check transmission fluid SSANGYONG MUSSO 1998 Workshop Repair Manual
[x] Cancel search | Manufacturer: SSANGYONG, Model Year: 1998, Model line: MUSSO, Model: SSANGYONG MUSSO 1998Pages: 1463, PDF Size: 19.88 MB
Page 38 of 1463
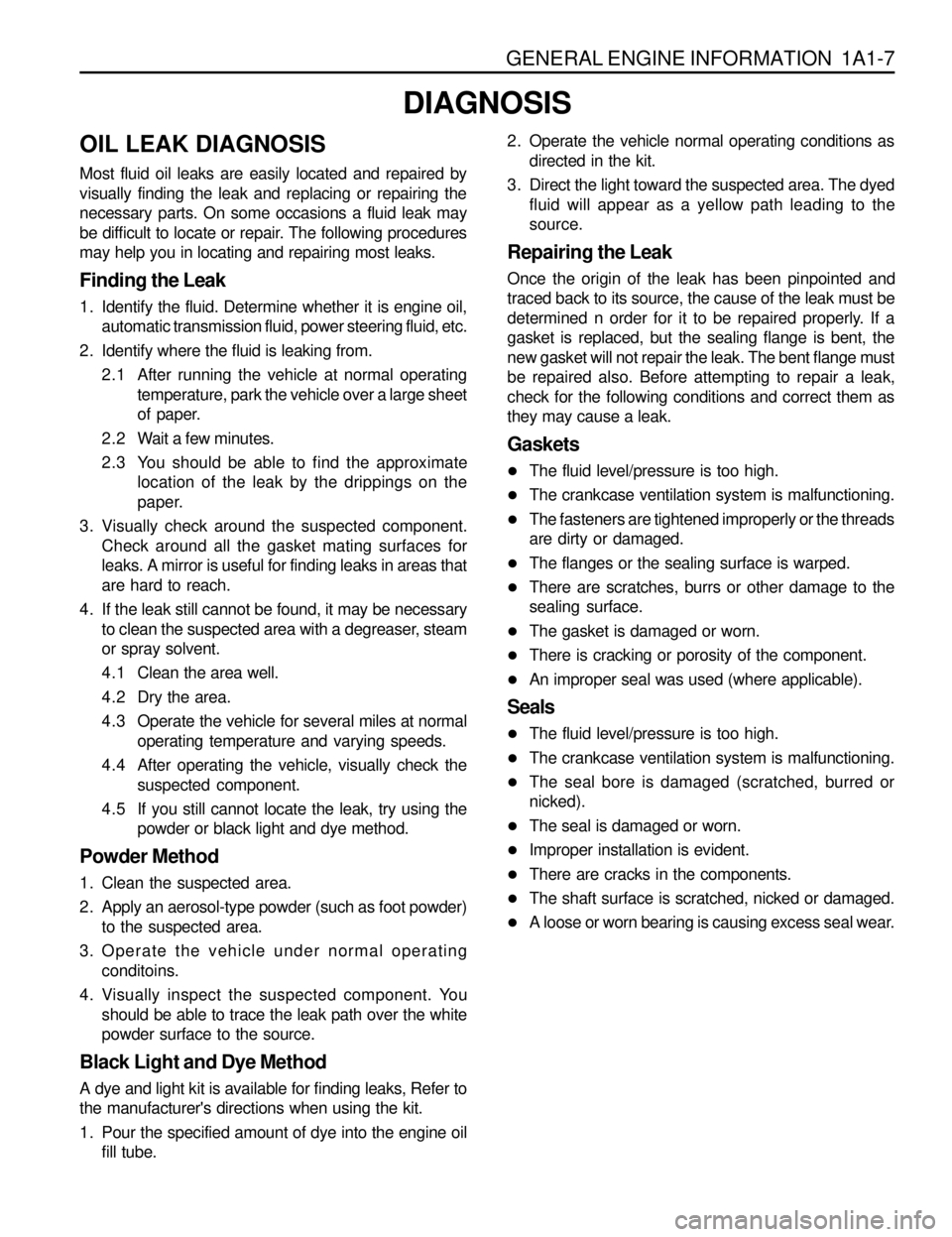
GENERAL ENGINE INFORMATION 1A1-7
OIL LEAK DIAGNOSIS
Most fluid oil leaks are easily located and repaired by
visually finding the leak and replacing or repairing the
necessary parts. On some occasions a fluid leak may
be difficult to locate or repair. The following procedures
may help you in locating and repairing most leaks.
Finding the Leak
1. Identify the fluid. Determine whether it is engine oil,
automatic transmission fluid, power steering fluid, etc.
2. Identify where the fluid is leaking from.
2.1 After running the vehicle at normal operating
temperature, park the vehicle over a large sheet
of paper.
2.2 Wait a few minutes.
2.3 You should be able to find the approximate
location of the leak by the drippings on the
paper.
3. Visually check around the suspected component.
Check around all the gasket mating surfaces for
leaks. A mirror is useful for finding leaks in areas that
are hard to reach.
4. If the leak still cannot be found, it may be necessary
to clean the suspected area with a degreaser, steam
or spray solvent.
4.1 Clean the area well.
4.2 Dry the area.
4.3 Operate the vehicle for several miles at normal
operating temperature and varying speeds.
4.4 After operating the vehicle, visually check the
suspected component.
4.5 If you still cannot locate the leak, try using the
powder or black light and dye method.
Powder Method
1. Clean the suspected area.
2. Apply an aerosol-type powder (such as foot powder)
to the suspected area.
3. Operate the vehicle under normal operating
conditoins.
4. Visually inspect the suspected component. You
should be able to trace the leak path over the white
powder surface to the source.
Black Light and Dye Method
A dye and light kit is available for finding leaks, Refer to
the manufacturer's directions when using the kit.
1. Pour the specified amount of dye into the engine oil
fill tube.2. Operate the vehicle normal operating conditions as
directed in the kit.
3. Direct the light toward the suspected area. The dyed
fluid will appear as a yellow path leading to the
source.
Repairing the Leak
Once the origin of the leak has been pinpointed and
traced back to its source, the cause of the leak must be
determined n order for it to be repaired properly. If a
gasket is replaced, but the sealing flange is bent, the
new gasket will not repair the leak. The bent flange must
be repaired also. Before attempting to repair a leak,
check for the following conditions and correct them as
they may cause a leak.
Gaskets
lThe fluid level/pressure is too high.
lThe crankcase ventilation system is malfunctioning.
lThe fasteners are tightened improperly or the threads
are dirty or damaged.
lThe flanges or the sealing surface is warped.
lThere are scratches, burrs or other damage to the
sealing surface.
lThe gasket is damaged or worn.
lThere is cracking or porosity of the component.
lAn improper seal was used (where applicable).
Seals
lThe fluid level/pressure is too high.
lThe crankcase ventilation system is malfunctioning.
lThe seal bore is damaged (scratched, burred or
nicked).
lThe seal is damaged or worn.
lImproper installation is evident.
lThere are cracks in the components.
lThe shaft surface is scratched, nicked or damaged.
lA loose or worn bearing is causing excess seal wear.
