RENAULT TWINGO RS 2009 2.G Chasiss ABS Repair Manual
Manufacturer: RENAULT, Model Year: 2009, Model line: TWINGO RS, Model: RENAULT TWINGO RS 2009 2.GPages: 76
Page 61 of 76
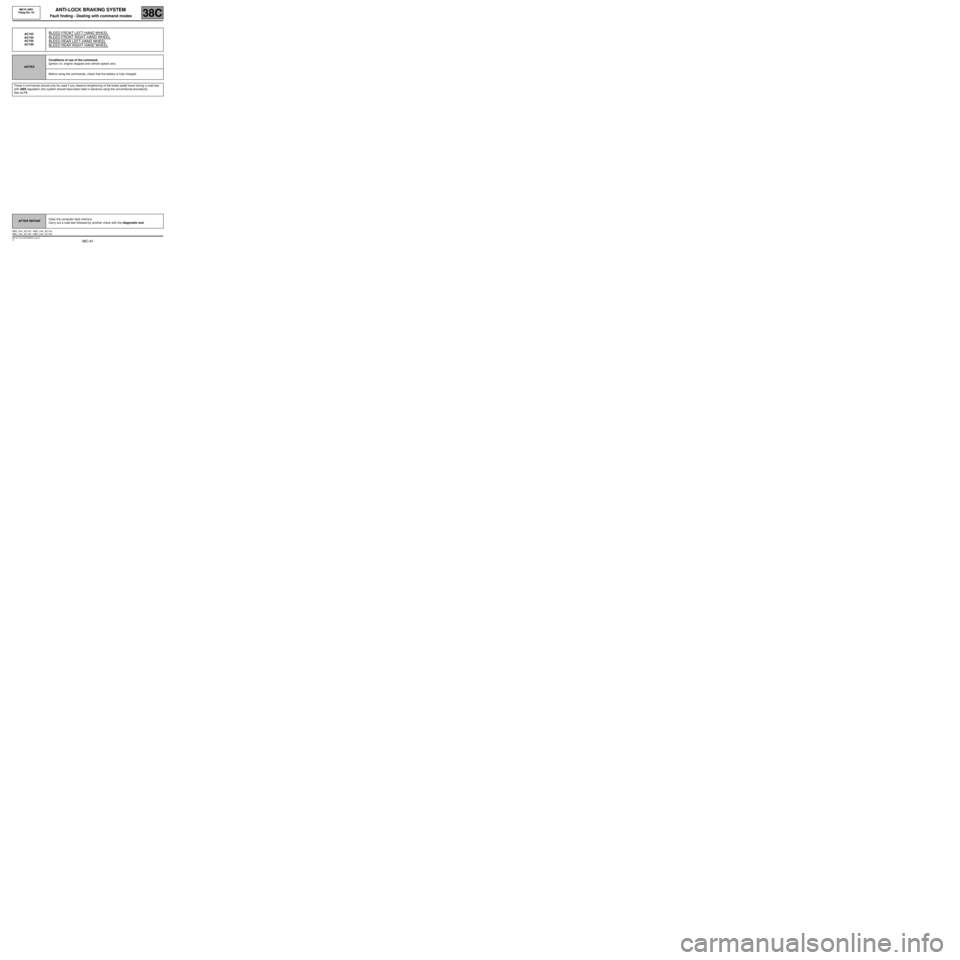
38C-61
MR-413-X44-38C000$846_eng.mif
V1
ANTI-LOCK BRAKING SYSTEM
Fault finding - Dealing with command modes
MK70 ABS
Vdiag No: 04
38C
AC153
AC154
AC155
AC156BLEED FRONT LEFT-HAND WHEEL
BLEED FRONT RIGHT-HAND WHEEL
BLEED REAR LEFT-HAND WHEEL
BLEED REAR RIGHT-HAND WHEEL
NOTESConditions of use of the command.
Ignition on, engine stopped and vehicle speed zero.
Before using the commands, check that the battery is fully charged.
These 4 commands should only be used if you observe lengthening of the brake pedal travel during a road test
with ABS regulation (the system should have been bled in advance using the conventional procedure).
See ALP8.
AFTER REPAIRClear the computer fault memory.
Carry out a road test followed by another check with the diagnostic tool.
