SUZUKI GRAND VITARA 2002 2.G Service Workshop Manual
Manufacturer: SUZUKI, Model Year: 2002, Model line: GRAND VITARA, Model: SUZUKI GRAND VITARA 2002 2.GPages: 801, PDF Size: 12.15 MB
Page 651 of 801
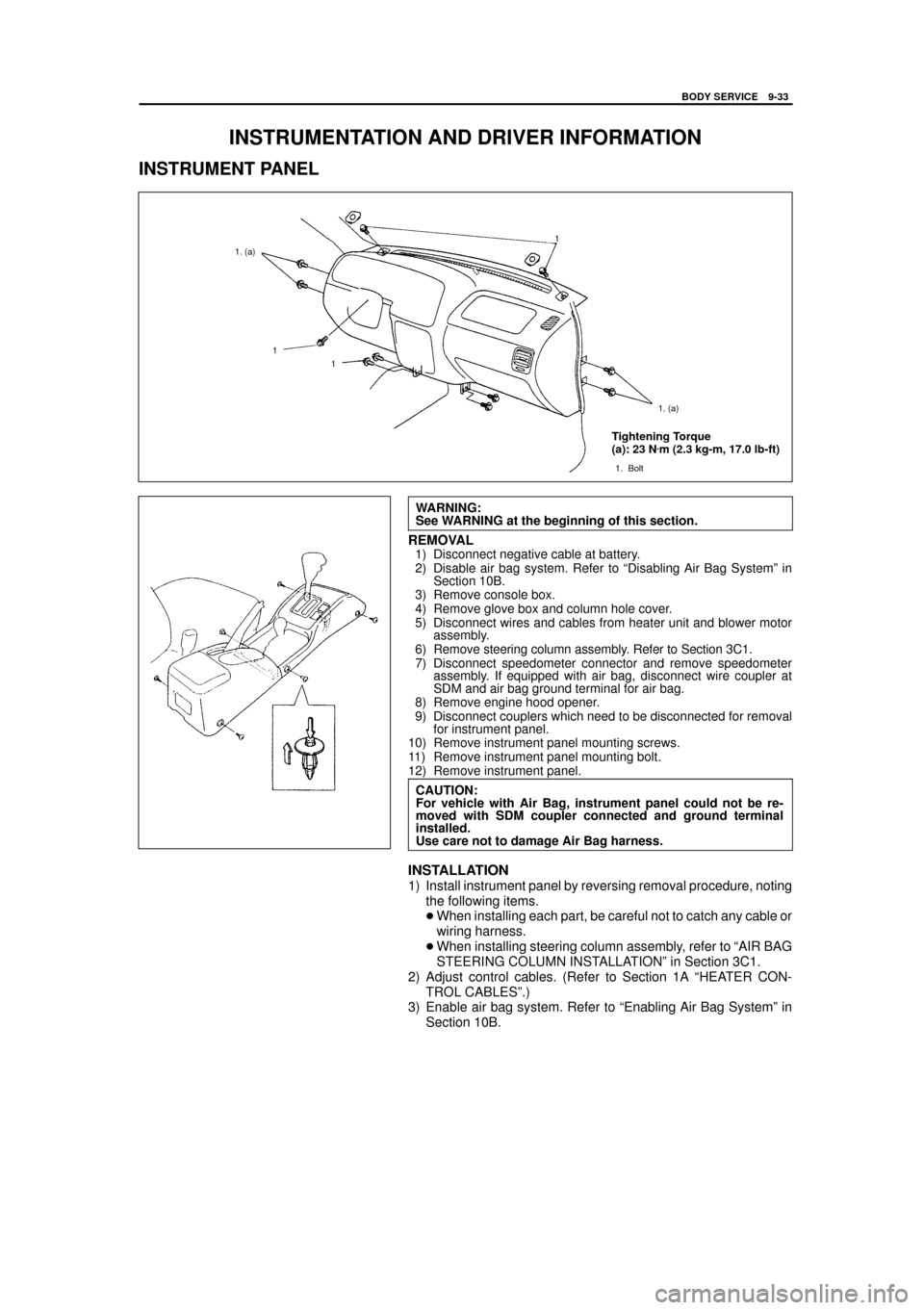
YH4
GRAND
VITARA
1. (a)
1. (a)
1
11
Tightening Torque
(a): 23 N.m (2.3 kg-m, 17.0 lb-ft)
1. Bolt
BODY SERVICE 9-33
INSTRUMENTATION AND DRIVER INFORMATION
INSTRUMENT PANEL
WARNING:
See WARNING at the beginning of this section.
REMOVAL
1) Disconnect negative cable at battery.
2) Disable air bag system. Refer to ªDisabling Air Bag Systemº in
Section 10B.
3) Remove console box.
4) Remove glove box and column hole cover.
5) Disconnect wires and cables from heater unit and blower motor
assembly.
6) Remove steering column assembly. Refer to Section 3C1.
7) Disconnect speedometer connector and remove speedometer
assembly. If equipped with air bag, disconnect wire coupler at
SDM and air bag ground terminal for air bag.
8) Remove engine hood opener.
9) Disconnect couplers which need to be disconnected for removal
for instrument panel.
10) Remove instrument panel mounting screws.
11) Remove instrument panel mounting bolt.
12) Remove instrument panel.
CAUTION:
For vehicle with Air Bag, instrument panel could not be re-
moved with SDM coupler connected and ground terminal
installed.
Use care not to damage Air Bag harness.
INSTALLATION
1) Install instrument panel by reversing removal procedure, noting
the following items.
When installing each part, be careful not to catch any cable or
wiring harness.
When installing steering column assembly, refer to ªAIR BAG
STEERING COLUMN INSTALLATIONº in Section 3C1.
2) Adjust control cables. (Refer to Section 1A ªHEATER CON-
TROL CABLESº.)
3) Enable air bag system. Refer to ªEnabling Air Bag Systemº in
Section 10B.
