sensor TOYOTA CAMRY V20 1986 Service Information
[x] Cancel search | Manufacturer: TOYOTA, Model Year: 1986, Model line: CAMRY V20, Model: TOYOTA CAMRY V20 1986Pages: 2389, PDF Size: 84.44 MB
Page 477 of 2389
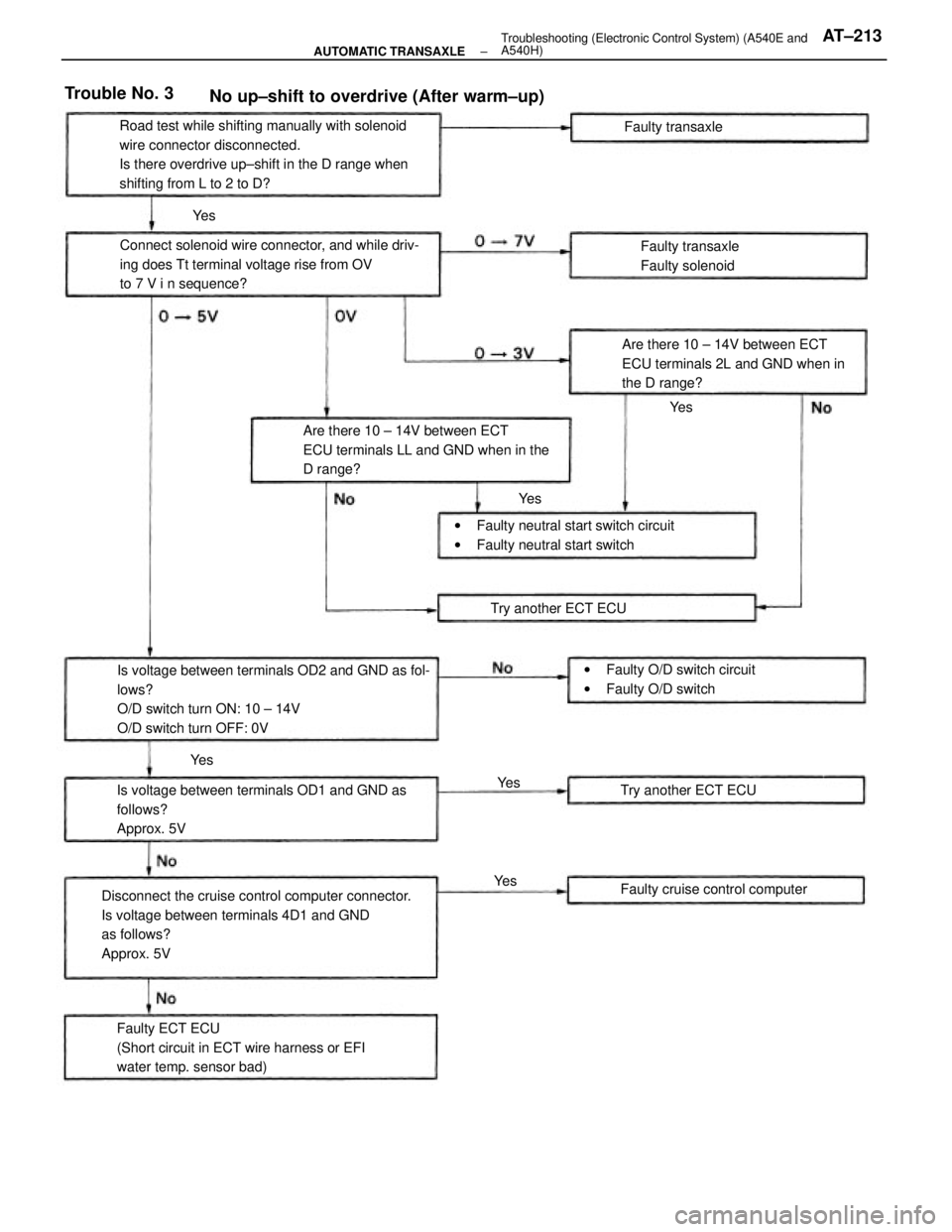
Disconnect the cruise control computer connector.
Is voltage between terminals 4D1 and GND
as follows?
Approx. 5VIs voltage between terminals OD2 and GND as fol-
lows?
O/D switch turn ON: 10 ± 14V
O/D switch turn OFF: 0VRoad test while shifting manually with solenoid
wire connector disconnected.
Is there overdrive up±shift in the D range when
shifting from L to 2 to D?
Is voltage between terminals OD1 and GND as
follows?
Approx. 5VConnect solenoid wire connector, and while driv-
ing does Tt terminal voltage rise from OV
to 7 V i n sequence?
Faulty ECT ECU
(Short circuit in ECT wire harness or EFI
water temp. sensor bad)Are there 10 ± 14V between ECT
ECU terminals LL and GND when in the
D range?
No up±shift to overdrive (After warm±up)
Are there 10 ± 14V between ECT
ECU terminals 2L and GND when in
the D range?
