Air Condition SUZUKI SWIFT 2000 1.G RG413 Service Repair Manual
[x] Cancel search | Manufacturer: SUZUKI, Model Year: 2000, Model line: SWIFT, Model: SUZUKI SWIFT 2000 1.GPages: 698, PDF Size: 16.01 MB
Page 112 of 698
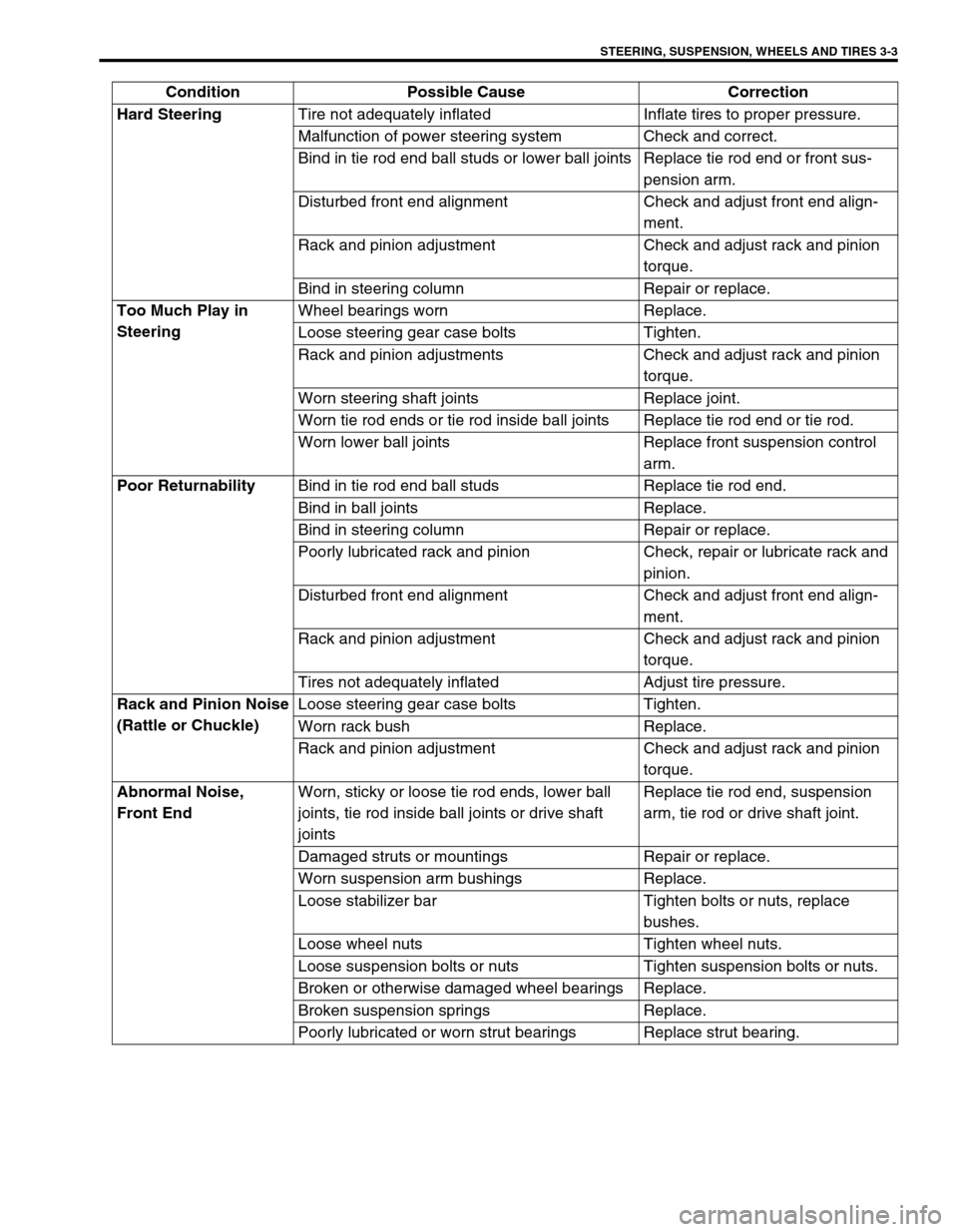
STEERING, SUSPENSION, WHEELS AND TIRES 3-3
Hard Steering
Tire not adequately inflated Inflate tires to proper pressure.
Malfunction of power steering system Check and correct.
Bind in tie rod end ball studs or lower ball joints Replace tie rod end or front sus-
pension arm.
Disturbed front end alignment Check and adjust front end align-
ment.
Rack and pinion adjustment Check and adjust rack and pinion
torque.
Bind in steering column Repair or replace.
Too Much Play in
SteeringWheel bearings worn Replace.
Loose steering gear case bolts Tighten.
Rack and pinion adjustments Check and adjust rack and pinion
torque.
Worn steering shaft joints Replace joint.
Worn tie rod ends or tie rod inside ball joints Replace tie rod end or tie rod.
Worn lower ball joints Replace front suspension control
arm.
Poor Returnability
Bind in tie rod end ball studs Replace tie rod end.
Bind in ball joints Replace.
Bind in steering column Repair or replace.
Poorly lubricated rack and pinion Check, repair or lubricate rack and
pinion.
Disturbed front end alignment Check and adjust front end align-
ment.
Rack and pinion adjustment Check and adjust rack and pinion
torque.
Tires not adequately inflated Adjust tire pressure.
Rack and Pinion Noise
(Rattle or Chuckle)Loose steering gear case bolts Tighten.
Worn rack bush Replace.
Rack and pinion adjustment Check and adjust rack and pinion
torque.
Abnormal Noise,
Front EndWorn, sticky or loose tie rod ends, lower ball
joints, tie rod inside ball joints or drive shaft
jointsReplace tie rod end, suspension
arm, tie rod or drive shaft joint.
Damaged struts or mountings Repair or replace.
Worn suspension arm bushings Replace.
Loose stabilizer bar Tighten bolts or nuts, replace
bushes.
Loose wheel nuts Tighten wheel nuts.
Loose suspension bolts or nuts Tighten suspension bolts or nuts.
Broken or otherwise damaged wheel bearings Replace.
Broken suspension springs Replace.
