sensor TOYOTA CAMRY V20 1986 Service Information
[x] Cancel search | Manufacturer: TOYOTA, Model Year: 1986, Model line: CAMRY V20, Model: TOYOTA CAMRY V20 1986Pages: 2389, PDF Size: 84.44 MB
Page 340 of 2389
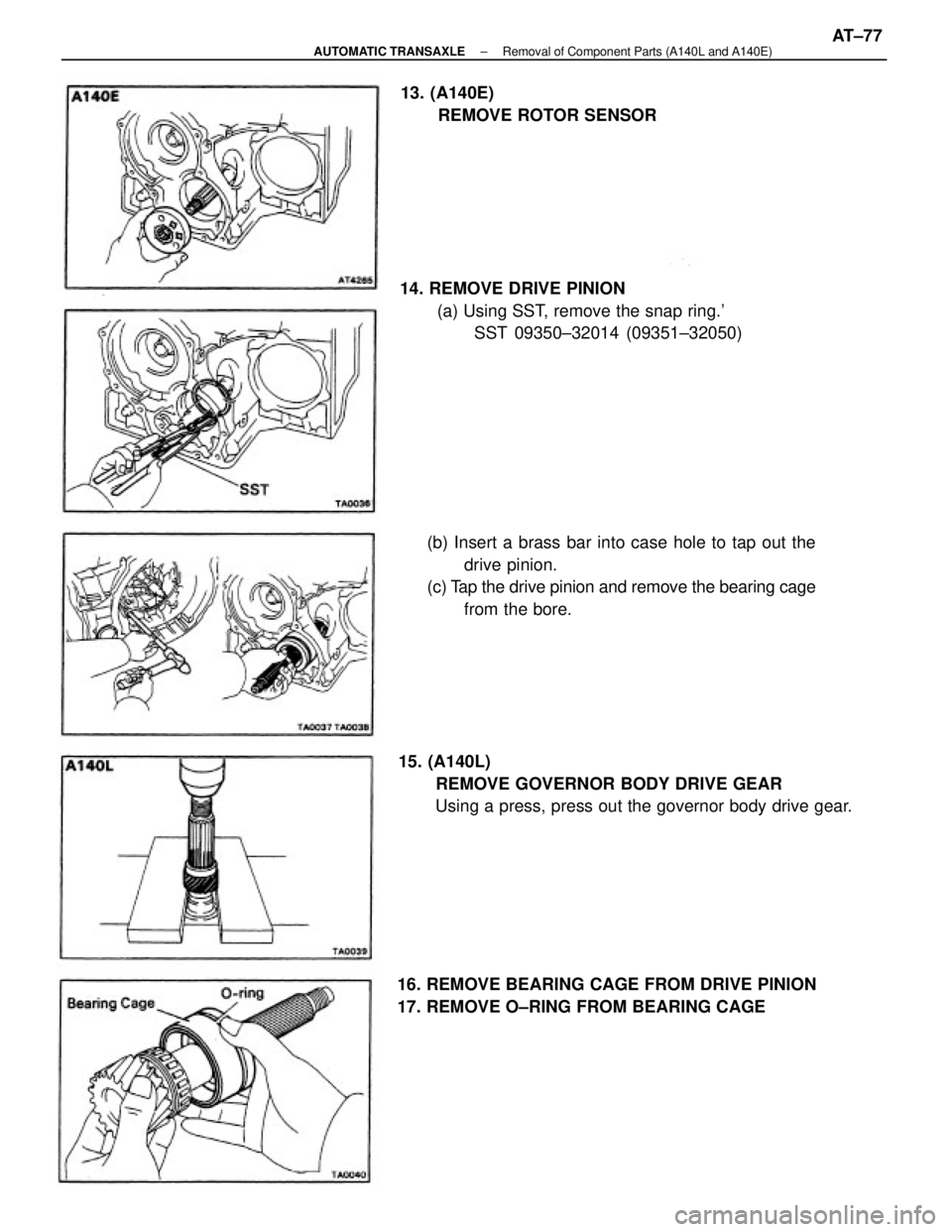
(b) Insert a brass bar into case hole to tap out the
drive pinion.
(c) Tap the drive pinion and remove the bearing cage
from the bore. 14. REMOVE DRIVE PINION
(a) Using SST, remove the snap ring.'
SST 09350±32014 (09351±32050)
15. (A140L)
REMOVE GOVERNOR BODY DRIVE GEAR
Using a press, press out the governor body drive gear.
