SUBARU LEGACY 1995 Service Manual Online
Manufacturer: SUBARU, Model Year: 1995, Model line: LEGACY, Model: SUBARU LEGACY 1995Pages: 2248, PDF Size: 48.81 MB
Page 81 of 2248
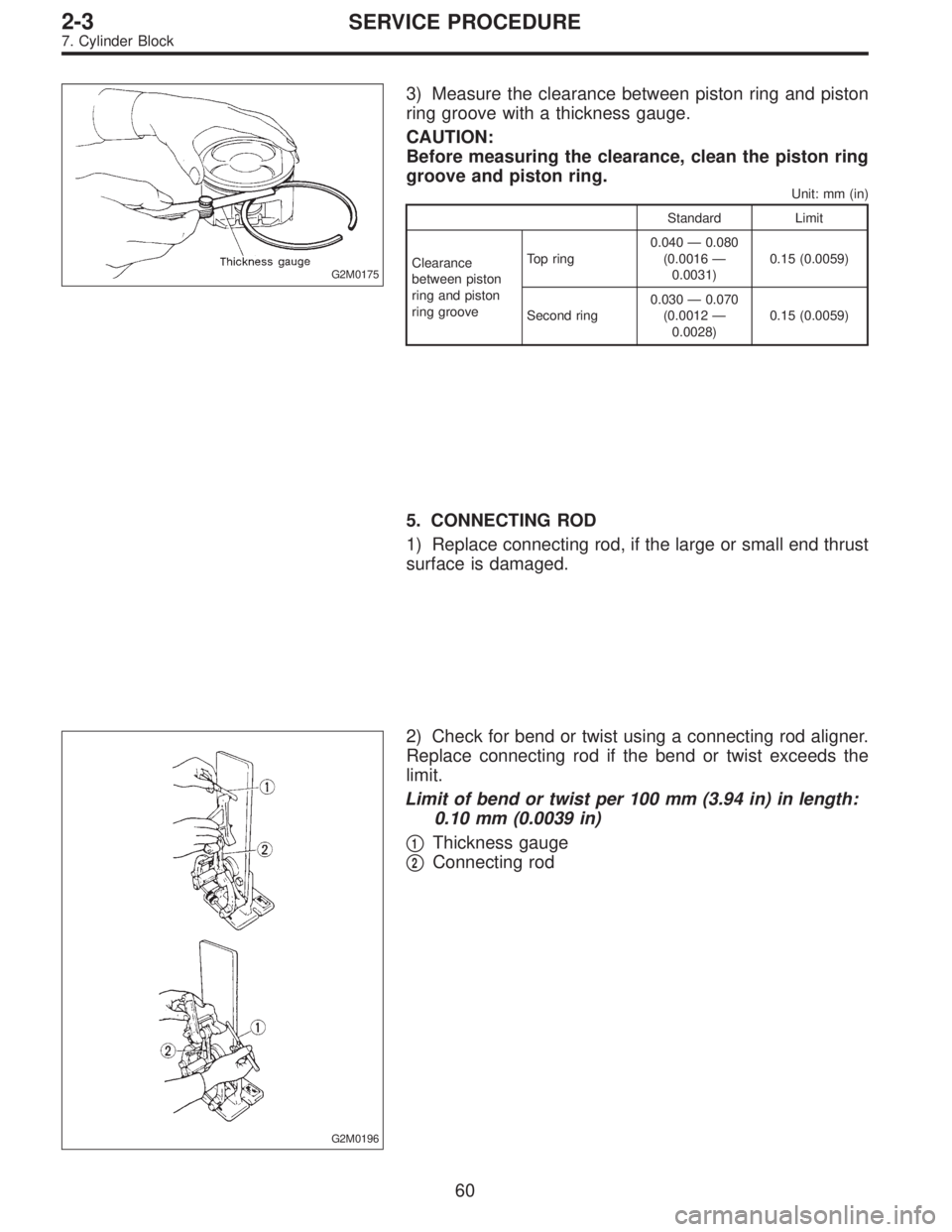
G2M0175
3) Measure the clearance between piston ring and piston
ring groove with a thickness gauge.
CAUTION:
Before measuring the clearance, clean the piston ring
groove and piston ring.
Unit: mm (in)
Standard Limit
Clearance
between piston
ring and piston
ring grooveTop ring0.040—0.080
(0.0016—
0.0031)0.15 (0.0059)
Second ring0.030—0.070
(0.0012—
0.0028)0.15 (0.0059)
5. CONNECTING ROD
1) Replace connecting rod, if the large or small end thrust
surface is damaged.
G2M0196
2) Check for bend or twist using a connecting rod aligner.
Replace connecting rod if the bend or twist exceeds the
limit.