ABS_V04_AC153 / ABS_V04_AC154
ABS_V04_AC155 / ABS_V04_AC156
Page 62 of 76
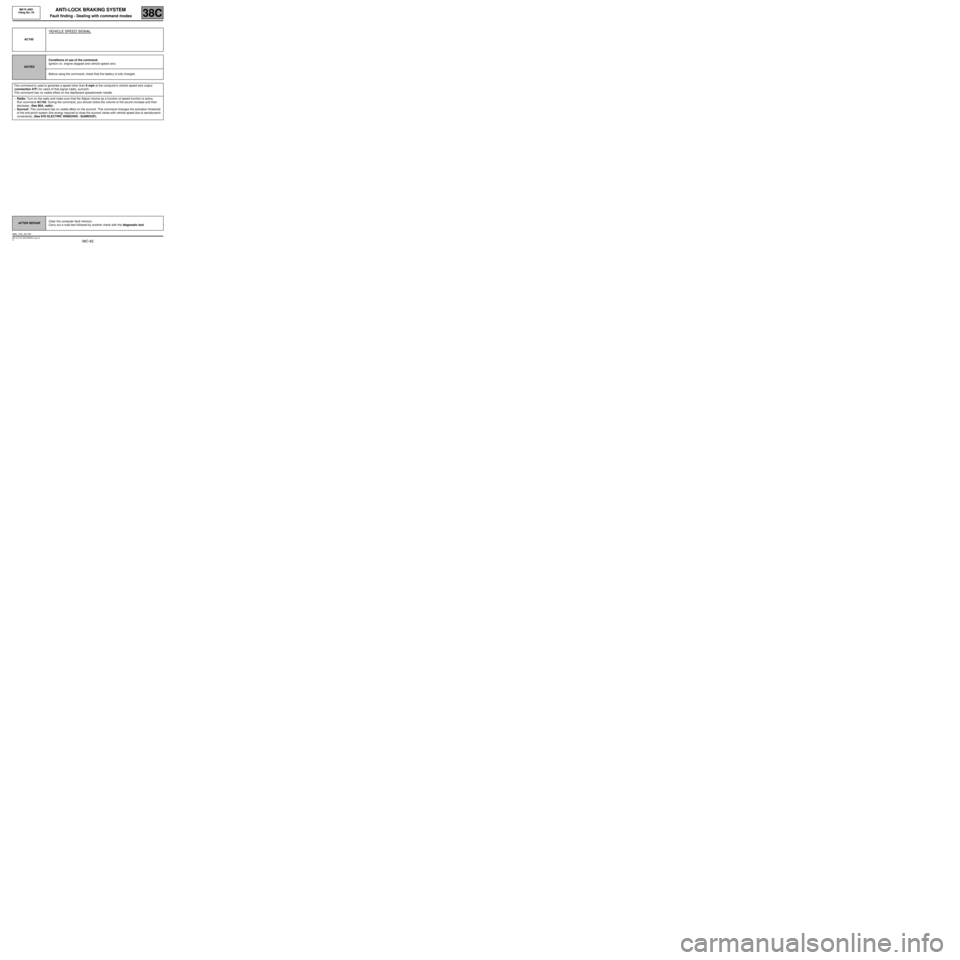
38C-62
MR-413-X44-38C000$846_eng.mif
V1
ANTI-LOCK BRAKING SYSTEM
Fault finding - Dealing with command modes
MK70 ABS
Vdiag No: 04
38C
AC195
VEHICLE SPEED SIGNAL
NOTESConditions of use of the command.
Ignition on, engine stopped and vehicle speed zero.
Before using the command, check that the battery is fully charged.
This command is used to generate a speed other than 0 mph at the computer's vehicle speed wire output
(connection 47F) for users of that signal (radio, sunroof).
This command has no visible effect on the dashboard speedometer needle.
–Radio: Turn on the radio and make sure that the Adjust volume as a function of speed function is active.
Run command AC195. During the command, you should notice the volume of the sound increase and then
decrease. (See 86A, radio).
–Sunroof: This command has no visible effect on the sunroof. This command changes the activation threshold
of the anti-pinch system (the energy required to close the sunroof varies with vehicle speed due to aerodynamic
constraints). (See 87D ELECTRIC WINDOWS - SUNROOF).
