fuse box connector SUZUKI SX4 2006 1.G Service Service Manual
[x] Cancel search | Manufacturer: SUZUKI, Model Year: 2006, Model line: SX4, Model: SUZUKI SX4 2006 1.GPages: 1556, PDF Size: 37.31 MB
Page 899 of 1556
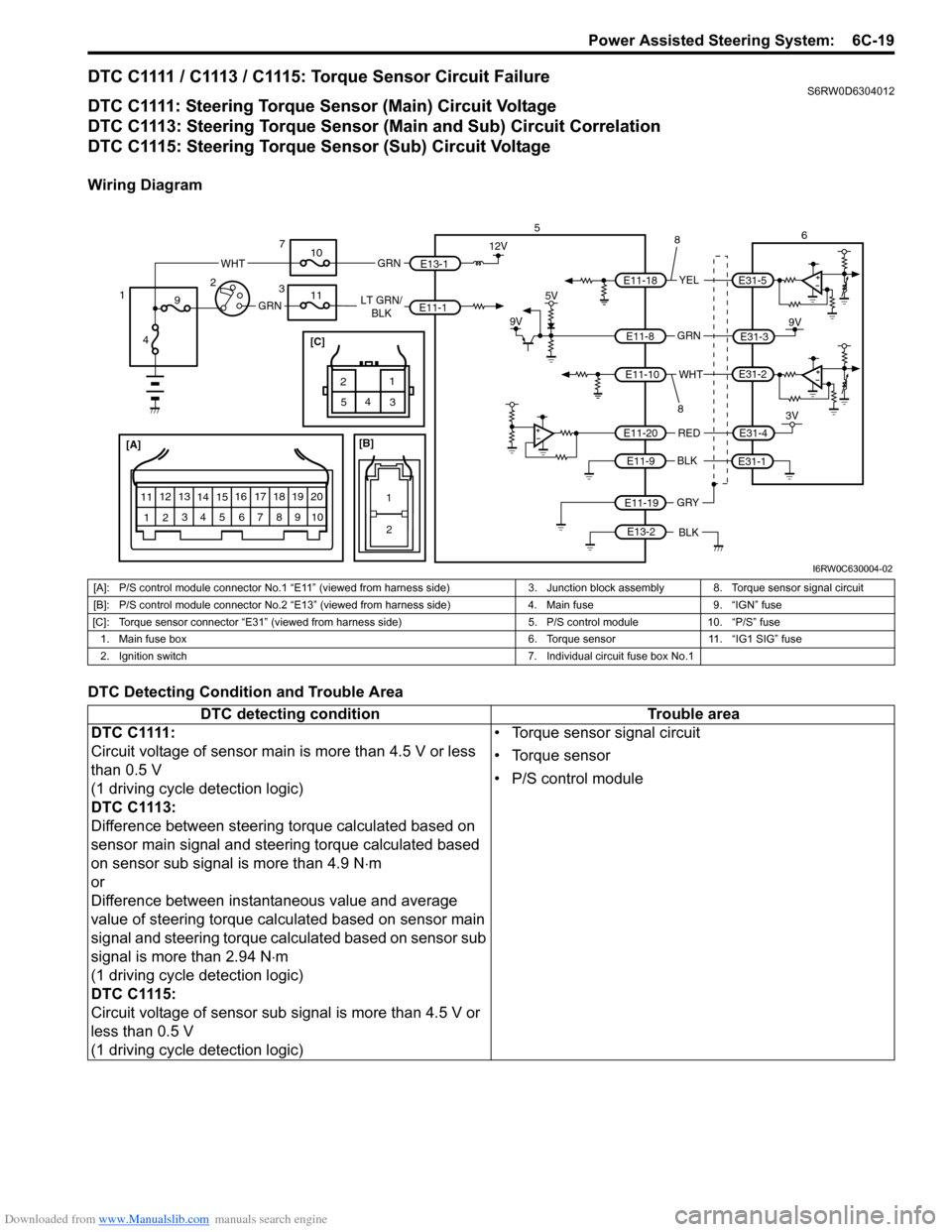
Downloaded from www.Manualslib.com manuals search engine Power Assisted Steering System: 6C-19
DTC C1111 / C1113 / C1115: Torque Sensor Circuit FailureS6RW0D6304012
DTC C1111: Steering Torque Sensor (Main) Circuit Voltage
DTC C1113: Steering Torque Sensor (Main and Sub) Circuit Correlation
DTC C1115: Steering Torque Sensor (Sub) Circuit Voltage
Wiring Diagram
DTC Detecting Condition and Trouble Area
[A]
123
453 21
4
5
67
8
9 11
10 12 13
141516
17 18 1920
1
2
[B]
[C]
LT GRN/
BLK
WHT GRN
BLK
E11-1
E11-10E11-8
E11-9
E11-19
E13-1 GRN
GRY
GRN
WHT
5
6
37
10
11
9
4 12
12V
E13-2BLK
9V
REDE11-20
5VYELE11-18E31-5
E31-2
E31-39V
E31-43V
E31-1
8
8
I6RW0C630004-02
[A]: P/S control module connector No.1 “E11” (viewed from harness side) 3. Junction block assembly 8. Torque sensor signal circuit
[B]: P/S control module connector No.2 “E13” (viewed from harness side) 4. Main fuse 9. “IGN” fuse
[C]: Torque sensor connector “E31” (viewed from harness side) 5. P/S control module 10. “P/S” fuse
1. Main fuse box 6. Torque sensor 11. “IG1 SIG” fuse
2. Ignition switch 7. Individual circuit fuse box No.1
DTC detecting condition Trouble area
DTC C1111:
Circuit voltage of sensor main is more than 4.5 V or less
than 0.5 V
(1 driving cycle detection logic)
DTC C1113:
Difference between steering torque calculated based on
sensor main signal and steering torque calculated based
on sensor sub signal is more than 4.9 N⋅m
or
Difference between instantaneous value and average
value of steering torque calculated based on sensor main
signal and steering torque calculated based on sensor sub
signal is more than 2.94 N⋅m
(1 driving cycle detection logic)
DTC C1115:
Circuit voltage of sensor sub signal is more than 4.5 V or
less than 0.5 V
(1 driving cycle detection logic)• Torque sensor signal circuit