wFaulty neutral start switch circuit
wFaulty neutral start switch
wFaulty O/D switch circuit
wFaulty O/D switch
Faulty cruise control computerFaulty transaxle
Faulty solenoid
Try another ECT ECU Try another ECT ECUFaulty transaxle
Trouble No. 3
Ye sYe s
Ye s
Ye sYe s Ye s
± AUTOMATIC TRANSAXLETroubleshooting (Electronic Control System) (A540E and
A540H)AT±213
Page 479 of 2389
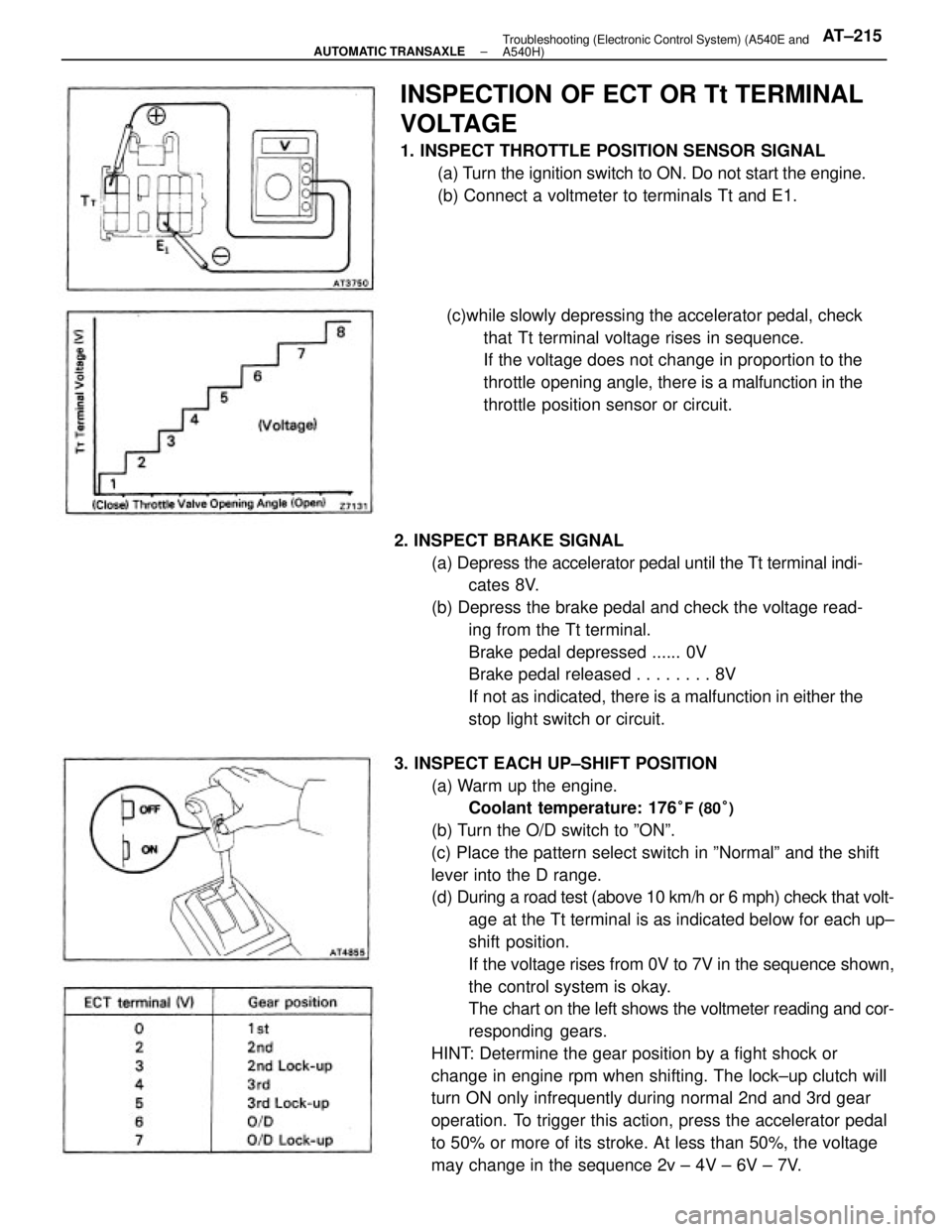
3. INSPECT EACH UP±SHIFT POSITION
(a) Warm up the engine.
Coolant temperature: 176
°F (80°)
(b) Turn the O/D switch to ºONº.
(c) Place the pattern select switch in ºNormalº and the shift
lever into the D range.
(d) During a road test (above 10 km/h or 6 mph) check that volt-
age at the Tt terminal is as indicated below for each up±
shift position.
If the voltage rises from 0V to 7V in the sequence shown,
the control system is okay.
The chart on the left shows the voltmeter reading and cor-
responding gears.
HINT: Determine the gear position by a fight shock or
change in engine rpm when shifting. The lock±up clutch will
turn ON only infrequently during normal 2nd and 3rd gear
operation. To trigger this action, press the accelerator pedal
to 50% or more of its stroke. At less than 50%, the voltage
may change in the sequence 2v ± 4V ± 6V ± 7V. 2. INSPECT BRAKE SIGNAL
(a) Depress the accelerator pedal until the Tt terminal indi-
cates 8V.
(b) Depress the brake pedal and check the voltage read-
ing from the Tt terminal.
Brake pedal depressed ...... 0V
Brake pedal released . . . . . . . . 8V
If not as indicated, there is a malfunction in either the
stop light switch or circuit.
INSPECTION OF ECT OR Tt TERMINAL
VOLTAGE
1. INSPECT THROTTLE POSITION SENSOR SIGNAL
(a) Turn the ignition switch to ON. Do not start the engine.
(b) Connect a voltmeter to terminals Tt and E1.
(c)while slowly depressing the accelerator pedal, check
that Tt terminal voltage rises in sequence.
If the voltage does not change in proportion to the
throttle opening angle, there is a malfunction in the
throttle position sensor or circuit.
