sensor SSANGYONG MUSSO 1998 Workshop Manual Online
[x] Cancel search | Manufacturer: SSANGYONG, Model Year: 1998, Model line: MUSSO, Model: SSANGYONG MUSSO 1998Pages: 1463, PDF Size: 19.88 MB
Page 719 of 1463
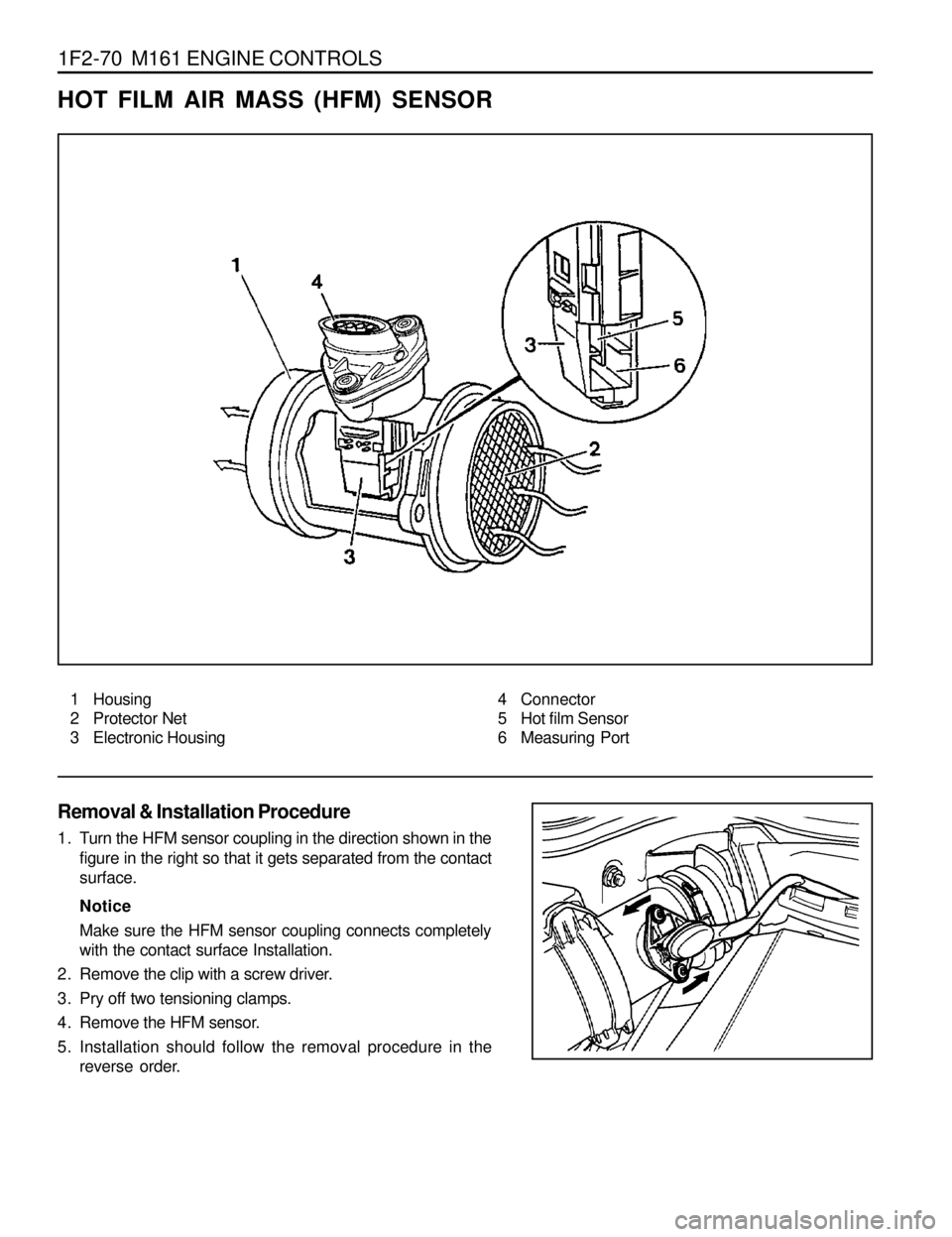
1F2-70 M161 ENGINE CONTROLS
HOT FILM AIR MASS (HFM) SENSOR
1 Housing
2 Protector Net
3 Electronic Housing
Removal & Installation Procedure
1. Turn the HFM sensor coupling in the direction shown in the
figure in the right so that it gets separated from the contact
surface.
Notice
Make sure the HFM sensor coupling connects completely
with the contact surface Installation.
