Compression SUZUKI SWIFT 2000 1.G SF310 Service Owner's Manual
[x] Cancel search | Manufacturer: SUZUKI, Model Year: 2000, Model line: SWIFT, Model: SUZUKI SWIFT 2000 1.GPages: 557, PDF Size: 14.35 MB
Page 299 of 557
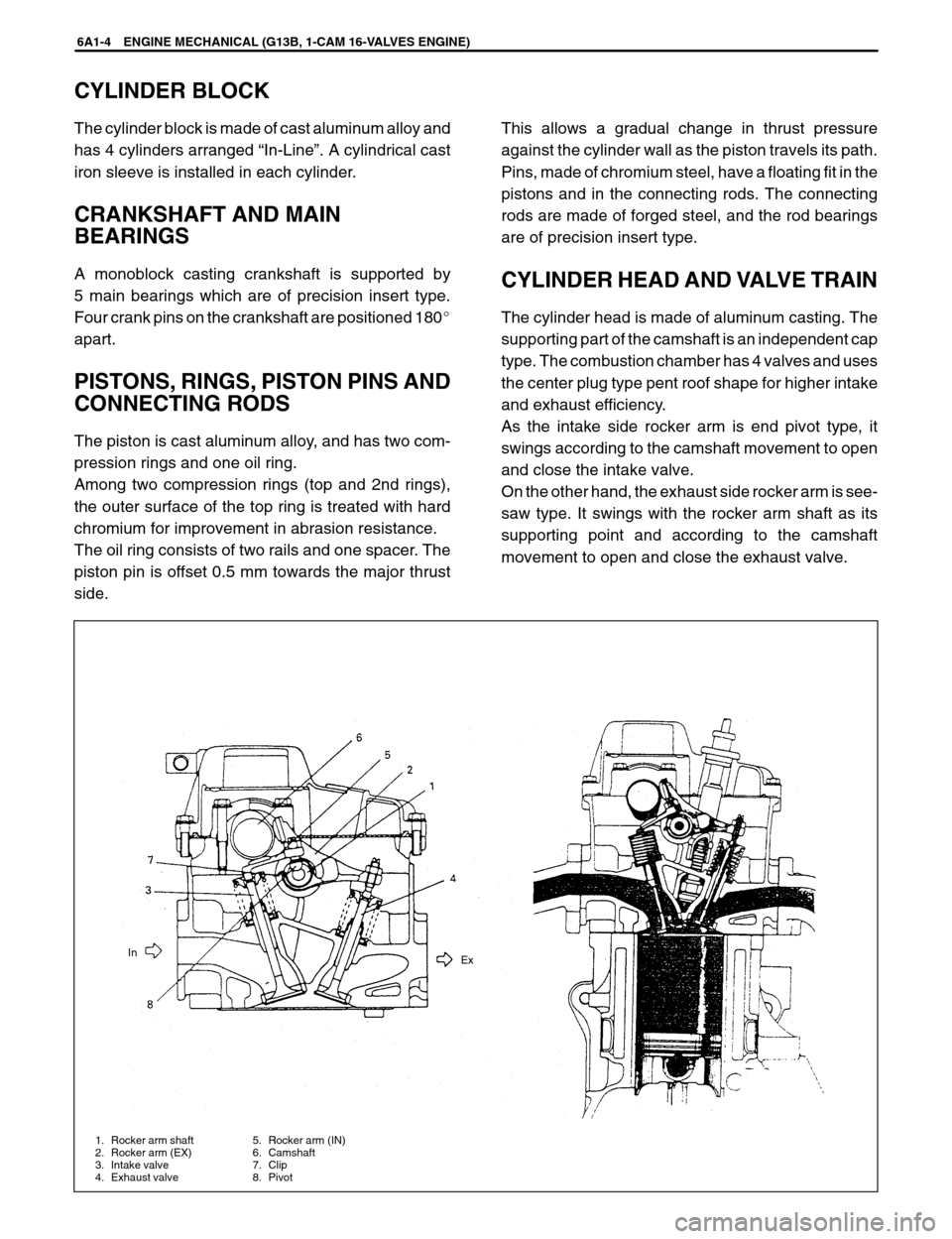
1. Rocker arm shaft
2. Rocker arm (EX)
3. Intake valve
4. Exhaust valve5. Rocker arm (IN)
6. Camshaft
7. Clip
8. PivotEx In
CYLINDER BLOCK
The cylinder block is made of cast aluminum alloy and
has 4 cylinders arranged “In-Line”. A cylindrical cast
iron sleeve is installed in each cylinder.
