automatic transmission SSANGYONG MUSSO 1998 Workshop Repair Manual
[x] Cancel search | Manufacturer: SSANGYONG, Model Year: 1998, Model line: MUSSO, Model: SSANGYONG MUSSO 1998Pages: 1463, PDF Size: 19.88 MB
Page 21 of 1463
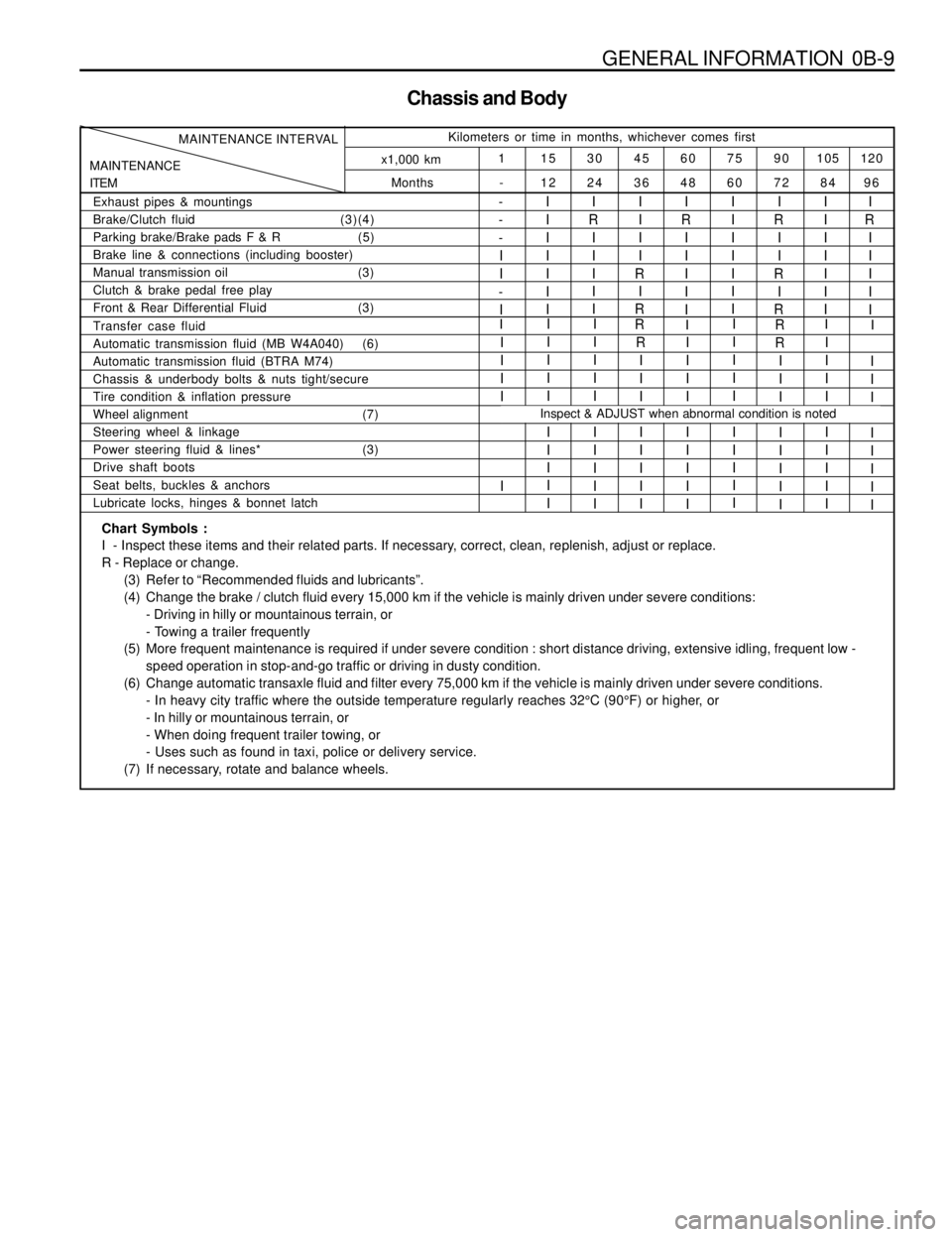
GENERAL INFORMATION 0B-9
Chassis and Body
Months
MAINTENANCE
ITEMMAINTENANCE INTERVALKilometers or time in months, whichever comes first
120 105 90 75 60 45 30 15 1
96 84 72 60 48 36 24 12
- x1,000 km
Exhaust pipes & mountings
Brake/Clutch fluid(3)(4)
Parking brake/Brake pads F & R (5)
Brake line & connections (including booster)
Manual transmission oil (3)
Clutch & brake pedal free play
Front & Rear Differential Fluid (3)I
R
I
I
I
I
I-
-
-
I
I
-
II
I
I
I
I
I
II
R
I
I
I
I
II
I
I
I
R
I
RI
I
I
I
I
I
II
R
I
I
R
I
RI
I
I
I
I
I
II
R
I
I
I
I
I
Automatic transmission fluid (MB W4A040) (6)
Automatic transmission fluid (BTRA M74)
Chassis & underbody bolts & nuts tight/secure
Tire condition & inflation pressure
Wheel alignment (7)
Steering wheel & linkage
Power steering fluid & lines* (3)
Drive shaft boots
Seat belts, buckles & anchors
Lubricate locks, hinges & bonnet latchI
I
I
I
II
I
I
I
I
I
I
I
I
II
I
I
I
I
I
I
I
I
IR
I
I
I
I
I
I
I
II
I
I
I
I
I
I
I
II
I
I
I
I
I
I
I
I
IR
R
I
I
I
I
I
I
I
II
I
I
I
I
I
I
I
I
Transfer case fluidRIII
Inspect & ADJUST when abnormal condition is noted
I
I
I
I
I
I
I
I
I
Chart Symbols :
I - Inspect these items and their related parts. If necessary, correct, clean, replenish, adjust or replace.
R - Replace or change.
(3) Refer to “Recommended fluids and lubricants”.
(4) Change the brake / clutch fluid every 15,000 km if the vehicle is mainly driven under severe conditions:
- Driving in hilly or mountainous terrain, or
- Towing a trailer frequently
(5) More frequent maintenance is required if under severe condition : short distance driving, extensive idling, frequent low -
speed operation in stop-and-go traffic or driving in dusty condition.
(6) Change automatic transaxle fluid and filter every 75,000 km if the vehicle is mainly driven under severe conditions.
- In heavy city traffic where the outside temperature regularly reaches 32°C (90°F) or higher, or
- In hilly or mountainous terrain, or
- When doing frequent trailer towing, or
- Uses such as found in taxi, police or delivery service.
(7) If necessary, rotate and balance wheels.