2. Remove the clip with a screw driver.
3. Pry off two tensioning clamps.
4. Remove the HFM sensor.
5. Installation should follow the removal procedure in the
reverse order.4 Connector
5 Hot film Sensor
6 Measuring Port
Page 720 of 1463
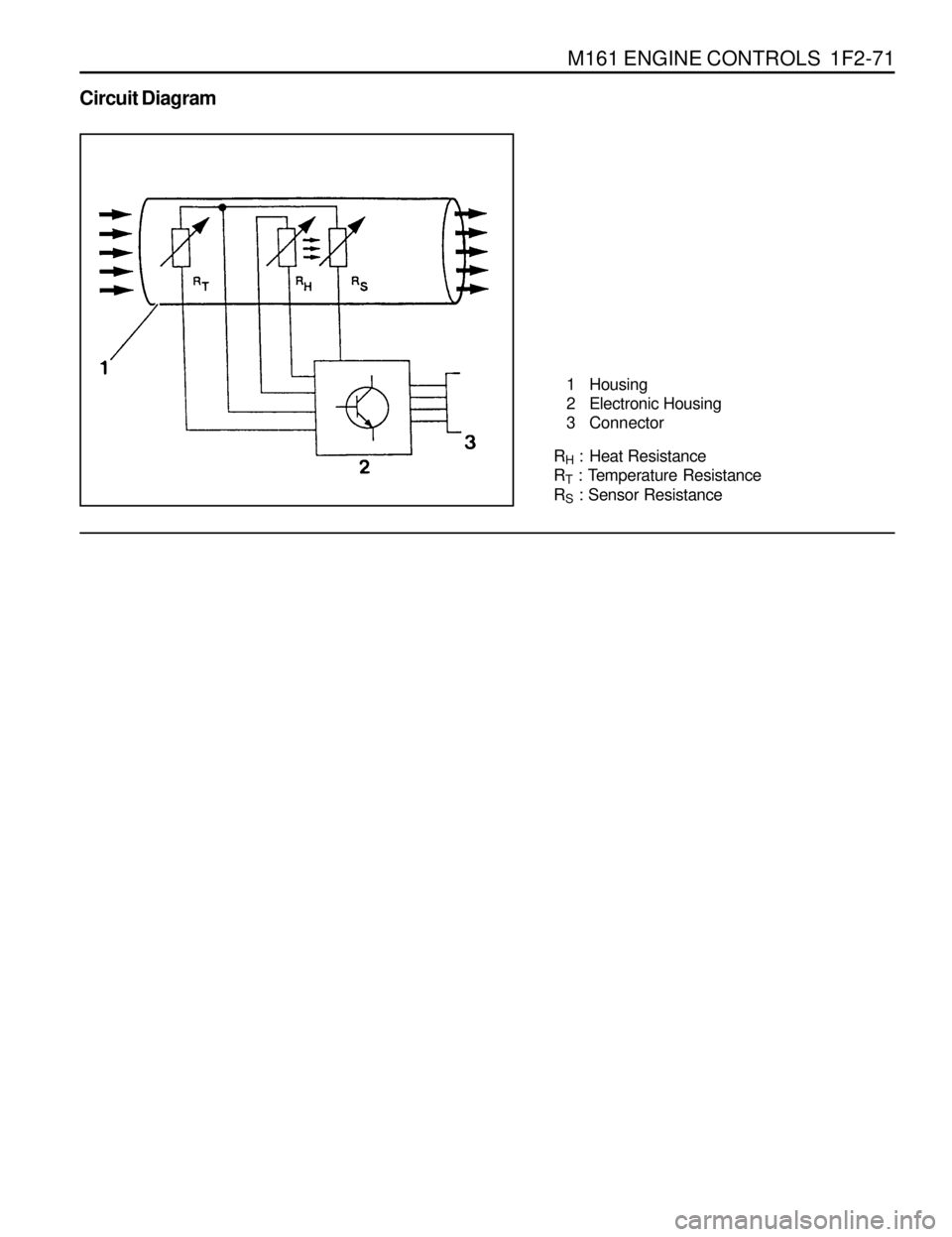
M161 ENGINE CONTROLS 1F2-71
Circuit Diagram
1 Housing
2 Electronic Housing
3 Connector
R
H : Heat Resistance
R
T : Temperature Resistance
R
S : Sensor Resistance
Page 721 of 1463
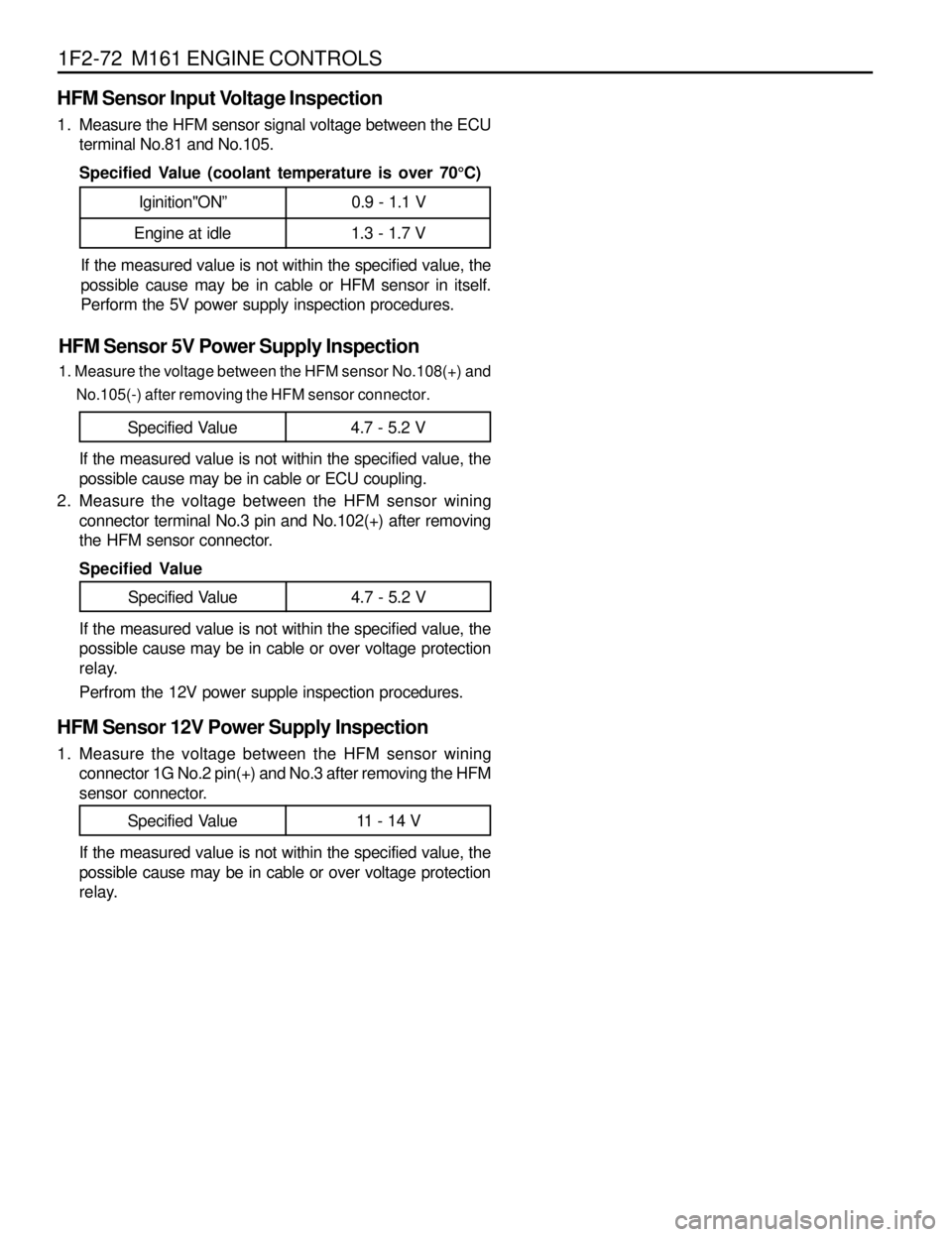
1F2-72 M161 ENGINE CONTROLS
If the measured value is not within the specified value, the
possible cause may be in cable or HFM sensor in itself.
