check engine YAMAHA TTR50 2006 User Guide
[x] Cancel search | Manufacturer: YAMAHA, Model Year: 2006, Model line: TTR50, Model: YAMAHA TTR50 2006Pages: 390, PDF Size: 9.69 MB
Page 156 of 390
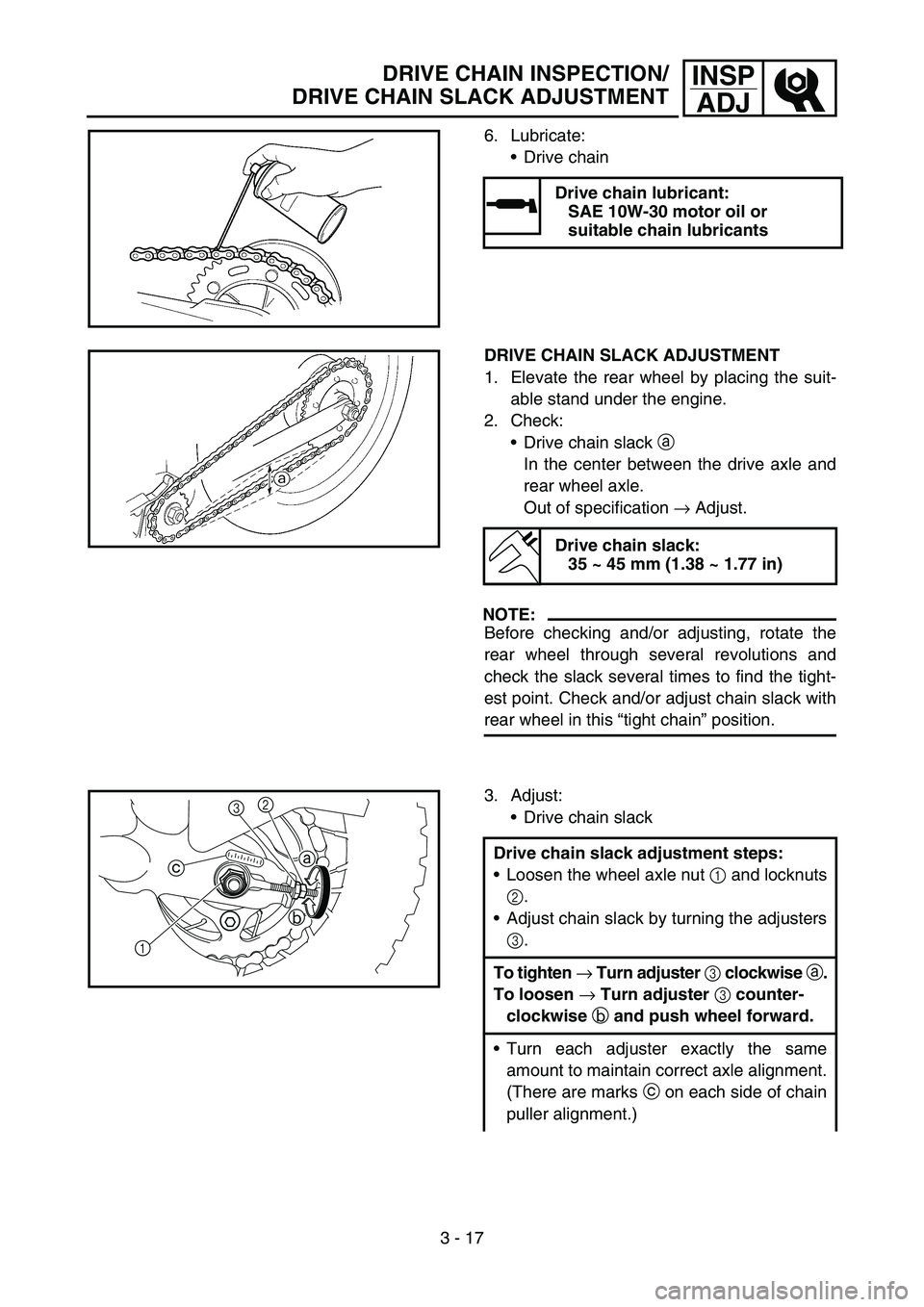
3 - 17
INSPADJ
6. Lubricate:
Drive chain
Drive chain lubricant:
SAE 10W-30 motor oil or
suitable chain lubricants
DRIVE CHAIN SLACK ADJUSTMENT
1. Elevate the rear wheel by placing the suit-
able stand under the engine.
2. Check: Drive chain slack a
In the center between the drive axle and
rear wheel axle.
Out of specification → Adjust.
NOTE:
Before checking and/or adjusting, rotate the
rear wheel through several revolutions and
check the slack several times to find the tight-
est point. Check and/or adjust chain slack with
rear wheel in this “tight chain ” position.
Drive chain slack:
35 ~ 45 mm (1.38 ~ 1.77 in)
3. Adjust:
Drive chain slack
Drive chain slack adjustment steps:
Loosen the wheel axle nut 1 and locknuts
2 .
Adjust chain slack by turning the adjusters
3 .
To tighten → Turn adjuster 3 clockwise a.
