engine RENAULT SCENIC 2011 J95 / 3.G Engine And Peripherals Siemens Injection Owner's Manual
[x] Cancel search | Manufacturer: RENAULT, Model Year: 2011, Model line: SCENIC, Model: RENAULT SCENIC 2011 J95 / 3.GPages: 329, PDF Size: 1.71 MB
Page 29 of 329
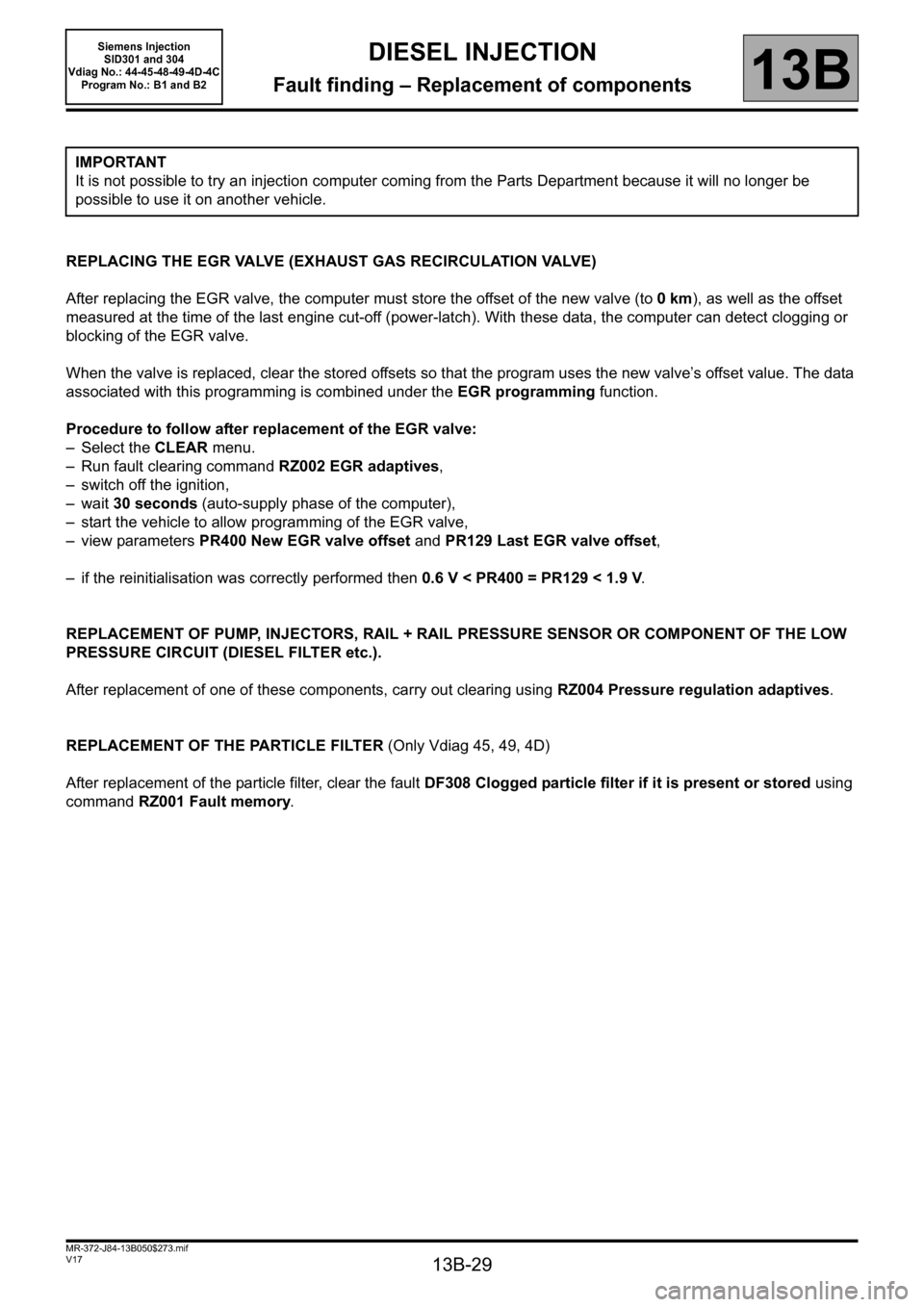
13B-29
MR-372-J84-13B050$273.mif
V17
Siemens Injection
SID301 and 304
Vdiag No.: 44-45-48-49-4D-4C
Program No.: B1 and B2DIESEL INJECTION
Fault finding – Replacement of components13B
REPLACING THE EGR VALVE (EXHAUST GAS RECIRCULATION VALVE)
After replacing the EGR valve, the computer must store the offset of the new valve (to 0 km), as well as the offset
measured at the time of the last engine cut-off (power-latch). With these data, the computer can detect clogging or
blocking of the EGR valve.
When the valve is replaced, clear the stored offsets so that the program uses the new valve’s offset value. The data
associated with this programming is combined under the EGR programming function.
Procedure to follow after replacement of the EGR valve:
– Select the CLEAR menu.
– Run fault clearing command RZ002 EGR adaptives,
– switch off the ignition,
–wait 30 seconds (auto-supply phase of the computer),
– start the vehicle to allow programming of the EGR valve,
– view parameters PR400 New EGR valve offset and PR129 Last EGR valve offset,
– if the reinitialisation was correctly performed then 0.6 V < PR400 = PR129 < 1.9 V.
REPLACEMENT OF PUMP, INJECTORS, RAIL + RAIL PRESSURE SENSOR OR COMPONENT OF THE LOW
PRESSURE CIRCUIT (DIESEL FILTER etc.).
After replacement of one of these components, carry out clearing using RZ004 Pressure regulation adaptives.
REPLACEMENT OF THE PARTICLE FILTER (Only Vdiag 45, 49, 4D)
After replacement of the particle filter, clear the fault DF308 Clogged particle filter if it is present or stored using
command RZ001 Fault memory. IMPORTANT
It is not possible to try an injection computer coming from the Parts Department because it will no longer be
possible to use it on another vehicle.
