ECU RENAULT TWINGO 2009 2.G Chasiss ESP Workshop Manual
[x] Cancel search | Manufacturer: RENAULT, Model Year: 2009, Model line: TWINGO, Model: RENAULT TWINGO 2009 2.GPages: 101
Page 3 of 101
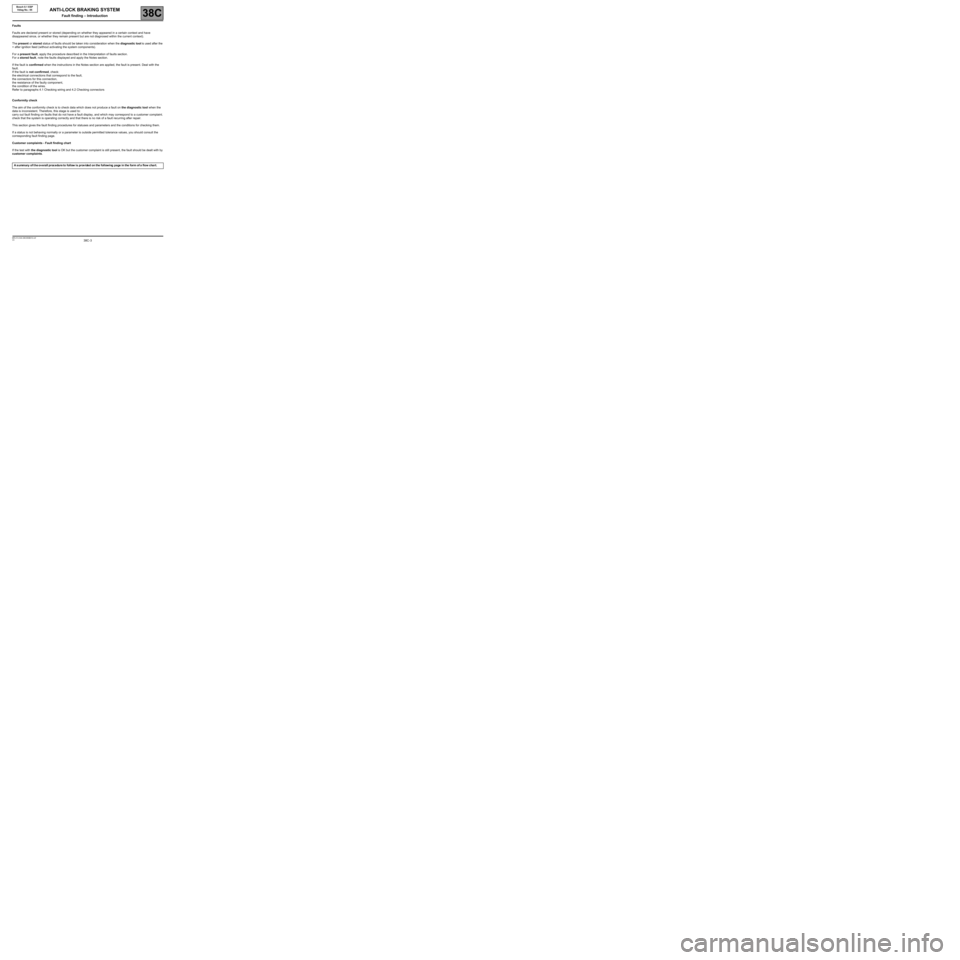
38C -3V3 MR-413-X44-38C050$010.mif
ANTI-LOCK BRAKING SYSTEM
Fault finding – Introduction
Bosch 8.1 ESP
Vdiag No.: 05
38C
Faults
Faults are declared present or stored (depending on whether they appeared in a certain context and have
disappeared since, or whether they remain present but are not diagnosed within the current context).
The present or stored status of faults should be taken into consideration when the diagnostic tool is used after the
+ after ignition feed (without activating the system components).
For a present fault, apply the procedure described in the Interpretation of faults section.
For a stored fault, note the faults displayed and apply the Notes section.
If the fault is confirmed when the instructions in the Notes section are applied, the fault is present. Deal with the
fault.
If the fault is not confirmed, check:
the electrical connections that correspond to the fault,
the connectors for this connection,
the resistance of the faulty component,
the condition of the wires.