Perform the 5V power supply inspection procedures.
HFM Sensor 5V Power Supply Inspection
1. Measure the voltage between the HFM sensor No.108(+) and
No.105(-) after removing the HFM sensor connector.
HFM Sensor Input Voltage Inspection
1. Measure the HFM sensor signal voltage between the ECU
terminal No.81 and No.105.
Specified Value (coolant temperature is over 70°C)
If the measured value is not within the specified value, the
possible cause may be in cable or ECU coupling.
Iginition"ON” 0.9 - 1.1 V
Engine at idle 1.3 - 1.7 V
Specified Value 4.7 - 5.2 V
2. Measure the voltage between the HFM sensor wining
connector terminal No.3 pin and No.102(+) after removing
the HFM sensor connector.
Specified Value
If the measured value is not within the specified value, the
possible cause may be in cable or over voltage protection
relay.
Perfrom the 12V power supple inspection procedures.
Specified Value 4.7 - 5.2 V
HFM Sensor 12V Power Supply Inspection
1. Measure the voltage between the HFM sensor wining
connector 1G No.2 pin(+) and No.3 after removing the HFM
sensor connector.
If the measured value is not within the specified value, the
possible cause may be in cable or over voltage protection
relay.
Specified Value 11 - 14 V
Page 722 of 1463
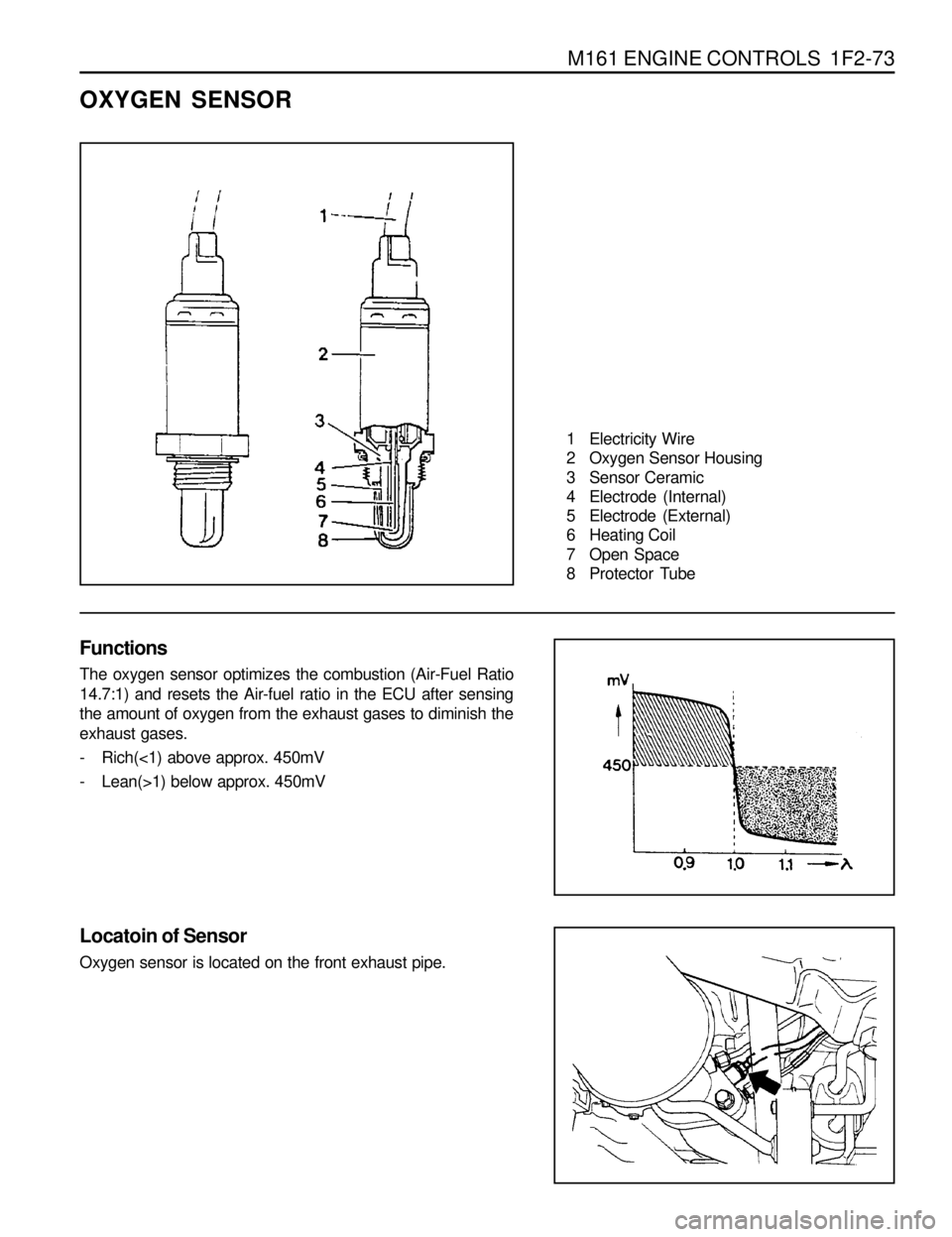
M161 ENGINE CONTROLS 1F2-73
OXYGEN SENSOR
1 Electricity Wire
2 Oxygen Sensor Housing
3 Sensor Ceramic
4 Electrode (Internal)
5 Electrode (External)
6 Heating Coil
7 Open Space
8 Protector Tube
Functions
The oxygen sensor optimizes the combustion (Air-Fuel Ratio
14.7:1) and resets the Air-fuel ratio in the ECU after sensing
the amount of oxygen from the exhaust gases to diminish the
exhaust gases.