Limit of bend or twist per 100 mm (3.94 in) in length:
0.10 mm (0.0039 in)
1Thickness gauge
2Connecting rod
60
2-3SERVICE PROCEDURE
7. Cylinder Block
Page 82 of 2248
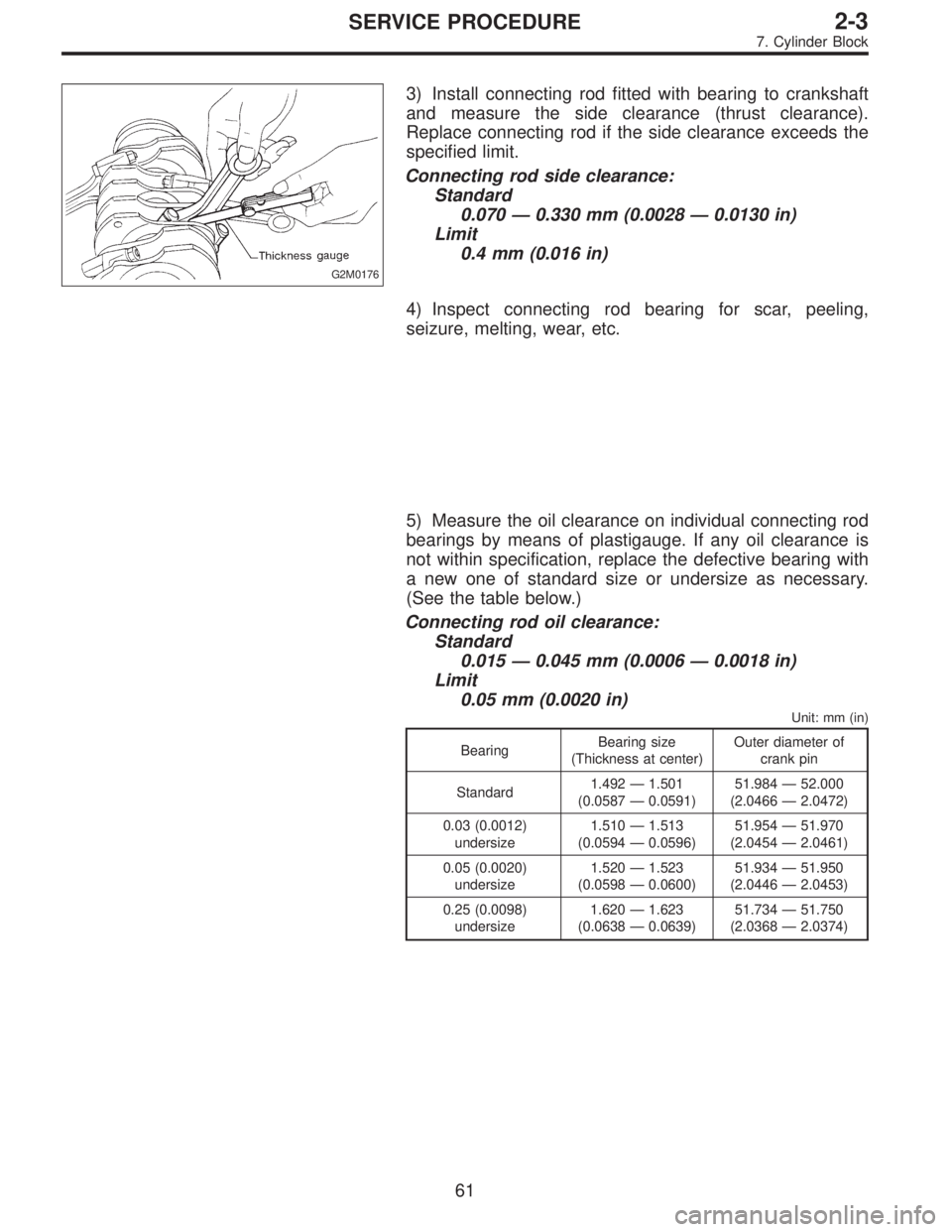
G2M0176
3) Install connecting rod fitted with bearing to crankshaft
and measure the side clearance (thrust clearance).
Replace connecting rod if the side clearance exceeds the
specified limit.
Connecting rod side clearance:
Standard
0.070—0.330 mm (0.0028—0.0130 in)
Limit
0.4 mm (0.016 in)
4) Inspect connecting rod bearing for scar, peeling,
seizure, melting, wear, etc.
5) Measure the oil clearance on individual connecting rod
bearings by means of plastigauge. If any oil clearance is
not within specification, replace the defective bearing with
a new one of standard size or undersize as necessary.
(See the table below.)
Connecting rod oil clearance:
Standard
0.015—0.045 mm (0.0006—0.0018 in)
Limit
0.05 mm (0.0020 in)
Unit: mm (in)
BearingBearing size
(Thickness at center)Outer diameter of
crank pin
Standard1.492—1.501
(0.0587—0.0591)51.984—52.000
(2.0466—2.0472)
0.03 (0.0012)
undersize1.510—1.513
(0.0594—0.0596)51.954—51.970
(2.0454—2.0461)
0.05 (0.0020)
undersize1.520—1.523
(0.0598—0.0600)51.934—51.950
(2.0446—2.0453)
0.25 (0.0098)
undersize1.620—1.623
(0.0638—0.0639)51.734—51.750
(2.0368—2.0374)
61
2-3SERVICE PROCEDURE
7. Cylinder Block
Page 83 of 2248
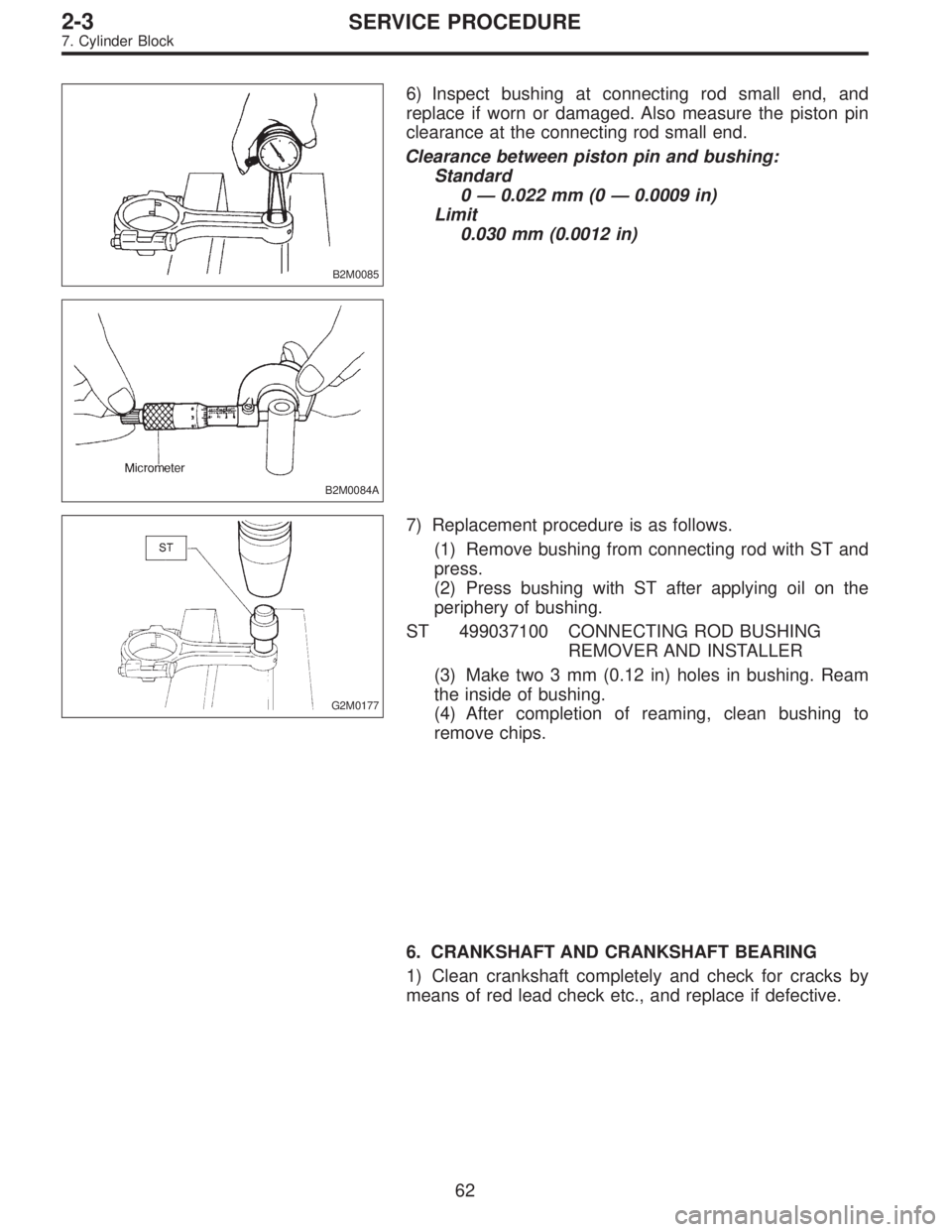
B2M0085
6) Inspect bushing at connecting rod small end, and
replace if worn or damaged. Also measure the piston pin
clearance at the connecting rod small end.
