fuel filter YAMAHA WR 250F 2009 Owners Manual
[x] Cancel search | Manufacturer: YAMAHA, Model Year: 2009, Model line: WR 250F, Model: YAMAHA WR 250F 2009Pages: 224, PDF Size: 13.93 MB
Page 16 of 224
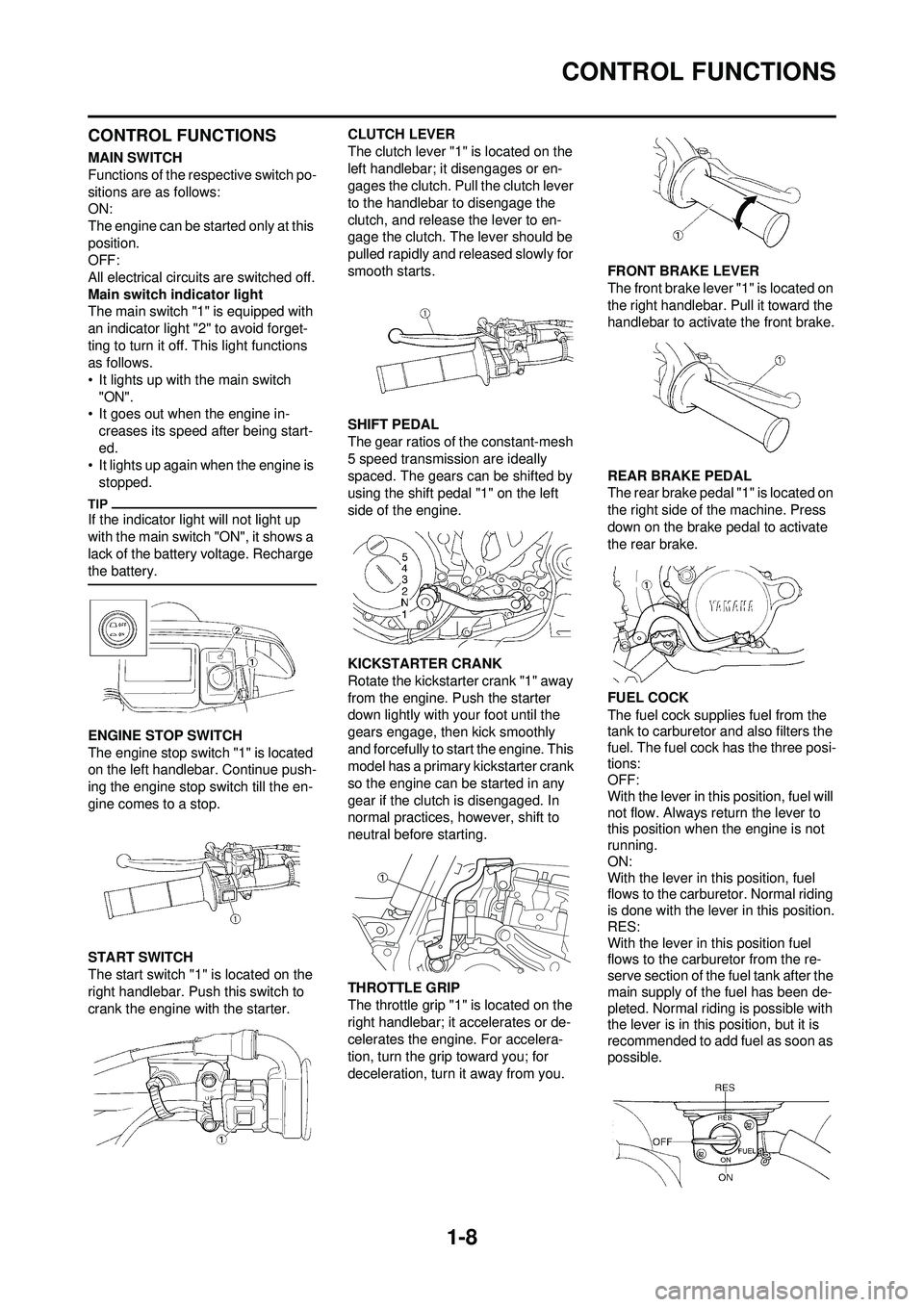
1-8
CONTROL FUNCTIONS
CONTROL FUNCTIONS
MAIN SWITCH
Functions of the respective switch po-
sitions are as follows:
ON:
The engine can be started only at this
position.
OFF:
All electrical circuits are switched off.
Main switch indicator light
The main switch "1" is equipped with
an indicator light "2" to avoid forget-
ting to turn it off. This light functions
as follows.
• It lights up with the main switch "ON".
• It goes out when the engine in-
creases its speed after being start-
ed.
• It lights up again when the engine is
stopped.
If the indicator light will not light up
with the main switch "ON", it shows a
lack of the battery voltage. Recharge
the battery.
ENGINE STOP SWITCH
The engine stop switch "1" is located
on the left handlebar. Continue push-
ing the engine stop switch till the en-
gine comes to a stop.
START SWITCH
The start switch "1" is located on the
right handlebar. Push this switch to
crank the engine with the starter. CLUTCH LEVER
The clutch lever "1" is located on the
left handlebar; it disengages or en-
gages the clutch. Pull the clutch lever
to the handlebar to disengage the
clutch, and release the lever to en-
gage the clutch. The lever should be
pulled rapidly and released slowly for
smooth starts.
SHIFT PEDAL
The gear ratios of the constant-mesh
5 speed transmission are ideally
spaced. The gears can be shifted by
using the shift pedal "1" on the left
side of the engine.
KICKSTARTER CRANK
Rotate the kickstarter crank "1" away
from the engine. Push the starter
down lightly with your foot until the
gears engage, then kick smoothly
and forcefully to start the engine. This
model has a primary kickstarter crank
so the engine can be started in any
gear if the clutch is disengaged. In
normal practices, however, shift to
neutral before starting.
THROTTLE GRIP
The throttle grip "1" is located on the
right handlebar; it accelerates or de-
celerates the engine. For accelera-
tion, turn the grip toward you; for
deceleration, turn it away from you.
FRONT BRAKE LEVER
The front brake lever "1" is located on
the right handlebar. Pull it toward the
handlebar to activate the front brake.
REAR BRAKE PEDAL
The rear brake pedal "1" is located on
the right side of the machine. Press
down on the brake pedal to activate
the rear brake.
FUEL COCK
The fuel cock supplies fuel from the
tank to carburetor and also filters the
fuel. The fuel cock has the three posi-
tions:
OFF:
With the lever in this position, fuel will
not flow. Always return the lever to
this position when the engine is not
running.
ON:
With the lever in this position, fuel
flows to the carburetor. Normal riding
is done with the lever in this position.
RES:
With the lever in this position fuel
flows to the carburetor from the re-
serve section of the fuel tank after the
main supply of the fuel has been de-
pleted. Normal riding is possible with
the lever is in this position, but it is
recommended to add fuel as soon as
possible.
