engine SUZUKI JIMNY 2005 3.G Service Workshop Manual
[x] Cancel search | Manufacturer: SUZUKI, Model Year: 2005, Model line: JIMNY, Model: SUZUKI JIMNY 2005 3.GPages: 687, PDF Size: 13.38 MB
Page 341 of 687
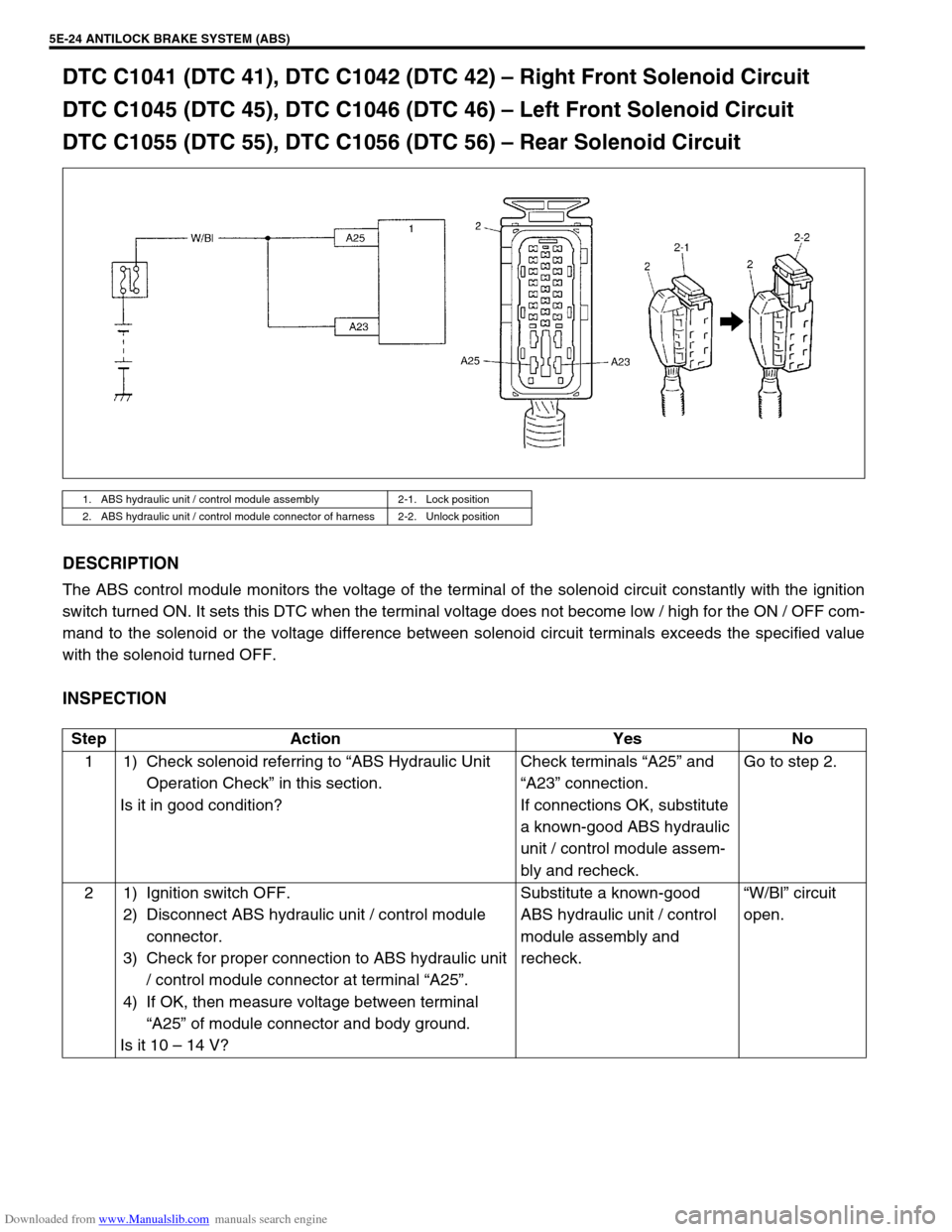
Downloaded from www.Manualslib.com manuals search engine 5E-24 ANTILOCK BRAKE SYSTEM (ABS)
DTC C1041 (DTC 41), DTC C1042 (DTC 42) – Right Front Solenoid Circuit
DTC C1045 (DTC 45), DTC C1046 (DTC 46) – Left Front Solenoid Circuit
DTC C1055 (DTC 55), DTC C1056 (DTC 56) – Rear Solenoid Circuit
DESCRIPTION
The ABS control module monitors the voltage of the terminal of the solenoid circuit constantly with the ignition
switch turned ON. It sets this DTC when the terminal voltage does not become low / high for the ON / OFF com-
mand to the solenoid or the voltage difference between solenoid circuit terminals exceeds the specified value
with the solenoid turned OFF.
INSPECTION
1. ABS hydraulic unit / control module assembly 2-1. Lock position
2. ABS hydraulic unit / control module connector of harness 2-2. Unlock position
Step Action Yes No
1 1) Check solenoid referring to “ABS Hydraulic Unit
Operation Check” in this section.
Is it in good condition?Check terminals “A25” and
“A23” connection.
If connections OK, substitute
a known-good ABS hydraulic
unit / control module assem-
bly and recheck.Go to step 2.
2 1) Ignition switch OFF.
2) Disconnect ABS hydraulic unit / control module
connector.
3) Check for proper connection to ABS hydraulic unit
/ control module connector at terminal “A25”.
4) If OK, then measure voltage between terminal
“A25” of module connector and body ground.
Is it 10 – 14 V?Substitute a known-good
ABS hydraulic unit / control
module assembly and
recheck.“W/Bl” circuit
open.
