Display SUZUKI SX4 2006 1.G Service Owner's Guide
[x] Cancel search | Manufacturer: SUZUKI, Model Year: 2006, Model line: SX4, Model: SUZUKI SX4 2006 1.GPages: 1556, PDF Size: 37.31 MB
Page 211 of 1556
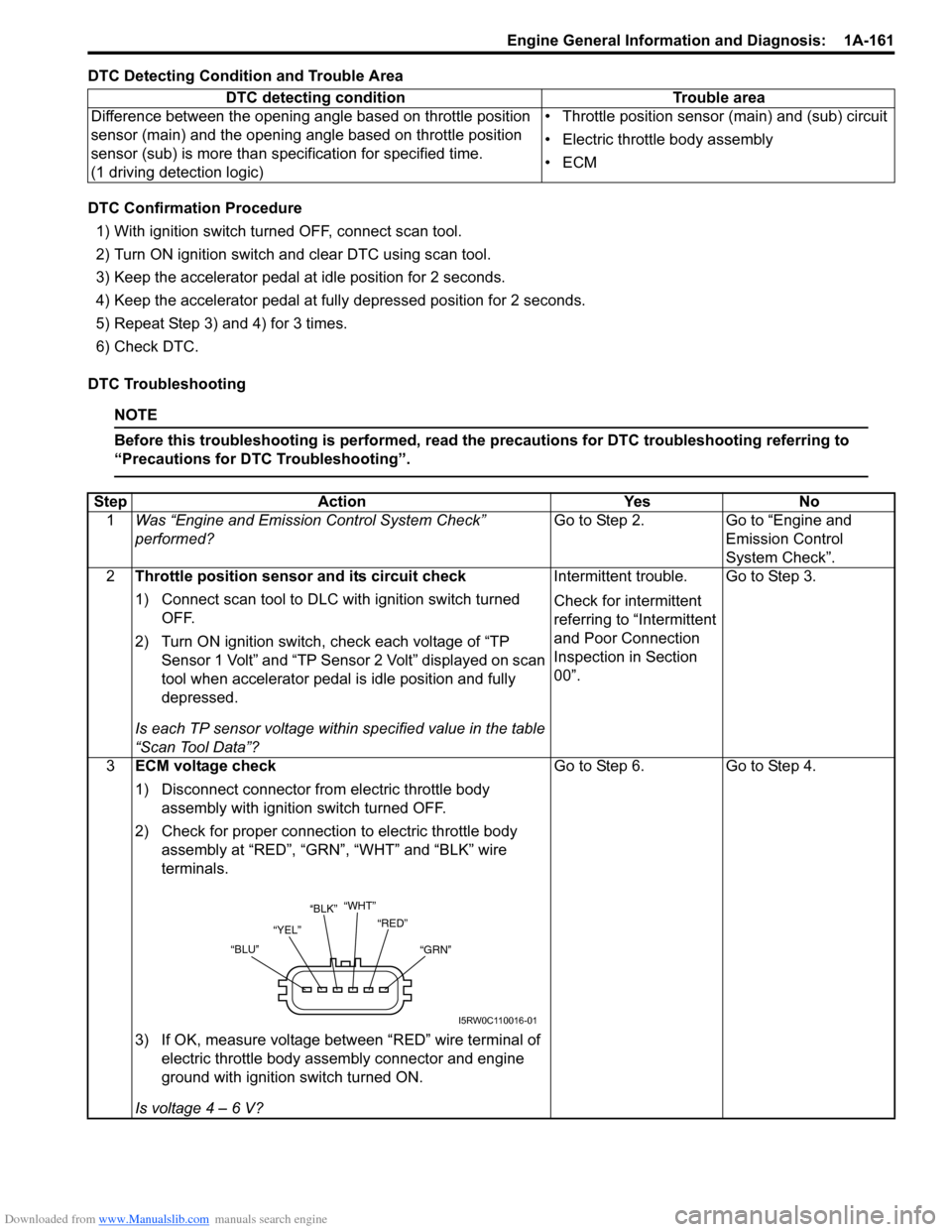
Downloaded from www.Manualslib.com manuals search engine Engine General Information and Diagnosis: 1A-161
DTC Detecting Condition and Trouble Area
DTC Confirmation Procedure
1) With ignition switch turned OFF, connect scan tool.
2) Turn ON ignition switch and clear DTC using scan tool.
3) Keep the accelerator pedal at idle position for 2 seconds.
4) Keep the accelerator pedal at fully depressed position for 2 seconds.
5) Repeat Step 3) and 4) for 3 times.
6) Check DTC.
DTC Troubleshooting
NOTE
Before this troubleshooting is performed, read the precautions for DTC troubleshooting referring to
“Precautions for DTC Troubleshooting”.
DTC detecting condition Trouble area
Difference between the opening angle based on throttle position
sensor (main) and the opening angle based on throttle position
sensor (sub) is more than specification for specified time.
(1 driving detection logic)• Throttle position sensor (main) and (sub) circuit
• Electric throttle body assembly
•ECM
Step Action Yes No
1Was “Engine and Emission Control System Check”
performed?Go to Step 2. Go to “Engine and
Emission Control
System Check”.
2Throttle position sensor and its circuit check
1) Connect scan tool to DLC with ignition switch turned
OFF.
2) Turn ON ignition switch, check each voltage of “TP
Sensor 1 Volt” and “TP Sensor 2 Volt” displayed on scan
tool when accelerator pedal is idle position and fully
depressed.
Is each TP sensor voltage within specified value in the table
“Scan Tool Data”?Intermittent trouble.
Check for intermittent
referring to “Intermittent
and Poor Connection
Inspection in Section
00”.Go to Step 3.
3ECM voltage check
1) Disconnect connector from electric throttle body
assembly with ignition switch turned OFF.
2) Check for proper connection to electric throttle body
assembly at “RED”, “GRN”, “WHT” and “BLK” wire
terminals.
3) If OK, measure voltage between “RED” wire terminal of
electric throttle body assembly connector and engine
ground with ignition switch turned ON.
Is voltage 4 – 6 V?Go to Step 6. Go to Step 4.