Refer to paragraphs 4.1 Checking wiring and 4.2 Checking connectors
Conformity check
The aim of the conformity check is to check data which does not produce a fault on the diagnostic tool when the
data is inconsistent. Therefore, this stage is used to:
carry out fault finding on faults that do not have a fault display, and which may correspond to a customer complaint.
check that the system is operating correctly and that there is no risk of a fault recurring after repair.
This section gives the fault finding procedures for statuses and parameters and the conditions for checking them.
If a status is not behaving normally or a parameter is outside permitted tolerance values, you should consult the
corresponding fault finding page.
Customer complaints - Fault finding chart
If the test with the diagnostic tool is OK but the customer complaint is still present, the fault should be dealt with by
customer complaints.
Asummary oftheoverall proc edure to follow isprovidedonthe fol lowing page in the form of a flow chart.
Page 5 of 101
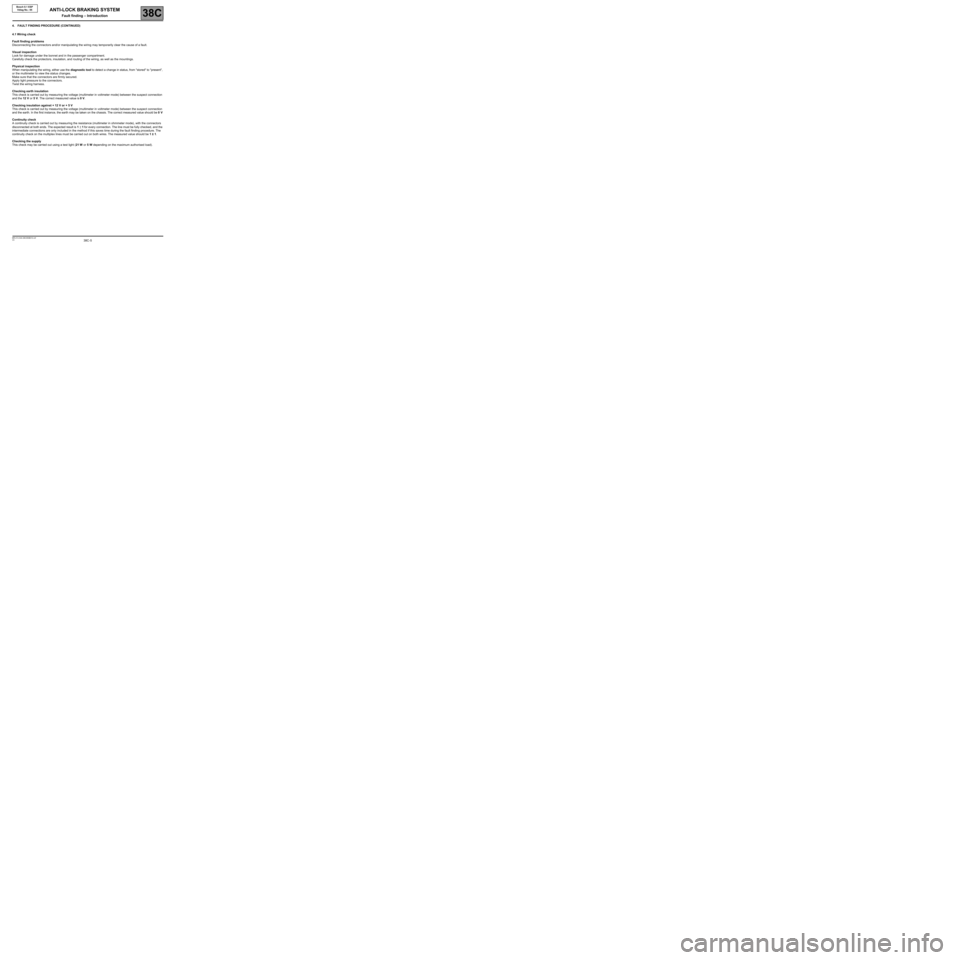
38C -5V3 MR-413-X44-38C050$010.mif
ANTI-LOCK BRAKING SYSTEM
Fault finding – Introduction
Bosch 8.1 ESP
Vdiag No.: 05
38C
4. FAULT FINDING PROCEDURE (CONTINUED)
4.1 Wiring check
Fault finding problems
Disconnecting the connectors and/or manipulating the wiring may temporarily clear the cause of a fault.
Visual inspection
Look for damage under the bonnet and in the passenger compartment.