Poorly lubricated or worn strut bearings Replace strut bearing. Condition Possible Cause Correction
Page 113 of 698
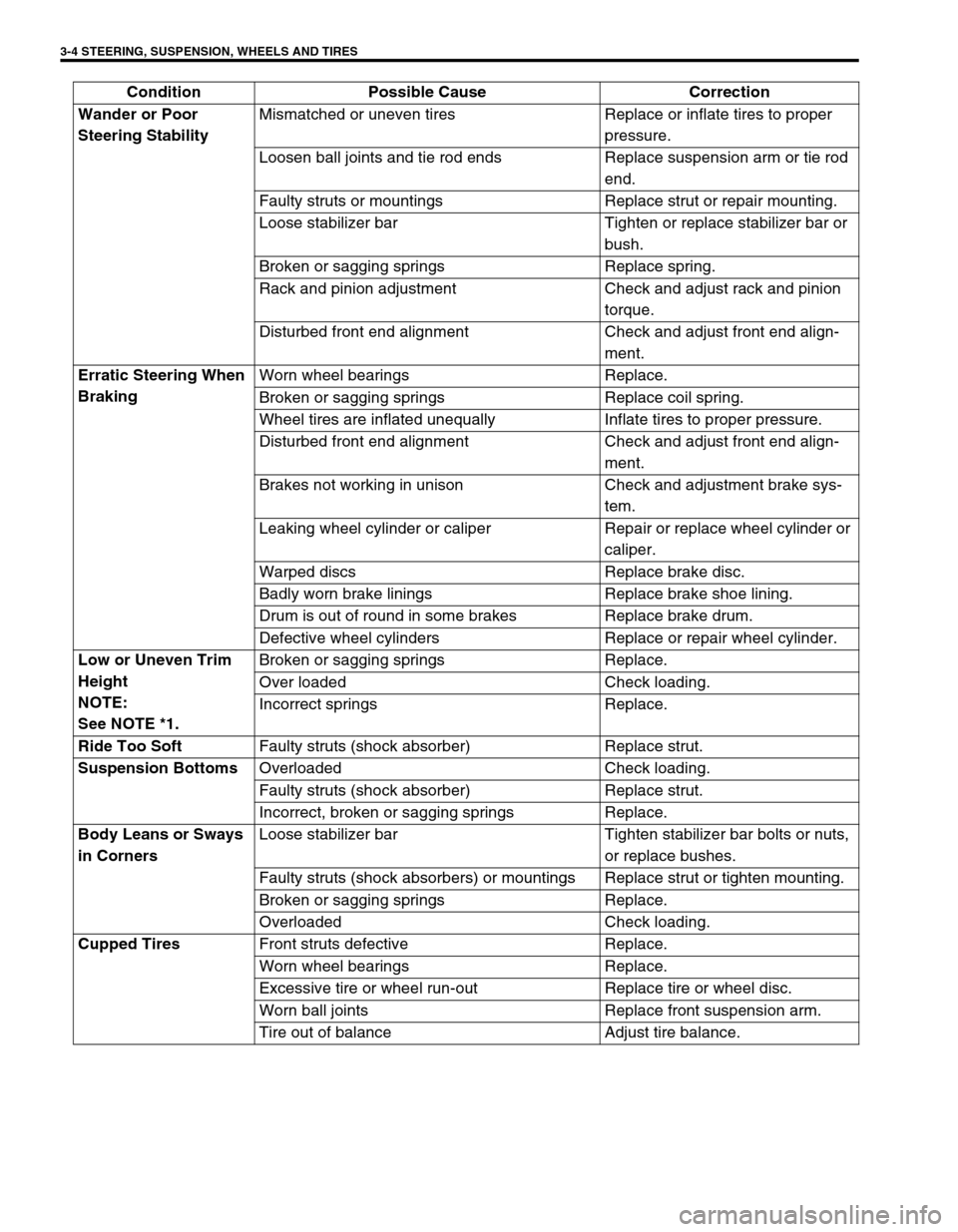
3-4 STEERING, SUSPENSION, WHEELS AND TIRES
Wander or Poor
Steering StabilityMismatched or uneven tires Replace or inflate tires to proper
pressure.
Loosen ball joints and tie rod ends Replace suspension arm or tie rod
end.
Faulty struts or mountings Replace strut or repair mounting.
Loose stabilizer bar Tighten or replace stabilizer bar or
bush.
Broken or sagging springs Replace spring.
Rack and pinion adjustment Check and adjust rack and pinion
torque.
Disturbed front end alignment Check and adjust front end align-
ment.
Erratic Steering When
BrakingWorn wheel bearings Replace.
Broken or sagging springs Replace coil spring.
Wheel tires are inflated unequally Inflate tires to proper pressure.
Disturbed front end alignment Check and adjust front end align-
ment.
Brakes not working in unison Check and adjustment brake sys-
tem.
Leaking wheel cylinder or caliper Repair or replace wheel cylinder or
caliper.
Warped discs Replace brake disc.
Badly worn brake linings Replace brake shoe lining.
Drum is out of round in some brakes Replace brake drum.
Defective wheel cylinders Replace or repair wheel cylinder.
Low or Uneven Trim
Height
NOTE:
See NOTE *1.Broken or sagging springs Replace.
Over loaded Check loading.
Incorrect springs Replace.
Ride Too Soft
Faulty struts (shock absorber) Replace strut.
Suspension Bottoms
Overloaded Check loading.
Faulty struts (shock absorber) Replace strut.
Incorrect, broken or sagging springs Replace.
Body Leans or Sways
in CornersLoose stabilizer bar Tighten stabilizer bar bolts or nuts,
or replace bushes.
Faulty struts (shock absorbers) or mountings Replace strut or tighten mounting.
Broken or sagging springs Replace.
Overloaded Check loading.
Cupped Tires
Front struts defective Replace.
Worn wheel bearings Replace.
Excessive tire or wheel run-out Replace tire or wheel disc.
Worn ball joints Replace front suspension arm.
Tire out of balance Adjust tire balance. Condition Possible Cause Correction
Page 119 of 698
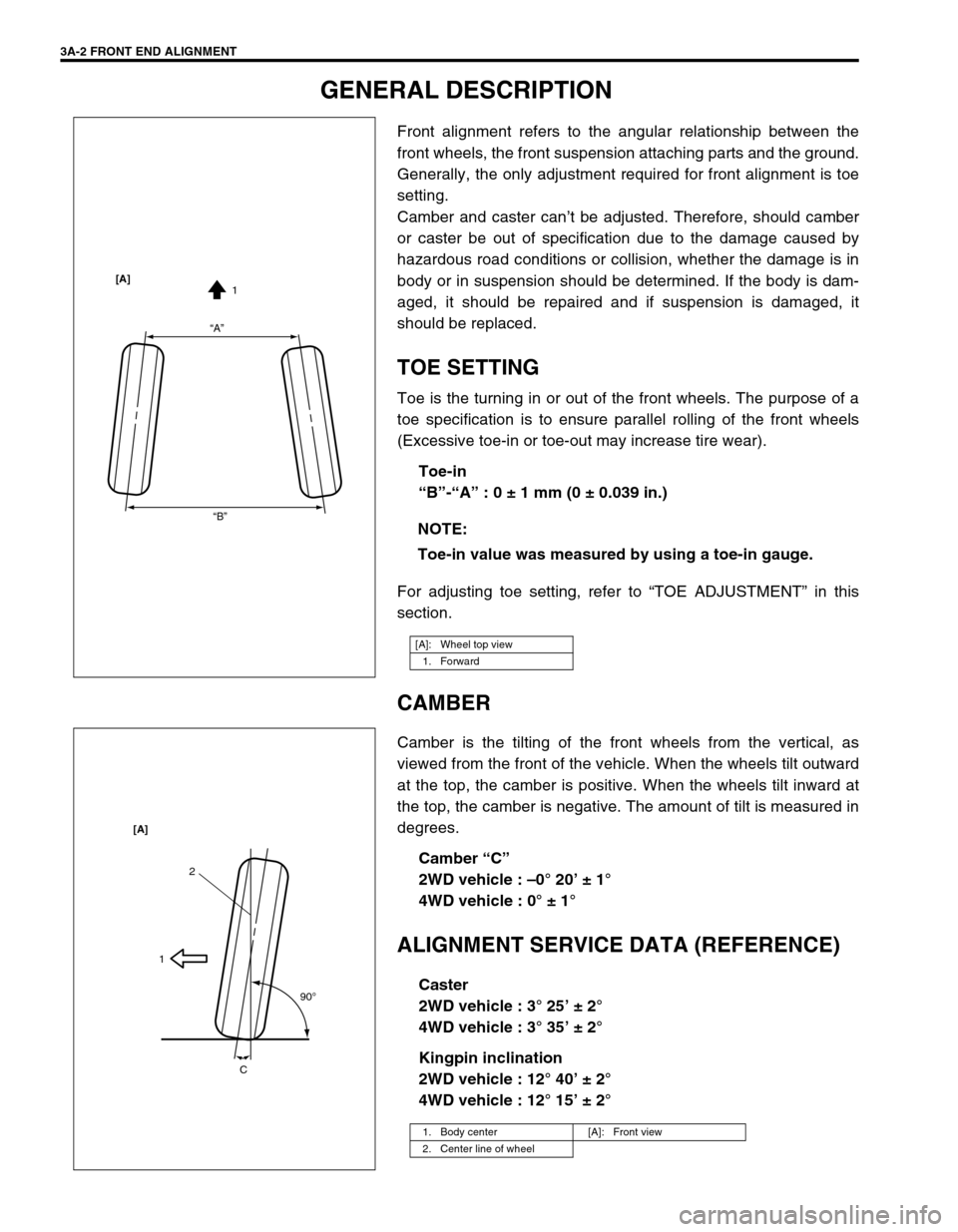
3A-2 FRONT END ALIGNMENT
GENERAL DESCRIPTION
Front alignment refers to the angular relationship between the
front wheels, the front suspension attaching parts and the ground.