• Torque sensor
• P/S control module
Page 901 of 1556
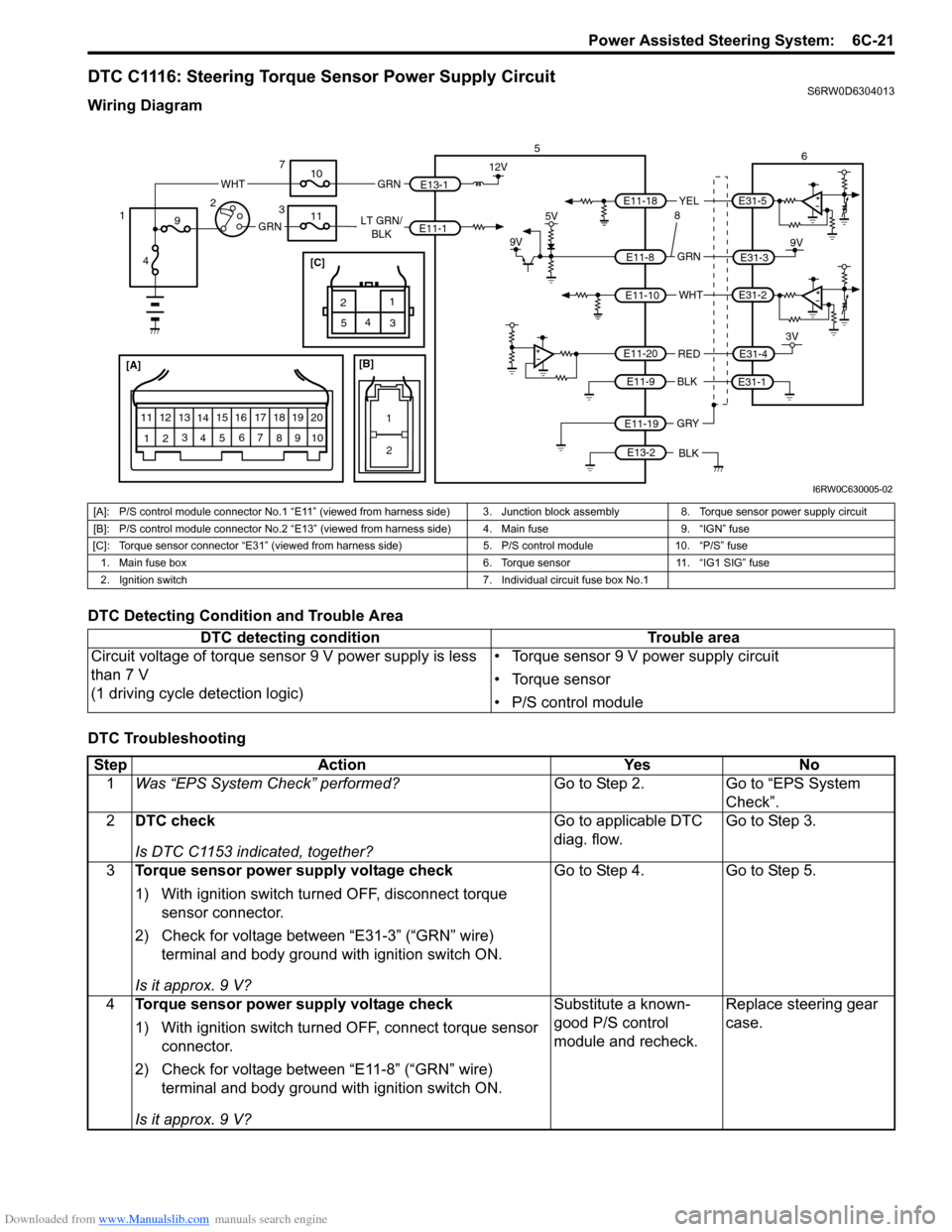
Downloaded from www.Manualslib.com manuals search engine Power Assisted Steering System: 6C-21
DTC C1116: Steering Torque Sensor Power Supply CircuitS6RW0D6304013
Wiring Diagram
DTC Detecting Condition and Trouble Area
DTC Troubleshooting
[A]
123
453 21
4
5
67
8
9 11
10 12 13
141516
17 18 1920
1
2
[B]
[C]
LT GRN/
BLK
WHT GRN
BLK
E11-1
E11-10E11-8
E11-9
E11-19
E13-1 GRN
GRY
GRN
WHT
5
6
37
10
11
9
4 12
12V
E13-2BLK
9V
REDE11-20
5VYELE11-18E31-5
E31-2
E31-39V
E31-43V
E31-1
8
I6RW0C630005-02
[A]: P/S control module connector No.1 “E11” (viewed from harness side) 3. Junction block assembly 8. Torque sensor power supply circuit
[B]: P/S control module connector No.2 “E13” (viewed from harness side) 4. Main fuse 9. “IGN” fuse
[C]: Torque sensor connector “E31” (viewed from harness side) 5. P/S control module 10. “P/S” fuse
1. Main fuse box 6. Torque sensor 11. “IG1 SIG” fuse
2. Ignition switch 7. Individual circuit fuse box No.1
DTC detecting condition Trouble area
Circuit voltage of torque sensor 9 V power supply is less
than 7 V
(1 driving cycle detection logic)• Torque sensor 9 V power supply circuit
• Torque sensor
• P/S control module
Step Action Yes No
1Was “EPS System Check” performed?Go to Step 2. Go to “EPS System
Check”.
2DTC check
Is DTC C1153 indicated, together?Go to applicable DTC
diag. flow.Go to Step 3.
3Torque sensor power supply voltage check
1) With ignition switch turned OFF, disconnect torque
sensor connector.
2) Check for voltage between “E31-3” (“GRN” wire)
terminal and body ground with ignition switch ON.
Is it approx. 9 V?Go to Step 4. Go to Step 5.
4Torque sensor power supply voltage check
1) With ignition switch turned OFF, connect torque sensor
connector.
2) Check for voltage between “E11-8” (“GRN” wire)
terminal and body ground with ignition switch ON.
Is it approx. 9 V?Substitute a known-
good P/S control
module and recheck.Replace steering gear
case.
