ECO mode SSANGYONG MUSSO 2003 Service Manual
[x] Cancel search | Manufacturer: SSANGYONG, Model Year: 2003, Model line: MUSSO, Model: SSANGYONG MUSSO 2003Pages: 1574, PDF Size: 26.41 MB
Page 702 of 1574
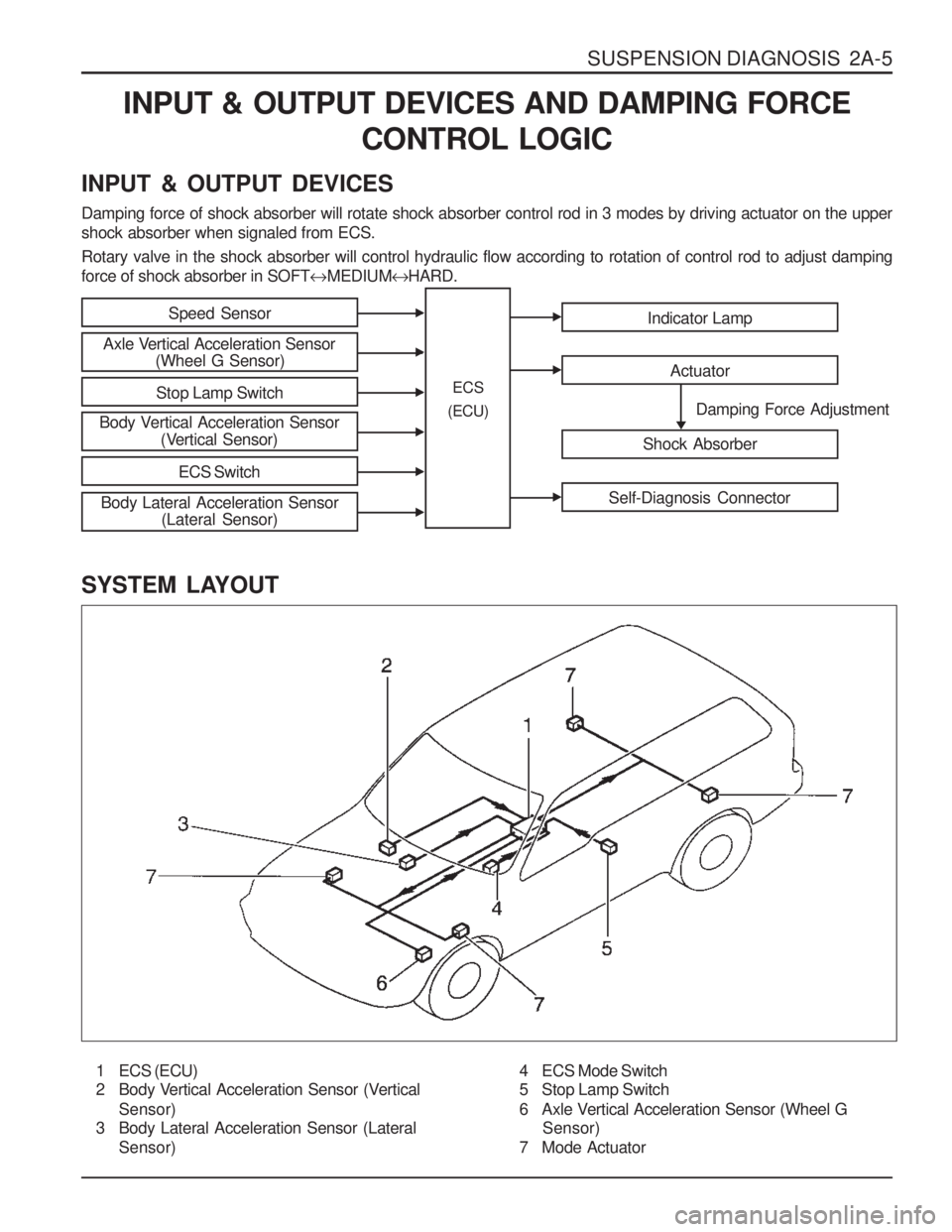
SUSPENSION DIAGNOSIS 2A-5
INPUT & OUTPUT DEVICES AND DAMPING FORCECONTROL LOGIC
INPUT & OUTPUT DEVICES Damping force of shock absorber will rotate shock absorber control rod in 3 modes by driving actuator on the upper shock absorber when signaled from ECS. Rotary valve in the shock absorber will control hydraulic flow according to rotation of control rod to adjust damping force of shock absorber in SOFT MEDIUM HARD.
SYSTEM LAYOUT
1 ECS (ECU)
2 Body Vertical Acceleration Sensor (Vertical Sensor)
3 Body Lateral Acceleration Sensor (Lateral
Sensor)
Speed Sensor
Axle Vertical Acceleration Sensor (Wheel G Sensor)
Stop Lamp Switch
Body Vertical Acceleration Sensor (Vertical Sensor)
ECS Switch
Indicator Lamp
Actuator
Shock Absorber
Self-Diagnosis Connector
Damping Force Adjustment
ECS
(ECU)
Body Lateral Acceleration Sensor (Lateral Sensor)
4 ECS Mode Switch
5 Stop Lamp Switch
6 Axle Vertical Acceleration Sensor (Wheel G
Sensor)
7 Mode Actuator
Page 703 of 1574
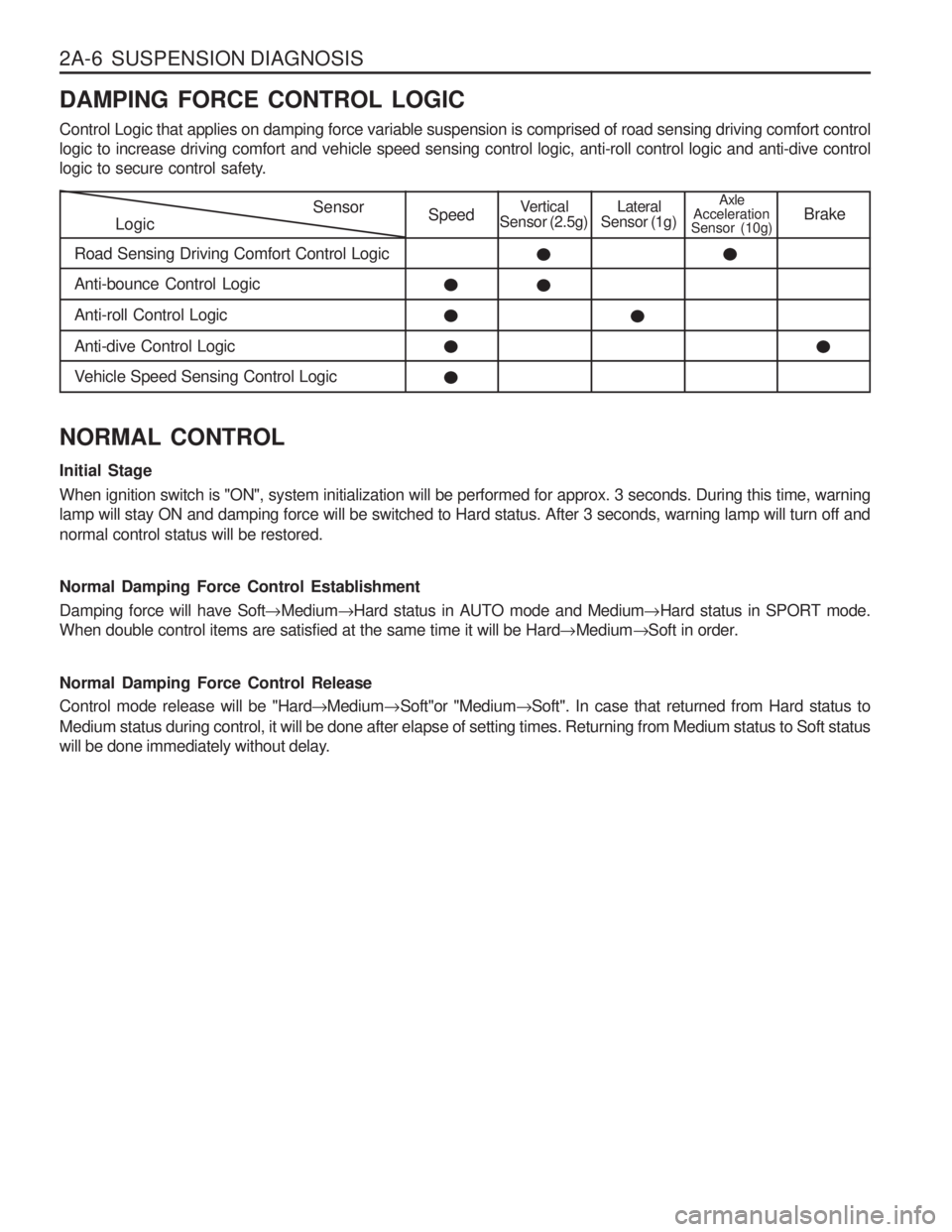
2A-6 SUSPENSION DIAGNOSIS DAMPING FORCE CONTROL LOGIC Control Logic that applies on damping force variable suspension is comprised of road sensing driving comfort control logic to increase driving comfort and vehicle speed sensing control logic, anti-roll control logic and anti-dive control