AFTER REPAIRClear the computer fault memory.
Carry out a road test followed by another check with the diagnostic tool.
ABS_V04_AC195
Page 63 of 76
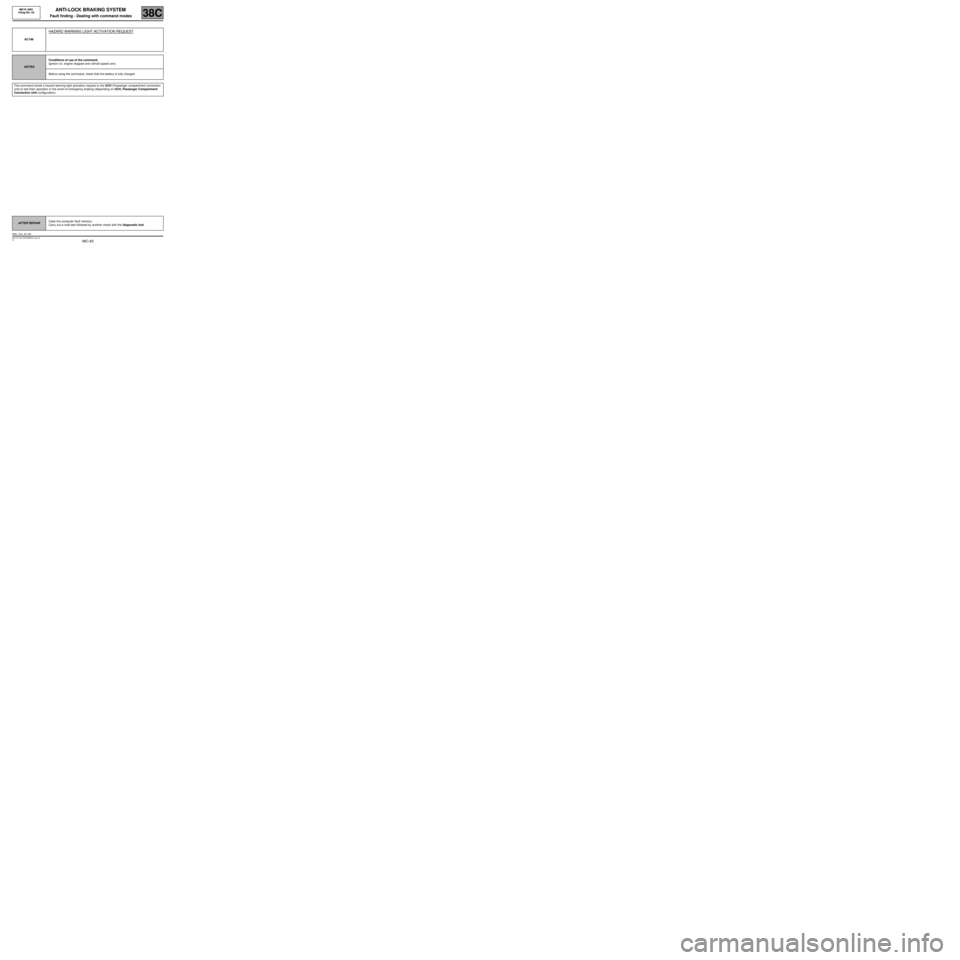
38C-63
MR-413-X44-38C000$846_eng.mif
V1
ANTI-LOCK BRAKING SYSTEM
Fault finding - Dealing with command modes
MK70 ABS
Vdiag No: 04
38C
AC196
HAZARD WARNING LIGHT ACTIVATION REQUEST
NOTESConditions of use of the command.
Ignition on, engine stopped and vehicle speed zero.
Before using the command, check that the battery is fully charged.
This command sends a hazard warning light activation request to the UCH (Passenger compartment connection
unit) to test their operation in the event of emergency braking (depending on UCH, Passenger Compartment
Connection Unit configuration).
AFTER REPAIRClear the computer fault memory.
Carry out a road test followed by another check with the diagnostic tool.
ABS_V04_AC196
Page 64 of 76
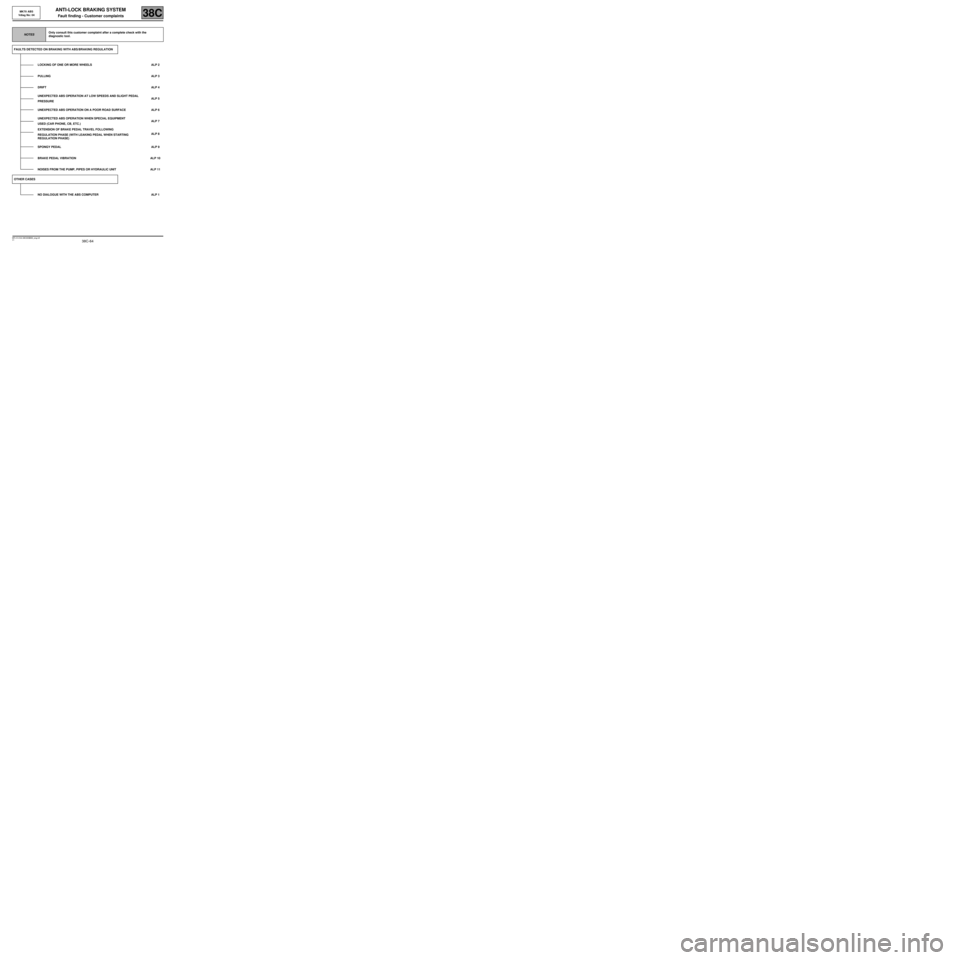
38C-64
MR-413-X44-38C000$893_eng.mif
V1
38C
ANTI-LOCK BRAKING SYSTEM
Fault finding - Customer complaints
NOTESOnly consult this customer complaint after a complete check with the
diagnostic tool.