“WHT”
“YEL”“RED”
“GRN” “BLU”“BLK”
I5RW0C110016-01
Page 214 of 1556
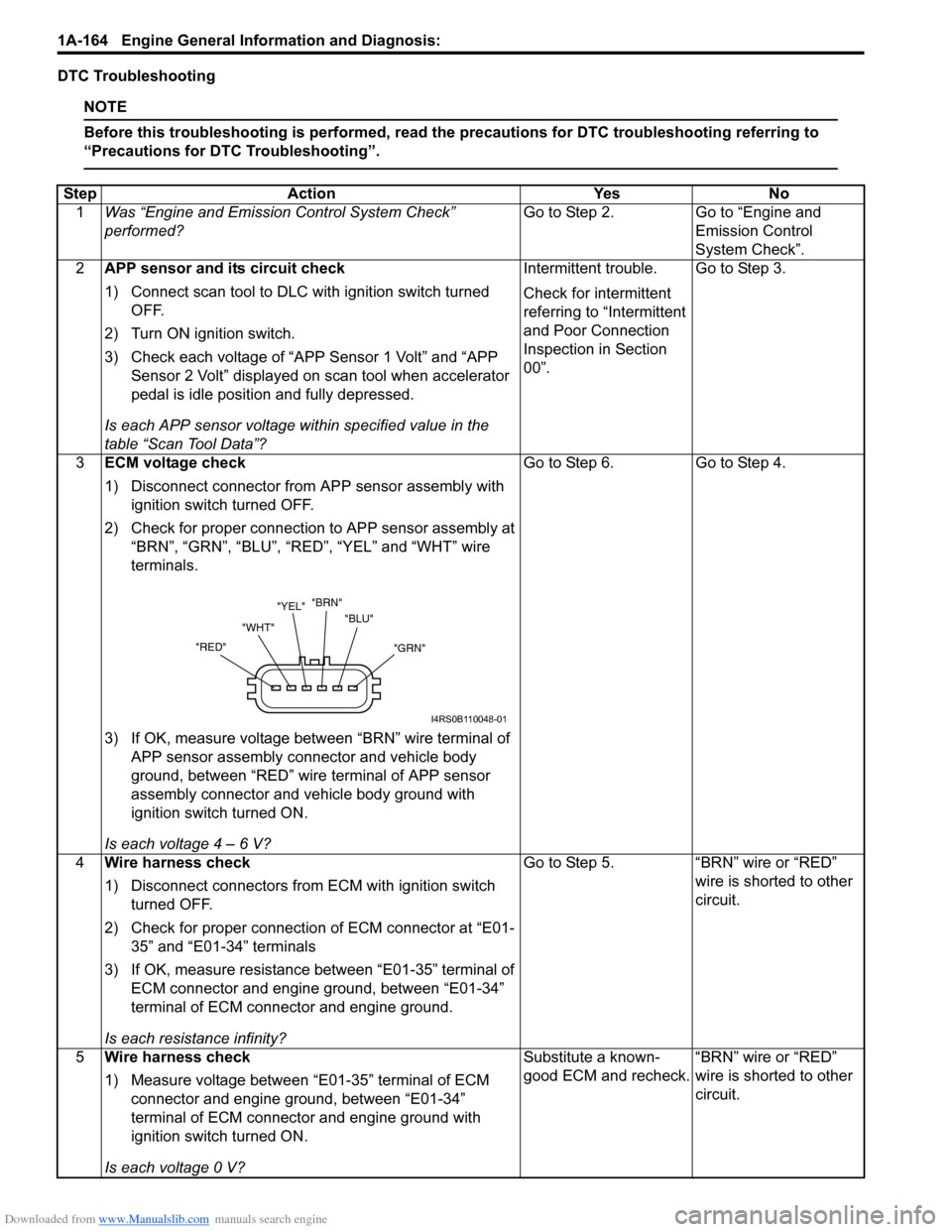
Downloaded from www.Manualslib.com manuals search engine 1A-164 Engine General Information and Diagnosis:
DTC Troubleshooting
NOTE
Before this troubleshooting is performed, read the precautions for DTC troubleshooting referring to
“Precautions for DTC Troubleshooting”.
Step Action Yes No
1Was “Engine and Emission Control System Check”
performed?Go to Step 2. Go to “Engine and
Emission Control
System Check”.
2APP sensor and its circuit check
1) Connect scan tool to DLC with ignition switch turned
OFF.
2) Turn ON ignition switch.
3) Check each voltage of “APP Sensor 1 Volt” and “APP
Sensor 2 Volt” displayed on scan tool when accelerator
pedal is idle position and fully depressed.
Is each APP sensor voltage within specified value in the
table “Scan Tool Data”?Intermittent trouble.
Check for intermittent
referring to “Intermittent
and Poor Connection
Inspection in Section
00”.Go to Step 3.
3ECM voltage check
1) Disconnect connector from APP sensor assembly with
ignition switch turned OFF.
2) Check for proper connection to APP sensor assembly at
“BRN”, “GRN”, “BLU”, “RED”, “YEL” and “WHT” wire
terminals.
3) If OK, measure voltage between “BRN” wire terminal of
APP sensor assembly connector and vehicle body
ground, between “RED” wire terminal of APP sensor
assembly connector and vehicle body ground with
ignition switch turned ON.
Is each voltage 4 – 6 V?Go to Step 6. Go to Step 4.
4Wire harness check
1) Disconnect connectors from ECM with ignition switch
turned OFF.
2) Check for proper connection of ECM connector at “E01-
35” and “E01-34” terminals
3) If OK, measure resistance between “E01-35” terminal of
ECM connector and engine ground, between “E01-34”
terminal of ECM connector and engine ground.
Is each resistance infinity?Go to Step 5. “BRN” wire or “RED”
wire is shorted to other
circuit.
5Wire harness check
1) Measure voltage between “E01-35” terminal of ECM
connector and engine ground, between “E01-34”
terminal of ECM connector and engine ground with
ignition switch turned ON.
Is each voltage 0 V?Substitute a known-
good ECM and recheck.“BRN” wire or “RED”
wire is shorted to other
circuit.
"GRN" "BLU" "BRN"
"YEL"
"WHT"
"RED"
I4RS0B110048-01
Page 217 of 1556
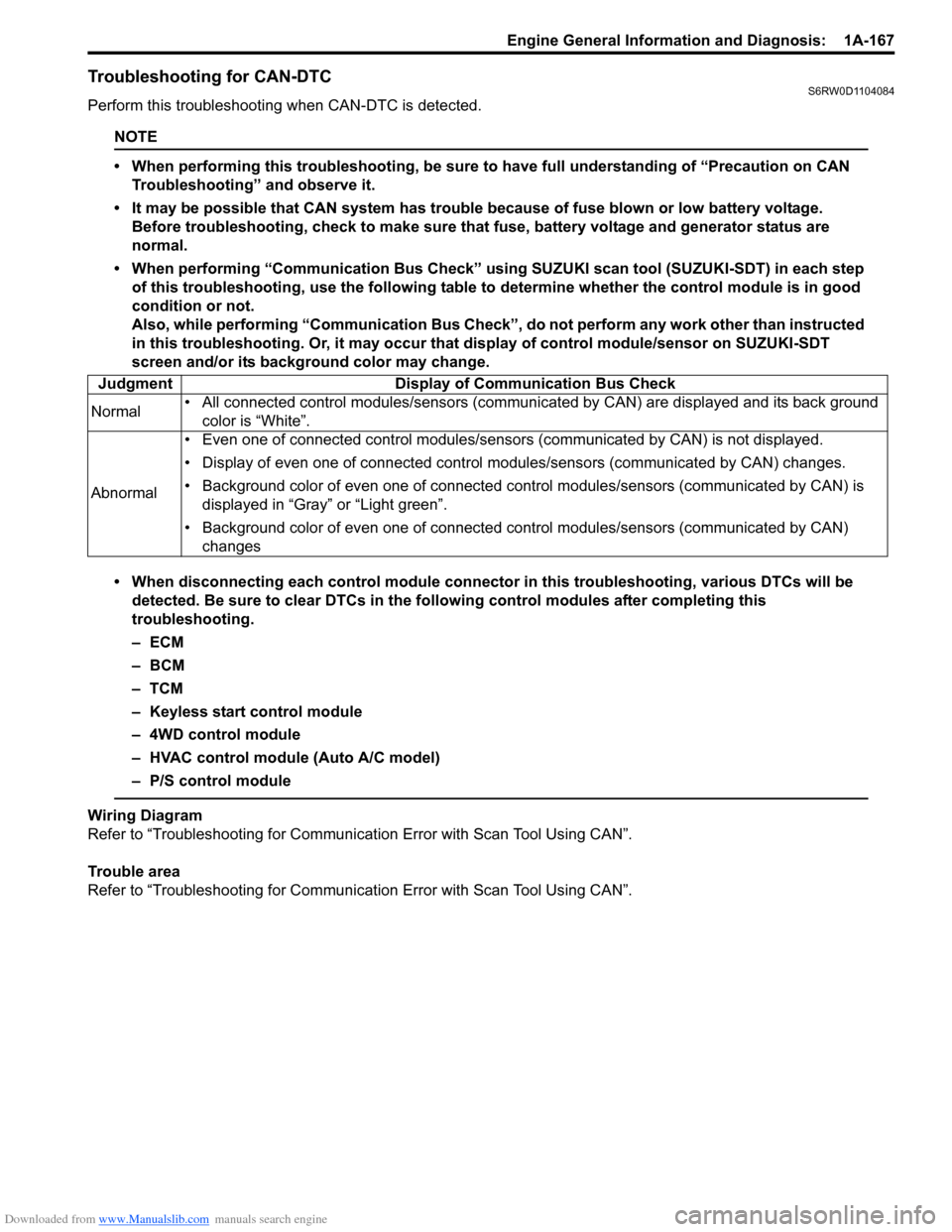
Downloaded from www.Manualslib.com manuals search engine Engine General Information and Diagnosis: 1A-167
Troubleshooting for CAN-DTCS6RW0D1104084
Perform this troubleshooting when CAN-DTC is detected.