logic to secure control safety.
LogicSensor
Road Sensing Driving Comfort Control LogicSpeedVertical
Sensor (2.5g)Lateral
Sensor (1g)Axle
Acceleration
Sensor (10g) Brake
Anti-bounce Control Logic Anti-roll Control LogicAnti-dive Control Logic
Vehicle Speed Sensing Control Logic
NORMAL CONTROL Initial Stage When ignition switch is "ON", system initialization will be performed for approx. 3 seconds. During this time, warning lamp will stay ON and damping force will be switched to Hard status. After 3 seconds, warning lamp will turn off and normal control status will be restored. Normal Damping Force Control Establishment Damping force will have Soft Medium Hard status in AUTO mode and Medium Hard status in SPORT mode.
When double control items are satisfied at the same time it will be Hard Medium Soft in order.
Normal Damping Force Control Release Control mode release will be "Hard Medium Soft"or "Medium Soft". In case that returned from Hard status to
Medium status during control, it will be done after elapse of setting times. Returning from Medium status to Soft status
will be done immediately without delay.
Page 704 of 1574
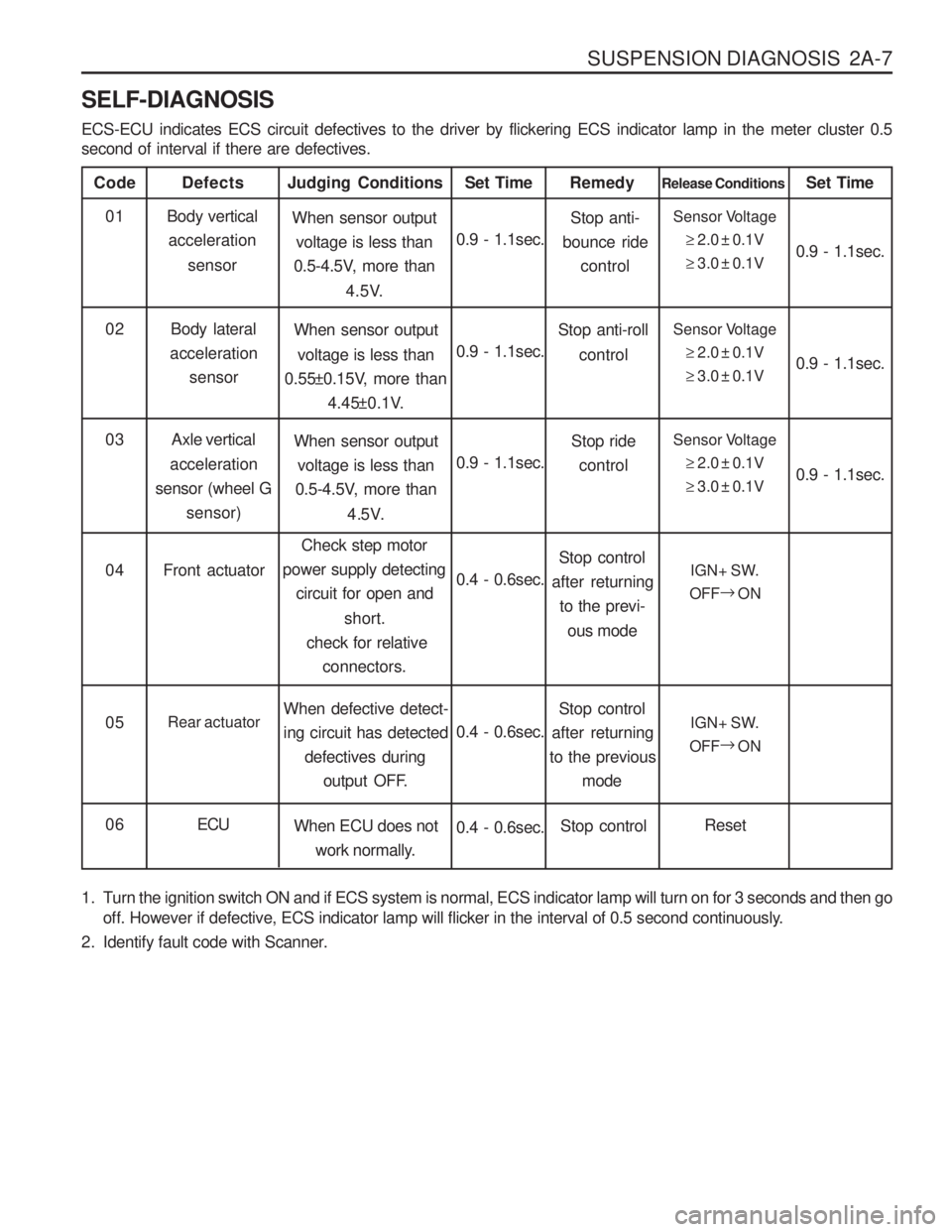
SUSPENSION DIAGNOSIS 2A-7
SELF-DIAGNOSIS ECS-ECU indicates ECS circuit defectives to the driver by flickering ECS indicator lamp in the meter cluster 0.5 second of interval if there are defectives.