Page 23 of 1463
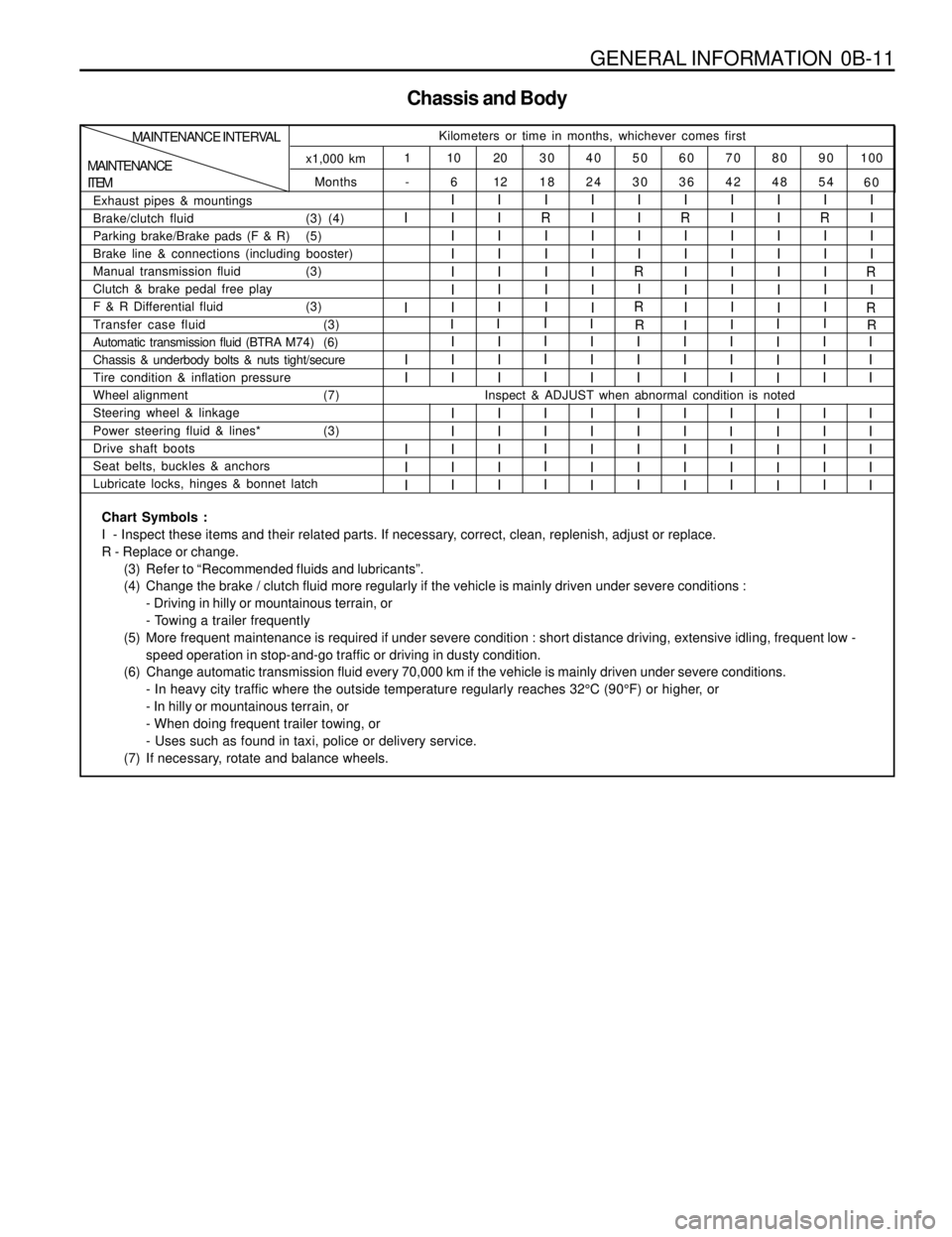
GENERAL INFORMATION 0B-11
Chassis and Body
Months
-
MAINTENANCE
ITEMMAINTENANCE INTERVAL
Kilometers or time in months, whichever comes first
100 90 80 70 60 50 40 30 20 10 1
60 54 48 42 36 30 24 18 12 6 x1,000 km
Exhaust pipes & mountings
Brake/clutch fluid(3) (4)
Parking brake/Brake pads (F & R) (5)
Brake line & connections (including booster)
Manual transmission fluid (3)
Clutch & brake pedal free play
F & R Differential fluid (3)
I
II
I
I
I
I
I
II
I
I
I
I
I
II
R
I
I
I
I
II
I
I
I
I
I
II
I
I
I
R
I
RI
R
I
I
I
I
II
I
I
I
I
I
II
I
I
I
I
I
II
R
I
I
I
I
II
I
I
I
R
I
R
Automatic transmission fluid (BTRA M74) (6)
Chassis & underbody bolts & nuts tight/secure
Tire condition & inflation pressure
Wheel alignment (7)
Steering wheel & linkage
Power steering fluid & lines* (3)
Drive shaft boots
Seat belts, buckles & anchors
Lubricate locks, hinges & bonnet latchI
I
I
I
I
I
I
II
I
I
I
I
I
I
II
I
I
I
I
I
I
I
II
I
I
I
I
I
I
II
I
I
I
I
I
I
II
I
I
I
I
I
I
II
I
I
I
I
I
II
I
I
I
I
I
I
II
I
I
I
I
I
I
I
Transfer case fluid (3)R
IR
I II
I
I
I
I
II
I
I
I
I
I
I
I
I
Inspect & ADJUST when abnormal condition is noted
II
I
Chart Symbols :
I - Inspect these items and their related parts. If necessary, correct, clean, replenish, adjust or replace.
R - Replace or change.
(3) Refer to “Recommended fluids and lubricants”.
(4) Change the brake / clutch fluid more regularly if the vehicle is mainly driven under severe conditions :
- Driving in hilly or mountainous terrain, or
- Towing a trailer frequently
(5) More frequent maintenance is required if under severe condition : short distance driving, extensive idling, frequent low -
speed operation in stop-and-go traffic or driving in dusty condition.
(6) Change automatic transmission fluid every 70,000 km if the vehicle is mainly driven under severe conditions.
- In heavy city traffic where the outside temperature regularly reaches 32°C (90°F) or higher, or
- In hilly or mountainous terrain, or
- When doing frequent trailer towing, or
- Uses such as found in taxi, police or delivery service.
(7) If necessary, rotate and balance wheels.