DIAGNOSIS
Page 52 of 1463
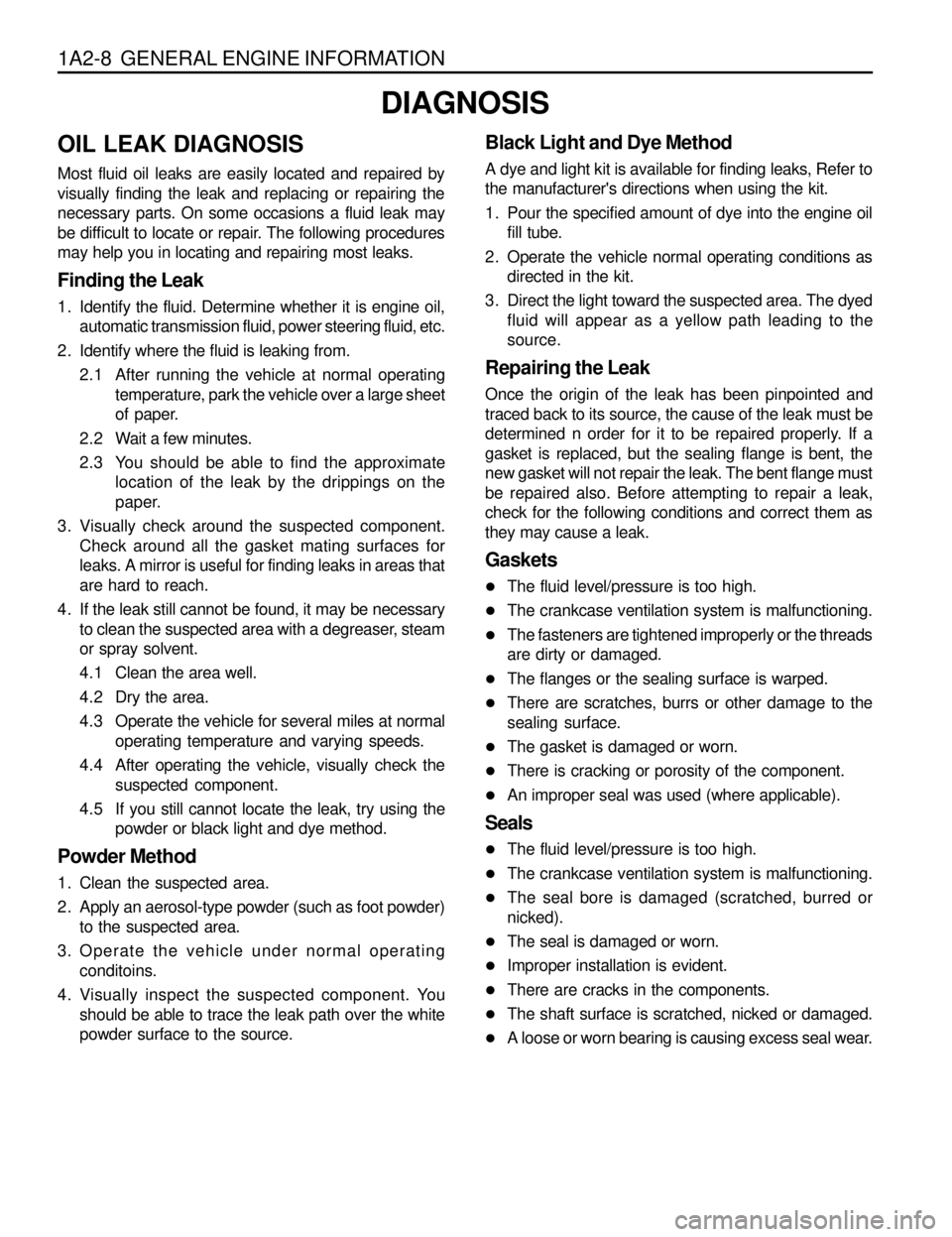
1A2-8 GENERAL ENGINE INFORMATION
OIL LEAK DIAGNOSIS
Most fluid oil leaks are easily located and repaired by
visually finding the leak and replacing or repairing the
necessary parts. On some occasions a fluid leak may
be difficult to locate or repair. The following procedures
may help you in locating and repairing most leaks.
Finding the Leak
1. Identify the fluid. Determine whether it is engine oil,
automatic transmission fluid, power steering fluid, etc.
2. Identify where the fluid is leaking from.
2.1 After running the vehicle at normal operating
temperature, park the vehicle over a large sheet
of paper.
2.2 Wait a few minutes.
2.3 You should be able to find the approximate
location of the leak by the drippings on the
paper.
3. Visually check around the suspected component.
Check around all the gasket mating surfaces for
leaks. A mirror is useful for finding leaks in areas that
are hard to reach.
4. If the leak still cannot be found, it may be necessary
to clean the suspected area with a degreaser, steam
or spray solvent.
4.1 Clean the area well.
4.2 Dry the area.
4.3 Operate the vehicle for several miles at normal
operating temperature and varying speeds.
4.4 After operating the vehicle, visually check the
suspected component.
4.5 If you still cannot locate the leak, try using the
powder or black light and dye method.
Powder Method
1. Clean the suspected area.
2. Apply an aerosol-type powder (such as foot powder)
to the suspected area.
3. Operate the vehicle under normal operating
conditoins.
4. Visually inspect the suspected component. You
should be able to trace the leak path over the white
powder surface to the source.
Black Light and Dye Method
A dye and light kit is available for finding leaks, Refer to
the manufacturer's directions when using the kit.
1. Pour the specified amount of dye into the engine oil
fill tube.
2. Operate the vehicle normal operating conditions as
directed in the kit.
3. Direct the light toward the suspected area. The dyed
fluid will appear as a yellow path leading to the
source.
Repairing the Leak
Once the origin of the leak has been pinpointed and
traced back to its source, the cause of the leak must be
determined n order for it to be repaired properly. If a
gasket is replaced, but the sealing flange is bent, the
new gasket will not repair the leak. The bent flange must
be repaired also. Before attempting to repair a leak,
check for the following conditions and correct them as
they may cause a leak.
Gaskets
lThe fluid level/pressure is too high.
lThe crankcase ventilation system is malfunctioning.
lThe fasteners are tightened improperly or the threads
are dirty or damaged.
lThe flanges or the sealing surface is warped.
lThere are scratches, burrs or other damage to the
sealing surface.
lThe gasket is damaged or worn.
lThere is cracking or porosity of the component.
lAn improper seal was used (where applicable).
Seals
lThe fluid level/pressure is too high.
lThe crankcase ventilation system is malfunctioning.
lThe seal bore is damaged (scratched, burred or
nicked).
lThe seal is damaged or worn.
lImproper installation is evident.
lThere are cracks in the components.
lThe shaft surface is scratched, nicked or damaged.
lA loose or worn bearing is causing excess seal wear.
