brake fluid SUZUKI SWIFT 2000 1.G Transmission Service Workshop Manual
[x] Cancel search | Manufacturer: SUZUKI, Model Year: 2000, Model line: SWIFT, Model: SUZUKI SWIFT 2000 1.GPages: 447, PDF Size: 10.54 MB
Page 44 of 447
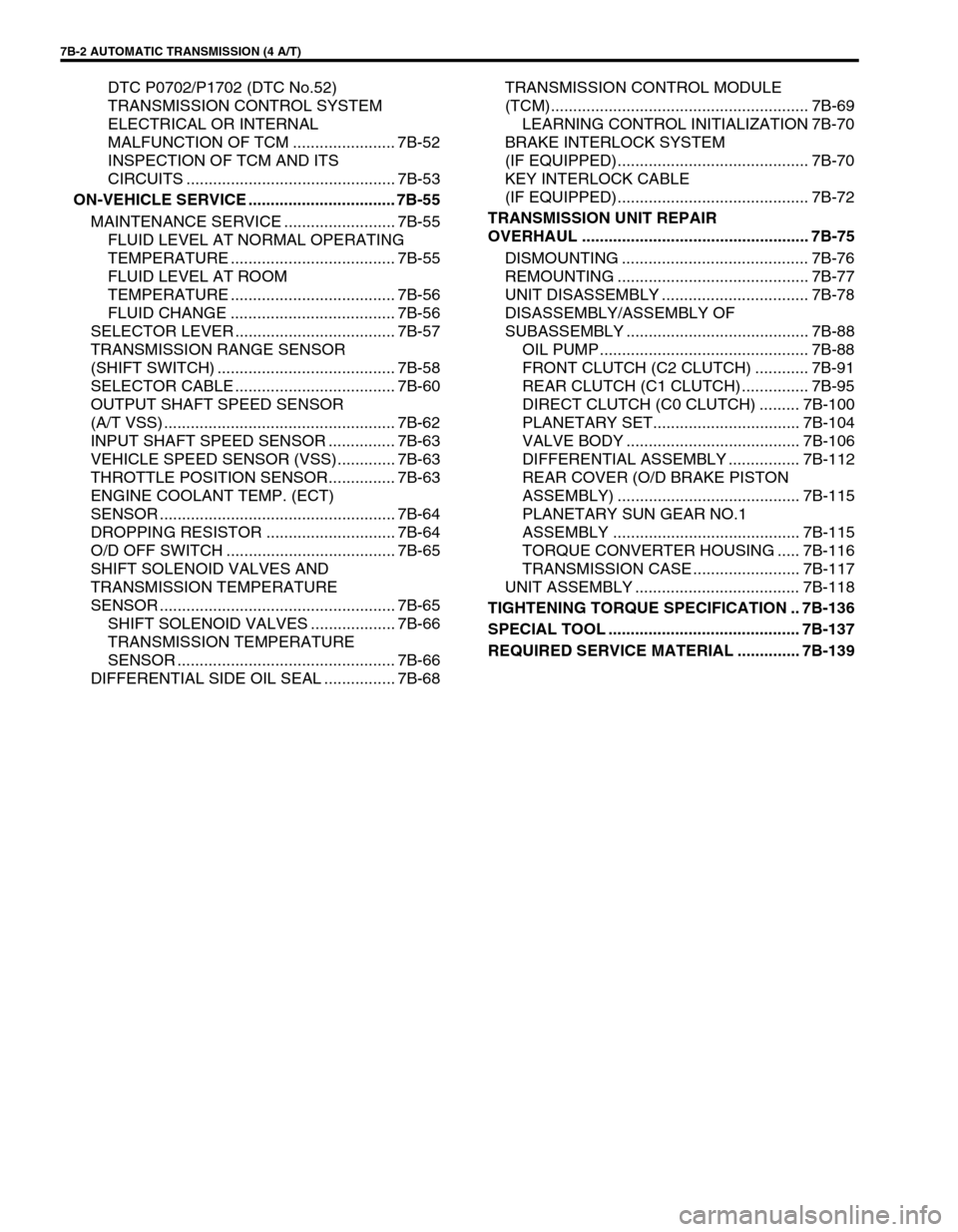
7B-2 AUTOMATIC TRANSMISSION (4 A/T)
DTC P0702/P1702 (DTC No.52)
TRANSMISSION CONTROL SYSTEM
ELECTRICAL OR INTERNAL
MALFUNCTION OF TCM ....................... 7B-52
INSPECTION OF TCM AND ITS
CIRCUITS ............................................... 7B-53
ON-VEHICLE SERVICE ................................. 7B-55
MAINTENANCE SERVICE ......................... 7B-55
FLUID LEVEL AT NORMAL OPERATING
TEMPERATURE ..................................... 7B-55
FLUID LEVEL AT ROOM
TEMPERATURE ..................................... 7B-56
FLUID CHANGE ..................................... 7B-56
SELECTOR LEVER .................................... 7B-57
TRANSMISSION RANGE SENSOR
(SHIFT SWITCH) ........................................ 7B-58
SELECTOR CABLE .................................... 7B-60
OUTPUT SHAFT SPEED SENSOR
(A/T VSS) .................................................... 7B-62
INPUT SHAFT SPEED SENSOR ............... 7B-63
VEHICLE SPEED SENSOR (VSS)............. 7B-63
THROTTLE POSITION SENSOR............... 7B-63
ENGINE COOLANT TEMP. (ECT)
SENSOR ..................................................... 7B-64
DROPPING RESISTOR ............................. 7B-64
O/D OFF SWITCH ...................................... 7B-65
SHIFT SOLENOID VALVES AND
TRANSMISSION TEMPERATURE