Page 902 of 1556
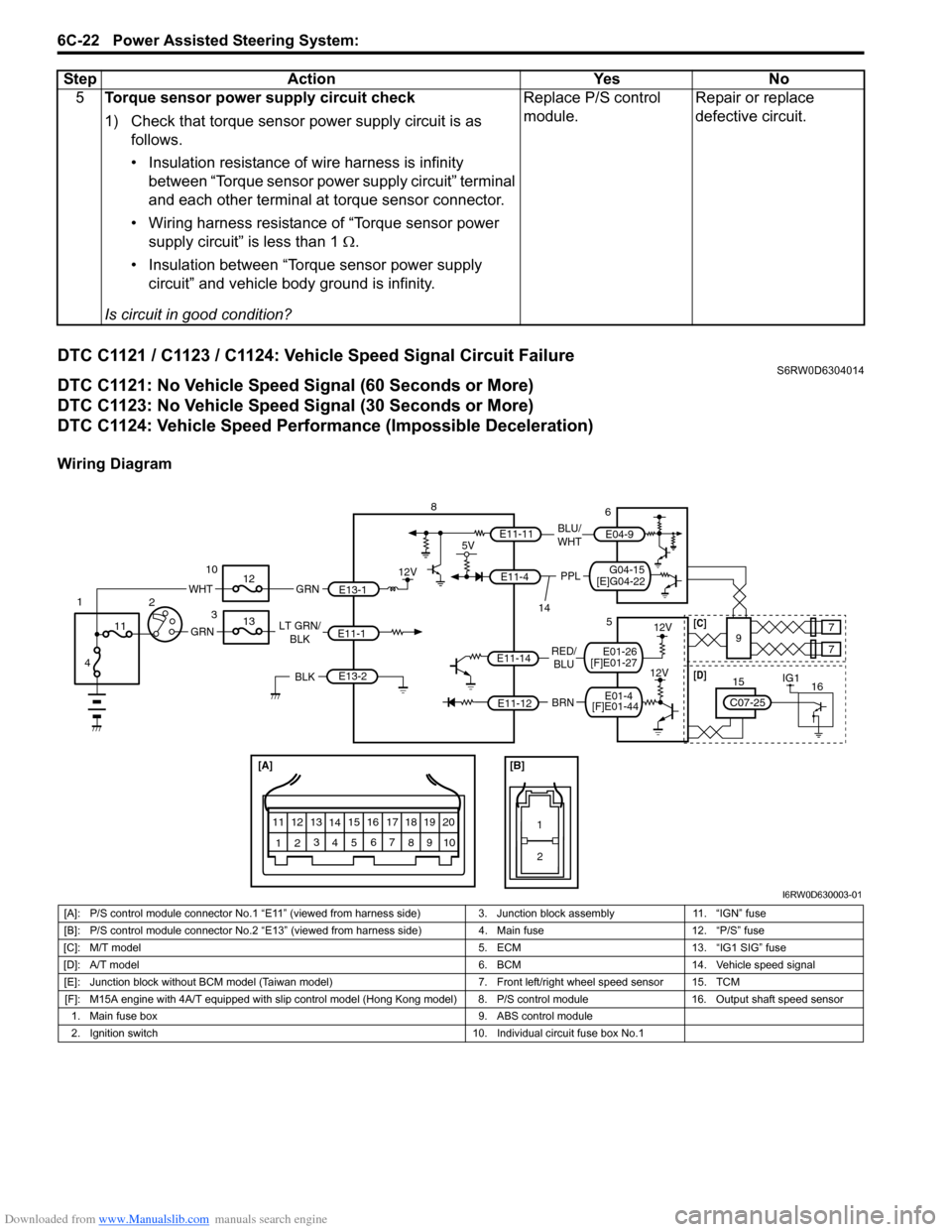
Downloaded from www.Manualslib.com manuals search engine 6C-22 Power Assisted Steering System:
DTC C1121 / C1123 / C1124: Vehicle Speed Signal Circuit FailureS6RW0D6304014
DTC C1121: No Vehicle Speed Signal (60 Seconds or More)
DTC C1123: No Vehicle Speed Signal (30 Seconds or More)
DTC C1124: Vehicle Speed Performance (Impossible Deceleration)
Wiring Diagram5Torque sensor power supply circuit check
1) Check that torque sensor power supply circuit is as
follows.
• Insulation resistance of wire harness is infinity
between “Torque sensor power supply circuit” terminal
and each other terminal at torque sensor connector.
• Wiring harness resistance of “Torque sensor power
supply circuit” is less than 1 Ω.
• Insulation between “Torque sensor power supply
circuit” and vehicle body ground is infinity.
Is circuit in good condition?Replace P/S control
module.Repair or replace
defective circuit. Step Action Yes No
[A]
123
4567
8
9 11
10 12 13
141516
17 18 1920
1
2
[B]
BRN RED/
BLU LT GRN/
BLK
E11-1
E11-14
E11-12
E13-1 GRN
GRN
WHT
8
3 10
12
13
11
4 1
2
12V
E13-2BLK
12V
12V
9 5
77
E11-11
G04-15
[E]G04-22
5V
PPL
E11-4
BLU/
WHTE04-9
6
14
IG11615
C07-25
[D][C]
[F]E01-44E01-4
[F]E01-27E01-26
I6RW0D630003-01
[A]: P/S control module connector No.1 “E11” (viewed from harness side) 3. Junction block assembly 11. “IGN” fuse
[B]: P/S control module connector No.2 “E13” (viewed from harness side) 4. Main fuse 12. “P/S” fuse
[C]: M/T model 5. ECM 13. “IG1 SIG” fuse
[D]: A/T model 6. BCM 14. Vehicle speed signal
[E]: Junction block without BCM model (Taiwan model) 7. Front left/right wheel speed sensor 15. TCM
[F]: M15A engine with 4A/T equipped with slip control model (Hong Kong model) 8. P/S control module 16. Output shaft speed sensor
1. Main fuse box 9. ABS control module
2. Ignition switch 10. Individual circuit fuse box No.1
Page 904 of 1556
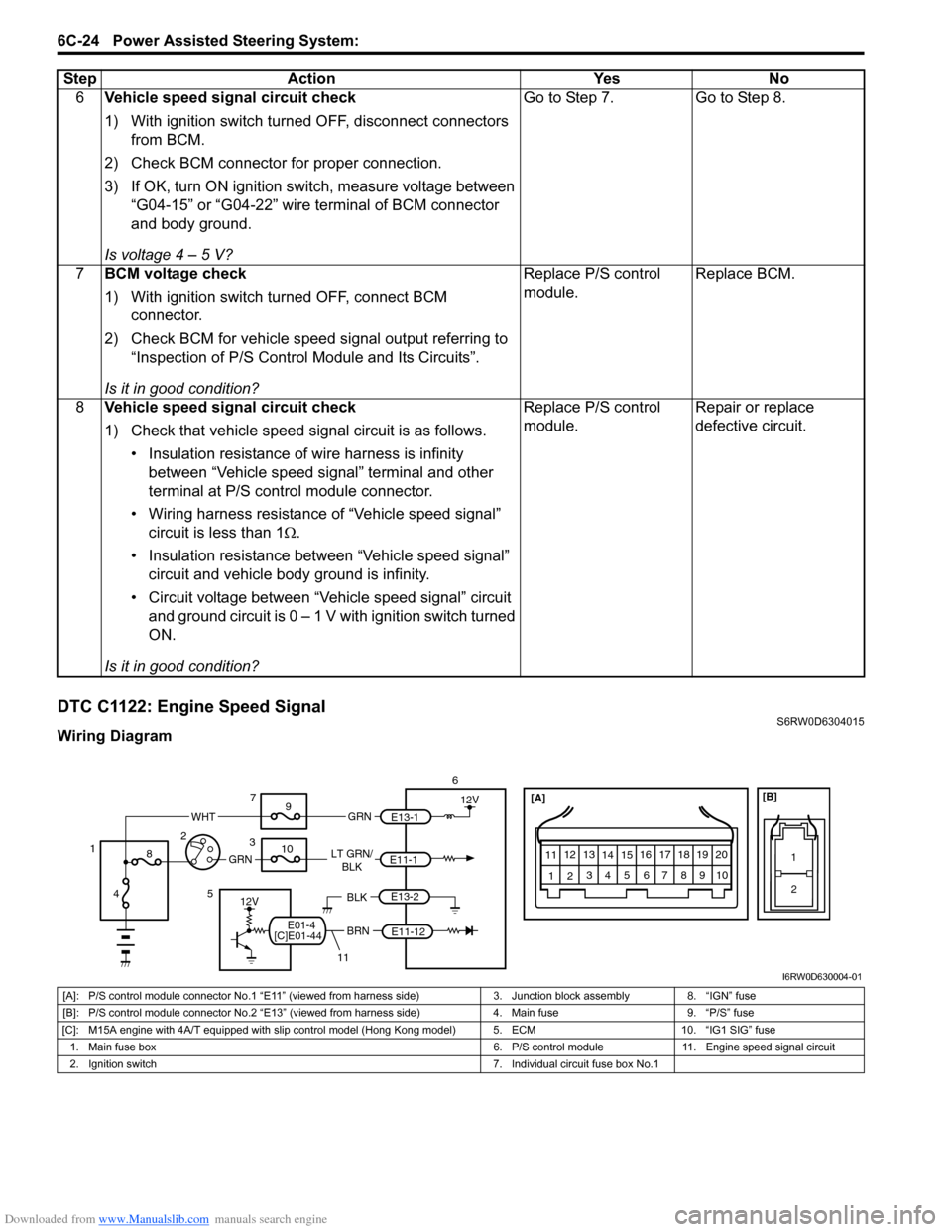
Downloaded from www.Manualslib.com manuals search engine 6C-24 Power Assisted Steering System:
DTC C1122: Engine Speed SignalS6RW0D6304015
Wiring Diagram6Vehicle speed signal circuit check
1) With ignition switch turned OFF, disconnect connectors
from BCM.
