wheel SSANGYONG RODIUS 2005 Workshop Manual
[x] Cancel search | Manufacturer: SSANGYONG, Model Year: 2005, Model line: RODIUS, Model: SSANGYONG RODIUS 2005Pages: 502, PDF Size: 70.43 MB
Page 274 of 502
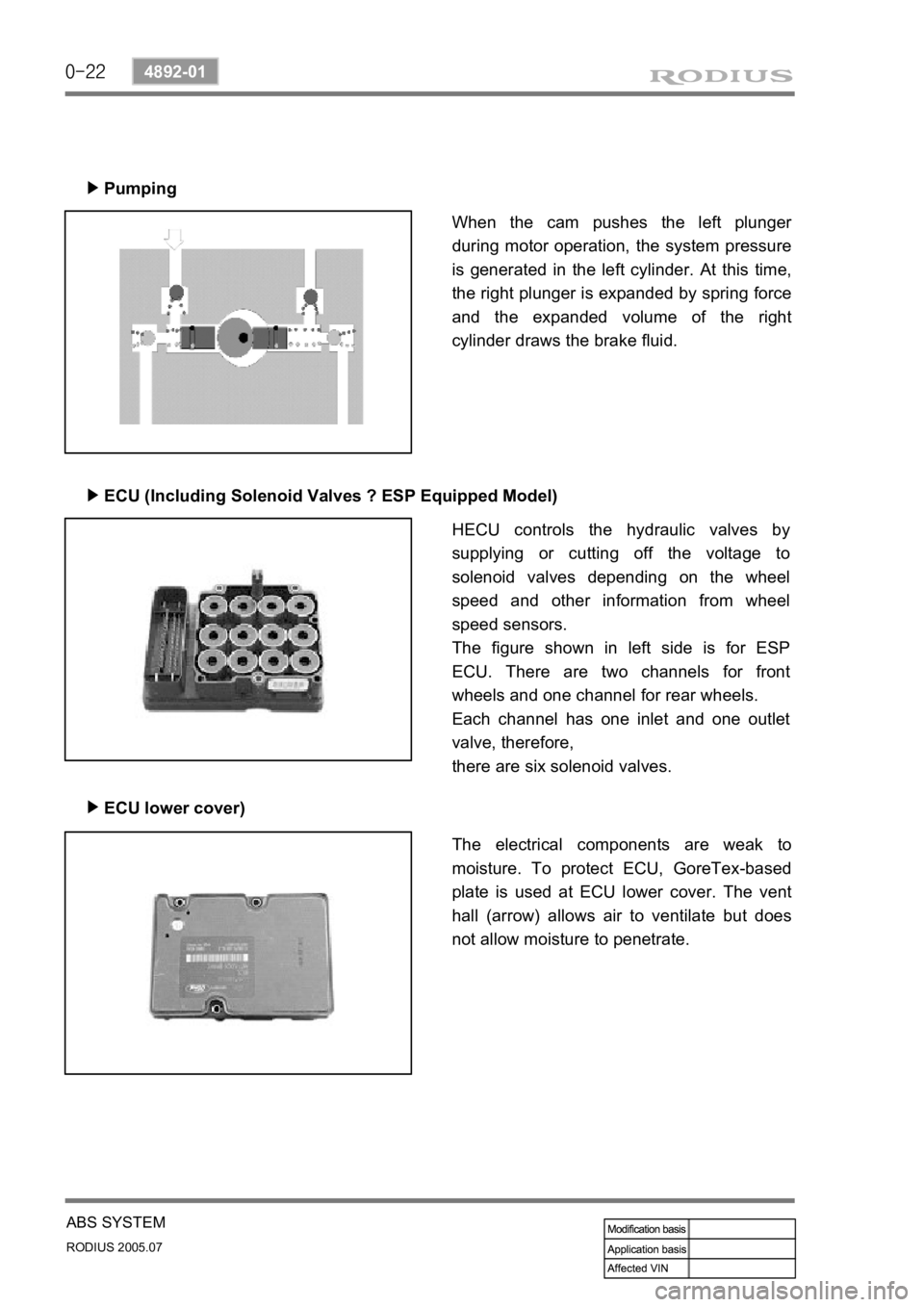
0-22
RODIUS 2005.07
4892-01
ABS SYSTEM
Pumping
▶
ECU (Including Solenoid Valves ? ESP Equipped Model)
▶
ECU lower cover)
▶
When the cam pushes the left plunger
during motor operation, the system pressure
is generated in the left cylinder. At this time,
the right plunger is expanded by spring force
and the expanded volume of the right
cylinder draws the brake fluid.
HECU controls the hydraulic valves by
supplying or cutting off the voltage to
solenoid valves depending on the wheel
speed and other information from wheel
speed sensors.
The figure shown in left side is for ESP
ECU. There are two channels for front
wheels and one channel for rear wheels.
Each channel has one inlet and one outlet
valve, therefore,
there are six solenoid valves.
The electrical components are weak to
moisture. To protect ECU, GoreTex-based
plate is used at ECU lower cover. The vent
hall (arrow) allows air to ventilate but does
not allow moisture to penetrate.