Page 652 of 801
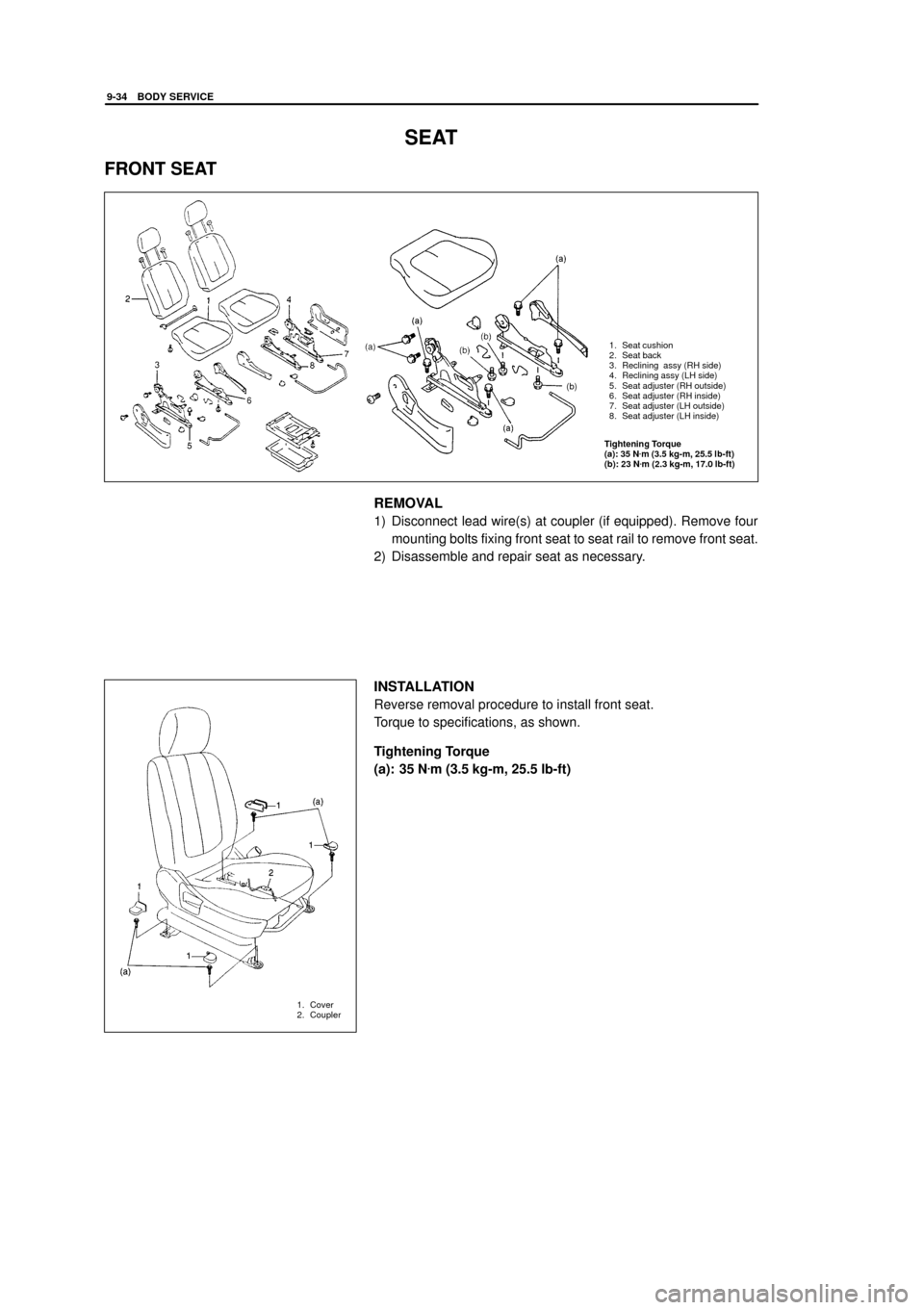
YH4
GRAND
VITARA
1. Seat cushion
2. Seat back
3. Reclining assy (RH side)
4. Reclining assy (LH side)
5. Seat adjuster (RH outside)
6. Seat adjuster (RH inside)
7. Seat adjuster (LH outside)
8. Seat adjuster (LH inside)
Tightening Torque
(a): 35 N
.m (3.5 kg-m, 25.5 lb-ft)
(b): 23 N.m (2.3 kg-m, 17.0 lb-ft)
1. Cover
2. Coupler(b)
9-34 BODY SERVICE
SEAT
FRONT SEAT
REMOVAL
1) Disconnect lead wire(s) at coupler (if equipped). Remove four
mounting bolts fixing front seat to seat rail to remove front seat.
2) Disassemble and repair seat as necessary.
INSTALLATION
Reverse removal procedure to install front seat.
Torque to specifications, as shown.