Generally, the only adjustment required for front alignment is toe
setting.
Camber and caster can’t be adjusted. Therefore, should camber
or caster be out of specification due to the damage caused by
hazardous road conditions or collision, whether the damage is in
body or in suspension should be determined. If the body is dam-
aged, it should be repaired and if suspension is damaged, it
should be replaced.
TOE SETTING
Toe is the turning in or out of the front wheels. The purpose of a
toe specification is to ensure parallel rolling of the front wheels
(Excessive toe-in or toe-out may increase tire wear).
Toe-in
“B”-“A” : 0 ± 1 mm (0 ± 0.039 in.)
For adjusting toe setting, refer to “TOE ADJUSTMENT” in this
section.
CAMBER
Camber is the tilting of the front wheels from the vertical, as
viewed from the front of the vehicle. When the wheels tilt outward
at the top, the camber is positive. When the wheels tilt inward at
the top, the camber is negative. The amount of tilt is measured in
degrees.
Camber “C”
2WD vehicle : –0° 20’ ± 1°
4WD vehicle : 0° ± 1°
ALIGNMENT SERVICE DATA (REFERENCE)
Caster
2WD vehicle : 3° 25’ ± 2°
4WD vehicle : 3° 35’ ± 2°
Kingpin inclination
2WD vehicle : 12° 40’ ± 2°
4WD vehicle : 12° 15’ ± 2° NOTE:
Toe-in value was measured by using a toe-in gauge.
[A]: Wheel top view
1. Forward
“A”
“B”1 [A]
1. Body center [A]: Front view
2. Center line of wheel
2
1
90
o
C [A]
Page 122 of 698
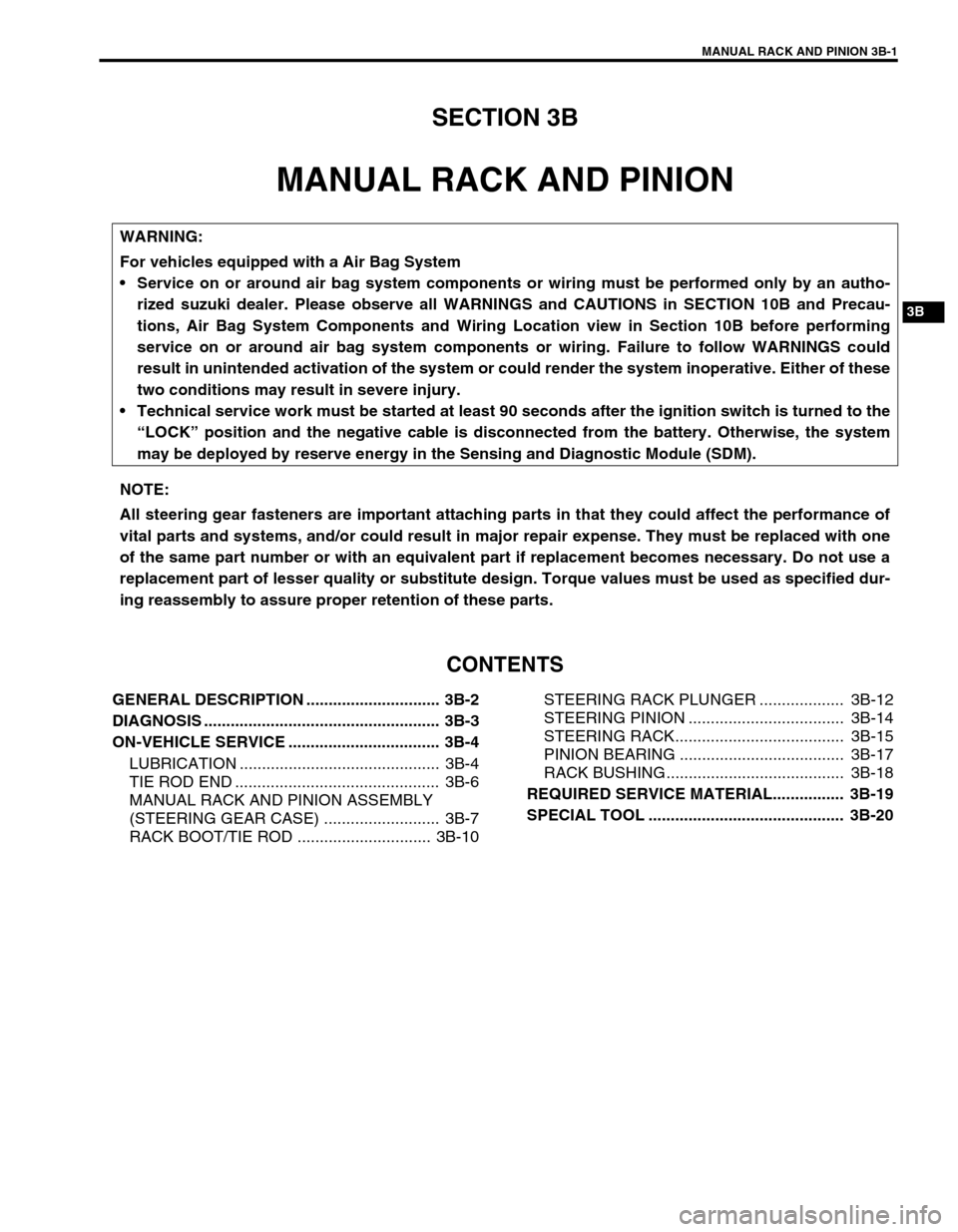
MANUAL RACK AND PINION 3B-1
6F1
6F2
6G
6H
7A
3B
7C1
7D
7E
7F
8A
8B
8C
8D
8E
9
10
10A
10B
SECTION 3B
MANUAL RACK AND PINION
CONTENTS
GENERAL DESCRIPTION .............................. 3B-2
DIAGNOSIS ..................................................... 3B-3
ON-VEHICLE SERVICE .................................. 3B-4
LUBRICATION ............................................. 3B-4
TIE ROD END .............................................. 3B-6
MANUAL RACK AND PINION ASSEMBLY
(STEERING GEAR CASE) .......................... 3B-7
RACK BOOT/TIE ROD .............................. 3B-10STEERING RACK PLUNGER ................... 3B-12
STEERING PINION ................................... 3B-14
STEERING RACK...................................... 3B-15
PINION BEARING ..................................... 3B-17
RACK BUSHING ........................................ 3B-18
REQUIRED SERVICE MATERIAL................ 3B-19
SPECIAL TOOL ............................................ 3B-20
WARNING:
For vehicles equipped with a Air Bag System
Service on or around air bag system components or wiring must be performed only by an autho-
rized suzuki dealer. Please observe all WARNINGS and CAUTIONS in SECTION 10B and Precau-
tions, Air Bag System Components and Wiring Location view in Section 10B before performing
service on or around air bag system components or wiring. Failure to follow WARNINGS could
result in unintended activation of the system or could render the system inoperative. Either of these
two conditions may result in severe injury.