Page 277 of 502
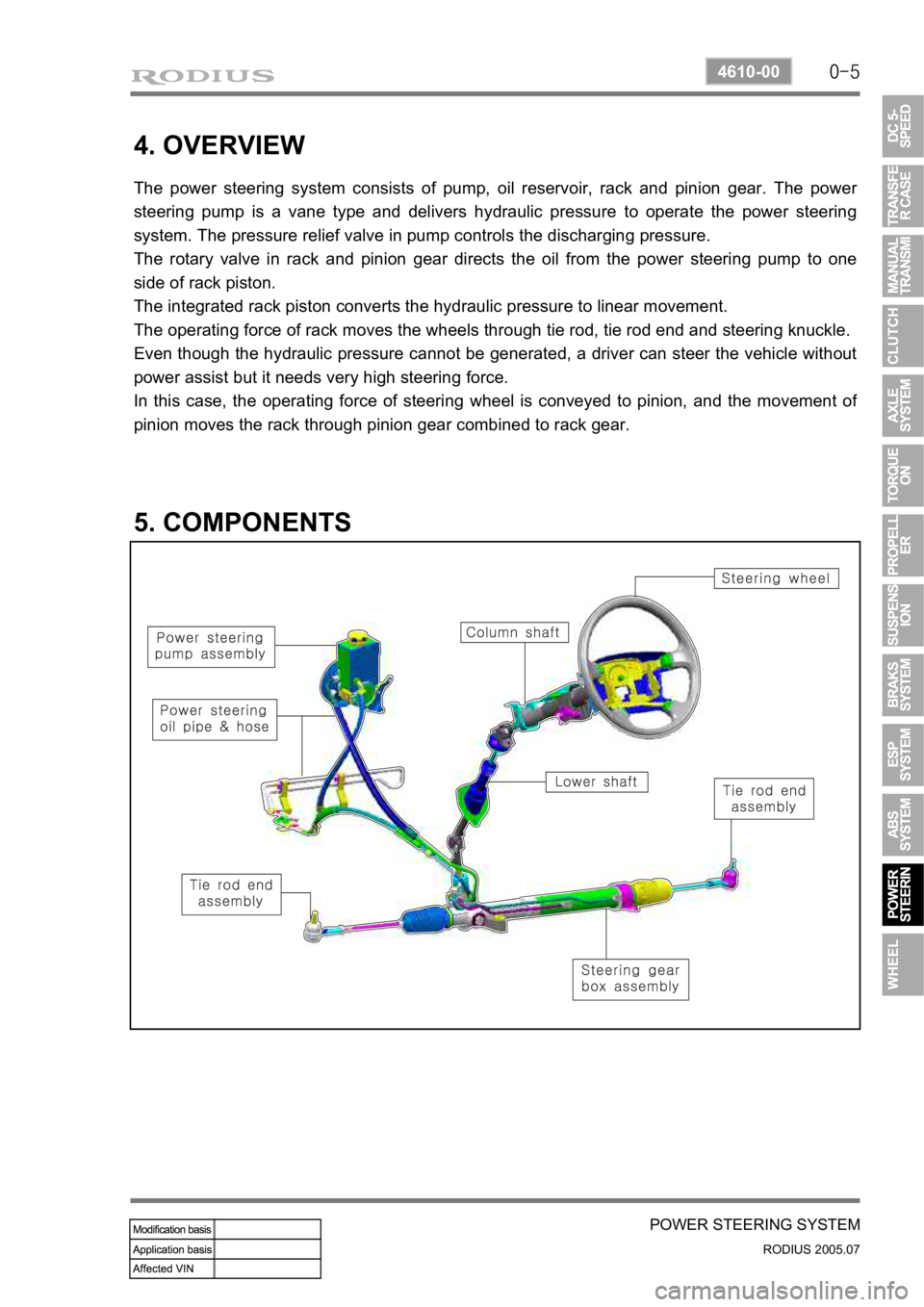
0-5
POWER STEERING SYSTEM
RODIUS 2005.07
4610-00
4. OVERVIEW
The power steering system consists of pump, oil reservoir, rack and pinion gear. The power
steering pump is a vane type and delivers hydraulic pressure to operate the power steering
system. The pressure relief valve in pump controls the discharging pressure.
The rotary valve in rack and pinion gear directs the oil from the power steering pump to one
side of rack piston.
The integrated rack piston converts the hydraulic pressure to linear movement.
The operating force of rack moves the wheels through tie rod, tie rod end and steering knuckle.
Even though the hydraulic pressure cannot be generated, a driver can steer the vehicle without
power assist but it needs very high steering force.
In this case, the operating force of steering wheel is conveyed to pinion, and the movement o
f
pinion moves the rack through pinion gear combined to rack gear.