- Rich(<1) above approx. 450mV
- Lean(>1) below approx. 450mV
Locatoin of Sensor
Oxygen sensor is located on the front exhaust pipe.
Page 723 of 1463
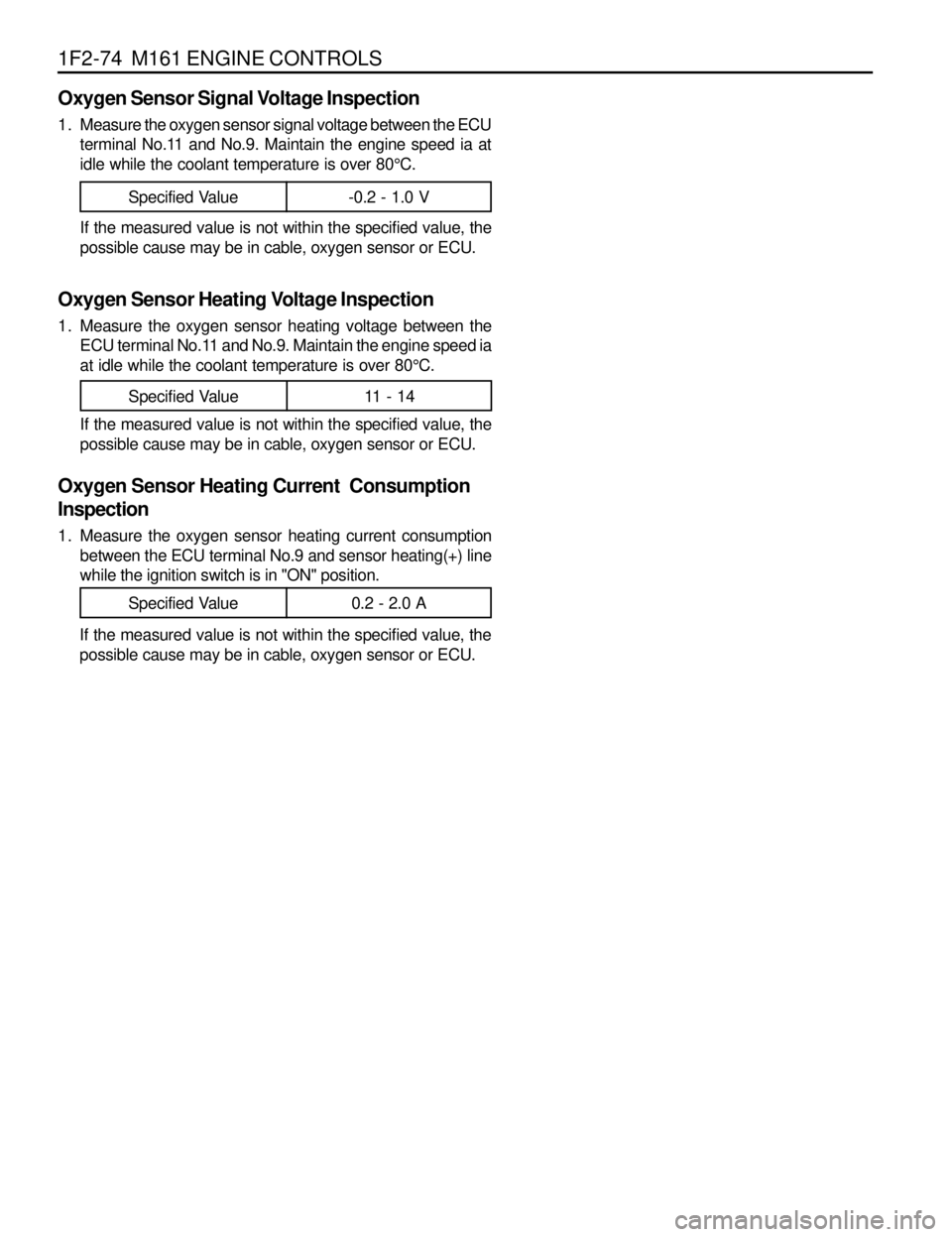
1F2-74 M161 ENGINE CONTROLS
Oxygen Sensor Signal Voltage Inspection
1. Measure the oxygen sensor signal voltage between the ECU
terminal No.11 and No.9. Maintain the engine speed ia at
idle while the coolant temperature is over 80°C.
If the measured value is not within the specified value, the
possible cause may be in cable, oxygen sensor or ECU.
Oxygen Sensor Heating Voltage Inspection
1. Measure the oxygen sensor heating voltage between the
ECU terminal No.11 and No.9. Maintain the engine speed ia
at idle while the coolant temperature is over 80°C.
If the measured value is not within the specified value, the
possible cause may be in cable, oxygen sensor or ECU.