Page 342 of 687
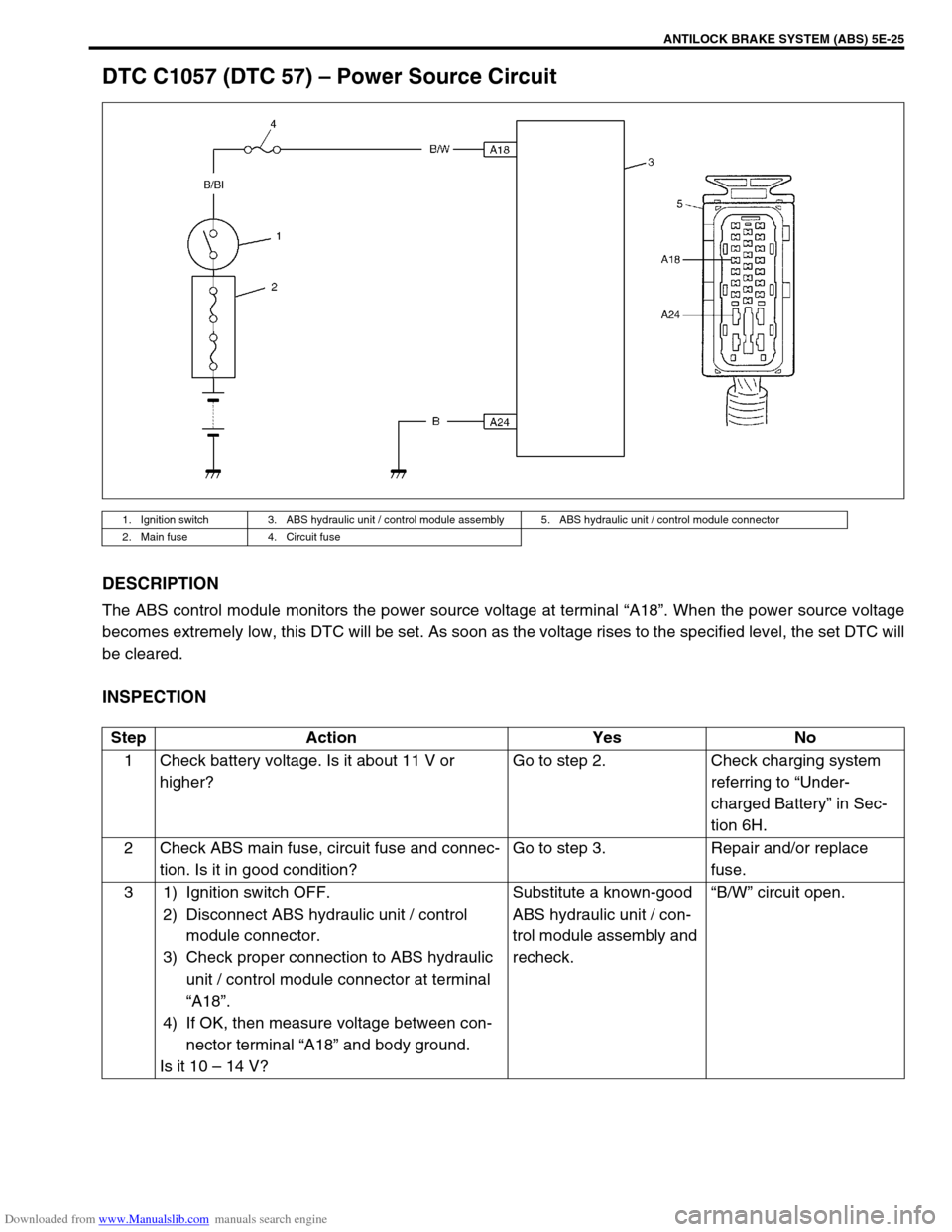
Downloaded from www.Manualslib.com manuals search engine ANTILOCK BRAKE SYSTEM (ABS) 5E-25
DTC C1057 (DTC 57) – Power Source Circuit
DESCRIPTION
The ABS control module monitors the power source voltage at terminal “A18”. When the power source voltage
becomes extremely low, this DTC will be set. As soon as the voltage rises to the specified level, the set DTC will
be cleared.
INSPECTION
1. Ignition switch 3. ABS hydraulic unit / control module assembly 5. ABS hydraulic unit / control module connector
2. Main fuse 4. Circuit fuse
Step Action Yes No
1 Check battery voltage. Is it about 11 V or
higher?Go to step 2. Check charging system
referring to “Under-
charged Battery” in Sec-
tion 6H.
2 Check ABS main fuse, circuit fuse and connec-
tion. Is it in good condition?Go to step 3. Repair and/or replace
fuse.
3 1) Ignition switch OFF.
2) Disconnect ABS hydraulic unit / control
module connector.
3) Check proper connection to ABS hydraulic
unit / control module connector at terminal
“A18”.
4) If OK, then measure voltage between con-
nector terminal “A18” and body ground.
Is it 10 – 14 V?Substitute a known-good
ABS hydraulic unit / con-
trol module assembly and
recheck.“B/W” circuit open.
Page 343 of 687
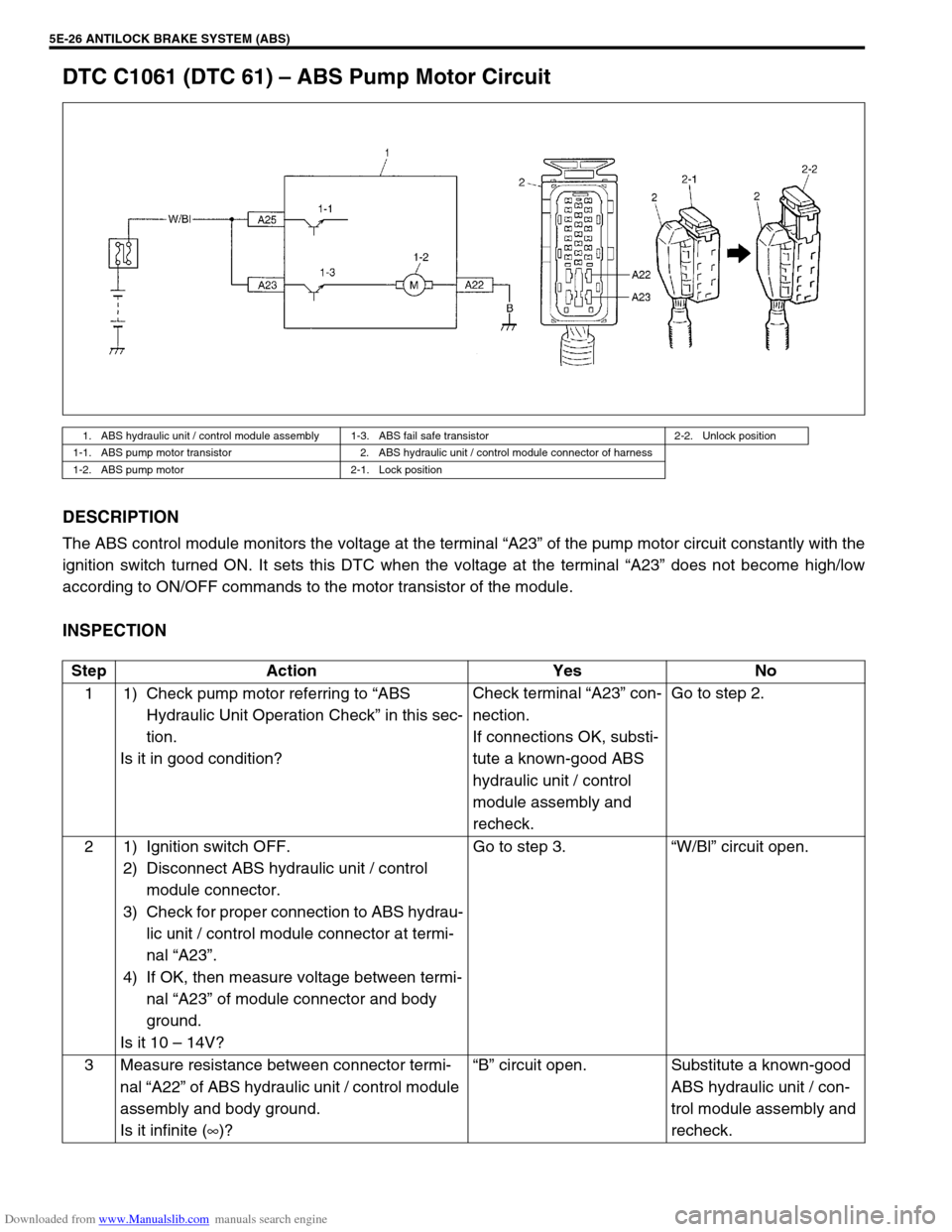
Downloaded from www.Manualslib.com manuals search engine 5E-26 ANTILOCK BRAKE SYSTEM (ABS)
DTC C1061 (DTC 61) – ABS Pump Motor Circuit
DESCRIPTION
The ABS control module monitors the voltage at the terminal “A23” of the pump motor circuit constantly with the
ignition switch turned ON. It sets this DTC when the voltage at the terminal “A23” does not become high/low