Clearance between piston pin and bushing:
Standard
0—0.022 mm (0—0.0009 in)
Limit
0.030 mm (0.0012 in)
B2M0084A
G2M0177
7) Replacement procedure is as follows.
(1) Remove bushing from connecting rod with ST and
press.
(2) Press bushing with ST after applying oil on the
periphery of bushing.
ST 499037100 CONNECTING ROD BUSHING
REMOVER AND INSTALLER
(3) Make two 3 mm (0.12 in) holes in bushing. Ream
the inside of bushing.
(4) After completion of reaming, clean bushing to
remove chips.
6. CRANKSHAFT AND CRANKSHAFT BEARING
1) Clean crankshaft completely and check for cracks by
means of red lead check etc., and replace if defective.
62
2-3SERVICE PROCEDURE
7. Cylinder Block
Page 84 of 2248
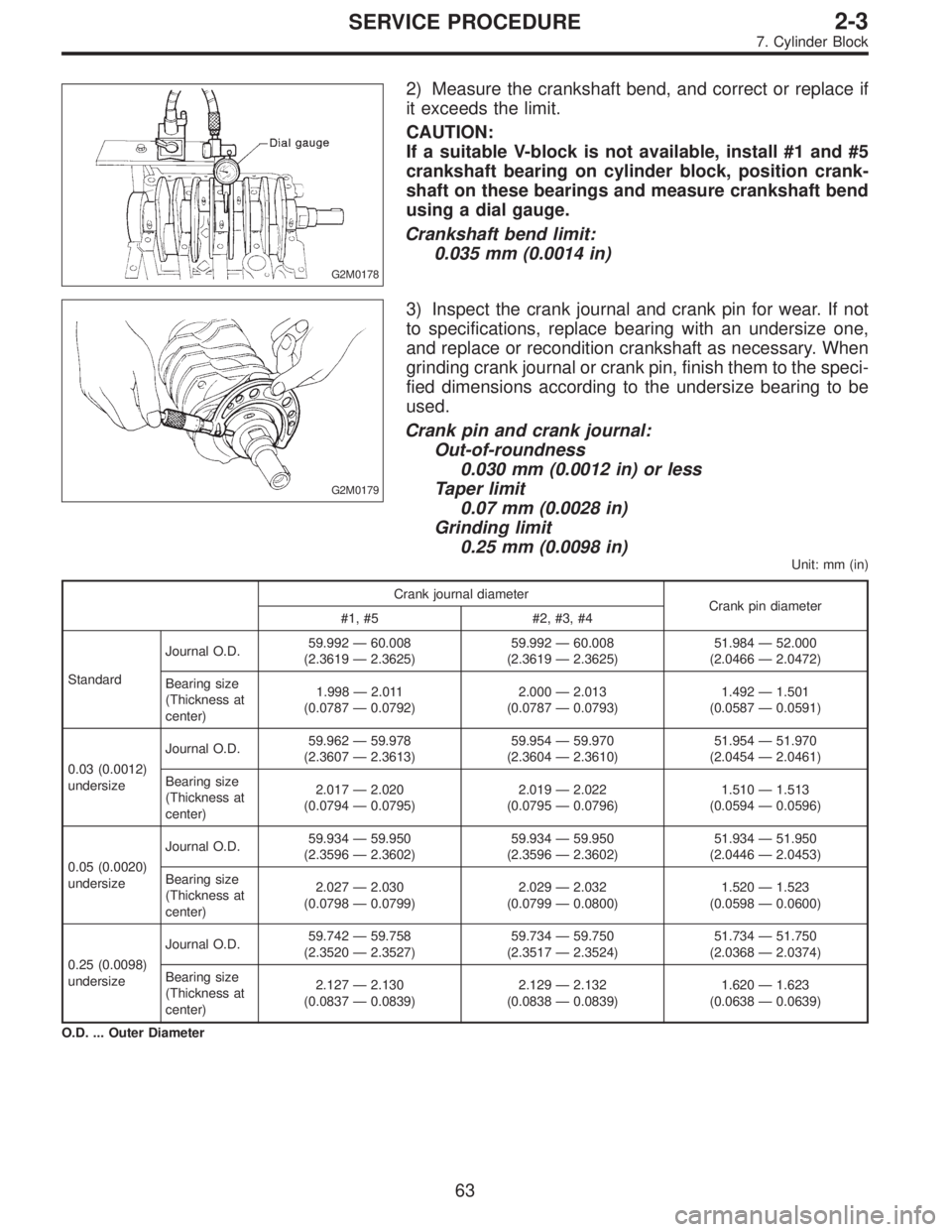
G2M0178
2) Measure the crankshaft bend, and correct or replace if
it exceeds the limit.