2) Check BCM connector for proper connection.
3) If OK, turn ON ignition switch, measure voltage between
“G04-15” or “G04-22” wire terminal of BCM connector
and body ground.
Is voltage 4 – 5 V?Go to Step 7. Go to Step 8.
7BCM voltage check
1) With ignition switch turned OFF, connect BCM
connector.
2) Check BCM for vehicle speed signal output referring to
“Inspection of P/S Control Module and Its Circuits”.
Is it in good condition?Replace P/S control
module.Replace BCM.
8Vehicle speed signal circuit check
1) Check that vehicle speed signal circuit is as follows.
• Insulation resistance of wire harness is infinity
between “Vehicle speed signal” terminal and other
terminal at P/S control module connector.
• Wiring harness resistance of “Vehicle speed signal”
circuit is less than 1Ω.
• Insulation resistance between “Vehicle speed signal”
circuit and vehicle body ground is infinity.
• Circuit voltage between “Vehicle speed signal” circuit
and ground circuit is 0 – 1 V with ignition switch turned
ON.
Is it in good condition?Replace P/S control
module.Repair or replace
defective circuit. Step Action Yes No
[A]
123
4567
8
9 11
10 12 13
141516
17 18 1920
1
2
[B]
BRN LT GRN/
BLK
E11-1
E11-12
E13-1 GRN
GRN
WHT
6
37
9
10
8
4 12
12V
E13-2BLK12V5
11
[C]E01-44E01-4
I6RW0D630004-01
[A]: P/S control module connector No.1 “E11” (viewed from harness side) 3. Junction block assembly 8. “IGN” fuse
[B]: P/S control module connector No.2 “E13” (viewed from harness side) 4. Main fuse 9. “P/S” fuse
[C]: M15A engine with 4A/T equipped with slip control model (Hong Kong model) 5. ECM 10. “IG1 SIG” fuse
1. Main fuse box 6. P/S control module 11. Engine speed signal circuit
2. Ignition switch 7. Individual circuit fuse box No.1
Page 906 of 1556
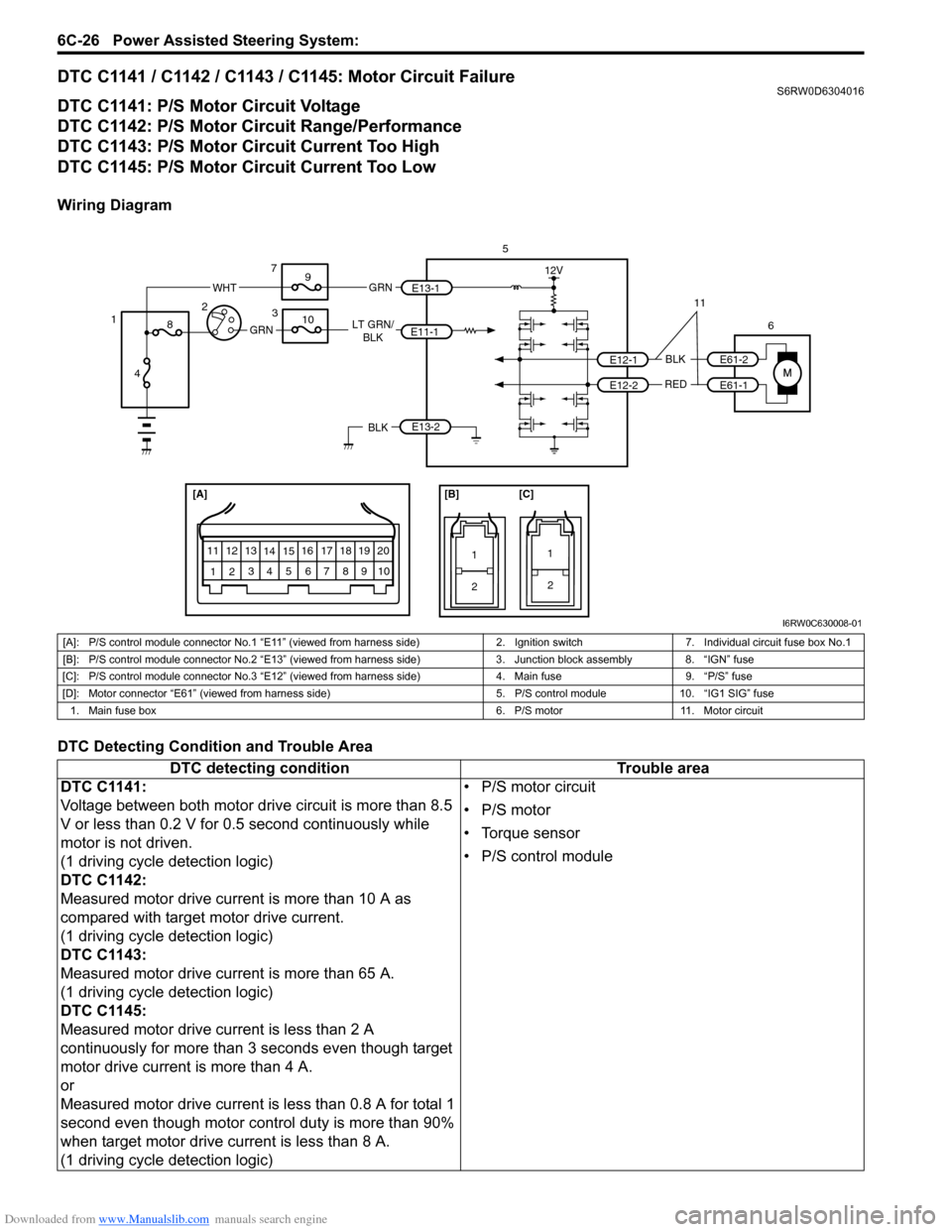
Downloaded from www.Manualslib.com manuals search engine 6C-26 Power Assisted Steering System:
DTC C1141 / C1142 / C1143 / C1145: Motor Circuit FailureS6RW0D6304016
DTC C1141: P/S Motor Circuit Voltage
DTC C1142: P/S Motor Circuit Range/Performance
