brake YAMAHA WR 250F 2009 Owners Manual
[x] Cancel search | Manufacturer: YAMAHA, Model Year: 2009, Model line: WR 250F, Model: YAMAHA WR 250F 2009Pages: 224, PDF Size: 13.93 MB
Page 6 of 224
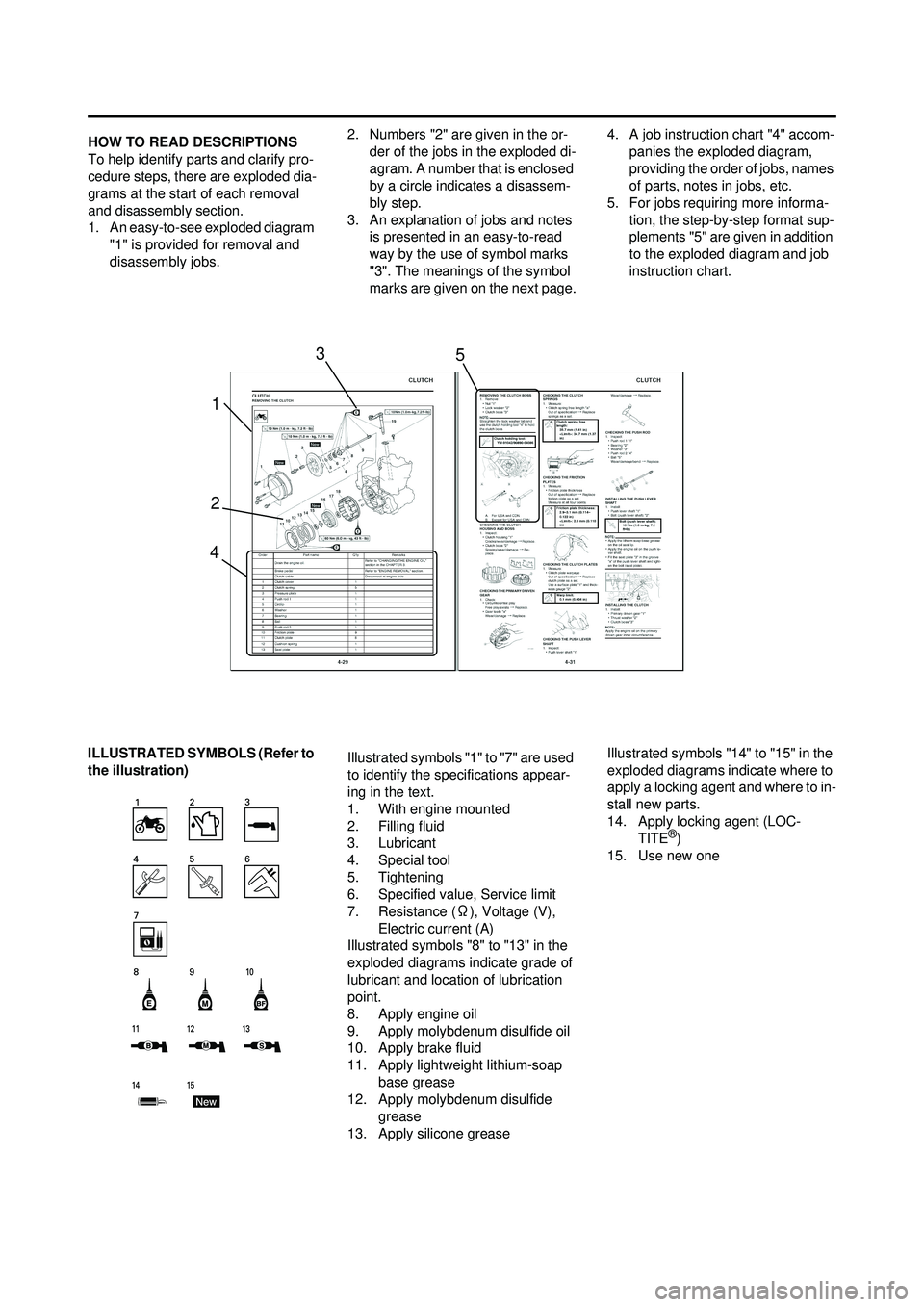
HOW TO READ DESCRIPTIONS
To help identify parts and clarify pro-
cedure steps, there are exploded dia-
grams at the start of each removal
and disassembly section.
1. An easy-to-see exploded diagram "1" is provided for removal and
disassembly jobs. 2. Numbers "2" are given in the or-
der of the jobs in the exploded di-
agram. A number that is enclosed
by a circle indicates a disassem-
bly step.
3. An explanation of jobs and notes is presented in an easy-to-read
way by the use of symbol marks
"3". The meanings of the symbol
marks are given on the next page. 4. A job instruction chart "4" accom-
panies the exploded diagram,
providing the order of jobs, names
of parts, notes in jobs, etc.
5. For jobs requiring more informa- tion, the step-by-step format sup-
plements "5" are given in addition
to the exploded diagram and job
instruction chart.
ILLUSTRATED SYMBOLS (Refer to
the illustration) Illustrated symbols "1" to "7" are used
to identify the specifications appear-
ing in the text.
1. With engine mounted
2. Filling fluid
3. Lubricant
4. Special tool
5. Tightening
6. Specified value, Service limit
7. Resistance (
Ω), Voltage (V),
Electric current (A)
Illustrated symbols "8" to "13" in the
exploded diagrams indicate grade of
lubricant and location of lubrication
point.
8. Apply engine oil
9. Apply molybdenum disulfide oil
10. Apply brake fluid
11. Apply lightweight lithium-soap
base grease
12. Apply molybdenum disulfide
grease
13. Apply silicone grease Illustrated symbols "14" to "15" in the
exploded diagrams indicate where to
apply a locking agent and where to in-
stall new parts.