Technical service work must be started at least 90 seconds after the ignition switch is turned to the
“LOCK” position and the negative cable is disconnected from the battery. Otherwise, the system
may be deployed by reserve energy in the Sensing and Diagnostic Module (SDM).
NOTE:
All steering gear fasteners are important attaching parts in that they could affect the performance of
vital parts and systems, and/or could result in major repair expense. They must be replaced with one
of the same part number or with an equivalent part if replacement becomes necessary. Do not use a
replacement part of lesser quality or substitute design. Torque values must be used as specified dur-
ing reassembly to assure proper retention of these parts.
Page 142 of 698
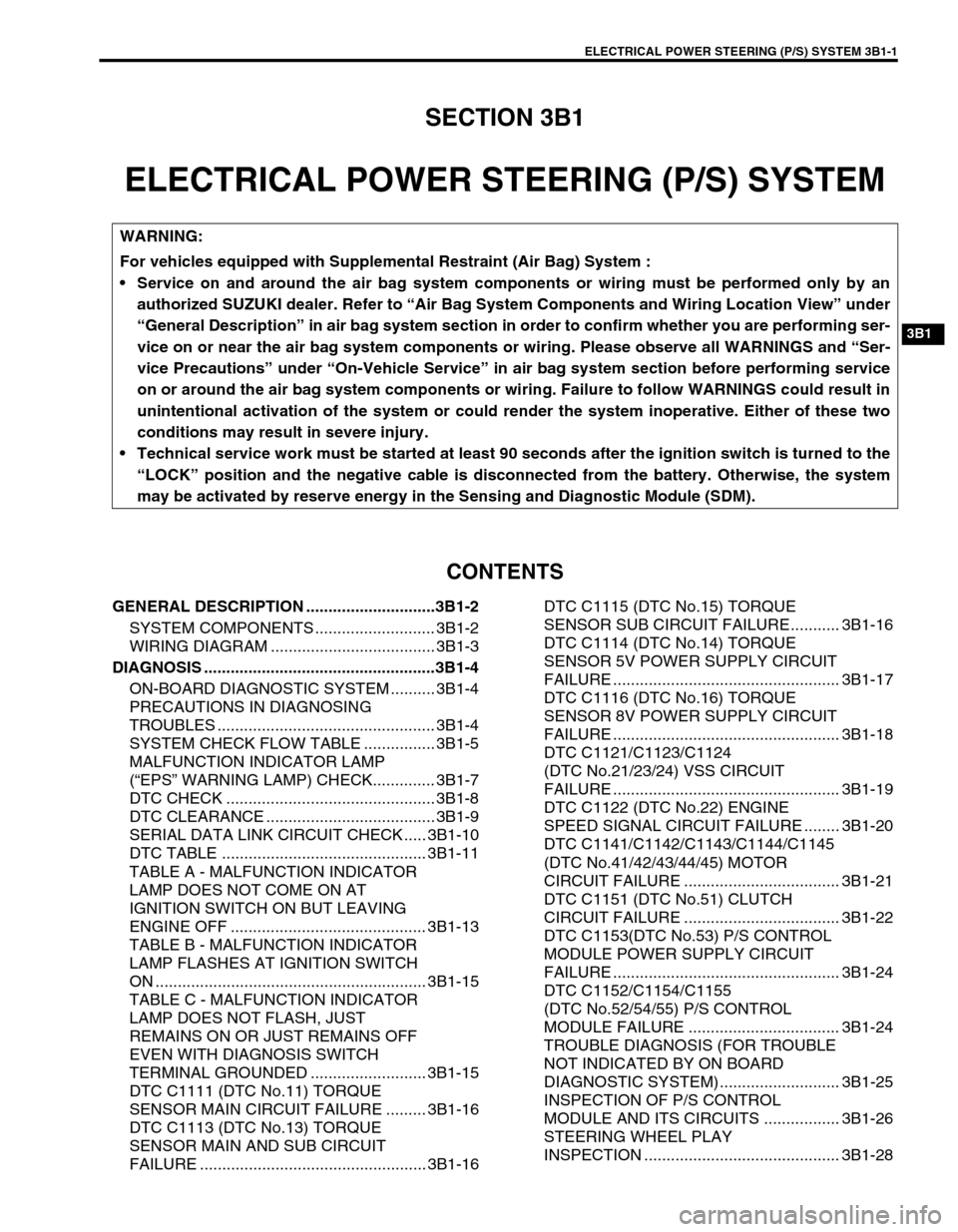
ELECTRICAL POWER STEERING (P/S) SYSTEM 3B1-1
6F1
6F2
6G
6H
6K
7A
7A1
3B1
7D
7E
7F
8A
8B
8C
8D
8E
9
10
10A
10B
SECTION 3B1
ELECTRICAL POWER STEERING (P/S) SYSTEM
CONTENTS
GENERAL DESCRIPTION .............................3B1-2
SYSTEM COMPONENTS ........................... 3B1-2
WIRING DIAGRAM ..................................... 3B1-3
DIAGNOSIS ....................................................3B1-4
ON-BOARD DIAGNOSTIC SYSTEM .......... 3B1-4
PRECAUTIONS IN DIAGNOSING
TROUBLES ................................................. 3B1-4
SYSTEM CHECK FLOW TABLE ................ 3B1-5
MALFUNCTION INDICATOR LAMP
(“EPS” WARNING LAMP) CHECK.............. 3B1-7
DTC CHECK ............................................... 3B1-8
DTC CLEARANCE ...................................... 3B1-9
SERIAL DATA LINK CIRCUIT CHECK ..... 3B1-10
DTC TABLE .............................................. 3B1-11
TABLE A - MALFUNCTION INDICATOR
LAMP DOES NOT COME ON AT
IGNITION SWITCH ON BUT LEAVING
ENGINE OFF ............................................ 3B1-13
TABLE B - MALFUNCTION INDICATOR
LAMP FLASHES AT IGNITION SWITCH
ON ............................................................. 3B1-15
TABLE C - MALFUNCTION INDICATOR
LAMP DOES NOT FLASH, JUST
REMAINS ON OR JUST REMAINS OFF
EVEN WITH DIAGNOSIS SWITCH
TERMINAL GROUNDED .......................... 3B1-15
DTC C1111 (DTC No.11) TORQUE
SENSOR MAIN CIRCUIT FAILURE ......... 3B1-16
DTC C1113 (DTC No.13) TORQUE
SENSOR MAIN AND SUB CIRCUIT
FAILURE ................................................... 3B1-16DTC C1115 (DTC No.15) TORQUE
SENSOR SUB CIRCUIT FAILURE........... 3B1-16
DTC C1114 (DTC No.14) TORQUE
SENSOR 5V POWER SUPPLY CIRCUIT
FAILURE ................................................... 3B1-17
DTC C1116 (DTC No.16) TORQUE
SENSOR 8V POWER SUPPLY CIRCUIT
FAILURE ................................................... 3B1-18
DTC C1121/C1123/C1124
(DTC No.21/23/24) VSS CIRCUIT
FAILURE ................................................... 3B1-19
DTC C1122 (DTC No.22) ENGINE
SPEED SIGNAL CIRCUIT FAILURE ........ 3B1-20
DTC C1141/C1142/C1143/C1144/C1145
(DTC No.41/42/43/44/45) MOTOR
CIRCUIT FAILURE ................................... 3B1-21
DTC C1151 (DTC No.51) CLUTCH
CIRCUIT FAILURE ................................... 3B1-22
DTC C1153(DTC No.53) P/S CONTROL
MODULE POWER SUPPLY CIRCUIT
FAILURE ................................................... 3B1-24
DTC C1152/C1154/C1155
(DTC No.52/54/55) P/S CONTROL
MODULE FAILURE .................................. 3B1-24
TROUBLE DIAGNOSIS (FOR TROUBLE
NOT INDICATED BY ON BOARD
DIAGNOSTIC SYSTEM)........................... 3B1-25
INSPECTION OF P/S CONTROL
MODULE AND ITS CIRCUITS ................. 3B1-26
STEERING WHEEL PLAY
INSPECTION ............................................ 3B1-28 WARNING:
For vehicles equipped with Supplemental Restraint (Air Bag) System :
Service on and around the air bag system components or wiring must be performed only by an
authorized SUZUKI dealer. Refer to “Air Bag System Components and Wiring Location View” under
“General Description” in air bag system section in order to confirm whether you are performing ser-
vice on or near the air bag system components or wiring. Please observe all WARNINGS and “Ser-
vice Precautions” under “On-Vehicle Service” in air bag system section before performing service
on or around the air bag system components or wiring. Failure to follow WARNINGS could result in
unintentional activation of the system or could render the system inoperative. Either of these two
conditions may result in severe injury.