Page 22 of 224
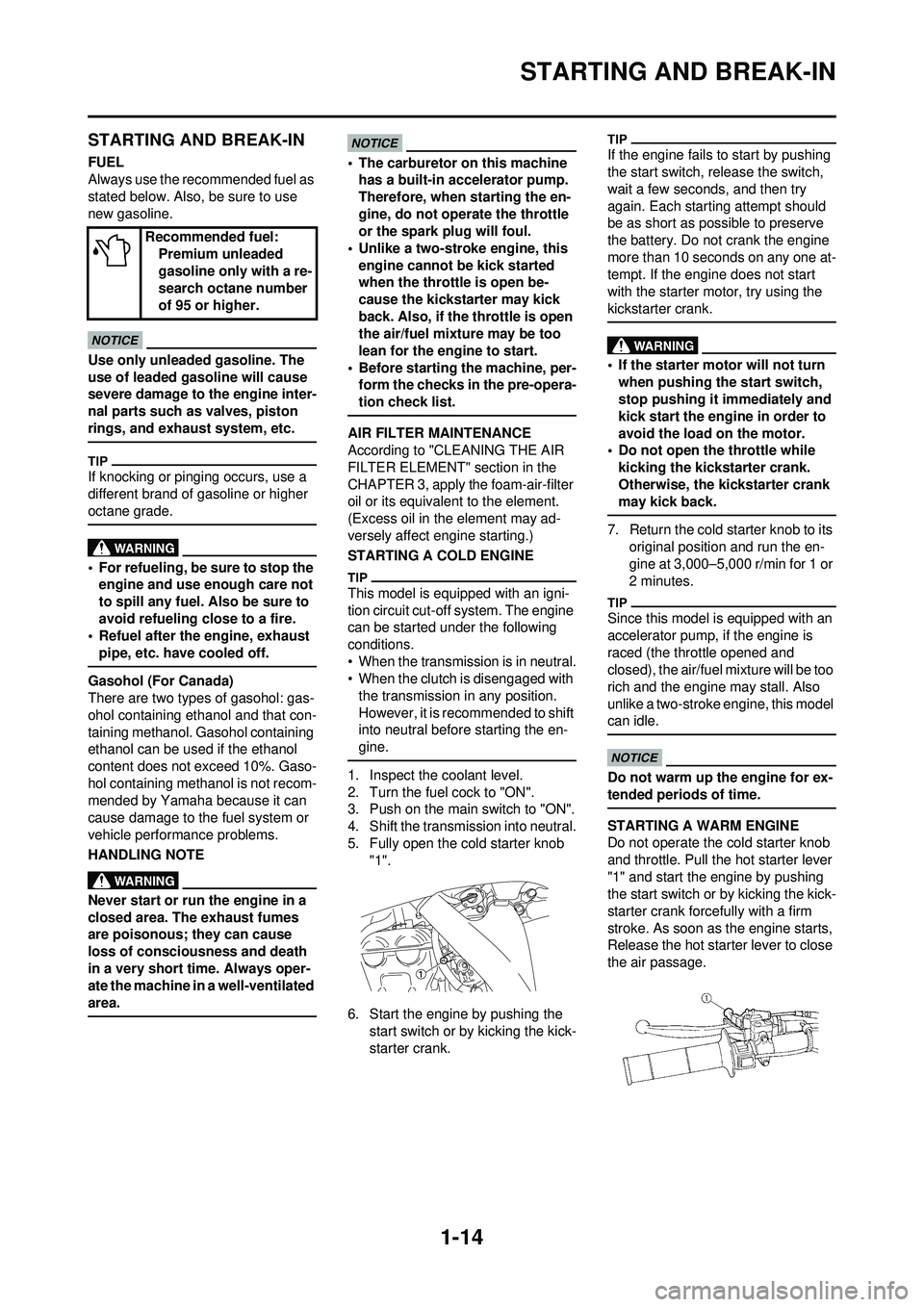
1-14
STARTING AND BREAK-IN
STARTING AND BREAK-IN
FUEL
Always use the recommended fuel as
stated below. Also, be sure to use
new gasoline.
Use only unleaded gasoline. The
use of leaded gasoline will cause
severe damage to the engine inter-
nal parts such as valves, piston
rings, and exhaust system, etc.
If knocking or pinging occurs, use a
different brand of gasoline or higher
octane grade.
• For refueling, be sure to stop the engine and use enough care not
to spill any fuel. Also be sure to
avoid refueling close to a fire.
• Refuel after the engine, exhaust
pipe, etc. have cooled off.
Gasohol (For Canada)
There are two types of gasohol: gas-
ohol containing ethanol and that con-
taining methanol. Gasohol containing
ethanol can be used if the ethanol
content does not exceed 10%. Gaso-
hol containing methanol is not recom-
mended by Yamaha because it can
cause damage to the fuel system or
vehicle performance problems.
HANDLING NOTE
Never start or run the engine in a
closed area. The exhaust fumes
are poisonous; they can cause
loss of consciousness and death
in a very short time. Always oper-
ate the machine in a well-ventilated
area.
• The carburetor on this machine has a built-in accelerator pump.
Therefore, when starting the en-
gine, do not operate the throttle
or the spark plug will foul.
• Unlike a two-stroke engine, this engine cannot be kick started
when the throttle is open be-
cause the kickstarter may kick
back. Also, if the throttle is open
the air/fuel mixture may be too
lean for the engine to start.
• Before starting the machine, per- form the checks in the pre-opera-
tion check list.
AIR FILTER MAINTENANCE
According to "CLEANING THE AIR
FILTER ELEMENT" section in the
CHAPTER 3, apply the foam-air-filter
oil or its equivalent to the element.
(Excess oil in the element may ad-
versely affect engine starting.)
STARTING A COLD ENGINE
This model is equipped with an igni-
tion circuit cut-off system. The engine
can be started under the following
conditions.
• When the transmission is in neutral.
• When the clutch is disengaged with
the transmission in any position.
However, it is recommended to shift
into neutral before starting the en-
gine.
1. Inspect the coolant level.
2. Turn the fuel cock to "ON".
3. Push on the main switch to "ON".
4. Shift the transmission into neutral.
5. Fully open the cold starter knob "1".
6. Start the engine by pushing the start switch or by kicking the kick-
starter crank.
If the engine fails to start by pushing
the start switch, release the switch,
wait a few seconds, and then try
again. Each starting attempt should
be as short as possible to preserve
the battery. Do not crank the engine
more than 10 seconds on any one at-
tempt. If the engine does not start
with the starter motor, try using the
kickstarter crank.
• If the starter motor will not turn
when pushing the start switch,
stop pushing it immediately and
kick start the engine in order to
avoid the load on the motor.
• Do not open the throttle while
kicking the kickstarter crank.
Otherwise, the kickstarter crank
may kick back.
7. Return the cold starter knob to its original position and run the en-
gine at 3,000–5,000 r/min for 1 or
2 minutes.
Since this model is equipped with an
accelerator pump, if the engine is
raced (the throttle opened and
closed), the air/fuel mixture will be too
rich and the engine may stall. Also
unlike a two-stroke engine, this model
can idle.
Do not warm up the engine for ex-
tended periods of time.
STARTING A WARM ENGINE
Do not operate the cold starter knob
and throttle. Pull the hot starter lever
"1" and start the engine by pushing
the start switch or by kicking the kick-
starter crank forcefully with a firm
stroke. As soon as the engine starts,
Release the hot starter lever to close
the air passage.
Recommended fuel:
Premium unleaded
gasoline only with a re-
search octane number
of 95 or higher.
