SUZUKI SWIFT 2000 1.G RG413 Service Workshop Manual
Manufacturer: SUZUKI, Model Year: 2000, Model line: SWIFT, Model: SUZUKI SWIFT 2000 1.GPages: 698, PDF Size: 16.01 MB
Page 671 of 698
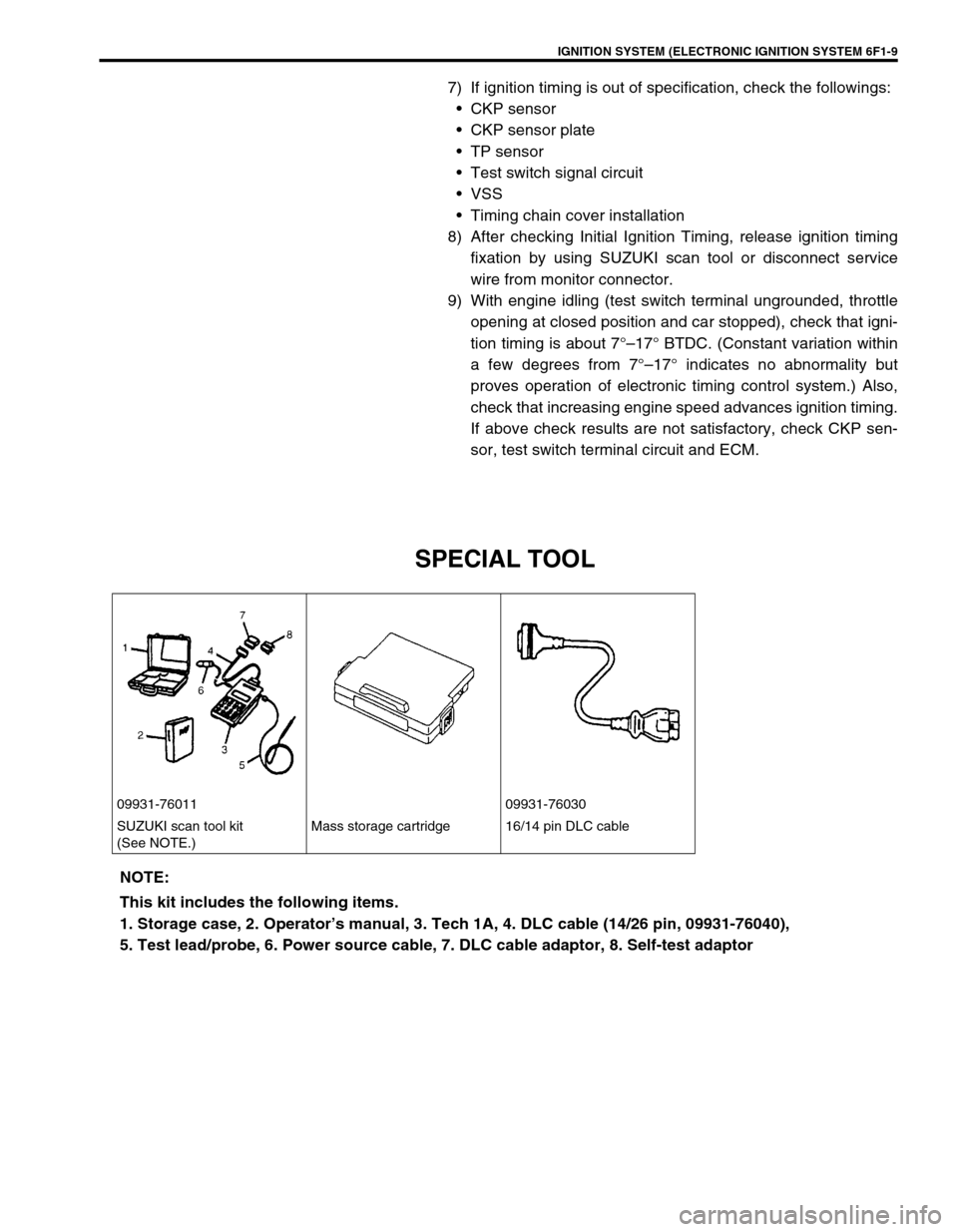
IGNITION SYSTEM (ELECTRONIC IGNITION SYSTEM 6F1-9
7) If ignition timing is out of specification, check the followings:
CKP sensor
CKP sensor plate
TP sensor
Test switch signal circuit
VSS
Timing chain cover installation
8) After checking Initial Ignition Timing, release ignition timing
fixation by using SUZUKI scan tool or disconnect service
wire from monitor connector.
9) With engine idling (test switch terminal ungrounded, throttle
opening at closed position and car stopped), check that igni-
tion timing is about 7°–17° BTDC. (Constant variation within
a few degrees from 7°–17° indicates no abnormality but
proves operation of electronic timing control system.) Also,
check that increasing engine speed advances ignition timing.
If above check results are not satisfactory, check CKP sen-
sor, test switch terminal circuit and ECM.
SPECIAL TOOL
09931-76011 09931-76030
SUZUKI scan tool kit
(See NOTE.)Mass storage cartridge 16/14 pin DLC cable
NOTE:
This kit includes the following items.