Page 30 of 329
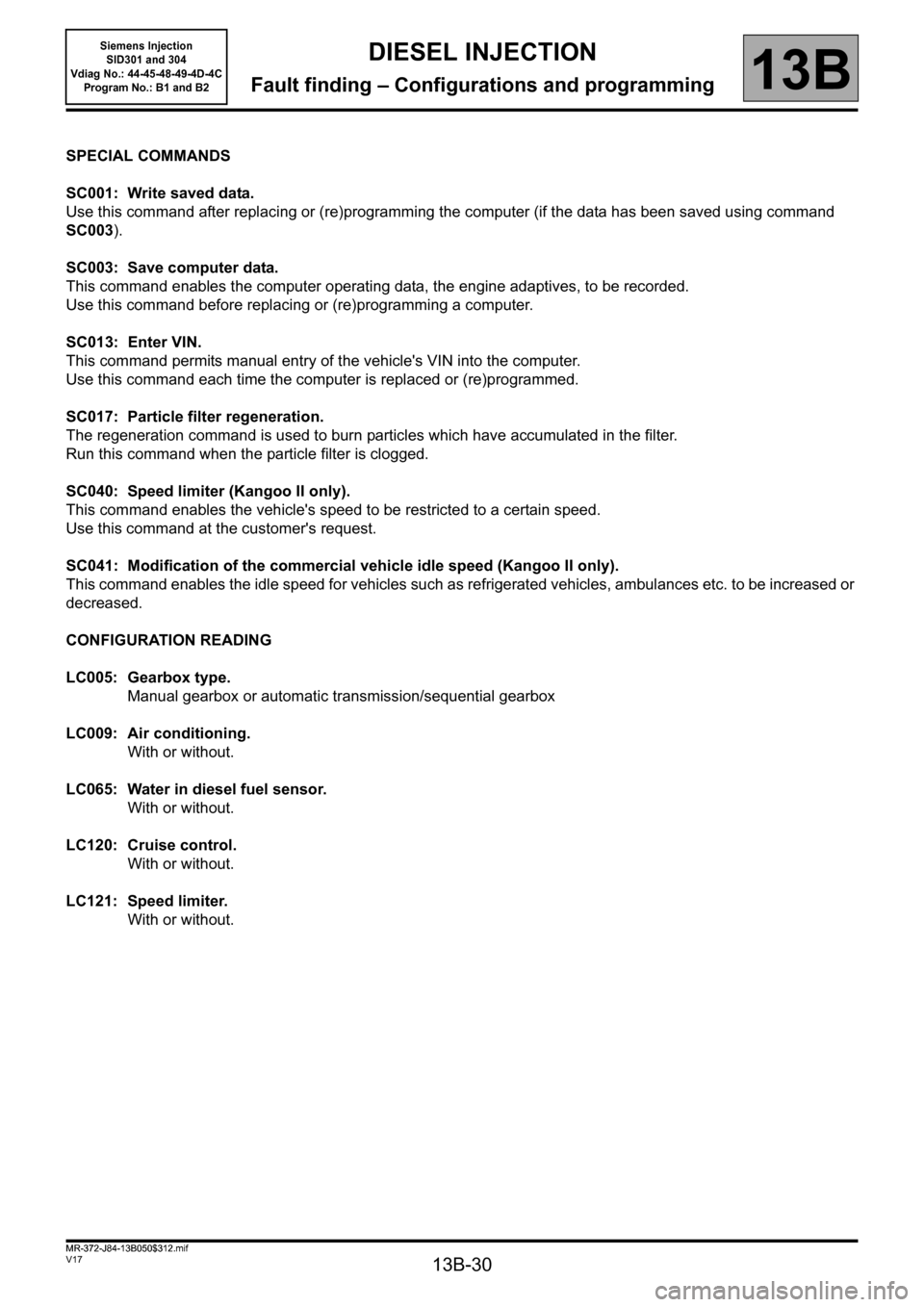
13B-30
MR-372-J84-13B050$312.mif
V17
13B
DIESEL INJECTION
Fault finding – Configurations and programming
SPECIAL COMMANDS
SC001: Write saved data.
Use this command after replacing or (re)programming the computer (if the data has been saved using command
SC003).
SC003: Save computer data.
This command enables the computer operating data, the engine adaptives, to be recorded.
Use this command before replacing or (re)programming a computer.
SC013: Enter VIN.
This command permits manual entry of the vehicle's VIN into the computer.
Use this command each time the computer is replaced or (re)programmed.
SC017: Particle filter regeneration.
The regeneration command is used to burn particles which have accumulated in the filter.
Run this command when the particle filter is clogged.
SC040: Speed limiter (Kangoo II only).
This command enables the vehicle's speed to be restricted to a certain speed.
Use this command at the customer's request.
SC041: Modification of the commercial vehicle idle speed (Kangoo II only).
This command enables the idle speed for vehicles such as refrigerated vehicles, ambulances etc. to be increased or
decreased.
CONFIGURATION READING
LC005: Gearbox type.
Manual gearbox or automatic transmission/sequential gearbox
LC009: Air conditioning.
With or without.
LC065: Water in diesel fuel sensor.
With or without.
LC120: Cruise control.
With or without.
LC121: Speed limiter.
With or without.
MR-372-J84-13B050$312.mif
Siemens Injection
SID301 and 304
Vdiag No.: 44-45-48-49-4D-4C
Program No.: B1 and B2
Page 31 of 329
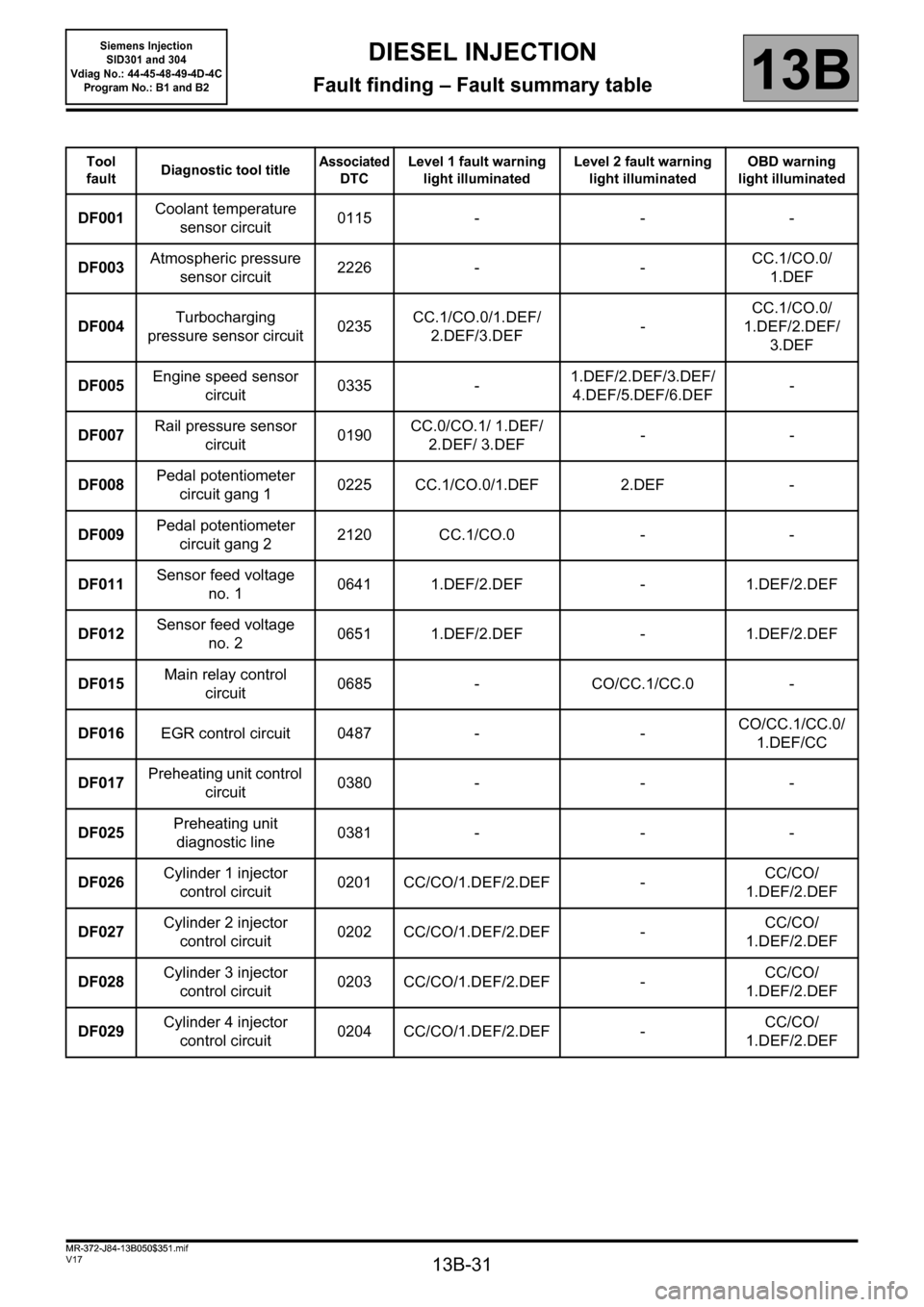
13B-31
MR-372-J84-13B050$351.mif
V17
13B
DIESEL INJECTION
Fault finding – Fault summary table
Tool
faultDiagnostic tool titleAssociated
DTCLevel 1 fault warning
light illuminatedLevel 2 fault warning
light illuminatedOBD warning
light illuminated
DF001Coolant temperature
sensor circuit0115 - - -
DF003Atmospheric pressure
sensor circuit2226 - -CC.1/CO.0/
1.DEF
DF004Turbocharging
pressure sensor circuit0235CC.1/CO.0/1.DEF/
2.DEF/3.DEF-CC.1/CO.0/
1.DEF/2.DEF/