± AUTOMATIC TRANSAXLETroubleshooting (Electronic Control System) (A540E and
A540H)AT±215
Page 484 of 2389
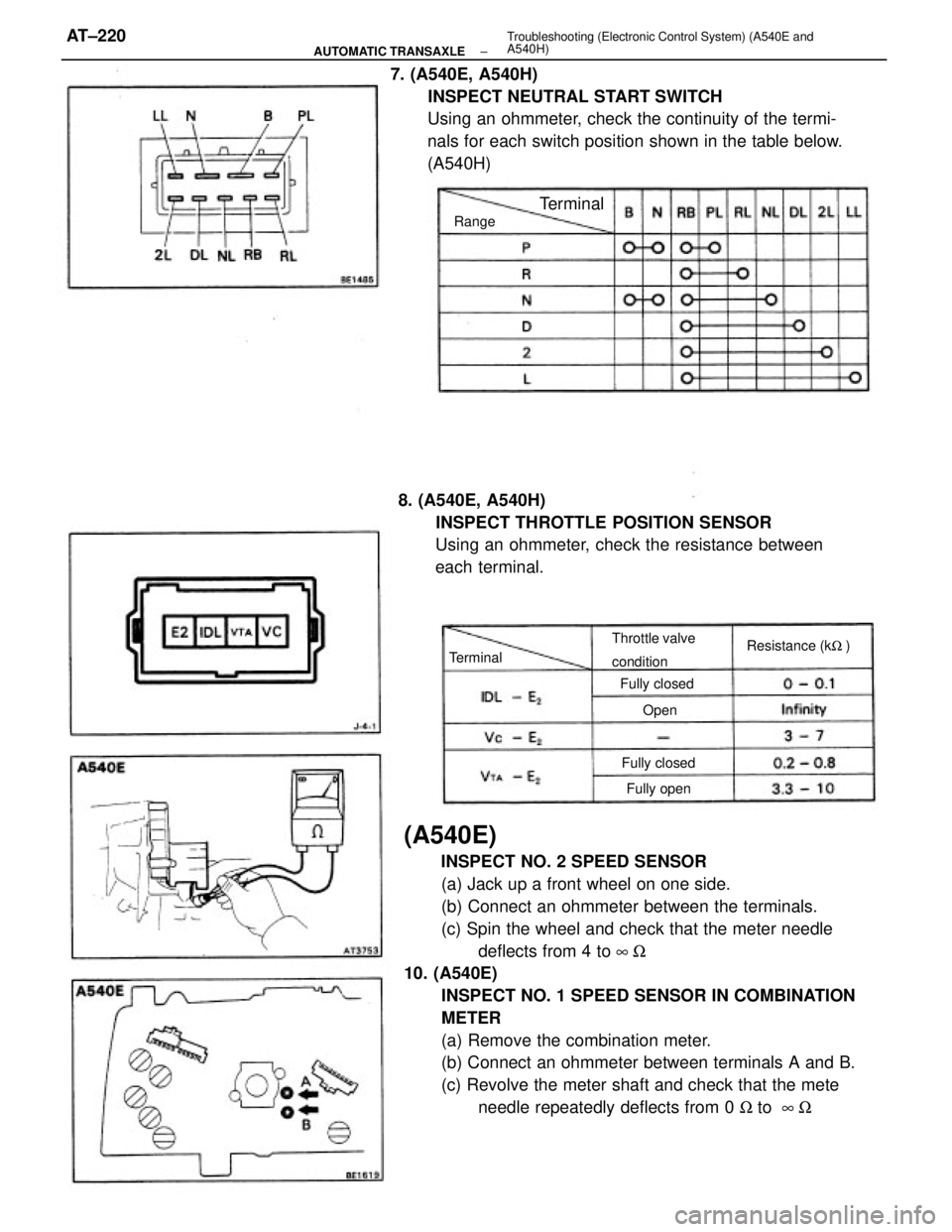
(A540E)
INSPECT NO. 2 SPEED SENSOR
(a) Jack up a front wheel on one side.
(b) Connect an ohmmeter between the terminals.
(c) Spin the wheel and check that the meter needle
deflects from 4 to 8W
10. (A540E)
INSPECT NO. 1 SPEED SENSOR IN COMBINATION
METER
(a) Remove the combination meter.
(b) Connect an ohmmeter between terminals A and B.
(c) Revolve the meter shaft and check that the mete
needle repeatedly deflects from 0 W to 8W 7. (A540E, A540H)
INSPECT NEUTRAL START SWITCH
Using an ohmmeter, check the continuity of the termi-
nals for each switch position shown in the table below.
(A540H)
8. (A540E, A540H)
INSPECT THROTTLE POSITION SENSOR
Using an ohmmeter, check the resistance between
each terminal.
Throttle valve
conditionResistance (kW )
Fully closed
Fully closed
Fully open
Terminal
TerminalRange
Open
± AUTOMATIC TRANSAXLETroubleshooting (Electronic Control System) (A540E and
A540H)AT±220
Page 485 of 2389
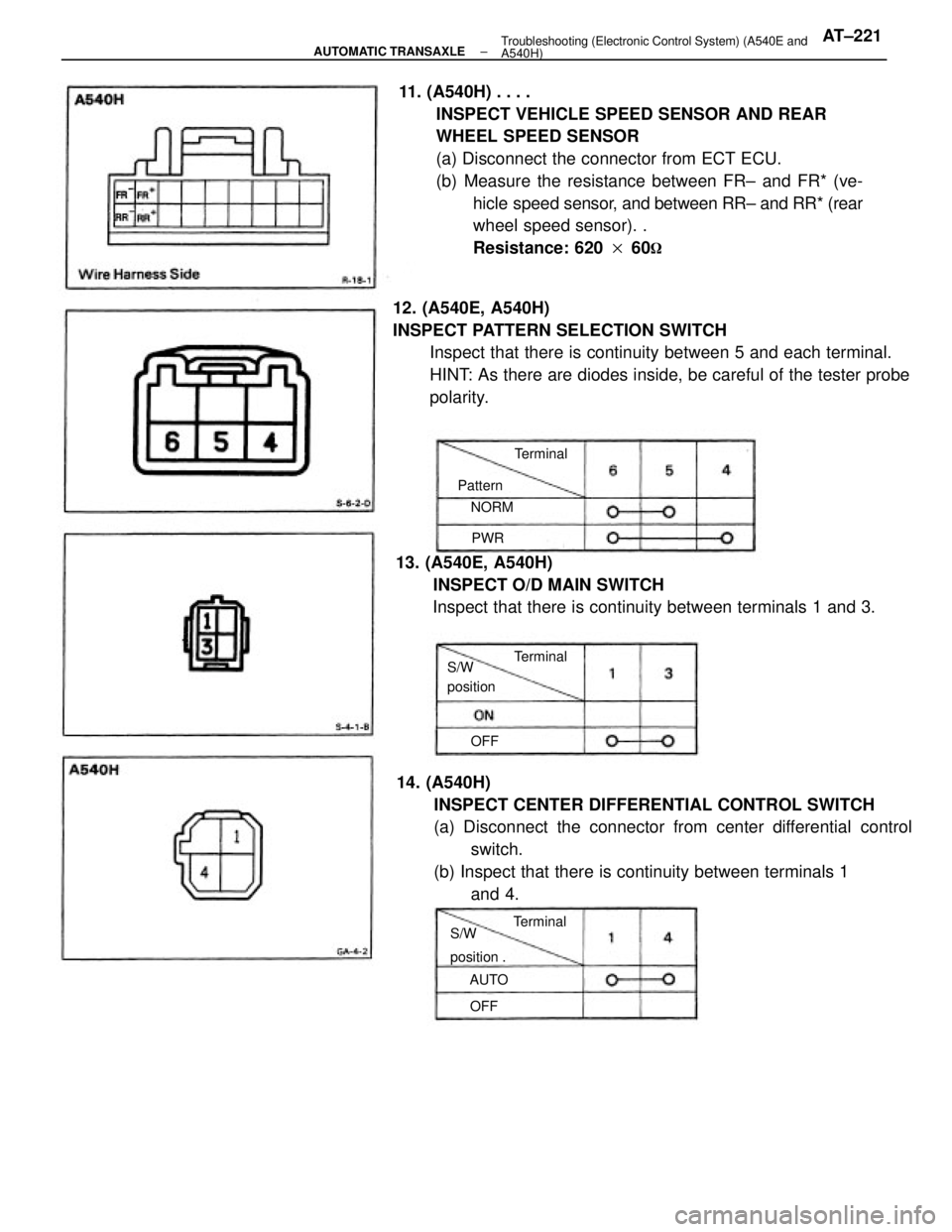
11. (A540H) . . . .