SENSOR ..................................................... 7B-65
SHIFT SOLENOID VALVES ................... 7B-66
TRANSMISSION TEMPERATURE
SENSOR ................................................. 7B-66
DIFFERENTIAL SIDE OIL SEAL ................ 7B-68TRANSMISSION CONTROL MODULE
(TCM).......................................................... 7B-69
LEARNING CONTROL INITIALIZATION 7B-70
BRAKE INTERLOCK SYSTEM
(IF EQUIPPED)........................................... 7B-70
KEY INTERLOCK CABLE
(IF EQUIPPED)........................................... 7B-72
TRANSMISSION UNIT REPAIR
OVERHAUL ................................................... 7B-75
DISMOUNTING .......................................... 7B-76
REMOUNTING ........................................... 7B-77
UNIT DISASSEMBLY ................................. 7B-78
DISASSEMBLY/ASSEMBLY OF
SUBASSEMBLY ......................................... 7B-88
OIL PUMP ............................................... 7B-88
FRONT CLUTCH (C2 CLUTCH) ............ 7B-91
REAR CLUTCH (C1 CLUTCH) ............... 7B-95
DIRECT CLUTCH (C0 CLUTCH) ......... 7B-100
PLANETARY SET................................. 7B-104
VALVE BODY ....................................... 7B-106
DIFFERENTIAL ASSEMBLY ................ 7B-112
REAR COVER (O/D BRAKE PISTON
ASSEMBLY) ......................................... 7B-115
PLANETARY SUN GEAR NO.1
ASSEMBLY .......................................... 7B-115
TORQUE CONVERTER HOUSING ..... 7B-116
TRANSMISSION CASE ........................ 7B-117
UNIT ASSEMBLY ..................................... 7B-118