Oxygen Sensor Heating Current Consumption
Inspection
1. Measure the oxygen sensor heating current consumption
between the ECU terminal No.9 and sensor heating(+) line
while the ignition switch is in "ON" position.
If the measured value is not within the specified value, the
possible cause may be in cable, oxygen sensor or ECU.
Specified Value 0.2 - 2.0 A
Specified Value -0.2 - 1.0 V
Specified Value 11 - 14
Page 724 of 1463
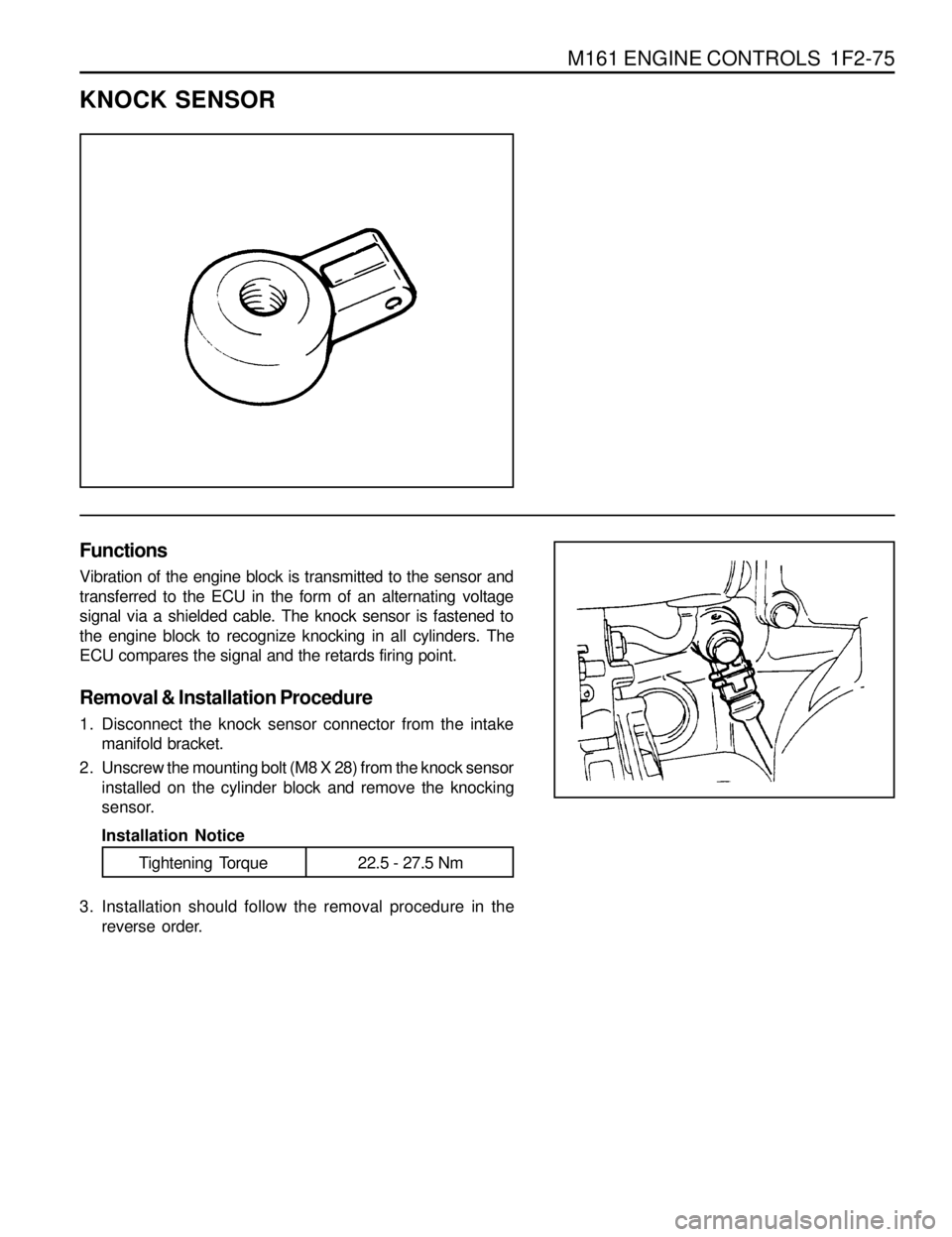
M161 ENGINE CONTROLS 1F2-75
KNOCK SENSOR
Functions
Vibration of the engine block is transmitted to the sensor and
transferred to the ECU in the form of an alternating voltage
signal via a shielded cable. The knock sensor is fastened to
the engine block to recognize knocking in all cylinders. The
ECU compares the signal and the retards firing point.
Removal & Installation Procedure
1. Disconnect the knock sensor connector from the intake
manifold bracket.
2. Unscrew the mounting bolt (M8 X 28) from the knock sensor
installed on the cylinder block and remove the knocking
sensor.
Installation Notice
3. Installation should follow the removal procedure in the
reverse order.