Carefully check the protectors, insulation, and routing of the wiring, as well as the mountings.
Physical inspection
When manipulating the wiring, either use the diagnostic tool to detect a change in status, from "stored" to "present",
or the multimeter to view the status changes.
Make sure that the connectors are firmly secured.
Apply light pressure to the connectors.
Twist the wiring harness.
Checking earth insulation
This check is carried out by measuring the voltage (multimeter in voltmeter mode) between the suspect connection
and the 12 V or 5 V. The correct measured value is 0 V.
Checking insulation against + 12 V or + 5 V
This check is carried out by measuring the voltage (multimeter in voltmeter mode) between the suspect connection
and the earth. In the first instance, the earth may be taken on the chassis. The correct measured value should be 0 V
Continuity check
A continuity check is carried out by measuring the resistance (multimeter in ohmmeter mode), with the connectors
disconnected at both ends. The expected result is 1
± 1 for every connection. The line must be fully checked, and the
intermediate connections are only included in the method if this saves time during the fault finding procedure. The
continuity check on the multiplex lines must be carried out on both wires. The measured value should be 1 ± 1.
Checking the supply
This check may be carried out using a test light (21 W or 5 W depending on the maximum authorised load).
Page 8 of 101
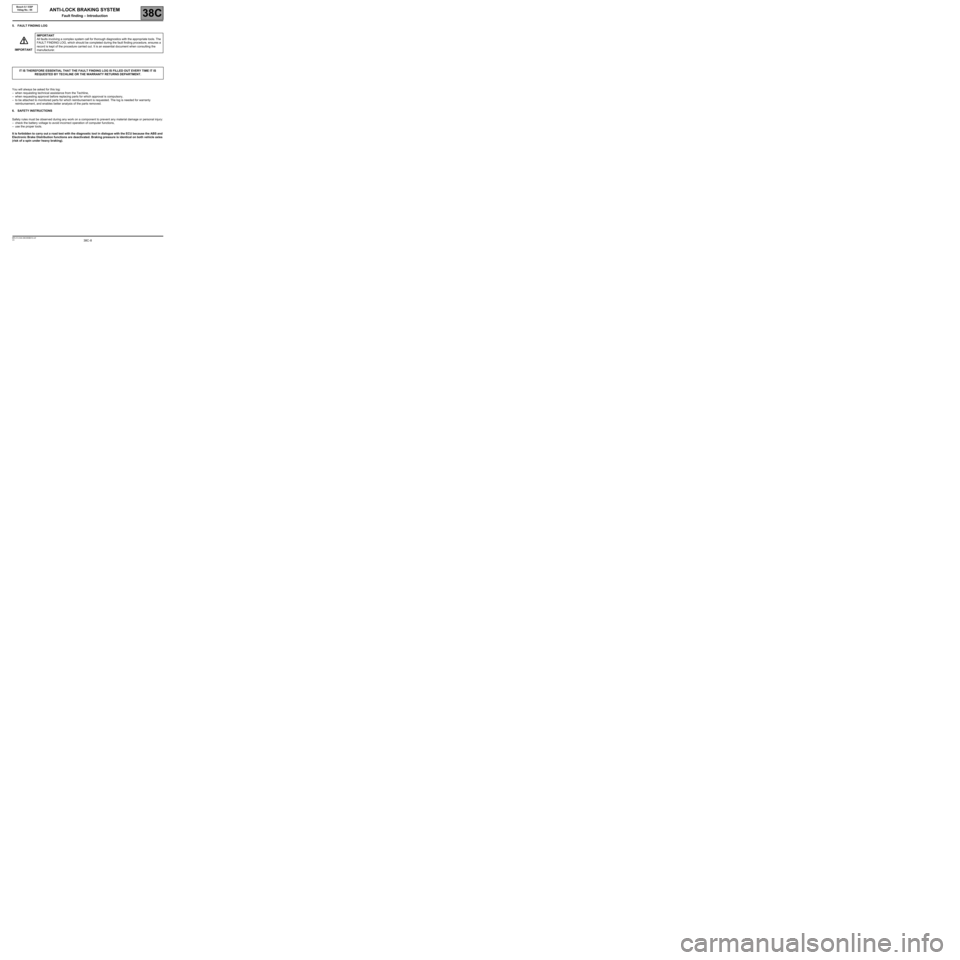
38C -8V3 MR-413-X44-38C050$010.mif
ANTI-LOCK BRAKING SYSTEM
Fault finding – Introduction
Bosch 8.1 ESP
Vdiag No.: 05
38C
5. FAULT FINDING LOG
You will always be asked for this log:
–when requesting technical assistance from the Techline,
–when requesting approval before replacing parts for which approval is compulsory,
–to be attached to monitored parts for which reimbursement is requested. The log is needed for warranty
reimbursement, and enables better analysis of the parts removed.