INSPECT VEHICLE SPEED SENSOR AND REAR
WHEEL SPEED SENSOR
(a) Disconnect the connector from ECT ECU.
(b) Measure the resistance between FR± and FR* (ve-
hicle speed sensor, and between RR± and RR* (rear
wheel speed sensor). .
Resistance: 620 60
12. (A540E, A540H)
INSPECT PATTERN SELECTION SWITCH
Inspect that there is continuity between 5 and each terminal.
HINT: As there are diodes inside, be careful of the tester probe
polarity.
14. (A540H)
INSPECT CENTER DIFFERENTIAL CONTROL SWITCH
(a) Disconnect the connector from center differential control
switch.
(b) Inspect that there is continuity between terminals 1
and 4. 13. (A540E, A540H)
INSPECT O/D MAIN SWITCH
Inspect that there is continuity between terminals 1 and 3.
S/W
position . S/W
positionTerminal
TerminalTerminal NORM Pattern
AUTOPWR
OFFOFF
± AUTOMATIC TRANSAXLETroubleshooting (Electronic Control System) (A540E and
A540H)AT±221
Page 509 of 2389
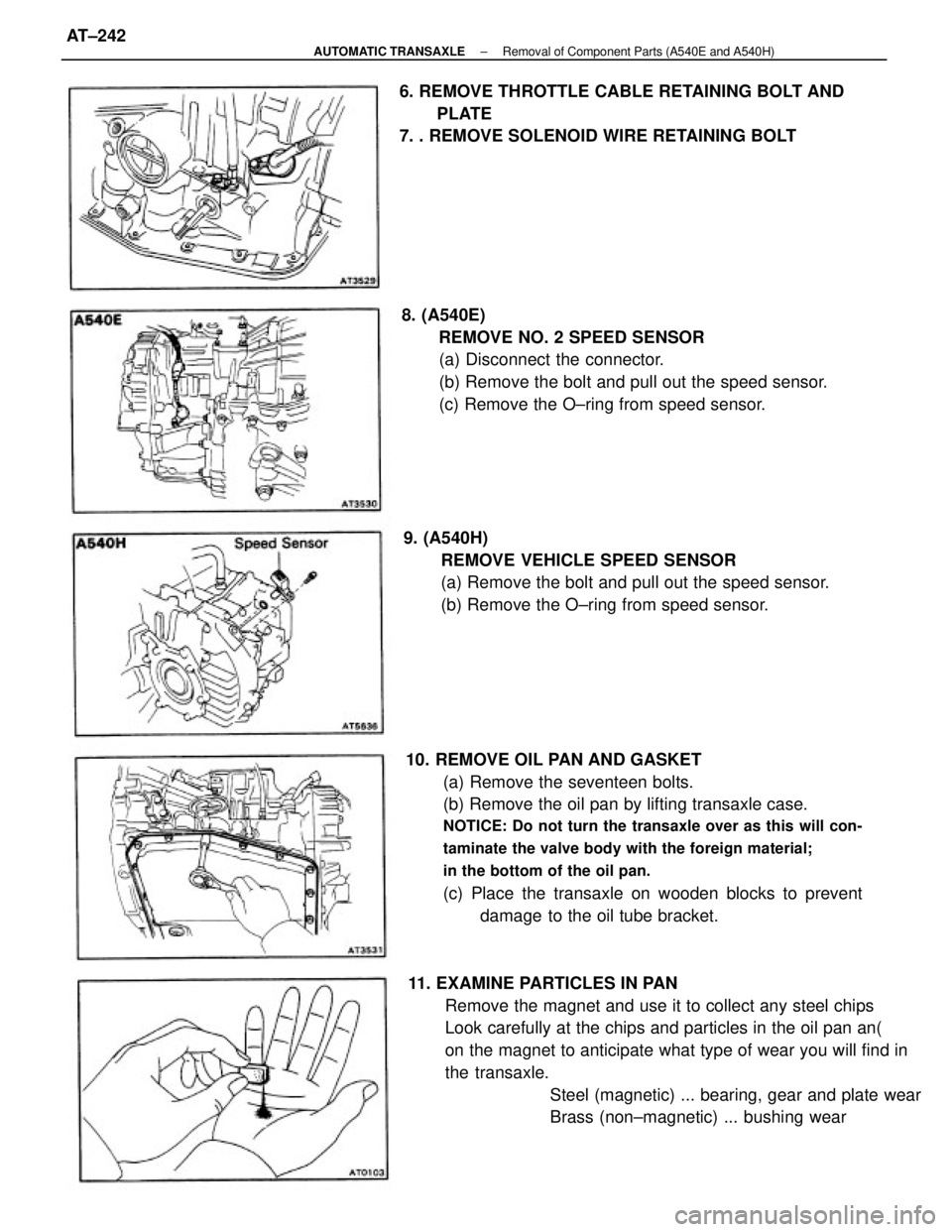
10. REMOVE OIL PAN AND GASKET
(a) Remove the seventeen bolts.