DIAGNOSIS
Page 68 of 1463
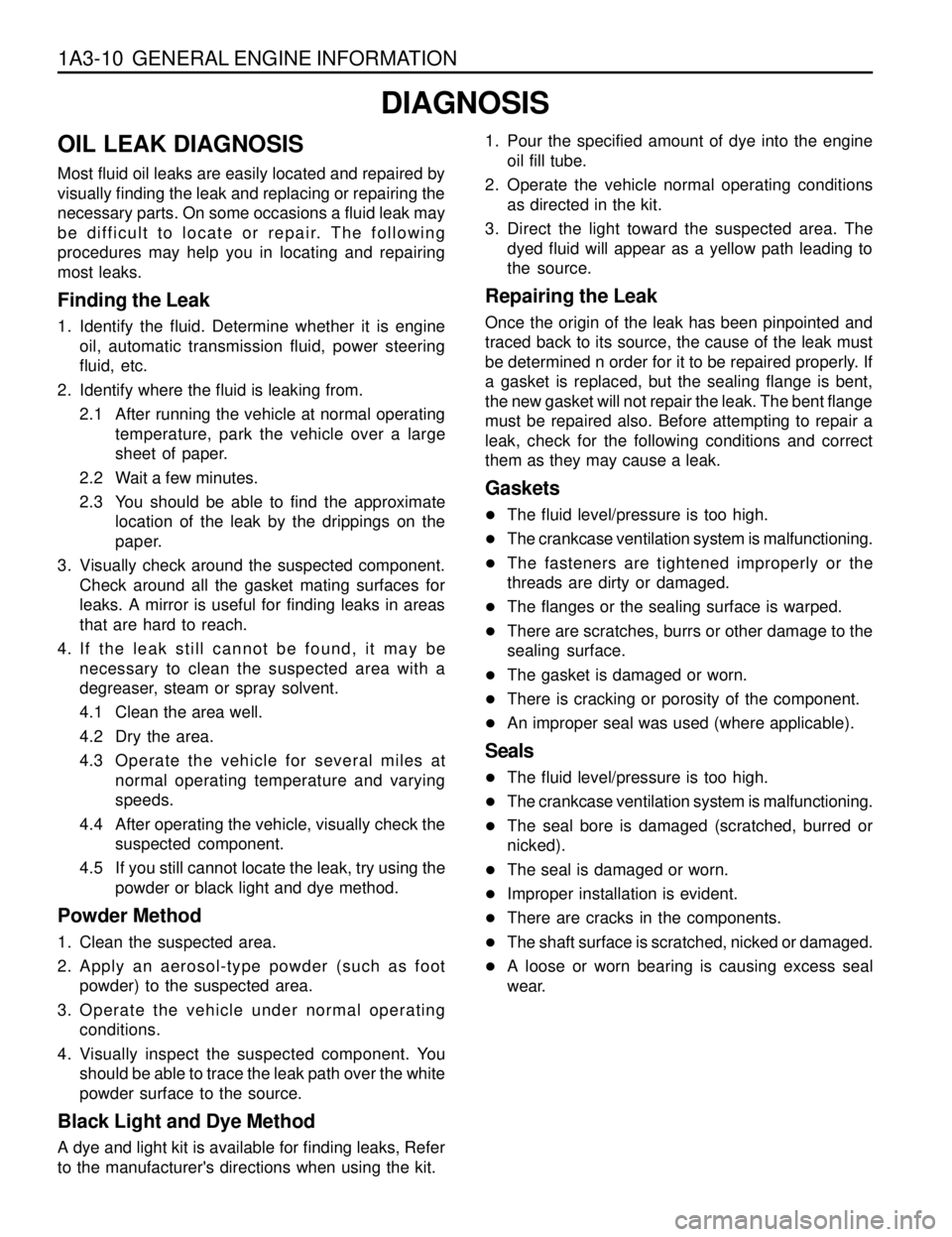
1A3-10 GENERAL ENGINE INFORMATION
OIL LEAK DIAGNOSIS
Most fluid oil leaks are easily located and repaired by
visually finding the leak and replacing or repairing the
necessary parts. On some occasions a fluid leak may
be difficult to locate or repair. The following
procedures may help you in locating and repairing
most leaks.
Finding the Leak
1. Identify the fluid. Determine whether it is engine
oil, automatic transmission fluid, power steering
fluid, etc.
2. Identify where the fluid is leaking from.
2.1 After running the vehicle at normal operating
temperature, park the vehicle over a large
sheet of paper.
2.2 Wait a few minutes.
2.3 You should be able to find the approximate
location of the leak by the drippings on the
paper.
3. Visually check around the suspected component.
Check around all the gasket mating surfaces for
leaks. A mirror is useful for finding leaks in areas
that are hard to reach.
4. If the leak still cannot be found, it may be
necessary to clean the suspected area with a
degreaser, steam or spray solvent.
4.1 Clean the area well.
4.2 Dry the area.
4.3 Operate the vehicle for several miles at
normal operating temperature and varying
speeds.
4.4 After operating the vehicle, visually check the
suspected component.
4.5 If you still cannot locate the leak, try using the
powder or black light and dye method.
Powder Method
1. Clean the suspected area.
2. Apply an aerosol-type powder (such as foot
powder) to the suspected area.
3. Operate the vehicle under normal operating
conditions.
4. Visually inspect the suspected component. You
should be able to trace the leak path over the white
powder surface to the source.
Black Light and Dye Method
A dye and light kit is available for finding leaks, Refer
to the manufacturer's directions when using the kit.1. Pour the specified amount of dye into the engine
oil fill tube.
2. Operate the vehicle normal operating conditions
as directed in the kit.
3. Direct the light toward the suspected area. The
dyed fluid will appear as a yellow path leading to
the source.
Repairing the Leak
Once the origin of the leak has been pinpointed and
traced back to its source, the cause of the leak must
be determined n order for it to be repaired properly. If
a gasket is replaced, but the sealing flange is bent,
the new gasket will not repair the leak. The bent flange
must be repaired also. Before attempting to repair a
leak, check for the following conditions and correct
them as they may cause a leak.
Gaskets
lThe fluid level/pressure is too high.
lThe crankcase ventilation system is malfunctioning.
lThe fasteners are tightened improperly or the
threads are dirty or damaged.
lThe flanges or the sealing surface is warped.
lThere are scratches, burrs or other damage to the
sealing surface.
lThe gasket is damaged or worn.
lThere is cracking or porosity of the component.
lAn improper seal was used (where applicable).
Seals
lThe fluid level/pressure is too high.
lThe crankcase ventilation system is malfunctioning.
lThe seal bore is damaged (scratched, burred or
nicked).
lThe seal is damaged or worn.
lImproper installation is evident.
lThere are cracks in the components.
lThe shaft surface is scratched, nicked or damaged.
lA loose or worn bearing is causing excess seal
wear.
DIAGNOSIS
Page 1046 of 1463
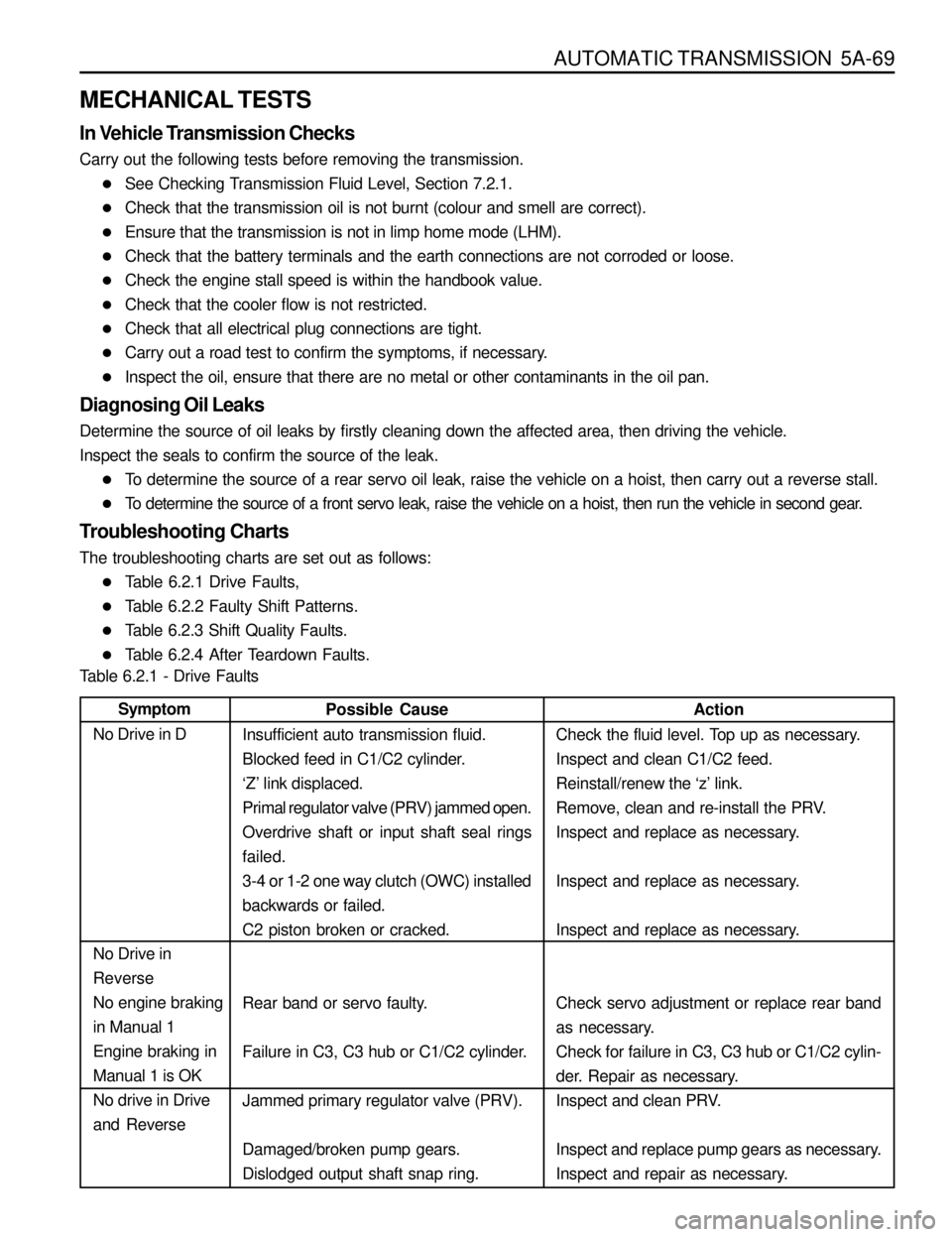
AUTOMATIC TRANSMISSION 5A-69
MECHANICAL TESTS
In Vehicle Transmission Checks
Carry out the following tests before removing the transmission.