FAULTS DETECTED ON BRAKING WITH ABS/BRAKING REGULATION
LOCKING OF ONE OR MORE WHEELS ALP 2
PULLING ALP 3
DRIFT ALP 4
UNEXPECTED ABS OPERATION AT LOW SPEEDS AND SLIGHT PEDAL
PRESSURE ALP 5
UNEXPECTED ABS OPERATION ON A POOR ROAD SURFACE ALP 6
UNEXPECTED ABS OPERATION WHEN SPECIAL EQUIPMENT
USED (CAR PHONE, CB, ETC.) ALP 7
EXTENSION OF BRAKE PEDAL TRAVEL FOLLOWING
REGULATION PHASE (WITH LEAKING PEDAL WHEN STARTING
REGULATION PHASE)ALP 8
SPONGY PEDAL ALP 9
BRAKE PEDAL VIBRATION ALP 10
NOISES FROM THE PUMP, PIPES OR HYDRAULIC UNIT ALP 11
OTHER CASES
NO DIALOGUE WITH THE ABS COMPUTER ALP 1
MK70 ABS
Vdiag No: 04
MR-413-X44-38C000$893_eng.mif
Page 65 of 76
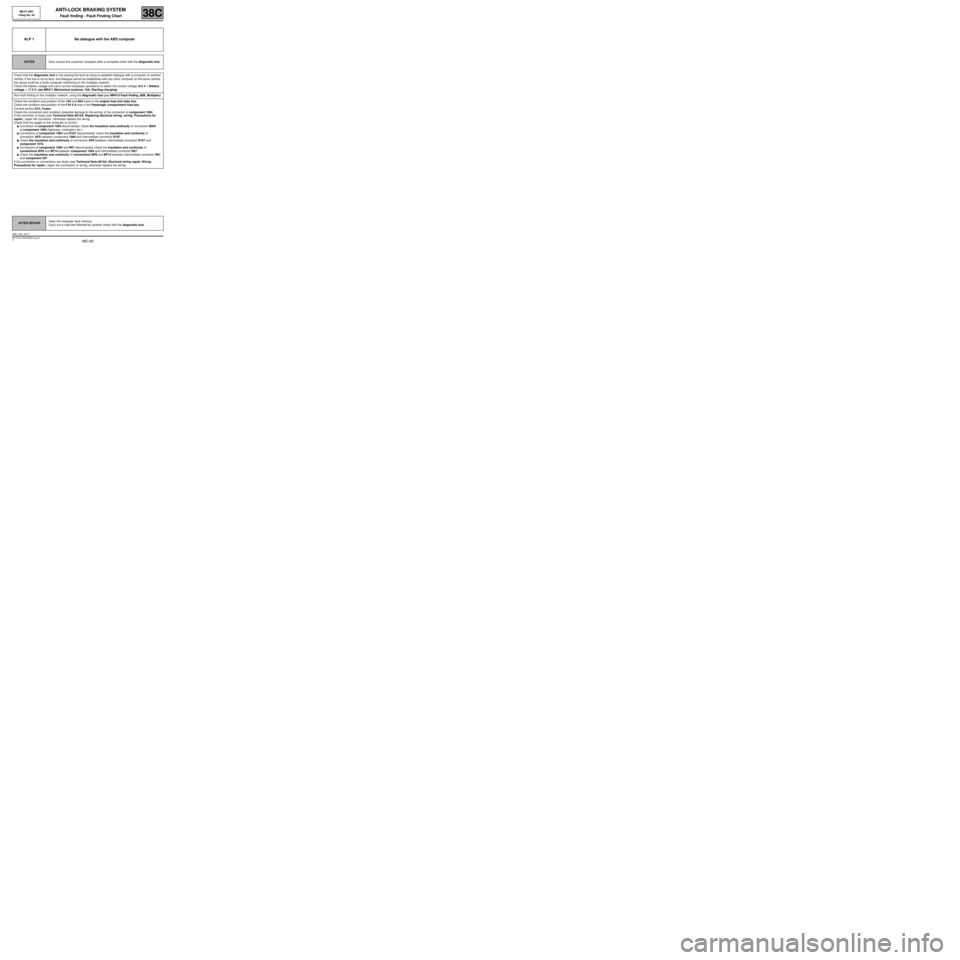
38C-65
MR-413-X44-38C000$940_eng.mif
V1
38C
ANTI-LOCK BRAKING SYSTEM
Fault finding - Fault Finding Chart
ALP 1 No dialogue with the ABS computer
NOTESOnly consult this customer complaint after a complete check with the diagnostic tool.
Check that the diagnostic tool is not causing the fault by trying to establish dialogue with a computer on another
vehicle. If the tool is not at fault, and dialogue cannot be established with any other computer on the same vehicle,
the cause could be a faulty computer interfering on the multiplex network.