NOTE
• When performing this troubleshooting, be sure to have full understanding of “Precaution on CAN
Troubleshooting” and observe it.
• It may be possible that CAN system has trouble because of fuse blown or low battery voltage.
Before troubleshooting, check to make sure that fuse, battery voltage and generator status are
normal.
• When performing “Communication Bus Check” using SUZUKI scan tool (SUZUKI-SDT) in each step
of this troubleshooting, use the following table to determine whether the control module is in good
condition or not.
Also, while performing “Communication Bus Check”, do not perform any work other than instructed
in this troubleshooting. Or, it may occur that display of control module/sensor on SUZUKI-SDT
screen and/or its background color may change.
• When disconnecting each control module connector in this troubleshooting, various DTCs will be
detected. Be sure to clear DTCs in the following control modules after completing this
troubleshooting.
–ECM
– BCM
–TCM
– Keyless start control module
– 4WD control module
– HVAC control module (Auto A/C model)
– P/S control module
Wiring Diagram
Refer to “Troubleshooting for Communication Error with Scan Tool Using CAN”.
Trouble area
Refer to “Troubleshooting for Communication Error with Scan Tool Using CAN”. Judgment Display of Communication Bus Check
Normal• All connected control modules/sensors (communicated by CAN) are displayed and its back ground
color is “White”.
Abnormal• Even one of connected control modules/sensors (communicated by CAN) is not displayed.
• Display of even one of connected control modules/sensors (communicated by CAN) changes.
• Background color of even one of connected control modules/sensors (communicated by CAN) is
displayed in “Gray” or “Light green”.
• Background color of even one of connected control modules/sensors (communicated by CAN)
changes
Page 219 of 1556
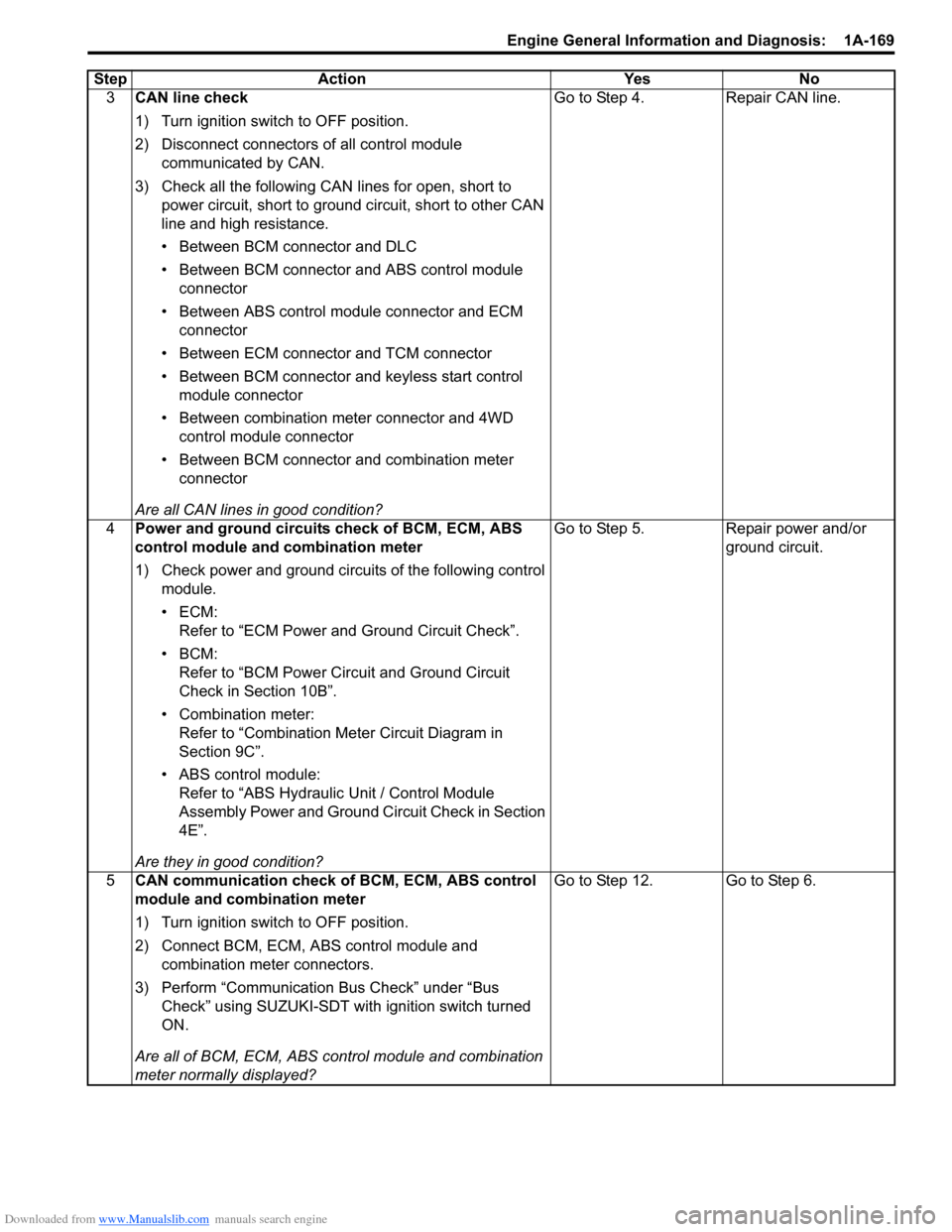
Downloaded from www.Manualslib.com manuals search engine Engine General Information and Diagnosis: 1A-169
3CAN line check
1) Turn ignition switch to OFF position.
2) Disconnect connectors of all control module
communicated by CAN.
3) Check all the following CAN lines for open, short to
power circuit, short to ground circuit, short to other CAN
line and high resistance.
• Between BCM connector and DLC
• Between BCM connector and ABS control module
connector
• Between ABS control module connector and ECM
connector
• Between ECM connector and TCM connector
• Between BCM connector and keyless start control
module connector
• Between combination meter connector and 4WD
control module connector
• Between BCM connector and combination meter
connector
Are all CAN lines in good condition?Go to Step 4. Repair CAN line.
4Power and ground circuits check of BCM, ECM, ABS
control module and combination meter
1) Check power and ground circuits of the following control
module.
•ECM:
Refer to “ECM Power and Ground Circuit Check”.