5. COMPONENTS
Page 280 of 502
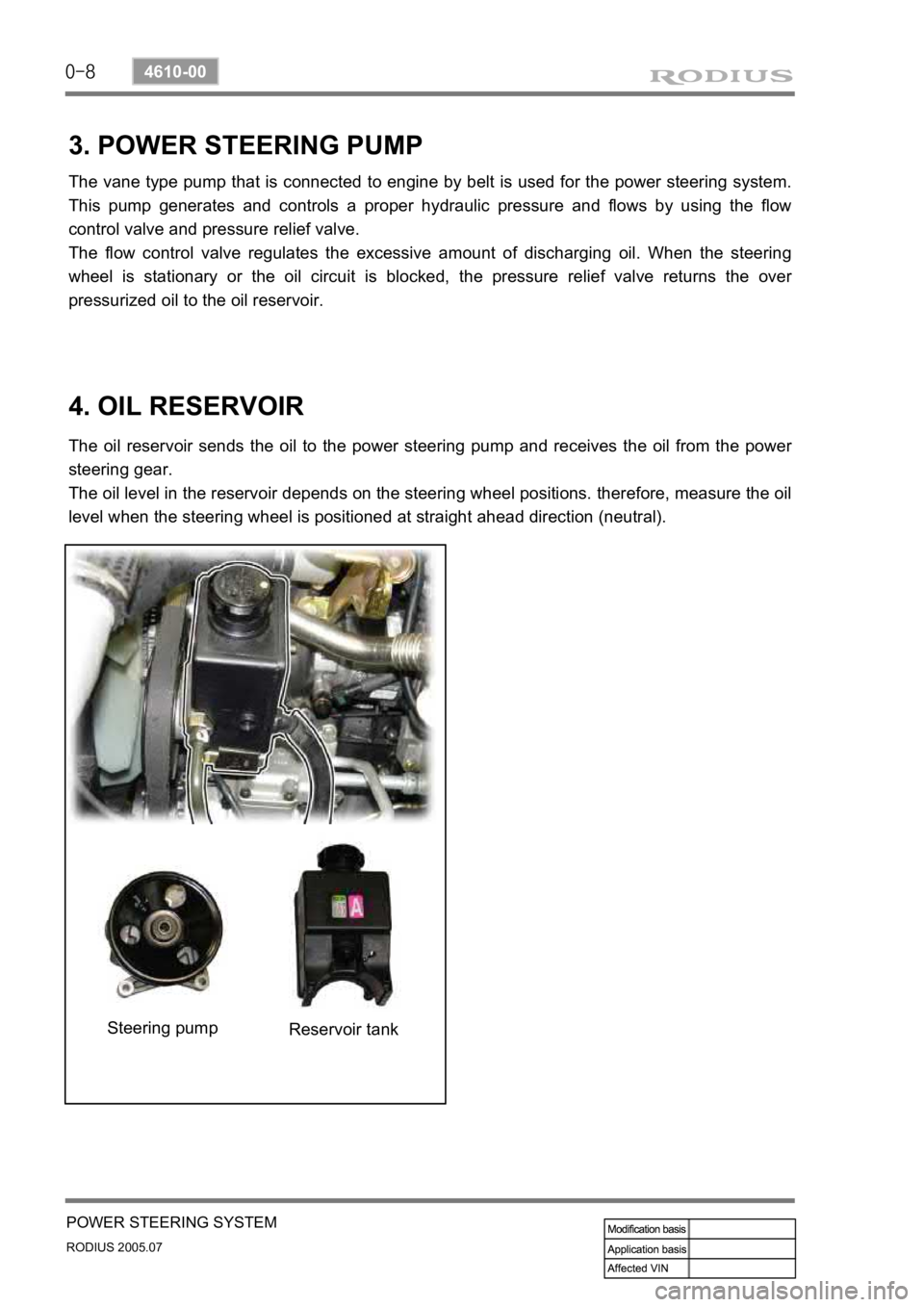
0-8
RODIUS 2005.07
4610-00
POWER STEERING SYSTEM
3. POWER STEERING PUMP
The vane type pump that is connected to engine by belt is used for the power steering system.
This pump generates and controls a proper hydraulic pressure and flows by using the flow
control valve and pressure relief valve.
The flow control valve regulates the excessive amount of discharging oil. When the steering
wheel is stationary or the oil circuit is blocked, the pressure relief valve returns the ove
r
pressurized oil to the oil reservoir.
4. OIL RESERVOIR
The oil reservoir sends the oil to the power steering pump and receives the oil from the power
steering gear.
The oil level in the reservoir depends on the steering wheel positions. therefore, measure the oil