Page 27 of 224
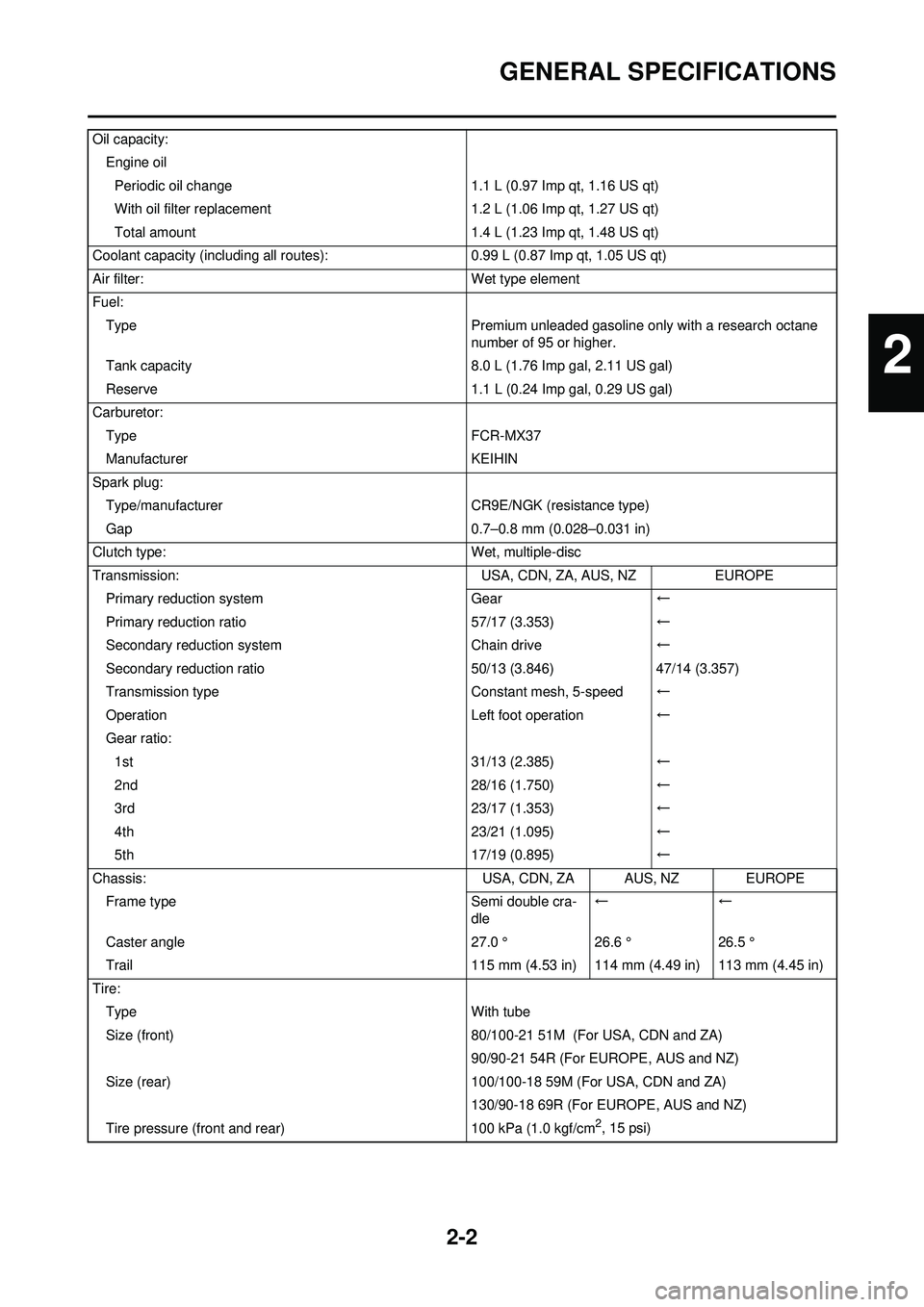
2-2
GENERAL SPECIFICATIONS
Oil capacity:Engine oilPeriodic oil change 1.1 L (0.97 Imp qt, 1.16 US qt)
With oil filter replacement 1.2 L (1.06 Imp qt, 1.27 US qt)
Total amount 1.4 L (1.23 Imp qt, 1.48 US qt)
Coolant capacity (including all routes): 0.99 L (0.87 Imp qt, 1.05 US qt)
Air filter: Wet type element
Fuel: Type Premium unleaded gasoline only with a research octane
number of 95 or higher.
Tank capacity 8.0 L (1.76 Imp gal, 2.11 US gal)
Reserve 1.1 L (0.24 Imp gal, 0.29 US gal)
Carburetor: Type FCR-MX37
Manufacturer KEIHIN
Spark plug: Type/manufacturer CR9E/NGK (resistance type)
Gap 0.7–0.8 mm (0.028–0.031 in)
Clutch type: Wet, multiple-disc
Transmission: USA, CDN, ZA, AUS, NZEUROPE
Primary reduction system Gear←
Primary reduction ratio 57/17 (3.353)←
Secondary reduction system Chain drive←
Secondary reduction ratio 50/13 (3.846)47/14 (3.357)
Transmission type Constant mesh, 5-speed←
Operation Left foot operation←
Gear ratio: 1st 31/13 (2.385)←
2nd 28/16 (1.750)←
3rd 23/17 (1.353)←
4th 23/21 (1.095)←
5th 17/19 (0.895)←
Chassis: USA, CDN, ZA AUS, NZ EUROPE
Frame type Semi double cra-
dle ←←
Caster angle 27.0 °26.6 ° 26.5 °
Trail 115 mm (4.53 in) 114 mm (4.49 in) 113 mm (4.45 in)
Tire: Type With tube
Size (front) 80/100-21 51M (For USA, CDN and ZA)
90/90-21 54R (For EUROPE, AUS and NZ)
Size (rear) 100/100-18 59M (For USA, CDN and ZA)
130/90-18 69R (For EUROPE, AUS and NZ)
Tire pressure (front and rear) 100 kPa (1.0 kgf/cm
2, 15 psi)
2
Page 54 of 224
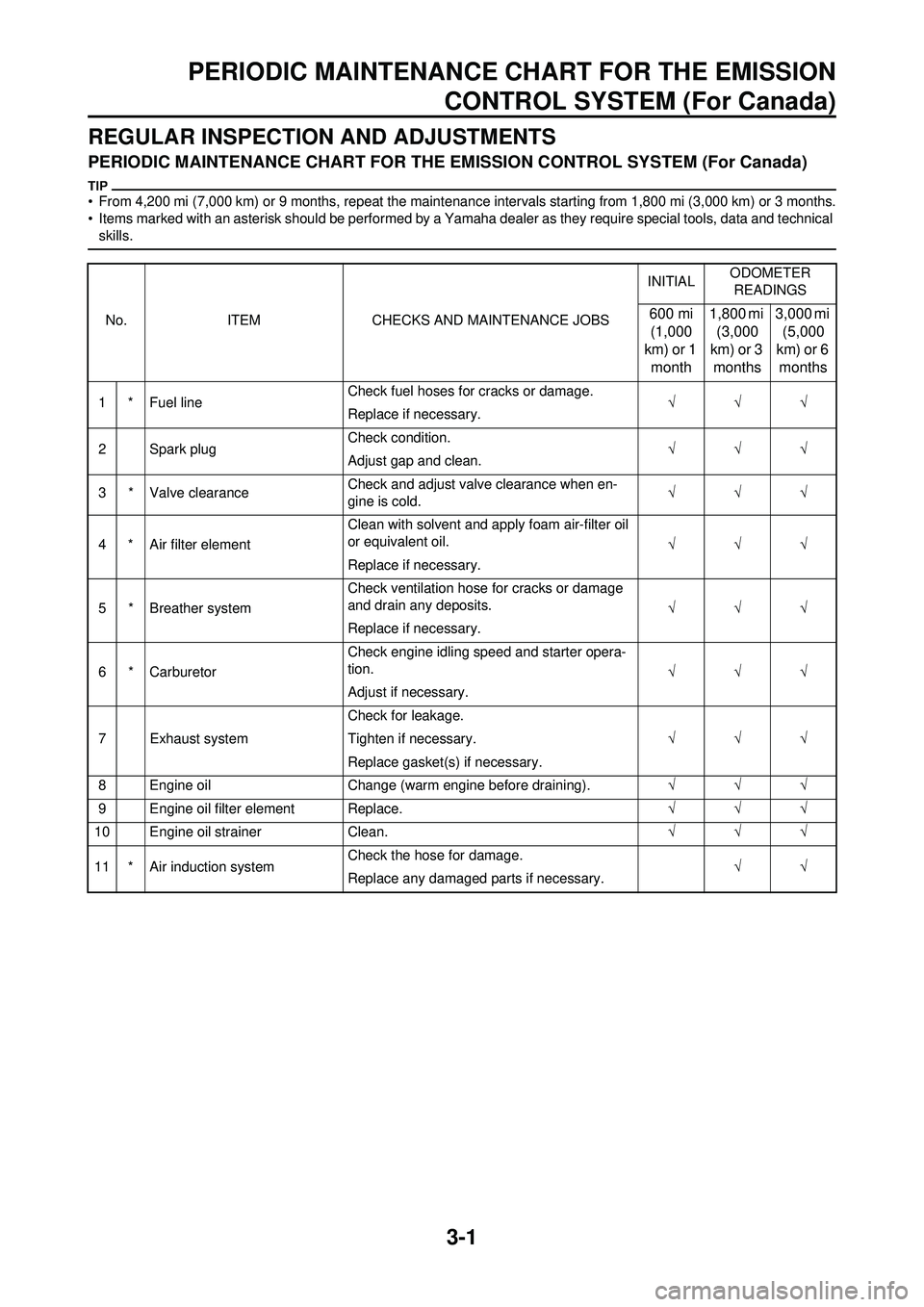
3-1
PERIODIC MAINTENANCE CHART FOR THE EMISSIONCONTROL SYSTEM (For Canada)