DTC C1143: P/S Motor Circuit Current Too High
DTC C1145: P/S Motor Circuit Current Too Low
Wiring Diagram
DTC Detecting Condition and Trouble Area
[A]
123
4567
8
9 11
10 12 13
141516
17 18 1920
1
2
[B]
1
2
[C]
LT GRN/
BLK
BLK
RED
E11-1
E12-1
E12-2 E13-1 GRNGRN
WHT
5
6 3 7
9
10
8
4 12
12V
E13-2BLK
E61-2
E61-1
11
I6RW0C630008-01
[A]: P/S control module connector No.1 “E11” (viewed from harness side) 2. Ignition switch 7. Individual circuit fuse box No.1
[B]: P/S control module connector No.2 “E13” (viewed from harness side) 3. Junction block assembly 8. “IGN” fuse
[C]: P/S control module connector No.3 “E12” (viewed from harness side) 4. Main fuse 9. “P/S” fuse
[D]: Motor connector “E61” (viewed from harness side) 5. P/S control module 10. “IG1 SIG” fuse
1. Main fuse box 6. P/S motor 11. Motor circuit
DTC detecting condition Trouble area
DTC C1141:
Voltage between both motor drive circuit is more than 8.5
V or less than 0.2 V for 0.5 second continuously while
motor is not driven.
(1 driving cycle detection logic)
DTC C1142:
Measured motor drive current is more than 10 A as
compared with target motor drive current.
(1 driving cycle detection logic)
DTC C1143:
Measured motor drive current is more than 65 A.
(1 driving cycle detection logic)
DTC C1145:
Measured motor drive current is less than 2 A
continuously for more than 3 seconds even though target
motor drive current is more than 4 A.
or
Measured motor drive current is less than 0.8 A for total 1
second even though motor control duty is more than 90%
when target motor drive current is less than 8 A.
(1 driving cycle detection logic)• P/S motor circuit
• P/S motor
• Torque sensor
• P/S control module
Page 907 of 1556
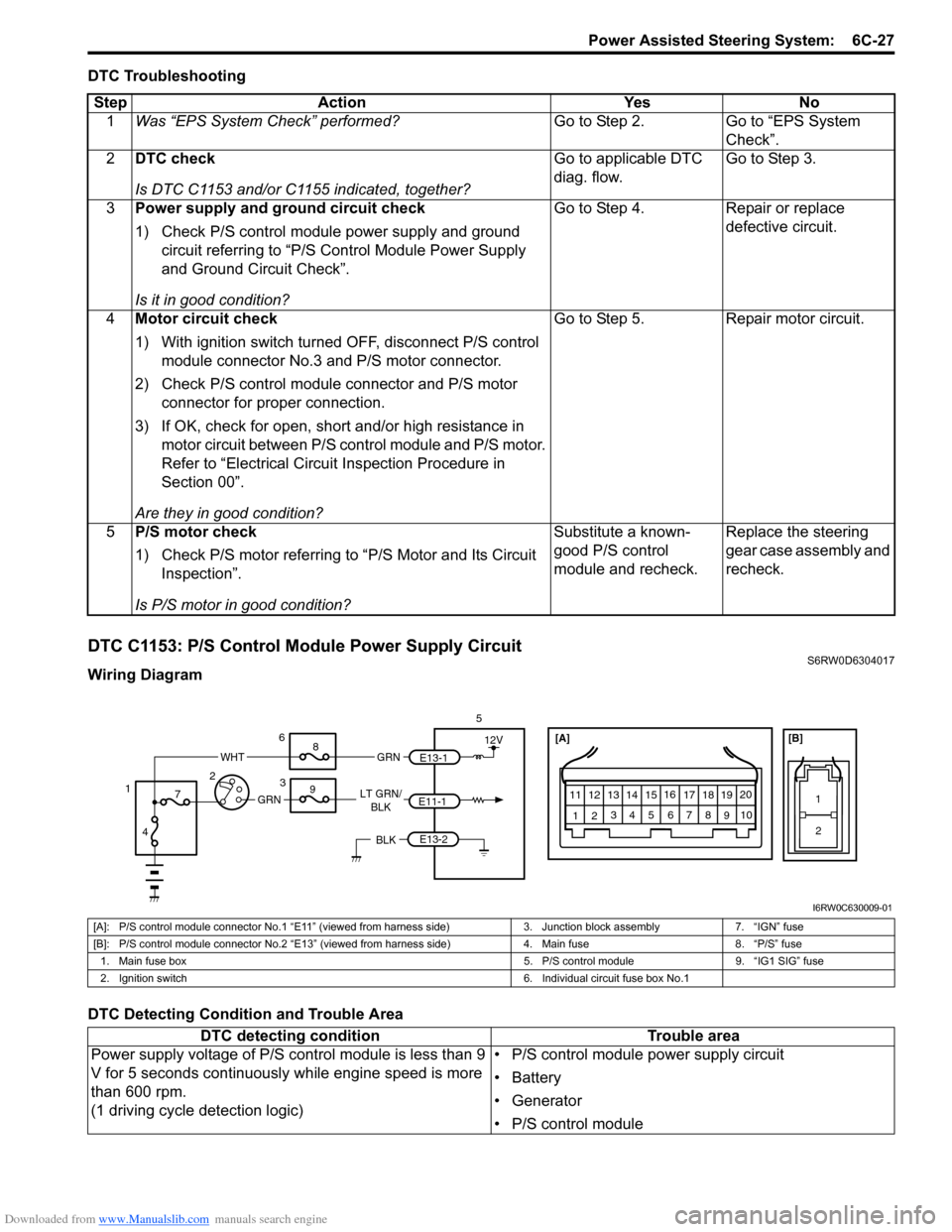
Downloaded from www.Manualslib.com manuals search engine Power Assisted Steering System: 6C-27
DTC Troubleshooting
DTC C1153: P/S Control Module Power Supply CircuitS6RW0D6304017
Wiring Diagram
DTC Detecting Condition and Trouble AreaStep Action Yes No
1Was “EPS System Check” performed?Go to Step 2. Go to “EPS System
Check”.