lSee Checking Transmission Fluid Level, Section 7.2.1.
lCheck that the transmission oil is not burnt (colour and smell are correct).
lEnsure that the transmission is not in limp home mode (LHM).
lCheck that the battery terminals and the earth connections are not corroded or loose.
lCheck the engine stall speed is within the handbook value.
lCheck that the cooler flow is not restricted.
lCheck that all electrical plug connections are tight.
lCarry out a road test to confirm the symptoms, if necessary.
lInspect the oil, ensure that there are no metal or other contaminants in the oil pan.
Diagnosing Oil Leaks
Determine the source of oil leaks by firstly cleaning down the affected area, then driving the vehicle.
Inspect the seals to confirm the source of the leak.
lTo determine the source of a rear servo oil leak, raise the vehicle on a hoist, then carry out a reverse stall.
lTo determine the source of a front servo leak, raise the vehicle on a hoist, then run the vehicle in second gear.
Troubleshooting Charts
The troubleshooting charts are set out as follows:
lTable 6.2.1 Drive Faults,
lTable 6.2.2 Faulty Shift Patterns.
lTable 6.2.3 Shift Quality Faults.
lTable 6.2.4 After Teardown Faults.
Table 6.2.1 - Drive Faults
Action
Check the fluid level. Top up as necessary.
Inspect and clean C1/C2 feed.
Reinstall/renew the ‘z’ link.
Remove, clean and re-install the PRV.
Inspect and replace as necessary.
Inspect and replace as necessary.
Inspect and replace as necessary.
Check servo adjustment or replace rear band
as necessary.
Check for failure in C3, C3 hub or C1/C2 cylin-
der. Repair as necessary.
Inspect and clean PRV.
Inspect and replace pump gears as necessary.
Inspect and repair as necessary. Possible Cause
Insufficient auto transmission fluid.
Blocked feed in C1/C2 cylinder.
‘Z’ link displaced.
Primal regulator valve (PRV) jammed open.
Overdrive shaft or input shaft seal rings
failed.
3-4 or 1-2 one way clutch (OWC) installed
backwards or failed.
C2 piston broken or cracked.
Rear band or servo faulty.
Failure in C3, C3 hub or C1/C2 cylinder.
Jammed primary regulator valve (PRV).
Damaged/broken pump gears.
Dislodged output shaft snap ring.Symptom
No Drive in D
No Drive in
Reverse
No engine braking
in Manual 1
Engine braking in
Manual 1 is OK
No drive in Drive
and Reverse
Page 1049 of 1463
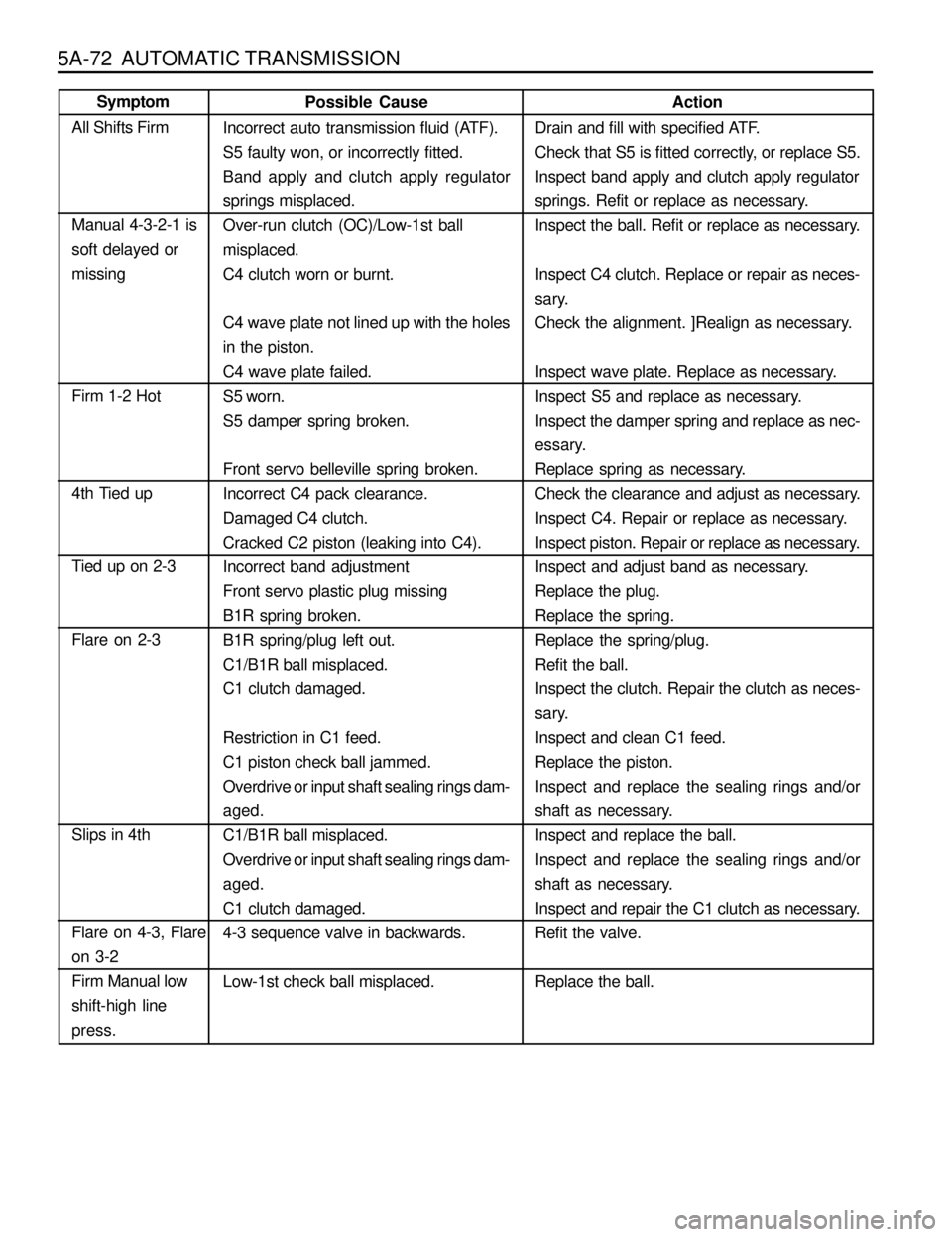
5A-72 AUTOMATIC TRANSMISSION
Action
Drain and fill with specified ATF.
Check that S5 is fitted correctly, or replace S5.
Inspect band apply and clutch apply regulator
springs. Refit or replace as necessary.