Page 38 of 1463
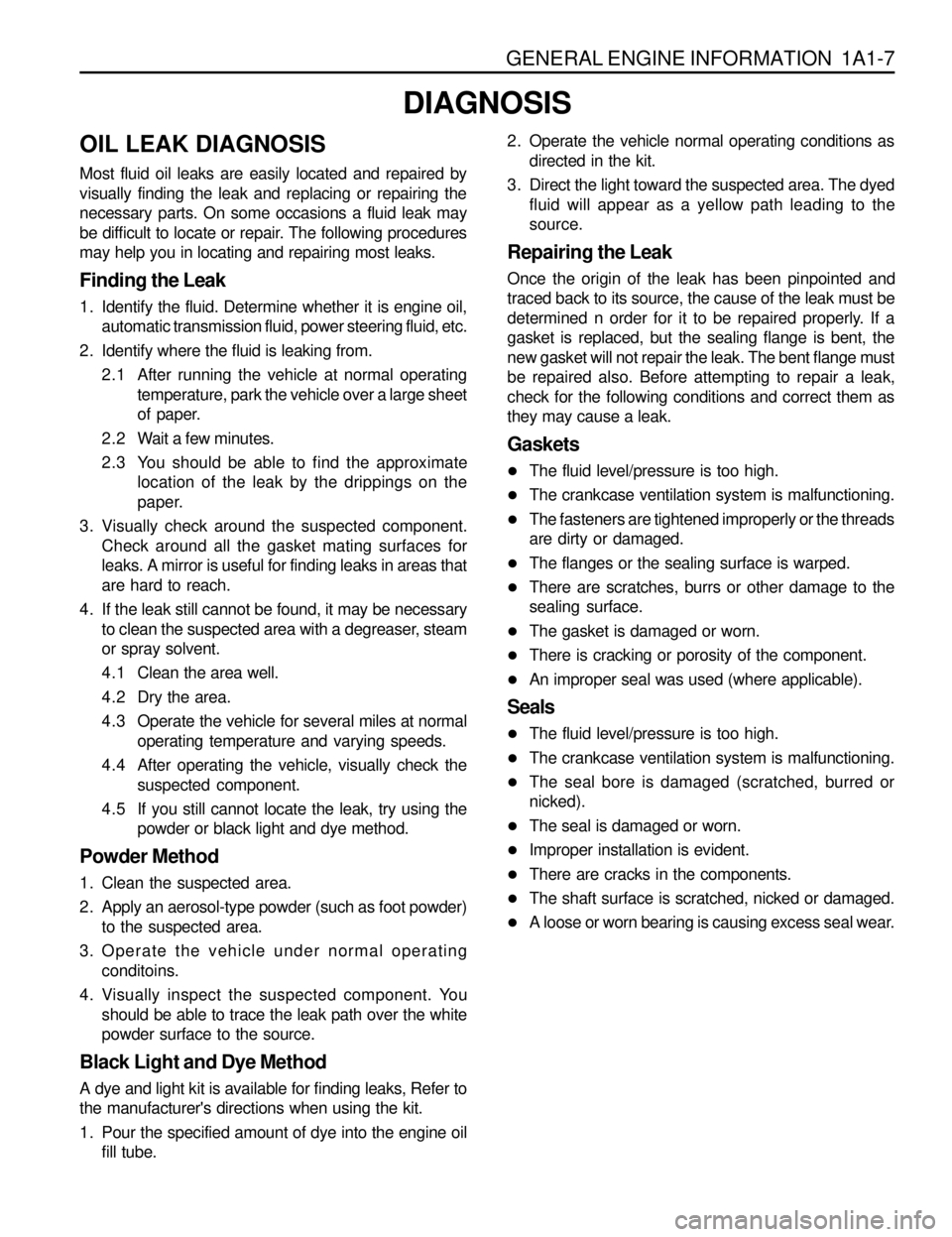
GENERAL ENGINE INFORMATION 1A1-7
OIL LEAK DIAGNOSIS
Most fluid oil leaks are easily located and repaired by
visually finding the leak and replacing or repairing the
necessary parts. On some occasions a fluid leak may
be difficult to locate or repair. The following procedures
may help you in locating and repairing most leaks.
Finding the Leak
1. Identify the fluid. Determine whether it is engine oil,
automatic transmission fluid, power steering fluid, etc.
2. Identify where the fluid is leaking from.
2.1 After running the vehicle at normal operating
temperature, park the vehicle over a large sheet
of paper.
2.2 Wait a few minutes.
2.3 You should be able to find the approximate
location of the leak by the drippings on the
paper.
3. Visually check around the suspected component.
Check around all the gasket mating surfaces for
leaks. A mirror is useful for finding leaks in areas that
are hard to reach.
4. If the leak still cannot be found, it may be necessary
to clean the suspected area with a degreaser, steam
or spray solvent.
4.1 Clean the area well.
4.2 Dry the area.
4.3 Operate the vehicle for several miles at normal
operating temperature and varying speeds.
4.4 After operating the vehicle, visually check the
suspected component.
4.5 If you still cannot locate the leak, try using the
powder or black light and dye method.
Powder Method
1. Clean the suspected area.
2. Apply an aerosol-type powder (such as foot powder)
to the suspected area.
3. Operate the vehicle under normal operating
conditoins.
4. Visually inspect the suspected component. You
should be able to trace the leak path over the white
powder surface to the source.
Black Light and Dye Method
A dye and light kit is available for finding leaks, Refer to
the manufacturer's directions when using the kit.
1. Pour the specified amount of dye into the engine oil
fill tube.2. Operate the vehicle normal operating conditions as
directed in the kit.
3. Direct the light toward the suspected area. The dyed
fluid will appear as a yellow path leading to the
source.
Repairing the Leak
Once the origin of the leak has been pinpointed and
traced back to its source, the cause of the leak must be
determined n order for it to be repaired properly. If a
gasket is replaced, but the sealing flange is bent, the
new gasket will not repair the leak. The bent flange must
be repaired also. Before attempting to repair a leak,
check for the following conditions and correct them as
they may cause a leak.
Gaskets
lThe fluid level/pressure is too high.
lThe crankcase ventilation system is malfunctioning.
lThe fasteners are tightened improperly or the threads
are dirty or damaged.
lThe flanges or the sealing surface is warped.
lThere are scratches, burrs or other damage to the
sealing surface.
lThe gasket is damaged or worn.
lThere is cracking or porosity of the component.
lAn improper seal was used (where applicable).
Seals
lThe fluid level/pressure is too high.
lThe crankcase ventilation system is malfunctioning.
lThe seal bore is damaged (scratched, burred or
nicked).
lThe seal is damaged or worn.
lImproper installation is evident.
lThere are cracks in the components.
lThe shaft surface is scratched, nicked or damaged.
lA loose or worn bearing is causing excess seal wear.