1. Storage case, 2. Operator’s manual, 3. Tech 1A, 4. DLC cable (14/26 pin, 09931-76040),
5. Test lead/probe, 6. Power source cable, 7. DLC cable adaptor, 8. Self-test adaptor
Page 672 of 698
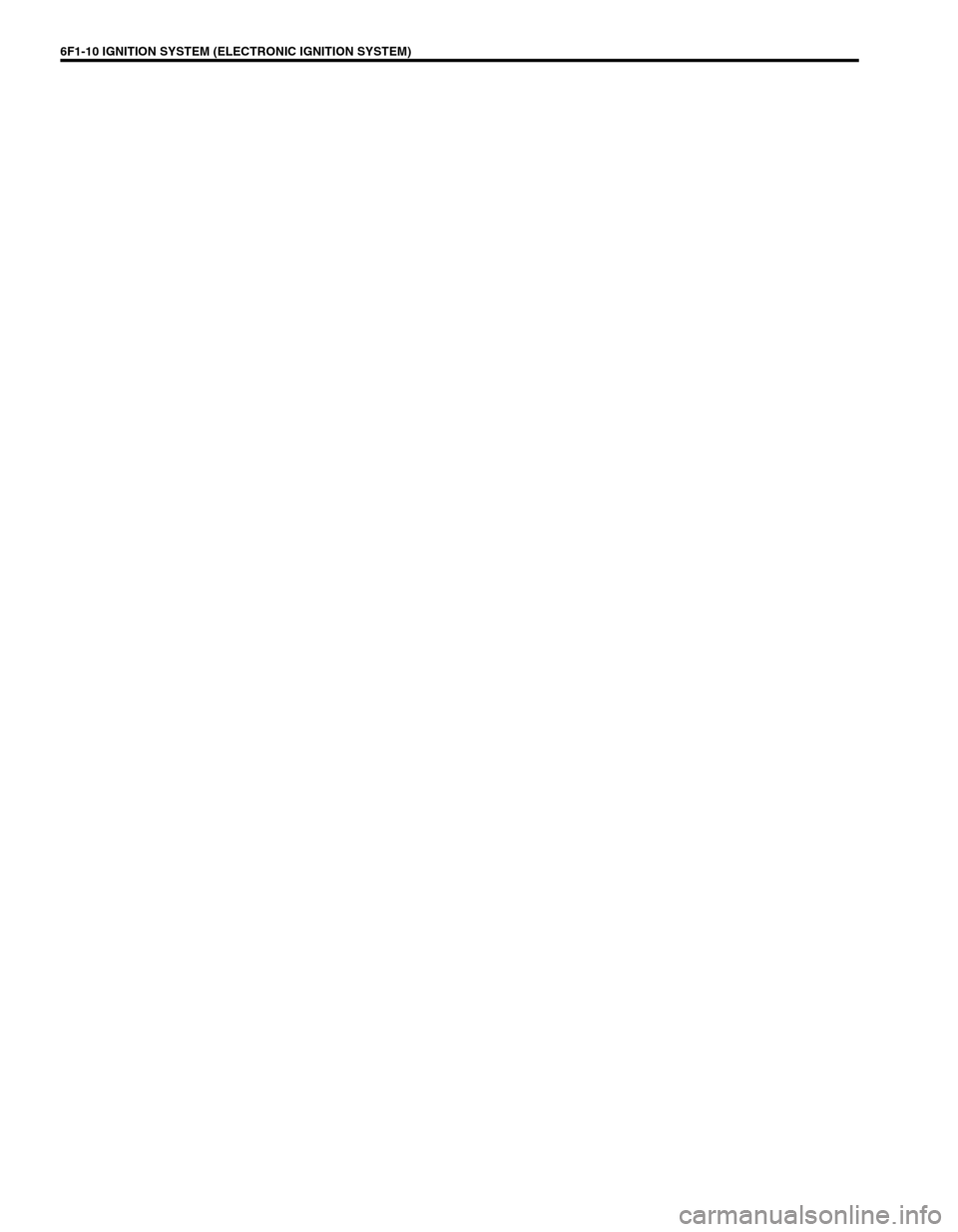
6F1-10 IGNITION SYSTEM (ELECTRONIC IGNITION SYSTEM)
Page 673 of 698
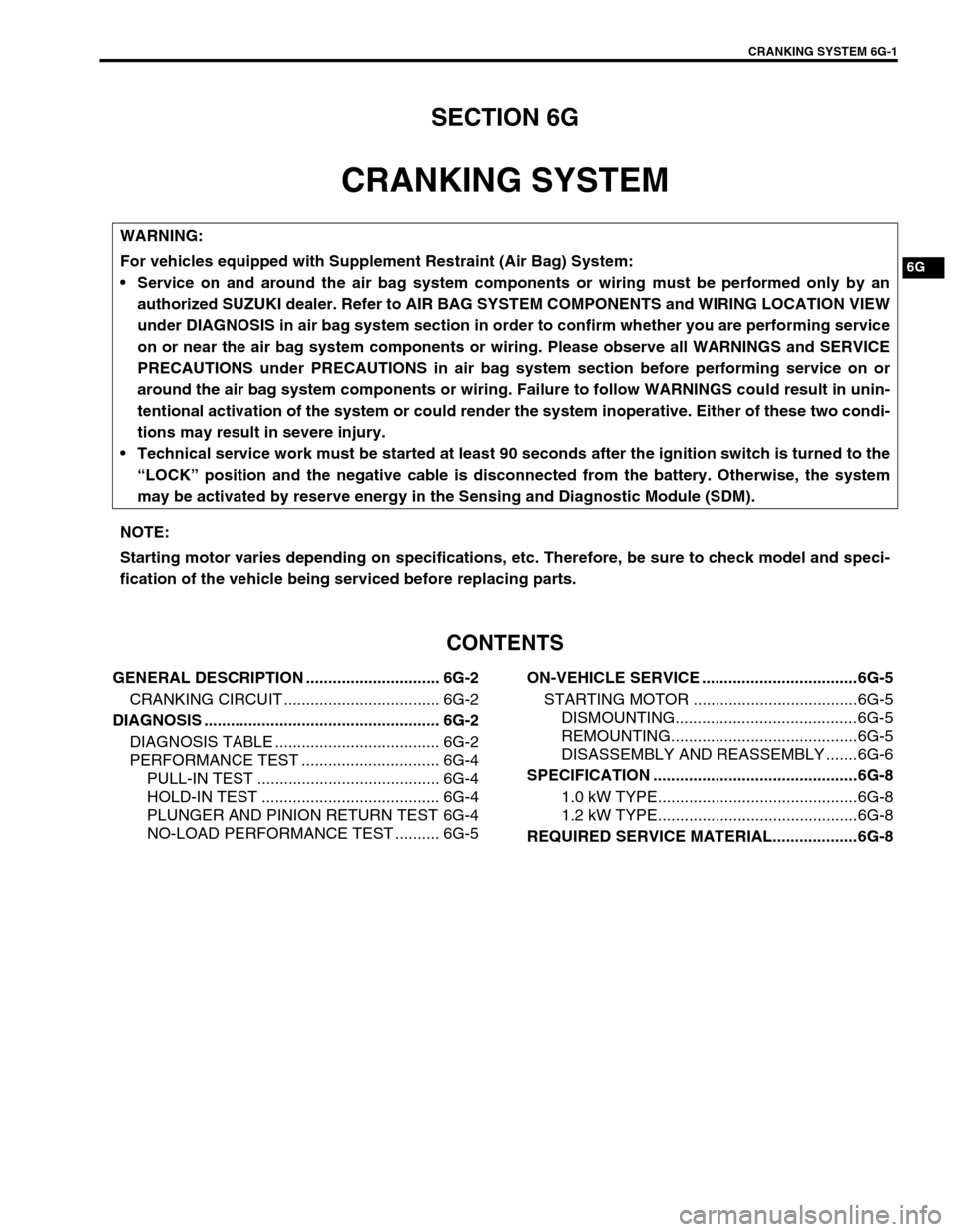
CRANKING SYSTEM 6G-1
6F1
6F2
6H
6K
6G
7A1
7B1
7C1
7D
7E
7F
8A
8B
8C
8D
8E
9
10
10A
10B
SECTION 6G
CRANKING SYSTEM
CONTENTS
GENERAL DESCRIPTION .............................. 6G-2
CRANKING CIRCUIT ................................... 6G-2
DIAGNOSIS ..................................................... 6G-2
DIAGNOSIS TABLE ..................................... 6G-2
PERFORMANCE TEST ............................... 6G-4
PULL-IN TEST ......................................... 6G-4
HOLD-IN TEST ........................................ 6G-4
PLUNGER AND PINION RETURN TEST 6G-4
NO-LOAD PERFORMANCE TEST .......... 6G-5ON-VEHICLE SERVICE ...................................6G-5
STARTING MOTOR .....................................6G-5
DISMOUNTING.........................................6G-5
REMOUNTING..........................................6G-5
DISASSEMBLY AND REASSEMBLY .......6G-6
SPECIFICATION ..............................................6G-8
1.0 kW TYPE.............................................6G-8
1.2 kW TYPE.............................................6G-8
REQUIRED SERVICE MATERIAL...................6G-8
WARNING:
For vehicles equipped with Supplement Restraint (Air Bag) System:
Service on and around the air bag system components or wiring must be performed only by an
