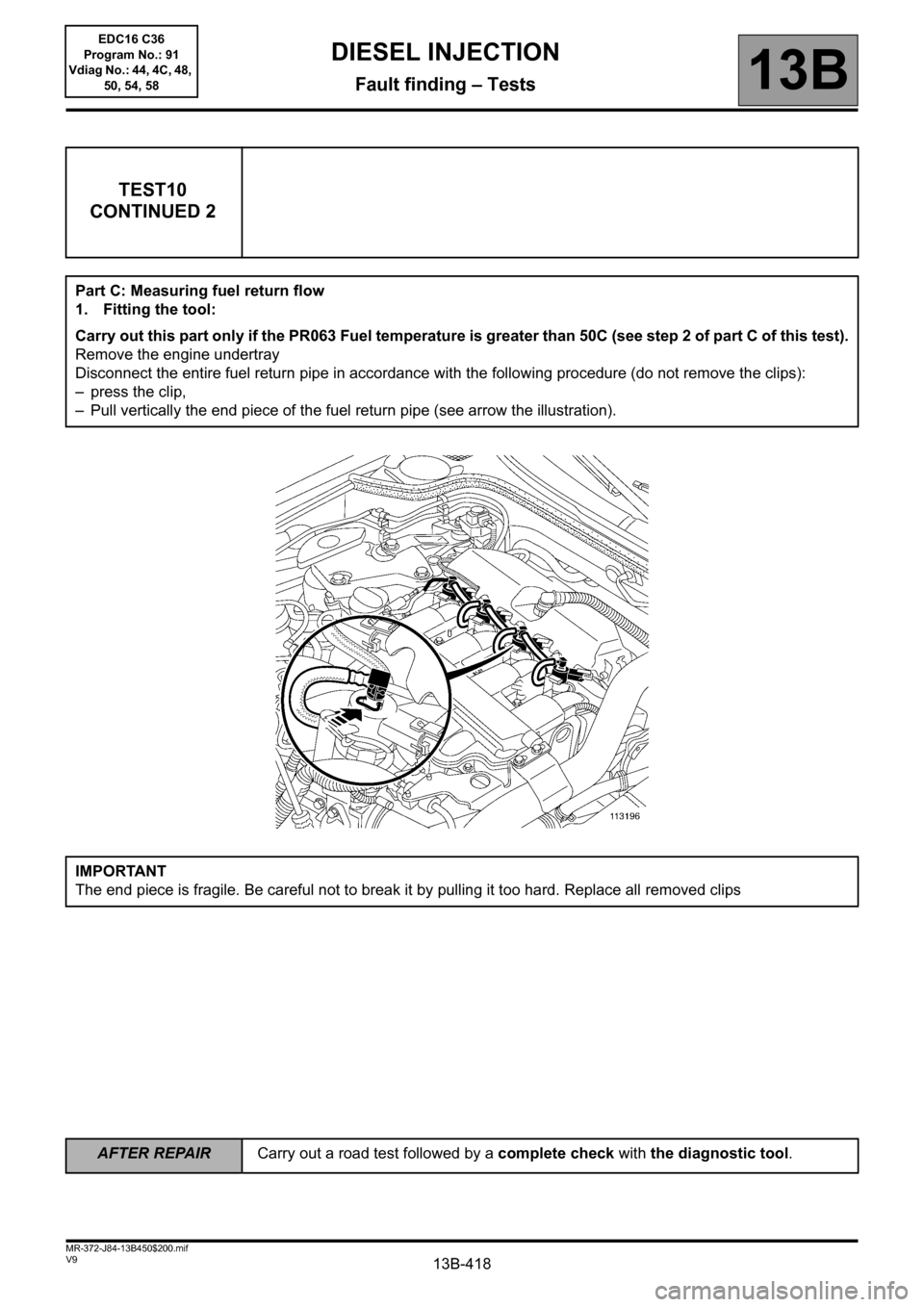
13B-418V9 MR-372-J84-13B450$200.mif
DIESEL INJECTION
Fault finding – Tests13B
TEST10
CONTINUED 2
Part C: Measuring fuel return flow
1. Fitting the tool:
Carry out this part only if the PR063 Fuel temperature is greater than 50C (see step 2 of part C of this test).
Remove the engine undertray
Disconnect the entire fuel return pipe in accordance with the following procedure (do not remove the clips):
– press the clip,
– Pull vertically the end piece of the fuel return pipe (see arrow the illustration).
IMPORTANT
The end piece is fragile. Be careful not to break it by pulling it too hard. Replace all removed clips
AFTER REPAIRCarry out a road test followed by a complete check with the diagnostic tool.