Code
Body verticalacceleration
sensor
Defects
When sensor outputvoltage is less than
0.5-4.5V, more than
4.5V.
Judging Conditions01
0.9 - 1.1sec.Set TimeSensor Voltage
2.0 ± 0.1V
3.0 ± 0.1V
Release Conditions
0.9 - 1.1sec.
Set Time
Body lateral
acceleration sensor When sensor output
voltage is less than
0.55±0.15V, more than
4.45±0.1V.
02
0.9 - 1.1sec.Sensor Voltage
2.0 ± 0.1V
3.0 ± 0.1V 0.9 - 1.1sec.
Stop anti-
bounce ride
control
Remedy
Stop anti-roll control
Axle vertical
acceleration
sensor (wheel G sensor) When sensor output
voltage is less than
0.5-4.5V, more than
4.5V.
03
0.9 - 1.1sec.Sensor Voltage
2.0 ± 0.1V
3.0 ± 0.1V 0.9 - 1.1sec.
Stop ride
control
Front actuator Check step motor
power supply detecting
circuit for open and
short.
check for relative connectors.
04
0.4 - 0.6sec.IGN+ SW.
OFF
ON
Stop control
after returning to the previ-
ous mode
Rear actuator When defective detect- ing circuit has detected
defectives during
output OFF.
05
0.4 - 0.6sec.IGN+ SW.
OFF
ON
Stop control
after returning
to the previous
mode
ECU When ECU does not
work normally.
06
0.4 - 0.6sec.Reset
Stop control
1. Turn the ignition switch ON and if ECS system is normal, ECS indicator lamp will turn on for 3 seconds and then go off. However if defective, ECS indicator lamp will flicker in the interval of 0.5 second continuously.
2. Identify fault code with Scanner.
Page 861 of 1574
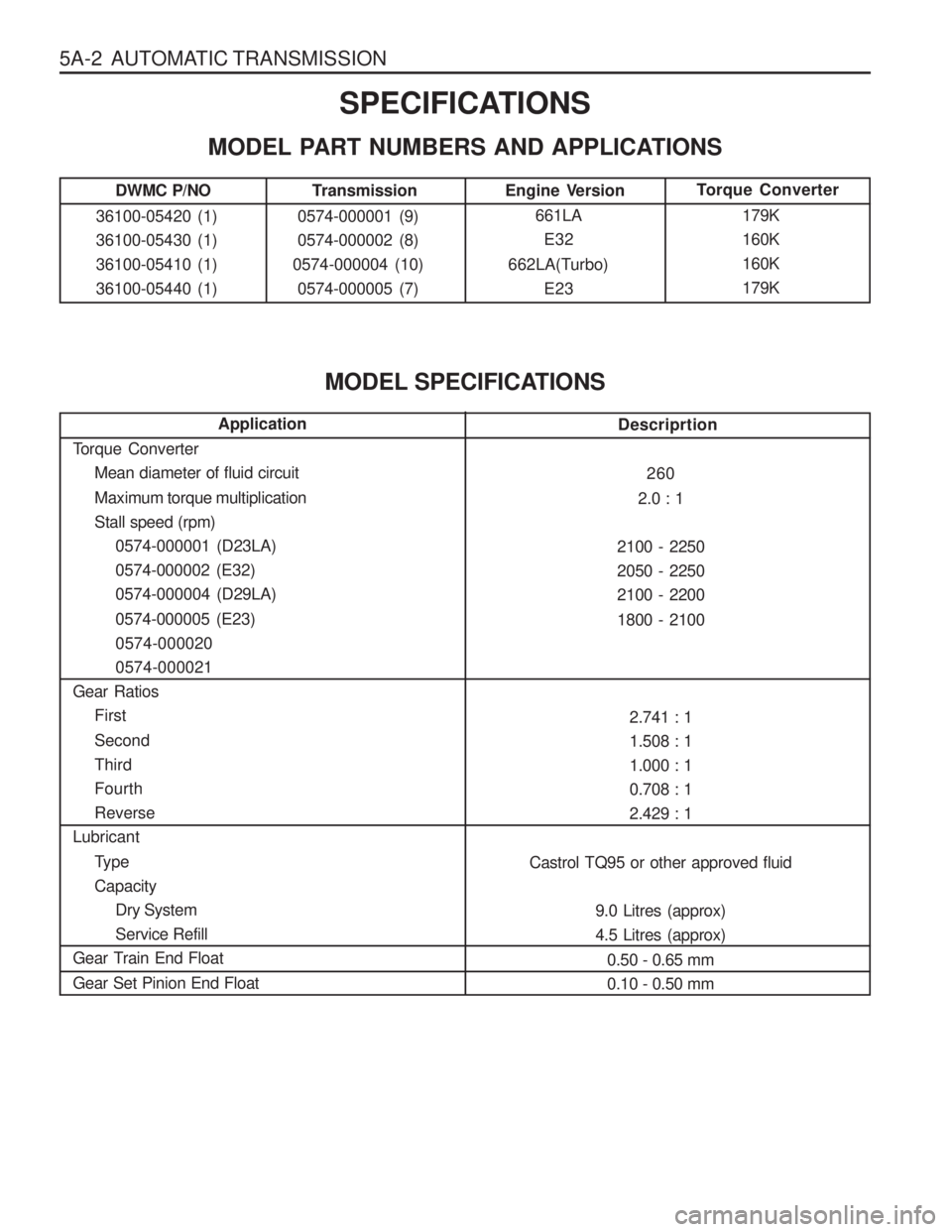
5A-2 AUTOMATIC TRANSMISSIONSPECIFICATIONS
MODEL PART NUMBERS AND APPLICATIONS
Transmission
0574-000001 (9) 0574-000002 (8)
0574-000004 (10) 0574-000005 (7) Torque Converter
179K160K160K179KEngine Version661LAE32
662LA(Turbo) E23
MODEL SPECIFICATIONS
Application
Torque Converter Mean diameter of fluid circuit Maximum torque multiplication Stall speed (rpm)0574-000001 (D23LA)0574-000002 (E32)0574-000004 (D29LA) 0574-000005 (E23) 0574-0000200574-000021
Gear Ratios First Second ThirdFourthReverse
Lubricant
TypeCapacityDry SystemService Refill
Gear Train End Float Gear Set Pinion End FloatDescriprtion
260
2.0 : 1
2100 - 2250 2050 - 22502100 - 2200 1800 - 2100
2.741 : 1 1.508 : 11.000 : 10.708 : 12.429 : 1
Castrol TQ95 or other approved fluid 9.0 Litres (approx)4.5 Litres (approx)0.50 - 0.65 mm0.10 - 0.50 mm
DWMC P/NO
36100-05420 (1)36100-05430 (1)36100-05410 (1)36100-05440 (1)
Page 877 of 1574
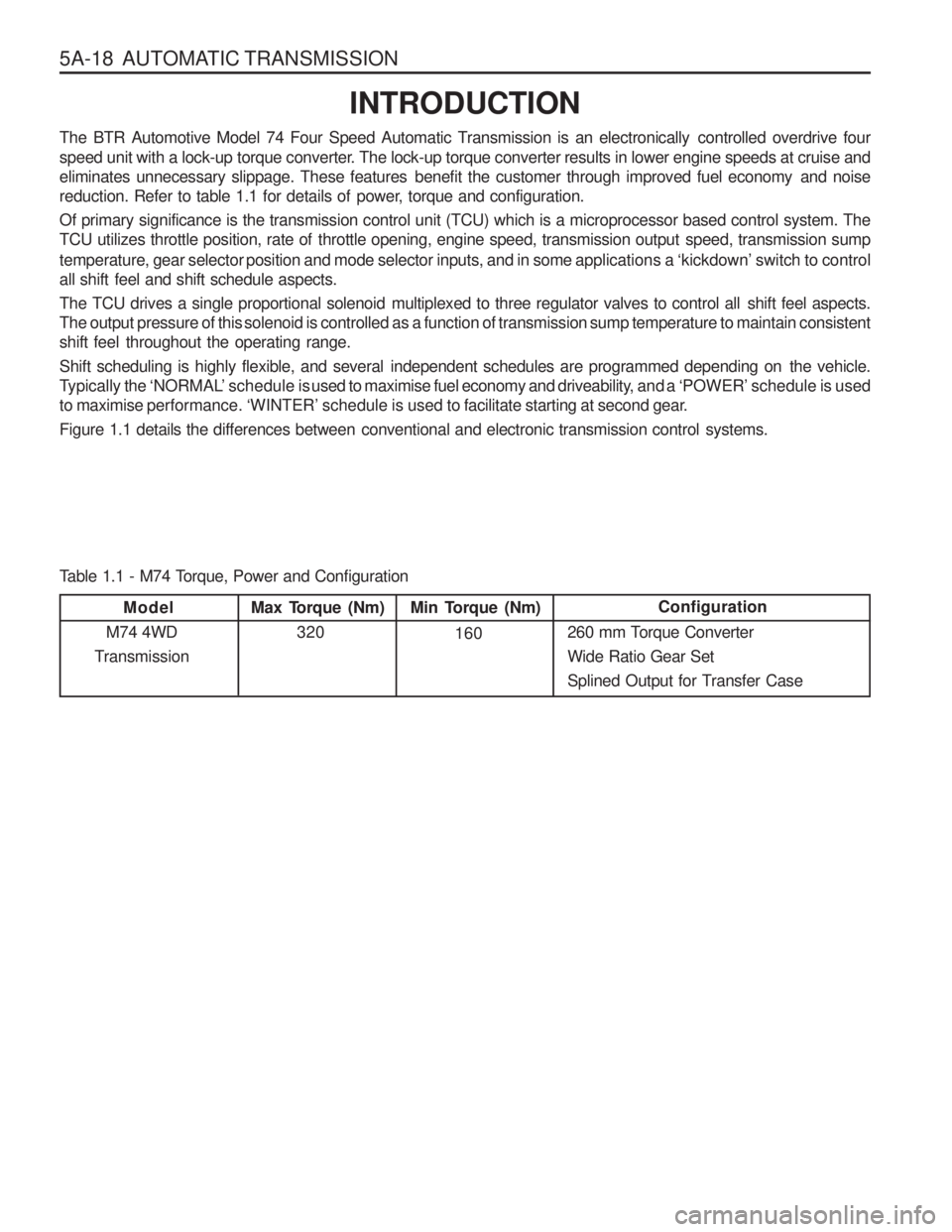
5A-18 AUTOMATIC TRANSMISSIONINTRODUCTION