3.DEF
DF005Engine speed sensor
circuit0335 -1.DEF/2.DEF/3.DEF/
4.DEF/5.DEF/6.DEF-
DF007Rail pressure sensor
circuit0190CC.0/CO.1/ 1.DEF/
2.DEF/ 3.DEF--
DF008Pedal potentiometer
circuit gang 10225 CC.1/CO.0/1.DEF 2.DEF -
DF009Pedal potentiometer
circuit gang 22120 CC.1/CO.0 - -
DF011Sensor feed voltage
no. 10641 1.DEF/2.DEF - 1.DEF/2.DEF
DF012Sensor feed voltage
no. 20651 1.DEF/2.DEF - 1.DEF/2.DEF
DF015Main relay control
circuit0685 - CO/CC.1/CC.0 -
DF016EGR control circuit 0487 - -CO/CC.1/CC.0/
1.DEF/CC
DF017Preheating unit control
circuit0380 - - -
DF025Preheating unit
diagnostic line0381 - - -
DF026Cylinder 1 injector
control circuit0201 CC/CO/1.DEF/2.DEF -CC/CO/
1.DEF/2.DEF
DF027Cylinder 2 injector
control circuit0202 CC/CO/1.DEF/2.DEF -CC/CO/
1.DEF/2.DEF
DF028Cylinder 3 injector
control circuit0203 CC/CO/1.DEF/2.DEF -CC/CO/
1.DEF/2.DEF
DF029Cylinder 4 injector
control circuit0204 CC/CO/1.DEF/2.DEF -CC/CO/
1.DEF/2.DEF
MR-372-J84-13B050$351.mif
Siemens Injection
SID301 and 304
Vdiag No.: 44-45-48-49-4D-4C
Program No.: B1 and B2
Page 33 of 329
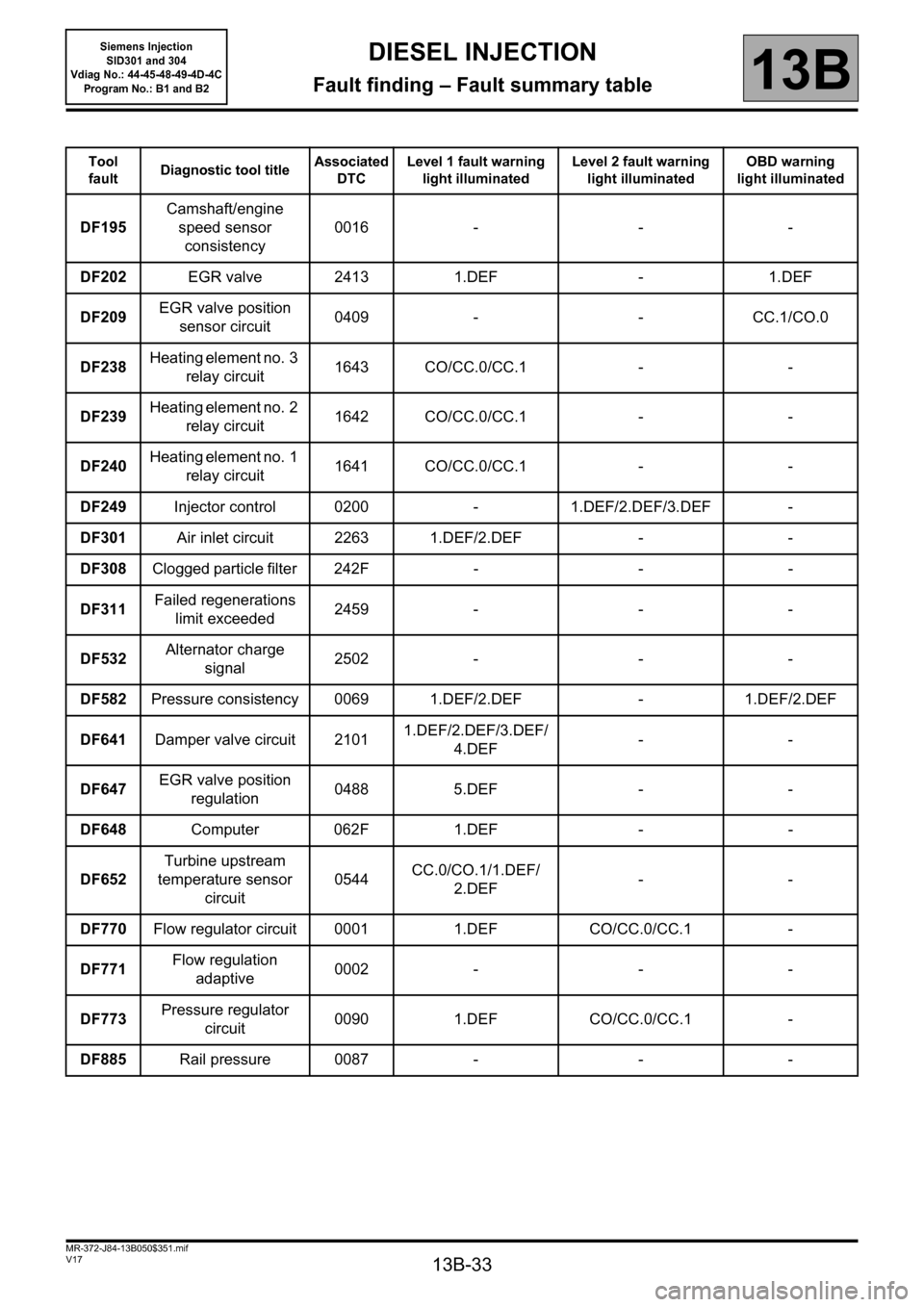
13B-33
MR-372-J84-13B050$351.mif
V17
Siemens Injection
SID301 and 304
Vdiag No.: 44-45-48-49-4D-4C
Program No.: B1 and B2DIESEL INJECTION
Fault finding – Fault summary table13B
Tool
faultDiagnostic tool titleAssociated
DTCLevel 1 fault warning
light illuminatedLevel 2 fault warning
light illuminatedOBD warning
light illuminated
DF195Camshaft/engine
speed sensor
consistency0016 - - -
DF202EGR valve 2413 1.DEF - 1.DEF
DF209EGR valve position
sensor circuit0409 - - CC.1/CO.0
DF238Heating element no. 3
relay circuit 1643 CO/CC.0/CC.1 - -
DF239Heating element no. 2
relay circuit 1642 CO/CC.0/CC.1 - -
DF240Heating element no. 1
relay circuit 1641 CO/CC.0/CC.1 - -
DF249Injector control 0200 - 1.DEF/2.DEF/3.DEF -
DF301Air inlet circuit 2263 1.DEF/2.DEF - -
DF308Clogged particle filter 242F - - -
DF311Failed regenerations
limit exceeded 2459 - - -
DF532Alternator charge
signal2502 - - -
DF582Pressure consistency 0069 1.DEF/2.DEF - 1.DEF/2.DEF
DF641Damper valve circuit 21011.DEF/2.DEF/3.DEF/
4.DEF--