•BCM:
Refer to “BCM Power Circuit and Ground Circuit
Check in Section 10B”.
• Combination meter:
Refer to “Combination Meter Circuit Diagram in
Section 9C”.
• ABS control module:
Refer to “ABS Hydraulic Unit / Control Module
Assembly Power and Ground Circuit Check in Section
4E”.
Are they in good condition?Go to Step 5. Repair power and/or
ground circuit.
5CAN communication check of BCM, ECM, ABS control
module and combination meter
1) Turn ignition switch to OFF position.
2) Connect BCM, ECM, ABS control module and
combination meter connectors.
3) Perform “Communication Bus Check” under “Bus
Check” using SUZUKI-SDT with ignition switch turned
ON.
Are all of BCM, ECM, ABS control module and combination
meter normally displayed?Go to Step 12. Go to Step 6. Step Action Yes No
Page 221 of 1556
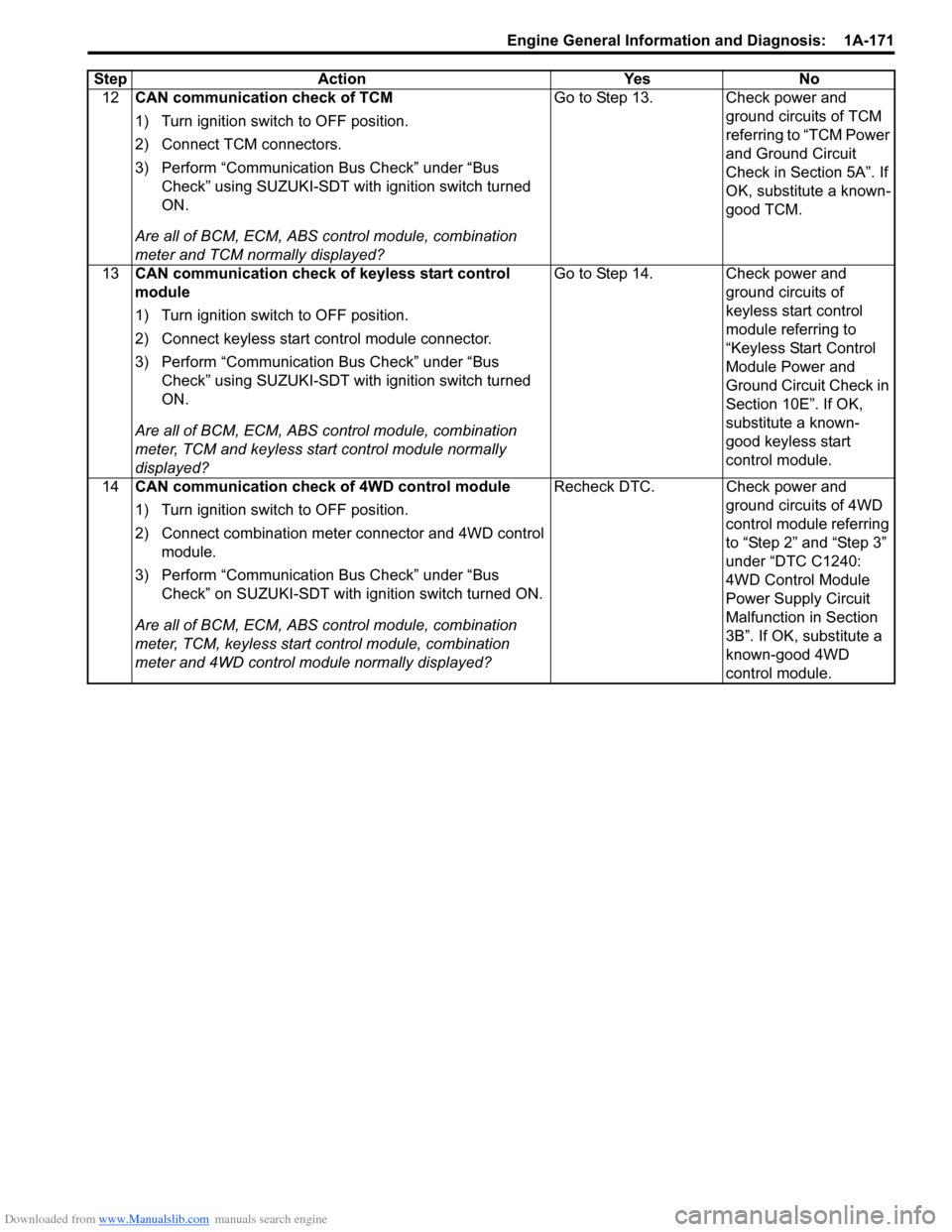
Downloaded from www.Manualslib.com manuals search engine Engine General Information and Diagnosis: 1A-171
12CAN communication check of TCM
1) Turn ignition switch to OFF position.
2) Connect TCM connectors.
3) Perform “Communication Bus Check” under “Bus
Check” using SUZUKI-SDT with ignition switch turned
ON.
Are all of BCM, ECM, ABS control module, combination
meter and TCM normally displayed?Go to Step 13. Check power and
ground circuits of TCM
referring to “TCM Power
and Ground Circuit
Check in Section 5A”. If
OK, substitute a known-
good TCM.
13CAN communication check of keyless start control
module
1) Turn ignition switch to OFF position.
2) Connect keyless start control module connector.
3) Perform “Communication Bus Check” under “Bus
Check” using SUZUKI-SDT with ignition switch turned
ON.
Are all of BCM, ECM, ABS control module, combination
meter, TCM and keyless start control module normally
displayed?Go to Step 14. Check power and
ground circuits of
keyless start control
module referring to
“Keyless Start Control
Module Power and
Ground Circuit Check in
Section 10E”. If OK,
substitute a known-
good keyless start
control module.
14CAN communication check of 4WD control module
1) Turn ignition switch to OFF position.
2) Connect combination meter connector and 4WD control
module.
3) Perform “Communication Bus Check” under “Bus
Check” on SUZUKI-SDT with ignition switch turned ON.