To loosen → Turn adjuster 3 counter-
clockwise b and push wheel forward.
Turn each adjuster exactly the same
amount to maintain correct axle alignment.
(There are marks c on each side of chain
puller alignment.)
1 b
c
a
23
DRIVE CHAIN INSPECTION/
DRIVE CHAIN SLACK ADJUSTMENT
Page 162 of 390
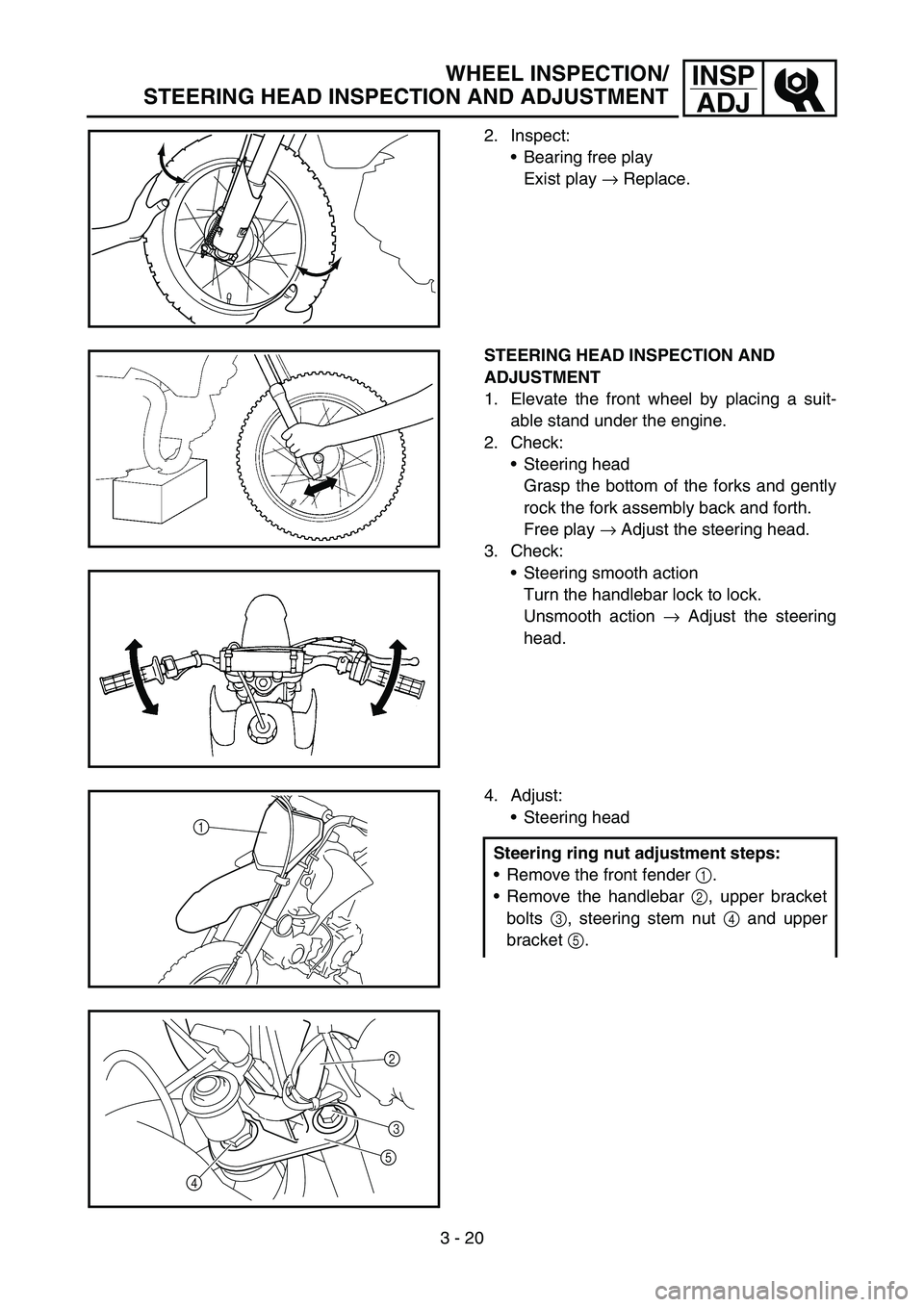
3 - 20
INSPADJWHEEL INSPECTION/
STEERING HEAD INSPECTION AND ADJUSTMENT
2. Inspect:
Bearing free play
Exist play → Replace.
STEERING HEAD INSPECTION AND
ADJUSTMENT
1. Elevate the front wheel by placing a suit-
able stand under the engine.
2. Check:
Steering head
Grasp the bottom of the forks and gently
rock the fork assembly back and forth.
Free play → Adjust the steering head.
3. Check: Steering smooth action
Turn the handlebar lock to lock.
Unsmooth action → Adjust the steering
head.
4. Adjust:
Steering head
Steering ring nut adjustment steps:
Remove the front fender 1.
Remove the handlebar 2, upper bracket
bolts 3, steering stem nut 4 and upper
bracket 5.