16. REMOVE BEARING CAGE FROM DRIVE PINION
17. REMOVE O±RING FROM BEARING CAGE13. (A140E)
REMOVE ROTOR SENSOR
± AUTOMATIC TRANSAXLERemoval of Component Parts (A140L and A140E)AT±77
Page 408 of 2389
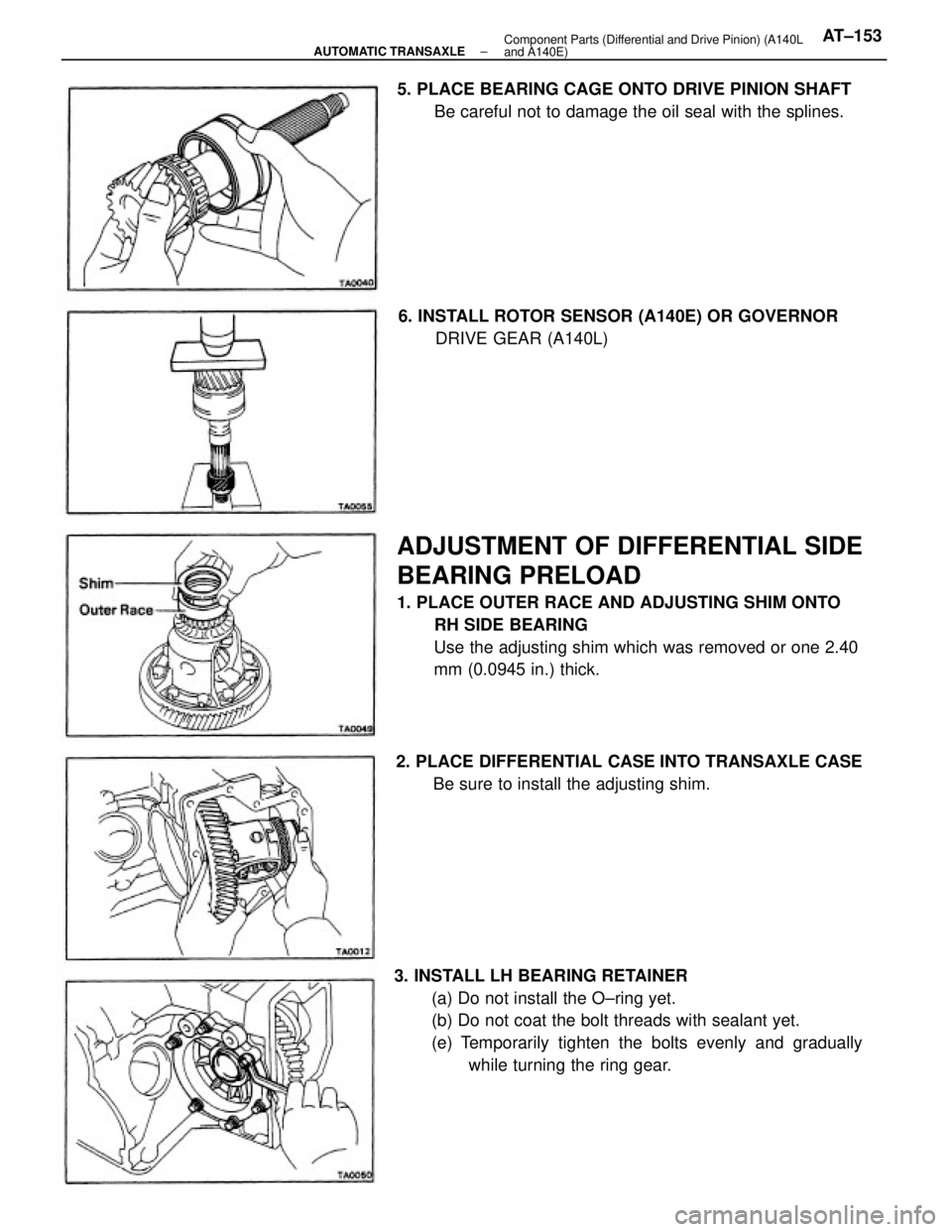
3. INSTALL LH BEARING RETAINER
(a) Do not install the O±ring yet.
(b) Do not coat the bolt threads with sealant yet.
(e) Temporarily tighten the bolts evenly and gradually
while turning the ring gear.
ADJUSTMENT OF DIFFERENTIAL SIDE
BEARING PRELOAD
1. PLACE OUTER RACE AND ADJUSTING SHIM ONTO
RH SIDE BEARING
Use the adjusting shim which was removed or one 2.40
mm (0.0945 in.) thick. 5. PLACE BEARING CAGE ONTO DRIVE PINION SHAFT
Be careful not to damage the oil seal with the splines.
2. PLACE DIFFERENTIAL CASE INTO TRANSAXLE CASE
Be sure to install the adjusting shim. 6. INSTALL ROTOR SENSOR (A140E) OR GOVERNOR
DRIVE GEAR (A140L)
± AUTOMATIC TRANSAXLEComponent Parts (Differential and Drive Pinion) (A140L
and A140E)AT±153
Page 414 of 2389
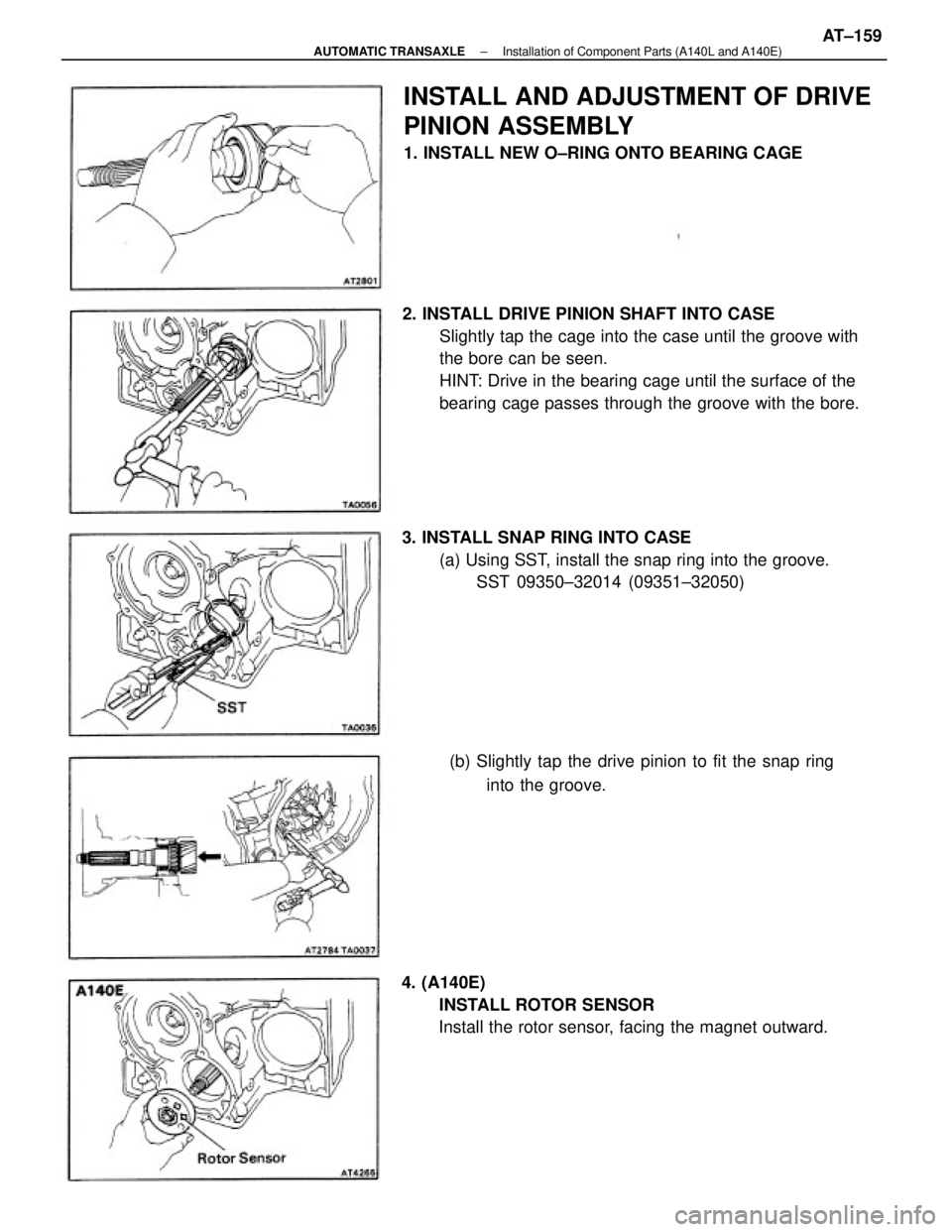
2. INSTALL DRIVE PINION SHAFT INTO CASE
Slightly tap the cage into the case until the groove with
the bore can be seen.