DIAGNOSIS
Page 52 of 1463
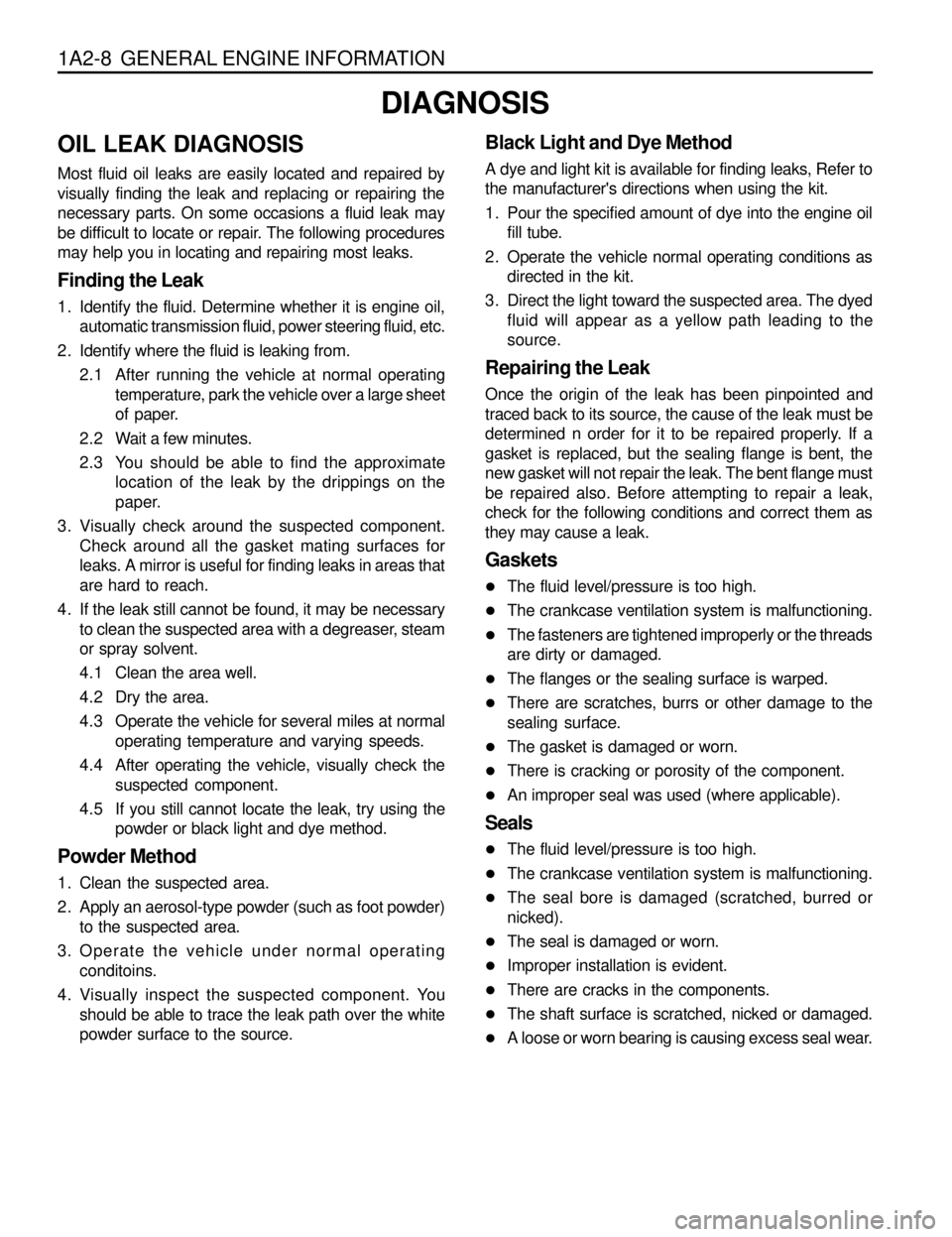
1A2-8 GENERAL ENGINE INFORMATION
OIL LEAK DIAGNOSIS
Most fluid oil leaks are easily located and repaired by
visually finding the leak and replacing or repairing the
necessary parts. On some occasions a fluid leak may
be difficult to locate or repair. The following procedures
may help you in locating and repairing most leaks.
Finding the Leak
1. Identify the fluid. Determine whether it is engine oil,
automatic transmission fluid, power steering fluid, etc.
2. Identify where the fluid is leaking from.
2.1 After running the vehicle at normal operating
temperature, park the vehicle over a large sheet
of paper.
2.2 Wait a few minutes.
2.3 You should be able to find the approximate
location of the leak by the drippings on the
paper.
3. Visually check around the suspected component.
Check around all the gasket mating surfaces for
leaks. A mirror is useful for finding leaks in areas that
are hard to reach.
4. If the leak still cannot be found, it may be necessary
to clean the suspected area with a degreaser, steam
or spray solvent.
4.1 Clean the area well.
4.2 Dry the area.
4.3 Operate the vehicle for several miles at normal
operating temperature and varying speeds.
4.4 After operating the vehicle, visually check the
suspected component.
4.5 If you still cannot locate the leak, try using the
powder or black light and dye method.
Powder Method
1. Clean the suspected area.
2. Apply an aerosol-type powder (such as foot powder)
to the suspected area.
3. Operate the vehicle under normal operating
conditoins.
4. Visually inspect the suspected component. You
should be able to trace the leak path over the white
powder surface to the source.
Black Light and Dye Method
A dye and light kit is available for finding leaks, Refer to
the manufacturer's directions when using the kit.
1. Pour the specified amount of dye into the engine oil
fill tube.
2. Operate the vehicle normal operating conditions as
directed in the kit.
3. Direct the light toward the suspected area. The dyed
fluid will appear as a yellow path leading to the
source.
Repairing the Leak
Once the origin of the leak has been pinpointed and
traced back to its source, the cause of the leak must be
determined n order for it to be repaired properly. If a
gasket is replaced, but the sealing flange is bent, the
new gasket will not repair the leak. The bent flange must
be repaired also. Before attempting to repair a leak,
check for the following conditions and correct them as
they may cause a leak.
Gaskets
lThe fluid level/pressure is too high.
lThe crankcase ventilation system is malfunctioning.
lThe fasteners are tightened improperly or the threads
are dirty or damaged.
lThe flanges or the sealing surface is warped.
lThere are scratches, burrs or other damage to the
sealing surface.
lThe gasket is damaged or worn.
lThere is cracking or porosity of the component.
lAn improper seal was used (where applicable).
Seals
lThe fluid level/pressure is too high.
lThe crankcase ventilation system is malfunctioning.
lThe seal bore is damaged (scratched, burred or
nicked).
lThe seal is damaged or worn.
lImproper installation is evident.
lThere are cracks in the components.
lThe shaft surface is scratched, nicked or damaged.
lA loose or worn bearing is causing excess seal wear.