Check the battery voltage and carry out the necessary operations to obtain the correct voltage (9.5 V < Battery
voltage < 17.5 V, see MR411 Mechanical systems, 16A, Starting-charging).
Run fault finding on the multiplex network, using the diagnostic tool (see MR413 Fault finding, 88B, Multiplex).
Check the condition and position of the 15A and 20A fuses in the engine fuse and relay box.
Check the condition and position of the F10 5 A fuse in the Passenger compartment fuse box.
Consult section 81C, Fuses.
Check the connection and condition (possible damage to the wiring) of the connector of component 1094.
If the connector is faulty (see Technical Note 6015A, Repairing electrical wiring, wiring: Precautions for
repair), repair the connector, otherwise replace the wiring.
Check that the supply to the computer is correct:
●Connector of component 1094 disconnected, check the insulation and continuity of connection MAH
of component 1094 (tightness, oxidisation etc.).
●Connectors of component 1094 and R107 disconnected, check the insulation and continuity of
connection AP5 between component 1094 and intermediate connector R107.
●Check the insulation and continuity of connection AP5 between intermediate connector R107 and
component 1016.
●Connectors of component 1094 and R67 disconnected, check the insulation and continuity of
connections BP8 and BP14 between component 1094 and intermediate connector R67.
●Check the insulation and continuity of connections BP8 and BP14 between intermediate connector R67
and component 597.
If the connection or connections are faulty (see Technical Note 6015A, Electrical wiring repair, Wiring:
Precautions for repair), repair the connectors or wiring, otherwise replace the wiring.
AFTER REPAIRClear the computer fault memory.
Carry out a road test followed by another check with the diagnostic tool.
ABS_V04_ALP1
MK70 ABS
Vdiag No: 04
MR-413-X44-38C000$940_eng.mif
Page 66 of 76
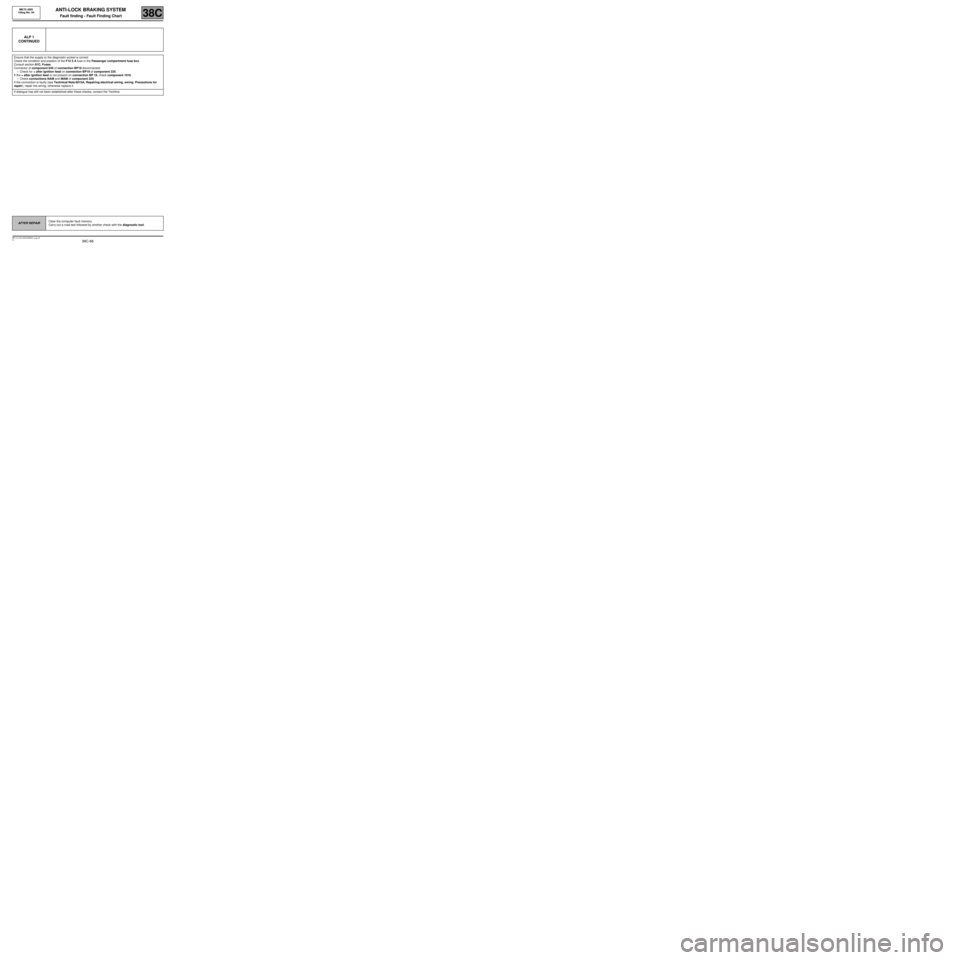
38C-66
MR-413-X44-38C000$940_eng.mif
V1
ANTI-LOCK BRAKING SYSTEM
Fault finding - Fault Finding Chart
MK70 ABS
Vdiag No: 04
38C
ALP 1
CONTINUED
Ensure that the supply to the diagnostic socket is correct:
Check the condition and position of the F12 5 A fuse in the Passenger compartment fuse box.
