ESP RENAULT TWINGO 2009 2.G Chasiss - Power Assisted Steering Workshop Manual
[x] Cancel search | Manufacturer: RENAULT, Model Year: 2009, Model line: TWINGO, Model: RENAULT TWINGO 2009 2.GPages: 54
Page 3 of 54
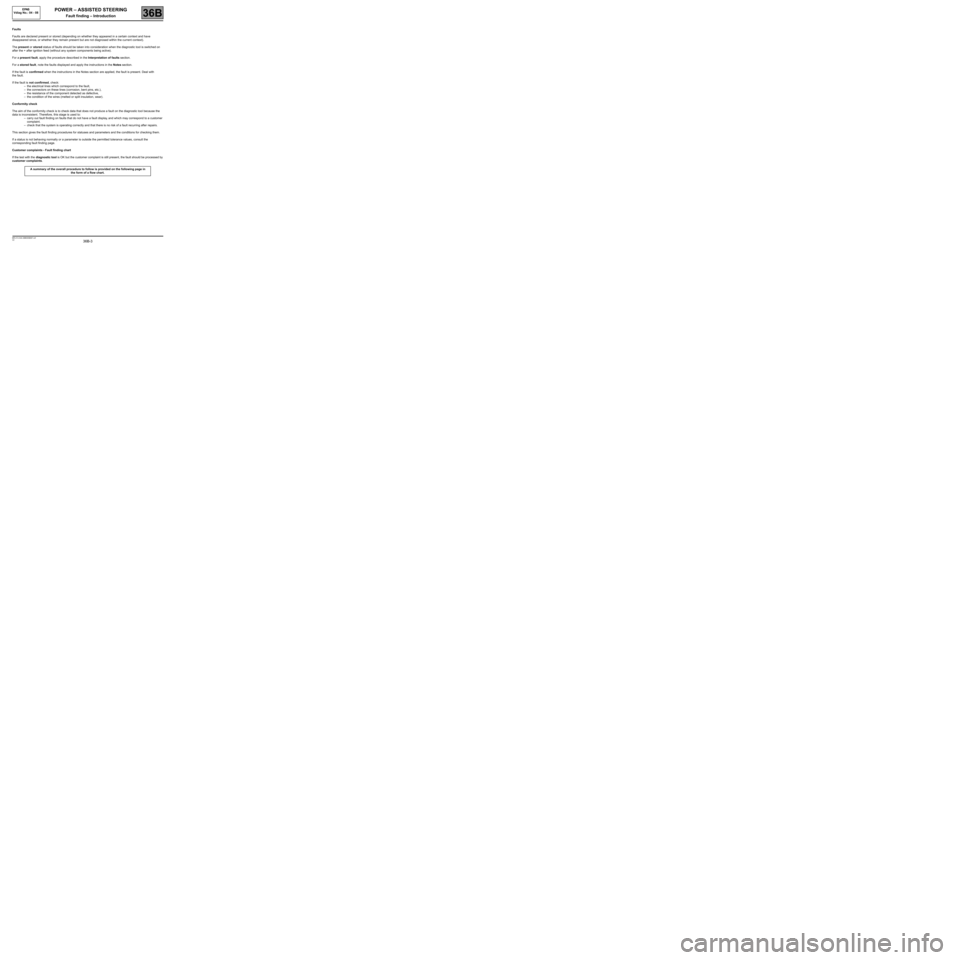
36B-3
MR-413-X44-36B000$067.mif
V2
POWER – ASSISTED STEERING
Fault finding – Introduction
EPAS
Vdiag No.: 04 - 08
36B
Faults
Faults are declared present or stored (depending on whether they appeared in a certain context and have
disappeared since, or whether they remain present but are not diagnosed within the current context).
The present or stored status of faults should be taken into consideration when the diagnostic tool is switched on
after the + after ignition feed (without any system components being active).
For a present fault, apply the procedure described in the Interpretation of faults section.
For a stored fault, note the faults displayed and apply the instructions in the Notes section.
If the fault is confirmed when the instructions in the Notes section are applied, the fault is present. Deal with
the fault.
If the fault is not confirmed, check:
–the electrical lines which correspond to the fault,
–the connectors on these lines (corrosion, bent pins, etc.),
–the resistance of the component detected as defective,
–the condition of the wires (melted or split insulation, wear).
Conformity check
The aim of the conformity check is to check data that does not produce a fault on the diagnostic tool because the
data is inconsistent. Therefore, this stage is used to:
–carry out fault finding on faults that do not have a fault display, and which may correspond to a customer
complaint.
–check that the system is operating correctly and that there is no risk of a fault recurring after repairs.
This section gives the fault finding procedures for statuses and parameters and the conditions for checking them.
If a status is not behaving normally or a parameter is outside the permitted tolerance values, consult the
corresponding fault finding page.
Customer complaints - Fault finding chart
If the test with the diagnostic tool is OK but the customer complaint is still present, the fault should be processed by
customer complaints.
A summary of the overall procedure to follow is provided on the following page in
the form of a flow chart.