HINT: Drive in the bearing cage until the surface of the
bearing cage passes through the groove with the bore.
INSTALL AND ADJUSTMENT OF DRIVE
PINION ASSEMBLY
1. INSTALL NEW O±RING ONTO BEARING CAGE
3. INSTALL SNAP RING INTO CASE
(a) Using SST, install the snap ring into the groove.
SST 09350±32014 (09351±32050)
4. (A140E)
INSTALL ROTOR SENSOR
Install the rotor sensor, facing the magnet outward.(b) Slightly tap the drive pinion to fit the snap ring
into the groove.
± AUTOMATIC TRANSAXLEInstallation of Component Parts (A140L and A140E)AT±159
Page 435 of 2389
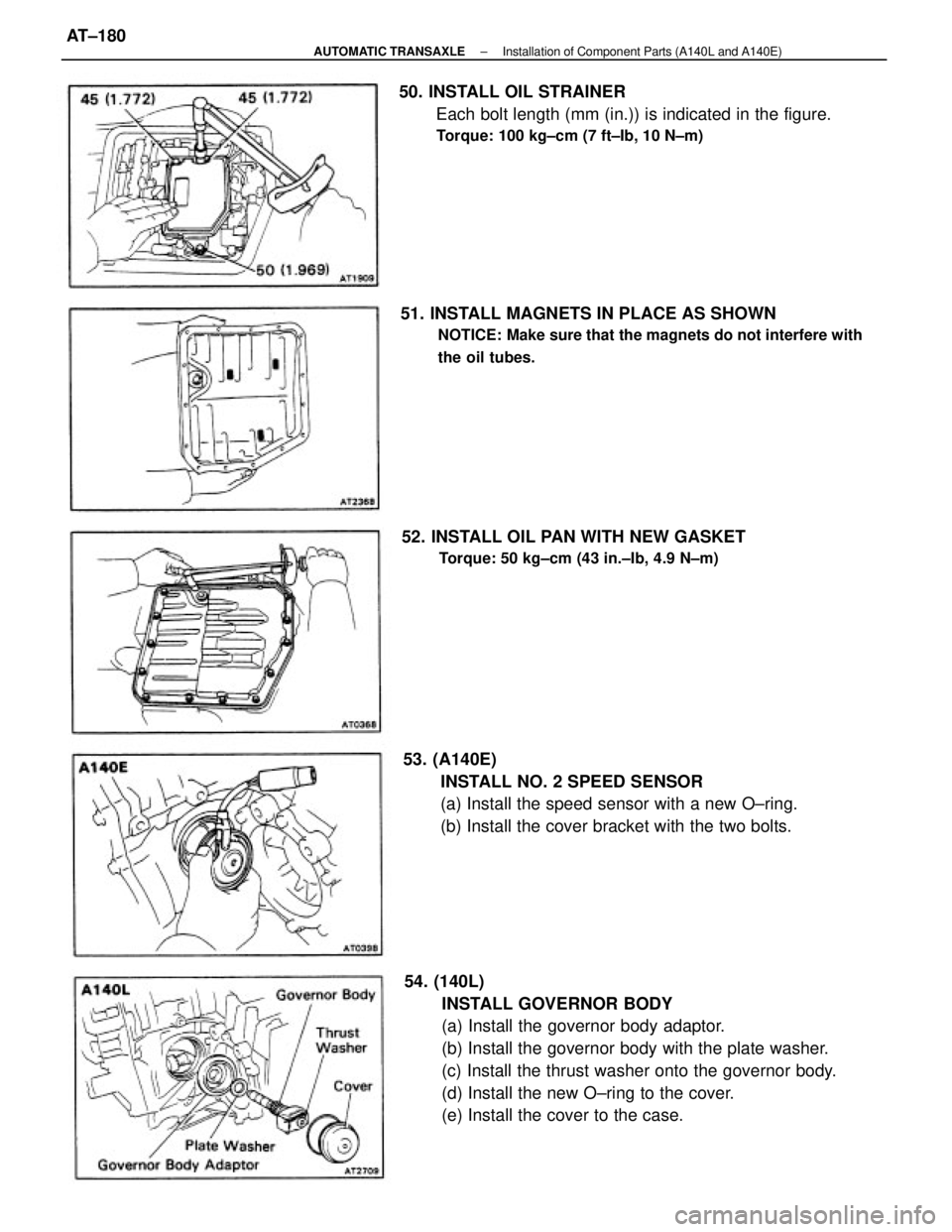
54. (140L)
INSTALL GOVERNOR BODY
(a) Install the governor body adaptor.
(b) Install the governor body with the plate washer.
(c) Install the thrust washer onto the governor body.
(d) Install the new O±ring to the cover.
(e) Install the cover to the case. 53. (A140E)
INSTALL NO. 2 SPEED SENSOR
(a) Install the speed sensor with a new O±ring.
(b) Install the cover bracket with the two bolts. 50. INSTALL OIL STRAINER
Each bolt length (mm (in.)) is indicated in the figure.
Torque: 100 kg±cm (7 ft±Ib, 10 N±m)
51. INSTALL MAGNETS IN PLACE AS SHOWN
NOTICE: Make sure that the magnets do not interfere with
the oil tubes.