Inspect the ball. Refit or replace as necessary.
Inspect C4 clutch. Replace or repair as neces-
sary.
Check the alignment. ]Realign as necessary.
Inspect wave plate. Replace as necessary.
Inspect S5 and replace as necessary.
Inspect the damper spring and replace as nec-
essary.
Replace spring as necessary.
Check the clearance and adjust as necessary.
Inspect C4. Repair or replace as necessary.
Inspect piston. Repair or replace as necessary.
Inspect and adjust band as necessary.
Replace the plug.
Replace the spring.
Replace the spring/plug.
Refit the ball.
Inspect the clutch. Repair the clutch as neces-
sary.
Inspect and clean C1 feed.
Replace the piston.
Inspect and replace the sealing rings and/or
shaft as necessary.
Inspect and replace the ball.
Inspect and replace the sealing rings and/or
shaft as necessary.
Inspect and repair the C1 clutch as necessary.
Refit the valve.
Replace the ball. Possible Cause
Incorrect auto transmission fluid (ATF).
S5 faulty won, or incorrectly fitted.
Band apply and clutch apply regulator
springs misplaced.
Over-run clutch (OC)/Low-1st ball
misplaced.
C4 clutch worn or burnt.
C4 wave plate not lined up with the holes
in the piston.
C4 wave plate failed.
S5 worn.
S5 damper spring broken.
Front servo belleville spring broken.
Incorrect C4 pack clearance.
Damaged C4 clutch.
Cracked C2 piston (leaking into C4).
Incorrect band adjustment
Front servo plastic plug missing
B1R spring broken.
B1R spring/plug left out.
C1/B1R ball misplaced.
C1 clutch damaged.
Restriction in C1 feed.
C1 piston check ball jammed.
Overdrive or input shaft sealing rings dam-
aged.
C1/B1R ball misplaced.
Overdrive or input shaft sealing rings dam-
aged.
C1 clutch damaged.
4-3 sequence valve in backwards.
Low-1st check ball misplaced.Symptom
All Shifts Firm
Manual 4-3-2-1 is
soft delayed or
missing
Firm 1-2 Hot
4th Tied up
Tied up on 2-3
Flare on 2-3
Slips in 4th
Flare on 4-3, Flare
on 3-2
Firm Manual low
shift-high line
press.
Page 1056 of 1463
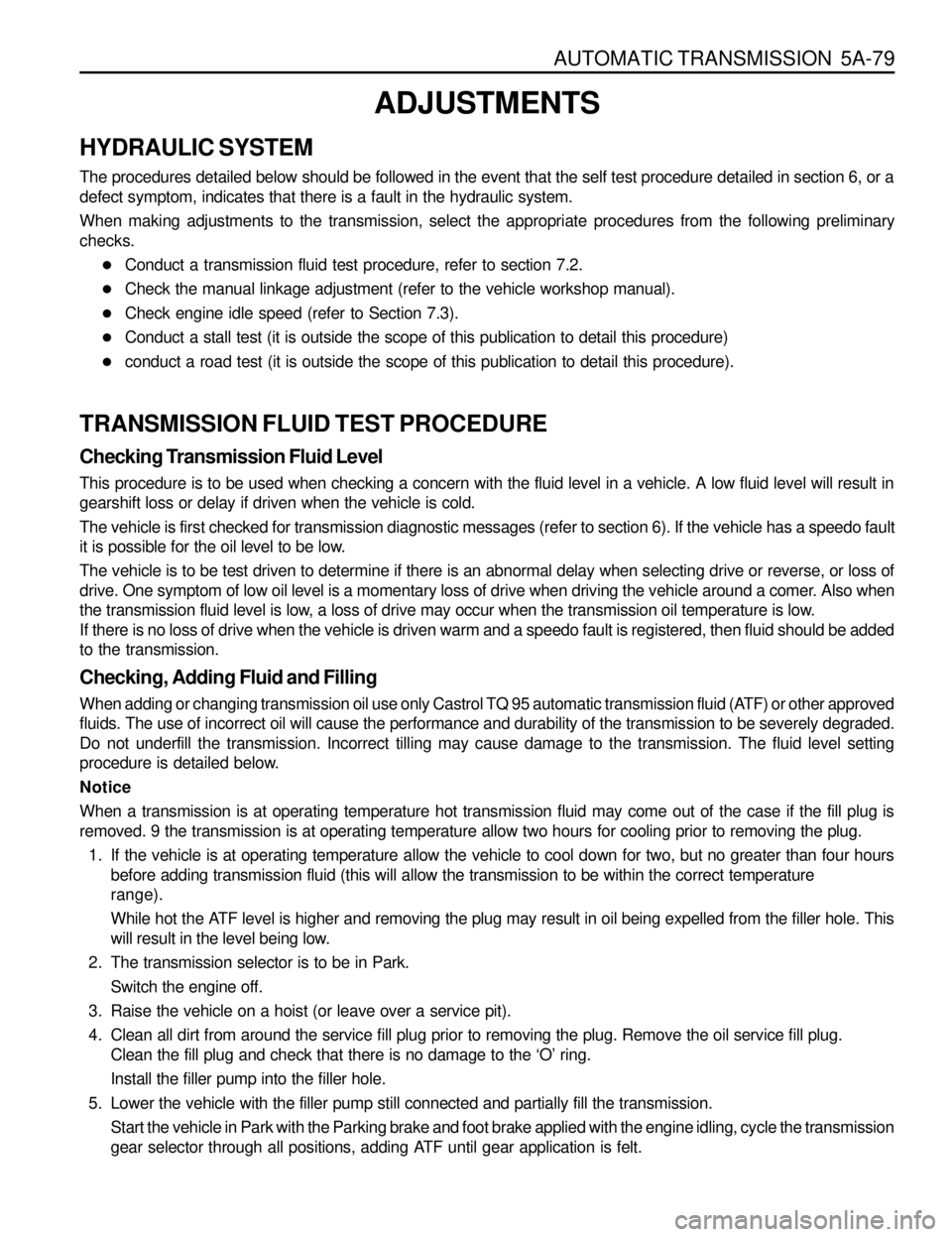
AUTOMATIC TRANSMISSION 5A-79
ADJUSTMENTS
HYDRAULIC SYSTEM
The procedures detailed below should be followed in the event that the self test procedure detailed in section 6, or a
defect symptom, indicates that there is a fault in the hydraulic system.
When making adjustments to the transmission, select the appropriate procedures from the following preliminary
checks.
lConduct a transmission fluid test procedure, refer to section 7.2.
lCheck the manual linkage adjustment (refer to the vehicle workshop manual).
lCheck engine idle speed (refer to Section 7.3).
lConduct a stall test (it is outside the scope of this publication to detail this procedure)
lconduct a road test (it is outside the scope of this publication to detail this procedure).
TRANSMISSION FLUID TEST PROCEDURE
Checking Transmission Fluid Level
This procedure is to be used when checking a concern with the fluid level in a vehicle. A low fluid level will result in
gearshift loss or delay if driven when the vehicle is cold.
The vehicle is first checked for transmission diagnostic messages (refer to section 6). If the vehicle has a speedo fault
it is possible for the oil level to be low.
The vehicle is to be test driven to determine if there is an abnormal delay when selecting drive or reverse, or loss of
drive. One symptom of low oil level is a momentary loss of drive when driving the vehicle around a comer. Also when
the transmission fluid level is low, a loss of drive may occur when the transmission oil temperature is low.
If there is no loss of drive when the vehicle is driven warm and a speedo fault is registered, then fluid should be added
to the transmission.
Checking, Adding Fluid and Filling
When adding or changing transmission oil use only Castrol TQ 95 automatic transmission fluid (ATF) or other approved
fluids. The use of incorrect oil will cause the performance and durability of the transmission to be severely degraded.