authorized SUZUKI dealer. Refer to AIR BAG SYSTEM COMPONENTS and WIRING LOCATION VIEW
under DIAGNOSIS in air bag system section in order to confirm whether you are performing service
on or near the air bag system components or wiring. Please observe all WARNINGS and SERVICE
PRECAUTIONS under PRECAUTIONS in air bag system section before performing service on or
around the air bag system components or wiring. Failure to follow WARNINGS could result in unin-
tentional activation of the system or could render the system inoperative. Either of these two condi-
tions may result in severe injury.
Technical service work must be started at least 90 seconds after the ignition switch is turned to the
“LOCK” position and the negative cable is disconnected from the battery. Otherwise, the system
may be activated by reserve energy in the Sensing and Diagnostic Module (SDM).
NOTE:
Starting motor varies depending on specifications, etc. Therefore, be sure to check model and speci-
fication of the vehicle being serviced before replacing parts.
Page 674 of 698
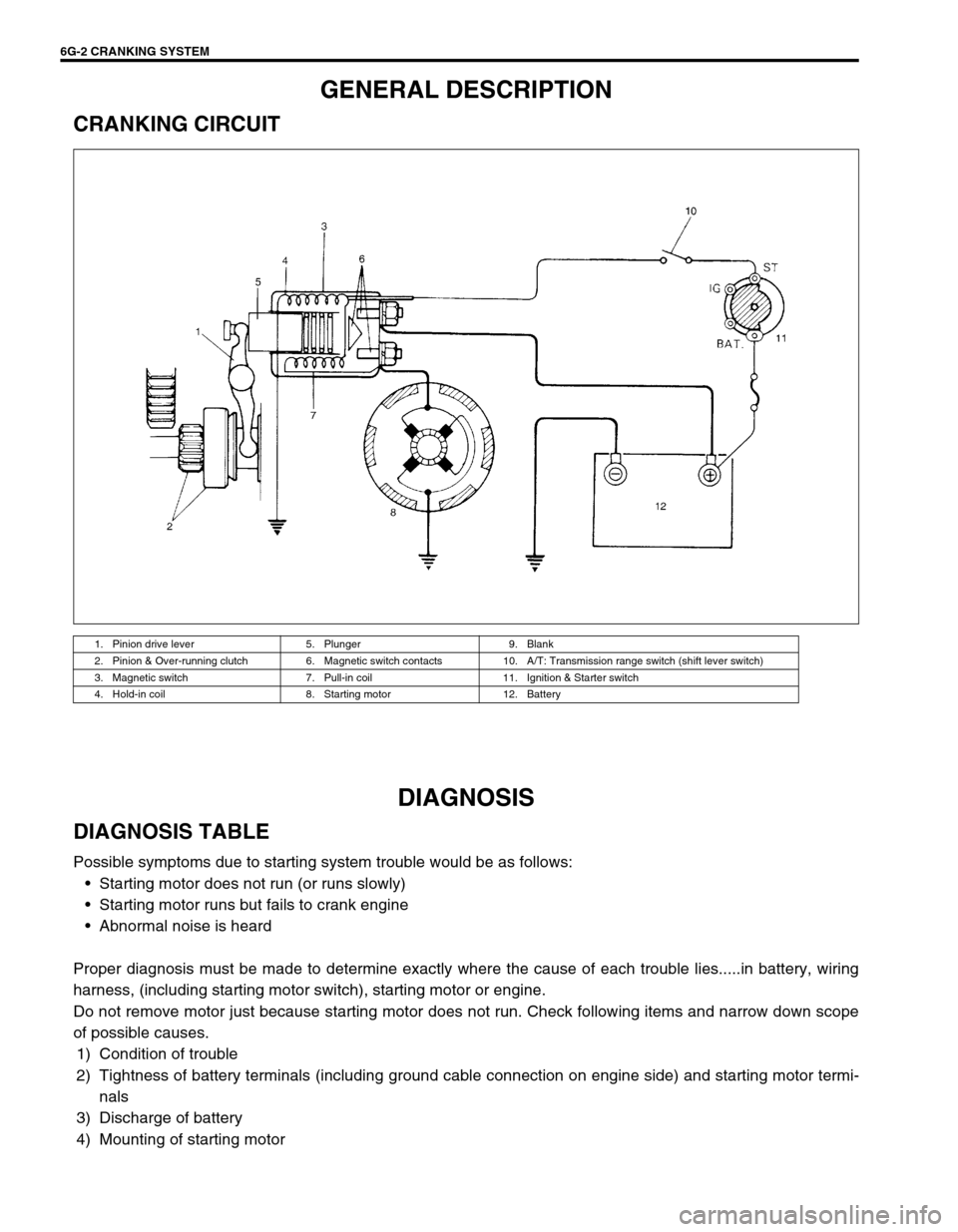
6G-2 CRANKING SYSTEM
GENERAL DESCRIPTION
CRANKING CIRCUIT
DIAGNOSIS
DIAGNOSIS TABLE
Possible symptoms due to starting system trouble would be as follows:
Starting motor does not run (or runs slowly)
Starting motor runs but fails to crank engine
Abnormal noise is heard
Proper diagnosis must be made to determine exactly where the cause of each trouble lies.....in battery, wiring
harness, (including starting motor switch), starting motor or engine.
