compression ratio RENAULT SCENIC 2014 J95 / 3.G Petrol Injection - Sagem3000 Workshop Manual
[x] Cancel search | Manufacturer: RENAULT, Model Year: 2014, Model line: SCENIC, Model: RENAULT SCENIC 2014 J95 / 3.GPages: 181
Page 89 of 181
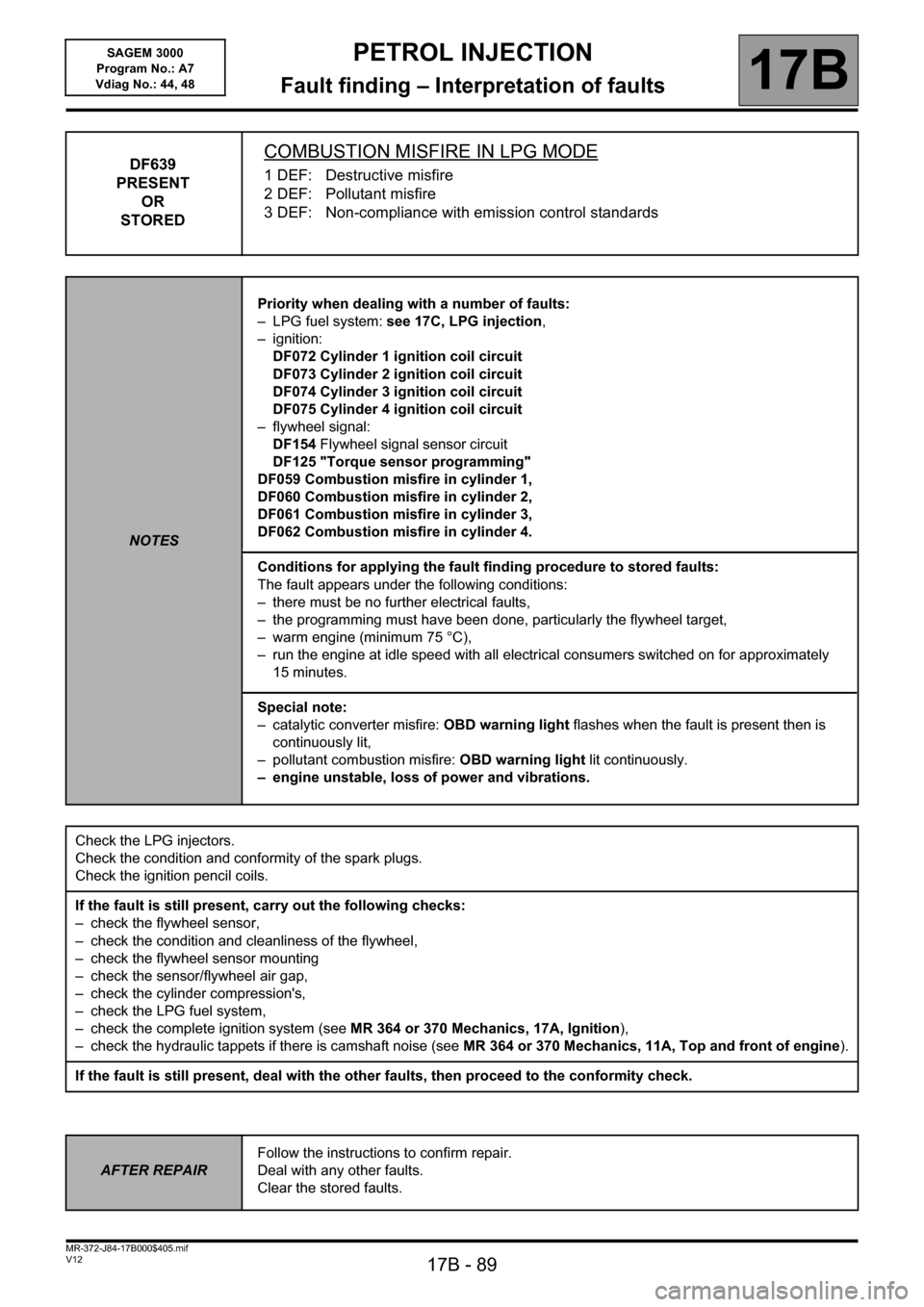
PETROL INJECTION
Fault finding – Interpretation of faults17B
17B - 89V12 MR-372-J84-17B000$405.mif
SAGEM 3000
Program No.: A7
Vdiag No.: 44, 48
DF639
PRESENT
OR
STOREDCOMBUSTION MISFIRE IN LPG MODE
1 DEF: Destructive misfire
2 DEF: Pollutant misfire
3 DEF: Non-compliance with emission control standards
NOTESPriority when dealing with a number of faults:
– LPG fuel system: see 17C, LPG injection,
– ignition:
DF072 Cylinder 1 ignition coil circuit
DF073 Cylinder 2 ignition coil circuit
DF074 Cylinder 3 ignition coil circuit
DF075 Cylinder 4 ignition coil circuit
– flywheel signal:
DF154 Flywheel signal sensor circuit
DF125 "Torque sensor programming"
DF059 Combustion misfire in cylinder 1,
DF060 Combustion misfire in cylinder 2,
DF061 Combustion misfire in cylinder 3,
DF062 Combustion misfire in cylinder 4.
Conditions for applying the fault finding procedure to stored faults:
The fault appears under the following conditions:
– there must be no further electrical faults,
– the programming must have been done, particularly the flywheel target,
– warm engine (minimum 75 °C),