The BTR Automotive Model 74 Four Speed Automatic Transmission is an electronically controlled overdrive four
speed unit with a lock-up torque converter. The lock-up torque converter results in lower engine speeds at cruise and
eliminates unnecessary slippage. These features benefit the customer through improved fuel economy and noise
reduction. Refer to table 1.1 for details of power, torque and configuration.
Of primary significance is the transmission control unit (TCU) which is a microprocessor based control system. The
TCU utilizes throttle position, rate of throttle opening, engine speed, transmission output speed, transmission sump
temperature, gear selector position and mode selector inputs, and in some applications a ‘kickdown’ switch to control
all shift feel and shift schedule aspects.
The TCU drives a single proportional solenoid multiplexed to three regulator valves to control all shift feel aspects.
The output pressure of this solenoid is controlled as a function of transmission sump temperature to maintain consistent
shift feel throughout the operating range.
Shift scheduling is highly flexible, and several independent schedules are programmed depending on the vehicle.
Typically the ‘NORMAL’ schedule is used to maximise fuel economy and driveability, and a ‘POWER’ schedule is used
to maximise performance. ‘WINTER’ schedule is used to facilitate starting at second gear.
Figure 1.1 details the differences between conventional and electronic transmission control systems.
Max Torque (Nm)
320 Configuration
260 mm Torque Converter Wide Ratio Gear Set
Splined Output for Transfer CaseMin Torque (Nm) 160
Model
M74 4WD
Transmission
Table 1.1 - M74 Torque, Power and Configuration
Page 880 of 1574
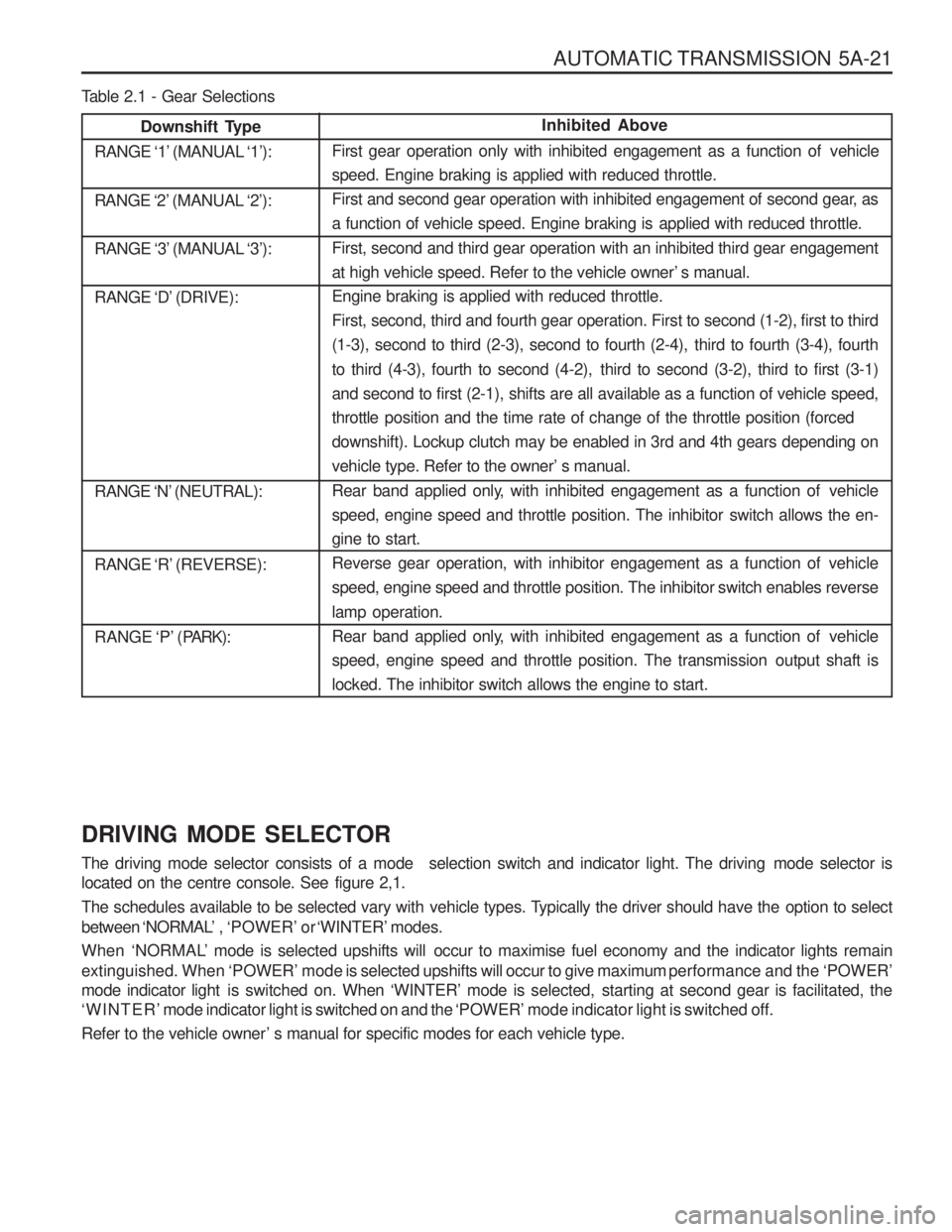
AUTOMATIC TRANSMISSION 5A-21
Downshift Type
RANGE ‘1’ (MANUAL ‘1’):
RANGE ‘2’ (MANUAL ‘2’):
RANGE ‘3’ (MANUAL ‘3’):
RANGE ‘D’ (DRIVE):
RANGE ‘N’ (NEUTRAL):
RANGE ‘R’ (REVERSE):
RANGE ‘P’ (P ARK):Inhibited Above
First gear operation only with inhibited engagement as a function of vehicle speed. Engine braking is applied with reduced throttle.
First and second gear operation with inhibited engagement of second gear, as
a function of vehicle speed. Engine braking is applied with reduced throttle.
First, second and third gear operation with an inhibited third gear engagement
at high vehicle speed. Refer to the vehicle owner’ s manual.Engine braking is applied with reduced throttle.
First, second, third and fourth gear operation. First to second (1-2), first to third