CRANKSHAFT AND MAIN
BEARINGS
A monoblock casting crankshaft is supported by
5 main bearings which are of precision insert type.
Four crank pins on the crankshaft are positioned 180
apart.
PISTONS, RINGS, PISTON PINS AND
CONNECTING RODS
The piston is cast aluminum alloy, and has two com-
pression rings and one oil ring.
Among two compression rings (top and 2nd rings),
the outer surface of the top ring is treated with hard
chromium for improvement in abrasion resistance.
The oil ring consists of two rails and one spacer. The
piston pin is offset 0.5 mm towards the major thrust
side.This allows a gradual change in thrust pressure
against the cylinder wall as the piston travels its path.
Pins, made of chromium steel, have a floating fit in the
pistons and in the connecting rods. The connecting
rods are made of forged steel, and the rod bearings
are of precision insert type.
CYLINDER HEAD AND VALVE TRAIN
The cylinder head is made of aluminum casting. The
supporting part of the camshaft is an independent cap
type. The combustion chamber has 4 valves and uses
the center plug type pent roof shape for higher intake
and exhaust efficiency.
As the intake side rocker arm is end pivot type, it
swings according to the camshaft movement to open
and close the intake valve.
On the other hand, the exhaust side rocker arm is see-
saw type. It swings with the rocker arm shaft as its
supporting point and according to the camshaft
movement to open and close the exhaust valve.
6A1-4 ENGINE MECHANICAL (G13B, 1-CAM 16-VALVES ENGINE)