– run the engine at idle speed with all electrical consumers switched on for approximately
15 minutes.
Special note:
– catalytic converter misfire: OBD warning light flashes when the fault is present then is
continuously lit,
– pollutant combustion misfire: OBD warning light lit continuously.
– engine unstable, loss of power and vibrations.
Check the LPG injectors.
Check the condition and conformity of the spark plugs.
Check the ignition pencil coils.
If the fault is still present, carry out the following checks:
– check the flywheel sensor,
– check the condition and cleanliness of the flywheel,
– check the flywheel sensor mounting
– check the sensor/flywheel air gap,
– check the cylinder compression's,
– check the LPG fuel system,
– check the complete ignition system (see MR 364 or 370 Mechanics, 17A, Ignition),
– check the hydraulic tappets if there is camshaft noise (see MR 364 or 370 Mechanics, 11A, Top and front of engine).
If the fault is still present, deal with the other faults, then proceed to the conformity check.
AFTER REPAIRFollow the instructions to confirm repair.
Deal with any other faults.
Clear the stored faults.
Page 179 of 181
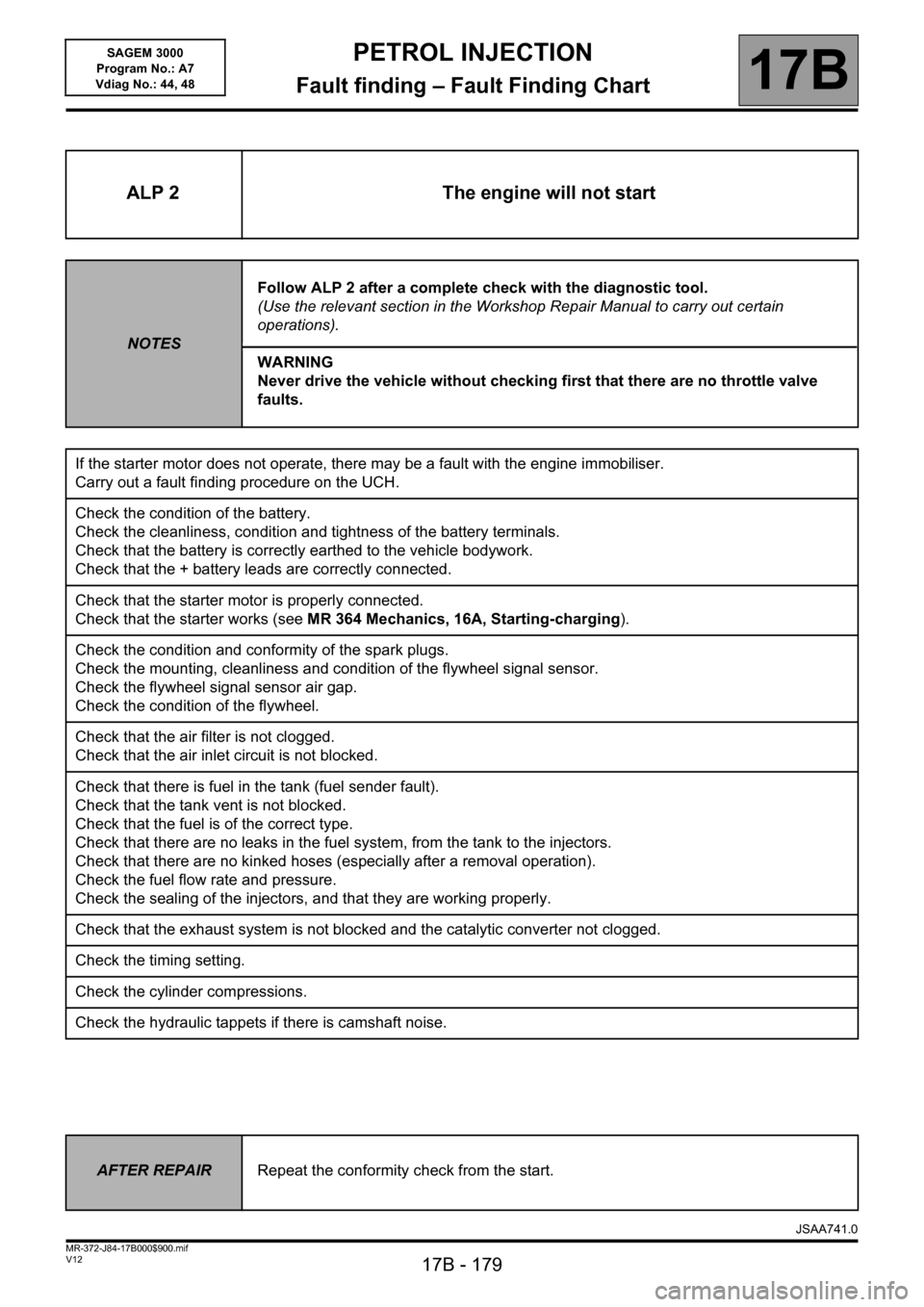
PETROL INJECTION
Fault finding – Fault Finding Chart17B
17B - 179V12 MR-372-J84-17B000$900.mif
SAGEM 3000
Program No.: A7
Vdiag No.: 44, 48
ALP 2 The engine will not start
NOTESFollow ALP 2 after a complete check with the diagnostic tool.
(Use the relevant section in the Workshop Repair Manual to carry out certain
operations).
WARNING
Never drive the vehicle without checking first that there are no throttle valve
faults.
If the starter motor does not operate, there may be a fault with the engine immobiliser.
Carry out a fault finding procedure on the UCH.
Check the condition of the battery.
Check the cleanliness, condition and tightness of the battery terminals.
Check that the battery is correctly earthed to the vehicle bodywork.
Check that the + battery leads are correctly connected.
Check that the starter motor is properly connected.
Check that the starter works (see MR 364 Mechanics, 16A, Starting-charging).
Check the condition and conformity of the spark plugs.
Check the mounting, cleanliness and condition of the flywheel signal sensor.
Check the flywheel signal sensor air gap.
Check the condition of the flywheel.
Check that the air filter is not clogged.
Check that the air inlet circuit is not blocked.
Check that there is fuel in the tank (fuel sender fault).
Check that the tank vent is not blocked.
Check that the fuel is of the correct type.
Check that there are no leaks in the fuel system, from the tank to the injectors.
Check that there are no kinked hoses (especially after a removal operation).
Check the fuel flow rate and pressure.