Technical service work must be started at least 90 seconds after the ignition switch is turned to the
“LOCK” position and the negative cable is disconnected from the battery. Otherwise, the system
may be activated by reserve energy in the Sensing and Diagnostic Module (SDM).
Page 145 of 698
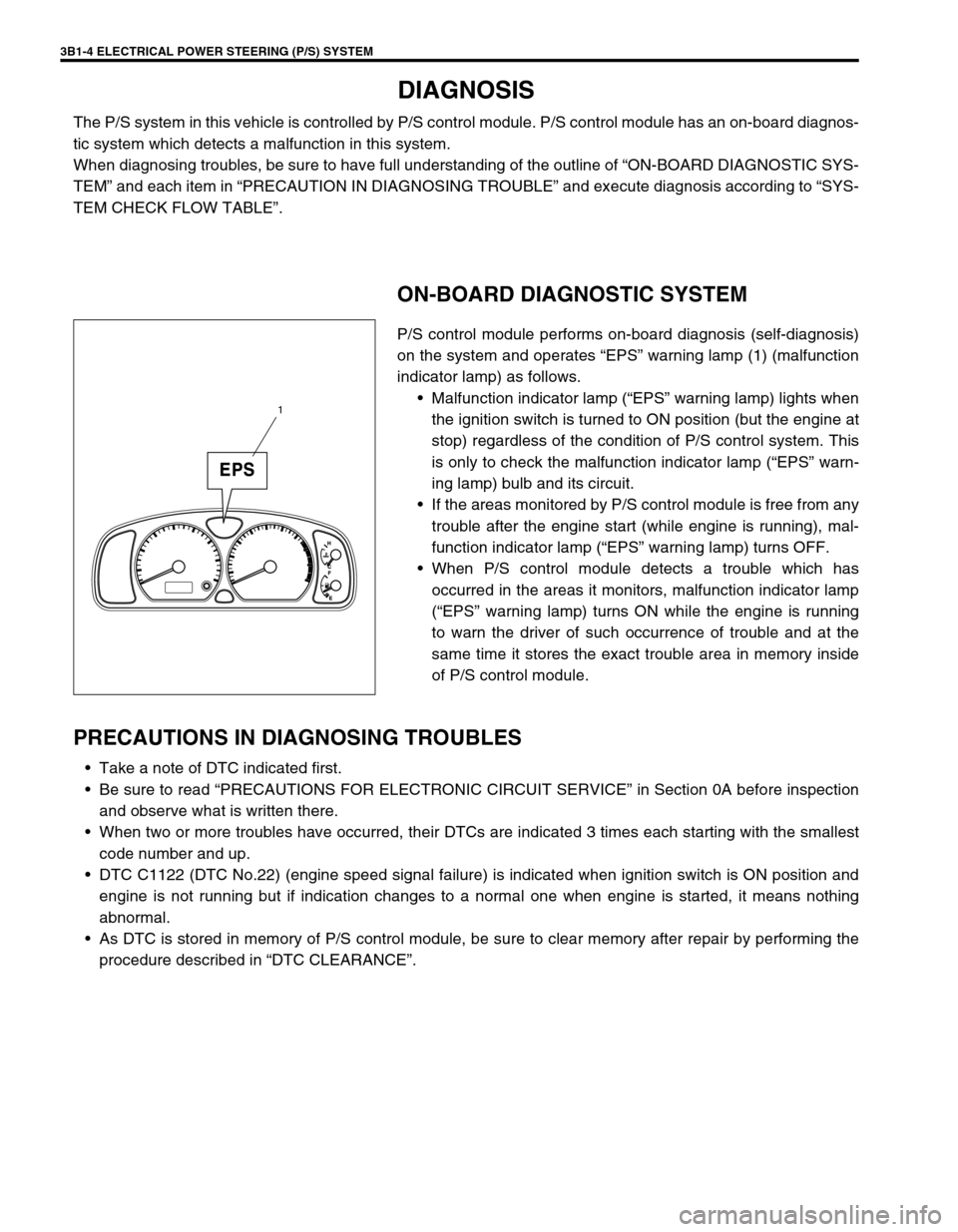
3B1-4 ELECTRICAL POWER STEERING (P/S) SYSTEM
DIAGNOSIS
The P/S system in this vehicle is controlled by P/S control module. P/S control module has an on-board diagnos-
tic system which detects a malfunction in this system.
When diagnosing troubles, be sure to have full understanding of the outline of “ON-BOARD DIAGNOSTIC SYS-
TEM” and each item in “PRECAUTION IN DIAGNOSING TROUBLE” and execute diagnosis according to “SYS-
TEM CHECK FLOW TABLE”.
ON-BOARD DIAGNOSTIC SYSTEM
P/S control module performs on-board diagnosis (self-diagnosis)
on the system and operates “EPS” warning lamp (1) (malfunction
indicator lamp) as follows.
Malfunction indicator lamp (“EPS” warning lamp) lights when
the ignition switch is turned to ON position (but the engine at
stop) regardless of the condition of P/S control system. This
is only to check the malfunction indicator lamp (“EPS” warn-
ing lamp) bulb and its circuit.
If the areas monitored by P/S control module is free from any
trouble after the engine start (while engine is running), mal-
function indicator lamp (“EPS” warning lamp) turns OFF.
When P/S control module detects a trouble which has
occurred in the areas it monitors, malfunction indicator lamp
(“EPS” warning lamp) turns ON while the engine is running
to warn the driver of such occurrence of trouble and at the
same time it stores the exact trouble area in memory inside
of P/S control module.