1
4
3
52
Page 168 of 390
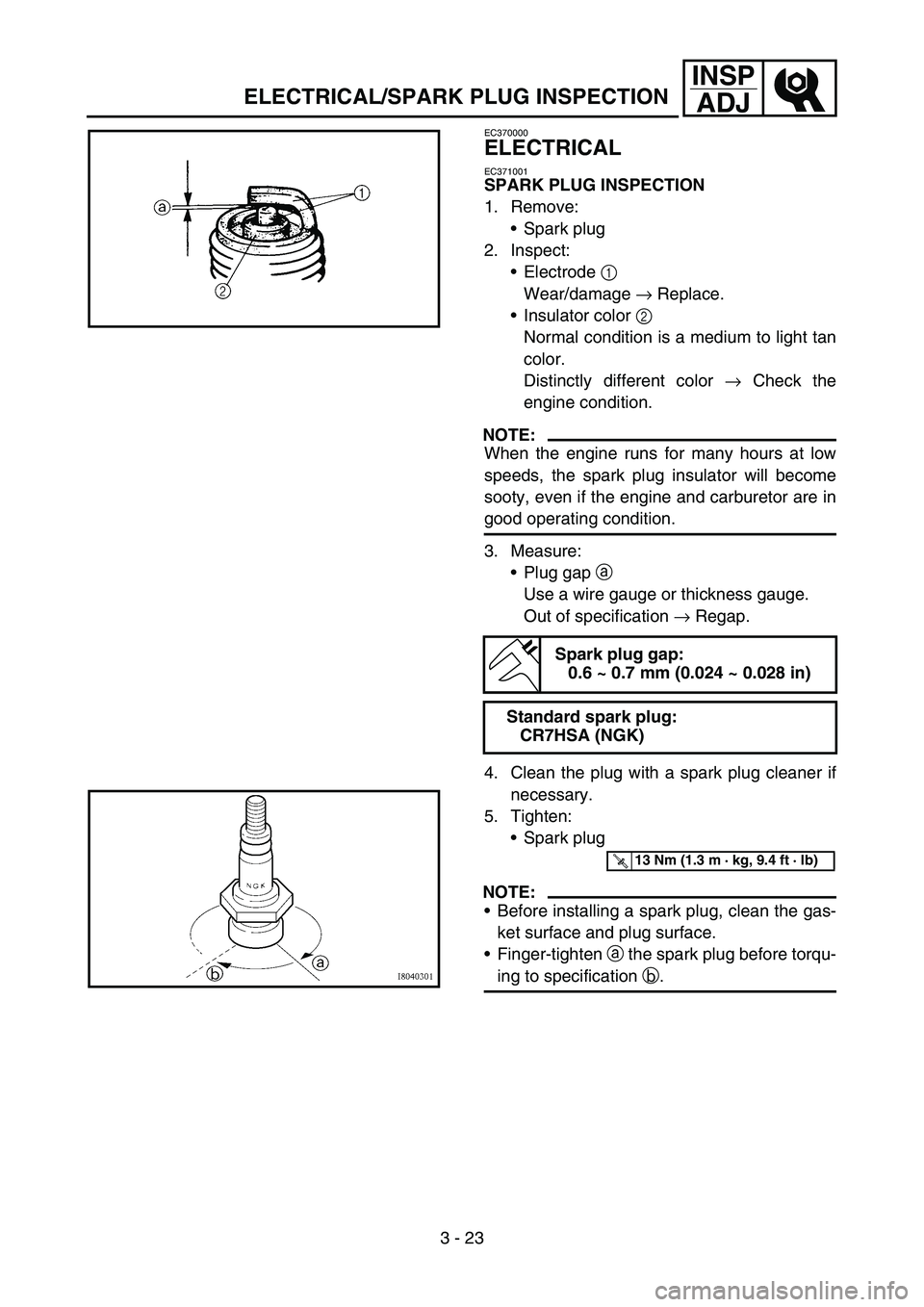
3 - 23
INSPADJ
ELECTRICAL/SPARK PLUG INSPECTION
EC370000
ELECTRICAL
EC371001
SPARK PLUG INSPECTION
1. Remove:
Spark plug
2. Inspect: Electrode 1
Wear/damage → Replace.
Insulator color 2
Normal condition is a medium to light tan
color.
Distinctly different color → Check the
engine condition.
NOTE:
When the engine runs for many hours at low
speeds, the spark plug insulator will become
sooty, even if the engine and carburetor are in
good operating condition.
3. Measure: Plug gap a
Use a wire gauge or thickness gauge.
Out of specification → Regap.
4. Clean the plug with a spark plug cleaner if necessary.
5. Tighten: Spark plug
NOTE:
Before installing a spark plug, clean the gas-
ket surface and plug surface.
Finger-tighten a the spark plug before torqu-
ing to specification b.
Spark plug gap:
0.6 ~ 0.7 mm (0.024 ~ 0.028 in)
Standard spark plug: CR7HSA (NGK)
T R..13 Nm (1.3 m · kg, 9.4 ft · lb)
Page 300 of 390

4 - 57
ENGSHIFT FORK, SHIFT CAM AND TRANSMISSION
2. Install:Main axle assembly 1
Drive axle assembly 2
Shift fork 2 “R ” 3
Shift fork 1 “L ” 4
Shift cam 5
Guide bar 6
NOTE:
The embossed marks on the shift forks
should face towards the right side of the
engine and be in the following sequence:
“R ”, “L ”.