Check the sealing of the injectors, and that they are working properly.
Check that the exhaust system is not blocked and the catalytic converter not clogged.
Check the timing setting.
Check the cylinder compressions.
Check the hydraulic tappets if there is camshaft noise.
AFTER REPAIRRepeat the conformity check from the start.
JSAA741.0
Page 180 of 181
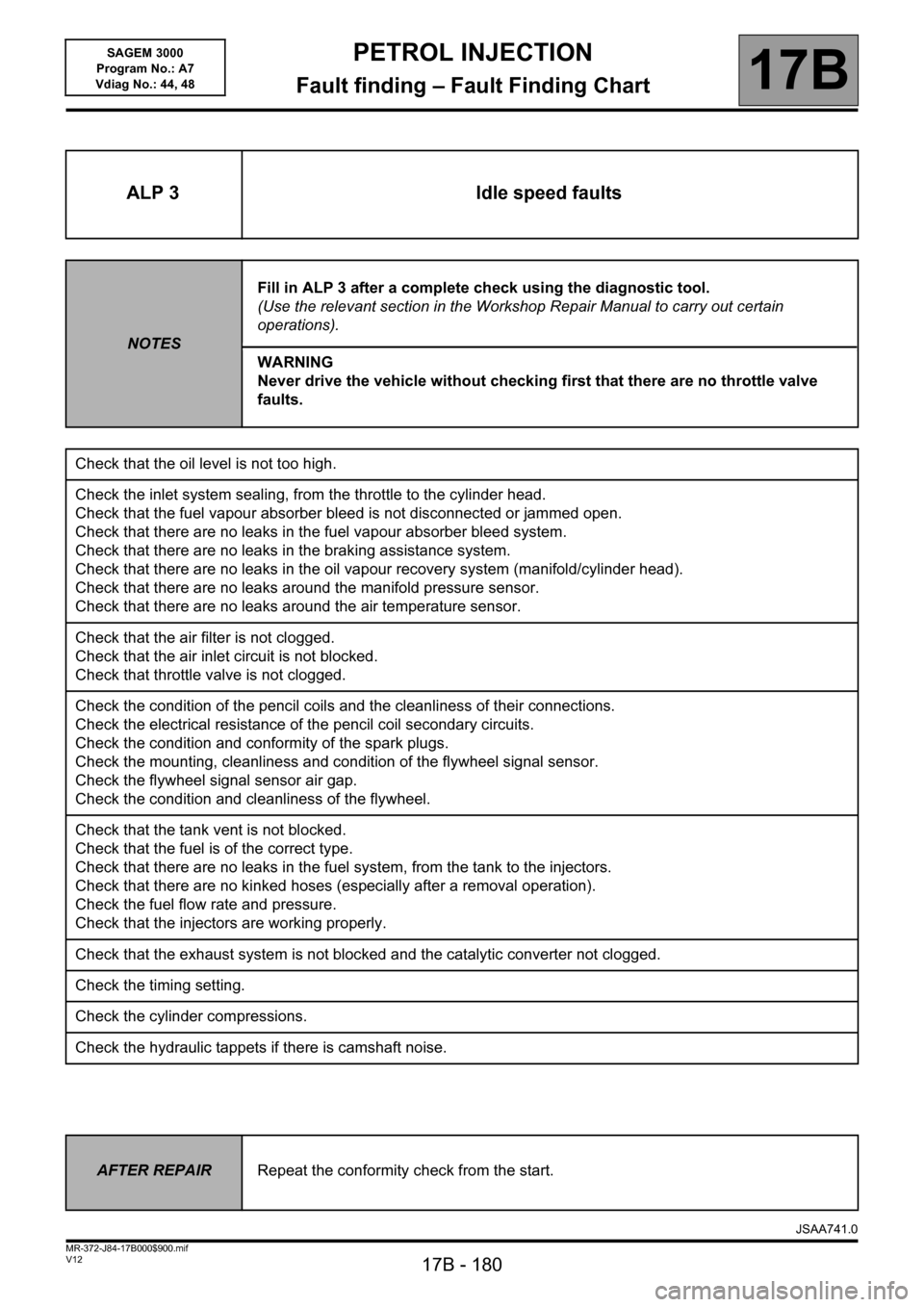
PETROL INJECTION
Fault finding – Fault Finding Chart17B
17B - 180V12 MR-372-J84-17B000$900.mif
SAGEM 3000
Program No.: A7
Vdiag No.: 44, 48
ALP 3 Idle speed faults
NOTESFill in ALP 3 after a complete check using the diagnostic tool.