according to ON/OFF commands to the motor transistor of the module.
INSPECTION
1. ABS hydraulic unit / control module assembly 1-3. ABS fail safe transistor 2-2. Unlock position
1-1. ABS pump motor transistor 2. ABS hydraulic unit / control module connector of harness
1-2. ABS pump motor 2-1. Lock position
Step Action Yes No
1 1) Check pump motor referring to “ABS
Hydraulic Unit Operation Check” in this sec-
tion.
Is it in good condition?Check terminal “A23” con-
nection.
If connections OK, substi-
tute a known-good ABS
hydraulic unit / control
module assembly and
recheck.Go to step 2.
2 1) Ignition switch OFF.
2) Disconnect ABS hydraulic unit / control
module connector.
3) Check for proper connection to ABS hydrau-
lic unit / control module connector at termi-
nal “A23”.
4) If OK, then measure voltage between termi-
nal “A23” of module connector and body
ground.
Is it 10 – 14V?Go to step 3.“W/Bl” circuit open.
3 Measure resistance between connector termi-
nal “A22” of ABS hydraulic unit / control module
assembly and body ground.
Is it infinite (∞)?“B” circuit open. Substitute a known-good
ABS hydraulic unit / con-
trol module assembly and
recheck.
Page 344 of 687
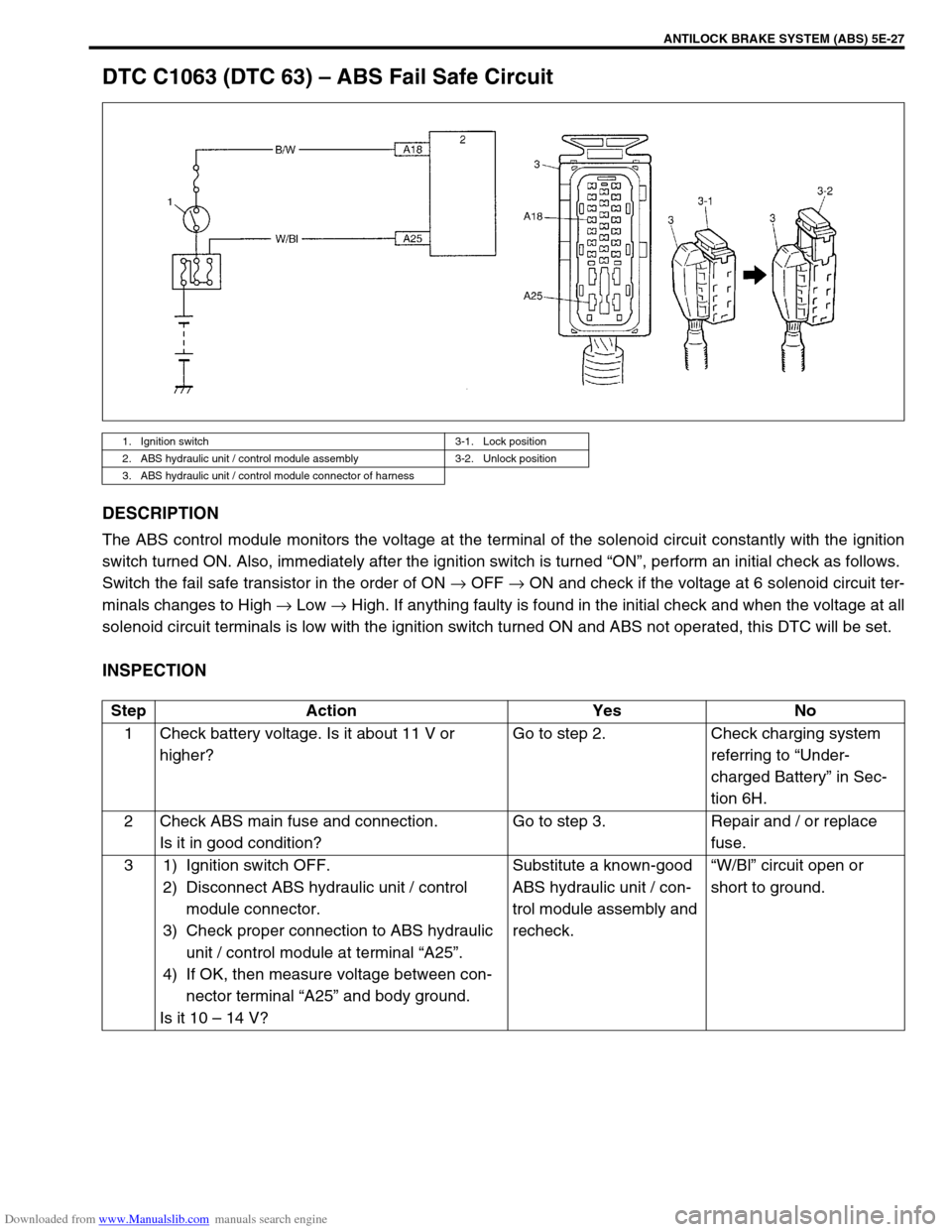
Downloaded from www.Manualslib.com manuals search engine ANTILOCK BRAKE SYSTEM (ABS) 5E-27
DTC C1063 (DTC 63) – ABS Fail Safe Circuit
DESCRIPTION
The ABS control module monitors the voltage at the terminal of the solenoid circuit constantly with the ignition
switch turned ON. Also, immediately after the ignition switch is turned “ON”, perform an initial check as follows.