14. Apply locking agent (LOC-
TITE
®)
15. Use new one
1
2 3
4 5
Page 8 of 224
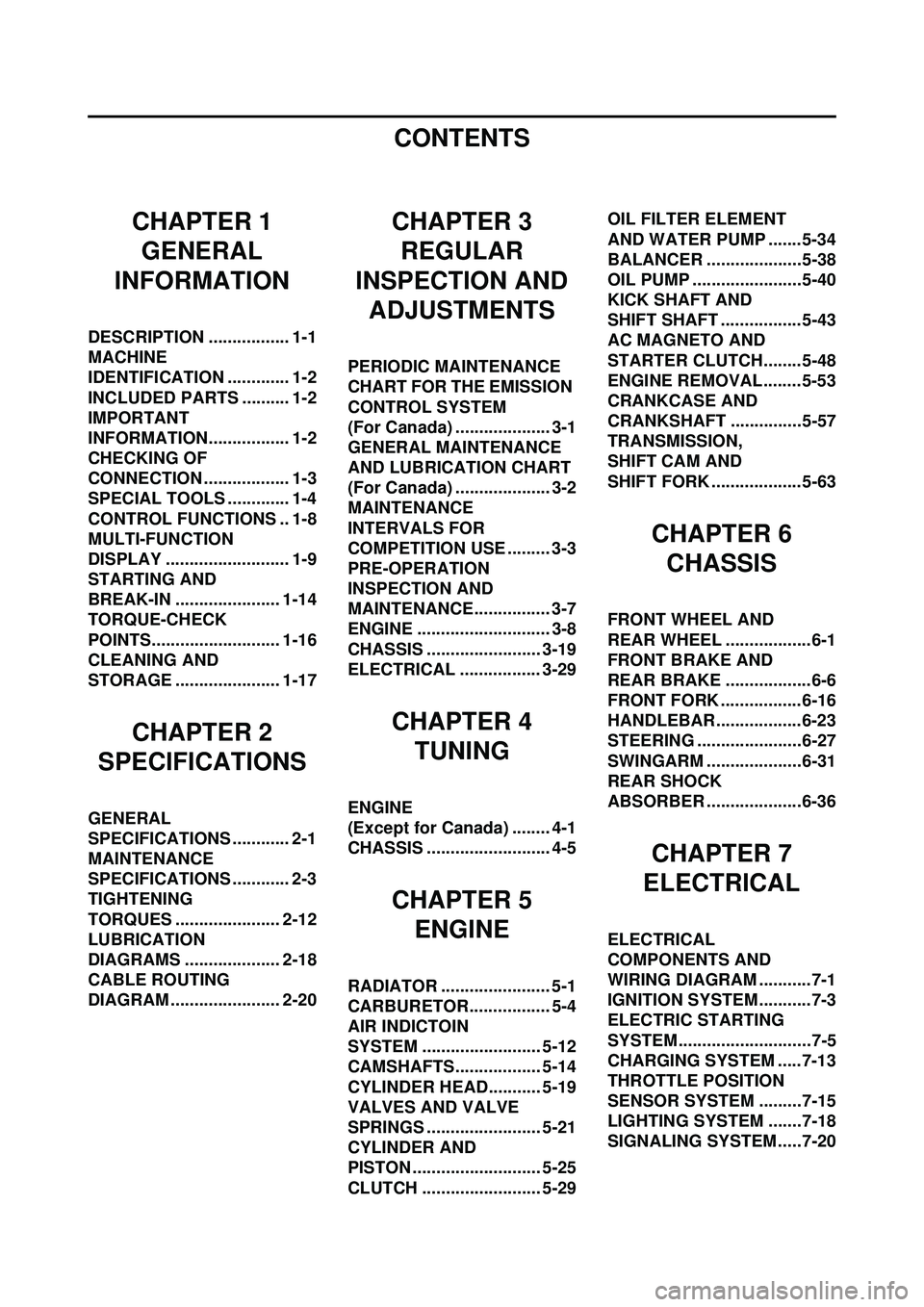
CONTENTS
CHAPTER 1GENERAL
INFORMATION
DESCRIPTION ................. 1-1
MACHINE
IDENTIFICATION ............. 1-2
INCLUDED PARTS .......... 1-2
IMPORTANT
INFORMATION................. 1-2
CHECKING OF
CONNECTION .................. 1-3
SPECIAL TOOLS ............. 1-4
CONTROL FUNCTIONS .. 1-8
MULTI-FUNCTION
DISPLAY .......................... 1-9
STARTING AND
BREAK-IN ...................... 1-14
TORQUE-CHECK
POINTS........................... 1-16
CLEANING AND
STORAGE ...................... 1-17
CHAPTER 2
SPECIFICATIONS
GENERAL
SPECIFICATIONS ............ 2-1
MAINTENANCE
SPECIFICATIONS ............ 2-3
TIGHTENING
TORQUES ...................... 2-12
LUBRICATION
DIAGRAMS .................... 2-18
CABLE ROUTING
DIAGRAM ....................... 2-20
CHAPTER 3 REGULAR
INSPECTION AND ADJUSTMENTS
PERIODIC MAINTENANCE
CHART FOR THE EMISSION
CONTROL SYSTEM
(For Canada) .................... 3-1
GENERAL MAINTENANCE
AND LUBRICATION CHART
(For Canada) .................... 3-2
MAINTENANCE
INTERVALS FOR
COMPETITION USE ......... 3-3
PRE-OPERATION
INSPECTION AND
MAINTENANCE................ 3-7
ENGINE ............................ 3-8
CHASSIS ........................ 3-19
ELECTRICAL ................. 3-29
CHAPTER 4 TUNING
ENGINE
(Except for Canada) ........ 4-1
CHASSIS .......................... 4-5
CHAPTER 5ENGINE
RADIATOR ....................... 5-1
CARBURETOR................. 5-4
AIR INDICTOIN
SYSTEM ......................... 5-12
CAMSHAFTS.................. 5-14
CYLINDER HEAD........... 5-19
VALVES AND VALVE
SPRINGS ........................ 5-21
CYLINDER AND
PISTON ........................... 5-25
CLUTCH ......................... 5-29 OIL FILTER ELEMENT
AND WATER PUMP .......5-34
BALANCER ....................5-38
OIL PUMP .......................5-40
KICK SHAFT AND
SHIFT SHAFT ................. 5-43
AC MAGNETO AND
STARTER CLUTCH........5-48
ENGINE REMOVAL........ 5-53
CRANKCASE AND
CRANKSHAFT ...............5-57
TRANSMISSION,
SHIFT CAM AND
SHIFT FORK ................... 5-63
CHAPTER 6
CHASSIS
FRONT WHEEL AND
REAR WHEEL ..................6-1
FRONT BRAKE AND
REAR BRAKE ..................6-6
FRONT FORK ................. 6-16
HANDLEBAR..................6-23
STEERING ......................6-27
SWINGARM ....................6-31
REAR SHOCK
ABSORBER ....................6-36
CHAPTER 7
ELECTRICAL
ELECTRICAL
COMPONENTS AND
WIRING DIAGRAM ...........7-1
IGNITION SYSTEM...........7-3
ELECTRIC STARTING
SYSTEM............................7-5
CHARGING SYSTEM .....7-13
THROTTLE POSITION
SENSOR SYSTEM .........7-15
LIGHTING SYSTEM .......7-18
SIGNALING SYSTEM.....7-20
Page 9 of 224
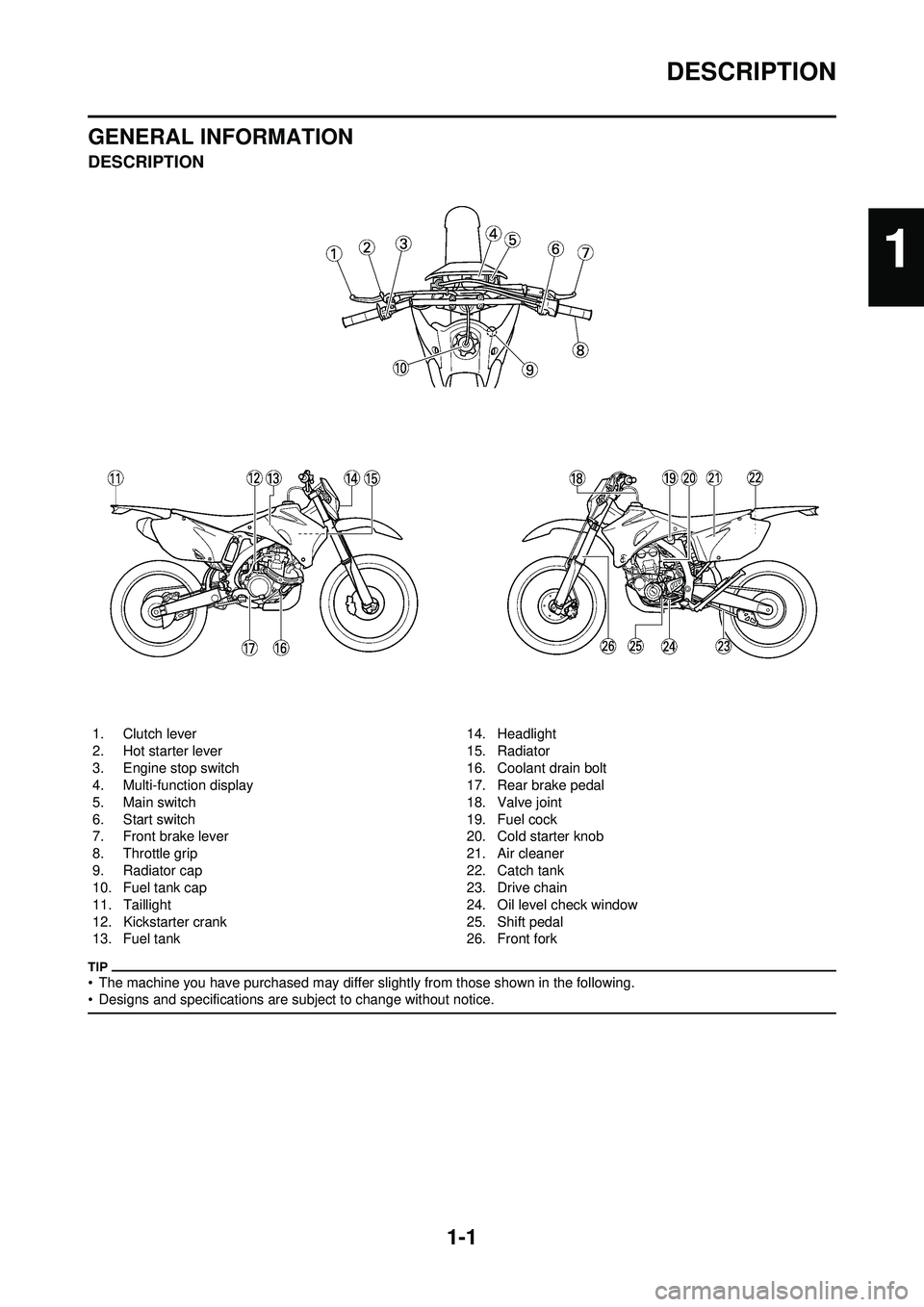
1-1
DESCRIPTION
GENERAL INFORMATION
DESCRIPTION
• The machine you have purchased may differ slightly from those shown in the following.