Tightening Torque
(a): 35 N
.m (3.5 kg-m, 25.5 lb-ft)
Page 653 of 801
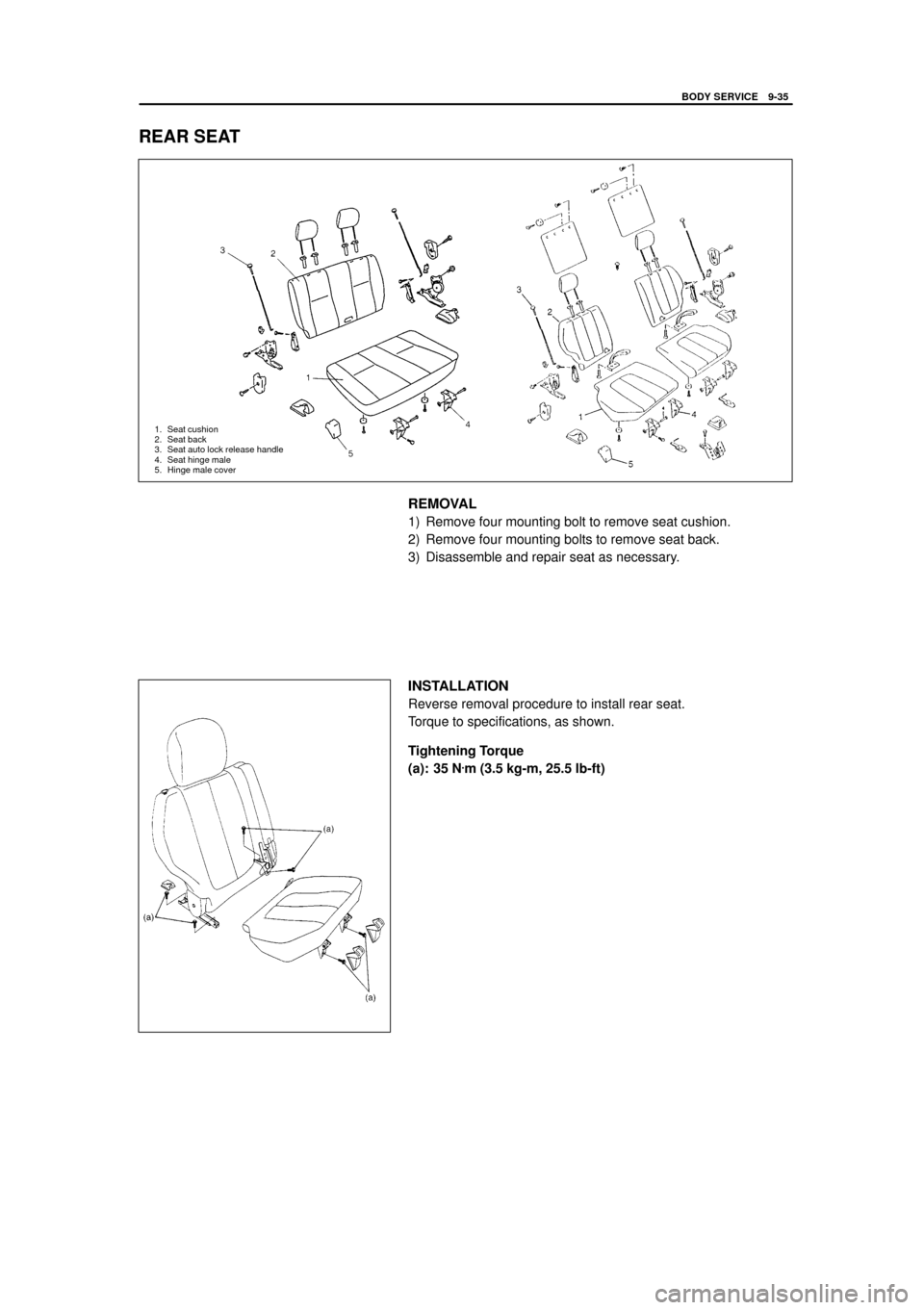
YH4
GRAND
VITARA
1. Seat cushion
2. Seat back
3. Seat auto lock release handle
4. Seat hinge male
5. Hinge male cover
BODY SERVICE 9-35
REAR SEAT
REMOVAL
1) Remove four mounting bolt to remove seat cushion.
2) Remove four mounting bolts to remove seat back.
3) Disassemble and repair seat as necessary.
INSTALLATION
Reverse removal procedure to install rear seat.
Torque to specifications, as shown.
Tightening Torque
(a): 35 N
.m (3.5 kg-m, 25.5 lb-ft)
Page 654 of 801
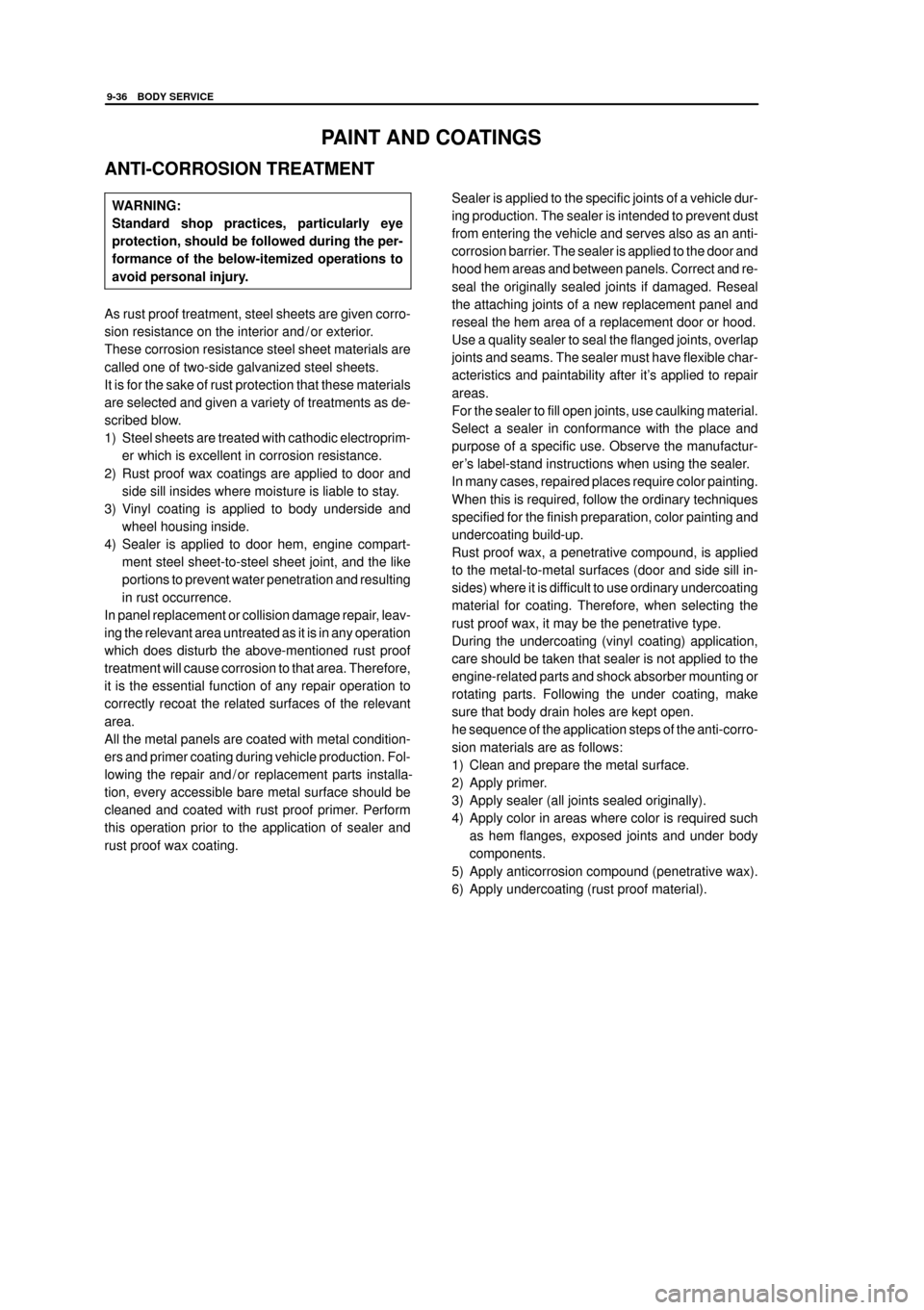
YH4
GRAND
VITARA
9-36 BODY SERVICE
Sealer is applied to the specific joints of a vehicle dur-
ing production. The sealer is intended to prevent dust
from entering the vehicle and serves also as an anti-
corrosion barrier. The sealer is applied to the door and
hood hem areas and between panels. Correct and re-
seal the originally sealed joints if damaged. Reseal
the attaching joints of a new replacement panel and
reseal the hem area of a replacement door or hood.