52. INSTALL OIL PAN WITH NEW GASKET
Torque: 50 kg±cm (43 in.±Ib, 4.9 N±m)
± AUTOMATIC TRANSAXLEInstallation of Component Parts (A140L and A140E)AT±180
Page 444 of 2389
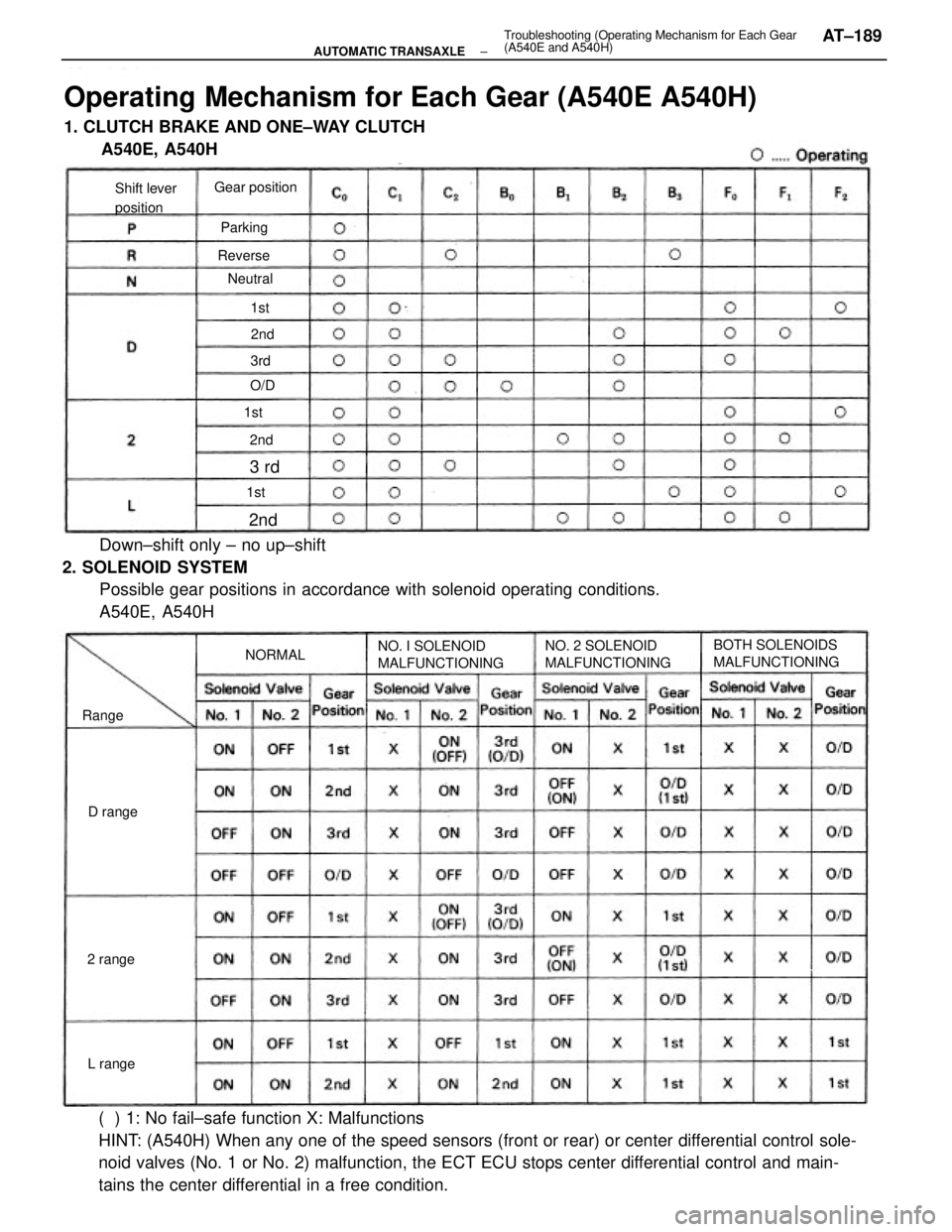
( ) 1: No fail±safe function X: Malfunctions
HINT: (A540H) When any one of the speed sensors (front or rear) or center differential control sole-
noid valves (No. 1 or No. 2) malfunction, the ECT ECU stops center differential control and main-
tains the center differential in a free condition.
Operating Mechanism for Each Gear (A540E A540H)
1. CLUTCH BRAKE AND ONE±WAY CLUTCH
A540E, A540H
Down±shift only ± no up±shift
2. SOLENOID SYSTEM
Possible gear positions in accordance with solenoid operating conditions.
A540E, A540H
NO. 2 SOLENOID
MALFUNCTIONING NO. I SOLENOID
MALFUNCTIONINGBOTH SOLENOIDS
MALFUNCTIONING Shift lever
positionGear position
NORMAL
D rangeParking
2 range
L rangeReverse
Neutral
Range
2nd3 rd
O/D
2nd1st
1st 1st2nd
3rd
± AUTOMATIC TRANSAXLETroubleshooting (Operating Mechanism for Each Gear
(A540E and A540H)AT±189
Page 445 of 2389
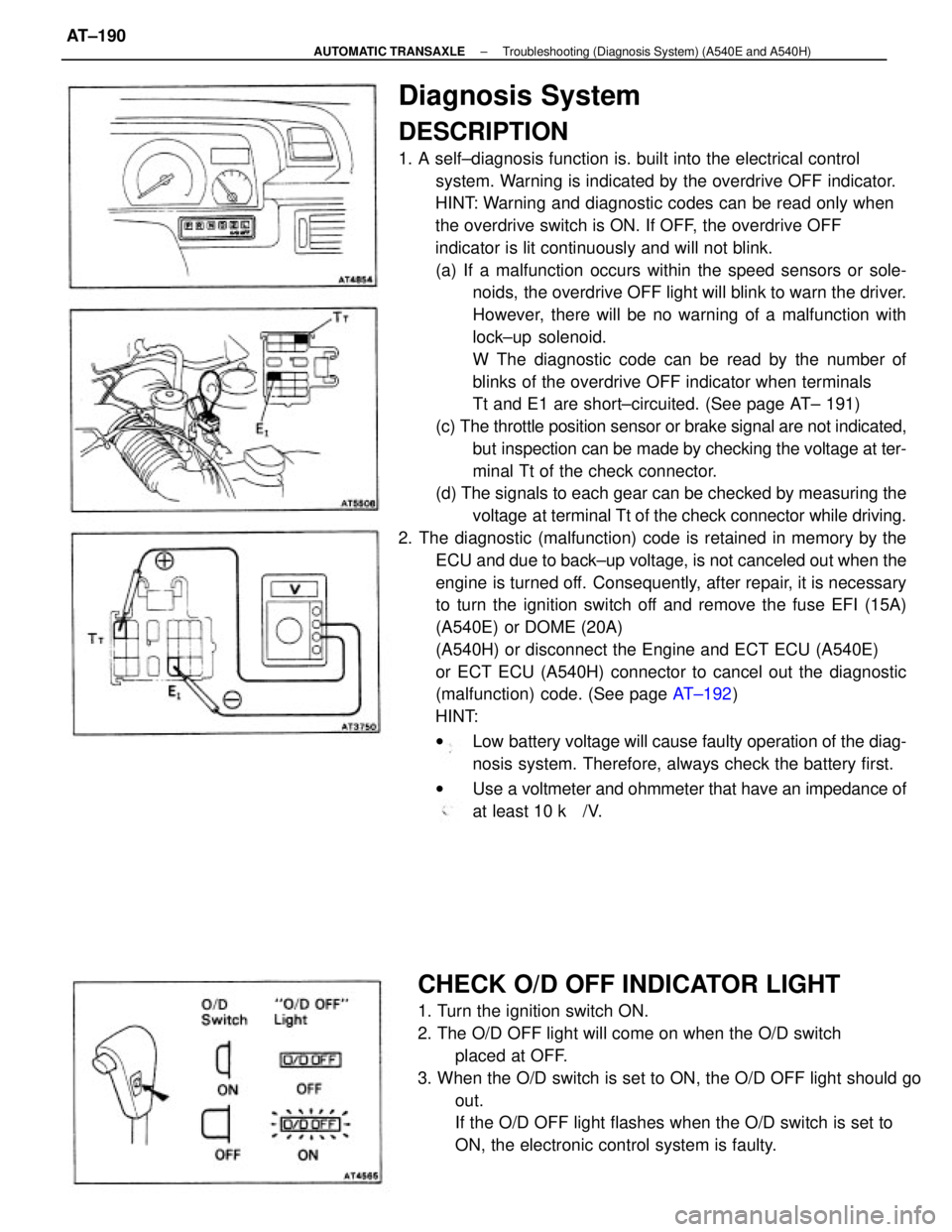
Diagnosis System
DESCRIPTION
1. A self±diagnosis function is. built into the electrical control
system. Warning is indicated by the overdrive OFF indicator.
HINT: Warning and diagnostic codes can be read only when
the overdrive switch is ON. If OFF, the overdrive OFF
indicator is lit continuously and will not blink.
(a) If a malfunction occurs within the speed sensors or sole-
noids, the overdrive OFF light will blink to warn the driver.
However, there will be no warning of a malfunction with
lock±up solenoid.
W The diagnostic code can be read by the number of
blinks of the overdrive OFF indicator when terminals