Do not remove motor just because starting motor does not run. Check following items and narrow down scope
of possible causes.
1) Condition of trouble
2) Tightness of battery terminals (including ground cable connection on engine side) and starting motor termi-
nals
3) Discharge of battery
4) Mounting of starting motor
1. Pinion drive lever 5. Plunger 9. Blank
2. Pinion & Over-running clutch 6. Magnetic switch contacts 10. A/T: Transmission range switch (shift lever switch)
3. Magnetic switch 7. Pull-in coil 11. Ignition & Starter switch
4. Hold-in coil 8. Starting motor 12. Battery
Page 675 of 698
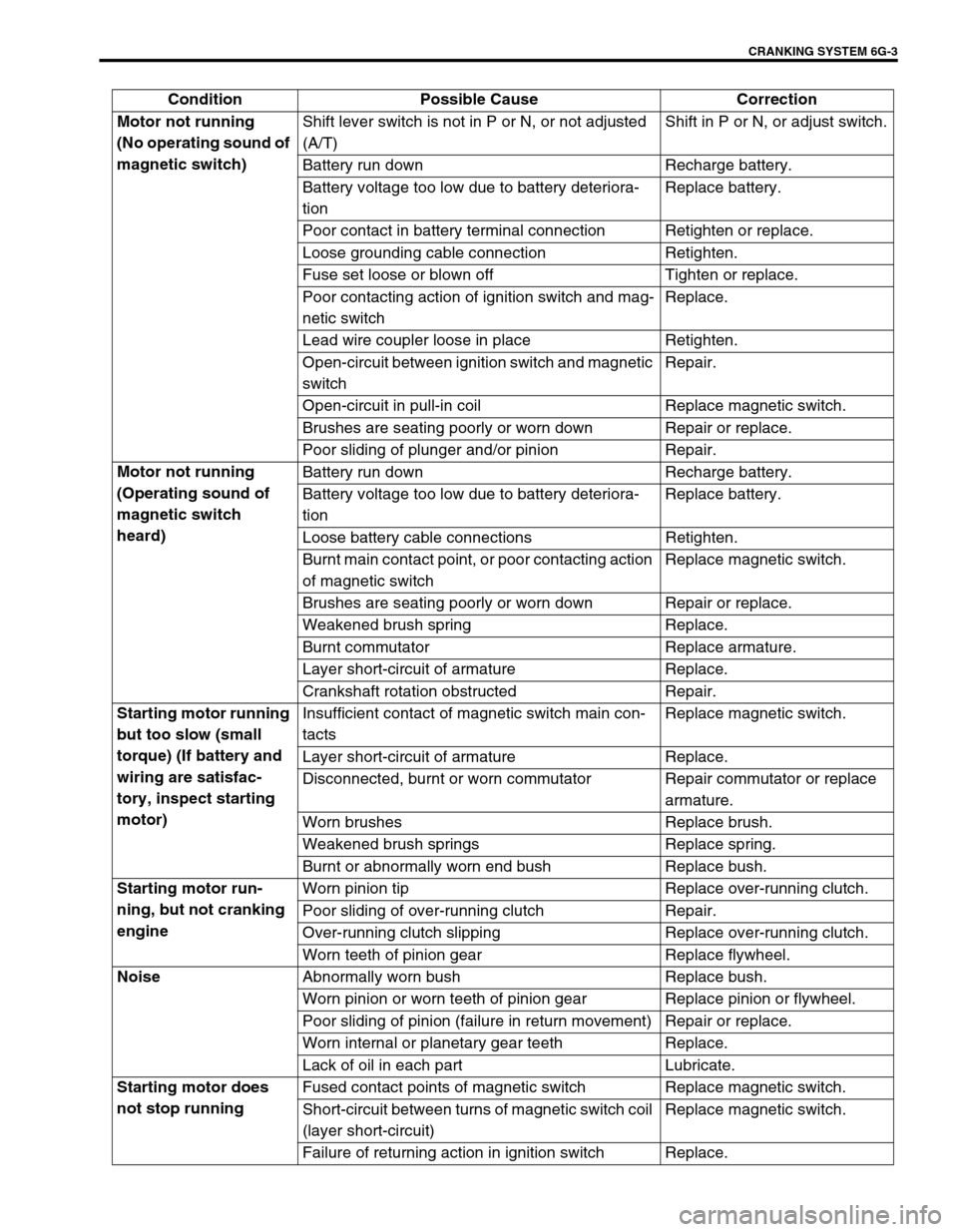
CRANKING SYSTEM 6G-3
Condition Possible Cause Correction
Motor not running
(No operating sound of
magnetic switch)Shift lever switch is not in P or N, or not adjusted
(A/T)Shift in P or N, or adjust switch.
Battery run down Recharge battery.
Battery voltage too low due to battery deteriora-
tionReplace battery.
Poor contact in battery terminal connection Retighten or replace.
Loose grounding cable connection Retighten.
Fuse set loose or blown off Tighten or replace.
Poor contacting action of ignition switch and mag-
netic switchReplace.
Lead wire coupler loose in place Retighten.
Open-circuit between ignition switch and magnetic
switchRepair.
Open-circuit in pull-in coil Replace magnetic switch.
Brushes are seating poorly or worn down Repair or replace.
Poor sliding of plunger and/or pinion Repair.
Motor not running
(Operating sound of
magnetic switch
heard)Battery run down Recharge battery.
Battery voltage too low due to battery deteriora-
tionReplace battery.
Loose battery cable connections Retighten.
Burnt main contact point, or poor contacting action
of magnetic switchReplace magnetic switch.