Use a quality sealer to seal the flanged joints, overlap
joints and seams. The sealer must have flexible char-
acteristics and paintability after it's applied to repair
areas.
For the sealer to fill open joints, use caulking material.
Select a sealer in conformance with the place and
purpose of a specific use. Observe the manufactur-
er's label-stand instructions when using the sealer.
In many cases, repaired places require color painting.
When this is required, follow the ordinary techniques
specified for the finish preparation, color painting and
undercoating build-up.
Rust proof wax, a penetrative compound, is applied
to the metal-to-metal surfaces (door and side sill in-
sides) where it is difficult to use ordinary undercoating
material for coating. Therefore, when selecting the
rust proof wax, it may be the penetrative type.
During the undercoating (vinyl coating) application,
care should be taken that sealer is not applied to the
engine-related parts and shock absorber mounting or
rotating parts. Following the under coating, make
sure that body drain holes are kept open.
he sequence of the application steps of the anti-corro-
sion materials are as follows:
1) Clean and prepare the metal surface.
2) Apply primer.
3) Apply sealer (all joints sealed originally).
4) Apply color in areas where color is required such
as hem flanges, exposed joints and under body
components.
5) Apply anticorrosion compound (penetrative wax).
6) Apply undercoating (rust proof material).
PAINT AND COATINGS
ANTI-CORROSION TREATMENT
WARNING:
Standard shop practices, particularly eye
protection, should be followed during the per-
formance of the below-itemized operations to
avoid personal injury.
As rust proof treatment, steel sheets are given corro-
sion resistance on the interior and / or exterior.
These corrosion resistance steel sheet materials are
called one of two-side galvanized steel sheets.
It is for the sake of rust protection that these materials
are selected and given a variety of treatments as de-
scribed blow.
1) Steel sheets are treated with cathodic electroprim-
er which is excellent in corrosion resistance.
2) Rust proof wax coatings are applied to door and
side sill insides where moisture is liable to stay.
3) Vinyl coating is applied to body underside and
wheel housing inside.
4) Sealer is applied to door hem, engine compart-
ment steel sheet-to-steel sheet joint, and the like
portions to prevent water penetration and resulting
in rust occurrence.
In panel replacement or collision damage repair, leav-
ing the relevant area untreated as it is in any operation
which does disturb the above-mentioned rust proof
treatment will cause corrosion to that area. Therefore,
it is the essential function of any repair operation to
correctly recoat the related surfaces of the relevant
area.
All the metal panels are coated with metal condition-
ers and primer coating during vehicle production. Fol-
lowing the repair and / or replacement parts installa-
tion, every accessible bare metal surface should be
cleaned and coated with rust proof primer. Perform
this operation prior to the application of sealer and
rust proof wax coating.
Page 655 of 801
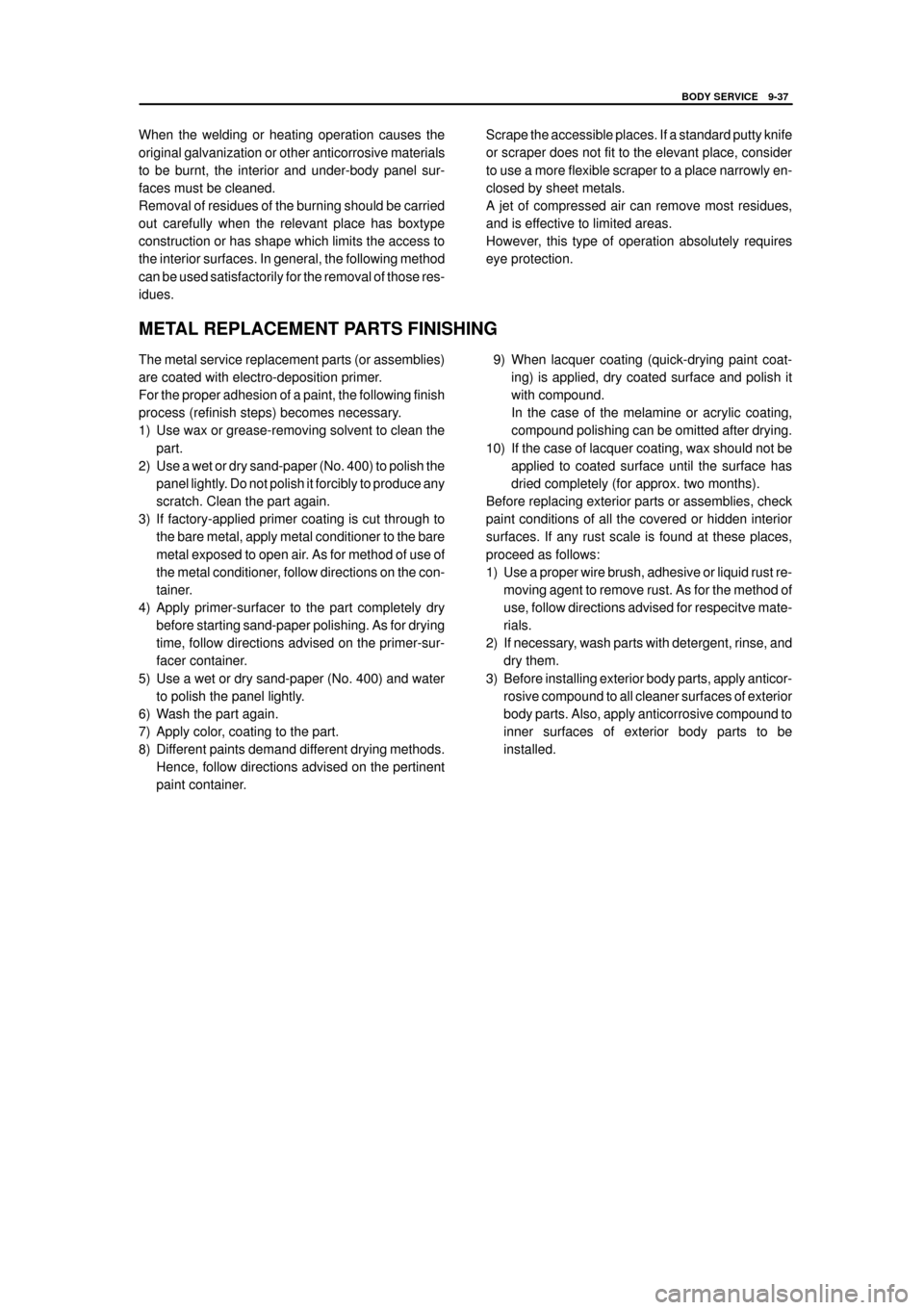
YH4
GRAND
VITARA
When the welding or heating operation causes the
original galvanization or other anticorrosive materials
to be burnt, the interior and under-body panel sur-
faces must be cleaned.