REGULAR INSPECTION AND ADJUSTMENTS
PERIODIC MAINTENANCE CHART FOR THE EMISSION CONTROL SYSTEM (For Canada)
• From 4,200 mi (7,000 km) or 9 months, repeat the maintenance intervals starting from 1,800 mi (3,000 km) or 3 months.
• Items marked with an asterisk should be performed by a Yamaha dealer as they require special tools, data and technical
skills.
No. ITEM CHECKS AND MAINTENANCE JOBS INITIAL
ODOMETER
READINGS600 mi (1,000
km) or 1 month 1,800 mi
(3,000
km) or 3 months 3,000 mi
(5,000
km) or 6 months
1*Fuel line Check fuel hoses for cracks or damage.
√√√
Replace if necessary.
2 Spark plug Check condition.
√√√
Adjust gap and clean.
3 * Valve clearance Check and adjust valve clearance when en-
gine is cold. √√√
4 * Air filter element Clean with solvent and apply foam air-filter oil
or equivalent oil.
√√√
Replace if necessary.
5 * Breather system Check ventilation hose for cracks or damage
and drain any deposits.
√√√
Replace if necessary.
6 * Carburetor Check engine idling speed and starter opera-
tion.
√√√
Adjust if necessary.
7 Exhaust system Check for leakage.
√√√
Tighten if necessary.
Replace gasket(s) if necessary.
8 Engine oil Change (warm engine before draining). √√√
9 Engine oil filter element Replace. √√√
10 Engine oil strainer Clean. √√√
11 * Air induction system Check the hose for damage.
√√
Replace any damaged parts if necessary.
Page 58 of 224
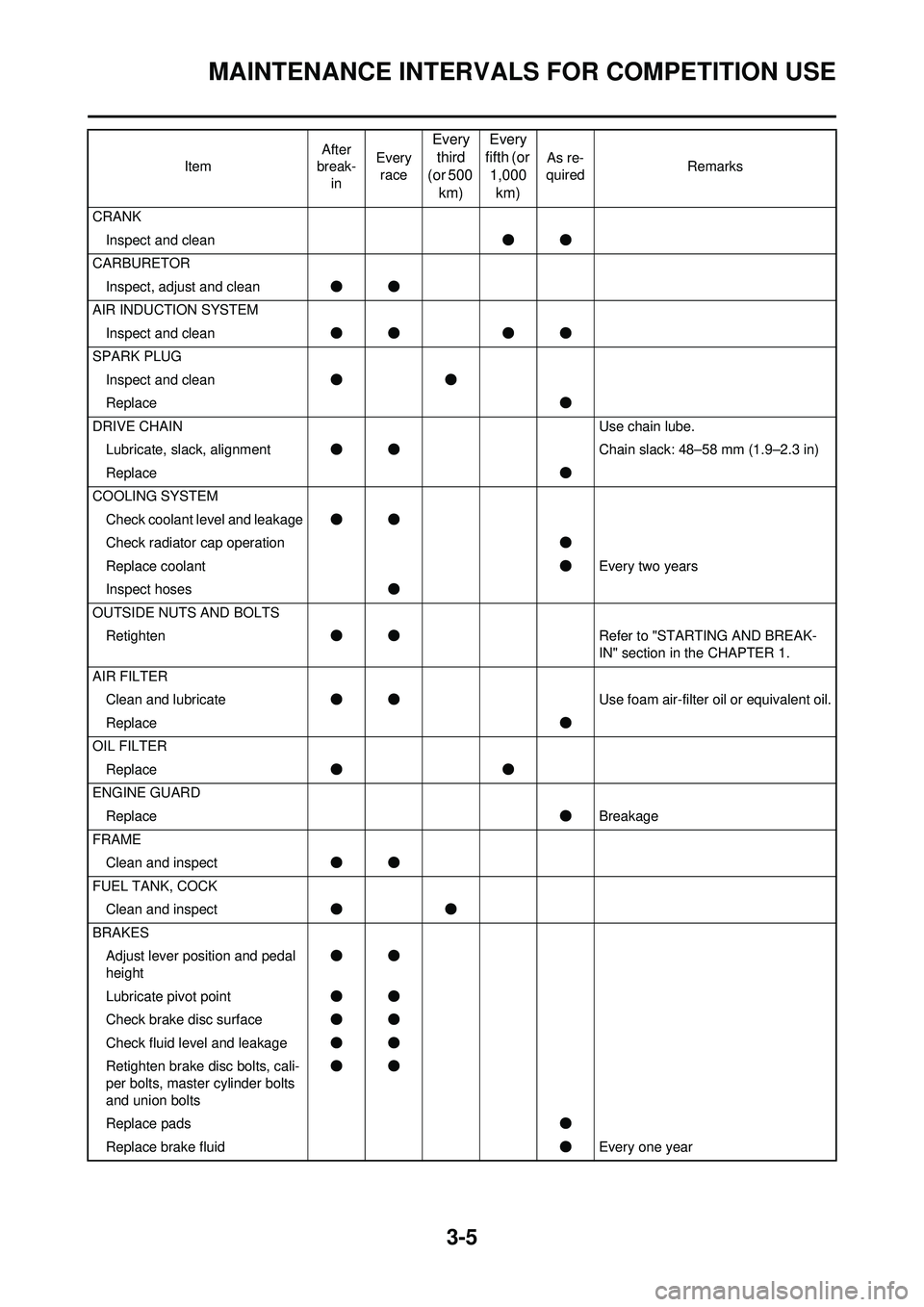
3-5
MAINTENANCE INTERVALS FOR COMPETITION USE
CRANKInspect and clean ●●
CARBURETOR Inspect, adjust and clean ●●
AIR INDUCTION SYSTEM Inspect and clean ●● ●●
SPARK PLUG Inspect and clean ●●
Replace ●
DRIVE CHAIN Use chain lube.