Page 5 of 54
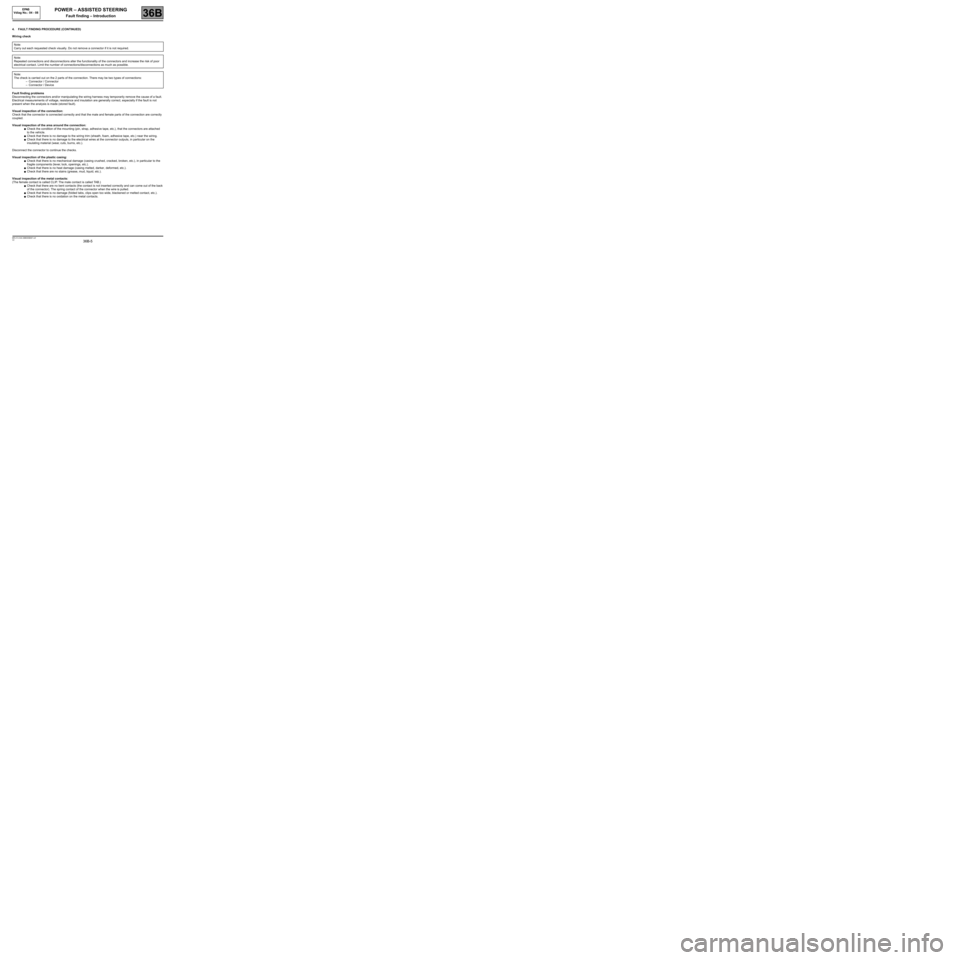
36B-5
MR-413-X44-36B000$067.mif
V2
POWER – ASSISTED STEERING
Fault finding – Introduction
EPAS
Vdiag No.: 04 - 08
36B
4. FAULT FINDING PROCEDURE (CONTINUED)
Wiring check
Fault finding problems
Disconnecting the connectors and/or manipulating the wiring harness may temporarily remove the cause of a fault.
Electrical measurements of voltage, resistance and insulation are generally correct, especially if the fault is not
present when the analysis is made (stored fault).
Visual inspection of the connection:
Check that the connector is connected correctly and that the male and female parts of the connection are correctly
coupled.
Visual inspection of the area around the connection:
●Check the condition of the mounting (pin, strap, adhesive tape, etc.), that the connectors are attached
to the vehicle.
●Check that there is no damage to the wiring trim (sheath, foam, adhesive tape, etc.) near the wiring.
●Check that there is no damage to the electrical wires at the connector outputs, in particular on the
insulating material (wear, cuts, burns, etc.).
Disconnect the connector to continue the checks.
Visual inspection of the plastic casing:
●Check that there is no mechanical damage (casing crushed, cracked, broken, etc.), in particular to the
fragile components (lever, lock, openings, etc.).
●Check that there is no heat damage (casing melted, darker, deformed, etc.).
●Check that there are no stains (grease, mud, liquid, etc.).
Visual inspection of the metal contacts:
(The female contact is called CLIP. The male contact is called TAB.)
●Check that there are no bent contacts (the contact is not inserted correctly and can come out of the back
of the connector). The spring contact of the connector when the wire is pulled.
●Check that there is no damage (folded tabs, clips open too wide, blackened or melted contact, etc.).
●Check that there is no oxidation on the metal contacts. Note:
Carry out each requested check visually. Do not remove a connector if it is not required.
Note:
Repeated connections and disconnections alter the functionality of the connectors and increase the risk of poor
electrical contact. Limit the number of connections/disconnections as much as possible.