Page 300 of 557
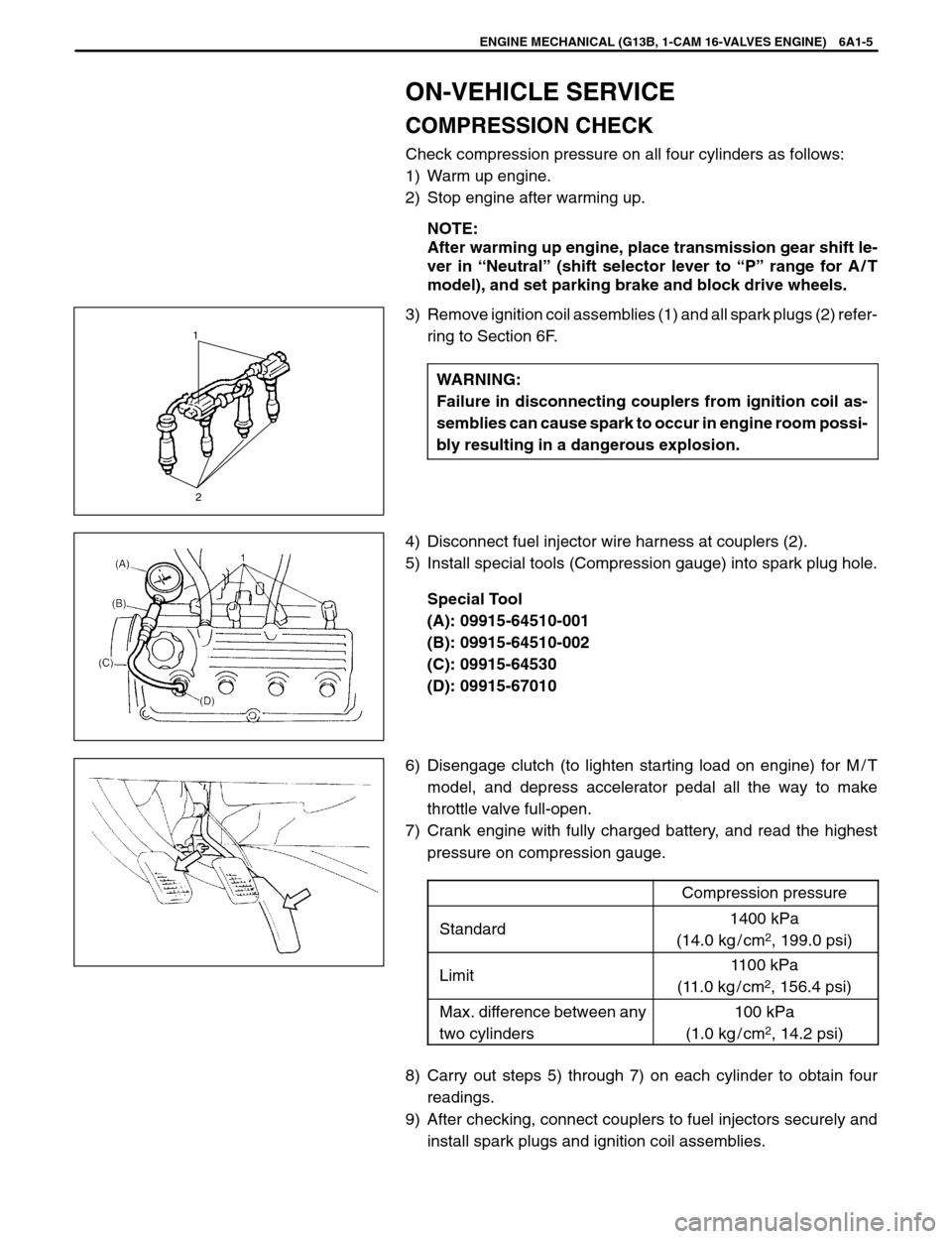
1
2
ENGINE MECHANICAL (G13B, 1-CAM 16-VALVES ENGINE) 6A1-5
ON-VEHICLE SERVICE
COMPRESSION CHECK
Check compression pressure on all four cylinders as follows:
1) Warm up engine.
2) Stop engine after warming up.
NOTE:
After warming up engine, place transmission gear shift le-
ver in “Neutral” (shift selector lever to “P” range for A / T
model), and set parking brake and block drive wheels.
3) Remove ignition coil assemblies (1) and all spark plugs (2) refer-
ring to Section 6F.
WARNING:
Failure in disconnecting couplers from ignition coil as-
semblies can cause spark to occur in engine room possi-
bly resulting in a dangerous explosion.
4) Disconnect fuel injector wire harness at couplers (2).
5) Install special tools (Compression gauge) into spark plug hole.
Special Tool
(A): 09915-64510-001
(B): 09915-64510-002
(C): 09915-64530
(D): 09915-67010
6) Disengage clutch (to lighten starting load on engine) for M / T
model, and depress accelerator pedal all the way to make
throttle valve full-open.
7) Crank engine with fully charged battery, and read the highest
pressure on compression gauge.
Compression pressure
Standard1400 kPa
(14.0 kg / cm
2, 199.0 psi)
Limit1100 kPa
(11.0 kg / cm
2, 156.4 psi)
Max. difference between any
two cylinders100 kPa
(1.0 kg / cm
2, 14.2 psi)
8) Carry out steps 5) through 7) on each cylinder to obtain four
readings.
9) After checking, connect couplers to fuel injectors securely and
install spark plugs and ignition coil assemblies.