2DTC check
Is DTC C1153 and/or C1155 indicated, together?Go to applicable DTC
diag. flow.Go to Step 3.
3Power supply and ground circuit check
1) Check P/S control module power supply and ground
circuit referring to “P/S Control Module Power Supply
and Ground Circuit Check”.
Is it in good condition?Go to Step 4. Repair or replace
defective circuit.
4Motor circuit check
1) With ignition switch turned OFF, disconnect P/S control
module connector No.3 and P/S motor connector.
2) Check P/S control module connector and P/S motor
connector for proper connection.
3) If OK, check for open, short and/or high resistance in
motor circuit between P/S control module and P/S motor.
Refer to “Electrical Circuit Inspection Procedure in
Section 00”.
Are they in good condition?Go to Step 5. Repair motor circuit.
5P/S motor check
1) Check P/S motor referring to “P/S Motor and Its Circuit
Inspection”.
Is P/S motor in good condition?Substitute a known-
good P/S control
module and recheck.Replace the steering
gear case assembly and
recheck.
[A]
123
4567
8
9 11
10 12 13
141516
17 18 1920
1
2
[B]
LT GRN/
BLKE11-1E13-1 GRNGRN
WHT
5
3 6
8
9
7
4 12
12V
E13-2BLK
I6RW0C630009-01
[A]: P/S control module connector No.1 “E11” (viewed from harness side) 3. Junction block assembly 7. “IGN” fuse
[B]: P/S control module connector No.2 “E13” (viewed from harness side) 4. Main fuse 8. “P/S” fuse
1. Main fuse box 5. P/S control module 9. “IG1 SIG” fuse
2. Ignition switch 6. Individual circuit fuse box No.1
DTC detecting condition Trouble area
Power supply voltage of P/S control module is less than 9
V for 5 seconds continuously while engine speed is more
than 600 rpm.
(1 driving cycle detection logic)• P/S control module power supply circuit
• Battery
• Generator
• P/S control module
Page 983 of 1556
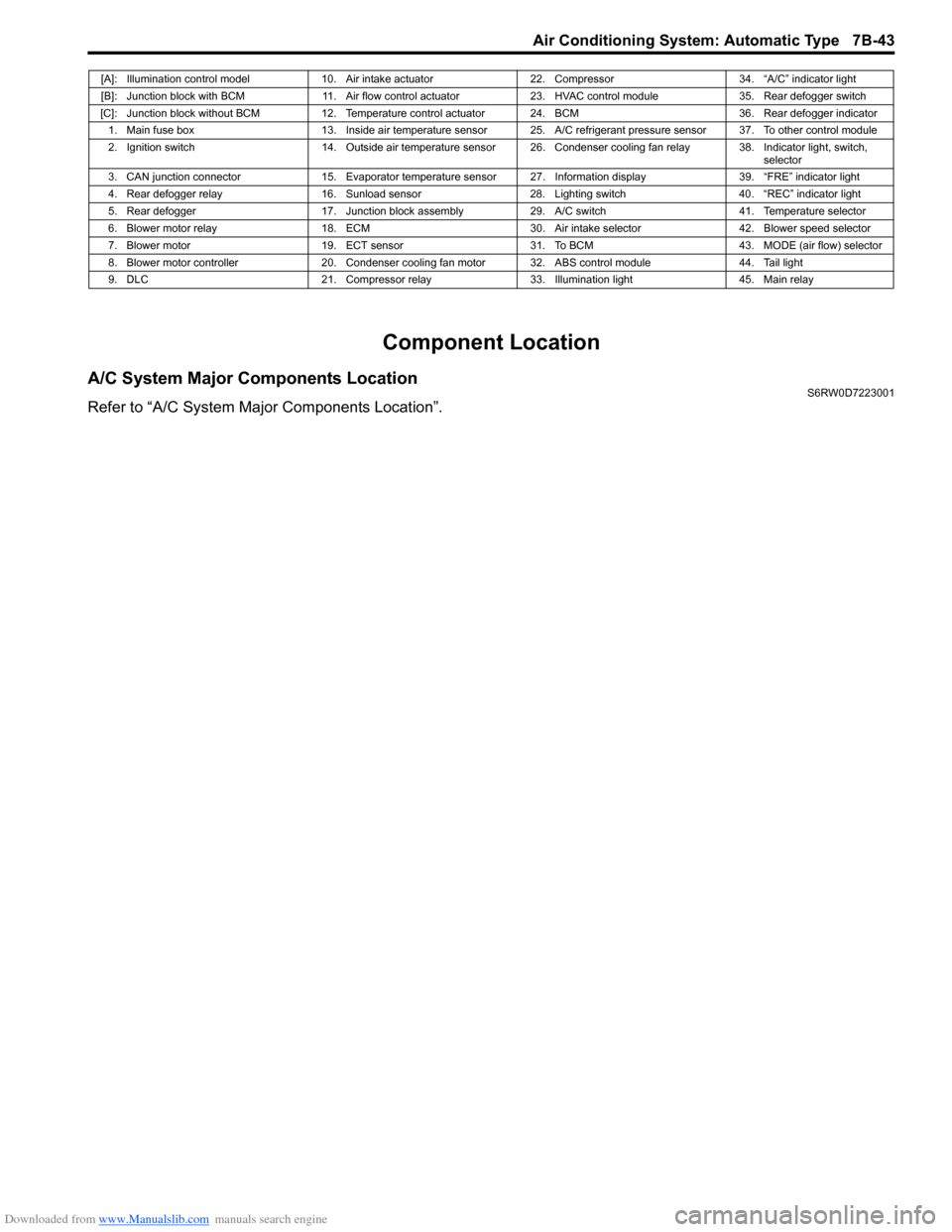
Downloaded from www.Manualslib.com manuals search engine Air Conditioning System: Automatic Type 7B-43
Component Location
A/C System Major Components LocationS6RW0D7223001
Refer to “A/C System Major Components Location”.