CAUTION:
If a suitable V-block is not available, install #1 and #5
crankshaft bearing on cylinder block, position crank-
shaft on these bearings and measure crankshaft bend
using a dial gauge.
Crankshaft bend limit:
0.035 mm (0.0014 in)
G2M0179
3) Inspect the crank journal and crank pin for wear. If not
to specifications, replace bearing with an undersize one,
and replace or recondition crankshaft as necessary. When
grinding crank journal or crank pin, finish them to the speci-
fied dimensions according to the undersize bearing to be
used.
Crank pin and crank journal:
Out-of-roundness
0.030 mm (0.0012 in) or less
Taper limit
0.07 mm (0.0028 in)
Grinding limit
0.25 mm (0.0098 in)
Unit: mm (in)
Crank journal diameter
Crank pin diameter
#1, #5 #2, #3, #4
StandardJournal O.D.59.992—60.008
(2.3619—2.3625)59.992—60.008
(2.3619—2.3625)51.984—52.000
(2.0466—2.0472)
Bearing size
(Thickness at
center)1.998—2.011
(0.0787—0.0792)2.000—2.013
(0.0787—0.0793)1.492—1.501
(0.0587—0.0591)
0.03 (0.0012)
undersizeJournal O.D.59.962—59.978
(2.3607—2.3613)59.954—59.970
(2.3604—2.3610)51.954—51.970
(2.0454—2.0461)
Bearing size
(Thickness at
center)2.017—2.020
(0.0794—0.0795)2.019—2.022
(0.0795—0.0796)1.510—1.513
(0.0594—0.0596)
0.05 (0.0020)
undersizeJournal O.D.59.934—59.950
(2.3596—2.3602)59.934—59.950
(2.3596—2.3602)51.934—51.950
(2.0446—2.0453)
Bearing size
(Thickness at
center)2.027—2.030
(0.0798—0.0799)2.029—2.032
(0.0799—0.0800)1.520—1.523
(0.0598—0.0600)
0.25 (0.0098)
undersizeJournal O.D.59.742—59.758
(2.3520—2.3527)59.734—59.750
(2.3517—2.3524)51.734—51.750
(2.0368—2.0374)
Bearing size
(Thickness at
center)2.127—2.130
(0.0837—0.0839)2.129—2.132
(0.0838—0.0839)1.620—1.623
(0.0638—0.0639)
O.D. ... Outer Diameter
63
2-3SERVICE PROCEDURE
7. Cylinder Block
Page 85 of 2248
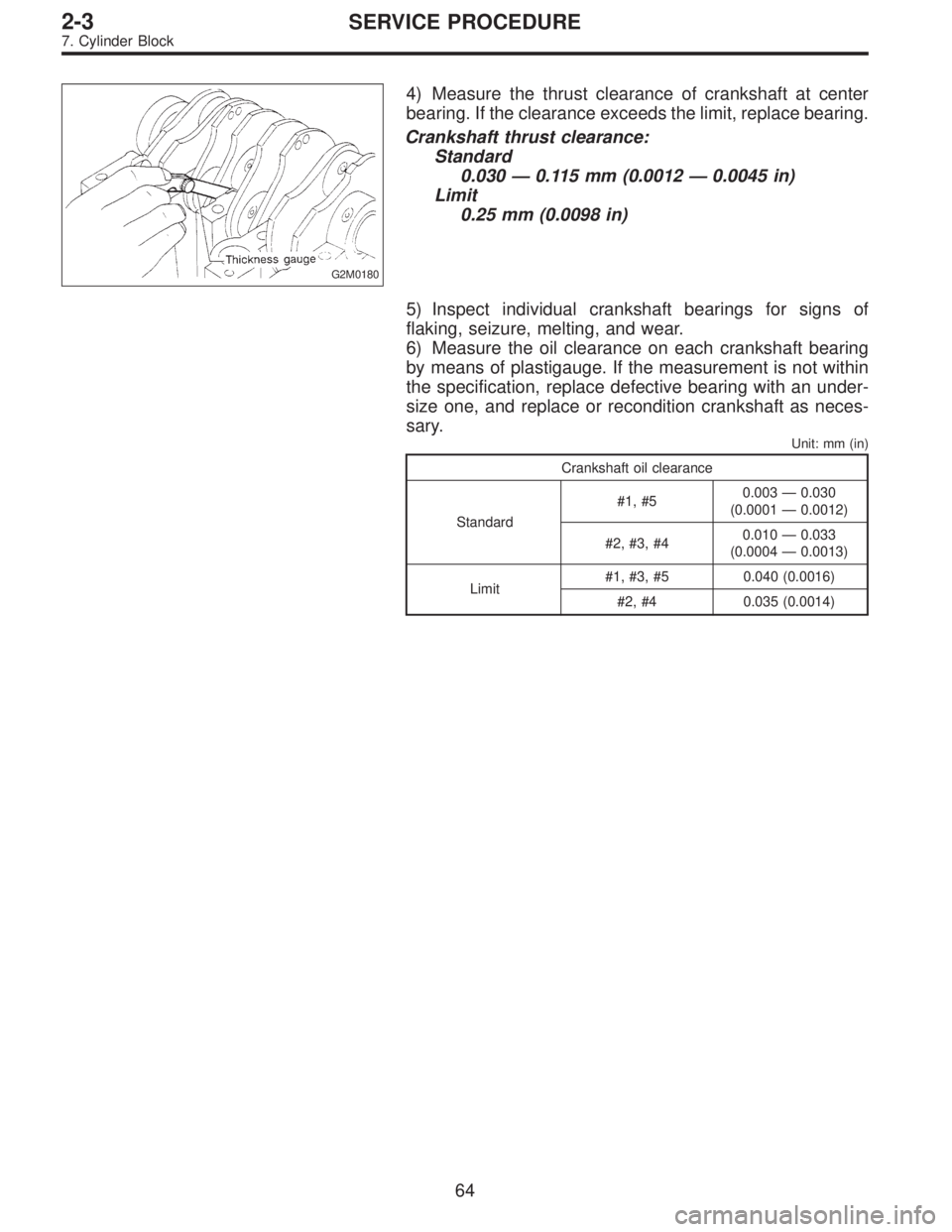
G2M0180
4) Measure the thrust clearance of crankshaft at center
bearing. If the clearance exceeds the limit, replace bearing.