6. SAFETY INSTRUCTIONS
Safety rules must be observed during any work on a component to prevent any material damage or personal injury:
–check the battery voltage to avoid incorrect operation of computer functions,
–use the proper tools.
It is forbidden to carry out a road test with the diagnostic tool in dialogue with the ECU because the ABS and
Electronic Brake Distribution functions are deactivated. Braking pressure is identical on both vehicle axles
(risk of a spin under heavy braking).IMPORTANTIMPORTANT
All faults involving a complex system call for thorough diagnostics with the appropriate tools. The
FAULT FINDING LOG, which should be completed during the fault finding procedure, ensures a
record is kept of the procedure carried out. It is an essential document when consulting the
manufacturer.
IT IS THEREFORE ESSENTIAL THAT THE FAULT FINDING LOG IS FILLED OUT EVERY TIME IT IS
REQUESTED BY TECHLINE OR THE WARRANTY RETURNS DEPARTMENT.
Page 58 of 101
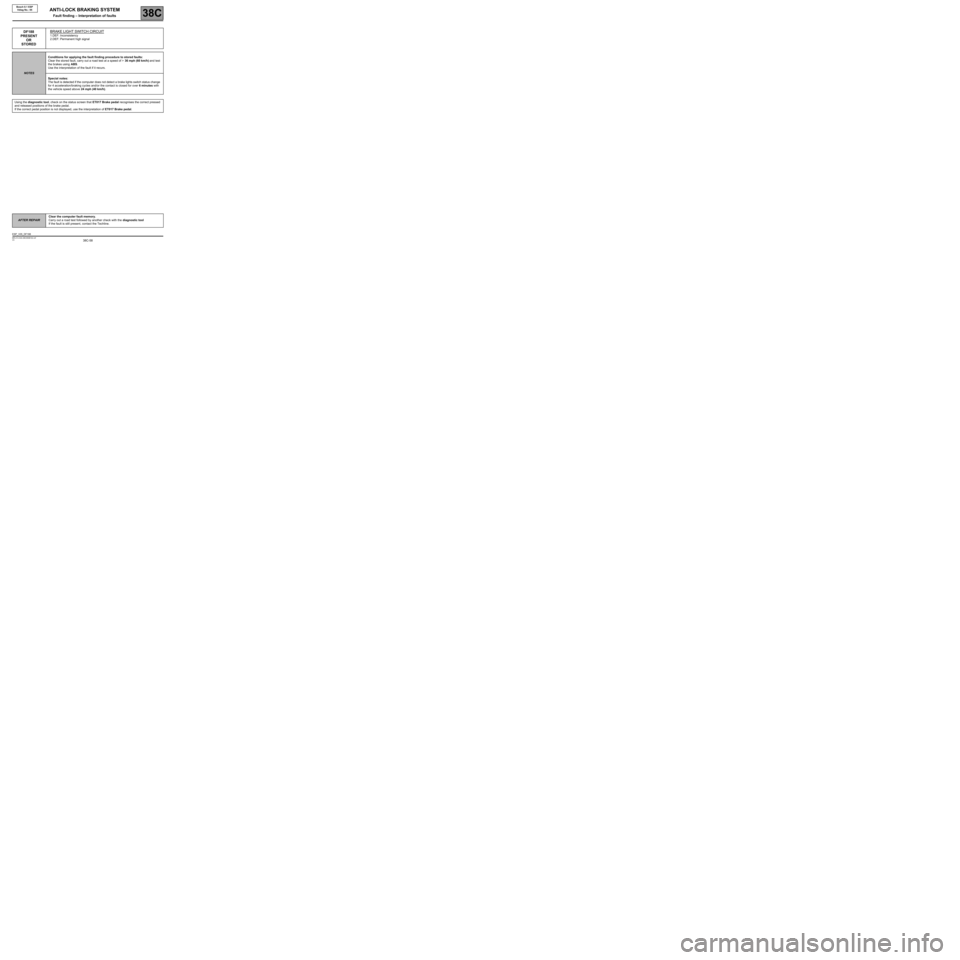
38C-58
AFTER REPAIRClear the computer fault memory.