Tt and E1 are short±circuited. (See page AT± 191)
(c) The throttle position sensor or brake signal are not indicated,
but inspection can be made by checking the voltage at ter-
minal Tt of the check connector.
(d) The signals to each gear can be checked by measuring the
voltage at terminal Tt of the check connector while driving.
2. The diagnostic (malfunction) code is retained in memory by the
ECU and due to back±up voltage, is not canceled out when the
engine is turned off. Consequently, after repair, it is necessary
to turn the ignition switch off and remove the fuse EFI (15A)
(A540E) or DOME (20A)
(A540H) or disconnect the Engine and ECT ECU (A540E)
or ECT ECU (A540H) connector to cancel out the diagnostic
(malfunction) code. (See page AT±192)
HINT:
wLow battery voltage will cause faulty operation of the diag-
nosis system. Therefore, always check the battery first.
wUse a voltmeter and ohmmeter that have an impedance of
at least 10 k
/V.
CHECK O/D OFF INDICATOR LIGHT
1. Turn the ignition switch ON.
2. The O/D OFF light will come on when the O/D switch
placed at OFF.
3. When the O/D switch is set to ON, the O/D OFF light should go
out.
If the O/D OFF light flashes when the O/D switch is set to
ON, the electronic control system is faulty.
± AUTOMATIC TRANSAXLETroubleshooting (Diagnosis System) (A540E and A540H)AT±190
Page 447 of 2389
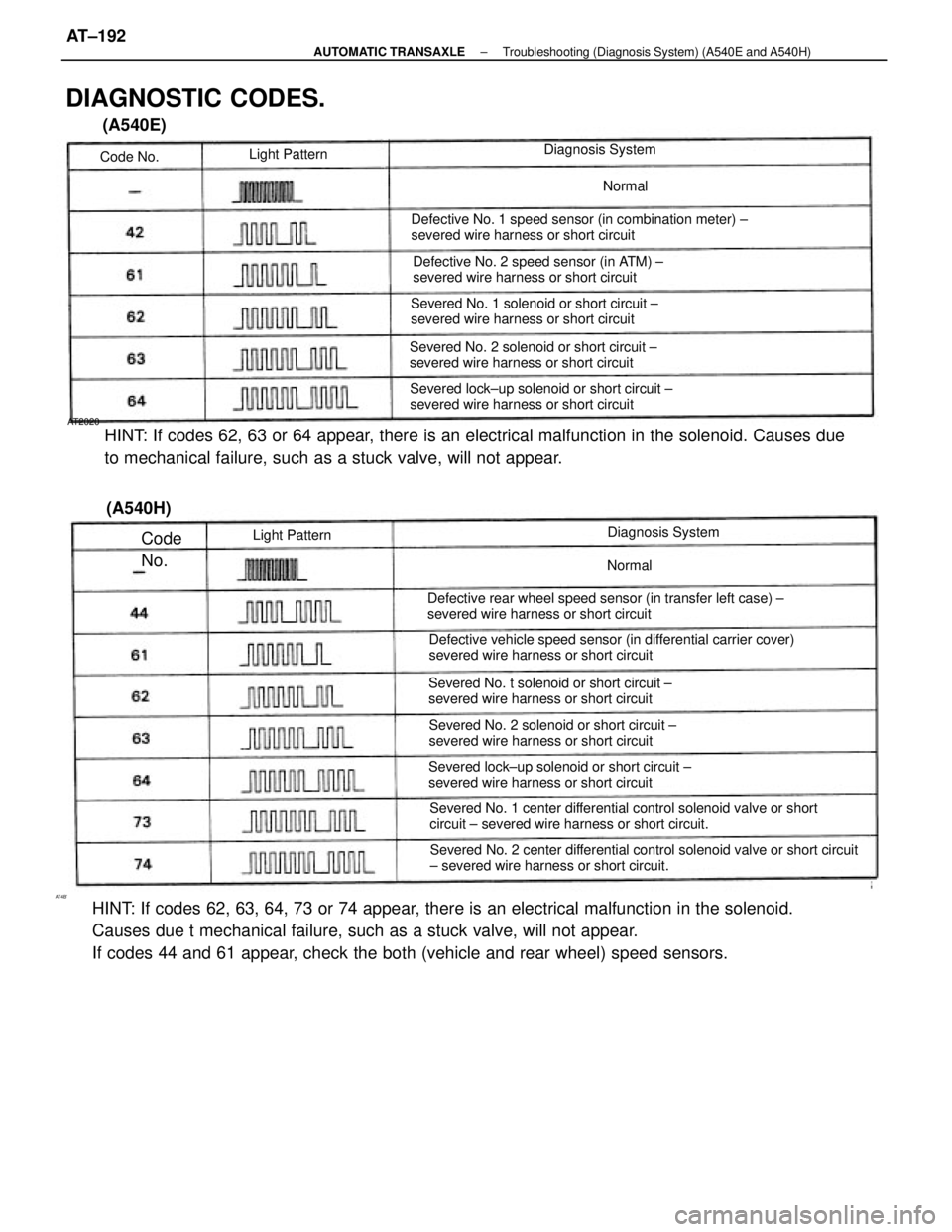
AT4B'
HINT: If codes 62, 63, 64, 73 or 74 appear, there is an electrical malfunction in the solenoid.
Causes due t mechanical failure, such as a stuck valve, will not appear.
If codes 44 and 61 appear, check the both (vehicle and rear wheel) speed sensors.
AT2020
HINT: If codes 62, 63 or 64 appear, there is an electrical malfunction in the solenoid. Causes due