Crankshaft thrust clearance:
Standard
0.030—0.115 mm (0.0012—0.0045 in)
Limit
0.25 mm (0.0098 in)
5) Inspect individual crankshaft bearings for signs of
flaking, seizure, melting, and wear.
6) Measure the oil clearance on each crankshaft bearing
by means of plastigauge. If the measurement is not within
the specification, replace defective bearing with an under-
size one, and replace or recondition crankshaft as neces-
sary.
Unit: mm (in)
Crankshaft oil clearance
Standard#1, #50.003—0.030
(0.0001—0.0012)
#2, #3, #40.010—0.033
(0.0004—0.0013)
Limit#1, #3, #5 0.040 (0.0016)
#2, #4 0.035 (0.0014)
64
2-3SERVICE PROCEDURE
7. Cylinder Block
Page 86 of 2248
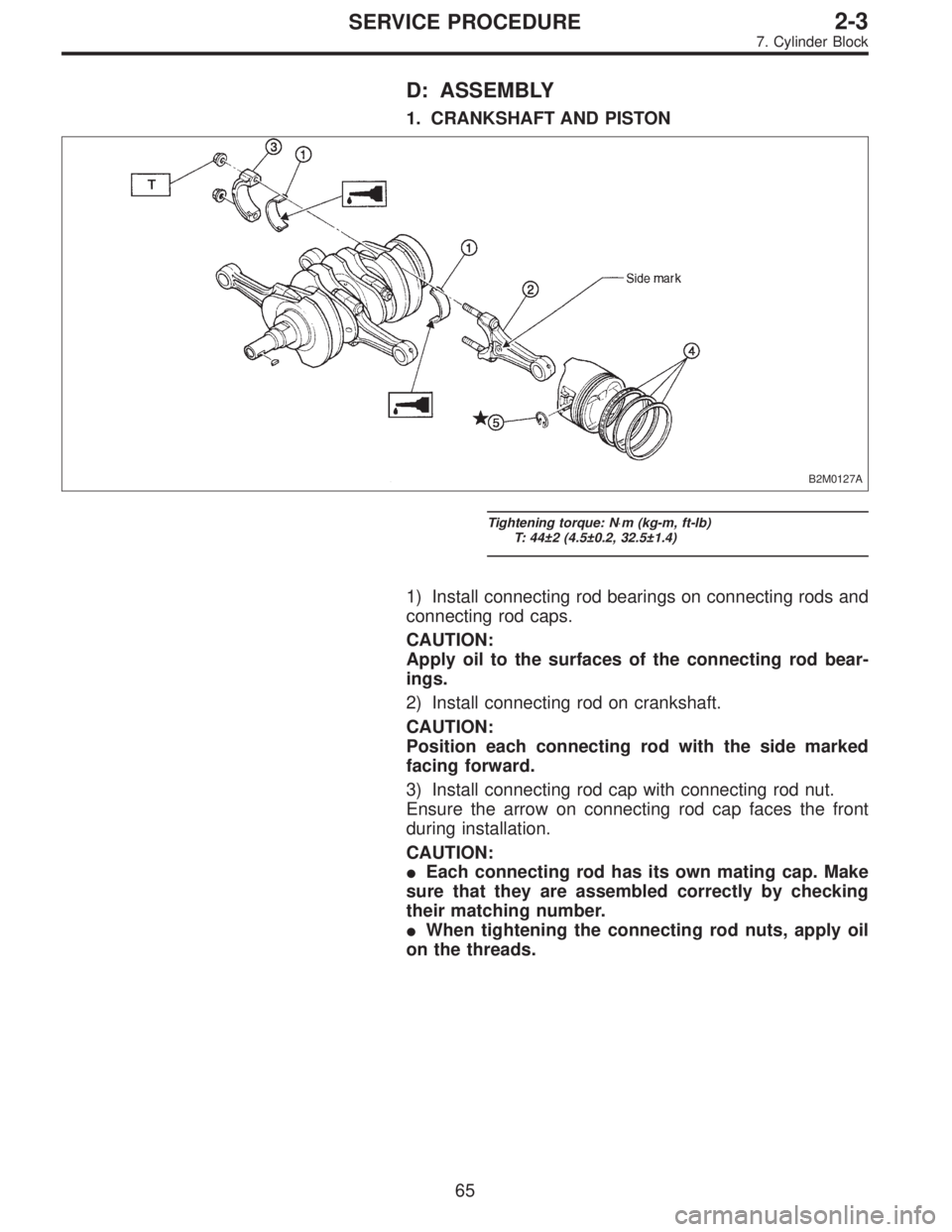
D: ASSEMBLY
1. CRANKSHAFT AND PISTON
B2M0127A
Tightening torque: N⋅m (kg-m, ft-lb)
T: 44±2 (4.5±0.2, 32.5±1.4)
1) Install connecting rod bearings on connecting rods and
connecting rod caps.
CAUTION:
Apply oil to the surfaces of the connecting rod bear-
ings.
2) Install connecting rod on crankshaft.
CAUTION:
Position each connecting rod with the side marked
facing forward.
3) Install connecting rod cap with connecting rod nut.
Ensure the arrow on connecting rod cap faces the front
during installation.
CAUTION:
Each connecting rod has its own mating cap. Make
sure that they are assembled correctly by checking
their matching number.
When tightening the connecting rod nuts, apply oil
on the threads.