Brushes are seating poorly or worn down Repair or replace.
Weakened brush spring Replace.
Burnt commutator Replace armature.
Layer short-circuit of armature Replace.
Crankshaft rotation obstructed Repair.
Starting motor running
but too slow (small
torque) (If battery and
wiring are satisfac-
tory, inspect starting
motor)Insufficient contact of magnetic switch main con-
tactsReplace magnetic switch.
Layer short-circuit of armature Replace.
Disconnected, burnt or worn commutator Repair commutator or replace
armature.
Worn brushes Replace brush.
Weakened brush springs Replace spring.
Burnt or abnormally worn end bush Replace bush.
Starting motor run-
ning, but not cranking
engineWorn pinion tip Replace over-running clutch.
Poor sliding of over-running clutch Repair.
Over-running clutch slipping Replace over-running clutch.
Worn teeth of pinion gear Replace flywheel.
Noise
Abnormally worn bush Replace bush.
Worn pinion or worn teeth of pinion gear Replace pinion or flywheel.
Poor sliding of pinion (failure in return movement) Repair or replace.
Worn internal or planetary gear teeth Replace.
Lack of oil in each part Lubricate.
Starting motor does
not stop runningFused contact points of magnetic switch Replace magnetic switch.
Short-circuit between turns of magnetic switch coil
(layer short-circuit)Replace magnetic switch.
Failure of returning action in ignition switch Replace.
Page 676 of 698
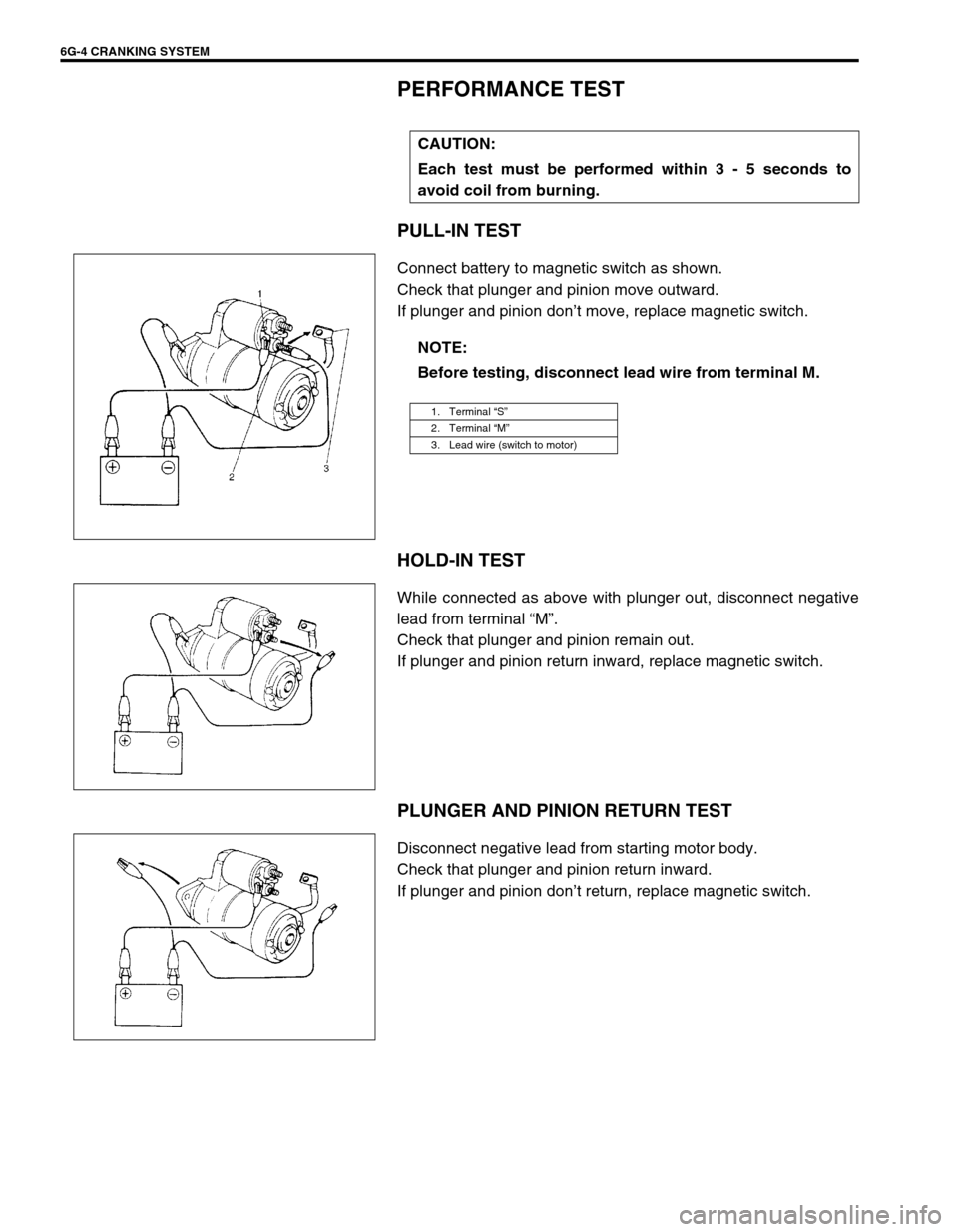
6G-4 CRANKING SYSTEM
PERFORMANCE TEST
PULL-IN TEST
Connect battery to magnetic switch as shown.
Check that plunger and pinion move outward.
If plunger and pinion don’t move, replace magnetic switch.
HOLD-IN TEST
While connected as above with plunger out, disconnect negative
lead from terminal “M”.
Check that plunger and pinion remain out.
If plunger and pinion return inward, replace magnetic switch.
PLUNGER AND PINION RETURN TEST
Disconnect negative lead from starting motor body.
Check that plunger and pinion return inward.
If plunger and pinion don’t return, replace magnetic switch. CAUTION:
Each test must be performed within 3 - 5 seconds to
avoid coil from burning.
NOTE:
Before testing, disconnect lead wire from terminal M.