Do not underfill the transmission. Incorrect tilling may cause damage to the transmission. The fluid level setting
procedure is detailed below.
Notice
When a transmission is at operating temperature hot transmission fluid may come out of the case if the fill plug is
removed. 9 the transmission is at operating temperature allow two hours for cooling prior to removing the plug.
1. If the vehicle is at operating temperature allow the vehicle to cool down for two, but no greater than four hours
before adding transmission fluid (this will allow the transmission to be within the correct temperature
range).
While hot the ATF level is higher and removing the plug may result in oil being expelled from the filler hole. This
will result in the level being low.
2. The transmission selector is to be in Park.
Switch the engine off.
3. Raise the vehicle on a hoist (or leave over a service pit).
4. Clean all dirt from around the service fill plug prior to removing the plug. Remove the oil service fill plug.
Clean the fill plug and check that there is no damage to the ‘O’ ring.
Install the filler pump into the filler hole.
5. Lower the vehicle with the filler pump still connected and partially fill the transmission.
Start the vehicle in Park with the Parking brake and foot brake applied with the engine idling, cycle the transmission
gear selector through all positions, adding ATF until gear application is felt.
Page 1057 of 1463
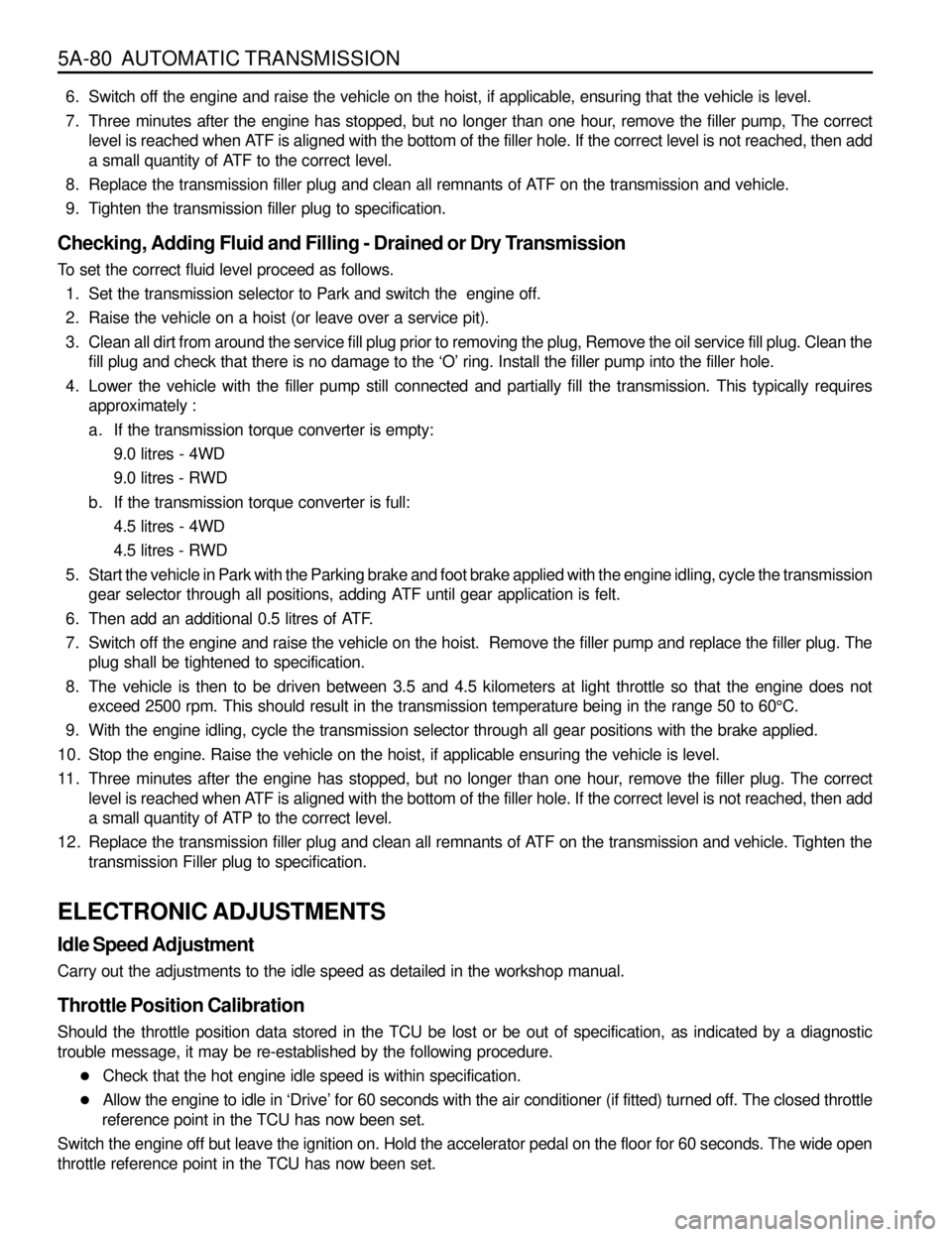
5A-80 AUTOMATIC TRANSMISSION
6. Switch off the engine and raise the vehicle on the hoist, if applicable, ensuring that the vehicle is level.
7. Three minutes after the engine has stopped, but no longer than one hour, remove the filler pump, The correct
level is reached when ATF is aligned with the bottom of the filler hole. If the correct level is not reached, then add
a small quantity of ATF to the correct level.
8. Replace the transmission filler plug and clean all remnants of ATF on the transmission and vehicle.
9. Tighten the transmission filler plug to specification.
Checking, Adding Fluid and Filling - Drained or Dry Transmission
To set the correct fluid level proceed as follows.
1. Set the transmission selector to Park and switch the engine off.
2. Raise the vehicle on a hoist (or leave over a service pit).
3. Clean all dirt from around the service fill plug prior to removing the plug, Remove the oil service fill plug. Clean the
fill plug and check that there is no damage to the ‘O’ ring. Install the filler pump into the filler hole.
4. Lower the vehicle with the filler pump still connected and partially fill the transmission. This typically requires
approximately :
a. If the transmission torque converter is empty:
9.0 litres - 4WD
9.0 litres - RWD
b. If the transmission torque converter is full:
4.5 litres - 4WD
4.5 litres - RWD
5. Start the vehicle in Park with the Parking brake and foot brake applied with the engine idling, cycle the transmission
gear selector through all positions, adding ATF until gear application is felt.
6. Then add an additional 0.5 litres of ATF.
7. Switch off the engine and raise the vehicle on the hoist. Remove the filler pump and replace the filler plug. The
plug shall be tightened to specification.
8. The vehicle is then to be driven between 3.5 and 4.5 kilometers at light throttle so that the engine does not
exceed 2500 rpm. This should result in the transmission temperature being in the range 50 to 60°C.
9. With the engine idling, cycle the transmission selector through all gear positions with the brake applied.
10. Stop the engine. Raise the vehicle on the hoist, if applicable ensuring the vehicle is level.
11. Three minutes after the engine has stopped, but no longer than one hour, remove the filler plug. The correct
level is reached when ATF is aligned with the bottom of the filler hole. If the correct level is not reached, then add
a small quantity of ATP to the correct level.
12. Replace the transmission filler plug and clean all remnants of ATF on the transmission and vehicle. Tighten the
transmission Filler plug to specification.
ELECTRONIC ADJUSTMENTS
Idle Speed Adjustment
Carry out the adjustments to the idle speed as detailed in the workshop manual.
Throttle Position Calibration
Should the throttle position data stored in the TCU be lost or be out of specification, as indicated by a diagnostic
trouble message, it may be re-established by the following procedure.
lCheck that the hot engine idle speed is within specification.
lAllow the engine to idle in ‘Drive’ for 60 seconds with the air conditioner (if fitted) turned off. The closed throttle
reference point in the TCU has now been set.