(b) Remove the oil pan by lifting transaxle case.
NOTICE: Do not turn the transaxle over as this will con-
taminate the valve body with the foreign material;
in the bottom of the oil pan.
(c) Place the transaxle on wooden blocks to prevent
damage to the oil tube bracket.
11. EXAMINE PARTICLES IN PAN
Remove the magnet and use it to collect any steel chips
Look carefully at the chips and particles in the oil pan an(
on the magnet to anticipate what type of wear you will find in
the transaxle.
Steel (magnetic) ... bearing, gear and plate wear
Brass (non±magnetic) ... bushing wear 8. (A540E)
REMOVE NO. 2 SPEED SENSOR
(a) Disconnect the connector.
(b) Remove the bolt and pull out the speed sensor.
(c) Remove the O±ring from speed sensor.
9. (A540H)
REMOVE VEHICLE SPEED SENSOR
(a) Remove the bolt and pull out the speed sensor.
(b) Remove the O±ring from speed sensor. 6. REMOVE THROTTLE CABLE RETAINING BOLT AND
PLATE
7. . REMOVE SOLENOID WIRE RETAINING BOLT
± AUTOMATIC TRANSAXLERemoval of Component Parts (A540E and A540H)AT±242
Page 527 of 2389
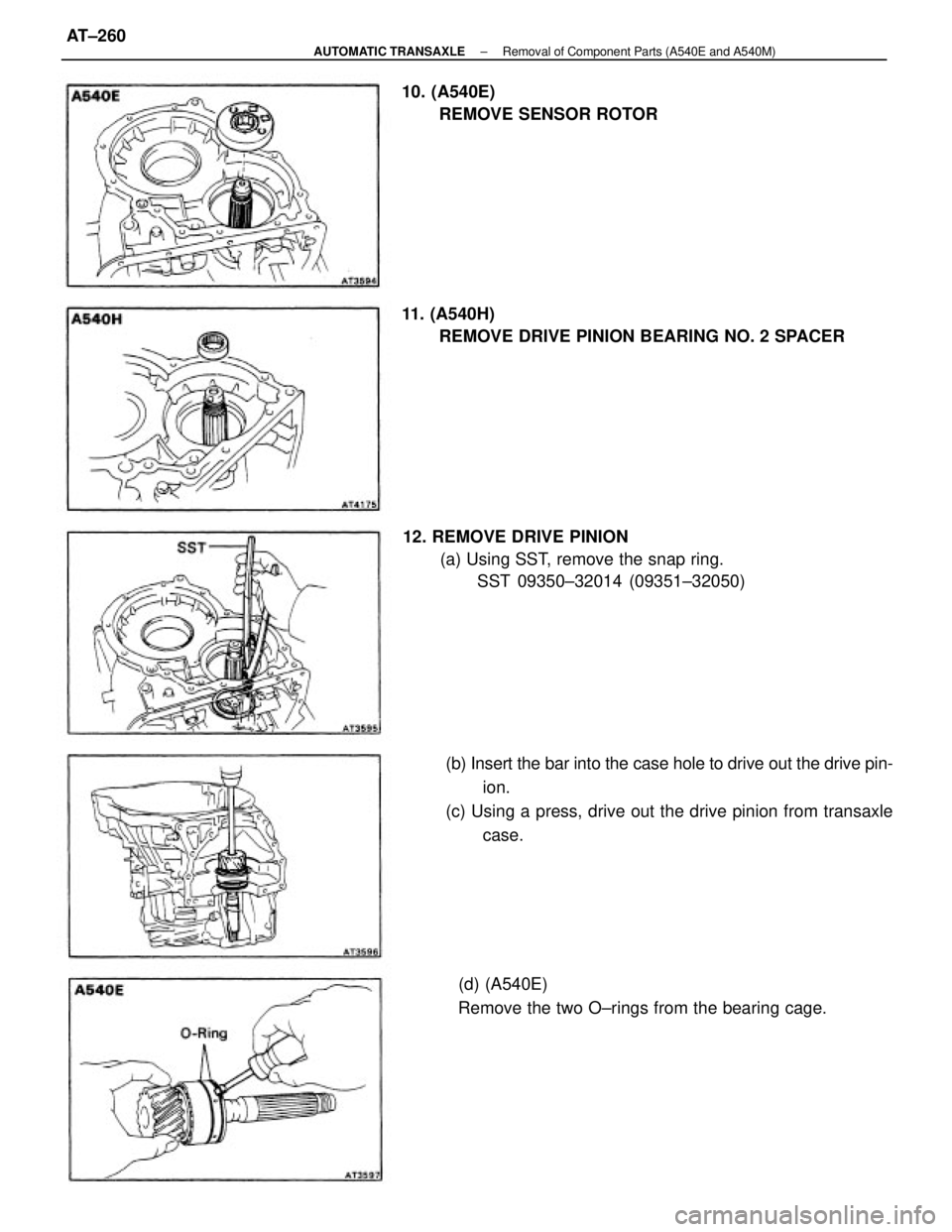
(b) Insert the bar into the case hole to drive out the drive pin-
ion.
(c) Using a press, drive out the drive pinion from transaxle
case. 11. (A540H)
REMOVE DRIVE PINION BEARING NO. 2 SPACER
12. REMOVE DRIVE PINION
(a) Using SST, remove the snap ring.