1. Terminal “S”
2. Terminal “M”
3. Lead wire (switch to motor)
Page 677 of 698
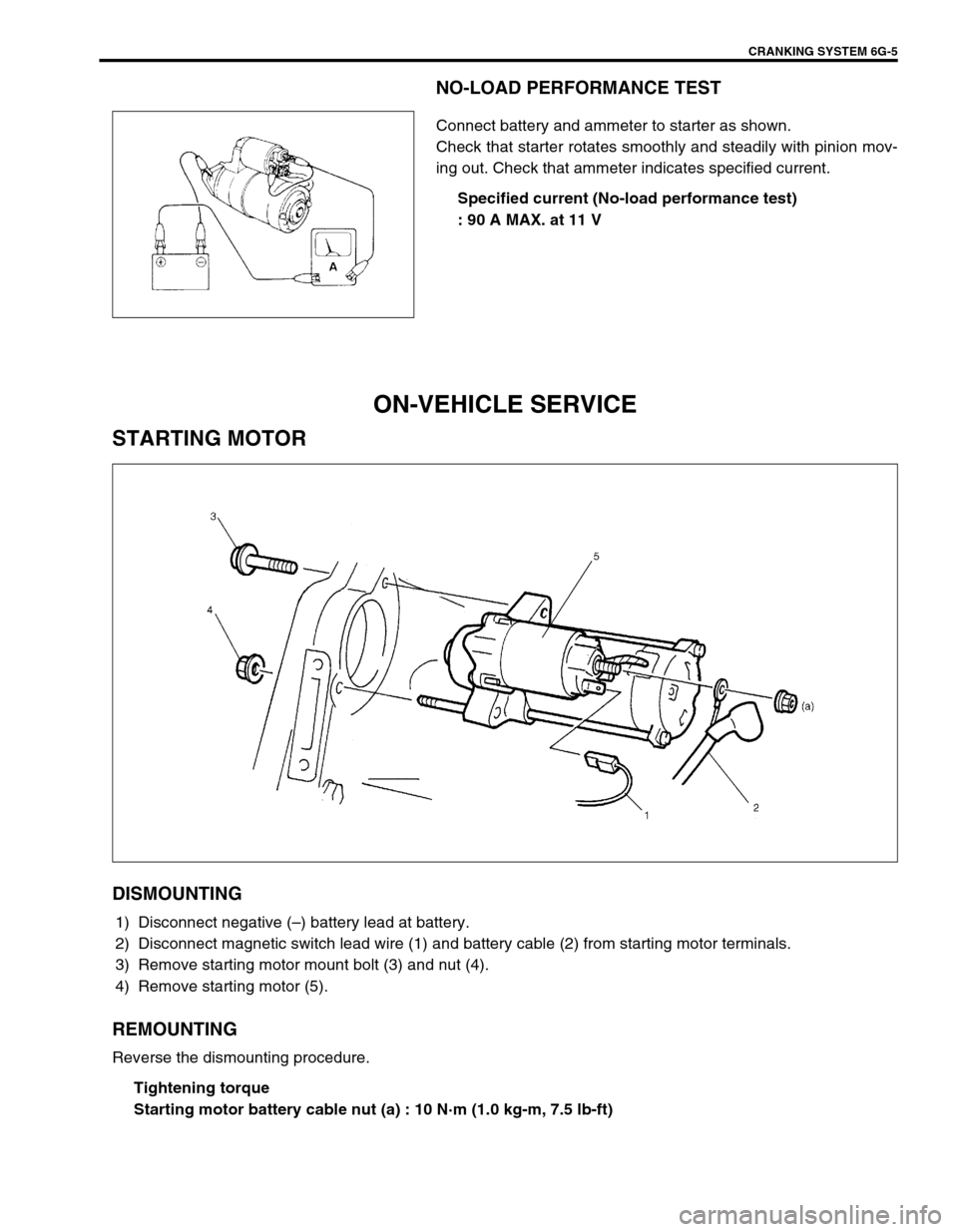
CRANKING SYSTEM 6G-5
NO-LOAD PERFORMANCE TEST
Connect battery and ammeter to starter as shown.
Check that starter rotates smoothly and steadily with pinion mov-
ing out. Check that ammeter indicates specified current.
Specified current (No-load performance test)
: 90 A MAX. at 11 V
ON-VEHICLE SERVICE
STARTING MOTOR
DISMOUNTING
1) Disconnect negative (–) battery lead at battery.
2) Disconnect magnetic switch lead wire (1) and battery cable (2) from starting motor terminals.
3) Remove starting motor mount bolt (3) and nut (4).
4) Remove starting motor (5).
REMOUNTING
Reverse the dismounting procedure.
Tightening torque
Starting motor battery cable nut (a) : 10 N·m (1.0 kg-m, 7.5 lb-ft)
Page 678 of 698
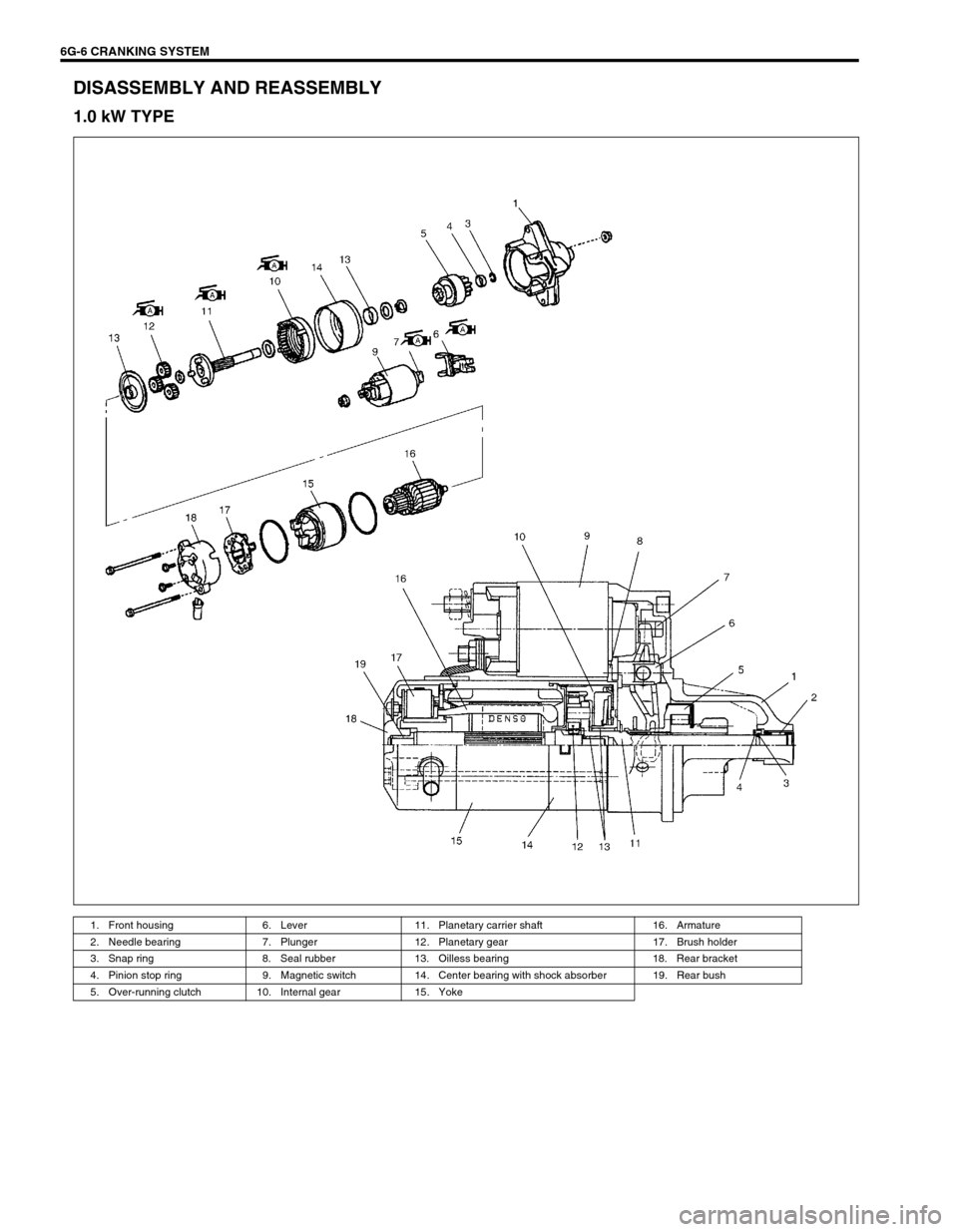
6G-6 CRANKING SYSTEM
DISASSEMBLY AND REASSEMBLY
1.0 kW TYPE
1. Front housing 6. Lever 11. Planetary carrier shaft 16. Armature
2. Needle bearing 7. Plunger 12. Planetary gear 17. Brush holder