• Designs and specifications are subject to change without notice.
1. Clutch lever
2. Hot starter lever
3. Engine stop switch
4. Multi-function display
5. Main switch
6. Start switch
7. Front brake lever
8. Throttle grip
9. Radiator cap
10. Fuel tank cap
11. Taillight
12. Kickstarter crank
13. Fuel tank14. Headlight
15. Radiator
16. Coolant drain bolt
17. Rear brake pedal
18. Valve joint
19. Fuel cock
20. Cold starter knob
21. Air cleaner
22. Catch tank
23. Drive chain
24. Oil level check window
25. Shift pedal
26. Front fork
1
Page 16 of 224
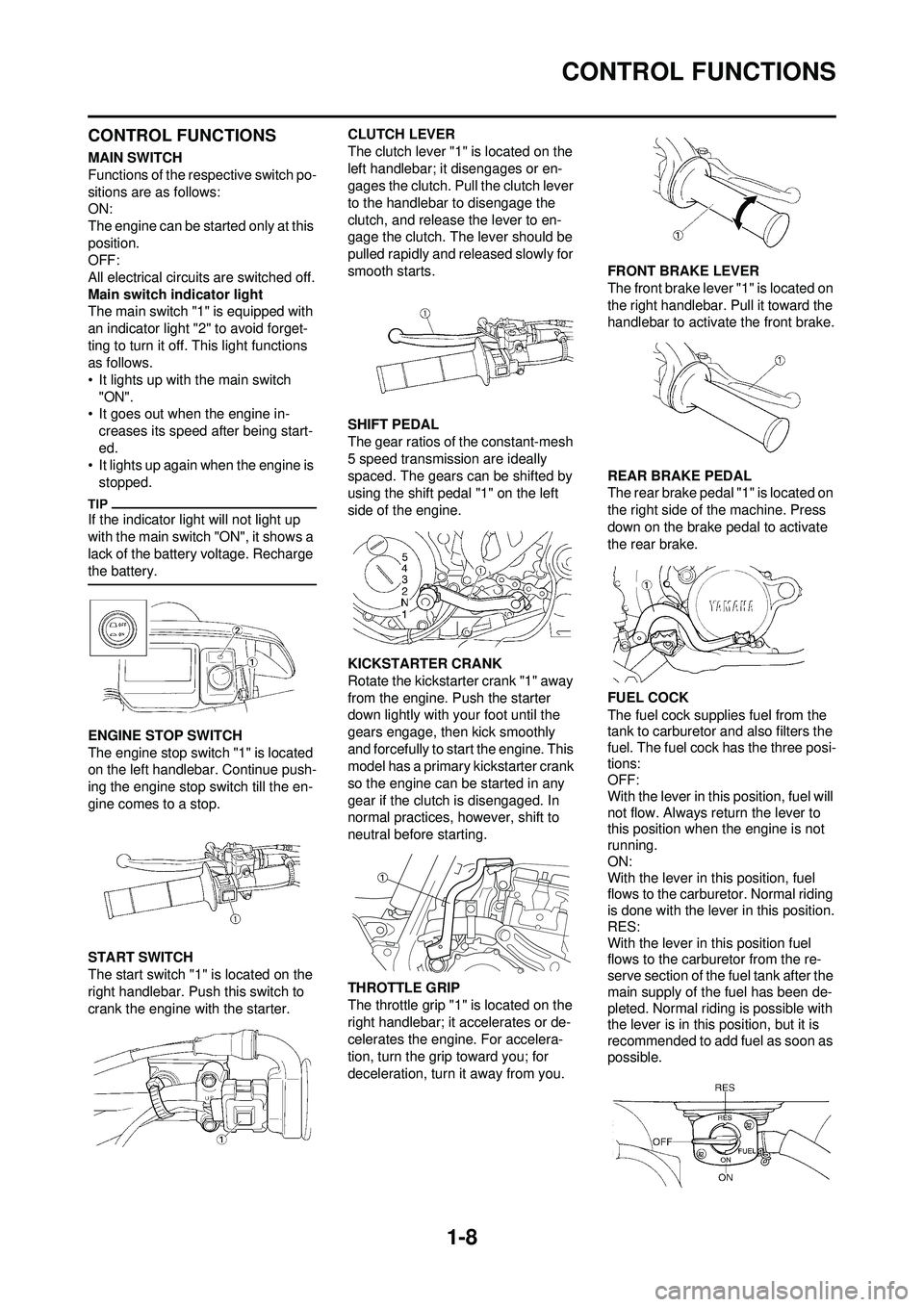
1-8
CONTROL FUNCTIONS
CONTROL FUNCTIONS
MAIN SWITCH
Functions of the respective switch po-
sitions are as follows:
ON:
The engine can be started only at this
position.
OFF:
All electrical circuits are switched off.
Main switch indicator light
The main switch "1" is equipped with
an indicator light "2" to avoid forget-
ting to turn it off. This light functions
as follows.
• It lights up with the main switch "ON".
• It goes out when the engine in-
creases its speed after being start-
ed.
• It lights up again when the engine is
stopped.
If the indicator light will not light up
with the main switch "ON", it shows a
lack of the battery voltage. Recharge
the battery.
ENGINE STOP SWITCH
The engine stop switch "1" is located
on the left handlebar. Continue push-
ing the engine stop switch till the en-
gine comes to a stop.
START SWITCH
The start switch "1" is located on the
right handlebar. Push this switch to
crank the engine with the starter. CLUTCH LEVER
The clutch lever "1" is located on the
left handlebar; it disengages or en-
gages the clutch. Pull the clutch lever
to the handlebar to disengage the
clutch, and release the lever to en-
gage the clutch. The lever should be
pulled rapidly and released slowly for
smooth starts.
SHIFT PEDAL
The gear ratios of the constant-mesh
5 speed transmission are ideally
spaced. The gears can be shifted by
using the shift pedal "1" on the left
side of the engine.
KICKSTARTER CRANK
Rotate the kickstarter crank "1" away
from the engine. Push the starter
down lightly with your foot until the
gears engage, then kick smoothly
and forcefully to start the engine. This
model has a primary kickstarter crank
so the engine can be started in any
gear if the clutch is disengaged. In
normal practices, however, shift to
neutral before starting.