SST 09350±32014 (09351±32050)
(d) (A540E)
Remove the two O±rings from the bearing cage. 10. (A540E)
REMOVE SENSOR ROTOR
± AUTOMATIC TRANSAXLERemoval of Component Parts (A540E and A540M)AT±260
Page 585 of 2389
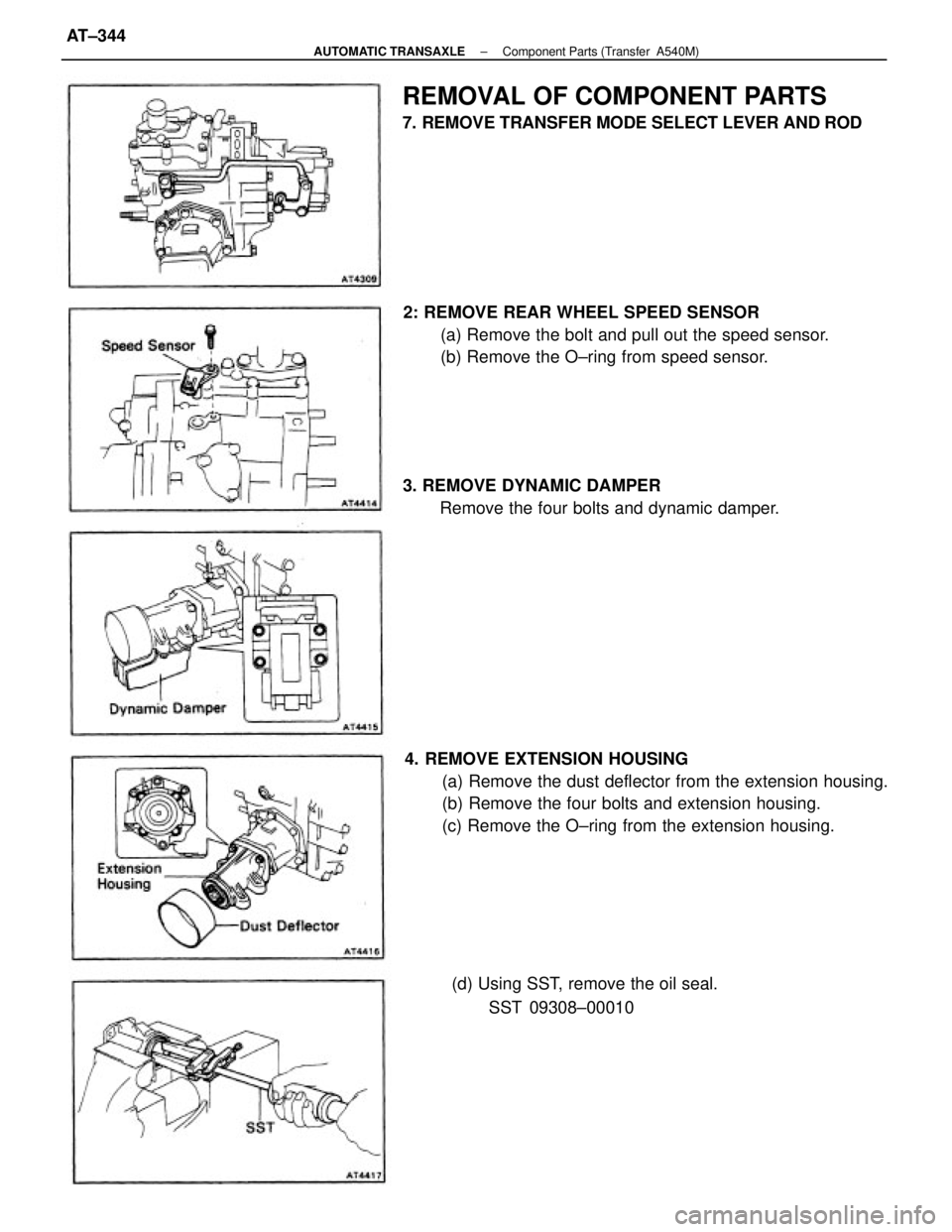
4. REMOVE EXTENSION HOUSING
(a) Remove the dust deflector from the extension housing.
(b) Remove the four bolts and extension housing.
(c) Remove the O±ring from the extension housing. 3. REMOVE DYNAMIC DAMPER
Remove the four bolts and dynamic damper.
REMOVAL OF COMPONENT PARTS
7. REMOVE TRANSFER MODE SELECT LEVER AND ROD
2: REMOVE REAR WHEEL SPEED SENSOR
(a) Remove the bolt and pull out the speed sensor.
(b) Remove the O±ring from speed sensor.
(d) Using SST, remove the oil seal.
SST 09308±00010
± AUTOMATIC TRANSAXLEComponent Parts (Transfer A540M)AT±344
Page 635 of 2389
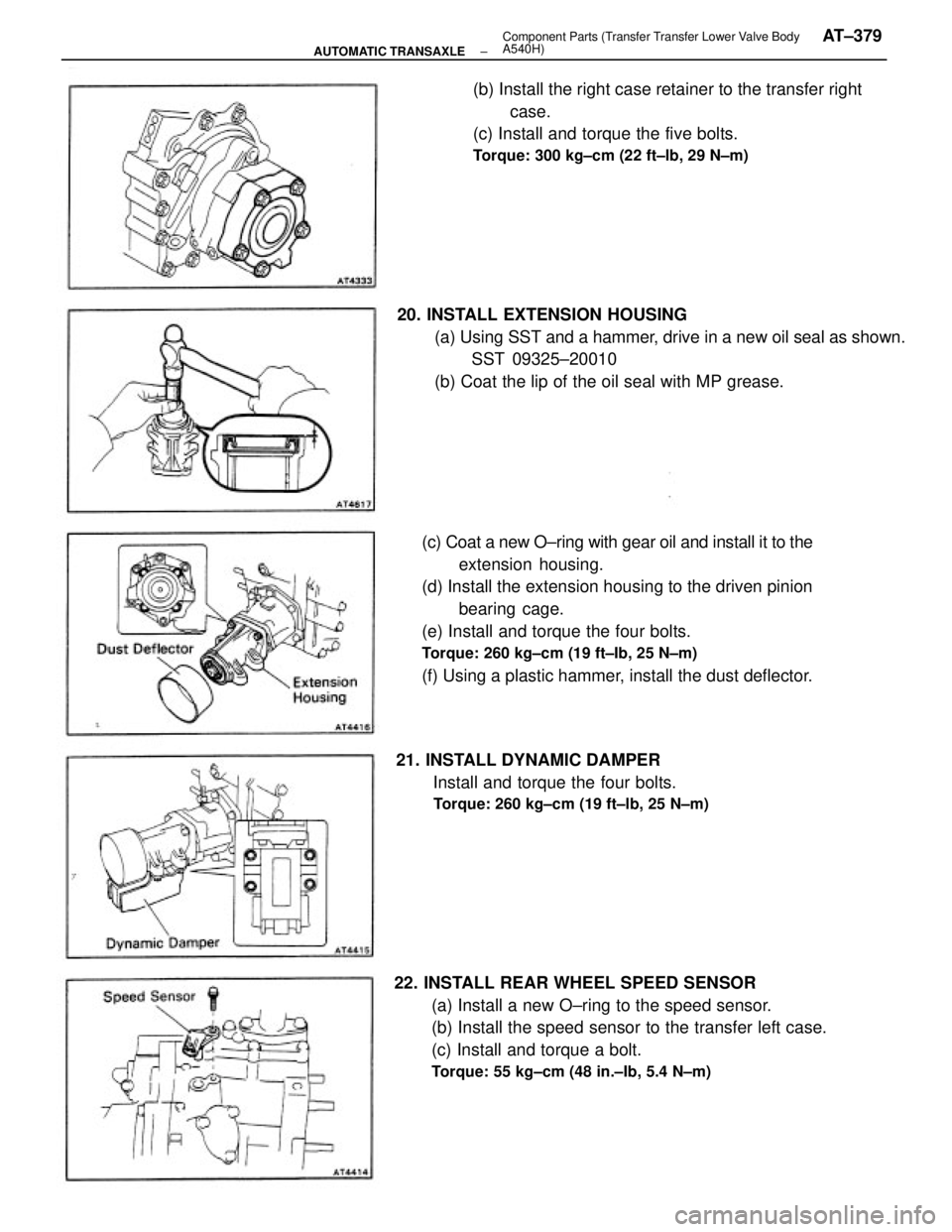
(c) Coat a new O±ring with gear oil and install it to the
extension housing.