[A]: Illumination control model 10. Air intake actuator 22. Compressor 34. “A/C” indicator light
[B]: Junction block with BCM 11. Air flow control actuator 23. HVAC control module 35. Rear defogger switch
[C]: Junction block without BCM 12. Temperature control actuator 24. BCM 36. Rear defogger indicator
1. Main fuse box 13. Inside air temperature sensor 25. A/C refrigerant pressure sensor 37. To other control module
2. Ignition switch 14. Outside air temperature sensor 26. Condenser cooling fan relay 38. Indicator light, switch,
selector
3. CAN junction connector 15. Evaporator temperature sensor 27. Information display 39. “FRE” indicator light
4. Rear defogger relay 16. Sunload sensor 28. Lighting switch 40. “REC” indicator light
5. Rear defogger 17. Junction block assembly 29. A/C switch 41. Temperature selector
6. Blower motor relay 18. ECM 30. Air intake selector 42. Blower speed selector
7. Blower motor 19. ECT sensor 31. To BCM 43. MODE (air flow) selector
8. Blower motor controller 20. Condenser cooling fan motor 32. ABS control module 44. Tail light
9. DLC 21. Compressor relay 33. Illumination light 45. Main relay
Page 1048 of 1556
![SUZUKI SX4 2006 1.G Service Service Manual Downloaded from www.Manualslib.com manuals search engine 8B-9 Air Bag System:
Terminal arrangement of SDM (viewed from harness side)
[A]: Shorting bar 11. BCM 25. Driver seat belt pretensioner
[B]: C SUZUKI SX4 2006 1.G Service Service Manual Downloaded from www.Manualslib.com manuals search engine 8B-9 Air Bag System:
Terminal arrangement of SDM (viewed from harness side)
[A]: Shorting bar 11. BCM 25. Driver seat belt pretensioner
[B]: C](/img/20/7612/w960_7612-1047.png)
Downloaded from www.Manualslib.com manuals search engine 8B-9 Air Bag System:
Terminal arrangement of SDM (viewed from harness side)
[A]: Shorting bar 11. BCM 25. Driver seat belt pretensioner
[B]: Connector 12. Combination meter 26. Passenger seat belt pretensioner
[C]: Junction block with BCM model 13. “AIR BAG” warning light27. Driver side-air bag (inflator) module (8-channel system)
[D]: Junction block without BCM model 14. Light driver 28. Passenger side-air bag (inflator) module (8-channel system)
1. Battery 15. SDM 29. Driver side curtain-air bag (inflator) module (8-channel
system)
2. Main fuse 16. To HVAC control module (auto A/C model) 30. Passenger side curtain-air bag (inflator) module (8-channel
system)
3. Fuse 17. Data link connector (DLC) 31. Safing power driver
4. Individual circuit fuse box No.1 18. Forward impact-sensor 32. X-Y-G (longitudinal / lateral acceleration)
5. “IGN” fuse 19. Driver side impact-sensor (8-channel
system)33. DC / DC converter
6. Ignition switch 20. Passenger side impact-sensor (8-channel
system)34. Mechanical longitudinal G sensor (switch)
7. Junction block assembly 21. Ground for air bag system 35. Back up capacitor