Consult section 81C, Fuses.
Connector of component 645 of connection BP19 disconnected:
–Check for + after ignition feed on connection BP19 of component 225.
If the + after ignition feed is not present on connection BP 19, check component 1016.
–Check connections NAM and MAM of component 225.
If the connection is faulty (see Technical Note 6015A, Repairing electrical wiring, wiring: Precautions for
repair), repair the wiring, otherwise replace it.
If dialogue has still not been established after these checks, contact the Techline.
AFTER REPAIRClear the computer fault memory.
Carry out a road test followed by another check with the diagnostic tool.
Page 67 of 76
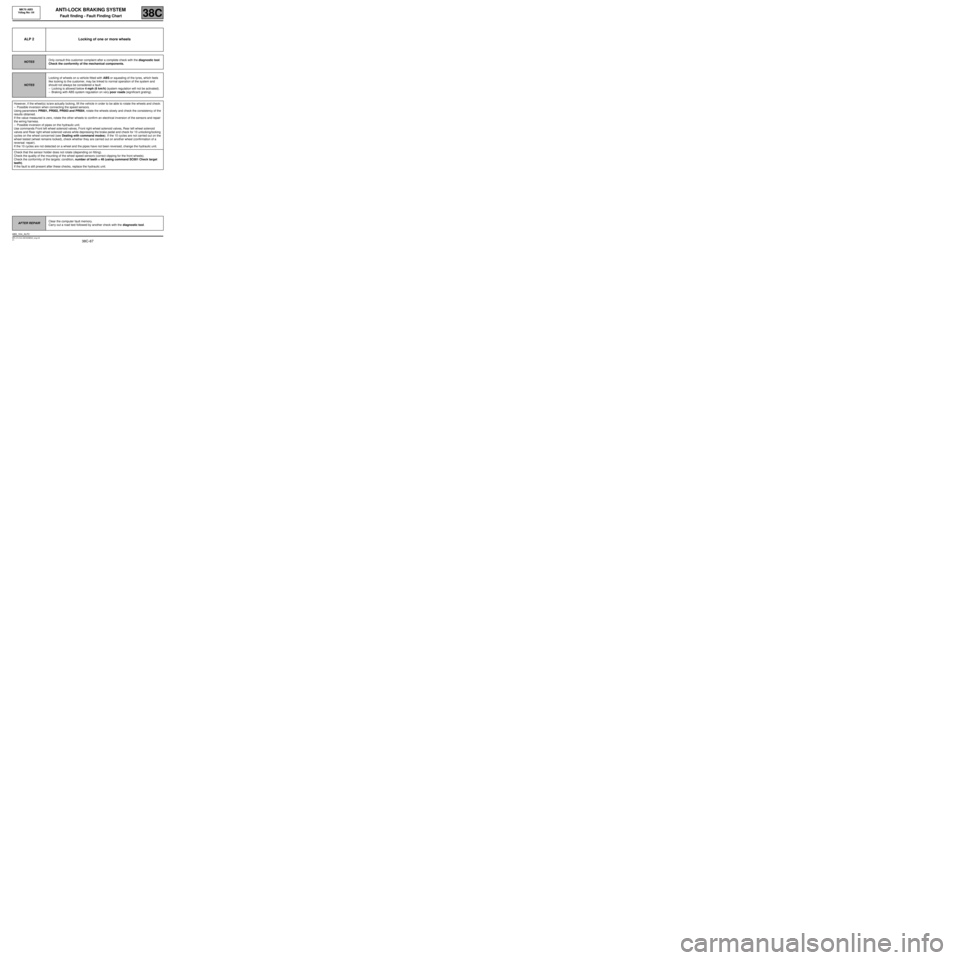
38C-67
MR-413-X44-38C000$940_eng.mif
V1
ANTI-LOCK BRAKING SYSTEM
Fault finding - Fault Finding Chart
MK70 ABS
Vdiag No: 04
38C
ALP 2 Locking of one or more wheels
NOTESOnly consult this customer complaint after a complete check with the diagnostic tool.
Check the conformity of the mechanical components.
NOTESLocking of wheels on a vehicle fitted with ABS or squealing of the tyres, which feels
like locking to the customer, may be linked to normal operation of the system and
should not always be considered a fault:
–Locking is allowed below 4 mph (6 km/h) (system regulation will not be activated).
–Braking with ABS system regulation on very poor roads (significant grating).
However, if the wheel(s) is/are actually locking, lift the vehicle in order to be able to rotate the wheels and check:
–Possible inversion when connecting the speed sensors.
Using parameters PR001, PR002, PR003 and PR004, rotate the wheels slowly and check the consistency of the
results obtained.
If the value measured is zero, rotate the other wheels to confirm an electrical inversion of the sensors and repair
the wiring harness.
–Possible inversion of pipes on the hydraulic unit.
Use commands Front left wheel solenoid valves, Front right wheel solenoid valves, Rear left wheel solenoid
valves and Rear right wheel solenoid valves while depressing the brake pedal and check for 10 unlocking/locking
cycles on the wheel concerned (see Dealing with command modes). If the 10 cycles are not carried out on the
wheel tested (wheel remains locked), check whether they are carried out on another wheel (confirmation of a
reversal: repair).