(d) Install the extension housing to the driven pinion
bearing cage.
(e) Install and torque the four bolts.
Torque: 260 kg±cm (19 ft±Ib, 25 N±m)
(f) Using a plastic hammer, install the dust deflector. 20. INSTALL EXTENSION HOUSING
(a) Using SST and a hammer, drive in a new oil seal as shown.
SST 09325±20010
(b) Coat the lip of the oil seal with MP grease.
22. INSTALL REAR WHEEL SPEED SENSOR
(a) Install a new O±ring to the speed sensor.
(b) Install the speed sensor to the transfer left case.
(c) Install and torque a bolt.
Torque: 55 kg±cm (48 in.±Ib, 5.4 N±m)
(b) Install the right case retainer to the transfer right
case.
(c) Install and torque the five bolts.
Torque: 300 kg±cm (22 ft±lb, 29 N±m)
21. INSTALL DYNAMIC DAMPER
Install and torque the four bolts.
Torque: 260 kg±cm (19 ft±lb, 25 N±m)
± AUTOMATIC TRANSAXLEComponent Parts (Transfer Transfer Lower Valve Body
A540H)AT±379
Page 642 of 2389
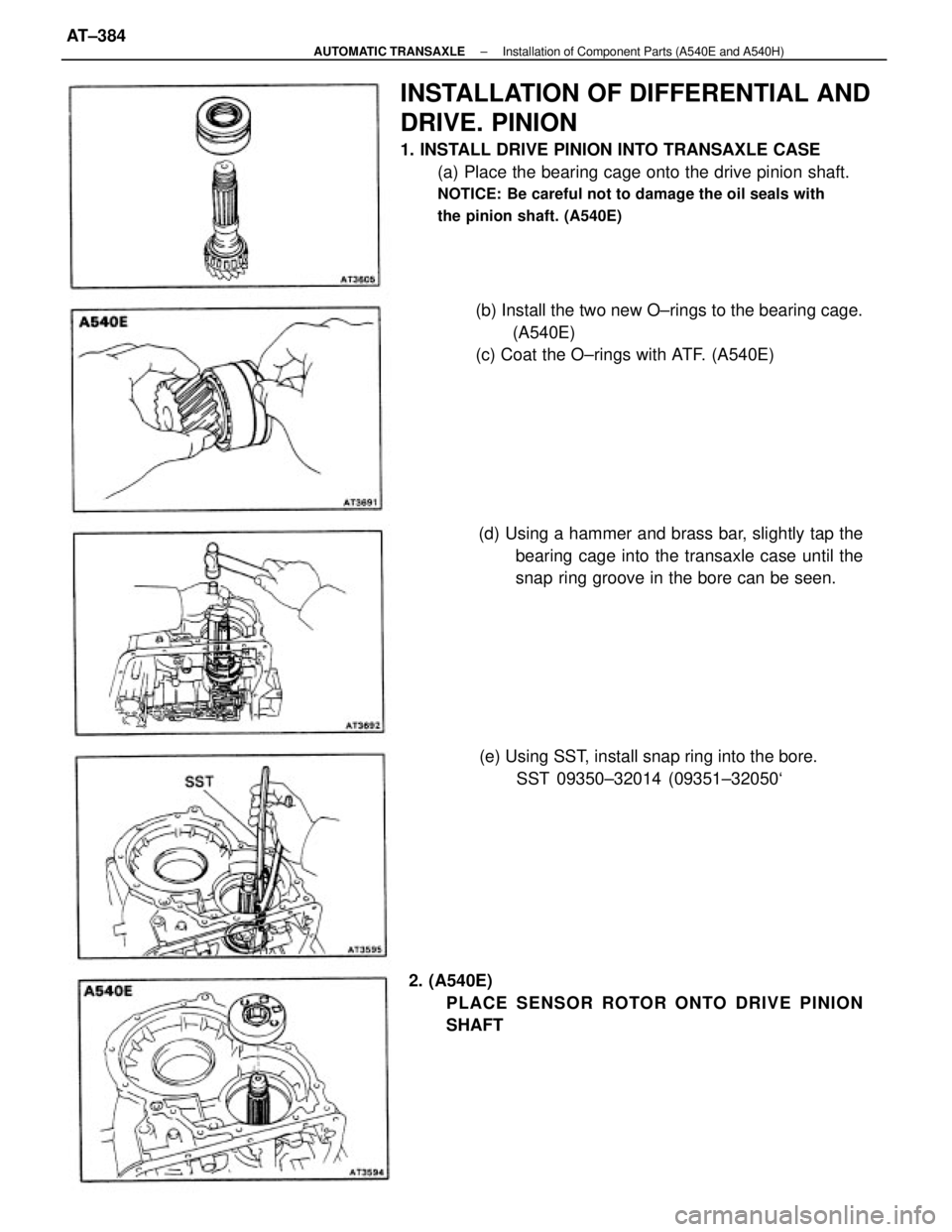
INSTALLATION OF DIFFERENTIAL AND
DRIVE. PINION
1. INSTALL DRIVE PINION INTO TRANSAXLE CASE
(a) Place the bearing cage onto the drive pinion shaft.