Carry out a road test followed by another check with the diagnostic tool
If the fault is still present, contact the Techline.
V3 MR-413-X44-38C050$102.mif
38C
Bosch 8.1 ESP
Vdiag No.: 05
DF188
PRESENT
OR
STOREDBRAKE LIGHT SWITCH CIRCUIT
1.DEF: Inconsistency
2.DEF: Permanent high signal
NOTESConditions for applying the fault finding procedure to stored faults:
Clear the stored fault, carry out a road test at a speed of > 36 mph (60 km/h) and test
the brakes using ABS.
Use the interpretation of the fault if it recurs.
Special notes:
The fault is detected if the computer does not detect a brake lights switch status change
for 4 acceleration/braking cycles and/or the contact is closed for over 6 minutes with
the vehicle speed above 24 mph (40 km/h).
Using the diagnostic tool, check on the status screen that ET017 Brake pedal recognises the correct pressed
and released positions of the brake pedal.
If the correct pedal position is not displayed, use the interpretation of ET017 Brake pedal.
ANTI-LOCK BRAKING SYSTEM
Fault finding – Interpretation of faults
ESP_V05_DF188
Page 88 of 101

38C-88
AFTER REPAIRClear the computer fault memory.
Carry out a road test followed by another check with the diagnostic tool.
V3 MR-413-X44-38C050$180.mif
ANTI-LOCK BRAKING SYSTEM
Fault finding – Fault finding chart38C
Bosch 8.1 ESP
Vdiag No.: 05
ALP2 Locking or braking of one or more wheels
NOTESOnly consult this customer complaint after a full check with the diagnostic tool.
Check the conformity of the mechanical components (see MR 411, Mechanical,
30A, General information, Brake, Specifications).
REMINDERLocking of wheels on a vehicle fitted with ABS or squealing of the tyres, which feels like
locking to the customer, may be linked to normal operation of the system and should not
always be considered a fault.
Braking with ABS regulation on very poor roads can cause significant squealing.
However, if the wheel(s) is/are actually locking, lift the vehicle in order to be able to rotate the wheels and check:
Possible inversion when connecting the speed sensors.
Use parameters PR001 Front right-hand wheel speed, PR002 Front left-hand wheel speed, PR003 Rear right-
hand wheel speed and PR004 Rear left-hand wheel speed whilst slowly turning the wheels in question and
checking the consistency of the results obtained.
If the value measured is zero, rotate the other wheels to confirm an electrical inversion of the sensors and repair
the wiring harness.
If a single reading is incorrect:
–Check that the sensor casing is secured when rotating.
–Check that the wheel speed sensor mounting is in good condition.
–If that is unsuccessful, replace the corresponding sensor and repeat the check procedure (see MR 411
Mechanical, 38C, Anti-lock braking system, Wheel speed sensor: Removal - Refitting).
–A possible inversion of the pipes on the hydraulic unit (see MR 411, Mechanical, 38C, Anti-lock braking
system, Hydraulic braking unit, List and location of components).
Run commands AC003 Front left-hand wheel solenoid valves, AC004 Front right-hand wheel solenoid
valves, AC005 Rear left-hand wheel solenoid valves and AC006 Rear right-hand wheel solenoid valves while
depressing the brake pedal and check for locking/unlocking cycles on the wheel concerned (see Dealing with
command modes).
If the cycles are not detected on the wheel tested (wheel remains locked), check if they occur on another wheel
(confirmation of a reversal after a repair, see MR 411, Mechanical, 38C, Hydraulic braking unit, List and
location of components).
If the cycles are not detected on a wheel and the pipes have not been inverted, replace component 1094
(see MR 411, Mechanical, 38C, Hydraulic braking unit, Removal- Refitting).
Check that the sensor holder does not rotate (depending on fitting).
Check the quality of the mounting of the wheel speed sensors (correct clipping for the front wheels).
Check the conformity of the targets: the condition and the number of teeth= 48 (using the command SC001
"Check target teeth").
Replace if necessary.
If the fault is still present after these checks, replace component 1094 (see MR 411, Mechanical, 38C, Hydraulic
braking unit, Removal- Refitting).