TIGHTENING TORQUE SPECIFICATION .. 7B-136
SPECIAL TOOL ........................................... 7B-137
REQUIRED SERVICE MATERIAL .............. 7B-139
Page 46 of 447
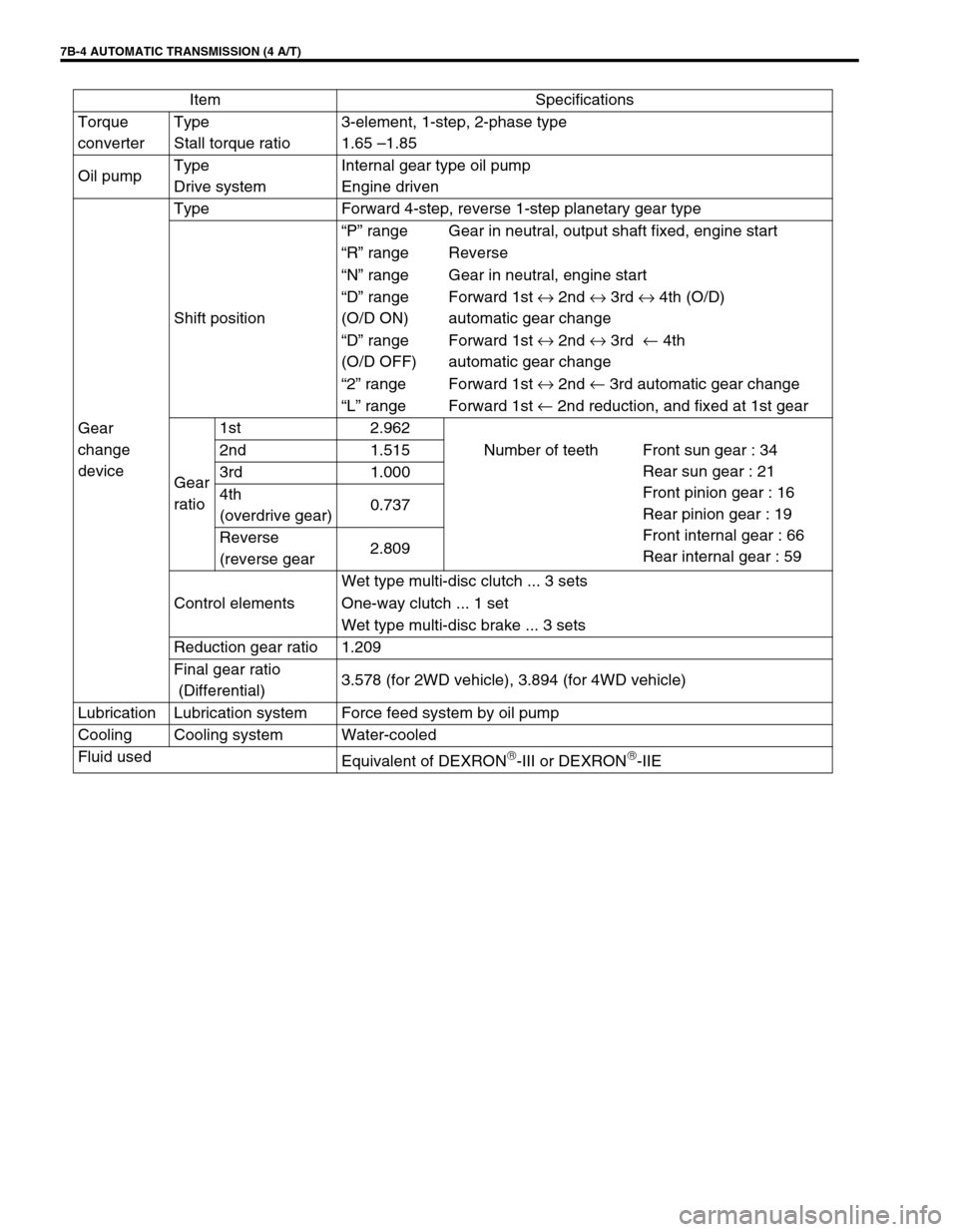
7B-4 AUTOMATIC TRANSMISSION (4 A/T)
Item Specifications
Torque
converterType
Stall torque ratio3-element, 1-step, 2-phase type
1.65 –1.85
Oil pumpType
Drive systemInternal gear type oil pump
Engine driven
Gear
change
deviceType Forward 4-step, reverse 1-step planetary gear type
Shift position“P” range Gear in neutral, output shaft fixed, engine start
“R” range Reverse
“N” range Gear in neutral, engine start
“D” range
(O/D ON)Forward 1st ↔
2nd ↔
3rd ↔
4th (O/D)
automatic gear change
“D” range
(O/D OFF)Forward 1st ↔
2nd ↔
3rd ←
4th
automatic gear change
“2” range Forward 1st ↔
2nd ←
3rd automatic gear change
“L” range Forward 1st ←
2nd reduction, and fixed at 1st gear
Gear
ratio1st 2.962
2nd 1.515 Number of teeth Front sun gear : 34
Rear sun gear : 21
Front pinion gear : 16
Rear pinion gear : 19
Front internal gear : 66
Rear internal gear : 59 3rd 1.000
4th
(overdrive gear)0.737
Reverse
(reverse gear2.809
Control elementsWet type multi-disc clutch ... 3 sets
One-way clutch ... 1 set
Wet type multi-disc brake ... 3 sets
Reduction gear ratio 1.209
Final gear ratio
(Differential)3.578 (for 2WD vehicle), 3.894 (for 4WD vehicle)
Lubrication Lubrication system Force feed system by oil pump
Cooling Cooling system Water-cooled
Fluid used
Equivalent of DEXRON
-III or DEXRON-IIE
Page 48 of 447
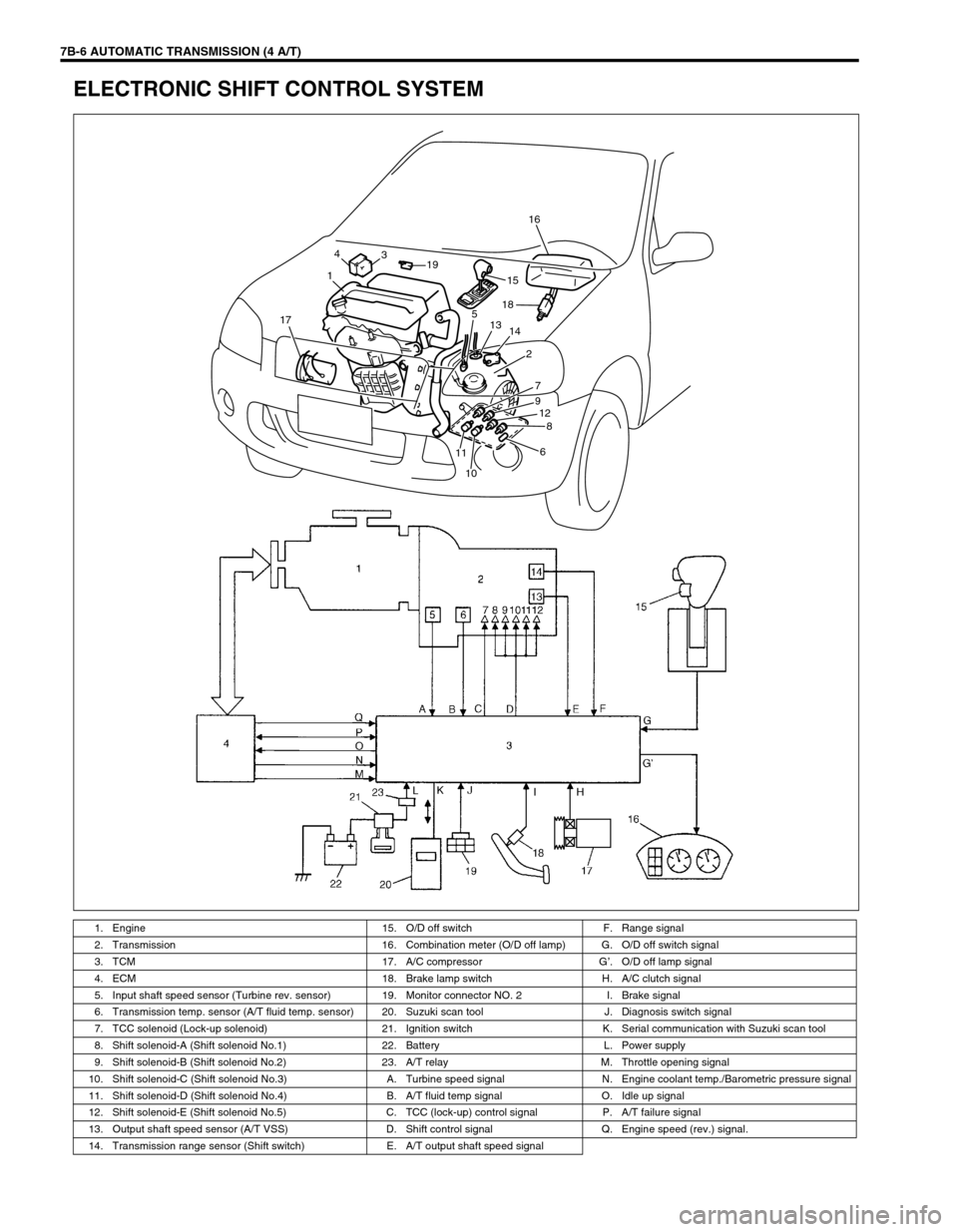
7B-6 AUTOMATIC TRANSMISSION (4 A/T)