65
2-3SERVICE PROCEDURE
7. Cylinder Block
Page 87 of 2248
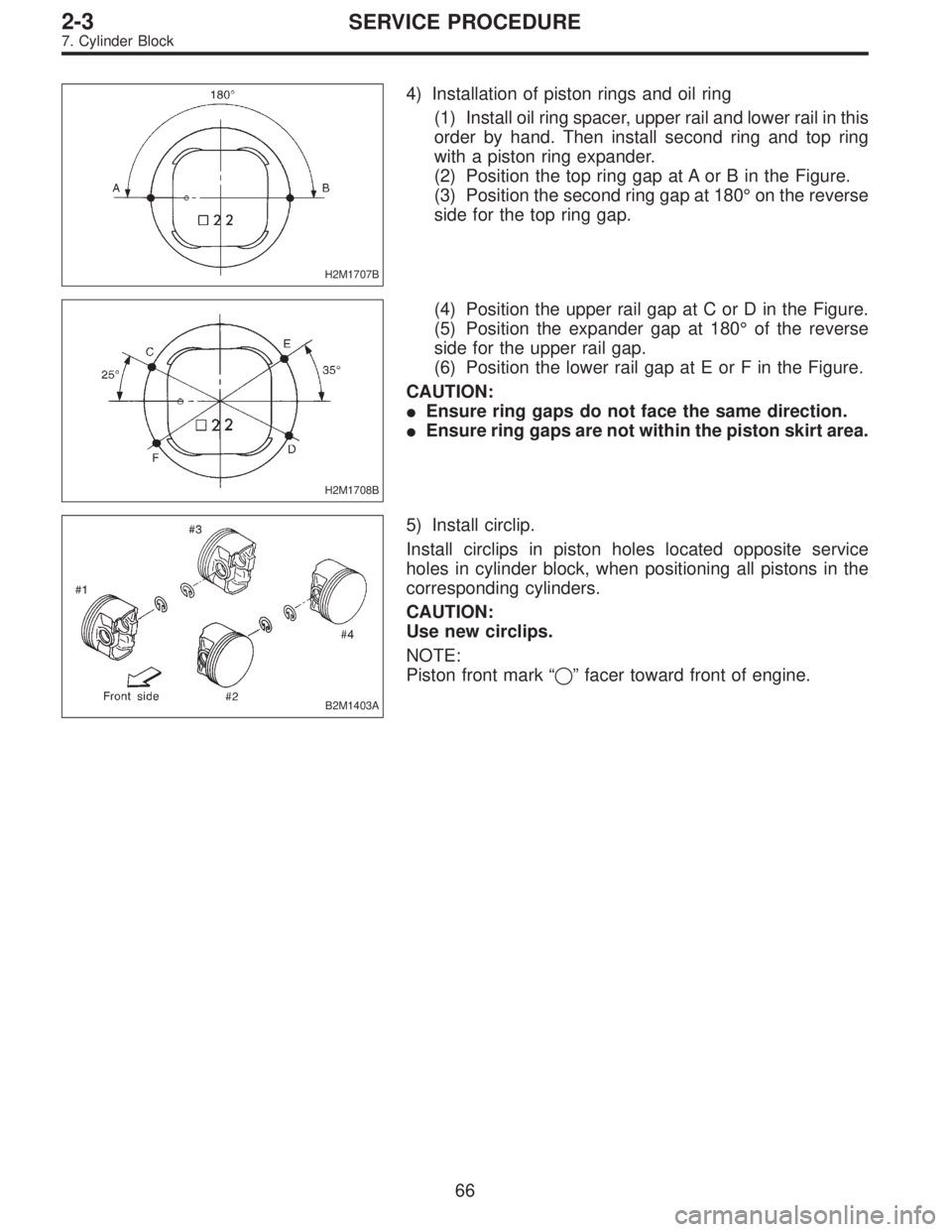
H2M1707B
4) Installation of piston rings and oil ring
(1) Install oil ring spacer, upper rail and lower rail in this
order by hand. Then install second ring and top ring
with a piston ring expander.
(2) Position the top ring gap at A or B in the Figure.
(3) Position the second ring gap at 180°on the reverse
side for the top ring gap.
H2M1708B
(4) Position the upper rail gap at C or D in the Figure.
(5) Position the expander gap at 180°of the reverse
side for the upper rail gap.
(6) Position the lower rail gap at E or F in the Figure.
CAUTION:
Ensure ring gaps do not face the same direction.
Ensure ring gaps are not within the piston skirt area.
B2M1403A
5) Install circlip.
Install circlips in piston holes located opposite service
holes in cylinder block, when positioning all pistons in the