Removal of residues of the burning should be carried
out carefully when the relevant place has boxtype
construction or has shape which limits the access to
the interior surfaces. In general, the following method
can be used satisfactorily for the removal of those res-
idues.Scrape the accessible places. If a standard putty knife
or scraper does not fit to the elevant place, consider
to use a more flexible scraper to a place narrowly en-
closed by sheet metals.
A jet of compressed air can remove most residues,
and is effective to limited areas.
However, this type of operation absolutely requires
eye protection.
BODY SERVICE 9-37
The metal service replacement parts (or assemblies)
are coated with electro-deposition primer.
For the proper adhesion of a paint, the following finish
process (refinish steps) becomes necessary.
1) Use wax or grease-removing solvent to clean the
part.
2) Use a wet or dry sand-paper (No. 400) to polish the
panel lightly. Do not polish it forcibly to produce any
scratch. Clean the part again.
3) If factory-applied primer coating is cut through to
the bare metal, apply metal conditioner to the bare
metal exposed to open air. As for method of use of
the metal conditioner, follow directions on the con-
tainer.
4) Apply primer-surfacer to the part completely dry
before starting sand-paper polishing. As for drying
time, follow directions advised on the primer-sur-
facer container.
5) Use a wet or dry sand-paper (No. 400) and water
to polish the panel lightly.
6) Wash the part again.
7) Apply color, coating to the part.
8) Different paints demand different drying methods.
Hence, follow directions advised on the pertinent
paint container.9) When lacquer coating (quick-drying paint coat-
ing) is applied, dry coated surface and polish it
with compound.
In the case of the melamine or acrylic coating,
compound polishing can be omitted after drying.
10) If the case of lacquer coating, wax should not be
applied to coated surface until the surface has
dried completely (for approx. two months).