(Use the relevant section in the Workshop Repair Manual to carry out certain
operations).
WARNING
Never drive the vehicle without checking first that there are no throttle valve
faults.
Check that the oil level is not too high.
Check the inlet system sealing, from the throttle to the cylinder head.
Check that the fuel vapour absorber bleed is not disconnected or jammed open.
Check that there are no leaks in the fuel vapour absorber bleed system.
Check that there are no leaks in the braking assistance system.
Check that there are no leaks in the oil vapour recovery system (manifold/cylinder head).
Check that there are no leaks around the manifold pressure sensor.
Check that there are no leaks around the air temperature sensor.
Check that the air filter is not clogged.
Check that the air inlet circuit is not blocked.
Check that throttle valve is not clogged.
Check the condition of the pencil coils and the cleanliness of their connections.
Check the electrical resistance of the pencil coil secondary circuits.
Check the condition and conformity of the spark plugs.
Check the mounting, cleanliness and condition of the flywheel signal sensor.
Check the flywheel signal sensor air gap.
Check the condition and cleanliness of the flywheel.
Check that the tank vent is not blocked.
Check that the fuel is of the correct type.
Check that there are no leaks in the fuel system, from the tank to the injectors.
Check that there are no kinked hoses (especially after a removal operation).
Check the fuel flow rate and pressure.
Check that the injectors are working properly.
Check that the exhaust system is not blocked and the catalytic converter not clogged.
Check the timing setting.
Check the cylinder compressions.
Check the hydraulic tappets if there is camshaft noise.
AFTER REPAIRRepeat the conformity check from the start.
JSAA741.0
Page 181 of 181
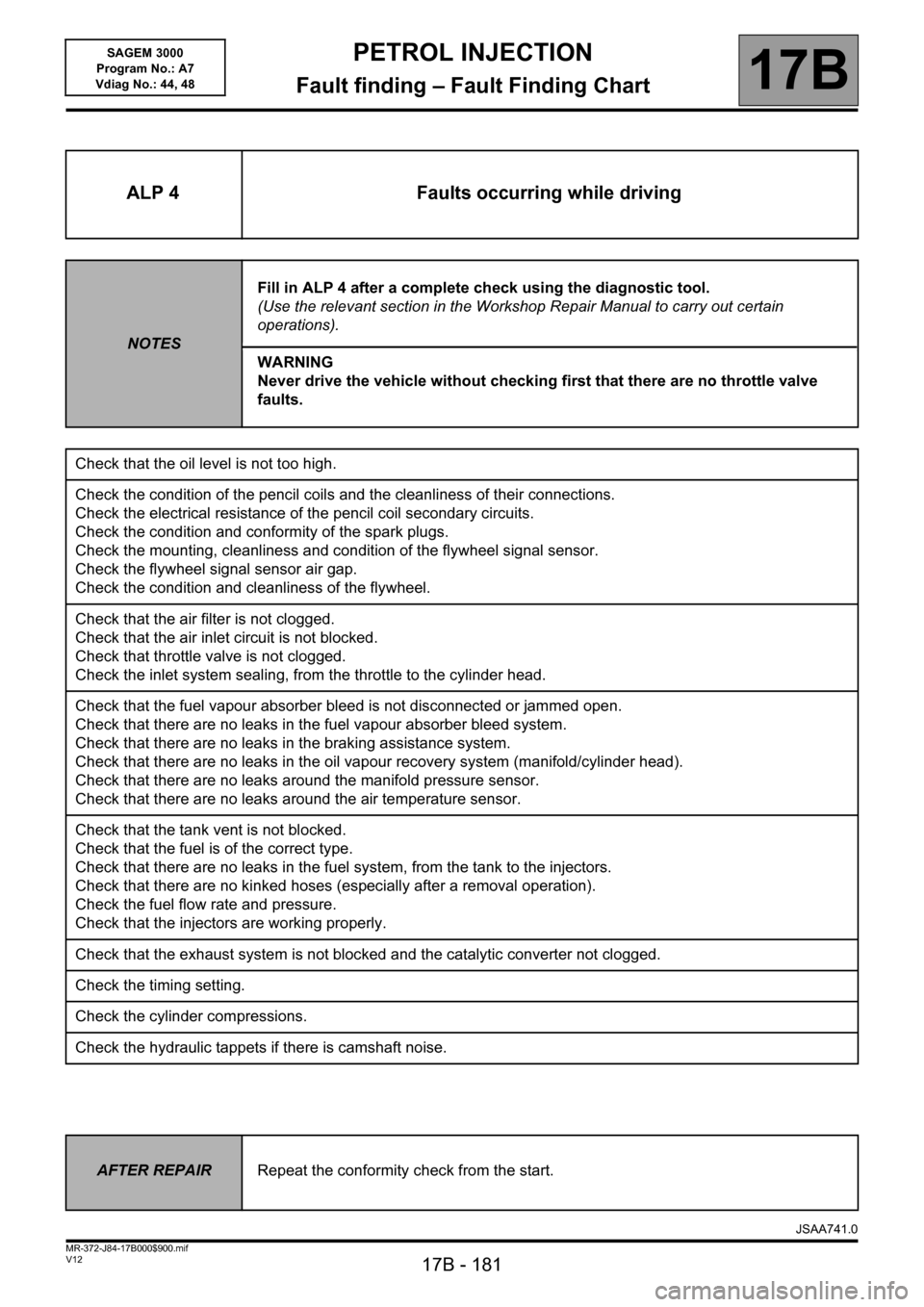
PETROL INJECTION
Fault finding – Fault Finding Chart17B
17B - 181V12 MR-372-J84-17B000$900.mif