THROTTLE GRIP
The throttle grip "1" is located on the
right handlebar; it accelerates or de-
celerates the engine. For accelera-
tion, turn the grip toward you; for
deceleration, turn it away from you.
FRONT BRAKE LEVER
The front brake lever "1" is located on
the right handlebar. Pull it toward the
handlebar to activate the front brake.
REAR BRAKE PEDAL
The rear brake pedal "1" is located on
the right side of the machine. Press
down on the brake pedal to activate
the rear brake.
FUEL COCK
The fuel cock supplies fuel from the
tank to carburetor and also filters the
fuel. The fuel cock has the three posi-
tions:
OFF:
With the lever in this position, fuel will
not flow. Always return the lever to
this position when the engine is not
running.
ON:
With the lever in this position, fuel
flows to the carburetor. Normal riding
is done with the lever in this position.
RES:
With the lever in this position fuel
flows to the carburetor from the re-
serve section of the fuel tank after the
main supply of the fuel has been de-
pleted. Normal riding is possible with
the lever is in this position, but it is
recommended to add fuel as soon as
possible.
Page 24 of 224
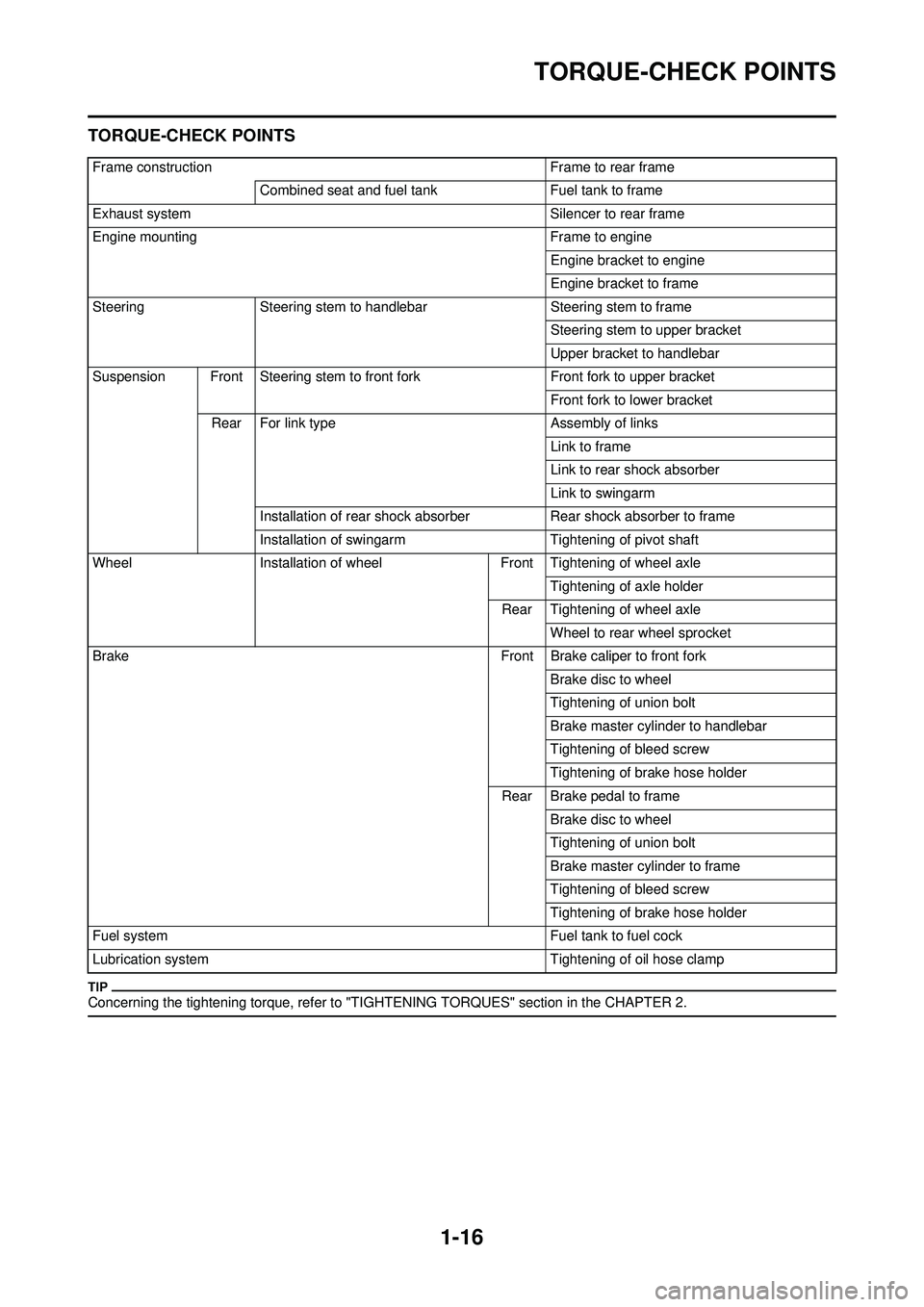
1-16
TORQUE-CHECK POINTS
TORQUE-CHECK POINTS
Concerning the tightening torque, refer to "TIGHTENING TORQUES" section in the CHAPTER 2.
Frame constructionFrame to rear frame
Combined seat and fuel tank Fuel tank to frame
Exhaust system Silencer to rear frame
Engine mounting Frame to engine
Engine bracket to engine
Engine bracket to frame
Steering Steering stem to handlebar Steering stem to frame
Steering stem to upper bracket
Upper bracket to handlebar
Suspension Front Steering stem to front fork Front fork to upper bracket
Front fork to lower bracket
Rear For link type Assembly of links
Link to frame
Link to rear shock absorber
Link to swingarm
Installation of rear shock absorber Rear shock absorber to frame
Installation of swingarm Tightening of pivot shaft
Wheel Installation of wheel Front Tightening of wheel axle
Tightening of axle holder
Rear Tightening of wheel axle Wheel to rear wheel sprocket
Brake Front Brake caliper to front fork
Brake disc to wheel