Page 350 of 557
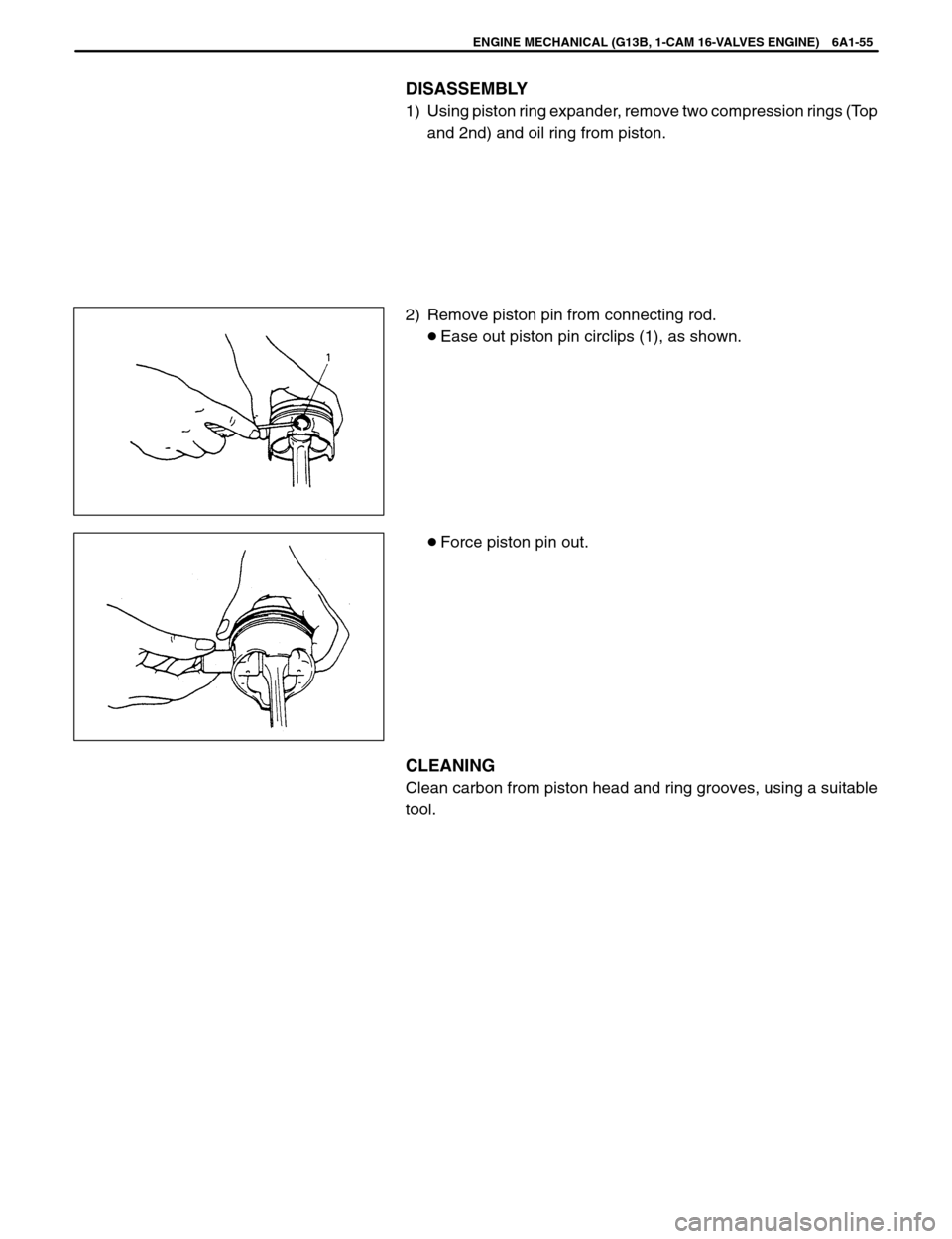
ENGINE MECHANICAL (G13B, 1-CAM 16-VALVES ENGINE) 6A1-55
DISASSEMBLY
1) Using piston ring expander, remove two compression rings (Top
and 2nd) and oil ring from piston.
2) Remove piston pin from connecting rod.
Ease out piston pin circlips (1), as shown.
Force piston pin out.
CLEANING
Clean carbon from piston head and ring grooves, using a suitable
tool.