Are all of BCM, ECM, ABS control module, combination
meter, TCM, keyless start control module, combination
meter and 4WD control module normally displayed?Recheck DTC. Check power and
ground circuits of 4WD
control module referring
to “Step 2” and “Step 3”
under “DTC C1240:
4WD Control Module
Power Supply Circuit
Malfunction in Section
3B”. If OK, substitute a
known-good 4WD
control module. Step Action Yes No
Page 224 of 1556
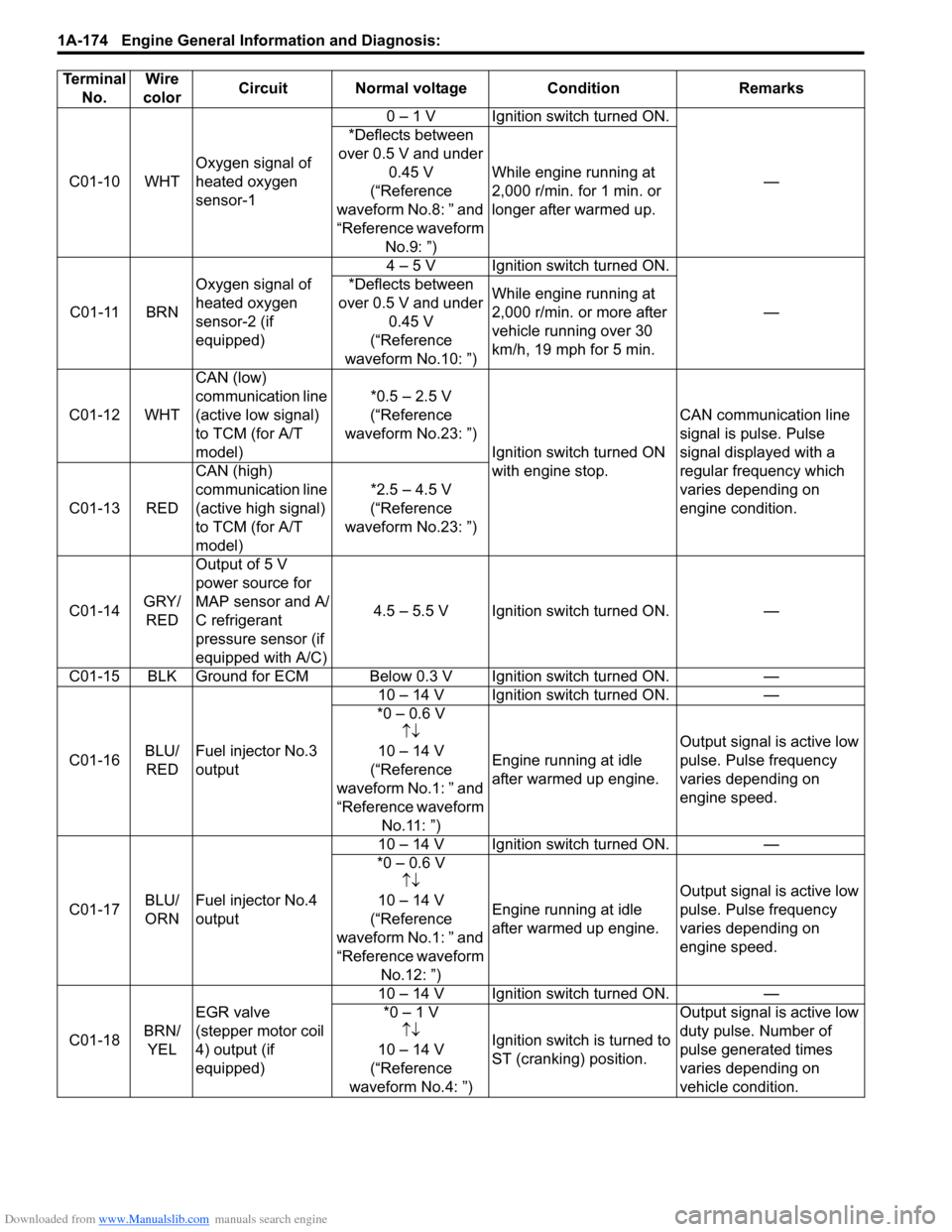
Downloaded from www.Manualslib.com manuals search engine 1A-174 Engine General Information and Diagnosis:
C01-10 WHTOxygen signal of
heated oxygen
sensor-10 – 1 V Ignition switch turned ON.
— *Deflects between
over 0.5 V and under
0.45 V
(“Reference
waveform No.8: ” and
“Reference waveform
No.9: ”)While engine running at
2,000 r/min. for 1 min. or
longer after warmed up.
C01-11 BRNOxygen signal of
heated oxygen
sensor-2 (if
equipped)4 – 5 V Ignition switch turned ON.
— *Deflects between
over 0.5 V and under
0.45 V
(“Reference
waveform No.10: ”)While engine running at
2,000 r/min. or more after
vehicle running over 30
km/h, 19 mph for 5 min.
C01-12 WHTCAN (low)
communication line
(active low signal)
to TCM (for A/T
model)*0.5 – 2.5 V
(“Reference
waveform No.23: ”)
Ignition switch turned ON
with engine stop.CAN communication line
signal is pulse. Pulse
signal displayed with a
regular frequency which
varies depending on
engine condition. C01-13 REDCAN (high)
communication line
(active high signal)
to TCM (for A/T
model)*2.5 – 4.5 V
(“Reference
waveform No.23: ”)
C01-14GRY/
REDOutput of 5 V
power source for
MAP sensor and A/
C refrigerant
pressure sensor (if
equipped with A/C)4.5 – 5.5 V Ignition switch turned ON. —
C01-15 BLK Ground for ECM Below 0.3 V Ignition switch turned ON. —
C01-16BLU/
REDFuel injector No.3
output10 – 14 V Ignition switch turned ON. —
*0 – 0.6 V
↑↓
10 – 14 V
(“Reference
waveform No.1: ” and
“Reference waveform
No.11: ”)Engine running at idle
after warmed up engine.Output signal is active low
pulse. Pulse frequency
varies depending on
engine speed.
C01-17BLU/
ORNFuel injector No.4
output10 – 14 V Ignition switch turned ON. —
*0 – 0.6 V
↑↓
10 – 14 V
(“Reference
waveform No.1: ” and
“Reference waveform
No.12: ”)Engine running at idle
after warmed up engine.Output signal is active low
pulse. Pulse frequency
varies depending on
engine speed.
C01-18BRN/
YELEGR valve
(stepper motor coil
4) output (if
equipped)10 – 14 V Ignition switch turned ON. —
*0 – 1 V
↑↓
10 – 14 V
(“Reference
waveform No.4: ”)Ignition switch is turned to
ST (cranking) position.Output signal is active low
duty pulse. Number of
pulse generated times
varies depending on
vehicle condition. Terminal
No.Wire
colorCircuit Normal voltage Condition Remarks
Page 227 of 1556
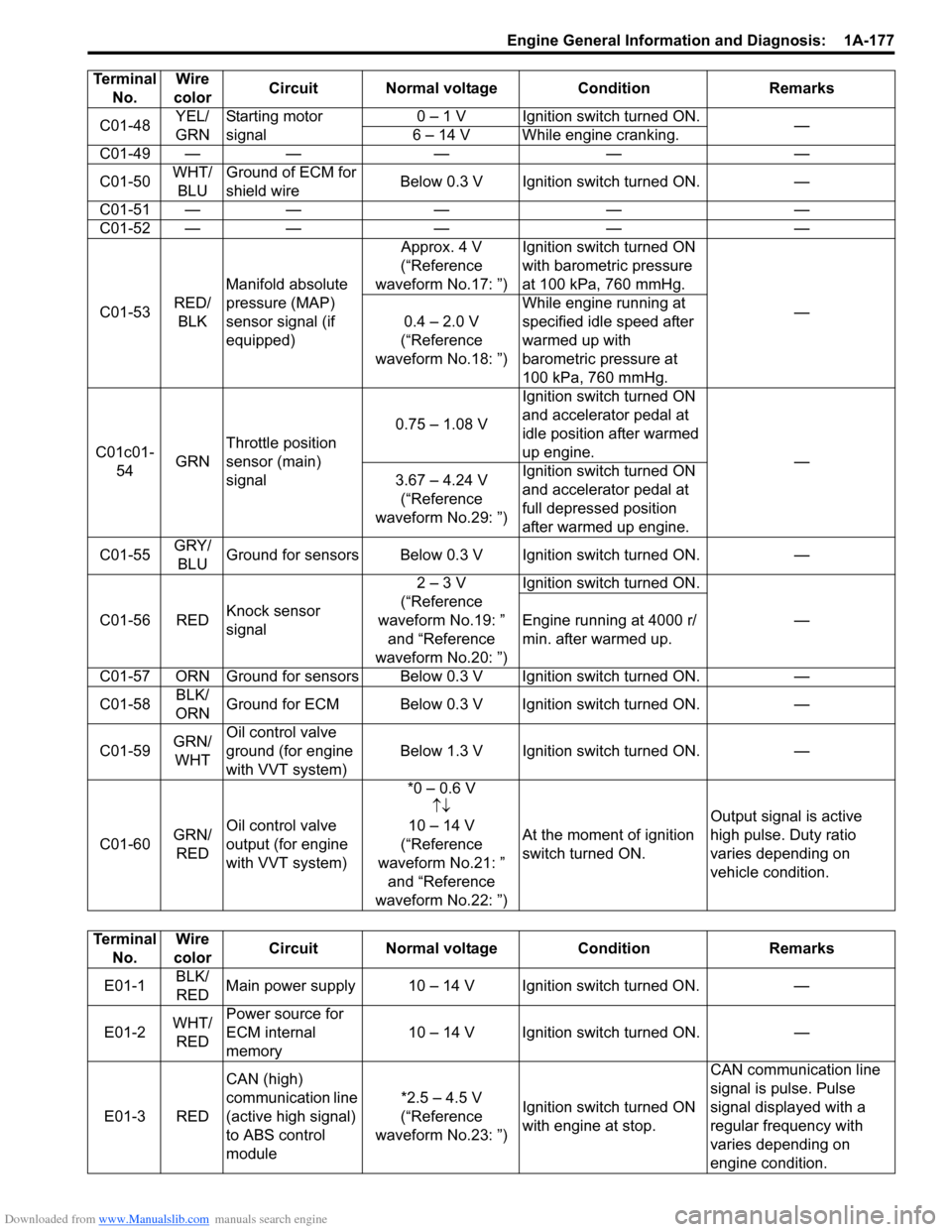
Downloaded from www.Manualslib.com manuals search engine Engine General Information and Diagnosis: 1A-177
C01-48YEL/
GRNStarting motor
signal0 – 1 V Ignition switch turned ON.