Note:
The check is carried out on the 2 parts of the connection. There may be two types of connections:
–Connector / Connector
–Connector / Device
Page 11 of 54
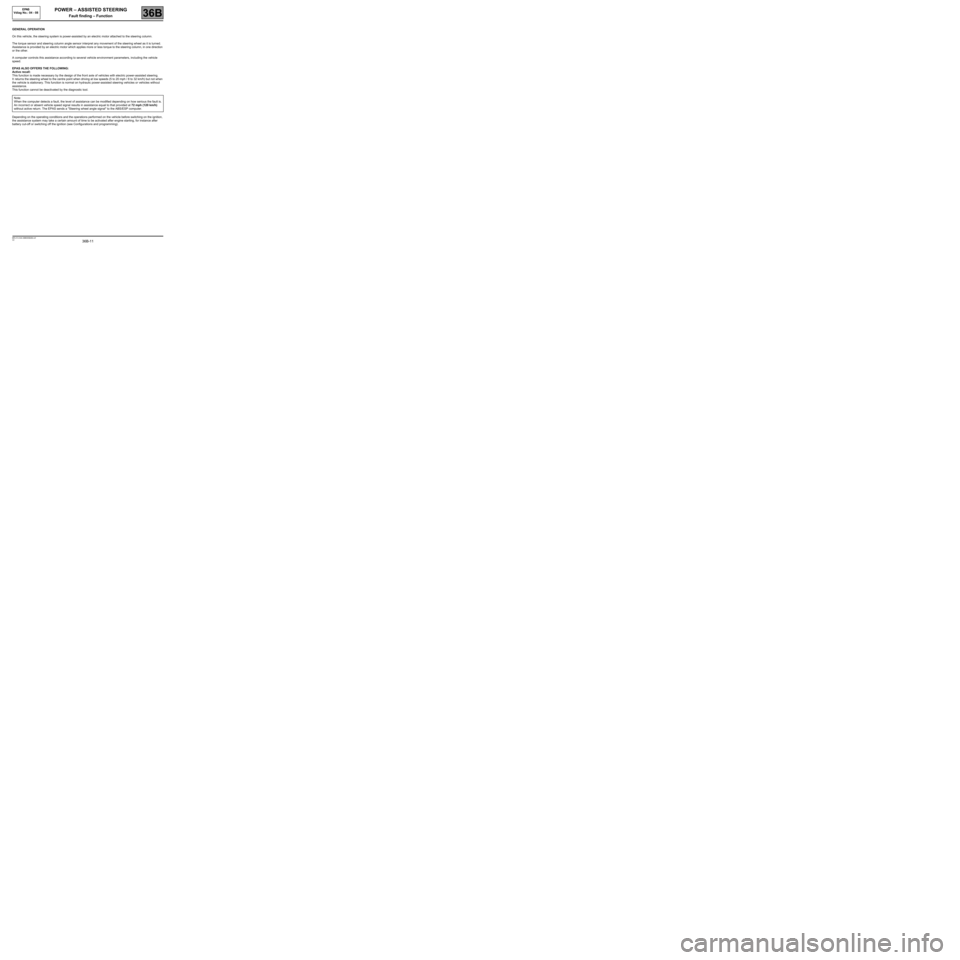
36B-11
MR-413-X44-36B000$268.mif
V2
POWER – ASSISTED STEERING
Fault finding – Function
EPAS
Vdiag No.: 04 - 08
36B
GENERAL OPERATION
On this vehicle, the steering system is power-assisted by an electric motor attached to the steering column.
The torque sensor and steering column angle sensor interpret any movement of the steering wheel as it is turned.
Assistance is provided by an electric motor which applies more or less torque to the steering column, in one direction
or the other.
A computer controls this assistance according to several vehicle environment parameters, including the vehicle
speed.
EPAS ALSO OFFERS THE FOLLOWING:
Active recall:
This function is made necessary by the design of the front axle of vehicles with electric power-assisted steering.
It returns the steering wheel to the centre point when driving at low speeds (5 to 20 mph / 8 to 32 km/h) but not when
the vehicle is stationary. This function is normal on hydraulic power-assisted steering vehicles or vehicles without
assistance.
This function cannot be deactivated by the diagnostic tool.
Depending on the operating conditions and the operations performed on the vehicle before switching on the ignition,
the assistance system may take a certain amount of time to be activated after engine starting, for instance after
battery cut-off or switching off the ignition (see Configurations and programming).Note:
When the computer detects a fault, the level of assistance can be modified depending on how serious the fault is.
An incorrect or absent vehicle speed signal results in assistance equal to that provided at 72 mph (120 km/h)
without active return. The EPAS sends a "Steering wheel angle signal" to the ABS/ESP computer.