Mesh the shift fork 2 “R ” with the 3rd wheel
gear on the drive axle.
Mesh the shift fork 1 “L ” with the 2nd pinion
gear on the main axle.
3. Check: Shifter operation
Transmission operation
Unsmooth operation → Repair.
3
4
5 1
6
2
Page 324 of 390
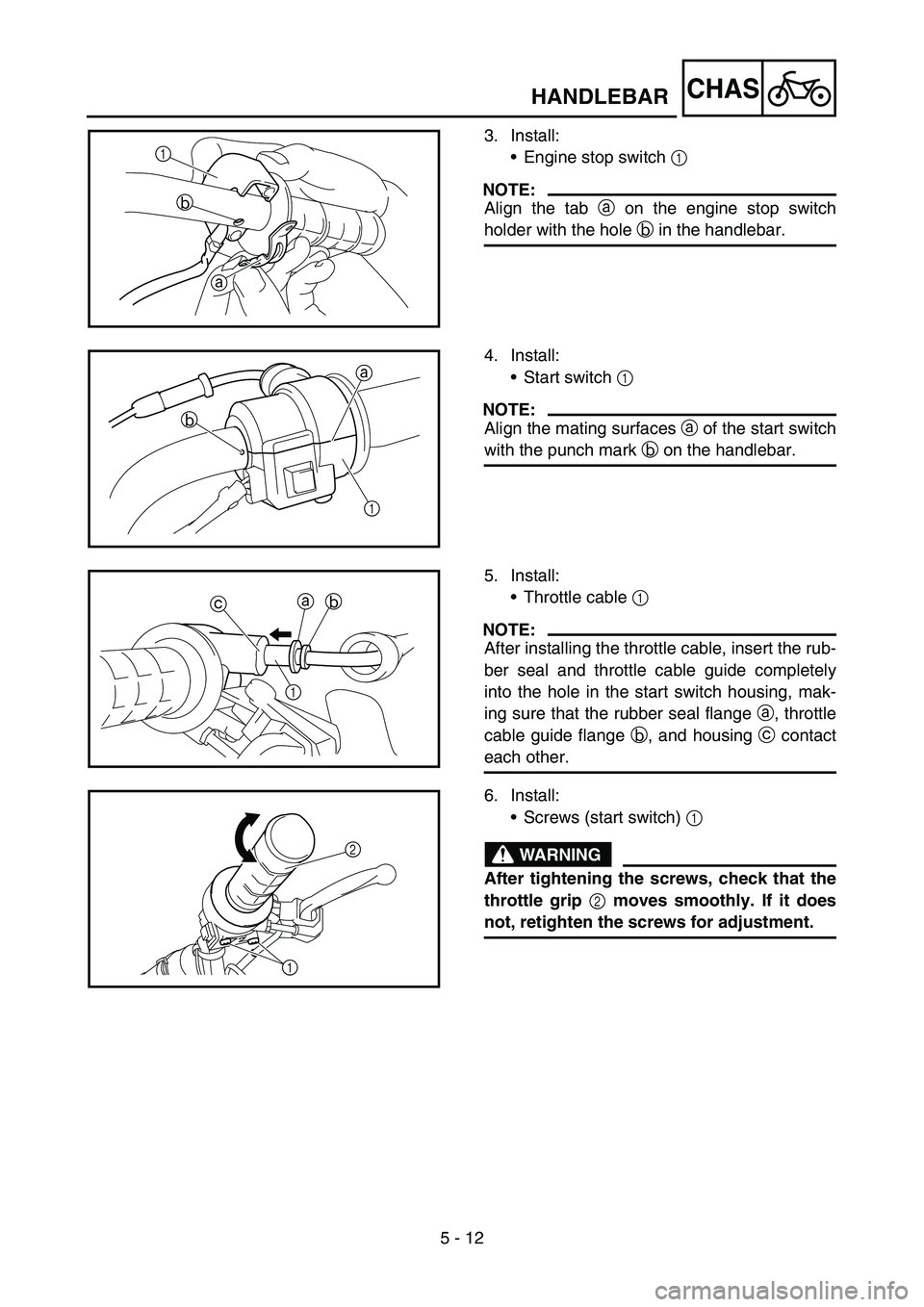
5 - 12
CHAS
3. Install:Engine stop switch 1
NOTE:
Align the tab a on the engine stop switch
holder with the hole b in the handlebar.
a
b
1
4. Install:
Start switch 1
NOTE:
Align the mating surfaces a of the start switch
with the punch mark b on the handlebar.
1
b a
5. Install:
Throttle cable 1
NOTE:
After installing the throttle cable, insert the rub-
ber seal and throttle cable guide completely
into the hole in the start switch housing, mak-
ing sure that the rubber seal flange a, throttle
cable guide flange b, and housing c contact
each other.
a
c b
1
6. Install:
Screws (start switch) 1
WARNING
After tightening the screws, check that the
throttle grip 2 moves smoothly. If it does
not, retighten the screws for adjustment.