Tightening Torque 22.5 - 27.5 Nm
Page 725 of 1463
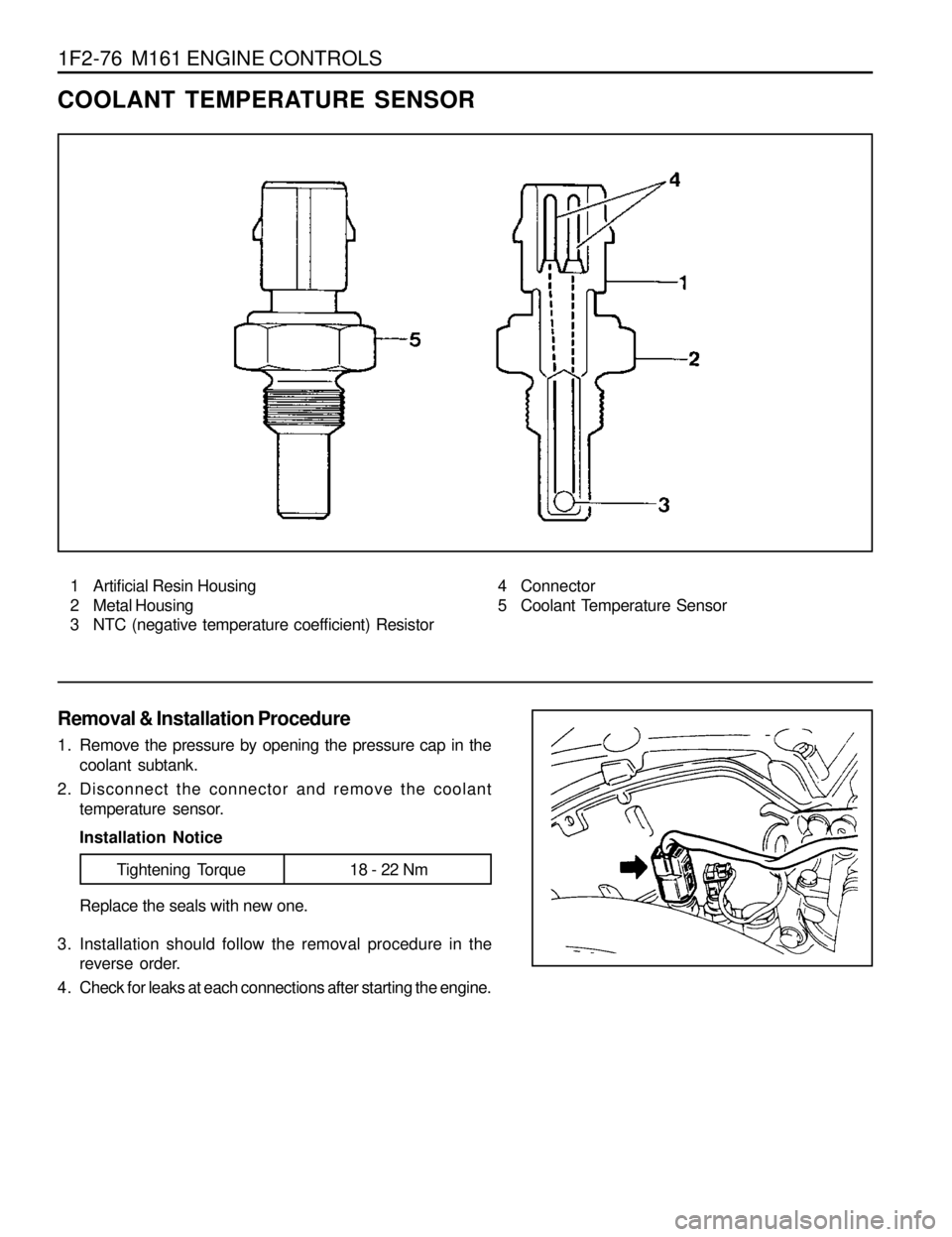
1F2-76 M161 ENGINE CONTROLS
COOLANT TEMPERATURE SENSOR
1 Artificial Resin Housing
2 Metal Housing
3 NTC (negative temperature coefficient) Resistor
Removal & Installation Procedure
1. Remove the pressure by opening the pressure cap in the
coolant subtank.
2. Disconnect the connector and remove the coolant
temperature sensor.
Installation Notice
Replace the seals with new one.
3. Installation should follow the removal procedure in the
reverse order.
4. Check for leaks at each connections after starting the engine.4 Connector
5 Coolant Temperature Sensor
Tightening Torque 18 - 22 Nm
Page 726 of 1463
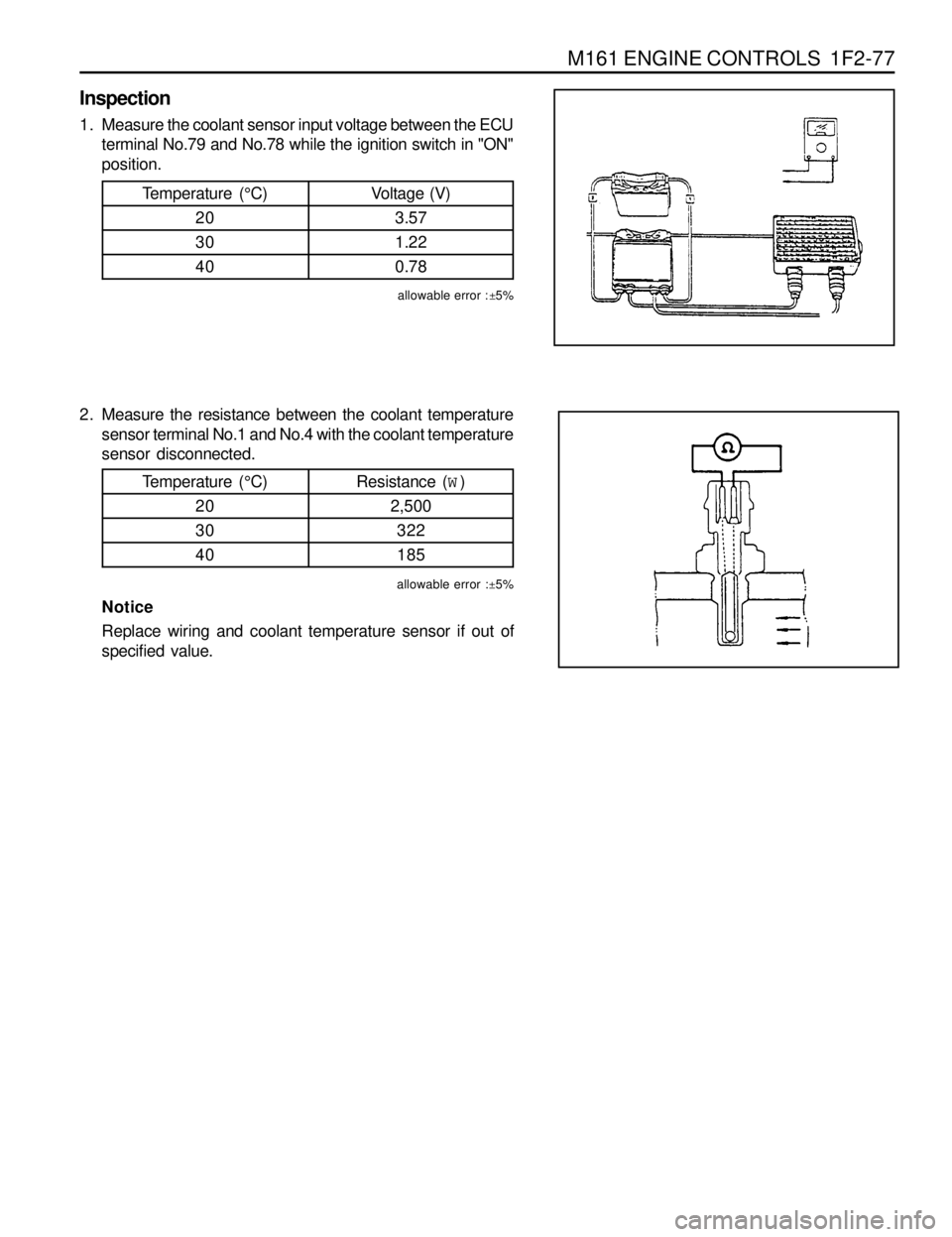
M161 ENGINE CONTROLS 1F2-77
2. Measure the resistance between the coolant temperature