to mechanical failure, such as a stuck valve, will not appear.
Severed No. 2 center differential control solenoid valve or short circuit
± severed wire harness or short circuit. Defective rear wheel speed sensor (in transfer left case) ±
severed wire harness or short circuit
Defective vehicle speed sensor (in differential carrier cover)
severed wire harness or short circuit
Severed No. 1 center differential control solenoid valve or short
circuit ± severed wire harness or short circuit. Defective No. 1 speed sensor (in combination meter) ±
severed wire harness or short circuit
DIAGNOSTIC CODES.
(A540E)
Severed lock±up solenoid or short circuit ±
severed wire harness or short circuit Severed lock±up solenoid or short circuit ±
severed wire harness or short circuitDefective No. 2 speed sensor (in ATM) ±
severed wire harness or short circuit
Severed No. t solenoid or short circuit ±
severed wire harness or short circuit
Severed No. 2 solenoid or short circuit ±
severed wire harness or short circuit Severed No. 1 solenoid or short circuit ±
severed wire harness or short circuit
Severed No. 2 solenoid or short circuit ±
severed wire harness or short circuitDiagnosis System
Diagnosis System Light Pattern
Light Pattern
(A540H)
Code No.
Code
No.
Normal Normal
± AUTOMATIC TRANSAXLETroubleshooting (Diagnosis System) (A540E and A540H)AT±192
Page 449 of 2389
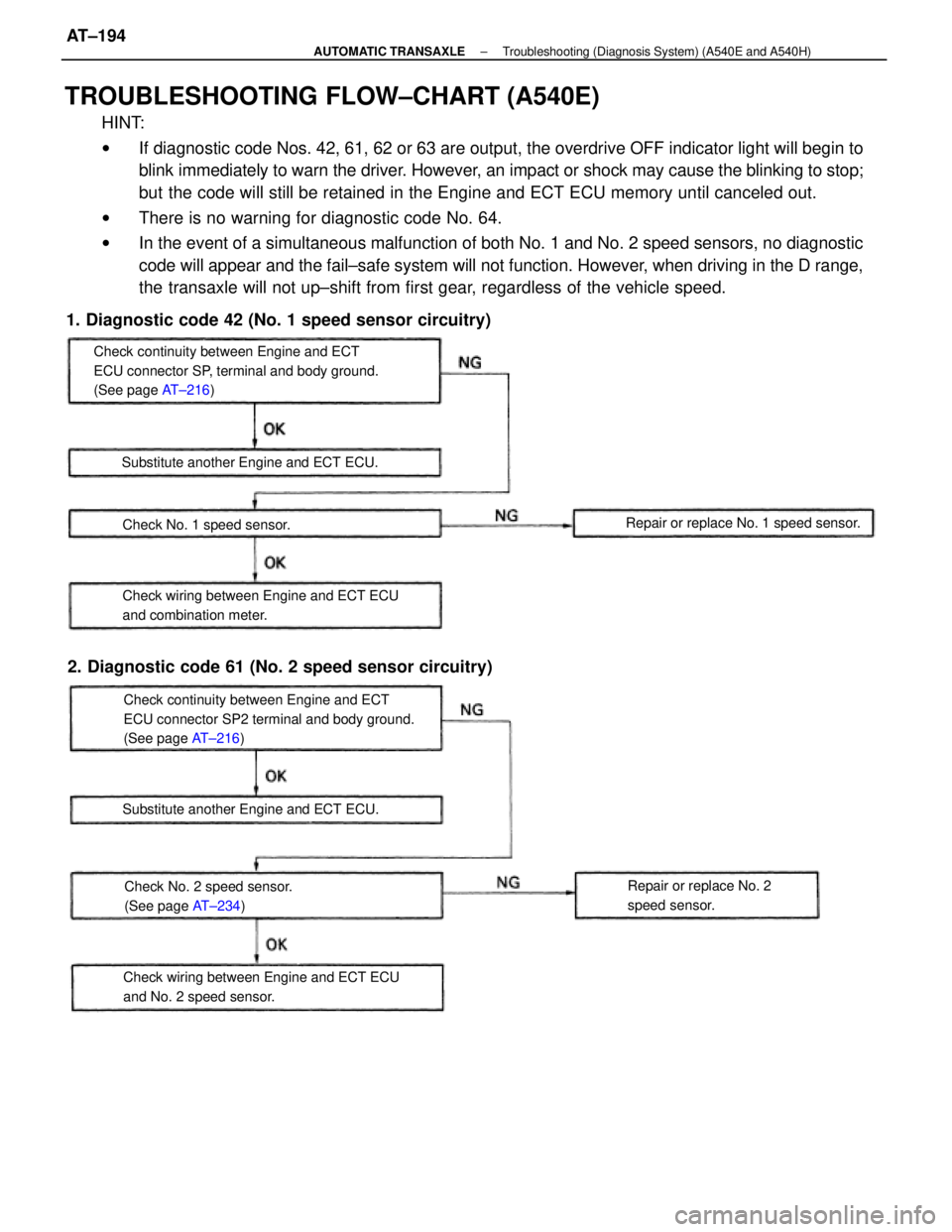
TROUBLESHOOTING FLOW±CHART (A540E)
HINT:
wIf diagnostic code Nos. 42, 61, 62 or 63 are output, the overdrive OFF indicator light will begin to
blink immediately to warn the driver. However, an impact or shock may cause the blinking to stop;
but the code will still be retained in the Engine and ECT ECU memory until canceled out.