3. Snap ring 8. Seal rubber 13. Oilless bearing 18. Rear bracket
4. Pinion stop ring 9. Magnetic switch 14. Center bearing with shock absorber 19. Rear bush
5. Over-running clutch 10. Internal gear 15. Yoke
Page 679 of 698
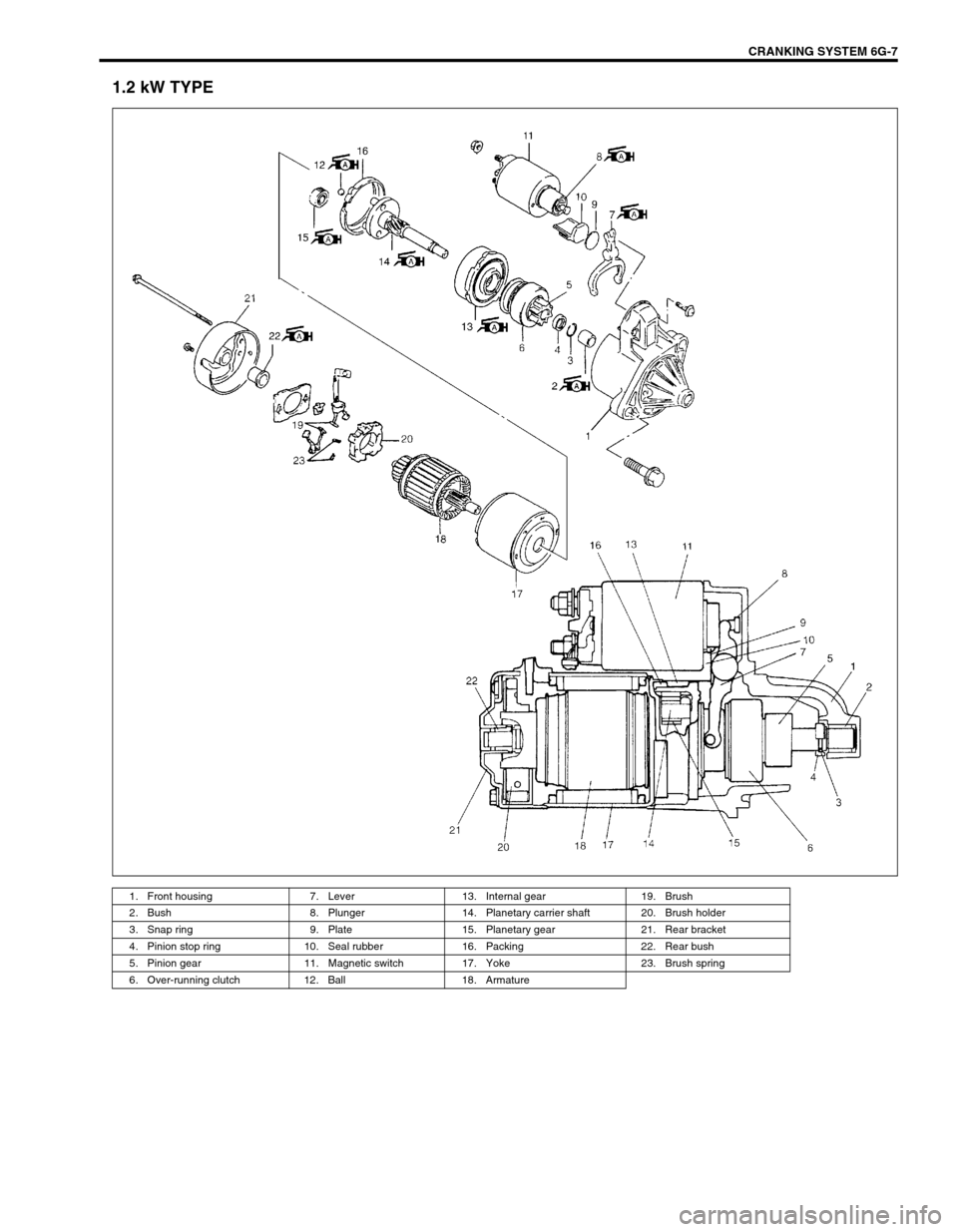
CRANKING SYSTEM 6G-7
1.2 kW TYPE
1. Front housing 7. Lever 13. Internal gear 19. Brush
2. Bush 8. Plunger 14. Planetary carrier shaft 20. Brush holder
3. Snap ring 9. Plate 15. Planetary gear 21. Rear bracket
4. Pinion stop ring 10. Seal rubber 16. Packing 22. Rear bush
5. Pinion gear 11. Magnetic switch 17. Yoke 23. Brush spring
6. Over-running clutch 12. Ball 18. Armature
Page 680 of 698
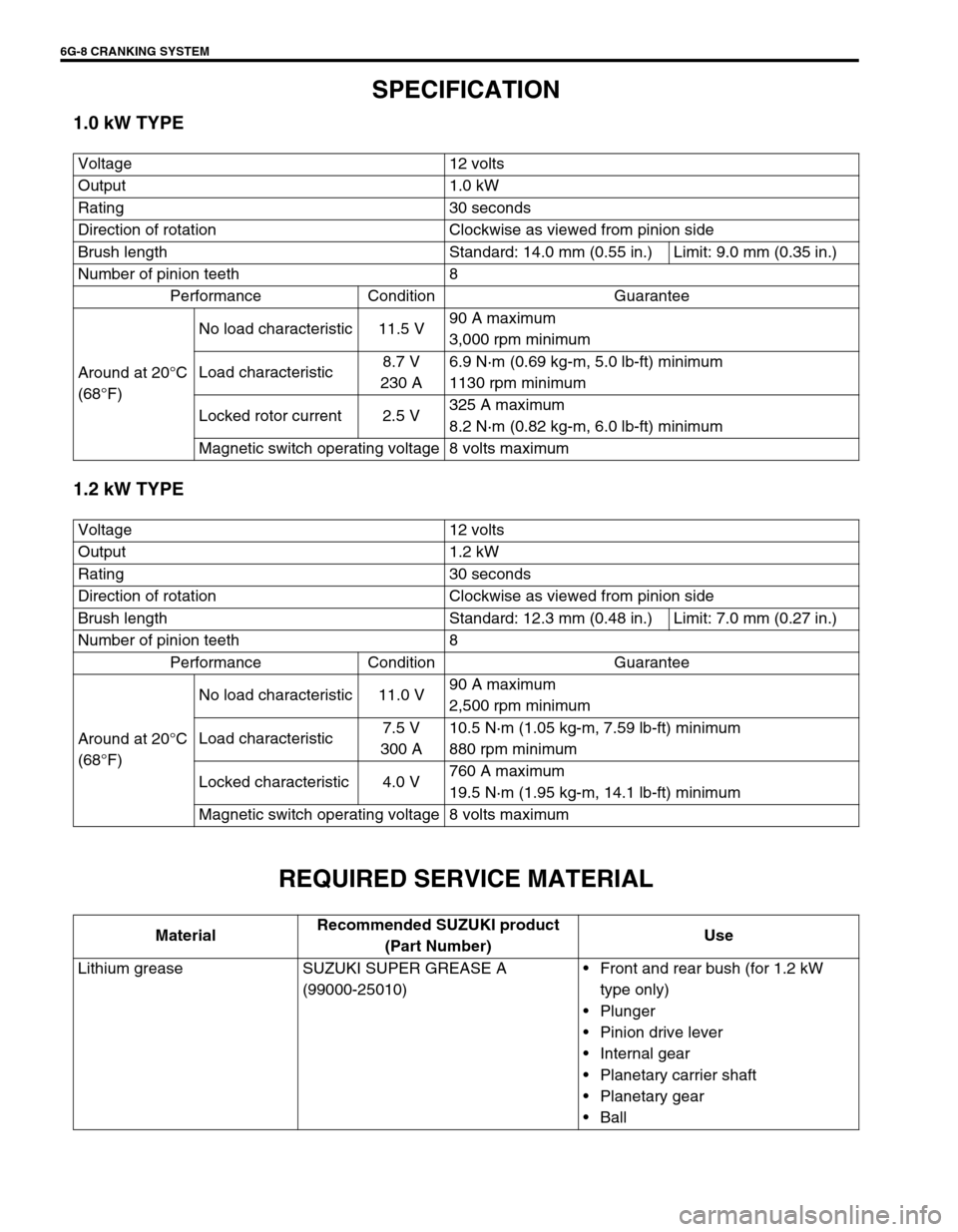
6G-8 CRANKING SYSTEM
SPECIFICATION
1.0 kW TYPE
1.2 kW TYPE
REQUIRED SERVICE MATERIAL
Voltage 12 volts
Output 1.0 kW
Rating 30 seconds
Direction of rotation Clockwise as viewed from pinion side
Brush length Standard: 14.0 mm (0.55 in.) Limit: 9.0 mm (0.35 in.)
Number of pinion teeth 8
Performance Condition Guarantee
Around at 20°C