ELECTRONIC SHIFT CONTROL SYSTEM
1. Engine 15. O/D off switch F. Range signal
2. Transmission 16. Combination meter (O/D off lamp) G. O/D off switch signal
3. TCM 17. A/C compressor G’. O/D off lamp signal
4. ECM 18. Brake lamp switch H. A/C clutch signal
5. Input shaft speed sensor (Turbine rev. sensor) 19. Monitor connector NO. 2 I. Brake signal
6. Transmission temp. sensor (A/T fluid temp. sensor) 20. Suzuki scan tool J. Diagnosis switch signal
7. TCC solenoid (Lock-up solenoid) 21. Ignition switch K. Serial communication with Suzuki scan tool
8. Shift solenoid-A (Shift solenoid No.1) 22. Battery L. Power supply
9. Shift solenoid-B (Shift solenoid No.2) 23. A/T relay M. Throttle opening signal
10. Shift solenoid-C (Shift solenoid No.3) A. Turbine speed signal N. Engine coolant temp./Barometric pressure signal
11. Shift solenoid-D (Shift solenoid No.4) B. A/T fluid temp signal O. Idle up signal
12. Shift solenoid-E (Shift solenoid No.5) C. TCC (lock-up) control signal P. A/T failure signal
13. Output shaft speed sensor (A/T VSS) D. Shift control signal Q. Engine speed (rev.) signal.
14. Transmission range sensor (Shift switch) E. A/T output shaft speed signal
14
3
19
15
1816
14 13 5
2
7
9
12
8
6
10 17
11
Page 49 of 447
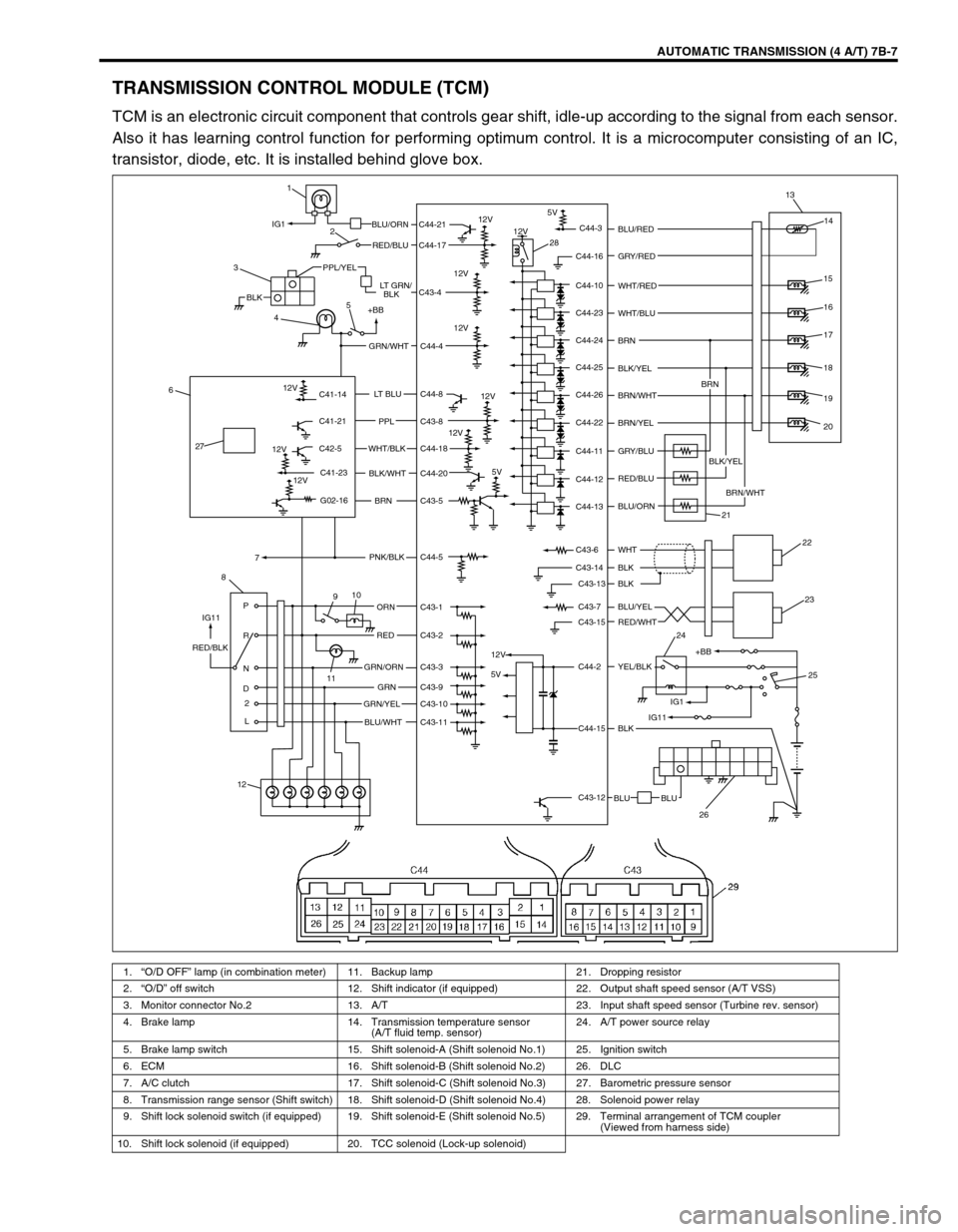
AUTOMATIC TRANSMISSION (4 A/T) 7B-7
TRANSMISSION CONTROL MODULE (TCM)
TCM is an electronic circuit component that controls gear shift, idle-up according to the signal from each sensor.
Also it has learning control function for performing optimum control. It is a microcomputer consisting of an IC,
transistor, diode, etc. It is installed behind glove box.
1.“O/D OFF” lamp (in combination meter) 11. Backup lamp 21. Dropping resistor
2.“O/D” off switch 12. Shift indicator (if equipped) 22. Output shaft speed sensor (A/T VSS)
3. Monitor connector No.2 13. A/T 23. Input shaft speed sensor (Turbine rev. sensor)
4. Brake lamp 14. Transmission temperature sensor
(A/T fluid temp. sensor)24. A/T power source relay
5. Brake lamp switch 15. Shift solenoid-A (Shift solenoid No.1) 25. Ignition switch
6. ECM 16. Shift solenoid-B (Shift solenoid No.2) 26. DLC
7. A/C clutch 17. Shift solenoid-C (Shift solenoid No.3) 27. Barometric pressure sensor
8. Transmission range sensor (Shift switch) 18. Shift solenoid-D (Shift solenoid No.4) 28. Solenoid power relay
9. Shift lock solenoid switch (if equipped) 19. Shift solenoid-E (Shift solenoid No.5) 29. Terminal arrangement of TCM coupler
(Viewed from harness side)
10. Shift lock solenoid (if equipped) 20. TCC solenoid (Lock-up solenoid)
C41-14
C41-21
C42-5
C41-23
G02-16
BLKBLKLT GRN/ RED/BLU BLU/ORN
PPL/YEL
3
45
+BB
GRN/WHT
LT BLU
PPL
WHT/BLK
BLK/WHT
BRN
PNK/BLK 6
7
8
C44-8
C43-8
C44-18
C44-20
C43-5
C44-5
910
ORN
RED
GRN/ORN RED/BLK
GRNC43-1
C43-2
C43-3
C43-9
C43-10
C43-11 GRN/YEL
BLU/WHT P
R
N
D
2
L11
12C44-21
C44-17