—
6 – 14 V While engine cranking.
C01-49 — — — — —
C01-50WHT/
BLUGround of ECM for
shield wireBelow 0.3 V Ignition switch turned ON. —
C01-51 — — — — —
C01-52 — — — — —
C01-53RED/
BLKManifold absolute
pressure (MAP)
sensor signal (if
equipped)Approx. 4 V
(“Reference
waveform No.17: ”)Ignition switch turned ON
with barometric pressure
at 100 kPa, 760 mmHg.
—
0.4 – 2.0 V
(“Reference
waveform No.18: ”)While engine running at
specified idle speed after
warmed up with
barometric pressure at
100 kPa, 760 mmHg.
C01c01-
54GRNThrottle position
sensor (main)
signal0.75 – 1.08 VIgnition switch turned ON
and accelerator pedal at
idle position after warmed
up engine.
—
3.67 – 4.24 V
(“Reference
waveform No.29: ”)Ignition switch turned ON
and accelerator pedal at
full depressed position
after warmed up engine.
C01-55GRY/
BLUGround for sensors Below 0.3 V Ignition switch turned ON. —
C01-56 REDKnock sensor
signal2 – 3 V
(“Reference
waveform No.19: ”
and “Reference
waveform No.20: ”)Ignition switch turned ON.
— Engine running at 4000 r/
min. after warmed up.
C01-57 ORN Ground for sensors Below 0.3 V Ignition switch turned ON. —
C01-58BLK/
ORNGround for ECM Below 0.3 V Ignition switch turned ON. —
C01-59GRN/
WHTOil control valve
ground (for engine
with VVT system)Below 1.3 V Ignition switch turned ON. —
C01-60GRN/
REDOil control valve
output (for engine
with VVT system)*0 – 0.6 V
↑↓
10 – 14 V
(“Reference
waveform No.21: ”
and “Reference
waveform No.22: ”)At the moment of ignition
switch turned ON.Output signal is active
high pulse. Duty ratio
varies depending on
vehicle condition. Terminal
No.Wire
colorCircuit Normal voltage Condition Remarks
Terminal
No.Wire
colorCircuit Normal voltage Condition Remarks
E01-1BLK/
REDMain power supply 10 – 14 V Ignition switch turned ON. —
E01-2WHT/
REDPower source for
ECM internal
memory10 – 14 V Ignition switch turned ON. —
E01-3 REDCAN (high)
communication line
(active high signal)
to ABS control
module*2.5 – 4.5 V
(“Reference
waveform No.23: ”)Ignition switch turned ON
with engine at stop.CAN communication line
signal is pulse. Pulse
signal displayed with a
regular frequency with
varies depending on
engine condition.
Page 228 of 1556
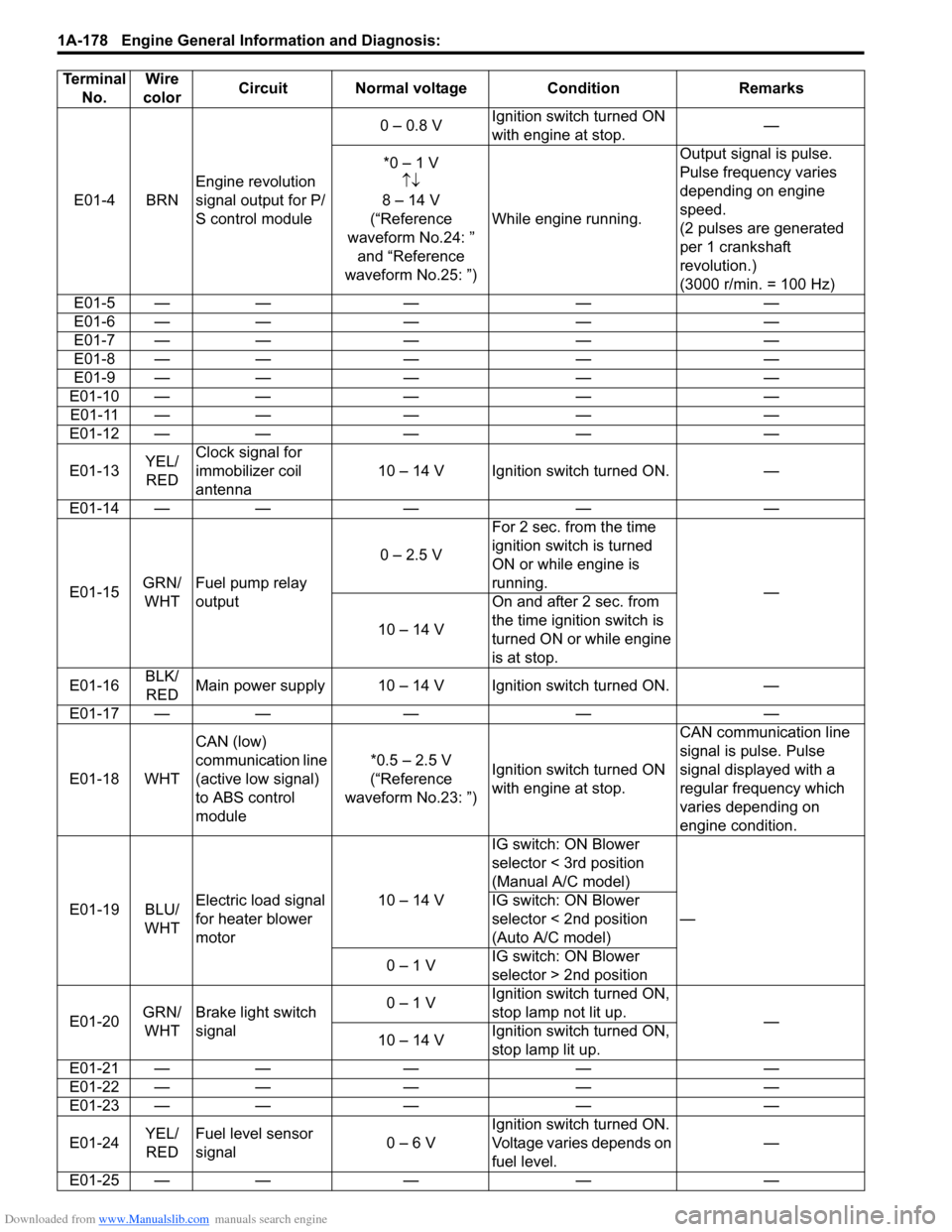
Downloaded from www.Manualslib.com manuals search engine 1A-178 Engine General Information and Diagnosis:
E01-4 BRNEngine revolution
signal output for P/
S control module0 – 0.8 VIgnition switch turned ON
with engine at stop.—
*0 – 1 V
↑↓
8 – 14 V
(“Reference
waveform No.24: ”
and “Reference
waveform No.25: ”)While engine running.Output signal is pulse.