(68°F)No load characteristic 11.5 V90 A maximum
3,000 rpm minimum
Load characteristic8.7 V
230 A6.9 N·m (0.69 kg-m, 5.0 lb-ft) minimum
1130 rpm minimum
Locked rotor current 2.5 V325 A maximum
8.2 N·m (0.82 kg-m, 6.0 lb-ft) minimum
Magnetic switch operating voltage 8 volts maximum
Voltage 12 volts
Output 1.2 kW
Rating 30 seconds
Direction of rotation Clockwise as viewed from pinion side
Brush length Standard: 12.3 mm (0.48 in.) Limit: 7.0 mm (0.27 in.)
Number of pinion teeth 8
Performance Condition Guarantee
Around at 20°C
(68°F)No load characteristic 11.0 V90 A maximum
2,500 rpm minimum
Load characteristic7.5 V
300 A10.5 N·m (1.05 kg-m, 7.59 lb-ft) minimum
880 rpm minimum
Locked characteristic 4.0 V760 A maximum
19.5 N·m (1.95 kg-m, 14.1 lb-ft) minimum
Magnetic switch operating voltage 8 volts maximum
MaterialRecommended SUZUKI product
(Part Number)Use
Lithium grease SUZUKI SUPER GREASE A
(99000-25010)Front and rear bush (for 1.2 kW
type only)
Plunger
Pinion drive lever
Internal gear
Planetary carrier shaft
Planetary gear
Ball