If the 10 cycles are not detected on a wheel and the pipes have not been reversed, change the hydraulic unit.
Check that the sensor holder does not rotate (depending on fitting).
Check the quality of the mounting of the wheel speed sensors (correct clipping for the front wheels).
Check the conformity of the targets: condition, number of teeth = 48 (using command SC001 Check target
teeth).
If the fault is still present after these checks, replace the hydraulic unit.
AFTER REPAIRClear the computer fault memory.
Carry out a road test followed by another check with the diagnostic tool.
ABS_V04_ALP2
Page 68 of 76
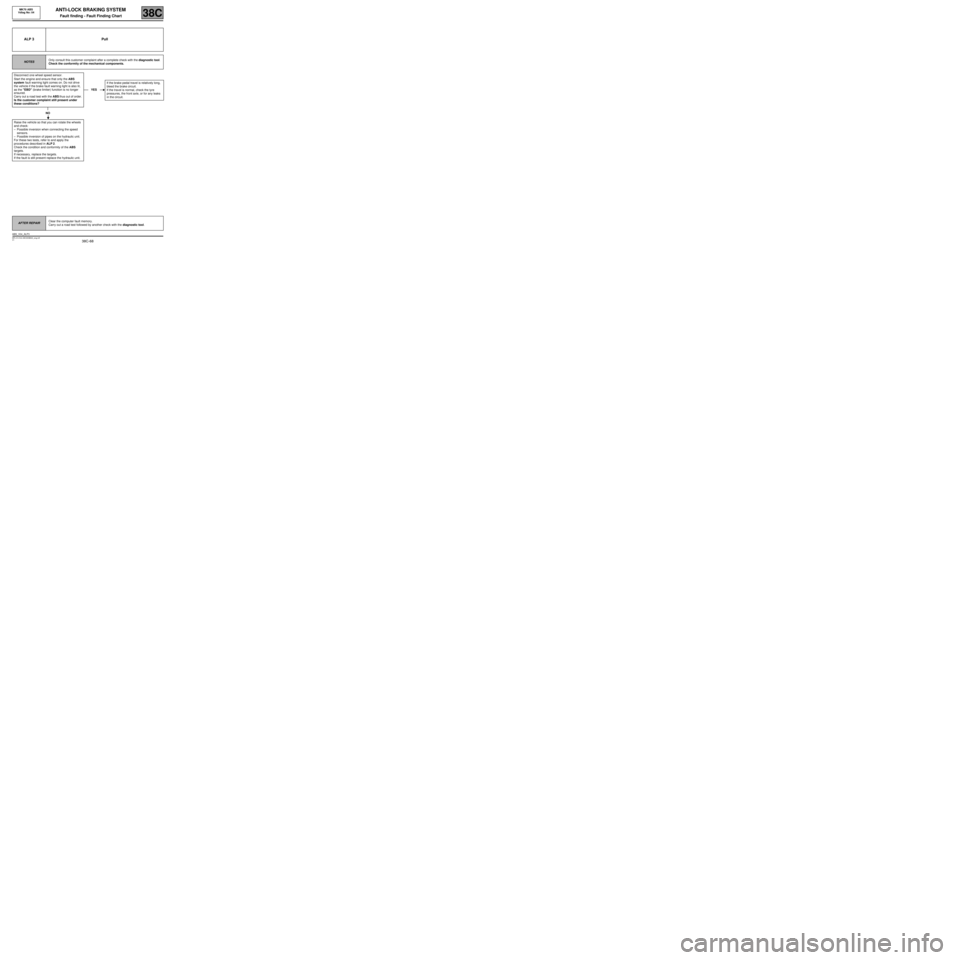
38C-68
MR-413-X44-38C000$940_eng.mif
V1
MK70 ABS
Vdiag No: 04ANTI-LOCK BRAKING SYSTEM
Fault finding - Fault Finding Chart38C
ALP 3 Pull
NOTESOnly consult this customer complaint after a complete check with the diagnostic tool.
Check the conformity of the mechanical components.
Disconnect one wheel speed sensor.
Start the engine and ensure that only the ABS
system fault warning light comes on. Do not drive
the vehicle if the brake fault warning light is also lit,
as the "EBD" (brake limiter) function is no longer
ensured.
Carry out a road test with the ABS thus out of order.
Is the customer complaint still present under
these conditions?
NO
Raise the vehicle so that you can rotate the wheels
and check:
–Possible inversion when connecting the speed
sensors.
–Possible inversion of pipes on the hydraulic unit.
For these two tests, refer to and apply the
procedures described in ALP 2.
Check the condition and conformity of the ABS
targets.
If necessary, replace the targets.
If the fault is still present replace the hydraulic unit.
YESIf the brake pedal travel is relatively long,
bleed the brake circuit.
If the travel is normal, check the tyre
pressures, the front axle, or for any leaks
in the circuit.
AFTER REPAIRClear the computer fault memory.
Carry out a road test followed by another check with the diagnostic tool.