Page 375 of 557
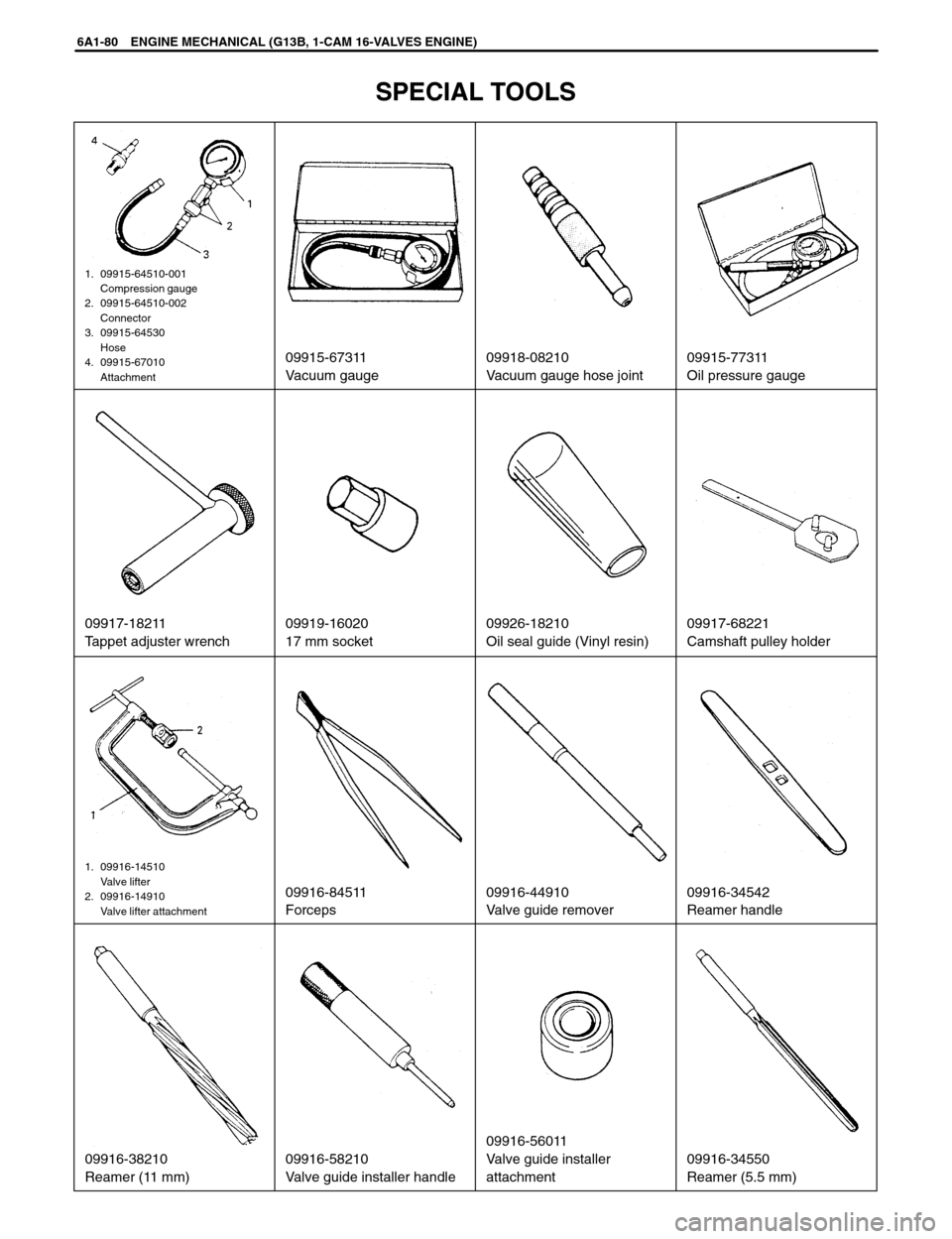
1. 09915-64510-001
Compression gauge
2. 09915-64510-002
Connector
3. 09915-64530
Hose
4. 09915-67010
Attachment
09915-67311
Vacuum gauge09918-08210
Vacuum gauge hose joint09915-77311
Oil pressure gauge
09917-18211
Tappet adjuster wrench09919-16020
17 mm socket09926-18210
Oil seal guide (Vinyl resin)09917-68221
Camshaft pulley holder
1. 09916-14510
Valve lifter
2. 09916-14910
Valve lifter attachment
09916-84511
Forceps09916-44910
Valve guide remover09916-34542
Reamer handle
09916-38210
Reamer (11 mm)09916-58210
Valve guide installer handle09916-56011
Valve guide installer
attachment09916-34550
Reamer (5.5 mm)
6A1-80 ENGINE MECHANICAL (G13B, 1-CAM 16-VALVES ENGINE)
SPECIAL TOOLS
Page 481 of 557
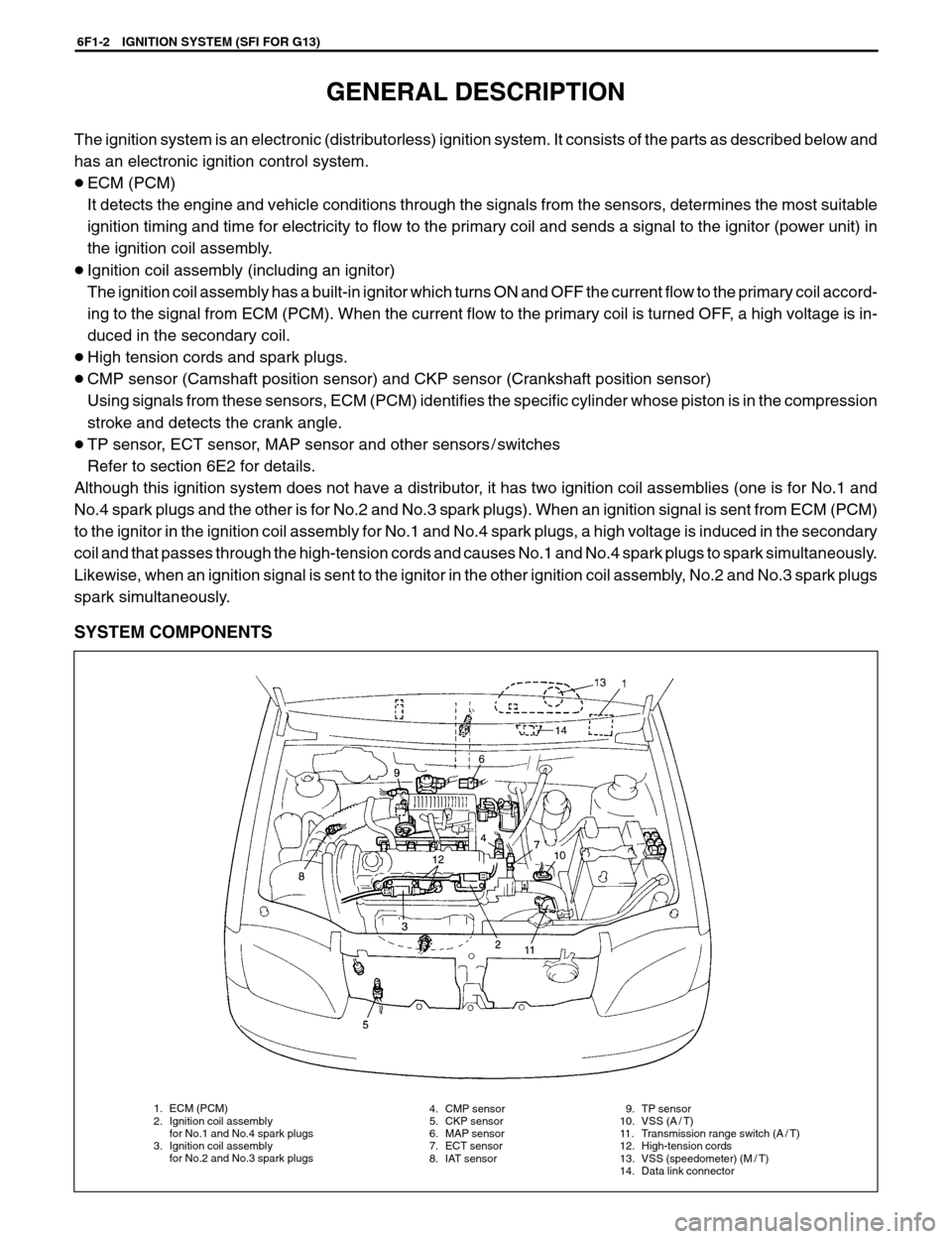
1. ECM (PCM)
2. Ignition coil assembly
for No.1 and No.4 spark plugs
3. Ignition coil assembly
for No.2 and No.3 spark plugs4. CMP sensor
5. CKP sensor
6. MAP sensor