NOTICE: Be careful not to damage the oil seals with
the pinion shaft. (A540E)
(b) Install the two new O±rings to the bearing cage.
(A540E)
(c) Coat the O±rings with ATF. (A540E)
(d) Using a hammer and brass bar, slightly tap the
bearing cage into the transaxle case until the
snap ring groove in the bore can be seen.
(e) Using SST, install snap ring into the bore.
SST 09350±32014 (09351±32050`
2. (A540E)
PLACE SENSOR ROTOR ONTO DRIVE PINION
SHAFT
± AUTOMATIC TRANSAXLEInstallation of Component Parts (A540E and A540H)AT±384
Page 664 of 2389
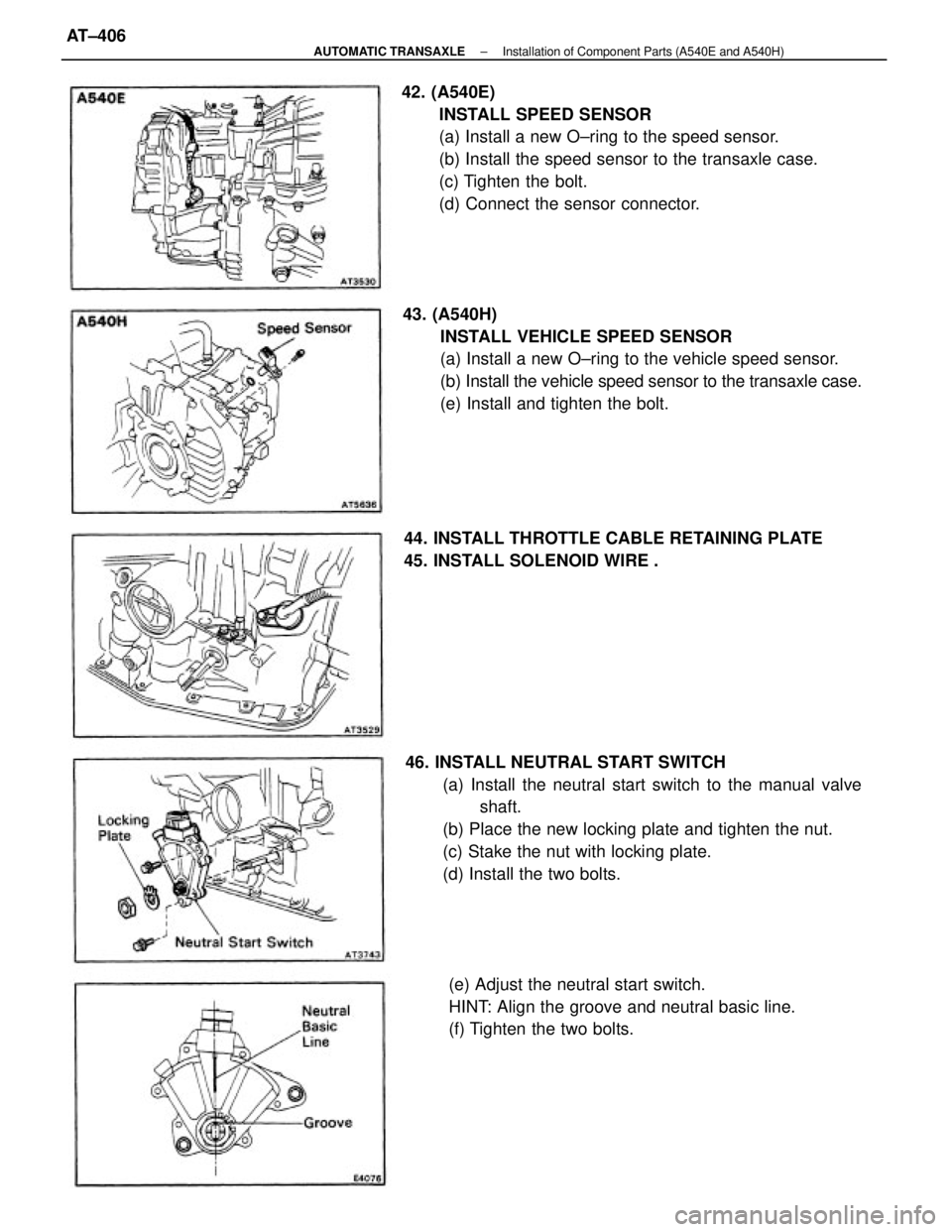
46. INSTALL NEUTRAL START SWITCH
(a) Install the neutral start switch to the manual valve
shaft.
(b) Place the new locking plate and tighten the nut.
(c) Stake the nut with locking plate.
(d) Install the two bolts. 42. (A540E)
INSTALL SPEED SENSOR
(a) Install a new O±ring to the speed sensor.
(b) Install the speed sensor to the transaxle case.
(c) Tighten the bolt.
(d) Connect the sensor connector.
43. (A540H)
INSTALL VEHICLE SPEED SENSOR
(a) Install a new O±ring to the vehicle speed sensor.
(b) Install the vehicle speed sensor to the transaxle case.
(e) Install and tighten the bolt.
(e) Adjust the neutral start switch.
HINT: Align the groove and neutral basic line.
(f) Tighten the two bolts. 44. INSTALL THROTTLE CABLE RETAINING PLATE
45. INSTALL SOLENOID WIRE .
± AUTOMATIC TRANSAXLEInstallation of Component Parts (A540E and A540H)AT±406