DIAGNOSIS
Page 68 of 1463
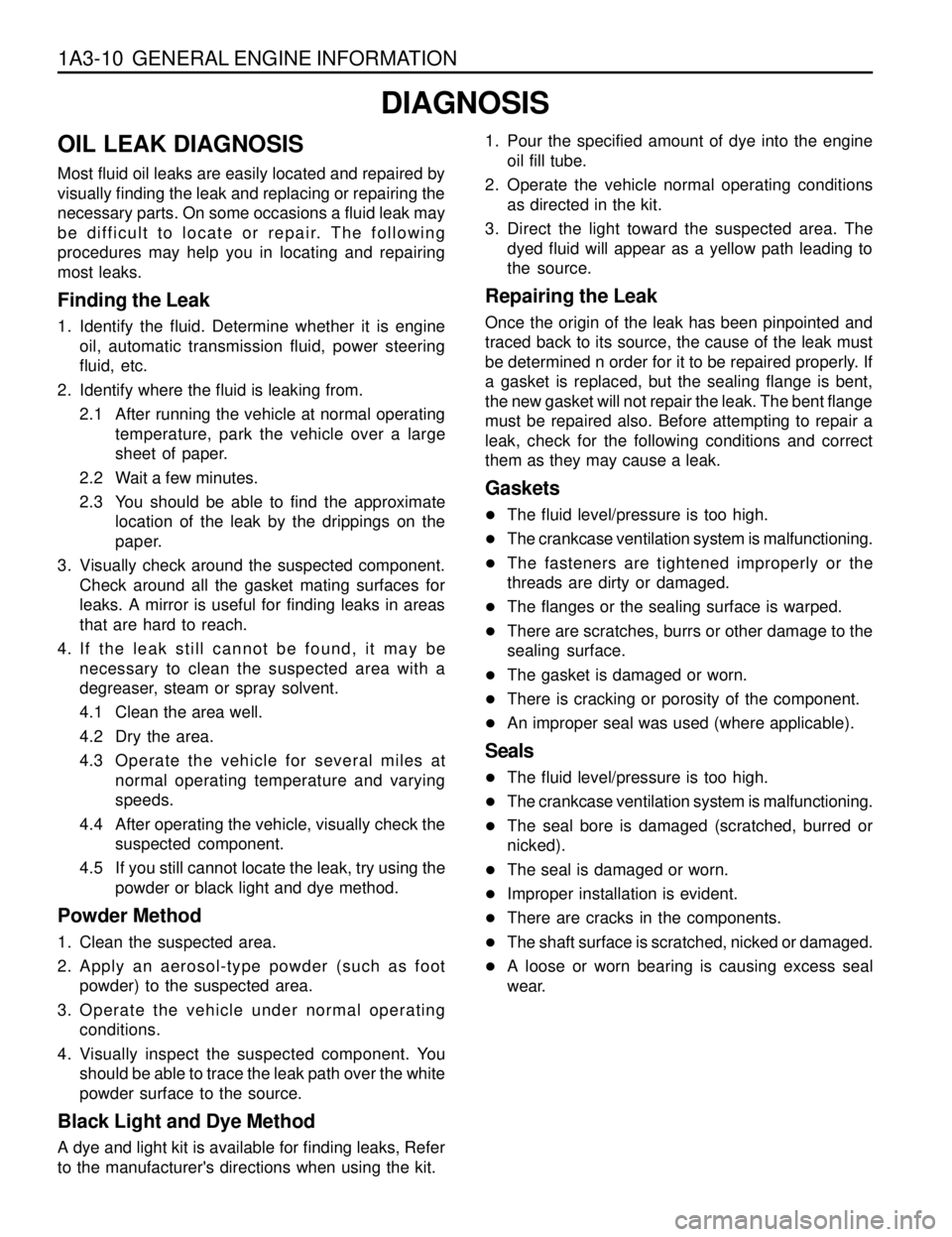
1A3-10 GENERAL ENGINE INFORMATION
OIL LEAK DIAGNOSIS
Most fluid oil leaks are easily located and repaired by
visually finding the leak and replacing or repairing the
necessary parts. On some occasions a fluid leak may
be difficult to locate or repair. The following
procedures may help you in locating and repairing
most leaks.
Finding the Leak
1. Identify the fluid. Determine whether it is engine
oil, automatic transmission fluid, power steering
fluid, etc.
2. Identify where the fluid is leaking from.
2.1 After running the vehicle at normal operating
temperature, park the vehicle over a large
sheet of paper.
2.2 Wait a few minutes.
2.3 You should be able to find the approximate
location of the leak by the drippings on the
paper.
3. Visually check around the suspected component.
Check around all the gasket mating surfaces for
leaks. A mirror is useful for finding leaks in areas
that are hard to reach.
4. If the leak still cannot be found, it may be
necessary to clean the suspected area with a
degreaser, steam or spray solvent.
4.1 Clean the area well.
4.2 Dry the area.
4.3 Operate the vehicle for several miles at
normal operating temperature and varying
speeds.
4.4 After operating the vehicle, visually check the
suspected component.
4.5 If you still cannot locate the leak, try using the
powder or black light and dye method.
Powder Method
1. Clean the suspected area.
2. Apply an aerosol-type powder (such as foot
powder) to the suspected area.
3. Operate the vehicle under normal operating
conditions.
4. Visually inspect the suspected component. You
should be able to trace the leak path over the white
powder surface to the source.
Black Light and Dye Method
A dye and light kit is available for finding leaks, Refer
to the manufacturer's directions when using the kit.1. Pour the specified amount of dye into the engine
oil fill tube.
2. Operate the vehicle normal operating conditions
as directed in the kit.
3. Direct the light toward the suspected area. The
dyed fluid will appear as a yellow path leading to
the source.
Repairing the Leak
Once the origin of the leak has been pinpointed and
traced back to its source, the cause of the leak must
be determined n order for it to be repaired properly. If
a gasket is replaced, but the sealing flange is bent,
the new gasket will not repair the leak. The bent flange
must be repaired also. Before attempting to repair a
leak, check for the following conditions and correct
them as they may cause a leak.
Gaskets
lThe fluid level/pressure is too high.
lThe crankcase ventilation system is malfunctioning.
lThe fasteners are tightened improperly or the
threads are dirty or damaged.
lThe flanges or the sealing surface is warped.
lThere are scratches, burrs or other damage to the
sealing surface.
lThe gasket is damaged or worn.
lThere is cracking or porosity of the component.
lAn improper seal was used (where applicable).
Seals
lThe fluid level/pressure is too high.
lThe crankcase ventilation system is malfunctioning.
lThe seal bore is damaged (scratched, burred or
nicked).
lThe seal is damaged or worn.
lImproper installation is evident.
lThere are cracks in the components.
lThe shaft surface is scratched, nicked or damaged.
lA loose or worn bearing is causing excess seal
wear.