2
1
HANDLEBAR
Page 342 of 390
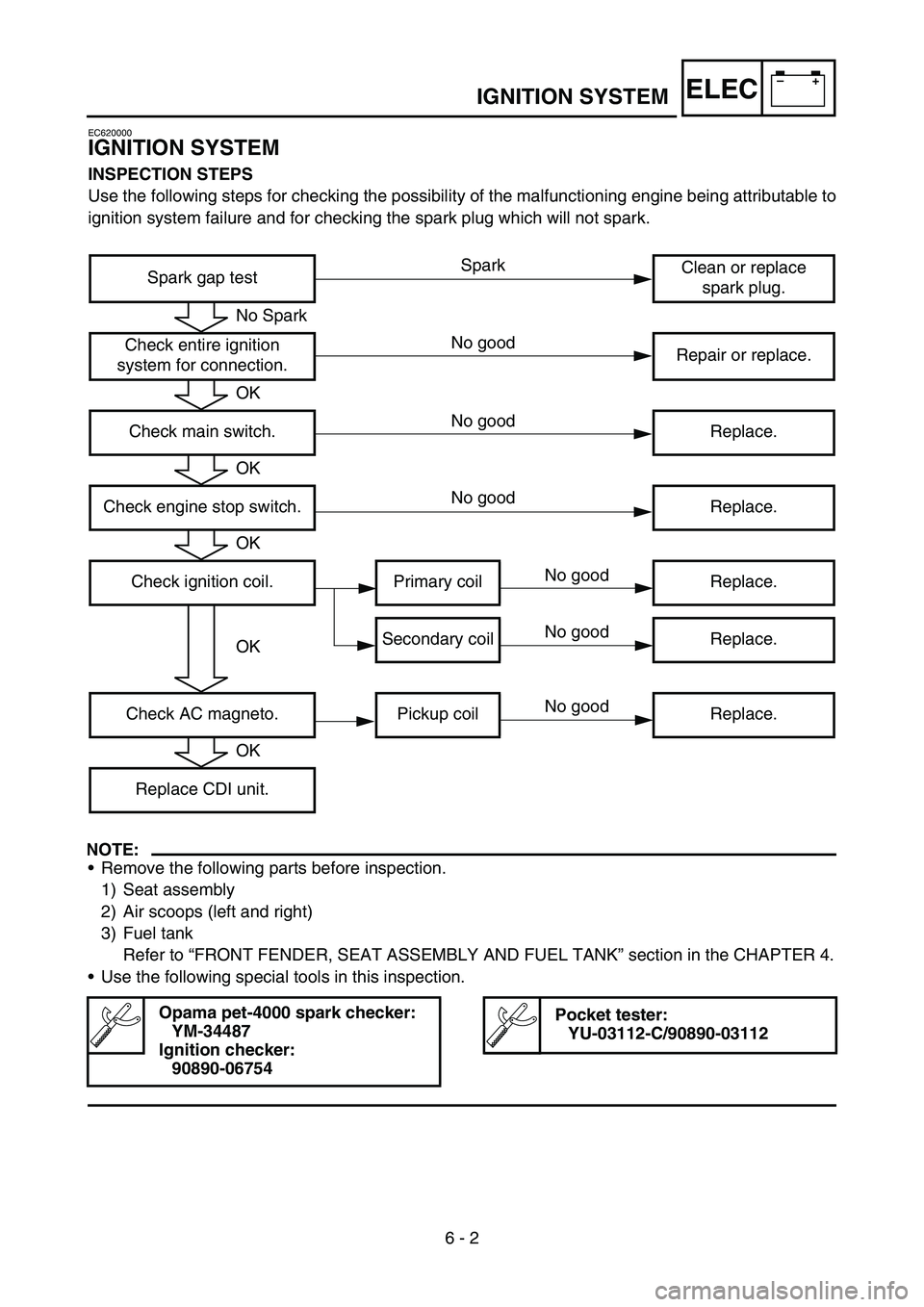
–+ELEC
6 - 2
IGNITION SYSTEM
EC620000
IGNITION SYSTEM
INSPECTION STEPS
Use the following steps for checking the possibility of the malfunctioning engine being attributable to
ignition system failure and for checking the spark plug which will not spark.
NOTE:
Remove the following parts before inspection.
1) Seat assembly
2) Air scoops (left and right)
3) Fuel tank
Refer to “FRONT FENDER, SEAT ASSEMBLY AND FUEL TANK ” section in the CHAPTER 4.
Use the following special tools in this inspection.
Opama pet-4000 spark checker:
YM-34487
Ignition checker: 90890-06754Pocket tester:YU-03112-C/90890-03112
Spark gap test Clean or replace
spark plug.
Check entire ignition
system for connection. Repair or replace.
Check main switch. Replace.
Check engine stop switch. Replace.
Check ignition coil. Primary coil Replace. Secondary coil Replace.
Check AC magneto. Pickup coil Replace. Replace CDI unit.