Lubricate, slack, alignment ●● Chain slack: 48–58 mm (1.9–2.3 in)
Replace ●
COOLING SYSTEM Check coolant level and leakage ●●
Check radiator cap operation ●
Replace coolant ●Every two years
Inspect hoses ●
OUTSIDE NUTS AND BOLTS Retighten ●● Refer to "STARTING AND BREAK-
IN" section in the CHAPTER 1.
AIR FILTER Clean and lubricate ●● Use foam air-filter oil or equivalent oil.
Replace ●
OIL FILTER Replace ●●
ENGINE GUARD Replace ●Breakage
FRAME Clean and inspect ●●
FUEL TANK, COCK Clean and inspect ●●
BRAKES Adjust lever position and pedal
height ●●
Lubricate pivot point ●●
Check brake disc surface ●●
Check fluid level and leakage ●●
Retighten brake disc bolts, cali-
per bolts, master cylinder bolts
and union bolts ●●
Replace pads ●
Replace brake fluid ●Every one year
Item
After
break-
in Every
race
Every third
(or 500 km) Every
fifth (or 1,000 km)
As re-
quired Remarks
Page 61 of 224
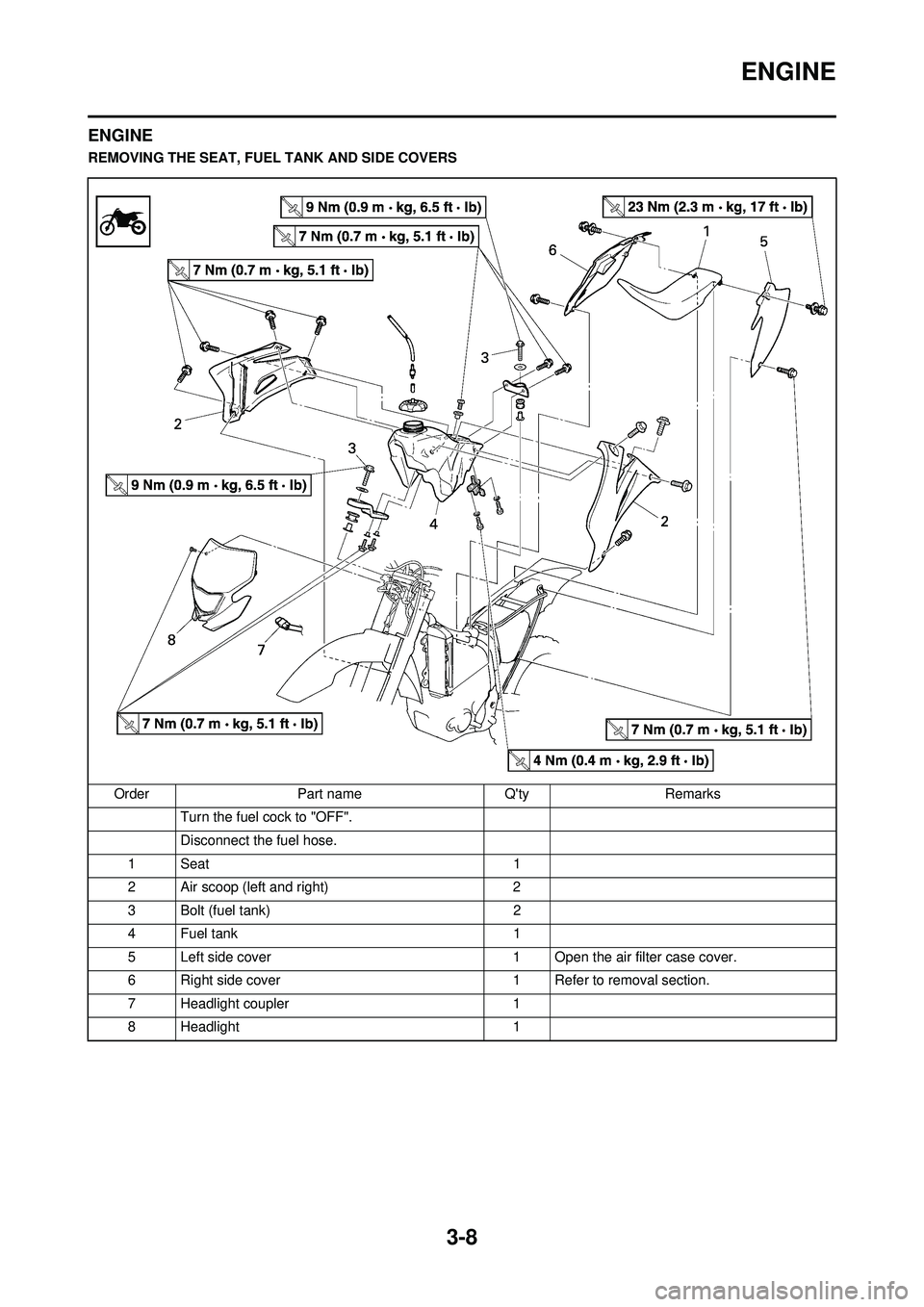
3-8
ENGINE
ENGINE
REMOVING THE SEAT, FUEL TANK AND SIDE COVERSOrder Part name Q'ty Remarks Turn the fuel cock to "OFF".
Disconnect the fuel hose.