Tightening of union bolt
Brake master cylinder to handlebar
Tightening of bleed screw
Tightening of brake hose holder
Rear Brake pedal to frame Brake disc to wheel
Tightening of union bolt
Brake master cylinder to frame
Tightening of bleed screw
Tightening of brake hose holder
Fuel system Fuel tank to fuel cock
Lubrication system Tightening of oil hose clamp
Page 25 of 224
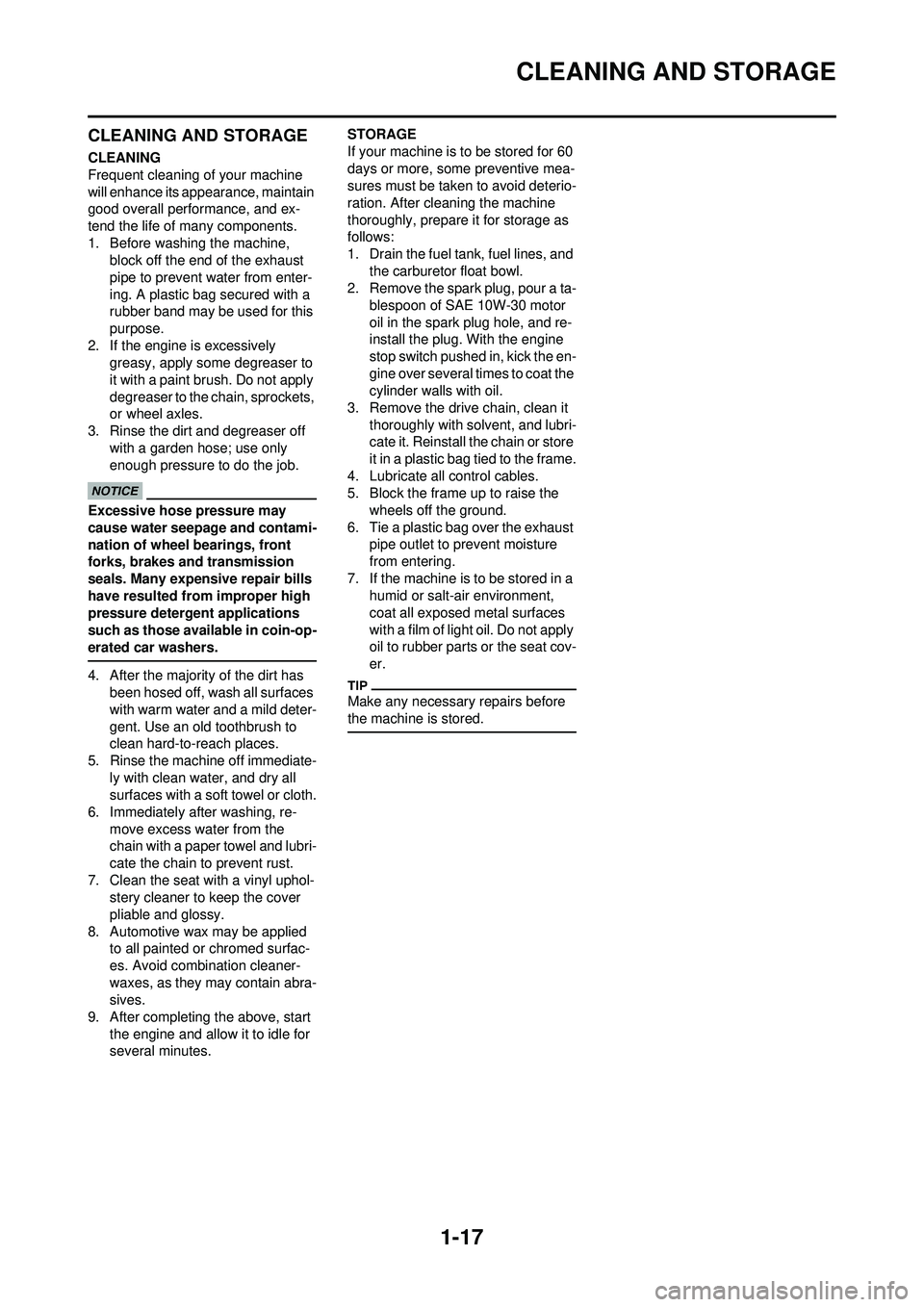
1-17
CLEANING AND STORAGE
CLEANING AND STORAGE
CLEANING
Frequent cleaning of your machine
will enhance its appearance, maintain
good overall performance, and ex-
tend the life of many components.
1. Before washing the machine, block off the end of the exhaust
pipe to prevent water from enter-
ing. A plastic bag secured with a
rubber band may be used for this
purpose.
2. If the engine is excessively greasy, apply some degreaser to
it with a paint brush. Do not apply
degreaser to the chain, sprockets,
or wheel axles.
3. Rinse the dirt and degreaser off with a garden hose; use only
enough pressure to do the job.
Excessive hose pressure may
cause water seepage and contami-
nation of wheel bearings, front
forks, brakes and transmission
seals. Many expensive repair bills
have resulted from improper high
pressure detergent applications
such as those available in coin-op-
erated car washers.
4. After the majority of the dirt has been hosed off, wash all surfaces
with warm water and a mild deter-
gent. Use an old toothbrush to
clean hard-to-reach places.
5. Rinse the machine off immediate- ly with clean water, and dry all
surfaces with a soft towel or cloth.
6. Immediately after washing, re- move excess water from the
chain with a paper towel and lubri-
cate the chain to prevent rust.
7. Clean the seat with a vinyl uphol- stery cleaner to keep the cover
pliable and glossy.
8. Automotive wax may be applied to all painted or chromed surfac-
es. Avoid combination cleaner-
waxes, as they may contain abra-
sives.
9. After completing the above, start the engine and allow it to idle for
several minutes. STORAGE
If your machine is to be stored for 60
days or more, some preventive mea-
sures must be taken to avoid deterio-
ration. After cleaning the machine