Switch the engine off but leave the ignition on. Hold the accelerator pedal on the floor for 60 seconds. The wide open
throttle reference point in the TCU has now been set.
Page 1062 of 1463
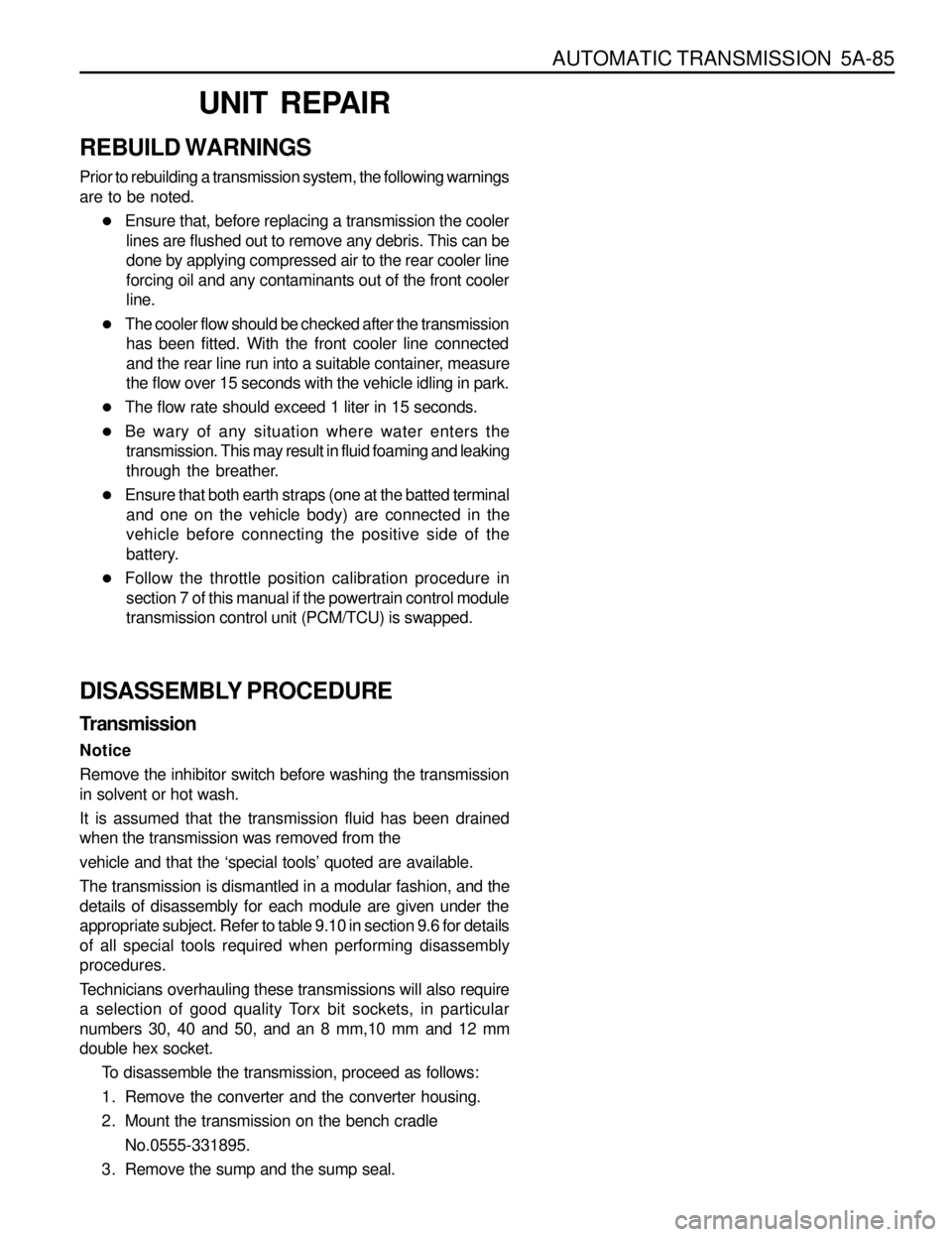
AUTOMATIC TRANSMISSION 5A-85
UNIT REPAIR
REBUILD WARNINGS
Prior to rebuilding a transmission system, the following warnings
are to be noted.
lEnsure that, before replacing a transmission the cooler
lines are flushed out to remove any debris. This can be
done by applying compressed air to the rear cooler line
forcing oil and any contaminants out of the front cooler
line.
lThe cooler flow should be checked after the transmission
has been fitted. With the front cooler line connected
and the rear line run into a suitable container, measure
the flow over 15 seconds with the vehicle idling in park.
lThe flow rate should exceed 1 liter in 15 seconds.
lBe wary of any situation where water enters the
transmission. This may result in fluid foaming and leaking
through the breather.
lEnsure that both earth straps (one at the batted terminal
and one on the vehicle body) are connected in the
vehicle before connecting the positive side of the
battery.
lFollow the throttle position calibration procedure in
section 7 of this manual if the powertrain control module
transmission control unit (PCM/TCU) is swapped.
DISASSEMBLY PROCEDURE
Transmission
Notice
Remove the inhibitor switch before washing the transmission
in solvent or hot wash.
It is assumed that the transmission fluid has been drained
when the transmission was removed from the
vehicle and that the ‘special tools’ quoted are available.
The transmission is dismantled in a modular fashion, and the
details of disassembly for each module are given under the
appropriate subject. Refer to table 9.10 in section 9.6 for details
of all special tools required when performing disassembly
procedures.
Technicians overhauling these transmissions will also require
a selection of good quality Torx bit sockets, in particular
numbers 30, 40 and 50, and an 8 mm,10 mm and 12 mm
double hex socket.
To disassemble the transmission, proceed as follows:
1. Remove the converter and the converter housing.
2. Mount the transmission on the bench cradle
No.0555-331895.
3. Remove the sump and the sump seal.
Page 1075 of 1463
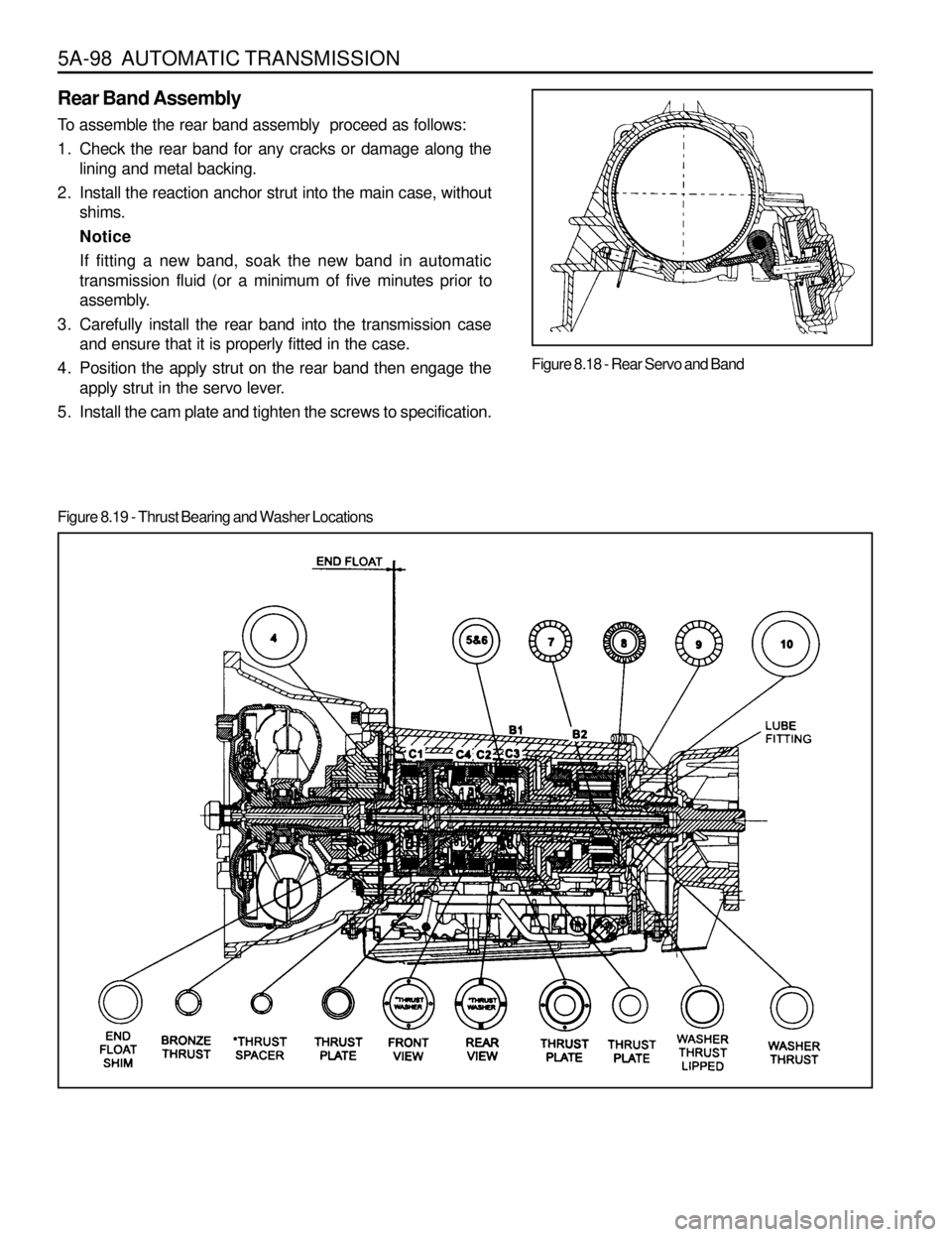
5A-98 AUTOMATIC TRANSMISSION
Rear Band Assembly
To assemble the rear band assembly proceed as follows:
1. Check the rear band for any cracks or damage along the
lining and metal backing.