PRECAUTIONS IN DIAGNOSING TROUBLES
Take a note of DTC indicated first.
Be sure to read “PRECAUTIONS FOR ELECTRONIC CIRCUIT SERVICE” in Section 0A before inspection
and observe what is written there.
When two or more troubles have occurred, their DTCs are indicated 3 times each starting with the smallest
code number and up.
DTC C1122 (DTC No.22) (engine speed signal failure) is indicated when ignition switch is ON position and
engine is not running but if indication changes to a normal one when engine is started, it means nothing
abnormal.
As DTC is stored in memory of P/S control module, be sure to clear memory after repair by performing the
procedure described in “DTC CLEARANCE”.
1
Page 146 of 698
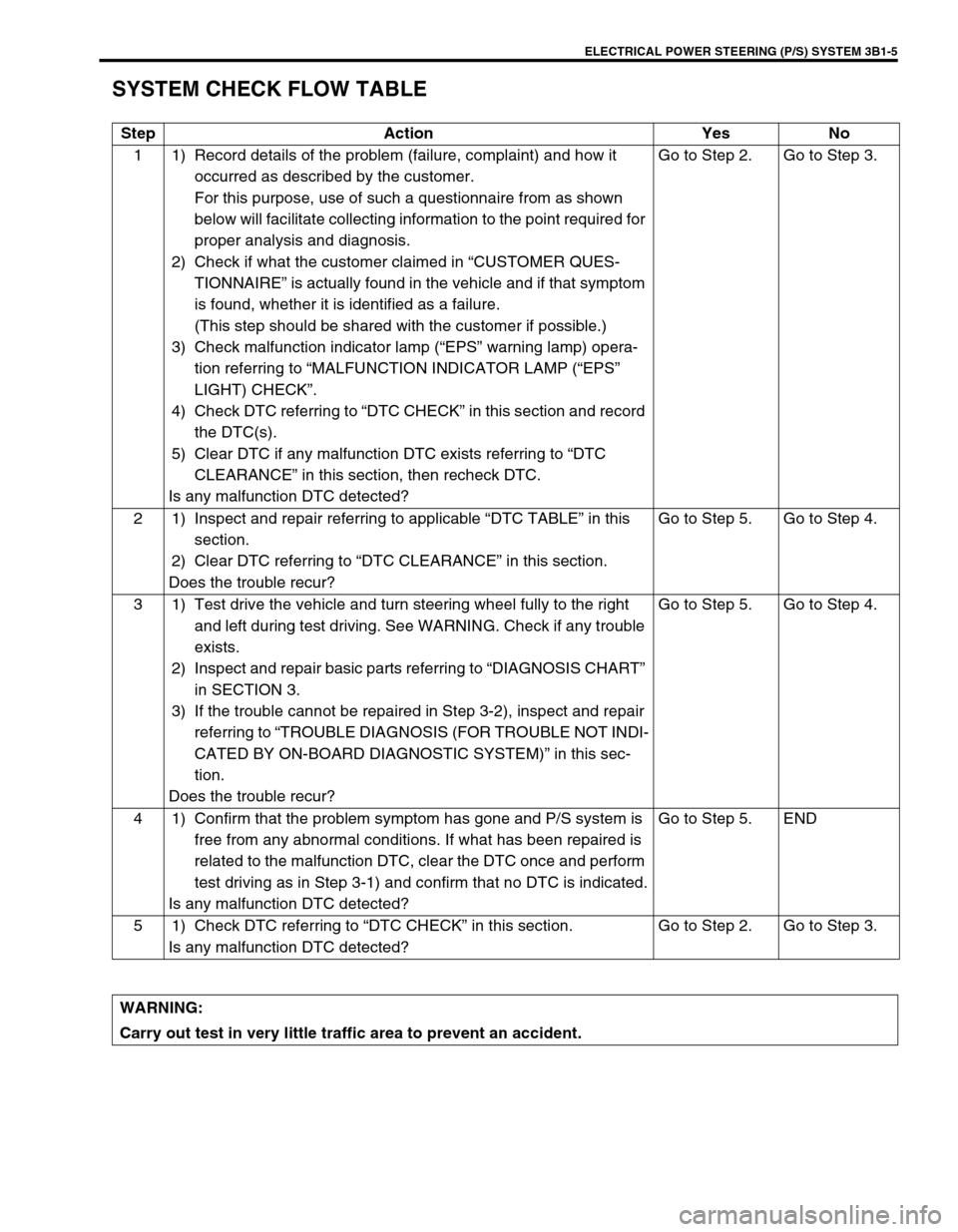
ELECTRICAL POWER STEERING (P/S) SYSTEM 3B1-5
SYSTEM CHECK FLOW TABLE
Step Action Yes No
1 1) Record details of the problem (failure, complaint) and how it
occurred as described by the customer.
For this purpose, use of such a questionnaire from as shown
below will facilitate collecting information to the point required for
proper analysis and diagnosis.
2) Check if what the customer claimed in “CUSTOMER QUES-
TIONNAIRE” is actually found in the vehicle and if that symptom
is found, whether it is identified as a failure.
(This step should be shared with the customer if possible.)
3) Check malfunction indicator lamp (“EPS” warning lamp) opera-
tion referring to “MALFUNCTION INDICATOR LAMP (“EPS”
LIGHT) CHECK”.
4) Check DTC referring to “DTC CHECK” in this section and record
the DTC(s).
5) Clear DTC if any malfunction DTC exists referring to “DTC
CLEARANCE” in this section, then recheck DTC.
Is any malfunction DTC detected?Go to Step 2. Go to Step 3.
2 1) Inspect and repair referring to applicable “DTC TABLE” in this
section.
2) Clear DTC referring to “DTC CLEARANCE” in this section.
Does the trouble recur?Go to Step 5. Go to Step 4.
3 1) Test drive the vehicle and turn steering wheel fully to the right
and left during test driving. See WARNING. Check if any trouble
exists.
2) Inspect and repair basic parts referring to “DIAGNOSIS CHART”
in SECTION 3.
3) If the trouble cannot be repaired in Step 3-2), inspect and repair
referring to “TROUBLE DIAGNOSIS (FOR TROUBLE NOT INDI-
CATED BY ON-BOARD DIAGNOSTIC SYSTEM)” in this sec-
tion.
Does the trouble recur?Go to Step 5. Go to Step 4.
4 1) Confirm that the problem symptom has gone and P/S system is
free from any abnormal conditions. If what has been repaired is
related to the malfunction DTC, clear the DTC once and perform
test driving as in Step 3-1) and confirm that no DTC is indicated.
Is any malfunction DTC detected?Go to Step 5. END
5 1) Check DTC referring to “DTC CHECK” in this section.
Is any malfunction DTC detected?Go to Step 2. Go to Step 3.
WARNING:
Carry out test in very little traffic area to prevent an accident.