thoroughly, prepare it for storage as
follows:
1. Drain the fuel tank, fuel lines, and
the carburetor float bowl.
2. Remove the spark plug, pour a ta-
blespoon of SAE 10W-30 motor
oil in the spark plug hole, and re-
install the plug. With the engine
stop switch pushed in, kick the en-
gine over several times to coat the
cylinder walls with oil.
3. Remove the drive chain, clean it thoroughly with solvent, and lubri-
cate it. Reinstall the chain or store
it in a plastic bag tied to the frame.
4. Lubricate all control cables.
5. Block the frame up to raise the wheels off the ground.
6. Tie a plastic bag over the exhaust pipe outlet to prevent moisture
from entering.
7. If the machine is to be stored in a humid or salt-air environment,
coat all exposed metal surfaces
with a film of light oil. Do not apply
oil to rubber parts or the seat cov-
er.
Make any necessary repairs before
the machine is stored.
Page 28 of 224
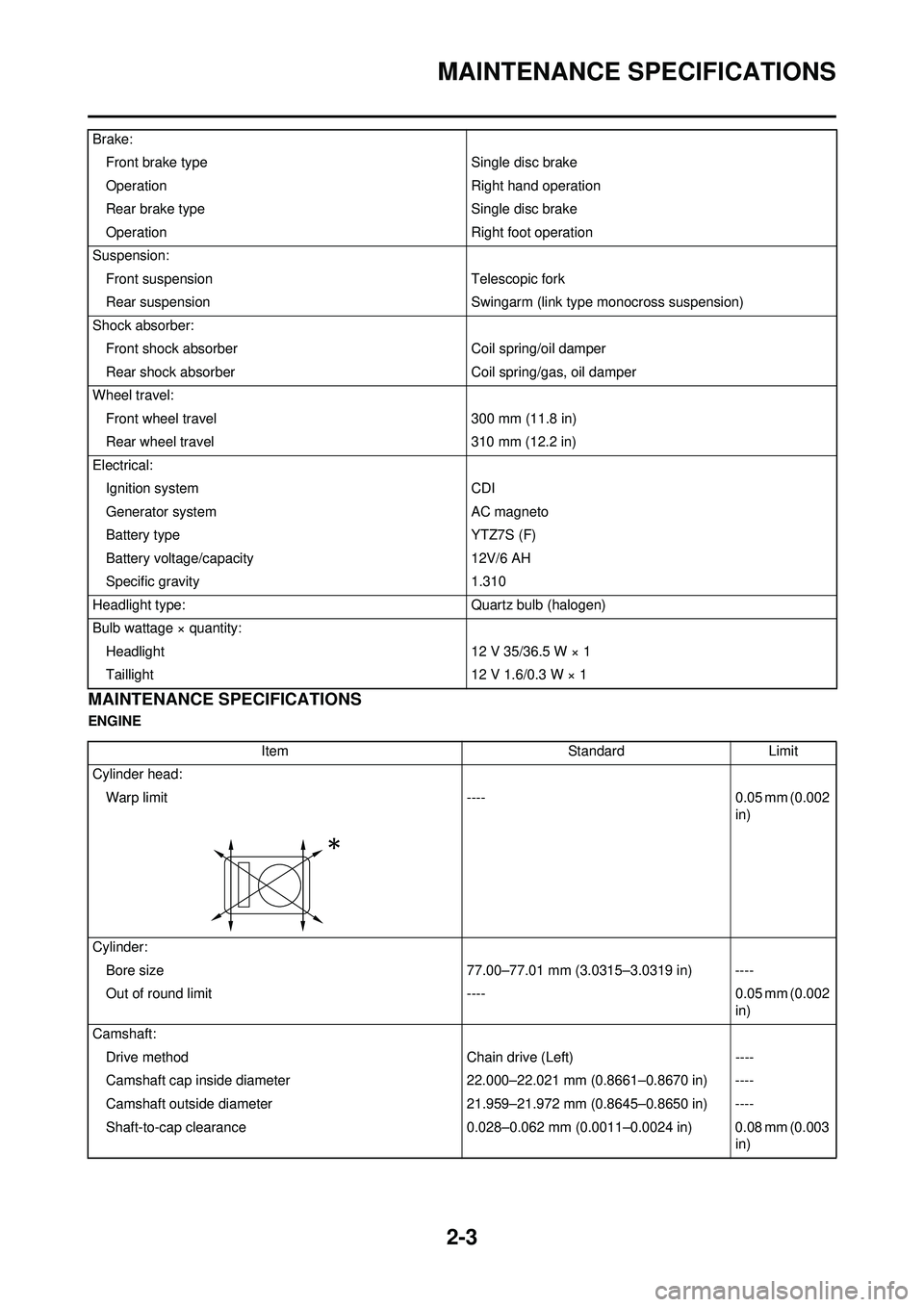
2-3
MAINTENANCE SPECIFICATIONS
MAINTENANCE SPECIFICATIONS
ENGINEBrake:
Front brake type Single disc brake
Operation Right hand operation
Rear brake type Single disc brake
Operation Right foot operation
Suspension: Front suspension Telescopic fork
Rear suspension Swingarm (link type monocross suspension)
Shock absorber: Front shock absorber Coil spring/oil damper
Rear shock absorber Coil spring/gas, oil damper
Wheel travel: Front wheel travel 300 mm (11.8 in)
Rear wheel travel 310 mm (12.2 in)
Electrical: Ignition system CDI
Generator system AC magneto
Battery type YTZ7S (F)
Battery voltage/capacity 12V/6 AH
Specific gravity 1.310
Headlight type: Quartz bulb (halogen)
Bulb wattage × quantity: Headlight 12 V 35/36.5 W × 1
Taillight 12 V 1.6/0.3 W × 1
ItemStandardLimit
Cylinder head: Warp limit ----0.05 mm (0.002
in)
Cylinder: Bore size 77.00–77.01 mm (3.0315–3.0319 in) ----
Out of round limit ----0.05 mm (0.002
in)
Camshaft: Drive method Chain drive (Left)----
Camshaft cap inside diameter 22.000–22.021 mm (0.8661–0.8670 in) ----
Camshaft outside diameter 21.959–21.972 mm (0.8645–0.8650 in) ----
Shaft-to-cap clearance 0.028–0.062 mm (0.0011–0.0024 in) 0.08 mm (0.003
in)
Page 35 of 224
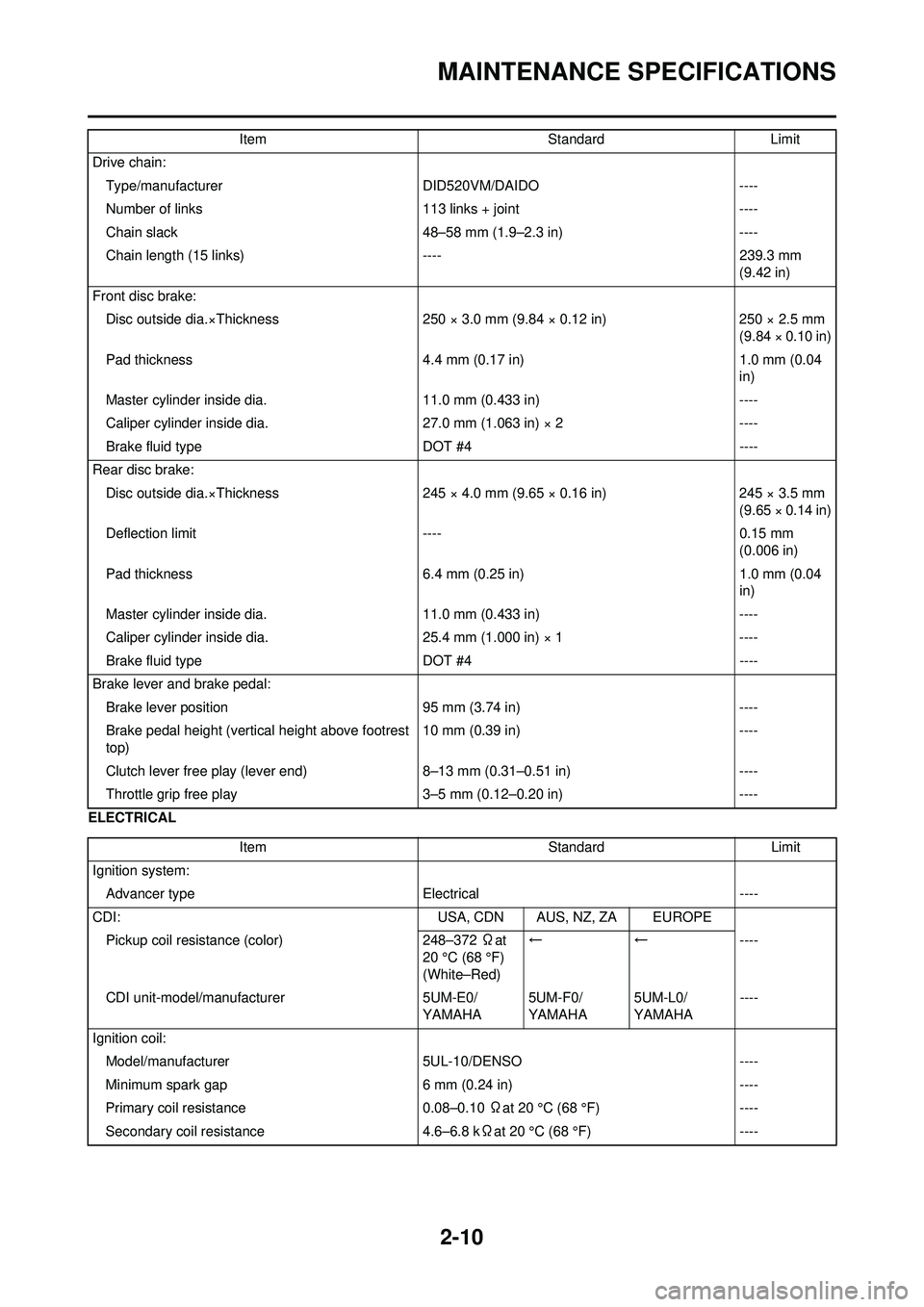