level when the steering wheel is positioned at straight ahead direction (neutral).
Steering pump Reservoir tank
Page 281 of 502
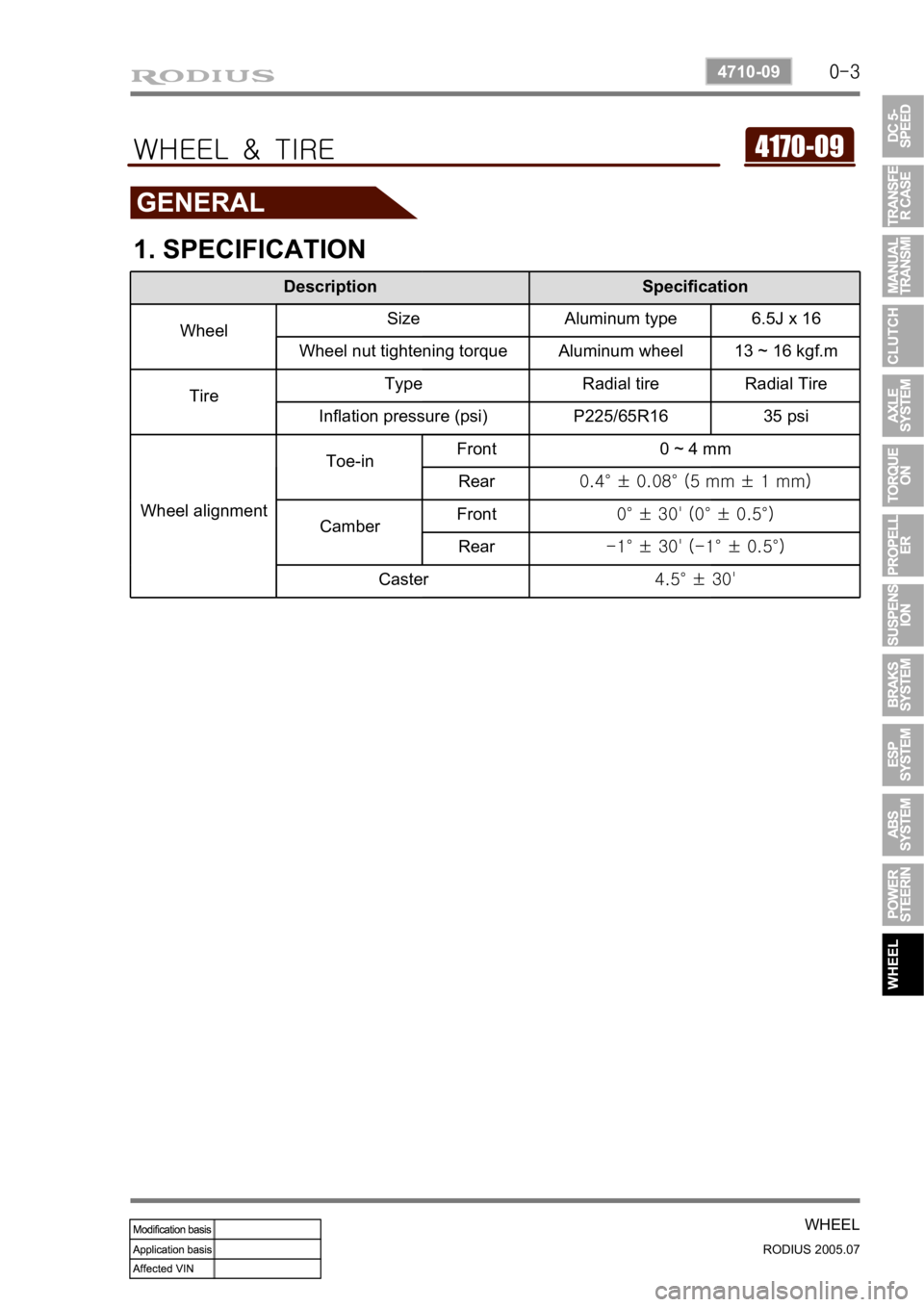
0-3
WHEEL
RODIUS 2005.07
4710-09
4170-09WHEEL & TIRE
1. SPECIFICATION
Description Specification
WheelSize Aluminum type 6.5J x 16
Wheel nut tightening torque Aluminum wheel 13 ~ 16 kgf.m
TireType Radial tire Radial Tire
Inflation pressure (psi) P225/65R16 35 psi
Wheel alignmentToe-inFront 0 ~ 4 mm
Rear0.4° ± 0.08° (5 mm ± 1 mm)
CamberFront0° ± 30' (0° ± 0.5°)
Rear-1° ± 30' (-1° ± 0.5°)
Caster4.5° ± 30'
Page 282 of 502
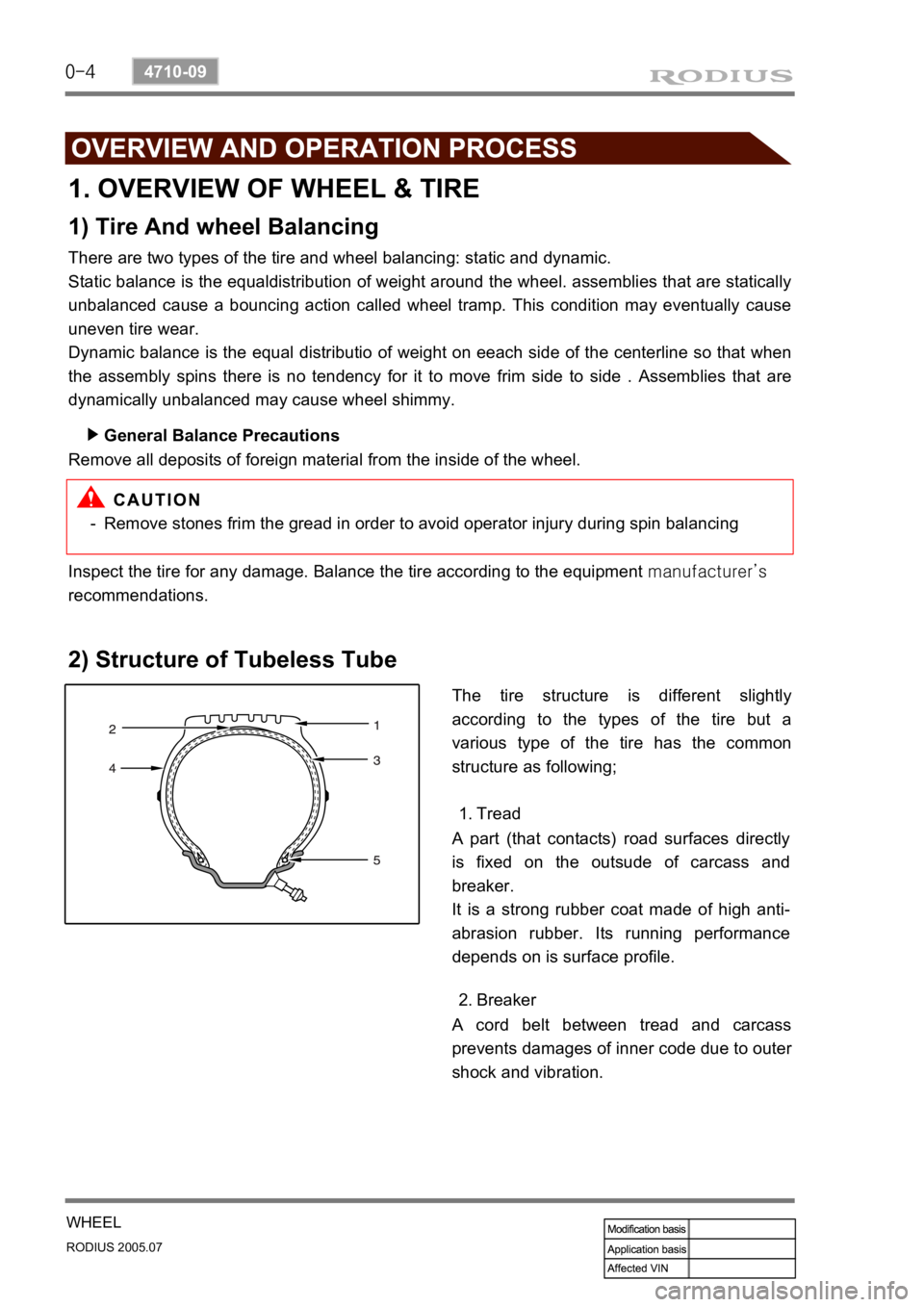
0-4
RODIUS 2005.07
4710-09
WHEEL
1. OVERVIEW OF WHEEL & TIRE
1) Tire And wheel Balancing
There are two types of the tire and wheel balancing: static and dynamic.