8. “DOME” fuse 22. Contact coil assembly
9. “METER” fuse 23. Driver air bag (inflator) module
10. “A/B” fuse 24. Passenger air bag (inflator) module
1
2 3 4 5 6 7 8 9 10 11 12 13 14 15 16 17 18 19 20 21 22 23 24 25 26
27 28 29 30 31 32 33 34 35 36 37 38 39 40 41 42 43 44 45 46 47 48 49 50 51
1
I7RW01822003-02
1. SDM Connector “L04”
Page 1062 of 1556
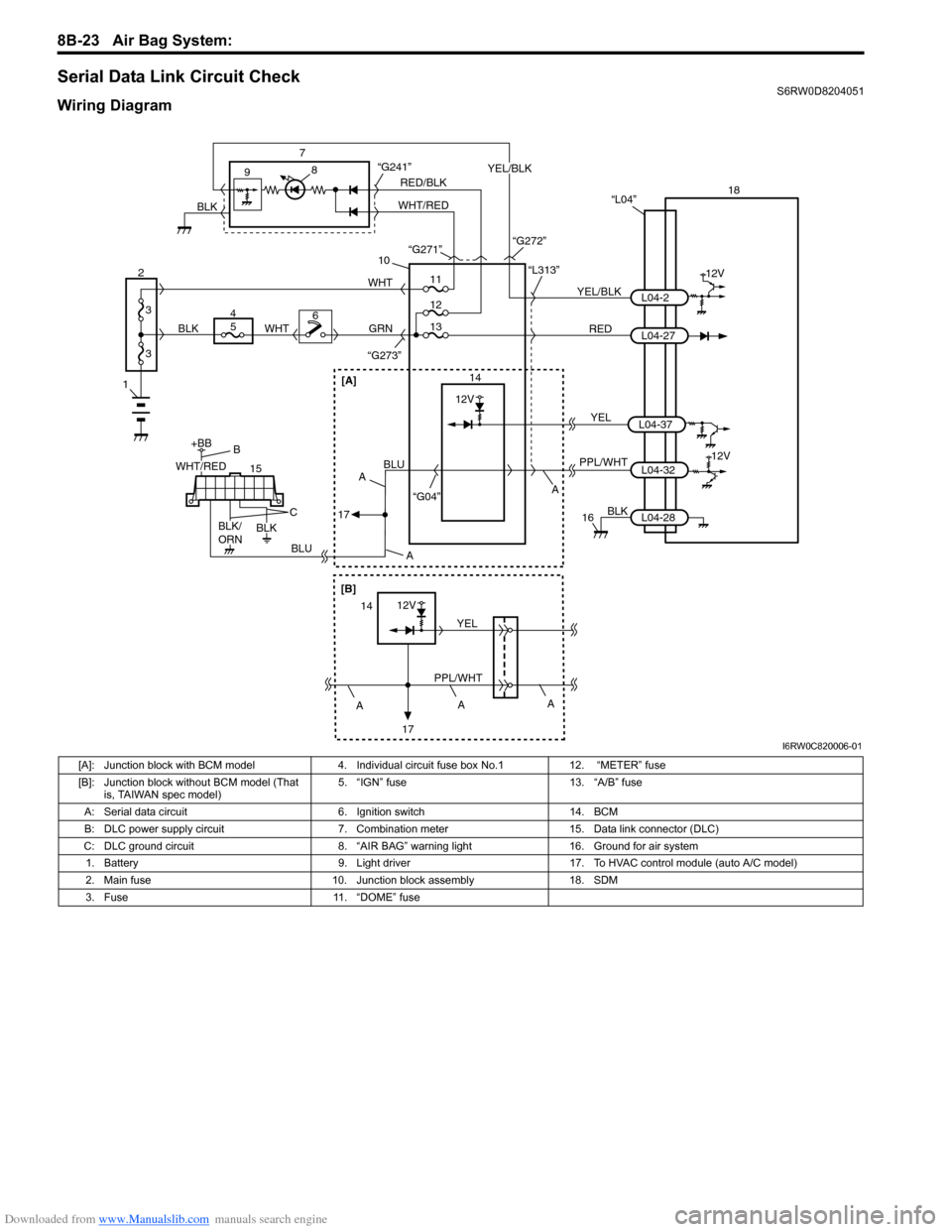
Downloaded from www.Manualslib.com manuals search engine 8B-23 Air Bag System:
Serial Data Link Circuit CheckS6RW0D8204051
Wiring Diagram
1
2
3
3
18
12V
RED 7
14 9
10
“L313”
“G273”
YEL/BLKL04-2
L04-27 “L04”
PPL/WHT
“G04”L04-3212V
8
GRN
15
+BB
56WHTWHT
4
BLUBLU
BLK
16
11
12
“G241”
13
BLK
L04-28
RED/BLK
WHT/REDYEL/BLK
BLK“G271”
“G272”
WHT/RED
BLK/
ORNBLK
B
C
A A
A
17
[A]
A
[B]
12V
PPL/WHTYEL14
17A
A
YELL04-37
12V
I6RW0C820006-01
[A]: Junction block with BCM model 4. Individual circuit fuse box No.1 12. “METER” fuse
[B]: Junction block without BCM model (That
is, TAIWAN spec model)5. “IGN” fuse 13. “A/B” fuse
A: Serial data circuit 6. Ignition switch 14. BCM
B: DLC power supply circuit 7. Combination meter 15. Data link connector (DLC)
C: DLC ground circuit 8. “AIR BAG” warning light 16. Ground for air system
1. Battery 9. Light driver 17. To HVAC control module (auto A/C model)
2. Main fuse 10. Junction block assembly 18. SDM
3. Fuse 11. “DOME” fuse
Page 1106 of 1556
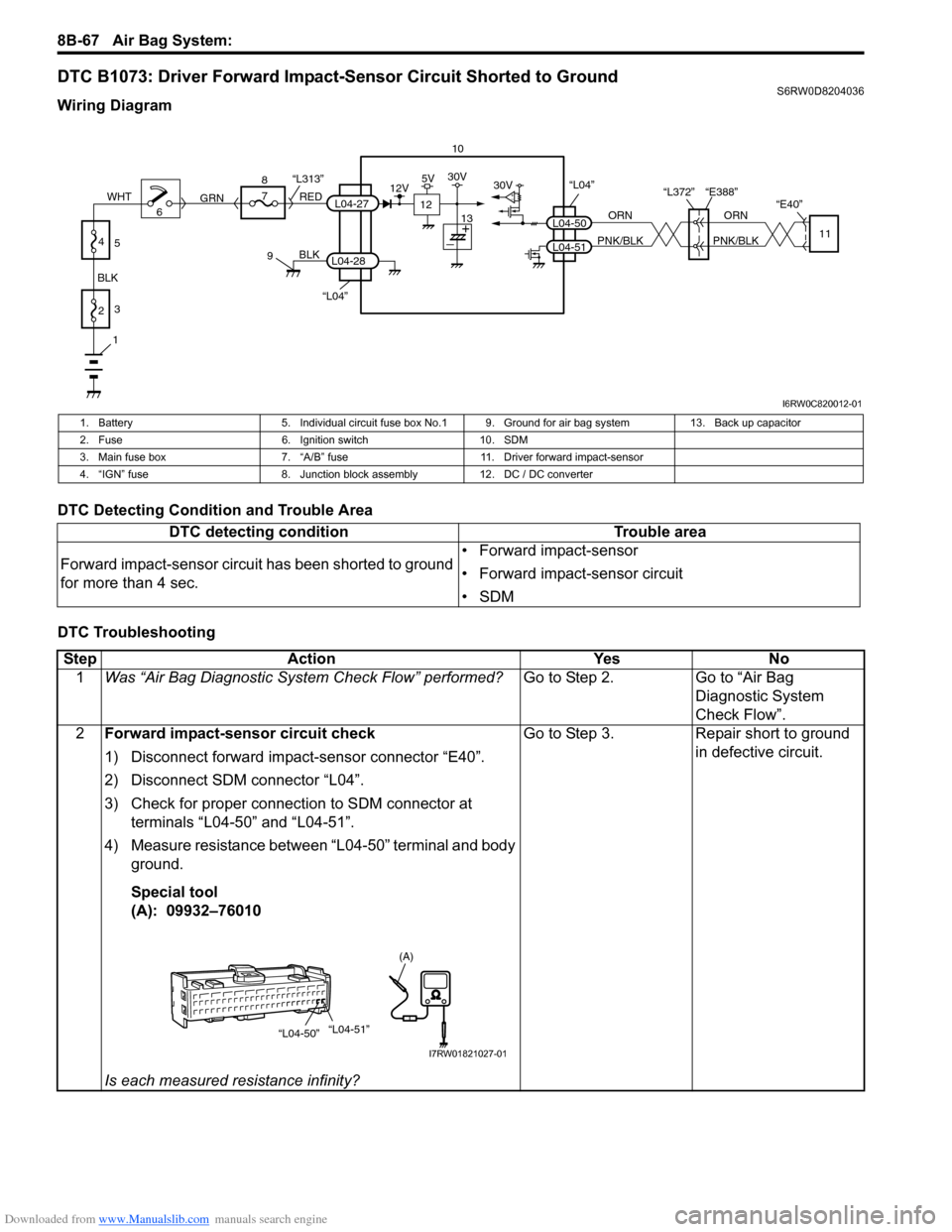
Downloaded from www.Manualslib.com manuals search engine 8B-67 Air Bag System:
DTC B1073: Driver Forward Impact-Sensor Circuit Shorted to GroundS6RW0D8204036
Wiring Diagram
DTC Detecting Condition and Trouble Area
DTC Troubleshooting
10
“L04”
“L372” “E388”
“E40”
ORN
PNK/BLKORN
PNK/BLKL04-50
L04-5111
30V
“L04”
BLK
L04-28
6 8
7
RED
GRN“L313”L04-27
9
1
2 BLKWHT3
4
5
12
12V5V30V
13
I6RW0C820012-01
1. Battery 5. Individual circuit fuse box No.1 9. Ground for air bag system 13. Back up capacitor
2. Fuse 6. Ignition switch 10. SDM
3. Main fuse box 7. “A/B” fuse 11. Driver forward impact-sensor
4. “IGN” fuse 8. Junction block assembly 12. DC / DC converter
DTC detecting condition Trouble area
Forward impact-sensor circuit has been shorted to ground
for more than 4 sec.• Forward impact-sensor
• Forward impact-sensor circuit
•SDM
Step Action Yes No
1Was “Air Bag Diagnostic System Check Flow” performed?Go to Step 2. Go to “Air Bag
Diagnostic System
Check Flow”.
2Forward impact-sensor circuit check
1) Disconnect forward impact-sensor connector “E40”.
2) Disconnect SDM connector “L04”.
3) Check for proper connection to SDM connector at
terminals “L04-50” and “L04-51”.
4) Measure resistance between “L04-50” terminal and body
ground.
Special tool
(A): 09932–76010
Is each measured resistance infinity?Go to Step 3. Repair short to ground
in defective circuit.
“L04-50”“L04-51”
(A)
I7RW01821027-01