7. ECT sensor
8. IAT sensor9. TP sensor
10. VSS (A / T)
11. Transmission range switch (A / T)
12. High-tension cords
13. VSS (speedometer) (M / T)
14. Data link connector
6F1-2 IGNITION SYSTEM (SFI FOR G13)
GENERAL DESCRIPTION
The ignition system is an electronic (distributorless) ignition system. It consists of the parts as described below and
has an electronic ignition control system.
ECM (PCM)
It detects the engine and vehicle conditions through the signals from the sensors, determines the most suitable
ignition timing and time for electricity to flow to the primary coil and sends a signal to the ignitor (power unit) in
the ignition coil assembly.
Ignition coil assembly (including an ignitor)
The ignition coil assembly has a built-in ignitor which turns ON and OFF the current flow to the primary coil accord-
ing to the signal from ECM (PCM). When the current flow to the primary coil is turned OFF, a high voltage is in-
duced in the secondary coil.
High tension cords and spark plugs.
CMP sensor (Camshaft position sensor) and CKP sensor (Crankshaft position sensor)
Using signals from these sensors, ECM (PCM) identifies the specific cylinder whose piston is in the compression
stroke and detects the crank angle.
TP sensor, ECT sensor, MAP sensor and other sensors / switches
Refer to section 6E2 for details.
Although this ignition system does not have a distributor, it has two ignition coil assemblies (one is for No.1 and
No.4 spark plugs and the other is for No.2 and No.3 spark plugs). When an ignition signal is sent from ECM (PCM)
to the ignitor in the ignition coil assembly for No.1 and No.4 spark plugs, a high voltage is induced in the secondary
coil and that passes through the high-tension cords and causes No.1 and No.4 spark plugs to spark simultaneously.
Likewise, when an ignition signal is sent to the ignitor in the other ignition coil assembly, No.2 and No.3 spark plugs
spark simultaneously.