DIAGNOSIS
Page 84 of 1463
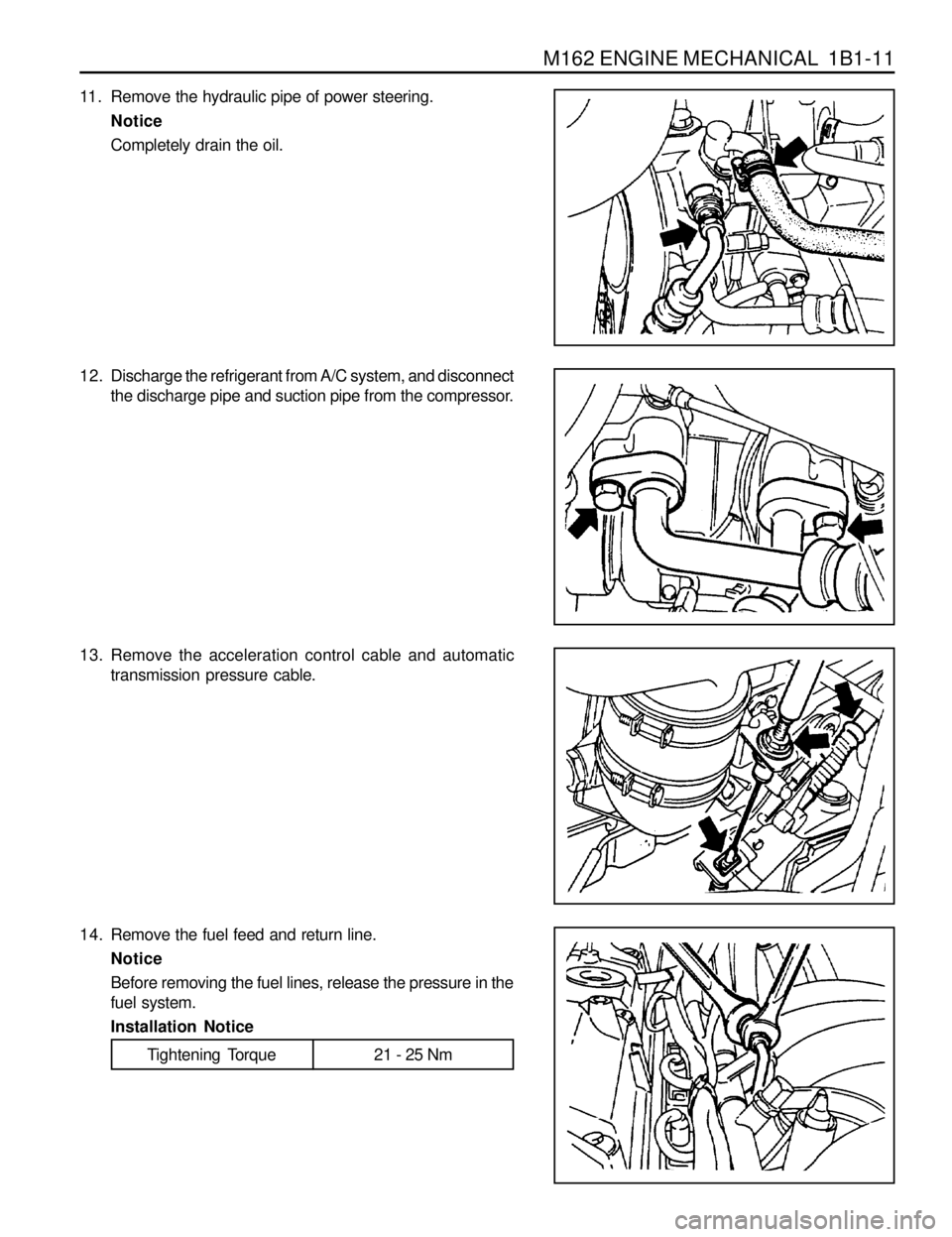
M162 ENGINE MECHANICAL 1B1-11
12. Discharge the refrigerant from A/C system, and disconnect
the discharge pipe and suction pipe from the compressor.
14. Remove the fuel feed and return line.
Notice
Before removing the fuel lines, release the pressure in the
fuel system.
Installation Notice 13. Remove the acceleration control cable and automatic
transmission pressure cable. 11. Remove the hydraulic pipe of power steering.
Notice
Completely drain the oil.
Tightening Torque 21 - 25 Nm
Page 85 of 1463
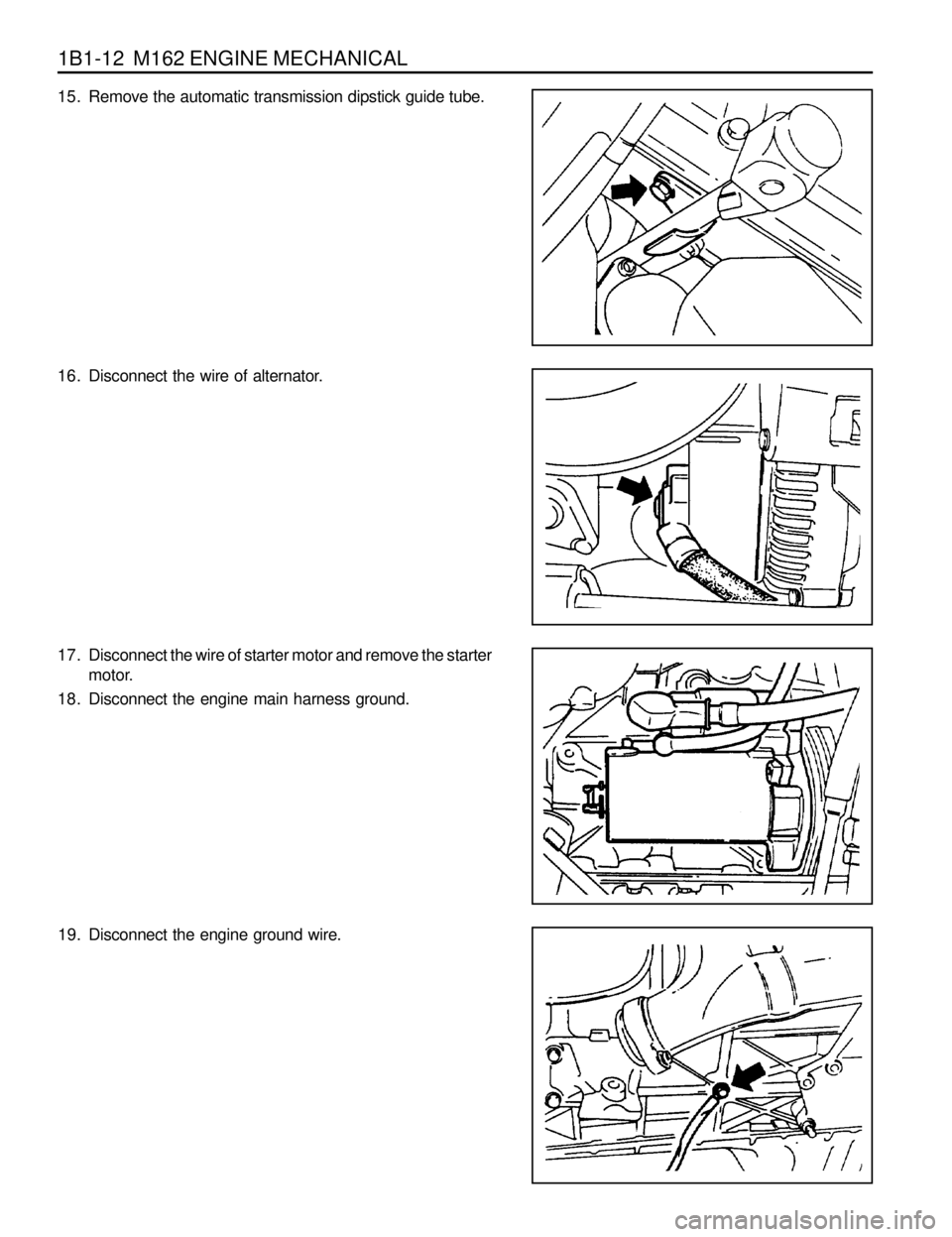
1B1-12 M162 ENGINE MECHANICAL
19. Disconnect the engine ground wire. 15. Remove the automatic transmission dipstick guide tube.
16. Disconnect the wire of alternator.
17. Disconnect the wire of starter motor and remove the starter
motor.