No Spark
OK
OK
OK
OK
OK
Spark
No good
No good
No good
No good
No good
No good
Page 346 of 390
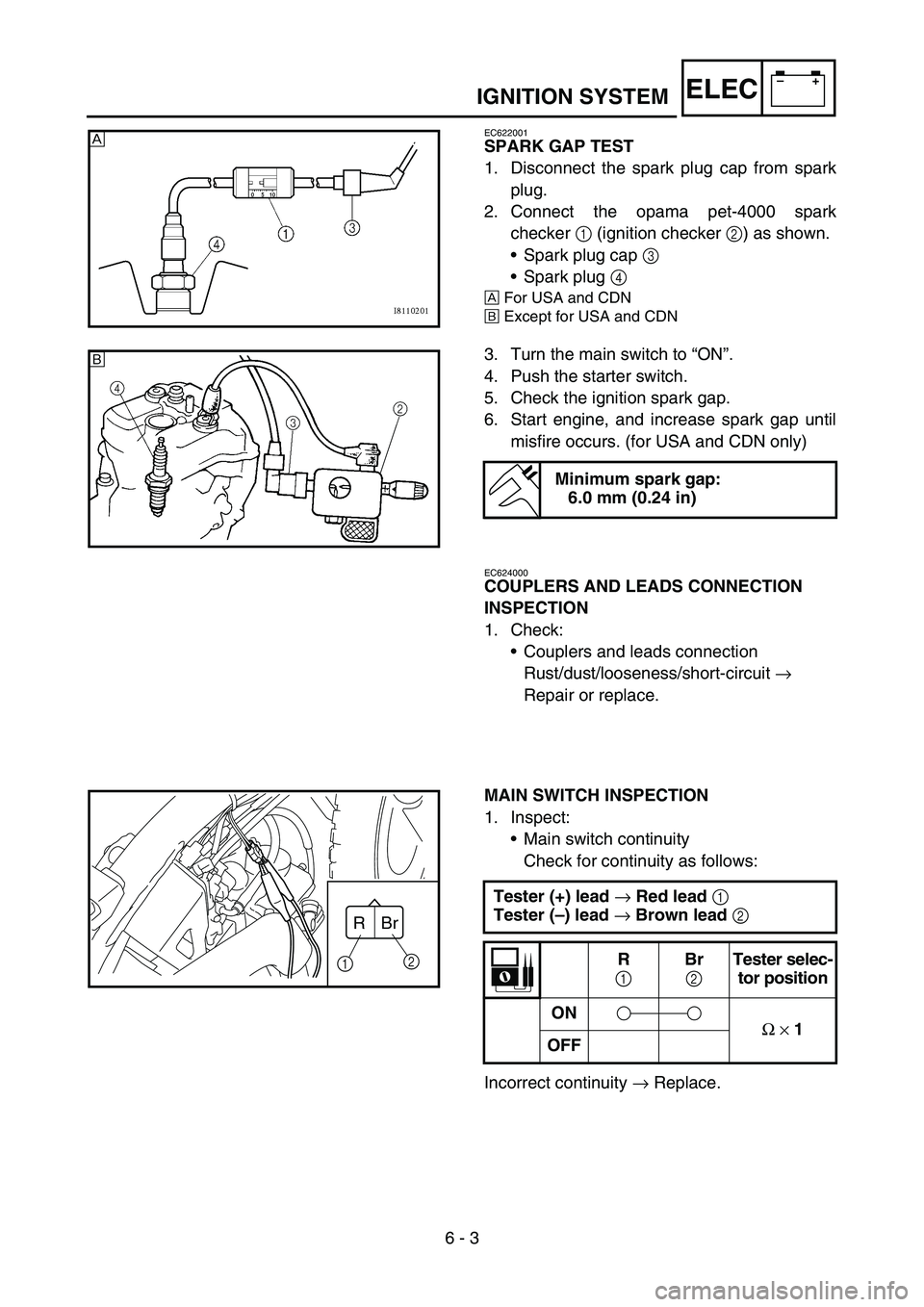
6 - 3
–+ELECIGNITION SYSTEM
EC622001
SPARK GAP TEST
1. Disconnect the spark plug cap from spark
plug.
2. Connect the opama pet-4000 spark
checker 1 (ignition checker 2) as shown.
Spark plug cap 3
Spark plug 4
È For USA and CDN
É Except for USA and CDN
3. Turn the main switch to
“ON ”.
4. Push the starter switch.
5. Check the ignition spark gap.
6. Start engine, and increase spark gap until misfire occurs. (for USA and CDN only)
Minimum spark gap:6.0 mm (0.24 in)
È
É
EC624000
COUPLERS AND LEADS CONNECTION
INSPECTION
1. Check:
Couplers and leads connection
Rust/dust/looseness/short-circuit →
Repair or replace.
MAIN SWITCH INSPECTION
1. Inspect: Main switch continuity
Check for continuity as follows:
Incorrect continuity → Replace.