C43-4
C44-4
12V 12V
12V
12V
12V IG1
IG115V
5VC44-3
C44-16
C44-10
C44-23
C44-24
C44-25
C44-26
C44-22
C44-11
C44-12
C44-13
C43-6
C43-14
C43-13
C43-7
C43-15
C44-2
C44-15
C43-12
BLU BLUBLK
BLK BLK
BLU/YEL
YEL/BLK RED/WHT WHT BLU/ORN RED/BLU GRY/BLU
BLK/YEL WHT/BLU
BRN/WHT BRN/WHT BRN WHT/RED
BLK/YEL
BRN/YEL BLU/RED
GRY/RED13
14
15
16
17
19
20 BRN
21
22
23
+BB 24
25
26
12V
12V
12V
12V
18
12V
IG1
IG11
5V
1
2
28
27
Page 62 of 447
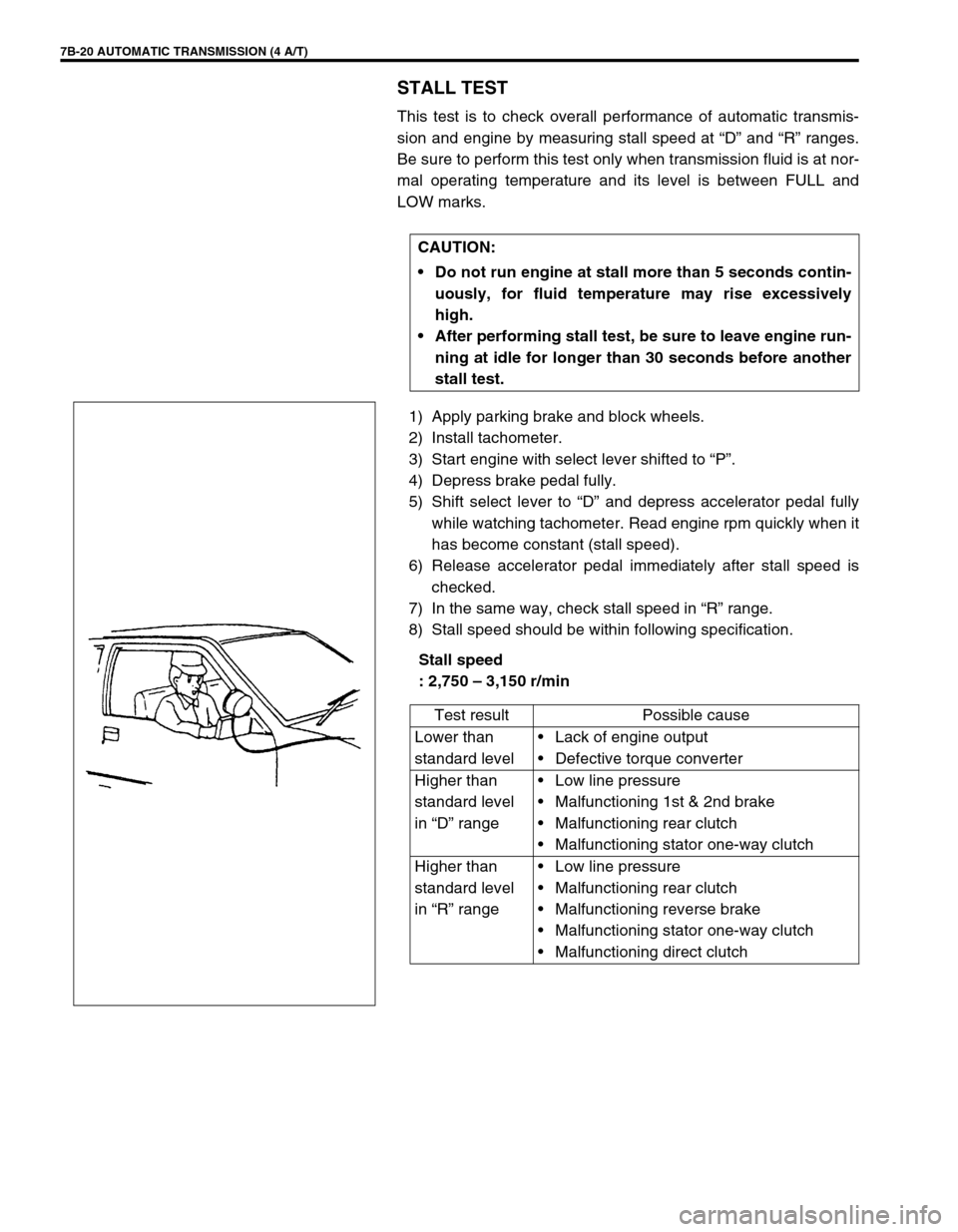
7B-20 AUTOMATIC TRANSMISSION (4 A/T)
STALL TEST
This test is to check overall performance of automatic transmis-
sion and engine by measuring stall speed at “D” and “R” ranges.
Be sure to perform this test only when transmission fluid is at nor-
mal operating temperature and its level is between FULL and
LOW marks.
1) Apply parking brake and block wheels.
2) Install tachometer.
3) Start engine with select lever shifted to “P”.
4) Depress brake pedal fully.
5) Shift select lever to “D” and depress accelerator pedal fully
while watching tachometer. Read engine rpm quickly when it
has become constant (stall speed).
6) Release accelerator pedal immediately after stall speed is
checked.
7) In the same way, check stall speed in “R” range.
8) Stall speed should be within following specification.
Stall speed
: 2,750 – 3,150 r/min CAUTION:
Do not run engine at stall more than 5 seconds contin-
uously, for fluid temperature may rise excessively
high.
After performing stall test, be sure to leave engine run-
ning at idle for longer than 30 seconds before another
stall test.
Test result Possible cause
Lower than
standard levelLack of engine output
Defective torque converter
Higher than
standard level
in “D” rangeLow line pressure
Malfunctioning 1st & 2nd brake
Malfunctioning rear clutch
Malfunctioning stator one-way clutch
Higher than
standard level
in “R” rangeLow line pressure
Malfunctioning rear clutch
Malfunctioning reverse brake
Malfunctioning stator one-way clutch
Malfunctioning direct clutch
Page 63 of 447

AUTOMATIC TRANSMISSION (4 A/T) 7B-21
TIME LAG TEST
This test is to check conditions of clutch, reverse brake and fluid
pressure. “Time lag” means time elapsed since select lever is
shifted with engine idling till shock is felt.
1) With chocks placed in front and behind front and rear wheels
respectively, depress brake pedal.
2) Start engine.
3) With stop watch ready, shift select lever from “N” to “D”
range and measure time from that moment till shock is felt.
4) Similarly measure time lag by shifting select lever from “N” to
“R” range.
Specification for time lag
“N”
→
→ → → “D” : Less than 1.0 sec.
“N”
→
→→ → “R” : Less than 1.2 sec.
NOTE:
Make sure that selector cable is properly adjusted.
When repeating this test, be sure to wait at least
minute after select lever is shifted back to “N” range.
Engine should be warmed up fully for this test.