Page 17 of 54
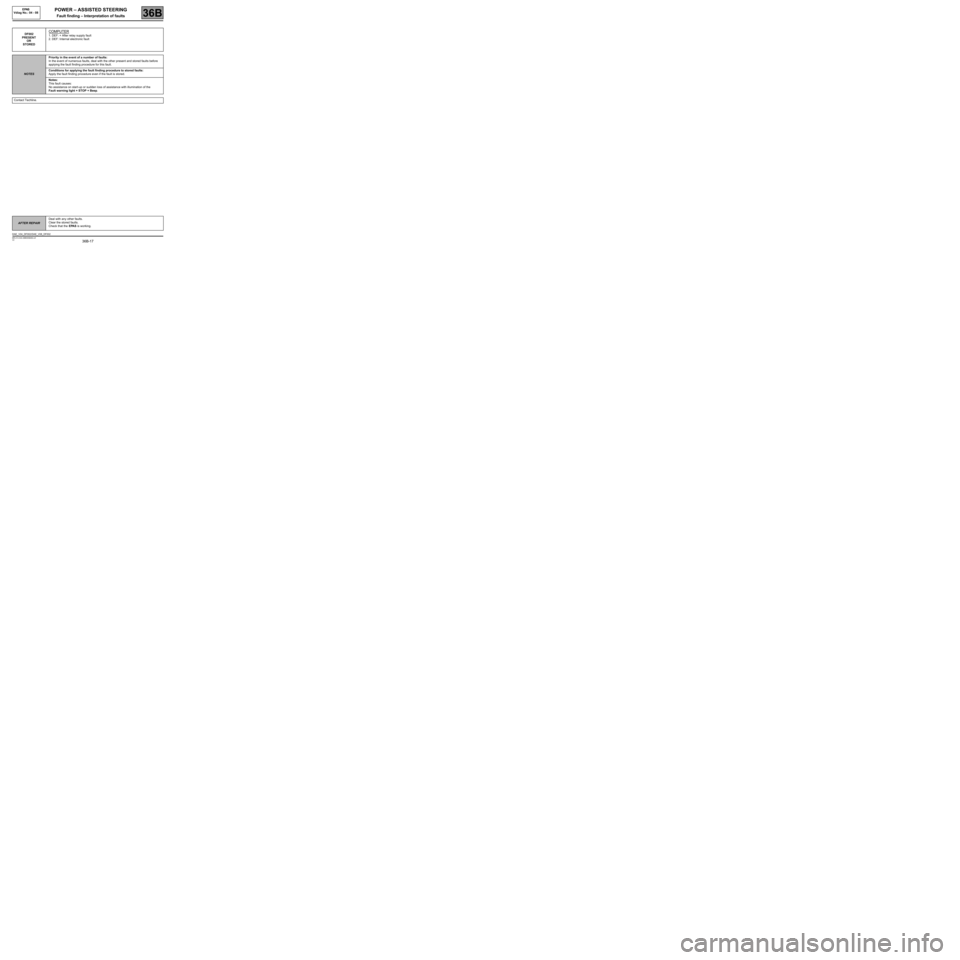
36B-17
MR-413-X44-36B000$469.mif
V2
POWER – ASSISTED STEERING
Fault finding – Interpretation of faults
EPAS
Vdiag No.: 04 - 08
36B
DF002
PRESENT
OR
STOREDCOMPUTER
1. DEF: + After relay supply fault
2. DEF: Internal electronic fault
NOTESPriority in the event of a number of faults:
In the event of numerous faults, deal with the other present and stored faults before
applying the fault finding procedure for this fault.
Conditions for applying the fault finding procedure to stored faults:
Apply the fault finding procedure even if the fault is stored.
Notes:
This fault causes:
No assistance on start-up or sudden loss of assistance with illumination of the
Fault warning light + STOP + Beep.
Contact Techline.
AFTER REPAIRDeal with any other faults.
Clear the stored faults.
Check that the EPAS is working.
DAE_V04_DF002 /DAE_V08_DF002
Page 24 of 54
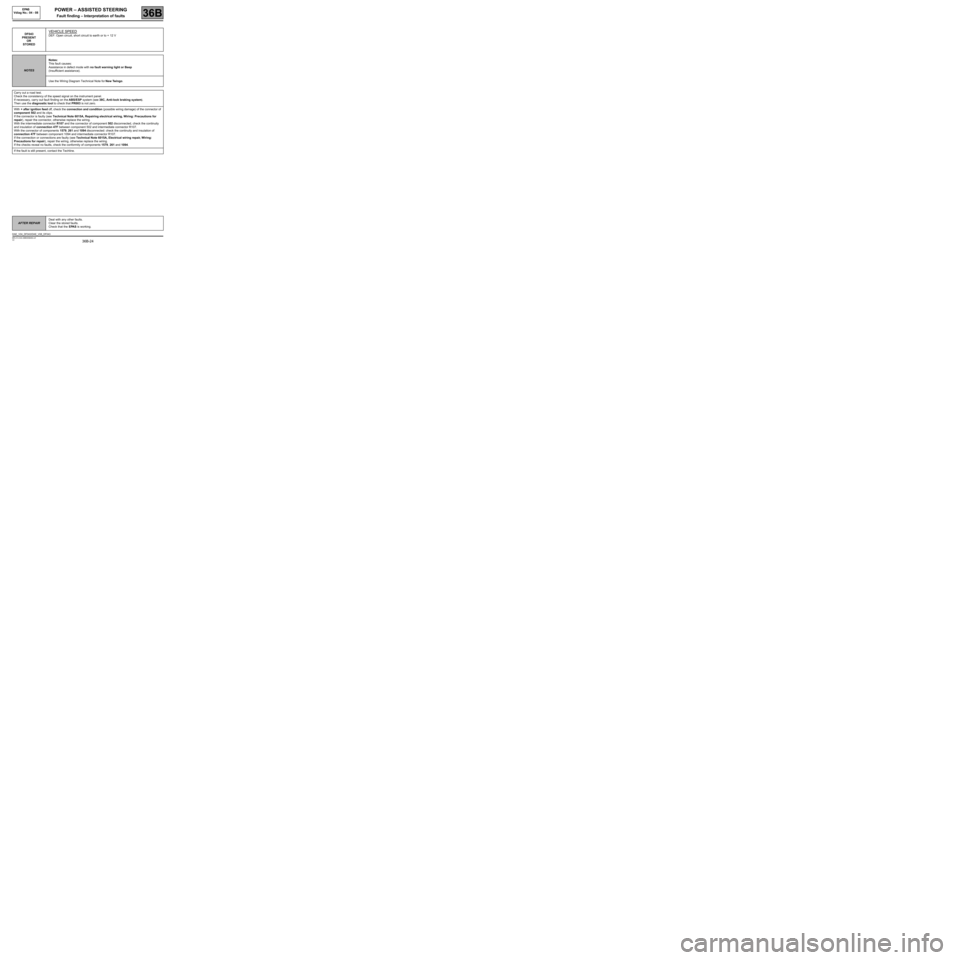
36B-24
MR-413-X44-36B000$469.mif
V2
POWER – ASSISTED STEERING
Fault finding – Interpretation of faults
EPAS
Vdiag No.: 04 - 08
36B
DF043
PRESENT
OR
STOREDVEHICLE SPEED
DEF: Open circuit, short circuit to earth or to + 12 V
NOTESNotes:
This fault causes:
Assistance in defect mode with no fault warning light or Beep
(Insufficient assistance).