Pulse frequency varies
depending on engine
speed.
(2 pulses are generated
per 1 crankshaft
revolution.)
(3000 r/min. = 100 Hz)
E01-5 — — — — —
E01-6 — — — — —
E01-7 — — — — —
E01-8 — — — — —
E01-9 — — — — —
E01-10 — — — — —
E01-11 — — — — —
E01-12 — — — — —
E01-13YEL/
REDClock signal for
immobilizer coil
antenna10 – 14 V Ignition switch turned ON. —
E01-14 — — — — —
E01-15GRN/
WHTFuel pump relay
output0 – 2.5 VFor 2 sec. from the time
ignition switch is turned
ON or while engine is
running.
—
10 – 14 VOn and after 2 sec. from
the time ignition switch is
turned ON or while engine
is at stop.
E01-16BLK/
REDMain power supply 10 – 14 V Ignition switch turned ON. —
E01-17 — — — — —
E01-18 WHTCAN (low)
communication line
(active low signal)
to ABS control
module*0.5 – 2.5 V
(“Reference
waveform No.23: ”)Ignition switch turned ON
with engine at stop.CAN communication line
signal is pulse. Pulse
signal displayed with a
regular frequency which
varies depending on
engine condition.
E01-19 BLU/
WHTElectric load signal
for heater blower
motor10 – 14 VIG switch: ON Blower
selector < 3rd position
(Manual A/C model)
— IG switch: ON Blower
selector < 2nd position
(Auto A/C model)
0 – 1 VIG switch: ON Blower
selector > 2nd position
E01-20GRN/
WHTBrake light switch
signal0 – 1 VIgnition switch turned ON,
stop lamp not lit up.
—
10 – 14 VIgnition switch turned ON,
stop lamp lit up.
E01-21 — — — — —
E01-22 — — — — —
E01-23 — — — — —
E01-24YEL/
REDFuel level sensor
signal0 – 6 VIgnition switch turned ON.
Voltage varies depends on
fuel level.—
E01-25 — — — — — Terminal
No.Wire
colorCircuit Normal voltage Condition Remarks
Page 253 of 1556
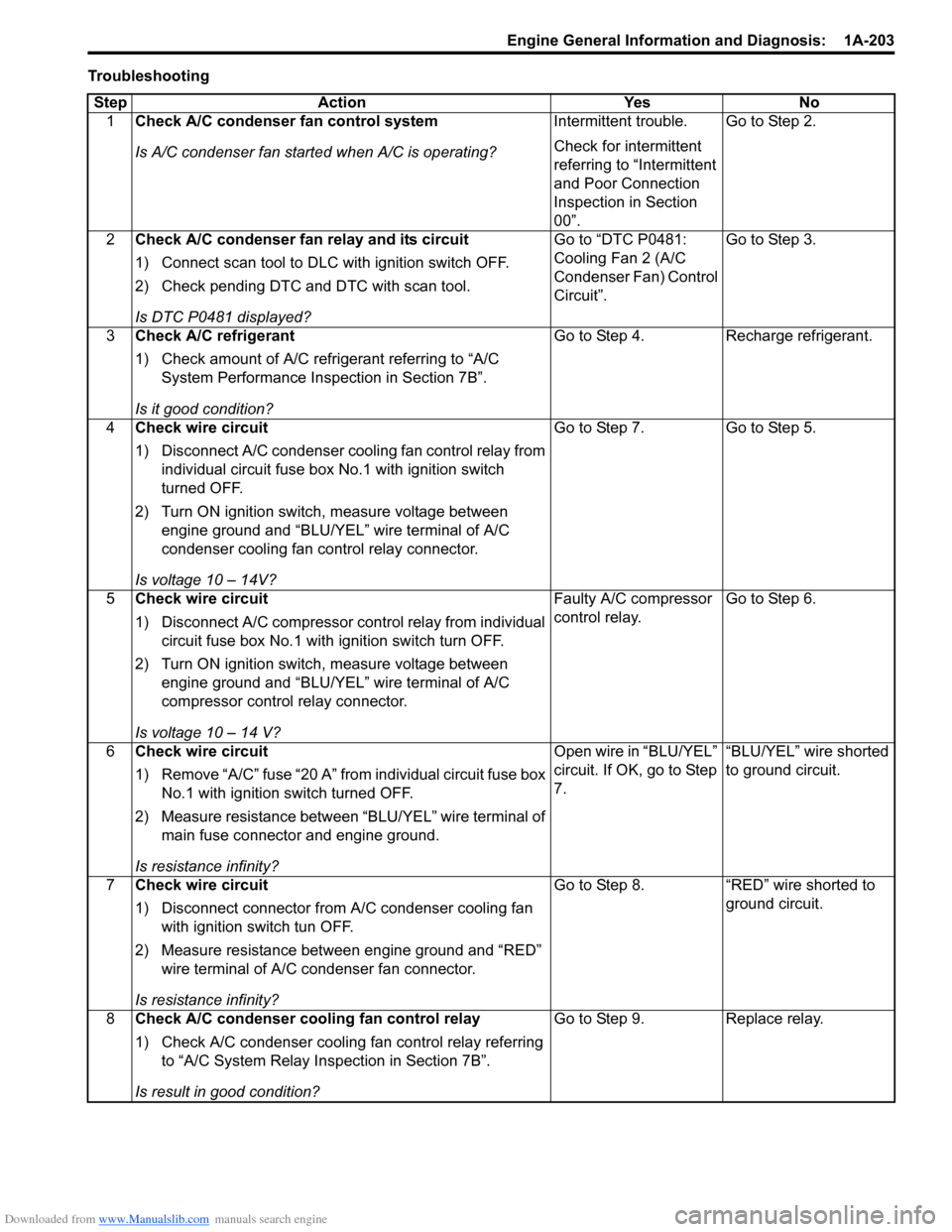
Downloaded from www.Manualslib.com manuals search engine Engine General Information and Diagnosis: 1A-203
Troubleshooting
Step Action Yes No
1Check A/C condenser fan control system
Is A/C condenser fan started when A/C is operating?Intermittent trouble.
Check for intermittent
referring to “Intermittent
and Poor Connection
Inspection in Section
00”.Go to Step 2.
2Check A/C condenser fan relay and its circuit
1) Connect scan tool to DLC with ignition switch OFF.
2) Check pending DTC and DTC with scan tool.
Is DTC P0481 displayed?Go to “DTC P0481:
Cooling Fan 2 (A/C
Condenser Fan) Control
Circuit”.Go to Step 3.