2-10
MAINTENANCE SPECIFICATIONS
ELECTRICALDrive chain:
Type/manufacturer DID520VM/DAIDO----
Number of links 113 links + joint----
Chain slack 48–58 mm (1.9–2.3 in)----
Chain length (15 links) ----239.3 mm
(9.42 in)
Front disc brake: Disc outside dia.×Thickness 250 × 3.0 mm (9.84 × 0.12 in)250 × 2.5 mm
(9.84 × 0.10 in)
Pad thickness 4.4 mm (0.17 in)1.0 mm (0.04
in)
Master cylinder inside dia. 11.0 mm (0.433 in)----
Caliper cylinder inside dia. 27.0 mm (1.063 in) × 2----
Brake fluid type DOT #4----
Rear disc brake: Disc outside dia.×Thickness 245 × 4.0 mm (9.65 × 0.16 in)245 × 3.5 mm
(9.65 × 0.14 in)
Deflection limit ----0.15 mm
(0.006 in)
Pad thickness 6.4 mm (0.25 in)1.0 mm (0.04
in)
Master cylinder inside dia. 11.0 mm (0.433 in)----
Caliper cylinder inside dia. 25.4 mm (1.000 in) × 1----
Brake fluid type DOT #4----
Brake lever and brake pedal: Brake lever position 95 mm (3.74 in)----
Brake pedal height (vertical height above footrest
top) 10 mm (0.39 in)
----
Clutch lever free play (lever end) 8–13 mm (0.31–0.51 in)----
Throttle grip free play 3–5 mm (0.12–0.20 in)----
Item
StandardLimit
Item StandardLimit
Ignition system: Advancer type Electrical ----
CDI: USA, CDN AUS, NZ, ZA EUROPE
Pickup coil resistance (color) 248–372 Ωat
20 °C (68 °F)
(White–Red) ←←----
CDI unit-model/manufacturer 5UM-E0/
YAMAHA 5UM-F0/
YAMAHA5UM-L0/
YAMAHA----
Ignition coil: Model/manufacturer 5UL-10/DENSO ----
Minimum spark gap 6 mm (0.24 in) ----
Primary coil resistance 0.08–0.10 Ωat 20 °C (68 °F) ----
Secondary coil resistance 4.6–6.8 kΩat 20 °C (68 °F) ----
Page 39 of 224
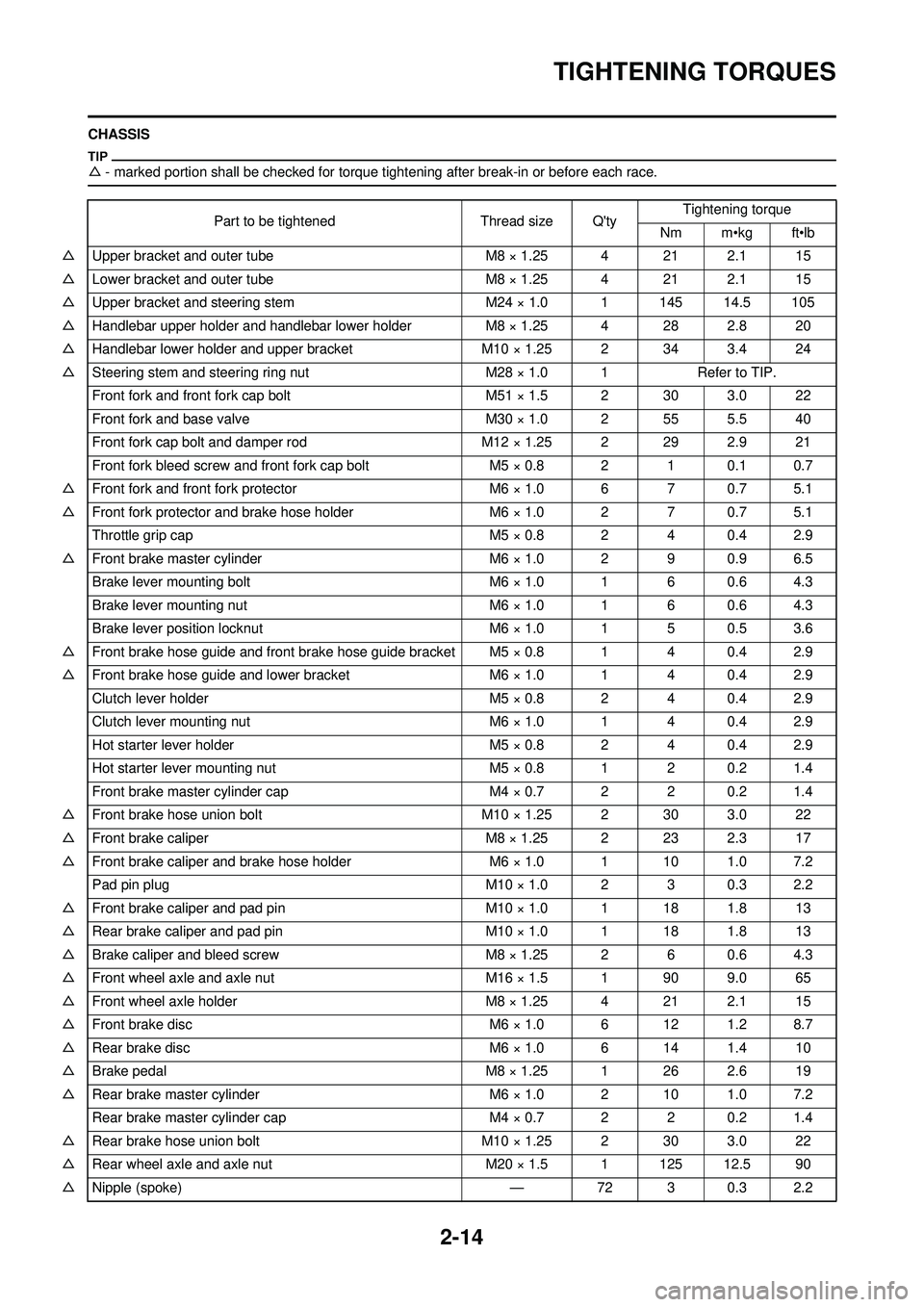
2-14
TIGHTENING TORQUES
CHASSIS
△- marked portion shall be checked for torque tightening after break-in or before each race.
Part to be tightened Thread size Q'tyTightening torque
Nm m•kg ft•lb
△ Upper bracket and outer tube M8 × 1.25 4 21 2.1 15
△ Lower bracket and outer tube M8 × 1.25 4 21 2.1 15
△ Upper bracket and steering stem M24 × 1.0 1 145 14.5 105
△ Handlebar upper holder and handlebar lower holder M8 × 1.25 4 28 2.8 20
△ Handlebar lower holder and upper bracket M10 × 1.25 2 34 3.4 24
△ Steering stem and steering ring nut M28 × 1.0 1Refer to TIP.