sensor terminal No.1 and No.4 with the coolant temperature
sensor disconnected.
Inspection
1. Measure the coolant sensor input voltage between the ECU
terminal No.79 and No.78 while the ignition switch in "ON"
position.
Notice
Replace wiring and coolant temperature sensor if out of
specified value.
allowable error :±5%
allowable error :±5%
Voltage (V)
3.57
1.22
0.78 Temperature (°C)
20
30
40
Resistance (W)
2,500
322
185 Temperature (°C)
20
30
40
Page 728 of 1463
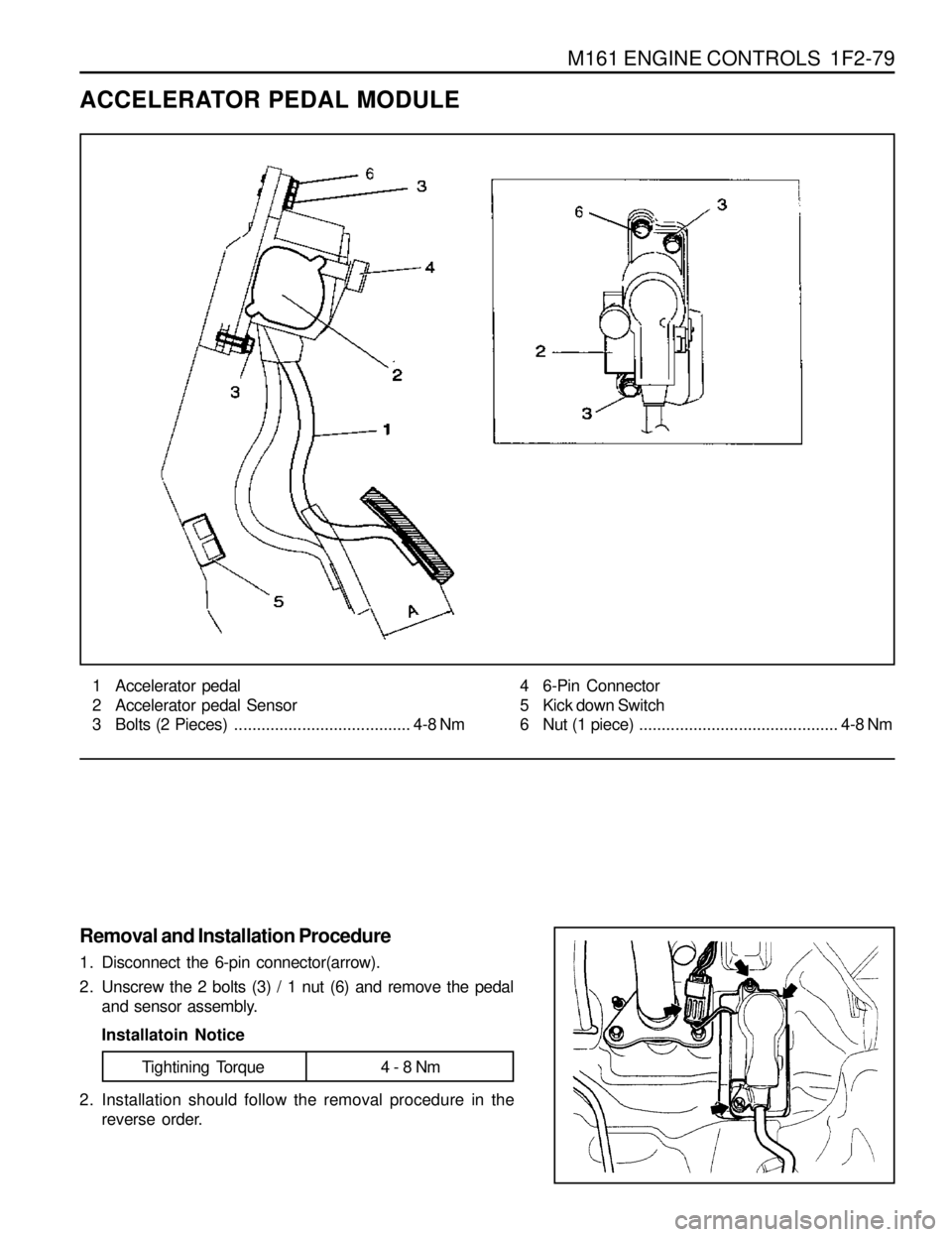
M161 ENGINE CONTROLS 1F2-79
ACCELERATOR PEDAL MODULE
1 Accelerator pedal
2 Accelerator pedal Sensor
3 Bolts (2 Pieces).......................................4-8 Nm
Removal and Installation Procedure
1. Disconnect the 6-pin connector(arrow).
2. Unscrew the 2 bolts (3) / 1 nut (6) and remove the pedal
and sensor assembly.