(1-3), second to third (2-3), second to fourth (2-4), third to fourth (3-4), fourth
to third (4-3), fourth to second (4-2), third to second (3-2), third to first (3-1)
and second to first (2-1), shifts are all available as a function of vehicle speed,throttle position and the time rate of change of the throttle position (forced
downshift). Lockup clutch may be enabled in 3rd and 4th gears depending on
vehicle type. Refer to the owner’ s manual.
Rear band applied only, with inhibited engagement as a function of vehicle
speed, engine speed and throttle position. The inhibitor switch allows the en-gine to start.
Reverse gear operation, with inhibitor engagement as a function of vehicle
speed, engine speed and throttle position. The inhibitor switch enables reverse lamp operation.
Rear band applied only, with inhibited engagement as a function of vehicle
speed, engine speed and throttle position. The transmission output shaft is
locked. The inhibitor switch allows the engine to start.
Table 2.1 - Gear Selections DRIVING MODE SELECTOR
The driving mode selector consists of a mode selection switch and indicator light. The driving mode selector is
located on the centre console. See figure 2,1.
The schedules available to be selected vary with vehicle types. Typically the driver should have the option to select
between ‘NORMAL’ , ‘POWER’ or ‘WINTER’ modes.
When ‘NORMAL’ mode is selected upshifts will occur to maximise fuel economy and the indicator lights remain
extinguished. When ‘POWER’ mode is selected upshifts will occur to give maximum performance and the ‘POWER’
mode indicator light is swi tched on. When ‘WINTER’ mode is selected, starting at second gear is facilitated, the
‘WINTER’ mode indicator light is switched on and the ‘POWER’ mode indicator light is switched off.
Refer to the vehicle owner ’ s manual for specific modes for each vehicle type.
Page 883 of 1574
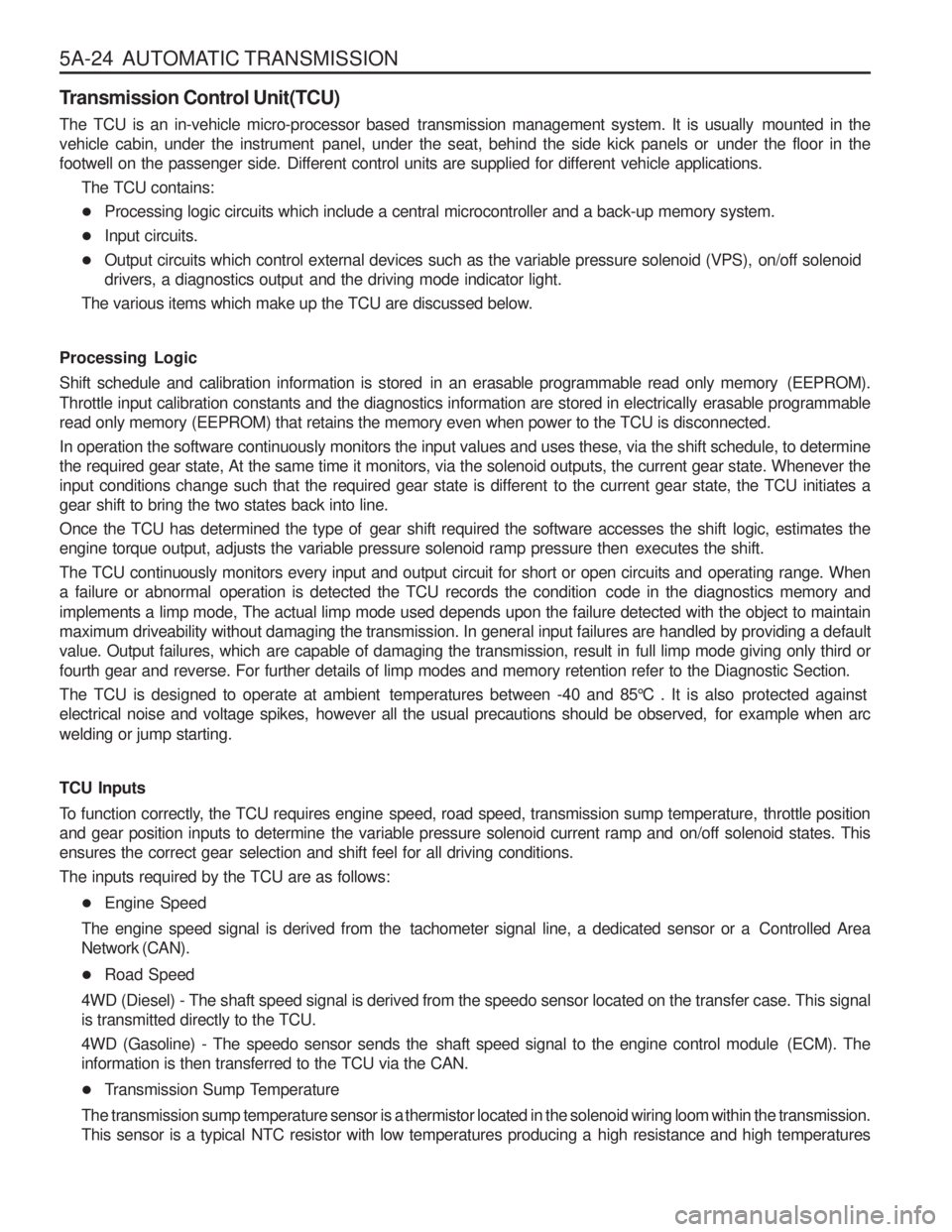
5A-24 AUTOMATIC TRANSMISSION
Transmission Control Unit(TCU)
The TCU is an in-vehicle micro-processor based transmission management system. It is usually mounted in the
vehicle cabin, under the instrument panel, under the seat, behind the side kick panels or under the floor in the
footwell on the passenger side. Different control units are supplied for different vehicle applications.The TCU contains:
Processing logic circuits which include a central microcontroller and a back-up memory system.