corresponding cylinders.
CAUTION:
Use new circlips.
NOTE:
Piston front mark“”facer toward front of engine.
66
2-3SERVICE PROCEDURE
7. Cylinder Block
Page 88 of 2248
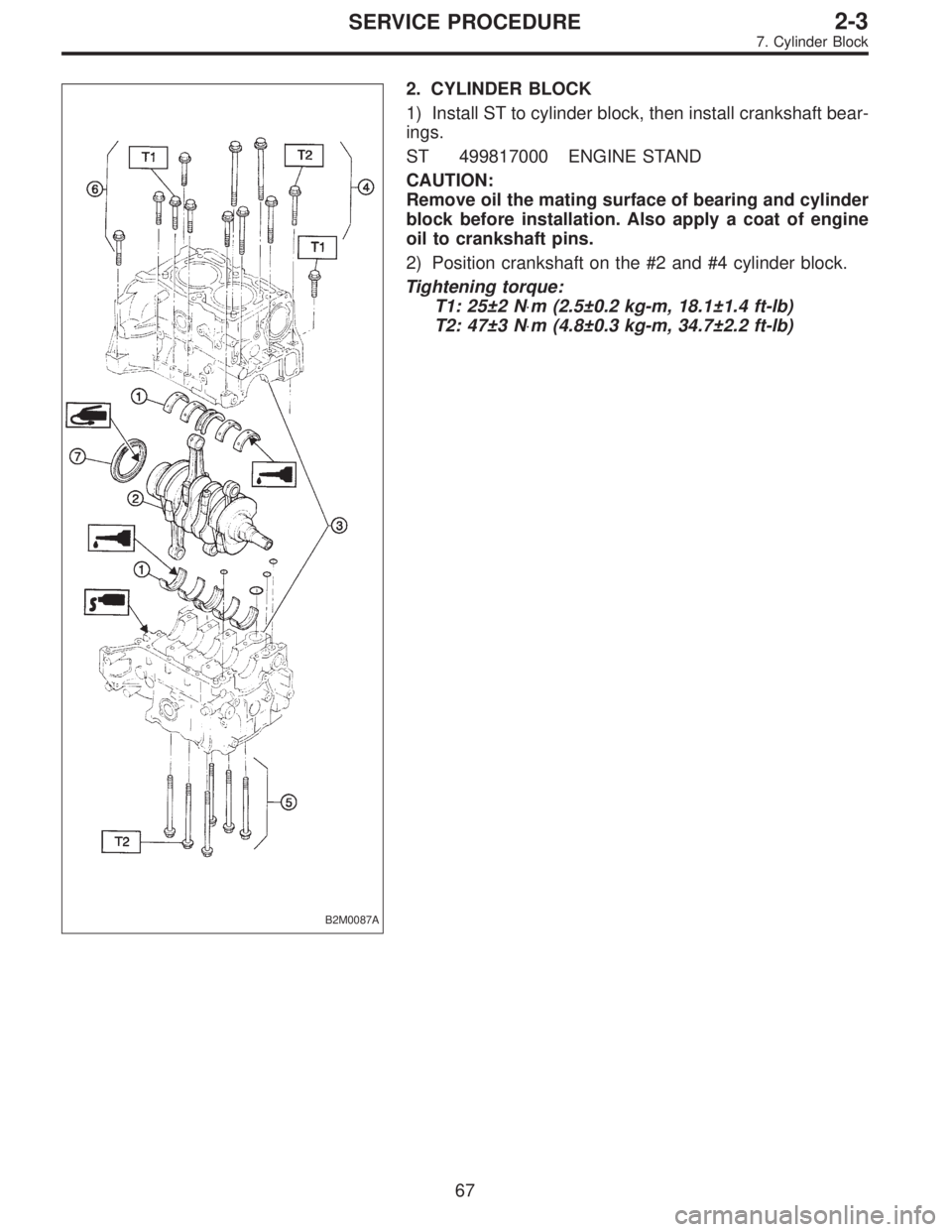
B2M0087A
2. CYLINDER BLOCK
1) Install ST to cylinder block, then install crankshaft bear-
ings.
ST 499817000 ENGINE STAND
CAUTION:
Remove oil the mating surface of bearing and cylinder
block before installation. Also apply a coat of engine
oil to crankshaft pins.
2) Position crankshaft on the #2 and #4 cylinder block.
Tightening torque:
T1: 25±2 N⋅m (2.5±0.2 kg-m, 18.1±1.4 ft-lb)
T2: 47±3 N⋅m (4.8±0.3 kg-m, 34.7±2.2 ft-lb)
67
2-3SERVICE PROCEDURE
7. Cylinder Block
Page 89 of 2248
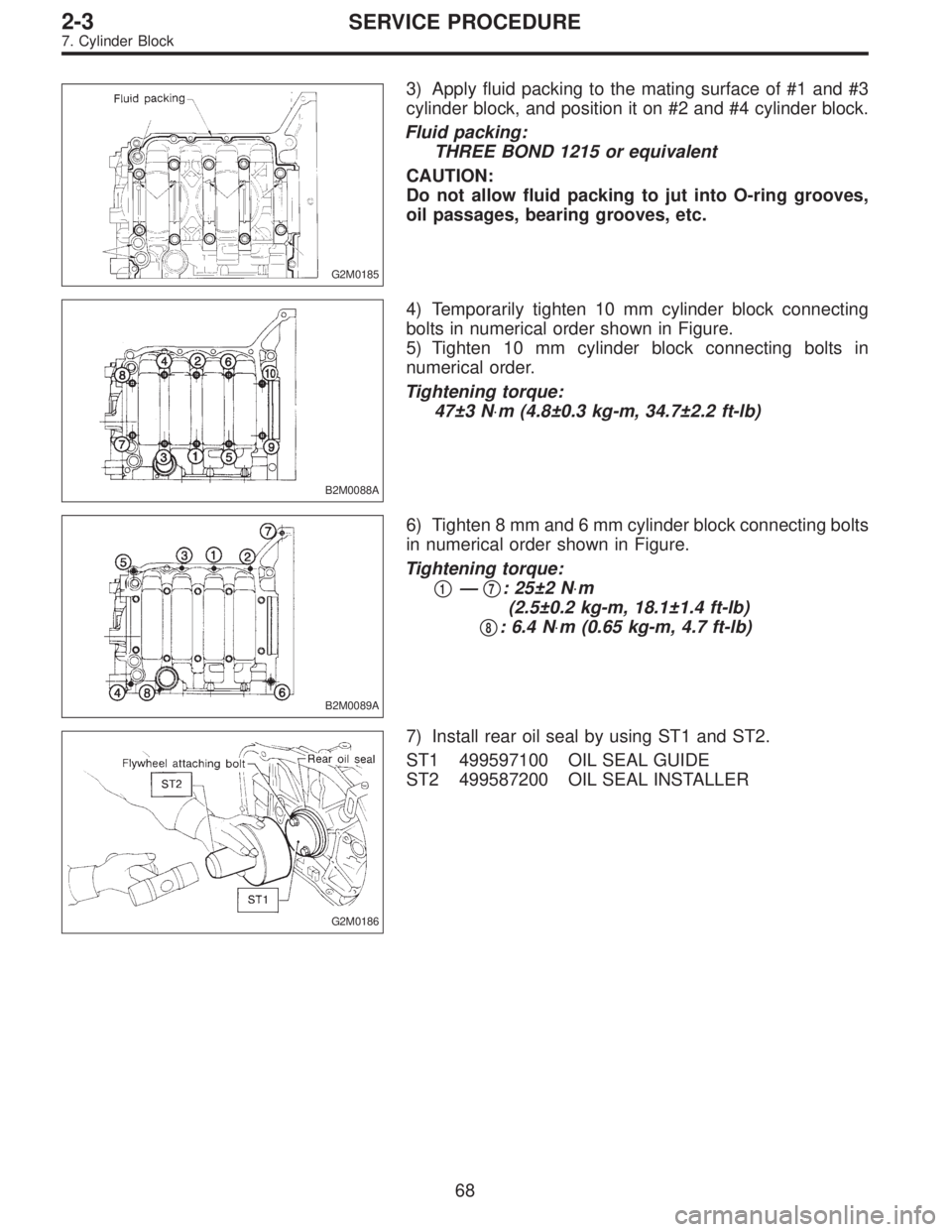
G2M0185
3) Apply fluid packing to the mating surface of #1 and #3
cylinder block, and position it on #2 and #4 cylinder block.