Use the Wiring Diagram Technical Note for New Twingo.
Carry out a road test.
Check the consistency of the speed signal on the instrument panel.
If necessary, carry out fault finding on the ABS/ESP system (see 38C, Anti-lock braking system).
Then use the diagnostic tool to check that PR003 is not zero.
With + after ignition feed off, check the connection and condition (possible wiring damage) of the connector of
component 502 and its clips.
If the connector is faulty (see Technical Note 6015A, Repairing electrical wiring, Wiring: Precautions for
repair), repair the connector, otherwise replace the wiring.
With the intermediate connector R107 and the connector of component 502 disconnected, check the continuity
and insulation of connection 47F between component 502 and intermediate connector R107.
With the connector of components 1579, 261 and 1094 disconnected: check the continuity and insulation of
connection 47F between component 1094 and intermediate connector R107.
If the connection or connections are faulty (see Technical Note 6015A, Electrical wiring repair, Wiring:
Precautions for repair), repair the wiring, otherwise replace the wiring.
If the checks reveal no faults, check the conformity of components 1579, 261 and 1094.
If the fault is still present, contact the Techline.
AFTER REPAIRDeal with any other faults.
Clear the stored faults.
Check that the EPAS is working.
DAE_V04_DF043/DAE_V08_DF043
Page 37 of 54
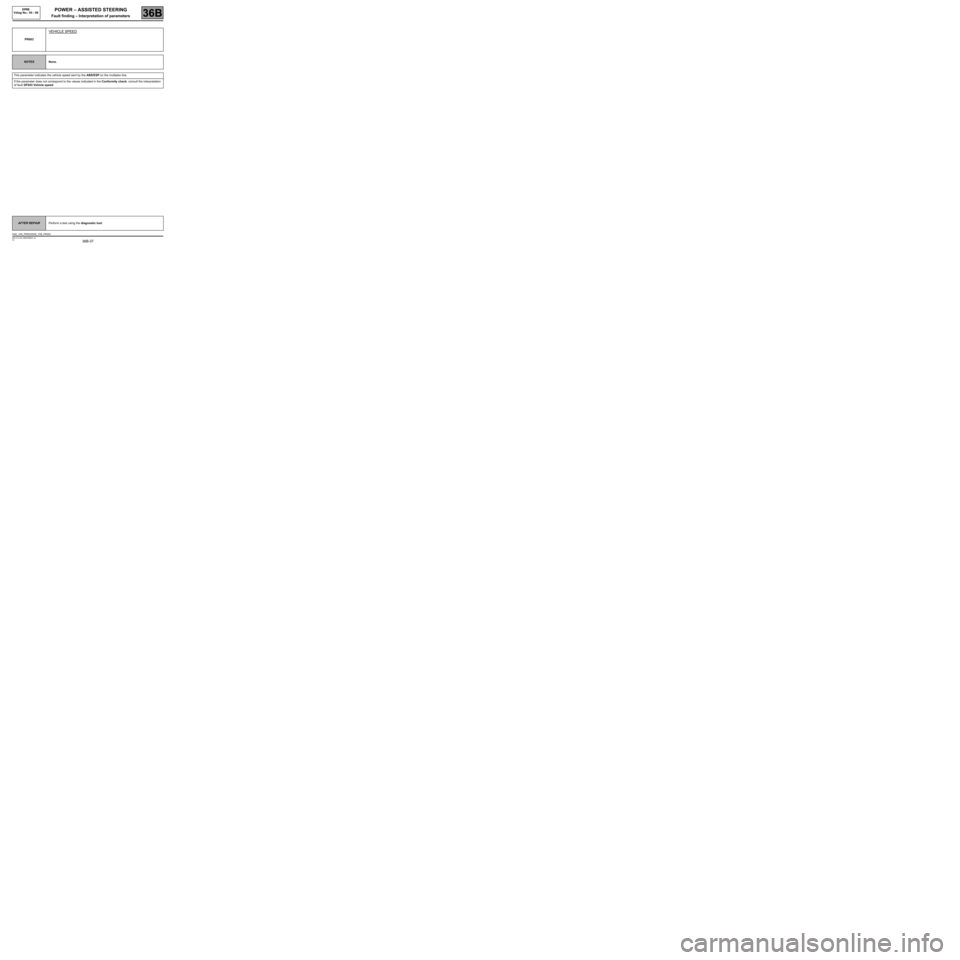
36B-37
MR-413-X44-36B000$804.mif
V2
POWER – ASSISTED STEERING
Fault finding – Interpretation of parameters
EPAS
Vdiag No.: 04 - 08
36B
PR003
VEHICLE SPEED
NOTESNone.