Test result Possible cause
When “N” →
“D”
time lag exceeds specification.Low line pressure
Worn rear clutch
Worn 1st & 2nd brake
When “N” →
“R”
time lag exceeds specification.Low line pressure
Worn rear clutch
Worn direct clutch
Worn reverse brake
Page 64 of 447
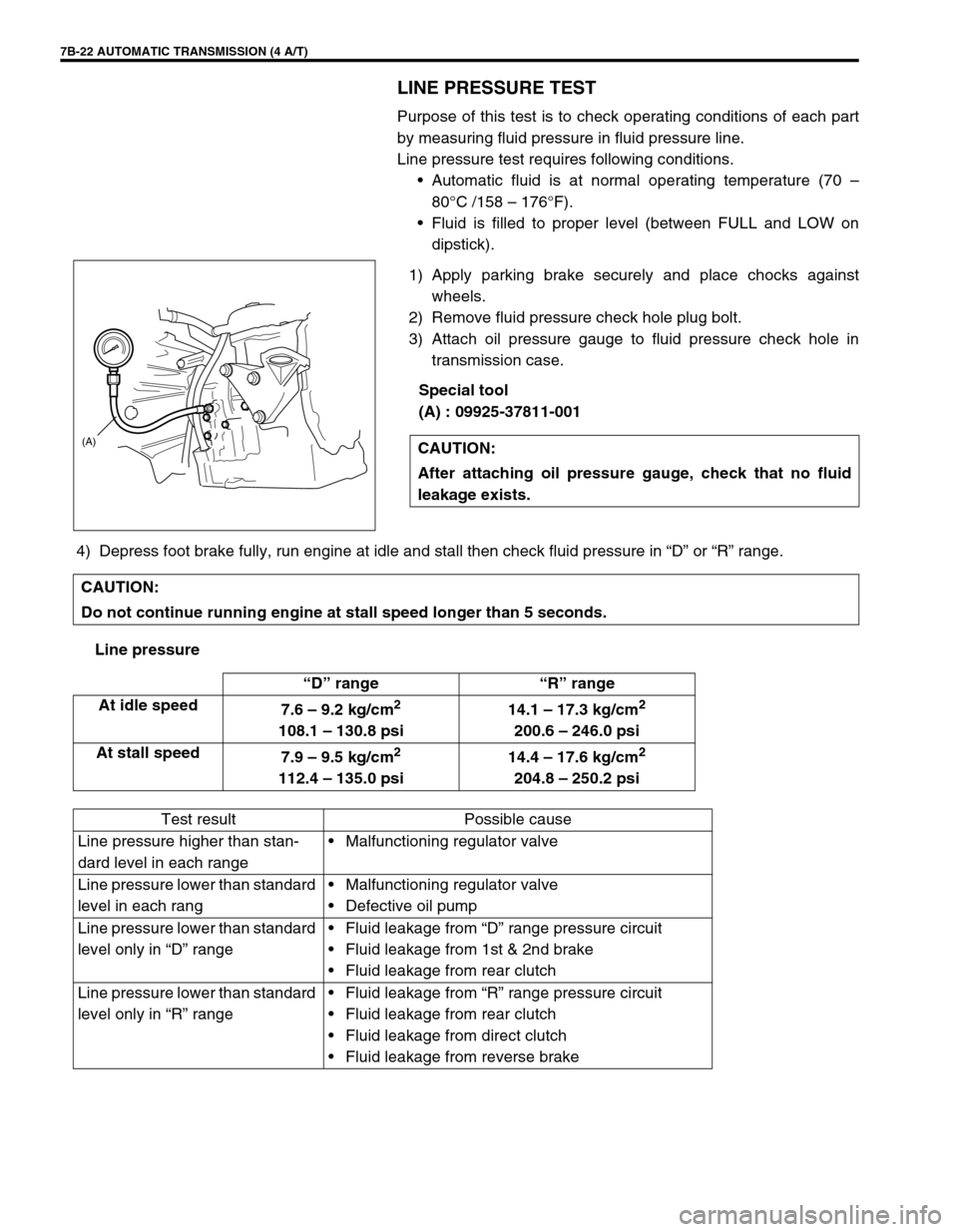
7B-22 AUTOMATIC TRANSMISSION (4 A/T)
LINE PRESSURE TEST
Purpose of this test is to check operating conditions of each part
by measuring fluid pressure in fluid pressure line.
Line pressure test requires following conditions.
Automatic fluid is at normal operating temperature (70 –
80°C /158 – 176°F).
Fluid is filled to proper level (between FULL and LOW on
dipstick).
1) Apply parking brake securely and place chocks against
wheels.
2) Remove fluid pressure check hole plug bolt.
3) Attach oil pressure gauge to fluid pressure check hole in
transmission case.
Special tool
(A) : 09925-37811-001
4) Depress foot brake fully, run engine at idle and stall then check fluid pressure in “D” or “R” range.
Line pressureCAUTION:
After attaching oil pressure gauge, check that no fluid
leakage exists.
(A)
CAUTION:
Do not continue running engine at stall speed longer than 5 seconds.
“D” range “R” range
At idle speed
7.6 – 9.2 kg/cm
2
108.1 – 130.8 psi14.1 – 17.3 kg/cm
2
200.6 – 246.0 psi
At stall speed
7.9 – 9.5 kg/cm
2
112.4 – 135.0 psi14.4 – 17.6 kg/cm
2
204.8 – 250.2 psi
Test result Possible cause
Line pressure higher than stan-
dard level in each rangeMalfunctioning regulator valve
Line pressure lower than standard
level in each rangMalfunctioning regulator valve
Defective oil pump
Line pressure lower than standard
level only in “D” rangeFluid leakage from “D” range pressure circuit
Fluid leakage from 1st & 2nd brake
Fluid leakage from rear clutch
Line pressure lower than standard
level only in “R” rangeFluid leakage from “R” range pressure circuit
Fluid leakage from rear clutch
Fluid leakage from direct clutch
Fluid leakage from reverse brake
Page 97 of 447
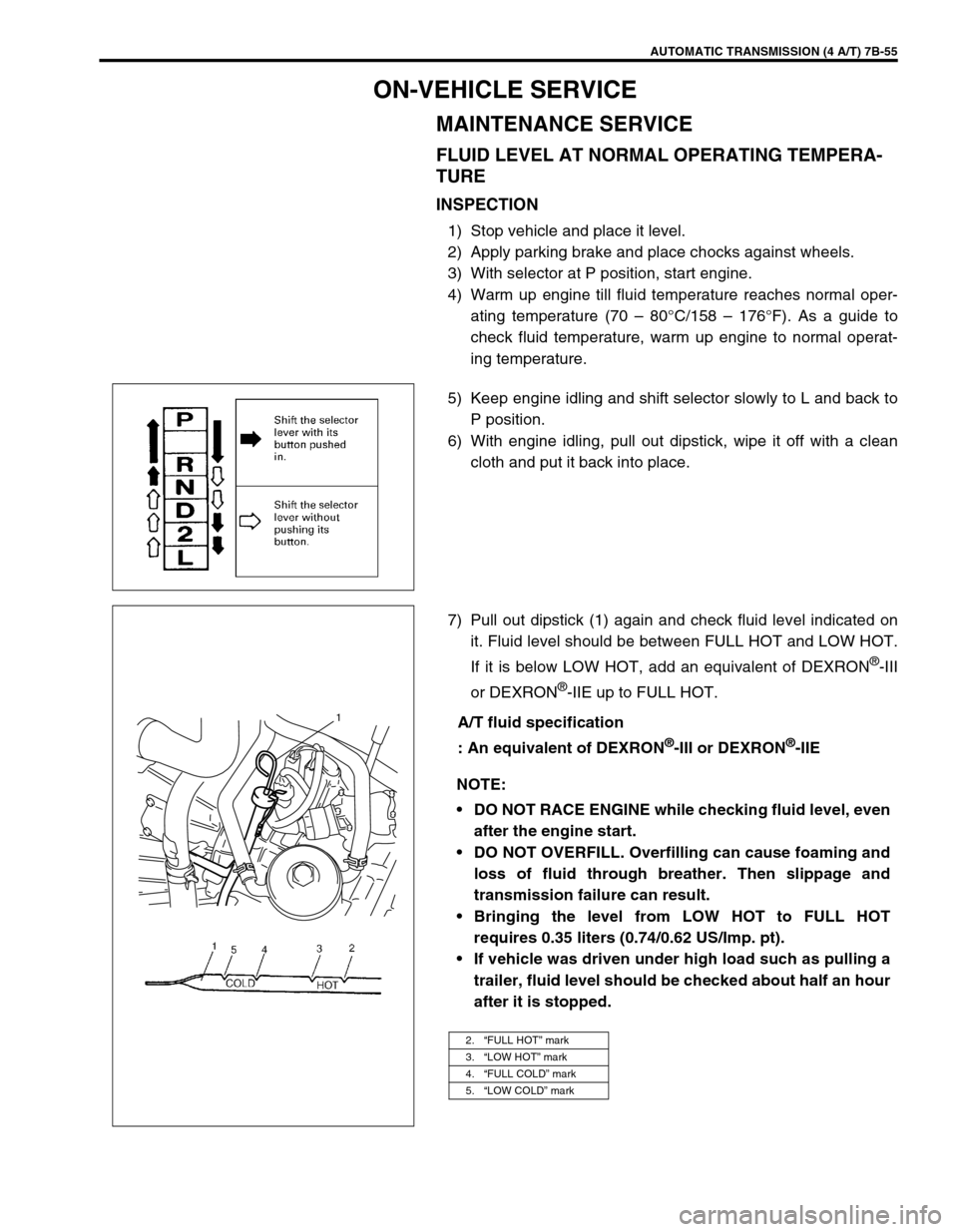
AUTOMATIC TRANSMISSION (4 A/T) 7B-55
ON-VEHICLE SERVICE
MAINTENANCE SERVICE
FLUID LEVEL AT NORMAL OPERATING TEMPERA-
TURE
INSPECTION
1) Stop vehicle and place it level.