DF647EGR valve position
regulation0488 5.DEF - -
DF648Computer 062F 1.DEF - -
DF652Turbine upstream
temperature sensor
circuit 0544CC.0/CO.1/1.DEF/
2.DEF--
DF770Flow regulator circuit 0001 1.DEF CO/CC.0/CC.1 -
DF771Flow regulation
adaptive0002 - - -
DF773Pressure regulator
circuit0090 1.DEF CO/CC.0/CC.1 -
DF885Rail pressure 0087 - - -
Page 34 of 329
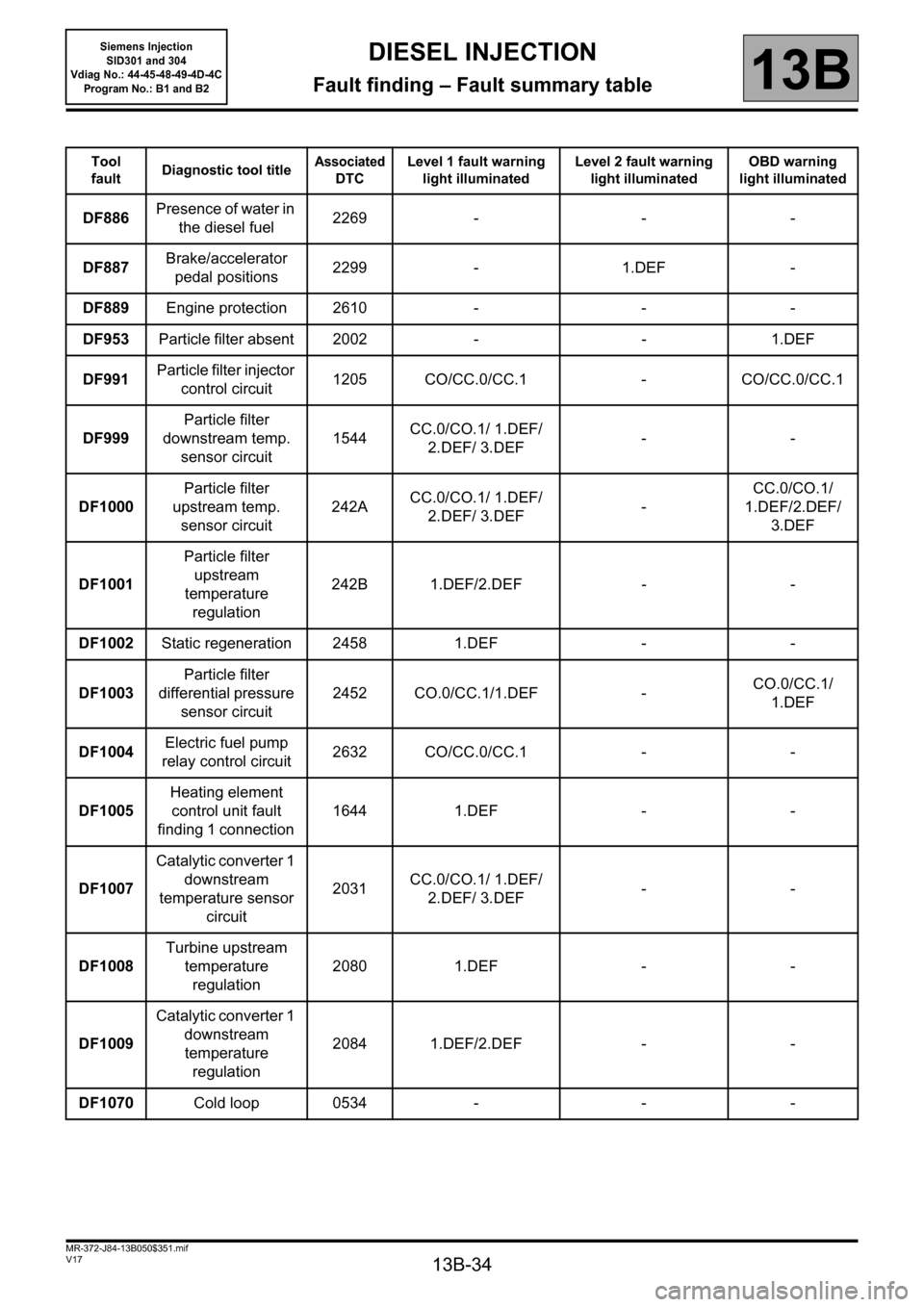
13B-34
MR-372-J84-13B050$351.mif
V17
Siemens Injection
SID301 and 304
Vdiag No.: 44-45-48-49-4D-4C
Program No.: B1 and B2DIESEL INJECTION
Fault finding – Fault summary table13B
Tool
faultDiagnostic tool titleAssociated
DTCLevel 1 fault warning
light illuminatedLevel 2 fault warning
light illuminatedOBD warning
light illuminated
DF886Presence of water in
the diesel fuel2269 - - -
DF887Brake/accelerator
pedal positions2299 - 1.DEF -
DF889Engine protection 2610 - - -
DF953Particle filter absent 2002 - - 1.DEF
DF991Particle filter injector
control circuit 1205 CO/CC.0/CC.1 - CO/CC.0/CC.1
DF999Particle filter
downstream temp.
sensor circuit1544CC.0/CO.1/ 1.DEF/
2.DEF/ 3.DEF--
DF1000Particle filter
upstream temp.
sensor circuit242ACC.0/CO.1/ 1.DEF/
2.DEF/ 3.DEF-CC.0/CO.1/
1.DEF/2.DEF/
3.DEF
DF1001Particle filter
upstream
temperature
regulation 242B 1.DEF/2.DEF - -
DF1002Static regeneration 2458 1.DEF - -
DF1003Particle filter
differential pressure
sensor circuit 2452 CO.0/CC.1/1.DEF -CO.0/CC.1/
1.DEF
DF1004Electric fuel pump
relay control circuit 2632 CO/CC.0/CC.1 - -
DF1005Heating element
control unit fault
finding 1 connection 1644 1.DEF - -
DF1007Catalytic converter 1
downstream
temperature sensor
circuit 2031CC.0/CO.1/ 1.DEF/
2.DEF/ 3.DEF--
DF1008Turbine upstream
temperature
regulation 2080 1.DEF - -
DF1009Catalytic converter 1
downstream
temperature
regulation 2084 1.DEF/2.DEF - -
DF1070Cold loop 0534 - - -
Page 35 of 329
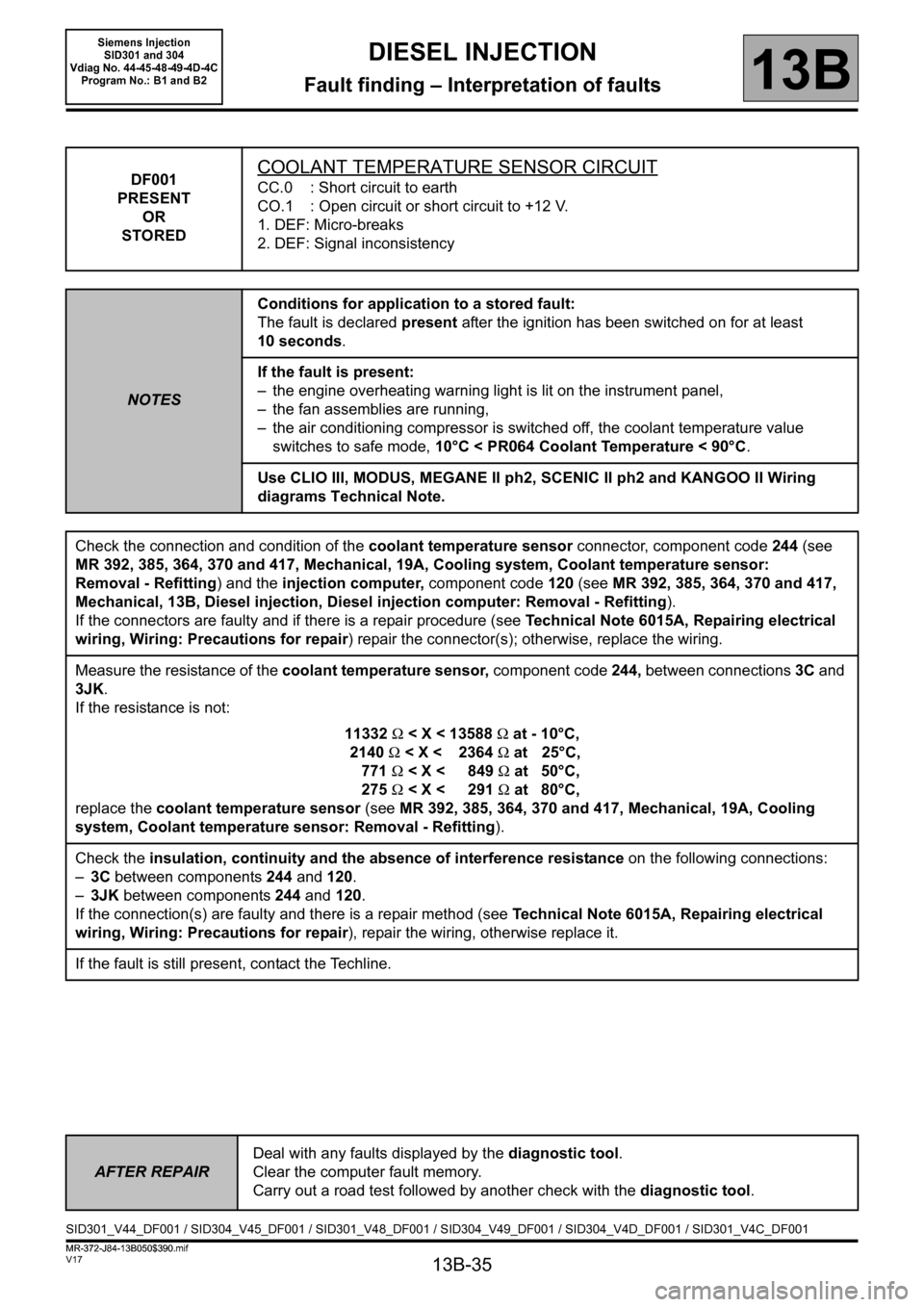
13B-35
MR-372-J84-13B050$390.mif
V17
13B
DIESEL INJECTION
Fault finding – Interpretation of faults
DF001
PRESENT
OR
STOREDCOOLANT TEMPERATURE SENSOR CIRCUIT
CC.0 : Short circuit to earth
CO.1 : Open circuit or short circuit to +12 V.