ESP_V05_ALP2
Page 97 of 101
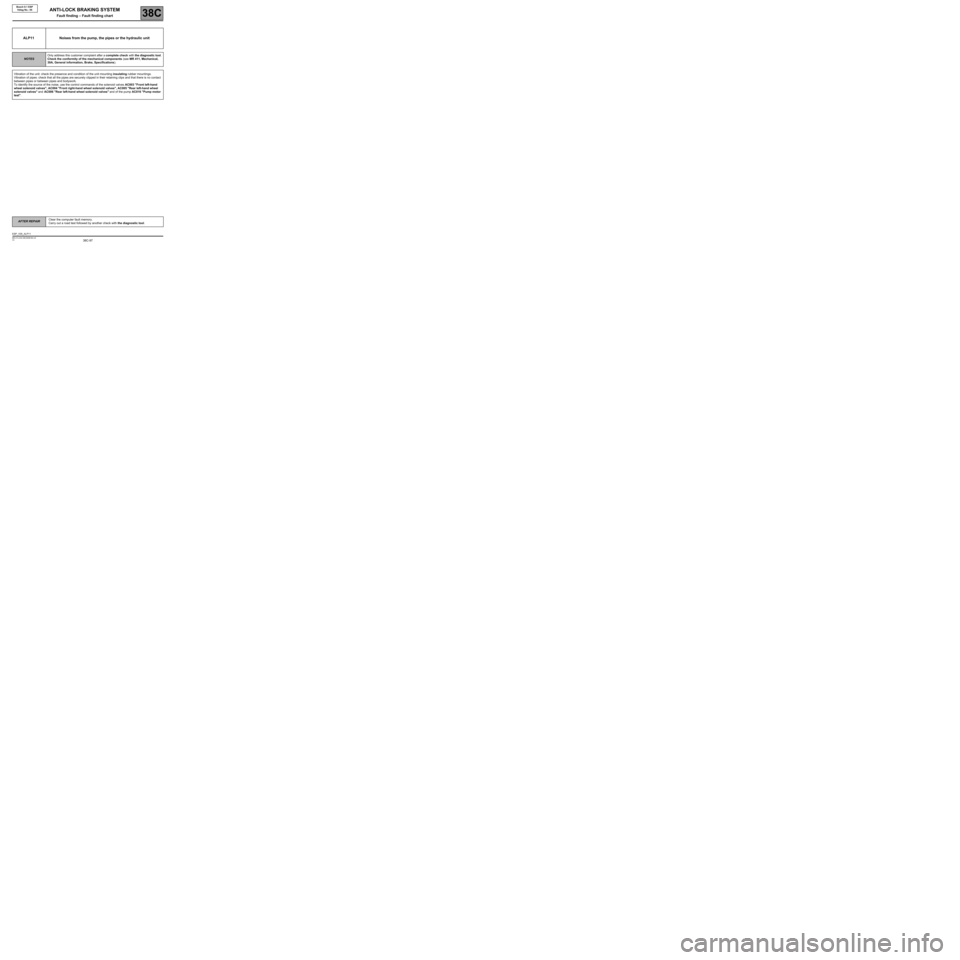
38C-97
AFTER REPAIRClear the computer fault memory.
Carry out a road test followed by another check with the diagnostic tool.
V3 MR-413-X44-38C050$180.mif
ANTI-LOCK BRAKING SYSTEM
Fault finding – Fault finding chart38C
Bosch 8.1 ESP
Vdiag No.: 05
ALP11 Noises from the pump, the pipes or the hydraulic unit
NOTESOnly address this customer complaint after a complete check with the diagnostic tool.
Check the conformity of the mechanical components (see MR 411, Mechanical,
30A, General information, Brake, Specifications).
Vibration of the unit: check the presence and condition of the unit mounting insulating rubber mountings.
Vibration of pipes: check that all the pipes are securely clipped in their retaining clips and that there is no contact
between pipes or between pipes and bodywork.
To identify the source of the noise, use the control commands of the solenoid valves AC003 "Front left-hand
wheel solenoid valves", AC004 "Front right-hand wheel solenoid valves", AC005 "Rear left-hand wheel
solenoid valves" and AC006 "Rear left-hand wheel solenoid valves" and of the pump AC016 "Pump motor
test".
ESP_V05_ALP11