EDC16 C36
Program No.: 91
Vdiag No.: 44, 4C, 48,
50, 54, 58
Page 419 of 431
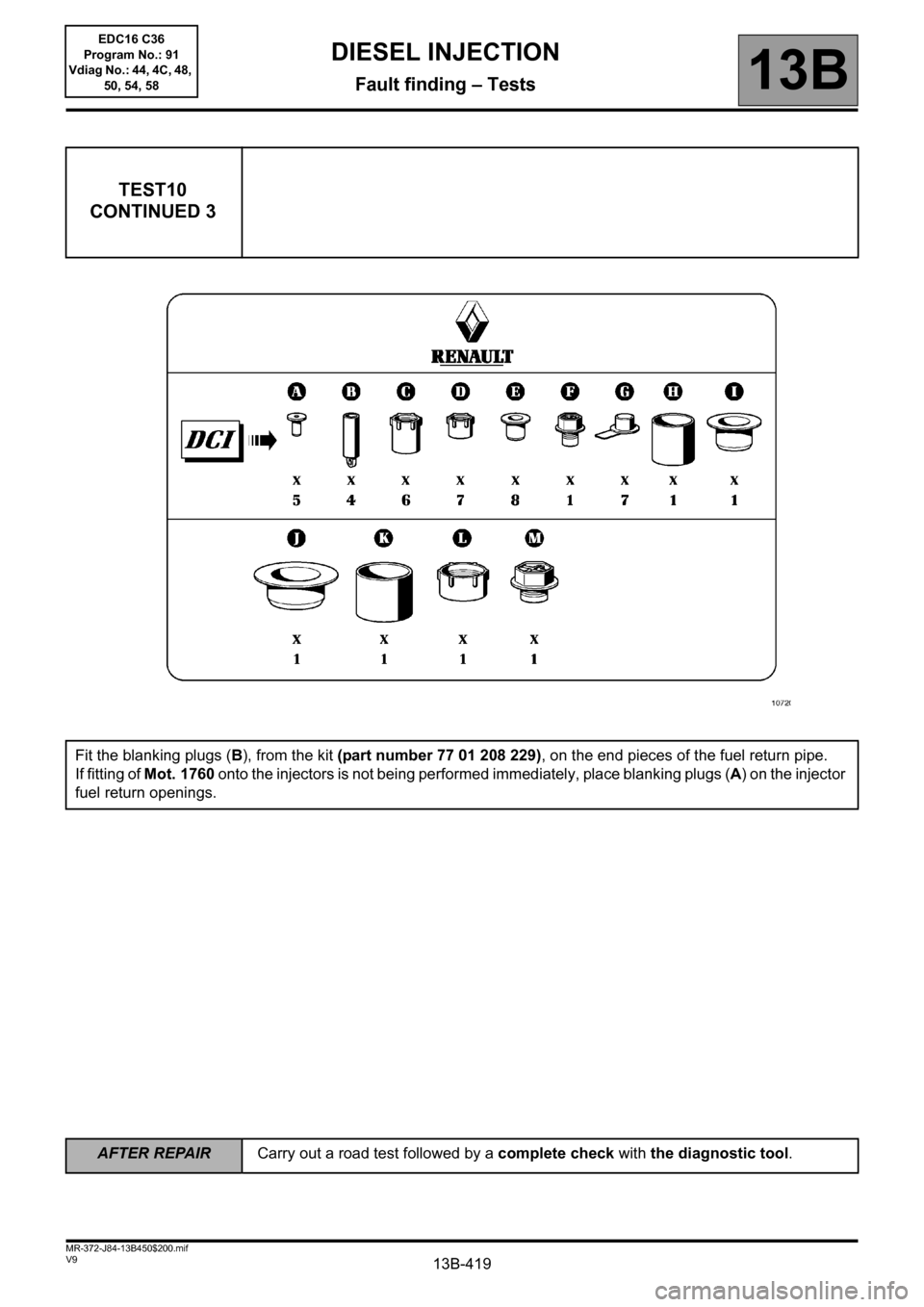
13B-419V9 MR-372-J84-13B450$200.mif
DIESEL INJECTION
Fault finding – Tests13B
TEST10
CONTINUED 3
Fit the blanking plugs (B), from the kit (part number 77 01 208 229), on the end pieces of the fuel return pipe.
If fitting of Mot. 1760 onto the injectors is not being performed immediately, place blanking plugs (A) on the injector
fuel return openings.
AFTER REPAIRCarry out a road test followed by a complete check with the diagnostic tool.