This parameter indicates the vehicle speed sent by the ABS/ESP on the multiplex line.
If the parameter does not correspond to the values indicated in the Conformity check, consult the interpretation
of fault DF043 Vehicle speed.
AFTER REPAIRPerform a test using the diagnostic tool.
DAE_V04_PR003/DAE_V08_PR003
Page 38 of 54
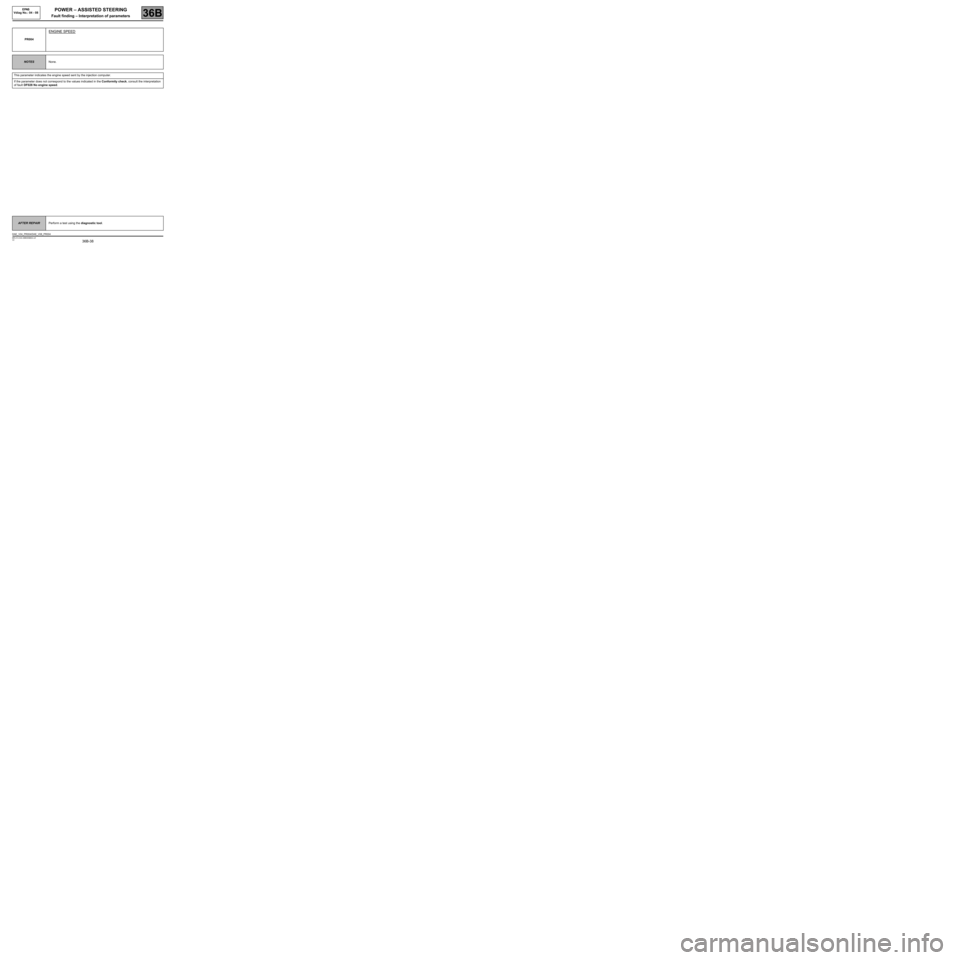
36B-38
MR-413-X44-36B000$804.mif
V2
POWER – ASSISTED STEERING
Fault finding – Interpretation of parameters
EPAS
Vdiag No.: 04 - 08
36B
PR004
ENGINE SPEED
NOTESNone.
This parameter indicates the engine speed sent by the injection computer.
If the parameter does not correspond to the values indicated in the Conformity check, consult the interpretation
of fault DF028 No engine speed.
AFTER REPAIRPerform a test using the diagnostic tool.