SYSTEM COMPONENTS
Page 528 of 557
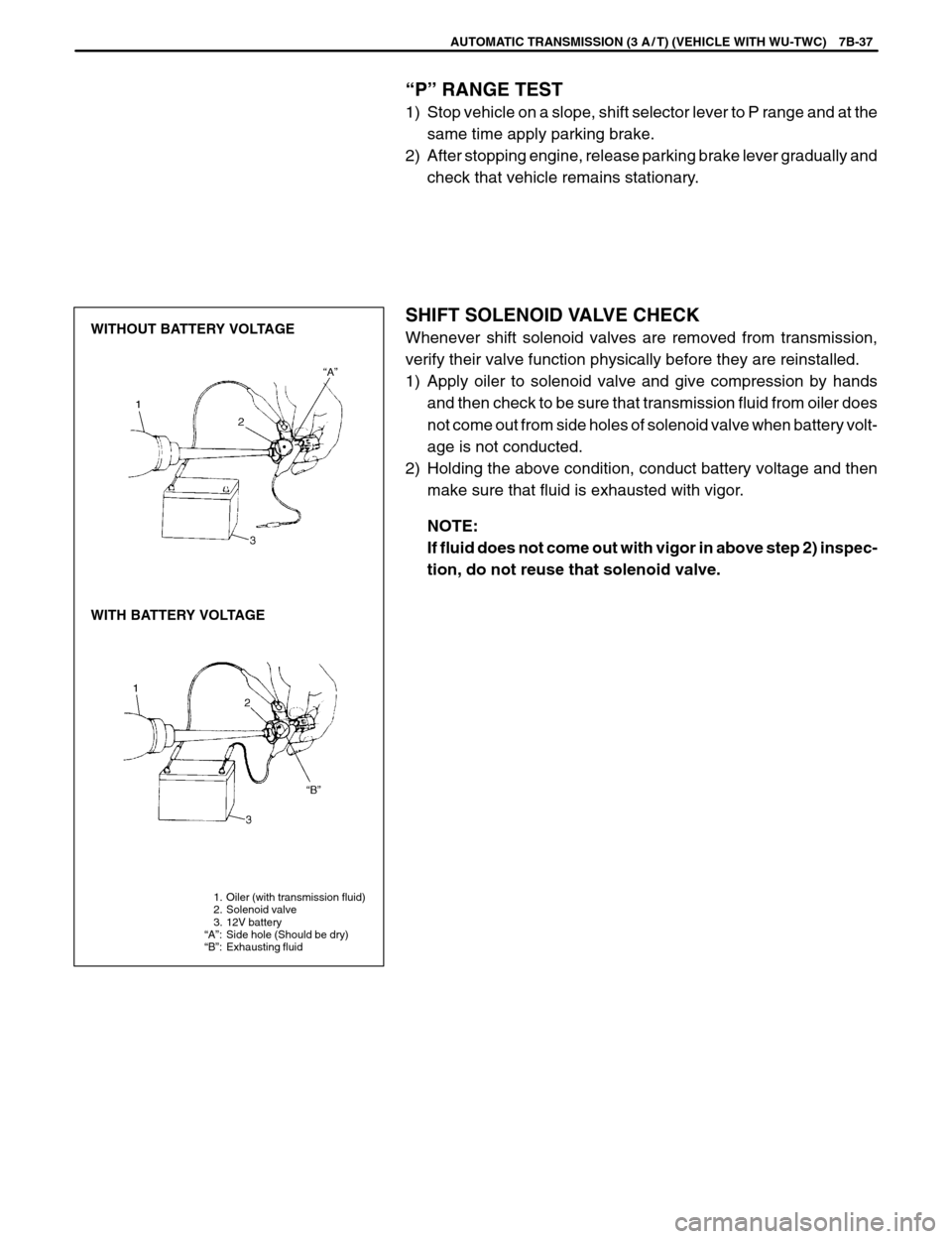
WITHOUT BATTERY VOLTAGE
WITH BATTERY VOLTAGE
1. Oiler (with transmission fluid)
2. Solenoid valve
3. 12V battery
“A”: Side hole (Should be dry)
“B”: Exhausting fluid
AUTOMATIC TRANSMISSION (3 A / T) (VEHICLE WITH WU-TWC) 7B-37
“P” RANGE TEST
1) Stop vehicle on a slope, shift selector lever to P range and at the
same time apply parking brake.
2) After stopping engine, release parking brake lever gradually and
check that vehicle remains stationary.
SHIFT SOLENOID VALVE CHECK
Whenever shift solenoid valves are removed from transmission,
verify their valve function physically before they are reinstalled.
1) Apply oiler to solenoid valve and give compression by hands
and then check to be sure that transmission fluid from oiler does
not come out from side holes of solenoid valve when battery volt-
age is not conducted.
2) Holding the above condition, conduct battery voltage and then
make sure that fluid is exhausted with vigor.
NOTE:
If fluid does not come out with vigor in above step 2) inspec-
tion, do not reuse that solenoid valve.