1. DEF: Micro-breaks
2. DEF: Signal inconsistency
NOTESConditions for application to a stored fault:
The fault is declared present after the ignition has been switched on for at least
10 seconds.
If the fault is present:
– the engine overheating warning light is lit on the instrument panel,
– the fan assemblies are running,
– the air conditioning compressor is switched off, the coolant temperature value
switches to safe mode, 10°C < PR064 Coolant Temperature < 90°C.
Use CLIO III, MODUS, MEGANE II ph2, SCENIC II ph2 and KANGOO II Wiring
diagrams Technical Note.
Check the connection and condition of the coolant temperature sensor connector, component code244 (see
MR 392, 385, 364, 370 and 417, Mechanical, 19A, Cooling system, Coolant temperature sensor:
Removal - Refitting) and the injection computer, component code120 (see MR 392, 385, 364, 370 and 417,
Mechanical, 13B, Diesel injection, Diesel injection computer: Removal - Refitting).
If the connectors are faulty and if there is a repair procedure (see Technical Note 6015A, Repairing electrical
wiring, Wiring: Precautions for repair) repair the connector(s); otherwise, replace the wiring.
Measure the resistance of the coolant temperature sensor, component code 244, between connections 3C and
3JK.
If the resistance is not:
11332Ω < X < 13588Ω at - 10°C,
2140Ω < X < 2364Ω at 25°C,
771Ω < X < 849Ω at 50°C,
275Ω < X < 291Ω at 80°C,
replace the coolant temperature sensor (see MR 392, 385, 364, 370 and 417, Mechanical, 19A, Cooling
system, Coolant temperature sensor: Removal - Refitting).
Check the insulation, continuity and the absence of interference resistance on the following connections:
–3C between components 244 and 120.
–3JK between components 244 and 120.
If the connection(s) are faulty and there is a repair method (see Technical Note 6015A, Repairing electrical
wiring, Wiring: Precautions for repair), repair the wiring, otherwise replace it.
If the fault is still present, contact the Techline.
AFTER REPAIRDeal with any faults displayed by the diagnostic tool.
Clear the computer fault memory.
Carry out a road test followed by another check with the diagnostic tool.
SID301_V44_DF001 / SID304_V45_DF001 / SID301_V48_DF001 / SID304_V49_DF001 / SID304_V4D_DF001 / SID301_V4C_DF001
MR-372-J84-13B050$390.mif
Siemens Injection
SID301 and 304
Vdiag No. 44-45-48-49-4D-4C
Program No.: B1 and B2
Page 38 of 329
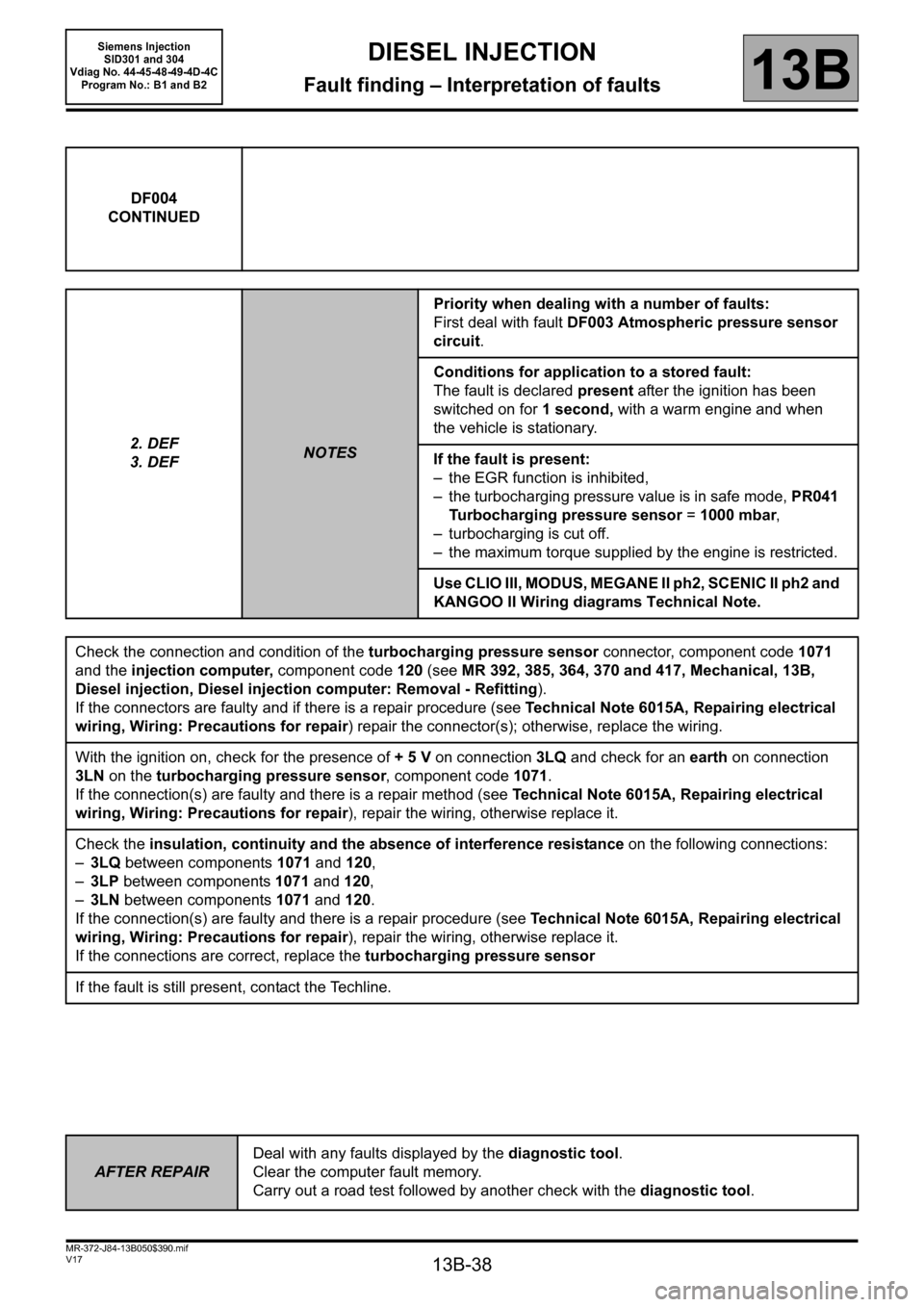
13B-38
MR-372-J84-13B050$390.mif
V17
DIESEL INJECTION
Fault finding – Interpretation of faults
Siemens Injection
SID301 and 304
Vdiag No. 44-45-48-49-4D-4C
Program No.: B1 and B2
13B
DF004
CONTINUED
2. DEF
3. DEF
NOTESPriority when dealing with a number of faults:
First deal with fault DF003 Atmospheric pressure sensor
circuit.