Before replacing exterior parts or assemblies, check
paint conditions of all the covered or hidden interior
surfaces. If any rust scale is found at these places,
proceed as follows:
1) Use a proper wire brush, adhesive or liquid rust re-
moving agent to remove rust. As for the method of
use, follow directions advised for respecitve mate-
rials.
2) If necessary, wash parts with detergent, rinse, and
dry them.
3) Before installing exterior body parts, apply anticor-
rosive compound to all cleaner surfaces of exterior
body parts. Also, apply anticorrosive compound to
inner surfaces of exterior body parts to be
installed.
METAL REPLACEMENT PARTS FINISHING
Page 656 of 801
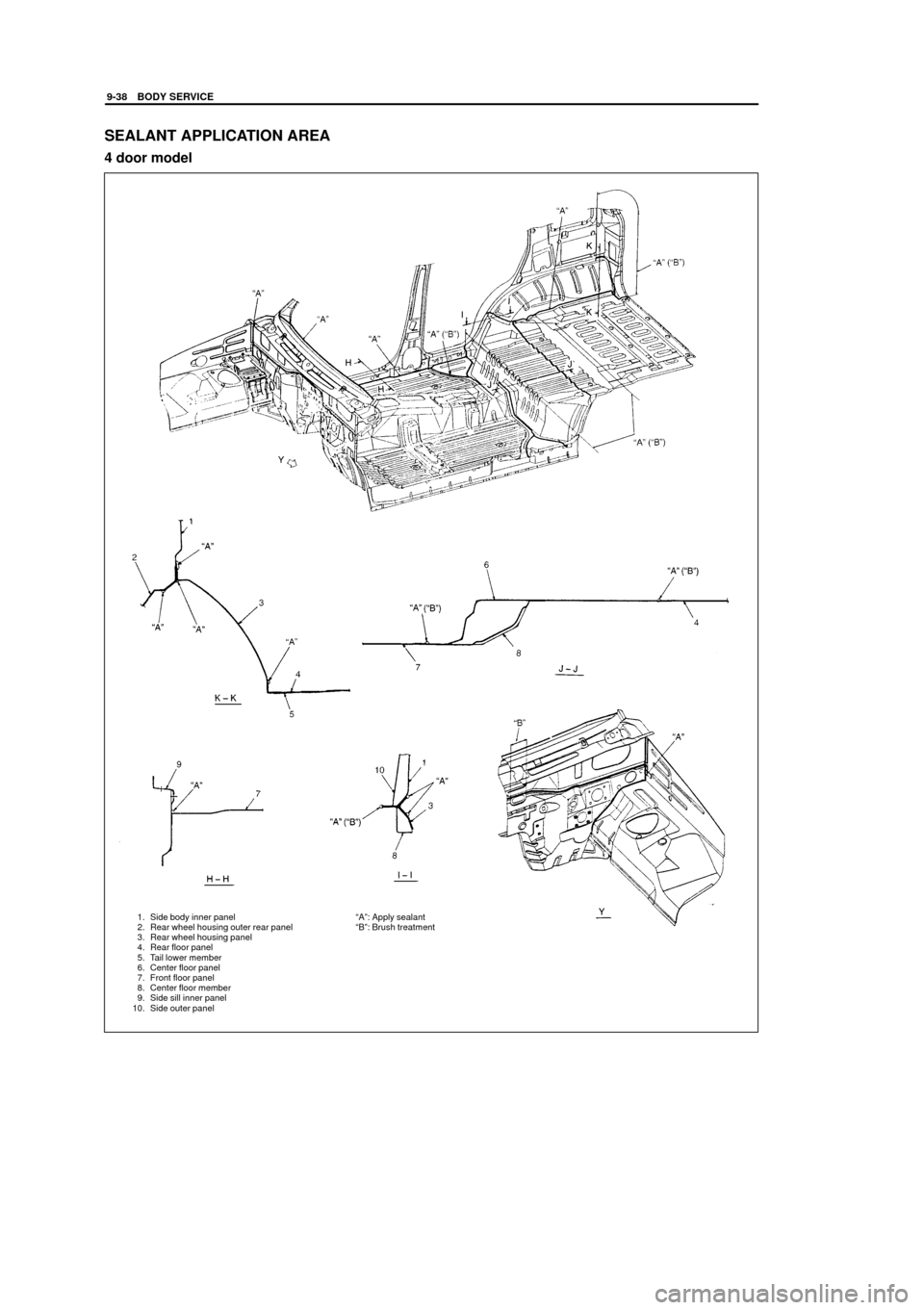
YH4
GRAND
VITARA
1. Side body inner panel
2. Rear wheel housing outer rear panel
3. Rear wheel housing panel
4. Rear floor panel
5. Tail lower member
6. Center floor panel
7. Front floor panel
8. Center floor member
9. Side sill inner panel
10. Side outer panelªAº: Apply sealant
ªBº: Brush treatment
9-38 BODY SERVICE
SEALANT APPLICATION AREA