2) Apply parking brake and place chocks against wheels.
3) With selector at P position, start engine.
4) Warm up engine till fluid temperature reaches normal oper-
ating temperature (70 – 80°C/158 – 176°F). As a guide to
check fluid temperature, warm up engine to normal operat-
ing temperature.
5) Keep engine idling and shift selector slowly to L and back to
P position.
6) With engine idling, pull out dipstick, wipe it off with a clean
cloth and put it back into place.
7) Pull out dipstick (1) again and check fluid level indicated on
it. Fluid level should be between FULL HOT and LOW HOT.
If it is below LOW HOT, add an equivalent of DEXRON
®-III
or DEXRON
®-IIE up to FULL HOT.
A/T fluid specification
: An equivalent of DEXRON
®-III or DEXRON®-IIE
NOTE:
DO NOT RACE ENGINE while checking fluid level, even
after the engine start.
DO NOT OVERFILL. Overfilling can cause foaming and
loss of fluid through breather. Then slippage and
transmission failure can result.
Bringing the level from LOW HOT to FULL HOT
requires 0.35 liters (0.74/0.62 US/Imp. pt).
If vehicle was driven under high load such as pulling a
trailer, fluid level should be checked about half an hour
after it is stopped.
2.“FULL HOT” mark
3.“LOW HOT” mark
4.“FULL COLD” mark
5.“LOW COLD” mark
1
Page 129 of 447
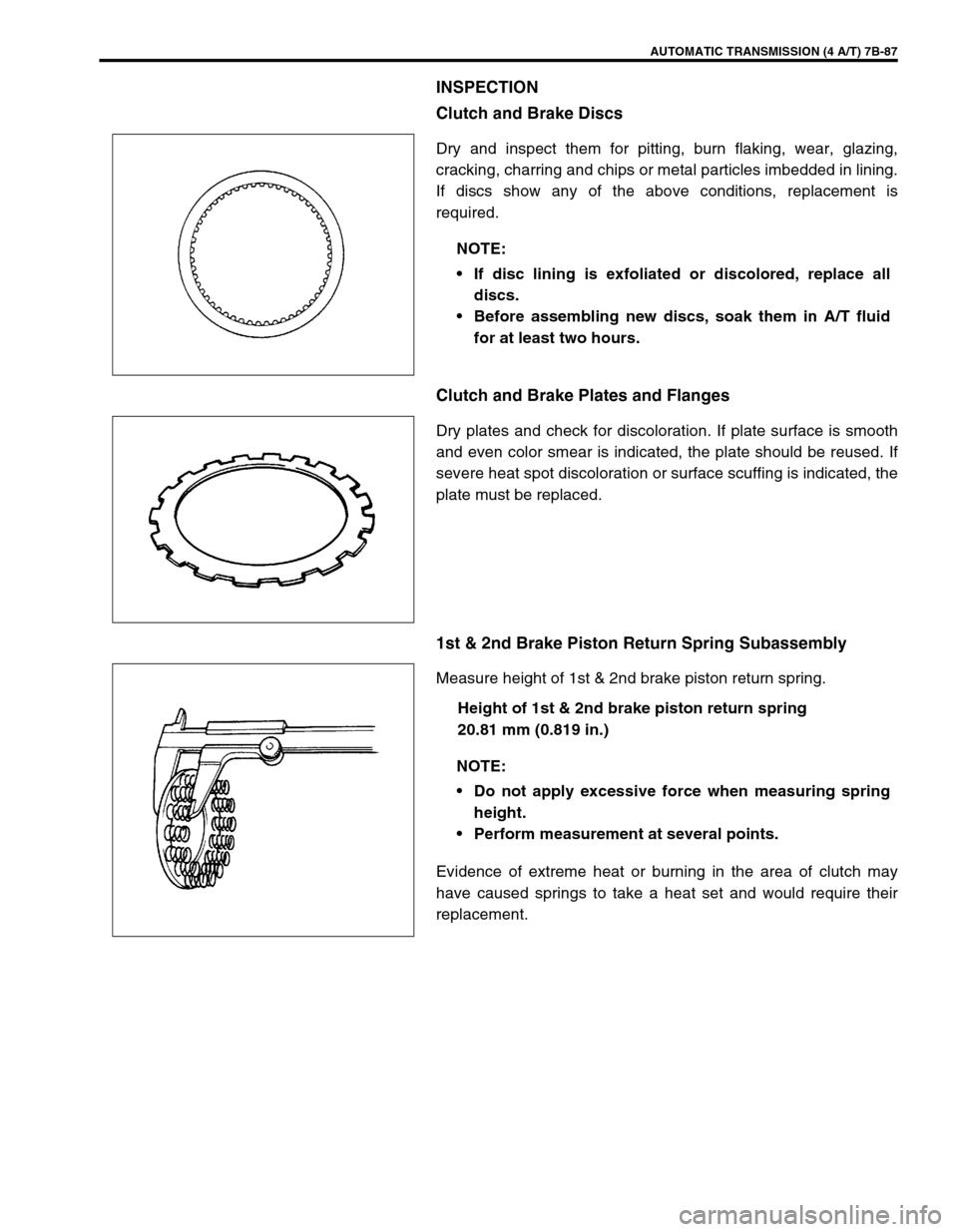
AUTOMATIC TRANSMISSION (4 A/T) 7B-87
INSPECTION
Clutch and Brake Discs
Dry and inspect them for pitting, burn flaking, wear, glazing,
cracking, charring and chips or metal particles imbedded in lining.