Conditions for application to a stored fault:
The fault is declared present after the ignition has been
switched on for 1 second, with a warm engine and when
the vehicle is stationary.
If the fault is present:
– the EGR function is inhibited,
– the turbocharging pressure value is in safe mode, PR041
Turbocharging pressure sensor = 1000 mbar,
– turbocharging is cut off.
– the maximum torque supplied by the engine is restricted.
Use CLIO III, MODUS, MEGANE II ph2, SCENIC II ph2 and
KANGOO II Wiring diagrams Technical Note.
Check the connection and condition of the turbocharging pressure sensor connector, component code1071
and the injection computer, component code120 (see MR 392, 385, 364, 370 and 417, Mechanical, 13B,
Diesel injection, Diesel injection computer: Removal - Refitting).
If the connectors are faulty and if there is a repair procedure (see Technical Note 6015A, Repairing electrical
wiring, Wiring: Precautions for repair) repair the connector(s); otherwise, replace the wiring.
With the ignition on, check for the presence of + 5 V on connection 3LQ and check for an earth on connection
3LN on the turbocharging pressure sensor, component code 1071.
If the connection(s) are faulty and there is a repair method (see Technical Note 6015A, Repairing electrical
wiring, Wiring: Precautions for repair), repair the wiring, otherwise replace it.
Check the insulation, continuity and the absence of interference resistance on the following connections:
–3LQ between components 1071 and 120,
–3LP between components 1071 and 120,
–3LN between components 1071 and 120.
If the connection(s) are faulty and there is a repair procedure (see Technical Note 6015A, Repairing electrical
wiring, Wiring: Precautions for repair), repair the wiring, otherwise replace it.
If the connections are correct, replace the turbocharging pressure sensor
If the fault is still present, contact the Techline.
AFTER REPAIRDeal with any faults displayed by the diagnostic tool.
Clear the computer fault memory.
Carry out a road test followed by another check with the diagnostic tool.
Page 39 of 329
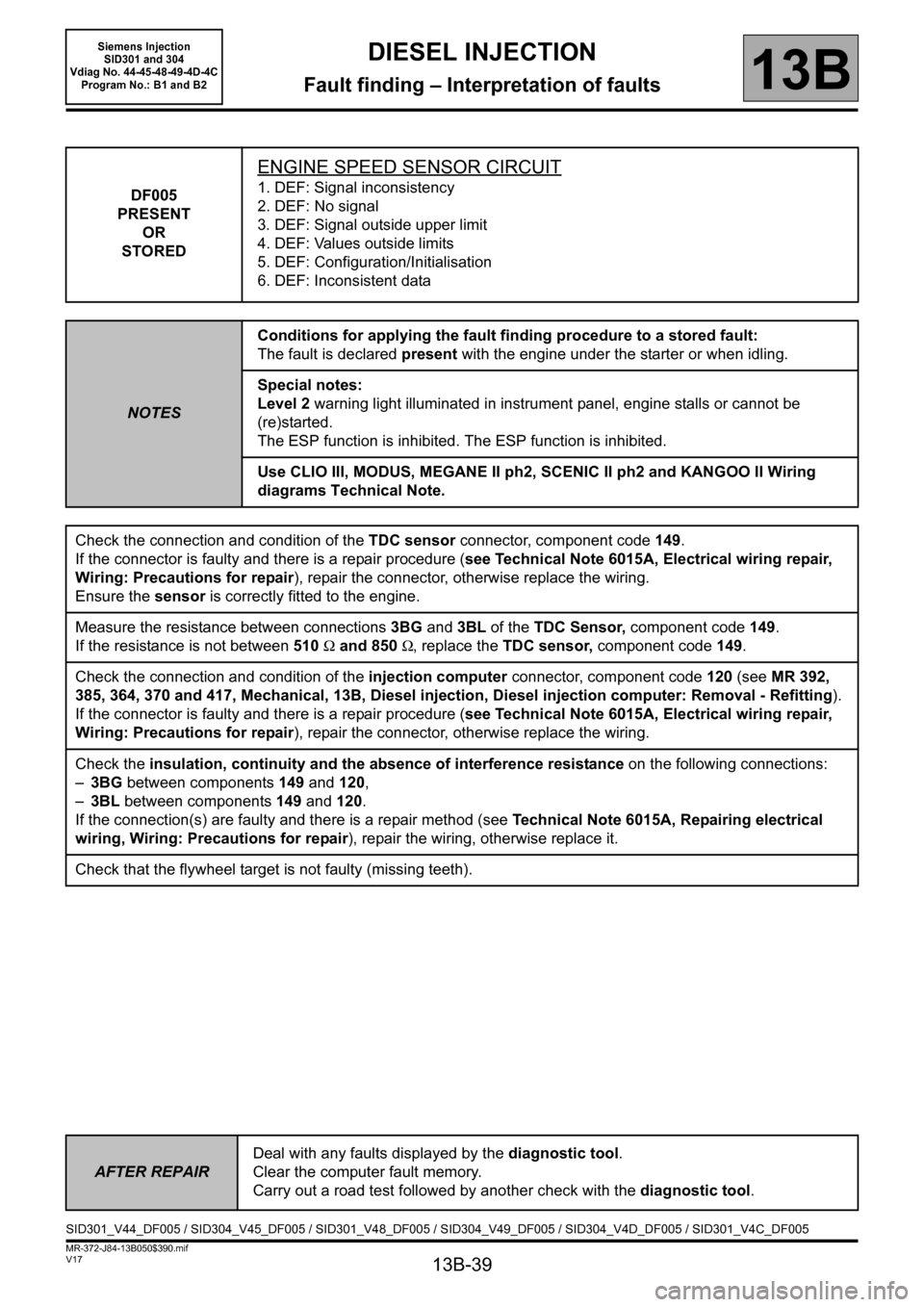
13B-39
MR-372-J84-13B050$390.mif
V17
DIESEL INJECTION
Fault finding – Interpretation of faults
Siemens Injection
SID301 and 304
Vdiag No. 44-45-48-49-4D-4C
Program No.: B1 and B2
13B
DF005
PRESENT
OR
STORED
ENGINE SPEED SENSOR CIRCUIT
1. DEF: Signal inconsistency
2. DEF: No signal
3. DEF: Signal outside upper limit
4. DEF: Values outside limits
5. DEF: Configuration/Initialisation
6. DEF: Inconsistent data
NOTESConditions for applying the fault finding procedure to a stored fault:
The fault is declared present with the engine under the starter or when idling.
Special notes:
Level 2 warning light illuminated in instrument panel, engine stalls or cannot be
(re)started.