Switch the fail safe transistor in the order of ON → OFF → ON and check if the voltage at 6 solenoid circuit ter-
minals changes to High → Low → High. If anything faulty is found in the initial check and when the voltage at all
solenoid circuit terminals is low with the ignition switch turned ON and ABS not operated, this DTC will be set.
INSPECTION
1. Ignition switch 3-1. Lock position
2. ABS hydraulic unit / control module assembly 3-2. Unlock position
3. ABS hydraulic unit / control module connector of harness
Step Action Yes No
1 Check battery voltage. Is it about 11 V or
higher?Go to step 2. Check charging system
referring to “Under-
charged Battery” in Sec-
tion 6H.
2 Check ABS main fuse and connection.
Is it in good condition?Go to step 3. Repair and / or replace
fuse.
3 1) Ignition switch OFF.
2) Disconnect ABS hydraulic unit / control
module connector.
3) Check proper connection to ABS hydraulic
unit / control module at terminal “A25”.
4) If OK, then measure voltage between con-
nector terminal “A25” and body ground.
Is it 10 – 14 V?Substitute a known-good
ABS hydraulic unit / con-
trol module assembly and
recheck.“W/Bl” circuit open or
short to ground.
Page 345 of 687
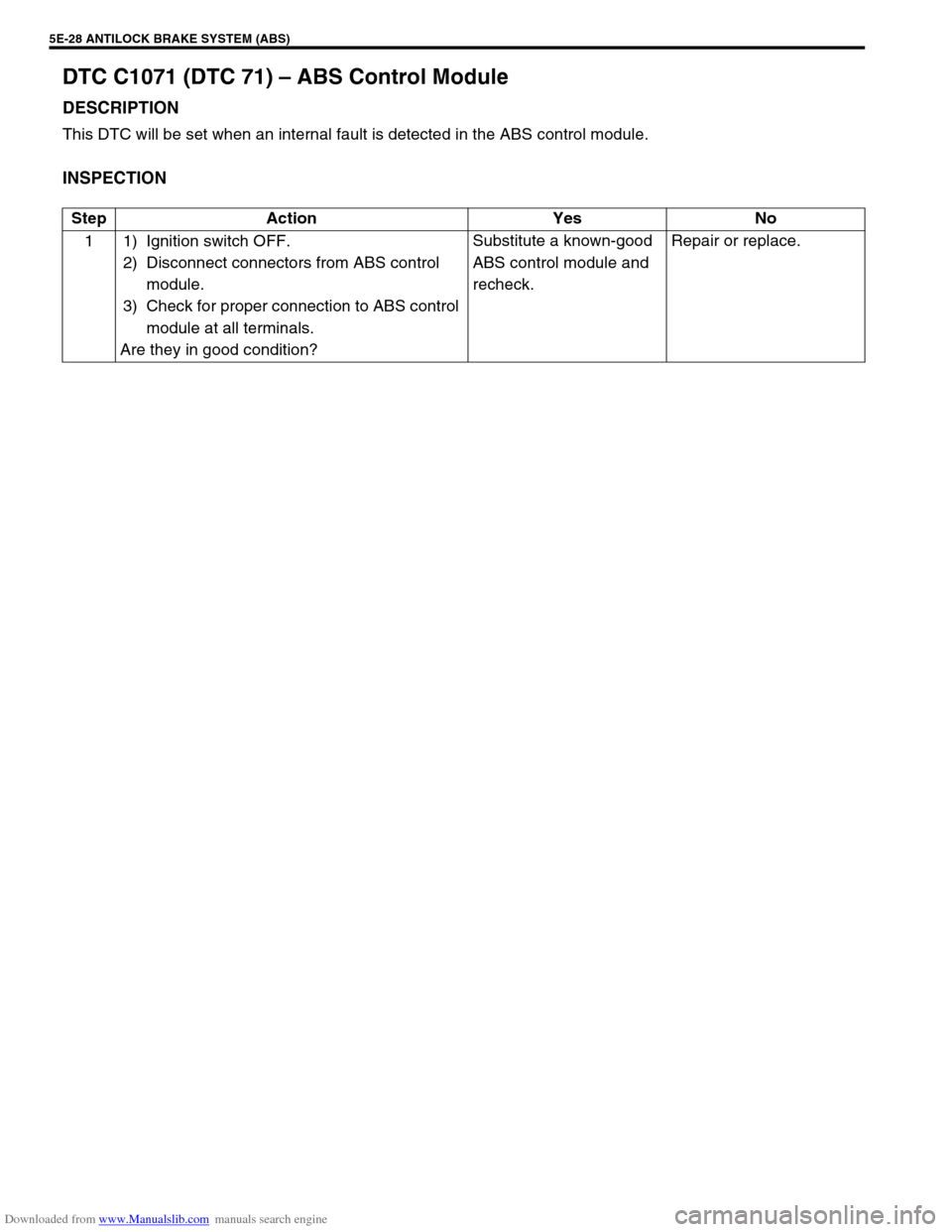
Downloaded from www.Manualslib.com manuals search engine 5E-28 ANTILOCK BRAKE SYSTEM (ABS)
DTC C1071 (DTC 71) – ABS Control Module
DESCRIPTION
This DTC will be set when an internal fault is detected in the ABS control module.