Page 148 of 698
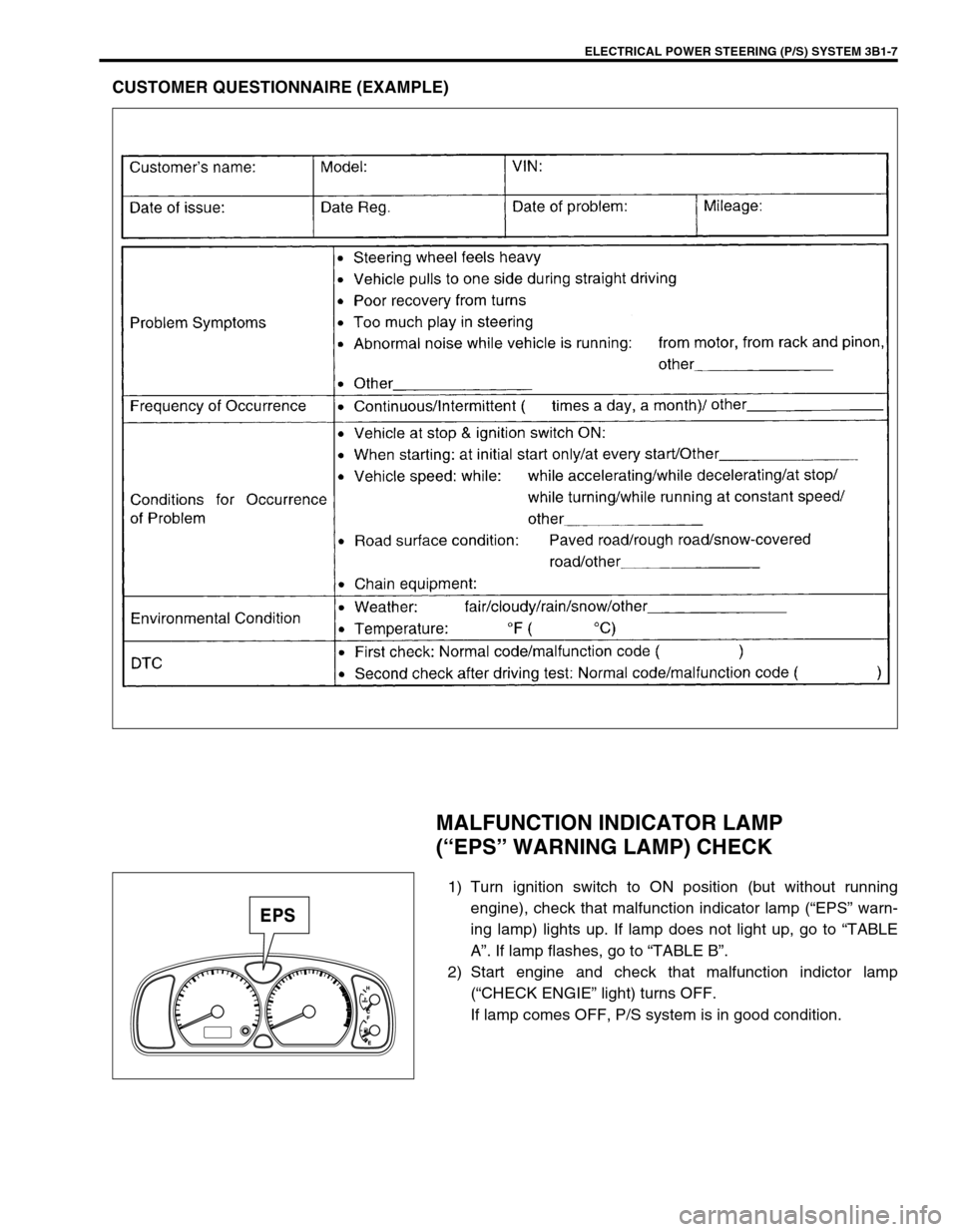
ELECTRICAL POWER STEERING (P/S) SYSTEM 3B1-7
CUSTOMER QUESTIONNAIRE (EXAMPLE)
MALFUNCTION INDICATOR LAMP
(“EPS” WARNING LAMP) CHECK
1) Turn ignition switch to ON position (but without running
engine), check that malfunction indicator lamp (“EPS” warn-
ing lamp) lights up. If lamp does not light up, go to “TABLE
A”. If lamp flashes, go to “TABLE B”.
2) Start engine and check that malfunction indictor lamp
(“CHECK ENGIE” light) turns OFF.
If lamp comes OFF, P/S system is in good condition.
Page 158 of 698
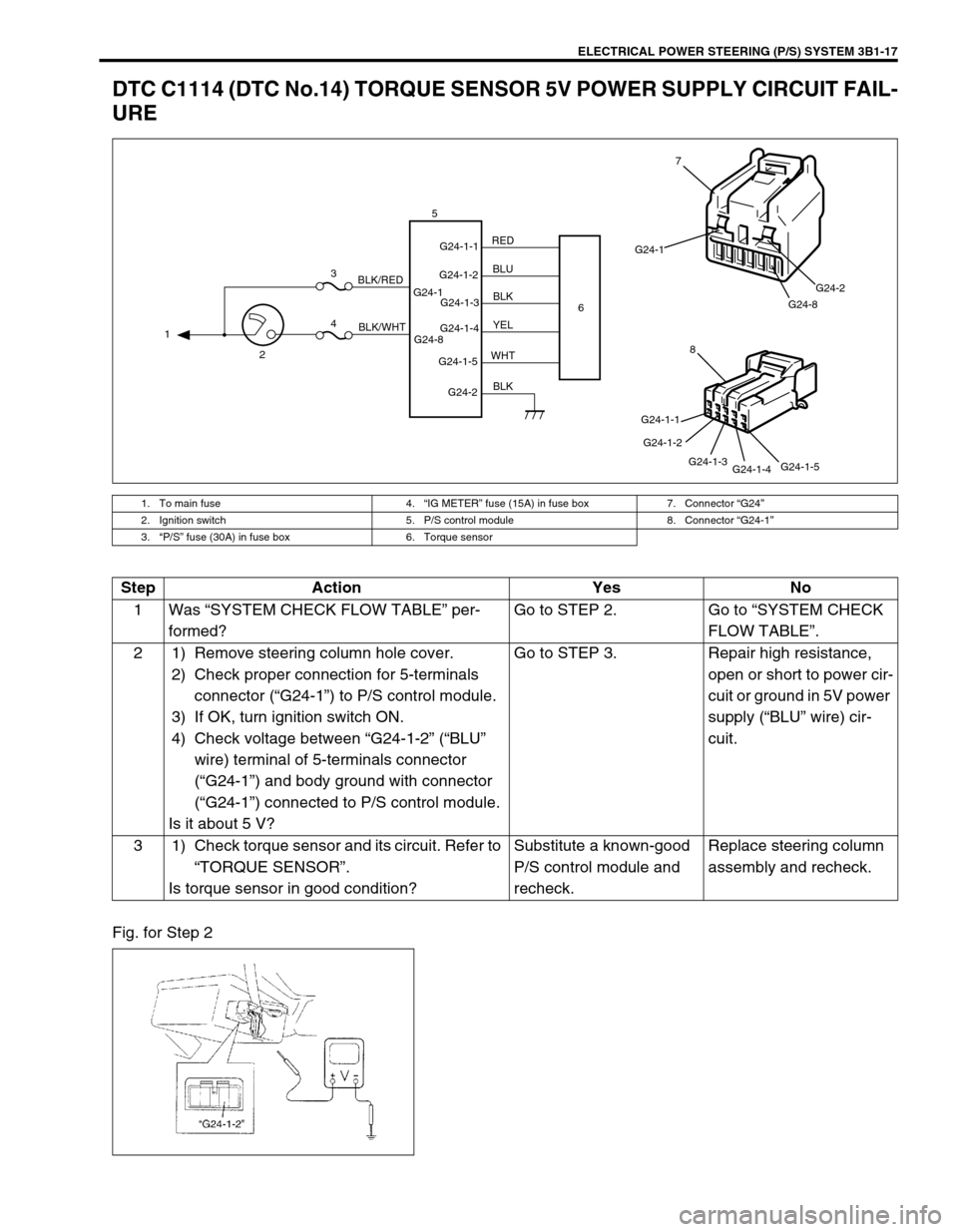
ELECTRICAL POWER STEERING (P/S) SYSTEM 3B1-17
DTC C1114 (DTC No.14) TORQUE SENSOR 5V POWER SUPPLY CIRCUIT FAIL-
URE
Fig. for Step 2
1. To main fuse 4.“IG METER” fuse (15A) in fuse box 7. Connector “G24”
2. Ignition switch 5. P/S control module 8. Connector “G24-1”
3.“P/S” fuse (30A) in fuse box 6. Torque sensor
G24-1
G24-8G24-2
7
G24-1-5
G24-1-4 G24-1-3 G24-1-2 G24-1-18
G24-2 G24-1
G24-8G24-1-4G24-1-3
G24-1-5G24-1-2G24-1-1
1
23
45
6
BLK/WHT BLK/RED
BLK WHTYEL BLK BLU RED
Step Action Yes No
1Was “SYSTEM CHECK FLOW TABLE” per-
formed?Go to STEP 2. Go to “SYSTEM CHECK
FLOW TABLE”.