The ESP function is inhibited. The ESP function is inhibited.
Use CLIO III, MODUS, MEGANE II ph2, SCENIC II ph2 and KANGOO II Wiring
diagrams Technical Note.
Check the connection and condition of the TDC sensor connector, component code 149.
If the connector is faulty and there is a repair procedure (see Technical Note 6015A, Electrical wiring repair,
Wiring: Precautions for repair), repair the connector, otherwise replace the wiring.
Ensure the sensor is correctly fitted to the engine.
Measure the resistance between connections3BG and 3BL of the TDC Sensor, component code149.
If the resistance is not between 510Ω and 850Ω, replace the TDC sensor, component code149.
Check the connection and condition of the injection computer connector, component code120 (see MR 392,
385, 364, 370 and 417, Mechanical, 13B, Diesel injection, Diesel injection computer: Removal - Refitting).
If the connector is faulty and there is a repair procedure (see Technical Note 6015A, Electrical wiring repair,
Wiring: Precautions for repair), repair the connector, otherwise replace the wiring.
Check the insulation, continuity and the absence of interference resistance on the following connections:
–3BG between components 149 and 120,
–3BL between components 149 and 120.
If the connection(s) are faulty and there is a repair method (see Technical Note 6015A, Repairing electrical
wiring, Wiring: Precautions for repair), repair the wiring, otherwise replace it.
Check that the flywheel target is not faulty (missing teeth).
AFTER REPAIRDeal with any faults displayed by the diagnostic tool.
Clear the computer fault memory.
Carry out a road test followed by another check with the diagnostic tool.
SID301_V44_DF005 / SID304_V45_DF005 / SID301_V48_DF005 / SID304_V49_DF005 / SID304_V4D_DF005 / SID301_V4C_DF005
Page 40 of 329
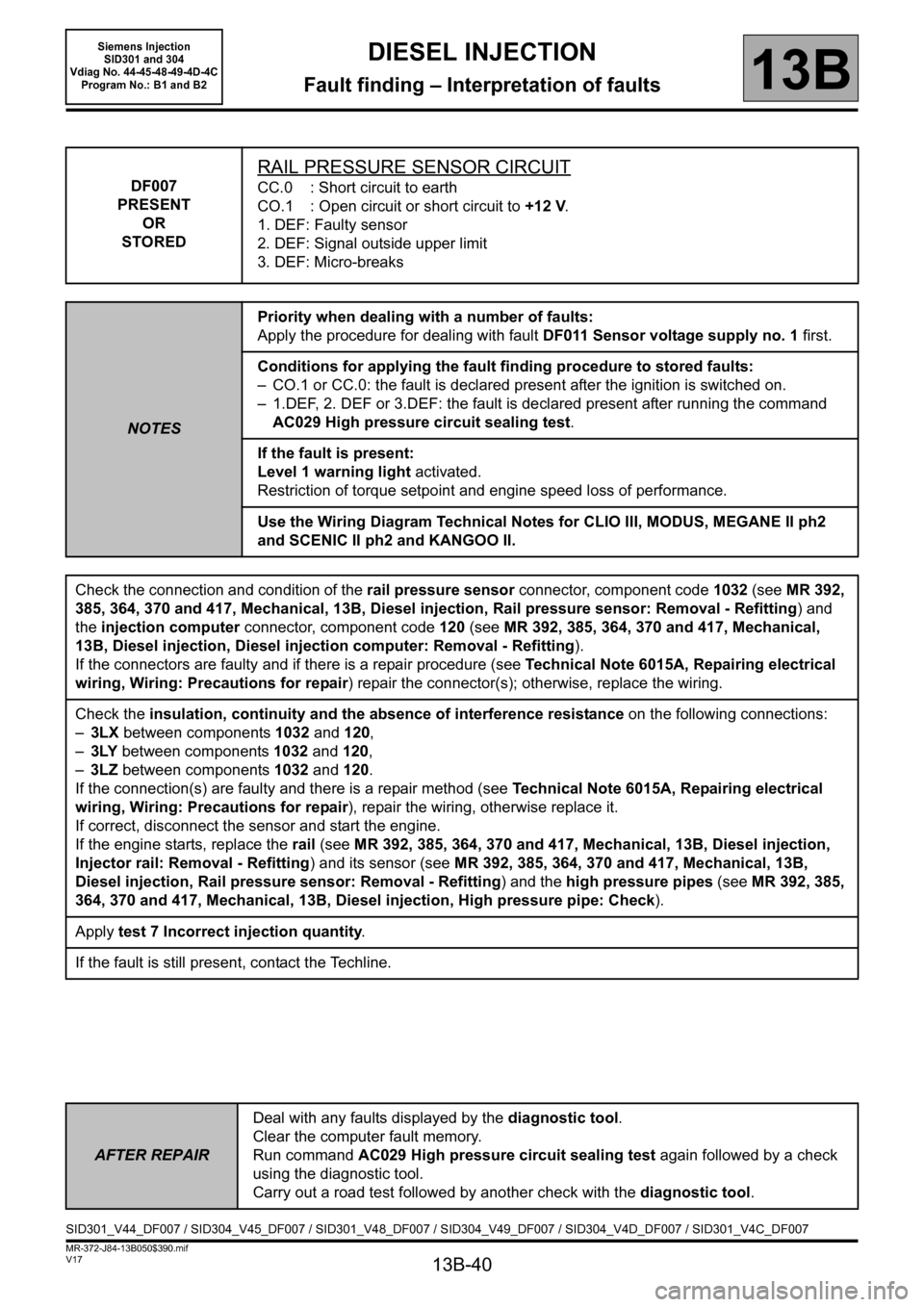
13B-40
MR-372-J84-13B050$390.mif
V17
DIESEL INJECTION
Fault finding – Interpretation of faults
Siemens Injection
SID301 and 304
Vdiag No. 44-45-48-49-4D-4C
Program No.: B1 and B2
13B
DF007
PRESENT
OR
STORED
RAIL PRESSURE SENSOR CIRCUIT
CC.0 : Short circuit to earth
CO.1 : Open circuit or short circuit to +12 V.
1. DEF: Faulty sensor
2. DEF: Signal outside upper limit
3. DEF: Micro-breaks
NOTESPriority when dealing with a number of faults:
Apply the procedure for dealing with fault DF011 Sensor voltage supply no. 1 first.
Conditions for applying the fault finding procedure to stored faults:
– CO.1 or CC.0: the fault is declared present after the ignition is switched on.
– 1.DEF, 2. DEF or 3.DEF: the fault is declared present after running the command
AC029 High pressure circuit sealing test.
If the fault is present:
Level 1 warning light activated.
Restriction of torque setpoint and engine speed loss of performance.
Use the Wiring Diagram Technical Notes for CLIO III, MODUS, MEGANE II ph2
and SCENIC II ph2 and KANGOO II.
Check the connection and condition of the rail pressure sensor connector, component code1032 (see MR 392,
385, 364, 370 and 417, Mechanical, 13B, Diesel injection, Rail pressure sensor: Removal - Refitting) and
the injection computer connector, component code120 (see MR 392, 385, 364, 370 and 417, Mechanical,
13B, Diesel injection, Diesel injection computer: Removal - Refitting).
If the connectors are faulty and if there is a repair procedure (see Technical Note 6015A, Repairing electrical
wiring, Wiring: Precautions for repair) repair the connector(s); otherwise, replace the wiring.
Check the insulation, continuity and the absence of interference resistance on the following connections:
–3LX between components 1032 and 120,
–3LY between components 1032 and 120,
–3LZ between components 1032 and 120.
If the connection(s) are faulty and there is a repair method (see Technical Note 6015A, Repairing electrical
wiring, Wiring: Precautions for repair), repair the wiring, otherwise replace it.
If correct, disconnect the sensor and start the engine.