DAE_V04_PR004/DAE_V08_PR004
Page 39 of 54
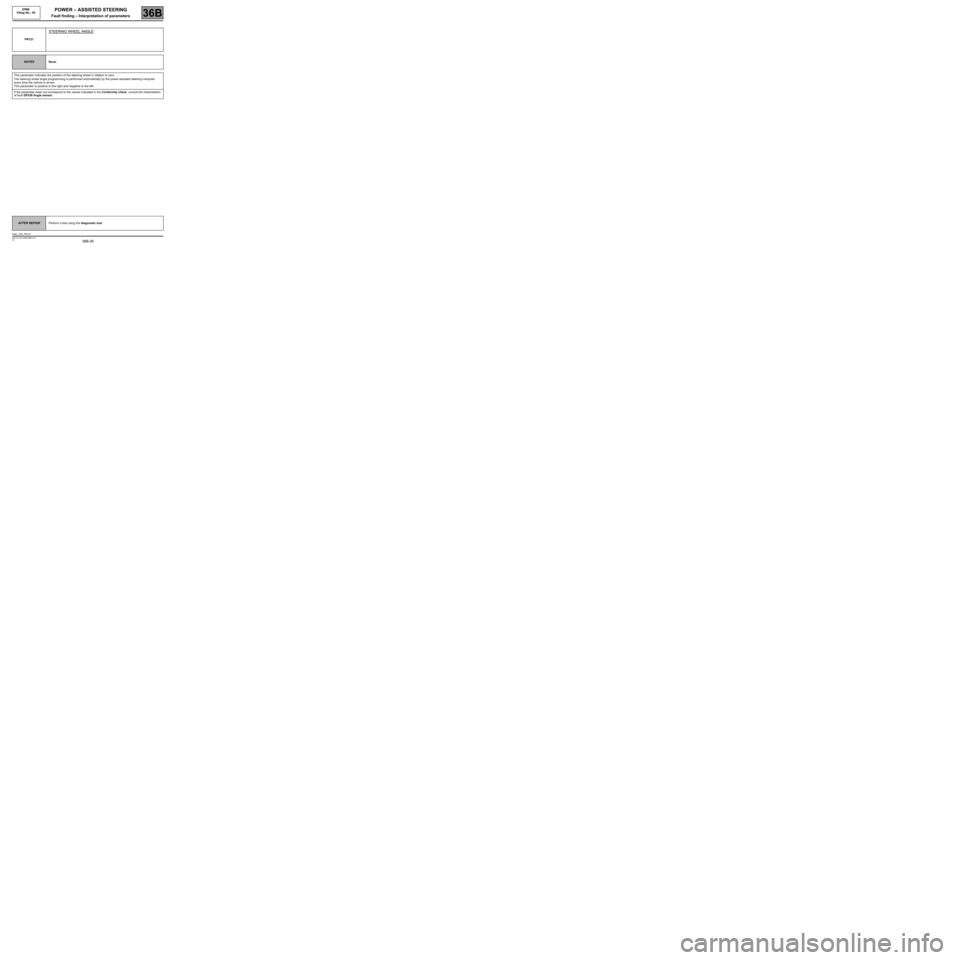
36B-39
MR-413-X44-36B000$804.mif
V2
POWER – ASSISTED STEERING
Fault finding – Interpretation of parameters36B
EPAS
Vdiag No.: 04
PR121
STEERING WHEEL ANGLE
NOTESNone.
This parameter indicates the position of the steering wheel in relation to zero.
The steering wheel angle programming is performed automatically by the power-assisted steering computer
every time the vehicle is driven.
This parameter is positive to the right and negative to the left.
If the parameter does not correspond to the values indicated in the Conformity check, consult the interpretation
of fault DF038 Angle sensor.
AFTER REPAIRPerform a test using the diagnostic tool.
DAE_V04_PR121
Page 44 of 54
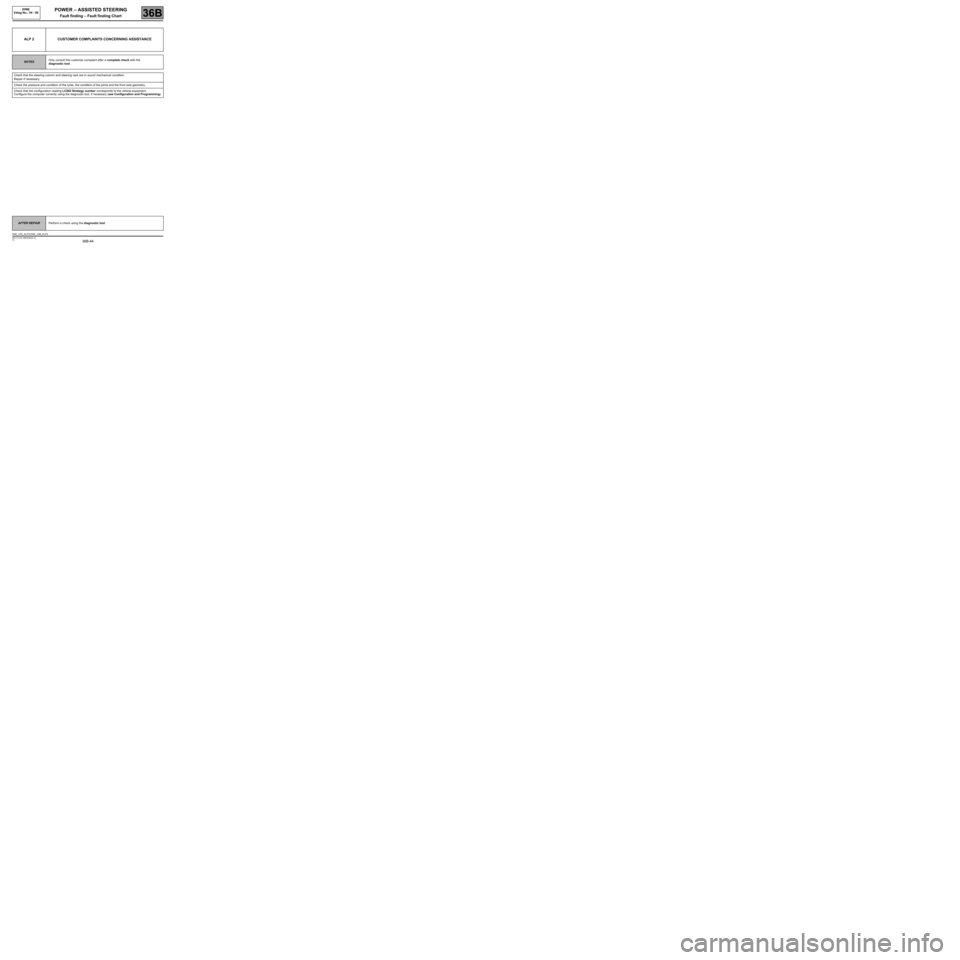
36B-44
MR-413-X44-36B000$938.mif
V2
POWER – ASSISTED STEERING
Fault finding – Fault finding Chart
EPAS
Vdiag No.: 04 - 08
36B
ALP 2 CUSTOMER COMPLAINTS CONCERNING ASSISTANCE
NOTESOnly consult this customer complaint after a complete check with the
diagnostic tool.