1 Seat 1
2 Air scoop (left and right) 2
3 Bolt (fuel tank) 2
4 Fuel tank 1
5 Left side cover 1 Open the air filter case cover.
6 Right side cover 1 Refer to removal section.
7 Headlight coupler 1
8 Headlight 1
Page 91 of 224
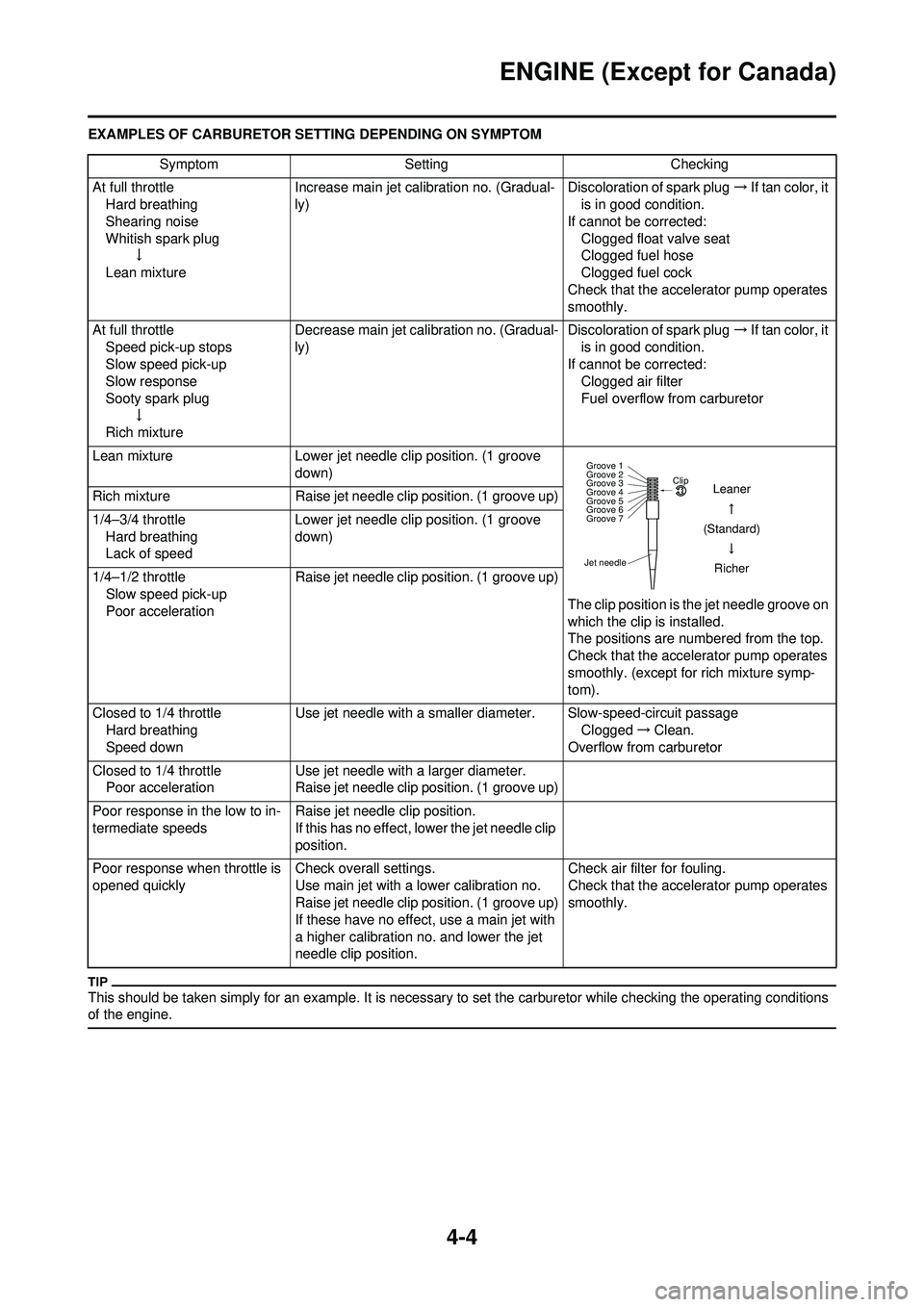
4-4
ENGINE (Except for Canada)
EXAMPLES OF CARBURETOR SETTING DEPENDING ON SYMPTOM
This should be taken simply for an example. It is necessary to set the carburetor while checking the operating conditions
of the engine.
SymptomSetting Checking
At full throttle Hard breathing
Shearing noise
Whitish spark plug ↓
Lean mixture Increase main jet calibration no. (Gradual-
ly)
Discoloration of spark plug
→If tan color, it
is in good condition.
If cannot be corrected: Clogged float valve seat
Clogged fuel hose
Clogged fuel cock
Check that the accelerator pump operates
smoothly.
At full throttle Speed pick-up stops
Slow speed pick-up
Slow response
Sooty spark plug ↓
Rich mixture Decrease main jet calibration no. (Gradual-
ly)
Discoloration of spark plug
→If tan color, it
is in good condition.
If cannot be corrected: Clogged air filter
Fuel overflow from carburetor
Lean mixture Lower jet needle clip position. (1 groove
down)
The clip position is the jet needle groove on
which the clip is installed.
The positions are numbered from the top.
Check that the accelerator pump operates
smoothly. (except for rich mixture symp-
tom).
Rich mixture
Raise jet needle clip position. (1 groove up)
1/4–3/4 throttle Hard breathing
Lack of speed Lower jet needle clip position. (1 groove
down)
1/4–1/2 throttle Slow speed pick-up
Poor acceleration Raise jet needle clip position. (1 groove up)
Closed to 1/4 throttle Hard breathing
Speed down Use jet needle with a smaller diameter. Slow-speed-circuit passage
Clogged→Clean.
Overflow from carburetor
Closed to 1/4 throttle Poor acceleration Use jet needle with a larger diameter.
Raise jet needle clip position. (1 groove up)
Poor response in the low to in-
termediate speeds Raise jet needle clip position.
If this has no effect, lower the jet needle clip
position.
Poor response when throttle is
opened quickly Check overall settings.
Use main jet with a lower calibration no.
Raise jet needle clip position. (1 groove up)
If these have no effect, use a main jet with
a higher calibration no. and lower the jet
needle clip position. Check air filter for fouling.
Check that the accelerator pump operates
smoothly.