2. Install the reaction anchor strut into the main case, without
shims.
Notice
If fitting a new band, soak the new band in automatic
transmission fluid (or a minimum of five minutes prior to
assembly.
3. Carefully install the rear band into the transmission case
and ensure that it is properly fitted in the case.
4. Position the apply strut on the rear band then engage the
apply strut in the servo lever.
5. Install the cam plate and tighten the screws to specification.
Figure 8.19 - Thrust Bearing and Washer LocationsFigure 8.18 - Rear Servo and Band
Page 1076 of 1463
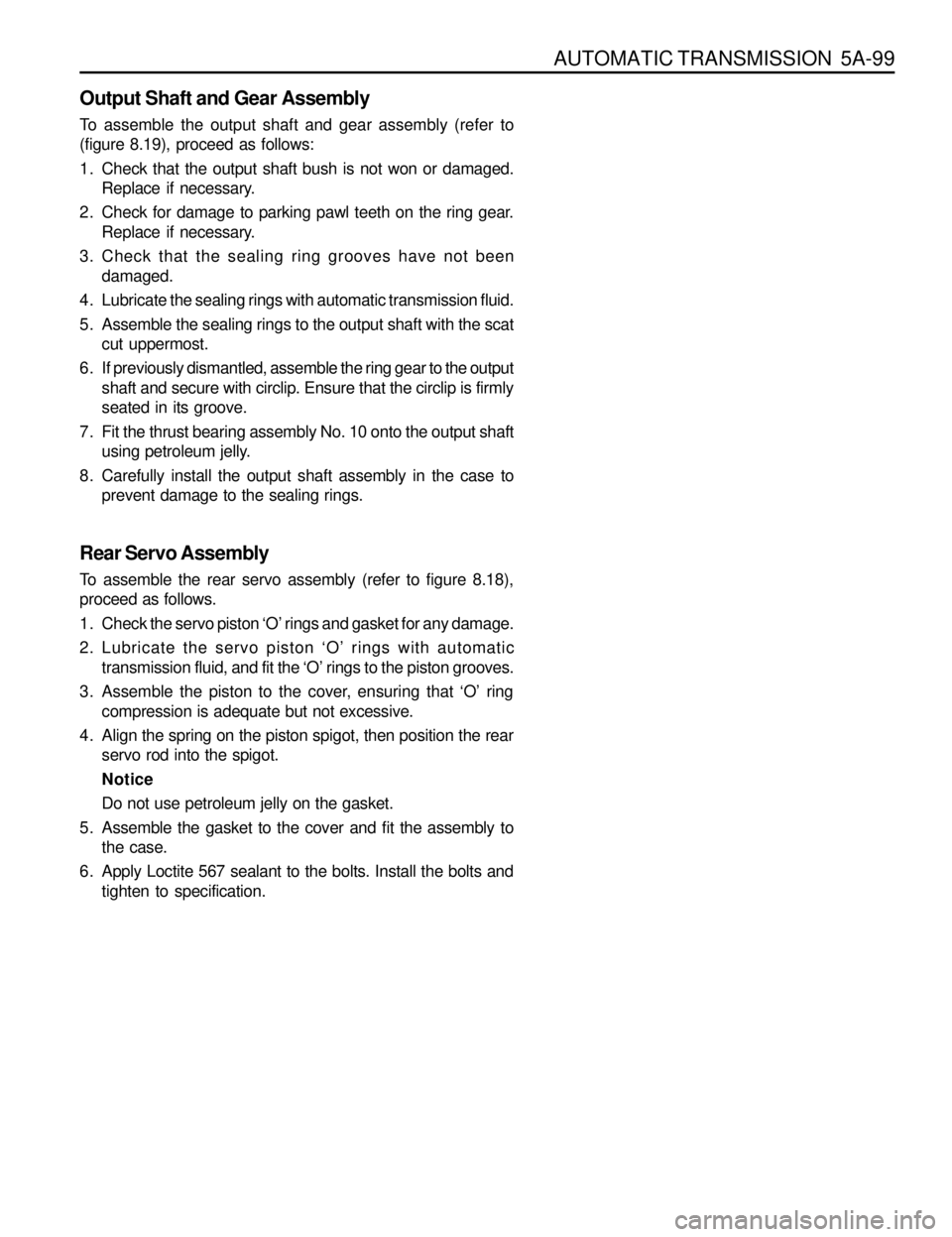
AUTOMATIC TRANSMISSION 5A-99
Output Shaft and Gear Assembly
To assemble the output shaft and gear assembly (refer to
(figure 8.19), proceed as follows:
1. Check that the output shaft bush is not won or damaged.
Replace if necessary.
2. Check for damage to parking pawl teeth on the ring gear.
Replace if necessary.
3. Check that the sealing ring grooves have not been
damaged.
4. Lubricate the sealing rings with automatic transmission fluid.
5. Assemble the sealing rings to the output shaft with the scat
cut uppermost.
6. If previously dismantled, assemble the ring gear to the output
shaft and secure with circlip. Ensure that the circlip is firmly
seated in its groove.
7. Fit the thrust bearing assembly No. 10 onto the output shaft
using petroleum jelly.
8. Carefully install the output shaft assembly in the case to
prevent damage to the sealing rings.
Rear Servo Assembly
To assemble the rear servo assembly (refer to figure 8.18),
proceed as follows.
1. Check the servo piston ‘O’ rings and gasket for any damage.
2. Lubricate the servo piston ‘O’ rings with automatic
transmission fluid, and fit the ‘O’ rings to the piston grooves.
3. Assemble the piston to the cover, ensuring that ‘O’ ring
compression is adequate but not excessive.
4. Align the spring on the piston spigot, then position the rear
servo rod into the spigot.
Notice
Do not use petroleum jelly on the gasket.
5. Assemble the gasket to the cover and fit the assembly to
the case.
6. Apply Loctite 567 sealant to the bolts. Install the bolts and
tighten to specification.