If discs show any of the above conditions, replacement is
required.
Clutch and Brake Plates and Flanges
Dry plates and check for discoloration. If plate surface is smooth
and even color smear is indicated, the plate should be reused. If
severe heat spot discoloration or surface scuffing is indicated, the
plate must be replaced.
1st & 2nd Brake Piston Return Spring Subassembly
Measure height of 1st & 2nd brake piston return spring.
Height of 1st & 2nd brake piston return spring
20.81 mm (0.819 in.)
Evidence of extreme heat or burning in the area of clutch may
have caused springs to take a heat set and would require their
replacement.NOTE:
If disc lining is exfoliated or discolored, replace all
discs.
Before assembling new discs, soak them in A/T fluid
for at least two hours.
NOTE:
Do not apply excessive force when measuring spring
height.
Perform measurement at several points.
Page 130 of 447
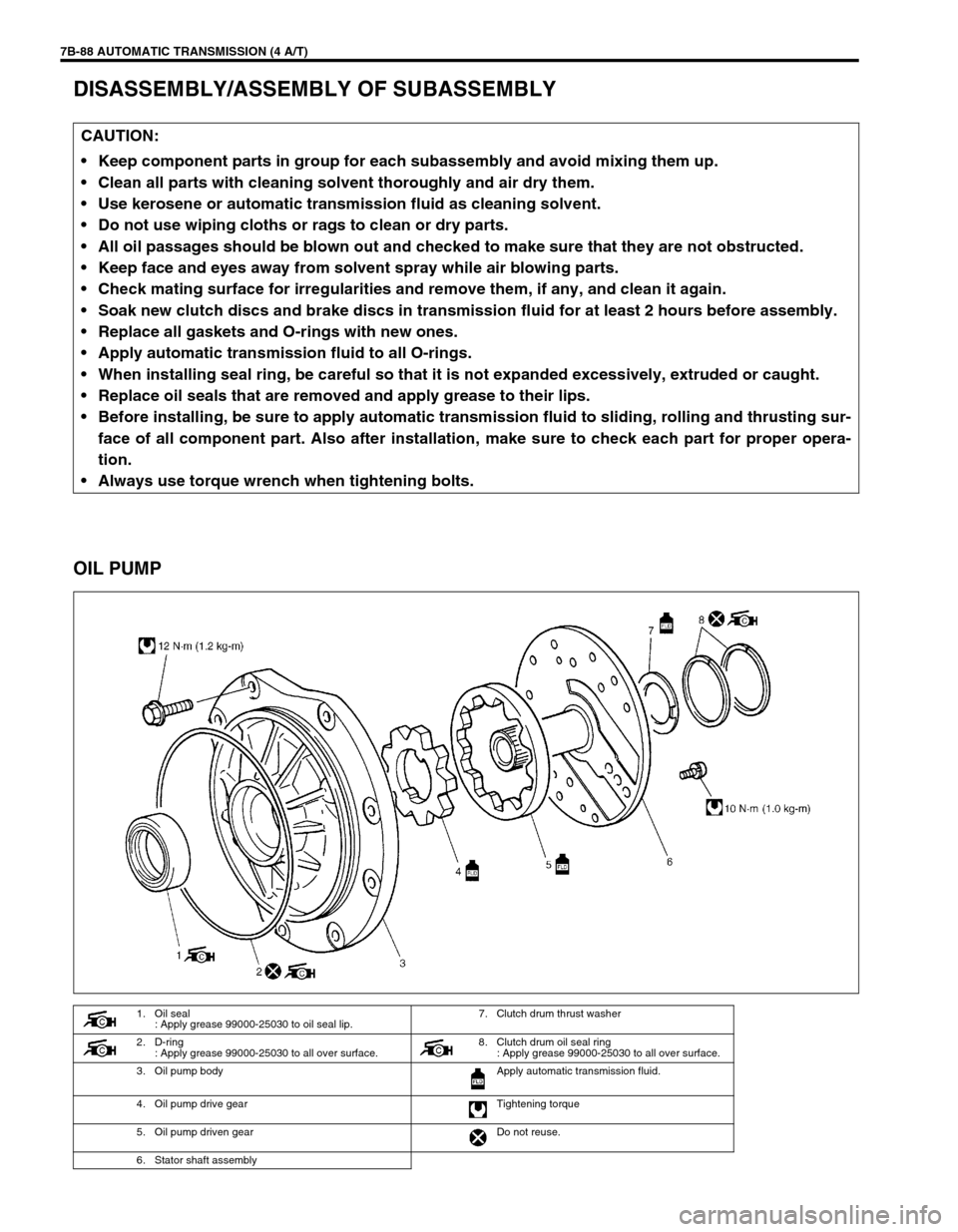
7B-88 AUTOMATIC TRANSMISSION (4 A/T)
DISASSEMBLY/ASSEMBLY OF SUBASSEMBLY
OIL PUMP
CAUTION:
Keep component parts in group for each subassembly and avoid mixing them up.
Clean all parts with cleaning solvent thoroughly and air dry them.
Use kerosene or automatic transmission fluid as cleaning solvent.
Do not use wiping cloths or rags to clean or dry parts.
All oil passages should be blown out and checked to make sure that they are not obstructed.
Keep face and eyes away from solvent spray while air blowing parts.
Check mating surface for irregularities and remove them, if any, and clean it again.
Soak new clutch discs and brake discs in transmission fluid for at least 2 hours before assembly.
Replace all gaskets and O-rings with new ones.
Apply automatic transmission fluid to all O-rings.
When installing seal ring, be careful so that it is not expanded excessively, extruded or caught.
Replace oil seals that are removed and apply grease to their lips.
Before installing, be sure to apply automatic transmission fluid to sliding, rolling and thrusting sur-
face of all component part. Also after installation, make sure to check each part for proper opera-
tion.
Always use torque wrench when tightening bolts.
1. Oil seal
: Apply grease 99000-25030 to oil seal lip.7. Clutch drum thrust washer
2. D-ring
: Apply grease 99000-25030 to all over surface. 8. Clutch drum oil seal ring
: Apply grease 99000-25030 to all over surface.
3. Oil pump body Apply automatic transmission fluid.
4. Oil pump drive gear Tightening torque
5. Oil pump driven gear Do not reuse.
6. Stator shaft assembly