Static balance is the equaldistribution of weight around the wheel. assemblies that are statically
unbalanced cause a bouncing action called wheel tramp. This condition may eventually cause
uneven tire wear.
Dynamic balance is the equal distributio of weight on eeach side of the centerline so that when
the assembly spins there is no tendency for it to move frim side to side . Assemblies that are
dynamically unbalanced may cause wheel shimmy.
General Balance Precautions ▶
Remove all deposits of foreign material from the inside of the wheel.
Remove stones frim the gread in order to avoid operator injury during spin balancing -
Inspect the tire for any damage. Balance the tire according to the equipment manufacturer’s
recommendations.
2) Structure of Tubeless Tube
The tire structure is different slightly
according to the types of the tire but a
various type of the tire has the common
structure as following;
Tread 1.
A part (that contacts) road surfaces directly
is fixed on the outsude of carcass and
breaker.
It is a strong rubber coat made of high anti-
abrasion rubber. Its running performance
depends on is surface profile.
A cord belt between tread and carcass
prevents damages of inner code due to oute
r
shock and vibration.Breaker 2.
Page 283 of 502
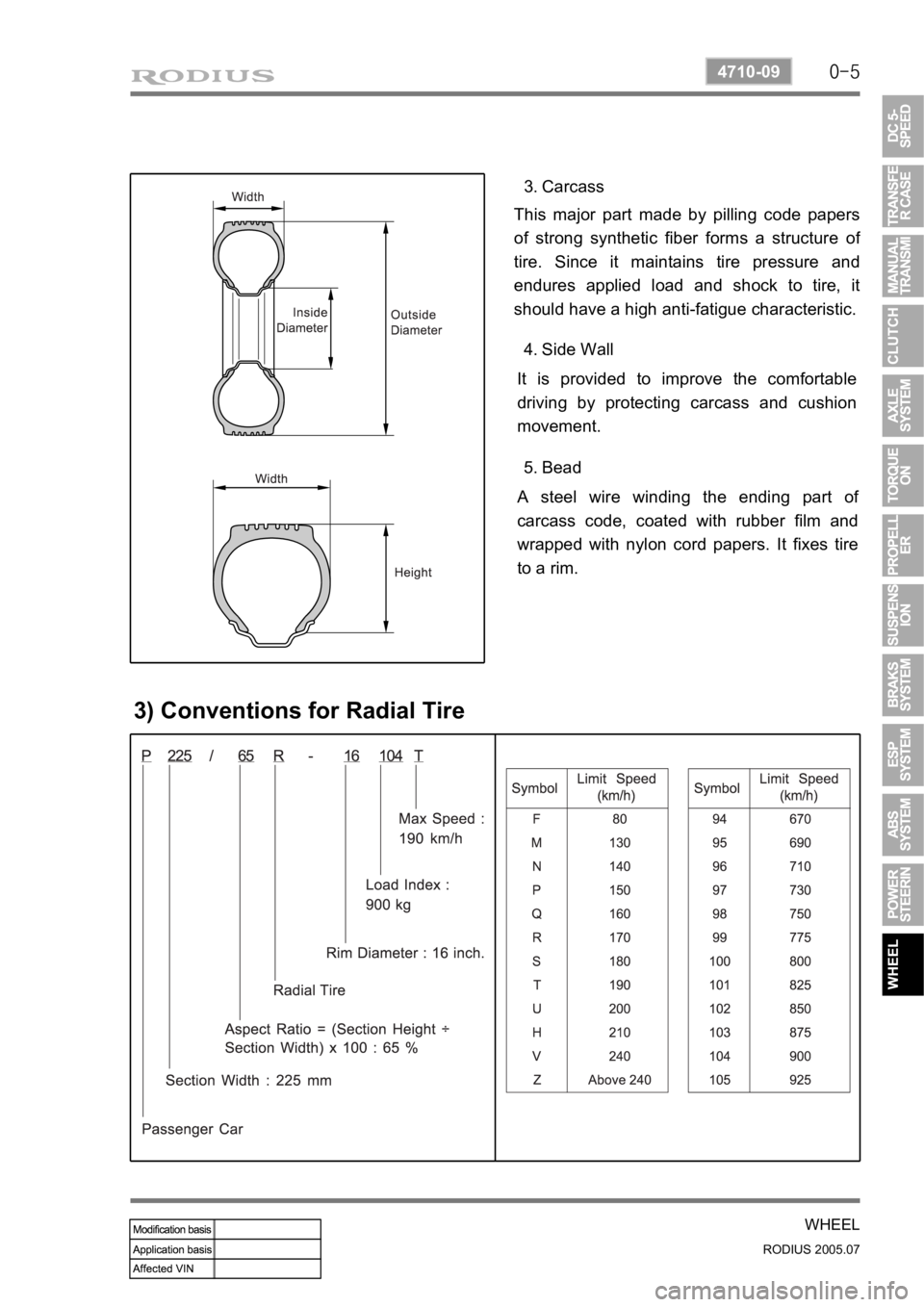
0-5
WHEEL
RODIUS 2005.07
4710-09
Carcass 3.