3Check A/C refrigerant
1) Check amount of A/C refrigerant referring to “A/C
System Performance Inspection in Section 7B”.
Is it good condition?Go to Step 4. Recharge refrigerant.
4Check wire circuit
1) Disconnect A/C condenser cooling fan control relay from
individual circuit fuse box No.1 with ignition switch
turned OFF.
2) Turn ON ignition switch, measure voltage between
engine ground and “BLU/YEL” wire terminal of A/C
condenser cooling fan control relay connector.
Is voltage 10 – 14V?Go to Step 7. Go to Step 5.
5Check wire circuit
1) Disconnect A/C compressor control relay from individual
circuit fuse box No.1 with ignition switch turn OFF.
2) Turn ON ignition switch, measure voltage between
engine ground and “BLU/YEL” wire terminal of A/C
compressor control relay connector.
Is voltage 10 – 14 V?Faulty A/C compressor
control relay.Go to Step 6.
6Check wire circuit
1) Remove “A/C” fuse “20 A” from individual circuit fuse box
No.1 with ignition switch turned OFF.
2) Measure resistance between “BLU/YEL” wire terminal of
main fuse connector and engine ground.
Is resistance infinity?Open wire in “BLU/YEL”
circuit. If OK, go to Step
7.“BLU/YEL” wire shorted
to ground circuit.
7Check wire circuit
1) Disconnect connector from A/C condenser cooling fan
with ignition switch tun OFF.
2) Measure resistance between engine ground and “RED”
wire terminal of A/C condenser fan connector.
Is resistance infinity?Go to Step 8. “RED” wire shorted to
ground circuit.
8Check A/C condenser cooling fan control relay
1) Check A/C condenser cooling fan control relay referring
to “A/C System Relay Inspection in Section 7B”.
Is result in good condition?Go to Step 9. Replace relay.
Page 256 of 1556
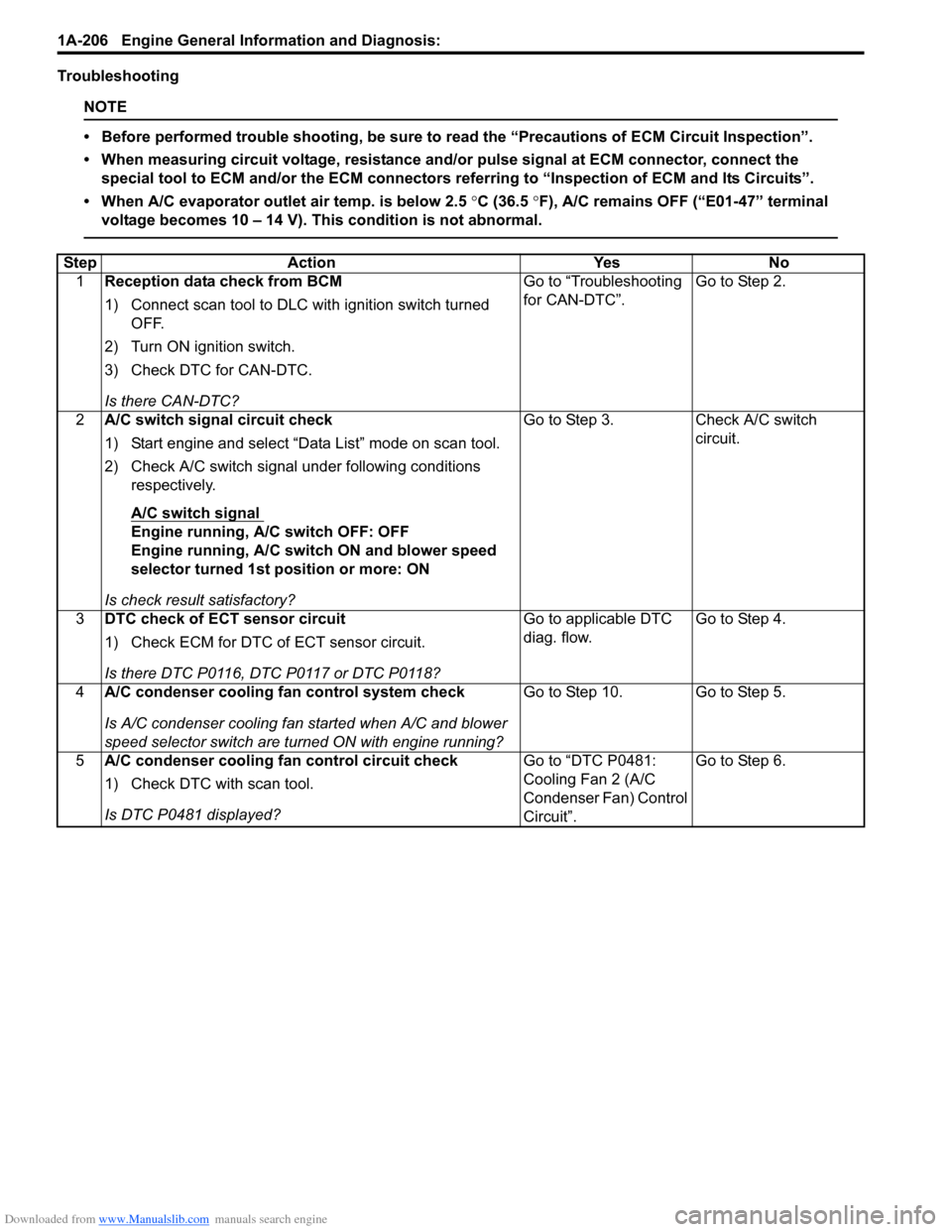
Downloaded from www.Manualslib.com manuals search engine 1A-206 Engine General Information and Diagnosis:
Troubleshooting
NOTE
• Before performed trouble shooting, be sure to read the “Precautions of ECM Circuit Inspection”.
• When measuring circuit voltage, resistance and/or pulse signal at ECM connector, connect the
special tool to ECM and/or the ECM connectors referring to “Inspection of ECM and Its Circuits”.
• When A/C evaporator outlet air temp. is below 2.5 °C (36.5 °F), A/C remains OFF (“E01-47” terminal
voltage becomes 10 – 14 V). This condition is not abnormal.
Step Action Yes No
1Reception data check from BCM
1) Connect scan tool to DLC with ignition switch turned
OFF.
2) Turn ON ignition switch.
3) Check DTC for CAN-DTC.
Is there CAN-DTC?Go to “Troubleshooting
for CAN-DTC”.Go to Step 2.
2A/C switch signal circuit check
1) Start engine and select “Data List” mode on scan tool.
2) Check A/C switch signal under following conditions
respectively.
A/C switch signal
Engine running, A/C switch OFF: OFF
Engine running, A/C switch ON and blower speed
selector turned 1st position or more: ON
Is check result satisfactory?Go to Step 3. Check A/C switch
circuit.
3DTC check of ECT sensor circuit
1) Check ECM for DTC of ECT sensor circuit.
Is there DTC P0116, DTC P0117 or DTC P0118?Go to applicable DTC
diag. flow.Go to Step 4.
4A/C condenser cooling fan control system check
Is A/C condenser cooling fan started when A/C and blower
speed selector switch are turned ON with engine running?Go to Step 10. Go to Step 5.
5A/C condenser cooling fan control circuit check
1) Check DTC with scan tool.
Is DTC P0481 displayed?Go to “DTC P0481:
Cooling Fan 2 (A/C
Condenser Fan) Control
Circuit”.Go to Step 6.