Tester (+) lead
→ Red lead
1
Tester ( –) lead
→ Brown lead
2
R
1 Br
2 Tester selec-
tor position
ON Ω
× 1
OFF
Br
R
1 2
Page 352 of 390
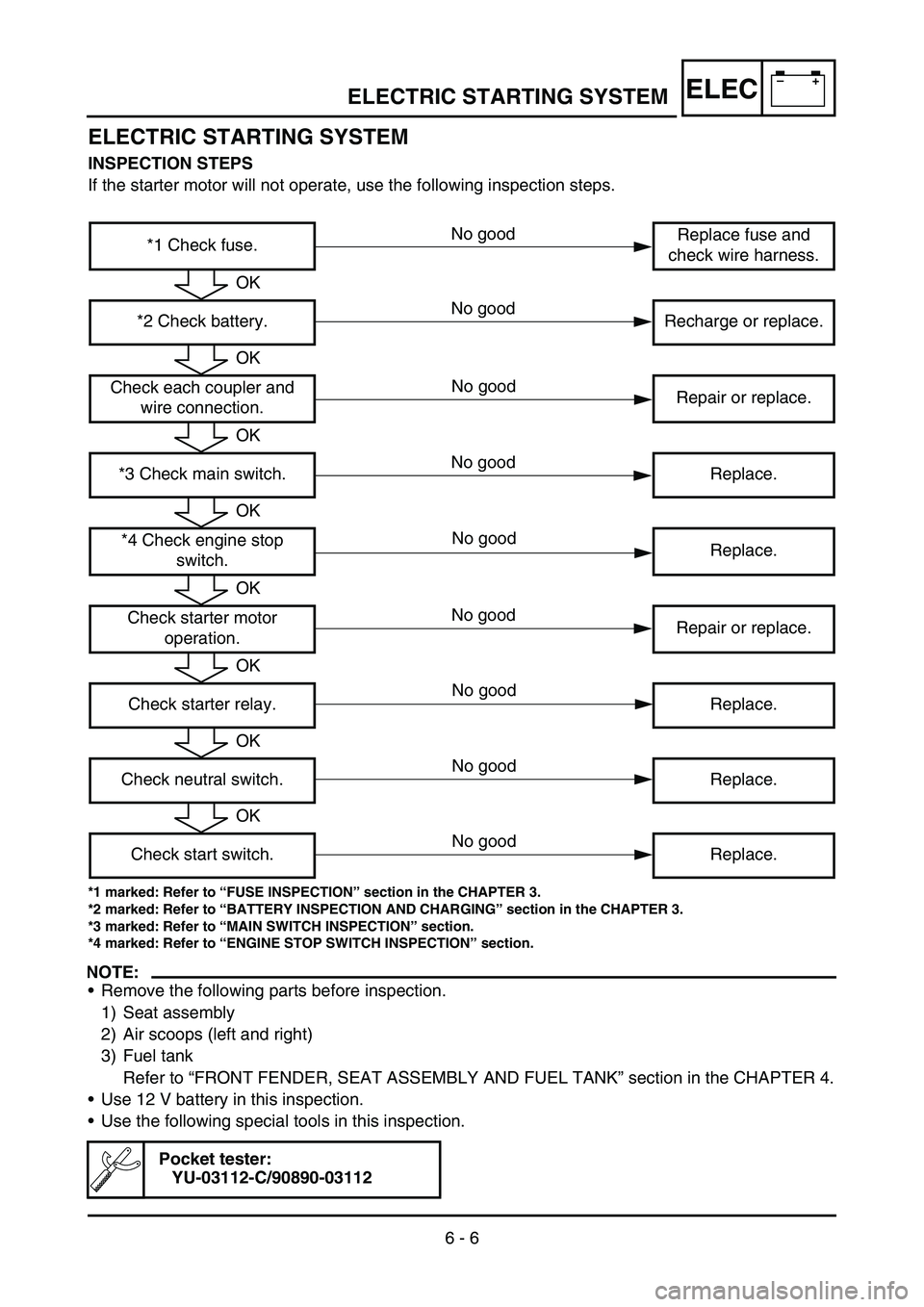
–+ELEC
6 - 6
ELECTRIC STARTING SYSTEM
INSPECTION STEPS
If the starter motor will not operate, use the following inspection steps.
*1 marked: Refer to “FUSE INSPECTION ” section in the CHAPTER 3.
*2 marked: Refer to “BATTERY INSPECTION AND CHARGING ” section in the CHAPTER 3.
*3 marked: Refer to “MAIN SWITCH INSPECTION ” section.
*4 marked: Refer to “ENGINE STOP SWITCH INSPECTION ” section.
NOTE:
Remove the following parts before inspection.
1) Seat assembly
2) Air scoops (left and right)
3) Fuel tank
Refer to “FRONT FENDER, SEAT ASSEMBLY AND FUEL TANK ” section in the CHAPTER 4.
Use 12 V battery in this inspection.
Use the following special tools in this inspection.
Pocket tester:
YU-03112-C/90890-03112
*1 Check fuse. Replace fuse and
check wire harness.
*2 Check battery. Recharge or replace.
Check each coupler and wire connection. Repair or replace.
*3 Check main switch. Replace. *4 Check engine stop switch. Replace.
Check starter motor operation. Repair or replace.
Check starter relay. Replace.
Check neutral switch. Replace. Check start switch. Replace.