INSPECTION
Step Action Yes No
1 1) Ignition switch OFF.
2) Disconnect connectors from ABS control
module.
3) Check for proper connection to ABS control
module at all terminals.
Are they in good condition?Substitute a known-good
ABS control module and
recheck.Repair or replace.
Page 346 of 687
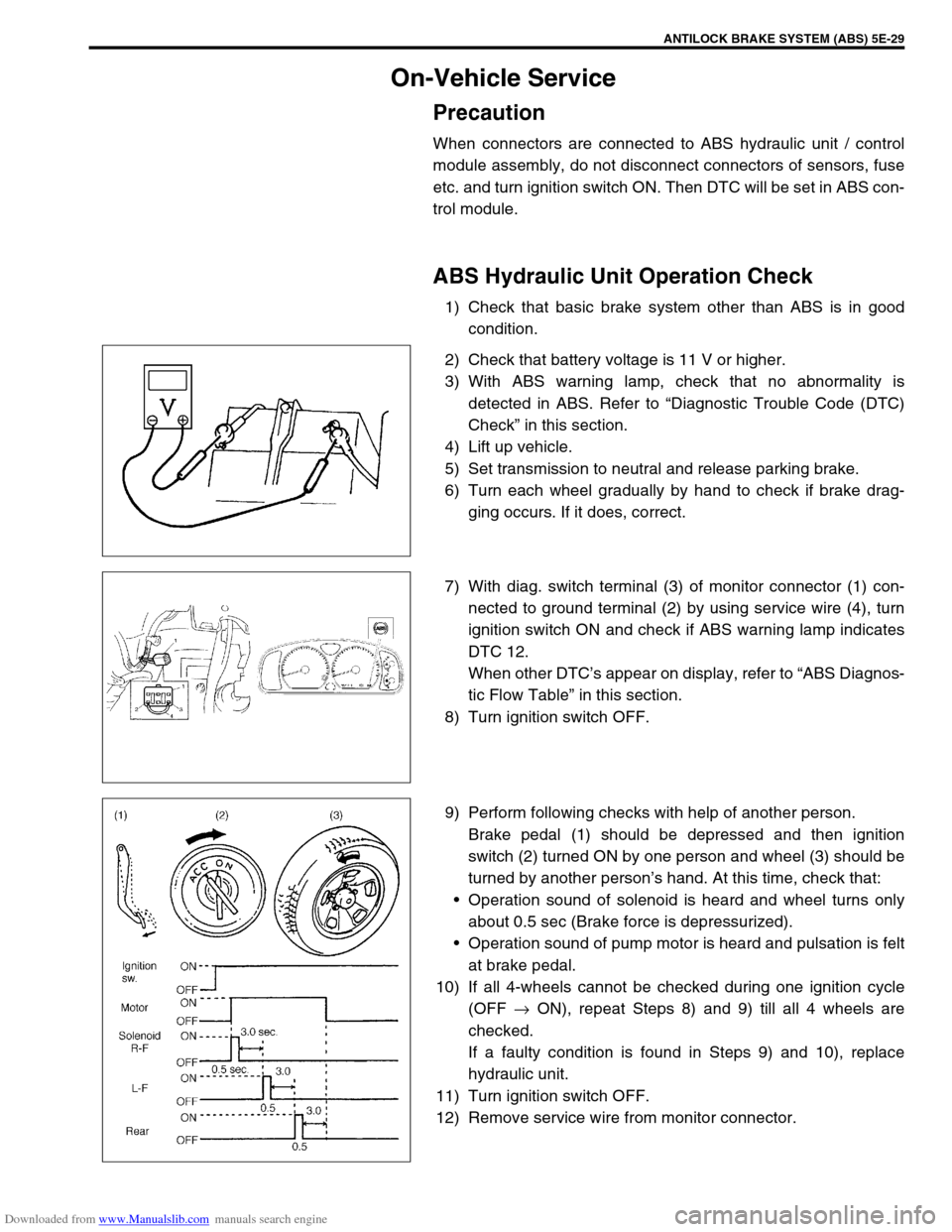
Downloaded from www.Manualslib.com manuals search engine ANTILOCK BRAKE SYSTEM (ABS) 5E-29
On-Vehicle Service
Precaution
When connectors are connected to ABS hydraulic unit / control
module assembly, do not disconnect connectors of sensors, fuse
etc. and turn ignition switch ON. Then DTC will be set in ABS con-
trol module.
ABS Hydraulic Unit Operation Check
1) Check that basic brake system other than ABS is in good
condition.
2) Check that battery voltage is 11 V or higher.
3) With ABS warning lamp, check that no abnormality is
detected in ABS. Refer to “Diagnostic Trouble Code (DTC)
Check” in this section.
4) Lift up vehicle.
5) Set transmission to neutral and release parking brake.
6) Turn each wheel gradually by hand to check if brake drag-
ging occurs. If it does, correct.
7) With diag. switch terminal (3) of monitor connector (1) con-
nected to ground terminal (2) by using service wire (4), turn
ignition switch ON and check if ABS warning lamp indicates
DTC 12.
When other DTC’s appear on display, refer to “ABS Diagnos-
tic Flow Table” in this section.
8) Turn ignition switch OFF.
9) Perform following checks with help of another person.
Brake pedal (1) should be depressed and then ignition
switch (2) turned ON by one person and wheel (3) should be
turned by another person’s hand. At this time, check that:
Operation sound of solenoid is heard and wheel turns only
about 0.5 sec (Brake force is depressurized).
Operation sound of pump motor is heard and pulsation is felt
at brake pedal.
10) If all 4-wheels cannot be checked during one ignition cycle
(OFF → ON), repeat Steps 8) and 9) till all 4 wheels are
checked.
If a faulty condition is found in Steps 9) and 10), replace
hydraulic unit.
11) Turn ignition switch OFF.
12) Remove service wire from monitor connector.