Input circuits.
Output circuits which control external devices such as the variable pressure solenoid (VPS), on/off solenoid
drivers, a diagnostics output and the driving mode indicator light.
The various items which make up the TCU are discussed below.
Processing Logic
Shift schedule and calibration information is stored in an erasable programmable read only memory (EEPROM).
Throttle input calibration constants and the diagnostics information are stored in electrically erasable programmable
read only memory (EEPROM) that retains the memory even when power to the TCU is disconnected. In operation the software continuously monitors the input values and uses these, via the shift schedule, to determine the required gear state, At the same time it monitors, via the solenoid outputs, the current gear state. Whenever the
input conditions change such that the required gear state is different to the current gear state, the TCU initiates a
gear shift to bring the two states back into line.
Once the TCU has determined the type of gear shift required the software accesses the shift logic, estimates the
engine torque output, adjusts the variable pressure solenoid ramp pressure then executes the shift.
The TCU continuously monitors every input and output circuit for short or open circuits and operating range. When
a failure or abnormal operation is detected the TCU records the condition code in the diagnostics memory and
implements a limp mode, The actual limp mode used depends upon the failure detected with the object to maintain
maximum driveability without damaging the transmission. In general input failures are handled by providing a default
value. Output failures, which are capable of damaging the transmission, result in full limp mode giving only third or
fourth gear and reverse. For further details of limp modes and memory retention refer to the Diagnostic Section.
The TCU is designed to operate at ambient temperatures between -40 and 85°C . It is also protected against
electrical noise and voltage spikes, however all the usual precautions should be observed, for example when arc welding or jump starting. TCU Inputs
To function correctly, the TCU requires engine speed, road speed, transmission sump temperature, throttle position
and gear position inputs to determine the variable pressure solenoid current ramp and on/off solenoid states. This
ensures the correct gear selection and shift feel for all driving conditions. The inputs required by the TCU are as follows: Engine Speed
The engine speed signal is derived from the tachometer signal line, a dedicated sensor or a Controlled Area Network (CAN).
Road Speed
4WD (Diesel) - The shaft speed signal is derived from the speedo sensor located on the transfer case. This signal is transmitted directly to the TCU.
4WD (Gasoline) - The speedo sensor sends the shaft speed signal to the engine control module (ECM). The
information is then transferred to the TCU via the CAN.
Transmission Sump Temperature
The transmission sump temperature sensor is a thermistor located in the solenoid wiring loom within the transmission.
This sensor is a typical NTC resistor with low temperatures producing a high resistance and high temperatures
Page 886 of 1574
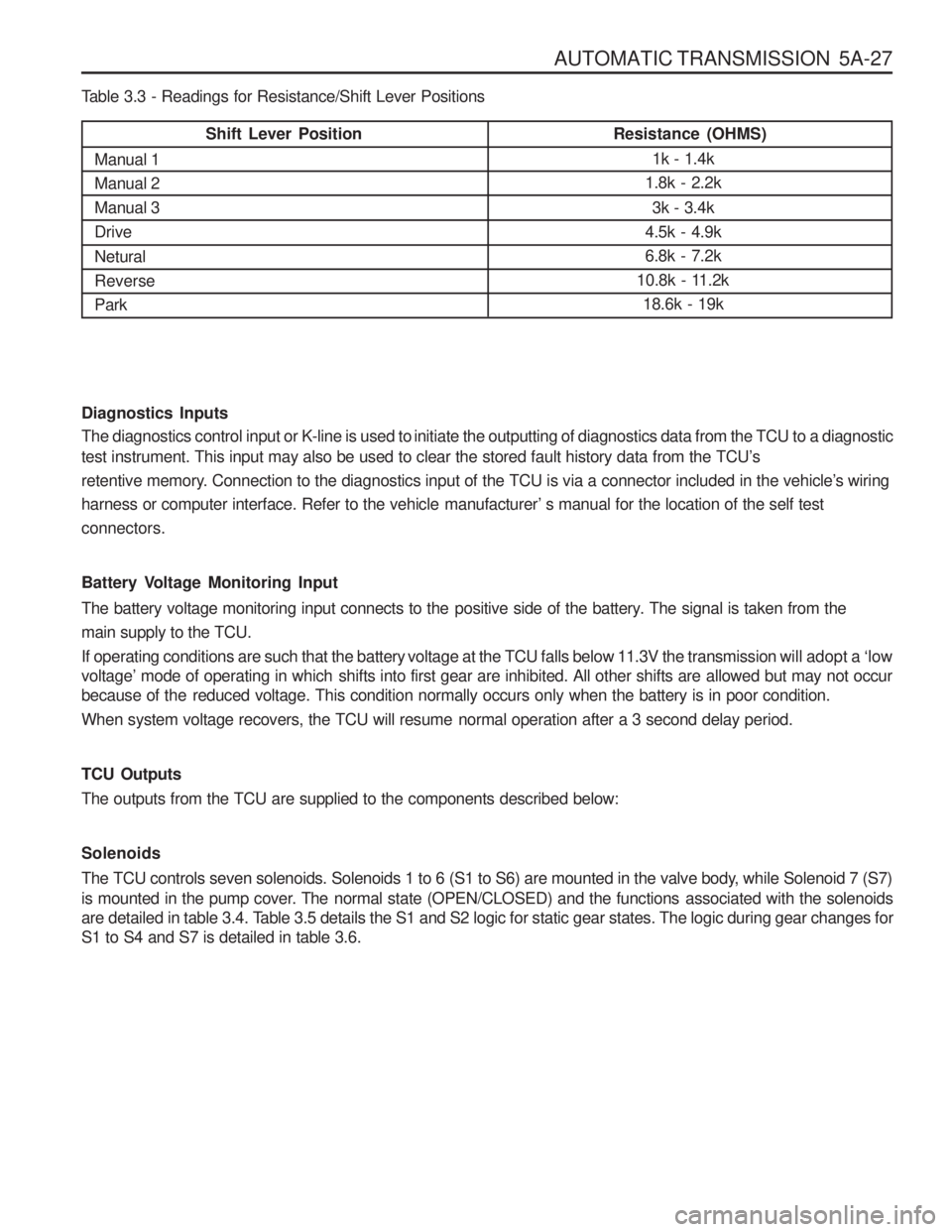
AUTOMATIC TRANSMISSION 5A-27
Shift Lever Position
Manual 1 Manual 2Manual 3Drive Netural ReverseParkResistance (OHMS) 1k - 1.4k
1.8k - 2.2k
3k - 3.4k
4.5k - 4.9k 6.8k - 7.2k
10.8k - 11.2k 18.6k - 19k
Table 3.3 - Readings for Resistance/Shift Lever Positions Diagnostics Inputs
The diagnostics control input or K-line is used to initiate the outputting of diagnostics data from the TCU to a diagnostic
test instrument. This input may also be used to clear the stored fault history data from the TCU’s
retentive memory. Connection to the diagnostics input of the TCU is via a connector included in the vehicle’s wiring
harness or computer interface. Refer to the vehicle manufacturer’ s manual for the location of the self test connectors.