wThere is no warning for diagnostic code No. 64.
wIn the event of a simultaneous malfunction of both No. 1 and No. 2 speed sensors, no diagnostic
code will appear and the fail±safe system will not function. However, when driving in the D range,
the transaxle will not up±shift from first gear, regardless of the vehicle speed.
Check continuity between Engine and ECT
ECU connector SP, terminal and body ground.
(See page AT±216)
Check continuity between Engine and ECT
ECU connector SP2 terminal and body ground.
(See page AT±216)
1. Diagnostic code 42 (No. 1 speed sensor circuitry)
Check wiring between Engine and ECT ECU
and No. 2 speed sensor. Check wiring between Engine and ECT ECU
and combination meter.
2. Diagnostic code 61 (No. 2 speed sensor circuitry)
Check No. 2 speed sensor.
(See page AT±234) Substitute another Engine and ECT ECU.
Substitute another Engine and ECT ECU.Repair or replace No. 1 speed sensor.
Repair or replace No. 2
speed sensor. Check No. 1 speed sensor.
± AUTOMATIC TRANSAXLETroubleshooting (Diagnosis System) (A540E and A540H)AT±194
Page 451 of 2389
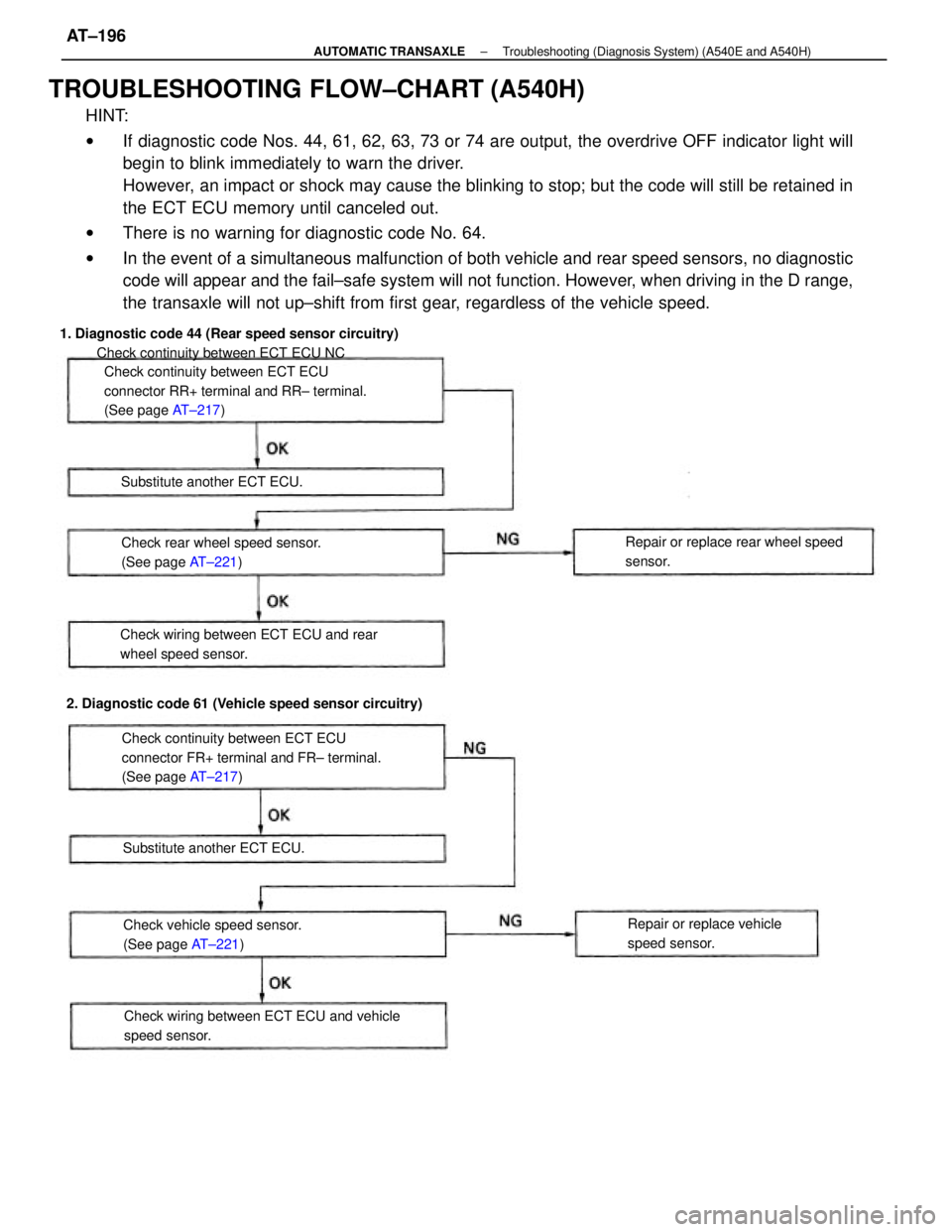
TROUBLESHOOTING FLOW±CHART (A540H)
HINT:
wIf diagnostic code Nos. 44, 61, 62, 63, 73 or 74 are output, the overdrive OFF indicator light will
begin to blink immediately to warn the driver.