Installatoin Notice
Tightining Torque 4 - 8 Nm
2. Installation should follow the removal procedure in the
reverse order.4 6-Pin Connector
5 Kick down Switch
6 Nut (1 piece)............................................4-8 Nm
Page 729 of 1463
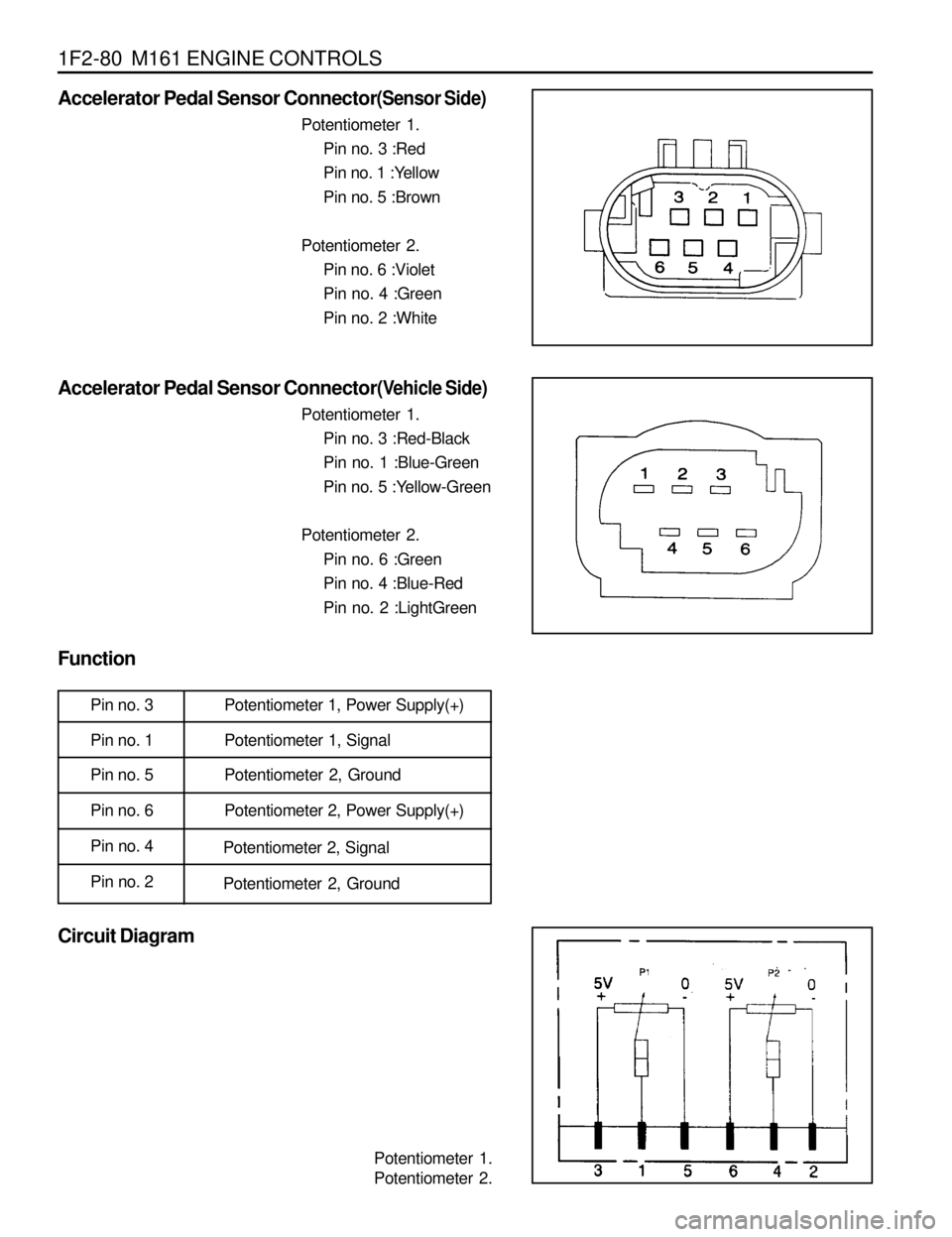
1F2-80 M161 ENGINE CONTROLS
Accelerator Pedal Sensor Connector(Sensor Side)
Potentiometer 1.
Pin no. 3 :Red
Pin no. 1 :Yellow
Pin no. 5 :Brown
Potentiometer 2.
Pin no. 6 :Violet
Pin no. 4 :Green
Pin no. 2 :White
Accelerator Pedal Sensor Connector(Vehicle Side)
Potentiometer 1.
Pin no. 3 :Red-Black
Pin no. 1 :Blue-Green
Pin no. 5 :Yellow-Green
Potentiometer 2.
Pin no. 6 :Green
Pin no. 4 :Blue-Red
Pin no. 2 :LightGreen
Circuit Diagram
Potentiometer 1.
Potentiometer 2.
Function
Potentiometer 1, Power Supply(+)
Potentiometer 1, Signal
Potentiometer 2, Ground
Potentiometer 2, Power Supply(+) Pin no. 3
Pin no. 1
Pin no. 5
Pin no. 6
Pin no. 4
Pin no. 2Potentiometer 2, Signal
Potentiometer 2, Ground