Battery Voltage Monitoring Input
The battery voltage monitoring input connects to the positive side of the battery. The signal is taken from the main supply to the TCU.
If operating conditions are such that the battery voltage at the TCU falls below 11.3V the transmission will adopt a ‘low
voltage’ mode of operating in which shifts into first gear are inhibited. All other shifts are allowed but may not occur
because of the reduced voltage. This condition normally occurs only when the battery is in poor condition.
When system voltage recovers, the TCU will resume normal operation after a 3 second delay period. TCU Outputs
The outputs from the TCU are supplied to the components described below: Solenoids
The TCU controls seven solenoids. Solenoids 1 to 6 (S1 to S6) are mounted in the valve body, while Solenoid 7 (S7)
is mounted in the pump cover. The normal state (OPEN/CLOSED) and the functions associated with the solenoids
are detailed in table 3.4. Table 3.5 details the S1 and S2 logic for static gear states. The logic during gear changes for
S1 to S4 and S7 is detailed in table 3.6.
Page 890 of 1574
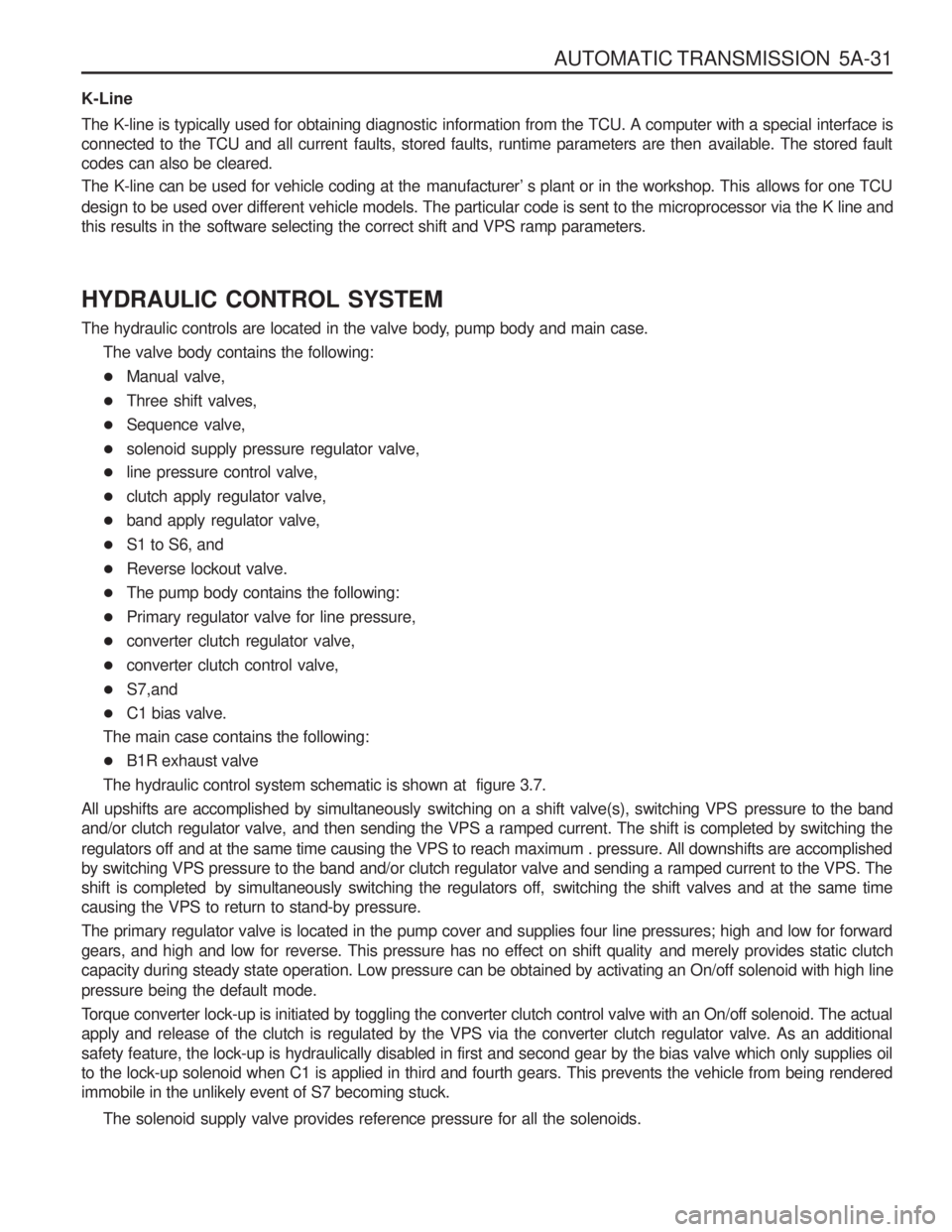
AUTOMATIC TRANSMISSION 5A-31
K-Line
The K-line is typically used for obtaining diagnostic information from the TCU. A computer with a special interface is
connected to the TCU and all current faults, stored faults, runtime parameters are then available. The stored faultcodes can also be cleared.
The K-line can be used for vehicle coding at the manufacturer’ s plant or in the workshop. This allows for one TCU
design to be used over different vehicle models. The particular code is sent to the microprocessor via the K line and
this results in the software selecting the correct shift and VPS ramp parameters. HYDRAULIC CONTROL SYSTEM
The hydraulic controls are located in the valve body, pump body and main case.The valve body contains the following:
Manual valve,
Three shift valves,
Sequence valve,
solenoid supply pressure regulator valve,
line pressure control valve,
clutch apply regulator valve,
band apply regulator valve,
S1 to S6, and
Reverse lockout valve.
The pump body contains the following:
Primary regulator valve for line pressure,
converter clutch regulator valve,
converter clutch control valve,
S7,and
C1 bias valve.
The main case contains the following:
B1R exhaust valve
The hydraulic control system schematic is shown at figure 3.7.