However, an impact or shock may cause the blinking to stop; but the code will still be retained in
the ECT ECU memory until canceled out.
wThere is no warning for diagnostic code No. 64.
wIn the event of a simultaneous malfunction of both vehicle and rear speed sensors, no diagnostic
code will appear and the fail±safe system will not function. However, when driving in the D range,
the transaxle will not up±shift from first gear, regardless of the vehicle speed.
1. Diagnostic code 44 (Rear speed sensor circuitry)
Check continuity between ECT ECU NC
Check continuity between ECT ECU
connector RR+ terminal and RR± terminal.
(See page AT±217)
Check continuity between ECT ECU
connector FR+ terminal and FR± terminal.
(See page AT±217)
Check wiring between ECT ECU and vehicle
speed sensor. Check wiring between ECT ECU and rear
wheel speed sensor.
2. Diagnostic code 61 (Vehicle speed sensor circuitry)Repair or replace rear wheel speed
sensor. Check rear wheel speed sensor.
(See page AT±221)
Check vehicle speed sensor.
(See page AT±221)Repair or replace vehicle
speed sensor. Substitute another ECT ECU. Substitute another ECT ECU.
± AUTOMATIC TRANSAXLETroubleshooting (Diagnosis System) (A540E and A540H)AT±196
Page 476 of 2389
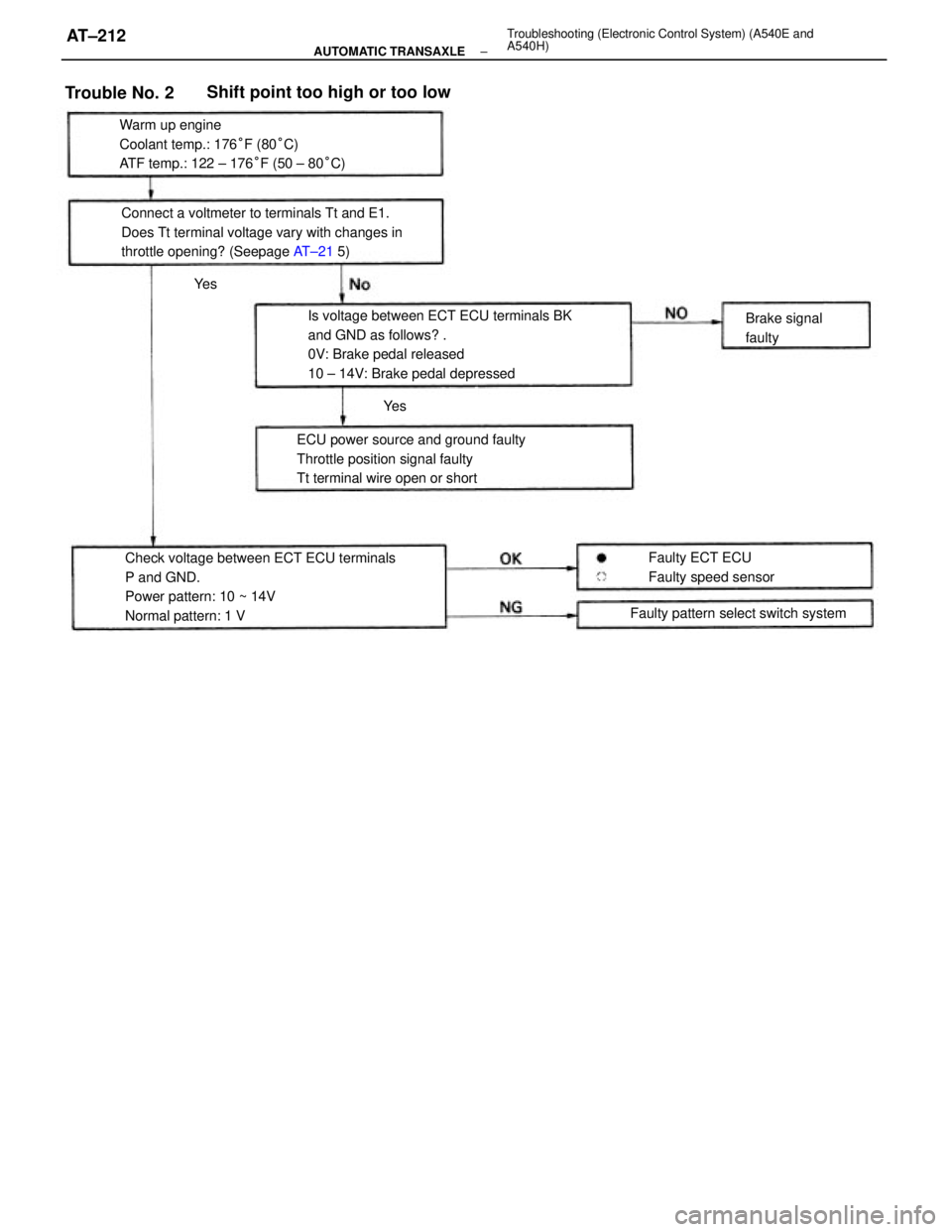
Is voltage between ECT ECU terminals BK
and GND as follows? .
0V: Brake pedal released
10 ± 14V: Brake pedal depressed
Check voltage between ECT ECU terminals
P and GND.
Power pattern: 10 ~ 14V
Normal pattern: 1 V Warm up engine
Coolant temp.: 176°F (80°C)
ATF temp.: 122 ± 176°F (50 ± 80°C)
Connect a voltmeter to terminals Tt and E1.
Does Tt terminal voltage vary with changes in
throttle opening? (Seepage AT±21 5)
ECU power source and ground faulty
Throttle position signal faulty
Tt terminal wire open or short
Faulty pattern select switch system
Shift point too high or too low
Faulty ECT ECU
Faulty speed sensorBrake signal
faulty
Trouble No. 2
Ye s
Ye s
± AUTOMATIC TRANSAXLETroubleshooting (Electronic Control System) (A540E and
A540H)AT±212