4 door model
Page 657 of 801
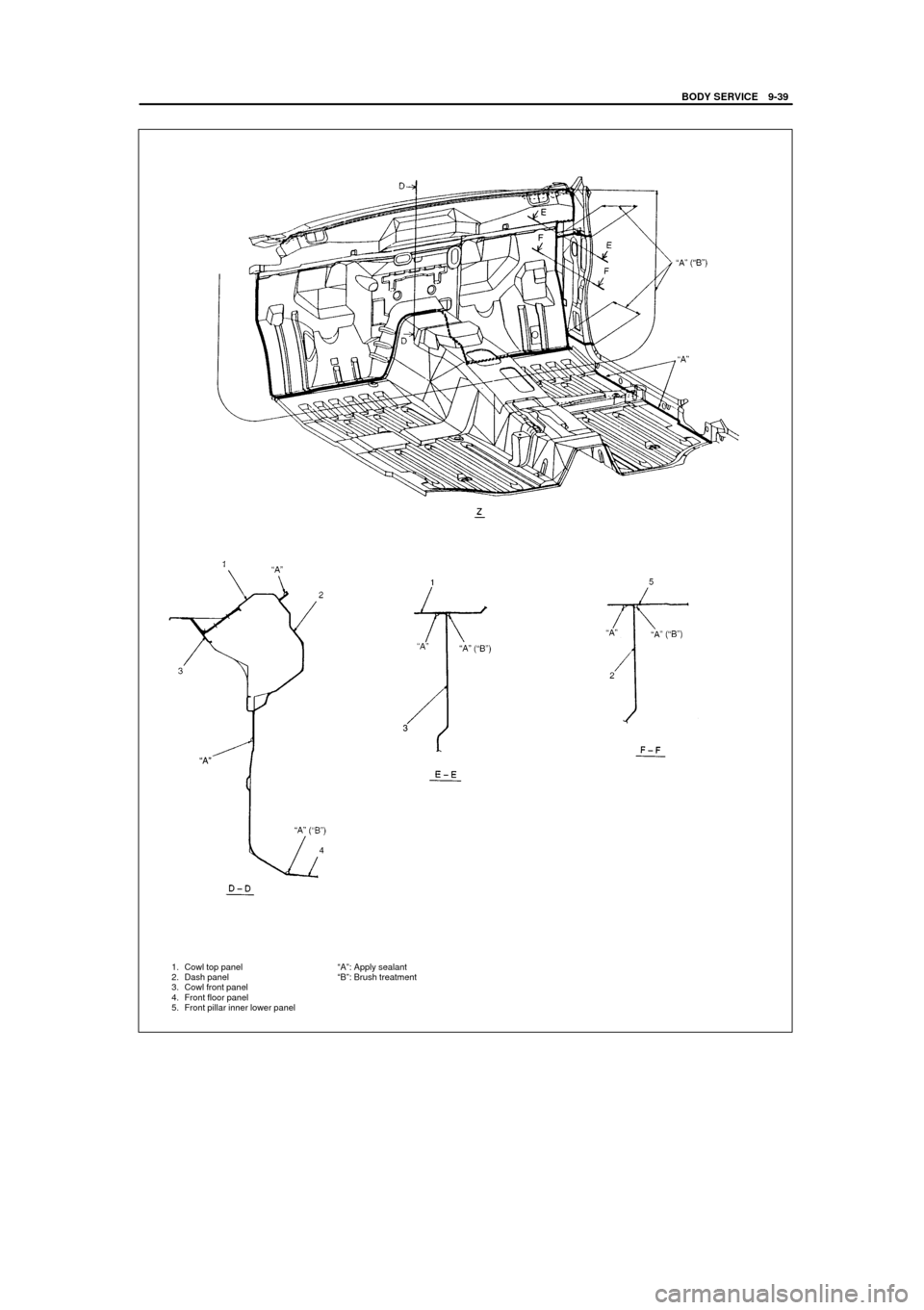
YH4
GRAND
VITARA
1. Cowl top panel
2. Dash panel
3. Cowl front panel
4. Front floor panel
5. Front pillar inner lower panelªAº: Apply sealant
ªBº: Brush treatment
BODY SERVICE 9-39
Page 658 of 801
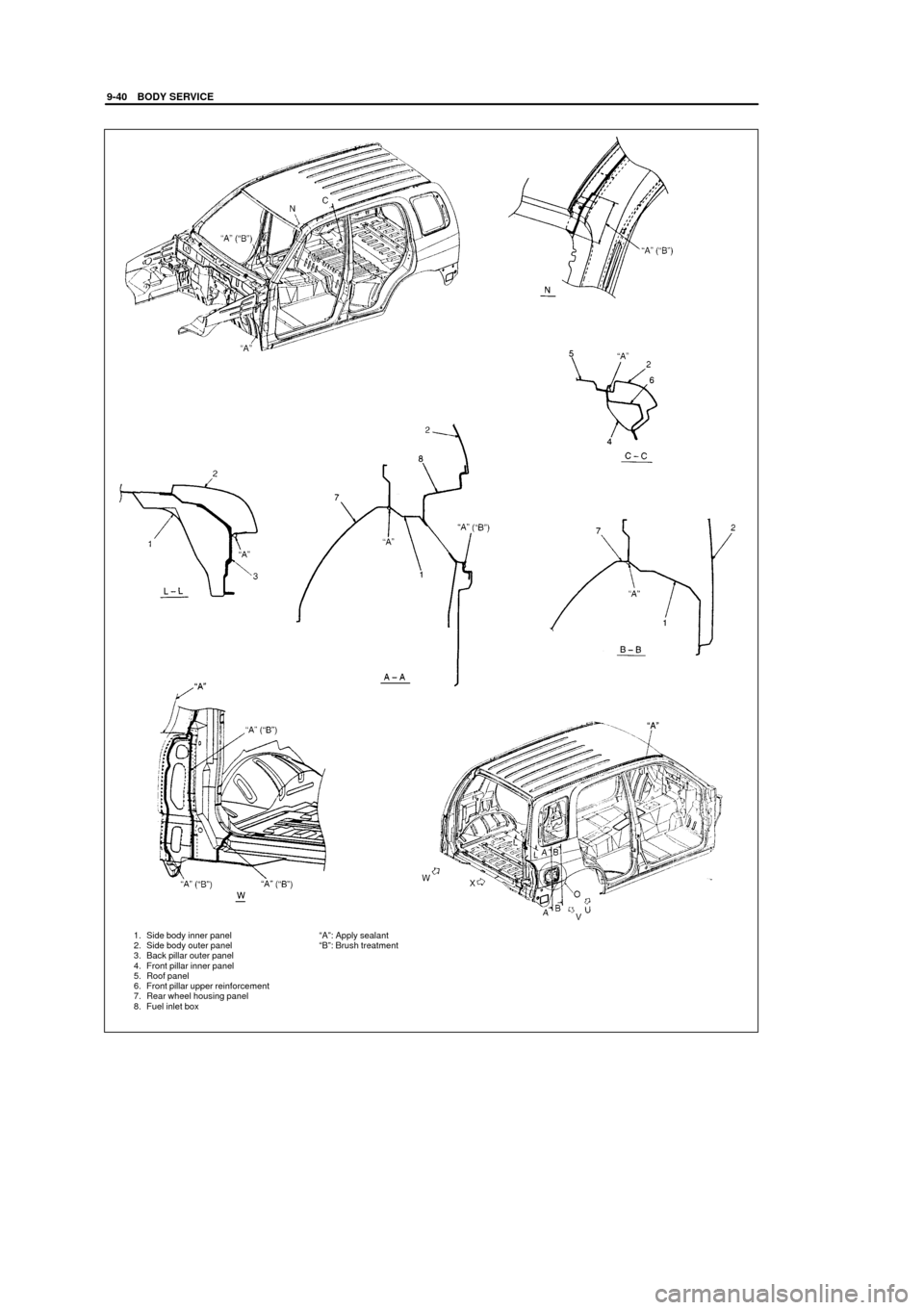
YH4
GRAND
VITARA
9-40 BODY SERVICE
1. Side body inner panel
2. Side body outer panel
3. Back pillar outer panel
4. Front pillar inner panel
5. Roof panel
6. Front pillar upper reinforcement
7. Rear wheel housing panel
8. Fuel inlet boxªAº: Apply sealant
ªBº: Brush treatment
Page 659 of 801
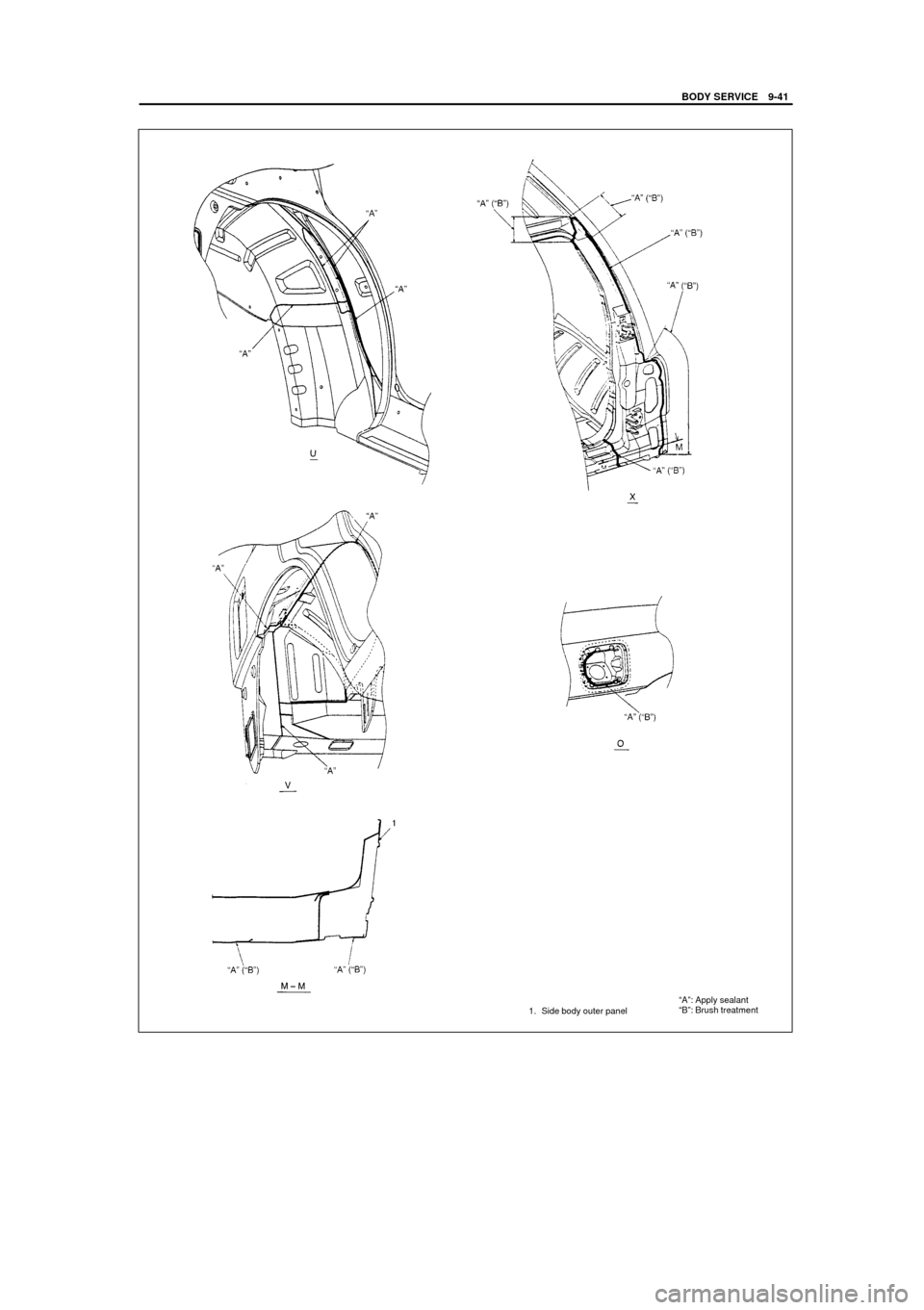
YH4
GRAND
VITARA
BODY SERVICE 9-41
1. Side body outer panelªAº: Apply sealant
ªBº: Brush treatment
Page 660 of 801
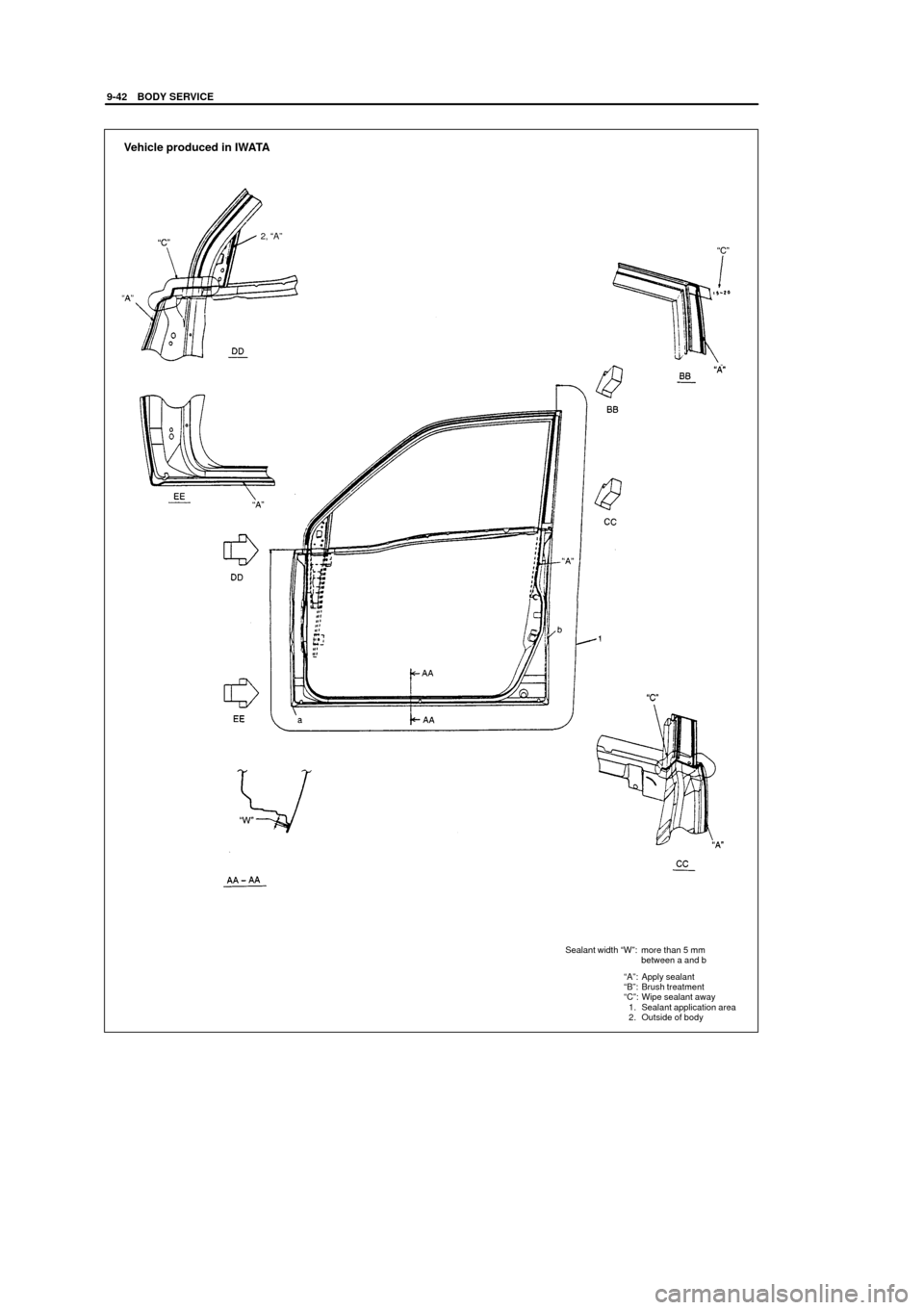
YH4
GRAND
VITARA
9-42 BODY SERVICE
Sealant width ªWº: more than 5 mm
between a and b
ªAº: Apply sealant
ªBº: Brush treatment
ªCº: Wipe sealant away
1. Sealant application area
2. Outside of body 2, ªAº
Vehicle produced in IWATA