Jet needleClip
Groove 7 Groove 6
Groove 5
Groove 4
Groove 3
Groove 2
Groove 1
Leaner
(Standard) Richer
Page 100 of 224
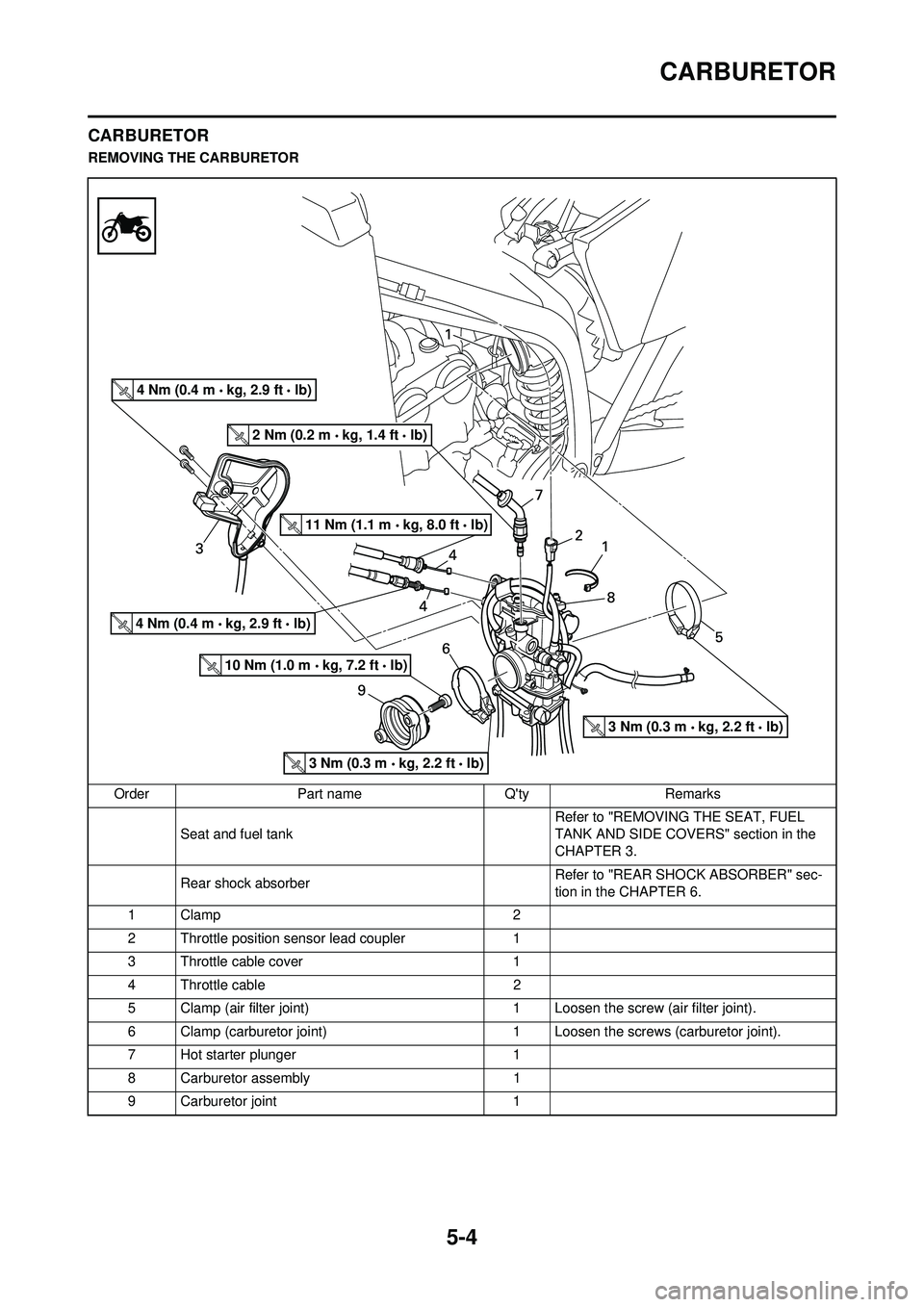
5-4
CARBURETOR
CARBURETOR
REMOVING THE CARBURETOROrder Part name Q'ty Remarks Seat and fuel tank Refer to "REMOVING THE SEAT, FUEL
TANK AND SIDE COVERS" section in the
CHAPTER 3.
Rear shock absorber Refer to "REAR SHOCK ABSORBER" sec-
tion in the CHAPTER 6.
1Clamp 2
2 Throttle position sensor lead coupler 1
3 Throttle cable cover 1
4 Throttle cable 2
5 Clamp (air filter joint) 1 Loosen the screw (air filter joint).
6 Clamp (carburetor joint) 1 Loosen the screws (carburetor joint).
7 Hot starter plunger 1
8 Carburetor assembly 1
9 Carburetor joint 1
4 Nm (0.4 m kg, 2.9 ft lb)
2 Nm (0.2 m kg, 1.4 ft lb)
11 Nm (1.1 m kg, 8.0 ft lb)
4 Nm (0.4 m kg, 2.9 ft lb)
10 Nm (1.0 m kg, 7.2 ft lb)
3 Nm (0.3 m kg, 2.2 ft lb)
3 Nm (0.3 m kg, 2.2 ft lb)
Page 103 of 224
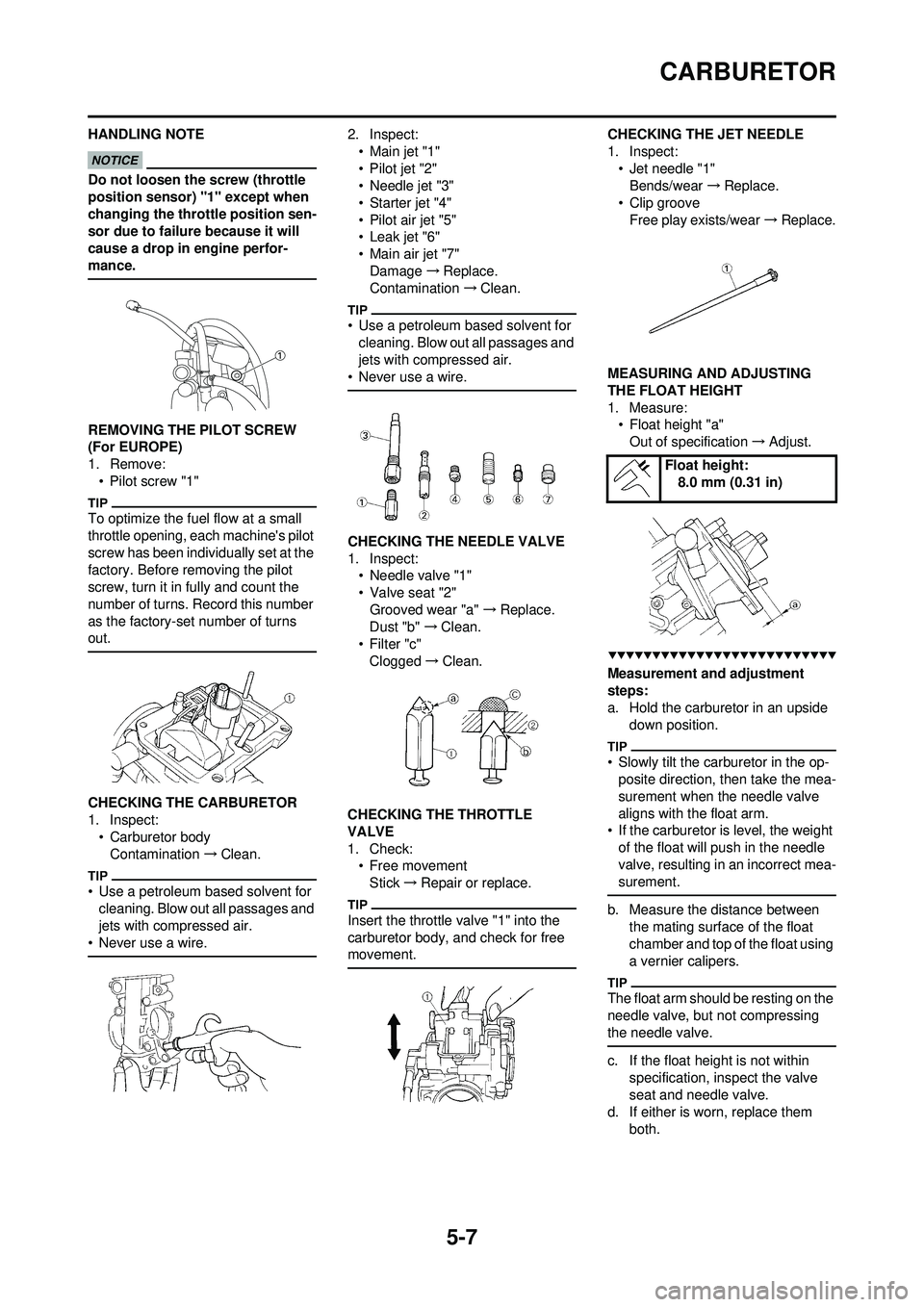
5-7
CARBURETOR
HANDLING NOTE
Do not loosen the screw (throttle
position sensor) "1" except when
changing the throttle position sen-
sor due to failure because it will
cause a drop in engine perfor-
mance.