EDC16 C36
Program No.: 91
Vdiag No.: 44, 4C, 48,
50, 54, 58
Page 420 of 431
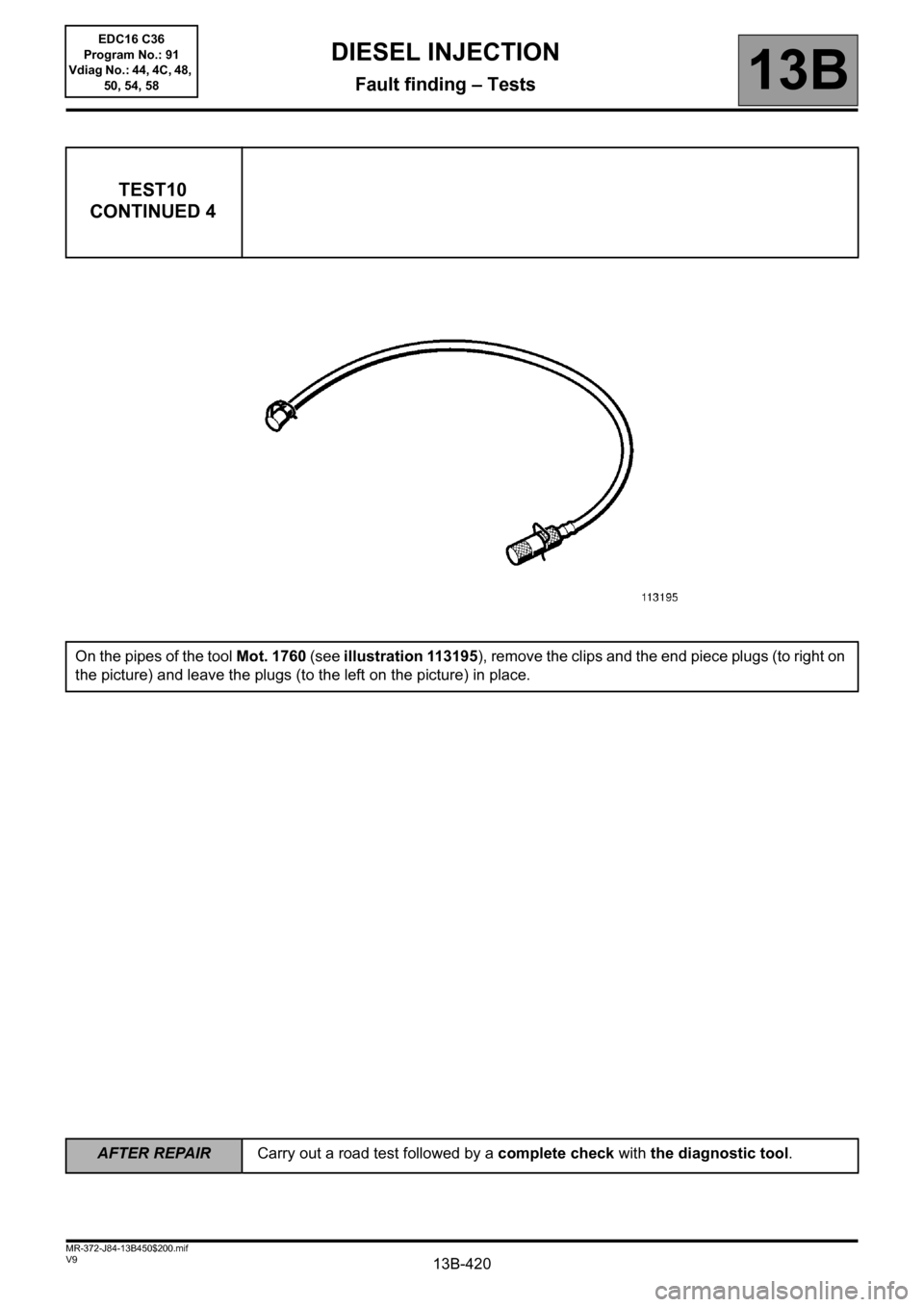
13B-420V9 MR-372-J84-13B450$200.mif
DIESEL INJECTION
Fault finding – Tests13B
TEST10
CONTINUED 4
On the pipes of the tool Mot. 1760 (see illustration 113195), remove the clips and the end piece plugs (to right on
the picture) and leave the plugs (to the left on the picture) in place.
AFTER REPAIRCarry out a road test followed by a complete check with the diagnostic tool.
EDC16 C36
Program No.: 91
Vdiag No.: 44, 4C, 48,
50, 54, 58