Page 347 of 687
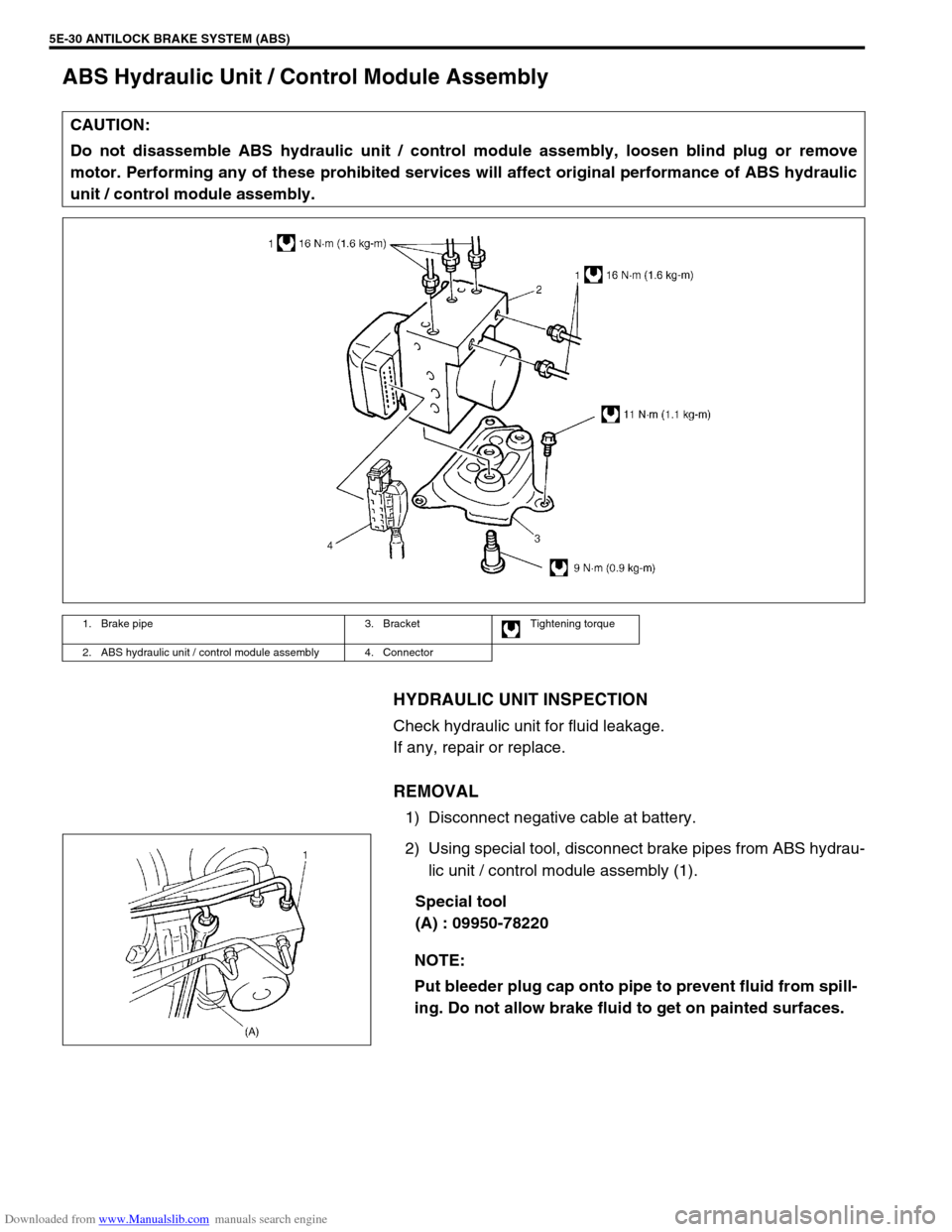
Downloaded from www.Manualslib.com manuals search engine 5E-30 ANTILOCK BRAKE SYSTEM (ABS)
ABS Hydraulic Unit / Control Module Assembly
HYDRAULIC UNIT INSPECTION
Check hydraulic unit for fluid leakage.
If any, repair or replace.
REMOVAL
1) Disconnect negative cable at battery.
2) Using special tool, disconnect brake pipes from ABS hydrau-
lic unit / control module assembly (1).
Special tool
(A) : 09950-78220 CAUTION:
Do not disassemble ABS hydraulic unit / control module assembly, loosen blind plug or remove
motor. Performing any of these prohibited services will affect original performance of ABS hydraulic
unit / control module assembly.
1. Brake pipe 3. Bracket Tightening torque
2. ABS hydraulic unit / control module assembly 4. Connector
NOTE:
Put bleeder plug cap onto pipe to prevent fluid from spill-
ing. Do not allow brake fluid to get on painted surfaces.
Page 348 of 687
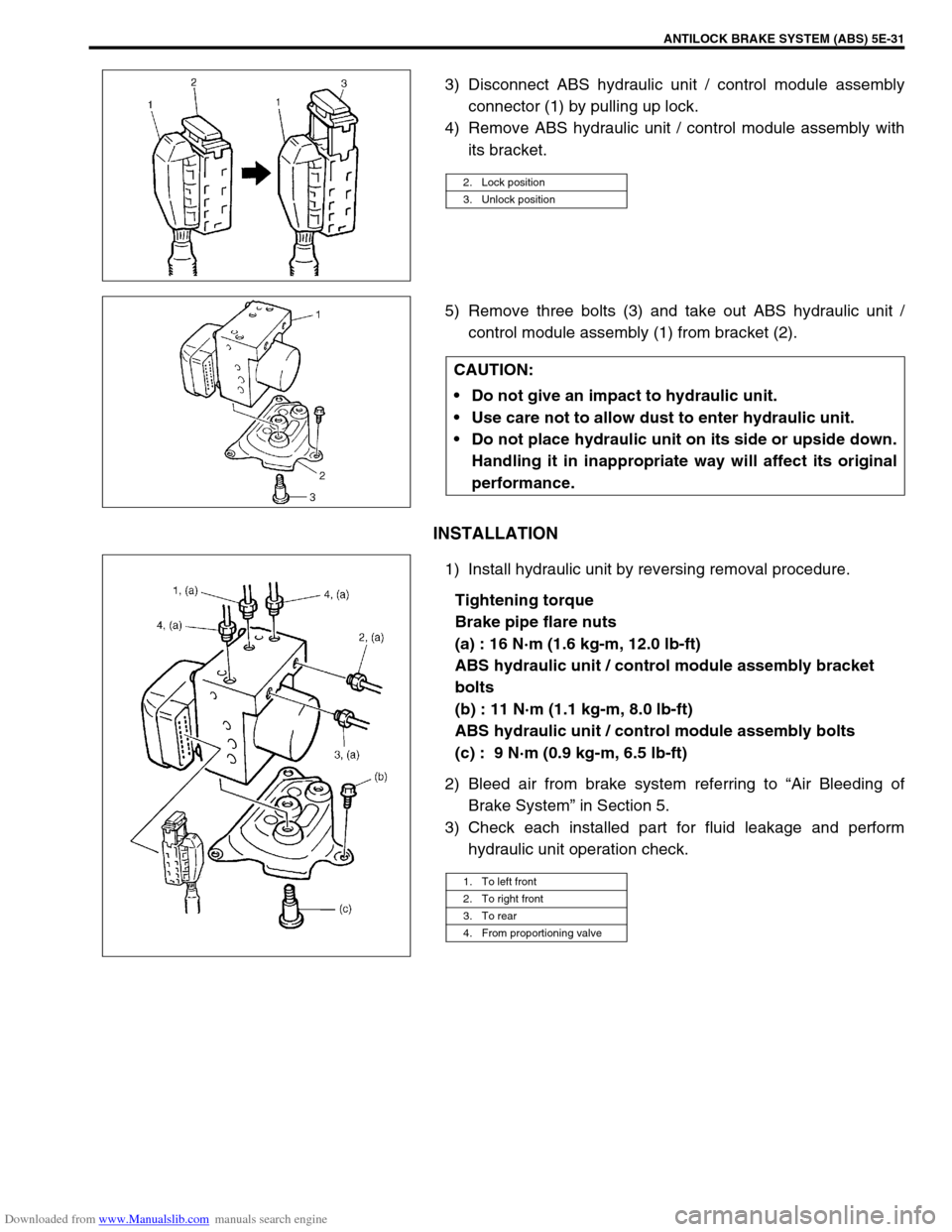
Downloaded from www.Manualslib.com manuals search engine ANTILOCK BRAKE SYSTEM (ABS) 5E-31
3) Disconnect ABS hydraulic unit / control module assembly
connector (1) by pulling up lock.
4) Remove ABS hydraulic unit / control module assembly with