REMOVING THE PILOT SCREW
(For EUROPE)
1. Remove:• Pilot screw "1"
To optimize the fuel flow at a small
throttle opening, each machine's pilot
screw has been individually set at the
factory. Before removing the pilot
screw, turn it in fully and count the
number of turns. Record this number
as the factory-set number of turns
out.
CHECKING THE CARBURETOR
1. Inspect:• Carburetor body
Contamination →Clean.
• Use a petroleum based solvent for
cleaning. Blow out all passages and
jets with compressed air.
• Never use a wire.
2. Inspect: •Main jet "1"
• Pilot jet "2"
• Needle jet "3"
• Starter jet "4"
• Pilot air jet "5"
•Leak jet "6"
• Main air jet "7"Damage →Replace.
Contamination →Clean.
• Use a petroleum based solvent for
cleaning. Blow out all passages and
jets with compressed air.
• Never use a wire.
CHECKING THE NEEDLE VALVE
1. Inspect: • Needle valve "1"
• Valve seat "2"
Grooved wear "a" →Replace.
Dust "b" →Clean.
•Filter "c" Clogged →Clean.
CHECKING THE THROTTLE
VALVE
1. Check: • Free movement
Stick →Repair or replace.
Insert the throttle valve "1" into the
carburetor body, and check for free
movement.
CHECKING THE JET NEEDLE
1. Inspect:
•Jet needle "1"Bends/wear →Replace.
• Clip groove Free play exists/wear →Replace.
MEASURING AND ADJUSTING
THE FLOAT HEIGHT
1. Measure: • Float height "a"
Out of specification →Adjust.
Measurement and adjustment
steps:
a. Hold the carburetor in an upside
down position.
• Slowly tilt the carburetor in the op-posite direction, then take the mea-
surement when the needle valve
aligns with the float arm.
• If the carburetor is level, the weight
of the float will push in the needle
valve, resulting in an incorrect mea-
surement.
b. Measure the distance between the mating surface of the float
chamber and top of the float using
a vernier calipers.
The float arm should be resting on the
needle valve, but not compressing
the needle valve.
c. If the float height is not within specification, inspect the valve
seat and needle valve.
d. If either is worn, replace them
both.
Float height:8.0 mm (0.31 in)
Page 197 of 224
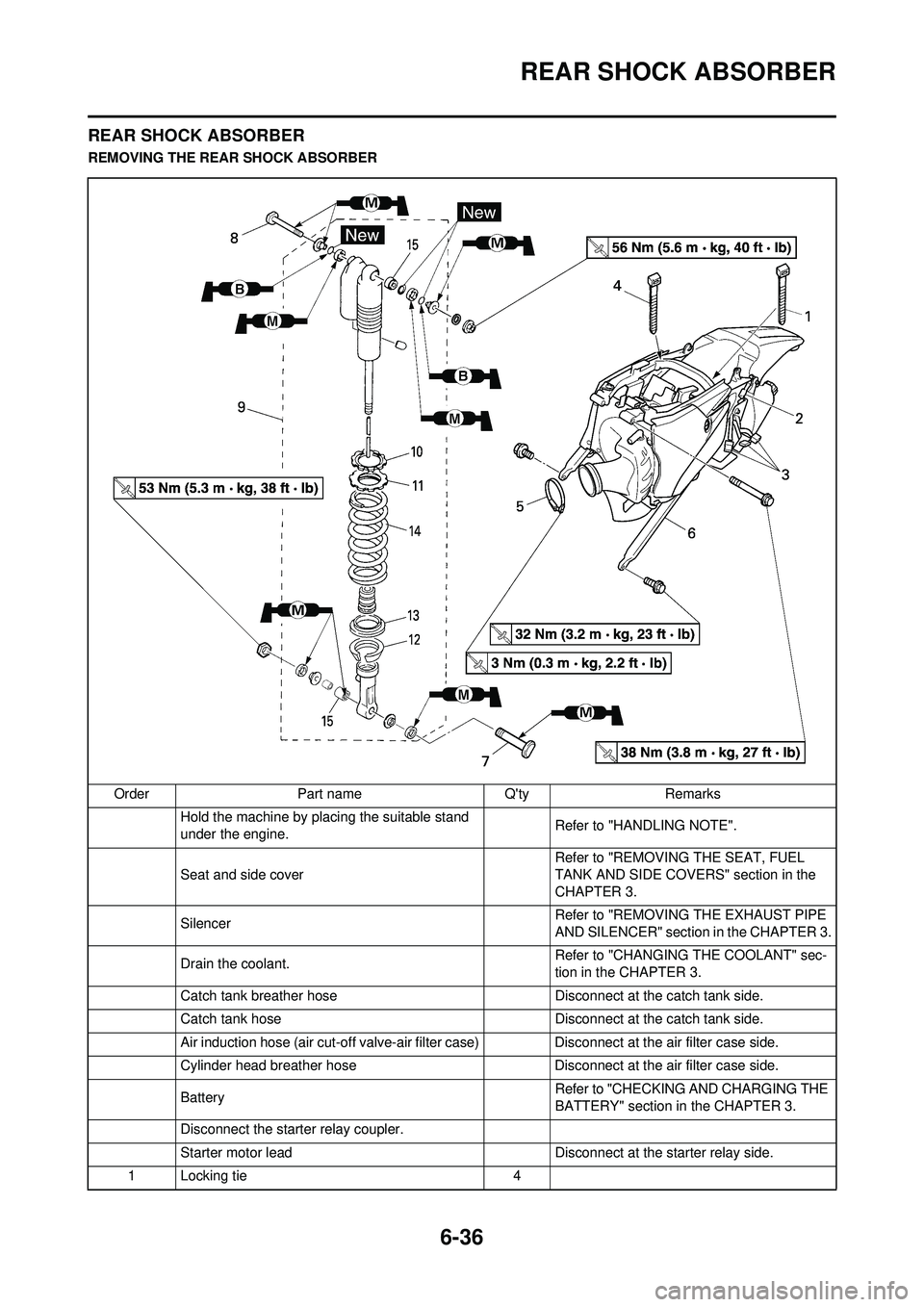
6-36
REAR SHOCK ABSORBER
REAR SHOCK ABSORBER
REMOVING THE REAR SHOCK ABSORBEROrder Part name Q'ty Remarks Hold the machine by placing the suitable stand
under the engine. Refer to "HANDLING NOTE".
Seat and side cover Refer to "REMOVING THE SEAT, FUEL
TANK AND SIDE COVERS" section in the
CHAPTER 3.
Silencer Refer to "REMOVING THE EXHAUST PIPE
AND SILENCER" section in the CHAPTER 3.
Drain the coolant. Refer to "CHANGING THE COOLANT" sec-
tion in the CHAPTER 3.
Catch tank breather hose Disconnect at the catch tank side.
Catch tank hose Disconnect at the catch tank side.
Air induction hose (air cut-off valve-air filter case) Disconnect at the air filter case side.
Cylinder head breather hose Disconnect at the air filter case side.
Battery Refer to "CHECKING AND CHARGING THE
BATTERY" section in the CHAPTER 3.
Disconnect the starter relay coupler.
Starter motor lead Disconnect at the starter relay side.
1 Locking tie 4