18. Disconnect the engine main harness ground.
Page 86 of 1463
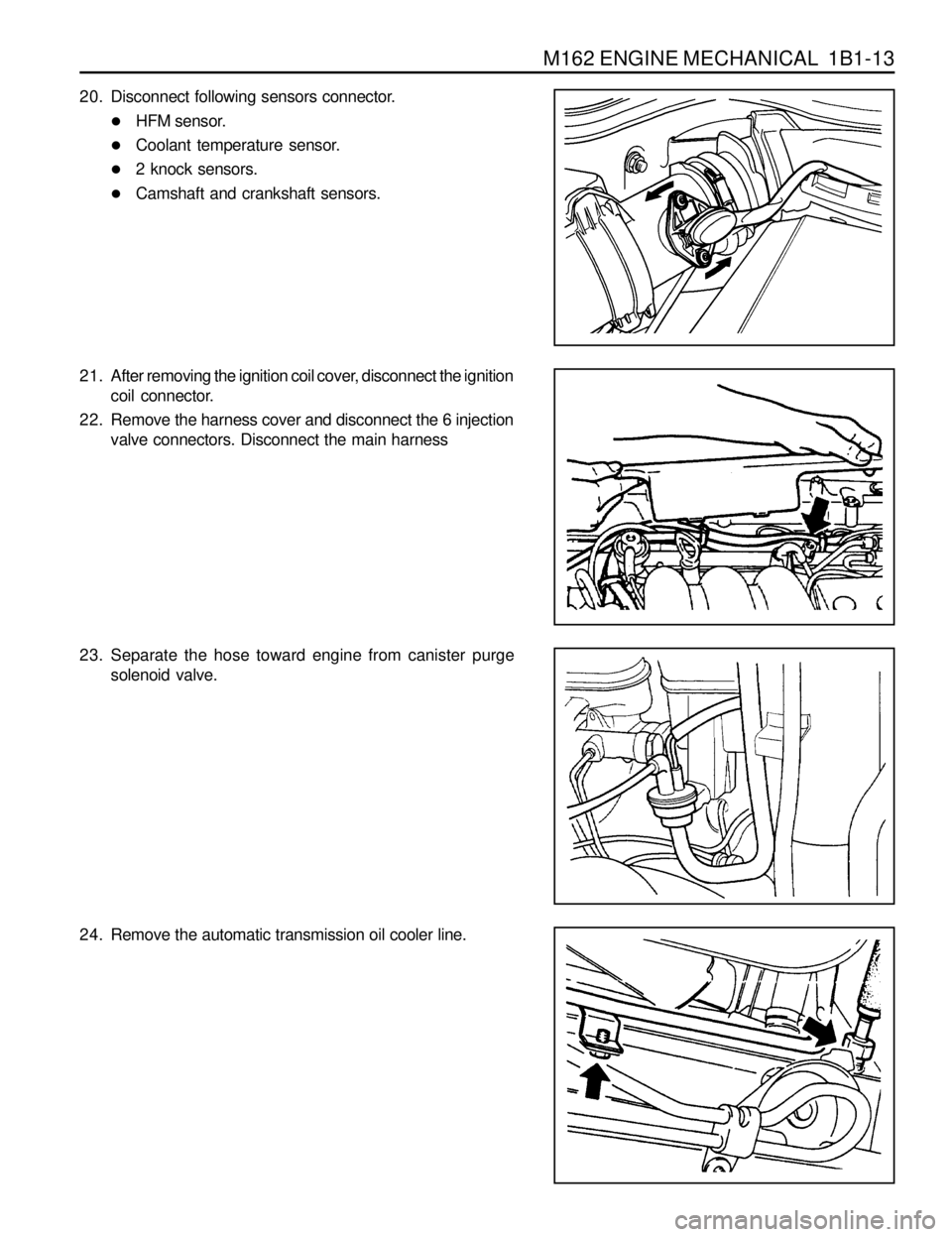
M162 ENGINE MECHANICAL 1B1-13
20. Disconnect following sensors connector.
lHFM sensor.
lCoolant temperature sensor.
l2 knock sensors.
lCamshaft and crankshaft sensors.
21. After removing the ignition coil cover, disconnect the ignition
coil connector.
22. Remove the harness cover and disconnect the 6 injection
valve connectors. Disconnect the main harness
23. Separate the hose toward engine from canister purge
solenoid valve.