Front fork and front fork cap bolt M51 × 1.5 2 30 3.0 22
Front fork and base valve M30 × 1.0 2 55 5.5 40
Front fork cap bolt and damper rod M12 × 1.25 2 29 2.9 21
Front fork bleed screw and front fork cap bolt M5 × 0.8 2 1 0.1 0.7
△ Front fork and front fork protector M6 × 1.0 6 7 0.7 5.1
△ Front fork protector and brake hose holder M6 × 1.0 2 7 0.7 5.1
Throttle grip cap M5 × 0.8 2 4 0.4 2.9
△ Front brake master cylinder M6 × 1.0 2 9 0.9 6.5
Brake lever mounting bolt M6 × 1.0 1 6 0.6 4.3
Brake lever mounting nut M6 × 1.0 1 6 0.6 4.3
Brake lever position locknut M6 × 1.0 1 5 0.5 3.6
△ Front brake hose guide and front brake hose guide bracket M5 × 0.8 1 4 0.4 2.9
△ Front brake hose guide and lower bracket M6 × 1.0 1 4 0.4 2.9
Clutch lever holder M5 × 0.8 2 4 0.4 2.9
Clutch lever mounting nut M6 × 1.0 1 4 0.4 2.9
Hot starter lever holder M5 × 0.8 2 4 0.4 2.9
Hot starter lever mounting nut M5 × 0.8 1 2 0.2 1.4
Front brake master cylinder cap M4 × 0.7 2 2 0.2 1.4
△ Front brake hose union bolt M10 × 1.25 2 30 3.0 22
△ Front brake caliper M8 × 1.25 2 23 2.3 17
△ Front brake caliper and brake hose holder M6 × 1.0 1 10 1.0 7.2
Pad pin plug M10 × 1.0 2 3 0.3 2.2
△ Front brake caliper and pad pin M10 × 1.0 1 18 1.8 13
△ Rear brake caliper and pad pin M10 × 1.0 1 18 1.8 13
△ Brake caliper and bleed screw M8 × 1.25 2 6 0.6 4.3
△ Front wheel axle and axle nut M16 × 1.5 1 90 9.0 65
△ Front wheel axle holder M8 × 1.25 4 21 2.1 15
△ Front brake disc M6 × 1.0 6 12 1.2 8.7
△ Rear brake disc M6 × 1.0 6 14 1.4 10
△ Brake pedal M8 × 1.25 1 26 2.6 19
△ Rear brake master cylinder M6 × 1.0 2 10 1.0 7.2
Rear brake master cylinder cap M4 × 0.7 2 2 0.2 1.4
△ Rear brake hose union bolt M10 × 1.25 2 30 3.0 22
△ Rear wheel axle and axle nut M20 × 1.5 1 125 12.5 90
△ Nipple (spoke) —72 3 0.3 2.2
Page 40 of 224
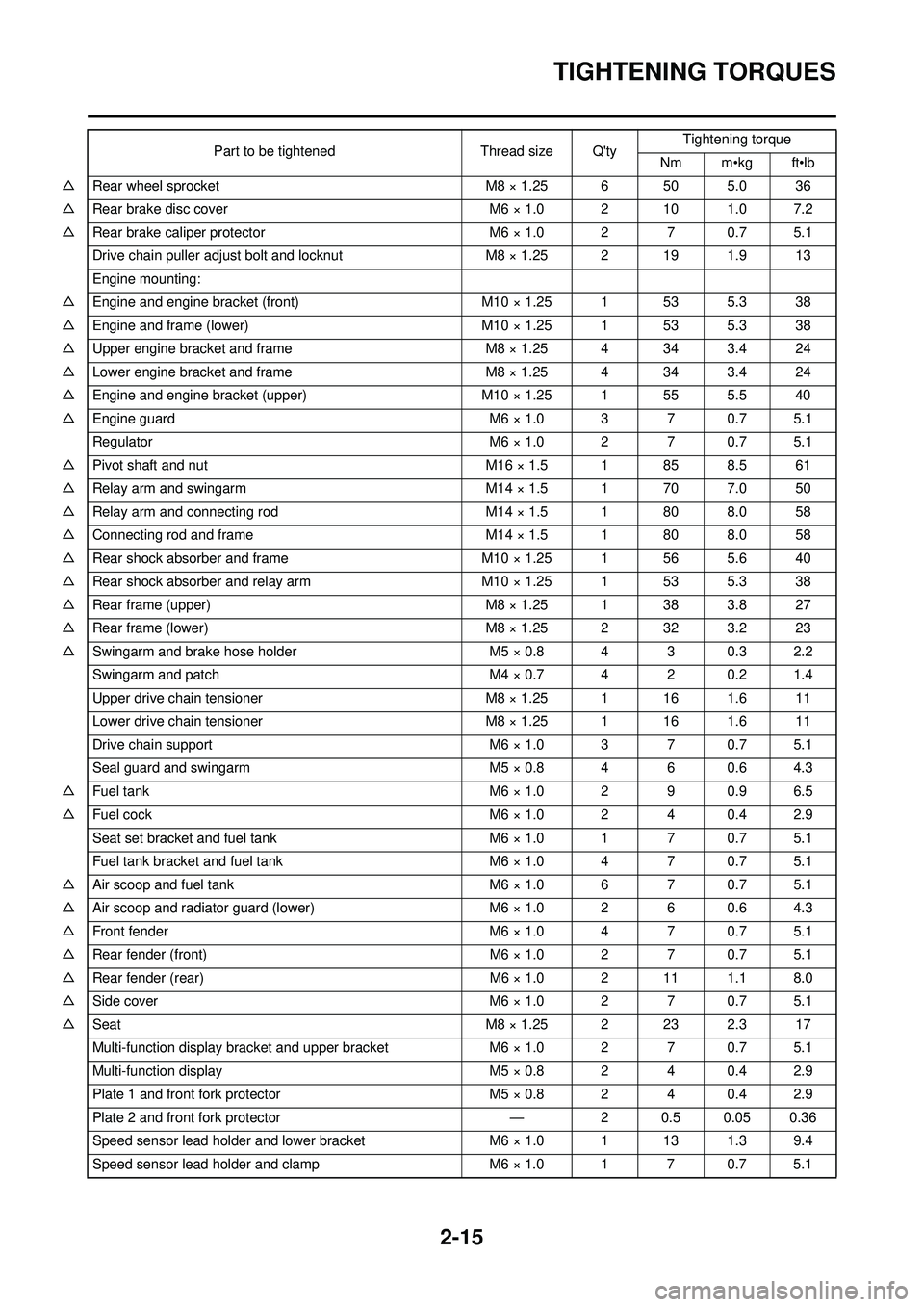
2-15
TIGHTENING TORQUES
△Rear wheel sprocket M8 × 1.25 6 50 5.0 36
△ Rear brake disc cover M6 × 1.0 2 10 1.0 7.2
△ Rear brake caliper protector M6 × 1.0 2 7 0.7 5.1
Drive chain puller adjust bolt and locknut M8 × 1.25 2 19 1.9 13
Engine mounting:
△ Engine and engine bracket (front) M10 × 1.25 1 53 5.3 38
△ Engine and frame (lower) M10 × 1.25 1 53 5.3 38
△ Upper engine bracket and frame M8 × 1.25 4 34 3.4 24
△ Lower engine bracket and frame M8 × 1.25 4 34 3.4 24
△ Engine and engine bracket (upper) M10 × 1.25 1 55 5.5 40
△ Engine guard M6 × 1.0 3 7 0.7 5.1
Regulator M6 × 1.0 2 7 0.7 5.1
△ Pivot shaft and nut M16 × 1.5 1 85 8.5 61
△ Relay arm and swingarm M14 × 1.5 1 70 7.0 50
△ Relay arm and connecting rod M14 × 1.5 1 80 8.0 58
△ Connecting rod and frame M14 × 1.5 1 80 8.0 58
△ Rear shock absorber and frame M10 × 1.25 1 56 5.6 40
△ Rear shock absorber and relay arm M10 × 1.25 1 53 5.3 38
△ Rear frame (upper) M8 × 1.25 1 38 3.8 27
△ Rear frame (lower) M8 × 1.25 2 32 3.2 23
△ Swingarm and brake hose holder M5 × 0.8 4 3 0.3 2.2
Swingarm and patch M4 × 0.7 4 2 0.2 1.4
Upper drive chain tensioner M8 × 1.25 1 16 1.6 11
Lower drive chain tensioner M8 × 1.25 1 16 1.6 11
Drive chain support M6 × 1.0 3 7 0.7 5.1
Seal guard and swingarm M5 × 0.8 4 6 0.6 4.3
△ Fuel tank M6 × 1.0 2 9 0.9 6.5
△ Fuel cock M6 × 1.0 2 4 0.4 2.9
Seat set bracket and fuel tank M6 × 1.0 1 7 0.7 5.1
Fuel tank bracket and fuel tank M6 × 1.0 4 7 0.7 5.1
△ Air scoop and fuel tank M6 × 1.0 6 7 0.7 5.1
△ Air scoop and radiator guard (lower) M6 × 1.0 2 6 0.6 4.3
△ Front fender M6 × 1.0 4 7 0.7 5.1
△ Rear fender (front) M6 × 1.0 2 7 0.7 5.1
△ Rear fender (rear) M6 × 1.0 2 11 1.1 8.0
△ Side cover M6 × 1.0 2 7 0.7 5.1
△ Seat M8 × 1.25 2 23 2.3 17
Multi-function display bracket and upper bracket M6 × 1.0 2 7 0.7 5.1
Multi-function display M5 × 0.8 2 4 0.4 2.9
Plate 1 and front fork protector M5 × 0.8 2 4 0.4 2.9
Plate 2 and front fork protector — 2 0.5 0.05 0.36
Speed sensor lead holder and lower bracket M6 × 1.0 1 13 1.3 9.4
Speed sensor lead holder and clamp M6 × 1.0 1 7 0.7 5.1 Part to be tightened Thread size Q'ty
Tightening torque
Nm m•kg ft•lb