Fluid packing:
THREE BOND 1215 or equivalent
CAUTION:
Do not allow fluid packing to jut into O-ring grooves,
oil passages, bearing grooves, etc.
B2M0088A
4) Temporarily tighten 10 mm cylinder block connecting
bolts in numerical order shown in Figure.
5) Tighten 10 mm cylinder block connecting bolts in
numerical order.
Tightening torque:
47±3 N⋅m (4.8±0.3 kg-m, 34.7±2.2 ft-lb)
B2M0089A
6) Tighten 8 mm and 6 mm cylinder block connecting bolts
in numerical order shown in Figure.
Tightening torque:
1—7: 25±2 N⋅m
(2.5±0.2 kg-m, 18.1±1.4 ft-lb)
8: 6.4 N⋅m (0.65 kg-m, 4.7 ft-lb)
G2M0186
7) Install rear oil seal by using ST1 and ST2.
ST1 499597100 OIL SEAL GUIDE
ST2 499587200 OIL SEAL INSTALLER
68
2-3SERVICE PROCEDURE
7. Cylinder Block
Page 90 of 2248
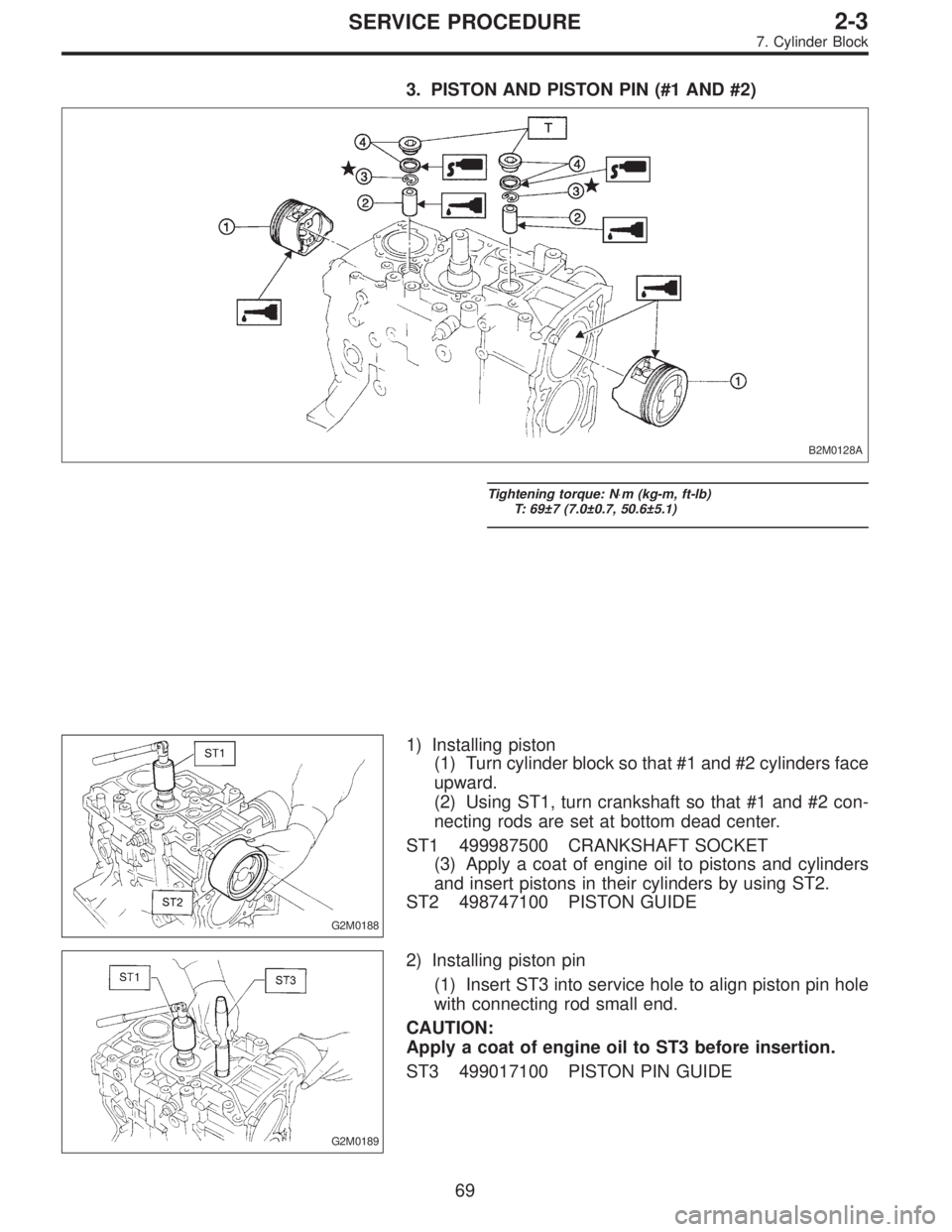
3. PISTON AND PISTON PIN (#1 AND #2)
B2M0128A
Tightening torque: N⋅m (kg-m, ft-lb)
T: 69±7 (7.0±0.7, 50.6±5.1)
G2M0188
1) Installing piston
(1) Turn cylinder block so that #1 and #2 cylinders face
upward.
(2) Using ST1, turn crankshaft so that #1 and #2 con-
necting rods are set at bottom dead center.
ST1 499987500 CRANKSHAFT SOCKET
(3) Apply a coat of engine oil to pistons and cylinders
and insert pistons in their cylinders by using ST2.
ST2 498747100 PISTON GUIDE
G2M0189
2) Installing piston pin
(1) Insert ST3 into service hole to align piston pin hole
with connecting rod small end.
CAUTION:
Apply a coat of engine oil to ST3 before insertion.
ST3 499017100 PISTON PIN GUIDE
69
2-3SERVICE PROCEDURE
7. Cylinder Block