If the engine starts, replace the rail (see MR 392, 385, 364, 370 and 417, Mechanical, 13B, Diesel injection,
Injector rail: Removal - Refitting) and its sensor (see MR 392, 385, 364, 370 and 417, Mechanical, 13B,
Diesel injection, Rail pressure sensor: Removal - Refitting) and the high pressure pipes (see MR 392, 385,
364, 370 and 417, Mechanical, 13B, Diesel injection, High pressure pipe: Check).
Apply test 7 Incorrect injection quantity
.
If the fault is still present, contact the Techline.
AFTER REPAIRDeal with any faults displayed by the diagnostic tool.
Clear the computer fault memory.
Run command AC029 High pressure circuit sealing test again followed by a check
using the diagnostic tool.
Carry out a road test followed by another check with the diagnostic tool.
SID301_V44_DF007 / SID304_V45_DF007 / SID301_V48_DF007 / SID304_V49_DF007 / SID304_V4D_DF007 / SID301_V4C_DF007
Page 41 of 329
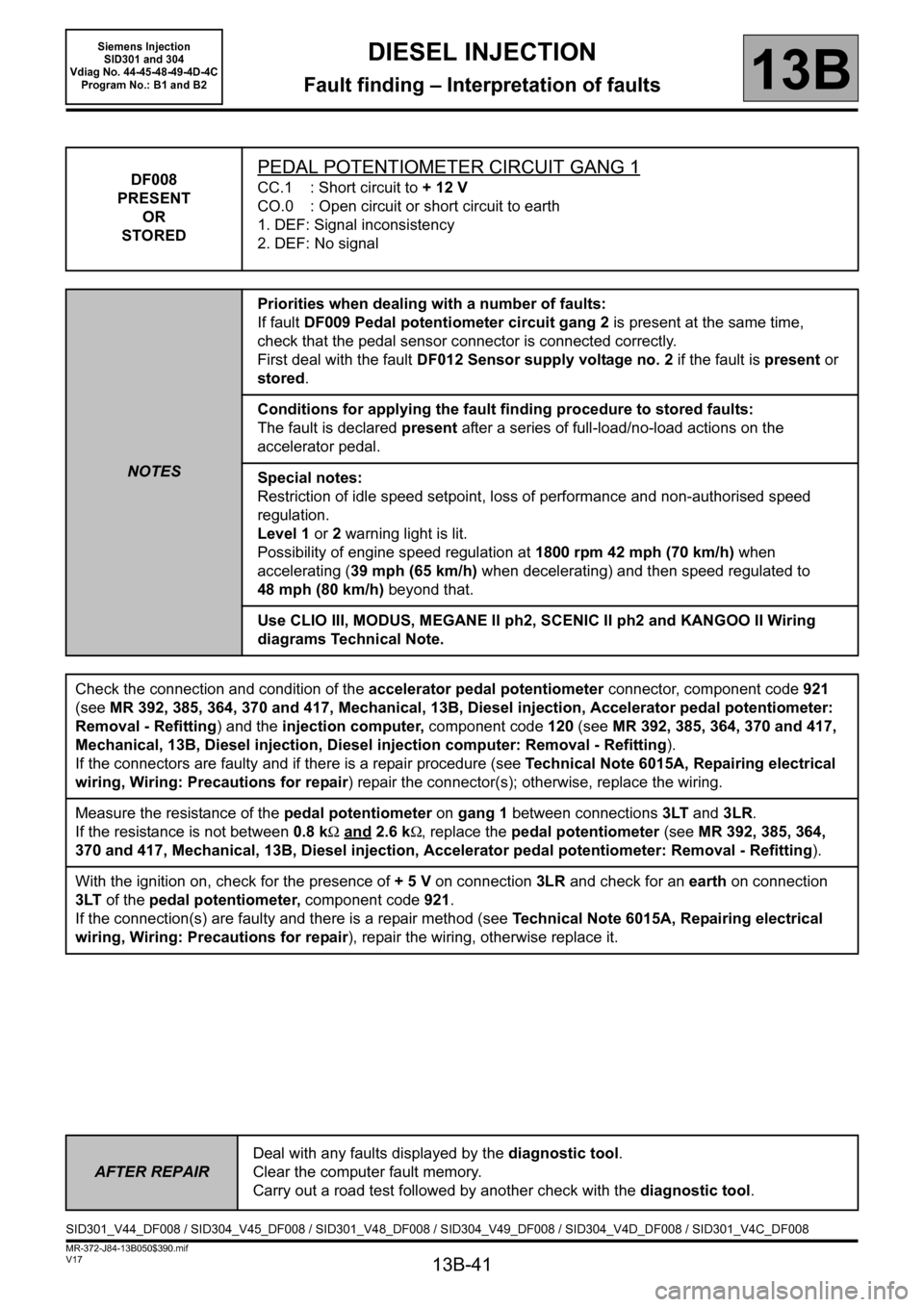
13B-41
MR-372-J84-13B050$390.mif
V17
DIESEL INJECTION
Fault finding – Interpretation of faults
Siemens Injection
SID301 and 304
Vdiag No. 44-45-48-49-4D-4C
Program No.: B1 and B2
13B
DF008
PRESENT
OR
STOREDPEDAL POTENTIOMETER CIRCUIT GANG 1
CC.1 : Short circuit to + 12 V
CO.0 : Open circuit or short circuit to earth
1. DEF: Signal inconsistency
2. DEF: No signal
NOTESPriorities when dealing with a number of faults:
If fault DF009 Pedal potentiometer circuit gang 2 is present at the same time,
check that the pedal sensor connector is connected correctly.
First deal with the fault DF012 Sensor supply voltage no. 2 if the fault is present or
stored.
Conditions for applying the fault finding procedure to stored faults:
The fault is declared present after a series of full-load/no-load actions on the
accelerator pedal.
Special notes:
Restriction of idle speed setpoint, loss of performance and non-authorised speed
regulation.
Level 1 or 2 warning light is lit.
Possibility of engine speed regulation at 1800 rpm 42 mph (70 km/h) when
accelerating (39 mph (65 km/h) when decelerating) and then speed regulated to
48 mph (80 km/h) beyond that.
Use CLIO III, MODUS, MEGANE II ph2, SCENIC II ph2 and KANGOO II Wiring
diagrams Technical Note.
Check the connection and condition of the accelerator pedal potentiometer connector, component code921
(see MR 392, 385, 364, 370 and 417, Mechanical, 13B, Diesel injection, Accelerator pedal potentiometer:
Removal - Refitting) and the injection computer, component code120 (see MR 392, 385, 364, 370 and 417,
Mechanical, 13B, Diesel injection, Diesel injection computer: Removal - Refitting).
If the connectors are faulty and if there is a repair procedure (see Technical Note 6015A, Repairing electrical
wiring, Wiring: Precautions for repair) repair the connector(s); otherwise, replace the wiring.
Measure the resistance of the pedal potentiometer on gang 1 between connections3LT and 3LR.
If the resistance is not between 0.8 kΩ and
2.6 kΩ, replace the pedal potentiometer (see MR 392, 385, 364,
370 and 417, Mechanical, 13B, Diesel injection, Accelerator pedal potentiometer: Removal - Refitting).
With the ignition on, check for the presence of + 5 V on connection 3LR and check for an earth on connection
3LT of the pedal potentiometer, component code 921.
If the connection(s) are faulty and there is a repair method (see Technical Note 6015A, Repairing electrical
wiring, Wiring: Precautions for repair), repair the wiring, otherwise replace it.
AFTER REPAIRDeal with any faults displayed by the diagnostic tool.
Clear the computer fault memory.
Carry out a road test followed by another check with the diagnostic tool.
SID301_V44_DF008 / SID304_V45_DF008 / SID301_V48_DF008 / SID304_V49_DF008 / SID304_V4D_DF008 / SID301_V4C_DF008