ABS_V04_ALP3
Page 69 of 76

38C-69
MR-413-X44-38C000$940_eng.mif
V1
MK70 ABS
Vdiag No: 04ANTI-LOCK BRAKING SYSTEM
Fault finding - Fault Finding Chart38C
ALP 4 Drift
NOTESOnly consult this customer complaint after a complete check with the diagnostic tool.
Disconnect one wheel speed sensor.
Start the engine and ensure that only the ABS
system fault warning light comes on. Do not drive
the vehicle if the brake fault warning light is also lit,
as the "EBD" (brake limiter) function is no longer
ensured.
Carry out a road test with the ABS thus out of order.
Is the customer complaint still present under
these conditions?
NO
Normal behaviour linked to the system operation
during the regulation phase, mainly on surfaces with
uneven grip or which are poorly laid.
YESRoad holding fault not related to the ABS.
Check the condition of the brake linings
and that they are to specification and
check the tyre pressures, the front axle,
etc.
AFTER REPAIRClear the computer fault memory.
Carry out a road test followed by another check with the diagnostic tool.
ABS_V04_ALP4
Page 70 of 76
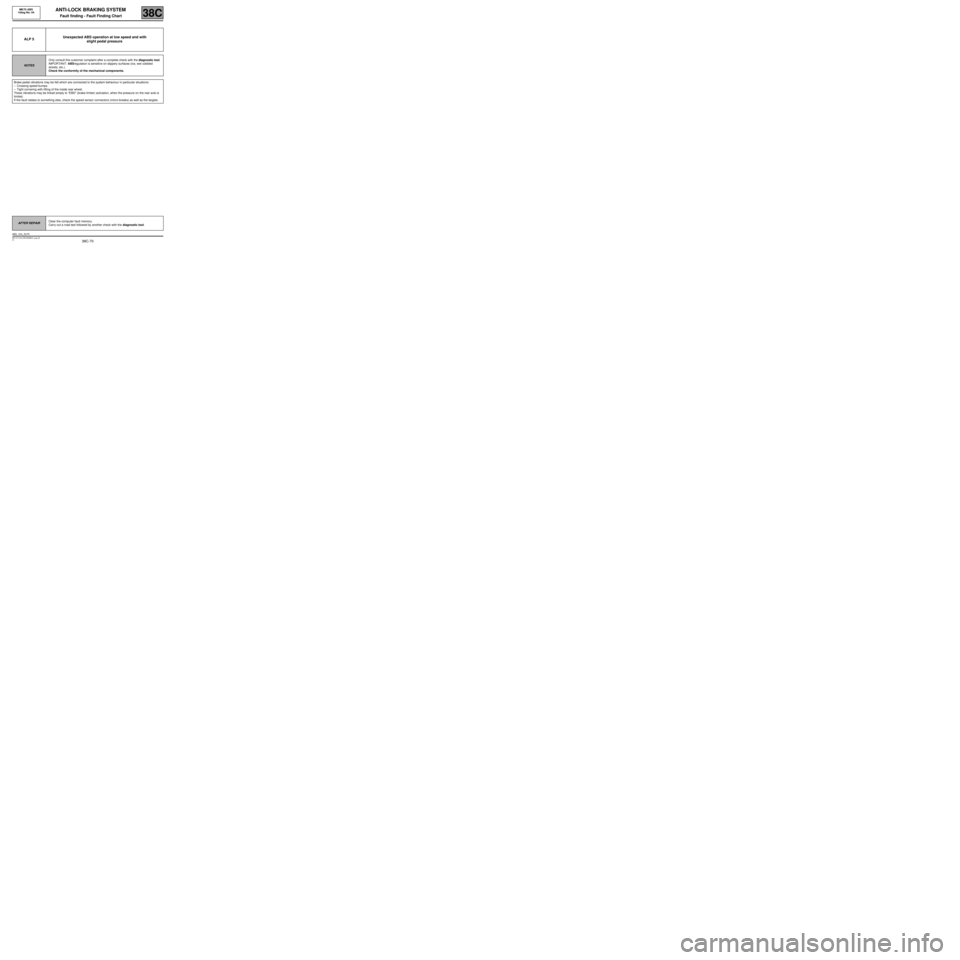
38C-70
MR-413-X44-38C000$940_eng.mif
V1
ANTI-LOCK BRAKING SYSTEM
Fault finding - Fault Finding Chart
MK70 ABS
Vdiag No: 04
38C
ALP 5Unexpected ABS operation at low speed and with
slight pedal pressure
NOTESOnly consult this customer complaint after a complete check with the diagnostic tool.
IMPORTANT: ABS regulation is sensitive on slippery surfaces (ice, wet cobbled
streets, etc.).
Check the conformity of the mechanical components.
Brake pedal vibrations may be felt which are connected to the system behaviour in particular situations:
–Crossing speed bumps.
–Tight cornering with lifting of the inside rear wheel.
These vibrations may be linked simply to "EBD" (brake limiter) activation, when the pressure on the rear axle is
limited.
If the fault relates to something else, check the speed sensor connectors (micro-breaks) as well as the targets.
AFTER REPAIRClear the computer fault memory.
Carry out a road test followed by another check with the diagnostic tool.
ABS_V04_ALP5