OK
OK
OK
OK
OK
OK
OK
OK
No good
No good
No good
No good
No good
No good
ELECTRIC STARTING SYSTEM
No good
No good
No good
Page 374 of 390
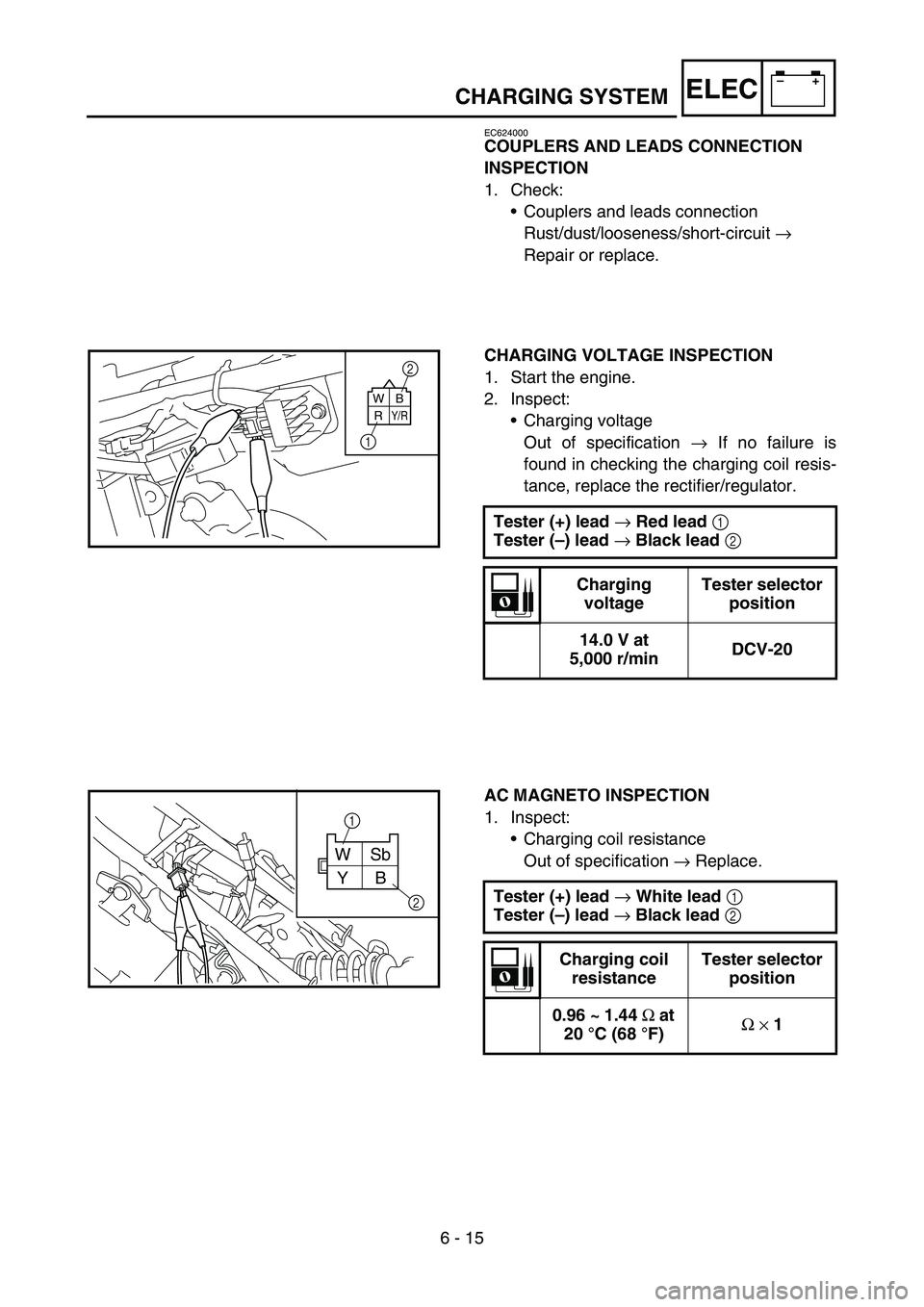
6 - 15
–+ELECCHARGING SYSTEM
EC624000
COUPLERS AND LEADS CONNECTION
INSPECTION
1. Check:
Couplers and leads connection
Rust/dust/looseness/short-circuit →
Repair or replace.
CHARGING VOLTAGE INSPECTION
1. Start the engine.
2. Inspect: Charging voltage
Out of specification → If no failure is
found in checking the charging coil resis-
tance, replace the rectifier/regulator.
Tester (+) lead → Red lead
1
Tester ( –) lead
→ Black lead
2
Charging
voltage Tester selector
position
14.0 V at
5,000 r/min DCV-20
2
1
W R
Y/R
B
AC MAGNETO INSPECTION
1. Inspect: Charging coil resistance
Out of specification → Replace.
Tester (+) lead → White lead
1
Tester ( –) lead
→ Black lead
2
Charging coil
resistance Tester selector
position
0.96 ~ 1.44 Ω at
20 °C (68 °F) Ω
× 1
WSb
B
Y 1
2