This major part made by pilling code papers
of strong synthetic fiber forms a structure o
f
tire. Since it maintains tire pressure and
endures applied load and shock to tire, it
should have a high anti-fatigue characteristic.
Side Wall 4.
It is provided to improve the comfortable
driving by protecting carcass and cushion
movement.
Bead 5.
A steel wire winding the ending part o
f
carcass code, coated with rubber film and
wrapped with nylon cord papers. It fixes tire
to a rim.
3) Conventions for Radial Tire
Page 284 of 502
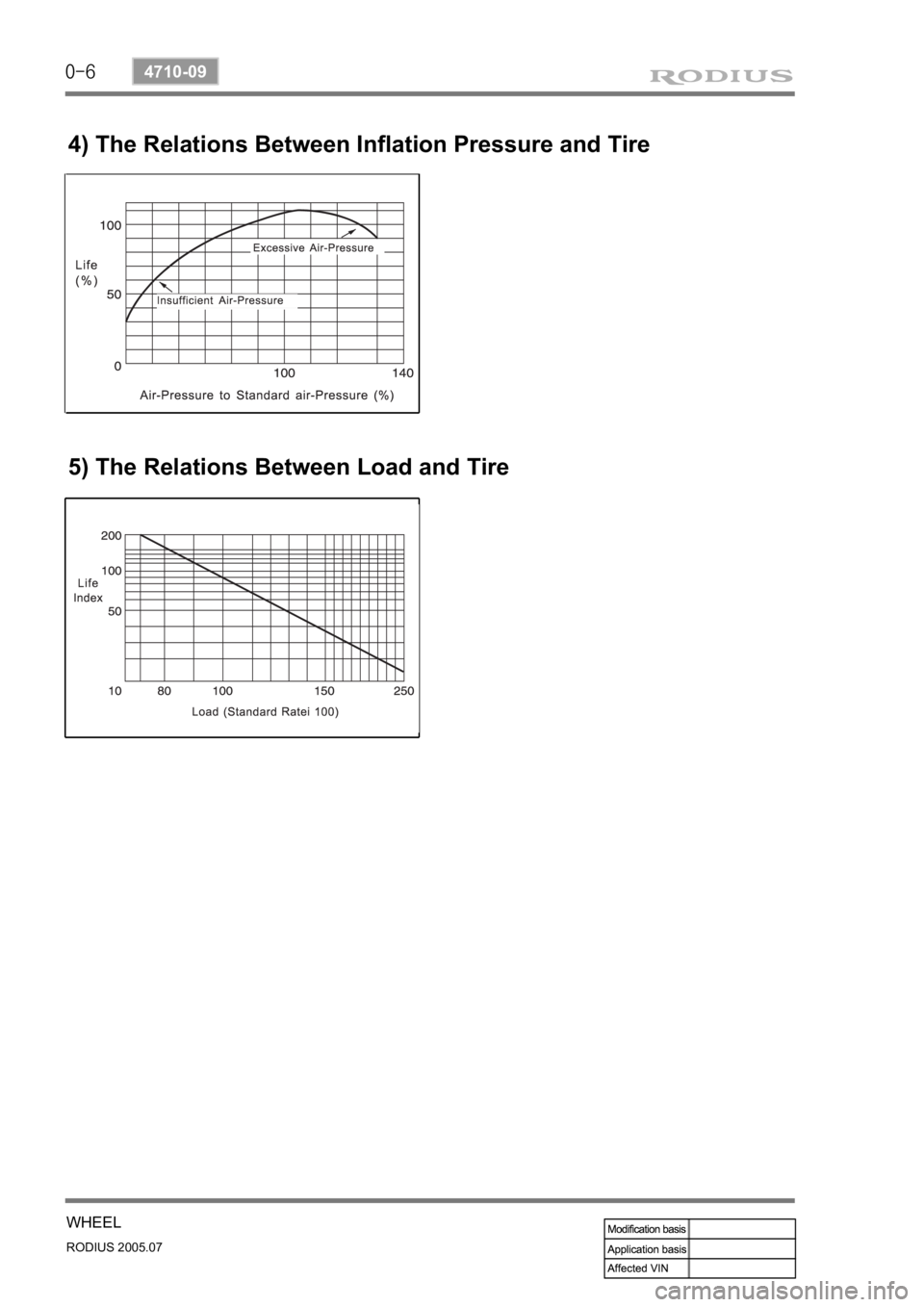
0-6
RODIUS 2005.07
4710-09
WHEEL
4) The Relations Between Inflation Pressure and Tire
5) The Relations Between Load and Tire
Page 285 of 502
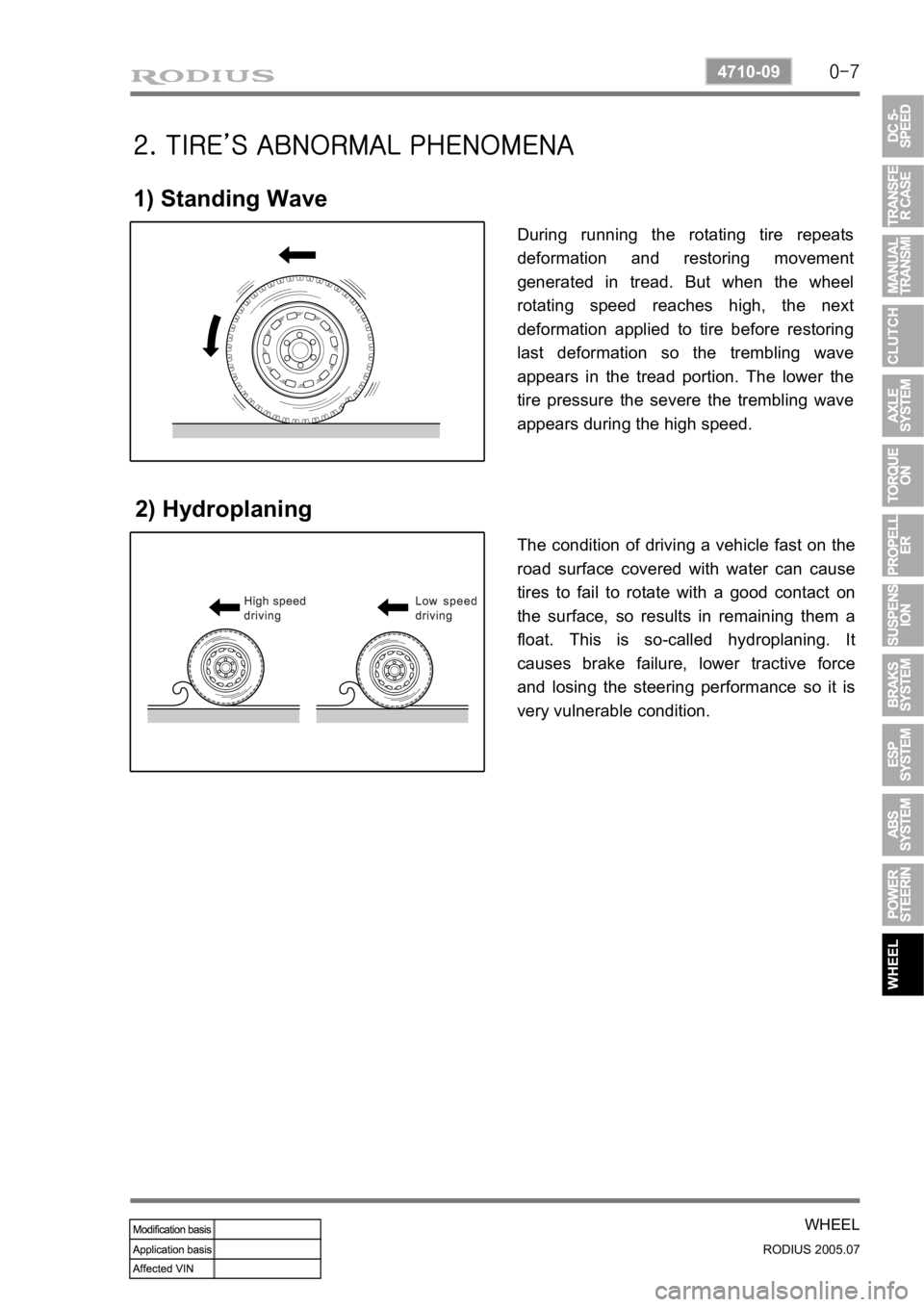
0-7
WHEEL
RODIUS 2005.07
4710-09
2. TIRE’S ABNORMAL PHENOMENA
1) Standing Wave
2) Hydroplaning
During running the rotating tire repeats
deformation and restoring movement
generated in tread. But when the wheel
rotating speed reaches high, the next
deformation applied to tire before restoring
last deformation so the trembling wave
appears in the tread portion. The lower the
tire pressure the severe the trembling wave
appears during the high speed.
The condition of driving a vehicle fast on the
road surface covered with water can cause
tires to fail to rotate with a good contact on
the surface, so results in remaining them a
float. This is so-called hydroplaning. It
causes brake failure, lower tractive force
and losing the steering performance so it is
very vulnerable condition.