Check that the steering column and steering rack are in sound mechanical condition.
Repair if necessary.
Check the pressure and condition of the tyres, the condition of the joints and the front axle geometry.
Check that the configuration reading LC002 Strategy number corresponds to the vehicle equipment.
Configure the computer correctly using the diagnostic tool, if necessary (see Configuration and Programming).
AFTER REPAIRPerform a check using the diagnostic tool.
DAE_V04_ALP2/ DAE_V08_ALP2
Page 49 of 54
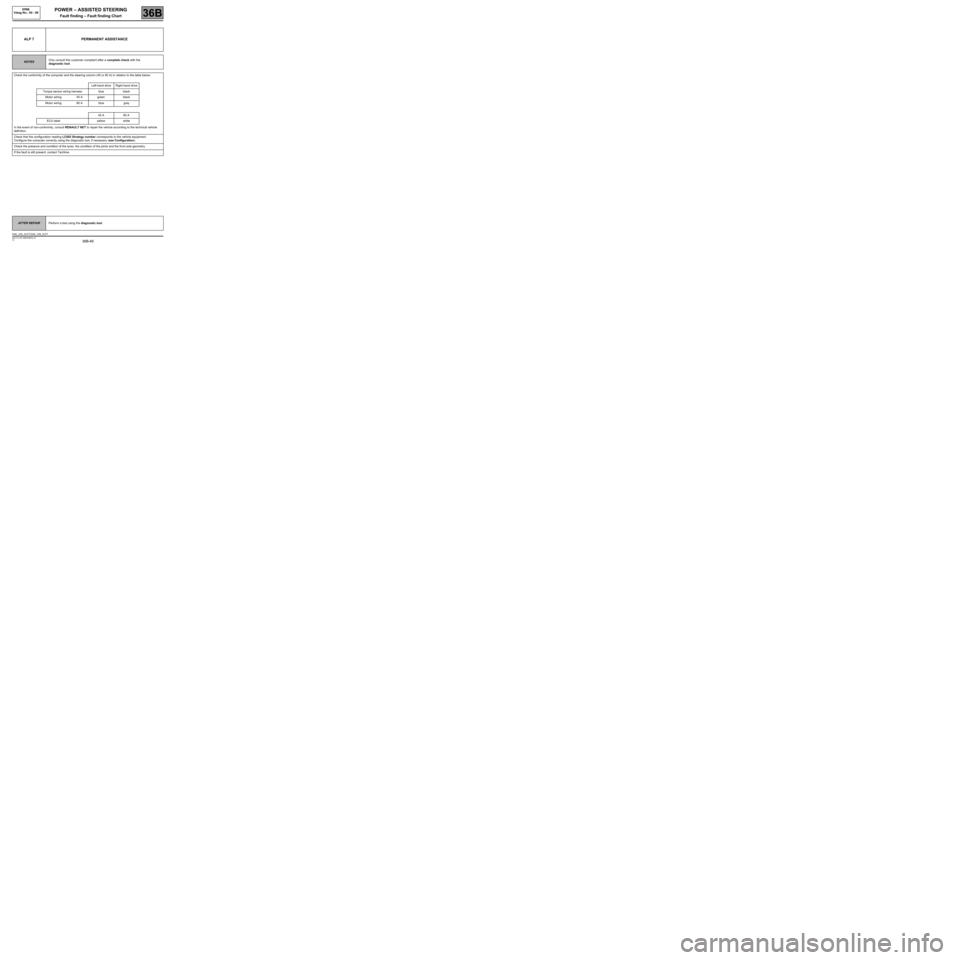
36B-49
MR-413-X44-36B000$938.mif
V2
POWER – ASSISTED STEERING
Fault finding – Fault finding Chart
EPAS
Vdiag No.: 04 - 08
36B
ALP 7 PERMANENT ASSISTANCE
NOTESOnly consult this customer complaint after a complete check with the
diagnostic tool.
Check the conformity of the computer and the steering column (45 or 60 A) in relation to the table below:
Left-hand drive Right-hand drive
Torque sensor wiring harness blue black
Motor wiring 45 A green black
Motor wiring 60 A blue grey
45 A 60 A
ECU label yellow white
In the event of non-conformity, consult RENAULT NET to repair the vehicle according to the technical vehicle
definition.
Check that the configuration reading LC002 Strategy number corresponds to the vehicle equipment.
Configure the computer correctly using the diagnostic tool, if necessary (see Configuration).
Check the pressure and condition of the tyres, the condition of the joints and the front axle geometry.
If the fault is still present, contact Techline.
AFTER REPAIRPerform a test using the diagnostic tool.
DAE_V04_ALP7/ DAE_V08_ALP7