SAGEM 3000
Program No.: A7
Vdiag No.: 44, 48
ALP 4 Faults occurring while driving
NOTESFill in ALP 4 after a complete check using the diagnostic tool.
(Use the relevant section in the Workshop Repair Manual to carry out certain
operations).
WARNING
Never drive the vehicle without checking first that there are no throttle valve
faults.
Check that the oil level is not too high.
Check the condition of the pencil coils and the cleanliness of their connections.
Check the electrical resistance of the pencil coil secondary circuits.
Check the condition and conformity of the spark plugs.
Check the mounting, cleanliness and condition of the flywheel signal sensor.
Check the flywheel signal sensor air gap.
Check the condition and cleanliness of the flywheel.
Check that the air filter is not clogged.
Check that the air inlet circuit is not blocked.
Check that throttle valve is not clogged.
Check the inlet system sealing, from the throttle to the cylinder head.
Check that the fuel vapour absorber bleed is not disconnected or jammed open.
Check that there are no leaks in the fuel vapour absorber bleed system.
Check that there are no leaks in the braking assistance system.
Check that there are no leaks in the oil vapour recovery system (manifold/cylinder head).
Check that there are no leaks around the manifold pressure sensor.
Check that there are no leaks around the air temperature sensor.
Check that the tank vent is not blocked.
Check that the fuel is of the correct type.
Check that there are no leaks in the fuel system, from the tank to the injectors.
Check that there are no kinked hoses (especially after a removal operation).
Check the fuel flow rate and pressure.
Check that the injectors are working properly.
Check that the exhaust system is not blocked and the catalytic converter not clogged.
Check the timing setting.
Check the cylinder compressions.
Check the hydraulic tappets if there is camshaft noise.
AFTER REPAIRRepeat the conformity check from the start.
JSAA741.0