its bracket.
5) Remove three bolts (3) and take out ABS hydraulic unit /
control module assembly (1) from bracket (2).
INSTALLATION
1) Install hydraulic unit by reversing removal procedure.
Tightening torque
Brake pipe flare nuts
(a) : 16 N·m (1.6 kg-m, 12.0 lb-ft)
ABS hydraulic unit / control module assembly bracket
bolts
(b) : 11 N·m (1.1 kg-m, 8.0 lb-ft)
ABS hydraulic unit / control module assembly bolts
(c) : 9 N·m (0.9 kg-m, 6.5 lb-ft)
2) Bleed air from brake system referring to “Air Bleeding of
Brake System” in Section 5.
3) Check each installed part for fluid leakage and perform
hydraulic unit operation check.
2. Lock position
3. Unlock position
CAUTION:
Do not give an impact to hydraulic unit.
Use care not to allow dust to enter hydraulic unit.
Do not place hydraulic unit on its side or upside down.
Handling it in inappropriate way will affect its original
performance.
1. To left front
2. To right front
3. To rear
4. From proportioning valve
Page 349 of 687
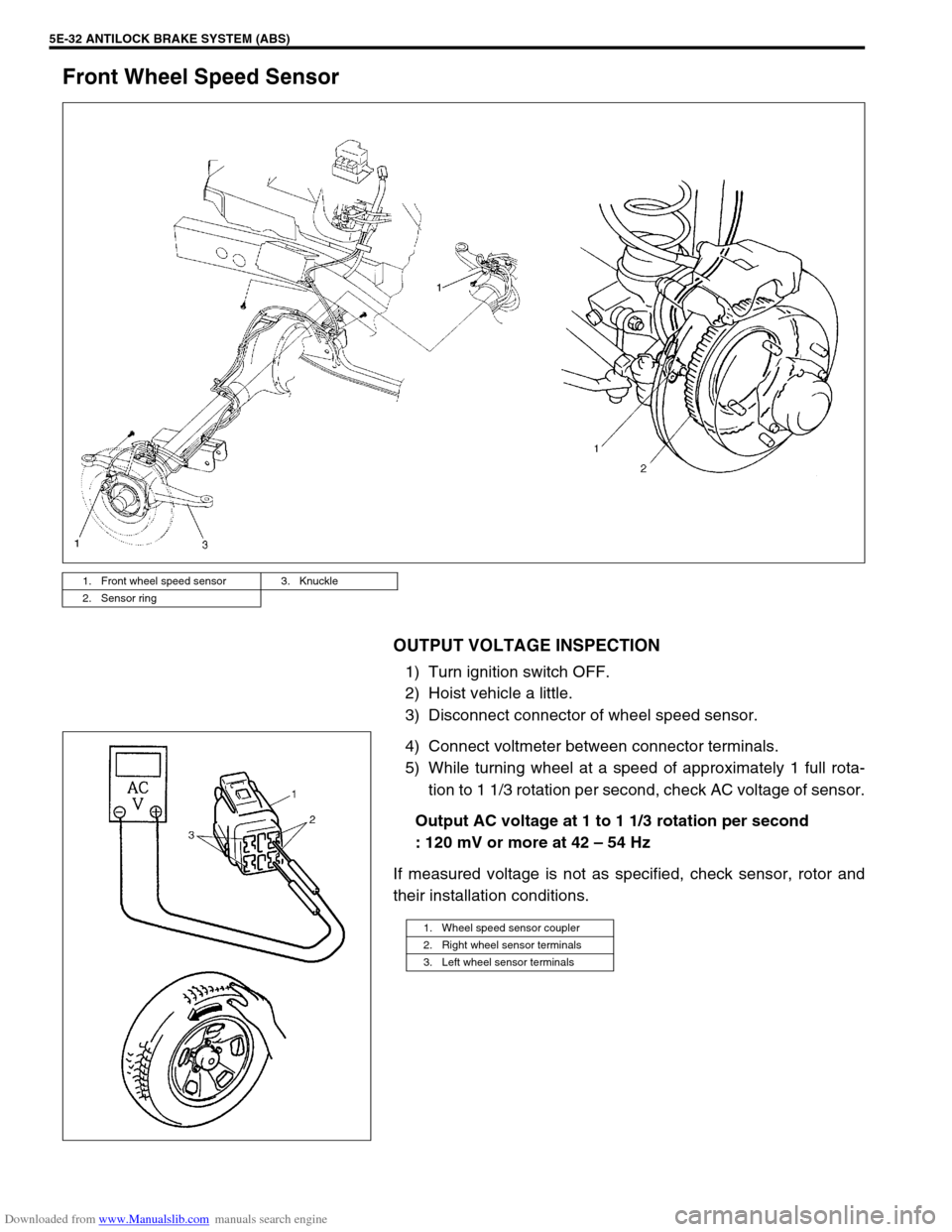
Downloaded from www.Manualslib.com manuals search engine 5E-32 ANTILOCK BRAKE SYSTEM (ABS)
Front Wheel Speed Sensor
OUTPUT VOLTAGE INSPECTION
1) Turn ignition switch OFF.