All upshifts are accomplished by simultaneously switching on a shift valve(s), switching VPS pressure to the band
and/or clutch regulator valve, and then sending the VPS a ramped current. The shift is completed by switching the
regulators off and at the same time causing the VPS to reach maximum . pressure. All downshifts are accomplished
by switching VPS pressure to the band and/or clutch regulator valve and sending a ramped current to the VPS. The
shift is completed by simultaneously switching the regulators off, switching the shift valves and at the same timecausing the VPS to return to stand-by pressure.
The primary regulator valve is located in the pump cover and supplies four line pressures; high and low for forward
gears, and high and low for reverse. This pressure has no effect on shift quality and merely provides static clutch
capacity during steady state operation. Low pressure can be obtained by activating an On/off solenoid with high line pressure being the default mode.
Torque converter lock-up is initiated by toggling the converter clutch control valve with an On/off solenoid. The actual apply and release of the clutch is regulated by the VPS via the converter clutch regulator valve. As an additionalsafety feature, the lock-up is hydraulically disabled in first and second gear by the bias valve which only supplies oilto the lock-up solenoid when C1 is applied in third and fourth gears. This prevents the vehicle from being renderedimmobile in the unlikely event of S7 becoming stuck.
The solenoid supply valve provides reference pressure for all the solenoids.
Page 919 of 1574
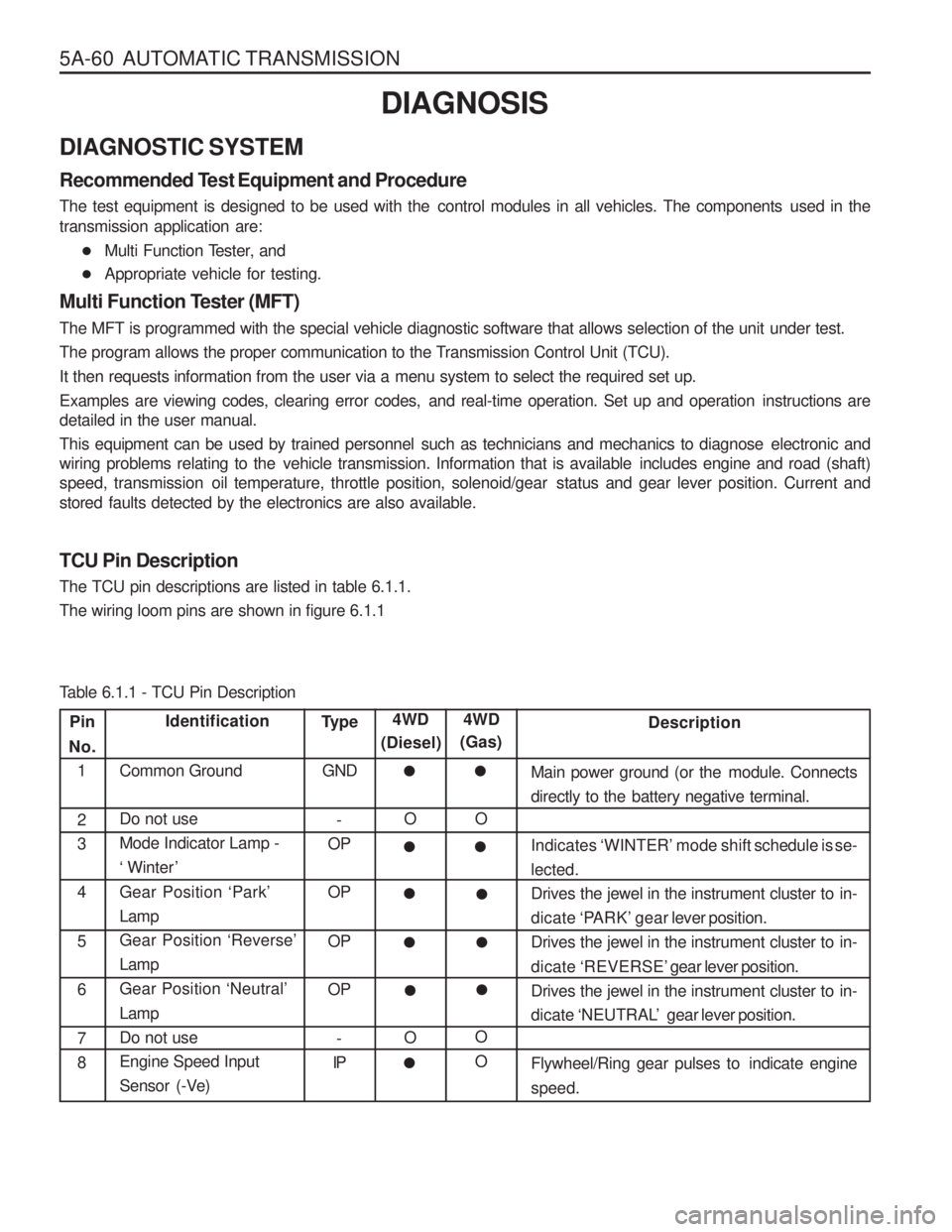
5A-60 AUTOMATIC TRANSMISSIONDIAGNOSIS
DIAGNOSTIC SYSTEM Recommended T est Equipment and Procedure
The test equipment is designed to be used with the control modules in all vehicles. The components used in the transmission application are: Multi Function Tester, and
Appropriate vehicle for testing.
Multi Function Tester (MFT)
The MFT is programmed with the special vehicle diagnostic software that allows selection of the unit under test.
The program allows the proper communication to the Transmission Control Unit (TCU).
It then requests information from the user via a menu system to select the required set up.
Examples are viewing codes, clearing error codes, and real-time operation. Set up and operation instructions are detailed in the user manual.
This equipment can be used by trained personnel such as technicians and mechanics to diagnose electronic and
wiring problems relating to the vehicle transmission. Information that is available includes engine and road (shaft)
speed, transmission oil temperature, throttle position, solenoid/gear status and gear lever position. Current andstored faults detected by the electronics are also available.
TCU Pin Description The TCU pin descriptions are listed in table 6.1.1. The wiring loom pins are shown in figure 6.1.1
Pin
No. 1 2 3 4 5 6 7 8Identification
Common Ground Do not use Mode Indicator Lamp -‘ Winter ’
Gear Position ‘Park ’
LampGear Position ‘Reverse ’
LampGear Position ‘Neutral ’
LampDo not useEngine Speed Input
Sensor (-Ve) Type
GND -
OP OP OP OP
-
IP Description
Main power ground (or the module. Connects
directly to the battery negative terminal. Indicates ‘WINTER ’ mode shift schedule is se-
lected.
Drives the jewel in the instrument cluster to in-dicate ‘PARK ’ gear lever position.
Drives the jewel in the instrument cluster to in- dicate ‘REVERSE ’ gear lever position.
Drives the jewel in the instrument cluster to in- dicate ‘NEUTRAL ’ gear lever position.
Flywheel/Ring gear pulses to indicate engine speed.
4WD
(Diesel)
O O
4WD
(Gas)
O O O
Table 6.1.1 - TCU Pin Description