24. Remove the automatic transmission oil cooler line.
Page 113 of 1463
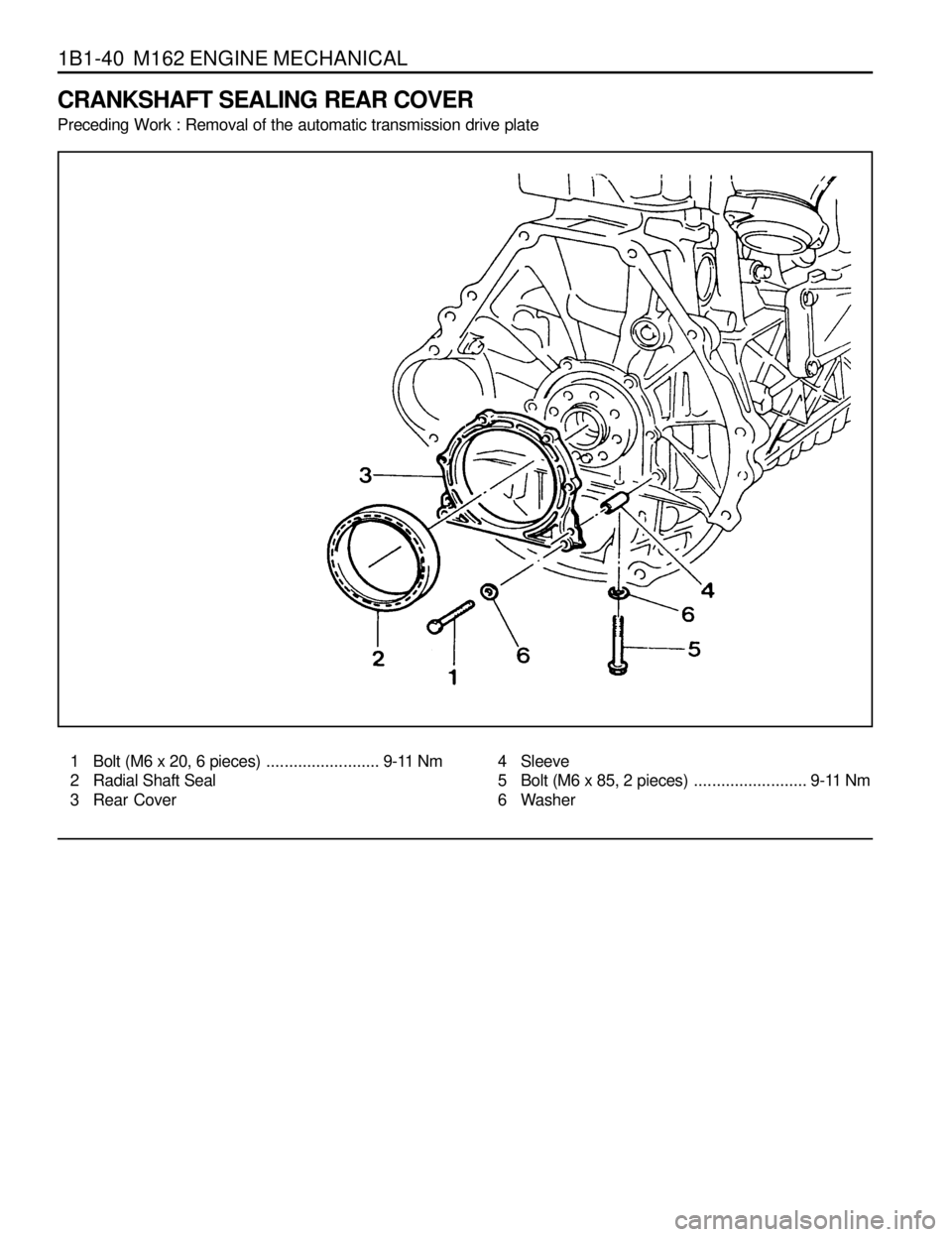
1B1-40 M162 ENGINE MECHANICAL
CRANKSHAFT SEALING REAR COVER
Preceding Work : Removal of the automatic transmission drive plate
1 Bolt (M6 x 20, 6 pieces)......................... 9-11 Nm
2 Radial Shaft Seal
3 Rear Cover4 Sleeve
5 Bolt (M6 x 85, 2 pieces)......................... 9-11 Nm
6 Washer
Page 126 of 1463
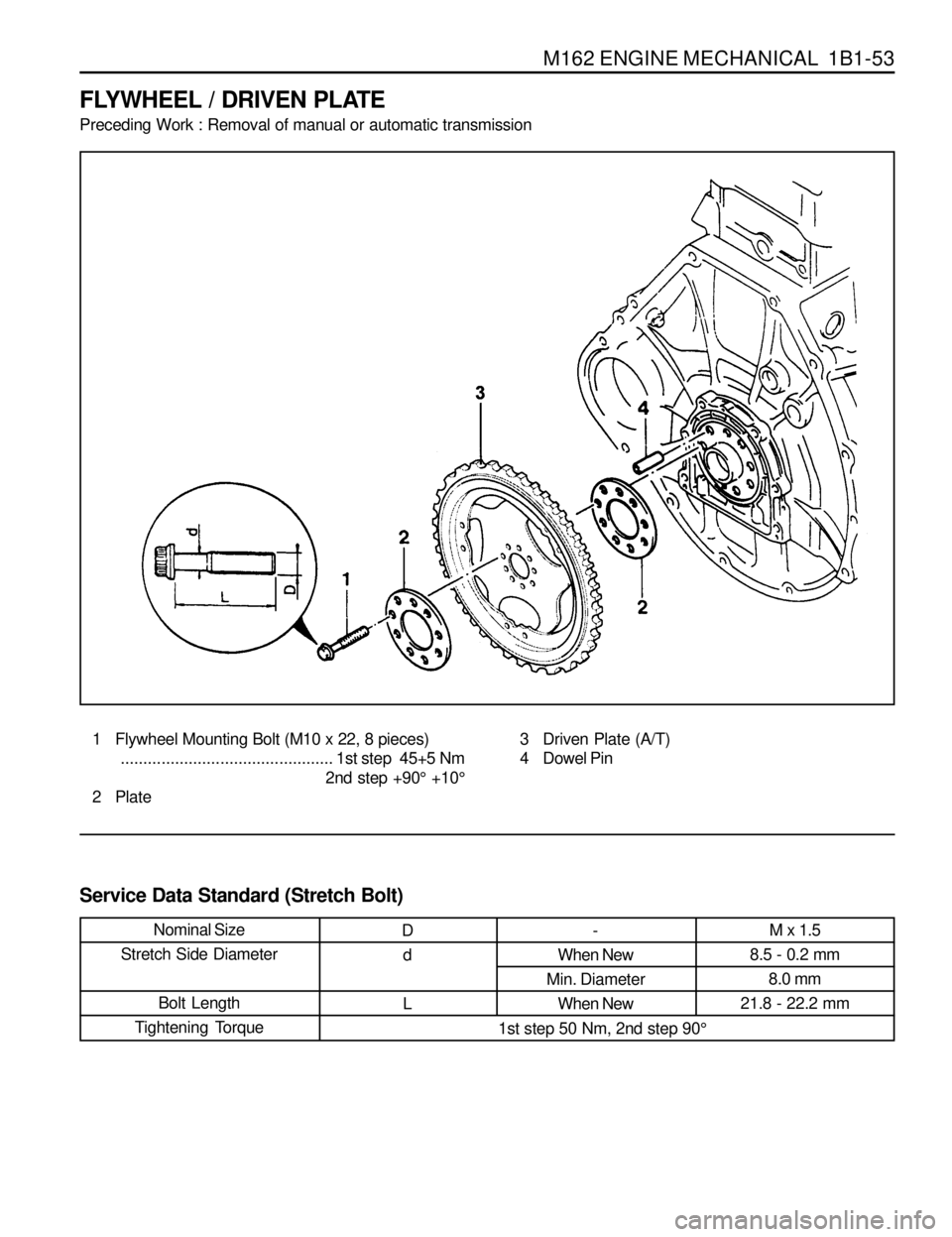
M162 ENGINE MECHANICAL 1B1-53
FLYWHEEL / DRIVEN PLATE
Preceding Work : Removal of manual or automatic transmission
1 Flywheel Mounting Bolt (M10 x 22, 8 pieces)
...............................................1st step 45+5 Nm
2nd step +90° +10°
2 Plate3 Driven Plate (A/T)
4 Dowel Pin
Service Data Standard (Stretch Bolt)
Nominal Size
Stretch Side Diameter
Bolt Length
Tightening TorqueM x 1.5
8.5 - 0.2 mm
8.0 mm
21.8 - 22.2 mm-
When New
Min. Diameter
When NewD
d
L
1st step 50 Nm, 2nd step 90°