2) Hoist vehicle a little.
3) Disconnect connector of wheel speed sensor.
4) Connect voltmeter between connector terminals.
5) While turning wheel at a speed of approximately 1 full rota-
tion to 1 1/3 rotation per second, check AC voltage of sensor.
Output AC voltage at 1 to 1 1/3 rotation per second
: 120 mV or more at 42 – 54 Hz
If measured voltage is not as specified, check sensor, rotor and
their installation conditions.
1. Front wheel speed sensor 3. Knuckle
2. Sensor ring
1. Wheel speed sensor coupler
2. Right wheel sensor terminals
3. Left wheel sensor terminals
Page 350 of 687
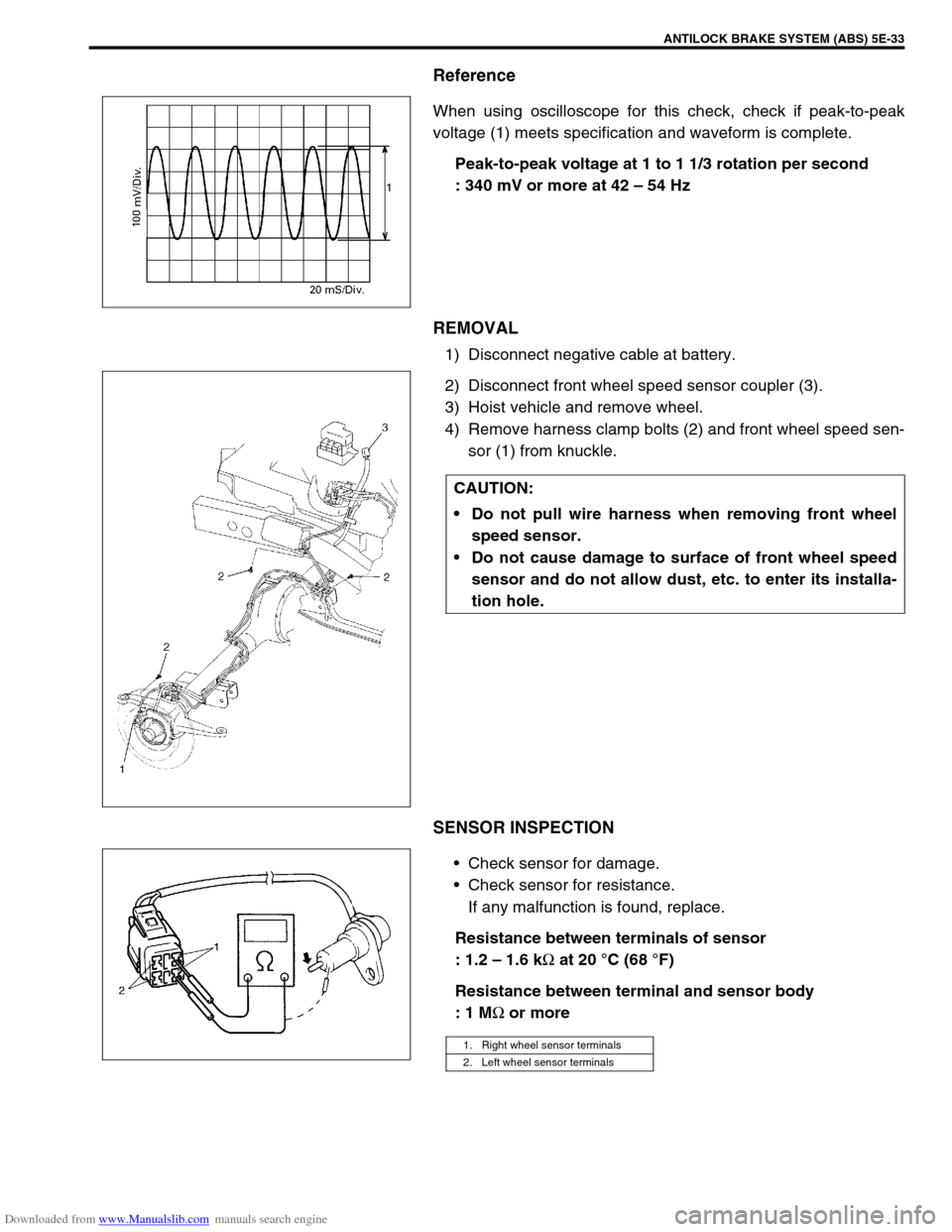
Downloaded from www.Manualslib.com manuals search engine ANTILOCK BRAKE SYSTEM (ABS) 5E-33
Reference
When using oscilloscope for this check, check if peak-to-peak
voltage (1) meets specification and waveform is complete.
Peak-to-peak voltage at 1 to 1 1/3 rotation per second
: 340 mV or more at 42 – 54 Hz
REMOVAL
1) Disconnect negative cable at battery.
2) Disconnect front wheel speed sensor coupler (3).
3) Hoist vehicle and remove wheel.
4) Remove harness clamp bolts (2) and front wheel speed sen-
sor (1) from knuckle.
SENSOR INSPECTION
Check sensor for damage.
Check sensor for resistance.
If any malfunction is found, replace.
Resistance between terminals of sensor
: 1.2 – 1.6 k
Ω at 20 °C (68 °F)
Resistance between terminal and sensor body
: 1 M
Ω or more
CAUTION:
Do not pull wire harness when removing front wheel
speed sensor.
Do not cause damage to surface of front wheel speed
sensor and do not allow dust, etc. to enter its installa-
tion hole.
1. Right wheel sensor terminals
2. Left wheel sensor terminals