2 1) Remove steering column hole cover.
2) Check proper connection for 5-terminals
connector (“G24-1”) to P/S control module.
3) If OK, turn ignition switch ON.
4) Check voltage between “G24-1-2” (“BLU”
wire) terminal of 5-terminals connector
(“G24-1”) and body ground with connector
(“G24-1”) connected to P/S control module.
Is it about 5 V?Go to STEP 3. Repair high resistance,
open or short to power cir-
cuit or ground in 5V power
supply (“BLU” wire) cir-
cuit.
3 1) Check torque sensor and its circuit. Refer to
“TORQUE SENSOR”.
Is torque sensor in good condition?Substitute a known-good
P/S control module and
recheck.Replace steering column
assembly and recheck.
Page 159 of 698
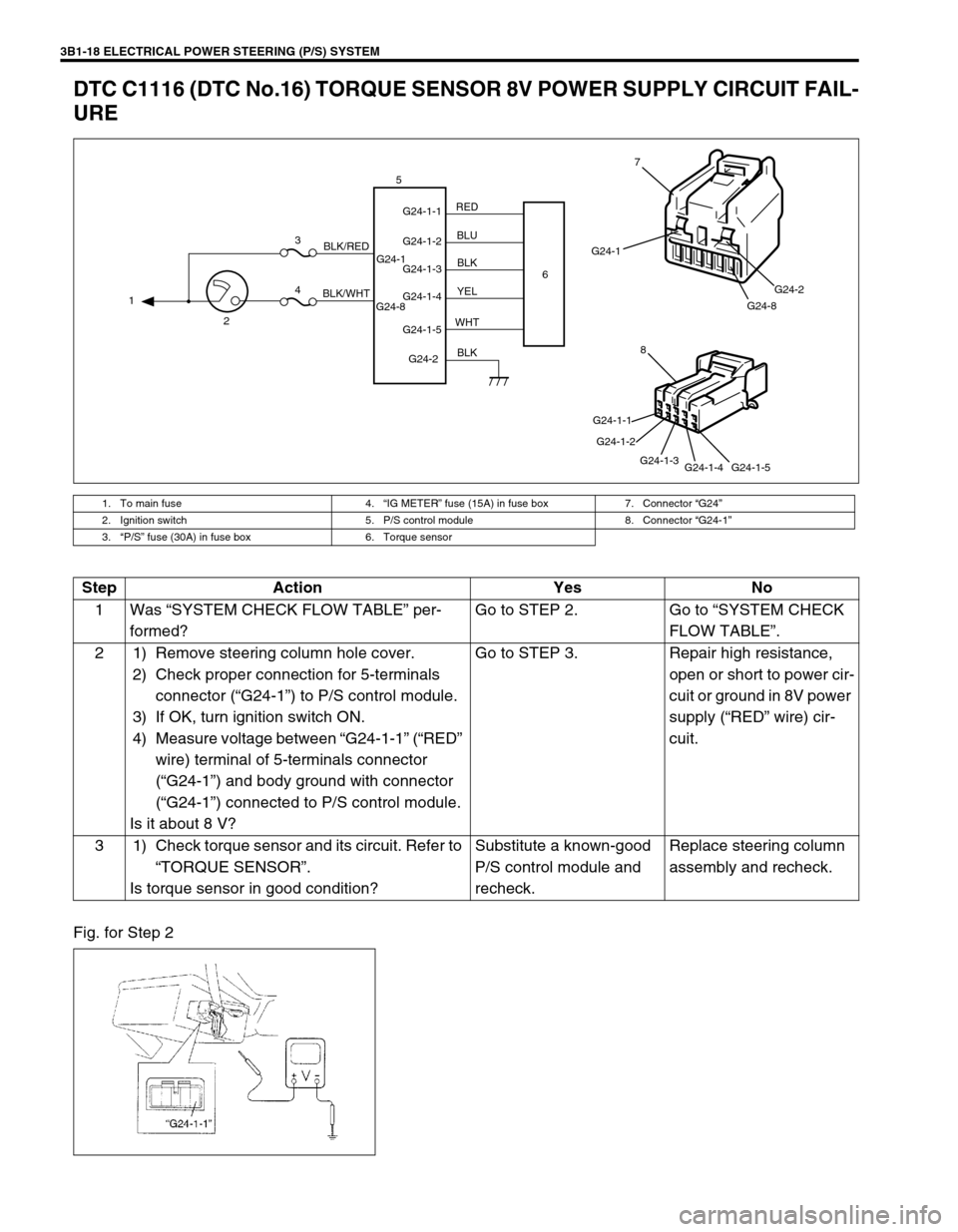
3B1-18 ELECTRICAL POWER STEERING (P/S) SYSTEM
DTC C1116 (DTC No.16) TORQUE SENSOR 8V POWER SUPPLY CIRCUIT FAIL-
URE
Fig. for Step 2
1. To main fuse 4.“IG METER” fuse (15A) in fuse box 7. Connector “G24”
2. Ignition switch 5. P/S control module 8. Connector “G24-1”
3.“P/S” fuse (30A) in fuse box 6. Torque sensor
G24-1
G24-8G24-2
7
G24-1-5
G24-1-4 G24-1-3 G24-1-2 G24-1-18
G24-2 G24-1
G24-8G24-1-4 G24-1-3
G24-1-5 G24-1-2 G24-1-1
1
23
45
6
BLK/WHTBLK/RED
BLK WHTYEL BLK BLU RED
Step Action Yes No
1Was “SYSTEM CHECK FLOW TABLE” per-
formed?Go to STEP 2. Go to “SYSTEM CHECK
FLOW TABLE”.
2 1) Remove steering column hole cover.
2) Check proper connection for 5-terminals
connector (“G24-1”) to P/S control module.
3) If OK, turn ignition switch ON.
4) Measure voltage between “G24-1-1” (“RED”
wire) terminal of 5-terminals connector
(“G24-1”) and body ground with connector
(“G24-1”) connected to P/S control module.
Is it about 8 V?Go to STEP 3. Repair high resistance,
open or short to power cir-
cuit or ground in 8V power
supply (“RED” wire) cir-
cuit.
3 1) Check torque sensor and its circuit. Refer to
“TORQUE SENSOR”.
Is torque sensor in good condition?Substitute a known-good
P/S control module and
recheck.Replace steering column
assembly and recheck.