Page 286 of 502
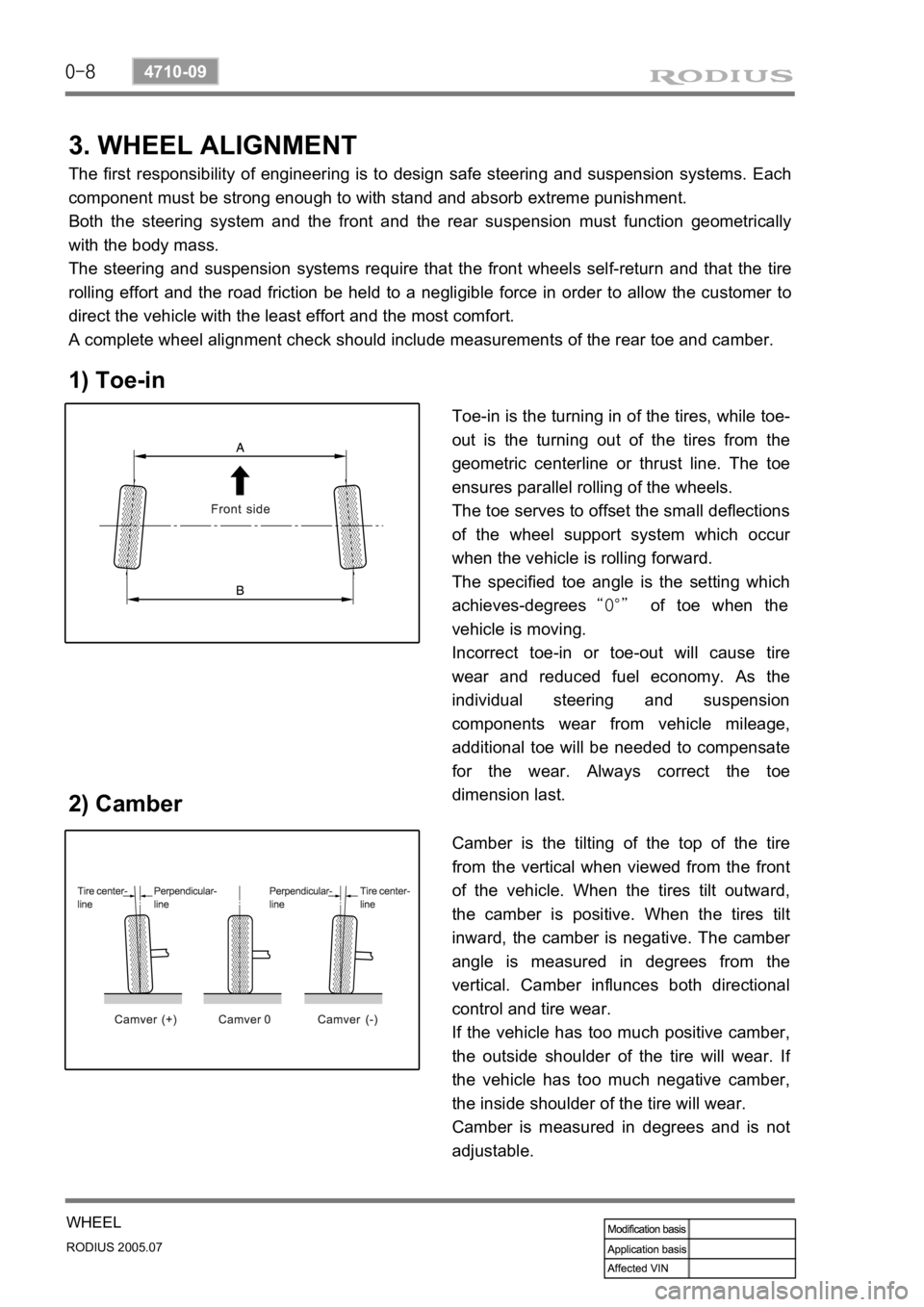
0-8
RODIUS 2005.07
4710-09
WHEEL
3. WHEEL ALIGNMENT
The first responsibility of engineering is to design safe steering and suspension systems. Each
component must be strong enough to with stand and absorb extreme punishment.
Both the steering system and the front and the rear suspension must function geometrically
with the body mass.
The steering and suspension systems require that the front wheels self-return and that the tire
rolling effort and the road friction be held to a negligible force in order to allow the customer to
direct the vehicle with the least effort and the most comfort.
A complete wheel alignment check should include measurements of the rear toe and camber.
1) Toe-in
2) Camber
Toe-in is the turning in of the tires, while toe-
out is the turning out of the tires from the
geometric centerline or thrust line. The toe
ensures parallel rolling of the wheels.
The toe serves to offset the small deflections
of the wheel support system which occu
r
when the vehicle is rolling forward.
The specified toe angle is the setting which
achieves-degrees “0°” of toe when the
vehicle is moving.
Incorrect toe-in or toe-out will cause tire
wear and reduced fuel economy. As the
individual steering and suspension
components wear from vehicle mileage,
additional toe will be needed to compensate
for the wear. Always correct the toe
dimension last.
Camber is the tilting of the top of the tire
from the vertical when viewed from the front
of the vehicle. When the tires tilt outward,
the camber is positive. When the tires tilt
inward, the camber is negative. The cambe
r
angle is measured in degrees from the
vertical. Camber influnces both directional
control and tire wear.
If the vehicle has too much positive camber,
the outside shoulder of the tire will wear. I
f
the vehicle has too much negative camber,
the inside shoulder of the tire will wear.
Camber is measured in degrees and is not
adjustable.
Page 287 of 502

0-9
WHEEL
RODIUS 2005.07
4710-09
3) Caster
Caster is the tilting of the uppermost point of
the steering axis either forward or backward
from the vertical when viewed from the side
of the vehicle. A backward tilt is positive
and a forward tilt negative. Caster influences
directional control of the steering but does
not affect tire wear.
Weak springs or overloading a vehicle will
affect caster.
One wheel with more positive caster will pull
toward the center of the car. This condition
will cause the car to move or lean toward the
side with the least amount of positive caster.
Caster is measures in degrees and is not
adjustable.